三维射流中颗粒碰撞的直接数值模拟 (1)
颗粒—壁面碰撞建模与数据处理
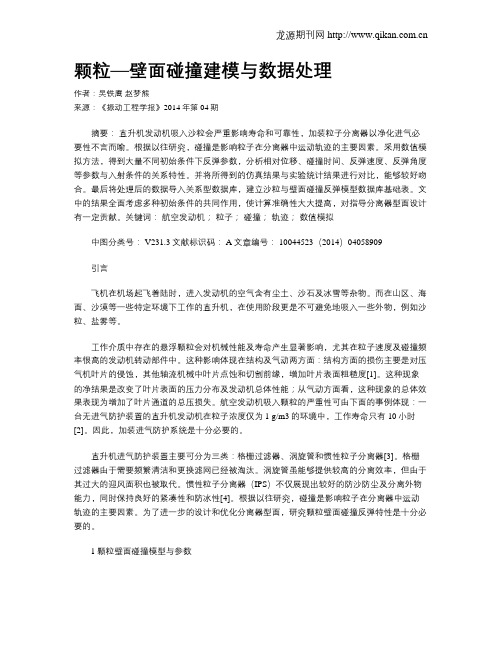
颗粒—壁面碰撞建模与数据处理作者:吴铁鹰赵梦熊来源:《振动工程学报》2014年第04期摘要:直升机发动机吸入沙粒会严重影响寿命和可靠性,加装粒子分离器以净化进气必要性不言而喻。
根据以往研究,碰撞是影响粒子在分离器中运动轨迹的主要因素。
采用数值模拟方法,得到大量不同初始条件下反弹参数,分析相对位移、碰撞时间、反弹速度、反弹角度等参数与入射条件的关系特性。
并将所得到的仿真结果与实验统计结果进行对比,能够较好吻合。
最后将处理后的数据导入关系型数据库,建立沙粒与壁面碰撞反弹模型数据库基础表。
文中的结果全面考虑多种初始条件的共同作用,使计算准确性大大提高,对指导分离器型面设计有一定贡献。
关键词:航空发动机;粒子;碰撞;轨迹;数值模拟中图分类号: V231.3文献标识码: A文章编号: 10044523(2014)04058909引言飞机在机场起飞着陆时,进入发动机的空气含有尘土、沙石及冰雪等杂物。
而在山区、海面、沙漠等一些特定环境下工作的直升机,在使用阶段更是不可避免地吸入一些外物,例如沙粒、盐雾等。
工作介质中存在的悬浮颗粒会对机械性能及寿命产生显著影响,尤其在粒子速度及碰撞频率很高的发动机转动部件中。
这种影响体现在结构及气动两方面:结构方面的损伤主要是对压气机叶片的侵蚀,其他轴流机械中叶片点蚀和切割前缘,增加叶片表面粗糙度[1]。
这种现象的净结果是改变了叶片表面的压力分布及发动机总体性能;从气动方面看,这种现象的总体效果表现为增加了叶片通道的总压损失。
航空发动机吸入颗粒的严重性可由下面的事例体现:一台无进气防护装置的直升机发动机在粒子浓度仅为1 g/m3的环境中,工作寿命只有10小时[2]。
因此,加装进气防护系统是十分必要的。
直升机进气防护装置主要可分为三类:格栅过滤器、涡旋管和惯性粒子分离器[3]。
格栅过滤器由于需要频繁清洁和更换滤网已经被淘汰。
涡旋管虽能够提供较高的分离效率,但由于其过大的迎风面积也被取代。
球磨过程中颗粒间相互作用的数值模拟与分析

球磨过程中颗粒间相互作用的数值模拟与分析球磨过程是粉末冶金中常用的一种加工方法,其作用是利用磨料间的摩擦击打作用,对原来的粉末进行研磨和混合,达到精细化和均匀化的目的。
球磨过程中颗粒间的相互作用是一个复杂的问题,涉及到多个物理过程,如磨料的摩擦、颗粒之间的碰撞和反弹、形变和破裂等。
因此,使用数值模拟的方法研究球磨过程中颗粒间的相互作用,具有重要的理论和实践意义。
首先,我们需要了解球磨过程中的物理模型。
球磨过程中,颗粒之间的相互作用受到多个力的影响,主要包括重力、离心力、摩擦力、碰撞力、弹性力和形变力等。
其中,重力和离心力是影响颗粒相互作用的根本力量,而摩擦和碰撞力则是颗粒之间的摩擦强度和碰撞频率的重要因素。
弹性力和形变力则涉及到颗粒之间的相对位移和变形情况,对颗粒的破坏和变形也有一定的影响。
在理解球磨过程的物理模型后,我们可以利用数值模拟的方法来模拟球磨过程中颗粒之间的相互作用过程。
数值模拟主要依靠计算机和相应的软件,通过对球磨过程中各种力的计算和统计,来模拟颗粒之间的相互作用。
数值模拟方法具有计算准确、速度快、能够反映物理现象的优点,可以为球磨过程的优化和设计提供重要的数据和参考。
球磨过程的数值模拟涉及多个领域,包括机械工程、物理学、计算机科学等。
一般来说,数值模拟包括两种方法:一种是基于流场的方法,另一种是基于离散元法的方法。
基于流场的方法主要是利用一系列的方程式来描述颗粒之间相互作用的过程,基于这些方程式进行计算,得到颗粒间相互作用力,进而预测颗粒在球磨过程中的轨迹和破碎情况。
离散元法则是将颗粒看作是离散的粒子,通过对微小时间段内粒子运动的分析,得到相邻粒子之间的相互作用力,并进行建模和预测。
在球磨过程的数值模拟中,一般会采用不同的软件来进行计算和分析。
目前比较流行的球磨过程数值模拟软件有:ABAQUS、ANSYS、FLUENT等。
这些软件具有不同的特点和适用范围,用户可以根据自己的需要来选择适合的软件进行模拟。
基于有限元法催化剂颗粒撞击壁面的数值模拟
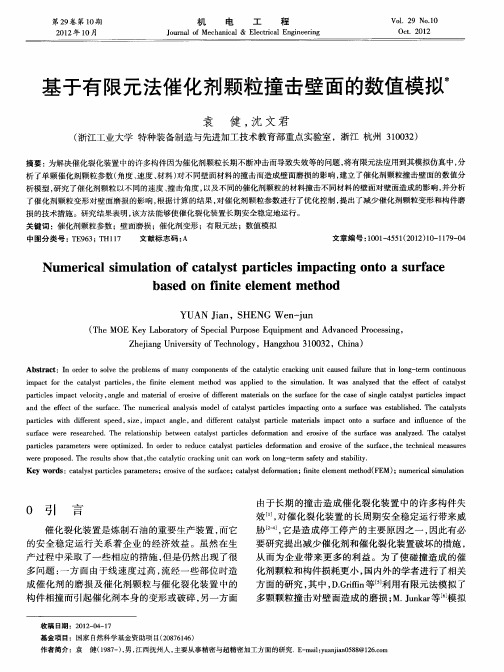
从而为企业 带来更 多的利益 。为 了使碰撞造成 的催 化剂 颗 粒 和构 件 损耗 更 小 , 国内外 的学者 进行 了相关 方面的研究 , 中, .r n 其 DGi 等 利用有限元法模拟了 i f 多颗颗粒撞击对壁面造成的磨损 ; . ukr 模拟 M Jna等
节 点发生 的最 大位移 如 图 8 所示 。
参考文 献 ( frne) Reeecs :
[ ] 杨 勇刚 , 勇. 1 罗 催化剂磨 损和再生器催化 剂跑损 的控制 [] 炼油设 计 ,0 13 ( )1ቤተ መጻሕፍቲ ባይዱ— 8 J. 2 0 ,19 :5 1. [ ] 刘仁桓 , 2 魏耀东 , 催化裂化装置跑损催化剂 的颗粒粒度分 析[] 石油化工设备 ,0 6 3 ( )9 1 . J. 20 ,5 2 :- 1
p r ce a a t r r p i z d n o d r t e u e c t y t p r ce e o mai n a d e o i e o h u f c t e t c n c a u e a il s p r me e s we e o t t mie .I r e o r d c aa s a t ls d fr t n r sv ft e s r e,h e h ia me s r s l i o a l
[ ] 陈学 东 , 3 王
冰, 关卫和 , 我国石化企业在用压力容器 等.
与管道使用现状和缺 陷状况分 析及失效预防对策 [] 压 J.
