影响烧结的因素(新)
烧结的问题和解答

烧结的问题和解答第九章烧结1、解释下列名词(1)烧结:粉料受压成型后在高温作用下而致密化的物理过程。
烧成:坯体经过高温处理成为制品的过程,烧成包括多种物理变化和化学变化。
烧成的含义包括的范围广,烧结只是烧成过程中的一个重要部分。
(2)晶粒生长:无应变的材料在热处理时,平均晶粒尺寸在不改变其分布的情况下,连续增大的过程。
二次再结晶:少数巨大晶粒在细晶消耗时成核长大过程。
(3)固相烧结:固态粉末在适当的温度、压力、气氛和时间条件下,通过物质与气孔之间的传质,变为坚硬、致密烧结体的过程。
液相烧结:有液相参加的烧结过程。
2、详细说明外加剂对烧结的影响?答:(1)外加剂与烧结主体形成固溶体使主晶格畸变,缺陷增加,有利结构基元移动而促进烧结;(2)外加剂与烧结主体形成液相,促进烧结;(3)外加剂与烧结主体形成化合物,促进烧结;(4)外加剂阻止多晶转变,促进烧结;(5)外加剂起扩大烧结范围的作用。
3、简述烧结过程的推动力是什么?答:能量差,压力差,空位差。
4、说明影响烧结的因素?答:(1)粉末的粒度。
细颗粒增加了烧结推动力,缩短原子扩散距离,提高颗粒在液相中的溶解度,从而导致烧结过程的加速;(2)外加剂的作用。
在固相烧结中,有少量外加剂可与主晶相形成固溶体,促进缺陷增加,在液相烧结中,外加剂改变液相的性质(如粘度,组成等),促进烧结。
(3)烧结温度:晶体中晶格能越大,离子结合也越牢固,离子扩散也越困难,烧结温度越高。
(4)保温时间:高温段以体积扩散为主,以短时间为好,低温段为表面扩散为主,低温时间越长,不仅不引起致密化,反而会因表面扩散,改变了气孔的形状而给制品性能带来损害,要尽可能快地从低温升到高温,以创造体积扩散条件。
(5)气氛的影响:氧化,还原,中性。
(6)成形压力影响:一般说成型压力越大颗粒间接触越紧密,对烧结越有利。
5、在扩散传质的烧结过程中,使坯体致密的推动力是什么?哪些方法可促进烧结?说明原因。
影响耐火材料烧结的因素

影响耐火材料烧结的因素指导老师:学院:能源科学与工程学院专业班级:热动姓名:学号:影响耐火材料烧结的因素耐火材料的烧结盟一个复杂的、受多种因素制约的过程。
影响烧结的主要因素包括原料的性质、添加剂、烧结温度和保温时间、烧成气氛以及坯体的成型方法和压力等。
一、原料的影响原料对烧结的影响分为内因和外因两个方面。
内因是物料的结晶化学特性,外因则主要体现为所用原料的颗粒组成。
物料晶体的晶格能是决定物料烧结和再结晶难易的重要参数。
晶格能大的晶体,结构较稳定,高温下质点的可移动性小,烧结困难。
晶体结构类型也是一个重要影响因素,物料阳离子的极性低,则其形成的化合物的晶体结构较稳定,必须在接近熔点的温度下才有显著缺陷,故该类化合物质点的可移动性小,不易烧结。
耐火材料中Al2O3 、MgO的晶格能高而极性低,故较难于烧结。
由微细晶粒组成的多晶体比单晶体易于烧结,因为在多晶体内含有许多晶界,此处是消除缺陷的主要地方,还可能是原子和离子扩散的快速通道。
离子晶体烧结时,正、负离子都必须扩散才能导致物质的传递和烧结。
其中扩散速率较慢的一种离子的扩散速率控制着烧结速度。
一般认为负离子的半径较大,扩散速率较慢,但对Al2O3 、Fe2O3的实验研究发现,O2-通过晶界提供的通道快速扩散,以致正离子Al3+、Fe3+的扩散比氧离子慢,成为烧结过程控速步骤。
晶体生长速度是影响烧结的另一个晶体化学特性。
例如MgO烧结时晶体生长很快,很容易长大至原始晶粒的1000~1500倍,但其密度只能达到理论值的60%~80%。
Al2O3 则不然,虽其晶粒长大仅50~100倍,却可达到理论密度的90%~95%,基本上达到充分烧结。
为使MgO材料密度提高,必须抑制晶粒长大的措施。
所用原料的粒度也是影响烧结致密化的重要因素,无论是固相烧结还是液相烧结,细颗粒均增加了烧结的推动力,缩短了粒子扩散的距离和提高了颗粒在液相中的溶解度而导致烧结过程的加速,有资料报道,MgO的原始粒度为20μm以上时,即使在1400℃长时间保温,仅能达到相对密度的70%而不能进一步致密化;当粒径在20μm以下时,温度为1400℃或粒径为1μm以下,在1000℃时,烧结速度很快;如果粒径在0.1μm以下时,其烧结速度与热压烧结相差无几。
催化剂烧结的原因

催化剂烧结的原因
催化剂烧结是指在高温下,催化剂颗粒之间发生结合,形成更大颗粒的过程。
这种现象在工业生产过程中经常出现,对于催化剂的活性和稳定性都会产生影响。
那么,催化剂烧结的原因是什么呢?
