实验一(铸造内应力的形成及测量分析)
铸造材料中应力产生的原因

铸造材料中应力产生的原因说到铸造材料中应力产生的原因,可能有些小伙伴会觉得有点儿抽象,觉得这个话题一听就有点复杂。
其实呢,真要聊开了,也没那么难理解,反而挺有意思的。
首先你得知道,铸造材料就是那些我们常见的金属,比如铸铁、铝合金这些,都是用来制造各种零件和设备的。
至于应力嘛,说白了就是材料内部的那种“内心挣扎”——它们因为外界的一些原因而变得有点儿“紧张”,甚至会发生变形或开裂。
是不是听起来有点像我们平时压力山大的感觉?铸造材料也是一样的,承受不住压力,它们也会出问题。
那什么原因会让这些材料产生应力呢?嗯,首先就是温度变化。
你想啊,铸造过程中材料融化成液态后,再倒入模具里冷却,温度一高一低,铸造材料就开始收缩和膨胀,这就像是你从夏天一下子跳进了冰水里,身体都不舒服,材料也一样,它会因为温度的剧烈变化而产生内应力。
这种情况在铸造过程中最为常见,甚至可以说是“家常便饭”。
如果冷却不均匀,外面冷了,里面还热乎,哎呀,内外不一致的压力就容易导致裂纹和变形。
就是铸造过程中材料本身的成分和结构。
铸造材料的成分不够均匀,或者合金中某些元素不兼容,这样材料内部就可能会出现不均匀的应力。
你可以想象成一锅汤,里面的盐放得不均匀,喝上一口就觉得有些地方咸死了,其他地方却又淡得很。
铸造材料也是这样,成分不均匀,材料就不稳定,产生应力的可能性大大增加。
还有一种情况呢,就是铸造过程中,如果模具设计得不够合理,或者操作不当,也会引发应力。
你想,模具一开始就没有设计好,导致铸件冷却不均匀,或者倒入液态金属的速度不对,铸造材料受到了不必要的拉扯、压迫,嘿,这样一来,材料内部的应力就会悄悄地积累,最后可能爆发,产生裂纹、变形或者直接影响产品的质量。
这也就好比你做事没有规划,搞得自己一团糟,压力也会越来越大,最后搞不好会出现大问题。
咱们说的这些原因,简单来说就是材料本身、铸造过程、环境因素三方面的共同作用。
就像一个人,受到天气变化、身体状况以及外界压力的影响,不同的因素结合在一起,最后才会让他承受不住压力,产生各种应力。
铸造合金应力框实验指导书[3]
![铸造合金应力框实验指导书[3]](https://img.taocdn.com/s3/m/0efb87d926fff705cc170ae4.png)
铸造合金应力框实验指导书
一、实验目的
本实验通过测量具有较大残余铸造应力的框形铸件在应力消失后的应变值,来计算框形铸件中的残余应力的大小。
并据此分析、了解铸件中不同壁厚部分内应力是如何产生的。
二、试样简介
实验所用的试样如下图所示,该试样有三根不同厚度的杆件组成,中间杆件横截面积大,两端杆件横截面积相同且比中间杆件小。
三根杆件的两端均横向连接在一起。
具体尺寸如图所示。
应力框图
三、实验所需仪器设备
实验所需仪器设备如下:钳工工作台、台钳、手锯、游标卡尺、砂轮机等。
四、实验步骤
1、 观察所用试样,并准备有关实验工具;
2、 在中间厚壁杆件上,找沿长度方向上距离100mm 左右的两点,将该位置用砂轮机各打磨出一光滑平面。
3、 用铁錾子在两个平面上各打出一个圆点,然后用游标卡尺测量两点之间的距离。
并记录,计为 L 2。
4、 有手锯将中间杆件在中间部位锯断。
5、 用游标卡尺重新测量前述两点之间的距离,并记录数据,计为 L 3。
6、 计算残余应力
按照胡克定律计算杆件中的残余应力
1E /L σε=⨯
其中 σ 应力; L 1 中间杆的总长; E 弹性模量; 实验所用的试样的材料为灰铸铁,其弹性模量一般为:70~110kN/mm 2, ε 应变; ε=L 3-L 2
五、实验报告要求
1、 根据应力框铸件的形状和结构,分析各部分内残余应力的方向和形成原因。
2、 计算出应力框内应力的大小;
3、 思考题:铸件中的铸造应力有那些类型,如何减少和消除?。
铸造应力形成的原因

