种电解铝阳极废料分离回收方法
废旧铝电解电容器回收拆解成套装备使用计划(八)

废旧铝电解电容器回收拆解成套装备使用计划一、实施背景随着科技的不断发展,电子产品的更新换代速度越来越快,废旧电子产品的数量也在不断增加。
废旧电子产品中含有大量的有害物质,对环境和人体健康造成严重影响。
废旧铝电解电容器是电子产品中常见的一种元器件,其中的铝元素对环境和人体健康具有潜在的危害。
因此,开展废旧铝电解电容器的回收拆解工作,对于环境保护和资源利用具有重要意义。
二、工作原理废旧铝电解电容器回收拆解成套装备使用计划的工作原理是通过回收废旧铝电解电容器,将其拆解成各个部件,并对其中的铝元素进行提取和回收。
具体的工作流程如下:1.收集废旧铝电解电容器:通过与各类电子产品制造商、维修商、回收企业等建立合作关系,收集废旧铝电解电容器。
2.拆解废旧铝电解电容器:将收集到的废旧铝电解电容器进行拆解,分离出其中的铝元素。
3.提取和回收铝元素:对拆解后的废旧铝电解电容器进行处理,提取其中的铝元素,并进行回收利用。
4.处理废弃物:对拆解后的其他部件进行分类处理,将可回收的部分进行回收利用,将不可回收的部分进行安全处理。
三、实施计划步骤1.建立合作关系:与各类电子产品制造商、维修商、回收企业等建立合作关系,确保能够获取足够的废旧铝电解电容器。
2.设立回收点:在各个城市设立回收点,方便用户将废旧铝电解电容器交给回收人员。
3.进行拆解工作:将收集到的废旧铝电解电容器进行拆解,分离出其中的铝元素。
4.提取和回收铝元素:对拆解后的废旧铝电解电容器进行处理,提取其中的铝元素,并进行回收利用。
5.处理废弃物:对拆解后的其他部件进行分类处理,将可回收的部分进行回收利用,将不可回收的部分进行安全处理。
6.宣传推广:通过各种渠道进行宣传推广,提高废旧铝电解电容器回收拆解的知名度和参与度。
四、适用范围废旧铝电解电容器回收拆解成套装备使用计划适用于各类电子产品制造商、维修商、回收企业等,以及广大用户。
通过与各类合作伙伴建立合作关系,可以收集到大量的废旧铝电解电容器,实现对其的回收和利用。
一种电解铝厂铝灰的高效利用工艺

一种电解铝厂铝灰的高效利用工艺铝灰是电解铝厂生产过程中产生的一种废弃物,其主要成分是氧化铝和杂质金属。
传统上,铝灰被视为废弃物,直接进行填埋或堆放处理。
然而,随着环境保护意识的增强和资源回收利用的重要性的认识,研发一种高效利用铝灰的工艺变得非常重要。
本文将介绍一种高效利用电解铝厂铝灰的工艺,以期对实际生产中的废弃物处理和资源回收利用提供借鉴。
铝灰中的氧化铝可以通过化学方法进行提取和回收。
目前常用的方法是采用酸浸法,将铝灰与稀硫酸反应,生成硫酸铝溶液。
经过过滤、蒸发和结晶等工艺步骤,可以得到高纯度的氧化铝产品。
这种方法不仅可以回收铝资源,还可以减少对天然铝矿石的开采,降低环境负荷。
铝灰中的杂质金属可以通过熔炼和分离的方法进行回收。
在高温条件下,将铝灰与适量的焦炭加热,使金属杂质发生还原和熔化,然后通过熔融分离的方法,将金属杂质与铝金属分离。
这种方法不仅可以回收铝金属,还可以回收其他有价值的金属元素,如铜、铁等。
通过精细的分离工艺,可以获得高纯度的金属产品。
铝灰还可以作为建筑材料的原料进行利用。
通过对铝灰进行研磨和筛分,可以获得适当粒度的铝灰粉末。
铝灰粉末可以用于生产水泥、混凝土、砖块等建筑材料,不仅可以降低原材料成本,还可以减少对天然资源的消耗。
同时,铝灰在建筑材料中的应用具有良好的隔热、隔音和耐火性能,可以提高建筑材料的功能性和性能。
铝灰还可以用于环境修复和土壤改良。
