涤棉混纺织物染色
涤棉混纺织物的染色教学设计
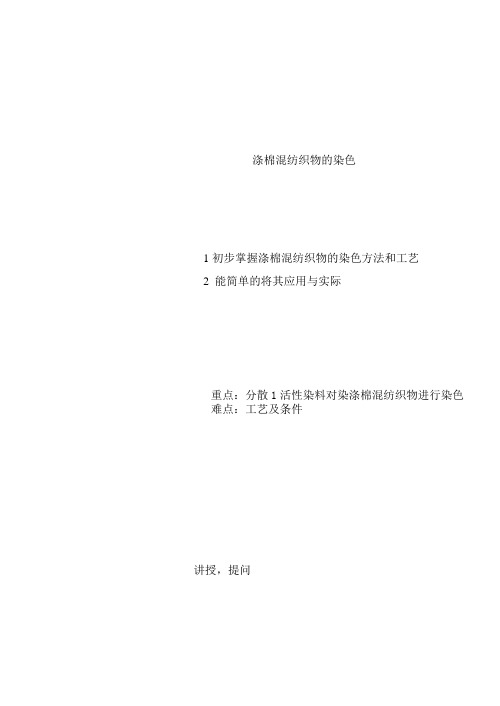
涤棉混纺织物的染色1初步掌握涤棉混纺织物的染色方法和工艺2 能简单的将其应用与实际重点:分散1活性染料对染涤棉混纺织物进行染色难点:工艺及条件讲授,提问4-3涤棉混纺织物的染色一染料选择 2.分散-活性二浴法二染色方法浸染三涤棉混纺织物的染色 1.分散染涤(一)分散染料染色 2.活性染棉(二)分散-活性染料染色(三)分散-还原染料染色轧染 1.分散-还原一浴法1分散-活性一浴法 1.流程(1)热浴轧蒸法 2.处方a 流程 3.条件b 处方分散-还原二浴法c 条件(2)热浴固色法1.分析分散-活性浸染二浴法染涤棉混纺织物工艺2.分析分散-还原一浴轧染涤棉混纺织物工艺4-3涤棉混纺织物的染色复习:涤棉混纺织物的前处理新课第一课时一,染料选择涤:分散染料棉:活性染料还原染料直接染料具体分析见表3-4-1 P143二染色方法两种染料染色方法二浴法一浴二步法一浴一步法三涤棉混纺织物的染色(一)分散染料染色1.单染涤纶,用于染淡色或()产品2.分析染料对棉有一定的沾色(二)分散-活性染料轧染染色1.分散-活性一浴法(1)热浴轧蒸法(一浴二步法)a 流程:浸轧分散-活性染料液-红外线顶烘-烘干-热浴-轧碱-汽蒸-水洗-烘干b 处方:分散染料xg/l (要求有较好的耐碱性)轧染液:活性染料yg/l防泳移剂10-30g/l尿素0-100g/l渗透剂1-2ml/l(碱液处方:氢氧化钠 4.5-9.0g/L碳酸钠40g/L元明粉200g/L)实验中C条件:培烘温度180-210摄氏度时间 1.2min汽蒸温度100-103摄氏度时间30-60S(2)热浴固色法(一浴一步法)浸轧染液-烘干-热浴-后处理NaHCO3 5-10g/l2.分散-活性二浴法先用分散染涤,后用活性染棉浸轧分散染料染液-红外线顶烘-热风烘干-热浴固色-水洗-皂洗-水洗-烘干-套染活性染料。
分散-活性浸染染色1.分散染料高温高压方法染涤2.活性染料套染棉第二课时(三)分散-还原染料染色1.分散-还原一浴法(1)流程:浸轧分散/还原染料液-红外线顶烘-热风烘干-热浴-浸轧还原液-还原汽蒸(100摄氏度.60S)-水洗-室温浸轧氧化液-皂洗-热水洗-冷水洗-烘干(2)处方浸轧液:分散染料xg/l还原染料yg/l (小于60g/l)防泳移剂15g/l渗透剂1-2g/l还原液:NaoH 22-26 26-35 35-4585摄氏度保险粉30-40 40-50 50-60(三)条件:T热浴180-210摄氏度t热浴1-2’T 热风烘干110-120摄氏度T 汽蒸100摄氏度t汽蒸60’2.分散-还原二浴法(1)分散染料高温高压法或热浴法染涤纤维(2)还原染料卷染(浸染)或悬浮体轧染棉纤维四小结五作业布置。
涤棉织物染整工艺设计
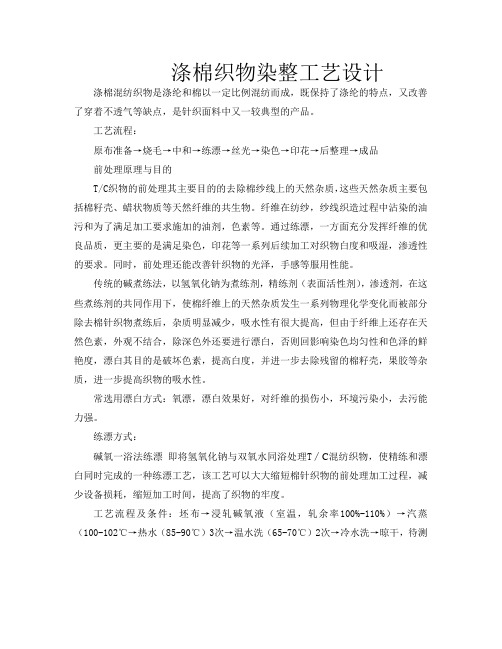
涤棉织物染整工艺设计涤棉混纺织物是涤纶和棉以一定比例混纺而成,既保持了涤纶的特点,又改善了穿着不透气等缺点,是针织面料中又一较典型的产品。
