如何利用控制图进行分析
化学分析实验室利用控制图进行内部质量控制

化学分析实验室利用控制图进行内部质量控制化学分析实验室是一个重要的实验室,它负责对各种化学样品进行分析和检测,以确保产品和环境的安全。
在实验室的工作中,内部质量控制是非常重要的,因为它可以帮助实验室监控实验过程中的任何变化,及时发现问题,并采取相应的措施。
在这方面,控制图是一种非常有效的工具,可以帮助实验室进行内部质量控制,本文将介绍化学分析实验室如何利用控制图进行内部质量控制。
一、控制图概述控制图是一种用于监测过程稳定性和识别异常的统计工具,它通过图形化表示过程数据的变化趋势,可以帮助人们更直观地了解过程的状态。
在化学分析实验室中,常用的控制图有X-条图、R-图、P-图和C-图等,它们分别适用于不同类型的过程数据。
X-条图用于监控过程的中心线变化,R-图用于监控过程的离散程度,P-图和C-图则用于监控不合格品的比例和计数。
通过对这些控制图的分析,可以及时发现过程中的问题,确保实验结果的准确性和可靠性。
二、控制图在化学分析实验室的应用1.监控分析结果的精确性和准确性在化学分析实验室中,实验过程中的数据变化会直接影响到分析结果的精确性和准确性,因此需要通过控制图来监控实验过程中的数据变化。
实验室对某种化学物质的含量进行分析,可以通过X-条图来监控每批样品分析结果的中心线变化,及时发现分析结果偏离了期望值,从而及时调整实验条件,保证分析结果的准确性。
2.监控实验过程中的不确定性三、控制图的建立和应用流程1.确定监控对象和目标在建立和应用控制图之前,首先需要确定监控对象和目标。
监控对象是指需要监控的过程数据,可以是实验结果的中心线变化、离散程度、不合格品的比例或计数等,而监控目标则是为了保证分析结果的准确性和可靠性。
根据监控对象和目标的不同,可以选择合适的控制图来进行监控。
2.收集和整理数据在确定监控对象和目标后,需要对实验过程中的数据进行收集和整理。
这些数据包括实验结果的测量值、标准偏差、不合格品的比例或计数等,通过对这些数据的分析,可以建立控制图,并确定控制限。
品质管理中的控制图分析方法

品质管理中的控制图分析方法控制图是品质管理中的一种重要工具,用于监控和改进过程的稳定性和可预测性。
控制图帮助企业追踪和分析过程数据,以便及时发现并纠正潜在问题,避免质量偏差和产品不合格。
下面将介绍几种常用的控制图分析方法。
1. 均值-范围控制图(X-bar R图)均值-范围控制图是用于监测过程平均值和变异性的控制图方法。
它由两个部分组成:均值控制图(X-bar图)和范围控制图(R图)。
均值控制图用来监控过程的平均值是否稳定,范围控制图用于监控过程的变异性。
通过同时使用这两个图,可以追踪过程的整体性能和特殊因素的影响。
2. 均值-极差控制图(X-bar S图)均值-极差控制图也是一种监测过程平均值和变异性的方法。
它由两个部分组成:均值控制图(X-bar图)和极差控制图(S图)。
均值控制图用于监测过程的平均值是否稳定,极差控制图用于监测过程的变异性。
与X-bar R图相比,X-bar S图更适用于样本容量较小或样本规模不一致的情况。
3. P控制图P控制图用于监测过程中的百分比或比例。
它是一种二项分布的控制图方法,适用于二分类的数据(如合格/不合格、良品/次品)。
