内应力的产生及解决对策
内应力的产生及消除方法
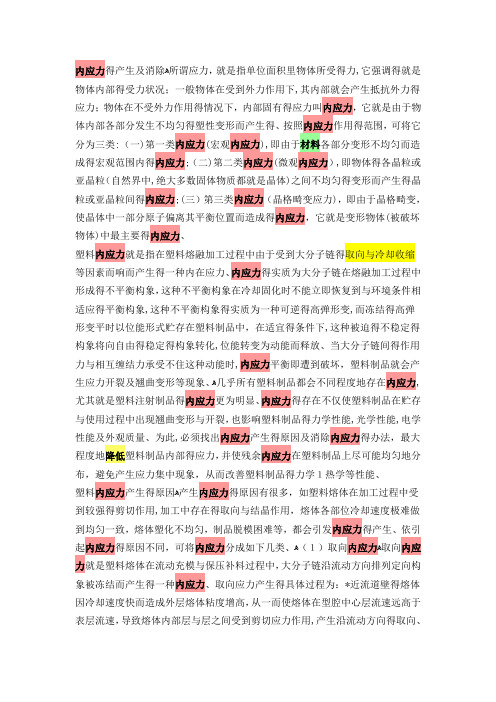
内应力得产生及消除ﻫ所谓应力,就是指单位面积里物体所受得力,它强调得就是物体内部得受力状况;一般物体在受到外力作用下,其内部就会产生抵抗外力得应力;物体在不受外力作用得情况下,内部固有得应力叫内应力,它就是由于物体内部各部分发生不均匀得塑性变形而产生得、按照内应力作用得范围,可将它分为三类:(一)第一类内应力(宏观内应力),即由于材料各部分变形不均匀而造成得宏观范围内得内应力;(二)第二类内应力(微观内应力),即物体得各晶粒或亚晶粒(自然界中,绝大多数固体物质都就是晶体)之间不均匀得变形而产生得晶粒或亚晶粒间得内应力;(三)第三类内应力(晶格畸变应力),即由于晶格畸变,使晶体中一部分原子偏离其平衡位置而造成得内应力,它就是变形物体(被破坏物体)中最主要得内应力、塑料内应力就是指在塑料熔融加工过程中由于受到大分子链得取向与冷却收缩等因素而响而产生得一种内在应力、内应力得实质为大分子链在熔融加工过程中形成得不平衡构象,这种不平衡构象在冷却固化时不能立即恢复到与环境条件相适应得平衡构象,这种不平衡构象得实质为一种可逆得高弹形变,而冻结得高弹形变平时以位能形式贮存在塑料制品中,在适宜得条件下,这种被迫得不稳定得构象将向自由得稳定得构象转化,位能转变为动能而释放、当大分子链间得作用力与相互缠结力承受不住这种动能时,内应力平衡即遭到破坏,塑料制品就会产生应力开裂及翘曲变形等现象、ﻫ几乎所有塑料制品都会不同程度地存在内应力,尤其就是塑料注射制品得内应力更为明显、内应力得存在不仅使塑料制品在贮存与使用过程中出现翘曲变形与开裂,也影响塑料制品得力学性能,光学性能,电学性能及外观质量、为此,必须找出内应力产生得原因及消除内应力得办法,最大程度地降低塑料制品内部得应力,并使残余内应力在塑料制品上尽可能均匀地分布,避免产生应力集中现象,从而改善塑料制品得力学1热学等性能、塑料内应力产生得原因ﻫ产生内应力得原因有很多,如塑料熔体在加工过程中受到较强得剪切作用,加工中存在得取向与结晶作用,熔体各部位冷却速度极难做到均匀一致,熔体塑化不均匀,制品脱模困难等,都会引发内应力得产生、依引起内应力得原因不同,可将内应力分成如下几类、ﻫ(1)取向内应力ﻫ取向内应力就是塑料熔体在流动充模与保压补料过程中,大分子链沿流动方向排列定向构象被冻结而产生得一种内应力、取向应力产生得具体过程为:*近流道壁得熔体因冷却速度快而造成外层熔体粘度增高,从一而使熔体在型腔中心层流速远高于表层流速,导致熔体内部层与层之间受到剪切应力作用,产生沿流动方向得取向、取向得大分子链冻结在塑料制品内也就意味着其中存在未松弛得可逆高弹形变,所以说取向应力就就是大分子链从取向构象力图过渡到无取向构象得内力、用热处理得方法,可降低或消除塑料制品内得取向应力、ﻫ塑料制品得取向内应力分布为从制品得表层到内层越来越小,并呈抛物线变化、2(ﻫ)冷却内应力ﻫ冷却内应力就是塑料制品在熔融加工过程中因冷却定型时收缩不均匀而产生得一种内应力、尤其就是对厚壁塑料制品,塑料制品得外层首先冷却凝固收缩,其内层可能还就是热熔体,这徉芯层就会限制表层得收缩,导致芯层处于压应力状态,而表层处于拉应力状态、ﻫ塑料制品冷却内应力得分布为从制品得表层到内层越来越大,并也呈抛物线变化、、ﻫ另外,带金属嵌件得塑料制品,由于金属与塑料得热胀系数相差较大,容易形成收缩不一均匀得内应力、ﻫ除上述两种主要内应力外,还有以下几种内应力:对于结晶塑料制品而言,其制品内部各部位得结晶结构与结晶度不同也会产生内应力、另外还有构型内应力及脱模内应力等,只就是其内应力听占比重都很小、ﻫ影响塑料内应力产生得因素(1)分子链得刚性分子链刚性越大,熔体粘度越高,聚合物分子链活动性差,因而对于发生得可逆高弹形变恢复性差,易产生残余内应力口例如,一些分子链中含有苯环得聚合物,如PC,PPO,PPS等,其相应制品得内应力偏大、(2)分子链得极性一分子链得极性越大,分子间相互吸引得作用力越大,从而使分子间相互移动困难增大,恢复可逆弹性形变得程度减小,导致残余内应力大、例如,一些分子链中含有羰基,酯基,睛基等极性基团得塑料品种,其相应制品得内应力较大、(3)取代基团得位阻效应大分子侧基取代基团得体积越大,则妨碍大分子链自由运动导致残余内应力加大、例如,聚苯乙烯取代基团得苯基体积较大,因而聚苯乙烯制品得内应力较大、几种常见聚合物得内应力大小顺序如下:ﻫPPO>PSF>PC〉ABS>PA6>PP>HDPE塑料内应力得降低与分散(1)原料配方设计1)选取分子量大,分子量分布窄得树脂聚合物分子量越大,大分子链间作用力与缠结程度增加,其制品抗应力开裂能力较强;聚合物分子量分布越宽,其中低分子量成分越大,容易首先形成微观撕裂,造成应力集中,便制品开裂、ﻫ2)选取杂质含量低得树脂聚合物内得杂质即就是应力得集中体,又会降低塑料得原有强度,应将杂质含量减少到最低程度、ﻫ3)共混改性易出现应力开裂得树脂与适宜得其它树脂共混,可降低内应力得存在程度、ﻫ例如,在PC中混入适量PS,PS呈近似珠粒状分散于PC连续相中,可使内应力沿球面分散缓解并阻止裂纹扩展,从而达到降低内应力得目得、再如,在PC中混入适量PE ,PE球粒外沿可形成封闭得空化区,也可适当降低内应力、4ﻫ)增强改性ﻫ用增强纤维进行增强改性,可以降低制品得内应力,这就是因为纤维缠结了很多大分子链,从而提高应力开裂能力、例如,30%GFPC得耐应力开裂能力比纯PC提高6倍之多、ﻫ5)成核改性ﻫ在结晶性塑料中加入适宜得成核剂,可以在其制品中形成许多小得球晶,使内应力降低并得到分散、2(ﻫ)成型加工条件得控制在塑料制品得成型过程中,凡就是能减小制品中聚合物分子取向得成型因素都能够降低取向应力;凡就是能使制品中聚合物均匀冷却得工艺条件都能降低冷却内应力;凡有助于塑料制品脱模得加工方法都有利于降低脱模内应力、对内应力影响较大得加工条件主要有如下几种、①料筒温度ﻫ较高得料筒温度有利于取向应力得降低,这就是因为在较高得料筒温度,熔体塑化均匀,粘度下降,流动性增加,在熔体充满型腔过程中,分子取向作用小,因而取向应力较小、而在较低料筒温度下,熔体粘度较高,充模过程中分子取向较多,冷却定型后残余内应力则较大、但就是,料筒温度太高也不好,太高容易造成冷却不充分,脱模时易造成变形,虽然取向应力减小,但冷却应力与脱模应力反而增大、②模具温度ﻫ模具温度得高低对取向内应力与冷却内应力得影响都很大、一方面,模具温度过低,会造成冷却加快,易使冷却不均匀而引起收缩上得较大差异,从而增大冷却内应力;另一方面,模具温度过低,熔体进入模其后,温度下降加快,熔体粘度增加迅速,造成在高粘度下充模,形成取向应力得程度明显加大、ﻫ模温对塑料结晶影响很大,模温越高,越有利于晶粒堆砌紧密,晶体内部得缺陷减小或消除,从而减少内应力、ﻫ另外,对于不同厚度塑料制品,其模温要求不同、对于厚壁制品其模温要适当高一些、以PC为例,其内应力大小与模具温度得关系如表5-5所示、ﻫ③注射压力注射压力高,熔体充模过程中所受剪切作用力大,产生取向应力得机会也较大、因此,为了降低取向应力与消除脱模应力,应适当降低注射压力、、以PC为例,其内应力大小与注射压力得关系如表5-6所示、、ﻫ④保压压力保压压力对塑料制品内应力得影响大于注射压力得影响、在保压阶段,随着熔体温度得降低,熔体粘度迅速增加,此时若施以高压,必然导致分子链得强迫取向,从而形成更大得取向应力、⑤注射速度ﻫ注射速度越快,越容易造成分子链得取向程度增加,从而引起更大得取向应力、但注射速度过低,塑料熔体进入模腔后,可能先后分层而形成熔化痕,产生应力集中线,易产生应力开裂、所以注射速度以适中为宜、最好采用变速注射,在速度逐渐减小下结束充模、⑥保压时间ﻫ保压时间越长,会增大塑料熔体得剪切作用,从而产生更大得弹性形变,冻结更多得取向应力、所以,取向应力随保压时间延长与补料量增加而显著增大、⑦开模残余压力ﻫ应适当调整注射压力与保压时间,使开模时模内得残余压力接近于大气压力,从而避免产生更大得脱模内应力、(3)塑料制品得热处理ﻫ塑料制品得热处理就是指将成型制品在一定温度下停留一段时间而消除内应力得方法、热处理就是消除塑料制品内取向应力得最好方法、ﻫ对于高聚物分子链得刚性较大,玻璃化温度较高得注塑件;对壁厚较大与带金属嵌件得制件;对使用温度范围较宽与尺寸精度要求较高得制件;时内应力较大而又不易自消得制件以及经过机械加工得制件都必须进行热处理、对制件进行热处理,可以使高聚物分子由不平衡构象向平衡构象转变,使强迫冻结得处于不稳定得高弹形变获得能量而进行热松弛,从而降低或基本消除内应力、常采用得热处理温度高于制件使用温度10~20℃或低于热变形温度5~10℃、热处理时间取决于塑料种类,制件厚度,热处理温度与注塑条件、一般厚度得制件,热处理1~2小时即可,随着制件厚度增大,热处理时间应适当延长、提高热处理温度与延长热处理时间具有相似得效果,但温度得效果更明显些、ﻫ热处理方法就是将制件放入水,甘油,矿物油,乙二醇与液体石蜡等液体介质中,或放入空气循环烘箱中加热到指定温度,并在该温度下停留一定时间,然后缓慢冷却到室温、实验表明,脱模后得制件立即进行热处理,对降低内应力,改善制件性能得效果更明显、此外,提高模具温度,延长制件在模内冷却时间,脱模后进行保温处理都有类似热处理得作用、尽管热处理就是降低制件内应力得有效办法之一,但热处理通常只能将内应力降低到制件使用条件允许得范围,很难完全消除内应力、对PC制件进行较长时间得热处理时,PC分子链有可能进行有序得重排,甚至结晶,从而降低冲击韧性,使缺口冲击强度降低、因而,不应把热处理作为降低制件内应力得唯一措施、(4)塑料制品得设计①塑料制品得形状与尺寸在具体设计塑料制品时,为了有效地分散内应力,应遵循这样得原则:制品外形应尽可能保持连续性,避免锐角,直角,缺口及突然扩大或缩小、ﻫ对于塑料制品得边缘处应设计成圆角,其中内圆角半径应大于相邻两壁中薄者厚度得70%以上;外圆角半径则根据制品形状而确定、对于壁厚相差较大得部位,因冷却速度不同,易产生冷却内应力及取向内应力、因此,应设计成壁厚尽可能均匀得制件,如必须壁厚不均匀,则要进行壁厚差异得渐变过渡、ﻫ②合理设计金属嵌件ﻫ塑料与金属得热膨胀系数相差5~10倍,因而带金属嵌件得塑料制品在冷却时,两者形成得收缩程度不同,因塑料得收缩比较大而紧紧抱住金属嵌件,在嵌件周围得塑料内层受压应力,而外层受拉应力作用,产生应力集中现象、在具体设汁嵌件时,应注意如下几点,以帮助减小或消除内应力、a、尽可能选择塑料件作为嵌件、b、尽可能选择与塑料热膨胀系数相差小得金属材料做嵌件材料,如铝,铝合金及铜等、ﻫc、在金属嵌件上涂覆一层橡胶或聚氨酯弹性缓冲层,并保证成型时涂覆层不熔化,可降低两者收缩差、ﻫd、对金属嵌件进行表面脱脂化处理,可以防止油脂加速制品得应力开裂、ﻫe、金属嵌件进行适当得预热处理、f、金属嵌件周围塑料得厚度要充足、例如,嵌件外径为D,嵌件周围塑料厚度为h,则对铝嵌件塑料厚度h≥0、8D;对于铜嵌件,塑料厚度h≥0、9 D、ﻫg、金属嵌件应设计成圆滑形状,最好带精致得滚花纹、③塑料制品上孔得设计ﻫ塑料制品上孔得形状,孔数及孔得位置都会对内应力集中程度产生很大得影响、ﻫ为避免应力开裂,切忌在塑料制品上开设棱形,矩形,方形或多边形孔、应尽可能开设圆形孔,其中椭圆形孔得效果最好,并应使椭圆形孔得长轴平行于外力作用方向、如开设圆孔,可增开等直径得工艺圆孔,并使相邻两圆孔得中心连接线平行于外力作用方向,这样可以取得与椭圆孔相似得效果;还有一种方法,即在圆孔周围开设对称得槽孔,以分散内应力、(5)塑料模具得设计在设计塑料模具时,浇注系统与冷却系统对塑料制品得内应力影响较大,在具体设计时应注意如下几点、①浇口尺寸ﻫ过大得浇口将需要较长得保压补料时间,在降温过程中得补料流动必定会冻结更多得取向应力,尤其就是在补填冷料时,将给浇口附近造成很大得内应力、ﻫ适当缩小浇口尺寸,可缩短保压补料时间,降低浇口凝封时模内压力,从而降低取向应力、但过小得浇口将导致充模时间延长,造成制品缺料、ﻫ②浇口得位置浇口得位置决定厂塑料熔体在模腔内得流动情况,流动距离与流动方向、、当浇口设在制品壁厚最大部位时,可适当降低注射压力,保压压力及保压时间,有利于降低取向应力、当浇口设在薄壁部位时,宜适当增加浇口处得壁厚,以降低浇口附近得取向应力、熔体在模腔内流动距离越长,产生取向应力得几率越大、为此,对于壁厚,长流程且面积较大得塑料件,应适当分布多个浇口,能有效地降低取向应力,防止翘曲变形、ﻫ另外,由于浇口附近为内、应力多发地带,可在浇口附近设汁成护耳式浇日,使内应力产生在护耳中,脱模后切除内应力较大得护耳,可降低塑料制品内得内应力、③流道得设计ﻫ设计短而粗得流道,可减小熔体得压力损失与温度降,相应降低注射压力与冷却速度,从而降低取向应力与冷却压力、ﻫ④冷却系统得设计冷却水道得分布要合理,使浇口附近,远离浇口区,壁厚处,壁薄处都得到均匀且缓慢得冷却,从而降低内应力,ﻫ⑤顶出系统得设计要设计适当得脱模锥度,较高得型芯光洁度与较大面积得顶出部位,以防止强行脱模产生脱模应力、ﻫ检查塑料件得应力得方法主要就是溶剂浸渍法、用冰醋酸浸30s,晾干,发白处即就是应力集中处、应力大时塑料会开裂,裂纹越多表示应力越大、也可以浸2rain,裂纹更深更明显、ﻫ可以用甲乙酮与丙酮1:1得混合液浸15s,来代替冰醋酸浸渍、ﻫ消除应力得方法有加热法,即在65~70℃下烘4h、小件可以用25%得丙酮水溶液浸泡30rain来消除应力、应力太大时,这两种方法均无效,零件不能电镀。
聚合物内应力产生与解决办法

