元器件焊盘设计
pcb焊盘设计规范
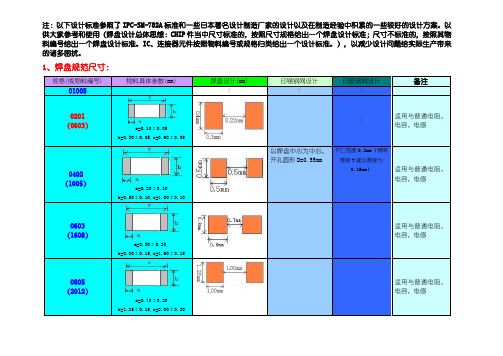
注:以下设计标准参照了IPC-SM-782A标准和一些日本著名设计制造厂家的设计以及在制造经验中积累的一些较好的设计方案。
以供大家参考和使用(焊盘设计总体思想:CHIP件当中尺寸标准的,按照尺寸规格给出一个焊盘设计标准;尺寸不标准的,按照其物料编号给出一个焊盘设计标准。
IC、连接器元件按照物料编号或规格归类给出一个设计标准。
),以减少设计问题给实际生产带来的诸多困扰。
1、焊盘规范尺寸:规格(或物料编号) 物料具体参数(mm) 焊盘设计(mm) 印锡钢网设计印胶钢网设计备注01005 / / / /0201(0603)a=0.10±0.05b=0.30±0.05,c=0.60±0.05 /适用与普通电阻、电容、电感0402(1005)a=0.20±0.10b=0.50±0.10,c=1.00±0.10 以焊盘中心为中心,开孔圆形D=0.55mm开口宽度0.2mm(钢网厚度T建议厚度为0.15mm)适用与普通电阻、电容、电感0603(1608)a=0.30±0.20,b=0.80±0.15,c=1.60±0.15 适用与普通电阻、电容、电感0805(2012)a=0.40±0.20b=1.25±0.15,c=2.00±0.20 适用与普通电阻、电容、电感1206(3216)a=0.50±0.20b=1.60±0.15,c=3.20±0.20 适用与普通电阻、电容、电感1210(3225)a=0.50±0.20b=2.50±0.20,c=3.20±0.20 适用与普通电阻、电容、电感1812(4532)a=0.50±0.20b=3.20±0.20,c=4.50±0.20 适用与普通电阻、电容、电感2010(5025)a=0.60±0.20b=2.50±0.20,c=5.00±0.20 适用与普通电阻、电容、电感2512(6432)a=0.60±0.20b=3.20±0.20,c=6.40±0.20 适用与普通电阻、电容、电感1:1开口,不避锡珠5700-250AA2-0300排阻0404(1010)a=0.25±0.10,b=1.00±0.10c=1.00±0.10,d=0.35±0.10p=0.65±0.05排阻0804(2010)a=0.25±0.10,b=2.00±0.10c=1.00±0.10,d=0.30±0.15p=0.50±0.05排阻1206(3216)a=0.30±0.15,b=3.2±0.15c=1.60±0.15,d=0.50±0.15p=0.80±0.10排阻 1606 (4016)a=0.25±0.10,b=4.00±0.20 c=1.60±0.15,d=0.30±0.10p=0.50±0.05472X-R05240-10a=0.38±0.05,b=2.50±0.10 c=1.00±0.10,d=0.20±0.05 d1=0.40±0.05,p=0.50钽质电容适用于钽质电容1206 (3216) a=0.80±0.30,b=1.60±0.20 c=3.20±0.20,d=1.20±0.10 A=1.50,B=1.20,G=1.401411 (3528) a=0.80±0.30,b=2.80±0.20 c=3.50±0.20,d=2.20±0.10 A=1.50,B=2.20,G=1.702312 (6032) a=1.30±0.30,b=3.20±0.30 c=6.00±0.30,d=2.20±0.10 A=2.00,B=2.20,G=3.202917 (7243)a=1.30±0.30,b=4.30±0.30 c=7.20±0.30,d=2.40±0.10A=2.00,B=2.40,G=4.50铝质电解电容适用于铝质电解电容(Ø4×5.4)d=4.0±0.5h=5.4±0.3a=1.8±0.2,b=4.3±0.2c=4.3±0.2,e=0.5~0.8p=1.0A=2.40,B=1.00P=1.20,R=0.50(Ø5×5.4)d=5.0±0.5h=5.4±0.3a=2.2±0.2,b=5.3±0.2c=5.3±0.2,e=0.5~0.8p=1.3A=2.80,B=1.00P=1.50,R=0.50(Ø6.3×5.4)d=6.3±0.5h=5.4±0.3a=2.6±0.2,b=6.6±0.2c=6.6±0.2,e=0.5~0.8p=2.2A=3.20,B=1.00P=2.40,R=0.50(Ø6.3×7.7)d=6.3±0.5h=7.7±0.3a=2.6±0.2,b=6.6±0.2c=6.6±0.2,e=0.5~0.8p=2.2A=3.20,B=1.00P=2.40,R=0.50(Ø8.0×6.5)d=6.3±0.5h=7.7±0.3a=3.0±0.2,b=8.3±0.2c=8.3±0.2,e=0.5~0.8p=2.2A=3.20,B=1.00P=2.40,R=0.50(Ø8×10.5)d=8.0±0.5h=10.5±0.3a=3.0±0.2,b=8.3±0.2c=8.3±0.2,e=0.8~1.1p=3.1A=3.60,B=1.30P=3.30,R=0.65(Ø10×10.5)d=10.0±0.5h=10.5±0.3a=3.5±0.2,b=10.3±0.2c=10.3±0.2,e=0.8~1.1p=4.6A=4.20,B=1.30P=4.80,R=0.65二极管(SMA) 4500-234031-T0 4500-205100-T0a=1.20±0.30b=2.60±0.30,c=4.30±0.30d=1.45±0.20,e=5.2±0.30二极管(SOD-323)4500-141482-T0a=0.30±0.10b=1.30±0.10,c=1.70±0.10d=0.30±0.05,e=2.50±0.20二极管(3515)a=0.30b=1.50±0.1,c=3.50±0.20二极管(5025)a=0.55b=2.50±0.10, c=5.00±0.20 