内应力的产生及消除方法
高等数学a2 内应力

高等数学a2 内应力在工程学和物理学领域,内应力是指物体内部的力学应力,也即物体内部由于受到外力作用而产生的应力。
内应力是研究材料在力学作用下变形和破坏的重要参数,对于设计和分析结构的稳定性和耐久性具有重要意义。
一、应力的概念和分类应力是指单位面积上作用的力的大小,是力对面积的分布,常用符号σ表示。
应力可分为正应力和剪应力两大类。
1. 正应力(Normal Stress):正应力是垂直于断面上一个内部点的应力,也就是作用在物体内部的拉力或压力。
正应力常用符号σ表示。
正应力的大小等于单位面积上的力的大小。
2. 剪应力(Shear Stress):剪应力是与物体内部一个点的某个平面上的切力。
剪应力常用符号τ表示。
剪应力是由两个平行力使物体的内部切变产生的。
二、内应力的计算方法1. 简单应力状态:对于只有一个方向的力或只有一个剪力的情况,内应力的计算相对简单。
例如,当物体受到垂直于其表面的力时,内应力的大小等于外力除以面积。
2. 复合应力状态:当物体受到多个力或多个剪力时,内应力的计算就比较复杂了。
此时,需要利用力的分解和向量的加法来确定内应力的大小和方向。
三、应力的均匀分布和不均匀分布1. 均匀应力分布:均匀应力分布是指物体在某一区域内,所有内部点的应力大小相等。
在均匀应力分布的条件下,材料的变形也是均匀的。
2. 不均匀应力分布:不均匀应力分布是指物体在某一区域内,内部点的应力大小不相等。
在不均匀应力分布的条件下,材料的变形也是不均匀的。
在实际工程和物理应用中,通过合理选择材料和结构布置,可以实现均匀应力分布,从而提高结构的稳定性和使用寿命。
四、内应力的影响因素内应力的大小和分布受到多种因素的影响,包括外力的大小和方向、物体的几何形状、材料的性质等。
1. 外力的大小和方向:外力的大小和方向决定了物体内部的力分布,从而对内应力的大小和分布产生影响。
2. 物体的几何形状:物体的几何形状决定了应力的分布规律。
内应力的产生及消除方法
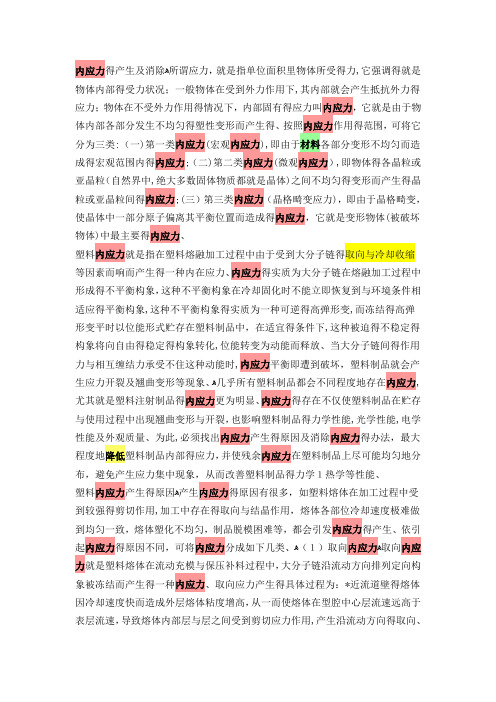
内应力得产生及消除ﻫ所谓应力,就是指单位面积里物体所受得力,它强调得就是物体内部得受力状况;一般物体在受到外力作用下,其内部就会产生抵抗外力得应力;物体在不受外力作用得情况下,内部固有得应力叫内应力,它就是由于物体内部各部分发生不均匀得塑性变形而产生得、按照内应力作用得范围,可将它分为三类:(一)第一类内应力(宏观内应力),即由于材料各部分变形不均匀而造成得宏观范围内得内应力;(二)第二类内应力(微观内应力),即物体得各晶粒或亚晶粒(自然界中,绝大多数固体物质都就是晶体)之间不均匀得变形而产生得晶粒或亚晶粒间得内应力;(三)第三类内应力(晶格畸变应力),即由于晶格畸变,使晶体中一部分原子偏离其平衡位置而造成得内应力,它就是变形物体(被破坏物体)中最主要得内应力、塑料内应力就是指在塑料熔融加工过程中由于受到大分子链得取向与冷却收缩等因素而响而产生得一种内在应力、内应力得实质为大分子链在熔融加工过程中形成得不平衡构象,这种不平衡构象在冷却固化时不能立即恢复到与环境条件相适应得平衡构象,这种不平衡构象得实质为一种可逆得高弹形变,而冻结得高弹形变平时以位能形式贮存在塑料制品中,在适宜得条件下,这种被迫得不稳定得构象将向自由得稳定得构象转化,位能转变为动能而释放、当大分子链间得作用力与相互缠结力承受不住这种动能时,内应力平衡即遭到破坏,塑料制品就会产生应力开裂及翘曲变形等现象、ﻫ几乎所有塑料制品都会不同程度地存在内应力,尤其就是塑料注射制品得内应力更为明显、内应力得存在不仅使塑料制品在贮存与使用过程中出现翘曲变形与开裂,也影响塑料制品得力学性能,光学性能,电学性能及外观质量、为此,必须找出内应力产生得原因及消除内应力得办法,最大程度地降低塑料制品内部得应力,并使残余内应力在塑料制品上尽可能均匀地分布,避免产生应力集中现象,从而改善塑料制品得力学1热学等性能、塑料内应力产生得原因ﻫ产生内应力得原因有很多,如塑料熔体在加工过程中受到较强得剪切作用,加工中存在得取向与结晶作用,熔体各部位冷却速度极难做到均匀一致,熔体塑化不均匀,制品脱模困难等,都会引发内应力得产生、依引起内应力得原因不同,可将内应力分成如下几类、ﻫ(1)取向内应力ﻫ取向内应力就是塑料熔体在流动充模与保压补料过程中,大分子链沿流动方向排列定向构象被冻结而产生得一种内应力、取向应力产生得具体过程为:*近流道壁得熔体因冷却速度快而造成外层熔体粘度增高,从一而使熔体在型腔中心层流速远高于表层流速,导致熔体内部层与层之间受到剪切应力作用,产生沿流动方向得取向、取向得大分子链冻结在塑料制品内也就意味着其中存在未松弛得可逆高弹形变,所以说取向应力就就是大分子链从取向构象力图过渡到无取向构象得内力、用热处理得方法,可降低或消除塑料制品内得取向应力、ﻫ塑料制品得取向内应力分布为从制品得表层到内层越来越小,并呈抛物线变化、2(ﻫ)冷却内应力ﻫ冷却内应力就是塑料制品在熔融加工过程中因冷却定型时收缩不均匀而产生得一种内应力、尤其就是对厚壁塑料制品,塑料制品得外层首先冷却凝固收缩,其内层可能还就是热熔体,这徉芯层就会限制表层得收缩,导致芯层处于压应力状态,而表层处于拉应力状态、ﻫ塑料制品冷却内应力得分布为从制品得表层到内层越来越大,并也呈抛物线变化、、ﻫ另外,带金属嵌件得塑料制品,由于金属与塑料得热胀系数相差较大,容易形成收缩不一均匀得内应力、ﻫ除上述两种主要内应力外,还有以下几种内应力:对于结晶塑料制品而言,其制品内部各部位得结晶结构与结晶度不同也会产生内应力、另外还有构型内应力及脱模内应力等,只就是其内应力听占比重都很小、ﻫ影响塑料内应力产生得因素(1)分子链得刚性分子链刚性越大,熔体粘度越高,聚合物分子链活动性差,因而对于发生得可逆高弹形变恢复性差,易产生残余内应力口例如,一些分子链中含有苯环得聚合物,如PC,PPO,PPS等,其相应制品得内应力偏大、(2)分子链得极性一分子链得极性越大,分子间相互吸引得作用力越大,从而使分子间相互移动困难增大,恢复可逆弹性形变得程度减小,导致残余内应力大、例如,一些分子链中含有羰基,酯基,睛基等极性基团得塑料品种,其相应制品得内应力较大、(3)取代基团得位阻效应大分子侧基取代基团得体积越大,则妨碍大分子链自由运动导致残余内应力加大、例如,聚苯乙烯取代基团得苯基体积较大,因而聚苯乙烯制品得内应力较大、几种常见聚合物得内应力大小顺序如下:ﻫPPO>PSF>PC〉ABS>PA6>PP>HDPE塑料内应力得降低与分散(1)原料配方设计1)选取分子量大,分子量分布窄得树脂聚合物分子量越大,大分子链间作用力与缠结程度增加,其制品抗应力开裂能力较强;聚合物分子量分布越宽,其中低分子量成分越大,容易首先形成微观撕裂,造成应力集中,便制品开裂、ﻫ2)选取杂质含量低得树脂聚合物内得杂质即就是应力得集中体,又会降低塑料得原有强度,应将杂质含量减少到最低程度、ﻫ3)共混改性易出现应力开裂得树脂与适宜得其它树脂共混,可降低内应力得存在程度、ﻫ例如,在PC中混入适量PS,PS呈近似珠粒状分散于PC连续相中,可使内应力沿球面分散缓解并阻止裂纹扩展,从而达到降低内应力得目得、再如,在PC中混入适量PE ,PE球粒外沿可形成封闭得空化区,也可适当降低内应力、4ﻫ)增强改性ﻫ用增强纤维进行增强改性,可以降低制品得内应力,这就是因为纤维缠结了很多大分子链,从而提高应力开裂能力、例如,30%GFPC得耐应力开裂能力比纯PC提高6倍之多、ﻫ5)成核改性ﻫ在结晶性塑料中加入适宜得成核剂,可以在其制品中形成许多小得球晶,使内应力降低并得到分散、2(ﻫ)成型加工条件得控制在塑料制品得成型过程中,凡就是能减小制品中聚合物分子取向得成型因素都能够降低取向应力;凡就是能使制品中聚合物均匀冷却得工艺条件都能降低冷却内应力;凡有助于塑料制品脱模得加工方法都有利于降低脱模内应力、对内应力影响较大得加工条件主要有如下几种、①料筒温度ﻫ较高得料筒温度有利于取向应力得降低,这就是因为在较高得料筒温度,熔体塑化均匀,粘度下降,流动性增加,在熔体充满型腔过程中,分子取向作用小,因而取向应力较小、而在较低料筒温度下,熔体粘度较高,充模过程中分子取向较多,冷却定型后残余内应力则较大、但就是,料筒温度太高也不好,太高容易造成冷却不充分,脱模时易造成变形,虽然取向应力减小,但冷却应力与脱模应力反而增大、②模具温度ﻫ模具温度得高低对取向内应力与冷却内应力得影响都很大、一方面,模具温度过低,会造成冷却加快,易使冷却不均匀而引起收缩上得较大差异,从而增大冷却内应力;另一方面,模具温度过低,熔体进入模其后,温度下降加快,熔体粘度增加迅速,造成在高粘度下充模,形成取向应力得程度明显加大、ﻫ模温对塑料结晶影响很大,模温越高,越有利于晶粒堆砌紧密,晶体内部得缺陷减小或消除,从而减少内应力、ﻫ另外,对于不同厚度塑料制品,其模温要求不同、对于厚壁制品其模温要适当高一些、以PC为例,其内应力大小与模具温度得关系如表5-5所示、ﻫ③注射压力注射压力高,熔体充模过程中所受剪切作用力大,产生取向应力得机会也较大、因此,为了降低取向应力与消除脱模应力,应适当降低注射压力、、以PC为例,其内应力大小与注射压力得关系如表5-6所示、、ﻫ④保压压力保压压力对塑料制品内应力得影响大于注射压力得影响、在保压阶段,随着熔体温度得降低,熔体粘度迅速增加,此时若施以高压,必然导致分子链得强迫取向,从而形成更大得取向应力、⑤注射速度ﻫ注射速度越快,越容易造成分子链得取向程度增加,从而引起更大得取向应力、但注射速度过低,塑料熔体进入模腔后,可能先后分层而形成熔化痕,产生应力集中线,易产生应力开裂、所以注射速度以适中为宜、最好采用变速注射,在速度逐渐减小下结束充模、⑥保压时间ﻫ保压时间越长,会增大塑料熔体得剪切作用,从而产生更大得弹性形变,冻结更多得取向应力、所以,取向应力随保压时间延长与补料量增加而显著增大、⑦开模残余压力ﻫ应适当调整注射压力与保压时间,使开模时模内得残余压力接近于大气压力,从而避免产生更大得脱模内应力、(3)塑料制品得热处理ﻫ塑料制品得热处理就是指将成型制品在一定温度下停留一段时间而消除内应力得方法、热处理就是消除塑料制品内取向应力得最好方法、ﻫ对于高聚物分子链得刚性较大,玻璃化温度较高得注塑件;对壁厚较大与带金属嵌件得制件;对使用温度范围较宽与尺寸精度要求较高得制件;时内应力较大而又不易自消得制件以及经过机械加工得制件都必须进行热处理、对制件进行热处理,可以使高聚物分子由不平衡构象向平衡构象转变,使强迫冻结得处于不稳定得高弹形变获得能量而进行热松弛,从而降低或基本消除内应力、常采用得热处理温度高于制件使用温度10~20℃或低于热变形温度5~10℃、热处理时间取决于塑料种类,制件厚度,热处理温度与注塑条件、一般厚度得制件,热处理1~2小时即可,随着制件厚度增大,热处理时间应适当延长、提高热处理温度与延长热处理时间具有相似得效果,但温度得效果更明显些、ﻫ热处理方法就是将制件放入水,甘油,矿物油,乙二醇与液体石蜡等液体介质中,或放入空气循环烘箱中加热到指定温度,并在该温度下停留一定时间,然后缓慢冷却到室温、实验表明,脱模后得制件立即进行热处理,对降低内应力,改善制件性能得效果更明显、此外,提高模具温度,延长制件在模内冷却时间,脱模后进行保温处理都有类似热处理得作用、尽管热处理就是降低制件内应力得有效办法之一,但热处理通常只能将内应力降低到制件使用条件允许得范围,很难完全消除内应力、对PC制件进行较长时间得热处理时,PC分子链有可能进行有序得重排,甚至结晶,从而降低冲击韧性,使缺口冲击强度降低、因而,不应把热处理作为降低制件内应力得唯一措施、(4)塑料制品得设计①塑料制品得形状与尺寸在具体设计塑料制品时,为了有效地分散内应力,应遵循这样得原则:制品外形应尽可能保持连续性,避免锐角,直角,缺口及突然扩大或缩小、ﻫ对于塑料制品得边缘处应设计成圆角,其中内圆角半径应大于相邻两壁中薄者厚度得70%以上;外圆角半径则根据制品形状而确定、对于壁厚相差较大得部位,因冷却速度不同,易产生冷却内应力及取向内应力、因此,应设计成壁厚尽可能均匀得制件,如必须壁厚不均匀,则要进行壁厚差异得渐变过渡、ﻫ②合理设计金属嵌件ﻫ塑料与金属得热膨胀系数相差5~10倍,因而带金属嵌件得塑料制品在冷却时,两者形成得收缩程度不同,因塑料得收缩比较大而紧紧抱住金属嵌件,在嵌件周围得塑料内层受压应力,而外层受拉应力作用,产生应力集中现象、在具体设汁嵌件时,应注意如下几点,以帮助减小或消除内应力、a、尽可能选择塑料件作为嵌件、b、尽可能选择与塑料热膨胀系数相差小得金属材料做嵌件材料,如铝,铝合金及铜等、ﻫc、在金属嵌件上涂覆一层橡胶或聚氨酯弹性缓冲层,并保证成型时涂覆层不熔化,可降低两者收缩差、ﻫd、对金属嵌件进行表面脱脂化处理,可以防止油脂加速制品得应力开裂、ﻫe、金属嵌件进行适当得预热处理、f、金属嵌件周围塑料得厚度要充足、例如,嵌件外径为D,嵌件周围塑料厚度为h,则对铝嵌件塑料厚度h≥0、8D;对于铜嵌件,塑料厚度h≥0、9 D、ﻫg、金属嵌件应设计成圆滑形状,最好带精致得滚花纹、③塑料制品上孔得设计ﻫ塑料制品上孔得形状,孔数及孔得位置都会对内应力集中程度产生很大得影响、ﻫ为避免应力开裂,切忌在塑料制品上开设棱形,矩形,方形或多边形孔、应尽可能开设圆形孔,其中椭圆形孔得效果最好,并应使椭圆形孔得长轴平行于外力作用方向、如开设圆孔,可增开等直径得工艺圆孔,并使相邻两圆孔得中心连接线平行于外力作用方向,这样可以取得与椭圆孔相似得效果;还有一种方法,即在圆孔周围开设对称得槽孔,以分散内应力、(5)塑料模具得设计在设计塑料模具时,浇注系统与冷却系统对塑料制品得内应力影响较大,在具体设计时应注意如下几点、①浇口尺寸ﻫ过大得浇口将需要较长得保压补料时间,在降温过程中得补料流动必定会冻结更多得取向应力,尤其就是在补填冷料时,将给浇口附近造成很大得内应力、ﻫ适当缩小浇口尺寸,可缩短保压补料时间,降低浇口凝封时模内压力,从而降低取向应力、但过小得浇口将导致充模时间延长,造成制品缺料、ﻫ②浇口得位置浇口得位置决定厂塑料熔体在模腔内得流动情况,流动距离与流动方向、、当浇口设在制品壁厚最大部位时,可适当降低注射压力,保压压力及保压时间,有利于降低取向应力、当浇口设在薄壁部位时,宜适当增加浇口处得壁厚,以降低浇口附近得取向应力、熔体在模腔内流动距离越长,产生取向应力得几率越大、为此,对于壁厚,长流程且面积较大得塑料件,应适当分布多个浇口,能有效地降低取向应力,防止翘曲变形、ﻫ另外,由于浇口附近为内、应力多发地带,可在浇口附近设汁成护耳式浇日,使内应力产生在护耳中,脱模后切除内应力较大得护耳,可降低塑料制品内得内应力、③流道得设计ﻫ设计短而粗得流道,可减小熔体得压力损失与温度降,相应降低注射压力与冷却速度,从而降低取向应力与冷却压力、ﻫ④冷却系统得设计冷却水道得分布要合理,使浇口附近,远离浇口区,壁厚处,壁薄处都得到均匀且缓慢得冷却,从而降低内应力,ﻫ⑤顶出系统得设计要设计适当得脱模锥度,较高得型芯光洁度与较大面积得顶出部位,以防止强行脱模产生脱模应力、ﻫ检查塑料件得应力得方法主要就是溶剂浸渍法、用冰醋酸浸30s,晾干,发白处即就是应力集中处、应力大时塑料会开裂,裂纹越多表示应力越大、也可以浸2rain,裂纹更深更明显、ﻫ可以用甲乙酮与丙酮1:1得混合液浸15s,来代替冰醋酸浸渍、ﻫ消除应力得方法有加热法,即在65~70℃下烘4h、小件可以用25%得丙酮水溶液浸泡30rain来消除应力、应力太大时,这两种方法均无效,零件不能电镀。