催化剂烧结的原因之一是催化剂颗粒之间的相互作用力。
在高温条件下,催化剂表面的活性位点会发生变化,使得催化剂颗粒之间的相互作用力增强。
这种相互作用力会导致催化剂颗粒之间结合在一起,形成更大颗粒的现象。
这种结合会导致催化剂的比表面积减小,从而影响催化剂的活性。
催化剂烧结的原因还可能与催化剂的成分和结构有关。
一些催化剂的成分可能会在高温下发生化学反应,导致催化剂颗粒之间的结合。
此外,催化剂的结构也会影响烧结的程度。
如果催化剂的结构不稳定或者存在缺陷,那么在高温条件下就容易发生烧结现象。
催化剂烧结的原因还可能与反应条件有关。
例如,反应器内部的流动状况、温度梯度等因素都会影响催化剂的烧结情况。
如果反应条件不稳定或者不合适,就容易导致催化剂的烧结现象发生。
为了避免催化剂烧结,可以采取一些措施。
首先,可以优化催化剂的成分和结构,使其在高温条件下更加稳定。
其次,可以控制好反应条件,避免出现不利于催化剂稳定的情况。
另外,定期清洗和更换催化剂也是防止烧结的有效方法。
总的来说,催化剂烧结是由多种因素共同作用导致的现象。
要想有效地防止烧结,就需要综合考虑催化剂的成分、结构、反应条件等因素,采取适当的措施进行处理。
只有这样,才能保证催化剂的活性和稳定性,提高工业生产的效率和质量。
固相烧结与液相烧结的影响因素

1以SiC 为例,分析影响液相烧结的因素及解决措施。
答:在液相烧结过程中,影响液相烧结的因素主要为以下几个方面:1、颗粒粒度与形状细颗粒有利于提高烧结致密化速度,便于获得高的最终烧结密度。
在颗粒重排阶段提高毛细管力便于固相颗粒在液相中移动(尽管会增加颗粒之间的摩擦力和固相颗粒之间的接触机会)。
在溶解-再析出阶段强化固相颗粒之间和固相/液相间的物质迁移加快烧结速度。
另外,细小晶粒的烧结组织有利于获得性能优异的烧结材料。
此外,颗粒重排阶段初期,颗粒形状影响毛细管力大小,形状复杂导致颗粒重排阻力增加,球形颗粒有利于颗粒重排,形状复杂的固相颗粒降低烧结组织的均匀性,综合力学性能较低在溶解-再析出阶段,颗粒形状的影响较小。
2、液相的影响[1]液相的粘度、表面张力、润湿性、数量等对烧结的影响。
液相的粘度愈低, 它们对固相的浸润愈好, 愈有利于烧结。
同时, 在一般情况下, 由于物质在液相中的扩散速度比在固相中快, 人们通常认为液相存在总是能促进烧结的, 但事实并非完全为人们所想像的那样。
在许多情况下液相存在反而阻碍烧结, 液相粘度降低和对固体浸润性能的改善并不一定总是有利于烧结的。
液相对烧结过程的作用主耍为两部分:首先是在液相毛细管力和由于表面曲率不同而引起的压力差的作用下所发生的固体颗粒重排过程,在这部分作用中, 液相对固相的浸润性能起重要作用。
其次为通过液相的重结晶过程。
润湿性液相对固相颗粒的表面润湿性好是液相烧结的重要条件之一,对致密化、合金组织与性能的影响极大。
润湿性由固相、液相的表面张力(比表面能)S γ、L γ以及两相的界面张力(界面能) SL γ所决定。
如图5—47所示:当液相润湿固相时,在接触点A 用杨氏方程表示平衡的热力学条件为cos S SL L γγγθ=+式中θ——湿润角或接触角。
完全润湿时,0θ=,cos SSL L γγγθ=+式变为S SL L γγγ=+;完全不润湿时,θ>90,则S L L S γγγ≥+。
烧结生产工艺改进思考
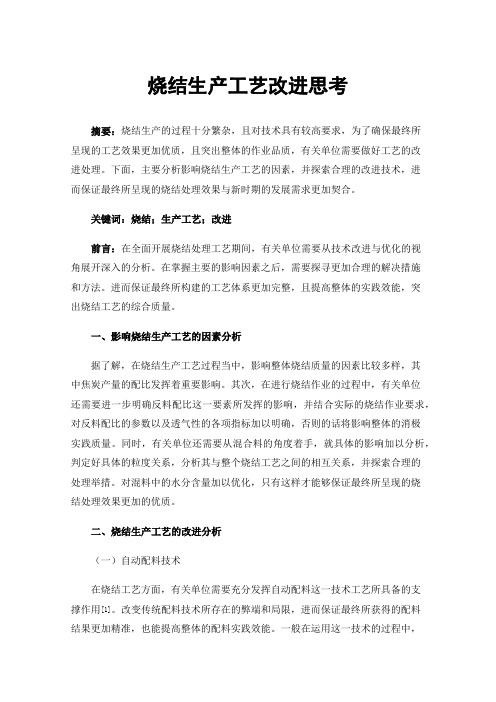
烧结生产工艺改进思考摘要:烧结生产的过程十分繁杂,且对技术具有较高要求,为了确保最终所呈现的工艺效果更加优质,且突出整体的作业品质,有关单位需要做好工艺的改进处理。
下面,主要分析影响烧结生产工艺的因素,并探索合理的改进技术,进而保证最终所呈现的烧结处理效果与新时期的发展需求更加契合。
关键词:烧结;生产工艺;改进前言:在全面开展烧结处理工艺期间,有关单位需要从技术改进与优化的视角展开深入的分析。
在掌握主要的影响因素之后,需要探寻更加合理的解决措施和方法。
进而保证最终所构建的工艺体系更加完整,且提高整体的实践效能,突出烧结工艺的综合质量。
一、影响烧结生产工艺的因素分析据了解,在烧结生产工艺过程当中,影响整体烧结质量的因素比较多样,其中焦炭产量的配比发挥着重要影响。
其次,在进行烧结作业的过程中,有关单位还需要进一步明确反料配比这一要素所发挥的影响,并结合实际的烧结作业要求,对反料配比的参数以及透气性的各项指标加以明确,否则的话将影响整体的消极实践质量。
同时,有关单位还需要从混合料的角度着手,就具体的影响加以分析,判定好具体的粒度关系,分析其与整个烧结工艺之间的相互关系,并探索合理的处理举措。