P值是指在一次观察中发生某一事件的概率。
P控制图通过监测P值的变化来判断过程的稳定性。
4. C控制图C控制图是对计数型数据(如缺陷数量、不良品数量)进行控制的一种方法。
C值是指在一次观察中发生某一事件的次数,如一个产品中的缺陷数量。
C控制图通过监测C值的变化来判断过程的稳定性。
与P控制图相比,C控制图更适用于缺陷发生率较低的情况。
5. 过程能力指数(Cp、Cpk)过程能力指数是评估过程能力的一种方法。
Cp是用于评估过程在规范限制范围内的能力,它考虑到了过程的稳定性和分布的偏移程度。
Cpk是用于评估过程在规范限制范围内的中心情况和离散情况,它考虑到了过程的稳定性、分布的偏移程度和偏移的影响程度。
这两个指数可以帮助企业判断过程是否满足客户要求,并确定是否需要改进过程。
控制图的原理及应用图解
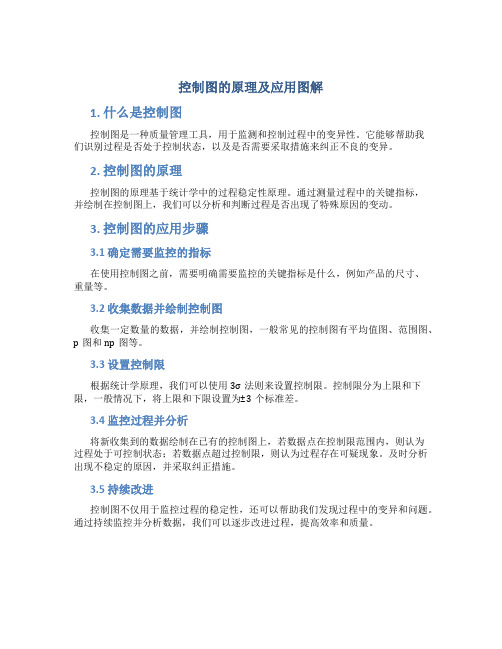
控制图的原理及应用图解1. 什么是控制图控制图是一种质量管理工具,用于监测和控制过程中的变异性。
它能够帮助我们识别过程是否处于控制状态,以及是否需要采取措施来纠正不良的变异。
2. 控制图的原理控制图的原理基于统计学中的过程稳定性原理。
通过测量过程中的关键指标,并绘制在控制图上,我们可以分析和判断过程是否出现了特殊原因的变动。
3. 控制图的应用步骤3.1 确定需要监控的指标在使用控制图之前,需要明确需要监控的关键指标是什么,例如产品的尺寸、重量等。
3.2 收集数据并绘制控制图收集一定数量的数据,并绘制控制图,一般常见的控制图有平均值图、范围图、p图和np图等。
3.3 设置控制限根据统计学原理,我们可以使用3σ法则来设置控制限。
控制限分为上限和下限,一般情况下,将上限和下限设置为±3个标准差。
3.4 监控过程并分析将新收集到的数据绘制在已有的控制图上,若数据点在控制限范围内,则认为过程处于可控制状态;若数据点超过控制限,则认为过程存在可疑现象。
及时分析出现不稳定的原因,并采取纠正措施。
3.5 持续改进控制图不仅用于监控过程的稳定性,还可以帮助我们发现过程中的变异和问题。
通过持续监控并分析数据,我们可以逐步改进过程,提高效率和质量。
4. 控制图的应用场景4.1 制造业在制造业中,控制图可以帮助企业监测生产线上的关键指标,例如产品尺寸、重量等。
通过控制图的分析,所产生的数据可以作为制造流程改进的依据。
4.2 服务业在服务业中,控制图可以用于监控服务质量。
例如餐饮行业使用控制图来监控食品加工过程中的关键环节,以确保食品质量符合标准。
4.3 医疗行业在医疗行业中,控制图可以用于监控医疗流程的关键环节。
例如手术室使用控制图来监控手术过程中的关键指标,以确保手术质量和安全。
4.4 金融行业在金融行业中,控制图可以用于监控交易过程中的关键指标,例如交易时间、成功率等。
通过控制图的应用,可以帮助金融机构提高交易效率和降低风险。
化学分析实验室利用控制图进行内部质量控制
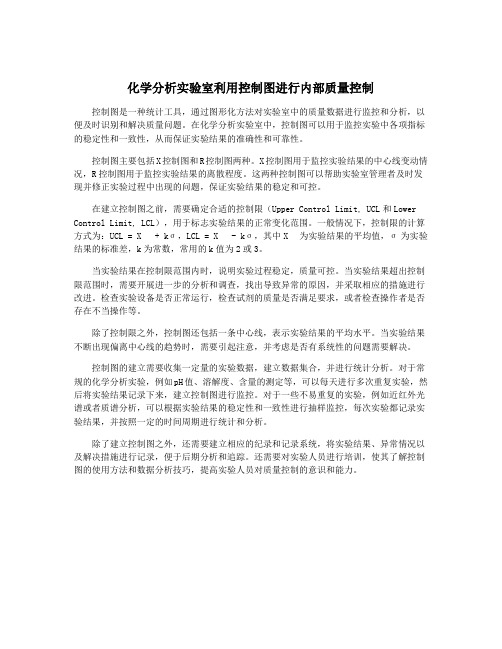
化学分析实验室利用控制图进行内部质量控制控制图是一种统计工具,通过图形化方法对实验室中的质量数据进行监控和分析,以便及时识别和解决质量问题。
在化学分析实验室中,控制图可以用于监控实验中各项指标的稳定性和一致性,从而保证实验结果的准确性和可靠性。