聚合物内应力的产生及消除一、内应力产生在注塑制品中,各处局部应力状态是不同的,制品变形程度将决定于应力分布。
如果制品在冷却时。
存在温度梯度,则这类应力会发展,所以这类应力又称为“成型应力”。
注塑制品的内应力包两种:一种是注塑制品成型应力,另一种是温度应力。
当熔体进入温度较低的模具时,靠近模腔壁的熔体讯速地冷却而固化,于是分子链段被“冻结”。
由于凝固的聚合物层,导热性很差,在制品厚度方向上产生较大的温度梯度。
制品心部凝固相当缓慢,以致于当浇口封闭时,制品中心的熔体单元还未凝固,这时注塑机又无法对冷却收缩进行补料。
这样制品内部收缩作用与硬皮层作用方向是相反的;心部处于静态拉伸而表层则处于静态压缩。
在熔体充模流动时,除了有体积收缩效应引起的应力外。
还有因流道,浇口出口的膨胀效应而引起的应力;前一种效应引起的应力与熔体流动方向有关,后者由于出口膨胀效应将引起在垂直于流动方向应力作用。
二、影响残余应力的工艺因素(1)向应力的影响在速冷条件下,取向会导致聚合物内应力的形成。
由于聚合物熔体的粘度高,内应力不能很快松驰,影响制品的物理性能和尺寸稳定性。
各参数对取向应力的影响a熔体温度,熔体温度高,粘度低,剪切应力降低取向度减小;另一方面由于熔体温度高会使应力松驰加快,促使解取向能力加强。
可是在不改变注塑机压力的情况下,模腔压力会增大,强剪切作用又导致取向应力的提高。
b在喷嘴封闭以前,延长保压时间,会导致取向应力增加。
c提高注射压力或保压压力,会增大取向应力,d模具温度高可保证制品缓慢冷却,起到解取向作用。
e增加制品厚度使取向应力降低,因为厚壁制品冷却时慢,粘度提高慢,应力松驰过程的时间长,所以取向应力小。
(2)温度对应力的影响如上所述由于在充模时熔体和型壁之间温度梯度很大,先凝固的外层熔体要助止后凝固的内层熔体的收缩,结果在外层产生压应力(收缩应力),内层产生拉应力(取向应力)。
如果充模后又在保压压力的作用下持续较长时间,聚合物熔体又补入模腔中,使模腔压力提高,此压力会改变由于温度不均而产生的内应力。
第46问:产品内应力的了解与改善

第46问产品内应力的了解与改善产生内应力的原因有很多,如塑性熔体在加工过程中受到较强的剪切作用,加工中存在的取向与结晶作用,熔体各部位冷却速度极难做到均匀一致,熔体塑化不均匀,制品脱模困难等,都会引发内应力的产生,依引起内应力的原因不同,可将内应力分成以下几类。
一、分子取向性:1.1 冷却内应力产生:在注塑制品中,各处局部应力状态是不同的,制品变形程度将决定于应力分布。
如果制品在冷却时。
存在温度梯度,则这类应力会发展,所以这类应力又称为“成型应力”与冷却内应力。
注塑制品的内应力包两种:一种是注塑制品成型应力,另一种是温度应力。
当熔体进入温度较低的模具时,靠近模腔壁的熔体讯速地冷却而固化,于是分子链段被“冻结”。
由于凝固的聚合物层,导热性很差,在制品厚度方向上产生较大的温度梯度。
制品心部凝固相当缓慢,以致于当浇口封闭时,制品中心的熔体单元还未凝固,这时注塑机又无法对冷却收缩进行补料。
这样制品内部收缩作用与硬皮层作用方向是相反的;心部处于静态拉伸而表层则处于静态压缩。
1.2 取向内应力:在熔体充模流动时,除了有体积收缩效应引起的应力外。
还有因流道、浇口出口的膨胀效应而引起的应力;前一种效应引起的应力与熔体流动方向有关,后者由于出口膨胀效应将引起在垂直于流动方向应力作用。
聚合物在加工过程中,在力的作用下,流动的大分子链段一定会取向,取向的性质和程度根据取向条件有很大的区别。
按熔体中大分子受力的形式误作用的性质可分为剪切应力作用下的“流动取向”和受拉伸作用下的“拉伸取向”。
按取向结构单元的取向方向,可分单轴和双轴或平面取向。
按熔体温场的稳定性可分等温和非等温流动取向。
也可分结晶和非结晶取向。
聚合物熔体在模腔中的流动是注塑的主要流动过程,熔体在型腔中取向过程,将直接影响制品的质量。
欲理解注塑制品在型腔中成型的机理需了解无定型聚合物的取向机理。
充模时,无定型聚合物熔体是沿型壁流动,熔体流入型腔首先同模壁接触霰成来不及取向的冻结层外壳。
内应力产生的原因