对混料中的水分含量加以优化,只有这样才能够保证最终所呈现的烧结处理效果更加的优质。
二、烧结生产工艺的改进分析(一)自动配料技术在烧结工艺方面,有关单位需要充分发挥自动配料这一技术工艺所具备的支撑作用[1]。
改变传统配料技术所存在的弊端和局限,进而保证最终所获得的配料结果更加精准,也能提高整体的配料实践效能。
一般在运用这一技术的过程中,需要根据具体的烧结工艺作业要求,备好一定数量的配合材料。
然后发挥先进技术设备的支撑作用,对其进行科学的配料处理。
在整个实践的过程中能够有效降低在人工方面的成本投入,也能够合理控制业为人工操作失误而造成的不良风险。
相较于以往的技术手段,该工艺所具备的时效性特征尤为显著,比较受到烧结工艺生产实践过程的推崇和应用,展现出独特的作用。
影响氧化铝陶瓷烧结的因素分析

19影响氧化铝陶瓷烧结的因素分析刘国祥(214221江苏省陶瓷研究所7401314)摘要阐述了氧化铝陶瓷的烧结机理,分析了烧成气氛、物料分散度及添加熔剂等因素对氧化铝制品烧结程度的影响,总结出理想的升温制度、保温时间、绘制烧成曲线。
关键词氧化铝陶瓷烧结机理影响因素烧成制度1前言进入“九五”以来,工业特种陶瓷得到了迅猛发展。
其中氧化铝陶瓷以其优良的特性如耐酸碱性、耐磨性、耐电性、机械强度高等,在工业化生产中得到了广泛的应用。
因此,深入研究氧化铝陶瓷的生产技术及其发展,服务于生产和社会需要就显得相当重要。
在氧化铝陶瓷的生产过程中,无论是原料制备、成型、烧结还是冷加工,每个环节都是不容忽视的。
坯体烧结后,制品的显微结构及其内在性能发生了根本的改变,很难通过其它办法进行补救。
因此,深入研究氧化铝陶瓷的烧结技术,合理选择理想的烧结制度确保产品的性能,对氧化铝陶瓷生产极有帮助。
2烧结机理烧结是指坯体由低温到高温发生一系列的物理化学反应,从而得到致密的、坚硬的制品的过程。
其中物理化学变化包含坯体中残余的拌料水分的排溢、物料中化合物结合水和有机物的分解排除、Al2O3同质异晶的晶型转变以及固态物质颗粒间直接进行反应———固相反应等。
固相反应在氧化铝陶瓷烧结中占有极为重要的位置,它实质上是通过物质质点的迁移扩散作用而进行的,随着温度的升高,晶体的热缺陷不断增加,质点迁移扩散由内扩散形式到外扩散,并更加充分,从而发生反应,产生新的物质(见图1)。
如图1所示,假定颗粒是圆的,温度升高,颗粒界面相互融合,形成勃颈并不断扩大,颗粒径距缩短,气孔变小并逐渐排除,晶粒长大,体积收缩,最后形成致密体。
从以上的分析可以看出,固相反应的关键是迁移,提高质点的迁移速度和效率,就能有效地促进烧结和致密过程;反之,就起阻碍作用。
3影响烧结性能的因素影响氧化铝陶瓷烧结程度的因素较多,主要表现为以下几点:3.1晶体的结构化学键强的化合物(晶体)具有较高的晶格能量,晶格结构牢固:即使在较高温度下,质点的振动迁移也较弱。
金属冶炼过程中的烧结技术
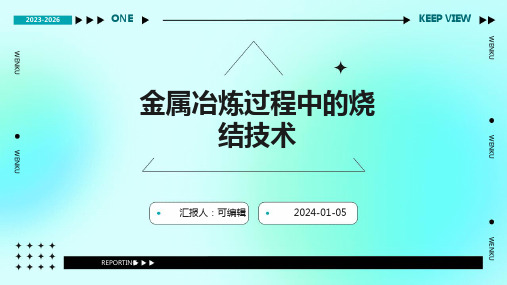
将混合好的烧结料在烧结设备中进行高温 烧结,使原料熔融、固结,形成具有一定 强度和冶金性能的烧结制品。
烧结制品在冷却过程中进行整粒处理,以 减小颗粒度,提高制品的物理性能。
烧结设备的分类与选择
连续式烧结设备
如带式烧结机、步进式烧结机等 ,适用于大规模、连续化生产。
间歇式烧结设备
如台车式烧结炉、转盘式烧结炉 等,适用于小规模、间歇性生产 。
2023-2026
ONKU
金属冶炼过程中的烧 结技术
WENKU
WENKU
WENKU
汇报人:可编辑
REPORTING
2024-01-05
CATALOGUE
目 录
• 烧结技术概述 • 烧结原理及影响因素 • 烧结工艺及设备 • 烧结技术的应用与实例 • 烧结技术的挑战与未来发展
烧结的目的是为了使粉末或压坯通过 烧结获得所要求的物理、化学和机械 性能,使其成为具有所需综合性能的 制品或材料。
意义
烧结是粉末冶金工艺中的关键工序, 通过烧结可得到各种密度、孔隙率、 机械性能和物理性能的制品或材料, 以满足各种不同的用途要求。
烧结技术的发展历程
古代烧结
人类在长期的生产实践中,如烧制陶器、冶炼金属等,发展了烧结 技术。
在烧结过程中,粉末颗粒之间的物理 化学作用力发生变化,导致颗粒间的 空隙逐渐缩小,最终形成致密的结构 。
烧结温度的影响因素
烧结温度是影响烧结过程的重要因素,它决定了粉末颗粒间的黏合程度和扩散速 度。
适当的烧结温度可以提高粉末的致密度和机械性能,而温度过高可能导致材料过 烧或性能下降。