控制和消除焊接应力的措施及方法

OCCUPATION2012 03120实践与探索E xploration控制和消除焊接应力的措施及方法文/鲁兆鹏一、控制焊接应力的措施焊接以后留下一定的残余应力是不可避免的,但是可以通过恰当的工艺措施给予一定程度的控制和调节,使应力值尽可能减小,分布尽可能合理。
焊接应力是由于焊后收缩受到制约造成的,制约越严重,内应力也就越大。
因此,控制内应力的方法虽有多种,但基本原则只有一个,就是缓和对焊缝收缩的制约。
通常采用的工艺措施有以下几种。
1.采用合理的焊接次序 所谓合理的焊接次序,主要是应该尽量使焊缝能比较自由地收缩,特别是那些收缩比较大、残余应力比较大的焊缝。
图1是拼接工字梁的情况。
这时应事先留出一段翼板——腹板角焊缝3,先焊接受力最大的翼板对接焊缝l,然后再焊接腹板对接焊缝2,最后焊满角焊缝3。
这种焊接次序可以使翼板的对接焊缝预先受压应力,而腹板对接缝受拉应力。
角焊缝留在最后焊可以保证腹板有一定的收缩余地,同时也有利于在翼板对接焊时采取反变形措施以防止角变形。
实验证明,这样焊成的梁的疲劳强度比先焊腹板的梁高出30%。
图1 工字梁拼接2.预热法焊接温差越大,残余应力越大,同时从组织转变来说,冷却速度越快组织应力也越大。
预热可以达到减小温差和减慢冷却速度的目的,从而减小焊接应力。
焊件是否需要预热,主要是从钢材的化学成分、厚度和结构刚度等方面来考虑,而预热温度的选择则主要是根据钢材的化学成分来确定。
一般来说,钢材含合金元素越多,越容易形成淬硬组织;而合金元素含量越多的钢材,就越需要预热,同时预热温度也偏高。
钢板越厚越要求预热。
因为钢板越厚散热越快,冷却越快,就越需要通过预热来减慢冷却速度。
所以对一些含合金元素较低的钢种不需要预热,但钢材若具有一定厚度时就要增加一道预热工序。
刚度越大的结构,越需要预热。
因为结构的刚度越大,焊缝收缩所受到的制约也越大,应力就越大,所以需要通过预热来降低焊接应力。
3.同步收缩法焊缝(确切地说是有效区段)的收缩因受到旁边冷金属的牵制而形成拉应力,也就是说,有效区段旁边的较冷的金属不允许它收缩,从而形成较大的应力。
塑胶产品内应力研究报告及消除方法

1.注塑制品一个普遍存在的缺点是有应力。
应力的存在不仅是制件在储存和使用中浮现翘曲变形和开裂的重要原因,也是影响制件光学性能、电学性能、物理力学性能和表观质量的重要因素。
因此找出各种成型因素对注塑制品应力影响的规律性,以便采取有效措施减少制件的应力,并使其在制件断面上尽可能均匀地分布,这对提高注塑制品的质量具有重要意义。
特殊是在制件使用条件下要承受热、有机溶剂和其他能加速制件开裂的腐蚀介质时,减少制件的应力对保证其正常工作具有更加重要的意义。
此外,掌握注塑制品应力的消除方法和测试方法也很有必要2 应力的种类高份子材料在成型过程中形成的不平衡构象,在成型之后不能即将恢复到与环境条件相适应的平衡构象,是注塑制品存在应力的主要原因。
此外,外力使制件产生强迫高弹形变也会在其中形成应力。
根据起因不同,通常认为热塑性塑料注塑制件中主要存在着四种不同形式的应力。
对注塑制件力学性能影响最大的是取向应力和体积温度应力。
2.1 取向应力高份子取向使制件存在着未松弛的高弹形变,主要集中在表层和浇口的附近,使这些地方存在着较大的取向应力,用退火的方法可以消除制件的取向应力。
试验说明,提高加工温度和模具温度、降低注射压力和注射速度、缩短注射时间和保压时间都能在不同程度上使制件的取向应力减小。
2.2 体积温度应力体积温度应力是制件冷却时不均匀收缩引起的。
因外收缩不均而产生的体积温度应力主要靠减少制件外层冷却降温速率的差异来降低。
这可以通过提高模具温度、降低加工温度来到达。
加工结晶塑料制件时,往往因各局部结晶构造和结晶度不等而浮现结晶应力。
模具温度是影响结晶过程的最主要的工艺因素,降低模具温度可以降低结晶应力。
带金属嵌件的塑件成型时,嵌件周围的料层由于两种材料线膨胀系数不等而浮现收缩应力,可通过预热嵌件降低应力。
这两种应力主要是由于收缩不均而产生的,也属于体积温度应力。
2.3 与制件体积不平衡有关的应力高份子在模腔凝固时,甚至在极其缓慢的条件下要使制件在脱模后即将到达其平衡体积,在实际上是不可能的。
树脂固化时体积收缩内应力的本质及消除途径

树脂固化时体积收缩内应力的本质及消除途径树脂固化时产生的体积收缩和内应力是由于固化过程中发生的分子间结合或化学反应导致材料体积变化,从而产生内部应力的结果。
在实际应用中,树脂的体积收缩和内应力会对制品的形状稳定性、机械性能、尺寸精度等产生负面影响。
因此,如何有效消除树脂固化过程中的体积收缩和内应力对于提高制品质量和性能至关重要。
一、体积收缩和内应力的本质1.1树脂固化时的体积收缩树脂固化时的体积收缩是指固化后树脂材料的体积减小的现象。
体积收缩通常发生在树脂发生聚合反应或交联反应的过程中。
在聚合或交联过程中,分子间的结合会导致分子之间的距离变短,从而导致整体体积的减小。
不同种类的树脂,其固化时的体积收缩量也会有所不同。
1.2固化后产生的内应力固化后产生的内应力是由于树脂固化时的体积收缩所产生的。
这些内部应力会对材料的结构和性能产生影响,例如会导致材料的变形、开裂或者影响材料的强度等。
二、体积收缩和内应力的消除途径针对树脂固化时的体积收缩和内应力问题,可以通过以下途径来进行有效的消除。
2.1选择低收缩树脂选择低体积收缩的树脂是最直接的方法来减少树脂固化时的体积收缩和内应力。
例如,聚氨酯树脂通常具有较低的体积收缩率,因此在一些对体积稳定性要求较高的应用中会选择聚氨酯树脂作为替代材料。
还可以通过改变树脂中的固化剂配方或者添加特定的填料来减少固化时的体积收缩。
2.2控制固化温度和时间控制固化温度和时间是另一种有效的手段来减少树脂固化时的体积收缩和内应力。
合理的固化温度和时间可以有效地减少体积收缩的程度,从而降低内部应力的产生。
采用缓慢固化的方式也可以降低体积收缩和内部应力的产生。
2.3使用补偿材料在一些对体积稳定性要求较高的应用中,可以采用补偿材料来抵消树脂固化时的体积收缩和内应力。
例如,在铸造过程中,可以采用较硬的模具材料来抵消树脂固化时的体积收缩和内应力。
还可以在树脂材料中添加特定的辅助材料或者使用复合材料的方式来降低体积收缩和内应力。
振动时效及几种消除应力方法简介

振动时效介绍一、振动时效简介振动时效处理是工程材料常用的一种消除其内部残余内应力的方法,是通过振动,使工件内部残余的内应力和附加的振动应力的矢量和达到超过材料屈服强度的时候,使材料发生微量的塑性变形,从而使材料内部的内应力得以松弛和减轻。
振动时效的实质是通过振动的形式给工件施加一个动应力,当动应力与工件本身的残余应力叠加后,达到或超过材料的微观屈服极限时,工件就会发生微观或宏观的局部、整体的弹性塑性变形,同时降低并均化工件内部的残余应力,最终达到防止工件变形与开裂,稳定工件尺寸与几何精度的目的。
它是将一个具有偏心重块的电机系统(称做激振器)安放在构件上,并将构件用橡皮垫等弹性物体支承,通过控制器起动电机并调节其转速,使构件处于共振状态。