控制图主要包括X控制图和R控制图两种。
X控制图用于监控实验结果的中心线变动情况,R控制图用于监控实验结果的离散程度。
这两种控制图可以帮助实验室管理者及时发现并修正实验过程中出现的问题,保证实验结果的稳定和可控。
在建立控制图之前,需要确定合适的控制限(Upper Control Limit, UCL和Lower Control Limit, LCL),用于标志实验结果的正常变化范围。
一般情况下,控制限的计算方式为:UCL = X̄ + kσ,LCL = X̄ - kσ,其中X̄为实验结果的平均值,σ为实验结果的标准差,k为常数,常用的k值为2或3。
当实验结果在控制限范围内时,说明实验过程稳定,质量可控。
当实验结果超出控制限范围时,需要开展进一步的分析和调查,找出导致异常的原因,并采取相应的措施进行改进。
检查实验设备是否正常运行,检查试剂的质量是否满足要求,或者检查操作者是否存在不当操作等。
除了控制限之外,控制图还包括一条中心线,表示实验结果的平均水平。
当实验结果不断出现偏离中心线的趋势时,需要引起注意,并考虑是否有系统性的问题需要解决。
控制图的建立需要收集一定量的实验数据,建立数据集合,并进行统计分析。
对于常规的化学分析实验,例如pH值、溶解度、含量的测定等,可以每天进行多次重复实验,然后将实验结果记录下来,建立控制图进行监控。
对于一些不易重复的实验,例如近红外光谱或者质谱分析,可以根据实验结果的稳定性和一致性进行抽样监控,每次实验都记录实验结果,并按照一定的时间周期进行统计和分析。
除了建立控制图之外,还需要建立相应的纪录和记录系统,将实验结果、异常情况以及解决措施进行记录,便于后期分析和追踪。
控制图的原理及应用
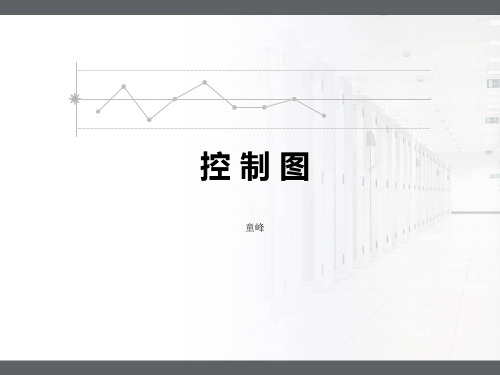
常态(正态)分布
=P[Z>z]
0
z
原则常态分布右边机率值
Z
Z
Z
0.00
0.500000000
1.50
0.066807201
3.00
0.001349898
0.01
0.496010644
1.51
要永久维持制造过程很正常旳生产,不让波动旳事项发生,
几乎是不可能旳。但当波动发生时,应立即查出原因,并加
以根除,或改善。
须调查原因
“波动”
成Resul果t
控制上限
控制下限
Time
波动分类 一般原因 特殊原因
出现次数 次数多
次数甚少
影响 微小 明显
结论 不值得调查原因 值得彻底调查其原因
明显旳波动,显示有特殊原因存在。假如做得到旳话,应加 以鉴定及矫正。控制界线以经济旳方式区别了这两种波动。
平衡曲线示意图
发生机率
UCL
α
β
LCL 一.第一种错误:虚发警报 二.第二种错误:漏发警报
第一种错误
第二种错误
1δ 2δ 3δ 4δ 5δ 6δ
利用经济平衡点措施求得,两种错误旳经济点:在±3δ处是最经济旳控制界 线
五、控制图旳应用
5.1 、控制图旳作用 5.2 、控制图旳分类 5.3 、控制图旳选用原则 5.4 、控制图旳计算 5.5 、控制图旳判断
LCL
第一种错误(α):生产者冒险率
生产质量相当良好,已到达允收水平,理应判为合格,但因为 控制线设置过窄,造成合格品误判为异常,其机率称为生产 者冒险率,所以种错误使生产者蒙受损失故得名之. 此冒险率又称为第一种错误 (TYPE Ⅰ ERROR) 简称(α).