内应力产生的原因
内应力产生的原因通常涉及材料的变形和载荷施加。
以下是一些常见的原因:
1.弹性变形:当材料受到外部载荷时,它会发生弹性变形,即变
形程度与施加的载荷成比例。
这会导致材料内部出现内应力,使其恢复原始形状。
2.塑性变形:当材料受到较大的载荷或持续的载荷时,会发生塑
性变形,即材料发生永久性变形而不恢复原状。
在塑性变形中,内应力被引入材料中以保持其形状。
3.温度变化:当材料受到温度变化时,由于热膨胀或热收缩,会
产生内应力。
当温度升高时,材料会膨胀,而在温度降低时,材料会收缩,这可能导致内部应力。
4.冷却或固化过程:在一些制造过程中,例如金属铸造或塑料注
塑,材料在冷却或固化过程中会发生体积变化。
这种体积变化会导致内部应力,可能导致材料开裂或变形。
5.不均匀变形:当材料的不同部分受到不同的力或变形限制时,
会发生不均匀的变形,从而产生内应力。
这可能发生在材料的表面和内部之间,或者在不同的材料之间。
6.外部载荷:外部施加在材料上的力、压力或扭矩等载荷也会导
致材料内部产生应力。
这些应力可以是压应力、剪应力或拉伸应力,取决于施加载荷的方向和大小。
需要注意的是,内应力的存在并不总是负面的,因为它们可以帮助
材料抵抗外部载荷并保持其结构的稳定性。
然而,当内应力超过材料的承载能力或引起材料破坏时,它们可能成为问题。
内应力的产生及消除方法

内应力的产生及消除方法内应力是指物体内部各部分之间以及各个分子之间产生的相互作用力。
内应力的产生主要是由于物体的形状变化或外部作用力的影响,而内应力的消除可以通过物体的形状恢复或有效地去除外部作用力来实现。
下面将详细介绍内应力的产生及消除方法。
一、内应力的产生1.形状变化:当物体的形状发生变化时,内部各部分之间的相互作用力会发生变化,产生内应力。
例如,当拉伸金属丝时,金属丝内部的晶格结构发生变形,使金属丝受到拉伸内应力。
2.外部作用力:当物体受到外部作用力时,外部作用力在物体内部传递,使内部各部分之间产生相互作用力,产生内应力。
例如,当压缩弹簧时,弹簧内部的分子间相互作用力增大,产生压缩内应力。
3.温度变化:当物体受到温度变化时,物体的形状会产生变化,分子之间的相互作用力也会发生变化,从而产生内应力。
例如,当金属材料受到高温热膨胀时,内部分子间的相互作用力会增大,产生热膨胀内应力。
二、内应力的消除方法1.形状恢复:通过改变物体的形状,使内部各部分之间的相互作用力恢复到原始状态,从而消除内应力。
例如,当金属材料受到变形时,可以通过加工、锻造等方法来恢复其原始形状并消除内应力。
2.降低外部作用力:减小物体受到的外部作用力,从而减小内部各部分之间的相互作用力,进而消除内应力。
例如,当弹簧受到压缩时,可以减小外部作用力来消除内应力。
3.控制温度变化:通过控制物体所处的温度,使其形状保持稳定,从而减小内应力。
例如,在制造金属制品时,可以控制金属材料的加热和冷却过程,以避免或减小温度变化引起的内应力。
4.应力放松:通过在物体上施加一个与内应力相反方向的应力来消除内应力。
例如,当金属材料受到弯曲后,可以施加相反方向的拉伸力来消除内应力。
5.材料选择:选择具有较小内应力的材料来制造物体,从而减小内应力的产生。
例如,选择材料的热膨胀系数较小的特性,可以减小温度变化引起的内应力。
综上所述,内应力的产生主要是由于物体的形状变化或外部作用力的影响。
什么叫内应力,该如何消除内应力

什么叫内应力,该如何消除内应力?
1. 物体由于外因(受力、湿度变化等)而变形时,在物体内各部分之间产生相互作用的内力,以抵抗这种外因的作用,并力图使物体从变形后的位置回复到变形前的位置。
在所考察的截面某一点单位面积上的内力称为应力。
同截面垂直的称为正应力或法向应力。
2. 在没有外力存在下,材料内部由于加工成型不当,温度变化,溶剂作用等原因所产生的应力。
3、内应力的取消有几种方法:一对物体进行热处理(只针对金属性质的工件)二是放到自然条件下进行消除。
三是人工通过敲打振动等方式进行消除。
内应力是在结构上无外力作用时保留于物体内部的应力没有外力存在时,弹性物体内所保存的应力叫做内应力,它的特点是在物体内形成一个平衡的力系,即遵守静力学条件.按性质和范围大小可分为宏观应力,微观应力和超微观应力.按引起原因可分为热应力和组织应力.按存在时间可分为瞬时应力和残余应力.按作用方向可分为纵向应力和横向应力.。
注塑件内应力的产生及解决对策

注塑件内应力的产生及解决对策注塑件内应力的产生是由于注塑过程中的热胀冷缩效应引起的。
具体而言,注塑过程中,塑料在高温下进入模具中,然后在冷却过程中,塑料会收缩并形成注塑件。
然而,由于注塑过程中塑料的不均匀收缩,以及与模具之间的附着力,注塑件内部会形成应力。
1.外观缺陷:注塑件可能会出现翘曲、扭曲、脱模或开缺等问题,从而影响其外观质量。
2.尺寸变化:由于应力会导致塑料变形,从而导致注塑件的尺寸变化。
3.力学性能下降:注塑件的内应力可能导致其力学性能下降,使得产品更容易断裂或失效。
以下是一些解决注塑件内应力的对策:1.优化模具设计:合理的模具设计可以减少内应力的产生。
例如,通过增加模具冷却通道和增加射胶点的数量和位置等方式,可以加快注塑件的冷却速度,减少应力的产生。
2.优化材料选择:选择合适的塑料材料也可以减少内应力的产生。
一些塑料材料具有更低的热胀冷缩系数,可以减少注塑件的收缩程度和应力水平。
3.控制注塑工艺参数:合理控制注塑工艺参数也可以减少内应力的产生。
例如,调整注射速度、保压时间和冷却时间等,可以减少塑料的不均匀收缩,并减少应力的产生。
4.使用预应力技术:预应力技术可以在注塑过程中施加一定的压力,以减小注塑件形成后的应力水平。
这可以通过在注塑模具上加装压力缸或在模具关闭之前施加辅助压力等方式实现。
5.热处理和退火:对于内应力较高的注塑件,可以通过热处理或退火等热处理方法,来减小或消除部分内应力。
总之,在注塑件生产中,必须重视注塑件内应力的产生和解决。
通过合理的模具设计、优化材料选择、控制工艺参数、使用预应力技术以及热处理和退火等方法,可以有效减少内应力的产生,并优化注塑件的性能和外观质量。
工业设计概论 内应力

工业设计概论内应力工业设计概论工业设计是一门通过创新和技术,将产品从概念到实际生产的全过程进行设计和改进的学科。
它涉及到产品的外观、功能、人机交互、材料选择等多个方面,旨在提高产品的质量、可靠性和用户体验。
内应力内应力是指物体内部各部分之间相互作用所产生的力。
在工程领域中,内应力是一个非常重要的概念。
它对材料的强度、刚度和耐久性等方面都有着重要影响。
内应力来源内应力来源主要有以下几个方面:1. 制造过程中产生的应力:例如焊接、锻造、淬火等制造过程中,由于加热或冷却速度不均匀,会导致物体表面与内部温度差异较大,从而产生应力。
2. 载荷引起的应力:当物体受到外部载荷作用时,会产生内部应力。
这种应力可以分为拉伸、压缩、剪切等几种类型。
3. 温度变化引起的应力:当物体受到温度变化时,由于不同材料具有不同的热膨胀系数,会导致内部应力的产生。
内应力的影响内应力对材料的性质和性能有着重要的影响。
它可以影响材料的强度、刚度、塑性、韧性和疲劳寿命等方面。
1. 强度:内应力会使材料中出现裂纹,从而降低其强度。
2. 刚度:由于内应力的存在,材料可能会发生变形或扭曲,从而降低其刚度。
3. 塑性:内应力会使材料中出现位错,从而减少其可塑性。
4. 韧性:内应力也可以影响材料的韧性。
当材料中存在较大的内部应力时,容易导致断裂。
5. 疲劳寿命:由于内部应力的存在,物体在长时间使用过程中容易出现疲劳断裂。
如何减小内应力为了减小物体中的内部应力,可以采取以下措施:1. 选择合适的制造工艺:在制造过程中选择合适的工艺和参数,可以减小物体中产生的内部应力。
2. 控制温度变化:在设计产品时尽量避免温度变化对材料产生影响,或者在制造过程中控制温度的变化。
3. 优化结构设计:在设计产品时,可以采用一些优化结构,如增加圆角、减小焊缝等,来减小内部应力。
4. 选择合适的材料:不同材料具有不同的热膨胀系数和弹性模量等特性,合理选择材料可以减小内部应力。
内应力的产生及消除
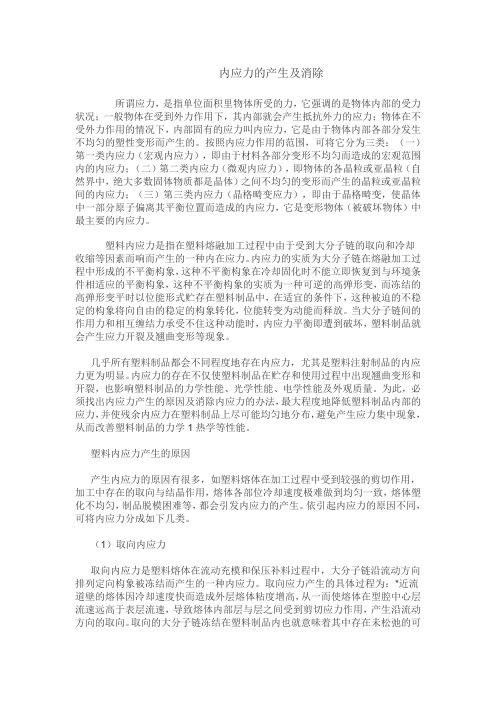
内应力的产生及消除所谓应力,是指单位面积里物体所受的力,它强调的是物体内部的受力状况;一般物体在受到外力作用下,其内部就会产生抵抗外力的应力;物体在不受外力作用的情况下,内部固有的应力叫内应力,它是由于物体内部各部分发生不均匀的塑性变形而产生的。
按照内应力作用的范围,可将它分为三类:(一)第一类内应力(宏观内应力),即由于材料各部分变形不均匀而造成的宏观范围内的内应力;(二)第二类内应力(微观内应力),即物体的各晶粒或亚晶粒(自然界中,绝大多数固体物质都是晶体)之间不均匀的变形而产生的晶粒或亚晶粒间的内应力;(三)第三类内应力(晶格畸变应力),即由于晶格畸变,使晶体中一部分原子偏离其平衡位置而造成的内应力,它是变形物体(被破坏物体)中最主要的内应力。
塑料内应力是指在塑料熔融加工过程中由于受到大分子链的取向和冷却收缩等因素而响而产生的一种内在应力。
内应力的实质为大分子链在熔融加工过程中形成的不平衡构象,这种不平衡构象在冷却固化时不能立即恢复到与环境条件相适应的平衡构象,这种不平衡构象的实质为一种可逆的高弹形变,而冻结的高弹形变平时以位能形式贮存在塑料制品中,在适宜的条件下,这种被迫的不稳定的构象将向自由的稳定的构象转化,位能转变为动能而释放。
当大分子链间的作用力和相互缠结力承受不住这种动能时,内应力平衡即遭到破坏,塑料制品就会产生应力开裂及翘曲变形等现象。
几乎所有塑料制品都会不同程度地存在内应力,尤其是塑料注射制品的内应力更为明显。
内应力的存在不仅使塑料制品在贮存和使用过程中出现翘曲变形和开裂,也影响塑料制品的力学性能、光学性能、电学性能及外观质量。
为此,必须找出内应力产生的原因及消除内应力的办法,最大程度地降低塑料制品内部的应力,并使残余内应力在塑料制品上尽可能均匀地分布,避免产生应力集中现象,从而改善塑料制品的力学1热学等性能。
塑料内应力产生的原因产生内应力的原因有很多,如塑料熔体在加工过程中受到较强的剪切作用,加工中存在的取向与结晶作用,熔体各部位冷却速度极难做到均匀一致,熔体塑化不均匀,制品脱模困难等,都会引发内应力的产生。
内应力的产生及消除方法

