炼油厂应用热管式蒸汽发生器
蒸汽发生器工作原理

蒸汽发生器工作原理蒸汽发生器是一种用于产生蒸汽的设备,通常用于工业生产和发电等领域。
它的工作原理是将水加热至沸点,使其转化为蒸汽。
蒸汽发生器的工作原理涉及热力学和热传递等多个领域的知识,下面将详细介绍蒸汽发生器的工作原理。
首先,蒸汽发生器通常由燃烧室、锅炉管和蒸汽室等部分组成。
在工作时,燃烧室内燃烧燃料,产生高温燃气。
这些燃气通过锅炉管内部流动,使管壁受热,然后传递热量给管内的水。
当水受热后,温度逐渐升高,最终达到沸点,水开始转化为蒸汽。
蒸汽在锅炉管内积聚,并通过管道输送至蒸汽室,最终用于工业生产或发电。
蒸汽发生器的工作原理基于热力学的热传递原理。
燃烧室内的燃料燃烧产生高温燃气,这些燃气通过锅炉管内部流动时,热量会传递给管壁,然后再传递给管内的水。
燃气和水之间的热传递是通过对流和传导来实现的。
对流是指燃气和水之间的热量传递是通过流体流动来实现的,而传导是指热量是通过固体(如管壁)传递给流体(如水)的。
通过这种热传递过程,水的温度逐渐升高,最终达到沸点,转化为蒸汽。
在蒸汽发生器的工作过程中,需要考虑的因素有很多,比如燃料的选择、燃烧室的设计、锅炉管的材质和结构等。
这些因素都会影响到蒸汽发生器的工作效率和安全性。
同时,蒸汽发生器还需要配备一系列的控制系统,用于监测和调节燃料的燃烧、水的供给、蒸汽的排放等,以确保蒸汽发生器的正常运行。
总之,蒸汽发生器的工作原理是通过将水加热至沸点,使其转化为蒸汽。
这一过程涉及热力学和热传递等多个领域的知识,需要综合考虑燃料、燃烧室、锅炉管等因素,以确保蒸汽发生器的高效、安全运行。
希望通过本文的介绍,读者对蒸汽发生器的工作原理有了更深入的了解。
导热油蒸汽发生器工作原理

导热油蒸汽发生器工作原理导热油蒸汽发生器工作原理什么是导热油蒸汽发生器?导热油蒸汽发生器是一种通过导热油将水加热为蒸汽的设备。
它利用导热油的高温传导性能,实现高效、稳定的蒸汽产生。
下面我们来详细了解一下它的工作原理。
导热油蒸汽发生器的工作方式1.导热油循环系统–导热油循环系统由导热油泵、导热油加热器和导热油蒸发器组成。
–导热油泵负责将导热油从加热器中抽出,并将其输送至蒸发器。
–导热油加热器则将来自燃烧器的热能传递给导热油,将其加热至一定温度。
2.蒸发器工作原理–导热油蒸发器是导热油蒸汽发生器的核心部件。
–导热油通过蒸发器内的管道流动,与蒸汽发生器内的水进行热交换。
–在热交换过程中,导热油释放热量,使水温升高并逐渐转化为蒸汽。
–最终,通过蒸汽排放口释放出的蒸汽可供工业生产或其他用途使用。
3.导热油的作用–导热油是导热油蒸汽发生器的关键媒介,起到传热媒介的作用。
–导热油具有较高的热传导性能和热稳定性,能够快速将热能传递给蒸发器内的水。
–导热油能够在高温下稳定工作,不易分解和变质,从而保证工作的可靠性和安全性。
4.控制系统–导热油蒸汽发生器配备了先进的控制系统,用于实时监测和调节设备的运行状态。
–控制系统能够根据需要自动控制导热油的温度、循环速度等参数,确保设备的高效运行。
–同时,控制系统还可以监测设备的故障并自动报警,提高设备的可靠性和安全性。
导热油蒸汽发生器的优势•高效性:导热油的热传导效率高,能够快速将热能传递给水,快速产生蒸汽,提高生产效率。
•稳定性:导热油具有较高的热稳定性,能够在高温下稳定工作,提供稳定的热源。
•安全性:导热油蒸汽发生器可以避免直接接触水和蒸汽,减少烫伤和腐蚀等安全风险。
•环保性:导热油蒸汽发生器可以降低燃煤时的烟气污染和噪音污染,对环境更友好。
综上所述,导热油蒸汽发生器利用导热油的高热传导性能,通过热交换将水加热为蒸汽。
它的高效、稳定和安全的特点,使其在工业生产中得到广泛应用。
蒸汽发生器工作原理

蒸汽发生器工作原理
蒸汽发生器是一种将水转化为蒸汽的设备,其工作原理基于热能传递和相变原理。
下面是蒸汽发生器的工作原理步骤:
1. 加热水:蒸汽发生器通过加热水来产生蒸汽。
水从水源进入发生器,并通过加热元件进行加热。
加热元件可以是燃烧器、电加热管或其他形式的热源。
2. 水受热:加热元件将热能传递给水,使水的温度逐渐升高。
当水温达到100℃时,水开始沸腾并转化为蒸汽。
3. 液态水和蒸汽共存:在蒸汽发生器中,液态水和蒸汽可以同时存在。
液态水位于较低的位置,而蒸汽位于较高的位置。
4. 蒸汽产生:当水沸腾时,产生的蒸汽会上升,并被导入到蒸汽发生器的出口。
蒸汽可以用作能源或热能传递的媒介,用于驱动机械设备、供暖或进行其他工业过程。