力容 器 ,0 1 1( )4 — 3 20 ,8 5 :3 5 . [ ] 万古军 , 4 魏耀东 , 时铭显. 化裂化再生器 树枝状 主风分 催
布管磨损 的气相流场分 析[ ]炼油技 术与工程 ,0 6 3 J. 2 0 ,6
基于离散单元法球形颗粒碰撞破碎行为的数值模拟_黄令军
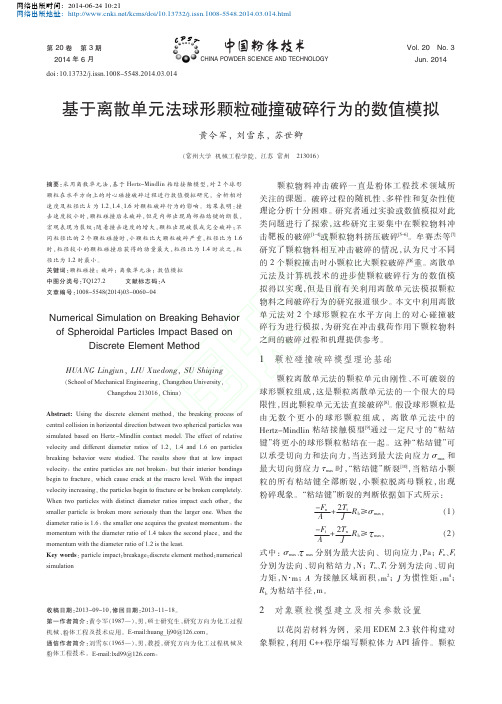
,
对象颗粒模型建立及相关参数设置
以花岗岩材料为例 ! 采用 ?@?' ,.A 软件构建对
象颗粒 ! 利用 B;; 程序编写颗粒体力 C=D 插件 & 颗粒
第期
黄令军 等 基于离散单元法球形颗粒碰撞破碎行为的数值模拟
-(
体力的作用是在用户给定的某一时间 + 时将所有的 大颗粒移除 同时根据对象颗粒的每个小颗粒的坐标 位置数据文件生成小颗粒 并替换原来的大颗粒 利 用 23456789:;<9: 粘结接触模型 把替换后的小颗粒 球团在某一时间 ,,=( 时按照一定的 粘结键 粘结 起来 得到对象颗粒 对象颗粒构建过程及对象颗粒 粘结键如图 ( 所示 对象颗粒为粒径为 ' ## 的球体 该颗粒由 ')> 个粒径为 >&' ## 的 小 颗 粒 粘 结 而 成 对象颗粒内部小颗粒之间的粘结键总个数为 * (,*
颗粒流动的数值模拟及实验研究

颗粒流动的数值模拟及实验研究颗粒流动是一种复杂的现象,涉及到颗粒间的相互作用、运动规律等多个方面。
为了深入研究颗粒流动的特征和机理,科研工作者们通过数值模拟和实验研究等多种手段,不断地探索和发现着新的知识和成果。
一、颗粒流动的特征颗粒流动是指由多颗粒组成的流体在外力驱动下的运动,其特征主要包括:流态发生变化、颗粒间存在复杂的相互作用、流体的分布形态和粒子的分布均匀性等方面。
二、数值模拟的研究方法数值模拟是通过计算机模拟的手段对颗粒流动进行分析和研究,其研究方法包括:离散元方法、CFD方法等。
离散元方法,即基于颗粒的微观模型,通过模拟颗粒的运动以及颗粒间的相互作用,得出颗粒流动的宏观行为。
这种方法主要适用于颗粒数较少,流动过程中颗粒的相互作用较为复杂的情况。
CFD方法,即计算流体力学,是基于流体的宏观模型,通过建立热力学方程和动量方程,对流动过程进行模拟和计算。
这种方法适用于流体密度较大、流体动力学参数较为简单的情况。
三、实验研究的手段和方法实验研究是通过实际操作和测量对颗粒流动进行分析和研究,其手段和方法包括:流变仪、振荡板等。
流变仪是实验室中常用的颗粒流变测试仪器,通过测量颗粒在不同条件下的流变特性,分析颗粒流动的变化和特征。
振荡板是一种实验装置,通过振动颗粒床,观察颗粒的运动和变化过程,从而研究颗粒流动的特征和规律。
四、数值模拟和实验研究的应用颗粒流动的数值模拟和实验研究在多个领域中都得到了广泛的应用,如:材料科学、工程力学等。
在材料科学中,颗粒流动的数值模拟和实验研究可用于分析材料的流变特性、制备过程中的颗粒分布、粒度分布等,从而优化材料制备工艺,提高产品质量。
在工程力学中,颗粒流动的数值模拟和实验研究可用于分析颗粒在输送过程中的运动特征、优化输送系统的设计、改进输送效率、降低系统的维护成本等。
综上所述,颗粒流动的数值模拟和实验研究,对于深入了解其特征和机理,优化材料制备工艺,提高系统的输送效率等方面都具有重要的意义和作用。
立式循环撞击流反应器三维流场的数值模拟
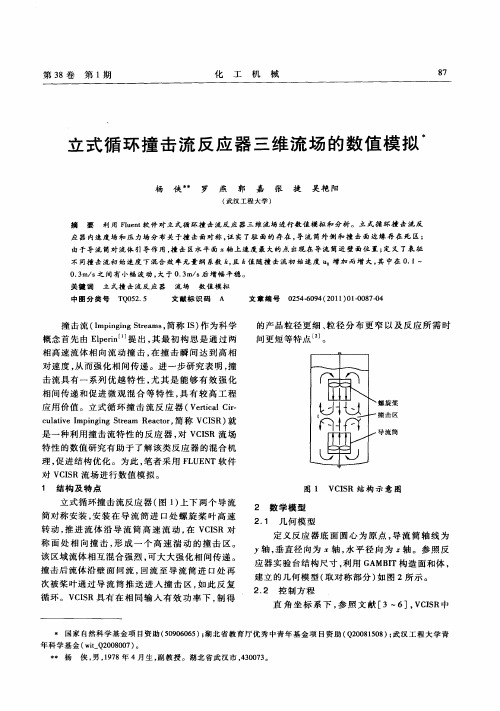
初 始速度 变化 范 围为 0 1~1 O / , 面上 表 压 . . m s液
图 2 V S 几 何 模 型 CIR
流 动 满 足 的 控 制 方 程 有 连 续 性 方 程 、 y 向 动 量 x z3
为 0 壁面满 足无 滑移条 件 , , 即相对 速度为 0 。 3 计算结 果及分 析
应 器 内速 度 场 和 压 力 场 分 布 关 于撞 击 面 对 称 , 实 了驻 面 的 存 在 , 流 筒 外 侧 和 撞 击 面 边 缘 存 在 死 区 ; 证 导 由于 导 流 筒 对 流 体 引 导作 用 , 击 区水 平 面 轴 上速 度 最 大 的 点 出现 在 导 流 筒 近 壁 面 位 置 ; 义 了表 征 撞 定 不 同撞 击 流初 始 速度 下 混合 效 率 无 量 纲 系数 k 且 k 随撞 击 流 初 始速 度 增 加 而 增 大 , 中 在 0 1— , 值 其 .
应 器实 验 台结构 尺寸 , 利用 G MBT构造 面和体 , A I
建 立 的几何模 型 ( 取对称 部 分 ) 图 2所 示 。 如
2 2 控 制方程 .