内应力的产生及消除方法所谓应力,是指单位面积里物体所受的力,它强调的是物体内部的受力状况;一般物体在受到外力作用下,其内部就会产生抵抗外力的应力;物体在不受外力作用的情况下,内部固有的应力叫内应力,它是由于物体内部各部分发生不均匀的塑性变形而产生的。
按照内应力作用的范围,可将它分为三类:(一)第一类内应力(宏观内应力),即由于材料各部分变形不均匀而造成的宏观范围内的内应力;(二)第二类内应力(微观内应力),即物体的各晶粒或亚晶粒(自然界中,绝大多数固体物质都是晶体)之间不均匀的变形而产生的晶粒或亚晶粒间的内应力;(三)第三类内应力(晶格畸变应力),即由于晶格畸变,使晶体中一部分原子偏离其平衡位置而造成的内应力,它是变形物体(被破坏物体)中最主要的内应力。
塑料内应力是指在塑料熔融加工过程中由于受到大分子链的取向和冷却收缩等因素而响而产生的一种内在应力。
内应力的实质为大分子链在熔融加工过程中形成的不平衡构象,这种不平衡构象在冷却固化时不能立即恢复到与环境条件相适应的平衡构象,这种不平衡构象的实质为一种可逆的高弹形变,而冻结的高弹形变平时以位能形式贮存在塑料制品中,在适宜的条件下,这种被迫的不稳定的构象将向自由的稳定的构象转化,位能转变为动能而释放。
当大分子链间的作用力和相互缠结力承受不住这种动能时,内应力平衡即遭到破坏,塑料制品就会产生应力开裂及翘曲变形等现象。
几乎所有塑料制品都会不同程度地存在内应力,尤其是塑料注射制品的内应力更为明显。
内应力的存在不仅使塑料制品在贮存和使用过程中出现翘曲变形和开裂,也影响塑料制品的力学性能,光学性能,电学性能及外观质量。
为此,必须找出内应力产生的原因及消除内应力的办法,最大程度地降低塑料制品内部的应力,并使残余内应力在塑料制品上尽可能均匀地分布,避免产生应力集中现象,从而改善塑料制品的力学热学等性能。
塑料内应力产生的原因产生内应力的原因有很多,如塑料熔体在加工过程中受到较强的剪切作用,加工中存在的取向与结晶作用,熔体各部位冷却速度极难做到均匀一致,熔体塑化不均匀,制品脱模困难等,都会引发内应力的产生。
举例说明减少铸件内应力的措施

举例说明减少铸件内应力的措施一、背景介绍铸造是制造业中常见的一种生产工艺,其过程中会产生内应力。
这些内应力会影响铸件的性能和寿命,因此需要采取措施减少内应力。
二、减少铸件内应力的原因1. 铸件在冷却过程中会收缩,导致形变和内应力;2. 铸件在浇注时会受到液态金属的冲击和挤压,导致内部形变和应力;3. 铸件在固化时由于温度梯度不均匀而产生热应力。
三、减少铸件内应力的措施1. 优化铸造工艺:合理选择浇注位置和浇注速度,避免液态金属对模具的冲击和挤压;2. 控制冷却速率:通过调整模具温度、喷水等方式控制铸件冷却速率,避免快速冷却引起的内部形变和应力;3. 热处理:通过热处理改变铸件组织结构,消除或减小内部残余应力;4. 降低浇注温度:降低浇注温度可以减少热应力;5. 选择合适的铸造材料:选择合适的铸造材料可以减少内部形变和应力。
四、具体措施详解1. 优化铸造工艺(1)合理选择浇注位置:浇注位置的选择会影响到液态金属流动轨迹和冲击力大小,因此需要根据铸件形状和结构设计合理的浇口;(2)控制浇注速度:过快或过慢的浇注速度都会对铸件产生不良影响,因此需要根据实际情况调整浇注速度;(3)避免液态金属对模具的冲击和挤压:通过增加模具强度、采用缓冲材料等方式来减小液态金属对模具的冲击和挤压。
2. 控制冷却速率(1)调整模具温度:通过调整模具温度来控制铸件冷却速率,避免快速冷却引起的内部形变和应力;(2)喷水降温:在必要时可以采用喷水等方式来降低铸件温度,避免快速冷却引起的内部形变和应力。
3. 热处理(1)退火:通过退火来消除或减小铸件内部残余应力;(2)淬火:通过淬火来改变铸件组织结构,减小内部残余应力;(3)正火:通过正火来改变铸件组织结构,消除内部残余应力。
4. 降低浇注温度降低浇注温度可以减少热应力,但需要注意不要过低影响铸造质量。
5. 选择合适的铸造材料选择合适的铸造材料可以减少内部形变和应力。
例如,采用低碳钢、球墨铸铁等材料可以减少热膨胀系数和收缩率,从而减少内部形变和应力。
材料中内应力对结构性能的影响分析
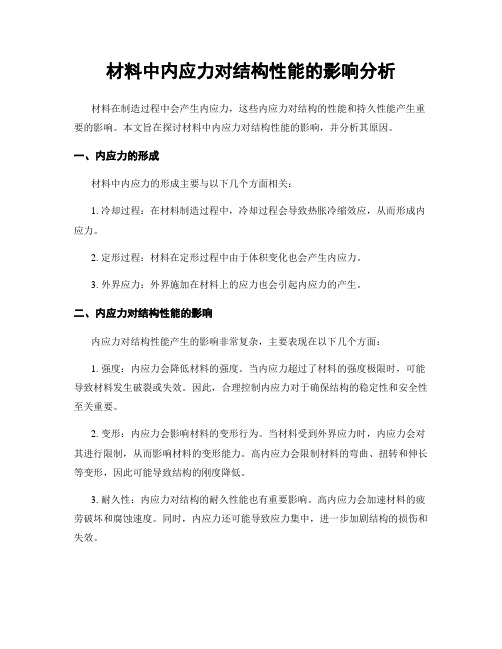
材料中内应力对结构性能的影响分析材料在制造过程中会产生内应力,这些内应力对结构的性能和持久性能产生重要的影响。
本文旨在探讨材料中内应力对结构性能的影响,并分析其原因。
一、内应力的形成材料中内应力的形成主要与以下几个方面相关:1. 冷却过程:在材料制造过程中,冷却过程会导致热胀冷缩效应,从而形成内应力。
2. 定形过程:材料在定形过程中由于体积变化也会产生内应力。
3. 外界应力:外界施加在材料上的应力也会引起内应力的产生。
二、内应力对结构性能的影响内应力对结构性能产生的影响非常复杂,主要表现在以下几个方面:1. 强度:内应力会降低材料的强度。
当内应力超过了材料的强度极限时,可能导致材料发生破裂或失效。
因此,合理控制内应力对于确保结构的稳定性和安全性至关重要。
2. 变形:内应力会影响材料的变形行为。
当材料受到外界应力时,内应力会对其进行限制,从而影响材料的变形能力。
高内应力会限制材料的弯曲、扭转和伸长等变形,因此可能导致结构的刚度降低。
3. 耐久性:内应力对结构的耐久性能也有重要影响。
高内应力会加速材料的疲劳破坏和腐蚀速度。
同时,内应力还可能导致应力集中,进一步加剧结构的损伤和失效。
4. 残余应力:一些制造工艺中产生的内应力在材料制造完成后仍然存在,称为残余应力。
残余应力会降低材料的耐久性能,增加结构的失效风险。
三、内应力产生的机制内应力的产生机制与材料的组织结构和加工过程密切相关。
以下是常见的内应力产生机制:1. 晶体缺陷:材料中的晶体缺陷,如晶界、位错等,会引起内应力的产生。
2. 相变:材料在相变过程中,如凝固、烧结等,由于组分变化和体积变化也会导致内应力的形成。
3. 加工过程:材料的加工过程会引入内应力,例如锻造、轧制等加工过程会造成材料的塑性变形,从而形成内应力。
4. 物理性能失配:材料中不同部分的物理性能差异,如热膨胀系数不一致等,也会引起内应力的产生。
四、减小内应力的措施为了减小材料中的内应力,可以采取以下几种措施:1. 合理的工艺控制:采用合理的工艺参数和工艺顺序,避免产生过大的内应力。
内应力的产生及消除方法
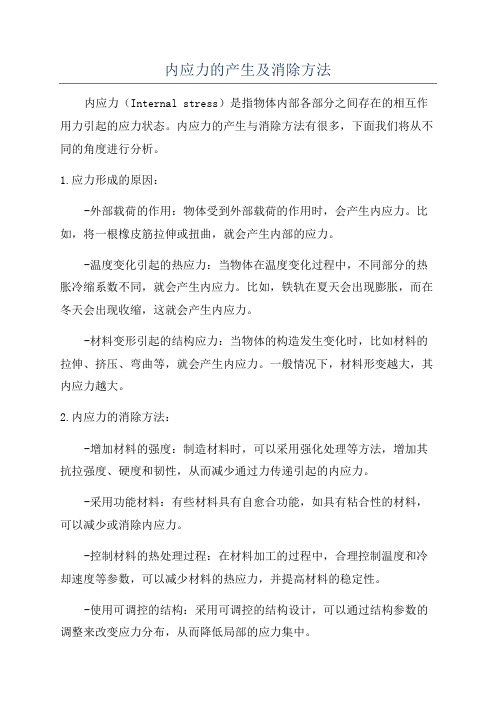
内应力的产生及消除方法内应力(Internal stress)是指物体内部各部分之间存在的相互作用力引起的应力状态。
内应力的产生与消除方法有很多,下面我们将从不同的角度进行分析。
1.应力形成的原因:-外部载荷的作用:物体受到外部载荷的作用时,会产生内应力。
比如,将一根橡皮筋拉伸或扭曲,就会产生内部的应力。
-温度变化引起的热应力:当物体在温度变化过程中,不同部分的热胀冷缩系数不同,就会产生内应力。
比如,铁轨在夏天会出现膨胀,而在冬天会出现收缩,这就会产生内应力。
-材料变形引起的结构应力:当物体的构造发生变化时,比如材料的拉伸、挤压、弯曲等,就会产生内应力。
一般情况下,材料形变越大,其内应力越大。
2.内应力的消除方法:-增加材料的强度:制造材料时,可以采用强化处理等方法,增加其抗拉强度、硬度和韧性,从而减少通过力传递引起的内应力。
-采用功能材料:有些材料具有自愈合功能,如具有粘合性的材料,可以减少或消除内应力。
-控制材料的热处理过程:在材料加工的过程中,合理控制温度和冷却速度等参数,可以减少材料的热应力,并提高材料的稳定性。
-使用可调控的结构:采用可调控的结构设计,可以通过结构参数的调整来改变应力分布,从而降低局部的应力集中。
-合理设计构件形状:设计构件的形状时,应该尽量避免出现棱角、悬臂和尖突的结构,这样可以减少应力集中,从而减少内应力。
3.内应力的分析方法:-数值模拟分析:通过数学模型和计算机仿真,可以对材料的内应力进行数值模拟分析,从而找到应力的分布规律,并确定合理的消除应力的方法。
-压缩应力测试方法:利用压缩应力测试设备,可以对材料的内应力进行测试,从而确定合理的消除应力的方式。
-切割应力测试方法:通过在材料上进行切割应力测试,可以测量材料的内应力分布情况,进而找到消除应力的方法。
注塑件内应力的影响因素和改善方案