三极管(SOT-523)a=0.40±0.10,b=0.80±0.05c=1.60±0.10,d=0.25±0.05p=1.00三极管(SOT-23)a=0.55±0.15,b=1.30±0.10c=2.90±0.10,d=0.40±0.10p=1.90±0.10SOT-25a=0.60±0.20,b=2.90±0.20c=1.60±0.20,d=0.45±0.10p=1.90±0.10SOT-26a=0.60±0.20,b=2.90±0.20c=1.60±0.20,d=0.45±0.10p=0.95±0.05SOT-223a1=1.75±0.25,a2=1.5±0.25b=6.50±0.20,c=3.50±0.20d1=0.70±0.1,d2=3.00±0.1p=2.30±0.05SOT-89a1=1.0±0.20,a2=0.6±0.20b=2.50±0.20,c=4.50±0.20d1=0.4±0.10,d2=0.5±0.10d3=1.65±0.20,p=1.5±0.05TO-252a1=1.1±0.2,a2=0.9±0.1b=6.6±0.20,c=6.1±0.20d1=5.0±0.2,d2=Max1.0e=9.70±0.70,p=2.30±0.10TO-263-2a1=1.30±0.1,a2=2.55±0.25b=9.97±0.32,c=9.15±0.50d1=1.3±0.10,d2=0.75±0.24e=15.25±0.50,p=2.54±0.10TO-263-3a1=1.30±0.1,a2=2.55±0.25b=9.97±0.32,c=9.15±0.50d1=1.3±0.10,d2=0.75±0.24e=15.25±0.50,p=2.54±0.10 TO-263-5a1=1.66±0.1,a2=2.54±0.20b=10.03±0.15,c=8.40±0.20d=0.81±0.10,e=15.34±0.2p=1.70±0.10SOP(引脚(Pitch>0.65mm)A=a+1.0,B=d+0.1G=e-2*(0.4+a)P=pSOP(Pitch≦0.65mm)A=a+0.7,B=dG=e-2*(0.4+a)P=pSOJ(Pitch≧0.8mm)A=1.8mm,B=d2+0.10mmG=g-1.0mm,P=pQFP(Pitch≧0.65mm)A=a+1.0,B=d+0.05P=pG1=e1-2*(0.4+a)G2=e2-2*(0.4+a)QFP(Pitch=0.5mm)A=a+0.9,B=0.25mmP=pG1=e1-2*(0.4+a)G2=e2-2*(0.4+a)QFP(Pitch=0.4mm)A=a+0.8,B=0.19mmP=pG1=e1-2*(0.4+a)G2=e2-2*(0.4+a) 引脚长由原来的a+0.70mm更改为a+0.80mm,有利于修理和印刷拉尖的处理。
PCB贴片元件焊盘尺寸规范

在PCB 中画元器件封装时,经常遇到焊盘的大小尺寸不好把握的问题,因为我们查阅的资料给岀的是元 器件本身的大小,如引脚宽度,间距等,但是在 PCB 板上相应的焊盘大小应该比引脚的尺寸要稍大,否则 焊接的可靠性将不能保证。
下面将主要讲述焊盘尺寸的规范问题。
为了确保贴片元件(SMT )焊接质量,在设计SMT 印制板时,除印制板应留出 3mm-8mm 的工艺边外,应按有关规范设计好各种元器件的焊盘图形和尺寸,布排好元器件的位向和相邻元器件之间的间距等以外,我们认为还应特别注意以下几点 : (1) 印制板上,凡位于阻焊膜下面的导电图形(如互连线、接地线、互导孔盘等)和所需留用的铜箔之处,均应为裸铜箔。
即绝不允许涂镀熔点低于焊接温度的金属涂层,如锡铅合金等,以避免引发位于涂镀 层处的阻焊膜破裂或起皱,以保证 PCB 板的焊接以及外观质量。
(2) 查选或调用焊盘图形尺寸资料时,应与自己所选用的元器件的封装外形、焊端、引脚等与焊接有关 的尺寸相匹配。
必须克服不加分析或对照就随意抄用或调用所见到的资料 J 或软件库中焊盘图形尺寸的不 良习惯。
设计、查选或调用焊盘图形尺寸时,还应分清自己所选的元器件,其代码(如片状电阻、电容) 和与焊接有关的尺寸(如SOIC,QFP 等)。
(3) 表面贴装元器件的焊接可靠性,主要取决于焊盘的长度而不是宽度。
(a )如图1所示,焊盘的长度 B 等于焊端(或引脚)的长度 T ,加上焊端(或引脚)内侧(焊盘)的延伸 长度bl ,再加上焊端(或引脚)外侧(焊盘)的延伸长度 b2,即B=T+b1+b2。
其中bl 的长度(约 为0.05mm — 0.6mm ),不仅应有利于焊料熔融时能形成良好的弯月形轮廓的焊点,还得避免焊料产生 桥接现象及兼顾元器件的贴装偏差为宜;b2的长度(约为0.25mm — 1.5mm ),主要以保证能形成最 佳的弯月形轮廓的焊点为宜(对于 soic 、QFP 等器件还应兼顾其焊盘抗剥离的能力)Tp h 卜 + ・ fr :仙 .-i — *■ bi—S. -----卜 " _____图1理想的优质焊点形状及真焊轴(b )焊盘的宽度应等于或稍大(或稍小)于焊端(或引脚)的宽度常见贴装元器件焊盘设计图解,如图 2所示。
通孔插装元器件焊孔、焊盘设计工艺规范

深圳市核达中远通电源技术有限公司SHENZHEN HOLDLUCK-ZYT POWER SUPPLY TECHNOLOGY CO., LTD.通孔插装元器件焊孔、焊盘设计工艺规范WI-EN-***版本:A/0分发号:1.0目的:规范元器件焊孔、焊盘设计,满足可制造性要求。
2.0适用范围:通孔插装元器件的焊孔、焊盘设计。3.0内容3.1定义3.1.1引脚直径:若无特殊说明,指圆形引脚的直径,或者指方形(含扁形)引脚截面的对角线长度,用d表示,如图3.1.1(a)、图3.1.1(b)所示。
3.1.2方形(或扁形)引脚截面尺寸:用w表示引脚宽度,用t表示引脚厚度,如图3.1.1(b)所示。
当方形引脚的宽厚比w/t大于2时称为扁形引脚。
3.1.3焊孔直径:圆形焊孔直径,用d1表示,如图3.1.1(c)所示。
3.1.4焊盘直径:圆形焊盘直径,用D表示,如图3.1.1(c)所示。
3.1.5椭圆(或方形)焊盘长度:用L表示,如图3.1.1(d)所示。
3.1.6椭圆(或方形)焊盘宽度:用W表示,如图3.1.1(d)所示。
图3.1.1(b) 方形(或扁形)引脚元器件元件(c) 圆形焊孔及焊盘(d) 圆形焊孔及椭圆(或方形)焊盘3.2 焊孔3.2.1一般情况下,焊孔直径d1按表3.2.1选取: 表3.2.1面板取下限。
注2:在仅有有限的几个插装元件,多数元件为贴装元件的情况下,有可能使用到 通孔回流焊工艺,比如模块针脚的焊接。
3.2.2脚距精度较高,且定位要求也较高的元器件,如输入、输出插座等,焊孔直径等于引脚直径加上0.15~0.2mm 。
3.2.3 方形引脚焊孔:3.2.3.1 w >2.5mm 时,设计为方焊孔(圆角R 为0.3~0.35mm,防止圆角影响插装),方焊孔尺寸如图3.2.3.1所示。
3.2.3.2 w <2 mm 时,设计为圆孔,焊孔直径d1=d+0.15~0.25mm, d 为引脚截面对角线长。
焊盘的设计
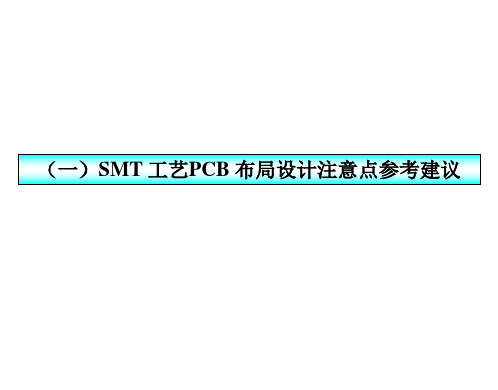
3mm以上
4.基板加工精度
・基板 MARK 基板原点 的加工精度:± 0.05m
