组合机床总体设计
机床总体设计(全)

机床结构布局:立式、卧式、斜置式。 基础支承件的形式:底座式、立柱式、龙门式。
基础支承件的结构形式:一体式、分离式。
同一种运动分配式可以有多种结构布局形式,运动分配 设计阶段评价后,需对结构布局方案进行评价,去除不 合理方案。 评价的主要依据是定性分析机床的刚度、占地面积、与 物流系统的可亲和性等。
设计结果是得到机床总体结构布局形态图。
机床支承形式的选择
• 机床的支承件:床身、底座、立柱、横梁、横臂等。
– 柱形:支承件是立柱,或立柱与底座的组合—立式机床。 – 倒T字形:支承件是床身和立柱的组合—复合式机床。 – 槽形:支承件是床身(底座)、立柱和横臂三者的组合—单 臂式机床。 – 框形:支承件由床身、横梁及双立柱组成,形成封闭的框形 结构—龙门式机床。
总体方案综合评价与选择:对各种方案进行综合评价,从中选择较 好的方案。 总体方案的设计修改与优化
对所选择的方案进行进一步修改或优化,确定最终方案。
BACK
3.1.3 机床的设计步骤
结构设计
设计机床的传动系统,确定各主要结构的原理方案,设计部件装配图,对主要 零部件进行分析计算和优化,设计液压原理图和相应液压部件装配图,设计电 气控制系统原理图和相应的电气安装接线图,设计和完善机床总装配图和总联 系尺寸图。
上述步骤反复进行,直到达到设计结果满意为止。 定型设计,结构设计完成之后,可进行实物样机的制造、实验及评价。根 据实物样机的评价结果进行修改设计,最终完成产品的定型设计。
BACK
3.1.4 机床总体设计一、床系列型谱的确定由于各种机床用户生产的产品和规模不同,对机床性 能和结构的要求也不同,因此,同一机床甚至同一规 格的机床,还需要有各种变形,以满足用户各种各样 的需求。为了以最少的品种规格,满足尽可能多用户 的不同需求,通常是按照该类机床的主参数标准,先 确定一种用途最广,需求量最大的机床作为“基型系 列”,在这系列的基础上,根据用户的需求派生出若 干变型机床,形成“变型系列”。“基型”和“变型” 构成了机床的“系列型谱”。
第四章组合机床设计资料

向力造成的振动。
② 当缸孔孔间距及平行度要求高(±0.02~0.03mm),缸孔
对定位基准位置精度要求高于±0.05mm时,通常采用由单个精
镗头组成的多轴机床结构方案,使各精镗头可单独调整位置。还 需配置高精度动力滑台,来提高机床工作的平稳性。
二、工艺方案的拟订
③ 同样精度的孔,因材料、硬度的不同,其工艺方案也不 同,如加工钢件一般比加工铸铁件的工步数多。 ④ 加工薄壁易振动的工件或刚性不足的工件,安排工序不
机械制造装备设计
第四章 组合机床设计
2019年1月1日
第四章 组合机床设计 第二节 组合机床总体设计
一、 组合机床设计步骤 二、 工艺方案的拟订 三、 确定切削用量及切削力 四、 组合机床三图一卡设计
一、组合机床设计步骤
组合机床设计是根据被加工零件的加工内容、加工精度、生
产率要求、成本价格等原始数据,进行总体设计、传动系设计、 夹具设计。 设计步骤: ♦ 调查研究, ♦ 总体方案设计, ♦ 技术设计, ♦ 工作设计。
二、工艺方案的拟订
3.合理实施工序集中
工序集中 运用多种刀具,采用多面、多工位和复合刀具加 工方法,在一台机床上对一个或几个零件完成多个工序过程,以 提高生产率。
(1)注意工序集中带来的问题
♦ 导致机床结构复杂,刀具数量增加, 调整不方便,可靠性降低,影响生产率 的提高。 ♦ 导致切削负荷加大,造成工件刚 性不足、工件变形而影响加工精度。
4.工作设计
绘制多轴箱、夹具等专用零部件的施工图纸、编制零部件明 细表;编写机床说明书,制订机床检验、试机等验收标准。
二、工艺方案的拟订
(一)工艺方案的制定内容
分析被加工零件图纸 ①根据组合机床各工艺方法能达到的
A2J-PK786前轴钻主削孔立式单面U钻组合机床总体设计

由于 厂 方 的技 术 协 议上 要 求 刀具 使 用 SC 刀 具 ,根 据表 2 EO ,推 荐切 削 用
组织 专业 化批量 生 产或 外购 。
产 的特 点设 计组 合 机床 的重要 因素 。被 加 工零 件 的 生产 批 量越 大 ,工 序安 排
一
般趋 于 分 散 。而 且 ,其 粗 、半 精 、精 加 工应 分 别 在不 同机 床上 完 成 。从 零