服务业如何运用控制图来监控服务质量

服务业如何运用控制图来监控服务质量?控制图,最初起源于制造业,用于监控生产过程中的质量波动,确保产品符合预定标准。
然而,其原理同样适用于服务业,成为衡量和监控服务质量的得力助手。
通过收集关键服务指标的数据(如客户满意度、服务响应时间、投诉率等),运用控制图进行分析,可以直观展示服务质量的稳定性及异常波动,为管理者提供及时、准确的决策依据。
具体步骤如天行健六西格玛顾问下文所述:一、确定关键质量指标首先,需要确定能够反映服务质量的关键指标。
这些指标可以包括客户满意度、服务响应时间、错误率、投诉率等。
根据服务的特点和目标,选择合适的关键质量指标进行监控。
二、收集数据1. 确定数据收集方法可以通过问卷调查、客户反馈、内部记录等方式收集数据。
确保数据收集方法的准确性和可靠性,以便后续分析。
2. 设定数据收集频率根据服务的性质和需求,确定数据收集的频率。
对于高频率的服务,可以每天或每周收集数据;对于低频率的服务,可以每月或每季度收集数据。
三、绘制控制图1. 选择控制图类型根据数据的类型和特点,选择合适的控制图类型。
常见的控制图类型有均值-极差控制图(X-R 图)、均值-标准差控制图(X-S 图)、单值-移动极差控制图(I-MR 图)等。
2. 计算控制限根据收集的数据,计算控制图的中心线和控制限。
中心线通常是数据的平均值,控制限可以通过统计方法计算得出。
3. 绘制控制图将收集的数据绘制在控制图上,包括中心线、上控制限和下控制限。
根据数据的时间顺序,依次将数据点绘制在控制图上,以便观察数据的变化趋势。
四、监控服务质量1. 观察控制图定期观察控制图,查看数据点是否在控制限内。
如果数据点在控制限内,说明服务质量处于稳定状态;如果数据点超出控制限,说明服务质量出现了异常。
2. 分析异常情况当发现数据点超出控制限时,需要进行分析,找出导致异常的原因。
可以使用鱼骨图、帕累托图等工具进行分析,确定问题的根本原因。
3. 采取纠正措施根据分析结果,采取相应的纠正措施,解决服务质量问题。
控制图的设计与分析

控制图的设计与分析控制图是一种用于监测过程稳定性和控制过程变异性的工具。
通过收集和分析过程数据,控制图能够帮助我们判断过程是否处于控制状态,并提供信息帮助我们识别问题的根本原因。
控制图的设计与分析涉及到以下几个关键步骤:1. 确定需要监控的过程特性在设计控制图之前,我们首先需要明确需要监控的过程特性。
这个过程特性可以是一个关键的输出变量,也可以是一个关键的输入变量,取决于我们关注的问题。
例如,我们可能关注产品的重量、尺寸、质量等特性,或者关注生产过程中的温度、压力、湿度等变量。
2. 收集过程数据为了设计和分析控制图,我们需要收集过程数据。
这些数据可以通过实时监测系统、实验设计、抽样和测量等方式获取。
数据的收集应该尽可能全面和准确,以确保可靠的分析结果。
3. 绘制控制图在收集到足够的过程数据后,我们可以开始绘制控制图。
常用的控制图有均值图(X-bar chart)、极差图(R chart)、标准差图(S chart)、过程能力图(Cp/Cpk chart)等。
控制图一般由中心线、控制限和数据点组成。
中心线代表过程的平均水平,控制限则用于判断过程的稳定性。
在绘制控制图时,我们需要计算出相应的统计指标,例如,均值、极差、标准差等。
这些统计指标可以帮助我们了解过程的中心位置、变异程度以及能力。
4. 分析控制图绘制完控制图后,我们需要对图形进行分析。