Y1 Y2 5mm 5mm
原点 X2
X1
注意点—2:
焊盘的设计(特别针对SMT中红胶工艺)
SMD‐波峰工艺(参考)
针对QFP的设计: 45度+脱锡焊盘的设计
针对SOP的设计: 脱锡焊盘的设计
针对电阻电容电感二极管三极管的设计: 进板方向
将线路铜箔开放为裸铜 作为偷锡焊盘
为防止过波峰时焊锡从通孔上溢到上板,导致零件对地短 路或零件脚之间短路,设计多层板时要注意,金属外壳的 元件,插件时外壳与印制板接触的,顶层的焊盘不可开, 一定要用绿油或丝印油盖住(例如两脚的晶振、3只脚的 LED)
绿油覆盖
走线要求
板面布线应疏密得当,当疏密差别太大时应以网状铜箔填 充;
需波峰焊的贴片IC各脚焊盘之间要加阻焊漆,在最后一脚 要设计偷锡焊盘;
偷锡焊盘
未做特别要求时,元件孔形状、焊盘与元件脚形状必须匹 配,并保证焊盘相对于孔中心的对称性(方形元件脚配方 形元件孔、方形焊盘;圆形元件脚配圆形元件孔、圆形焊 盘),以保证焊点吃锡饱满;
需要过锡炉后才焊的元件,焊盘要开走锡位,方向与过锡方 向相反,宽度视孔的大小为0.5~1.0mm,以防止过波峰后 堵孔;
合理
不合理
PCB尺寸及外形要求
圆角:为方便单板加工,不拼板的单板板角应为R型倒角, 对于有工艺边和拼板的单板,工艺边应为R型倒角,一般 圆角直径为Φ5,小板可适当调整。有特殊要求按结构图 表示方法明确标出R大小,以便厂家加工; 工艺边:板边5mm范围内有较多元器件影响PCB加工时,可 以采用加辅助边(工艺边)的方法,工艺边一般加在长边; Mark点:基准点用于锡膏印刷和元件贴片时的光学定位。 根据基准点在PCB板上的用途,可以分为全局基准点、单 元板基准点、个别器件基准点。
pcb焊盘设计规范
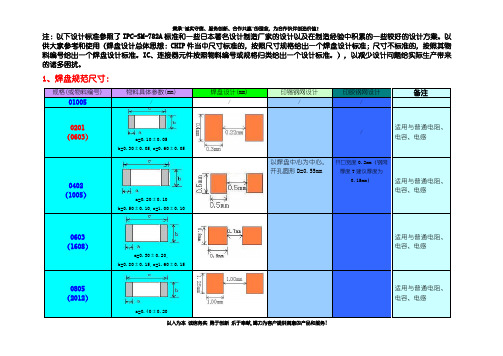
注:以下设计标准参照了IPC-SM-782A标准和一些日本著名设计制造厂家的设计以及在制造经验中积累的一些较好的设计方案。
以供大家参考和使用(焊盘设计总体思想:CHIP件当中尺寸标准的,按照尺寸规格给出一个焊盘设计标准;尺寸不标准的,按照其物料编号给出一个焊盘设计标准。
IC、连接器元件按照物料编号或规格归类给出一个设计标准。
),以减少设计问题给实际生产带来的诸多困扰。
1、焊盘规范尺寸:规格(或物料编号) 物料具体参数(mm) 焊盘设计(mm) 印锡钢网设计印胶钢网设计备注01005 / / / /0201(0603)a=0.10±0.05b=0.30±0.05,c=0.60±0.05 /适用与普通电阻、电容、电感0402(1005)a=0.20±0.10b=0.50±0.10,c=1.00±0.10 以焊盘中心为中心,开孔圆形D=0.55mm开口宽度0.2mm(钢网厚度T建议厚度为0.15mm)适用与普通电阻、电容、电感0603(1608)a=0.30±0.20,b=0.80±0.15,c=1.60±0.15 适用与普通电阻、电容、电感0805(2012)a=0.40±0.20 适用与普通电阻、电容、电感b=1.25±0.15,c=2.00±0.201206(3216)a=0.50±0.20b=1.60±0.15,c=3.20±0.20 适用与普通电阻、电容、电感1210(3225)a=0.50±0.20b=2.50±0.20,c=3.20±0.20 适用与普通电阻、电容、电感1812(4532)a=0.50±0.20b=3.20±0.20,c=4.50±0.20 适用与普通电阻、电容、电感2010(5025)a=0.60±0.20b=2.50±0.20,c=5.00±0.20 适用与普通电阻、电容、电感2512 (6432)适用与普通电阻、电容、电感a=0.60±0.20b=3.20±0.20,c=6.40±0.201:1开口,不避锡珠5700-250AA2-0300排阻0404(1010)a=0.25±0.10,b=1.00±0.10c=1.00±0.10,d=0.35±0.10p=0.65±0.05排阻0804(2010)a=0.25±0.10,b=2.00±0.10c=1.00±0.10,d=0.30±0.15p=0.50±0.05排阻1206(3216)a=0.30±0.15,b=3.2±0.15c=1.60±0.15,d=0.50±0.15p=0.80±0.10排阻1606(4016)a=0.25±0.10,b=4.00±0.20c=1.60±0.15,d=0.30±0.10p=0.50±0.05472X-R05240-10a=0.38±0.05,b=2.50±0.10c=1.00±0.10,d=0.20±0.05d1=0.40±0.05,p=0.50钽质电容适用于钽质电容1206 (3216) a=0.80±0.30,b=1.60±0.20 c=3.20±0.20,d=1.20±0.10 A=1.50,B=1.20,G=1.401411 (3528) a=0.80±0.30,b=2.80±0.20 c=3.50±0.20,d=2.20±0.10 A=1.50,B=2.20,G=1.702312 (6032) a=1.30±0.30,b=3.20±0.30 c=6.00±0.30,d=2.20±0.10 A=2.00,B=2.20,G=3.202917 (7243)a=1.30±0.30,b=4.30±0.30 c=7.20±0.30,d=2.40±0.10A=2.00,B=2.40,G=4.50铝质 电解 电容适用于铝质电解电容(Ø4×5.4)d=4.0±0.5 h=5.4±0.3a=1.8±0.2,b=4.3±0.2 c=4.3±0.2,e=0.5~0.8 p=1.0A=2.40,B=1.00 P=1.20,R=0.50(Ø5×5.4)d=5.0±0.5 h=5.4±0.3a=2.2±0.2,b=5.3±0.2 c=5.3±0.2,e=0.5~0.8 p=1.3A=2.80,B=1.00 P=1.50,R=0.50(Ø6.3×5.4) d=6.3±0.5 h=5.4±0.3a=2.6±0.2,b=6.6±0.2c=6.6±0.2,e=0.5~0.8 p=2.2A=3.20,B=1.00 P=2.40,R=0.50(Ø6.3×7.7) d=6.3±0.5 h=7.7±0.3a=2.6±0.2,b=6.6±0.2c=6.6±0.2,e=0.5~0.8p=2.2A=3.20,B=1.00P=2.40,R=0.50(Ø8.0×6.5) d=6.3±0.5 h=7.7±0.3a=3.0±0.2,b=8.3±0.2c=8.3±0.2,e=0.5~0.8p=2.2A=3.20,B=1.00P=2.40,R=0.50(Ø8×10.5) d=8.0±0.5 