次 被桨 叶通过 导 流筒 推 送进 入撞 击 区 , 此 反 复 如 循环 。V IR具 有 在相 同输 入 有 效 功 率 下 , 得 CS 制
称 面处 相 向撞 击 , 成 一 个 高 速 湍 动 的 撞 击 区。 形
定 义反 应器 底 面 圆 心 为原 点 , 流 筒 轴 线 为 导
Y轴 , 直径 向为 轴 , 平 径 向为 轴 。参 照 反 垂 水
该 区域 流体相 互混 合强烈 , 大大 强化相 间传 递 。 可
撞击 后 流体沿 壁 面 回流 , 回流 至 导 流筒 进 口处 再
绕流中颗粒与柱体碰撞和磨损的直接数值模拟

绕流中颗粒与柱体碰撞和磨损的直接数值模拟闫洁;李文春;樊建人;岑可法【期刊名称】《浙江大学学报(工学版)》【年(卷),期】2007(041)004【摘要】为了研究圆柱近壁区颗粒与柱体的碰撞和磨损问题,采用高精度有限差分的方法对圆柱绕流进行了直接数值模拟.在获得高精度计算流场信息的基础上,采用Lagrangian方法追踪了颗粒在圆柱近壁区的运动.利用非弹性碰撞模型的壁面磨损量经验公式,进行了壁面磨损量的计算,详尽考察了不同粒径的颗粒与壁面的碰撞磨损情况.研究发现,随着颗粒粒径的增大,颗粒与壁面的碰撞频率变高;局部碰撞频率的曲线较为特殊,粒径较大颗粒的碰撞多发生在与来流方向平行的中心轴线处,而小粒径颗粒的碰撞则要外移一定的位置.还发现颗粒对壁面的磨损率也是随粒径的增大而增大.颗粒的冲击角对壁面的磨损同样起着至关重要的影响,对于塑性材料,冲击角为20°~30°时,壁面的磨损率最大.【总页数】5页(P589-593)【作者】闫洁;李文春;樊建人;岑可法【作者单位】浙江大学,热能工程研究所,能源洁净利用国家重点实验室,浙江,杭州,310027;浙江大学,热能工程研究所,能源洁净利用国家重点实验室,浙江,杭州,310027;浙江大学,热能工程研究所,能源洁净利用国家重点实验室,浙江,杭州,310027;浙江大学,热能工程研究所,能源洁净利用国家重点实验室,浙江,杭州,310027【正文语种】中文【中图分类】O357【相关文献】1.三维气固圆柱绕流颗粒扩散的直接数值模拟 [J], 陈懿;樊建人;任安禄;岑可法2.速度剪切流中圆柱体绕流特性的数值模拟 [J], 周强;曹曙阳;王通;周志勇3.基于颗粒摩擦和碰撞模型的离心泵叶片磨损预测 [J], 程效锐;董富弟;杨从新;赵伟国;张楠4.高炉渣颗粒绕流异形管磨损过程的数值模拟 [J], 郭燕;于庆波;秦勤5.三维射流中颗粒碰撞的直接数值模拟 [J], 闫洁;罗坤;樊建人因版权原因,仅展示原文概要,查看原文内容请购买。
三维喷动流化床流动特性数值模拟

Mn t f d ctn Su es U vrt, aj g209 ,C i ) isy0 E ua o , ot at n e i N ni 106 h a ir i h i sy n n
As b嘣
: r -ies nl uea u -u oe adt iecho f r u r o ee pldt s d te a- l A t e d ni a E l nm l fi m dln h knt er 0 g nl fww r ap e o t yh ss — he m o f i i tl d e it y a al i u g o
o f a n0 s g
i o b h vo naso tf i e ol aie .A l so t udbdw t imee f10mi a i ltd h eerh df w e airi pu-udb dca s r l l g f i s l pu-i e i ada tr 0 lw ssmuae .T ersac ma l f h 0 l
w s oeo h ee p et f/i e a j , a- l lw pn rs ne ie n oe I niosadd t a n nt dvl m n 0 1n r le gss i o aeI dr f r t pr 1 c d i n i ̄ d e o 8 tn t odf lu d e g o tn . s
中图分类号 :T 01 1 Q .3 5 文献标 志码 :A 文章编 号 :10 -702 0 )400 -5 0684 (0 70 -390
S mu a in o l w a a t r i r e Di e so a i l to fF o Ch r c e n Th e . m n i n l S o tFl i d p u - u d Be
颗粒碰撞模型与数值研究
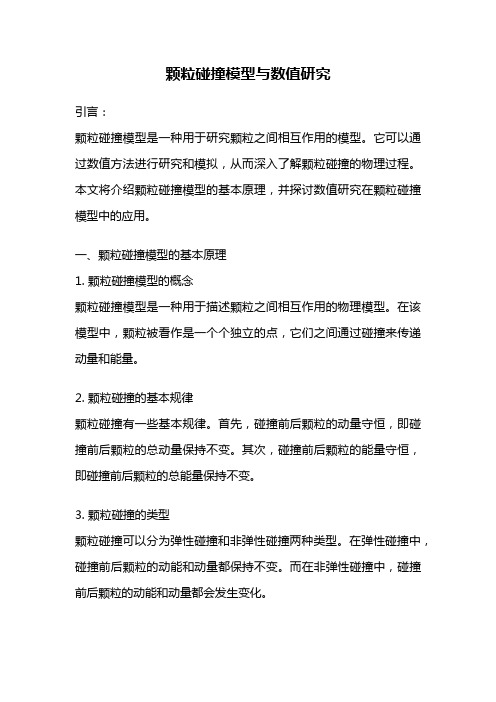
颗粒碰撞模型与数值研究引言:颗粒碰撞模型是一种用于研究颗粒之间相互作用的模型。
它可以通过数值方法进行研究和模拟,从而深入了解颗粒碰撞的物理过程。
本文将介绍颗粒碰撞模型的基本原理,并探讨数值研究在颗粒碰撞模型中的应用。
一、颗粒碰撞模型的基本原理1. 颗粒碰撞模型的概念颗粒碰撞模型是一种用于描述颗粒之间相互作用的物理模型。
在该模型中,颗粒被看作是一个个独立的点,它们之间通过碰撞来传递动量和能量。
2. 颗粒碰撞的基本规律颗粒碰撞有一些基本规律。
首先,碰撞前后颗粒的动量守恒,即碰撞前后颗粒的总动量保持不变。
其次,碰撞前后颗粒的能量守恒,即碰撞前后颗粒的总能量保持不变。
3. 颗粒碰撞的类型颗粒碰撞可以分为弹性碰撞和非弹性碰撞两种类型。
在弹性碰撞中,碰撞前后颗粒的动能和动量都保持不变。
而在非弹性碰撞中,碰撞前后颗粒的动能和动量都会发生变化。
二、数值研究在颗粒碰撞模型中的应用1. 数值方法的优势数值方法是一种重要的研究颗粒碰撞模型的手段。
它可以通过计算机模拟来快速获取大量的数据,并通过分析这些数据来揭示颗粒碰撞的规律。
相比传统的实验方法,数值方法具有成本低、实验条件可控等优势。
2. 数值模拟的步骤进行数值研究时,首先需要建立颗粒碰撞模型的数学描述,包括颗粒的形状、质量、速度等参数。
然后,利用计算机程序对模型进行数值模拟。
通过调整模型参数和初值条件,可以模拟出不同条件下的颗粒碰撞过程。
3. 数值方法的应用数值方法在颗粒碰撞模型中有广泛的应用。
例如,可以通过数值模拟来研究颗粒碰撞的能量转化过程,探究不同碰撞类型对能量损失的影响。
此外,数值方法还可以用于优化颗粒碰撞模型的设计,提高碰撞效率。
4. 数值方法的局限性虽然数值方法在颗粒碰撞模型中具有很大的应用潜力,但也存在一些局限性。
首先,数值模拟的结果受到模型参数的选择和初值条件的影响,需要进行合理的设定。
其次,数值模拟的计算量较大,需要消耗大量的计算资源和时间。
三、颗粒碰撞模型与数值研究的未来发展1. 模型精度的提高随着计算机技术的不断发展,颗粒碰撞模型的数值模拟精度将会得到进一步提高。
流体流动中的三维射流模拟

流体流动中的三维射流模拟摘要流体力学是一门研究流体运动规律的科学,广泛应用于各个领域,如汽车工业、航空航天、海洋工程等。
其中,射流模拟是流体力学中的一个重要研究方向。
本文主要介绍了流体流动中的三维射流模拟的原理、方法和应用。
引言射流是指某一流体通过出口处流出时,流速较高、流动方向较集中的现象。
在工程领域中,射流模拟是一项十分重要的研究内容。
通过对射流的模拟,可以更好地理解和预测流体运动及其对周围环境的影响。
三维射流模拟原理三维射流模拟是指在三维坐标系下对射流运动进行数值模拟和预测。
其原理基于流体力学的基本方程和离散化方法,通常采用计算流体力学(CFD)方法进行模拟。
CFD方法主要基于三个基本假设:连续介质假设、雷诺平均和湍流模型。
首先,连续介质假设认为流体是连续分布的,并可以用连续介质力学进行描述。
其次,雷诺平均假设认为流体的宏观运动可以用平均值描述,忽略了微观细节。
最后,湍流模型用于描述流体中的湍流现象,通常采用雷诺平均应力方程进行模拟。
三维射流模拟的基本步骤包括几何建模、离散化和求解、后处理等。
几何建模是指将实际流动的几何形状转换为计算机能够处理的几何模型的过程。
离散化和求解是将流体区域分割为网格,并对区域内的各个物理量进行离散化处理,然后使用数值方法求解离散方程。
后处理是对求解结果进行分析和解释的过程。