经过适当的处理和改良,铝灰可以作为土地改良剂或肥料使用。
铝灰中的氧化铝和其他元素可以为植物提供营养,改善土壤结构和肥力。
此外,铝灰还可以用于修复重金属污染土壤,通过吸附和沉淀作用,减少重金属的毒性和迁移性,恢复土壤的生态功能。
电解铝厂铝灰的高效利用工艺可以通过化学提取、金属回收、建筑材料利用和环境修复等多种方式实现。
这种工艺不仅可以减少废弃物的排放和对自然资源的消耗,还可以回收有价值的物质和能源。
同时,这种工艺还可以降低生产成本,提高资源利用效率,促进电解铝行业的可持续发展。
铝电解废旧阴极中碳和电解质的分离及回收利用

铝电解废旧阴极中碳和电解质的分离及回收利用铝电解废旧阴极中碳和电解质的分离及回收利用近年来,随着工业化的快速发展,铝产量急剧增长,导致铝电解废旧阴极的数量不断增加。
废旧阴极中含有大量的碳和电解质,若能有效地分离和回收利用,不仅可以减少资源的浪费,还能对环境产生正面的影响。
首先,我们需要了解铝电解废旧阴极的特点。
废旧阴极通常由碳块和铝金属组成,以及一定量的电解质。
碳块作为阴极主体材料,不仅含有大量的有机碳,还含有一定量的铝金属。
电解质则主要由氟化铝和铝酸盐组成,其功能是提供离子导电和维持电解质中铝含量的稳定。
针对废旧阴极中碳和电解质的分离,目前主要采用的方法是热处理。
热处理可以通过提高温度将碳和电解质分离,但这种方法存在能源消耗大、产生有害气体以及对环境造成污染等问题。
基于上述问题,我们提出了一种新的分离和回收利用方法——机械化学分离法。
该方法首先采用机械方法将废旧阴极块破碎成小颗粒,然后在化学溶液中进行浸泡。
在溶液中,碳块中的有机碳和铝金属会与溶液中的特定化学物质发生反应,使碳块中的有机碳得以溶解。
而电解质则会沉淀于溶液中,经过沉淀和过滤等步骤,可以将电解质从溶液中分离出来。
但是,机械化学分离法也存在一定的缺陷。
首先,机械化学分离法无法完全除去碳块中的有机碳,因为有机碳在机械处理和化学反应过程中可能无法充分溶解。
其次,电解质的回收仍需进一步优化,以提高回收效率。
针对以上问题,我们提出了进一步的改进方案。
对于碳块中的有机碳,可以引入高温氧化和煅烧等处理方法,将有机碳转化为二氧化碳和水蒸气,从而实现有机碳的完全分解和回收。
对于电解质的回收,可以考虑利用膜分离技术或离子交换技术,通过膜的选择性渗透性或离子交换树脂的吸附选择性,将电解质与其他杂质分离。
同时,我们还应关注废旧阴极的综合利用方面。
除了碳和电解质的分离和回收,废旧阴极中的铝金属也具有很高的价值。
可以利用电解法将废旧阴极中的铝金属再次提纯,以实现铝金属的循环利用。
废铝的分离与回收
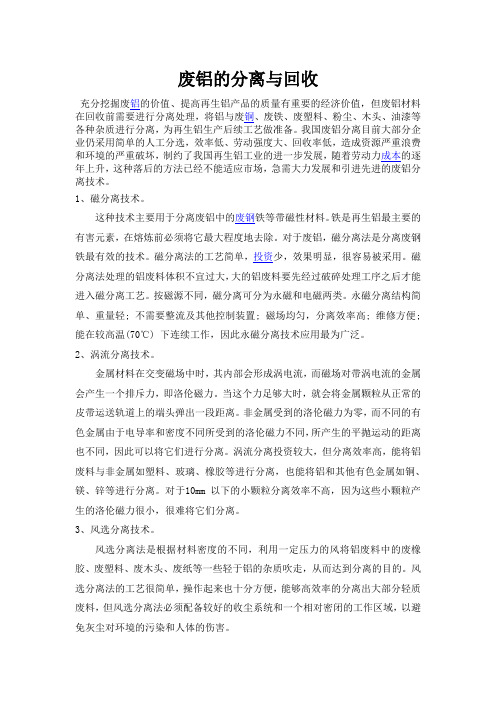
废铝的分离与回收充分挖掘废铝的价值、提高再生铝产品的质量有重要的经济价值,但废铝材料在回收前需要进行分离处理,将铝与废铜、废铁、废塑料、粉尘、木头、油漆等各种杂质进行分离,为再生铝生产后续工艺做准备。
我国废铝分离目前大部分企业仍采用简单的人工分选,效率低、劳动强度大、回收率低,造成资源严重浪费和环境的严重破坏,制约了我国再生铝工业的进一步发展,随着劳动力成本的逐年上升,这种落后的方法已经不能适应市场,急需大力发展和引进先进的废铝分离技术。
1、磁分离技术。
这种技术主要用于分离废铝中的废钢铁等带磁性材料。
铁是再生铝最主要的有害元素,在熔炼前必须将它最大程度地去除。
对于废铝,磁分离法是分离废钢铁最有效的技术。
磁分离法的工艺简单,投资少,效果明显,很容易被采用。
磁分离法处理的铝废料体积不宜过大,大的铝废料要先经过破碎处理工序之后才能进入磁分离工艺。