5. 残余水排出:蒸汽产生后,水中的溶解气体和固体物质可能会残留在发生器内,它们需要通过排污系统进行处理和排放,以保持蒸汽发生器的正常运行。
蒸汽发生器的工作原理是通过传递热能将水加热,并使其转化为蒸汽。
这种装置广泛应用于发电、工业加热、供暖和其他领域,它在许多工业过程中起着重要的作用。
印染厂锅炉烟气热能利用技术改造方案

印染厂锅炉烟气热能利用技术改造方案纺织染整工业中,蒸汽锅炉被广泛应用。
锅炉烟气直接排放不仅带走大量的热能,造成锅炉热效率下降,对自然环境也会形成热污染。
锅炉中,从炉膛出口流出的烟气向过路的其它换热面传递热量,直到达到锅炉的排烟温度,烟气在锅炉中经历了很大的温度变化。
根据烟气温度高低,分为高温烟气(>600℃)、中温烟气(230-600℃)和低温烟气(<230℃)。
高温烟气温度高,热能较高,容易加以利用,一般应最大限度地将其转化为机械能,用于动力,即所谓的“高质高用”。
中、低温烟气一般需要通过各种热交换设备,将烟气的热能传递给不同的工作介质而加以利用。
1.1蒸汽锅炉参数和烟气工艺流程以印染厂浆染车间为例,型号为SZL6-1.25-WA链条锅炉额定蒸汽蒸发量为10 t/h,额定蒸汽压力为1.25 MPa,烟气温度高达250℃,排烟热损失较大。
1.2余热回收方案热能回收系统主要设备为热管式蒸汽发生器及省煤器。
热管式蒸汽发生器具有传热效率高、结构紧凑、流体阻损小和利于控制露点腐蚀等优点。
热管是其主要的组成部分,具有极高的导热性能,它通过在全封闭真空管内工质的蒸发与凝结来传递热量,管外缠绕高频焊翅片,具有极高的导热性和良好的等温性。
其冷热两侧的传热面积可任意改变,可远距离传热和控制温度。
设备采用对称结构,两侧箱体通过高温烟气,中间设备主体走解析脱氧水。
烟气先从一侧箱体的人口进入,横掠冲刷热管,热量通过热管传递至设备主体,产生的饱和蒸汽进人汽包。
由于热管是单支点焊接,可以自由伸缩,所以不存在温差应力问题。
省煤器处于锅炉尾部烟道中将锅炉给水加热成汽包压力下的饱和水的受热面,由于它吸收的是比较低温的烟气,故降低了烟气的排烟温度,节省了能源,提高了效率。
省煤器的节能原理是增加一个回热过程,提高吸热平均温度,从而提高循环效率。
在锅炉的启动过程中,由于没有建立汽水管道的循环,即锅炉给水处于停滞状态,此时省煤器内的水处于不流动的状态,随着锅炉燃烧的加强,烟气温度提高,省煤器内的水容易汽化,使省煤器局部处于超温状态。
炼油厂常减压蒸馏装置生产原理
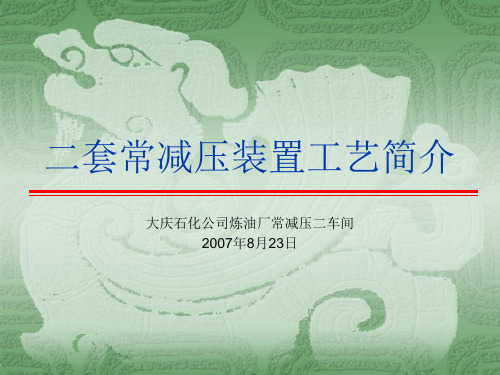
万米罐储存,经8/3#管线由东向西进入装置内泵-1/1.2处。
二套常减压工艺简介
20
原料来源及产品走向产品去向
初顶瓦斯去原油稳定,也可以去F-1作燃料气。 初顶汽油去重整做铂料。 常顶瓦斯去原油稳定,或去F-1低压瓦斯火嘴烧掉。
常顶汽油去88单元进70#管调。不合格进88单元139#、140#、
不足由装置外补给 采用常一中段回流做热源发生压力为0.4MPa的蒸汽
经过加热炉(炉-2)过热到≮360℃
各塔供汽提用
不足由装置外补充供给
本装置发生蒸汽所需的除氧水,在本装置内自设除氧站。
14
二套常减压工艺简介
工艺流程简介装置外输热系统概述
为了进一步回收装置内各侧线油品的低温余热,初馏塔顶及 常四线,减压二,四线及减压渣油等物流都设有采暖水热交换 器
装置的技术改造减压塔改全填料
目的提高装置润滑油料的质量和收率 将精馏段原网孔塔盘及原有规整填料拆除,更换成清华大学 SP系列规整填料
将原有的动力式液体分配器更换成重力式液体分配器
原有的矩鞍环填料利旧,减一及减五线集油箱利旧 提馏段将原有的F1浮阀塔盘更换成清华大学的ADV浮阀塔盘
7
二套常减压工艺简介
装置流程概述
其中常压塔设有一个顶回流,两个中段回流(常一中、 常二中),常底油经过泵-3/1.2 抽出到减压炉加热到 395℃左右后进入减压塔第四层上方,减压塔底吹入蒸 汽。减顶设有两级抽真空系统,减顶油汽经过一级予冷 器和一级抽空器和二级予冷器及二级抽空器,不凝气到 常压炉烧掉,冷却下来的油水经减顶油水分液罐(容-6) 分出的油经泵送出装置,减压塔沿塔壁至上而下依次馏 出减一线、减二线、减三线、减四线、减五线,各侧线 (除减五线)经过气提塔在由各泵抽出到各换热器进行 换热,冷却最后送出装置,减压塔经过泵-21/1.2 抽出。 经过两路换热,一部分热料去重催、焦化,另一部分经 过冷却做冷渣送出装置。
油浆蒸汽发生器内漏原因分析及对策
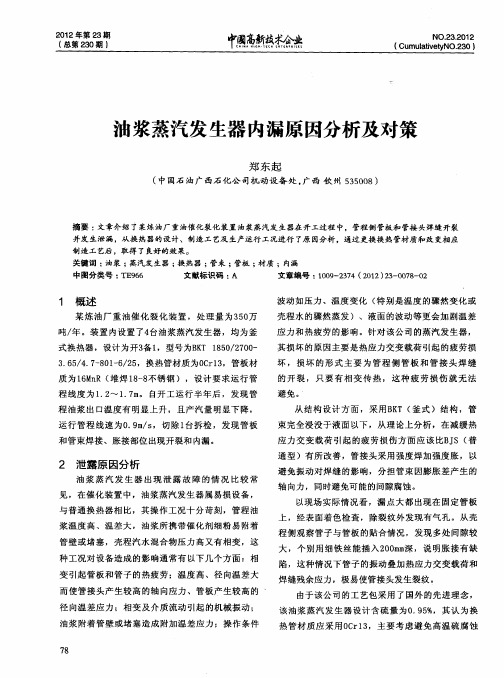
工业 出版 社 。0 6 20.