三维射流模拟方法在三维射流模拟中,常用的方法包括有限体积法、有限差分法和有限元法。
有限体积法通过将流动区域划分为有限体积单元,然后对每个单元进行质量、能量和动量守恒方程的求解。
有限差分法将流动区域离散为网格点,通过有限差分近似导数,然后将方程进行离散化求解。
有限元法将流动区域分割为离散的单元,通过对流体流动方程进行加权残差积分,得到离散方程组。
不同的方法具有各自的优缺点和适用范围。
有限体积法适用于处理不规则几何形状和复杂边界条件的问题,有限差分法适用于规则几何形状和简单边界条件的问题,有限元法适用于对流体运动较为精确描述的问题。
蒸汽喷射器三维流场的数值模拟计算与分析

大连理工大学硕士学位论文蒸汽喷射器三维流场的数值模拟计算与分析姓名:***申请学位级别:硕士专业:热能工程指导教师:李素芬;沈胜强20000601摘要r气体喷射器作为一种节能装置,可回收大量余热,起到了节能和环保的双重作用,在工业部门中得到广泛应用。
其内部经历着复杂的多维湍流流动过程,而其中喷嘴更是决定喷射器是否正常工作的关键部件。
j本文在详细分析喷射器内部流动的基础上,建立了三维湍流流动的数值模拟计算模型,并主要对喷嘴的流场进行了详细的计算分析。
本文主要内容有:1、深入分析了KIVA系列程序与相关的CFD理论方法,结合气体喷射器喷嘴的流动特点,建立了喷射器喷嘴复杂流场结构的三维数值模拟计算模型和计算方法,并应用于喷射器喷嘴稳态流场的数值模拟计算中。
2、根据气体喷射器结构和特点建立了喷射器整体及喷嘴通用计算网格的生成方法,并编制了相应的计算网格生成程序。
其网格生成方法及程序适用于各种结构及尺寸的喷嘴和喷射器,充分体现了其灵活性和实用性。
3、运用本文开发的通用计算网格生成程序结合三维流场数值模拟计算程序,针对不同的边界条件和结构尺寸的喷嘴流场,进行了数值模拟计算,考察了以上各特性参数对喷射器内部流动的影响,并根据计算结构的分析提出了喷射器喷嘴设计的建议。
4、比较全面地考虑了各种不可逆因素(如摩擦、散热等)对流场各参数的影响,进一步完善了喷射器的研究■一一关键词:喷嘴、数值模拟、流场ABSTRACTAsakindofdevice,thesteamejectorcarlrecycleagreatdealofenergy,andatthesametime,itplayagreatroleofenvironmentprotection,SOitisappliedinmanyindustrydepartments.Itsflowfieldismulti—dimensions,transient,turbulent,subsonicandsupersonicflows.Andthenozzleisthekeyoftheejector.Onthebaseofexpatiatingontheflowsinsidethesteamejector,athree—dimensional,turbulent,numericalsimulationcomputationalmode】.andthemethodiSutilizedemphaticallyonanalysisandcalculationtheflowfieldofthenozzle.Themainworksaresummarizedasfollows:1.AnalyzetheprincipleofnumericalcomputationoftheKIVA一3codeandCFDmeans.combiningtheflowingcharacteristicofnozzle,aprogramsuitabletocomputethiskindofflowfieldbynumericalsimulationmethodiscompiled.2.Applythemethodofbody·fittedmeshgenerationandtheblock—structuredmethod,acommonprogramiscompiled.Itcanbenotonlyutilizedontheejector,butmanycomplicatestructureflowfields.3.Mobilizingthecurrentgriddingprogramandthenumericalsimulationcomputationalmodel,analyzeandcalculatetheflOWfieldOfthenozzle,discnsstheeffeCtsontheflOW0fvarj0USboundarYCOnditions,structureSize.Theresultspresentparticularsuggestionfortheoptimizingdesignofthenozzle.4.GenerallycOnsidertheinfeCtiOnSofmanYkindSOfunreversiblefactors(friction,heatdispersion),andmaketheresearchofnozzleorejectormoreperfect.Keywords:nozzle,numericalsimulation,flowfield第一章绪论第一章绪论本章在查阅大-¥-文献的基础上.xea-喷射器及:g-数值-}-I-算等研究领域的发展和概况进行了详细的综述,并概括出本文的主要内容。
三维粒状脆性材料颗粒破碎的数值三轴试验_孙德胜
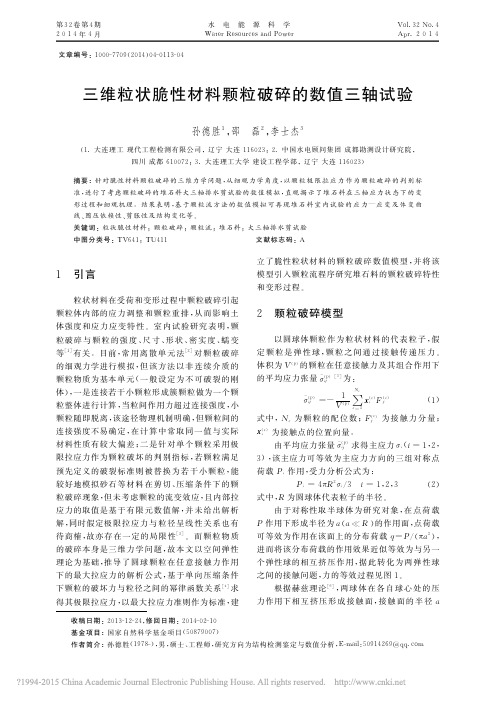
三维粒状脆性材料颗粒破碎的数值三轴试验
孙德胜1, 邵 磊2, 李士杰3
( 1.大连理工 现代工程检测有限公司 ,辽宁 大连 1 1 6 0 2 3; 2.中国水电顾问集团 成都勘测设计研究院 , ) 四川 成都 6 1 0 0 7 2; 3.大连理工大学 建设工程学部 ,辽宁 大连 1 1 6 0 2 3 摘要 :针对脆性材料颗粒破碎的三维力学问题 , 从细观 力 学 角 度 , 以颗粒极限拉应力作为颗粒破碎的判别标 准, 进行了考虑颗粒破碎的堆石料大三轴排水剪试验的数 值 模 拟 , 直观揭示了堆石料在三轴应力状态下的变 形过程和细观机理 。 结果表明 , 基于 颗 粒 流 方 法 的 数 值 模 拟 可 再 现 堆 石 料 室 内 试 验 的 应 力 — 应 变 及 体 变 曲 围压依赖性 、 剪胀性及结构变化等 。 线、 关键词 :粒状脆性材料 ;颗粒破碎 ;颗粒流 ;堆石料 ;大三轴排水剪试验 中图分类号 : TV 6 4 1; TU 4 1 1 文献标志码 :A
第3 2卷 第4期 2 0 1 4年4月 ( ) 文章编号 : 1 0 0 0 7 7 0 9 2 0 1 4 0 4 0 1 1 3 0 4 - - -
水 电 能 源 科 学 W a t e r R e s o u r c e s a n d P o w e r
V o l . 3 2N o . 4 A r . 2 0 1 4 p
求
得其极限拉应力 , 以最大拉应力准则作为标准 , 建
, 收稿日期 : 修回日期 : 2 0 1 3 1 2 2 4 2 0 1 4 0 2 1 0 - - - - ) 基金项目 :国家自然科学基金项目 ( 5 0 8 7 9 0 0 7
力作用下相 互 挤 压 形 成 接 触 面 , 接触面的半径a
颗粒高速撞击并嵌入金属表面的三维动力学有限元模拟
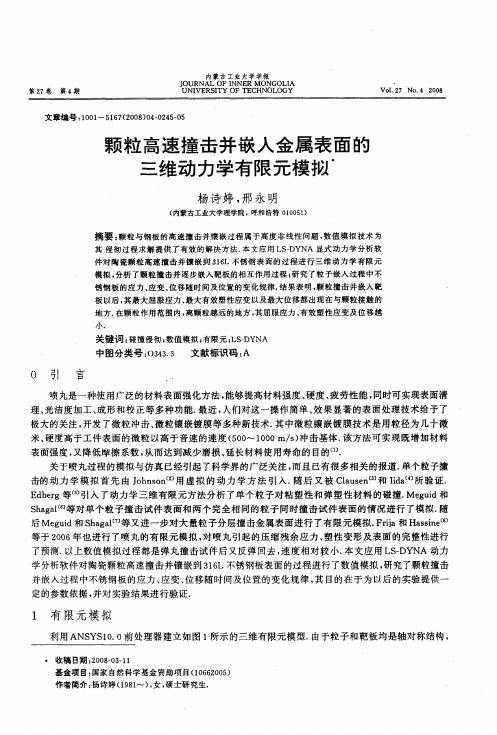
极大的关注, 开发了微粒冲击 、 微粒镶嵌镀膜等多种新技术. 其中微粒镶嵌镀膜技术是用粒径为几十微 米 、 度高于工 件表 面 的微粒 以高于 音速 的速 度 (0  ̄1 0 s 冲击 基体 . 硬 5 0 0 0m/ ) 该方 法 可实 现既增 加材 料
表面强 度 , 又降低 雎擦 系数 , 从而达 到减 少磨损 、 延长 材料使 用寿命 的 目的n.
板 为 无限域. 陶瓷颗粒 半径 为2mm, 1 L不锈 钢板 的长取为 1 36 6mm、 宽取 为 1 6 mm、 高取 为1 2mm. 颗粒 垂直 撞击不锈 钢板并 最终镶 嵌 在钢板 表面 . 约束 钢板底 面的所有 自由度.