铸造应力形成的原因1. 哎呀,大家伙儿快来听听,咱今天聊聊这铸造应力是咋回事。
你们可别小看了这玩意儿,它可是铸造界的大麻烦!就像是咱们吃饭时候的骨头卡喉咙,让人难受得很。
2. 说到铸造应力啊,它就跟人的脾气似的,说来就来,还不好打发。
你看啊,它形成的原因可多着呢!就像是煮稀饭,火候掌握不好,就容易糊锅底。
3. 咱先说说温度不均匀这个坏东西。
你想啊,铸件冷却的时候,表面和内部温度能一样吗?那肯定不能啊!就跟咱们喝热汤一样,表面凉了,里面还烫嘴呢。
这不均匀的温度,就跟两口子吵架似的,闹得铸件里面鸡飞狗跳的,这不就产生应力了嘛。
4. 再说说这冷却速度不一致的问题。
铸件各部位冷却速度不一样,就跟跑步比赛似的,有的跑得快,有的跑得慢。
跑得快的想拉着跑得慢的走,跑得慢的又不乐意,这一拉一扯的,不就闹矛盾了嘛。
这矛盾啊,就是咱们说的应力。
5. 哎呀,别忘了还有这截面厚度不均匀的毛病。
你看啊,就像是咱们穿衣服,有的地方厚,有的地方薄。
厚的地方暖和,薄的地方凉飕飕的,这不就别扭了嘛。
铸件也是一样,厚薄不均匀,冷却起来就不舒服,这不就憋出应力来了。
6. 再来说说这金属收缩的问题。
哎呀,这可有意思了。
你想啊,铸件冷却的时候,就跟人减肥似的,身材越来越小。
但是呢,有的地方瘦得快,有的地方瘦得慢,这不就跟穿紧身衣似的,憋得慌啊。
这憋屈劲儿,就是咱们说的应力。
7. 还有啊,这金属相变也是个捣蛋鬼。
就跟人变脸似的,一会儿这样,一会儿那样。
金属在冷却过程中,结构发生变化,体积也跟着变,这不就跟变魔术似的。
但是呢,这变化不均匀,就跟穿鞋不合脚似的,走起路来别别扭扭的,这不就产生应力了嘛。
8. 哎呀,差点忘了说这模具的问题。
模具要是不听话,不让铸件自由收缩,那可就麻烦了。
就跟小孩子长个子,裤子不让你长似的,憋得慌啊。
这憋屈劲儿,不就是应力嘛。
9. 再说说这浇注温度的事儿。
温度高了呢,就跟火锅烫嘴似的,收缩量大,应力就大。
温度低了呢,又跟喝凉水似的,金属流动性差,容易产生缺陷,这缺陷啊,就跟绊脚石似的,也会引起应力。
铸造应力和流动性实验指导书

铸造应力检测实验指导书一、实验简介本实验利用不等粗三杆应力框模拟铸造合金凝固过程中铸造应力的产生和演变过程,以及其与温度的关系,借助于热电偶和拉压传感器,通过模数转换将信号动态显示于电子计算机屏幕上。
是学生理解合金成分、逐渐结构和温度对铸造应力的影响,学习拉力传感器和热电偶的使用方法,具有在材料成型及控制工程实践中基本掌握并使用各种技术、技能和现代化工程工具的能力。
主要内容:1、铸造合金凝固过程中铸造应力的产生和演变过程,以及其与温度的关系;2、合金成分对铸造应力的影响。
二、实验原理金属材料及其合金由液态变为固态时产生体积收缩,由于铸件各个部位厚度不同,开始凝固的时间也不同,所以当铸件某一部位的收缩受到其他部位的阻碍时,则在铸件中产生铸造应力。
本实验利用不等粗三杆应力框(中间粗、两边细)模拟铸造合金凝固过程中铸造应力的产生和演变过程,使用热电偶和拉压传感器分别检测应力框三根杆的温度和应力。
三、实验步骤及操作方法1、主要参数应力框尺寸:粗杆:20×20×300 mm细杆:20×10×300 mm粗杆:出厂时装1000kgf的拉压力传感器细杆:两细杆的应力和与粗杆大小相等、方向相反。
实验合金合金:Al-3%Cu合金,约1kg。
2、实验方法1)造型:用定位销锁紧好上箱、模板和下箱造下箱造上箱并扎通气孔上箱和模板一起起模并翻转 模板从上箱上起模修型。
2)做外浇口箱。
3)合箱:在连接套上带螺纹的一端按装好铸焊和联接试件的3*M16螺丝 先将下箱按放在仪器平台上 用定位销调正下箱与平面台上定位孔的位置 清理三个接口处的砂子(上箱和下箱) 锁紧定位销由上箱插入下箱,放入平台定位孔 放上外浇口箱准备浇注。
4)热电偶一对放在中间杆中点处,另一对放在侧杆的中点处,另一端与模数转换器连接。
5)配料,使用电阻炉熔化合金,当温度达到合金液相点+50~80℃时保温。
6)启动计算机,将屏幕上的初始信号调零。
铸造应力的产生机理