h=10.5±0.3a=3.0±0.2,b=8.3±0.2c=8.3±0.2,e=0.8~1.1p=3.1A=3.60,B=1.30P=3.30,R=0.65(Ø10×10.5) d=10.0±0.5 h=10.5±0.3a=3.5±0.2,b=10.3±0.2c=10.3±0.2,e=0.8~1.1p=4.6A=4.20,B=1.30P=4.80,R=0.65二极管(SMA)4500-234031-T04500-205100-T0a=1.20±0.30b=2.60±0.30,c=4.30±0.30d=1.45±0.20,e=5.2±0.30二极管(SOD-323)4500-141482-T0a=0.30±0.10b=1.30±0.10,c=1.70±0.10d=0.30±0.05,e=2.50±0.20二极管(3515)a=0.30b=1.50±0.1,c=3.50±0.20二极管(5025)a=0.55b=2.50±0.10, c=5.00±0.20三极管(SOT-523)a=0.40±0.10,b=0.80±0.05c=1.60±0.10,d=0.25±0.05p=1.00三极管(SOT-23)a=0.55±0.15,b=1.30±0.10c=2.90±0.10,d=0.40±0.10p=1.90±0.10SOT-25a=0.60±0.20,b=2.90±0.20c=1.60±0.20,d=0.45±0.10p=1.90±0.10SOT-26a=0.60±0.20,b=2.90±0.20c=1.60±0.20,d=0.45±0.10p=0.95±0.05SOT-223a1=1.75±0.25,a2=1.5±0.25b=6.50±0.20,c=3.50±0.20d1=0.70±0.1,d2=3.00±0.1p=2.30±0.05SOT-89a1=1.0±0.20,a2=0.6±0.20b=2.50±0.20,c=4.50±0.20d1=0.4±0.10,d2=0.5±0.10d3=1.65±0.20,p=1.5±0.05TO-252a1=1.1±0.2,a2=0.9±0.1b=6.6±0.20,c=6.1±0.20d1=5.0±0.2,d2=Max1.0e=9.70±0.70,p=2.30±0.10TO-263-2a1=1.30±0.1,a2=2.55±0.25b=9.97±0.32,c=9.15±0.50d1=1.3±0.10,d2=0.75±0.24e=15.25±0.50,p=2.54±0.10TO-263-3a1=1.30±0.1,a2=2.55±0.25b=9.97±0.32,c=9.15±0.50d1=1.3±0.10,d2=0.75±0.24e=15.25±0.50,p=2.54±0.10TO-263-5a1=1.66±0.1,a2=2.54±0.20b=10.03±0.15,c=8.40±0.20d=0.81±0.10,e=15.34±0.2p=1.70±0.10SOP(引脚(Pitch>0.65mm)A=a+1.0,B=d+0.1G=e-2*(0.4+a)P=pSOP(Pitch≦0.65mm)A=a+0.7,B=dG=e-2*(0.4+a)P=pSOJ(Pitch≧0.8mm)A=1.8mm,B=d2+0.10mmG=g-1.0mm,P=pQFP(Pitch≧0.65mm)A=a+1.0,B=d+0.05P=pG1=e1-2*(0.4+a)G2=e2-2*(0.4+a)QFP(Pitch=0.5mm)A=a+0.9,B=0.25mmP=pG1=e1-2*(0.4+a)G2=e2-2*(0.4+a)QFP(Pitch=0.4mm)A=a+0.8,B=0.19mmP=pG1=e1-2*(0.4+a)G2=e2-2*(0.4+a) 引脚长由原来的a+0.70mm更改为a+0.80mm,有利于修理和印刷拉尖的处理。
(完整版)PCB焊盘与孔径设计一般规范(仅参考)

PCB 焊盘与孔设计工艺规范1. 目的规范产品的PCB焊盘设计工艺,规定PCB焊盘设计工艺的相关参数,使得PCB 的设计满足可生产性、可测试性、安规、EMC 、EMI 等的技术规范要求,在产品设计过程中构建产品的工艺、技术、质量、成本优势。
2. 适用范围本规范适用于空调类电子产品的PCB 工艺设计,运用于但不限于PCB 的设计、PCB 批产工艺审查、单板工艺审查等活动。
本规范之前的相关标准、规范的内容如与本规范的规定相抵触的,以本规范为准3. 引用/参考标准或资料TS—S0902010001 << 信息技术设备PCB 安规设计规范>>TS—SOE0199001 << 电子设备的强迫风冷热设计规范>>TS—SOE0199002 << 电子设备的自然冷却热设计规范>>IEC60194 << 印制板设计、制造与组装术语与定义>> ( Printed Circuit Board design manufacture and assembly-terms and definitions )IPC—A—600F << 印制板的验收条件>> ( Acceptably of printed board ) IEC609504. 规范内容4.1 焊盘的定义通孔焊盘的外层形状通常为圆形、方形或椭圆形。
具体尺寸定义详述如下,名词定义如图所示。
1) 孔径尺寸:若实物管脚为圆形:孔径尺寸(直径) =实际管脚直径+0.20 ∽0.30mm(8.0∽12.0MIL )左右;若实物管脚为方形或矩形: 孔径尺寸(直径) =实际管脚对角线的尺寸+0.10 ∽0.20mm( 4.0 ∽8.0MIL )左右。
2) 焊盘尺寸:常规焊盘尺寸=孔径尺寸(直径) +0.50mm(20.0 MIL) 左右。
4.2 焊盘相关规范4.2.1 所有焊盘单边最小不小于0.25mm,整个焊盘直径最大不大于元件孔径的 3 倍。
PCB焊盘设计工艺要求
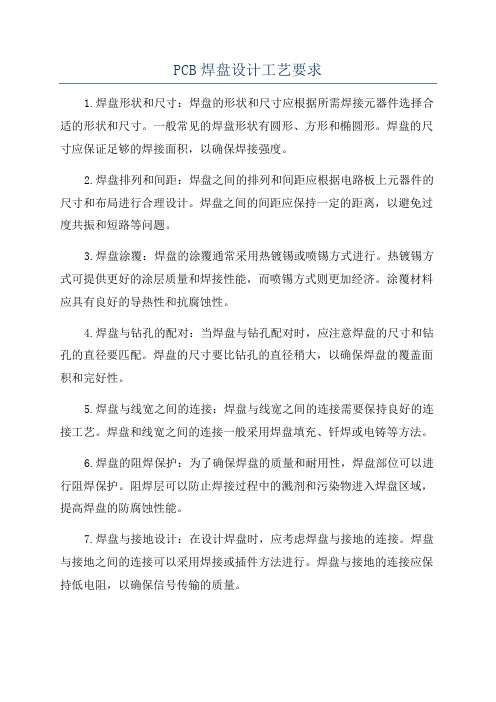
PCB焊盘设计工艺要求1.焊盘形状和尺寸:焊盘的形状和尺寸应根据所需焊接元器件选择合适的形状和尺寸。
一般常见的焊盘形状有圆形、方形和椭圆形。
焊盘的尺寸应保证足够的焊接面积,以确保焊接强度。
2.焊盘排列和间距:焊盘之间的排列和间距应根据电路板上元器件的尺寸和布局进行合理设计。
焊盘之间的间距应保持一定的距离,以避免过度共振和短路等问题。
3.焊盘涂覆:焊盘的涂覆通常采用热镀锡或喷锡方式进行。
热镀锡方式可提供更好的涂层质量和焊接性能,而喷锡方式则更加经济。
涂覆材料应具有良好的导热性和抗腐蚀性。
4.焊盘与钻孔的配对:当焊盘与钻孔配对时,应注意焊盘的尺寸和钻孔的直径要匹配。