一个稳定的过程应该在控制限范围内波动。
如果过程超出了控制限,则表示过程出现了变异,并且可能需要进行进一步的调查和改进。
具体分析控制图的方法包括以下几个方面:•判断过程是否处于控制状态:我们可以通过观察控制图上的数据点,判断是否有异常变动、趋势或连续出现的数据点等。
如果过程处于控制状态,我们可以认为过程是稳定的。
•判断过程的变异情况:控制图上的控制限能够帮助我们识别过程的变异情况。
较大的控制限表示过程的变异较大,而较小的控制限则表示过程的变异较小。
我们可以通过比较数据点与控制限的位置关系,来判断过程的变异是否处于可接受的范围内。
控制图的工作原理及应用
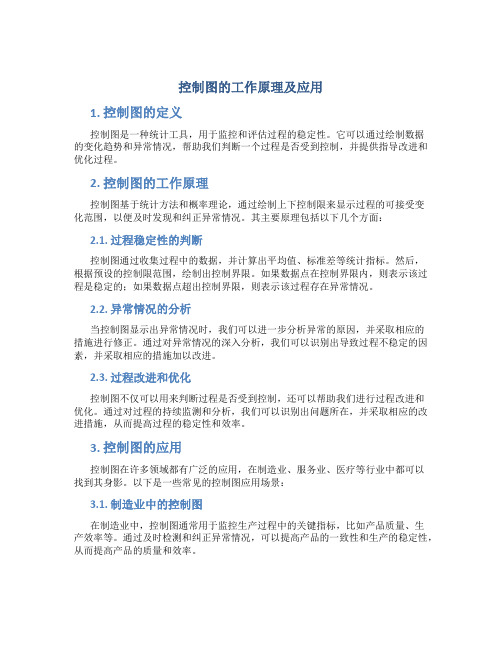
控制图的工作原理及应用1. 控制图的定义控制图是一种统计工具,用于监控和评估过程的稳定性。
它可以通过绘制数据的变化趋势和异常情况,帮助我们判断一个过程是否受到控制,并提供指导改进和优化过程。
2. 控制图的工作原理控制图基于统计方法和概率理论,通过绘制上下控制限来显示过程的可接受变化范围,以便及时发现和纠正异常情况。
其主要原理包括以下几个方面:2.1. 过程稳定性的判断控制图通过收集过程中的数据,并计算出平均值、标准差等统计指标。
然后,根据预设的控制限范围,绘制出控制界限。
如果数据点在控制界限内,则表示该过程是稳定的;如果数据点超出控制界限,则表示该过程存在异常情况。
2.2. 异常情况的分析当控制图显示出异常情况时,我们可以进一步分析异常的原因,并采取相应的措施进行修正。
通过对异常情况的深入分析,我们可以识别出导致过程不稳定的因素,并采取相应的措施加以改进。
2.3. 过程改进和优化控制图不仅可以用来判断过程是否受到控制,还可以帮助我们进行过程改进和优化。
通过对过程的持续监测和分析,我们可以识别出问题所在,并采取相应的改进措施,从而提高过程的稳定性和效率。
3. 控制图的应用控制图在许多领域都有广泛的应用,在制造业、服务业、医疗等行业中都可以找到其身影。
以下是一些常见的控制图应用场景:3.1. 制造业中的控制图在制造业中,控制图通常用于监控生产过程中的关键指标,比如产品质量、生产效率等。
通过及时检测和纠正异常情况,可以提高产品的一致性和生产的稳定性,从而提高产品的质量和效率。
3.2. 服务业中的控制图在服务业中,控制图可以用于监控和评估服务质量,比如客户满意度、服务响应时间等。
通过对服务过程的持续监测和分析,可以及时发现服务异常和瓶颈,从而提供更好的服务体验。
3.3. 医疗中的控制图在医疗领域中,控制图可以用于监控和评估医疗过程中的关键指标,比如手术成功率、医疗事故率等。
通过对医疗过程的监测和分析,可以及时发现潜在的风险和问题,并采取措施加以修正,从而提高医疗质量和安全性。
- 1、下载文档前请自行甄别文档内容的完整性,平台不提供额外的编辑、内容补充、找答案等附加服务。
- 2、"仅部分预览"的文档,不可在线预览部分如存在完整性等问题,可反馈申请退款(可完整预览的文档不适用该条件!)。
- 3、如文档侵犯您的权益,请联系客服反馈,我们会尽快为您处理(人工客服工作时间:9:00-18:30)。
如何利用控制图进行分析
一、机械行业成功案例
某机械制造集团由于成立较早,内部流程复杂,存在响应速度慢、非增值活动多、库存及产品交付周期长等问题。
为了更快地供应合格的产品,缩短产品的制造周期,在合规的前提下使用更低的成本,更快地响应速度以增加产品的市场竞争力,企业急需改善质量管理。