铸造应力的产生机理
在现代工业生产中,铸造是一种常见的加工方式,而在铸造过程中,铸造应力的产生是一个不可避免的问题。
那么,铸造应力产生的机理是什么呢?下面将从几个方面进行详细阐述。
第一、温度梯度的影响
在铸造过程中,金属液凝固后会发生收缩,这时候就会产生应力。
其中最主要的就是“固态相变应力”。
它是由于金属在凝固时,由高温到低温有一个温度梯度的分布,导致了铸件的体积收缩不均匀而产生的。
这种应力主要集中于铸件的极端部分,也就是沿着铸件壁厚方向分布。
第二、金属流动的影响
在铸造过程中,金属液在浇注到模型中之后,会在模型中逐渐凝固,这时候颗粒之间的分离,分布不均也会导致应力的产生。
同时,金属液还会受到气流、浇口等因素的影响,因而产生没有规律的金属流动。
这些因素都会导致金属拉伸和压缩变形,从而使得金属内部出现应力。
第三、金属内部组织结构的影响
金属的内部结构是产生应力的关键之一。
铸造过程中,金属液在凝固的过程中,会出现晶粒拒绝现象,从而使得铸造材料存在着不同的晶粒组织和晶界,而不同的晶粒组织和晶界之间的应变状态是不同的,所以也就导致了应力的产生。
综上所述,铸造应力的产生机理主要包括:温度梯度的影响、金属流动的影响以及内部组织结构的影响等。
在铸造过程中,我们需要充分考虑这些因素,做好相关工作,以保证铸件的质量和安全性。
同时,在生产过程中,还需要加强管理,提高工人的技能水平,以及加强设备的维护保养,以确保铸造过程的有效运行。
铸造应力产生的原因

铸造应力产生的原因铸造应力是指金属在铸造过程中产生的内应力,其产生的原因主要有以下几个方面:1. 温度梯度引起的热应力:在铸造过程中,金属液体首先接触到模具的壁面,由于模具的温度较低,金属液体在接触面上迅速冷却凝固,而内部金属液体温度较高。
这样就会在金属件内部产生温度梯度,从而引起热应力。
当金属件表面和内部的温度梯度过大时,会使金属产生较大的热应力。
2. 冷却收缩引起的应力:金属在铸造过程中,由于冷却收缩而产生体积变化。
当金属凝固时,由于温度的降低,金属的体积会收缩。
而在铸造过程中,由于金属液体与模具接触,受到模具的限制而不能自由收缩,从而产生应力。
这种应力主要集中在金属的外层,如果收缩阻力较大,就会产生较大的应力。
3. 金属凝固过程中的相变引起的应力:在金属凝固过程中,由于相变的发生,会引起体积的变化,从而产生应力。
例如,当金属凝固时,晶粒从液态相变为固态相,由于晶粒的体积较大,就会产生应力。
这种应力主要集中在晶粒的界面上,如果晶粒的体积变化较大,就会产生较大的应力。
4. 金属流动引起的应力:在金属液体从浇口流入模腔的过程中,由于金属液体的流动速度不同,就会产生流动应力。
当金属液体流动速度较大时,由于惯性的作用,就会产生较大的流动应力。
这种应力主要集中在金属液体的表面层,如果流动速度较大,就会产生较大的应力。
5. 内部缺陷引起的应力:金属在铸造过程中,由于内部存在缺陷,如气孔、夹杂物等,就会在凝固过程中引起应力集中。
这些缺陷会使金属的力学性能降低,并且在受力作用下容易产生断裂。
以上是铸造应力产生的几个主要原因。
在铸造过程中,应合理控制这些应力的产生,采取相应的措施来减小应力的影响。
例如,可以通过合理设计模具,控制金属液体的流动速度,减小热应力的产生;在金属凝固过程中,可以采取适当的降温措施,减小冷却收缩引起的应力;同时,还可以通过改善金属的化学成分和净化金属液体,减小内部缺陷的产生,从而减小应力的影响。
铸造加工中的变形和应力分析

铸造加工中的变形和应力分析在铸造加工生产中,变形和应力分析是一项非常重要的任务。
通过对铸造加工过程中的变形和应力进行分析,我们可以更好地了解铸造加工的特性,优化设计和工艺,提高生产效率和质量。
首先,让我们来看一下铸造加工中的变形分析。
铸造加工过程中,金属材料经过加热、注模、凝固和冷却等过程,会产生一定的变形。
这些变形通常由以下几个因素引起:1.物理因素:如热膨胀、收缩等。
2.化学因素:如内部应力、晶格结构等。
3.加工因素:如注模压力、铸模温度、施力方向等。
为了减少这些变形,我们需要采取一些措施。
比如,可以通过合理控制铸造材料的成分、加热温度和加工过程中的操作方法等来减少变形。
此外,还可以使用一些辅助工具,如模具夹具、加热器等来帮助控制变形。
另外,对于一些需要高精度的零件,可以采用精密投影仪和坐标测量系统等工具来精确测量和控制变形。
除了变形分析外,应力分析也是铸造加工中不可忽视的一环。
在铸造加工过程中,很容易产生各种应力,如热应力、内应力、剪切应力等。
这些应力会产生许多不利的影响,如导致零件变形、影响零件的强度和韧性等。
为了减少这些应力,我们需要采取一些措施,例如选择合适的材料和设计合理的零件结构、调整加工过程中的参数等。
此外,我们还可以使用一些辅助工具来帮助进行应力分析和控制。
例如,可以使用有限元分析软件、应力测试仪等工具来帮助进行应力分析和控制。
在实际的铸造加工中,有效的变形和应力分析可以帮助我们更好地预测和控制铸造加工过程中的变形和应力,从而提高生产效率和零件质量。
另外,它也可以给我们提供一些有价值的信息,帮助我们优化设计和工艺,从而进一步提高铸造加工生产的效率和质量。
总之,变形和应力分析是铸造加工生产中非常重要的一环。
通过对变形和应力的分析和控制,我们可以更好地了解铸造加工的特性,提高生产效率和质量。
因此,在铸造加工生产中,我们应该充分重视变形和应力分析,并采取一些有效的措施来进行分析和控制。
铸造应力产生的原因及解决方法