按磁源不同,磁分离可分为永磁和电磁两类。
永磁分离结构简单、重量轻; 不需要整流及其他控制装置; 磁场均匀,分离效率高; 维修方便; 能在较高温(70℃) 下连续工作,因此永磁分离技术应用最为广泛。
2、涡流分离技术。
金属材料在交变磁场中时,其内部会形成涡电流,而磁场对带涡电流的金属会产生一个排斥力,即洛伦磁力。
当这个力足够大时,就会将金属颗粒从正常的皮带运送轨道上的端头弹出一段距离。
非金属受到的洛伦磁力为零,而不同的有色金属由于电导率和密度不同所受到的洛伦磁力不同,所产生的平抛运动的距离也不同,因此可以将它们进行分离。
涡流分离投资较大,但分离效率高,能将铝废料与非金属如塑料、玻璃、橡胶等进行分离,也能将铝和其他有色金属如铜、镁、锌等进行分离。
对于10mm 以下的小颗粒分离效率不高,因为这些小颗粒产生的洛伦磁力很小,很难将它们分离。
3、风选分离技术。
风选分离法是根据材料密度的不同,利用一定压力的风将铝废料中的废橡胶、废塑料、废木头、废纸等一些轻于铝的杂质吹走,从而达到分离的目的。
铝型材废铝回收工艺流程

铝型材废铝回收工艺流程随着工业的发展和资源的日益稀缺,废铝的回收已成为一项重要的环保产业。
铝型材是一种常见的铝合金产品,其回收利用对于节约资源和减少环境污染具有重要意义。
下面将介绍铝型材废铝回收的工艺流程。
1. 收集和分类废铝的回收过程首先需要进行收集和分类。
收集可以通过回收站、废品回收公司等渠道进行,分类则是根据废铝的种类和杂质程度进行分别处理。
常见的铝型材废铝有铝门窗型材、铝合金管等,其杂质主要包括铁、塑料等。
2. 破碎和分选经过分类后的铝型材废铝需要进行破碎和分选。
破碎是将废铝进行细碎,以便后续处理。
分选则是根据废铝的杂质种类和粒度大小进行分离,常用的分选设备有磁选机、振动筛等。
3. 清洗和除杂清洗是指将废铝进行除尘和除油处理,以去除表面的杂质和污染物。
除尘可以通过风力或水力进行,除油则可以使用溶剂或碱性清洗剂。
除杂是指将废铝中的其他杂质如塑料、胶带等进行分离,常用的方法有重力分离、气浮分离等。
4. 熔化和精炼经过前面的处理,废铝被破碎、分选、清洗和除杂后得到的纯净铝料需要进行熔化和精炼。
熔化是指将废铝加热至熔点,使其转化为液态铝。
精炼则是通过去除铝中的杂质,提高铝的纯度。
常用的精炼方法有氧化剂精炼、电解精炼等。
5. 再生和成型经过熔化和精炼后的铝液可以进行再生利用。
再生是指将铝液进行冷却固化,形成铝型材。
再生后的铝型材可以按照需要进行进一步的加工和成型,如铝型材压铸、铝型材挤压等。
6. 检测和质量控制铝型材废铝回收过程中需要进行检测和质量控制,以确保回收产品的质量符合标准。
常见的检测方法有化学分析、物理性能测试等。
质量控制则是对回收过程中的各个环节进行监控和管理,确保产品的质量稳定和一致性。
7. 废渣处理回收过程中产生的废渣需要进行处理和处置。
废渣主要包括破碎后的杂质、清洗和除杂过程中的污染物等。
废渣处理可以采用物理方法如压实、焚烧等,也可以采用化学方法如中和、固化等。
铝型材废铝回收工艺流程包括收集和分类、破碎和分选、清洗和除杂、熔化和精炼、再生和成型、检测和质量控制,以及废渣处理等环节。
废铝合金的回收方法

废铝合金的回收方法
废铝合金的回收方法主要有以下几种:
1. 熔炼回收:将废铝合金加热至熔点,然后通过熔炼设备将其熔化成液态铝,并去除杂质。
这种方法适用于纯铝合金或者低合金度较高的废铝合金。
2. 溶解回收:将废铝合金放入酸性或碱性溶液中进行溶解,使铝与其他元素分离。
然后通过沉淀、过滤、电解等工艺步骤,将铝从溶液中提取出来。