件 的外 型 及轮 廓 尺 寸看 ,可采 用 单工 位 固 定式 夹 具 的机床 配 置 形式 。 由于 被 加 工零 件 的 生产 批 量大 ( 生产 量6 0 0件 ),两 以 Ir 年 9 00 : 芋的安排 趋 于 分散 属 于粗 加 工阶段 。四是机 床 使用 条件 。主 要 有 : ① 车 间布 置 情况 :工 件输 送 滚 道 穿过 机 床 , l 没引成 通 过 式 ,且 配 涞 置不 超 过三 面 ;同 时,装 卸 工件 只 能推进 拉 出,机 床 安 嚣 中间 导向 。
术的前提下进 行的 。被加 工工件材料 为4 C M / B 0 7 2 r o G 3 7 ,工件硬度 为H 2 9 3 9 B 6 — 0 ,由此 及被加工 孔的位置 ,初步制定 组合机床 的方案 ,决定采 厢立 式单面组台机床 , 由 一
面 两销进行 定位 。由于被加 工零件 的生产批量 大 ( 生产量6 0 0 件 ),所 以工序 的安排趋 于分散 ,属于粗 加工阶 段,推 荐切削用 量为v = 5 / ,f O 3 m r 年 90 0 l 1 m mn - . m / ,选 择 采 用S C 刀具 。最 后为设计 的关键点 :三 图一卡 。即对被加工零 件工序 图、加工示意 图、机床联 系尺寸 图、机床 生产 率计算 卡的绘制与 计算 。 EO 关键词: 组合机床 :三 图一卡 ;工件材料 ;立式单面组合 机床
(完整版)组合机床总体设计
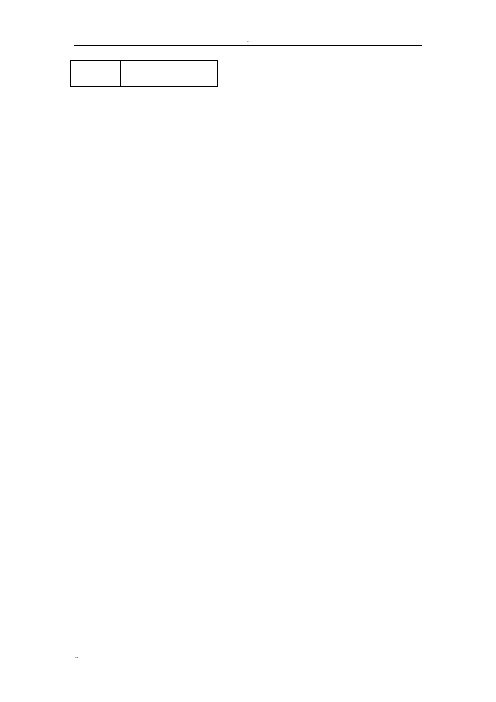
2009年5月23 日目录第一部分组合机床总体设计 (3)一、工艺方案的制定 (3)1.1零件工艺基面的选择 (3)1.2 加工工艺分析 (3)1.3 孔切削用量的选择 (3)二、机床配置型式和结构方案的确定 (4)三、组合机床方案图纸设计 (4)3.1被加工零件工序图 (4)3.2加工示意图 (5)3.2.1加工示意图的编制步骤 (6)3.3组合机床生产率的计算 (11)3.3.1生产率的计算和生产率计算卡的绘制 (11)3.4机床联系尺寸图的绘制 (13)3.4.1机床主要联系尺寸的确定 (14)第一部分组合机床总体设计一、工艺方案的制定1.1零件工艺基面的选择由于被加工零件(缝纫机体)是箱体类零件,所以我选择了“一面二孔”的定位方法。
该方法有以下特点:a、很简便的消除工件的六个自由读,使工件获得稳定的固定位置;b、有同时加工五个面的可能。
既能高度集中加工工序,又有利于提高各面上孔的位置精度;c、该方法可以作为从粗加工到精加工的全部工序加工的基准,使整个工艺过程实现基准统一;d、该方法使夹紧方便,夹紧机构简单。
容易使夹紧力对准支承,消除夹紧力引起工件变形对加工精度的影响。
为了保证零件的加工精度及技术要求,工艺基面必须规定相应的公差。
根据缝纫机体零件的大小,定位销孔径选择∅16,太小时,定位销很细,加工中易受力产生较大的变形。
销孔的精度为2级,两销孔中心距定为321毫米,其公差为±毫米。
0.061.2 加工工艺分析由于被加工零件只需要钻孔,所以该机床只有一个钻孔加工工艺。
而且钻孔深度不大,属于一般钻孔。
1.3 孔切削用量的选择由于该缝纫机体是铸铁件,而且硬度大概在200~241左右,根据下表选取切削用量。
表1用高速钢钻头加工铸铁件的切削用量二、机床配置型式和结构方案的确定由于被加工的缝纫机体是一个箱体件,一次只加工一个,生产率要求不是很高,所以我选择了单工位组合机床,而且该零件孔中心线与定位基准面平行,而且需要同时加工两个面,因此选择单工位组合机床中的卧式双面组合机床。
组合机床总体及主轴箱的设计

1前言1.1研究的目的和意义主轴箱是选用通用零件,按专业要求进行设计的。
它通过按一定速比排布传动齿轮,把动力从动力部件——动力头、动力箱、电动机等传递给各工作主轴,使之获得所要求的转速和转向。
主轴箱主轴前端外伸部分和机床刀具装置连接,从而完成被加工零件。
目的是熟练利用CAD绘图软件进行绘图,掌握基本的设计方法和能力,为以后的学习和工作打下良好的基础。
研究汽缸盖钻铰组合机床不但有助于汽缸盖的加工水平提高,从而提高我国的汽车生产水平,而且对我国组合机床的发展也有重要意义。