焊盘的尺寸要比钻孔的直径稍大,以确保焊盘的覆盖面积和完好性。
5.焊盘与线宽之间的连接:焊盘与线宽之间的连接需要保持良好的连接工艺。
焊盘和线宽之间的连接一般采用焊盘填充、钎焊或电铸等方法。
6.焊盘的阻焊保护:为了确保焊盘的质量和耐用性,焊盘部位可以进行阻焊保护。
阻焊层可以防止焊接过程中的溅剂和污染物进入焊盘区域,提高焊盘的防腐蚀性能。
7.焊盘与接地设计:在设计焊盘时,应考虑焊盘与接地的连接。
焊盘与接地之间的连接可以采用焊接或插件方法进行。
焊盘与接地的连接应保持低电阻,以确保信号传输的质量。
8.焊盘的兼容性设计:在设计焊盘时,应考虑焊盘与其他元器件的兼容性。
特别是焊盘与插件的兼容性,以确保焊接过程中的稳定性和可靠性。
在进行PCB焊盘设计工艺时,还需要遵循以下注意事项:1.根据元器件的类型和尺寸合理选择焊盘形状和尺寸。
2.确保焊盘之间的排列和间距合适,避免导致电路板布线困难。
3.注意焊盘与钻孔的配对,确保焊盘的尺寸与钻孔直径匹配。
4.根据焊盘的连接方式选择合适的连接技术和工艺。
5.为了提高焊盘的耐用性和防腐蚀性,可以采取焊盘阻焊保护措施。
总之,PCB焊盘设计工艺要求是保证PCB焊盘质量和稳定性的重要步骤。
通过合理选择焊盘形状和尺寸,合适的排列和间距,以及采用适当的连接工艺和防护措施,可以提高焊盘的品质和可靠性,确保PCB的正常工作和使用寿命。
sop焊盘设计标准

sop焊盘设计标准
SOP焊盘设计的标准如下:
1.焊盘中心距等于引脚中心距。
2.单个引脚焊盘设计的一般原则是:Y=T+b1+b2=1.5~2mm
(b1=0.3~1.0mm,b2=0.3~0.7mm),X=1~1.2W。
3.相对两排焊盘内侧距离按下式计算(单位:mm):G=F-K,其中G
为两排焊盘之间距离,F为元器件壳体封装尺寸,K为系数,一般取
0.25mm。
4.良好的焊点应该包含前端的“脚趾”和后端的“脚跟”,而且焊点的强度
主要由这两个部分保证。
5.焊盘的长度比焊盘宽度更为重要,焊盘的可靠性主要取决于焊盘的长
度。
在焊盘长度的选择中,需要考虑引脚的长度以及引脚内侧和外侧的延伸长度。
6.对于0805以上的电阻、电容元件,或引脚间距在1.27mm以上的SO、
SOJ封装的IC芯片,宽度一般在元件实际引脚的基础上再加一个数量值,这个数据范围为0.1~0.25mm;而对于0.64(包括0.64mm)引脚间距以下的芯片,焊盘宽度等于引脚宽度。
7.对于细间距的QFP封装的器件,有时焊盘的宽度相对引脚来说还要
适当减小(如果两引脚间需要有引线出来的话)。
以上标准仅供参考,实际应用中可能还需要根据具体的产品和工艺进行调整。
PCB_焊盘工艺设计规范分解
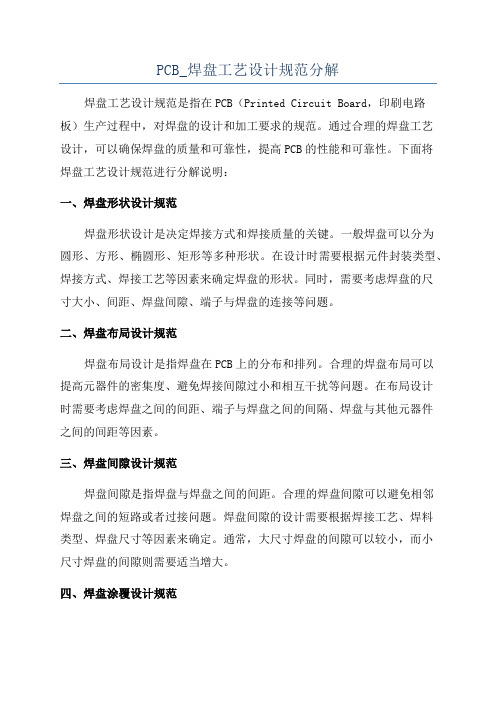
PCB_焊盘工艺设计规范分解焊盘工艺设计规范是指在PCB(Printed Circuit Board,印刷电路板)生产过程中,对焊盘的设计和加工要求的规范。
通过合理的焊盘工艺设计,可以确保焊盘的质量和可靠性,提高PCB的性能和可靠性。
下面将焊盘工艺设计规范进行分解说明:一、焊盘形状设计规范焊盘形状设计是决定焊接方式和焊接质量的关键。
一般焊盘可以分为圆形、方形、椭圆形、矩形等多种形状。
在设计时需要根据元件封装类型、焊接方式、焊接工艺等因素来确定焊盘的形状。
同时,需要考虑焊盘的尺寸大小、间距、焊盘间隙、端子与焊盘的连接等问题。
二、焊盘布局设计规范焊盘布局设计是指焊盘在PCB上的分布和排列。
合理的焊盘布局可以提高元器件的密集度、避免焊接间隙过小和相互干扰等问题。
在布局设计时需要考虑焊盘之间的间距、端子与焊盘之间的间隔、焊盘与其他元器件之间的间距等因素。
三、焊盘间隙设计规范焊盘间隙是指焊盘与焊盘之间的间距。
合理的焊盘间隙可以避免相邻焊盘之间的短路或者过接问题。
焊盘间隙的设计需要根据焊接工艺、焊料类型、焊盘尺寸等因素来确定。
通常,大尺寸焊盘的间隙可以较小,而小尺寸焊盘的间隙则需要适当增大。
四、焊盘涂覆设计规范焊盘涂覆是指在焊盘上涂覆一层焊接助剂,用于提高焊接的质量和可靠性。
合理的焊盘涂覆设计可以提高焊盘的润湿性和耐腐蚀性,同时也能够减少焊接过程中的气泡和其他缺陷。
在涂覆设计时需要考虑涂覆层的厚度、均匀性、涂覆方式等因素。
五、焊盘刚化设计规范焊盘刚化是指通过改变焊盘的材料或者结构来提高焊盘的刚度和稳定性。
焊盘刚化设计需要考虑焊盘的材料选择、厚度、形状等因素。
一般情况下,大功率焊盘需要更高的刚度和稳定性。
六、焊盘检测规范焊盘检测是指对焊盘进行质量检测和可靠性验证。
焊盘检测需要使用相关的测试设备和工具,对焊盘的焊接质量、焊盘与元器件的连接可靠性、焊盘与PCB的连接质量等进行检测。
同时还需要制定相应的测试标准和流程,确保焊盘的质量符合要求。
pcb插件孔焊盘设计标准

pcb插件孔焊盘设计标准
在PCB设计中设计PCB焊盘时,需要严格按照相关要求和标准进行设计。
因为在SMT贴片加工中,PCB焊盘的设计非常重要。
焊盘设计会直接影响元件的可焊性、稳定性和热传递,这关系到贴片加工的质量。
1、调用PCB标准封装库。
2、焊盘最小单边不小于0.25mm,整个焊盘最大直径不大于元件直径的3倍。
3、尽量保证两个焊盘边缘的距离大于0.4mm。
4.孔径超过1.2mm或焊盘直径超过3.0mm的焊盘应设计为菱形或梅花形焊盘
5.在布线密集的情况下,建议使用椭圆形和椭圆形连接焊盘。
单面焊盘的直径或最小宽度为1.6mm;双面弱电电路焊盘只需在孔径上增加0.5mm,焊盘太大造成不必要的连续焊接。
直插元器件焊盘设计的一些基本要求

直插元器件焊盘设计的一些基本要求When designing printed circuit boards (PCBs) with through-hole components, it is essential to ensure that the pad sizes for the components' leads are appropriate to allow for efficient soldering.在设计具有直插元器件的印刷电路板(PCB)时,必须确保元器件引脚的焊盘尺寸合适,以实现有效的焊接。
The size and shape of the pad must match the lead of the component to provide enough surface area for the solder to bond properly. It is important to consider the thermal conductivity of the pad material to ensure that heat is properly distributed during soldering.焊盘的大小和形状必须与元件的引脚相匹配,以提供足够的表面积,使焊料能够正确粘结。