3 3 2 管 孔 加 工 。管 孔加 工 是 管板 制造 中重 . . 要 的 一个环 节 ,应严格 控制 划线 、钻孔 、刻 槽 、倒
作 者简 介: 东起 ( 9 1 , 山东菏泽人 , 郑 18一)男, 中国石油广
西 石化 公 司机 动 设 备 处设 备 工程 师 , 究 方 向 : 备 管理 。 研 设
见 ,在催化 装置 中 ,油 浆蒸汽 发生器 属 易损 设备 , 与普通 换热 器相 比 ,其 操作工 况十 分苛刻 ,管程 油 浆温 度高 、温差 大 ,油浆所携 带催化 剂细 粉易 附着
管壁 或堵塞 ,壳程汽 水混合物 压力 高又有 相变 ,这
种 工况对 设备造 成 的影响通 常有 以下几 个方面 :相 变 引起管 板和 管子 的热疲 劳 ;温度 高 、径 向温 差大
术难 题 ,极 易产 生裂纹 ,这 种焊 接在 高温 和有疲 劳
的工况 下是 很不 利 的, 国内设计 理念一 般倾 向于 选
用 碳 钢 或 l— 不锈 钢 。 88
板 、管 孔 的加工粗 糙度 和换 热管 的外径尺 寸偏 差应 符 合要 求 ,使 之 间的 间隙符合 制造 标准 , 以免在 焊
1 概述
某 炼 油厂 重 油催 化裂 化 装 置 ,处理 量 为3 0 5 万
吨/ 。装 置 内设 置 了4 年 台油浆 蒸汽发 生器 ,均为 釜 式换热器 ,设计为 开3 ,型号为B T 8 0 2 0 - 备1 K 1 5 / 7 0 36 / .-0 -/ 5 . 5 4 7 8 1 6 2 ,换热管材质 为O r 3 C l ,管 板材 质 为 1 M R ( 焊 1 — 不 锈钢 ),设计 要求 运行 管 6n 堆 88 程 线度 为 1 2 i 7 。 自开工 运行 半年 后 ,发现 管 .~ .m 程 油浆 出 口温度 有 明显上升 ,且产汽 量 明显下 降 , 运 行 管程线 速 为0 9 / ,切 除l .m s 台拆检 ,发 现 管板 和 管束焊接 、胀接 部位 出现 开裂和 内漏 。
石油化工品储罐快速加热技术(二篇)
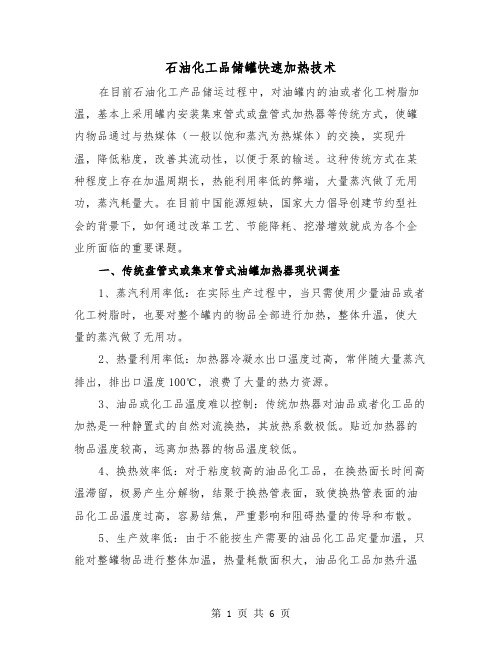
石油化工品储罐快速加热技术在目前石油化工产品储运过程中,对油罐内的油或者化工树脂加温,基本上采用罐内安装集束管式或盘管式加热器等传统方式,使罐内物品通过与热媒体(一般以饱和蒸汽为热媒体)的交换,实现升温,降低粘度,改善其流动性,以便于泵的输送。
这种传统方式在某种程度上存在加温周期长,热能利用率低的弊端,大量蒸汽做了无用功,蒸汽耗量大。
在目前中国能源短缺,国家大力倡导创建节约型社会的背景下,如何通过改革工艺、节能降耗、挖潜增效就成为各个企业所面临的重要课题。
一、传统盘管式或集束管式油罐加热器现状调查1、蒸汽利用率低:在实际生产过程中,当只需使用少量油品或者化工树脂时,也要对整个罐内的物品全部进行加热,整体升温,使大量的蒸汽做了无用功。
2、热量利用率低:加热器冷凝水出口温度过高,常伴随大量蒸汽排出,排出口温度100℃,浪费了大量的热力资源。
3、油品或化工品温度难以控制:传统加热器对油品或者化工品的加热是一种静置式的自然对流换热,其放热系数极低。
贴近加热器的物品温度较高,远离加热器的物品温度较低。
4、换热效率低:对于粘度较高的油品化工品,在换热面长时间高温滞留,极易产生分解物,结聚于换热管表面,致使换热管表面的油品化工品温度过高,容易结焦,严重影响和阻碍热量的传导和布散。
5、生产效率低:由于不能按生产需要的油品化工品定量加温,只能对整罐物品进行整体加温,热量耗散面积大,油品化工品加热升温缓慢,加温时间长,而且油品化工品整体升温分布不均衡。
特别是在冬季生产中,由于受环境温度的影响,加热时间会更长。
6、影响油品化工品质量:油品化工品在长时间、多次反复的加热过程中产生大量细小的分解物,溶于油品化工品中,对质量产生一定的影响,增加了后期处理的成本。
二、解决方案针对上述问题,本着提高生产效率,节能降耗的指导思想,于xx 年2月成立了油罐局部快速加热,提高生产效率,节能降耗攻关小组。
山东普利龙压力容器有限公司、中国石化润滑油济南分公司合作,采用涡流热膜换热器技术(国家专利产品,专利号:02268208.2),成功设计研发出了一款《新型油罐局部快速加热器》(国家专利产品,专利号:xx9405.3),在实际运用中取得了良好效果,节能明显,有效解决了加热过程中能耗过大的弊端,生产效率明显提升,生产运行费用大大降低。
生物质蒸汽发生器的分类

生物质蒸汽发生器的分类生物质蒸汽发生器是一种利用生物质作为燃料产生蒸汽的设备。
根据不同的分类标准,生物质蒸汽发生器可以分为多种类型,包括直接燃烧式生物质蒸汽发生器、气化式生物质蒸汽发生器和液化式生物质蒸汽发生器。
下面将分别介绍这三种类型的生物质蒸汽发生器。
一、直接燃烧式生物质蒸汽发生器直接燃烧式生物质蒸汽发生器是最常见的一种类型。
它通过将生物质直接燃烧产生高温烟气,然后将烟气传热给水,使水蒸发产生蒸汽。
这种类型的生物质蒸汽发生器结构简单,操作稳定可靠。
常见的直接燃烧式生物质蒸汽发生器有固定炉排式、流化床式和倒置炉排式等。
1. 固定炉排式生物质蒸汽发生器:固定炉排式生物质蒸汽发生器采用固定炉排来燃烧生物质,燃烧过程中废气通过炉排从上向下排出。
这种发生器适用于生物质燃烧时产生的灰渣较多的情况。