1.2国内外研究现状我国的组合机床产业发展比较晚,原因之一是我国整体的工业发展就比较晚,其次我国的工业水平已经落后了一大截。
组合机床的发展是由汽车产业的带动,由专用机床发展而来的。
改革开放后,我国的组合机床产业得到了很大的发展,特别是民营企业对发展组合机床起到了很大的作用,他们的设计和改良使得组合机床的效率和加工水平得到了极大的提高。
我国的组合机床主要优势在于劳动力密集,缺点是精度不高,没有什么科技水平。
工业革命后,国外的工业发展很快,组合机床的发展更是如此。
由于他们的起步早,发展到现在,组合机床的种类繁多,可以满足用户和生产的各种需求。
国外的组合机床自动化程度高,广泛使用了数控技术,不仅提高了生产效率,而且对操作人员的安全有保障。
1.3研究内容和方法组合机床总体设计是针对具体的被加工零件,在选定工艺方案和结构方案的基础上,进行方案图纸设计,本设计要求完成机床联系尺寸图、被加工零件工序图、加工示意图。
主轴箱传动系统是多轴、多齿轮、多排次的复杂齿轮传动系统。
在完成组合机床总体设计之后,利用CAD绘图软件设计有四根主轴的主轴箱,主轴的转速分别为200r/min。
根据所提供的技术数据,选择主要通用部件,然后按照组合机床设计步骤进行:绘制机床总图、加工工序图、计算切削用量及绘制加工示意图、主轴箱传动系统设计(4轴n=200r/min),最后绘制主轴箱装配图和主要零件图,并写出设计说明书。
组合机床总体设计

变速器上盖组合机床总体设计摘要组合机床是根据工件加工需要,以大量通用部件为基础,配以少量专用部件组成的一种高效专用机床。
目前,组合机床主要用于平面加工和孔加工两类工序。
而且其生产效率高,加工精度稳定,自动化程度高,使工人劳动强度降低。
由于本次加工的零件为变速器箱体,为大批量生产,而且所要加工的孔较多,本次设计的组合机床主要是对孔进行加工。
此设计绘制的是机床联系尺寸总图。
它是以被加工零件工序图和加工示意图为依据,并初步按选定的主要通用部件以及确定的专用部件的总体结构而绘制的。
是用来表示机床的配置形式,主要构成及各部件安装位置,相互联系,运动关系的总体布局图。
由于组合机床进行加工能够进行多工位加工,提高自动化程度,缩短加工时间和辅助时间。
而且组合机床大部分都是由通用部件组成,研制周期较短,便于设计,制造和使用维护,成本低。
而且机床易于改造,产品和工艺变化时,通用部件还能重复利用,经济性较好。
所以组合机床在大批量生产中的应用十分广泛。
关键词:组合机床,机床总图,自动化The overall design of combination machine tools for the cover oftransmissionABSTRACTThe assembly machine processes is according to the requirement of work pieces , and it is made of a lot of general use parts and a little exclusive use parts and it is a kind of a efficiently production machine. The present, assembly machine tool primarily is used in making the plane surface and the apertures. And because of high production efficiency, the accuracy of process, the stability of it's result, the automation extent higher, and so it can debase the strength of the labour.Because this parts for processing is transmission box, there is a lot of apertures in the part , and want that the processed bore is more, so the main process is making the holes.The design