工艺流程:原布准备→烧毛→中和→练漂→丝光→染色→印花→后整理→成品前处理原理与目的T/C织物的前处理其主要目的的去除棉纱线上的天然杂质,这些天然杂质主要包括棉籽壳、蜡状物质等天然纤维的共生物。
纤维在纺纱,纱线织造过程中沾染的油污和为了满足加工要求施加的油剂,色素等。
通过练漂,一方面充分发挥纤维的优良品质,更主要的是满足染色,印花等一系列后续加工对织物白度和吸湿,渗透性的要求。
同时,前处理还能改善针织物的光泽,手感等服用性能。
传统的碱煮练法,以氢氧化钠为煮练剂,精练剂(表面活性剂),渗透剂,在这些煮练剂的共同作用下,使棉纤维上的天然杂质发生一系列物理化学变化而被部分除去棉针织物煮练后,杂质明显减少,吸水性有很大提高,但由于纤维上还存在天然色素,外观不结合,除深色外还要进行漂白,否则回影响染色均匀性和色泽的鲜艳度,漂白其目的是破坏色素,提高白度,并进一步去除残留的棉籽壳,果胶等杂质,进一步提高织物的吸水性。
常选用漂白方式:氧漂,漂白效果好,对纤维的损伤小,环境污染小,去污能力强。
练漂方式:碱氧一浴法练漂即将氢氧化钠与双氧水同浴处理T∕C混纺织物,使精练和漂白同时完成的一种练漂工艺,该工艺可以大大缩短棉针织物的前处理加工过程,减少设备损耗,缩短加工时间,提高了织物的牢度。
工艺流程及条件:坯布→浸轧碱氧液(室温,轧余率100%-110%)→汽蒸(100-102℃→热水(85-90℃)3次→温水洗(65-70℃)2次→冷水洗→晾干,待测练漂工艺处方:100% NaOH 10g/l100%H2O2 8 g/l氧漂稳定剂 5 g/l高效精炼剂5g/l浴比1:20测试毛效:11cm/30min 贴样:白度:74.4%练漂前断裂强度:853.6N/㎡练漂后断裂强度:750.2 N/㎡强力损伤率:12.11%丝光丝光是指棉布或棉纱在张力状态下用浓碱处理,赋予棉纤维一定的光泽,并改善纤维制品应用性能得加工过程。
涤棉混纺织物染色加工中的色差问题
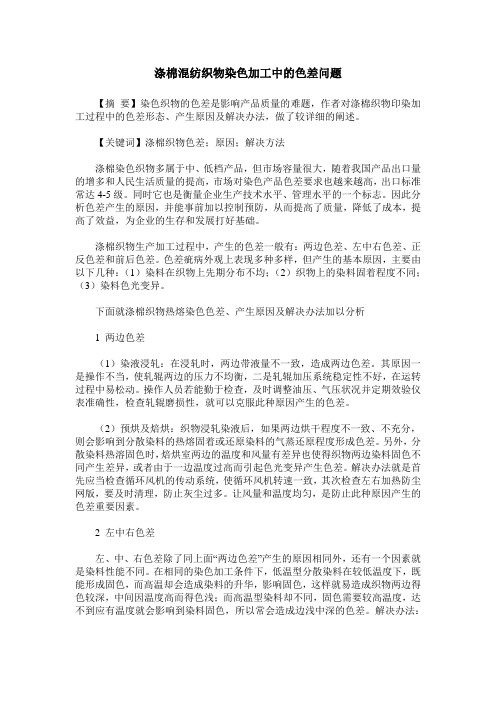
涤棉混纺织物染色加工中的色差问题【摘要】染色织物的色差是影响产品质量的难题,作者对涤棉织物印染加工过程中的色差形态、产生原因及解决办法,做了较详细的阐述。
【关键词】涤棉织物色差;原因;解决方法涤棉染色织物多属于中、低档产品,但市场容量很大,随着我国产品出口量的增多和人民生活质量的提高,市场对染色产品色差要求也越来越高,出口标准常达4-5级。
同时它也是衡量企业生产技术水平、管理水平的一个标志。
因此分析色差产生的原因,并能事前加以控制预防,从而提高了质量,降低了成本,提高了效益,为企业的生存和发展打好基础。
涤棉织物生产加工过程中,产生的色差一般有:两边色差、左中右色差、正反色差和前后色差。
色差疵病外观上表现多种多样,但产生的基本原因,主要由以下几种:(1)染料在织物上先期分布不均;(2)织物上的染料固着程度不同;(3)染料色光变异。
下面就涤棉织物热熔染色色差、产生原因及解决办法加以分析1 两边色差(1)染液浸轧:在浸轧时,两边带液量不一致,造成两边色差。