这种方法适用于高合金度的废铝合金。
3. 粉碎回收:将废铝合金进行机械粉碎,得到细小的颗粒。
然后通过重力分选、磁选、浮选等物理分离方法,将铝与其他材料分离,再利用特定的提纯技术提取纯度较高的铝。
4. 压缩回收:对大体积的废铝合金进行压缩处理,使其体积减小,方便储存和运输。
压缩后的废铝合金可以直接作为原料出售给冶炼厂或再生铝加工企业进行回收利用。
以上是常见的废铝合金回收方法,具体选择哪种方法取决于废铝合金的类型、合金度和市场需求等因素。
值得注意的是,在进行废铝合金回收时,应遵守环境保护法规,采取相应的防护措施,确保回收过程安全环保。
阳极泥中有价金属的绿色高效回收关键技术

阳极泥中有价金属的绿色高效回收关键技术随着现代工业的发展,电解铝生产已经成为工业生产中必不可少的一环。
在电解铝生产过程中,阳极泥是不可避免的产物之一。
阳极泥是一种由铝电解池阳极产生的含有高浓度的氧化铝及各种金属的残渣。
其中大量包含有铝、钛、镁等高价值金属和一些稀土元素。
对于这些金属,市场需求较大,其高效回收显得尤为重要。
因此,各国在阳极泥的有价金属回收方面加大了力度,针对其进行了深入研究,探索出了多种高效回收技术。
一、盐酸浸出法盐酸浸出法是目前应用最广的阳极泥中有价金属回收技术。
其主要原理是将阳极泥放入加热的酸液中进行浸出,然后进行分离、净化、还原等处理,得到目标金属。
优点:1.回收率高,能够回收大部分有价金属;2.工艺简单,在生产实践中得到广泛应用;3.符合环保要求,使用的酸性物质可以循环利用,不会对环境造成污染。
1.消耗大量的酸性物质,造成一定的经济负担;2.生产过程中涉及到的酸液使用和回收都需要较高的技术要求。
二、氧化铝煮沸法氧化铝煮沸法是指先将阳极泥烧成氧化铝,然后进行煮沸、酸洗、还原等处理,得到有价金属。
1.获得的产品质量高,不夹杂其他杂质;2.回收率高,相对稳定;3.操作简单,不需要过于复杂的设备和技术设备。
1.需要先将阳极泥烧成氧化铝,过程较为耗时;2.工艺复杂,需要严格控制操作条件和参数。
三、甲苯溶液重提法甲苯溶液重提法是指将阳极泥在甲苯中进行溶解和过滤,过滤后得到含有有价金属离子的溶液,然后通过重提、还原、沉淀等步骤获取有价金属。
1.节省了工艺流程,节省了许多时间;2.回收的有价金属品质高,可以减少不必要的净化工作。
1.不适用于阳极泥中含有较高浓度的铝、钛等金属,回收率偏低;2.甲苯为有机物,易挥发,操作中需要注意操作人员的健康和安全。
电解铝过程中废弃含锂电解质的回收技术研究进展

管理及其他M anagement and other电解铝过程中废弃含锂电解质的回收技术研究进展况 鑫摘要:目前我国工业炼铝主要采用的方法为霍尔—埃鲁炼铝法,其技术原理为以冰晶石Na3AlF6为溶剂、氧化铝为溶质而组成的冰晶石—氧化铝熔盐电解法。
在铝电解槽中,固体氧化铝溶解在熔融态的冰晶石溶剂中,形成对应的电解质体系,并在直流电的作用下,将电解质中的氧化铝分解还原得到金属铝。
同时随着电解过程的进行,铝土矿中伴生资源锂也以氟化锂的形态被逐渐富集于电解质中。
由于缺乏锂的析出手段,氟化锂在电解质中处于持续富集的状态。
根据行业相关研究显示,电解质中存在的氟化锂可起到降低初晶温度、降低电解质密度、可提高电导率等正面的影响,在冶炼过程一定浓度的锂对冶炼有着助推作用,因此,在一定浓度范围时工厂并未对其采取剥离处理,部分企业甚至在初期会补加锂盐做助溶剂,以改善电解质性质,降低能耗提高电解效率。
根据相关统计,每年堆存的废弃含锂电解质约有40万吨~50万吨,其中夹带的氟化锂资源含量可达到5%~7%,折合锂1.3%~1.8%。