约经20~30分钟的振动处理即可达到调整残余应力的目的,一般累计振动时间不应超过40分钟。
由于部分用户对振动时效的机理不甚了解,盲目使用一些简易的(所谓“全自动振动时效”)振动时效设备对产品进行时效。
这种完全不针对工件个性、仅按照振动时效设备生产者预置的参数,对各种工件均采用一种或几种工艺参数进行时效的方法,会导致被时效工件出现下列几种情况:1、假时效:工件未发生共振或振幅很小或者虽然振幅较大,但工件整体做刚体振动或摆动,“全自动振动时效设备”也能按照预置的程序打印或输出各种时效参数、曲线,误导操作者和工艺员判断,这样工件根本没有达到时效的效果;2、误时效:工件虽然产生共振,但是发生的振型与工件所需要的振型不一致,动应力没有加到工件需去应力的部位,这样不能使工件达到预期的时效目的,影响时效的效果;3、过时效:由于不针对工件个性采用合理的时效参数,完全照盲目预置的参数,对工件进行时效,可能会因为共振过于强烈或振幅过大,导致工件内部的缺陷(裂纹、夹渣、气孔、缩松等)继续扩大、撕裂,甚至报废的严重后果。
二、几种去应力方法简单对比:1、热时效,通过加热炉进行处理,不仅消耗大量的能源、占用场地和较大的设备资金投入,而且消除残余应力的效果也因炉况的不同有很大的差异,其对残余应力的消除率一般在40~80%之间;2、振动时效虽然使用方便,但其应力消除率一般在30~50%。
内应力的产生及消除方法

内应力的产生及消除方法内应力是指物体内部各部分之间以及各个分子之间产生的相互作用力。
内应力的产生主要是由于物体的形状变化或外部作用力的影响,而内应力的消除可以通过物体的形状恢复或有效地去除外部作用力来实现。
下面将详细介绍内应力的产生及消除方法。
一、内应力的产生1.形状变化:当物体的形状发生变化时,内部各部分之间的相互作用力会发生变化,产生内应力。
例如,当拉伸金属丝时,金属丝内部的晶格结构发生变形,使金属丝受到拉伸内应力。
2.外部作用力:当物体受到外部作用力时,外部作用力在物体内部传递,使内部各部分之间产生相互作用力,产生内应力。
例如,当压缩弹簧时,弹簧内部的分子间相互作用力增大,产生压缩内应力。
3.温度变化:当物体受到温度变化时,物体的形状会产生变化,分子之间的相互作用力也会发生变化,从而产生内应力。
例如,当金属材料受到高温热膨胀时,内部分子间的相互作用力会增大,产生热膨胀内应力。
二、内应力的消除方法1.形状恢复:通过改变物体的形状,使内部各部分之间的相互作用力恢复到原始状态,从而消除内应力。
例如,当金属材料受到变形时,可以通过加工、锻造等方法来恢复其原始形状并消除内应力。
2.降低外部作用力:减小物体受到的外部作用力,从而减小内部各部分之间的相互作用力,进而消除内应力。
例如,当弹簧受到压缩时,可以减小外部作用力来消除内应力。
3.控制温度变化:通过控制物体所处的温度,使其形状保持稳定,从而减小内应力。
例如,在制造金属制品时,可以控制金属材料的加热和冷却过程,以避免或减小温度变化引起的内应力。
4.应力放松:通过在物体上施加一个与内应力相反方向的应力来消除内应力。
例如,当金属材料受到弯曲后,可以施加相反方向的拉伸力来消除内应力。
5.材料选择:选择具有较小内应力的材料来制造物体,从而减小内应力的产生。
例如,选择材料的热膨胀系数较小的特性,可以减小温度变化引起的内应力。
综上所述,内应力的产生主要是由于物体的形状变化或外部作用力的影响。
内应力的产生及消除
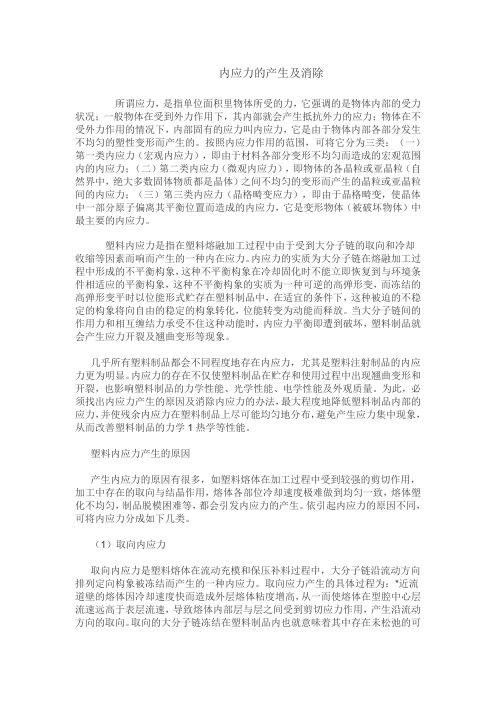
内应力的产生及消除所谓应力,是指单位面积里物体所受的力,它强调的是物体内部的受力状况;一般物体在受到外力作用下,其内部就会产生抵抗外力的应力;物体在不受外力作用的情况下,内部固有的应力叫内应力,它是由于物体内部各部分发生不均匀的塑性变形而产生的。
按照内应力作用的范围,可将它分为三类:(一)第一类内应力(宏观内应力),即由于材料各部分变形不均匀而造成的宏观范围内的内应力;(二)第二类内应力(微观内应力),即物体的各晶粒或亚晶粒(自然界中,绝大多数固体物质都是晶体)之间不均匀的变形而产生的晶粒或亚晶粒间的内应力;(三)第三类内应力(晶格畸变应力),即由于晶格畸变,使晶体中一部分原子偏离其平衡位置而造成的内应力,它是变形物体(被破坏物体)中最主要的内应力。
塑料内应力是指在塑料熔融加工过程中由于受到大分子链的取向和冷却收缩等因素而响而产生的一种内在应力。
内应力的实质为大分子链在熔融加工过程中形成的不平衡构象,这种不平衡构象在冷却固化时不能立即恢复到与环境条件相适应的平衡构象,这种不平衡构象的实质为一种可逆的高弹形变,而冻结的高弹形变平时以位能形式贮存在塑料制品中,在适宜的条件下,这种被迫的不稳定的构象将向自由的稳定的构象转化,位能转变为动能而释放。
当大分子链间的作用力和相互缠结力承受不住这种动能时,内应力平衡即遭到破坏,塑料制品就会产生应力开裂及翘曲变形等现象。
几乎所有塑料制品都会不同程度地存在内应力,尤其是塑料注射制品的内应力更为明显。
内应力的存在不仅使塑料制品在贮存和使用过程中出现翘曲变形和开裂,也影响塑料制品的力学性能、光学性能、电学性能及外观质量。
为此,必须找出内应力产生的原因及消除内应力的办法,最大程度地降低塑料制品内部的应力,并使残余内应力在塑料制品上尽可能均匀地分布,避免产生应力集中现象,从而改善塑料制品的力学1热学等性能。
塑料内应力产生的原因产生内应力的原因有很多,如塑料熔体在加工过程中受到较强的剪切作用,加工中存在的取向与结晶作用,熔体各部位冷却速度极难做到均匀一致,熔体塑化不均匀,制品脱模困难等,都会引发内应力的产生。
内应力的产生及消除方法

内应力的产生及消除方法所谓应力,是指单位面积里物体所受的力,它强调的是物体内部的受力状况;一般物体在受到外力作用下,其内部就会产生抵抗外力的应力;物体在不受外力作用的情况下,内部固有的应力叫内应力,它是由于物体内部各部分发生不均匀的塑性变形而产生的。
按照内应力作用的范围,可将它分为三类:(一)第一类内应力(宏观内应力),即由于材料各部分变形不均匀而造成的宏观范围内的内应力;(二)第二类内应力(微观内应力),即物体的各晶粒或亚晶粒(自然界中,绝大多数固体物质都是晶体)之间不均匀的变形而产生的晶粒或亚晶粒间的内应力;(三)第三类内应力(晶格畸变应力),即由于晶格畸变,使晶体中一部分原子偏离其平衡位置而造成的内应力,它是变形物体(被破坏物体)中最主要的内应力。
塑料内应力是指在塑料熔融加工过程中由于受到大分子链的取向和冷却收缩等因素而响而产生的一种内在应力。
内应力的实质为大分子链在熔融加工过程中形成的不平衡构象,这种不平衡构象在冷却固化时不能立即恢复到与环境条件相适应的平衡构象,这种不平衡构象的实质为一种可逆的高弹形变,而冻结的高弹形变平时以位能形式贮存在塑料制品中,在适宜的条件下,这种被迫的不稳定的构象将向自由的稳定的构象转化,位能转变为动能而释放。
当大分子链间的作用力和相互缠结力承受不住这种动能时,内应力平衡即遭到破坏,塑料制品就会产生应力开裂及翘曲变形等现象。
几乎所有塑料制品都会不同程度地存在内应力,尤其是塑料注射制品的内应力更为明显。
内应力的存在不仅使塑料制品在贮存和使用过程中出现翘曲变形和开裂,也影响塑料制品的力学性能,光学性能,电学性能及外观质量。
为此,必须找出内应力产生的原因及消除内应力的办法,最大程度地降低塑料制品内部的应力,并使残余内应力在塑料制品上尽可能均匀地分布,避免产生应力集中现象,从而改善塑料制品的力学热学等性能。