draw's is a total diagram of size of contact of tool machine. It is with was process the spare parts work preface diagram and process sketch map is basis, and the first step press the total structure of the main and in general use parts and certain appropriation parts that make selection but draw of. Is to use to mean that the tool machine installs the form, main composing and each parts install the position, contacting mutually, exercise total layout diagram of relation.Because the assembly machine tool can process some parts together ,so it can boost to automate extent, and shorten the time of process,And that assembly machine tool is made of a lot of general use parts, short the time of design, and it is convenient for designing, fabrication , the cost is low. And the machine tool is apt to be reconstructed, When the technics route changes, the general parts can be reused again, so we use assemble machine tool is economical .So large numbers of assembly machine tools are applied in the machine industrial.KEY WORDS: assembled machine tool,two-sided,active boring board,total diagram of tool machine,automation目录第1章组合机床理论基础 (5)1.1机床在国民经济的地位 (5)1.2组合机床的组成及特点 (5)1.3 组合机床研究基本内容 (6)第2章组合机床方案的制定 (7)2.1 组合机床的工艺范围及配置形式 (7)2.1.1 组合机床工艺范围 (7)2.1.2 组合机床配置形式 (7)2.2 组合机床工艺方案的拟定 (8)2.2.1 确定工艺方案的基本原则 (8)2.2.2 确定工艺方案应注意的问题 (8)第3章组合机床总体设计 (10)3.1 被加工零件工序图 (10)3.1.1 被加工零件工序图的作用与内容 (10)3.1.2 加工零件要求 (10)3.2组合机床切削用量 (11)3.2.1 确定切削用量应注意的问题 (11)3.2.2 切削用量的计算 (12)第4章加工示意图 (14)4.1 加工示意图的作用和内容 (14)4.2刀具,工具,导向装置的选择 (15)4.2.1刀具的选择 (15)4.2.2接杆的选择 (15)4.2.3导向套的选择 (15)4.3初定主轴类型、尺寸和外伸长度 (16)4.4动力部件的工作循环及工作行程的确定 (16)第5章机床联系尺寸图及生产率计算卡 (18)5.1 机床动力部件的选择 (18)5.1.1 动力箱的选择 (18)5.1.2 动力滑台的选择及附属部件 (19)5.2 确定机床尺寸 (21)5.2.1 确定装料高度 (21)5.2.2 中间底座轮廓尺寸 (21)5.2.3 多轴箱轮廓尺寸 (22)5.2 确定机床尺寸 (23)5.3 机床生产率计算卡 (24)结论 (27)谢辞 (28)参考文献 (29)第1章组合机床理论基础1.1机床在国民经济的地位随着现代化工业技术的快速发展,特别是随着它在自动化领域内的快速发展,组合机床的研究已经成为当今机器制造界的一个重要方向,在现代工业运用中,大多数机器的设计和制造都是用机床大批量完成的。