必须考虑焊盘材料的热导率,以确保焊接过程中热量被正确传导。
Additionally, the pad layout should take into account the spacing between pads to prevent solder bridging, which can cause shortcircuits and potentially damage the components. Proper spacing and alignment of the pads can also facilitate the soldering process and improve the overall reliability of the PCB.此外,焊盘布局应考虑焊盘之间的间距,以防止焊料桥接,这可能会导致短路并潜在地损坏元件。
SMT工艺要求-PCB元器件焊盘设计
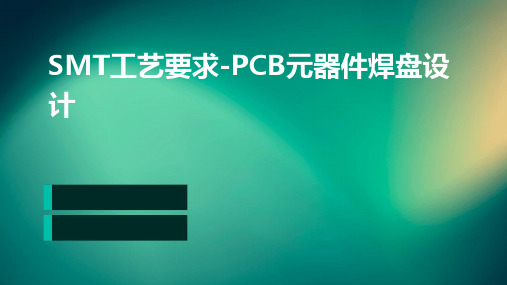
填埋等,以降低其对环境的影响。
06 PCB元器件焊盘设计案例 分析
案例一:多层板焊盘设计
总结词
多层板焊盘设计需考虑各层之间的连接和导通性,确保焊盘与元件引脚之间的可靠连接。
详细描述
在多层板焊盘设计中,需要考虑各层之间的连接方式和导通性,以确保焊盘与元件引脚之间的可靠连接。设计时 需充分考虑多层板的叠层结构,合理规划焊盘的尺寸、位置和导通孔的位置、数量和尺寸,以满足焊接工艺的要 求。
兼容性考虑
无铅焊盘设计应考虑与现 有设备和工艺的兼容性, 以确保生产过程的顺利进 行。
可靠性测试
无铅焊盘应经过严格的可 靠性测试,以确保其性能 和稳定性。
有害物质限制使用
限制使有害物质
在PCB元器件焊盘设计中,应尽 量避免使用对人体和环境有害的
物质,如铅、汞等。
替代方案
对于必须使用的有害物质,应积极 寻找替代方案,以减少对环境的负 面影响。
焊盘间距设计
焊盘间距应满足工艺要求,以保证焊接过程中不会发生桥接现象。
考虑到焊接过程中可能出现的热膨胀和收缩,焊盘间距应适当留有余量,以避免 焊接后出现断路或短路问题。
03 PCB元器件焊盘的可靠性 设计
焊点的可靠性
焊点的可靠性是确保PCB元器件稳定工作的关键 因素。
焊点的可靠性要求焊盘具有足够的机械强度和耐 热性,以承受焊接过程中的热应力和机械应力。
自动化程度高
SMT工艺采用自动化设备 进行元器件贴装和焊接, 提高了生产效率和产品质 量。
SMT工艺流程
印刷
贴装
将焊膏或胶粘剂印刷到 PCB上,形成焊膏图案。
将元器件贴装到PCB的 焊膏图案上。
焊接
通过加热或固化过程, 使焊膏熔化或胶粘剂固 化,将元器件与PCB连
PCB设计中焊盘的种类及设计标准

PCB设计中焊盘的种类及设计标准在PCB设计中,焊盘是一个非常重要的概念,PCB工程师对它一定不陌生。
不过,虽然熟悉,很多工程师对焊盘的知识却是一知半解。
今天来了解下焊盘的种类,以及在PCB设计中焊盘的设计标准。
焊盘,表面贴装装配的基本构成单元,用来构成电路板的焊盘图案(land pattern),即各种为特殊元件类型设计的焊盘组合。
焊盘用于电气连接、器件固定或两者兼备的部分导电图形。
PCB焊盘的种类一、常见焊盘1、方形焊盘印制板上元器件大而少、且印制导线简单时多采用。
在手工自制PCB时,采用这种焊盘易于实现。
2、圆形焊盘广泛用于元件规则排列的单、双面印制板中。
若板的密度允许,焊盘可大些,焊接时不至于脱落。
3、岛形焊盘焊盘与焊盘间的连线合为一体。
常用于立式不规则排列安装中。
4、多边形焊盘用于区别外径接近而孔径不同的焊盘,便于加工和装配。
5、椭圆形焊盘这种焊盘有足够的面积增强抗剥能力,常用于双列直插式器件。
6、开口形焊盘为了保证在波峰焊后,使手工补焊的焊盘孔不被焊锡封死时常用。
二、特殊焊盘1、梅花焊盘梅花焊盘通常用在大的过孔接地的位置,这样设计有以下几点原因:1)固定孔需要金属化和GND相连,如果该固定孔是全金属化的,在回流焊的时候容易将该孔堵住。
2)采用内部的金属螺孔可能由于安装或多次拆装等原因,造成该接地处于不良的状态。
而采用梅花孔焊盘,不管应力如何变化,均能保证良好的接地。
2、十字花焊盘十字花焊盘又称热焊盘、热风焊盘等。
其作用是减少焊盘在焊接中向外散热,以防止因过度散热而导致的虚焊或PCB起皮。
1)当你的焊盘是地线时候。
十字花可以减少连接地线面积,减慢散热速度,方便焊接。
2)当你的PCB是需要机器贴片,并且是回流焊机,十字花焊盘可以防止PCB起皮(因为需要更多热量来融化锡膏)。
3、泪滴焊盘当焊盘连接的走线较细时常采用,以防焊盘起皮、走线与焊盘断开。
这种焊盘常用在高频电路中。
PCB设计中焊盘的设计标准一、PCB焊盘的形状和尺寸设计标准1、所有焊盘单边最小不小于0.25mm,整个焊盘直径最大不大于元件孔径的3倍。
SMT工艺中常见元器件的焊盘与钢网开孔可制造性设计

正面焊端焊点上锡最小高度:
最小焊点高度(F)为焊锡厚度(G) 加可焊端高度(H)的25%或 0.5mm,其中较小者。(决定因素钢 网厚度,元件焊端尺寸,焊盘大小)
正面焊端焊点上锡高度:
最大焊点高度为焊锡厚度加元件 可焊端高度。(决定因素钢网厚 度,元件焊端尺寸,焊盘大小
正面焊端最大高度:
最大高度可以超出焊盘或爬升 至可焊端顶部,但不可接触元 件体。(此类现象多发生在 0201,0402类元件上)
SMT工艺中常见元器件的焊盘与钢网开孔可制造性设计 工艺中常见元器件的焊盘与钢网开孔可制造性设计
珠海伟创力 尹纪兵 SMT 工艺中的可制造性设计(DFM)越来越受到 工艺中的可制造性设计( )越来越受到OEM,ODM及EMS厂 , 及 厂 商的关注。一个被优化的可制造性设计能使产品更好的制造出来,减少制造难度系数, 商的关注。一个被优化的可制造性设计能使产品更好的制造出来,减少制造难度系数, 避免了被返修的可能。不仅能更快更好的交货,更能在某种程度上节约成本, 避免了被返修的可能。不仅能更快更好的交货,更能在某种程度上节约成本, 创造利润。本文将以IPC标准为基础,结合实际生产中的要求对 标准为基础, 创造利润。本文将以 标准为基础 结合实际生产中的要求对PCB 焊盘及钢 网的设计进行阐述。 网的设计进行阐述。 SMT工艺中关键的一点是焊接,可以这样说,SMT就是如何将元件放到预 工艺中关键的一点是焊接, 工艺中关键的一点是焊接 可以这样说, 就是如何将元件放到预 定位置,通过焊接达到一定的电气性能的过程。 定位置,通过焊接达到一定的电气性能的过程。 如何根据元件尺寸与特性设计出合理的焊盘, 如何根据元件尺寸与特性设计出合理的焊盘,如何根据元件与焊盘及焊点要求设计出 钢网,并且设计出来的焊盘与钢网是可制造性,这将是一个工艺工程师面临的问题。 钢网,并且设计出来的焊盘与钢网是可制造性,这将是一个工艺工程师面临的问题。 本文将从如上几方面进行论述。 本文将从如上几方面进行论述。