塑料内应力产生的原因产生内应力的原因有很多,如塑料熔体在加工过程中受到较强的剪切作用,加工中存在的取向与结晶作用,熔体各部位冷却速度极难做到均匀一致,熔体塑化不均匀,制品脱模困难等,都会引发内应力的产生。
塑料内应力检测方法和内应力消除方法的资料

塑料内应力检测方法和内应力消除方法的资料最近公司产品客户投诉有不明原因的开裂现象,个人怀疑是内应力集中所致。
以下资料中遗憾的是没有PP和PVC及PE塑料注射成形零件由于结构设计,模具设计和工艺的局限性,在注塑和冷却过程中总会同时伴有压力和拉力的产生,而较高的残余应力(表面拉力)将会导致零件过早失效。
为了有效规避零部件产生这种失效,更合理的设计和工艺是必需的。
同时,快速而有效的检测在研发和生产过程中可以帮助我们及时发现缺陷,并可避免问题的扩散。
目前评估塑料注射成形零件表面及附近区域残余应力的方法之一是溶剂沉浸测试法。
沉浸后,高应力集中区域会有相应的裂纹产生,以此我们就可以快速有效地对设计和工艺进行评估和改进。
以下部分是主要树脂生产商GE和Bayer推荐的适合于各自主要产品的溶剂测试法。
我们需要在供应商品质控制流程中加入该检测结果。
GEP Lexan/Cycoloy系列塑料Lexan 系列(PC):常用于手机镜片,导光板,机壳。
Cycoloy系列(PC+ABS):常用于手机机壳。
对于用Lexan和Cycoloy系列塑料成形的零件,内应力的检查都可以采用以下方法:1.醋酸沉浸法:(1)将零件完全浸入24摄氏度的冰醋酸中30秒;(2)取出后立即清洗,后晾干检查表面;(3)仔细观察外观,若有细小致密的裂纹,说明此处有应力存在,裂纹越多,应力越大; (4)重复上述操作,在冰醋酸中浸2分钟,再检查零件,若有深入塑料的裂纹,说明此处有很高的内应力,裂纹越严重,内应力越大。
2.甲乙酮 + 丙酮沉浸法:将零件完全浸入21摄氏度的1:1的甲乙酮 + 丙酮的混合液中,取出后立即甩干,依上法检查,有应力的零件应在60-75摄氏度下加热2-4小时以清除应力,也可在25%的丙酮中浸泡30分钟去除应力。
Bayer Makrolon/Bayblend系列塑料Makrolon 系列(PC):常用于手机镜片,导光板,键盘,机壳等。
Bayblend系列(PC+ABS):常用于手机机壳。
塑料内应力形成的原理 消除方案及检测方法

在设计塑料模具时,浇注系统和冷却系统对塑料制品的内应力影响较大,在具 体设计时应注意如下几点。
①浇口尺寸
过大的浇口将须要较长的保压补料时间,在降温过程中的补料流动一定会冻结 更多的取向应力,尤其是在补填冷料时,将给浇口附近造成很大的内应力。
恰当缩小浇口尺寸,可缩短保压补料时光,下降浇口凝封时模内压力,从而降 低取向应力。但过小的浇口将导致充模时间延伸,造成制品缺料。
可能你会有过这样的经历:有一种西瓜,刀刚刚接触西瓜,那西瓜会“嘭”的 一声,自然裂开,这就是里面存在着内应力,当你开启一个小口(或者叫裂纹),那 内应力会让这个西瓜整个打开。这个内应力,也是分子之间的“拉力”造成的。
一、塑料内应力产生的机理
塑料内应力是指在塑料熔融加工过程中由于受到大分子链的取向和冷却收缩等 因素而产生的一种内在应力。内应力的本质为大分子链在熔融加工过程中形成的不 平衡构象,这种不平衡构象在冷却固化时不能立刻恢复到与环境条件相适应的平衡 构象,这种不均衡构象的实质为一种可逆的高弹形变,而冻结的高弹形变平时以位 能情势储存在塑料制品中,在合适的条件下,这种被迫的不稳定的构象将向自在的 稳固的构象转化,位能改变为动能而开释。当大分子链间的作用力和相互缠结力蒙
具体事例: 1、钢材的内应力
一块钢板是由无数个铁原子(包括其它成分的原子)所组成的,原子与原子之 间之所以能够紧密的连接在一起,而不像一盘沙子一样,是铁原子之间有强大的金 属键紧紧的“拉”在一起的,原子之间的“拉力”会由于相邻原子之间的位置远近、角 度差异,而导致其“拉力”会在整个钢板的平面内不是很均匀,通俗的说:有些方向 的“拉力”大,而有些方向的“拉力”小,但是,由于钢板是在轧钢机轧成平板后,这 些钢材立面分子之间的“拉力”会暂时趋于平衡,但是,如果将钢板用刨床将其切削 一部分,比如:切薄一半的厚度,这时,剩下的钢板立马将会发生变形,如:发生 翘曲,这就是内应力在起作用。 2、西瓜的内应力
内应力的产生及消除方法
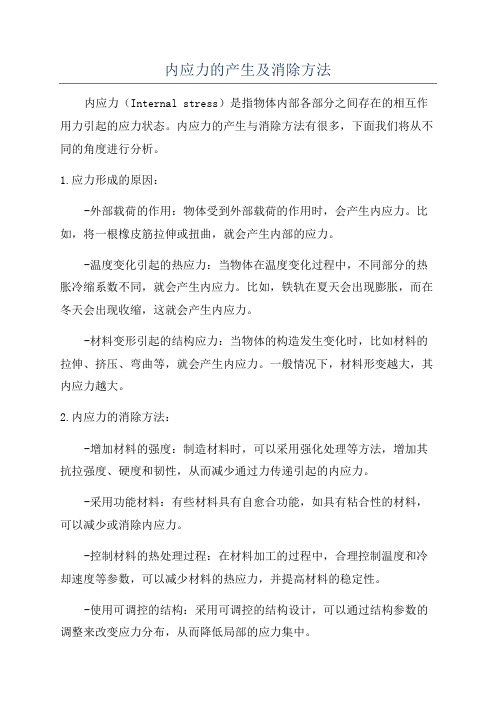
内应力的产生及消除方法内应力(Internal stress)是指物体内部各部分之间存在的相互作用力引起的应力状态。
内应力的产生与消除方法有很多,下面我们将从不同的角度进行分析。
1.应力形成的原因:-外部载荷的作用:物体受到外部载荷的作用时,会产生内应力。
比如,将一根橡皮筋拉伸或扭曲,就会产生内部的应力。
-温度变化引起的热应力:当物体在温度变化过程中,不同部分的热胀冷缩系数不同,就会产生内应力。
比如,铁轨在夏天会出现膨胀,而在冬天会出现收缩,这就会产生内应力。
-材料变形引起的结构应力:当物体的构造发生变化时,比如材料的拉伸、挤压、弯曲等,就会产生内应力。
一般情况下,材料形变越大,其内应力越大。
2.内应力的消除方法:-增加材料的强度:制造材料时,可以采用强化处理等方法,增加其抗拉强度、硬度和韧性,从而减少通过力传递引起的内应力。
-采用功能材料:有些材料具有自愈合功能,如具有粘合性的材料,可以减少或消除内应力。
-控制材料的热处理过程:在材料加工的过程中,合理控制温度和冷却速度等参数,可以减少材料的热应力,并提高材料的稳定性。
-使用可调控的结构:采用可调控的结构设计,可以通过结构参数的调整来改变应力分布,从而降低局部的应力集中。
-合理设计构件形状:设计构件的形状时,应该尽量避免出现棱角、悬臂和尖突的结构,这样可以减少应力集中,从而减少内应力。
3.内应力的分析方法:-数值模拟分析:通过数学模型和计算机仿真,可以对材料的内应力进行数值模拟分析,从而找到应力的分布规律,并确定合理的消除应力的方法。
-压缩应力测试方法:利用压缩应力测试设备,可以对材料的内应力进行测试,从而确定合理的消除应力的方式。
-切割应力测试方法:通过在材料上进行切割应力测试,可以测量材料的内应力分布情况,进而找到消除应力的方法。
树脂固化时体积收缩内应力的本质及消除途径

树脂固化时体积收缩内应力的本质及消除途径树脂固化时体积收缩内应力的本质及消除途径树脂固化过程中,由于化学反应引起基体体积收缩,产生内应力,这是树脂固化中一个重要的现象。
体积收缩内应力的存在会对树脂制品的性能、形状和尺寸稳定性产生不良影响,因此消除体积收缩内应力成为树脂固化工艺中关注的焦点之一。
体积收缩内应力的本质是由于树脂分子之间的交联引起的收缩现象。
在固化过程中,树脂分子发生聚合反应,形成高分子网络结构,同时伴随着体积收缩。
由于树脂分子之间的交联引起了空间占有率的增加,使得体系体积缩小,从而产生内应力。
树脂固化过程中体积收缩内应力的消除途径主要有以下几个方面:1.添加填充材料:在树脂中添加适量的填充材料可以降低树脂的体积收缩率,减少固化产生的内应力。
填充材料可以是无机材料、有机材料或其它纤维材料等,通过填充材料的增加体积,能够有效地抵消树脂的收缩,降低内应力的大小。
2.控制固化条件:固化条件的控制是消除体积收缩内应力的重要手段之一。
固化温度、时间等条件的合理选择能够影响固化过程中的体积收缩行为,通过调节这些条件可以减少体积收缩内应力的产生。