免费组合数控机床设计(一).doc
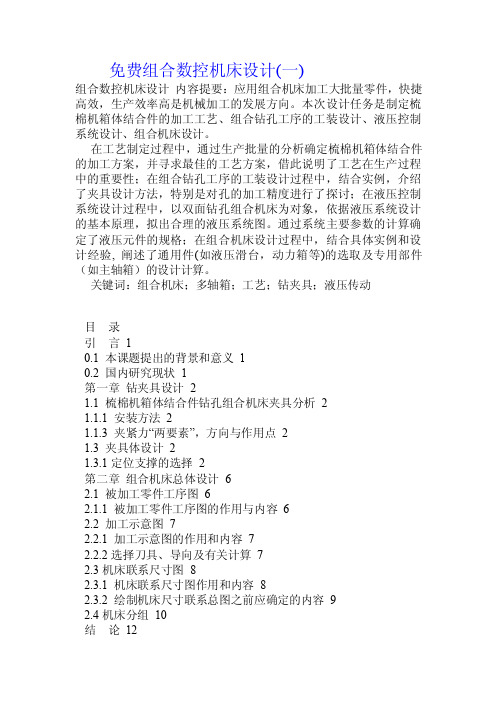
免费组合数控机床设计(一)组合数控机床设计内容提要:应用组合机床加工大批量零件,快捷高效,生产效率高是机械加工的发展方向。
本次设计任务是制定梳棉机箱体结合件的加工工艺、组合钻孔工序的工装设计、液压控制系统设计、组合机床设计。
在工艺制定过程中,通过生产批量的分析确定梳棉机箱体结合件的加工方案,并寻求最佳的工艺方案,借此说明了工艺在生产过程中的重要性;在组合钻孔工序的工装设计过程中,结合实例,介绍了夹具设计方法,特别是对孔的加工精度进行了探讨;在液压控制系统设计过程中,以双面钻孔组合机床为对象,依据液压系统设计的基本原理,拟出合理的液压系统图。
通过系统主要参数的计算确定了液压元件的规格;在组合机床设计过程中,结合具体实例和设计经验, 阐述了通用件(如液压滑台,动力箱等)的选取及专用部件(如主轴箱)的设计计算。
关键词:组合机床;多轴箱;工艺;钻夹具;液压传动目录引言10.1 本课题提出的背景和意义10.2 国内研究现状1第一章钻夹具设计 21.1 梳棉机箱体结合件钻孔组合机床夹具分析21.1.1 安装方法21.1.3 夹紧力“两要素”,方向与作用点21.3 夹具体设计21.3.1定位支撑的选择2第二章组合机床总体设计 62.1 被加工零件工序图62.1.1 被加工零件工序图的作用与内容62.2 加工示意图72.2.1 加工示意图的作用和内容72.2.2选择刀具、导向及有关计算72.3机床联系尺寸图82.3.1 机床联系尺寸图作用和内容82.3.2 绘制机床尺寸联系总图之前应确定的内容92.4机床分组10结论12致谢13引言0.1 本课题提出的背景和意义在第四代梳棉机生产过程中,先进的生产工艺和生产设备被引入。
本文针对组合机床在梳棉机制造过程中的应用现状,以梳棉机箱体结合件的加工为例,阐述了工艺、工装、组合机床的设计过程。
0.2 国内研究现状第一章钻夹具设计1.1 梳棉机箱体结合件钻孔组合机床夹具分析1.1.1 安装方法根据工件不同的生产条件,可以有各种不同的安装方法:a)找正安装法;b)夹具安装法。
毕业论文组合机床设计

毕业设计题目:两缸柴油机机体8-M8螺纹底孔组合钻床的总体设计及主轴箱设计学科部:___________________________________专业:____________________________________班级:____________________________________学号:____________________________________学生姓名:_________________________________指导教师:_________________________________起讫日期:_________________________________中文摘要本次设计是对卧式单面8 轴组合钻床的设计,设计的内容包括组合钻床的总体设计以及多轴箱的设计。
组合钻床的总体设计主要是“三图”的设计。
三图的设计包括:被加工零件工序图、加工示意图、机床联系尺寸图。
多轴箱的设计关键是传动系统方案的确定。
再根据传动系统图确定手柄轴和油泵轴的位置安排,然后进行坐标计算,绘制多轴箱装配总图,箱体补充加工图,前盖补充加工图、最后根据上面的内容设计组合钻床。
关键子字:组合钻床、多轴箱、被加工零件工序图、加工示意图、机床联系尺寸图。