其原因一是操作不当,使轧辊两边的压力不均衡,二是轧辊加压系统稳定性不好,在运转过程中易松动。
操作人员若能勤于检查,及时调整油压、气压状况并定期效验仪表准确性,检查轧辊磨损性,就可以克服此种原因产生的色差。
(2)预烘及焙烘:织物浸轧染液后,如果两边烘干程度不一致、不充分,则会影响到分散染料的热熔固着或还原染料的气蒸还原程度形成色差。
另外,分散染料热溶固色时,焙烘室两边的温度和风量有差异也使得织物两边染料固色不同产生差异,或者由于一边温度过高而引起色光变异产生色差。
解决办法就是首先应当检查循环风机的传动系统,使循环风机转速一致,其次检查左右加热防尘网版,要及时清理,防止灰尘过多。
让风量和温度均匀,是防止此种原因产生的色差重要因素。
2 左中右色差左、中、右色差除了同上面“两边色差”产生的原因相同外,还有一个因素就是染料性能不同。
在相同的染色加工条件下,低温型分散染料在较低温度下,既能形成固色,而高温却会造成染料的升华,影响固色,这样就易造成织物两边得色较深,中间因温度高而得色浅;而高温型染料却不同,固色需要较高温度,达不到应有温度就会影响到染料固色,所以常会造成边浅中深的色差。
涤棉混纺织物双色染整工艺
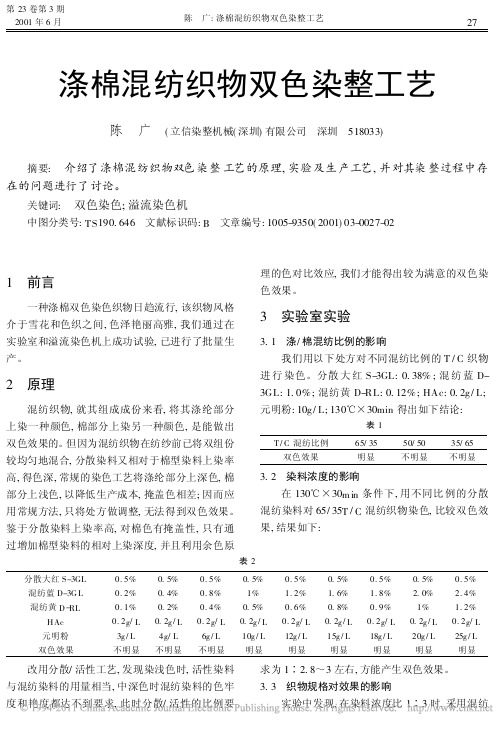
涤棉混纺织物双色染整工艺陈 广 (立信染整机械(深圳)有限公司 深圳 518033) 摘要: 介绍了涤棉混纺织物双色染整工艺的原理,实验及生产工艺,并对其染整过程中存在的问题进行了讨论。
关键词: 双色染色;溢流染色机中图分类号:TS190.646 文献标识码:B 文章编号:1005-9350(2001)03-0027-021 前言一种涤棉双色染色织物日趋流行,该织物风格介于雪花和色织之间,色泽艳丽高雅,我们通过在实验室和溢流染色机上成功试验,已进行了批量生产。
2 原理混纺织物,就其组成成份来看,将其涤纶部分上染一种颜色,棉部分上染另一种颜色,是能做出双色效果的。
但因为混纺织物在纺纱前已将双组份较均匀地混合,分散染料又相对于棉型染料上染率高,得色深,常规的染色工艺将涤纶部分上深色,棉部分上浅色,以降低生产成本,掩盖色相差;因而应用常规方法,只将处方做调整,无法得到双色效果。
鉴于分散染料上染率高,对棉色有掩盖性,只有通过增加棉型染料的相对上染深度,并且利用余色原理的色对比效应,我们才能得出较为满意的双色染色效果。
3 实验室实验3.1 涤/棉混纺比例的影响我们用以下处方对不同混纺比例的T/C织物进行染色。
分散大红S-3GL:0.38%;混纺蓝D-3GL:1.0%;混纺黄D-RL:0.12%;HAc:0.2g/L;元明粉:10g/L;130℃×30min得出如下结论:表1T/C混纺比例65/3550/5035/65双色效果明显不明显不明显3.2 染料浓度的影响在130℃×30m in条件下,用不同比例的分散混纺染料对65/35T/C混纺织物染色,比较双色效果,结果如下:表2分散大红S-3GL0.5%0.5%0.5%0.5%0.5%0.5%0.5%0.5%0.5%混纺蓝D-3G