实施QSmart SPC Monitor质量管理系统改善优化后,机械制造集团提高了效率,降低了库存,减少了浪费。
在保证产品质量的前提下,增加经济效益60余万元,同时增强了跨部门的协作,最终增强了公司对市场的适应能力和公司在行业中的竞争能力,巩固了该集团亚太地区机械零件生产供应基地的地位。
二、休哈特SPC控制图与过程能力
质量改进团队面对庞大的生产集团,最常提出的问题之一便是“过程能力”。
有些成员人为“这一过程本身就不能满足规格的要求”。
不同意的人主张“该过程能力没有问题,只是运行的不好”。
在最近几十年,人们设计了许多工具以检验这类说法,尤其是应用于生产过程中。
一个普遍的测试过工程能力的方法便是“休哈特控制图”。
数据通常以相同时间间隔从过程中抽取出来。
由控制图分析确定过程处于稳定状态后,将数据与规格条件进行比较。
这一比较得出了一个量度,衡量了过程持续产出规定界限内结果的能力。
许多这类过程是这样的一种序列,其中的工作以一种顺序的方式从一个部门流到另一个部门。
一个循环会花费好几天(或几周,甚至几个月),但完成工作的时间却只用几个小时。
其余的时间都是在个步骤上的等待、返工等构成的。
对于这样的过程,理论上的过程能力是累加工作时间。
如果某个人经过训练能够完成所有的步骤,能够利用所有的数据库,这个人可能会达到这个理论能力。
这些公司将缩短运转周期时间的目标设定为理论过程能力的两倍。
三、过程能力分解
分析一个能力充分的过程为什么不能正常运转,有一种常用的方法称为“过程分解”。
这种方法试图到过程中的源头去对缺陷进行探索,过程的分解有多种形式。
中间测试阶段
当过程尾端出现缺陷时,并不知道是哪个步骤所造成的。
这种情况下,一种有用的方法是在中间阶段的步骤对产品进行检验或测试以找出最初出现缺陷的步骤。
这一寻找如果成功的话,会大大减少验证推测所需的努力。
流-流分析
大批量产品通常要求有多个生产源头(称为流),如多个供应商、多个及其、多个轮班和工人等。
这些流看起来似乎没什么区别,但生产出的产品却不尽然。
流-流分析就是把生产分解为最初的流,测定流与流之间的区别,以期找出导致缺陷发生的流。
时间-时间分析
分解过程的另一种方法是时间-时间分析。
目的是发现缺陷是否集中在特定的时间范围内。
这一分析被用于分析异变间时间、工作轮班变动的效果、年中季节的影响,以及许多此类的潜在原因。
一个常见的时间-时间分析的例子是休哈特控制图,即SPC控制图。
它能够显示出生产过程的变异是由于随机性的还是系统性的原因引起的。
时间-时间变化的一种特殊的情况是漂移,即过程某个方面的持续恶化。
例如在生产过程中,化学溶液会变得越来越稀,工具会逐渐磨损,工人会变得疲劳等。
四、质量改进日益重要
20世纪80年代初期,由于质量不良,在美国约有三分之一的工作是对以往所做的工作的返工。
人们普遍认识到这样的浪费不应该再继续下去,因为它大大削弱了在成本方面的竞争力。
近几十年来的经验教训使得人们在质量管理的地位、所面临的机会和威胁以及必须采取什么行动方面正在形成共识。
顾客越来越强烈地要求供应商改进质量。
这种要求遍及整个供应链。
顾客不仅要求改进产品,而且还要求改进质量管理体系。
文章开始提到的某机械生产集团通
过产品检验以避免不合格产品流入顾客手中。
尽管如此,一个大客户仍要求该公司改进其质量管理体系,并一次作为继续签约的条件,从而安装QSmart SPC Monitor质量管理系统,实现实时监控,自动分析,提前预警,数据共享的基础。