外文摘要This design is to horizontal axis combination drilling machine of single anddesign, the design of content including combination drilling machine of the overall design and the design of the spindle box. Combination drilling machine of the overall design mainly is the "three figure" design. The design of the three figure includes: processing parts process diagram, processing schemes, machine tool contact size figure. The design of the spindle box is key to the scheme determination of transmission system. Again according to the transmission system graph determine the handle axis and oil pump shaft placement, and then coordinate calculation, draw spindle box of general assembly, the casing is added processing figure, the front cover added processing diagram, according to the content of the above design combination drilling machine.Key son word : combination drilling machine, spindle box, be processing parts process diagram, processing schemes, machine tool contact size figure.、尸■、亠前言组合机床是用按系列化标准化设计的通用部件和按被加工零件的形状及加工工艺要求设计的专用部件组成的专用机床。
- 1、下载文档前请自行甄别文档内容的完整性,平台不提供额外的编辑、内容补充、找答案等附加服务。
- 2、"仅部分预览"的文档,不可在线预览部分如存在完整性等问题,可反馈申请退款(可完整预览的文档不适用该条件!)。
- 3、如文档侵犯您的权益,请联系客服反馈,我们会尽快为您处理(人工客服工作时间:9:00-18:30)。
制订组合机床工艺方案的主要依据
工件的材料及硬度,加工部位的结构形状,工 件刚性,定位基面的特点等,对组合机床工艺 方案的制订都有着重要影响
不可选择零件上直径太小的孔作为定位销孔,因定位销过细,易受力变形,甚至 因装卸工件碰撞而破坏定位。根据箱体零件的大小及重量,销孔直径可能参考下 表选取
定位销孔推荐直径
工件重量(kg) 定位销孔直径
< 20 > Φ12
20 ~ 50 > Φ16
50 ~ 100 > Φ20
> 100 > Φ25
有的箱体零件不具备“一面双孔”定位基准,可采用“三平面”定位。 应当注意,不管是“一面双孔”还是“三平面”定位,其主要定位面最好采用箱
一 确定组合机床工艺方案的基本原则及注意的问题
(一)确定组合机床工艺方案的基本原则
粗、精加工分开原则
①同一台多工位机床(如回转工作台 式机床)上粗、精加工工序分开在相 隔工位数较多的两个位置上进行. ②粗、精加工分开在自动线或流水线 相隔机床数(工序数)较多的两台机 床上进行
工序集中原则
适当考虑相同 类型工序的集 中
采用钻—倒角复合
4、螺纹孔一般采用一个工步一次攻至所需深度。当螺纹孔较深时,为防止丝锥折断,可 利用二次进给攻丝,即第一次攻到一段距离后丝锥反转退回,但不全部退出工件孔,第二
次攻至全深。
4、影响工艺方案的主要因素
1)加工工序内容和加工精度
2)被加工零件的特点 3)零件的生产批量
4)厂后方车间制造能力
螺纹孔类型
工艺过程
一般紧固螺纹孔 较高精度螺纹孔
钻底孔、(倒角)、攻丝 钻孔、扩至底尺寸、(倒角)攻丝(或用挤压丝锥加工)
注:1、螺纹孔加工应根据不同直径及加工精度,采取不同工步数;
2、攻丝前最好在孔口倒角,以确保攻丝精度;
ห้องสมุดไป่ตู้
3、中小零件,可在多工位机床上采用一个工位倒角,有时也可 刀具在一个工位上进行;
。 体设计基准,即箱体在机器中的主要安装面
2)非箱体类零件定位基准的选择