具有极高的潜在回收价值。
本文通过对现有含锂铝电解质相关研究的资源收集,进行了归纳整理,并结合实际的开发技术经验,提出后续技术开发思路。
关键词:含锂电解质;锂回收随着世界工业化进程的不断推进,能源经历了从初期取之不尽用之不竭的快速消耗时代转入能源不可再生,需可持续发展的新能源循环时代。
我国虽然地大物博,有着较高的挖掘潜力,但是在能源板块上存在先天不足。
基于此,自进入21世纪以来,我国确立了走可持续发展、安全可靠的新能源战略发展方针,其中电能作为能源转化的核心中轴,储能技术的发展水平关系到整体能源战略的根基稳固情况。
锂电池由于其独特的元素性质,在目前储存市场上已经形成一家独大的锂电池使用市场,锂电池各类产品也在不断的推陈出新,如三元锂、钴酸锂、磷酸锂电池以及概念中的锂空电池等。
锂作为锂电池核心的支撑材料,可以预计的锂在未来的电能储能市场上将始终占据着最重要的地位,其资源的战略重要性亦将始终贯穿于新能源行业的发展主线。
种电解铝阳极废料分离回收方法
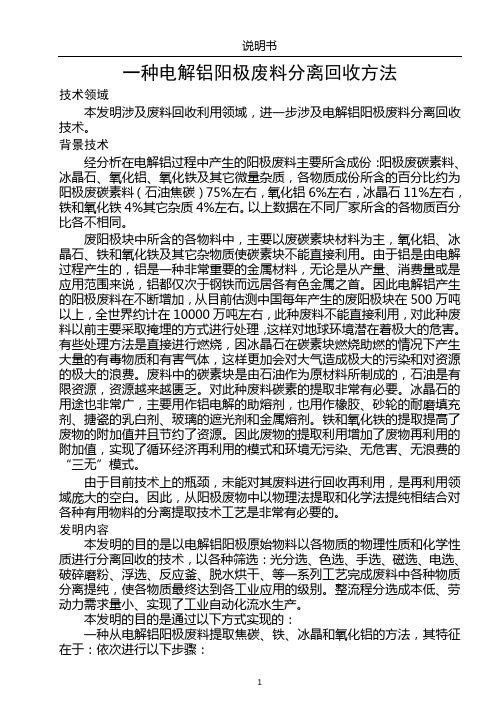
一种电解铝阳极废料分离回收方法技术领域本发明涉及废料回收利用领域,进一步涉及电解铝阳极废料分离回收技术。
背景技术经分析在电解铝过程中产生的阳极废料主要所含成份:阳极废碳素料、冰晶石、氧化铝、氧化铁及其它微量杂质,各物质成份所含的百分比约为阳极废碳素料(石油焦碳)75%左右,氧化铝6%左右,冰晶石11%左右,铁和氧化铁4%其它杂质4%左右。
以上数据在不同厂家所含的各物质百分比各不相同。
废阳极块中所含的各物料中,主要以废碳素块材料为主,氧化铝、冰晶石、铁和氧化铁及其它杂物质使碳素块不能直接利用。
由于铝是由电解过程产生的,铝是一种非常重要的金属材料,无论是从产量、消费量或是应用范围来说,铝都仅次于钢铁而远居各有色金属之首。
因此电解铝产生的阳极废料在不断增加,从目前估测中国每年产生的废阳极块在500万吨以上,全世界约计在10000万吨左右,此种废料不能直接利用,对此种废料以前主要采取掩埋的方式进行处理,这样对地球环境潜在着极大的危害。
有些处理方法是直接进行燃烧,因冰晶石在碳素块燃烧助燃的情况下产生大量的有毒物质和有害气体,这样更加会对大气造成极大的污染和对资源的极大的浪费。
废料中的碳素块是由石油作为原材料所制成的,石油是有限资源,资源越来越匮乏。
对此种废料碳素的提取非常有必要。
冰晶石的用途也非常广,主要用作铝电解的助熔剂,也用作橡胶、砂轮的耐磨填充剂、搪瓷的乳白剂、玻璃的遮光剂和金属熔剂。
铁和氧化铁的提取提高了废物的附加值并且节约了资源。
因此废物的提取利用增加了废物再利用的附加值,实现了循环经济再利用的模式和环境无污染、无危害、无浪费的“三无”模式。
由于目前技术上的瓶颈,未能对其废料进行回收再利用,是再利用领域庞大的空白。
因此,从阳极废物中以物理法提取和化学法提纯相结合对各种有用物料的分离提取技术工艺是非常有必要的。
发明内容本发明的目的是以电解铝阳极原始物料以各物质的物理性质和化学性质进行分离回收的技术,以各种筛选:光分选、色选、手选、磁选、电选、破碎磨粉、浮选、反应釜、脱水烘干、等一系列工艺完成废料中各种物质分离提纯,使各物质最终达到各工业应用的级别。
- 1、下载文档前请自行甄别文档内容的完整性,平台不提供额外的编辑、内容补充、找答案等附加服务。
- 2、"仅部分预览"的文档,不可在线预览部分如存在完整性等问题,可反馈申请退款(可完整预览的文档不适用该条件!)。
- 3、如文档侵犯您的权益,请联系客服反馈,我们会尽快为您处理(人工客服工作时间:9:00-18:30)。