L0.2%0.4%0.8%1% 1.2% 1.6% 1.8% 2.0% 2.4%混纺黄D-RL0.1%0.2%0.4%0.5%0.6%0.8%0.9%1% 1.2% HAc0.2g/L0.2g/L0.2g/L0.2g/L0.2g/L0.2g/L0.2g/L0.2g/L0.2g/L 元明粉3g/L4g/L6g/L10g/L12g/L15g/L18g/L20g/L25g/L 双色效果不明显不明显不明显明显明显明显明显明显明显 改用分散/活性工艺,发现染浅色时,活性染料与混纺染料的用量相当,中深色时混纺染料的色牢度和艳度都达不到要求,此时分散/活性的比例要求为1∶2.8~3左右,方能产生双色效果。
涤棉一浴一步法染色加工方法的探究
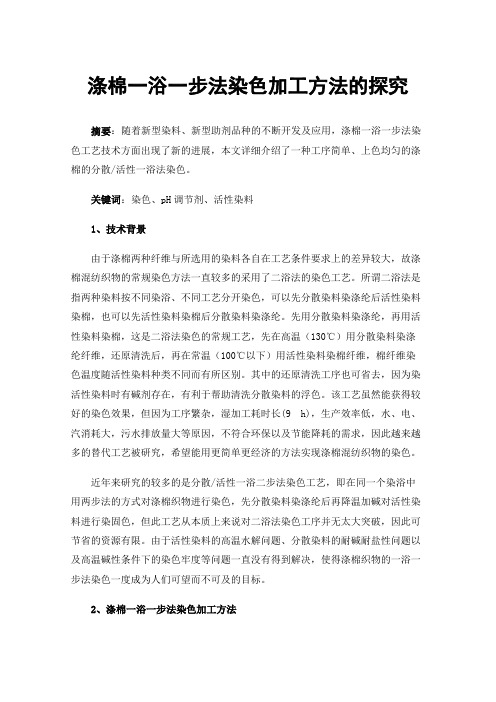
涤棉一浴一步法染色加工方法的探究摘要:随着新型染料、新型助剂品种的不断开发及应用,涤棉一浴一步法染色工艺技术方面出现了新的进展,本文详细介绍了一种工序简单、上色均匀的涤棉的分散/活性一浴法染色。
关键词:染色、pH调节剂、活性染料1、技术背景由于涤棉两种纤维与所选用的染料各自在工艺条件要求上的差异较大,故涤棉混纺织物的常规染色方法一直较多的采用了二浴法的染色工艺。
所谓二浴法是指两种染料按不同染浴、不同工艺分开染色,可以先分散染料染涤纶后活性染料染棉,也可以先活性染料染棉后分散染料染涤纶。
先用分散染料染涤纶,再用活性染料染棉,这是二浴法染色的常规工艺,先在高温(130℃)用分散染料染涤纶纤维,还原清洗后,再在常温(100℃以下)用活性染料染棉纤维,棉纤维染色温度随活性染料种类不同而有所区别。
其中的还原清洗工序也可省去,因为染活性染料时有碱剂存在,有利于帮助清洗分散染料的浮色。
该工艺虽然能获得较好的染色效果,但因为工序繁杂,湿加工耗时长(9 h),生产效率低,水、电、汽消耗大,污水排放量大等原因,不符合环保以及节能降耗的需求,因此越来越多的替代工艺被研究,希望能用更简单更经济的方法实现涤棉混纺织物的染色。
近年来研究的较多的是分散/活性一浴二步法染色工艺,即在同一个染浴中用两步法的方式对涤棉织物进行染色,先分散染料染涤纶后再降温加碱对活性染料进行染固色,但此工艺从本质上来说对二浴法染色工序并无太大突破,因此可节省的资源有限。
由于活性染料的高温水解问题、分散染料的耐碱耐盐性问题以及高温碱性条件下的染色牢度等问题一直没有得到解决,使得涤棉织物的一浴一步法染色一度成为人们可望而不可及的目标。
2、涤棉一浴一步法染色加工方法将布料加入到染色浴中,其中染色浴温度为40℃时,依次加入染料及pH调节剂07,运行10分钟后再加染色助剂,其中,染色助剂的添加分两次,第一次添加总添加量的1/3,运行10分钟后将剩余2/3添加进去,保持20 分钟;然后升温至80℃,升温速率为 2 ℃/min,保持20分钟;继续升温至130℃,升温速率为1.67℃/min,在此温度下,保持30分钟,完成染色;降温到80℃后,依次进行初水洗、皂洗和后水洗,初水洗温度为常温,初水洗时间为10分钟;皂洗采用的是酸性皂洗剂DM261,皂洗温度为98℃,皂洗时间为10分钟;后水洗温度为常温,后水洗时间为10分钟。
