影响耐火材料烧结的因素
2021耐火材料知识竞赛真题模拟及答案(4)

2021耐火材料知识竞赛真题模拟及答案(4)1、耐火制品的形状正确与否,尺寸是否符合要求,直接影响筑炉施工质量和窑炉及其他设备的()(单选题)A. 热震稳定性B. 使用寿命C. 高温使用试题答案:B2、摩擦压砖机的工作装置主要有两部分:一是垂直安装的(),另一个是人工操纵杆,通过杠杆制动,将力传递到拨杈,迫使轴承连同摩擦轮一起左右移动,来改换飞轮的旋转方向,从而使螺杆向上或向下移动,完成冲压动作。
(单选题)A. 摩擦轮B. 液压轮C. 杠杆试题答案:A3、下列人员中为服务人员的是()。
(单选题)A. 搬运工B. 描图员C. 中式烹调师D. 清砂工试题答案:C4、试卷的整体构成与试卷的选择是按照以()为基础的试卷模板来确定的。
(多选题)A. 考核目标要求B. 鉴定要素和组卷模型C. 试题特征D. 实际考核需要试题答案:C,D5、在考评方法中,当前我国职业技能鉴定考核中采用最普遍的最经济的方法是()。
(单选题)A. 模拟操作法B. 现场实际操作法C. 阅卷法D. 典型作业法试题答案:D6、安全生产管理指标应细化和分解到()。
(单选题)A. 各部门和船舶B. 各岗位C. 各部门、船舶和岗位试题答案:C7、()是鉴定要素最小不可测量单位。
(单选题)A. 鉴定内容B. 鉴定操作题C. 鉴定知识D. 鉴定点试题答案:D8、耐火材料的成型方法除常见的方法外还有热压成型、热压铸成型和()等。
(单选题)A. 等静压成型B. 震动成型C. 机压成型9、推行职业资格证书制度必须坚持()基本原则。
(单选题)A. 社会效益第一、质量第一B. 经济效益和社会效益优先C. 社会效益优先,经济效益兼顾D. 质量第一,经济社会效益并存试题答案:A10、考评组长应具有()以上的职业技能鉴定工作经验。
(单选题)A. 一年B. 两年C. 三年D. 四年试题答案:B11、理论知识试题利用层次属性编制的优点有()。
(多选题)A. 使试题的编写更加规范B. 使试题的编写易于统一C. 使试题的内容测量更统一D. 使试题的编写易于操作试题答案:A,B,C12、考评机构应组织()名以上具有相应资质的考评人员成立考评组。
耐火材料的烧结
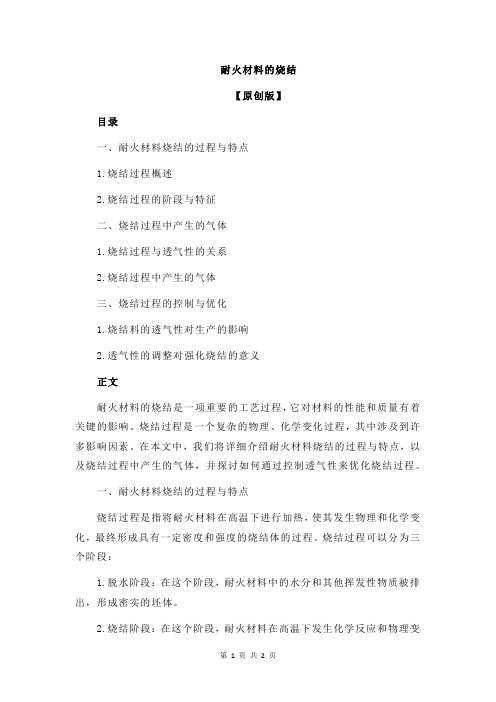
耐火材料的烧结【原创版】目录一、耐火材料烧结的过程与特点1.烧结过程概述2.烧结过程的阶段与特征二、烧结过程中产生的气体1.烧结过程与透气性的关系2.烧结过程中产生的气体三、烧结过程的控制与优化1.烧结料的透气性对生产的影响2.透气性的调整对强化烧结的意义正文耐火材料的烧结是一项重要的工艺过程,它对材料的性能和质量有着关键的影响。
烧结过程是一个复杂的物理、化学变化过程,其中涉及到许多影响因素。
在本文中,我们将详细介绍耐火材料烧结的过程与特点,以及烧结过程中产生的气体,并探讨如何通过控制透气性来优化烧结过程。
一、耐火材料烧结的过程与特点烧结过程是指将耐火材料在高温下进行加热,使其发生物理和化学变化,最终形成具有一定密度和强度的烧结体的过程。
烧结过程可以分为三个阶段:1.脱水阶段:在这个阶段,耐火材料中的水分和其他挥发性物质被排出,形成密实的坯体。
2.烧结阶段:在这个阶段,耐火材料在高温下发生化学反应和物理变化,形成具有一定强度和密度的烧结体。
3.冷却阶段:在这个阶段,烧结体逐渐冷却至室温,使其结构和性能得到稳定。
二、烧结过程中产生的气体烧结过程中,由于耐火材料的物理和化学变化,会产生一定量的气体。
这些气体主要包括:水蒸气、二氧化碳、一氧化碳、氮氧化物等。
其中,水蒸气是烧结过程中最主要的气体,其产生量与材料的含水量、烧结温度和烧结时间等因素有关。
烧结过程与透气性密切相关。
透气性好坏决定了烧结过程的顺利进行,并影响烧结矿产量和质量。
因此,在烧结生产控制中,需要密切关注透气性的变化,并根据实际情况进行调整。
三、烧结过程的控制与优化为了提高烧结过程的产量和质量,需要对烧结过程进行严格的控制和优化。
其中,最关键的是控制烧结料的透气性。
透气性是指烧结料在高温下的气体通量。
良好的透气性有利于烧结过程中气体的排出,有利于提高烧结矿的产量和质量。
为了优化烧结过程,可以采取以下措施:1.选择合适的原料和配比,以提高烧结料的透气性。
第六章烧结(1)详解
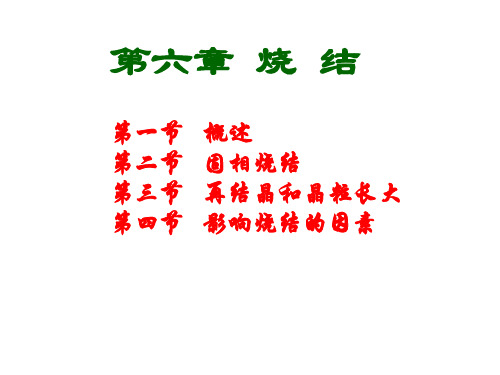
2. 烧结过程的模型示意图 根据烧结性质随温度的变化,我们可以把
烧结过程用图2的模型来表示,以增强我们对 烧结过程的感性认识。
第六章 烧 结
第一节 概述 第二节 固相烧结 第三节 再结晶和晶粒长大 第四节 影响烧结的因素
1.1 概述
烧结过程是一门古老的工艺。现在,烧 结过程在许多工业部门得到广泛应用,如陶瓷、 耐火材料、粉末冶金、超高温材料等生产过程 中都含有烧结过程。
烧结的目的是把粉状材料转变为致密体。
材料的性能不仅与材料的组成有关,还与 材料的显微结构有密切关系,而烧结过程直接 影响材料的显微结构,如材料的晶粒尺寸和分 布,气孔尺寸及分布等。因此,了解粉末坯体 烧结过程的现象和机理,了解烧结动力学及其 影响因素对控制和改进材料的性能有着十分重 要的实际意义。
初期
中期
末期
图2 粉状成型体的烧结过程示意图
根据上面讨论,烧结过程可以分为三个阶段:烧结初 期、中期和后期。
烧结初期:
坯体中颗粒重排,接触处产生键合,空隙变形、缩小 (即大气孔消失),气孔的总体积迅速减小,但颗粒 之间仍以点接触为主,固-气总表面积没有变化。 烧结中期:
传质开始,粒界增大(颗粒间由点接触逐渐扩大为面接 触),空隙进一步变形、缩小,但仍然连通,形如隧道。 烧结后期:
模型中是两个等径球体,随之烧结的进 行,质点通过传质等过程,各接触点开始形 成颈部,并逐渐扩大,最后烧结成一个整体, 由于各颈部所处的环境和几何条件相同,所 以只需确定两个颗粒形成颈部的成长速率就 基本代表了整个烧结初期的动力学关系。
材料科学基础--第九章-烧结

中心距L缩短 坯体收缩
适用: 蒸发-凝聚传质
扩散传质
球体-平板模型
扩散传质
烧结会引起体积的收缩和致密度增加,常用线收缩率或密度值来评
价烧结的程度。对模型(B),烧结收缩是因颈部长大,两球心距离 缩短所引起的。故可用球心距离的缩短率 L 来表示线收缩率(L0烧结前两球心距离,L-烧结后缩短值): L0
烧结后期:传质继续进行,粒子长大,气孔变成孤立闭气孔,密 度达到95%以上,制品强度提高。
(二)烧结推动力
能量差(具体表现为:压力差、空位浓度差、溶解度差)
1、能量差 粉状物料的表面能大于多晶烧结体的晶界能,即能量差是烧结的 推动力,但较小。烧结不能自发进行,必须对粉料加以高温,才 能促使粉末体转变为烧结体
2、颈部空位浓度分析
1)无应力区(晶体内部)的空位浓度:
c0
n0 N
exp
EV kT
2)应力区的空位浓度:
受压应力时,形成体积为Ω空位所做的附加功为:
En
受张应力时,形成体积为Ω空位所做的附加功为:
Et
所以,在接触点或颈部区域形成一个空位所做的功为:
3)温度的影响
T↑,D*=D0exp(-Q/RT)↑↑, x/r、△L/L↑↑。
温度升高,加快烧结。温度在烧 结中往往起决定性作用。
在扩散为主的烧结中,除体积扩
散外,质点还可以沿表面、界面或
位错等处进行多种途径的扩散。库
津斯基综合各种烧结过程,得出烧
结动力学典型方程为:
( x)n r
F(T ) rm
多相反应和熔融、溶解、烧结等,其包括范围较宽。 烧结:仅是粉料经加热而致密化的简单过程,是烧成过程的一个
耐火材料复习题
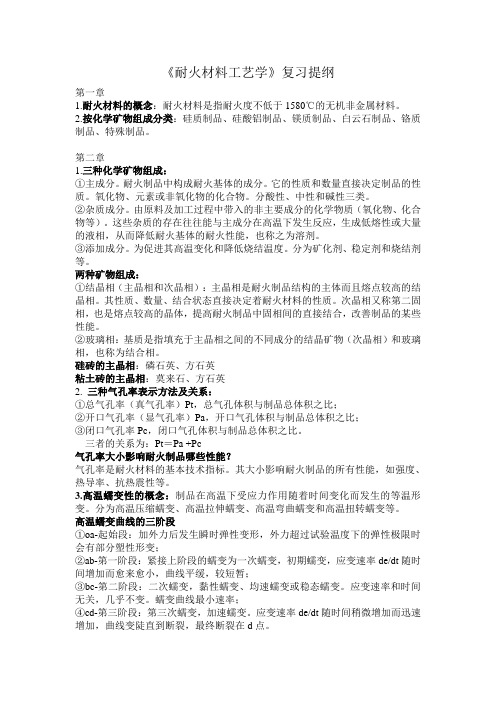
《耐火材料工艺学》复习提纲第一章1.耐火材料的概念:耐火材料是指耐火度不低于1580℃的无机非金属材料。
2.按化学矿物组成分类:硅质制品、硅酸铝制品、镁质制品、白云石制品、铬质制品、特殊制品。
第二章1.三种化学矿物组成:①主成分。
耐火制品中构成耐火基体的成分。
它的性质和数量直接决定制品的性质。
氧化物、元素或非氧化物的化合物。
分酸性、中性和碱性三类。
②杂质成分。
由原料及加工过程中带入的非主要成分的化学物质(氧化物、化合物等)。
这些杂质的存在往往能与主成分在高温下发生反应,生成低熔性或大量的液相,从而降低耐火基体的耐火性能,也称之为溶剂。
③添加成分。
为促进其高温变化和降低烧结温度。
分为矿化剂、稳定剂和烧结剂等。
两种矿物组成:①结晶相(主晶相和次晶相):主晶相是耐火制品结构的主体而且熔点较高的结晶相。
其性质、数量、结合状态直接决定着耐火材料的性质。
次晶相又称第二固相,也是熔点较高的晶体,提高耐火制品中固相间的直接结合,改善制品的某些性能。
②玻璃相:基质是指填充于主晶相之间的不同成分的结晶矿物(次晶相)和玻璃相,也称为结合相。
硅砖的主晶相:磷石英、方石英粘土砖的主晶相:莫来石、方石英2.三种气孔率表示方法及关系:①总气孔率(真气孔率)Pt,总气孔体积与制品总体积之比;②开口气孔率(显气孔率)Pa,开口气孔体积与制品总体积之比;③闭口气孔率Pc,闭口气孔体积与制品总体积之比。
三者的关系为:Pt=Pa +Pc气孔率大小影响耐火制品哪些性能?气孔率是耐火材料的基本技术指标。
其大小影响耐火制品的所有性能,如强度、热导率、抗热震性等。
3.高温蠕变性的概念:制品在高温下受应力作用随着时间变化而发生的等温形变。
分为高温压缩蠕变、高温拉伸蠕变、高温弯曲蠕变和高温扭转蠕变等。
高温蠕变曲线的三阶段①oa-起始段:加外力后发生瞬时弹性变形,外力超过试验温度下的弹性极限时会有部分塑性形变;②ab-第一阶段:紧接上阶段的蠕变为一次蠕变,初期蠕变,应变速率de/dt随时间增加而愈来愈小,曲线平缓,较短暂;③bc-第二阶段:二次蠕变,黏性蠕变、均速蠕变或稳态蠕变。
陶瓷材料的烧结与晶粒生长
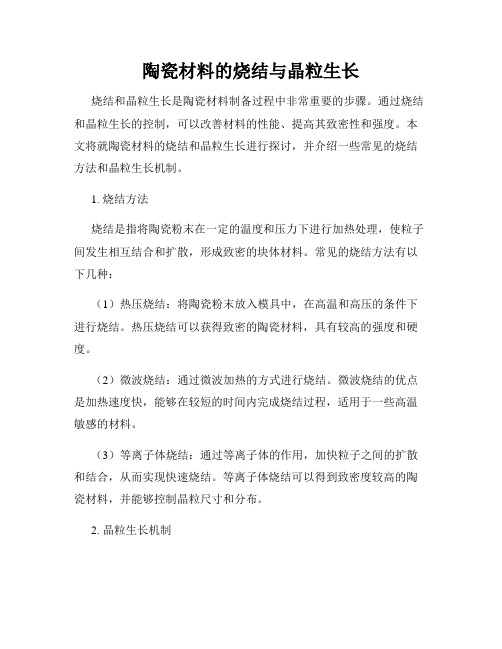
陶瓷材料的烧结与晶粒生长烧结和晶粒生长是陶瓷材料制备过程中非常重要的步骤。
通过烧结和晶粒生长的控制,可以改善材料的性能、提高其致密性和强度。
本文将就陶瓷材料的烧结和晶粒生长进行探讨,并介绍一些常见的烧结方法和晶粒生长机制。
1. 烧结方法烧结是指将陶瓷粉末在一定的温度和压力下进行加热处理,使粒子间发生相互结合和扩散,形成致密的块体材料。
常见的烧结方法有以下几种:(1)热压烧结:将陶瓷粉末放入模具中,在高温和高压的条件下进行烧结。
热压烧结可以获得致密的陶瓷材料,具有较高的强度和硬度。
(2)微波烧结:通过微波加热的方式进行烧结。
微波烧结的优点是加热速度快,能够在较短的时间内完成烧结过程,适用于一些高温敏感的材料。
(3)等离子体烧结:通过等离子体的作用,加快粒子之间的扩散和结合,从而实现快速烧结。
等离子体烧结可以得到致密度较高的陶瓷材料,并能够控制晶粒尺寸和分布。
2. 晶粒生长机制晶粒生长是指陶瓷材料在烧结过程中晶粒尺寸的增大。
晶粒尺寸的大小和分布对陶瓷材料的性能有着重要的影响。
常见的晶粒生长机制包括以下几种:(1)一维生长:晶粒沿着某个方向生长,呈现出棒状或柱状的形态。
一维生长机制适用于一些具有纤维状结构的陶瓷材料。