一种电解铝阳极废料分离回收方法技术领域本发明涉及废料回收利用领域,进一步涉及电解铝阳极废料分离回收技术。
背景技术经分析在电解铝过程中产生的阳极废料主要所含成份:阳极废碳素料、冰晶石、氧化铝、氧化铁及其它微量杂质,各物质成份所含的百分比约为阳极废碳素料(石油焦碳)75%左右,氧化铝6%左右,冰晶石11%左右,铁和氧化铁4%其它杂质4%左右。
以上数据在不同厂家所含的各物质百分比各不相同。
废阳极块中所含的各物料中,主要以废碳素块材料为主,氧化铝、冰晶石、铁和氧化铁及其它杂物质使碳素块不能直接利用。
由于铝是由电解过程产生的,铝是一种非常重要的金属材料,无论是从产量、消费量或是应用范围来说,铝都仅次于钢铁而远居各有色金属之首。
因此电解铝产生的阳极废料在不断增加,从目前估测中国每年产生的废阳极块在500万吨以上,全世界约计在10000万吨左右,此种废料不能直接利用,对此种废料以前主要采取掩埋的方式进行处理,这样对地球环境潜在着极大的危害。
有些处理方法是直接进行燃烧,因冰晶石在碳素块燃烧助燃的情况下产生大量的有毒物质和有害气体,这样更加会对大气造成极大的污染和对资源的极大的浪费。
废料中的碳素块是由石油作为原材料所制成的,石油是有限资源,资源越来越匮乏。
对此种废料碳素的提取非常有必要。
冰晶石的用途也非常广,主要用作铝电解的助熔剂,也用作橡胶、砂轮的耐磨填充剂、搪瓷的乳白剂、玻璃的遮光剂和金属熔剂。
铁和氧化铁的提取提高了废物的附加值并且节约了资源。
因此废物的提取利用增加了废物再利用的附加值,实现了循环经济再利用的模式和环境无污染、无危害、无浪费的“三无”模式。
由于目前技术上的瓶颈,未能对其废料进行回收再利用,是再利用领域庞大的空白。
因此,从阳极废物中以物理法提取和化学法提纯相结合对各种有用物料的分离提取技术工艺是非常有必要的。
发明内容本发明的目的是以电解铝阳极原始物料以各物质的物理性质和化学性质进行分离回收的技术,以各种筛选:光分选、色选、手选、磁选、电选、破碎磨粉、浮选、反应釜、脱水烘干、等一系列工艺完成废料中各种物质分离提纯,使各物质最终达到各工业应用的级别。
整流程分选成本低、劳动力需求量小、实现了工业自动化流水生产。
本发明的目的是通过以下方式实现的:一种从电解铝阳极废料提取焦碳、铁、冰晶和氧化铝的方法,其特征在于:依次进行以下步骤:a将电解铝废料用上料工具送至收尘储料仓,储料仓为上端封闭型有收尘孔,当物料进仓时风道上端电阀门自动打开并进行收尘,仓内壁有橡胶铺垫,仓下端为出料口可根据物料大小来调整口径。
b把物料通过大型皮带输送机送入振动收尘筛,振动筛如图X,振动筛下侧有收尘系统和储料仓,振动筛孔可根据物料筛选要求的粒度来调整,振动筛为活动型,一端固定在仓体一侧,另一端放置在仓体橡胶垫上。
振动筛由上端拉动定时为筛网上的物料进行清理,振动筛拉至垂直角度后30°左右,使物料自动脱落下,并落至下端橡胶皮垫上。
使大焦碳块物料直径或长度大于13cm左右以上的物料通过机下皮带输送机运至机外(大块物料全部为焦碳块,此类焦碳块所含灰粉极少,无需再次加工分选,可直接利用)。
c把筛下小与13cm左右的物料通过磁选皮带输送机6A送至组合圆筒除尘筛7,6A输送的同时把磁性物C1提取。
d组合圆筒除尘筛7把送至的物料进行筛选分级,在筛选的同时各物料在组合圆筒除尘筛中互相碰撞摩擦,使焦碳表面附着结合的冰晶石或氧化铝受到摩擦脱落。
并把产生的粉尘收集。
e把组合圆筒除尘筛筛分的各类物料通过送料机送至料仓或直接进入色选机、光分选机以及手工光照分选(根据物料颜色和透明性差异及光性不同进行分选)。