烧结气氛的影响因素
烧结技术的挑战与未来发 展
烧结技术的挑战
高温环境下的材料稳定性
粉末冶金原理考试题
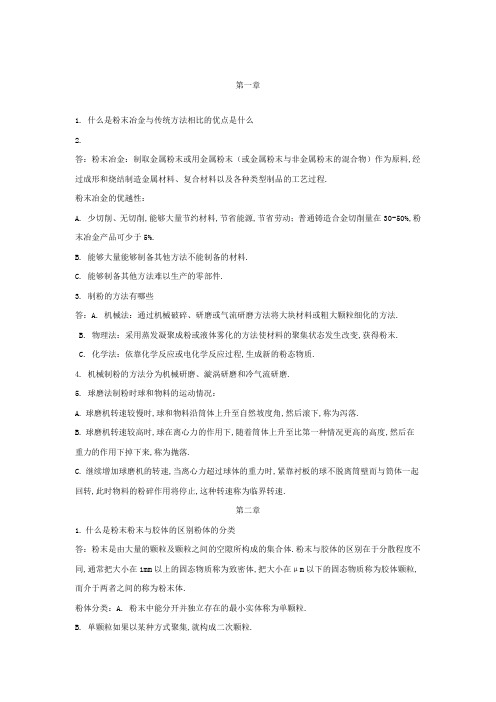
第一章1. 什么是粉末冶金与传统方法相比的优点是什么2.答:粉末冶金:制取金属粉末或用金属粉末(或金属粉末与非金属粉末的混合物)作为原料,经过成形和烧结制造金属材料、复合材料以及各种类型制品的工艺过程.粉末冶金的优越性:A. 少切削、无切削,能够大量节约材料,节省能源,节省劳动;普通铸造合金切削量在30-50%,粉末冶金产品可少于5%.B. 能够大量能够制备其他方法不能制备的材料.C. 能够制备其他方法难以生产的零部件.3. 制粉的方法有哪些答:A. 机械法:通过机械破碎、研磨或气流研磨方法将大块材料或粗大颗粒细化的方法.B. 物理法:采用蒸发凝聚成粉或液体雾化的方法使材料的聚集状态发生改变,获得粉末.C. 化学法:依靠化学反应或电化学反应过程,生成新的粉态物质.4. 机械制粉的方法分为机械研磨、漩涡研磨和冷气流研磨.5. 球磨法制粉时球和物料的运动情况:A.球磨机转速较慢时,球和物料沿筒体上升至自然坡度角,然后滚下,称为泻落.B.球磨机转速较高时,球在离心力的作用下,随着筒体上升至比第一种情况更高的高度,然后在重力的作用下掉下来,称为抛落.C.继续增加球磨机的转速,当离心力超过球体的重力时,紧靠衬板的球不脱离筒壁而与筒体一起回转,此时物料的粉碎作用将停止,这种转速称为临界转速.第二章1.什么是粉末粉末与胶体的区别粉体的分类答:粉末是由大量的颗粒及颗粒之间的空隙所构成的集合体.粉末与胶体的区别在于分散程度不同,通常把大小在1mm以上的固态物质称为致密体,把大小在μm以下的固态物质称为胶体颗粒,而介于两者之间的称为粉末体.粉体分类:A. 粉末中能分开并独立存在的最小实体称为单颗粒.B. 单颗粒如果以某种方式聚集,就构成二次颗粒.2. 聚集体、絮凝体、团聚体的划分答:A. 聚集体:通过单颗粒聚集得到的二次颗粒被称为聚集体;B. 絮凝体:用溶胶凝胶方法制备的粉末,是一种由单颗粒或二次颗粒结合成的更松软的聚集颗粒;C. 团聚体:由单颗粒或二次颗粒依靠范德华引力的作用下结合而成的粉末颗粒,易于分散.3.粉末的物理性能包括:颗粒形状与结构、颗粒大小与粒度组成、比表面积、颗粒的密度、显微硬度、光学和电学性质、熔点、比热容、蒸汽压等热学性质,由颗粒内部结构决定的X射线、电子射线的反射和衍射性质,磁学与半导体性质.4.粉末的工艺性能包括松装密度、振实密度、流动性、压缩性与成形性.A.松装密度:粉末在规定条件下自然充填容器时,单位体积内自由松装粉末体的质量(g/cm3).B.振实密度:粉末装于振动容器内,在规定条件下,经过振动敲打后测得的粉末密度.C.流动性:一定量粉末(50g) 流经标准漏斗所需的时间,单位为(s/50g).D.压缩性:粉末在压制过程中被压紧的能力.在规定的模具和润滑条件下加以测定,用在一定的单位压制压力(500MPa)下粉末所达到的压坯密度表示.E.成形性:压制后,粉末压坯保持形状的能力.用压坯强度表示.5. 粉末粒度:以mm或μm的表示的颗粒的大小称颗粒直径,简称粒径或粒度.粒度组成:具有不同粒径的颗粒占全部粉末的百分含量称粉末的粒度组成,又称粒度分布 .6.粉末比表面积的测定方法:A. 气体吸附法 B. 透过法(气体透过法、液体透过法)7.粉体粒度大小、形状对粉体性能的影响答: 颗粒的形状直接影响粉末的流动性、松装密度、气体透过性、另外对压制性与烧结性及烧结体强有显着影响;细粉末易“搭桥”和粘附妨碍颗粒相互移动,故松装密度减小;粒度范围窄的粗细粉末松装密度都很低,当粗细粉末按一定比例混合后,可获得大的松装密度.第三章1.原料的各种预处理及其作用答:(1)退火:可使氧化物还原,降低碳和其他杂质的含量,提高粉末的纯度;同时还能消除粉末的加工硬化、稳定粉末的晶体结构.(2)混合:将两种或两种以上不同成分的粉末混合均匀,有利于烧结的均匀化.(3)筛分:目的在于把大小不同的原始粉末进行分级.(4)制粒:目的是将小颗粒的粉末制成大颗粒或团粒的工序,常用来改善粉末的流动性.(5)加成形剂、润滑剂:成形剂是为了提高压坯强度或为了防止粉末混合料离析而添加的物质;润滑剂是为了降低压形时粉末颗粒与模壁和模冲间摩擦、改善压坯的密度分布、减少压模磨损和有利于脱模.2.粉末变形形式:(1)弹性变形(2)塑性变形(3)脆性断裂3.影响压坯密度分布不均匀的因素及其改进方法答:压力损失是造成压坯密度分布不均的主要因素.