注塑件内应力的影响因素和改善方案在注塑加工过程中,注塑制品存在着一个内在的质量问题------内应力。
内应力的来源与所使用的塑料原料种类、注塑机的类型与塑化系统的结构、模具的结构及精度、塑料制品的结构、注塑成型的工艺参数的设定及控制、生产环境及操作者的状态等有关。
其中任何一项出现问题,都将影响到制品的质量。
而且,由于制品的表面质量是内在质量的反映,所以,凡是能引起制品内在质量的因素,都能同时引起制品的表面质量及其他质量问题,如引起制品的开裂、银纹、翘曲、变形、力学强度降低,甚至失去使用价值等问题。
由于注塑过程中,除了引起制品翘曲变形的内应力可以直观感觉到外,其它质量问题不但用肉眼看不到,而且在短时间内也没有表露出来。
所以注塑加工现场的工程人员对于这个问题一般不很重视,但是却可能存在着很大的质量隐患。
本文针对内应力这个内在的质量问题展开分析,并提出控制的一些方法,希望对现场控制产品质量的工程人员有所帮助和启示。
一、内应力的种类及产生原因注塑制品的内应力主要有以下四种:1、温度应力:是制品冷却时温度不均产生的应力。
当熔体进入温度较低的模具时,靠近模腔壁的熔体迅速地冷却而固化。
由于凝固的聚合物层导热性很差,因而在制品厚度方向上产生较大的温度梯度。
先凝固的外层熔体要阻止后凝固的内层熔体的收缩,结果在外层产生压应力(收缩应力),内层产生拉应力(取向应力)。
另方面,因制品壁厚不均匀,冷却速度不一致,从而产生冷却温度不均现象。
2、取向应力:是制品内部大分子取向产生的应力。
对于线形树脂和纤维增强的塑料,在加工中最容易产生取向应力。
其结果,沿着流动方向的分子取向程度最大,在速冷条件下,如果被拉直的分子链来不及松弛,则在该方向上产生了取向应力。
3、收缩应力:注塑过程中,塑料分子本身的平衡状态受到破坏,并产生不平衡体积时的应力。
如结晶塑料的晶区与非晶区界面因收缩不均产生的内应力。
4、脱模应力:脱模时制品变形产生的应力。
内应力产生原因及解决方法

内应力产生原因及解决方法概述:内应力是物体内部的力,通常由于外部作用力或变形引起。
内应力的产生原因有很多,包括材料的结构、形状、温度变化以及外力的作用等。
本文将从不同角度探讨内应力的产生原因,并提出相应的解决方法。
一、材料结构:材料的结构是内应力产生的重要原因之一。
当材料内部有不一致的结构时,会导致内部应力的积累。
例如,在金属材料中,晶界的存在会导致内应力的产生。
晶界是晶体之间的结合面,由于晶体的结构不同,晶界处的结构也会不一致,从而产生内应力。
解决这个问题的方法是通过热处理或合适的形变工艺来改善材料的结构,使其更加均匀,从而减少内应力的产生。
二、形状:材料的形状也会影响内应力的产生。
当材料的形状发生变化时,内部会产生应力来抵抗这种变形。
例如,在金属加工过程中,如果材料受到了过大的压力或拉伸,就会产生内应力。
解决这个问题的方法是通过控制加工参数,如温度、速度和力度等,来减少材料的变形,从而减少内应力的产生。
三、温度变化:温度变化也是引起内应力的重要原因之一。
当材料受到温度变化时,其体积也会发生变化,从而产生内应力。
例如,在焊接过程中,焊接部位会受到高温的加热,而周围区域温度较低,这就会导致焊接部位发生热胀冷缩现象,从而产生内应力。
解决这个问题的方法是控制焊接过程的温度,避免温度梯度过大,或者采用预热和后热处理等方法来减少内应力的产生。
四、外力作用:外力的作用是内应力产生的直接原因之一。
当外力施加在材料上时,材料内部会产生应力来抵抗这种外力。
例如,在机械零件的装配过程中,如果装配力过大,就会导致零件产生内应力。
解决这个问题的方法是合理设计零件的装配方式,控制装配力度,或者采用适当的装配工艺,如加热或冷却等,来减少内应力的产生。
内应力的产生原因有很多,包括材料的结构、形状、温度变化以及外力的作用等。
为了解决这个问题,我们可以通过改善材料的结构、控制材料的形状、调控温度以及合理设计外力作用方式等手段来减少内应力的产生。
塑料内应力形成的原理消除方案及检测方法
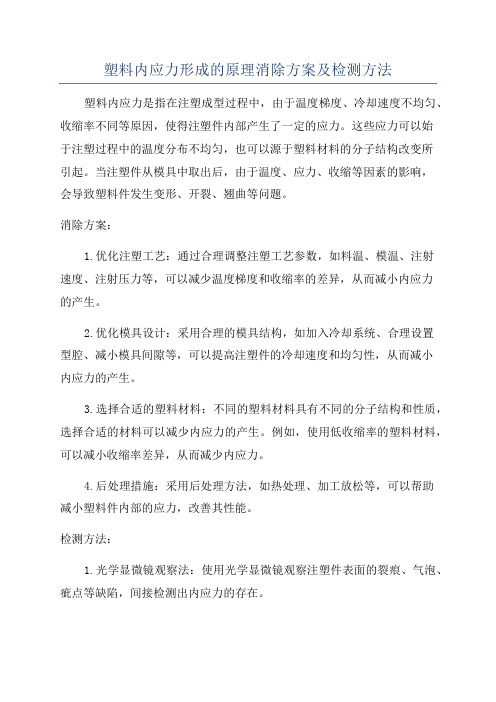
塑料内应力形成的原理消除方案及检测方法塑料内应力是指在注塑成型过程中,由于温度梯度、冷却速度不均匀、收缩率不同等原因,使得注塑件内部产生了一定的应力。
这些应力可以始于注塑过程中的温度分布不均匀,也可以源于塑料材料的分子结构改变所引起。
当注塑件从模具中取出后,由于温度、应力、收缩等因素的影响,会导致塑料件发生变形、开裂、翘曲等问题。
消除方案:1.优化注塑工艺:通过合理调整注塑工艺参数,如料温、模温、注射速度、注射压力等,可以减少温度梯度和收缩率的差异,从而减小内应力的产生。
2.优化模具设计:采用合理的模具结构,如加入冷却系统、合理设置型腔、减小模具间隙等,可以提高注塑件的冷却速度和均匀性,从而减小内应力的产生。
3.选择合适的塑料材料:不同的塑料材料具有不同的分子结构和性质,选择合适的材料可以减少内应力的产生。
例如,使用低收缩率的塑料材料,可以减小收缩率差异,从而减少内应力。
4.后处理措施:采用后处理方法,如热处理、加工放松等,可以帮助减小塑料件内部的应力,改善其性能。
检测方法:1.光学显微镜观察法:使用光学显微镜观察注塑件表面的裂痕、气泡、疵点等缺陷,间接检测出内应力的存在。
2.射线衍射法:通过使用射线衍射技术,对注塑件进行射线照射后,观察衍射图案的变化,可以判断出注塑件中的应力分布情况。
3.室温拉伸试验法:对注塑件进行拉伸试验,在试验过程中观察和记录试样的变形情况,通过分析变形程度和变形形状,可以间接推断出注塑件中的内应力程度。
4.热膨胀法:测量注塑件在不同温度下的尺寸变化,通过分析尺寸变化规律,可以推断出注塑件中的内应力分布情况。
总结:塑料内应力是注塑件常见的质量问题之一,可以通过优化注塑工艺、模具设计、选择合适的材料和后处理措施来减小或消除内应力的产生。
同时,通过光学显微镜观察、射线衍射、室温拉伸试验和热膨胀等检测方法,可以对注塑件的内应力进行检测和分析。
内应力对材料强度的影响

内应力对材料强度的影响引言:内应力是指材料内部的分子间相互作用力所引起的应力。
内应力对材料的强度具有重要影响。
本文将探讨内应力对材料强度的影响,并分析内应力产生的原因和减小内应力的方法。
一、内应力的产生原因内应力的产生可以有多种原因,包括材料加工过程中的机械变形、温度变化、化学反应等。
以下是内应力产生的几种常见原因:1.1 机械变形:在材料的加工过程中,由于外力的作用,材料会发生塑性变形或弹性变形。
这会导致材料内部产生应力,即内应力。
1.2 温度变化:材料在温度变化时,由于热胀冷缩效应,会引起内部应力的产生。
例如,当材料被加热时,由于热膨胀,内部产生的热应力会导致材料破裂或变形。
1.3 化学反应:在某些化学反应中,产生的化学物质会引起材料内部的应力。
例如,在金属的腐蚀过程中,产生的氧化物会引起内部应力的积累。
二、内应力对材料强度的影响内应力对材料的强度具有重要影响。
以下是内应力对材料强度的几种主要影响:2.1 破坏性影响:当内应力超过材料的强度极限时,材料会发生破坏。
内应力的积累会导致材料的开裂、断裂等破坏形式。
因此,了解和控制内应力对于材料的强度至关重要。
2.2 强度下降:内应力会减小材料的强度。
由于内应力的存在,材料的局部区域会受到约束,使其失去一部分强度。
这会导致材料的整体强度下降。
2.3 导致变形:内应力会引起材料的变形。
当内应力超过材料的屈服强度时,材料会发生塑性变形。
这会导致材料的形状改变,影响其功能和使用寿命。
三、减小内应力的方法为了提高材料的强度和延长使用寿命,需要采取措施减小内应力。
以下是几种常见的减小内应力的方法:3.1 适当的材料选择:选择合适的材料可以减小内应力。
不同材料具有不同的热膨胀系数和机械性能,选择适合的材料可以降低温度和机械变形引起的内应力。
3.2 控制加工工艺:合理控制加工工艺可以减少内应力的产生。
例如,在金属加工过程中,可以采用适当的冷却速度和模具设计,以减小内应力的积累。
材料应力处理方案