A.产生热应力的原因:由于铸件壁厚不均匀,各部分的冷却速度也不相同,以致在同一时间内,铸件各部分的收缩不一致而造成铸件内部产生应力。
B.防止或消除变形的方法:
(1)基本方法是采用合理的铸造工艺,使铸件的凝固过程符合同时凝固原则;
(2)造型工艺上,采取相应措施以减小铸造应力,如改善铸型﹑型芯的退让性(型芯﹑砂内加入木屑、焦炭末等附加物,控制舂砂松紧度),合理设置浇、冒口等。
(3)铸件结构上,尽量避免牵制收缩的结构,使铸件各部分能自由收缩。
如壁厚均匀,壁和壁之间连接均匀﹑热节小而分散的结构,可减小铸造应力。
(4)去应力退火。
将铸件加热到塑形状态,对灰口铸铁。
金属铸件应力测定实验报告

金属铸件应力测定实验报告一、实验目的本实验旨在通过对金属铸件应力测定实验的进行,了解金属铸件加工过程中的应力分布情况,并掌握应力测定的方法和步骤。
二、实验原理在金属铸件加工过程中,由于化学成分、凝固过程、热处理等因素的影响,铸件内部会产生应力。
应力的大小和分布对铸件的性能和寿命有着重要的影响。
因此,了解铸件内部应力的大小和分布情况就显得尤为重要。
实验中,常用的应力测定方法有两种:一种是切割法,即在铸件上进行切割,然后测量切口两侧的应力;另一种是钻孔法,即在铸件上钻孔,然后测量钻孔周围的应力。
三、实验步骤1. 准备工作:(1)将需要测定应力的铸件上表面清理干净,去掉表面的氧化物和油污等杂质。
(2)准备好应力测量仪器。
常见的应力测量仪器有应力计、应变计等。
2. 应力测定:(1)切割法:①在需要测定应力的位置上,用锯子或切割机进行切割,切口长度一般为5-10mm。
②用应力计或应变计测量切口两侧的应力,记录数据。
(2)钻孔法:①在需要测定应力的位置上,用钻头在铸件上钻孔,钻孔的深度和直径要足够大。
②将应力计或应变计插入钻孔中,测量钻孔周围的应力,记录数据。
四、实验数据处理将所测得的应力数据进行统计和分析,计算出铸件内部应力的大小和分布情况。
可以建立应力分布图,进一步了解铸件内部应力的分布规律。
五、实验注意事项1. 在进行应力测定实验前,务必保证铸件表面清洁干净,避免杂质的干扰。
2. 在进行钻孔法测定时,要注意钻孔的深度和直径,以免造成铸件的破坏。
3. 在进行数据处理时,要保证数据的准确性和可靠性,避免出现误差。
六、实验结论通过本次实验,我们了解了金属铸件加工过程中应力的产生原因和分布情况,掌握了应力测定的方法和步骤。
实验结果对于进一步提高金属铸件的性能和寿命具有重要的指导意义。
3.3.1 铸造应力的形成

铸造应力的形成副教授:陈云
铸造应力的形成
铸造应力
热应力
机械应力由于铸件壁厚不均匀,各部分的冷却速度也不相同,以致在同一时间内,铸件各部分的收缩不一致而造成铸件内部产生的应力,称为热应力。
合金的固态收缩受到铸型或型芯的机械阻碍而形成的内应力,称为机械应力。
铸件在冷却过程中,其固态收缩受到阻碍时,就会在铸件内部产生应力,称为铸造应力。
一、热应力
t 0——t 1 高温阶段,塑性状态,内应力通过塑性变
形消除
t 1 ——t 2 Ⅱ杆弹性状态,Ⅰ塑性状态,Ⅱ杆受拉应
力,Ⅰ受压应力,内应力通过Ⅰ塑性变形消除
t 2 ——t 3 Ⅰ、Ⅱ杆弹性状态,Ⅰ比Ⅱ温度高,Ⅰ收
缩大于Ⅱ,Ⅰ收缩受Ⅱ的阻碍,产生拉应力 热应力使铸件的厚壁或心部受拉伸,薄壁或表层受压缩。
Ⅰ Ⅱ Ⅲ
二、机械应力
铸件冷却到弹性状态以后,由于受到铸型、型芯和浇、冒口等的机械阻碍而产生的应力,称机械应力。
法兰的机械应力
机械应力与热应力共同作用,当大于材料的强度极限时会导致裂纹的形成。
三、减小和消除铸造应力的方法
1、工艺方面:尽量采用合理的铸造工艺,使铸件的凝固过程符合同时凝固原则
2、造型工艺上:采取相应措施以减小铸造应力,如改善铸型、型芯的退让性(型芯、砂内加入木屑、焦碳沫等附加物,控制舂砂松紧度),合理设置浇、冒口等。
3、铸件结构上:尽量避免牵制收缩的结构,使铸件各部分能自由收缩(铸件的结构尽可能对称、铸件的壁厚尽可能均匀)。
4、去应力退火;人工时效;自然时效。
5、消除机械应力可以通过适时开箱加以解决。
谢谢观看。
实验一(铸造内应力的形成及测量分析)