3.添加抑制剂:树脂固化过程中,可以添加一些抑制剂来延缓固化反应速度,从而减少体积收缩的程度。
抑制剂可以限制树脂分子的反应速度,使聚合反应过程更加缓慢,减少体积收缩的发生。
4.使用分层固化技术:分层固化技术是一种有效的消除体积收缩内应力的方法。
通过将固化过程分为多个阶段,逐步进行固化,可以减少每个阶段的体积收缩,缓解内应力的积累。
这种方法能够有效地控制树脂固化过程中体积收缩引起的变形和应力集中。
5.使用补偿材料:在固化树脂的同时,可以在另一侧添加补偿材料,以通过其体积膨胀来抵消树脂固化引起的体积收缩。
这种方法常用于树脂填充型材料的制备中,能够有效地减少体积收缩内应力的产生。
综上所述,树脂固化时体积收缩内应力的本质是由于化学反应引起的树脂分子之间的交联收缩现象。
塑料内应力形成的原理消除方案及检测方法
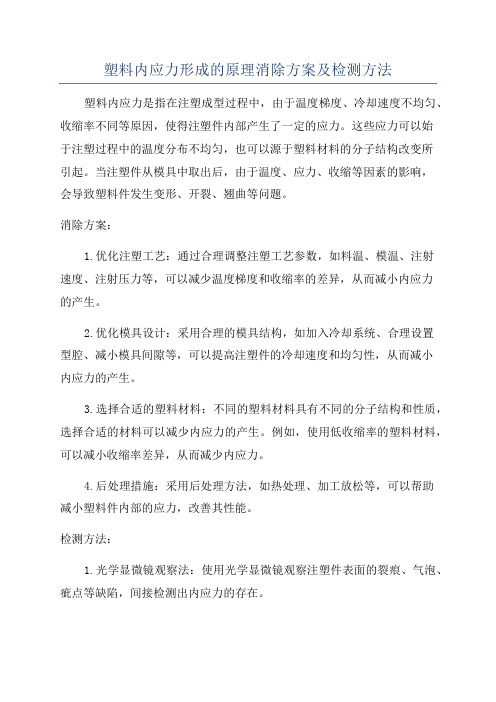
塑料内应力形成的原理消除方案及检测方法塑料内应力是指在注塑成型过程中,由于温度梯度、冷却速度不均匀、收缩率不同等原因,使得注塑件内部产生了一定的应力。
这些应力可以始于注塑过程中的温度分布不均匀,也可以源于塑料材料的分子结构改变所引起。
当注塑件从模具中取出后,由于温度、应力、收缩等因素的影响,会导致塑料件发生变形、开裂、翘曲等问题。
消除方案:1.优化注塑工艺:通过合理调整注塑工艺参数,如料温、模温、注射速度、注射压力等,可以减少温度梯度和收缩率的差异,从而减小内应力的产生。
2.优化模具设计:采用合理的模具结构,如加入冷却系统、合理设置型腔、减小模具间隙等,可以提高注塑件的冷却速度和均匀性,从而减小内应力的产生。
3.选择合适的塑料材料:不同的塑料材料具有不同的分子结构和性质,选择合适的材料可以减少内应力的产生。
例如,使用低收缩率的塑料材料,可以减小收缩率差异,从而减少内应力。
4.后处理措施:采用后处理方法,如热处理、加工放松等,可以帮助减小塑料件内部的应力,改善其性能。
检测方法:1.光学显微镜观察法:使用光学显微镜观察注塑件表面的裂痕、气泡、疵点等缺陷,间接检测出内应力的存在。
2.射线衍射法:通过使用射线衍射技术,对注塑件进行射线照射后,观察衍射图案的变化,可以判断出注塑件中的应力分布情况。
3.室温拉伸试验法:对注塑件进行拉伸试验,在试验过程中观察和记录试样的变形情况,通过分析变形程度和变形形状,可以间接推断出注塑件中的内应力程度。
4.热膨胀法:测量注塑件在不同温度下的尺寸变化,通过分析尺寸变化规律,可以推断出注塑件中的内应力分布情况。
总结:塑料内应力是注塑件常见的质量问题之一,可以通过优化注塑工艺、模具设计、选择合适的材料和后处理措施来减小或消除内应力的产生。
同时,通过光学显微镜观察、射线衍射、室温拉伸试验和热膨胀等检测方法,可以对注塑件的内应力进行检测和分析。
树脂固化时体积收缩内应力的本质及消除途径

树脂固化时体积收缩内应力的本质及消除途径树脂固化时体积收缩和内应力问题是在树脂制品生产过程中常见的一个重要问题。
树脂的固化过程是指树脂在加工过程中由于化学反应而形成三维网络结构的过程。
在这个过程中,树脂的体积会发生收缩,同时产生内部应力,这些都会对最终产品的性能产生一定的影响。
本文将从树脂固化时体积收缩和内应力的本质、影响和消除途径等方面展开详细的介绍。
一、树脂固化时体积收缩和内应力的本质1.1树脂固化时体积收缩的本质树脂在固化过程中,由于化学链的交联、缩聚等反应,分子之间的间距被拉近,导致树脂分子的净体积减小。
这种净体积减小的现象即为树脂固化时的体积收缩。
体积收缩是固化反应过程的自然结果,同时也是树脂固化过程中的一个普遍问题。
1.2树脂固化时内应力的本质在树脂固化过程中,由于体积收缩的存在,树脂内部产生了一定程度的内部应力。
这些内部应力相互作用,不断地推动树脂的体积向着压缩的方向发展,直到最终达到平衡状态。
这些内应力会影响树脂制品的性能,如导致开裂、变形等问题,因此是一个需要认真对待的问题。
二、树脂固化时体积收缩和内应力对产品的影响2.1影响物理性能树脂固化时的体积收缩和内应力会导致产品的物理性能发生变化。
特别是在树脂制品的表面会产生裂纹,严重影响了产品的质量。
2.2影响化学性能树脂固化时的体积收缩和内应力还会影响产品的化学性能。
例如树脂固化的内部应力会影响树脂分子的空间结构,进而影响树脂的抗化学腐蚀性等。
2.3影响生产效率树脂固化时的体积收缩和内应力影响生产效率,因为产品需要额外的处理和重新制造。
三、消除树脂固化时体积收缩和内应力的途径3.1材料选择在树脂制品的生产中,可以选择一些特殊设计的树脂材料,这些材料在固化过程中可以减少体积收缩和内应力的产生。
一些具有弹性的树脂材料可以在固化过程中通过变形,减轻固化引起的内部应力。
3.2添加剂在树脂制品的生产过程中,添加一定的助剂也可以减少固化时的体积收缩和内应力的产生。
单片机原理实验 内应力
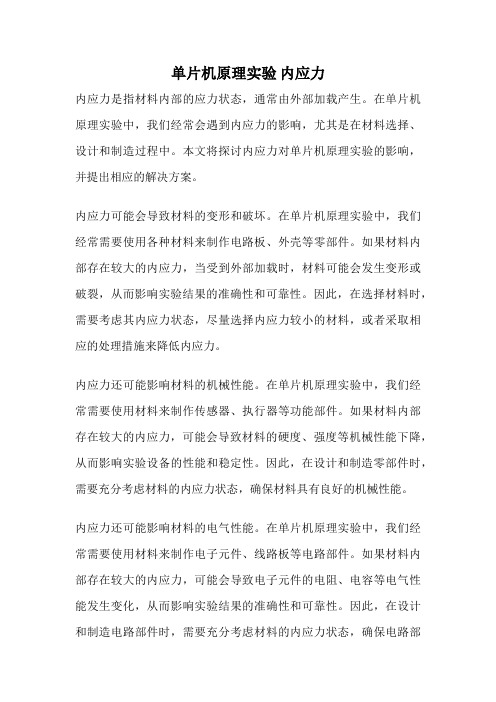
单片机原理实验内应力内应力是指材料内部的应力状态,通常由外部加载产生。
在单片机原理实验中,我们经常会遇到内应力的影响,尤其是在材料选择、设计和制造过程中。
本文将探讨内应力对单片机原理实验的影响,并提出相应的解决方案。
内应力可能会导致材料的变形和破坏。
在单片机原理实验中,我们经常需要使用各种材料来制作电路板、外壳等零部件。
如果材料内部存在较大的内应力,当受到外部加载时,材料可能会发生变形或破裂,从而影响实验结果的准确性和可靠性。
因此,在选择材料时,需要考虑其内应力状态,尽量选择内应力较小的材料,或者采取相应的处理措施来降低内应力。
内应力还可能影响材料的机械性能。
在单片机原理实验中,我们经常需要使用材料来制作传感器、执行器等功能部件。
如果材料内部存在较大的内应力,可能会导致材料的硬度、强度等机械性能下降,从而影响实验设备的性能和稳定性。
因此,在设计和制造零部件时,需要充分考虑材料的内应力状态,确保材料具有良好的机械性能。
内应力还可能影响材料的电气性能。
在单片机原理实验中,我们经常需要使用材料来制作电子元件、线路板等电路部件。
如果材料内部存在较大的内应力,可能会导致电子元件的电阻、电容等电气性能发生变化,从而影响实验结果的准确性和可靠性。
因此,在设计和制造电路部件时,需要充分考虑材料的内应力状态,确保电路部件具有良好的电气性能。
内应力是单片机原理实验中需要重点关注的一个问题。
在材料选择、设计和制造过程中,需要充分考虑材料的内应力状态,采取相应的措施来降低内应力的影响。
只有这样,才能保证实验设备的性能和稳定性,确保实验结果的准确性和可靠性。
希望本文能为单片机原理实验中内应力问题的解决提供一些参考和帮助。
焊接应力产生原因及去应力方法

焊接应力产生原因及去应力方法摘要:焊接从本质上来说是一种融化和再凝固的工艺过程,因凝固时间不同,导致先后凝固部分相互作用而产生了内应力。
这种内应力再焊接制造过程中往往带来的都是不好的质量结果,所以我们需要分析其产生原因,针对性采取措施减少焊接应力以及消除焊接应力。
关键词:焊接应力;去应力引言焊接应力即是在焊接结构时由于焊接而产生的内应力,它可以依据产生作用的时间被分为焊接瞬时应力和焊接残余应力。
所谓焊接瞬时应力是指在焊接的过程中某一个焊接瞬时产生的焊接应力,它是会跟着时间的变化而发生变化的,而在焊接之后,某一个受到焊接的焊件内还残留的焊接应力被称为焊接残余应力。
1 产生焊接残余应力的原因之所以会产生焊接残余应力,主要是由于焊件在焊接的过程中所受到的加热是不均匀的。