材料应力处理方案引言材料的应力处理是指通过特定的加工和热处理等方法,对材料中存在的内应力进行调整和释放,以提高材料的机械性能和稳定性。
本文将介绍材料应力的产生原因、存在的问题以及相应的处理方案。
应力的产生原因材料在制造和加工过程中,常常会产生内源性应力。
这些内应力主要来源于以下几个方面:1.热应力:材料在热处理过程中由于温度变化导致体积变化,从而产生内应力。
2.塑性应力:材料的加工过程中,由于塑性变形引起的内应力。
3.冷却应力:材料在冷却过程中,由于温度梯度引起的内应力。
4.残余应力:材料在焊接、铸造等过程中,由于相变或相位转变引起的内应力。
5.力学应力:外加载荷作用于材料,导致材料内部产生应力。
应力存在的问题应力对材料的性能和稳定性有着重要的影响。
如果材料中存在过多的应力,将导致以下问题:1.引起材料的变形和破损。
2.减少材料的抗拉强度和抗压强度。
3.降低材料的耐腐蚀性能。
4.引起材料的开裂和断裂。
因此,对于材料中存在的应力,需要采取相应的处理方案,以减小或消除应力的影响。
应力处理方案1. 热处理热处理是一种常见的材料应力处理方法。
通过控制材料的加热和冷却过程,来调整和释放材料中的应力。
热处理常用的方法有以下几种:•退火:通过加热材料到一定温度,保持一定时间后,缓慢冷却到室温,以减小或消除应力,提高材料的塑性和韧性。
•规化:通过加热材料到一定温度,保持一定时间后,以适当速度冷却,以消除应力和改善材料的组织结构。
•淬火:通过迅速冷却材料,使其产生高强度和高硬度,以减小或消除残余应力。
•回火:在淬火后,将材料加热到一定温度,保持一定时间,再适当冷却,以减小强度和硬度,减小残余应力,提高韧性和延展性。
2. 机械加工机械加工是通过改变材料的形状和结构,来调整和释放材料中的应力。
常见的机械加工方法有以下几种:•等径磨削:通过磨削材料的表面,以消除表面的应力和改善表面质量。
•拉伸和压缩:通过施加拉力或压力,以引起材料的塑性变形,从而减小或消除应力。
内应力的产生及消除方法

内应力的产生及消除所谓应力,是指单位面积里物体所受的力,它强调的是物体内部的受力状况;一般物体在受到外力作用下,其内部就会产生抵抗外力的应力;物体在不受外力作用的情况下,内部固有的应力叫内应力,它是由于物体内部各部分发生不均匀的塑性变形而产生的.按照内应力作用的范围,可将它分为三类:(一)第一类内应力(宏观内应力),即由于材料各部分变形不均匀而造成的宏观范围内的内应力;(二)第二类内应力(微观内应力),即物体的各晶粒或亚晶粒(自然界中,绝大多数固体物质都是晶体)之间不均匀的变形而产生的晶粒或亚晶粒间的内应力;(三)第三类内应力(晶格畸变应力),即由于晶格畸变,使晶体中一部分原子偏离其平衡位置而造成的内应力,它是变形物体(被破坏物体)中最主要的内应力.塑料内应力是指在塑料熔融加工过程中由于受到大分子链的取向和冷却收缩等因素而响而产生的一种内在应力.内应力的实质为大分子链在熔融加工过程中形成的不平衡构象,这种不平衡构象在冷却固化时不能立即恢复到与环境条件相适应的平衡构象,这种不平衡构象的实质为一种可逆的高弹形变,而冻结的高弹形变平时以位能形式贮存在塑料制品中,在适宜的条件下,这种被迫的不稳定的构象将向自由的稳定的构象转化,位能转变为动能而释放.当大分子链间的作用力和相互缠结力承受不住这种动能时,内应力平衡即遭到破坏,塑料制品就会产生应力开裂及翘曲变形等现象.几乎所有塑料制品都会不同程度地存在内应力,尤其是塑料注射制品的内应力更为明显.内应力的存在不仅使塑料制品在贮存和使用过程中出现翘曲变形和开裂,也影响塑料制品的力学性能,光学性能,电学性能及外观质量.为此,必须找出内应力产生的原因及消除内应力的办法,最大程度地降低塑料制品内部的应力,并使残余内应力在塑料制品上尽可能均匀地分布,避免产生应力集中现象,从而改善塑料制品的力学1热学等性能.塑料内应力产生的原因产生内应力的原因有很多,如塑料熔体在加工过程中受到较强的剪切作用,加工中存在的取向与结晶作用,熔体各部位冷却速度极难做到均匀一致,熔体塑化不均匀,制品脱模困难等,都会引发内应力的产生.依引起内应力的原因不同,可将内应力分成如下几类.⑴取向内应力取向内应力是塑料熔体在流动充模和保压补料过程中,大分子链沿流动方向排列定向构象被冻结而产生的一种内应力.取向应力产生的具体过程为:*近流道壁的熔体因冷却速度快而造成外层熔体粘度增高,从一而使熔体在型腔中心层流速远高于表层流速,导致熔体内部层与层之间受到剪切应力作用,产生沿流动方向的取向.取向的大分子链冻结在塑料制品内也就意味着其中存在未松弛的可逆高弹形变,所以说取向应力就是大分子链从取向才^象力图过渡到无取向构象的内力.用热处理的方法,可降低或消除塑料制品内的取向应力.塑料制品的取向内应力分布为从制品的表层到内层越来越小,并呈抛物线变化.⑵冷却内应力冷却内应力是塑料制品在熔融加工过程中因冷却定型时收缩不均匀而产生的一种内应力.尤其是对厚壁塑料制品,塑料制品的外层首先冷却凝固收缩,其内层可能还是热熔体,这徉芯层就会限制表层的收缩,导致芯层处于压应力状态,而表层处于拉应力状态. 塑料制品冷却内应力的分布为从制品的表层到内层越来越大,并也呈抛物线变化..另外,带金属嵌件的塑料制品,由于金属与塑料的热胀系数相差较大,容易形成收缩不一均匀的内应力.除上述两种主要内应力外,还有以下几种内应力:对于结晶塑料制品而言,其制品内部各部位的结晶结构和结晶度不同也会产生内应力.另外还有构型内应力及脱模内应力等,只是其内应力听占比重都很小.影响塑料内应力产生的因素⑴分子链的刚性分子链刚性越大,熔体粘度越高,聚合物分子链活动性差,因而对于发生的可逆高弹形变恢复性差,易产生残余内应力口例如,一些分子链中含有苯环的聚合物,如PC,PPO,PP 第,其相应制品的内应力偏大.⑵分子链的极性一分子链的极性越大,分子间相互吸引的作用力越大,从而使分子间相互移动困难增大,恢复可逆弹性形变的程度减小,导致残余内应力大.例如,一些分子链中含有染基,酯基,睛基等极性基团的塑料品种,其相应制品的内应力较大.⑶取代基团的位阻效应大分子侧基取代基团的体积越大,则妨碍大分子链自由运动导致残余内应力加大.例如,聚苯乙烯取代基团的苯基体积较大,因而聚苯乙烯制品的内应力较大.几种常见聚合物的内应力大小顺序如下:PPO>PSF>PC>ABA>PP>HDPE塑料内应力的降低与分散(1)原料配方设计1)选取分子量大,分子量分布窄的树脂聚合物分子量越大,大分子链间作用力和缠结程度增加,具制品抗应力开裂能力较强;聚合物分子量分布越宽,其中低分子量成分越大,容易首先形成微观撕裂,造成应力集中,便制品开裂.2)选取杂质含量低的树脂聚合物内的杂质即是应力的集中体,又会降低塑料的原有强度,应将杂质含量减少到最低程度.3)共混改性易出现应力开裂的树脂与适宜的其它树脂共混,可降低内应力的存在程度.例如,在PC中混入适量PS,PS呈近似珠粒状分散于PC连续相中,可使内应力沿球面分散缓解并阻止裂纹扩展,从而达到降低内应力的目的.再如,在PC中混入适量PE,PE球粒外沿可形成封闭的空化区,也可适当降低内应力.4)增强改性用增强纤维进行增强改性,可以降低制品的内应力,这是因为纤维缠结了很多大分子链,从而提高应力开裂能力.例如,30%GFPC勺耐应力开裂能力比纯PC提高6倍之多.5)成核改性在结晶性塑料中加入适宜的成核剂,可以在其制品中形成许多小的球晶,使内应力降低并得到分散.(2)成型加工条件的控制在塑料制品的成型过程中,凡是能减小制品中聚合物分子取向的成型因素都能够降低取向应力;凡是能使制品中聚合物均匀冷却的工艺条件都能降低冷却内应力凡有助于塑料制品脱模的加工方法都有利于降低脱模内应力.