实验一 铸造内应力的形成及测量分析1、实验目的1)了解坩锅炉熔炼原理及工艺过程。
2)测定应力框产生的铸造热应力。
3)分析应力框产生内应力的原因、应力对铸件质量的影响。
2、实验原理根据“T ”形杆冷却过程中形成“粗杆受拉、细杆受压”的原理,设计如图1所示的应力框。
合金浇铸、冷却后,会在应力框的粗、细杆中形成不同性质的应力。
将粗杆锯断,将使应力约束条件释放,致使应力杆的尺寸发生变化。
测量应力杆的尺寸变化大小,根据虎克定律,便可计算出应力框中应力杆的大小。
应力框尺寸如图1所示,采用潮模砂造型,在电阻坩锅炉中熔炼ZL101合金,浇铸应力框。
3、实验步骤及方法1)手工造型应力框铸型。
2)坩锅电阻炉中熔炼ZL101 合金。
3)浇铸应力框。
4)冷却后清理。
5)将中间的粗杆打两点标志,测量两点距离L 0,然后将中间杆锯断,再测量两点的距离L 1。
6)根据测量结果,计算杆中的铸造应力。
σ= E ε = E (L 1 – L 0)/ L ( N/mm 2)式中: E --- 弹性模量,ZL101 为:72.4×103 N/mm 2;L ---- 中间杆的长度 mm 。
4、实验报告1)画出应力框图,标出细杆和粗杆中存在的铸造应力性质(拉应力为+,压应力为-)。
2)测量、计算铸造应力。
测量结果:L 0、L 1、L ;计算结果:σ3)分析应力框产生的原因和铸造应力对铸件质量的影响。
实测数据:L 0 = 80mm L 1 = 80.5mm L = 300mm图1铸造应力框。
铸造应力的产生、危害及防治措施

金属在凝固冷却的状态时,热胀冷缩引起的体积变化受到来自外界或其来自于本身的制约,就会导致其变形过程受到阻碍,就会产生一个铸造应力。
铸造的方法就是将加热熔融为液体的合金倒入事先准备好的模具中去使其填充满,等到热的液体变冷凝固以后,就得到链初步的毛坯产品。
除此之外,在整个铸造生产的过程中,特别是对于单件进行小批量的生产,如果工人的劳动条件较差、且劳动强度大,铸造的应用过程也会受到一定程度的限制。
铸造应力是当一个铸件冷却到其弹性状态之后,在收缩过程中会受到阻碍,进而产生的一种弹性应力。
铸造应力如果存在于机械设备中,会导致设备的结构强度降低,承载能力下降,使用寿命缩短等。
但通常我们讲的铸造应力一般指的是残余应力。
当铸件有残余应力存在的时候,铸件经过机械加工之后就有可能产生一个新的变形,导致零件的精准度降低、尺寸变差;如果铸件的工作应力和残存应力进行叠加就会损坏到铸件;倘若残存应力一直存在与铸件之内,经过长时间的积累之后就会使得铸件发生形变;如果铸件长时期处的环境都是潮湿有腐蚀性的空气中,那么时间长了以后就可能会让铸件被腐蚀掉。
所以,在浇注完毕的冷却过程中对与铸件中残存的应力的消除的研究是十分有必要的,这对于提升铸件的工艺品质是极其重要的。
当一个铸件凝固之后,伴随着温度的下降,铸件都会变为固态在这个过程中会发生相变,随着铸件变为固态的相变过程,相变体也会发生收缩或者膨胀的过程,由于铸件较为厚的外壁存在,所以外层的温度下降的很快,内层的温度下降的慢,所以壁厚越厚冷却用时越长。
这种现象致使一个完整的铸件的内层和外层以及薄厚不一样的地方的收缩程度不一样,这样的现象会影响到铸件的薄厚和内外层之间发生相互牵制的作用,导致铸件拉深或者发生不可逆的形变。
热应力现象就是由于铸造过程中铸件壁的薄厚不一致在相同的单位时间内它们收缩的程度不同而产生的一种现象。
要去研究热应力形成的条件,需要对金属在冷却的进程中内部的应力是如何进行分布的。
实验应力分析实验报告