(2)表面扩散:晶粒表面发生扩散,并与周围的颗粒结合。
表面扩散是晶粒生长的主要机制之一,通过控制晶粒表面的扩散速率,可以调控晶粒尺寸和形态。
(3)体内扩散:晶粒内部的原子通过扩散运动,使晶粒尺寸增大。
体内扩散主要取决于材料的化学成分和温度条件。
3. 影响烧结和晶粒生长的因素烧结和晶粒生长受到多种因素的影响,下面介绍其中几个重要的因素:(1)温度:温度是烧结和晶粒生长的关键因素之一。
适当的温度可以促进晶粒的结合和生长,但过高的温度可能引起过烧,导致晶粒长大过快。
(2)压力:压力可以提高粒子的结合程度和致密性,对烧结效果有重要影响。
不同材料和形状的陶瓷,适宜的压力范围也有所不同。
(3)时间:烧结时间影响烧结程度和晶粒生长的速率。
影响氧化铝陶瓷烧结的因素分析

19影响氧化铝陶瓷烧结的因素分析刘国祥(214221江苏省陶瓷研究所7401314)摘要阐述了氧化铝陶瓷的烧结机理,分析了烧成气氛、物料分散度及添加熔剂等因素对氧化铝制品烧结程度的影响,总结出理想的升温制度、保温时间、绘制烧成曲线。
关键词氧化铝陶瓷烧结机理影响因素烧成制度1前言进入“九五”以来,工业特种陶瓷得到了迅猛发展。
其中氧化铝陶瓷以其优良的特性如耐酸碱性、耐磨性、耐电性、机械强度高等,在工业化生产中得到了广泛的应用。
因此,深入研究氧化铝陶瓷的生产技术及其发展,服务于生产和社会需要就显得相当重要。
在氧化铝陶瓷的生产过程中,无论是原料制备、成型、烧结还是冷加工,每个环节都是不容忽视的。
坯体烧结后,制品的显微结构及其内在性能发生了根本的改变,很难通过其它办法进行补救。
因此,深入研究氧化铝陶瓷的烧结技术,合理选择理想的烧结制度确保产品的性能,对氧化铝陶瓷生产极有帮助。
2烧结机理烧结是指坯体由低温到高温发生一系列的物理化学反应,从而得到致密的、坚硬的制品的过程。
其中物理化学变化包含坯体中残余的拌料水分的排溢、物料中化合物结合水和有机物的分解排除、Al2O3同质异晶的晶型转变以及固态物质颗粒间直接进行反应———固相反应等。
固相反应在氧化铝陶瓷烧结中占有极为重要的位置,它实质上是通过物质质点的迁移扩散作用而进行的,随着温度的升高,晶体的热缺陷不断增加,质点迁移扩散由内扩散形式到外扩散,并更加充分,从而发生反应,产生新的物质(见图1)。
如图1所示,假定颗粒是圆的,温度升高,颗粒界面相互融合,形成勃颈并不断扩大,颗粒径距缩短,气孔变小并逐渐排除,晶粒长大,体积收缩,最后形成致密体。
从以上的分析可以看出,固相反应的关键是迁移,提高质点的迁移速度和效率,就能有效地促进烧结和致密过程;反之,就起阻碍作用。
3影响烧结性能的因素影响氧化铝陶瓷烧结程度的因素较多,主要表现为以下几点:3.1晶体的结构化学键强的化合物(晶体)具有较高的晶格能量,晶格结构牢固:即使在较高温度下,质点的振动迁移也较弱。
烧结内容提要本章叙述了烧结定义推动力和基本模型分析
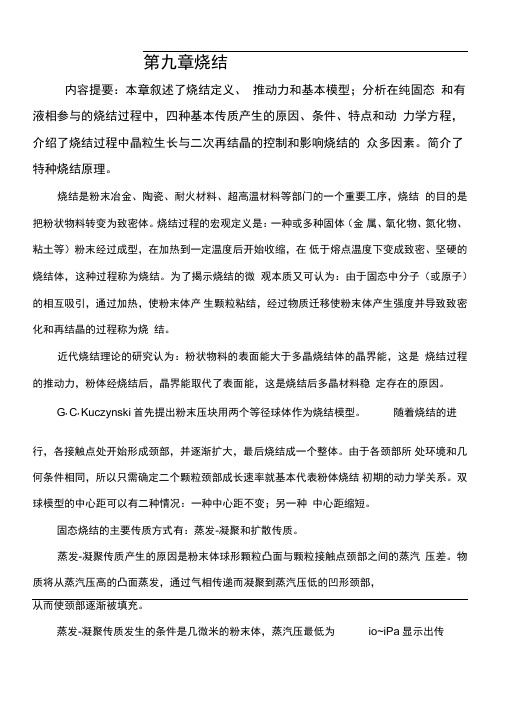
第九章烧结内容提要:本章叙述了烧结定义、推动力和基本模型;分析在纯固态和有液相参与的烧结过程中,四种基本传质产生的原因、条件、特点和动力学方程,介绍了烧结过程中晶粒生长与二次再结晶的控制和影响烧结的众多因素。
简介了特种烧结原理。
烧结是粉末冶金、陶瓷、耐火材料、超高温材料等部门的一个重要工序,烧结的目的是把粉状物料转变为致密体。
烧结过程的宏观定义是:一种或多种固体(金属、氧化物、氮化物、粘土等)粉末经过成型,在加热到一定温度后开始收缩,在低于熔点温度下变成致密、坚硬的烧结体,这种过程称为烧结。
为了揭示烧结的微观本质又可认为:由于固态中分子(或原子)的相互吸引,通过加热,使粉末体产生颗粒粘结,经过物质迁移使粉末体产生强度并导致致密化和再结晶的过程称为烧结。
近代烧结理论的研究认为:粉状物料的表面能大于多晶烧结体的晶界能,这是烧结过程的推动力,粉体经烧结后,晶界能取代了表面能,这是烧结后多晶材料稳定存在的原因。
G• C• Kuczynski首先提出粉末压块用两个等径球体作为烧结模型。
随着烧结的进行,各接触点处开始形成颈部,并逐渐扩大,最后烧结成一个整体。
由于各颈部所处环境和几何条件相同,所以只需确定二个颗粒颈部成长速率就基本代表粉体烧结初期的动力学关系。
双球模型的中心距可以有二种情况:一种中心距不变;另一种中心距缩短。
固态烧结的主要传质方式有:蒸发-凝聚和扩散传质。
蒸发-凝聚传质产生的原因是粉末体球形颗粒凸面与颗粒接触点颈部之间的蒸汽压差。
物质将从蒸汽压高的凸面蒸发,通过气相传递而凝聚到蒸汽压低的凹形颈部,从而使颈部逐渐被填充。
蒸发-凝聚传质发生的条件是几微米的粉末体,蒸汽压最低为io~iPa显示出传质效果。
这种传质的特点是烧结时颈部扩大,气孔形状改变,但双球之间中心距不变,因此由蒸发-凝聚单一传质发生烧结,坯体不发生收缩,即「丄L = 0。
扩散传质是大多数固体材料烧结传质的主要形式。
产生扩散传质的原因是颗粒不同部位空位浓度差。
烧结剂对耐火材料的影响

水玻璃结合剂(water glass binder)一种无机材料的胶结剂。
又称泡花碱。
在工业上呗广泛用作无机材料胶结剂,在耐火材料工业作为结合剂用相当广泛,也广泛用于造纸及纺织等工业。
添加剂对耐火材料烧结的影响在固相烧结时,少量的添加剂(烧结助剂)可与主晶相形成固溶体促进缺陷增加;在液相烧结时,添加剂能够改变液相的性质(如粘度、组成等),因而能起促进烧结的作用。
添加剂的作用可能在于以下几个方面。
形成固溶体。
当添加物与烧结物形成固溶体时,可以增加晶格缺陷,活化晶格,从而促进烧结。