对内应力影响较大的加工条件主要有如下几种.①料筒温度较高的料筒温度有利于取向应力的降低,这是因为在较高的料筒温度,熔体塑化均匀,粘度下降,流动性增加,在熔体充满型腔过程中,分子取向作用小,因而取向应力较小.而在较低料筒温度下,熔体粘度较高,充模过程中分子取向较多,冷却定型后残余内应力则较大.但是,料筒温度太高也不好,太高容易造成冷却不充分脱模时易造成变形,虽然取向应力减小,但冷却应力和脱模应力反而增大.②模具温度模具温度的高低对取向内应力和冷却内应力的影响都很大.一方面,模具温度过低,会造成冷却加快,易使冷却不均匀而引起收缩上的较大差异,从而增大冷却内应力;另一方面,模具温度过低,熔体进入模具后,温度下降加快,熔体粘度增加迅速,造成在高粘度下充模,形成取向应力的程度明显加大.模温对塑料结晶影响很大,模温越高,越有利于晶粒堆砌紧密,晶体内部的缺陷减小或消除,从而减少内应力.另外,对于不同厚度塑料制品,其模温要求不同.对于厚壁制品其模温要适当高一些. 以PC为例,其内应力大小与模具温度的关系如表5-5所示.③注射压力注射压力高,熔体充模过程中所受剪切作用力大,产生取向应力的机会也较大.因此,为了降低取向应力和消除脱模应力,应适当降低注射压力..以PC为例,其内应力大小与注射压力的关系如表5-6所示..④保压压力保压压力对塑料制品内应力的影响大于注射压力的影响.在保压阶段,随着熔体温度的降低,熔体粘度迅速增加,此时若施以高压,必然导致分子链的强迫取向,从而形成更大的取向应力.⑤注射速度注射速度越快,越容易造成分子链的取向程度增加,从而引起更大的取向应力.但注射速度过低,塑料熔体进入模腔后,可能先后分层而形成熔化痕,产生应力集中线,易产生应力开裂.所以注射速度以适中为宜.最好采用变速注射,在速度逐渐减小下结束充模.⑥保压时间保压时间越长,会增大塑料熔体的剪切作用,从而产生更大的弹性形变,冻结更多的取向应力.所以,取向应力随保压时间延长和补料量增加而显著增大.⑦开模残余压力应适当调整注射压力和保压时间,使开模时模内的残余压力接近于大气压力,从而避免产生更大的脱模内应力.(3)塑料制品的热处理塑料制品的热处理是指将成型制品在一定温度下停留一段时间而消除内应力的方法.热处理是消除塑料制品内取向应力的最好方法.对于高聚物分子链的刚性较大,玻璃化温度较高的注塑件;对壁厚较大和带金属嵌件的制件;对使用温度范围较宽和尺寸精度要求较高的制件;时内应力较大而又不易自消的制件以及经过机械加工的制件都必须进行热处理.对制件进行热处理,可以使高聚物分子由不平衡构象向平衡构象转变,使强迫冻结的处于不稳定的高弹形变获得能量而进行热松弛,从而降低或基本消除内应力常采用的热处理温度高于制件使用温度10~20C或低于热变形温度5~10c.热处理时间取决于塑料种类,制件厚度,热处理温度和注塑条件.一般厚度的制件,热处理1~2小时即可,随着制件厚度增大,热处理时间应适当延长.提高热处理温度和延长热处理时间具有相似的效果,但温度的效果更明显些.热处理方法是将制件放入水,甘油,矿物油,乙二醇和液体石蜡等液体介质中,或放入空气循环烘箱中加热到指定温度,并在该温度下停留一定时间,然后缓慢冷却到室温.实验表明,脱模后的制件立即进行热处理,对降低内应力,改善制件性能的效果更明显.此外,提高模具温度,延长制件在模内冷却时间,脱模后进行保温处理都有类似热处理的作用.尽管热处理是降低制件内应力的有效办法之一,但热处理通常只能将内应力降低到制件使用条件允许的范围,很难完全消除内应力.对PC制件进行较长时间的热处理时,PC分子链有可能进行有序的重排,甚至结晶,从而降低冲击韧性,使缺口冲击强度降低.因而,不应把热处理作为降低制件内应力的唯一措施.⑷塑料制品的设计①塑料制品的形状和尺寸在具体设计塑料制品时,为了有效地分散内应力,应遵循这样的原则:制品外形应尽可能保持连续性,避免锐角,直角,缺口及突然扩大或缩小.对于塑料制品的边缘处应设计成圆角,其中内圆角半径应大于相邻两壁中薄者厚度的70犯上;外圆角半径则根据制品形状而确定.对于壁厚相差较大的部位,因冷却速度不同,易产生冷却内应力及取向内应力.因此,应设计成壁厚尽可能均匀的制件,如必须壁厚不均匀,则要进行壁厚差异的渐变过渡.②合理设计金属嵌件塑料与金属的热膨胀系数相差5~10倍,因而带金属嵌件的塑料制品在冷却时,两者形成的收缩程度不同,因塑料的收缩比较大而紧紧抱住金属嵌件,在嵌件周围的塑料内层受压应力,而外层受拉应力作用,产生应力集中现象.在具体设汁嵌件时,应注意如下几点,以帮助减小或消除内应力.a.尽可能选择塑料件作为嵌件.b.尽可能选择与塑料热膨胀系数相差小的金属材料做嵌件材料,如铝,铝合金及铜等.c.在金属嵌件上涂覆一层橡胶或聚氨酯弹性缓冲层,并保证成型时涂覆层不熔化可降低两者收缩差.d.对金属嵌件进行表面脱脂化处理,可以防止油脂加速制品的应力开裂.e.金属嵌件进行适当的预热处理.f.金属嵌件周围塑料的厚度要充足.例如,嵌件外径为D,嵌件周围塑料厚度为h,则对铝嵌件塑料厚度h>0.8D;对于铜嵌件,塑料厚度h>0.9D.g.金属嵌件应设计成圆滑形状,最好带精致的滚花纹.③塑料制品上孔的设计塑料制品上孔的形状,孔数及孔的位置都会对内应力集中程度产生很大的影响.为避免应力开裂,切忌在塑料制品上开设棱形,矩形,方形或多边形孔.应尽可能开设圆形孔,其中椭圆形孔的效果最好,并应使椭圆形孔的长轴平行于外力作用方向.如开设圆孔,可增开等直径的工艺圆孔,并使相邻两圆孔的中心连接线平行于外力作用方向,这样可以取得与椭圆孔相似的效果;还有一种方法,即在圆孔周围开设对称的槽孔,以分散内应力.(5)塑料模具的设计在设计塑料模具时,浇注系统和冷却系统对塑料制品的内应力影响较大,在具体设计时应注意如下几点.①浇口尺寸过大的浇口将需要较长的保压补料时间,在降温过程中的补料流动必定会冻结更多的取向应力,尤其是在补填冷料时,将给浇口附近造成很大的内应力.适当缩小浇口尺寸,可缩短保压补料时间,降低浇口凝封时模内压力,从而降低取向应力.但过小的浇口将导致充模时间延长,造成制品缺料.②浇口的位置浇口的位置决定厂塑料熔体在模腔内的流动情况,流动距离和流动方向..当浇口设在制品壁厚最大部位时,可适当降低注射压力,保压压力及保压时间,有利于降低取向应力.当浇口设在薄壁部位时,宜适当增加浇口处的壁厚,以降低浇口附近的取向应力.熔体在模腔内流动距离越长,产生取向应力的几率越大.为此,对于壁厚,长流程且面积较大的塑料件,应适当分布多个浇口,能有效地降低取向应力,防止翘曲变形.另外,由于浇口附近为内.应力多发地带,可在浇口附近设汁成护耳式浇日,使内应力产生在护耳中,脱模后切除内应力较大的护耳,可降低塑料制品内的内应力.③流道的设计设计短而粗的流道,可减小熔体的压力损失和温度降,相应降低注射压力和冷却速度,从而降低取向应力和冷却压力.④冷却系统的设计冷却水道的分布要合理,使浇口附近,远离浇口区,壁厚处,壁薄处都得到均匀且缓慢的冷却,从而降低内应力,⑤顶出系统的设计要设计适当的脱模锥度,较高的型芯光洁度和较大面积的顶出部位,以防止强行脱模产生脱模应力.检查塑料件的应力的方法主要是溶剂浸渍法.用冰醋酸浸30s,晾干,发白处即是应力集中处.应力大时塑料会开裂,裂纹越多表示应力越大.也可以浸2rain,裂纹更深更明显. 可以用甲乙酮和丙酮1:1的混合液浸15s,来代替冰醋酸浸渍.消除应力的方法有加热法,即在65〜70c下烘4h.小件可以用25%勺丙酮水溶液浸泡30rain来消除应力.应力太大时,这两种方法均无效,零件不能电镀。
内应力的产生及解决对策