实验应力分析实验报告实验应力分析实验报告引言实验应力分析是一项重要的实验技术,它可以帮助我们了解材料在受力时的行为和性能。
通过实验应力分析,我们可以测量和分析材料的应力分布、应变变化以及材料的强度和刚度等关键参数。
本实验报告将介绍实验应力分析的基本原理、实验装置和实验结果,并对实验结果进行分析和讨论。
实验原理实验应力分析是基于材料力学和应变测量原理的。
在实验中,我们通常使用应变计或应变片来测量材料的应变变化。
应变计是一种敏感的应变测量仪器,它可以将材料受力后产生的微小应变转化为电信号。
通过测量这些电信号的变化,我们可以推断出材料的应变分布和应力分布。
实验装置实验应力分析通常需要使用一些特殊的装置和设备。
在本次实验中,我们使用了一台万能材料试验机和一套应变计测量系统。
万能材料试验机是一种常见的实验设备,它可以施加不同的载荷和测量材料的力学性能。
应变计测量系统由应变计和数据采集设备组成,它可以实时记录材料的应变变化,并将数据传输到计算机进行处理和分析。
实验步骤在实验中,我们首先需要选择合适的试样和应变计。
试样的选择要考虑到材料的特性和实验要求。
应变计的选择要根据试样的形状和应变范围来确定。
然后,我们将应变计粘贴在试样表面,并将试样安装到万能材料试验机上。
在施加载荷前,我们需要对应变计进行校准,以确保测量的准确性。
接下来,我们可以施加不同的载荷和测量试样的应变变化。
最后,我们将实验数据导入计算机,并进行数据处理和分析。
实验结果与分析通过实验应力分析,我们得到了试样在不同载荷下的应变数据。
根据这些数据,我们可以绘制应变-载荷曲线,从而分析试样的应力分布和强度特性。
同时,我们还可以计算试样的刚度和弹性模量等力学参数。
通过对实验结果的分析,我们可以得出以下结论:1. 应变分布不均匀:在试样受力过程中,应变分布通常不是均匀的。
这是由于试样的几何形状、材料的性质以及施加的载荷等因素的影响。
通过实验应力分析,我们可以观察到应变的集中区域和变化规律,从而了解材料的应力分布情况。
铸造内应力、变形和裂纹
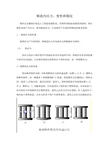
铸造内应力、变形和裂纹铸件完全凝固后便进入了固态收缩阶段,若铸件的固态收缩受到阻碍,将在铸件内部产生应力,称为铸造应力。
它是铸件产生变形和裂纹的基本原因。
1.铸造应力的形成按照应力产生的原因,将铸造应力分为热应力和机械应力两种。
(1)热应力热应力是由于铸件壁厚不均或各部分冷却速度不同,使铸件各部分的收缩不同步而引起的。
它在铸件落砂后仍然存在于铸件内部,是一种残留应力。
1)残留热应力的形成现以框形铸件为例,分析残留热应力的形成过程。
如图3.12中 1) 图所示的框形铸件,由一根粗杆I和两根细杆II组成。
假设铸件完全凝固后,两杆从同一温度T固开始冷却,最后达到同一温度T,两杆的固态冷却曲线如图3.12中2) 图所示。
Tk为临界温度,在此温度以上铸件处于塑性状态。
在此状态下,较小的应力可使铸件发生塑性变形,变形之后应力可自行消除;在Tk温度以下,铸件处于弹性状态,在应力作用下将产生弹性变形,变形之后应力还继续存在。
下面用图3.12中图2)所示的冷却曲线来分析热应力的形成过程。
当铸件处于高温阶段(t0-t1)时,两杆都处于塑性状态,尽管此时两杆的冷速不同、收缩也不同步,但瞬时的应力可通过塑性变形来自行消失,在铸件内无应力产生;继续冷却,冷速较快的杆II进入弹性状态,粗杆I仍然处于塑性状态(t1-t2),此时由于细杆II的冷速较快、收缩较大,所以细杆II会受到拉伸,粗杆I会受到压缩(图b),形成暂时内应力,但此内应力很快因粗杆I发生了微量的受压塑性变形而自行消失(图c);当进一步冷至更低温度时(t2-t3),两杆均进入了弹性状态,此时由于两杆的温度不同、冷却速度也不同,所以二者的收缩也不同步,粗杆I的温度较高,还要进行较大的收缩,细杆II的温度较低,收缩已趋于停止,因此粗杆I的收缩必定受到细杆II的阻碍,使其收缩不彻底,在部产生拉应力;而杆II则受到杆I因收缩而施与的压应力(图d)。
直到室温,残留热应力一直存在。
铸造内应力的形成与消除措施