一般来说,他们之间形成有限置换固溶体更有助于促进烧结。
添加剂离子的电价、半径与主晶格离子的电价、半径相差越大,晶格畸变程序也越大,促进烧结的作用也越明显。
如Al2O3烧结时,加入3%的Cr2O3形成连续固溶体可在1860℃烧结,而加入1%~2%只需在1600℃左右就能致密化。
阻止晶型转变。
有些氧化物在烧结时发生晶型转变并伴有较大的体积效应,这就难以实现烧结致密化,并容易引起坯体开裂。
这时若能选用适宜的添加剂加以抑制,即可促进烧结。
ZrO2烧结时添加一定量的CaO、MgO就属这一机理。
约在1200℃,m- ZrO2转变为t- ZrO2,并伴有约10%的体积收缩,使制品稳定性变坏。
引入电价比Zr4+低的Ca2+(或Mg2+),可形成稳定的立方萤石结构的固溶体。
这样,既防止了制品的开裂,又增加了晶体中缺陷浓度,使烧结加快。
抑制晶粒长大。
烧结后期晶粒长大,对促进烧结致密化有重要作用。
但若二次再结晶或间断性晶粒长大过快,会使晶粒变粗、晶界变宽而出现反致密化现象并影响制品的显微结构。
这时,可通过加入能抑制晶粒异常长大的添加剂来促进烧结。
在烧结透明Al2O3制品时,为抑制二次再结晶,消除晶界上的气孔,一般加入MgO或MgF2,高温下形成镁铝尖晶石包裹在Al2O3晶粒表面,抑制了晶界迁移的速度,并促使气孔的排出,对促进坯体的烧结具有显著的作用。
第三章-耐火材料生产过程
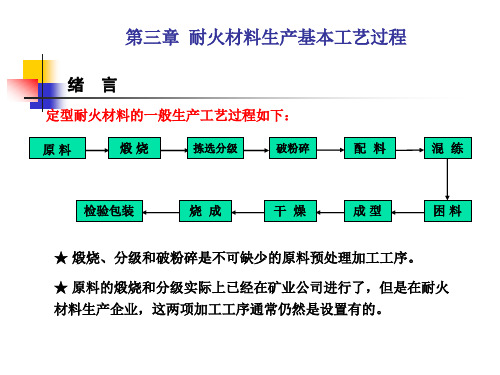
(2)虽然增加颗粒粒度的组份数量有利于提高堆积密度,但当组 份数目超过时,效果不再明显。故在实际生产中,通常采取三组份 颗粒配料,有时也采取四组份颗粒配料。
2. 拣选对象:耐火粘土、高铝矾土、菱镁矿等
方法:根据熟料的外观颜色、有无显而易见的杂质、比重、致密度等 情况进行人工拣选。
三、原料的破粉碎
1. 破粉碎的重要意义
(1)各种原料只有破粉碎到一定细度,才可能充分混合均匀,从而 保证制品组织结构的均匀性。
(2)通过破粉碎将各种原料加工成适当粒度,以保证制品的成型密度。 (3)只有将原料粉碎到一定细度,才能提高原料的反应活性,促进高 温下的固相反应,形成预期的矿物组成和显微组织结构,以及降低烧成 温度。
B P2
C
坯料被进一步压缩,但呈
阶梯式变化——坯料被压
P1
缩到一定程度后,即阻碍
进一步压缩,一旦压力继 续增大到使颗粒再度产生
压缩,mm
变形的外力时,坯料的体积又得以被压缩。这种增压—压缩的
过程短促而频繁,最后,压制过程进入第三阶段。
阶段C: 在极限压力 P2 作用下,坯料不再被压缩,坯体的密度不 再增大。
2. 颗粒组成(颗粒级配)设计 (1)颗粒级配的含义
(2)调配颗粒组成的必要性 保证坯体的成型密度
减小坯体的烧成收缩
保证制品的质量与性能
§3-2 坯料的制备
颗粒组成和制品性质的关系:
(a)—气孔率;(b)—常温耐压强度;(c)—烧成收缩 (d)—透气率;(e)—耐热冲击性
§3-2 坯料的制备
烧结过程概述
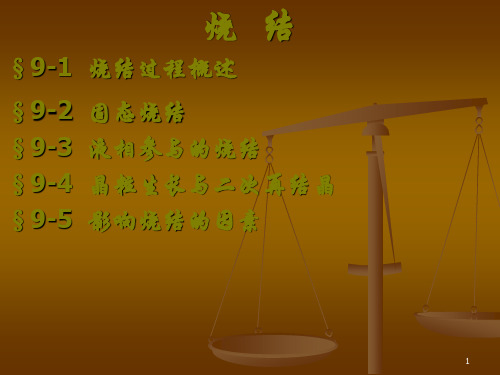
P MP0 dRT
蒸发-凝聚传质的特点: 颈部区域扩大;颗粒形状改变;气孔形状改 变;但颗粒间中心距 不变,即坯体不收缩。
11
二.扩散传质
1.基本原理 颈部应力模型——表明烧结过程推动力如何促使质点在固相中
迁移,(如图) 。
在颈部区取一曲面元ABCD; 颈部中心→颈部表面的曲率半径 为x(正号); 沿颈部表面的曲率半径为ρ(负 号); x与x;ρ与ρ之间的夹角均为θ,( 且θ值很小); 颈部表面横向力Fx,竖向力Fρ;
27
设:圆柱形空隙的长度(十四面体的棱长)为L;
圆柱形空隙的半径r; 十四面体的体积V,气孔体积v;
烧结中期坯体气孔率Pc=v/V ; 烧结时间t;烧结进入中期的时间tf ; 烧结速度公式气孔率Pc与时间t的关系:
Pc
10D* kTL3
(t
f
t)
D*——自扩散系数; ——表面张力; Ω——一个空位的体积; k——波尔兹曼常数。
3
烧结是一个物理过程,没有化学反应发生。随着烧
结过程的完成,坯体表现为体积收缩、气孔率下降、致密、 强度增加、电阻率减小等。
性
气孔
质
率
电 密度 阻
强 度
晶粒尺 寸
温度
图9-2 烧结温度对材料性质的影响
4
3.衡量烧结程度的几个指标
(1)用坯体的收缩率ΔL/L表示; (2)用坯体的气孔率(气孔体积/总体积)表示; (3)用坯体的相对密度(实际密度/理论密度)表示;
4.烧结的分类
(1)从参加烧结的物质状态分: 固相烧结与液相烧结;
(2)从参加烧结的物质有无化学反应发生分: 物理烧结与化学烧结;
耐火材料 烧结的化学原理
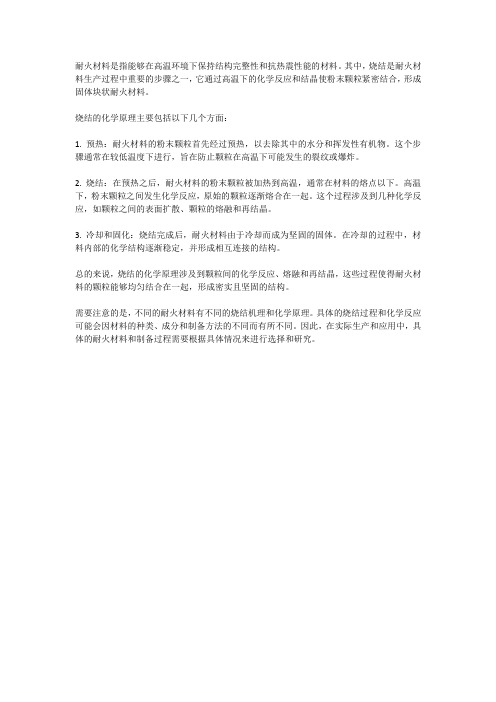
耐火材料是指能够在高温环境下保持结构完整性和抗热震性能的材料。
其中,烧结是耐火材料生产过程中重要的步骤之一,它通过高温下的化学反应和结晶使粉末颗粒紧密结合,形成固体块状耐火材料。
烧结的化学原理主要包括以下几个方面:
1. 预热:耐火材料的粉末颗粒首先经过预热,以去除其中的水分和挥发性有机物。
这个步骤通常在较低温度下进行,旨在防止颗粒在高温下可能发生的裂纹或爆炸。
2. 烧结:在预热之后,耐火材料的粉末颗粒被加热到高温,通常在材料的熔点以下。
高温下,粉末颗粒之间发生化学反应,原始的颗粒逐渐熔合在一起。
这个过程涉及到几种化学反应,如颗粒之间的表面扩散、颗粒的熔融和再结晶。
3. 冷却和固化:烧结完成后,耐火材料由于冷却而成为坚固的固体。
在冷却的过程中,材料内部的化学结构逐渐稳定,并形成相互连接的结构。