2. 流化床式生物质蒸汽发生器:流化床式生物质蒸汽发生器采用流化床来燃烧生物质,废气通过流化床上升排出。
流化床可以提供较好的气固两相混合和传热条件,使得燃烧效率更高,废气排放更清洁。
这种发生器适用于生物质燃烧时产生的灰渣较少的情况。
3. 倒置炉排式生物质蒸汽发生器:倒置炉排式生物质蒸汽发生器采用倒置的炉排来燃烧生物质,燃烧过程中废气通过炉排从下向上排出。
这种发生器适用于燃烧生物质时要求燃烧温度高的情况。
二、气化式生物质蒸汽发生器气化式生物质蒸汽发生器是利用生物质进行气化反应产生气体燃料,再将气体燃料燃烧产生蒸汽。
这种类型的生物质蒸汽发生器可以实现高效利用生物质能源,减少污染物排放。
常见的气化式生物质蒸汽发生器有固定床式、流化床式和旋风床式等。
1. 固定床式生物质蒸汽发生器:固定床式生物质蒸汽发生器采用固定床来进行气化反应,将生物质转化为气体燃料。
然后将气体燃料送入燃烧室进行燃烧,产生高温烟气用于蒸汽产生。
2. 流化床式生物质蒸汽发生器:流化床式生物质蒸汽发生器采用流化床来进行气化反应,将生物质转化为气体燃料。
流化床可以提供较好的气固两相混合和传热条件,使得气化效率更高。
蒸汽发生器工作原理
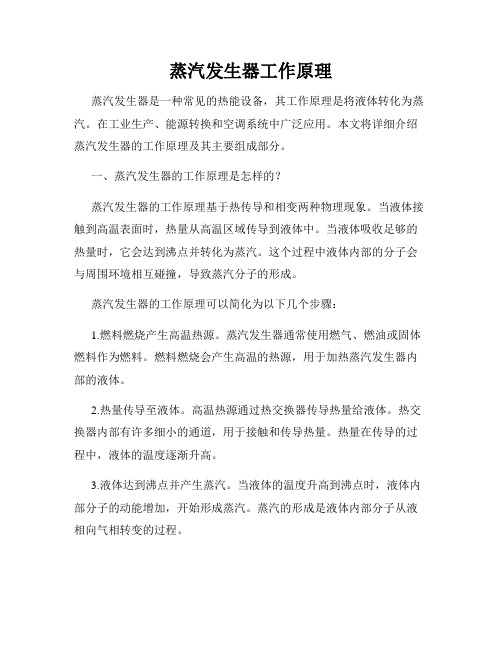
蒸汽发生器工作原理蒸汽发生器是一种常见的热能设备,其工作原理是将液体转化为蒸汽。
在工业生产、能源转换和空调系统中广泛应用。
本文将详细介绍蒸汽发生器的工作原理及其主要组成部分。
一、蒸汽发生器的工作原理是怎样的?蒸汽发生器的工作原理基于热传导和相变两种物理现象。
当液体接触到高温表面时,热量从高温区域传导到液体中。
当液体吸收足够的热量时,它会达到沸点并转化为蒸汽。
这个过程中液体内部的分子会与周围环境相互碰撞,导致蒸汽分子的形成。
蒸汽发生器的工作原理可以简化为以下几个步骤:1.燃料燃烧产生高温热源。
蒸汽发生器通常使用燃气、燃油或固体燃料作为燃料。
燃料燃烧会产生高温的热源,用于加热蒸汽发生器内部的液体。
2.热量传导至液体。
高温热源通过热交换器传导热量给液体。
热交换器内部有许多细小的通道,用于接触和传导热量。
热量在传导的过程中,液体的温度逐渐升高。
3.液体达到沸点并产生蒸汽。
当液体的温度升高到沸点时,液体内部分子的动能增加,开始形成蒸汽。
蒸汽的形成是液体内部分子从液相向气相转变的过程。
4.蒸汽被抽出。
蒸汽通过蒸汽出口被抽出蒸汽发生器。
蒸汽可以用于推动涡轮机、驱动发电机产生电能,或者作为热源供给工业生产或建筑物的空调系统等。
二、蒸汽发生器的主要组成部分蒸汽发生器通常由以下主要组成部分构成:1.燃烧室:用于燃料的燃烧,产生高温热源。
2.热交换器:负责将燃烧产生的热量传导给液体,并将液体加热至沸点。
3.水箱:用于存储和补充液体,保证蒸汽发生器的稳定运行。
水箱通常位于蒸汽发生器的下部。
4.蒸汽出口:通过蒸汽出口将产生的蒸汽抽出。
5.控制系统:用于监测和控制蒸汽发生器的温度、压力和流量等参数,以确保安全运行和高效工作。
三、蒸汽发生器的应用领域蒸汽发生器在各个领域都有广泛的应用,以下是一些常见的应用领域:1.能源转换:蒸汽发生器通常与涡轮机和发电机相结合,用于发电生产。
当蒸汽驱动涡轮机旋转时,涡轮机会带动发电机发电。
2.工业生产:蒸汽可作为热源用于工业过程,如纸张制造、化工生产和石油精炼等。
蒸汽发生器的工作原理

蒸汽发生器的工作原理
蒸汽发生器是一种用于产生高温高压蒸汽的设备,主要应用于工业生产、发电和加热等领域。
其工作原理主要包括以下几个步骤:
1. 蒸汽发生器的工作开始于给水系统,给水通过给水泵进入蒸汽发生器,供应给发生器中的蒸汽产生部分。
2. 经过进水阀的控制,给水进入蒸汽发生器的锅炉筒体内部。
进入筒体的给水将通过下部的燃烧室。
3. 燃烧室中的燃料(可以是煤、油或天然气等)在点火系统的作用下燃烧。
燃料燃烧产生的高温气体通过锅炉的加热面将水加热,在加热的过程中,水逐渐转化为蒸汽。
4. 系统中的排烟管道将燃烧后的废气排出,以保持锅炉的正常工作环境。
5. 锅炉内壁上覆盖着许多加热面,这些面积较大的金属管材能够更好地吸收燃料燃烧产生的热量。
热量的传递使得加热面的温度升高,将水中的热量逐渐传导到水中。
6. 经过加热的水在锅炉内部升温,当温度足够高时,水开始沸腾并逐渐转化为蒸汽。
蒸汽通过锅炉筒体的蒸汽出口进入下一个使用环节,如涡轮机或加热设备等。
7. 蒸汽发生器设备中还配备了安全阀和水位控制系统等安全保
护措施,以保证设备的安全运行。
综上所述,蒸汽发生器的工作原理主要依靠燃料燃烧产生的高温气体传递热量给水,在锅炉内部将水加热转化为蒸汽,实现对应用领域的蒸汽供应需求。
热效率及运行安全

(4)采用烟气余热锅炉以发生蒸汽。
有些加热炉如连续重整的四合一重整炉,热负荷很大,为了减少 压降又不能在对流室排炉管,只能将对流室作为烟气余热锅 炉。再如制氢装置的转化炉,其转化反应只能在辐射室的转 化管内进行,热负荷相当大,烟气出辐射室的温度也比一般 加热炉高得多,对流室仅靠预热原料气远不能将烟气温度降 下来,也只能采用烟气余热锅炉。最近设计的煤炼油的煤浆 炉只有辐射室,烟气热量只能靠余热锅炉回收。大型化的加 氢反应炉也是一样。虽然一般炼油厂并不缺少蒸汽,但对于 这样的炉子也只能采用余热锅炉来回收烟气余热,产生的蒸 汽并入管网,使得全厂蒸汽过剩,只能停掉一些蒸汽锅炉来 平衡。让这些炉子少产或不产蒸汽,是设计者多年来追求的 目标。后面将要介绍的“蓄热式高温空气贫氧燃烧技术” 如 果应用到炼油管式炉上,前述问题可能得到解决,实现少产