颗粒和 靶板 均采 用 由 8节 点构 成 的 s l 1 4三 维实 oi 6 d 体单 元进 行 离散 , 并采 用 单 点积 分 的 L g a g a rn e算法 . 不
锈钢板材料的本构关系采用双线性各向同性模型, 其密
度为 7 9 /m 弹性 模 量 为 1 6GP , 服极 限 为 2 0 . 8g c , 9 a 屈 8
MP . 陶 瓷颗 粒 假定 为 刚 性 材 料 模 型 , 密 度为 3 2 a而 其 .7
gc . /m。考虑 到 计算 的精 确性 并 节省 计 算 时间 , 划分 网格
关于 喷丸过 程的模 拟与仿 真 已经 引起 了科学界 的广泛关 注 , 且 已有很 多相关 的报道 . 而 单个粒子 撞 击的动 力学 模 拟 首 先 由 Jh sn 虚 拟 的 动 力 学 方 法 引入 . 后 又 被 C a sn I a 验 证. o no 。 用 随 lu e 。 和 i “ 所 d E br d eg等 引入 了动力 学三 维 有限 元方 法分 析 了单 个粒 子 对粘 塑性 和 弹 塑性 材 料 的碰 撞. g i Meud和 S a a ’ 对单 个粒 子撞 击 试件 表 面和 两个 完 全相 同的 粒子 同 时撞击 试 件 表面 的情 况进 行 了模拟 . hg l 等 随 后 Me ud和 S a a订等 又进 一步 对大 量粒 子分 层撞击 金属 表面 进行 了 有限 元模 拟. ra和 Has e ’ gi h g l Fi j si 。 n 等 于 2 0 年 也进 行 了喷丸 的有 限元 模拟 , 喷丸 引起 的 压缩 残余 应力 、 性变 形 及表 面 的完整性 进行 06 对 塑 了预测. 以上数值 模拟 过 程都是 弹 丸撞 击试 件后 又反 弹 回去 , 度相对 较 小. 速 本文 应 用 L — Y S D NA 动力 学分析软 件对陶 瓷颗粒 高速撞 击并 镶嵌到 3 6 1L不锈 钢板表 面的过 程进行 了数值模拟 , 究了颗粒撞击 研 并嵌 入过程 中不锈 钢板 的应 力 、 应变 、 位移 随时 间及 位置 的变化 规律 , 目的在 于为 以后 的实 验提供 一 其
爆炸压实过程中颗粒碰撞问题的SPH法数值模拟
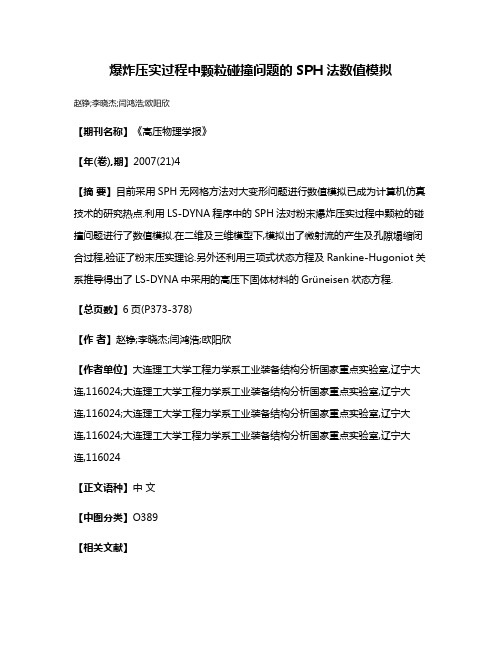
爆炸压实过程中颗粒碰撞问题的SPH法数值模拟
赵铮;李晓杰;闫鸿浩;欧阳欣
【期刊名称】《高压物理学报》
【年(卷),期】2007(21)4
【摘要】目前采用SPH无网格方法对大变形问题进行数值模拟已成为计算机仿真技术的研究热点.利用LS-DYNA程序中的SPH法对粉末爆炸压实过程中颗粒的碰撞问题进行了数值模拟.在二维及三维模型下,模拟出了微射流的产生及孔隙塌缩闭合过程,验证了粉末压实理论.另外还利用三项式状态方程及Rankine-Hugoniot关系推导得出了LS-DYNA中采用的高压下固体材料的Grüneisen状态方程.
【总页数】6页(P373-378)
【作者】赵铮;李晓杰;闫鸿浩;欧阳欣
【作者单位】大连理工大学工程力学系工业装备结构分析国家重点实验室,辽宁大连,116024;大连理工大学工程力学系工业装备结构分析国家重点实验室,辽宁大连,116024;大连理工大学工程力学系工业装备结构分析国家重点实验室,辽宁大连,116024;大连理工大学工程力学系工业装备结构分析国家重点实验室,辽宁大连,116024
【正文语种】中文
【中图分类】O389
【相关文献】
1.高速碰撞问题的三维SPH数值模拟 [J], 梁龙河;董师舜;王政;曹菊珍
2.基于SPH方法的柱状装药爆炸扩腔数值模拟 [J], 李福强;杨军;刘鑫;屈梅
3.基于SPH方法的爆炸压实孔隙塌缩模拟 [J], 李晓杰;陈翔;闫鸿浩;王小红;王宇新
4.钢箱内部爆炸破坏的SPH数值模拟 [J], 强洪夫; 孙新亚; 王广; 黄拳章
5.基于SPH法的爆炸焊接边界效应二维数值模拟 [J], 缪广红;艾九英;胡昱;马宏昊;沈兆武
因版权原因,仅展示原文概要,查看原文内容请购买。
颗粒—壁面碰撞建模与数据处理
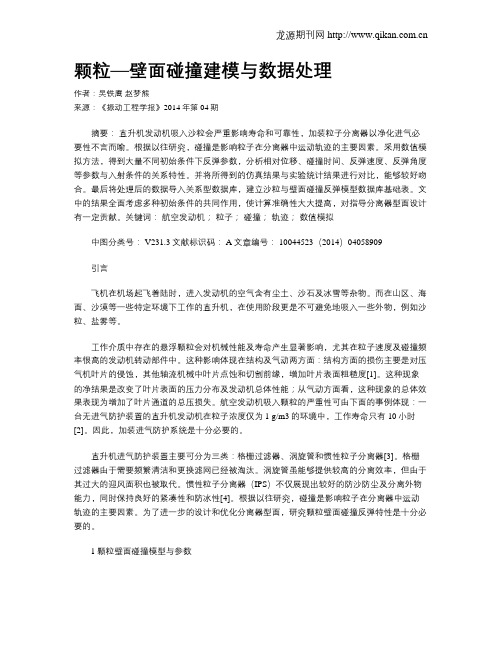
颗粒—壁面碰撞建模与数据处理作者:吴铁鹰赵梦熊来源:《振动工程学报》2014年第04期摘要:直升机发动机吸入沙粒会严重影响寿命和可靠性,加装粒子分离器以净化进气必要性不言而喻。
根据以往研究,碰撞是影响粒子在分离器中运动轨迹的主要因素。
采用数值模拟方法,得到大量不同初始条件下反弹参数,分析相对位移、碰撞时间、反弹速度、反弹角度等参数与入射条件的关系特性。
并将所得到的仿真结果与实验统计结果进行对比,能够较好吻合。
最后将处理后的数据导入关系型数据库,建立沙粒与壁面碰撞反弹模型数据库基础表。
文中的结果全面考虑多种初始条件的共同作用,使计算准确性大大提高,对指导分离器型面设计有一定贡献。
关键词:航空发动机;粒子;碰撞;轨迹;数值模拟中图分类号: V231.3文献标识码: A文章编号: 10044523(2014)04058909引言飞机在机场起飞着陆时,进入发动机的空气含有尘土、沙石及冰雪等杂物。
而在山区、海面、沙漠等一些特定环境下工作的直升机,在使用阶段更是不可避免地吸入一些外物,例如沙粒、盐雾等。
工作介质中存在的悬浮颗粒会对机械性能及寿命产生显著影响,尤其在粒子速度及碰撞频率很高的发动机转动部件中。
这种影响体现在结构及气动两方面:结构方面的损伤主要是对压气机叶片的侵蚀,其他轴流机械中叶片点蚀和切割前缘,增加叶片表面粗糙度[1]。
这种现象的净结果是改变了叶片表面的压力分布及发动机总体性能;从气动方面看,这种现象的总体效果表现为增加了叶片通道的总压损失。
航空发动机吸入颗粒的严重性可由下面的事例体现:一台无进气防护装置的直升机发动机在粒子浓度仅为1 g/m3的环境中,工作寿命只有10小时[2]。
因此,加装进气防护系统是十分必要的。
直升机进气防护装置主要可分为三类:格栅过滤器、涡旋管和惯性粒子分离器[3]。
格栅过滤器由于需要频繁清洁和更换滤网已经被淘汰。
涡旋管虽能够提供较高的分离效率,但由于其过大的迎风面积也被取代。
新型搅拌设备中粒子运动与碰撞的三维仿真
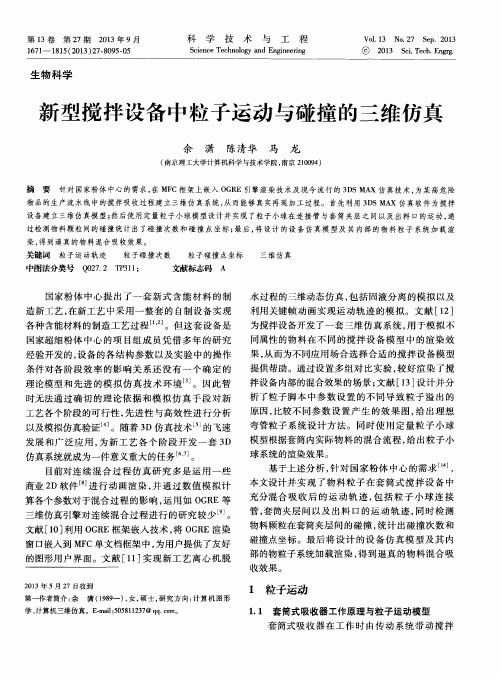
第一作者简介 : 余
潇( 1 9 8 9 一) , 女, 硕士, 研究 方 向 : 计 算机 图形
1 粒子运动
1 . 1 套筒 式吸收 器 工作原 理 与粒子 运动模 型 套 筒式 吸收 器 在 工 作 时 由传 动 系 统 带 动 搅 拌
学、 计算机三维仿真。E — m a i l : 5 0 5 8 1 1 2 3 7 @q q . c o n。 r
经验开发的, 设备的各结构参数以及实验 中的操作
条 件对 各 阶 段 效 率 的影 响关 系 还 没 有 一 个 确 定 的
果, 从而为不同应用场合选择合适 的搅拌设 备模 型 提供帮助。通过设 置多组对 比实验 , 较好渲染 了搅
拌设 备 内部 的混合 效果 的场 景 ; 文献 [ 1 3 ] 设 计 并 分 析 了粒 子 脚 本 中 参 数设 置 的不 同导 致 粒 子 溢 出 的 原 因, 比较 不 同参 数 设 置 产 生 的 效 果 图 , 给 出 理 想
弯管粒子系统设计方法。同时使用定量粒 子小球