元器件焊盘设计
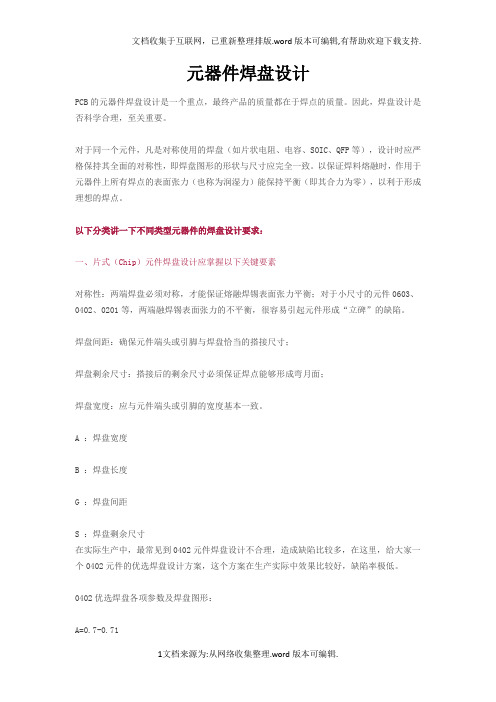
元器件焊盘设计PCB的元器件焊盘设计是一个重点,最终产品的质量都在于焊点的质量。
因此,焊盘设计是否科学合理,至关重要。
对于同一个元件,凡是对称使用的焊盘(如片状电阻、电容、SOIC、QFP等),设计时应严格保持其全面的对称性,即焊盘图形的形状与尺寸应完全一致。
以保证焊料熔融时,作用于元器件上所有焊点的表面张力(也称为润湿力)能保持平衡(即其合力为零),以利于形成理想的焊点。
以下分类讲一下不同类型元器件的焊盘设计要求:一、片式(Chip)元件焊盘设计应掌握以下关键要素对称性:两端焊盘必须对称,才能保证熔融焊锡表面张力平衡;对于小尺寸的元件0603、0402、0201等,两端融焊锡表面张力的不平衡,很容易引起元件形成“立碑”的缺陷。
焊盘间距:确保元件端头或引脚与焊盘恰当的搭接尺寸;焊盘剩余尺寸:搭接后的剩余尺寸必须保证焊点能够形成弯月面;焊盘宽度:应与元件端头或引脚的宽度基本一致。
A :焊盘宽度B :焊盘长度G :焊盘间距S :焊盘剩余尺寸在实际生产中,最常见到0402元件焊盘设计不合理,造成缺陷比较多,在这里,给大家一个0402元件的优选焊盘设计方案,这个方案在生产实际中效果比较好,缺陷率极低。
0402优选焊盘各项参数及焊盘图形:A=0.7-0.71B=0.38G=0.52S=0.14焊盘的两端可以设计成半园形,焊接后的焊点比较饱满。
二、SOP及QFP设计原则:1、焊盘中心距等于引脚中心距;2、单个引脚焊盘设计的一般原则Y=T+b1+b2=1.5~2mm (b1=0.3~1.0mm b2=0.3~0.7mm)X=1~1.2W3、相对两排焊盘内侧距离按下式计算(单位mm)G=F-K式中:G—两排焊盘之间距离,F—元器件壳体封装尺寸,K—系数,一般取0.25mm,SOP 包括QFP的焊盘设计中,需要注意的就是上面第2条中的b1和b2两个参数。
良好的焊点可以看下面的图,在这个图里,前面称为的焊点的脚趾,后面称为焊点的脚跟,一个合格的焊点,必须包含这两部分,缺一不可,而且焊点的强度也是靠这两个部位来保证的,尤其是脚跟部位。
PCB板焊盘及通孔的设计规范
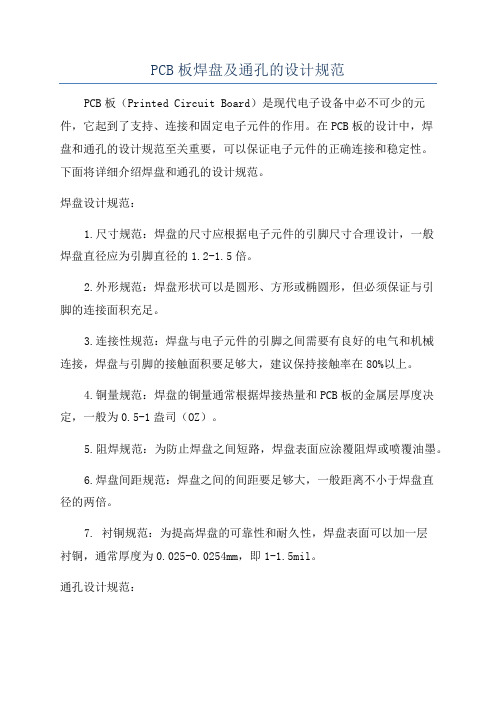
PCB板焊盘及通孔的设计规范PCB板(Printed Circuit Board)是现代电子设备中必不可少的元件,它起到了支持、连接和固定电子元件的作用。
在PCB板的设计中,焊盘和通孔的设计规范至关重要,可以保证电子元件的正确连接和稳定性。
下面将详细介绍焊盘和通孔的设计规范。
焊盘设计规范:1.尺寸规范:焊盘的尺寸应根据电子元件的引脚尺寸合理设计,一般焊盘直径应为引脚直径的1.2-1.5倍。
2.外形规范:焊盘形状可以是圆形、方形或椭圆形,但必须保证与引脚的连接面积充足。
3.连接性规范:焊盘与电子元件的引脚之间需要有良好的电气和机械连接,焊盘与引脚的接触面积要足够大,建议保持接触率在80%以上。
4.铜量规范:焊盘的铜量通常根据焊接热量和PCB板的金属层厚度决定,一般为0.5-1盎司(OZ)。
5.阻焊规范:为防止焊盘之间短路,焊盘表面应涂覆阻焊或喷覆油墨。
6.焊盘间距规范:焊盘之间的间距要足够大,一般距离不小于焊盘直径的两倍。
7. 衬铜规范:为提高焊盘的可靠性和耐久性,焊盘表面可以加一层衬铜,通常厚度为0.025-0.0254mm,即1-1.5mil。
通孔设计规范:1.尺寸规范:通孔的内径和外径应根据焊接或安装元件时所需的引脚尺寸合理设计,一般通孔的外径为引脚直径的1.2-1.5倍。
2. 垂直度规范:通孔的垂直度对焊接和组装的质量有很大影响,通孔的垂直度误差应控制在0.05mm以内。
3.阻焊规范:为避免通孔与焊盘短路,通孔的内壁和外壁应涂覆阻焊或喷覆油墨。
4.理顺规范:通孔所连接的多层板之间的走线布局应合理,通孔的位置要避免与其他元器件、走线或焊盘过近。
5.通孔填充规范:在一些特殊的情况下,可以使用孔内填充物(如尼龙套管等)来增加通孔的可靠性和机械强度,但填充物的选择和使用应满足特定的设计要求。
总结:焊盘和通孔是PCB板设计中非常重要的组成部分,它们的设计规范直接影响到电子元件的连接可靠性和整个电路板的稳定性。
电路板焊盘设计工艺

电路板焊盘设计工艺
一、焊盘设计
焊盘是电路板设计中重要的组成部分,其设计合理与否直接影响到电路板的性能和生产成本。
1.1确定焊盘尺寸
焊盘尺寸的大小应根据元器件的引脚间距和引脚数量来确定。
一般来说,焊盘的直径应略大于元器件的引脚直径,以方便焊接。
1.2选择焊盘类型
焊盘类型包括圆形、方形、椭圆形等。
选择焊盘类型应根据电路板的设计要求和实际需要来确定。
1.3设定焊盘边缘
焊盘边缘应与电路板边缘保持一定距离,以确保电路板的加工精度和可靠性。
一般来说,焊盘边缘应比电路板边缘小1-2mm。
二、电路板布局
电路板布局是电路板设计的核心环节,其合理与否直接影响到电路板的性能和生产成本。
2.1确定元器件位置
元器件的排列位置应符合电路设计的要求,同时应考虑方便生产、维修和调试等因素。
2.2优化电路板布局
在确定元器件位置的基础上,应对电路板进行优化设计,使电路板的布线更加合理、美观。
2.3检查布线可行性
在布局完成后,应对电路板进行布线可行性检查,以确保布线不会对其他部分产生干扰或影响。
三、元器件封装选择
元器件封装是电路板设计中重要的组成部分,其选择合理与否直接影响到电路板的性能和生产成本。
3.1选择合适的封装形式
应根据元器件的类型和引脚间距等因素来选择合适的封装形式。
3.2确定封装参数
封装参数包括引脚间距、引脚数量、封装高度等。
这些参数应根据元器件的技术手册来确定。
- 1、下载文档前请自行甄别文档内容的完整性,平台不提供额外的编辑、内容补充、找答案等附加服务。
- 2、"仅部分预览"的文档,不可在线预览部分如存在完整性等问题,可反馈申请退款(可完整预览的文档不适用该条件!)。
- 3、如文档侵犯您的权益,请联系客服反馈,我们会尽快为您处理(人工客服工作时间:9:00-18:30)。
元器件焊盘设计