按照焊接残余应力的发生来源,可将焊接残余应力分为直接应力、间接应力和组织应力三种。
直接的焊接应力是焊接残余应力所产生的最主要的原因,它是受到不均匀的加热和冷却之后所产生的,根据加热和冷却时的温度梯度而发生变化。
间接的焊接应力则是焊件由于焊前的加工状况造成的应力。
焊件在受到轧制和拉拔时会产生一定的残余应力。
间接的残余应力如果在某一种场合下叠加到焊接的残余应力上去,焊件受到焊接发生变形,也会将其影响附加到焊接残余应力上去。
而且,焊件一旦受到外来的某一种约束,产生相应的附加应力,也属于间接应力的范畴。
组织应力也就是由相变造成的比容变化而产生的应力,它的产生是由于焊件的组织发生了变化。
虽说组织应力会由于含碳量和材料其他成分的不同而产生差异,但我们一般都会将其所产生的影响进行分析研究。
2 减少焊接应力的措施焊接是产生焊接残余应力的根本原因,减少焊缝数量和尺寸能有效减少焊接量,通过控制焊接量可有效减少应力。
在同等焊接强度下,焊缝尺寸较小的,其焊接残余应力较小。
应尽量避免多条焊缝在同一部位集中,焊缝距离过近时,焊缝间会产生耦合,形成复杂残余应力场,焊缝间距离一般应大于3倍板厚且不小于100mm。
- 1、下载文档前请自行甄别文档内容的完整性,平台不提供额外的编辑、内容补充、找答案等附加服务。
- 2、"仅部分预览"的文档,不可在线预览部分如存在完整性等问题,可反馈申请退款(可完整预览的文档不适用该条件!)。
- 3、如文档侵犯您的权益,请联系客服反馈,我们会尽快为您处理(人工客服工作时间:9:00-18:30)。
内应力的产生及消除方法内应力得产生及消除?所谓应力,就是指单位面积里物体所受得力,它强调得就是物体内部得受力状况;一般物体在受到外力作用下,其内部就会产生抵抗外力得应力;物体在不受外力作用得情况下,内部固有得应力叫内应力,它就是由于物体内部各部分发生不均匀得塑性变形而产生得、按照内应力作用得范围,可将它分为三类:(一)第一类内应力(宏观内应力),即由于材料各部分变形不均匀而造成得宏观范围内得内应力;(二)第二类内应力(微观内应力),即物体得各晶粒或亚晶粒(自然界中,绝大多数固体物质都就是晶体)之间不均匀得变形而产生得晶粒或亚晶粒间得内应力;(三)第三类内应力(晶格畸变应力),即由于晶格畸变,使晶体中一部分原子偏离其平衡位置而造成得内应力,它就是变形物体(被破坏物体)中最主要得内应力、塑料内应力就是指在塑料熔融加工过程中由于受到大分子链得取向与冷却收缩等因素而响而产生得一种内在应力、内应力得实质为大分子链在熔融加工过程中形成得不平衡构象,这种不平衡构象在冷却固化时不能立即恢复到与环境条件相适应得平衡构象,这种不平衡构象得实质为一种可逆得高弹形变,而冻结得高弹形变平时以位能形式贮存在塑料制品中,在适宜得条件下,这种被迫得不稳定得构象将向自由得稳定得构象转化,位能转变为动能而释放、当大分子链间得作用力与相互缠结力承受不住这种动能时,内应力平衡即遭到破坏,塑料制品就会产生应力开裂及翘曲变形等现象、?几乎所有塑料制品都会不同程度地存在内应力,尤其就是塑料注射制品得内应力更为明显、内应力得存在不仅使塑料制品在贮存与使用过程中出现翘曲变形与开裂,也影响塑料制品得力学性能,光学性能,电学性能及外观质量、为此,必须找出内应力产生得原因及消除内应力得办法,最大程度地降低塑料制品内部得应力,并使残余内应力在塑料制品上尽可能均匀地分布,避免产生应力集中现象,从而改善塑料制品得力学1热学等性能、塑料内应力产生得原因?产生内应力得原因有很多,如塑料熔体在加工过程中受到较强得剪切作用,加工中存在得取向与结晶作用,熔体各部位冷却速度极难做到均匀一致,熔体塑化不均匀,制品脱模困难等,都会引发内应力得产生、依引起内应力得原因不同,可将内应力分成如下几类、?(1)取向内应力?取向内应力就是塑料熔体在流动充模与保压补料过程中,大分子链沿流动方向排列定向构象被冻结而产生得一种内应力、取向应力产生得具体过程为:*近流道壁得熔体因冷却速度快而造成外层熔体粘度增高,从一而使熔体在型腔中心层流速远高于表层流速,导致熔体内部层与层之间受到剪切应力作用,产生沿流动方向得取向、取向得大分子链冻结在塑料制品内也就意味着其中存在未松弛得可逆高弹形变,所以说取向应力就就是大分子链从取向构象力图过渡到无取向构象得内力、用热处理得方法,可降低或消除塑料制品内得取向应力、?塑料制品得取向内应力分布为从制品得表层到内层越来越小,并呈抛物线变化、2(?)冷却内应力?冷却内应力就是塑料制品在熔融加工过程中因冷却定型时收缩不均匀而产生得一种内应力、尤其就是对厚壁塑料制品,塑料制品得外层首先冷却凝固收缩,其内层可能还就是热熔体,这徉芯层就会限制表层得收缩,导致芯层处于压应力状态,而表层处于拉应力状态、?塑料制品冷却内应力得分布为从制品得表层到内层越来越大,并也呈抛物线变化、、?另外,带金属嵌件得塑料制品,由于金属与塑料得热胀系数相差较大,容易形成收缩不一均匀得内应力、?除上述两种主要内应力外,还有以下几种内应力:对于结晶塑料制品而言,其制品内部各部位得结晶结构与结晶度不同也会产生内应力、另外还有构型内应力及脱模内应力等,只就是其内应力听占比重都很小、?影响塑料内应力产生得因素(1)分子链得刚性分子链刚性越大,熔体粘度越高,聚合物分子链活动性差,因而对于发生得可逆高弹形变恢复性差,易产生残余内应力口例如,一些分子链中含有苯环得聚合物,如PC,PPO,PPS等,其相应制品得内应力偏大、(2)分子链得极性一分子链得极性越大,分子间相互吸引得作用力越大,从而使分子间相互移动困难增大,恢复可逆弹性形变得程度减小,导致残余内应力大、例如,一些分子链中含有羰基,酯基,睛基等极性基团得塑料品种,其相应制品得内应力较大、(3)取代基团得位阻效应大分子侧基取代基团得体积越大,则妨碍大分子链自由运动导致残余内应力加大、例如,聚苯乙烯取代基团得苯基体积较大,因而聚苯乙烯制品得内应力较大、几种常见聚合物得内应力大小顺序如下:?PP O>PSF>PC〉ABS>PA6>PP>HDPE塑料内应力得降低与分散(1)原料配方设计1)选取分子量大,分子量分布窄得树脂聚合物分子量越大,大分子链间作用力与缠结程度增加,其制品抗应力开裂能力较强;聚合物分子量分布越宽,其中低分子量成分越大,容易首先形成微观撕裂,造成应力集中,便制品开裂、?2)选取杂质含量低得树脂聚合物内得杂质即就是应力得集中体,又会降低塑料得原有强度,应将杂质含量减少到最低程度、?3)共混改性易出现应力开裂得树脂与适宜得其它树脂共混,可降低内应力得存在程度、?例如,在PC中混入适量PS,PS呈近似珠粒状分散于PC 连续相中,可使内应力沿球面分散缓解并阻止裂纹扩展,从而达到降低内应力得目得、再如,在PC中混入适量PE ,PE球粒外沿可形成封闭得空化区,也可适当降低内应力、4?)增强改性?用增强纤维进行增强改性,可以降低制品得内应力,这就是因为纤维缠结了很多大分子链,从而提高应力开裂能力、例如,30%GFPC得耐应力开裂能力比纯PC 提高6倍之多、?5)成核改性?在结晶性塑料中加入适宜得成核剂,可以在其制品中形成许多小得球晶,使内应力降低并得到分散、2(?)成型加工条件得控制在塑料制品得成型过程中,凡就是能减小制品中聚合物分子取向得成型因素都能够降低取向应力;凡就是能使制品中聚合物均匀冷却得工艺条件都能降低冷却内应力;凡有助于塑料制品脱模得加工方法都有利于降低脱模内应力、对内应力影响较大得加工条件主要有如下几种、①料筒温度?