(施教授)涤纶及其混纺织物染色

分散红3B
10.8
13.1
载体
苯甲醚 苯甲醛 苯甲醇
溶解度参数 涤纶上的溶解度 (4.184J)1/2/cm3/2 (g/100g纤维)
9.5
7.4
10.4
9.7
11.97
8.5
3. 分散染料上染的吸附等温线
[D]f
[D]f
140 120 100 80 60 40 20
0 20 30 40 50 60 70 80 [D]s
涤纶 锦纶66
分散坚牢 地来诺尔
橙G
红2B
4.1
12.0
2.0
4.4
分散紫 2R 0.4
4.9
地来诺尔坚 牢黄A 7.1
5.0
2. 由于分散染料以偶氮型为主,当织物上残留有还原性 物质时,如浆料、纤维素纤维、分散剂(含亚硫酸 盐)、羊毛的胱氨酸,会使染料被还原为芳胺化合物 而不能上染涤纶纤维。
(三)分散染料的热稳定性
1. 分散染料分子量小,分子链短,含极性基团少,与纤 维的结合力小,在纤维上的固着是借助外界条件溶解 于纤维中。染色织物在高温热处理下,染料易升华, 导致褪色或沾染白地或其它颜色,以及高温热处理设 备。
二、普通涤纶纤维的性能
(一)比重:结晶部分比重为1.455,无定形部分比重为 1.355,一般为1.38~1.40,比锦纶和腈纶高。
(二)力学性能
1. 强度和伸长度。涤纶纤维的强度很高,干强4~7cN/dtex,湿 态下强度不下降。主要是因为:
① 在涤纶纤维的大分子之间,能相互镶嵌结合形成结晶度高达60%左右 的结晶区。
• 室温时溶解度为0.1~10mg/L
• 80℃时约为0.2~100mg/L
• 100℃时约为0.4~200mg/L
涤棉混纺织物染色加工中的色差问题

涤棉混纺织物染色加工 中的色差 问题
崔成 玉
【 牡丹 江床 单色织厂 )
【 摘 要】 染 色织物的 色差是影 响产品质量的难题 ,作者对涤 棉 织物 印染加工过程 中的 色差形 态、产生原因及 解决 办法 ,做 了较
详 细度、风量不一致,引起染料泳移 ,产 生正反色差 。解 决办 法:热风 部分采用横辊穿布方式 ,防止正反面 色差 :还可 以在 染液 中加 入适当的防泳移剂 ,如海藻酸钠 、聚丙烯 酸衍生物等 防止 正反色差 。 4 前 后 色 差 ( 1 )坯布方面:如纤维种类 、配 比和上浆情况 的不 同,造成 染 料 因吸收程度差异而形成色光 不一、深浅不 一。 ( 2)前处理方面:就煮练而言 ,若轧碱浓度 、汽 蒸温度 和时间 控制不当,就会造成毛效一段高一段低 ,染色就会跟 着一 段深一段 浅;再如 白度, 由于轧液浓度 、轧液率 、汽蒸温度和 堆置 时间等条 下面就涤棉织物热熔染色色差 、产生 原因及 解决办 法加以分析 件波动,造成 白度差异 ,白度不一 ,染色后必然反 映在色 光上,严 1 两 边 色 差 重 的 就会 影 响 色 差 。 ( 1 )染液浸轧:在浸轧时 , 两边 带液量 不一 致,造成两边色差 ( 3 ) 染色 方面: 进焙烘箱之 前织物干潮不一致 , 影响热熔效果 , 其 原因一是操 作不当 ,使轧辊两边 的压力不均衡 ,二是轧辊加压系 造成 明显色差 ( 含水率低 于 3 0 % ,可有 效防止因泳移造成色差 ;热 统稳定性 不好 ,在运 转过程中易松动 。操作人 员若能 勤于检 查 ,及 熔温度是染色过程中影响色差最显著因素,一般温差控制在 3 — 5 ℃; 时调整 油压 、气压状况并定期效验仪表准确性 ,检查轧辊磨损性 , 车速 、还原浓度 、还原汽 蒸温度 以及氧 化液 浓度等工艺条件掌握不 就 可以克服此种 原因产 生的色差。 致 ,造成前后得色不一 致而 产生色差;采用了不同产地 、批次染 ( 2 )预烘及焙烘 :织物浸 轧染液 后 ,如果两边烘干程度不一 料 ,使得染料颗粒在批 与批之 间大小不一,得色不一 ,造成前后色 致 、不 充分,则会影响到分散染料 的热熔 固着 或还原染料的气蒸还 差 。 ( 4 ) 后整理方面: 由于涤棉产 品大都采用分散热熔法染色工艺 , 原程度 形成色差 。另外 ,分散染料 热溶 固色时,焙烘室两边 的温度 和风量 有差异也使得织物两边染料 固色 不同产生差异 ,或者 由于一 染色后半制 品幅 宽收缩较 多, 在采用高温 ( 1 7 0 — 1 8 0 ℃)拉幅和树脂 边温度过高而 引起色光变异产 生色差。解决办法就是首先应 当检查 整理 中,热拉或焙烘温度控制 不当,引起 染料色泽变异 ,产 生色差 。 循环风机的传动系统 ,使循环风机 转速 一致,其次检查左右加热防 解 决办 法 : 尘网版 ,要及时清理 ,防止灰尘过 多。让风量和温度均匀 ,是 防止 I )不同坯布分 别堆放 ,分批使用 ,并且使用前抽查 。 此种原因产生的色差重要因素 。 2 )经常检查定型机,保持风道畅通 ,热 风烘房温度均匀 ,左右 2 左 中 右 色 差 前 后 一致 。 左 、 中 、右 色 差 除 了 同 上 面 “ 两 边 色 差 ”产 生 的原 因相 同 外 , 3 )染整加 工的半制品,其退浆及 丝光织物上 的 p H值必须做 到 还有一个因素就是染料性 能不同。在相 同的染色加工条件 下,低温 各机台出布工检查、挡车工复查、染色前抽查 ,并保证半 制品其它 型分散染料在较低温 度下,既能形成固色 ,而高温却会造 成染料的 各项理化 指标均 匀。 升华 ,影响 固色,这 样就易造成织物两边得色较深 ,中间因温度高 4 )染料要按产地、批量分开存放 ,并且要求在 2 以下粒子 占 而得色浅 :而 高温 型染料 却不同, 固色需要较高温度 ,达 不到应有 8 0 % 以上。织物从预烘箱进 入焙烘 箱之前一定要 烘干。 温度就会影 响到染料 固色 ,所 以常会造成边浅 中深 的色差。解决办 5 )控制好预烘、焙烘温度、风速 以及其他工艺条件。 法: 5结束语 ( 1 )采用均 匀轧车,是解决左、 中、右色差的好办法 。 预防和控制涤棉织 物染色;  ̄ n - r 过程中所产生的色差 ,除加强生 ( 2 )改善干 燥设备 性能,提高织物干燥的均匀性。 