f组合圆筒除尘筛筛下的3cm以下的物料通过磁选输送机6B把非磁性物输送至多层振动除尘筛。
6B输送的同时把磁性物C2提取分离。
g多台多层振动除尘筛把筛选物料分成:Φ20-30mm、Φ10-20mm、Φ5-10mm、Φ3-5mm、Φ1-3mm、Φ0.5-1mm、Φ0.5mm以下的共7种物料,并把各类物料通过送料机送至各自的储料仓。
h把各种物料从各自的料仓中用过各自的送料机,送至各类物料相对应的加热式电选机进行分选。
物料的粒径不同,所用的加热式电选机内部结构和喂料不尽相同,分选时可用多辊或单辊进行反复分选,直达到各自分选的物料质量要求为准,大于Φ3mm以上的物料电选设备各送料系统尽量用皮带输送机输送,因皮带输送机不易破坏原物料的粒度,并且不易使非焦碳物外表附着细焦碳粉。
分选此类物料的加热型电选机机上端要用振动喂料系统,因振动喂料系统不易破坏物料的粒度。
小于Φ3mm以下的物料所用加热型电选机,因粒度较小,可用花键罗拉轴来进行喂料。
通过各类加热型电选机分选,把焦碳和其他物料分选开,此类分选的焦碳因粒度较大,所含灰粉极少,可直接利用(改变了原始把各种粒度的物料全部进行粉碎、磨粉,再用浮选方法进行焦碳的提取,节省了大量能源、水源和劳动力)。
i把分离出的非焦碳物A1、A2、A3通过破碎机进行破碎(由锤式破碎机、鄂式破碎机、对辊式破碎机、锥湿破碎机进行破碎),粉碎后直接进入磨粉设备(涡流磨、振动磨、球磨机、对辊磨机等)进行细磨,磨出的粉通过集料器收集后进行筛选,把粒度大于50目的物料返回磨机进行再次磨粉,各粉碎设备和筛机都有除尘设备。
j把粉碎后粒度小于50目以下的物料送入浮选机,浮选时加入浮选药剂(捕收剂、起泡剂、调整剂),使焦碳和非碳物(冰晶石、氧化铝)分离开,焦碳经多次浮选分离后进行脱水、烘干形成纯净的焦碳粉B7,分离出冰晶石和氧化铝的混合物(浮选所用的水和浮选药剂全部循环利用)。
k分出的冰晶石、氧化铝经过脱水和烘干后进入加热型电选机进行分选,根据冰晶石和氧化铝的电性差异(包括介电常数、电导率、及相对电阻、电热性、比导电度及整流性等),进行电选分离得到纯净的冰晶石和含有微量杂质的氧化铝。
l把含杂的氧化铝送入反应釜,加入数倍的含氟盐酸,再加热温度至50-100℃,搅拌反应一定时间排出,再经过过滤、脱液,把过滤、脱液的液体循环使用,把脱液后的物料进行水洗,水洗后进行脱水、烘干得到高纯的冰晶石。
m焦碳物B6Φ1-3mm、焦碳B6Φ1-0.5mm和焦碳B750目以下按一定比例加入沥青进行搅拌、混捏、压块成型、焙烧等工艺制成焦碳块(或把各类焦碳粒B直接利用或出售)。
n分选过程中的磁性物C1和C2通过分选把大块纯铁物分选出来,把氧化铁和碳的结合物再进行粉碎、磨粉和磁选,分选出焦碳和氧化铁。
附图说明图1为本发明的示意图。
图2为本发明的图。
具体实施方式以下结合实施例对发明的结构及使用情况加以详细说明:实施例1:电解铝废渣,上料(铲车1),收尘储料仓2,自动输送机3,振动收尘机筛4,分离为大于13厘米的炭物和小于或等于13厘米的物料,其中:大于13厘米的炭物经输送机5送至物料仓炭C1;物料仓炭C1收集备用;小于或等于13厘米的物料,经磁选输送机6A分离为磁性物L1,其余再经组合圆筒风选筛7,按颗粒大小分解为7-13厘米物料(大于7厘米、小于或等于13厘米,不含7厘米),3-7厘米物料(大于或等于3厘米,小于或等于7厘米),3厘米以下物料(不含3厘米)三种;其中,7-13厘米物料经输送机8输送至料仓9,再经输送机10,经色选机、手工分选或光分离方法分离出纯炭C2,电解质和非炭物A1;纯炭C2收集备用;3-7厘米物料经输送机11输送至料仓12,再经输送机13,经色选机、手工分选或光分离方法分离出纯炭C3,电解质和非炭物A2;纯炭C3收集备用;3厘米以下物料经磁选输送机6B分离为磁性物L2、多层振动风选机14。