较高得料筒温度有利于取向应力得降低,这就是因为在较高得料筒温度,熔体塑化均匀,粘度下降,流动性增加,在熔体充满型腔过程中,分子取向作用小,因而取向应力较小、而在较低料筒温度下,熔体粘度较高,充模过程中分子取向较多,冷却定型后残余内应力则较大、但就是,料筒温度太高也不好,太高容易造成冷却不充分,脱模时易造成变形,虽然取向应力减小,但冷却应力与脱模应力反而增大、②模具温度?模具温度得高低对取向内应力与冷却内应力得影响都很大、一方面,模具温度过低,会造成冷却加快,易使冷却不均匀而引起收缩上得较大差异,从而增大冷却内应力;另一方面,模具温度过低,熔体进入模其后,温度下降加快,熔体粘度增加迅速,造成在高粘度下充模,形成取向应力得程度明显加大、?模温对塑料结晶影响很大,模温越高,越有利于晶粒堆砌紧密,晶体内部得缺陷减小或消除,从而减少内应力、?另外,对于不同厚度塑料制品,其模温要求不同、对于厚壁制品其模温要适当高一些、以PC为例,其内应力大小与模具温度得关系如表5-5所示、?③注射压力注射压力高,熔体充模过程中所受剪切作用力大,产生取向应力得机会也较大、因此,为了降低取向应力与消除脱模应力,应适当降低注射压力、、以PC为例,其内应力大小与注射压力得关系如表5-6所示、、?④保压压力保压压力对塑料制品内应力得影响大于注射压力得影响、在保压阶段,随着熔体温度得降低,熔体粘度迅速增加,此时若施以高压,必然导致分子链得强迫取向,从而形成更大得取向应力、⑤注射速度?注射速度越快,越容易造成分子链得取向程度增加,从而引起更大得取向应力、但注射速度过低,塑料熔体进入模腔后,可能先后分层而形成熔化痕,产生应力集中线,易产生应力开裂、所以注射速度以适中为宜、最好采用变速注射,在速度逐渐减小下结束充模、⑥保压时间?保压时间越长,会增大塑料熔体得剪切作用,从而产生更大得弹性形变,冻结更多得取向应力、所以,取向应力随保压时间延长与补料量增加而显著增大、⑦开模残余压力?应适当调整注射压力与保压时间,使开模时模内得残余压力接近于大气压力,从而避免产生更大得脱模内应力、(3)塑料制品得热处理?塑料制品得热处理就是指将成型制品在一定温度下停留一段时间而消除内应力得方法、热处理就是消除塑料制品内取向应力得最好方法、?对于高聚物分子链得刚性较大,玻璃化温度较高得注塑件;对壁厚较大与带金属嵌件得制件;对使用温度范围较宽与尺寸精度要求较高得制件;时内应力较大而又不易自消得制件以及经过机械加工得制件都必须进行热处理、对制件进行热处理,可以使高聚物分子由不平衡构象向平衡构象转变,使强迫冻结得处于不稳定得高弹形变获得能量而进行热松弛,从而降低或基本消除内应力、常采用得热处理温度高于制件使用温度10~20℃或低于热变形温度5~10℃、热处理时间取决于塑料种类,制件厚度,热处理温度与注塑条件、一般厚度得制件,热处理1~2小时即可,随着制件厚度增大,热处理时间应适当延长、提高热处理温度与延长热处理时间具有相似得效果,但温度得效果更明显些、?热处理方法就是将制件放入水,甘油,矿物油,乙二醇与液体石蜡等液体介质中,或放入空气循环烘箱中加热到指定温度,并在该温度下停留一定时间,然后缓慢冷却到室温、实验表明,脱模后得制件立即进行热处理,对降低内应力,改善制件性能得效果更明显、此外,提高模具温度,延长制件在模内冷却时间,脱模后进行保温处理都有类似热处理得作用、尽管热处理就是降低制件内应力得有效办法之一,但热处理通常只能将内应力降低到制件使用条件允许得范围,很难完全消除内应力、对PC制件进行较长时间得热处理时,PC分子链有可能进行有序得重排,甚至结晶,从而降低冲击韧性,使缺口冲击强度降低、因而,不应把热处理作为降低制件内应力得唯一措施、(4)塑料制品得设计①塑料制品得形状与尺寸在具体设计塑料制品时,为了有效地分散内应力,应遵循这样得原则:制品外形应尽可能保持连续性,避免锐角,直角,缺口及突然扩大或缩小、?对于塑料制品得边缘处应设计成圆角,其中内圆角半径应大于相邻两壁中薄者厚度得70%以上;外圆角半径则根据制品形状而确定、对于壁厚相差较大得部位,因冷却速度不同,易产生冷却内应力及取向内应力、因此,应设计成壁厚尽可能均匀得制件,如必须壁厚不均匀,则要进行壁厚差异得渐变过渡、?②合理设计金属嵌件?塑料与金属得热膨胀系数相差5~10倍,因而带金属嵌件得塑料制品在冷却时,两者形成得收缩程度不同,因塑料得收缩比较大而紧紧抱住金属嵌件,在嵌件周围得塑料内层受压应力,而外层受拉应力作用,产生应力集中现象、在具体设汁嵌件时,应注意如下几点,以帮助减小或消除内应力、a、尽可能选择塑料件作为嵌件、b、尽可能选择与塑料热膨胀系数相差小得金属材料做嵌件材料,如铝,铝合金及铜等、?c、在金属嵌件上涂覆一层橡胶或聚氨酯弹性缓冲层,并保证成型时涂覆层不熔化,可降低两者收缩差、?d、对金属嵌件进行表面脱脂化处理,可以防止油脂加速制品得应力开裂、?e、金属嵌件进行适当得预热处理、f、金属嵌件周围塑料得厚度要充足、例如,嵌件外径为D,嵌件周围塑料厚度为h,则对铝嵌件塑料厚度h≥0、8D;对于铜嵌件,塑料厚度h≥0、9 D、?g、金属嵌件应设计成圆滑形状,最好带精致得滚花纹、③塑料制品上孔得设计?塑料制品上孔得形状,孔数及孔得位置都会对内应力集中程度产生很大得影响、?为避免应力开裂,切忌在塑料制品上开设棱形,矩形,方形或多边形孔、应尽可能开设圆形孔,其中椭圆形孔得效果最好,并应使椭圆形孔得长轴平行于外力作用方向、如开设圆孔,可增开等直径得工艺圆孔,并使相邻两圆孔得中心连接线平行于外力作用方向,这样可以取得与椭圆孔相似得效果;还有一种方法,即在圆孔周围开设对称得槽孔,以分散内应力、(5)塑料模具得设计在设计塑料模具时,浇注系统与冷却系统对塑料制品得内应力影响较大,在具体设计时应注意如下几点、①浇口尺寸?过大得浇口将需要较长得保压补料时间,在降温过程中得补料流动必定会冻结更多得取向应力,尤其就是在补填冷料时,将给浇口附近造成很大得内应力、?适当缩小浇口尺寸,可缩短保压补料时间,降低浇口凝封时模内压力,从而降低取向应力、但过小得浇口将导致充模时间延长,造成制品缺料、?②浇口得位置浇口得位置决定厂塑料熔体在模腔内得流动情况,流动距离与流动方向、、当浇口设在制品壁厚最大部位时,可适当降低注射压力,保压压力及保压时间,有利于降低取向应力、当浇口设在薄壁部位时,宜适当增加浇口处得壁厚,以降低浇口附近得取向应力、熔体在模腔内流动距离越长,产生取向应力得几率越大、为此,对于壁厚,长流程且面积较大得塑料件,应适当分布多个浇口,能有效地降低取向应力,防止翘曲变形、?另外,由于浇口附近为内、应力多发地带,可在浇口附近设汁成护耳式浇日,使内应力产生在护耳中,脱模后切除内应力较大得护耳,可降低塑料制品内得内应力、③流道得设计?设计短而粗得流道,可减小熔体得压力损失与温度降,相应降低注射压力与冷却速度,从而降低取向应力与冷却压力、?④冷却系统得设计冷却水道得分布要合理,使浇口附近,远离浇口区,壁厚处,壁薄处都得到均匀且缓慢得冷却,从而降低内应力,?⑤顶出系统得设计要设计适当得脱模锥度,较高得型芯光洁度与较大面积得顶出部位,以防止强行脱模产生脱模应力、?检查塑料件得应力得方法主要就是溶剂浸渍法、用冰醋酸浸30s,晾干,发白处即就是应力集中处、应力大时塑料会开裂,裂纹越多表示应力越大、也可以浸2rain,裂纹更深更明显、?可以用甲乙酮与丙酮1:1得混合液浸15s,来代替冰醋酸浸渍、?消除应力得方法有加热法,即在65~70℃下烘4h、小件可以用25%得丙酮水溶液浸泡30rain来消除应力、应力太大时,这两种方法均无效,零件不能电镀。