改进方法:(1)降低压坯的高径比.(2)采用模壁光洁度很高的压模并在模壁上涂润滑油,能减少外摩擦系数,改善密度分布.(3)可采用双面压制法来改善密度分布的不均.(5)还可采用利用摩擦力的压制方法.4.弹性后效:在压制过程中,当除去压制力并把压坯压出亚模后,由于内应力的作用,压坯发生弹性膨胀,这种现象称为弹性后效.产生弹性膨胀的原因:粉末体在压制过程中受到压力作用后,粉末颗粒发生弹塑性变形,从而在压坯内部聚集很大的内应力—弹性内应力,其方向与颗粒所受的外力方向相反,力图阻止颗粒变形.当压制压力消除后,弹性内应力便要松弛,改变颗粒的外形和颗粒间的接触状态,这就使粉末压坯产生了膨胀.5.压制过程中力的分析:(1)应力和应力分布净压力(P1):使粉末产生位移、变形、克服粉末的内摩擦;压力损失(P2):克服粉末颗粒与模壁之间外摩擦的力.(2)A.侧压力:压制过程中由垂直压力所引起的模壁施加于压坯的侧面压力.B.模壁摩擦力.(3)脱模压力:使压坯由模中脱出所需的压力.(4)弹性后效6. 影响压制过程的因素答:(1)粉末性能对压制过程的影响.(粉末本身的硬度和可塑性、粉末的摩擦性能、粉末纯度、粒度及粒度组成、形状、松装密度等)(2)润滑剂和成形剂的影响.(3)压制方式的影响(加压方式、加压保持时间、振动压制、磁场压制等).7. 压坯密度的分布:压坯中密度分布的不均匀性.第四章1.特殊成形的种类及各自的原理答:(1)等静压成形:在高温高压密封容器中,以高压氩气为介质,对其中的粉末或待压实的烧结坯料(或零件)施加各向均等静压力,形成高致密度坯料(或零件)的方法. 理论根据:帕斯卡原理关于液体传递压强的规律.(2)粉末连续成形:粉末在压力作用下由松散状态经过连续变化而成为具有一定密度、强度以及所需尺寸形状压坯或制品的过程.(3)粉浆浇注成形:将粉末预先制成悬浮液或糊状物,然后注入石膏模具中的粉末成形方法.(4)粉末注射成形:将粉末与热塑性材料(如聚苯乙烯)均匀混合使成为具有良好流动性能的流态物质,而后把这种流态物质在注射成形机上经一定的温度和压力,注入温度较低的模具内成形.(5)爆炸成形:板料在炸药爆炸瞬间产生的冲击波作用下高速成形的方法.第五章1. 烧结:指粉末或压坯,在适当的温度和气氛条件下加热所发生的现象或过程.烧结系统的分类:(1)单元系烧结:纯金属或化合物在其熔点以下的温度进行的固相烧结.(2)多元系烧结:A. 多元系固相烧结:由两种及以上的组分构成,在低熔组分的熔点以下进行的烧结过程.B. 多元系液相烧结:以超过系统中低熔组分熔点的温度进行的烧结过程.2.烧结机构的内涵及分类:(1)内涵:研究烧结过程中各种可能的物质迁移方式及速率.(2)分类:A. 表面迁移:S—S B. 宏观迁移:V—V C. 粘性流动 D. 塑性流动 E. 晶界扩散 F. 位错管道扩散3.影响烧结的因素:(1) 结晶构造与异晶转变 (2) 粉末活性 (3) 外来物质 (4) 压制压力.4.液相烧结所需满足的条件:(1)满足润湿条件,即润湿角θ<90. (2)固相在液相中有一定的溶解度.5.影响液相烧结过程的因素:(1)粒度(2)颗粒形状(3)粉末颗粒内开孔隙(4)粉末的化学计量(5)低熔点组元的分布均匀性(6)低熔组元的含量(7)压坯密度(8)加热与冷却速度(9)温度与时间(10)气氛6.烧结气氛的作用:(1)防止或减少周围环境对烧结产品的有害反应,从而保证烧结顺利进行和产品质量稳定. (2)排除有害杂质,如吸附气体、表面氧化物或内部夹杂,提高烧结动力,加快烧结速度,而且能改善烧结制品的性能. (3)维持或改变烧结材料中的有用成分,这些成分常常能与烧结金属生成合金或活化烧结过程.7.烧结气氛的分类:氧化性气氛、还原性气氛、惰性或中性气氛、渗碳气氛、氮化气氛.8.活化烧结:指采用化学或物理的措施,使烧结温度降低、烧结过程加快,或使烧结体的密度和其它性能得到提高的方法.9.热压烧结:把粉末装在模腔内,在加压的同时使粉末加热到正常烧结温度或更低一些的温度,经过较短时间烧结成致密而均匀的制品.。
影响粉末体烧结的因素

影响粉末体烧结的因素
影响粉末体烧结的因素主要包括以下几个方面:
1. 粉末粒度:粉末的粒度大小直接影响烧结过程中的粒子间的相互作用力和表面扩散速率。
粉末的细度越高,粒子间的相互作用力越大,烧结速度越快。
2. 粉末成分:粉末的化学成分决定了其烧结温度和烧结过程中的相变行为。
不同成分的粉末在烧结过程中会发生不同的反应,从而影响烧结的结果。
3. 烧结温度:烧结温度是影响烧结过程的重要参数。