多层振动风选机14按颗粒大小分离为五种:其一,20-30毫米(大于或等于20毫米,小于30毫米),经送料机16;其二,10-20毫米(大于或等于10毫米,小于20毫米),经送料机17;两种大小颗粒分别送至组合式料仓18的相分隔的两个仓体内,仓体下部有控制调节板,其可控制物料的释放;释放至送料机19送至提升机20,再经电选机21,分离出纯炭C4和少量炭和杂物,其中,纯炭C4收集备用;少量炭和杂物经上料机22输送至电选机23,电选机23分离出炭和少量杂物及电解质和杂物A3,其中,炭和少量杂物经提升机24返回电选机21;其三,5-10毫米(大于或等于5毫米,小于10毫米),经送料机25;其四,3-5毫米(大于或等于3毫米,小于5毫米),经送料机26;两种大小颗粒分别送至组合式料仓27的相分隔的两个仓体内,仓体下部有控制调节板,其可控制物料的释放;释放至送料机28送至提升机29,再经电选机30,分离出纯炭C5和少量炭和杂物,其中,纯炭C5收集备用;少量炭和杂物经上料机31输送至电选机33,电选机33分离出炭和少量杂物及电解质和杂物A4,其中,炭和少量杂物经送料机32返回电选机30;其五,小于3毫米的物料经多层振动风选筛15分离为大小不同的三种物料:其一,1-3毫米(大于或等于1毫米,小于3毫米),经送料机34;其二,0.5-1毫米(大于或等于0.5毫米,小于1毫米),经送料机35;两种大小颗粒分别送至组合式料仓36的相分隔的两个仓体内,仓体下部有控制调节板,其可控制物料的释放;释放至送料机37送至提升机38,再经电选机39,分离出纯炭C6和少量炭和杂物,其中,纯炭C6收集备用;少量炭和杂物经上料机40输送至电选机41,电选机41分离出炭和少量杂物及电解质和杂物A5,其中,炭和少量杂物经送料机42返回电选机39;其三,0.5以下物料D2;收尘储料仓2、振动收尘机筛4、组合圆筒风选筛7、多层振动风选机14、多层振动风选机15产生的尘土经收尘设备65收集形成细电解质废渣D1;A1、A2、A3送至破碎机43,经破碎后,与A4、A5一同经送料机44,送至磨粉机45磨粉,进入一道集料器46及二道集料器49,其中,进入一道集料器46的大部分的小于或等于60目物料直接转入二道集料器49;大于60目物料经一道集料器46下沉收集的物料再投入振动筛48,分为两种:大于60目物料与小于或等于60目物料,其中,大于60目物料返回磨粉机45;小于或等于60目物料,与直接进入二道集料器49的物料合并,通过送料机50送至浮选机51,加入浮选药剂(搜捕剂、起泡剂、调整剂等),再进入浮选机52,进入沉淀池53(浮选机51和浮选机52由沉淀池53供水),沉淀后形成湿炭与湿电解质;其中,湿炭经脱水机54脱水后,进入烘干机55烘干形成炭C7;湿杂物经脱水机56(各脱水机废液体进入沉淀池53沉淀后使用),脱水后烘干再经过电选30C分离出纯净冰晶石和杂质送至反应釜57(反应釜由储液罐提供化学药物――含氟盐酸,经反应后的药物返回储液罐)(反应釜反应条件是:加热50-100℃,再加入数倍的含氟盐酸进行搅拌反应,从而得到纯度高的冰晶石),经石晶冰湿,脱液机58(脱液后的化学药物返回储液罐)后送料机59送入水洗机60(水洗机60由蓄水池供水,水洗后的水再返回至蓄水池),经送料机61送入脱水机62脱水后进入送料机63,废水含酸性,经碱化中和处理达标后排放;再送入烘干机64烘干,形成高纯度冰晶石。