ηr--散热损失占燃料低发热量的百分率,一般取1.5%~2.5%。当 用于估算、或空气不预热以及燃烧空气为燃气轮机高温尾气等 情况下,可认为ηr是散热损失占总供给热量的百分数,也就可 以按(3)式的后半部分计算:
qs--排烟损失,kJ/kg燃料,包括烟气离开热平衡体系带走 的显热和不完全燃烧的化学热。由于加热炉的燃烧都比较完全, 一般不计不完全燃烧损失。在现场难以进行详细计算时,可根 据过剩空气系数和排烟温度从下图查得排烟损失与燃料低发热
单位时间的输入能量=单位时间的输出能量
QGG=QYX +QSS ⑴
式中 QGG--单位时间的供给能量,MW; QYX--单位时间的有效能量,MW; QSS--单位时间的损失能量,MW。
蒸汽发生器的工作原理

蒸汽发生器的工作原理
蒸汽发生器是一种用于产生蒸汽的设备,它的工作原理是将液体转化为蒸气。
通常情况下,蒸汽发生器是通过加热液体来生成蒸汽的。
蒸汽发生器包含一个热源,它可以是燃气、燃油或电力。
当热源启动时,它会加热蒸汽发生器中的液体。
这种液体可以是水,也可以是其他液体,如燃料油或溶剂。
当液体开始加热时,它的温度逐渐升高。
一旦液体达到其沸点温度,它会开始蒸发,并释放出蒸汽。
蒸汽发生器内部通常有一个导流系统,它有助于将液体和蒸汽分离。
当液体蒸发时,蒸汽会向上升腾,并通过导流系统进入蒸汽管道。
导流系统还有助于防止液体被带入蒸汽管道,从而保持蒸汽的纯净性。
在蒸汽管道中,蒸汽被输送到需要蒸汽的设备或系统中,如汽轮机、加热系统或工业生产过程中的其他设备。
在这些设备中,蒸汽的能量可以被利用,以产生动力、供暖或执行其他工艺操作。
同时,蒸汽发生器通常还配有安全装置,以确保在出现异常情况时能够保持安全运行。
这些安全装置可以包括压力控制阀、温度传感器和紧急停机装置等,它们可以监测和控制蒸汽发生器的压力和温度,并在需要时自动停机或释放过多的蒸汽,以保护设备和操作人员的安全。
总的来说,蒸汽发生器的工作原理是通过加热液体来产生蒸汽,并将蒸汽输送到需要蒸汽的设备或系统中。
通过合理的控制和安全装置,蒸汽发生器可以稳定、高效地工作,满足不同的工业和商业需求。
炼油厂管式加热炉
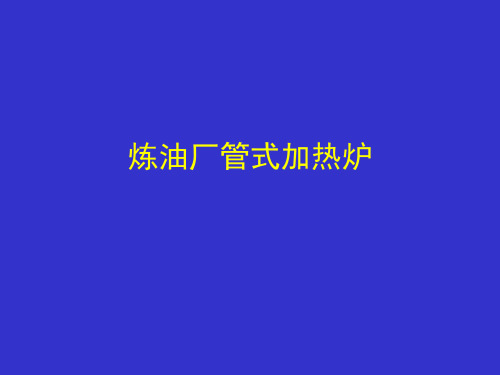
烟气露点腐蚀
烟气露点腐蚀主要和使SO2转化成SO3的因素有关, 和总硫关系不大。建议最低金属温度
金属温度 0C 177
149 121 93
66
1.0
2.0
3.0
4.0
5.0
燃料含硫%W
API 560-95
烟气露点腐蚀影响因素(和氧化氮相似) l 燃料含硫量 l 燃料和烟气添加剂(喷氨或氧化镁) l 烟气氧含量 l 烟气水分含量 l 燃烧温度(燃料流量) l 炉子清洁度 l 燃烧器设计(烟气内循环25%,SO3 减少一 半 露点温度相当6℃ 减少腐蚀1/3)
API 560-95
炉墙 陶纤材料:用于热面最小厚度25毫米,密度大于 128KG/M3针刺材料; 用于耐热层最小厚度38 毫米,密度大于240KG/M3纤维板; 用于背层 密度大于96KG/M3纤维板 烟气流速 : .>12.2M/S不用于耐热层 12.2M/S-24.4M/S 热面层用湿毯 >24.4M/S 热面层不能用陶纤材料 腐蚀 : 燃料含硫大于10PPM 壳体表面涂耐温 度177℃涂料; 燃料含硫大于500PPM 用188(304) 薄板作水汽保护隔板(在设计计算露点 高56℃位置)
积灰
项 目 松散性积灰 粘结性积灰
形成机理
产生场合 积灰分布形成 积灰特征 烟气流速影响
分子引力及静电作 用
固体、气体燃料炉 及过程流体 主要在管子的背面 有脱落的可能 速度增加积灰减少
分子间较强的粘结作 用
燃烧不充分的燃油及 过程粘性流体 主要在管子的正面 有无限生长的趋势 速度增加积灰加剧
流体阻力
积灰的清除
阻力增加缓慢
容易
阻力增加较快
困难
吹灰器
印染厂生物质蒸汽发生器工作原理

印染厂生物质蒸汽发生器工作原理生物质蒸汽发生器是一种利用生物质燃料进行燃烧,产生热能并将其转化为蒸汽能的装置。
生物质蒸汽发生器的工作原理如下:1.燃料供给:生物质蒸汽发生器首先将生物质燃料送入燃料供给系统中,燃料可以是各种形式的生物质,如木屑、秸秆、锯末等。
2.燃烧过程:生物质燃料在燃烧室中进行燃烧过程。
燃烧室通常采用颗粒流化床燃烧技术,即燃烧室中的燃烧床是由燃烧过程中的燃料颗粒悬浮在燃烧空气中的。
通过加热风机或气体喷嘴将适量的氧气和燃料送入燃烧室,燃烧反应在高温下进行,产生大量热能。
3.烟气处理:随着生物质的燃烧,燃烧室产生的烟气包括各种气体(如CO2、CO、NOx等)和颗粒物。
这些烟气需要经过除尘器、脱硫装置等进行处理,以确保排放的烟气符合环保排放标准。
4.热能传输:生物质蒸汽发生器通过燃烧过程产生的高温烟气,通过烟气余热回收系统,将烟气余热传输给水,使水变为高温和高压的蒸汽。
5.蒸汽生成:烟气余热传输给水后,水在锅炉中受热蒸发,产生高温和高压的蒸汽。
蒸汽可用于各种工业应用,如发电、供热和驱动等。