产过程的工艺管理 、质量管理和严把质量关 外,还 必须积 极采用新 ( 3 ) 染色时要合理选择 染料 , 应尽量选择固着 曲线相似的染料 , 技术、新工艺 、新助剂和短流 程的工艺设备,如:变 “ 二浴二段 ” 以利 于 色 差 的 克 服 。 为“ 一浴二段 ” 。 使 用热迁 移提升级( 分散 固色剂 ) T h e r m o f i x T M R + T M F ( 4 )改进加料方法 ,在各工序有续加料液地方 ,在液槽 的进布 及特殊净洗剂 A p a t r - o n e其皂洗 牢度提高 0 . 5 - 1级等 。 最终达到更 多 处装 设插板或淋管 ,使料液与布面 均匀 接触,消除布面左 、中、右 克服染疵和降耗提质的 目的。
分散染料染色—涤棉混纺织物的染色

双组分纤维纺织品染色方法
•一种染料一浴一步法:一种染料同一浴同一条件下同 时上染两种纤维。如活性染料染棉/麻。
•一种染料一浴二步法:一种染料同一浴不同一条件下 分别上染两种纤维。如聚酯士林染料染T/C。
•两种染料一浴一步法:两种染料在同一浴中同一条件 下分别上染两种纤维。如分散/直接染T/C。
1)一浴法 ①分散/活性一浴法 热熔焙固一步法 流程:浸轧染液→烘干→热熔→汽蒸→水洗后处理 处方组成
分散染料 X 活性染料 Y 尿素 10g/L 小苏打 30g/L 防泳移剂 30-40g/L 表面活性剂 1mL/L
工艺说明 -染料要求:分散染料要求耐碱、升华牢度高;活性染 料耐高温(K型) ,弱碱条件下固色, -尿素作用:助溶、吸湿膨化作用、防止棉纤维高温带 碱处理产生的泛黄现象 -碱剂:碱剂常用小苏打,以减轻对分散染料的影响。 -海藻酸钠为常用的防泳移剂。 -为防止碱剂对分散染料和涤纶纤维的影响,可采用膦 酸基型(P型)活性染料在弱酸性条件下染色。
2、两种染料染色 根据两种染料是否放在同一染浴中染色,可分为一浴
法和二浴法。一浴法工艺流程短,可提高生产效率,但 染料选用要求高,上染率低,染深浓色困难;二浴法染 色一般先染涤纶后染棉,工艺繁复,但色光易控制。 常用染色工艺:
•分散/活性一浴一步法 •分散/活性一浴二步法 •分散/活性二浴法 •分散/还原一浴二步法 •分散/还原二浴法
还原液: 烧碱 保险粉 还原染液
工艺说明: -染料颗粒要求在2um以下。 -染浴中可不加分散剂。 -轧余率不能太高(55-60%) -热熔温度应略高,有利于棉纤维上的分散染料 向涤纶转移。 -无需进行料染涤纶、后用棉用染料染棉,
分浴进行,染色工艺分别同各自染料染色。 ①分散/活性二浴法 染涤:浸轧分散液→烘干→热熔→还原清洗→皂洗→水洗 染棉: 一浴法:浸轧染液→烘干→汽蒸或焙烘→水洗后处理 二浴法:浸轧染液→烘干→轧固色液→汽蒸→水洗后处理 ②分散/还原二浴法 染涤:浸轧分散液→烘干→热熔→冷却 染棉:浸轧还原染料悬浮液→烘干→浸轧还原液→汽蒸→水 洗→氧化→皂洗→水洗
- 1、下载文档前请自行甄别文档内容的完整性,平台不提供额外的编辑、内容补充、找答案等附加服务。
- 2、"仅部分预览"的文档,不可在线预览部分如存在完整性等问题,可反馈申请退款(可完整预览的文档不适用该条件!)。