模 型根据 套筒 内实 际物 料 的 混合 流程 , 给 出粒 子 小
球 系统 的渲染 效果 。
仿真系统就成为一件意义重大的任务 , 。
目前 对 连 续 混 合 过 程 仿 真 研 究 多 是 运 用 一 些 商业 2 D软 件 进 行 动 画 渲 染 , 并 通 过 数 值 模 拟 计 算 各 个参 数对 于混 合 过 程 的影 响 , 运用如 O G R E等 三维仿 真 引擎 对 连续 混 合 过程 进行 的研 究 较 少 。
第1 3卷
第2 7期
2 0 1 3年 9月
科
学
技
术
与
颗粒圆孔射流碰撞大规模并行直接数值模拟算法研究
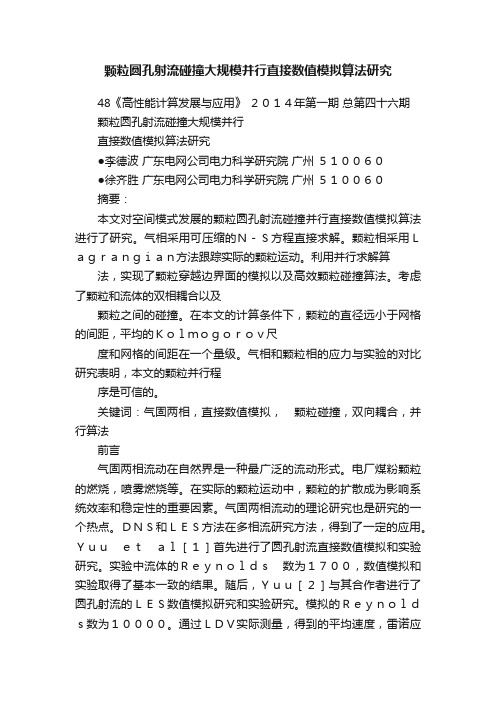
颗粒圆孔射流碰撞大规模并行直接数值模拟算法研究48《高性能计算发展与应用》2014年第一期总第四十六期颗粒圆孔射流碰撞大规模并行直接数值模拟算法研究●李德波广东电网公司电力科学研究院广州510060●徐齐胜广东电网公司电力科学研究院广州510060摘要:本文对空间模式发展的颗粒圆孔射流碰撞并行直接数值模拟算法进行了研究。
气相采用可压缩的N-S方程直接求解。
颗粒相采用Lagrangian方法跟踪实际的颗粒运动。
利用并行求解算法,实现了颗粒穿越边界面的模拟以及高效颗粒碰撞算法。
考虑了颗粒和流体的双相耦合以及颗粒之间的碰撞。
在本文的计算条件下,颗粒的直径远小于网格的间距,平均的Kolmogorov尺度和网格的间距在一个量级。
气相和颗粒相的应力与实验的对比研究表明,本文的颗粒并行程序是可信的。
关键词:气固两相,直接数值模拟,颗粒碰撞,双向耦合,并行算法前言气固两相流动在自然界是一种最广泛的流动形式。
电厂煤粉颗粒的燃烧,喷雾燃烧等。
在实际的颗粒运动中,颗粒的扩散成为影响系统效率和稳定性的重要因素。
气固两相流动的理论研究也是研究的一个热点。
DNS和LES方法在多相流研究方法,得到了一定的应用。
Yuuetal[1]首先进行了圆孔射流直接数值模拟和实验研究。
实验中流体的Reynolds数为1700,数值模拟和实验取得了基本一致的结果。
随后,Yuu[2]与其合作者进行了圆孔射流的LES数值模拟研究和实验研究。
模拟的Reynolds数为10000。
通过LDV实际测量,得到的平均速度,雷诺应力与实验吻合比较好。
Yamamotoetal[3]研究了竖直管道里面颗粒碰撞的LES模拟,他们提出了颗粒碰撞硬球模拟的算法。
采用DNS方法研究颗粒圆孔射流,能够得到空间和时间发展颗粒和流体湍流特性信息,从而为工程应用提供定量的参考。
在圆孔射流的数值模拟中,颗粒碰撞对气相流场和颗粒扩散的影响,目前还缺乏必要的认识[4]。
为了进一步研究颗粒和流体的相互作用,本文考虑和颗粒和流体的双向耦合,以及颗粒与颗粒之间的碰撞。
颗粒高速撞击并嵌入金属表面的三维动力学有限元模拟
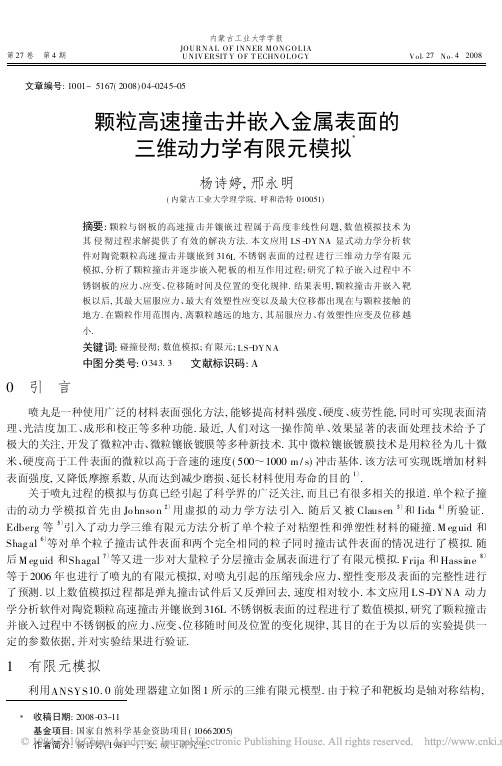
内蒙古工业大学学报JOURNAL OF INNER M ONGOLIA第27卷 第4期UNIVERSIT Y OF T ECHNOLOGY Vol.27No.42008 文章编号:1001-5167(2008)04-0245-05颗粒高速撞击并嵌入金属表面的三维动力学有限元模拟杨诗婷,邢永明(内蒙古工业大学理学院,呼和浩特010051)摘要:颗粒与钢板的高速撞击并镶嵌过程属于高度非线性问题,数值模拟技术为其侵彻过程求解提供了有效的解决方法.本文应用LS-DY NA显式动力学分析软件对陶瓷颗粒高速撞击并镶嵌到316L不锈钢表面的过程进行三维动力学有限元模拟,分析了颗粒撞击并逐步嵌入靶板的相互作用过程;研究了粒子嵌入过程中不锈钢板的应力、应变、位移随时间及位置的变化规律.结果表明,颗粒撞击并嵌入靶板以后,其最大屈服应力、最大有效塑性应变以及最大位移都出现在与颗粒接触的地方.在颗粒作用范围内,离颗粒越远的地方,其屈服应力、有效塑性应变及位移越小.关键词:碰撞侵彻;数值模拟;有限元;L S-DY N A中图分类号:O343.3 文献标识码:A0 引 言 喷丸是一种使用广泛的材料表面强化方法,能够提高材料强度、硬度、疲劳性能,同时可实现表面清理、光洁度加工、成形和校正等多种功能.最近,人们对这一操作简单、效果显著的表面处理技术给予了极大的关注,开发了微粒冲击、微粒镶嵌镀膜等多种新技术.其中微粒镶嵌镀膜技术是用粒径为几十微米、硬度高于工件表面的微粒以高于音速的速度(500~1000m/s)冲击基体.该方法可实现既增加材料表面强度,又降低摩擦系数,从而达到减少磨损、延长材料使用寿命的目的〔1〕.关于喷丸过程的模拟与仿真已经引起了科学界的广泛关注,而且已有很多相关的报道.单个粒子撞击的动力学模拟首先由Jo hnso n〔2〕用虚拟的动力学方法引入.随后又被Clausen〔3〕和Iida〔4〕所验证. Edberg等〔5〕引入了动力学三维有限元方法分析了单个粒子对粘塑性和弹塑性材料的碰撞.M eg uid和Shag al〔6〕等对单个粒子撞击试件表面和两个完全相同的粒子同时撞击试件表面的情况进行了模拟.随后M eg uid和Shagal〔7〕等又进一步对大量粒子分层撞击金属表面进行了有限元模拟.Frija和Hassine〔8〕等于2006年也进行了喷丸的有限元模拟,对喷丸引起的压缩残余应力、塑性变形及表面的完整性进行了预测.以上数值模拟过程都是弹丸撞击试件后又反弹回去,速度相对较小.本文应用LS-DYNA动力学分析软件对陶瓷颗粒高速撞击并镶嵌到316L不锈钢板表面的过程进行了数值模拟,研究了颗粒撞击并嵌入过程中不锈钢板的应力、应变、位移随时间及位置的变化规律,其目的在于为以后的实验提供一定的参数依据,并对实验结果进行验证.1 有限元模拟 利用ANSYS10.0前处理器建立如图1所示的三维有限元模型.由于粒子和靶板均是轴对称结构,收稿日期:2008-03-11基金项目:国家自然科学基金资助项目(10662005)作者简介:杨诗婷(1981~),女,硕士研究生.为了计算方便并节省机时,在分析过程中采用四分之一模型进行计算.本文模拟过程中,粒子材料取为陶瓷,靶板材料取为316L 不锈钢.忽略空气和温度场的影响.靶板远端受到弹丸的作用很小,可认为靶板为无限域.陶瓷颗粒半径为2mm ,316L 不锈钢板的长取为16m m 、宽取为16m m 、高取为12mm.颗粒垂直撞击不锈钢板并最终镶嵌在钢板表面.约束钢板底面的所有自由度. 颗粒和靶板均采用由8节点构成的so lid 164三维实体单元进行离散,并采用单点积分的Lagrange 算法.不锈钢板材料的本构关系采用双线性各向同性模型,其密度为7.98g/cm 3,弹性模量为196GPa,屈服极限为280M Pa .而陶瓷颗粒假定为刚性材料模型,其密度为3.27g /cm 3.考虑到计算的精确性并节省计算时间,划分网格时对靶板的不同区域采用不同的网格密度,公法线周围接触区域的网格划分较密,远离接触区域的网格划分相对较疏(如图1所示).颗粒嵌入钢板表面的过程属于侵彻接触,接触发生在弹丸和钢板的表面,所以采用了LS-DYNA 提供的“面-面”侵蚀(ESTS )接触算法.采用M ises 屈服条件来描述靶板材料的破坏.2 计算结果和讨论图1 三维有限元模型 利用Ls-prepo st 后处理器对求解结果进行处理,得到碰撞过程中各时刻的力学参数.图2所示陶瓷颗粒镶嵌过程中三维模型计算结果不同时刻的中心剖面图,颗粒从初始时刻到最终镶嵌在钢板表面共用时间为0.01ms.