6.蒸汽处理:产生的蒸汽需要送入蒸汽处理装置中进行后续处理,包括蒸汽过滤、除尘、脱硫、脱碱等步骤,以确保蒸汽的纯净性和质量。
7.燃料灰渣处理:生物质燃烧过程中的灰渣需要进行处理。
灰渣通常包括飞灰和底渣两种类型,飞灰通过除尘器进行回收利用,而底渣则需要进行固体废物处理。
总结起来,生物质蒸汽发生器主要通过燃烧生物质燃料产生高温烟气,利用烟气余热回收系统将烟气余热传输给水,使水变为高温和高压的蒸汽。
这样产生的蒸汽可以用于各种工业应用。
生物质蒸汽发生器的工作原理主要包括燃烧过程、烟气处理、热能传输、蒸汽生成、蒸汽处理以及燃料灰渣处理等步骤。
油浆蒸汽发生器泄漏原因分析及预防措施

成分符台 J/r 7 6 _0《 力窑器用碳索钢和低台 n .42 2 川
盒锕锻件》的要求,从Ni u管板材质是台格的 i ̄ E
管 扳上分别取金相试样.经磨光、抛光,侵蚀 后.在台 显做镜下对其显做组织进行分析.断J 表面 I 颜色版晴 曾板中存在带状组织和夹杂物,无明显塑性 变形 .为瞻性断裂 在管 热影响区有多箫脚蚀{ 句,说 叫裂纹形成后.腐蚀介质对裂纹有冲击腐蚀的作用.隧
下 良好基础。定位 孔 的 深浅 要 适宜 ,过浅 会 使 中心 移
磨后,管口外表面不得有纵向刀痕及影响胀接的棱角和
不 圆度 。
焊前用丙酮彻底清理接头坡 I处铁锈、油污等杂 : 1 质,并进行 1 %渗透检查 ,焊接工作应委托责任心强 0 0 和操作技术高的焊工, 采取小电流、快速焊的工艺进行 焊接,管头伸出高度为 3 m m 。 ()加大换热管直径 在加工管板孔时,采用不同 5
直径的扩孔 钻分几 次加工 管孔 ,这样 可增 加钻头 刚度 ,
位; 过深如中心不准确时修改困难,其深度和直径 由管 孔的直径决定。操作工为提高生产效率采用摇臂钻床, 大的切削进给量,势必造成孔桥宽度偏差加大和表面粗
糙度超差 ,致使换热管胀接处泄漏率增大。 ()管子与管板的焊 接 是油 浆蒸汽发生 器管束加 5 工的重要结构部分 ,工作量大 且要求焊工 责任心强 , 而 且在设备的运行中, 必须保证连接处介质无泄漏且具有承 受介质压力的能力。有的焊工为赶生产进度采取大热输入
( 1管扳的化学成分和金相分析 在瞥板 ( 2 毖层)
裂毁皿 取样 j行 化学 成分 分析 .结 果管 板材 料 的化 学 £
蒸汽发生器结构

蒸汽发生器结构
蒸汽发生器是一种将水转化为蒸汽的设备,广泛应用于工业、农业、
医疗等领域。
其结构主要包括以下几个部分:
1. 炉膛:炉膛是蒸汽发生器的核心部分,用于燃烧燃料产生热能,将
水加热转化为蒸汽。
炉膛通常由炉壁、炉排、燃烧室、烟道等组成,
不同类型的蒸汽发生器炉膛结构也有所不同。
2. 水箱:水箱是蒸汽发生器中储存水的部分,通常位于炉膛下方。
水
箱的大小和形状根据蒸汽发生器的规格和使用需求而定,一般分为上
水箱和下水箱两种。
3. 管束:管束是蒸汽发生器中传递热量的部分,通常由多根管子组成。
管束的材质和数量也根据蒸汽发生器的规格和使用需求而定,一般分
为水管式和火管式两种。
4. 烟囱:烟囱是蒸汽发生器中排放烟气的部分,通常位于炉膛上方。
烟囱的高度和直径根据蒸汽发生器的规格和使用需求而定,一般要求
排放的烟气不会对环境造成污染。
5. 控制系统:控制系统是蒸汽发生器中控制温度、压力、水位等参数
的部分,通常由传感器、控制器、执行器等组成。
控制系统的稳定性和精度对蒸汽发生器的安全性和效率有着重要的影响。
以上是蒸汽发生器的主要结构内容,不同类型的蒸汽发生器在结构上也有所不同。
在使用蒸汽发生器时,需要根据具体情况选择合适的类型和规格,并按照操作规程进行操作和维护,以确保蒸汽发生器的安全和稳定运行。
炼油厂装置生产原理及工艺流程讲解
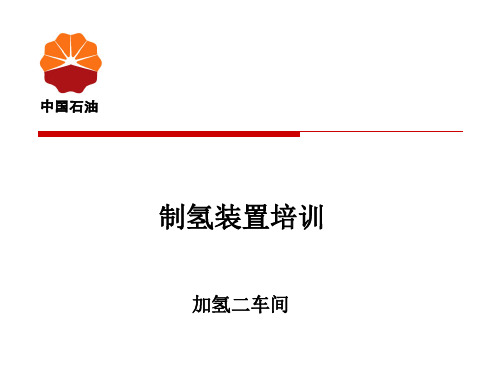
CO+H2O→CO2+H2 上述变换气经过提纯即可得到较纯净的氢气。 这种工艺路线的原料价格比较便宜,但是工艺流程复杂, 生产条件苛刻,产氢率低,投资大,危险程度高,能耗高, 因而在制氢生产中很少采用,但在将来石油资源枯竭的时 候,它可以作为一种炼厂气制氢的替代方案使用。
大庆石化公司
生产方法及反应机理
大庆石化公司
二、生产方法及反应机理
氢气的工业制法 目前,氢气的工业制法主要有如下几种: (1)电解法 用直流电电解15-20%氢氧化钠或氢氧化钾溶液,在阴极上放出氢气, 在阳极上放出氧气。 阴极:2H++2e-→H2↑ 阳极:4OH--4e-→2H2O+O2↑ 阴极上产生的氢气纯度为99.5~99.9%。另外电解食盐溶液制备氢 氧化钠时,氢气是重要的副产品。由于电解法制得的氢气比较纯净, 所以工业上氢化反应用的氢常通过电解法制得。但是由于该方法所制 得的氢气造价很高,因而不适用于工业大规模的制氢生产。
制氢装置培训
加氢二车间
目录
一、装置简介 二、生产方法及反应机理 三、工艺技术路线及流程 四、装置技术经济水平 五、装置开停工操作 六、装置改造项目及节能效果 七、生产中存在的问题及解决措施
- 1、下载文档前请自行甄别文档内容的完整性,平台不提供额外的编辑、内容补充、找答案等附加服务。
- 2、"仅部分预览"的文档,不可在线预览部分如存在完整性等问题,可反馈申请退款(可完整预览的文档不适用该条件!)。
- 3、如文档侵犯您的权益,请联系客服反馈,我们会尽快为您处理(人工客服工作时间:9:00-18:30)。