PCB的元器件焊盘设计是一个重点,最终产品的质量都在于焊点的质量。
因此,焊盘设计是否科学合理,至关重要。
对于同一个元件,凡是对称使用的焊盘(如片状电阻、电容、SOIC、QFP等),设计时应严格保持其全面的对称性,即焊盘图形的形状与尺寸应完全一致。
以保证焊料熔融时,作用于元器件上所有焊点的表面张力(也称为润湿力)能保持平衡(即其合力为零),以利于形成理想的焊点。
以下分类讲一下不同类型元器件的焊盘设计要求:
一、片式(Chip)元件焊盘设计应掌握以下关键要素
对称性:两端焊盘必须对称,才能保证熔融焊锡表面张力平衡;对于小尺寸的元件0603、0402、0201等,两端融焊锡表面张力的不平衡,很容易引起元件形成“立碑”的缺陷。
焊盘间距:确保元件端头或引脚与焊盘恰当的搭接尺寸;
焊盘剩余尺寸:搭接后的剩余尺寸必须保证焊点能够形成弯月面;
焊盘宽度:应与元件端头或引脚的宽度基本一致。
A :焊盘宽度
B :焊盘长度
G :焊盘间距
S :焊盘剩余尺寸
在实际生产中,最常见到0402元件焊盘设计不合理,造成缺陷比较多,在这里,给大家一个0402元件的优选焊盘设计方案,这个方案在生产实际中效果比较好,缺陷率极低。
0402优选焊盘各项参数及焊盘图形:
A=0.7-0.71
B=0.38
G=0.52
S=0.14
焊盘的两端可以设计成半园形,焊接后的焊点比较饱满。
二、SOP及QFP设计原则:
1、焊盘中心距等于引脚中心距;
2、单个引脚焊盘设计的一般原则
Y=T+b1+b2=1.5~2mm (b1=0.3~1.0mm b2=0.3~0.7mm)
X=1~1.2W
3、相对两排焊盘内侧距离按下式计算(单位mm)
G=F-K
式中:G—两排焊盘之间距离,
F—元器件壳体封装尺寸,
K—系数,一般取0.25mm,
SOP 包括QFP的焊盘设计中,需要注意的就是上面第2条中的b1和b2两个参数。
良好的焊点可以看下面的图,在这个图里,前面称为的焊点的脚趾,后面称为焊点的脚跟,一个合格的焊点,必须包含这两部分,缺一不可,而且焊点的强度也是靠这两个部位来保证的,尤其是脚跟部位。
在一些设计不良的案例中,或者是b2太短,或者b1太短,导致的结果就是无法形成合格的焊点。
三、BGA的焊盘设计原则
1、PCB上的每个焊盘的中心与BGA底部相对应的焊球中心相吻合;
2、PCB焊盘图形为实心圆,导通孔不能加工在焊盘上;
3、与焊盘连接的导线宽度要一致,一般为0.15mm~0.2mm;
4、阻焊尺寸比焊盘尺寸大0.1mm~0.15mm;
5、焊盘附近的导通孔在金属化后,必须用阻焊剂进行堵塞,高度不得超过焊盘高度;
6、在BGA器件外廓四角加工丝网图形,丝网图形的线宽为0.2mm~0.25mm。
BGA器件的焊盘形状为圆形,通常PBGA焊盘直径应比焊球直径小20%。
焊盘旁边的通孔,在制板时须做好阻焊,以防引起焊料流失造成短路或虚焊。
BGA焊盘间距应按公制设计,由于元件手册会给出公制和英制两种尺寸标注,实际上元件是按公制生产的,按英制设计焊盘会造成安装偏差。
上面提到的PBGA是塑封体,有铅PBGA的焊球的材料为63Sn37Pb,与有铅焊料的成份是一致的,在焊接过程中与焊料同时融化,形成焊点。
无铅PBGA的焊球是SAC307或SAC305,与常用的无铅焊料的成份也比较接近,在焊接中也会融化,形成焊点。
但是还有一种BGA,封装体是陶瓷,称为CBGA,CBGA的焊球是高温焊料,其熔点远远高于常见的焊料,在焊接中,CBGA的焊球是不融化的,因此,CBGA的焊盘设计与PBGA的焊盘设计是不一样的。
具体设计参数可参考下图:
四、焊盘的热隔离
SMD器件的引脚与大面积筒箔连接时,要进行热隔离处理,否则会由于元件两端热量不均衡,造成焊接缺陷。
五、再流焊工艺导通孔的设置
1、一般导通孔直径不小于0.75mm;
2、除SOIC、QFP、PLCC 等器件外,不能在其它元器件下面打导通孔;
3、导通孔不能设计在焊接面上片式元件的两个焊盘中间的位置;
4、更不允许直接将导通孔作为BGA器件的焊盘来用;
5、导通孔和焊盘之间应有一段涂有阻焊膜的细连线相连,细连线的长度应大于0.5mm;宽度大于0.4mm。
要绝对避免在表面安装焊盘以内设置导通孔,在距表面安装焊盘0.635mm以内设置导通孔,应该通过一小段导线连接,并用阻焊剂将焊料流失通道阻断,否则容易引起“立片”或“焊料不足”等缺陷。
六、插装元器件焊盘设计
1、孔距为5.08mm或以上的,焊盘直径不得小于3mm;
2、孔距为2.54mm的,焊盘直径最小不应小于1.7mm;
3、电路板上连接220V电压的焊盘间距,最小不应小于3mm;
4、流过电流超过0.5A(含0.5A)的焊盘直径应大于等于4mm;
5、焊盘以尽可能大一点为好,对于一般焊点,其焊盘直径最小不得小于2mm。
插装元器件焊盘孔径设计
采用波峰焊接工艺时,元件插孔孔径,一般比其引脚线径大0.1 mm- 0.3mm为宜,其焊盘的直径应大于孔径的3倍。
电阻、二极管的安装孔距应设计为标准系列7.5mm、10mm、12.5mm、15mm,电解电容的安装孔距应与元件引脚距一致,三极管的安装孔距应为2.54mm。
七、采用波峰焊工艺时,贴片元件的焊盘设计
采用波峰焊焊接片式元件时,应注意“阴影效应(缺焊)、‘桥接’(短路)”的发生,对于
CHIP元件,应将元件的轴向方向垂直于PCB的传送方向,小的元件应在大的元件前面,间距应大于2.5mm;
采用波峰焊工艺时焊盘设计的几个要点
1、高密度布线时应采用椭圆焊盘图形,以减少连焊;
2、为了减小阴影效应提高焊接质量,波峰焊的焊盘图形设计时对于SOT、钽电容,延伸元件体外的焊盘长度,在长度方向应比正常设计的焊盘向外扩展0.3mm;
3、对于SOP,为防止桥接,对SOP最外侧的两对焊盘加宽,以吸附多余的焊锡;或设置工艺焊盘(也称为盗锡焊盘)。
工艺焊盘是个空焊盘,作用就是吸收多余的焊锡,它的位置是在沿传送方向的最后一个焊盘的后面。
八、丝印字符的设计
1、一般情况需要在丝印层标出元器件的丝印图形,丝印图形包括丝印符号、元器件位号、极性和IC的第一脚标志,高密度窄间距时可采用简化符号,特殊情况可省去元器件的位号;
2、有极性的元器件,应按照实际安装位置标出极性以及安装方向;
3、对两边或四周引出脚的集成电路,要用符号(如:小方块、小圆圈、小圆点)标出第1号管脚的位置,符号大小要和实物成比例;
4、BGA器件最好用阿拉伯数字和英文字母以矩阵的方式标出第一脚的位置;
5、对连接器类元件,要标出安装方向、1号脚的位置。
6、以上所有标记应在元件安装框外,以免焊接后遮盖,不便于检查。
7、丝印字符应清晰,大小一致,方向尽量整齐,便于查找;
8、字符中的线、符号等不得压住焊盘,以免造成焊接不良。