总的来说,烧结的化学原理涉及到颗粒间的化学反应、熔融和再结晶,这些过程使得耐火材料的颗粒能够均匀结合在一起,形成密实且坚固的结构。
需要注意的是,不同的耐火材料有不同的烧结机理和化学原理。
具体的烧结过程和化学反应可能会因材料的种类、成分和制备方法的不同而有所不同。
因此,在实际生产和应用中,具体的耐火材料和制备过程需要根据具体情况来进行选择和研究。
烧结的概念——精选推荐

第十二章烧结(Sinter)第一节基本概念一、烧结1、烧结的意义烧结是粉末冶金、陶瓷、耐火材料、超高温材料等部门的一个重要工序。
烧结的目的是把粉状物料转变为致密体。
这种烧结致密体是一种多晶材料,其显微结构由晶体、玻璃相和气孔组成,烧结过程直接影响显微结构中晶粒尺寸和分布,气孔尺寸和分布以及晶界体积分数….。
烧结过程可以通过控制晶界移动而抑制晶粒的异常生长或通过控制表面扩散、晶界扩散和晶格扩散而充填气孔,用改变显微结构方法使材料性能改善。
因此,当配方、原料粒度、成型等工序完成以后,烧结是使材料获得预期的显微结构以使材料性能充分发挥的关键工序。
2、烧结的定义宏观定义:一种或多种固体(金属、氧化物、氮化物等)粉末经过成型,在加热到一定温度后开始收缩,在低于熔点温度下变成致密、坚硬的烧结体,这种过程称为烧结。
微观定义:由于固态中分子(或原子)的相互吸引,通过加热,使粉末体产生颗粒粘结,经过物质迁移使粉末体产生强度并导致致密化和再结晶的过程。
由于烧结体宏观上出现体积收缩,致密度提高和强度增加,因此烧结程度可以用坯体收缩率、气孔率、吸水率或烧结体密度与理论密度之比(相对密度)等指标来衡量。
3、与烧结有关的一些概念A.烧结与烧成(firing):烧成:包括多种物理和化学变化。
例如脱水、坯体内气体分解、多相反应和熔融、溶解、烧结等。
而烧结仅仅指粉料经加热而致密化的简单物理过程,烧结仅仅是烧成过程的一个重要部分。
B.烧结和熔融(Melt):烧结是在远低于固态物质的熔融温度进行的。
泰曼发现烧结温度(T S)和熔融温度(T M)的关系有一定规律:金属粉末 T S=(0.3~0.4)T M盐类 T S=0.57T M硅酸盐 T S=(0.8~0.9)T M烧结和熔融这两个过程都是由原子热振动而引起的,但熔融时全部组元都为液相,而烧结时至少有一组元是处于固态。
C.烧结与固相反应:两个过程均在低于材料熔点或熔融温度之下进行的。
烧结多孔砖耐火极限

烧结多孔砖耐火极限烧结多孔砖是一种常见的耐火材料,其具有优异的耐火性能和良好的保温隔热性能,在冶金、化工、建筑等领域得到广泛的应用。
其中,烧结多孔砖的耐火极限是评价其性能的重要指标之一。
烧结多孔砖的耐火极限是指其在高温条件下能够保持稳定的物理和化学性质的最高温度。
在实际应用中,烧结多孔砖所承受的温度往往会超过其耐火极限,因此耐火极限的高低直接关系到砖块的使用寿命和安全性。
烧结多孔砖的耐火极限受多种因素的影响,主要包括材料成分、烧结工艺、孔隙率、砖块形状和尺寸等。
其中,材料成分是影响耐火极限的最重要因素。
一般来说,烧结多孔砖的成分应具有高的耐火性能和化学稳定性,如氧化铝、硅酸盐、碳化硅等。
同时,还需要控制材料成分的比例和烧结温度,以确保砖块的致密度和孔隙率在合理范围内。
烧结多孔砖的孔隙率也是影响其耐火极限的重要因素之一。
孔隙率过高会导致砖块的强度和热稳定性下降,从而影响其耐火性能。
因此,烧结多孔砖的孔隙率应控制在适当范围内,一般在30%~50%之间。
烧结多孔砖的形状和尺寸也会影响其耐火极限。
一般来说,烧结多孔砖的形状应尽量规则,避免出现过多的凸起或凹陷,以免影响砖块的热传导性能。
同时,砖块的尺寸也应控制在合理范围内,避免出现过大或过小的砖块,从而影响砖块的热稳定性和耐火性能。
在实际应用中,烧结多孔砖的耐火极限还受到工作环境的影响。
例如,在高温高压的工作环境下,烧结多孔砖的耐火极限往往会下降。
因此,在选择烧结多孔砖时,需要综合考虑其材料成分、孔隙率、形状和尺寸等因素,以及工作环境的条件,从而选择合适的砖块。
烧结多孔砖的耐火极限是评价其性能的重要指标之一。
其受到多种因素的影响,其中材料成分是影响最为重要的因素之一。
在选择烧结多孔砖时,需要综合考虑其材料成分、孔隙率、形状和尺寸等因素,以及工作环境的条件,从而选择合适的砖块,以确保其具有优异的耐火性能和良好的保温隔热性能。
耐火材料生产过程

① ②
毛细管力、粘结剂附着力、
机械捏合力等作用,物料 产生团聚、捏合。但总体 之内。
混练过程中物料混合不均匀度与时间的关系
而言,这两种作用的结果,是使配合料的均匀性波动在一定范围 (h1~h2)
二、混 练
(2)混练效率
● 混合效率可用混合指数 i 来表示。在整个坯料的不同部位
进行多点取样,并测定某一组分的含量 C, 就可以计算出整个
二、半干法压制成型
1. 压制过程
耐火材料的压制成型过程可 以大致分为以下三个阶段: 阶段A: 在压力作用下,颗粒发生 明显的位移,重新分布形成较紧 密的堆积,坯料被压缩明显。 压缩,mm P1
压力,MPa
A
B
P2
C
二、半干法压制成型
1. 压制过程
阶段B: 当压力增至 P1 后,
颗粒发生脆性及弹性变形, 坯料被进一步压缩,但呈 阶梯式变化——坯料被压 缩到一定程度后,即阻碍 进一步压缩,一旦压力继 续增大到使颗粒再度产生 过程短促而频繁,最后,压制过程进入第三阶段。 阶段C: 在极限压力 P2 作用下,坯料不再被压缩,坯体的密度不
增大而降低,从而使得成型坯体的密度亦不均匀,产生所谓的