余热回收工程一、锅炉烟气余热回收简介:工业燃油、燃气、燃煤锅炉设计制造时,为了防止锅炉尾部受热面腐蚀和堵灰,标准状态排烟温度一般不低于180℃,最高可达250℃,高温烟气排放不但造成大量热能浪费,同时也污染环境。
热管余热回收器可将烟气热量回收,回收的热量根据需要加热水用作锅炉补水和生活用水,或加热空气用作锅炉助燃风或干燥物料。
节省燃料费用,降低生产成本,减少废气排放,节能环保一举两得。
改造投资3-10个回收,经济效益显著。
(一)气—气式热管换热器(1)热管空气预热器系列应用场合:从烟气中吸收余热,加热助燃空气,以降低燃料消耗,改善燃烧工况,从而达到节能的目的;也可从烟气中吸收余热,用于加热其他气体介质如煤气等。
设备优点:*因为属气/气换热,两侧皆用翅片管,传热效率高,为普通空预器的5-8倍;*因为烟气在管外换热,有利于除灰;*因每支热管都是独立的传热元件,拆卸方便,且允许自由膨胀;*通过设计,可调节壁温,有利于避开露点腐蚀结构型式:有两种常用的结构型式,即:热管垂直放置型,烟气和空气反向水平流动,见图1;热管倾斜放置型,烟气和空气反向垂直上下流动,见图2。
(二)气—液式热管换热器应用场合:从烟气中吸收热量,用来加热给水,被加热后的水可以返回锅炉(作为省煤器),也可单独使用(作为热水器),从而提高能源利用率,达到节能的目的。
设备优点:*烟气侧为翅片管,水侧为光管,传热效率高;*通过合理设计,可提高壁温,避开露点腐蚀;*可有效防止因管壁损坏而造成冷热流体的掺混;结构型式:根据水侧加热方式的不同,有两种常用的结构型式:水箱整体加热式(多采用热管立式放置)和水套对流加热式(多采用热管倾斜放置),如图3所示(三)气—汽式热管换热器应用场合:应用热管作为传热元件,吸收较高温度的烟气余热用来产生蒸汽,所产生的蒸汽可以并倂入蒸汽管网(需达到管网压力),也可用于发电(汽量较大且热源稳定)或其他目的。
对钢厂,石化厂及工业窑炉而言,这是一种最受欢迎的余热利用形式。
设备优点:每支热管都是一个独立的传热单元,可根据不同的温度水平而设计;*根据需要可选择易拆卸的热管结构,使检修和安装更方便;*热管彻底隔离了热源和冷源,不会产生冷热流体的掺混;*烟气侧为管外换热,除灰容易。
结构型式:有两种结构型式,见图a和图b。
图a为汽包内直接沸腾式,即热管的冷却段直接伸入汽包内,使汽包内的水产生沸腾;图b为套管内沸腾式,即热管的冷却段被水套管包围,使套管内的水在流动状态下沸腾,所产生的蒸汽再汇入汽包。
二、陶瓷窑炉余热回收简介:生产陶瓷的一个重要过程是烧成,烧成是在窑炉中进行的。
陶瓷生产的窑炉有连续式的(隧道窑)也有间隙式的(倒焰窑),不管是隧道窑还是倒焰窑,其热效率都比较低。
效率低的原因除了燃烧损失、散热损失等原因外,重要的一点是排烟损失。
烧成隧道窑废气带走的热量损失约占总热量的20%~40%,而倒焰窑废气带走的热量约占燃料消耗量的30%~50%。
因之回收窑尾废气的热量加以利用是提高窑炉效率的关键。
国内隧道窑排烟温度一般在200~300℃,也有高达400℃,个别倒焰窑的排烟温度可高达560℃。
一方面窑炉排烟带走大量余热,另一方面为了干燥坯件,一些工厂又另外建造窑炉或锅炉产生热风和蒸汽以满足烘干坯件的要求。
采用热管换热器来回收烟气中的余热加热空气作为烘干坯件的热源,可以取得较好的节能效果。
隧道窑烟道气余热利用:隧道窑余热回收主要用以加热空气作为烘干坯件的热源,也可作为助燃空气以提高窑炉本身的热效率,两者的选择可依据各工厂具体情况而定。
其回收流程下图所示。
电瓷厂隧道窑冷却带余热利用:将电瓷厂隧道窑冷却带400℃~450℃的废气抽出通过热管换热器换热,烟气温度降至300℃,再返回窑炉中烧成带作为气氛膜风使用。
被加热的新鲜空气送入烘房,干燥电瓷坯件。
倒焰窑烟道气余热利用:某厂倒焰窑排烟温度为564℃,实测该窑炉热效率仅为23%,由于坯件入窑前需要预热烘干,因之需再建一个烘干窑,以煤作为燃料,燃烧的烟气作为烘干热源。
根据计算,如将560℃烟气降到160℃排空,将新鲜空气加热到60~120℃,其热量足够烘干坯件所用。
三、水泥工业余热回收简介:在水泥生产中,回转窑、冷却机、悬浮预热器、烘干机等都是重要的热工设备。
在保证满足工艺条件要求的基础上,提高这些热工设备的热效率是水泥生产节能降耗的关键。
根据近年来工业应用开发的实践,热管技术在以下几方面已获得了较为成功的应用。
窑尾冷却机的余热利用:水泥生产回转窑尾冷却机低温段排出的废气温度一般为200~300℃,这部分余热的品位较低,它的最好用途是产生低压蒸汽,作为生活用水,冬天用来取暖和浴室用水;夏天可作为溴化锂制冷机的热源制取冷气供生产车间及生活区降温,或作为其他工段余热锅炉的换热器加热锅炉给水。
小水泥窑尾废气余热利用:许多小水泥厂的烧成回转窑窑尾排出的废气温度在450~600℃左右,由于产量较小,废气量也比较少,一般均将回收的余热产生压力为0.3~0.8MPa的低压蒸汽供生产工艺或者说生活使用。
从干法中空回转窑尾排出的废气经过旋风除尘后进入热管蒸汽发生器,废气温度从600℃左右降至200℃以下,入布袋收尘系统,经引风机排入烟囱。
其优点是:◇将高温废气降至200℃以下,可直接进入布袋收尘器;◇每吨熟料可回收0.4~0.5吨的低压蒸汽;◇结构紧凑压力降小,一般小于500Pa;◇不易积灰,管壁温度可调整在烟气露点以上,可以达到自清灰目的。