由于在计算过程中假设陶瓷颗粒为刚体,故颗粒没有变形或碎裂.而且模拟过程中没有考虑摩擦和温度场的影响,即颗粒在初始时刻所具有的机械能最终都转换成钢板的变形能.图2(a )为0.008ms 时颗粒嵌入钢板的位置,图2(b )为颗粒最终嵌入钢板后所在位置.两图相比可知,图(a)中颗粒嵌入深度比图(b)中颗粒嵌入深度稍大,也就是说颗粒嵌入深度达到最大以后又有微小的反弹.这是因为颗粒在镶嵌过程中,钢板初始时发生弹性变形,随着颗粒的不断嵌入使钢板进入弹塑性阶段,当颗粒嵌入深度达到最大值时,弹性变形部分趋于恢复其原始尺寸,而塑性变形将抵制这种恢复,最后使钢板的变形达到一个平衡位置.(a )T =0.008ms(b )T =0.01ms图2 不同时刻颗粒镶嵌的中心剖面图 图3(a)为颗粒最终嵌入钢板后的俯视网格图,图3(b)给出了图3(a)中标注的A 、B 、C 、D 、E 、F 、G 、H 、I 、J 、K 、L 、M 、N 十四个单元的X 坐标与对应单元等效应变之间的关系;图3(c)给出了图3(a)中标注的A 、B 、C 、D 、E 、F 、G 、H 、I 、J 、K 、L 、M 、N 十四个单元的X 坐标与对应单元等效应力之间的关系.由图可看出,在距离颗粒越近的地方,等效应变和等效应力越大,随着距离的增加等效应变和等效应力开始逐渐减小,在距离颗粒大约5mm 的地方钢板的等效应变几乎为零.可见在远离颗粒的地方钢板受颗粒的作用非常小.而且,在等效应变趋于零的地方,单元的等效应力也趋于钢板的屈服极限,这与理论分析相符.图(d)给出了图(a)中标注的A 、B 、C 、D 、E 、F 、G 、H 、I 、J 、K 、L 、M 、N 十四个单元的等效应力随时间的变化规律.图中显示,在大约0.007ms 时,各单元的等效应力开始增加,在约0.008ms 时,大部分单元的246内蒙古工业大学学报2008年等效应力达到最大,并达到了316L 不锈钢板的屈服极限.(a )颗粒最终嵌入钢板后的俯视网格图 (b )颗粒最终嵌入钢板后不同单元x坐标与对应等效应变之间的关系(c)颗粒最终嵌入钢板后不同单元x 坐标与对应等效应力之间的关系 (d)不同单元等效应力随时间的变化规律图3 图4为颗粒嵌入钢板后不同节点坐标与对应节点在X 方向产生位移之间的关系.由图可知,距离颗粒越近的节点产生的位移越大,变化规律成逐渐递减的趋势.在距离颗粒大约4.8mm 处节点位移趋近于零.可以推断,当半径为2mm 的颗粒撞击并嵌入钢板表面时,对钢板的作用范围半径大约是6.8mm ,是颗粒大小的约3.4倍. 图5给出了颗粒在嵌入钢板表面之后v onmises 应力的等值面图.图(a)为vo n m ises 应力等值面图的俯视图.由图可以看出,应力波在图4 颗粒嵌入钢板后不同节点坐标与对应位移之间的关系XOZ 平面内对称向四周扩展.与颗粒接触的中心位置处von m ises 屈服应力最大,随着应力波的逐渐向外扩展,应力值逐渐减小.在单元9575上,屈服应力达到最大值,为297.564MPa .图(b )为von m ises 应力等值面图的中心剖面图.在XOY 平面内,应力波从接触面开始沿Y 轴负方向逐渐向下扩展,对应的应力值也逐渐减小.316L 不锈钢的屈服极限为280MPa ,所以,颗粒冲击时接触区域的最大v on mises 应力已经超过了不锈钢的屈服应力,此处钢处于高度屈服状态.这些结论与理论分析相吻合. 本文对颗粒与靶板相距5mm 时,颗粒嵌入靶板的过程进行了反复的模拟,并给出了颗粒速度和颗粒的嵌入深度之间的关系,如图6所示.图中显示,颗粒嵌入金属表面的速度的范围约为580m /s ~600m /s .速度小于580m /s 时,颗粒将反弹回去;速度大于600m /s 时,颗粒将嵌入钢板内部或穿透钢板.而且,颗粒的大小不同,速度的变化范围也不同.247第4期杨诗婷,邢永明 颗粒高速撞击并嵌入金属表面的三维动力学有限元模拟(a )vo n mises 应力俯视等值面图(单位:M Pa ) (b )vo n mises 应力中心剖面图(单位:M Pa )图53 结 论 通过非线性动力学有限元软件LS-DYN A 对陶瓷颗粒撞击并嵌入316L 不锈钢板的过程进行了有限元模拟.得到如下结论:3.1 颗粒撞击并嵌入不锈钢表面的过程中,开始时钢板发生弹性变形,随着颗粒的不断嵌入,钢板进入弹塑性变形阶段,在某一时刻,钢板的变形达到最大.随着时间的推移,钢板的一部分弹性变形趋于恢复,最终达到一个平衡位置.图6 颗粒速度和嵌入深度之间的关系3.2 颗粒最终嵌入不锈钢表面以后,与颗粒接触的位置,其等效塑性应变、位移和等效应力都达到最大值.随着与粒子之间的距离的增大,这些值均逐渐减小,最后等效塑性应变和位移均趋于零,而等效应力逐渐趋于316L 不锈钢的屈服极限.同时,与颗粒首先接触的单元,最先发生塑性变形.3.3 当颗粒与靶板相距5mm 处,速度大约为580m /s ~600m/s 时,颗粒恰好可以嵌入金属表面;速度小于580m /s 时,颗粒将反弹回去;速度大于600m /s 时,颗粒将穿透钢板.颗粒的大小不同,速度的变化范围也不同.参考文献:[1] 栾伟玲,涂善东.喷丸表面改性技术的研究进展[J].中国机械工程.2005,16(15):1405~1409.[2] W .Johnson .Impa ct Streng th of M at erials [M ].L ondo n :A rno ld ,1972.[3] R.Clausen.Er mit tlung V on Einflussgr ossen Beim K ug elst ralen D ur ch Einzelko rnv ersuche [C].Par is:1st I nt.Co nf.on Shot -Peening ,1981.279~285.[4] K .Iida ,Dent and A ffected L ayer P ro duced by Shot Peening [C ].Chicag o ,U SA :2nd Int .Conf .on Shot Peening ,1984.217~227.[5] J.Edberg ,L.L indgr en,K.M or i.Shot P eening Simulat ed by T w o D iffer ent Finite Element Fo rmulatio ns [C].Balkema ,Ro tter dam :in :Shen ,Da wson (Eds .),Simulation o f M at eria ls P ro cessing :T heor y ,M et ho ds and A pplications,1995.425~430.[6] S.A.M eg uid,G.Shag al,J.C.St ranar t,ed al.T hree-dim ensio nal D ynamic F inite Element A na ly sis of Shot -peening I nduced Residual St resses [J ].Finit e Element in A nalysis and Design .1999,31,179~191.