失, 这 种 应 力称 为 临 时应 力 ; 如 原 因 消 除之 后 应 力 仍 然存在 , 则称 为 残 留应 力 。 热 应 力是 由 于铸 件 壁 厚 不均 匀 ,冷 却速 度 不 同 ,
在 同一 时 间 内铸 件各 部 分 收缩 不一 样 而 引起 的 。 为了
因此 , 常 用 单位 长度 收 缩 量 来表 示 , 它 可导 致 铸 件 形
状、 尺 寸 变化 , 产 生应力和 变形 , 甚 至 使 铸 件 产 生 裂
纹 。
的方 法 。铸 造是 历 史最 为悠 久 的金 属 成 形 方法 , 在 各
种 类 型 的 机 器 设 备 中铸 件 所 占的 比重 很 大 ,如 在 机 床、 内燃 机 中 , 铸 件 占机 器 总重 的 7 0 %~8 0 %, 农 业 机 械 占4 0 %~7 0 %。铸 造 具有 适 应性 广 , 成 本低 等 特 点 。 然而 , 铸 造 生产 工序 繁 多 , 且 一 些 工 艺过 程 难 以精 确 控制 , 这 就使 铸 件 质 量 不稳 定 , 造 成废 品率 高 ; 由 于铸
合金的固态收缩虽然也是体积上的缩减但它只在铸件的尺寸上缩减因此常用单位长度收缩量来表示它可导致铸件形状尺寸变化产生应力和变形甚至使铸件产生裂铸件在凝固之后继续冷却过程中其固态收缩若受到阻碍铸件内部将产生内应力称为铸造内应力
黑龙江科学
第 6卷 2 0 1 5 年 6月
HEI L O NGJ I ANG S C I ENC E
Abs t r a c t :T h e f o u n d r y i s h i s t o y r i s mo s t l o n g me t a l f o r mi n g , c a s t i n g p r o c e s s , a r e s u l t o f c o n n e c t e d v o l u me c h a n g e s
铸造残余应力的测定实验报告

铸造残余应力的测定实验报告1. 实验目的(1) 了解铸造残余应力的产生原因。
(2) 了解用应力框测定铸造残余应力的方法。
(3) 了解退火对消除残余应力的效果。
2. 实验原理2.1 铸造应力铸件在凝固和冷却过程中由于各部分体积变化不一致导致彼此制约而引起的应力称为铸造应力。
铸造应力可分为三种,即热应力、相变应力和收缩应力。
铸造应力可能是暂时性的,当引起应力的原因消除以后,应力随之消失,称为临时应力;否则为残余应力。
铸造应力对铸件质量有重要影响,如果铸造应力超过材料的屈服强度,铸件则产生变形;如果铸造应力超过材料的强度极限时,铸件则产生裂纹。
残余应力还会降低铸件的使用性能,如失去精度、在使用过程中造成断裂或产生应力腐蚀等。
2.2 铸造应力的测定方法——应力框试验法图1为测定铸造残余应力的框形铸件,由于I 杆和II 杆截面尺寸差别大,因而铸造后细杆I 中形成压应力,粗杆II 中形成拉应力。
若在A-A 截面处将粗杆锯开,锯至一定程度时,由于截面变小,粗杆被拉断。
受弹性拉长的粗杆长度较自由收缩条件下的长度缩短,其缩短量∆L 和铸造残留应力成正比,其值可根据锯断前、后粗杆上小凸台的长度(L 0 ,L 1)差求出,即∆L =L 1一L 0。
铸造残留应力σ1和σ2的计算公式为:细杆残留应力σ1=-E)21(211F F L L L +- ,粗杆残留应力σ2=-E )21(1201F F L L L +-图 1 应力框铸件图式中:σ1,σ2——细杆、粗杆中的铸造应力(MPa ); L 0,L 1——锯断前、后小凸台的长度(mm ); F 1,F 2——细杆、粗杆的横截面积(mm 2);L——杆的长度,L=130mm;E——弹性模量,普通灰铸铁取9×104MPa,球墨铸铁取1.8×105MPa。
2.3减小及消除残余应力的方法铸造应力导致铸件翘曲变形甚至开裂,特别是铸件中的残余应力,如不消除,将降低零件的加工精度,在使用中会继续变形,降低机械性能和使用性能。
液态成形应力框架的实验数据分析

液态成形应力框架实验数据分析报告
班级:姓名:学号:
一、实验目的
1、学会区分力与应力两个概念之间的不同
2、认识液态成形过程中铸件内应力的存在;
3、学会分析铸件冷却过程中内应力的演化过程;
4、掌握铸件中内应力的计算方法和过程;
5、针对应力框架,提出减少铸造内应力的具体措施。
二、应力框架内应力的分析、测试与计算
应力框架的材料为灰口铸铁,成形方式为铸造。
1、分析应力框架在铸造过程中产生的内应力
2、锯切应力框架中间梁
对中间梁进行锯切,锯切量超过其直径的1/2后,中间梁自行断开,如图所示。
分析中间梁自行断开的原因。
3、 断口面积的确定
将拉断后的中间梁截取下来,其断面示意图如图所示,经测量中间梁直径为25mm,拉断断口的弦长21.2mm ,计算被拉断部分的面积。
4、拉伸试棒的加工及拉伸试验
将截取的中间梁车削成拉伸试验用的标准试棒,如图所示,在拉伸试验机上进行拉伸试验,测得试样拉断时的载荷为15.7 KN 。
计算应力框架的σb 及应力框架中间梁能够承受的最大拉力。
5、计算应力框架中间梁中的内应力大小
6、根据结果,判断该灰口铸铁的具体牌号
7、针对该应力框架,提出减少铸造内应力的具体措施。
金属铸造中残余应力的数值模拟研究