“层密度”现象。 ● 压强随砖坯厚度改变的关系如下: Sh = S0· exp(-Kh/R) Sh——距受压面 h mm 处的压强;S0——受压面上的压强; K—— 与模型结构有关的系数;R——坯体截面的当量半径。
二、半干法压制成型
2. 砖坯中的压力分布和层密度现象 ● 由于坯体的气孔率取决于压强大小,故沿坯体厚度方向的 压强落差即在一定程度上确定了坯体密度的均匀性。因此, 坯体密度的均匀性可用 Sh和 S0 的比值来估计: β =Sh/ S0 = exp(-Kh/R) 显然, β 越接近于1,则坯体密度的均匀性越好。 3. 影响坯体密度均匀性的因素 (1) 坯料的性质:包括其流动性、自然堆积密度等。 (2) 坯料颗粒间的内摩擦力及颗粒与模壁间的外摩擦力大小:与 颗粒形状、含水率、塑化剂或润滑剂性质及含量有关。 (3) 加压速度及加压方式。 (4) 坯体的大小、厚薄及形状等。
烧结
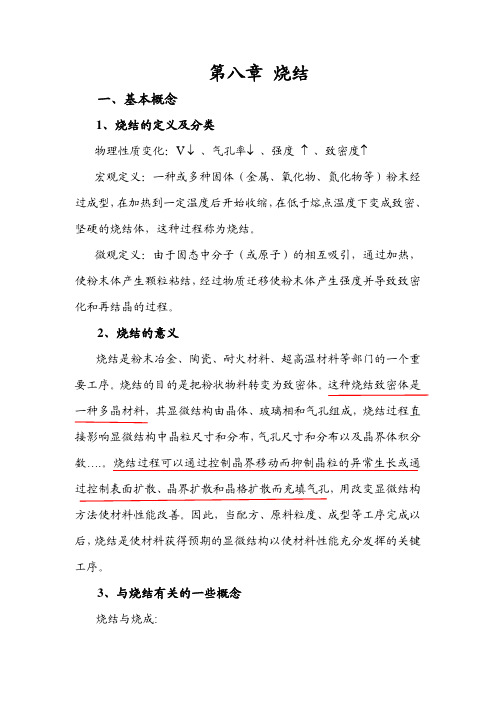
第八章烧结一、基本概念1、烧结的定义及分类物理性质变化:V ↓、气孔率↓、强度↑、致密度↑宏观定义:一种或多种固体(金属、氧化物、氮化物等)粉末经过成型,在加热到一定温度后开始收缩,在低于熔点温度下变成致密、坚硬的烧结体,这种过程称为烧结。
微观定义:由于固态中分子(或原子)的相互吸引,通过加热,使粉末体产生颗粒粘结,经过物质迁移使粉末体产生强度并导致致密化和再结晶的过程。
2、烧结的意义烧结是粉末冶金、陶瓷、耐火材料、超高温材料等部门的一个重要工序。
烧结的目的是把粉状物料转变为致密体。
这种烧结致密体是一种多晶材料,其显微结构由晶体、玻璃相和气孔组成,烧结过程直接影响显微结构中晶粒尺寸和分布,气孔尺寸和分布以及晶界体积分数….。
烧结过程可以通过控制晶界移动而抑制晶粒的异常生长或通过控制表面扩散、晶界扩散和晶格扩散而充填气孔,用改变显微结构方法使材料性能改善。
因此,当配方、原料粒度、成型等工序完成以后,烧结是使材料获得预期的显微结构以使材料性能充分发挥的关键工序。
3、与烧结有关的一些概念烧结与烧成:烧成:包括多种物理和化学变化。
例如脱水、坯体内气体分解、多相反应和熔融、溶解、烧结等。
而烧结仅仅指粉料经加热而致密化的简单物理过程,烧结仅仅是烧成过程的一个重要部分。
烧结和熔融:烧结是在远低于固态物质的熔融温度进行的。
烧结和熔融这两个过程都是由原子热振动而引起的,但熔融时全部组元都为液相,而烧结时至少有一组元是处于固态。
烧结与固相反应:两个过程均在低于材料熔点或熔融温度之下进行的。
并且在过程的自始自终都至少有一相是固态。
两个过程不同之处是固相反应必须至少有两组元A和B参加,并发生化学反应,最后生成化合物AB。
AB结构与性能不同于A和B。
而烧结可以只有单组元,或者两组元参加,但两组元并不发生化学反应。
仅仅是在表面能驱动下,由粉体变成致密体。
从结晶化学观点看,烧结体除可见的收缩外,微观晶相组成并未变化,仅仅是晶相显微组织上排列致密和结晶程度更完善。
齐鲁工业大学耐火材料试题及答案
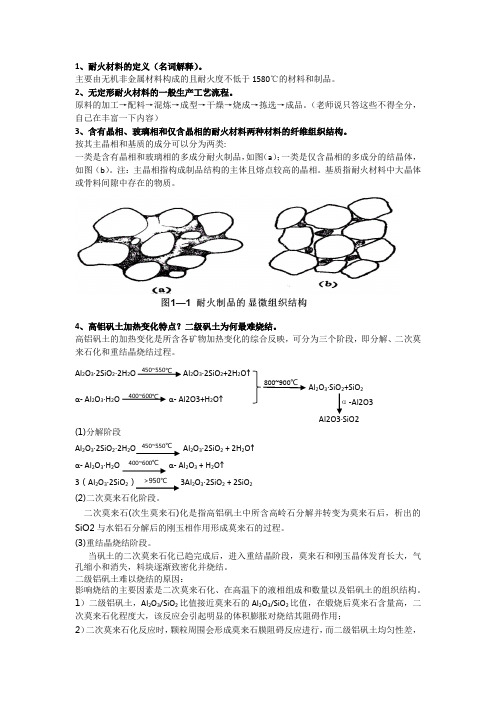
1、耐火材料的定义(名词解释)。
主要由无机非金属材料构成的且耐火度不低于1580℃的材料和制品。
2、无定形耐火材料的一般生产工艺流程。
原料的加工→配料→混炼→成型→干燥→烧成→拣选→成品。
(老师说只答这些不得全分,自己在丰富一下内容)3、含有晶相、玻璃相和仅含晶相的耐火材料两种材料的纤维组织结构。
按其主晶相和基质的成分可以分为两类:一类是含有晶相和玻璃相的多成分耐火制品,如图(a );一类是仅含晶相的多成分的结晶体,如图(b )。
注:主晶相指构成制品结构的主体且熔点较高的晶相。
基质指耐火材料中大晶体或骨料间隙中存在的物质。
4、高铝矾土加热变化特点?二级矾土为何最难烧结。
高铝矾土的加热变化是所含各矿物加热变化的综合反映,可分为三个阶段,即分解、二次莫来石化和重结晶烧结过程。
Al 2O 3∙2SiO 2∙2H 2O 450~550℃ Al 2O 3∙2SiO 2+2H 2O ↑α- Al 2O 3∙H 2O 400~600℃ α- Al2O3+H 2O ↑(1)分解阶段Al 2O 3∙2SiO 2∙2H 2O 450~550℃ Al 2O 3∙2SiO 2 + 2H 2O ↑α- Al 2O 3∙H 2O 400~600℃ α- Al 2O 3 + H 2O ↑3(Al 2O 3∙2SiO 2) >950℃ 3Al 2O 3∙2SiO 2 + 2SiO 2(2)二次莫来石化阶段。
二次莫来石(次生莫来石)化是指高铝矾土中所含高岭石分解并转变为莫来石后,析出的SiO2与水铝石分解后的刚玉相作用形成莫来石的过程。
(3)重结晶烧结阶段。
当矾土的二次莫来石化已趋完成后,进入重结晶阶段,莫来石和刚玉晶体发育长大,气孔缩小和消失,料块逐渐致密化并烧结。
二级铝矾土难以烧结的原因:影响烧结的主要因素是二次莫来石化、在高温下的液相组成和数量以及铝矾土的组织结构。
1)二级铝矾土,Al 2O 3/SiO 2比值接近莫来石的Al 2O 3/SiO 2比值,在煅烧后莫来石含量高,二次莫来石化程度大,该反应会引起明显的体积膨胀对烧结其阻碍作用;2)二次莫来石化反应时,颗粒周围会形成莫来石膜阻碍反应进行,而二级铝矾土均匀性差,煅烧时由于矿物分布不均匀,莫来石膜厚度增加,铝、硅离子的扩散距离增长,使反应更难进行;3)二级铝矾土在烧结过程中,液相量少于三级铝矾土,生成液相黏度高于特级和一级铝矾土,,对烧结作用的促进效果差。
反应烧结碳化硅做耐火材料特性__反应烧结碳化硅影响因素主要有哪些