过低的烧结温度会导致烧结不完全,粉末颗粒之间的结合力不足;过高的烧结温度会使粉末过烧,颗粒聚结,从而影响材料的性能。
4. 烧结气氛:烧结气氛对烧结过程和烧结产物的影响较大。
不同气氛下的烧结过程会引起不同的物理、化学反应,从而影响烧结产物的组织结构和性能。
5. 烧结时间:烧结时间是指粉末在烧结过程中的暴露时间。
烧结时间过长会导致过度烧结,烧结颗粒之间的结合力过强,从而影响材料的性能;烧结时间过短会导致烧结不完全,颗粒之间结合力不足,影响材料的致密性和力学性能。
6. 烧结压力:烧结过程中施加的压力可以改变粉末的形变、流动和扩散行为,从而影响烧结过程中的粒子间的结合力和材料的微结构。
这些因素的综合作用决定了粉末体烧结的效果和最终材料的性能。
催化剂烧结的原因

催化剂烧结的原因催化剂是一种能够加速化学反应速率的物质,广泛应用于许多工业和科学领域中。
然而,在使用催化剂的过程中,烧结现象经常会发生,这会导致催化剂活性下降、寿命缩短等问题。
本文将从催化剂烧结的原因、影响和预防措施三个方面进行详细介绍。
一、催化剂烧结的原因1.温度:高温是引起催化剂烧结的主要原因之一。
当温度超过某个临界值时,催化剂表面吸附物分子会发生解离并与其他吸附物分子相互作用形成较大的颗粒,从而导致烧结。
2.气体成分:气体成分对催化剂也有很大影响。
例如,一些气体成分可能会与催化剂表面上的活性位点发生反应,并形成不容易挥发的产物,这些产物可能会在表面上积累并导致烧结。
3.湿度:湿度也是引起催化剂烧结的一个重要因素。
在潮湿环境中,催化剂表面上的水分子可能会与吸附物分子相互作用并形成较大的颗粒,从而导致烧结。
4.催化剂本身:催化剂本身也可能导致烧结。
例如,催化剂中的金属颗粒可能会在高温下融合并形成较大的颗粒,从而导致烧结。
5.反应条件:反应条件也是影响催化剂烧结的一个因素。
例如,在高压下进行反应时,催化剂表面上的吸附物分子可能会形成较大的颗粒,并导致烧结。
二、催化剂烧结的影响1.降低活性:当催化剂发生烧结时,其活性会显著下降。
这是因为烧结会使得催化剂表面积减小、孔隙度变小、活性位点数量减少等因素都会影响其活性。
2.缩短寿命:由于烧结引起了活性位点数量减少等问题,因此使用寿命也会受到影响。
这意味着需要更频繁地更换催化剂,并增加生产成本。
3.增加能耗:由于催化剂活性下降,反应速率变慢,因此需要更高的温度和压力来维持反应速率。
这会导致能源消耗的增加。
三、催化剂烧结的预防措施1.降低温度:降低反应温度是避免催化剂烧结的有效方法之一。
通过控制反应温度,可以减少吸附物分子的解离和聚集,从而减缓烧结的发生。
2.改变气体成分:选择合适的气体成分也可以避免催化剂烧结。
例如,在某些情况下,增加氢气浓度可以减少催化剂表面上产生的碳沉积物并避免烧结。
烧结的概念——精选推荐

第十二章烧结(Sinter)第一节基本概念一、烧结1、烧结的意义烧结是粉末冶金、陶瓷、耐火材料、超高温材料等部门的一个重要工序。
烧结的目的是把粉状物料转变为致密体。
这种烧结致密体是一种多晶材料,其显微结构由晶体、玻璃相和气孔组成,烧结过程直接影响显微结构中晶粒尺寸和分布,气孔尺寸和分布以及晶界体积分数….。
烧结过程可以通过控制晶界移动而抑制晶粒的异常生长或通过控制表面扩散、晶界扩散和晶格扩散而充填气孔,用改变显微结构方法使材料性能改善。
因此,当配方、原料粒度、成型等工序完成以后,烧结是使材料获得预期的显微结构以使材料性能充分发挥的关键工序。
2、烧结的定义宏观定义:一种或多种固体(金属、氧化物、氮化物等)粉末经过成型,在加热到一定温度后开始收缩,在低于熔点温度下变成致密、坚硬的烧结体,这种过程称为烧结。
微观定义:由于固态中分子(或原子)的相互吸引,通过加热,使粉末体产生颗粒粘结,经过物质迁移使粉末体产生强度并导致致密化和再结晶的过程。
由于烧结体宏观上出现体积收缩,致密度提高和强度增加,因此烧结程度可以用坯体收缩率、气孔率、吸水率或烧结体密度与理论密度之比(相对密度)等指标来衡量。
3、与烧结有关的一些概念A.烧结与烧成(firing):烧成:包括多种物理和化学变化。
例如脱水、坯体内气体分解、多相反应和熔融、溶解、烧结等。
而烧结仅仅指粉料经加热而致密化的简单物理过程,烧结仅仅是烧成过程的一个重要部分。
B.烧结和熔融(Melt):烧结是在远低于固态物质的熔融温度进行的。
泰曼发现烧结温度(T S)和熔融温度(T M)的关系有一定规律:金属粉末 T S=(0.3~0.4)T M盐类 T S=0.57T M硅酸盐 T S=(0.8~0.9)T M烧结和熔融这两个过程都是由原子热振动而引起的,但熔融时全部组元都为液相,而烧结时至少有一组元是处于固态。