[7] S.A.M eguid *,G.Shag al,J.C.St ranar t.3D F E Analysis of Peening o f Strain-r ate Sensitive M ater ialsusingM ultiple Impingement M odel [J].Inter natio nal Jour nal o f Impact Eng ineer ing.2002,27,119~134.248内蒙古工业大学学报2008年[8] M.Fr ija,T .Hassine,R.Fathallah,C.Bo ur ao ui,A.Do gui b,L abor atoire de G ′enie M ′ecanique.F inite ElementM odelling o f Shot Peening Pr ocess:Pr edictio n o f t he Co mpr essive Residual Str esses,T he Plastic Defo rmations and t he Sur face Int egr ity [J].M ater ials Science and Eng ineer ing A.2006,426,173~180.T HREE-DIM ENSIO N A L DY N A M IC SIM U L A T IONO F HIG H SPEED PA RT ICL E IM PACT AN D IN LA YON M ET A L SU RFA CE BY U SE OF FIN IT E EL EM ENT M ET HODYANG Shi-ting,XIN G Yong -ming(School of S cience ,I nner Mongolia Univer sity o f Technology ,H ohhot 010051,China ) Abstract :The hig h speed impact and inlay process o f particle is a high no n -linear pro blem .T he num erical sim ulation of the process pro vides a valid solution to it.In this paper,an introductio n is made to the simulation of the high speed impact and inlay pr ocess of ceram ic particle on the surface of 316L stainless steel by use o f LS -DYNA three -dim ensional dy namic finite elem ent code .T he interaction process of hig h speed impact and inlay of particle can be directly analy zed.Variation of stress,str ain and displacem ent o f stainless steel plate with time and position during the particle inlay can be studied.Results show that,w hen particle impact and inlay take place on the targ et,its max imum yield str ess ,m aximum effective plastic strain and max imum displacem ent ar e all found in the place w her e particle is bro ug ht into co ntact w ith the target.Within the rang e of particle function,the far ther the position is from the par ticle,the smaller the yield stress,effective plastic strain and displacem ent w ill be .Keywords :impact and penetration ;numerical sim ulation ;finite element ;LS -DYN A 249第4期杨诗婷,邢永明 颗粒高速撞击并嵌入金属表面的三维动力学有限元模拟。
冲击载荷下颗粒碰撞的SPH法数值模拟
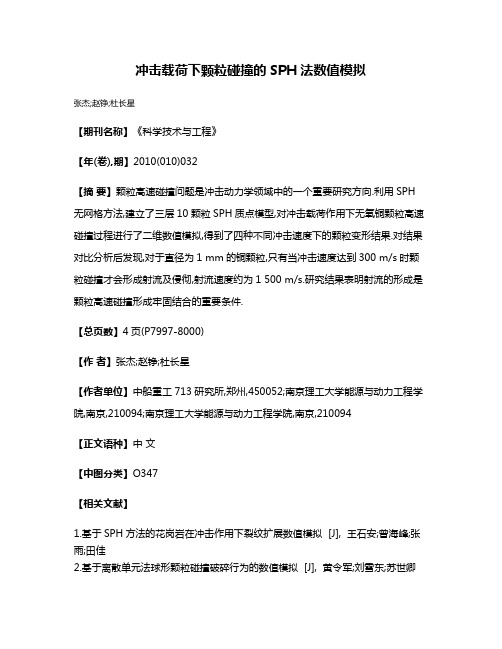
冲击载荷下颗粒碰撞的SPH法数值模拟
张杰;赵铮;杜长星
【期刊名称】《科学技术与工程》
【年(卷),期】2010(010)032
【摘要】颗粒高速碰撞问题是冲击动力学领域中的一个重要研究方向.利用SPH 无网格方法,建立了三层10颗粒SPH质点模型,对冲击载荷作用下无氧铜颗粒高速碰撞过程进行了二维数值模拟,得到了四种不同冲击速度下的颗粒变形结果.对结果对比分析后发现,对于直径为1 mm的铜颗粒,只有当冲击速度达到300 m/s时颗粒碰撞才会形成射流及侵彻,射流速度约为1 500 m/s.研究结果表明射流的形成是颗粒高速碰撞形成牢固结合的重要条件.
【总页数】4页(P7997-8000)
【作者】张杰;赵铮;杜长星
【作者单位】中船重工713研究所,郑州,450052;南京理工大学能源与动力工程学院,南京,210094;南京理工大学能源与动力工程学院,南京,210094
【正文语种】中文
【中图分类】O347
【相关文献】
1.基于SPH方法的花岗岩在冲击作用下裂纹扩展数值模拟 [J], 王石安;曾海峰;张雨;田佳
2.基于离散单元法球形颗粒碰撞破碎行为的数值模拟 [J], 黄令军;刘雪东;苏世卿
3.基于SPH法的冰与船舶螺旋桨碰撞数值模拟 [J], 桂洪斌;胡志宽
4.爆炸压实过程中颗粒碰撞问题的SPH法数值模拟 [J], 赵铮;李晓杰;闫鸿浩;欧阳欣
5.高冲击载荷作用下平面式电涡流阻尼器特性数值模拟研究 [J], 黄通;高钦和;刘志浩;刘大伟
因版权原因,仅展示原文概要,查看原文内容请购买。
- 1、下载文档前请自行甄别文档内容的完整性,平台不提供额外的编辑、内容补充、找答案等附加服务。
- 2、"仅部分预览"的文档,不可在线预览部分如存在完整性等问题,可反馈申请退款(可完整预览的文档不适用该条件!)。
- 3、如文档侵犯您的权益,请联系客服反馈,我们会尽快为您处理(人工客服工作时间:9:00-18:30)。
游移动,在下游区域形成了较大的椭圆形颗粒轮廓。
不过可以看出,此时扩散出去的颗粒个数是较少的,火部分颗粒直接穿过涡核区向下游运动,所以颗粒发生碰撞的位置主要集中在射流中心颗粒比较集中的区域,如图2(c),(d)所示。
图2不同时刻颗粒碰撞在射流流场中的空间分布
(a)t=18(b)t=26(c)t=50(d)t=66
妊
懿
譬
捌
崔
耀
酲
岳
喀
堪
图3网格q,最大的颗粒个数和流场中颗粒碰撞的次数随时问的发展
(a)网格巾最大的颗粒个数的发展(b)流场中颗粒碰撞次数的发展
3.2颗粒碰撞的次数
为了考察碰撞随时问的演化,图3给山了网格中最大的颗粒个数和流场中颗粒碰撞的
259。