反应烧结碳化硅做耐火材料特性__反应烧结碳化硅影响因素主要有哪些反应烧结出的产品,表面光滑、密度高、强度也高。
反应烧结碳化硅现在不仅应用在电厂脱硫系统、采矿选矿、水泥制造、金属热处理、镀锌镀铝、垃圾焚烧、石油化工机械及太阳能等行业。
将来反应烧结碳化硅所制造的部件,会越来越多的应用在超高温、热震、磨损和高腐蚀的材料工业领域。
反应烧结碳化硅还可以做耐火材料,那么反应烧结碳化硅做耐火材料特性有哪些呢?【反应烧结碳化硅做耐火材料特性】①具有1600℃以上的耐火度;②高导热率;③高强度,高耐磨性;④抗侵蚀性好;⑤抗热震性好;⑥低成本,高寿命【反应烧结碳化硅影响因素主要有哪些】1:原始粉料的粒度,无论在固态或者液态的烧结中,细颗粒由于增加了烧结的推动力,缩短了原子扩散的距离和提高颗粒在液相中的溶解度而导致烧结过程的加速。
一般烧结速率与起始粒度的1/3次方成正比。
2:外加剂的作用,在固相烧结中,少量外加剂(烧结助剂)可与主晶相形成固溶体促进缺陷增加;在液相烧结中,外加剂能改变液相的性质(如粘度、组成等),因而都能起到促进烧结的作用3:烧结温度和保温时间,在晶体中晶格能越大,离子结合越牢固,离子对扩散也越困难,所需的烧结温度也越高。
但是各种晶体键合情况不同,因此烧结温度也相差很大,即使对于同一晶体,烧结温度也不是一个固定的值。
但是高温短时间烧结是制造致密陶瓷材料的好方法,但还要考虑材料店传热系数,二次再结晶的温度,扩散系数等各种因数,合理制定烧结温度。
4:盐类的选择以及煅烧条件:在通常情况下,原始配料以眼泪形式加入,经过加热后以氧化物形式烧结。
盐类具有层状结构,当其分解是这种结构往往不能完全破坏,原料盐类与生成物之间若保持结构上的关联性,那么盐类的种类、分解温度和时间将影响烧结氧化物的结构缺陷和内部应变,从而影响烧结速率与性能。
5:气氛的影响:一般地说,在由扩散控制的氧化物烧结中,气氛的影响与扩散控制因素有关,与气孔内气体的扩散和溶解能力有关。
耐火干振料 标准

耐火干振料是一种不定形耐火材料,由耐火骨料、粉料、烧结剂和外加剂组成。
其标准主要涉及以下几个方面:
耐火骨料和粉料:耐火干振料应选用高纯度、高硬度的耐火骨料和粉料,以确保高温下不易软化、熔融或变形。
根据不同的使用温度和使用环境,选择合适的骨料和粉料,并进行相应的粒度和化学成分的检测和控制。
烧结剂和外加剂:烧结剂和外加剂是影响耐火干振料性能的关键因素。
应选择能够与骨料和粉料良好结合的烧结剂和外加剂,以提高材料的致密度、强度和耐火性能。
此外,外加剂还应具有足够的稳定性,以确保材料在使用过程中不易变质或产生有害气体。
工艺性能:耐火干振料应具有良好的施工性能,包括适当的流动性和可塑性,以方便其在工业炉窑或高温设备中快速、准确地施工。
同时,干振料应具有良好的干燥性能,包括较高的干燥强度和较短的干燥周期,以减少施工时间并提高生产效率。
物理性能:耐火干振料应具有适当的物理性能,如密度、气孔率、吸水率等。
这些参数将直接影响干振料的耐火性能、保温性能和机械强度。
不同用途的耐火干振料有不同的物理性能要求,应根据具体需求进行选择。
安全性:耐火干振料应符合国家有关安全、环保等方面的规定,不应对人体健康和环境造成危害。
在选择和使用耐火干振料时,应关注其成分、有害物质含量、安全性能等方面的信息,以确保其符合相关标准和规定。
总之,耐火干振料的标准涉及多个方面,包括耐火骨料和粉料的选择、烧结剂和外加剂的选用、工艺性能和物理性能的要求以及安全性的考虑等。
在选择和使用耐火干振料时,应综合考虑这些因素,以确保其满足实际需求并具有可靠性。
- 1、下载文档前请自行甄别文档内容的完整性,平台不提供额外的编辑、内容补充、找答案等附加服务。
- 2、"仅部分预览"的文档,不可在线预览部分如存在完整性等问题,可反馈申请退款(可完整预览的文档不适用该条件!)。
- 3、如文档侵犯您的权益,请联系客服反馈,我们会尽快为您处理(人工客服工作时间:9:00-18:30)。
影响耐火材料烧结的因素
指导老师:
学院:能源科学与工程学院
专业班级:热动
姓名:
学号:
影响耐火材料烧结的因素
耐火材料的烧结盟一个复杂的、受多种因素制约的过程。
影响烧结的主要因素包括原料的性质、添加剂、烧结温度和保温时间、烧成气氛以及坯体的成型方法和压力等。
一、原料的影响
原料对烧结的影响分为内因和外因两个方面。
内因是物料的结晶化学特性,外因则主要体现为所用原料的颗粒组成。
物料晶体的晶格能是决定物料烧结和再结晶难易的重要参数。
晶格能大的晶体,结构较稳定,高温下质点的可移动性小,烧结困难。
晶体结构类型也是一个重要影响因素,物料阳离子的极性低,则其形成的化合物的晶体结构较稳定,必须在接近熔点的温度下才有显著缺陷,故该类化合物质点的可移动性小,不易烧结。
耐火材料中Al2O3 、MgO的晶格能高而极性低,故较难于烧结。
由微细晶粒组成的多晶体比单晶体易于烧结,因为在多晶体内含有许多晶界,此处是消除缺陷的主要地方,还可能是原子和离子扩散的快速通道。
离子晶体烧结时,正、负离子都必须扩散才能导致物质的传递和烧结。
其中扩散速率较慢的一种离子的扩散速率控制着烧结速度。
一般认为负离子的半径较大,扩散速率较慢,但对Al2O3 、Fe2O3的实验研究发现,O2-通过晶界提供的通道快速扩散,以致正离子Al3+、Fe3+的扩散比氧离子慢,成为烧结过程控速步骤。
晶体生长速度是影响烧结的另一个晶体化学特性。
例如MgO烧结时晶体生长很快,很容易长大至原始晶粒的1000~1500倍,但其密度只能达到理论值的60%~80%。
Al2O3 则不然,虽其晶粒长大仅50~100倍,却可达到理论密度的90%~95%,基本上达到充分烧结。