C.烧结与固相反应:两个过程均在低于材料熔点或熔融温度之下进行的。
陶瓷烧结原理
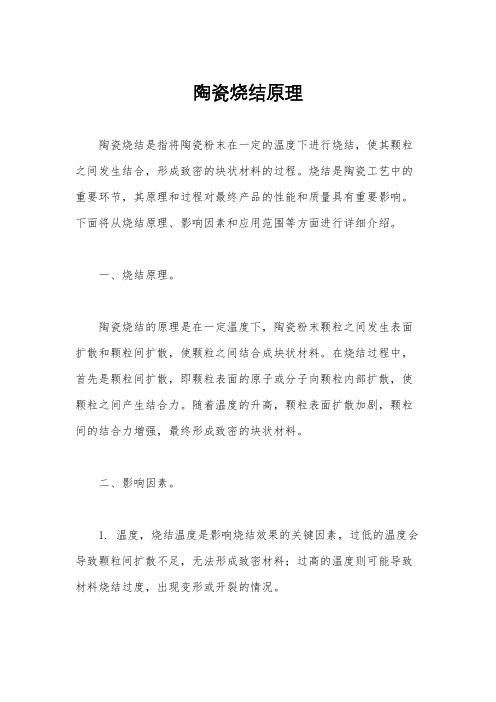
陶瓷烧结原理陶瓷烧结是指将陶瓷粉末在一定的温度下进行烧结,使其颗粒之间发生结合,形成致密的块状材料的过程。
烧结是陶瓷工艺中的重要环节,其原理和过程对最终产品的性能和质量具有重要影响。
下面将从烧结原理、影响因素和应用范围等方面进行详细介绍。
一、烧结原理。
陶瓷烧结的原理是在一定温度下,陶瓷粉末颗粒之间发生表面扩散和颗粒间扩散,使颗粒之间结合成块状材料。
在烧结过程中,首先是颗粒间扩散,即颗粒表面的原子或分子向颗粒内部扩散,使颗粒之间产生结合力。
随着温度的升高,颗粒表面扩散加剧,颗粒间的结合力增强,最终形成致密的块状材料。
二、影响因素。
1. 温度,烧结温度是影响烧结效果的关键因素,过低的温度会导致颗粒间扩散不足,无法形成致密材料;过高的温度则可能导致材料烧结过度,出现变形或开裂的情况。
2. 时间,烧结时间也是影响烧结效果的重要因素,过短的时间会导致烧结不完全,材料性能不达标;过长的时间则可能造成能耗浪费和生产效率低下。
3. 压力,在烧结过程中施加一定的压力可以促进颗粒间的结合,提高烧结效率和材料密度。
4. 添加剂,适量的添加剂可以改善陶瓷粉末的流动性和烧结性能,提高最终产品的质量。
三、应用范围。
陶瓷烧结广泛应用于陶瓷制品的生产过程中,如陶瓷砖、陶瓷器皿、陶瓷瓷砖等。
通过烧结工艺,可以使陶瓷制品具有较高的强度、硬度和耐磨性,满足不同领域的需求。
总结,陶瓷烧结是一项重要的陶瓷加工工艺,其原理是在一定温度下实现颗粒间的结合,影响因素包括温度、时间、压力和添加剂等,应用范围广泛,可用于生产各种陶瓷制品。
掌握烧结原理和技术,对于提高陶瓷制品的质量和性能具有重要意义。
纳米颗粒烧结机理

纳米颗粒烧结机理引言:纳米颗粒烧结是一种重要的材料加工方法,通过高温下的压力和热处理,将纳米颗粒结合成致密的块状材料。
本文将探讨纳米颗粒烧结的机理,包括烧结过程中的原理和影响因素。
一、纳米颗粒烧结的原理纳米颗粒烧结的原理基于固体颗粒之间的扩散和结合过程。
在高温下,纳米颗粒表面的原子会发生扩散,使颗粒之间的接触面积增大。
当颗粒之间的接触面积足够大时,原子会重新排列,形成新的结合界面。
这种界面的形成使得纳米颗粒之间的结合更加牢固,从而形成致密的块状材料。
二、纳米颗粒烧结的影响因素1. 温度:温度是纳米颗粒烧结过程中最重要的影响因素之一。
较高的温度可以促进原子的扩散和结合,从而加快烧结速度。
然而,过高的温度可能导致颗粒的烧结过度,使得材料的性能下降。
2. 压力:压力可以增加颗粒之间的接触力,促进原子的扩散和结合。
适当的压力可以提高烧结的致密度和强度,但过高的压力可能导致颗粒的变形或破碎。
3. 时间:烧结时间是影响纳米颗粒烧结的另一个重要因素。
较长的烧结时间可以使得颗粒之间的结合更加牢固,但过长的时间可能导致能量浪费和生产效率的降低。
4. 纳米颗粒的性质:纳米颗粒的形状、大小和表面性质都会影响烧结过程。
较小的颗粒通常具有更高的表面能,需要更高的温度和压力才能实现有效的烧结。
此外,表面修饰和添加剂的引入也可以改善烧结效果。
三、纳米颗粒烧结的应用纳米颗粒烧结技术在材料科学和工程领域具有广泛的应用前景。
以下是一些典型的应用领域:1. 陶瓷材料:纳米颗粒烧结可以用于制备高性能的陶瓷材料,如氧化铝、氧化锆等。
通过控制烧结条件和添加适当的添加剂,可以获得具有优异力学性能和高温稳定性的陶瓷材料。
2. 金属材料:纳米颗粒烧结也可以用于制备金属材料,如铜、铁等。
通过烧结过程中的原子扩散和结合,可以获得高密度和高强度的金属材料。
3. 磁性材料:纳米颗粒烧结可以用于制备磁性材料,如氧化铁、钕铁硼等。
通过控制烧结条件和添加适当的添加剂,可以获得具有优异磁性性能的材料。
液相烧结影响因素
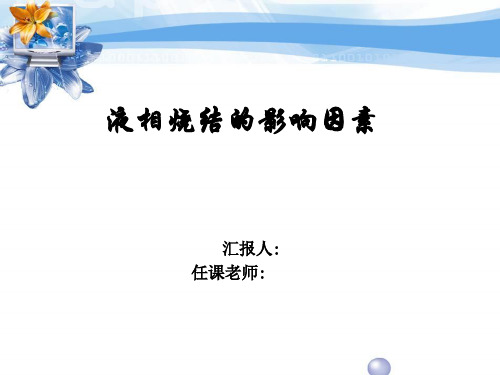
• 对于冷切速度快慢的优劣,应根据具体的情况的不同进行选择: (1)冷却速度过快,基体中的合金化元素越容易达到饱和,因此得到的 烧结强度越高,但在液相的凝固温度下,容易形成孔隙,因此,过快的 冷却速度是有害的。 (2)冷却速度可以控制杂质的析出。由于杂质可以降低界面能,因此将 优先在界面处偏析,从而造成制品的脆性,因此快速冷却是有好处的。
• 如右图所示
•