- 3、如文档侵犯您的权益,请联系客服反馈,我们会尽快为您处理(人工客服工作时间:9:00-18:30)。
T/C混纺织物染色综合实验
一、实验内容
1、T/C混纺织物轧--焙法染色
2、T/C混纺织物二步法染色
二、实验目的:学习T/C混纺织物不同工艺染色的方法
三、实验原理
T/C混纺材料的纺织品,在纺织品消耗总量中占很大比例。
由于涤、棉两种纤维性能差异大,染色时要求的pH值、温度不同,染色工艺相对复杂,生产单位还往往根据自己的设备情况,制定工艺。
近年来,性能优良的染料不断问世,使T/C混纺织物染色工艺不断优化。
涤纶是疏水性纤维,结构紧密,使用分散染料染色。
染色须在高温高压(130℃)或热熔培烘(180℃以上)条件下进行。
在高温下,纤维大分子链段振动频率增大,出现了许多允许染料了通过和容纳染料的空隙,温度越高染料扩散越快。
温度降到玻璃化温度以下时,染料分子便固定在纤维中。
棉纤维可以用直接、活性、还原等多种染料染色,染色工艺可以是轧染法和浸染法,常温染色。
选择棉用染料一般根据色相和要求的色牢度、深度而定。
四、实验步骤和工艺条件
(一)、分散活性轧-焙一步法染色
流程
二浸二轧(室温、轧余率60-70%)→烘干(80-90℃)→焙烘(190℃、90s)→热水洗(80℃、5min)→皂洗(皂粉2g/L、95℃、10min)→水洗→烘干
处方
分散红S-BWFL(g/L)24
分散金黄E-RGFL(g/L)16
活性橙KGN(g/L)25
尿素(g/L)50
碳酸钠(g/L)15
JFC(g/L) 2
六偏磷酸钠(g/L)
含固量4%防泳移剂(g/L)15
(二)、两步法染色工艺
1、分散、活性染色工艺
流程
二浸二轧分散染料(室温、轧余率60-70%)→烘干(80-90℃)→焙烘(200℃、60s)→热水洗(80℃、5min)→水洗→烘干→活性套染棉
套染棉工艺
60℃ 15’ 15’20‘
3
分散浴处方:套染棉处方:
分散红玉S-2GFL(g/L)活性红BES (owf%) 3 分散蓝2BLN(g/L)活性蓝BET(owf%) 2 分散青莲S-BLN(g/L) 2 碳酸钠(g/L)20 含固量4%防泳移剂(g/L)15 硫酸钠(g/L)30
六偏磷酸钠(g/L) 2
浴比:1:30
2、分散/还原悬浮体染色工艺
流程:
二浸二轧工作液(室温、轧余率60-70%)→烘干(80-90℃)→焙烘(190℃、90s)二浸二轧浸轧还原液→用薄膜包好→汽蒸(100℃、2min)→水洗→透风氧化→水洗(50-60℃、5min)→皂煮→晾干
处方:还原浴处方:
分散大红HBGL(g/L) 3 氢氧化钠(g/L)20
还原黄RK(g/L)85%保险粉(g/L)20
还原桃红R(g/L)
含固量4%防泳移剂(g/L)15
六偏磷酸钠(g/L) 2
实验注意事项:
1、织物进焙烘机应平整,否则会因泳移而染花。
附:防泳移剂的制备
称取4g的海藻酸钠,边搅拌边撒入40℃的96ml的软化水中,不断搅拌,至无颗粒即成为含固量4%的原糊。