(1)对曲轴、连杆、转向器壳、半轴、拨叉等零件,应采用以V形铁为 主要定位元件的定位方法。
提高定位精度,应对V形铁定位圆提出精度要求;V形铁角度一般取90º~ 120º 。
(2)对“法兰”类零件,常采用一个孔(或外圆)及一个平面的定位方法。
有相对位置精 度要求的工序 应集中加工
1.集中攻螺纹 2.集中深孔加 3.集中镗孔 4.集中一般的钻、铰
(二)确定组合机床工艺方案应注意的问题
按一般原则拟订工艺 方案时的一些限制
1 孔间中心距的限制 2 工件结构工艺性的 限制
其它应注意的问题
1 精镗孔注意孔表面是否允许留有退刀刀痕。 2 对互相结合的两壳体零件,均应分别从结合面加工联
加工精度
H6
孔
Φ40以下(无底孔)
H7
加工直径到Φ16 mm
钻、铰或钻、扩、铰
加工直径大于Φ16 mm
钻、扩、铰或钻、扩、粗铰、精铰
H8
加工直径到Φ20 mm
钻、扩、铰或钻—铰复合
加工直径大于Φ20 mm
钻、扩、铰或钻—镗复合
H8—H10
加工直径到Φ25 mm 钻、扩或钻、铰 加工直径大于Φ25 mm 钻、镗或钻、扩—铰复合
深入现场调查分析零件的加工工艺方法,定位和夹紧方式,所采用的 设备、刀具及切削用量,生产率情况及工作条件等方面的现行工艺资 料,以便制订出切合实际的合理工艺方案。
2 定位基准和夹压部件的选择
1)箱体类零件定位基准的选择
定位基准选择“一面双孔”是最常用的方法。
特点
1 消除工件的六个自由度使其获得稳定可靠的定位。
H11
加工直径到Φ30 mm
钻
加工直径大于Φ30 mm
钻、扩或钻—铰复合
径
Φ40以上(有铸孔) 扩(粗镗)、扩(半精镗)、精镗、细镗 扩、半精镗、精镗 扩、扩、粗铰、精铰 粗镗、半精镗、精镗
粗镗、精镗(单刀) 粗镗、精镗(双刀) 扩、铰—挤复合
扩、扩 扩、铰 粗镗、精镗
扩 粗镗 粗镗、半精镗
表3—5 螺纹孔的典型工艺过程
3 组合机床常用工艺方法能达到的精度及表面粗糙度
由于被加工零件的精度要求、 加工部位尺寸、 形状、 结构特点、 材料、 生产率要求不同, 设计组合机床必须采用不同的工艺方法和工艺过程。
不同配置型式组合机床采取的常用工艺方法及所能达到的经济精度及表面粗糙度 见表3—2至表3—5 。
表3—3 铸铁件不同精度孔所采用的典型工艺方法
在选择定位基面的同时,要相应决定夹压位置。此时应注意的问题 是:
(1)确保零件夹压后定位稳定。为使工件在加工过程中不产 生振动和位移,夹压力要足够,夹压点布置应使夹压合力 落在定位平面内,力求接近定位平面的中心。
(2)尽量减少和避免工件夹压后的变形,消除其对加工精度 的不利影响。为此,应避免把夹压点放在工件加工孔的上 方和容易引起变形之处。例如,加工刚性差的零件应适当 增加辅助支承或采用多点夹压方法,以使夹压分力布均匀, 减少夹压变形,提高加工精度。
接孔。 3 钻阶梯孔先钻大孔后钻小孔。 4 平面一般采用铣削加工。 5 制订加工一个工件的几台成套机床或流水线的工艺方
案时,应尽可能使精加工集中在所有粗加工之后, 以减少内应力变形影响,有利于保证加工精度。
二 组合机床工艺方案的拟订
拟订组合机床工艺方案的
1 分析、研究加工要求和现场工艺
如被加工零件的用途及其结构特点,加工部位及其精度、表面粗糙度、 技术要求及生产纲领。
当需要限制零件的六个自由度时,可再用一个孔(或一个筋或凸台)来限制 零件圆周方向的转动。
3)选择定位基准的原则
确保工件 稳定定位
基准重合原则
定位基准
被加工零件不 具备理想的定 位基准或工件 刚性不足,可 在机床上设置 辅助支承,以 增加定位稳定 性和承受较大 的切削力。
基准统一原则
4)夹压点位置确定
2 加工零件五个表面时能高度集中工序和提高各面上孔的位置
一 面
精度。
双 孔
3 使零件整个工艺过程基准统一和机床各工序(工位)的许多
(
部件(如夹具)实现通用化。
最
常
4 易于实现自动化定位、夹紧,并有利于防止切屑落于定位基
用
)
面上。
作为定位基准的平面和销孔的一般要求:尺寸精度、表面粗糙度及位置精度。 销孔 H7级精度 二销孔中心距L公差 ± 0.03 ~ 0.1 mm (工件轮廓尺寸大时取大值) 平面 平面度公差 ± 0.05 ~ 0.1 mm 表面粗糙度 Ra = 16 ~ 8 μm