由于添加剂的颗粒大小控制着添加剂颗粒的原来位置所形成 的孔隙的大小,因此,应该选用具有小而均匀的颗粒尺寸的 添加剂。
对于液相烧结会产生膨胀的系统,使用小颗粒和提高加热速 度可以使得膨胀量最小,达到最好的致密化。
3.粉末内部的孔隙
• 在液相烧结过程中,液相将首先进入固体颗 粒内部的孔隙,从而减小了颗粒之间液相的 数量。由于颗粒内部孔隙的体积小于颗粒之 间孔隙的体积,因此颗粒内部孔隙中液体的 毛细作用要比颗粒之间孔隙中液体的毛细作 用大得多。因此,不同材料或相同材料不同 状态下,粉末孔隙的多少以及他们的分布影 响材料的烧结。
二.粉末的特性
1.颗粒的形状
• 颗粒的形状在压坯的成形阶段和在液相烧结的颗粒重新排列阶段 具有重要作用。
• 压坯成形阶段 颗粒不均匀 颗粒间摩擦力增大 生坯的密度减小 烧结的密
度降低。 • 重新排列阶段
颗粒的形状变化 排布期间毛细管力的变化。 通常,球形对毛细 管力的作用比较敏感。 形状复杂导致颗粒重排阻力增加,故球形颗粒有利于颗粒重排。 不规则形状的颗粒粉末比使用球形的颗粒粉末所得到的烧结显微组 织的不均匀性要大得多,从而造成制品性能的降低。 • 在液相烧结的后期阶段,由于溶解-再析出作用,颗粒形状将变化,
烧结影响因素
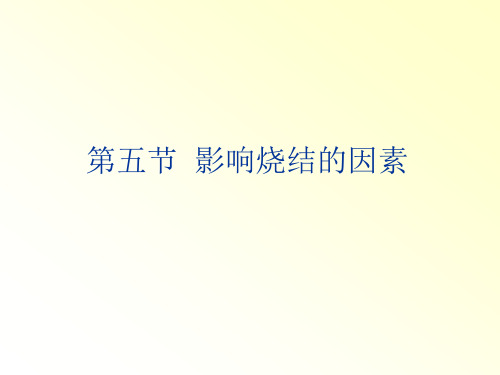
二.外加剂的作用
1.外加剂与烧结主体形成固溶体 形成固溶体,主晶相晶格畸变,缺陷增加,便 于结构基元的移动而促进烧结。 一般地说有限置换型固溶体比连续固溶体更有 助于促进烧结。外加剂离子的电价和半径与烧结主 体离子的电价、半径相差愈大,使晶格畸变程度增 加,促进烧结的作用也愈明显。 Al2O3烧结时,加入Cr203形成连续固溶体可以在 1860℃烧结,而加入1%一2%TiO:只需在1600℃左 右就能致密化。
5.外加剂起扩大烧结范围的作用
三.烧结温度与保温时间
四.盐类的选择及其煅烧条件 五.气氛的影响:与扩散控制的因素有关,与
气孔内气体和扩散和溶解度有关.
六.成型压力的影响
2.外加剂与烧结主体形成液相
液相中扩散传质阻力小、流动传质速度快。 降低烧结温度,提高致密度。 高温下形成镁铝尖晶石而包裹在氧化铝晶 粒表面,抑制品界移动运动,充分排除晶界 上的气孔,对促进坯体致密化有显著作用。
3.外加剂与烧结主体形成化合物
4.外加剂阻止多晶转变 CaO加入到ZrO2,阻止多晶转变,促进烧结。
第五节 影响烧ห้องสมุดไป่ตู้的因素
一.原始粉料的粒度
在固态或液态的烧结 中,r越小,x/r越大. 1.细颗粒增加烧结的推 动力; 2. 缩短了原子扩散距 离; 3.提高颗粒在液相中的 溶解度。
起始粒径细而均匀,可防止二次再结晶,最
适宜的粉末粒度为0.05一0.5um, 原料粉末的粒度不同,烧结机理可能不同。 A1N烧结粒度为0.78-4.4um时,粗颗粒按体积 扩散机理进行烧结,而细颗粒则按晶界扩散 或表面扩散机理进行烧结。
第九章-烧结分析

烧
再
概
结
结
过
晶
程
和
及
晶
述
机
粒
理
长
大
影 响 烧 结 的 因 素
§9.1 概述
烧结过程是一门古老的工艺,早在公元前3000 年,人类就掌握了这门工艺,但对烧结理论的研 究和发展仅开始于20世纪中期。现在,烧结过程 在许多工业部门得到广泛应用,如陶瓷、耐火材 料、粉末冶金、超高温材料等生产过程中都含有 烧结过程。
F v
S
x
式中,τ是极限剪切力。
烧结时的粘性流动和塑性流动都会出现 在含有固、液两相的系统。当液相量较大并 且液相粘度较低时,是以黏性流动为主;而 当固相量较多或粘度高时则以塑性流动为主。
⑵ 扩散传质(固相烧结传质方式)
扩散传质是指质点(或空位)借助于浓度梯度推动而迁 移的传质过程。烧结初期由于粘附作用使粒子间的接触 界面逐渐扩大并形成具有负曲率的接触区(颈部)。在 表面张力的作用下,所产生的附加压力使颈部的空位浓 度比离子其他部位的浓度大,存在一个过剩空位浓度。
度提高。
二、烧结推动力
粉体颗料尺寸很小,比表面积大,具有 较高的表面能,即使在加压成型体中,颗料 间接面积也很小,总表面积很大而处于较高 能量状态。根据最低能量原理,它将自发地 向最低能量状态变化,使系统的表面能减少。
烧结是一个自发的不可逆过程,系统表面 能降低是推动烧结进行的基本动力。
表面张力能使凹、凸表面处的蒸气压P分别低 于和高于平面表面处的蒸气压Po,并可以用开尔 文本公式表达:
粘性流动传质 : 若存在着某种外力场,如表面张力作用时,
则质点(或空位)就会优先沿此表面张力作用的
方向移动,并呈现相应的定向物质流,其迁移