大型窑尾废气的余热利用:水泥生产中锻烧熟料的回转窑窑尾废气排出的温度一般在900~1000℃左右,每吨熟料废气量约为(标准状态)1.658 m3。
该废气的主要用途一般用作悬浮物预热器的热源,预热入窑的生料粉;另一种用途是与窑尾冷却机的热空气混合进入窑外分解的分解炉;也有将窑尾废气用于发电等其他用途。
水泥旋窑窑体表面的余热回收:水泥旋窑工作时烧成段窑体表面温度达300-350℃,目前都采用风冷降温,大量的热能直接散发到大气中,这不仅浪费了大量的热能,也造成了窑体周围的高温污染。
窑体表面散失的热能是可以回收利用的,我公司研制开发了集热式窑体表面余热回收系统。
根据企业的需要,将回收的热能加热水或空气,热水可供生活和制冷,热空气可供烘干用。
既能降低窑体温度又节省了加热水或空气所需的燃料费、风扇电费,减少粉尘和二氧化碳排放。
节能环保一举两得,改造投资一年内可以全部收回,经济效率十分显著。
四、冶金工业余热回收简介:冶金工业是耗能大户,不论是有色冶金或黑色冶金工业都存在大量的节能问题。
以钢铁企业为例,焦炉、高炉及炼钢工序均有相当数量的的余热未能回收利用。
余热的温度最高可达1600℃,热能的形态有固体、气体、液体,其中很多为间隙排放,因之给余热回收带来了一定的难度。
由于热管的的众多特点,特别适用于上述场合的余热回收利用。
高温热管及高温热管空气预热器、高温热管蒸汽发生器开发运用成功,给冶金企业的高品位余能利用带来了新的希望。
加热炉和均热炉的余热利用:轧钢连续加热和均热炉是钢铁企业中耗能较多的设备。
其热效率一般只有20%~30%,约有70%~80%的热量散失于周围环境和被排烟带走。
其中烟气带走的热损失约占30%~35%。
加热炉的烟气量根据炉型大小不同,一般在(标准状态)7000~300000m3/h的范围内。
烟气温度一般为550~990℃,也有超过100 0℃以上的。
从直接节能来考虑,工程界希望将烟气的余热用来加热助燃空气。
当助燃空气被加热到400℃时,可以得到节能20%~25%的效果。
线材退火炉的余热回收下图所示一线材退火炉,炉内温度为1000℃左右,排烟温度约800℃,在烟道中放置一高温热管空气预热器,高温烟气通过热管换热器热管的蒸发段,烟气降至150~170℃排空。
20℃的常温空气通过换热器热管的冷凝段,被加热到40 0~500℃,作为助燃空气进入燃烧喷嘴。
应用结果表明,节约燃料可达23%。
轧钢连续加热炉的余热回收轧钢连续加热炉排出的烟气温度很高,有时可达1000~1100℃,余热回收利用的方式首推采用空气预热器。
回收的余热,除了热损失可以百分之百地用于燃烧炉内,不仅节约燃料而且可以改善燃烧效果。
但常规的空气预热器体积庞大,所以许多工厂采用了余热锅炉的办法来回收余热产生蒸汽。
这样虽然可以达到节能的目的,但不能直接节约燃料,也得不到由于燃烧条件改善而对产品产量质量方面带来的好处。
当前很多工厂采用余热锅炉和空气预热器相结合的办法来达到兼顾的目的。
烧结工序的余热利用:烧结工序是高炉矿料入炉以前的准备工序。
有块状烧结和球团状烧结两种工艺。
块状烧结是将不能直接加入炉的炼铁原料,如精矿粉、高炉炉尘、硫酸渣等配加一定的燃料和溶剂,加热到1300~1500℃,使粉料烧结成块状。
球团烧结则是将细磨物料,如精矿粉配加一定的黏结剂,在造球设备上滚成球,然后在烧结设备上高温烧结。
两种烧结过程都要消耗大量的能源。
据统计,烧结工序的能耗约占冶金总能耗的12%。
而其排放的余热约占总能耗热能的49%。
回收和利用这些余热,显然极为重要。
烧结工序内废气温度分布示意图如下图。
回收余热主要在成品显热及冷却机的排气显热两个方面。
烧结余热回收的应用流程如下图所示:高炉热风炉余热回收:高炉热风炉是产生热风的设备,由于风温可高达1200℃以上,因之热风炉都是蓄热式。
其工作原理是先使煤气和助燃空气在燃烧室燃烧,燃烧生成的高温烟气进入蓄热室内的格子砖加热,然后停止燃烧,再将鼓风机送来的冷空气通过蓄热式格子砖,将格子砖所积蓄的热量带走,冷空气被加热到所需的温度进入高炉。
热风炉烟道废气的温度一般限制在300~350℃,最高不得超过400℃。
使用热管换热器回收的这部分余热,用来加热助燃空气则可以改善蓄热炉内的燃烧状况,从而使炉顶温度提高。
对于以煤气为燃料的单位,一般多采用分离式热管换热器回收排烟余热,回收的余热同时用来加热空气和煤气,因之称为“双预热”。
五、玻璃窑炉余热回收简介:玻璃生产过程中,从池窑蓄热室、换热室(或换热器)出来的烟气一般在500℃以下。
这些烟气可以通过热管余热锅炉来产生蒸汽。
蒸汽可用于加热和雾化重油、管道保温,以及生活取暖等。
对于排烟量较大,温度较高的烟气,可通过热管余热锅炉产生较高压力的蒸汽(3.5MPa)用于蒸汽透平来发电,或者直接驱动透平空压机、风机、水泵等机械。
对于从工作池和供料道等处排出的烟气,气量少而温度高,可以采用少量的高温热管(工作温度>650℃)来预热空气,当离炉烟气温度为1000~1200℃,空气预热温度可达400~500℃,节油效果可达2 0%。
在退火炉烟气的烟道中,以及退火炉缓冷带以后的部位都可以设制热管换热器以回收烟气的余热和玻璃制品的散热量来预热空气,作为助燃空气、干燥热源或车间取暖等的热源,都可以获得很好的节能效果。