为使MgO材料密度提高,必须抑制晶粒长大的措施。
所用原料的粒度也是影响烧结致密化的重要因素,无论是固相烧结还是液相烧结,细颗粒
均增加了烧结的推动力,缩短了粒子扩散的距离和提高了颗粒在液相中的溶解度而导致烧结过程的加速,有资料报道,MgO的原始粒度为20μm以上时,即使在1400℃长时间保温,仅能达到相对密度的70%而不能进一步致密化;当粒径在20μm以下时,温度为1400℃或粒径为1μm以下,在1000℃时,烧结速度很快;如果粒径在0.1μm以下时,其烧结速度与热压烧结相差无几。
从防止二次再结晶的角度考虑,如果细粉内有少量大颗粒存在,则易发生晶粒的异常长大而不于烧结。
一般氧化物材料适宜的粉末粒度为0.05~0.5μm。
原始粉末的粒度不同,烧结机理有时也会发生改变。
例如AIN的烧结,据报道,当粒度为0.78~4.4μm时,粗颗粒按体积扩散机理进行烧结,而细颗粒则按晶界扩散或表面扩散机理进行烧结。
二、添加剂的影响
在固相烧结时,少量添加剂(烧结助剂)可与主晶相形成固溶体促进缺陷增加;在液相烧结时,添加剂能够改变液相的性质(如粘土、组成等),因而能起促进烧结的作用。
添加剂的作用可能在于以下几个方面
1. 形成固溶体。
当添加物与烧结物形成固溶体时,可以增加晶格缺陷,活化晶格,从而促进烧结。
一般来说,它们之间形成有限置换固溶体更有助于促进烧结。
添加剂离子的电价、半径与主晶格离子的电价,半径相差越大,晶格畸变程度也越大,促进烧结的作用也越明显。
如Al2O3 烧结时,加入3%的Cr2O3形成连续固溶体可在1860℃烧结,而加入1%~2%TiO2只需在1600℃左右就能致密化。
2. 阻止晶型转变,有些氧化物在烧结时发生晶型转变并伴有较大的体积效应,这就难以实现烧结致密化,并容易引起坯体开裂。
这时若能选用适宜的添加剂加以抑制,即可促进烧结。
ZrO2烧结时添加一定量的CaO、MgO就属这一机理。
约在1200℃,m- ZrO2转变为t- ZrO2,并伴有约10%的体积收缩,使制品稳定性变坏。
引入电价比Zr4+低的Ca2+(或Mg2+),可形成稳定的立方萤石结构的固溶体。
这样,既防止了制品的开裂,又增加了晶体中缺陷浓度,使烧结加快.
3. 抑制品粒长大,烧结后期晶粒长大,对促进烧结致密化有重要作用。
但若二次再结晶或间断性晶粒长大过快,会使晶粒变粗、晶界变宽而出现反致密化现象并影响制品的显微结构。
这时,可通过加入能抑制品粒异常长大的添加剂来促进烧结,在烧结透明Al2O3 制品
时,为抑制二次再结晶,消除晶界上的气孔,一般加入MgO或MgF2,高温下形成镁铝尖晶石包裹在Al2O3 晶粒表面,抑制了晶界迁移的速度,并促使气孔的排出,对促进坯体的烧结具有显著的作用。
4. 形成液相。
添加剂在烧结过程中形成液相。
液相形成的原因可能在于两方面:添加剂本身的熔点较低,添加剂与烧结物形成多元低共熔物;由于液相的传质阻力小、传质速度快,从而降低了烧结温度和提高了坯体的密度。
例如在制造95% Al2O3 陶瓷时,一般加入CaO 和SiO2,当CaO:SiO2=1时,由于生成CaO- Al2O3- SiO2液相,从而使材料在1540℃就能烧结。
应该指出的是,能促进形成液相的添加剂并非都会促进烧结,如向Al2O3 中加入部分碱金属氧化物就会严重妨碍其烧结。
另外,形成液要虽然有利于烧结,但会严重影响材料的高温性能,故必须统筹考虑。
三、烧结温度和保温时间的影响
烧结温度和保温时间是耐火材料烧结的重要外因。
随着温度的升高,物料的蒸气压增加,扩散系数增大,液相粘度降低,从而促进了蒸发-凝聚,离子和空位的扩散,颗粒重排和粘、塑性流动等物质传递过程,故使烧结速度加快。
延长烧结时间也可促进烧结的完成,然而在烧结后期,不合理地延长烧结时间,有时会加剧二次再结晶作用,反而得不到充分致密的制品。
耐火制品的烧成最高温度应该控制在烧结温度的范围内,在此温度下应保持适当的烧结时间以使烧结完成,若继续升高温度会使坯体变形。
四、气氛的影响
气氛直接影响烧成效果和制品质量、烧成气氛一般可分为氧化性气氛、中性气氛和还原性气氛,对于不同材质的坏体应选择不同的气氛,以保证坯体中物理化学反应的顺利进行。
烧结末期,当气孔处于封闭状态时,气氛(气孔中气体的类型)对烧结是有影响的。
研究
Al2O3 的烧结时发现,当气体在晶格中的溶解度很小而扩散很慢时,则孤立的气孔不易从坏体中排出。
例如,Al2O3 在氩气和空气中的烧结就是这样。
相反,当气体在晶格中的扩散速度足够快时,则气氛对烧结末期没有影响。
如果气氛对控制结构有一定的作用,则可扩散而有利于烧结的进行。
必须指出,烧成气氛的影响到材料组成、烧结条件、添加剂的种类和数量等因素有关。
因此,应该针对不同问题进行具体分析。
在实际烧结过程中,上述因素的影响是相互联系、彼此制约的。
在不同的条件下起主要作用的因素可能是不同的。
1. 回转窑的操作控制
回转窑中煅烧熟料的质量与产量,与很多因素有关,如窑体结构、原料、燃料性质等,且在很大程度上决定于操作技术水平。
回转窑操作中应考虑下列原则:1)必须保证煅烧熟质量,烧后熟料应没有欠烧和过烧产品,熟料性能应符合耐火材料生产的技术要求。
2)保证窑能持续地、正常地、稳定地运转。
因为只有回转窑运转稳定,才能使产品产量和质量稳定。
所谓运转稳定,是指只需变动很少的(或者全不变动)控制变量,而能保持窑的平衡状态。
3)要求燃料完全燃烧,在提高燃烧热效率的同时提高传热速率。
回转窑运转时应力求热工制度稳定。
为此必须经常了解窑内情况,及时进行控制,以小变动克服大变动,保证生产在最适宜的条件下进行。