内应力的产生及解决对策一般射出成品定型前,存在成品内部的压力约为300kg/cm2 -500kg/cm2之间,如因调整不当造成射胶压力过高,射入模内虽经过浇道、浇口、成品之间的阻力以及成品逐渐冷却,压力逐渐之降低,而存在成品内部进胶口及远端之压力不同,成品经过一段时日于热接触,内应力渐渐释放出来而造成变形或破裂。
内应力太高时,可实施退火处理解决。
内应力的产生:(1)过度充填。
(2)肉厚不均,gate开设在肉薄处。
(3)密度太商而造成脱膜困难。
(4)埋入件周围应变所致,易造成龟裂及冷热差距过大而使收缩不同所致,欲使埋入件周围充填饱模,需施加较大的射压,形成有过大的残留应力。
(5)直接浇口肉薄而又浅口者极易残留应力。
(6)结晶性塑胶、冷却太快内应力不易释放出来。
解决及对策:(1)提高料温、模温,在各原料标准条件内设定。
(2)缩短保压时间。
(3)非结晶性塑胶,保压压力不需太高,乃因较不会缩水。
(4)肉厚设计要均匀gate开设在肉厚处。
(5)顶出要均匀。
(6)埋植件要预热(用夹子或手套塞入)。
(7)避免用新次料混合,如PC易加水分解,如需混合要彻底烘干。
(8)加大竖浇口、横浇道、浇口等,以减少流动阻力,成形品远处易于传达。
(9)已发生之产生可实施退火处理,依二及二-1之条件实施。
(10)加大射嘴射径,长射嘴需加热片控制。
(11)工程塑胶及加玻织者需用模温60℃以上成型。
产品易脆裂的原因及解决方法。
产品易脆裂是产品使用水口料和次料太多造成产品易脆裂,或是料在料管内停留时间过长,造成胶料老化,使产品易脆裂。
增加新料的比例,减少水口料回收使用次数,一般不能超过三次,避免胶料在料管内长时间停留内部应力,致使总应力值高出塑料的破坏强度而产生的破裂。
化学应力破裂在成型品的装配过程中,使用润滑剂、洗剂等时,其所含有的一部分物质可诱发产品破裂。
根据产品的脆弱结构、残留应力标准,是否产生破裂存在一定的差异,受温度压力等的影响。
- 1、下载文档前请自行甄别文档内容的完整性,平台不提供额外的编辑、内容补充、找答案等附加服务。
- 2、"仅部分预览"的文档,不可在线预览部分如存在完整性等问题,可反馈申请退款(可完整预览的文档不适用该条件!)。
- 3、如文档侵犯您的权益,请联系客服反馈,我们会尽快为您处理(人工客服工作时间:9:00-18:30)。
内应力的产生及解决对策一般射出成品定型前,存在成品内部的压力约为300kg/cm2 -500kg/cm2之间,如因调整不当造成射胶压力过高,射入模内虽经过浇道、浇口、成品之间的阻力以及成品逐渐冷却,压力逐渐之降低,而存在成品内部进胶口及远端之压力不同,成品经过一段时日于热接触,内应力渐渐释放出来而造成变形或破裂。
内应力太高时,可实施退火处理解决。
内应力的产生:(1)过度充填。
(2)肉厚不均,gate开设在肉薄处。
(3)密度太商而造成脱膜困难。
(4)埋入件周围应变所致,易造成龟裂及冷热差距过大而使收缩不同所致,欲使埋入件周围充填饱模,需施加较大的射压,形成有过大的残留应力。
(5)直接浇口肉薄而又浅口者极易残留应力。
(6)结晶性塑胶、冷却太快内应力不易释放出来。
解决及对策:(1)提高料温、模温,在各原料标准条件内设定。
(2)缩短保压时间。
(3)非结晶性塑胶,保压压力不需太高,乃因较不会缩水。
(4)肉厚设计要均匀gate开设在肉厚处。
(5)顶出要均匀。
(6)埋植件要预热(用夹子或手套塞入)。
(7)避免用新次料混合,如PC易加水分解,如需混合要彻底烘干。
(8)加大竖浇口、横浇道、浇口等,以减少流动阻力,成形品远处易于传达。
(9)已发生之产生可实施退火处理,依二及二-1之条件实施。
(10)加大射嘴射径,长射嘴需加热片控制。
(11)工程塑胶及加玻织者需用模温60℃以上成型。
产品易脆裂的原因及解决方法。
产品易脆裂是产品使用水口料和次料太多造成产品易脆裂,或是料在料管内停留时间过长,造成胶料老化,使产品易脆裂。
增加新料的比例,减少水口料回收使用次数,一般不能超过三次,避免胶料在料管内长时间停留内部应力,致使总应力值高出塑料的破坏强度而产生的破裂。
化学应力破裂在成型品的装配过程中,使用润滑剂、洗剂等时,其所含有的一部分物质可诱发产品破裂。
根据产品的脆弱结构、残留应力标准,是否产生破裂存在一定的差异,受温度压力等的影响。
因化学药品造成的破裂,其破裂面根干净,有时会产生光泽,可轻易得到确认。
为了防止因化学应力引起的破裂,工艺上应禁止使用可诱发破裂的化学药品。
在用户的使用条件下,会形成问题的配件应通过改变材料等方法作到防患于未燃。
引发化学应力破裂的化学药品如下:冰乙酸、增塑剂(DOP等)。
酒精类、石蜡系列的油脂、酯、过多的硅系列脱模剂、汽油石油等油类、豆油等食用油、溶剂类等。
塑料注射成形零件由于结构设计,模具设计和工艺的局限性,在注塑和冷却过程中总会同时伴有压力和拉力的产生,而较高的残余应力(表面拉力)将会导致零件过早失效。
为了有效规避零部件产生这种失效,更合理的设计和工艺是必需的。
同时,快速而有效的检测在研发和生产过程中可以帮助我们及时发现缺陷,并可避免问题的扩散。
目前评估塑料注射成形零件表面及附近区域残余应力的方法之一是溶剂沉浸测试法。
沉浸后,高应力集中区域会有相应的裂纹产生,以此我们就可以快速有效地对设计和工艺进行评估和改进。
以下部分是主要树脂生产商GE和Bayer推荐的适合于各自主要产品的溶剂测试法。
我们需要在供应商品质控制流程中加入该检测结果。
GEP Lexan/Cycoloy系列塑料Lexan 系列(PC):常用于手机镜片,导光板,机壳。
Cycoloy系列(PC+ABS):常用于手机机壳。
对于用Lexan和Cycoloy系列塑料成形的零件,内应力的检查都可以采用以下方法:1.醋酸沉浸法:(1)将零件完全浸入24摄氏度的冰醋酸中30秒;(2)取出后立即清洗,后晾干检查表面;(3)仔细观察外观,若有细小致密的裂纹,说明此处有应力存在,裂纹越多,应力越大;(4)重复上述操作,在冰醋酸中浸2分钟,再检查零件,若有深入塑料的裂纹,说明此处有很高的内应力,裂纹越严重,内应力越大。
2.甲乙酮 + 丙酮沉浸法:将零件完全浸入21摄氏度的1:1的甲乙酮 + 丙酮的混合液中,取出后立即甩干,依上法检查,有应力的零件应在60-75摄氏度下加热2-4小时以清除应力,也可在25%的丙酮中浸泡30分钟去除应力。
Bayer Makrolon/Bayblend系列塑料Makrolon 系列(PC):常用于手机镜片,导光板,键盘,机壳等。
Bayblend系列(PC+ABS):常用于手机机壳。
以下介绍的TnP(toluene and n-propyl alcohol甲苯+正苯醇)溶剂测试法仅适用于Makrolon(PC),对于Bayblend(PC+ABS)系列,只需将溶剂中的甲苯(Toluene)换为乙酸乙酯(Ethyl Acetate)在按相同方法测试即可。
1.TnP测试法在甲醛和正苯醇的容积比1:10的情况下,可以适用于:(1) PC注塑成形零件但无外部负荷要求;(2) 装配件中PC注塑成形零件(作为非主要零件)。
经验表明在沉浸3分钟后,残余拉力高于2,900psi(20Mpa)的部位会开始出现龟裂。
2.TnP测试法在甲醛和正苯醇的容积比1:3的情况下,可以适用于:(1) PC注塑成形零件且有外部负荷要求;(2) 装配件中的PC注塑成形零件(作为主要零件)。
经验表明在沉浸3分钟后,残余拉力高于1,450psi(10Mpa)的部位会开始出现龟裂。
3.TnP 具体检测方法:1. 准备足量的溶剂(1:10或1:3);2. 将被检零件沉浸在摄氏23度的TnP溶剂中3分钟。
注意:检测前零件应冷却至室温。
3. 取出后立即用清水清洗,擦干;4. 零件清洗擦干后,仔细检查外观是否有龟裂。
如果观察有任何异常,则说明由于可能的零件设计或模具设计或工艺不合适产生了过多的残余应力。
可以用甲乙酮和丙酮1:1的混合液浸15s,来代替冰醋酸浸渍。
消除应力的方法有加热法,即在65~70℃下烘4h。
小件可以用25%的丙酮水溶液浸泡30rain来消除应力。
应力太大时,这两种方法均无效,零件不能电镀1.邵氏硬度ASTM D2240试验范围:邵氏硬度用于确定塑料或橡胶等软性材料的相对硬度. 它测量了规定压针在指定压强和时间条件下的针入度. 硬度值用来识别或指定特殊硬度的塑料,也可作为多批材料的质量控制.试验方法:将试样置于硬而平的台面上. 把硬度计的压针压入试样内, 并保证它与台面平行. 每一秒钟读一数(或由试验者决定).试样规格:通常, 试样厚度为6.4mm(0.25英寸). 可将几个试样重叠,以达到上述高度, 但最好用一个试样.试验数据:硬度值由硬度计读出. 常见的硬度计有A型和D型. A型用于较软材料;D 型用于较硬材料.2.洛氏硬度ASTM D785, ISO 2039试验范围:洛氏硬度试验是基于试样上施加不同负荷时压入试样的深度差的硬度测量方法. 硬度值无量纲, 通常用R, L, M, E和K标尺给出. 每个标尺表示的硬度值越高, 材料越硬.试验方法:将标准试样置于洛氏硬度计的表面. 施加初负荷, 并调零. 放开控制杆,施加主负荷. 15秒之后将主负荷卸除. 15秒钟静置, 使试样恢复, 读出初负荷下的硬度值.试样规格:标准试样的厚度为6.4mm(0.25英寸), 可以是注塑的, 也可以是从片材上切下来的.试验数据:R, L, M,E或K标尺的硬度值直接从表中读取. 每个标尺的硬度值读数越高,材料越硬. R, M 标尺通常用于塑料.3.巴柯尔硬度ASTM D2583试验范围:巴柯尔硬度用于确定增强和非增强型刚硬塑料的硬度.试验方法:将试样置于巴柯尔硬度仪的压头下方, 施加一定压力, 直到表中指针达到最大值. 压入的深度转换为绝对巴柯尔硬度值.试样规格:试样厚度不得小于1/16 英寸.试验数据:数据由仪器给出, 表现为巴柯尔硬度值.光泽度透明塑料的雾度和透光率黄色指数(YI)透明有机塑料折射指数(折光率)1.光泽度ASTM D2457, D523试验范围:镜面光泽度是光被某种材料反射时反射光强度的量度. 光泽度可以是材料所固有的, 也可以是成型过程或表面网纹的结果. 光泽度也受风蚀和表面腐蚀等环境因素的影响. 因此, 光泽度可用于提升产品质量, 开发工艺过程和最终使用性能试验中.试验方法:光泽度的测量, 通常以某种标准为参考给定反射角(20o,60o或85o). 将光泽计的角度调试成适当的角度, 量好口径, 并与光泽计中给定的标准相比较. 将光度计置于试样上, 读取数据.试样规格:大于光度计底面的平的试样即可. 最小可能尺寸为45×145mm(1.75"×5.625").试验数据:20o 光泽度(%)60o 光泽度(%)85o 光泽度(%)2.透明塑料的雾度和透光率ASTM D1003 (方法B)试验范围:雾度是射入透明材料中的光由于散射作用而导致的不清晰和/或闪耀的程度, 可以是材料本身固有的性质,或是成型过程的结果. 它也可能是由表面网纹或风蚀、表面腐蚀等环境因素造成的. 透光率是测定透过试样的光通量的. 因此, 雾度和透光率对于提升产品质量, 开发工艺过程和最终使用性能试验中十分有用.试验方法:BYK 加德纳分光光度计是一种高自动仪器. 指定光源、观测角度和参比色之后, 将试样插入试样架中, 读数. 读三个数, 取平均.试样规格:任何可以被试样架夹住的平形试样均可, 但最常用的是50mm(2")或100mm(4")圆形试样.试验数据:雾度(%)总透光率(%)散射率(%)(diffuse transmittance)3.黄色指数(YI)ASTM E313试验范围:黄色指数由分光光度计的读数计算而得, 描述了一种试样从无色透明或白色到黄色的颜色变化. 这一试验最常用于评价一种材料在真实或模拟的日照下的颜色变化.试验方法:试样的包装、处理和准备(最好不要有清洁过程)过程会改变试样表面, 进而影响试验结果. 黄色指数测定试验是一较长时间段内一系列的相对测量, 因此在测试之前, 首先应该定义上述因素. BYK 加德纳分光光度计是一种高自动仪器. 指定光源、观测角度和参比色之后, 将试样插入试样架中, 读数. 读多个数,取平均.试样规格:T任何可以被试样架夹住的平形试样均可, 但最常用的是4"(100mm)圆形试样.试验数据:黄色指数(YI)4.透明有机塑料折射指数(折光率)ASTM D542试验范围:折光率是光在真空中的传播速率与在透明介质中的传播速率之比. 折光率可用来计算一束光从一透明介质进入另一透明介质时的折射角. 因此, 折光率用于光学棱镜的设计和透明塑料的质量控制检验.试验方法:A sm滴一小滴接触液于棱镜中心, 再将试样放上去. 通过目镜,将光源、index arm、compensator drum 与试样对齐. 由折射仪读出折光率的数值.试样规格:任何形状的可置于折射仪棱镜上的抛光表面面的试样都可以使用. 最常用的是一面为6.3×12.7mm以上的试样.试验数据:折光率介电常数和介质损耗因子介电强度表面电阻率/体积电阻率1.介电常数和介质损耗因子ASTM D150IEC 60250试验范围:介电常数用于衡量绝缘体储存电能的性能. 它是两块金属板之间以绝缘材料为介质时的电容量与同样的两块板之间以空气为介质或真空时的电容量之比. 介质损耗因子定义为一定频率下绝缘材料的电抗与其电阻的比值. 它测量了绝缘材料的无效性. 如果要将一种材料应用于严格绝缘的用途上, 则它的介电常数越小越好. 如果一种材料会应用在需要高电抗的电器上, 则需要高损耗因子. 本试验可在10Hz到2MHz的不同频率范围上进行.试验方法:将试样置于两块金属板中, 测定其电容量. 再将试样取出, 测两块板之间的电容量. 二者的比值即为介电常数.试样规格:试样必须平整, 且大于测量用的50mm(2 ")圆形电极.试验数据:介电常数=试样为介质时的电容量/空气为介质(或真空)时的电容量2.介电强度ASTM D149IEC 80243试验范围:介电强度是一种材料作为绝缘体时的电强度的量度. 它定义为试样被击穿时, 单位厚度承受的最大电压, 表示为伏特每单位厚度. 物质的介电强度越大, 它作为绝缘体的质量越好.试验方法:有以下三种方法可用来确定绝缘体的介电强度,它们分别是: 短时间法、慢速上升法和逐步法. 每种方法都有着相同的基本装置: 一个试样介于两个电极之间.最常用的方法-短时间法中, 加在两电极间的电压从零开始以相同的速率上升, 直至介质被击穿. 慢速上升法从短时间法确定的击穿电压的50%开始, 以相同的速率上升. 逐级升压法从短时间法确定的50%击穿电压开始,在一段时期内, 以相同的幅度上升, 直到试样被击穿.为了防止由电极到地面arcing, 本实验有时在油中进行.试样规格:建议使用4英寸或以上的方形试样. 任何厚度均可, 但最常用的试样厚度介于0.8mm 到3.2mm(0.032"到0.125")之间试验数据:数据表示为伏特/mil. 介电强度是击穿电压除于试样厚度. 介电强度越高, 绝缘体质量越好.3.表面电阻率/体积电阻率ASTM D257, IFC60093试验范围:表面电阻率是绝缘材料抵抗表面漏泄电流的能力. 体积电阻率是绝缘材料抵抗体内漏泄电流的能力. 表面电阻率、体积电阻率越高, 漏泄电流越小, 材料的导电性能越差.试验方法:将标准规格的试样置于两电极之间, 60秒的时间内, 加500伏特的电压并测量电阻. 计算表面/体积电阻率.试样规格:建议使用4英寸的圆形试样.试验数据:算出表面/体积电阻率.表面电阻率的单位是欧(每平方米)体积电阻率的单位是欧·cm密度吸水性(24小时/平衡)透湿性剥离试验摩擦系数1.密度密度和相对密度ASTM D792, ISO 1183试验范围:密度是单位体积物质的质量。