金属铸造中残余应力的数值模拟研究一、引言金属铸造是一项基础性工艺,它在现代工业生产中占有不可替代的重要地位。
然而,由于金属铸造过程中金属被快速加热和冷却,导致金属铸件内部产生残余应力。
如果残余应力得不到有效控制,将会导致铸件的变形、裂纹、失效等问题,从而影响铸件的功能和质量。
因此,准确地研究金属铸造中残余应力的产生和分布规律,对于提高铸造质量和生产效率具有非常重要的意义。
二、金属铸造中残余应力的产生机制在金属铸造中,铸件内部的残余应力主要有热应力和冷却应力两种。
其中,热应力是由于金属在铸造过程中受到高温冲击而引起的,而冷却应力则是因为金属在冷却过程中收缩而产生的。
具体来说,金属在熔化和注入模具时受到热冲击,温度梯度造成铸件的局部收缩和膨胀,进而形成热应力。
当铸件从高温状态快速冷却到室温时,金属在与模具的接触面上发生冷却收缩,并通过连通的铸造结构传递,最终导致整个铸件内部出现冷却应力。
这些残余应力可以持续存在并在使用中不断积累,对铸件的性能和寿命产生严重影响。
因此,了解金属铸造中残余应力的产生机制和规律,对于减少铸件失效和提高其使用寿命至关重要。
三、金属铸造中残余应力的数值模拟研究为了准确地研究金属铸造中的残余应力和控制其产生,数值模拟已经成为一种有效的方法。
数值模拟可以针对特定材料和工艺,模拟铸件的生产过程,预测铸件内部残余应力、变形等情况,从而为工程师和设计师提供重要的参考依据。
在金属铸造中,一般采用有限元法进行数值模拟,该方法可以将铸造过程分割成许多小区域,精细地描述局部温度、应力、变形等情况,并对铸件的结构以及加工工艺进行优化设计。
(一)数值模拟流程金属铸造中残余应力数值模拟的流程如下:1、建立三维数值模型,并进行网格划分;2、设定边界条件,包括温度、热流、材料物性等参数;3、对模型进行数值计算,模拟铸件的加热、注模、冷却等过程;4、计算铸件内部应力和变形,并分析残余应力的大小和分布情况;5、根据分析结果,优化设计金属铸造的结构和工艺,减少残余应力的产生。
- 1、下载文档前请自行甄别文档内容的完整性,平台不提供额外的编辑、内容补充、找答案等附加服务。
- 2、"仅部分预览"的文档,不可在线预览部分如存在完整性等问题,可反馈申请退款(可完整预览的文档不适用该条件!)。
- 3、如文档侵犯您的权益,请联系客服反馈,我们会尽快为您处理(人工客服工作时间:9:00-18:30)。
实验一 铸造内应力的形成及测量分析
1、实验目的
1)了解坩锅炉熔炼原理及工艺过程。
2)测定应力框产生的铸造热应力。
3)分析应力框产生内应力的原因、应力对铸件质量的影响。
2、实验原理
根据“T”形杆冷却过程中形成“粗杆受拉、细杆受压”的原理,设计如图2所示的应力框。
合金浇铸、冷却后,会在应力框的粗、细杆中形成不同性质的应力。
将粗杆锯断,将使应力约束条件释放,致使应力杆的尺寸发生变化。
测量应力杆的尺寸变化大小,根据虎克定律,便可计算出应力框中应力杆的大小。
应力框尺寸如图2所示,采用潮模砂造型,在电阻坩锅炉中熔炼ZL101合金,浇铸应力框。
3、实验步骤及方法
1)手工造型应力框铸型。
2)坩锅电阻炉中熔炼ZL101 合金。
3)浇铸应力框。
4)冷却后清理。
5)将中间的粗杆打两点标志,测量两点距离L 0,然后将中间杆锯断,再测
量两点的距离L 1。
6)根据测量结果,计算杆中的铸造应力。
σ= E ε = E(L 1 – L 0)/ L ( N/mm 2)
式中: E --- 弹性模量,ZL101 为:72.4×103 N/mm 2;
L ---- 中间杆的长度 mm。
4、实验报告
1)画出应力框图,标出细杆和粗杆中存在的铸造应力性质(拉应力为+,压应力为-)。
2)测量、计算铸造应力。
测量结果:L 0、L 1、L;计算结果:σ
3)分析应力框产生的原因和铸造应力对铸件质量的影响。
图2铸造应力框。