汽车变速器 计算参考共17页
变速器的设计计算
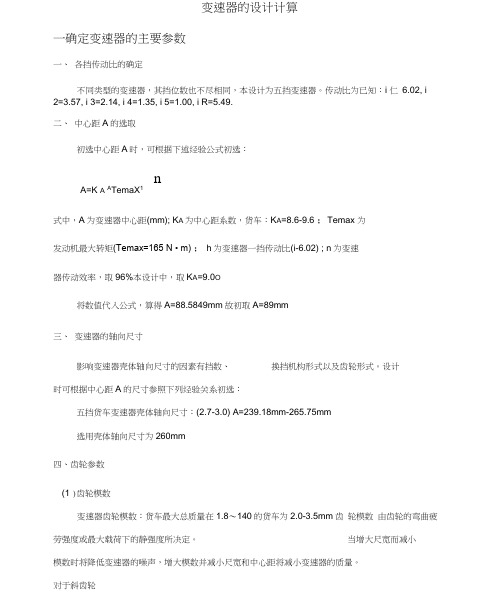
变速器的设计计算一确定变速器的主要参数一、各挡传动比的确定不同类型的变速器,其挡位数也不尽相同,本设计为五挡变速器。
传动比为已知:i 仁6.02, i 2=3.57, i 3=2.14, i 4=1.35, i 5=1.00, i R=5.49.二、中心距A的选取初选中心距A时,可根据下述经验公式初选:nA=K A A TemaX1式中,A为变速器中心距(mm); K A为中心距系数,货车:K A=8.6-9.6 ;Temax 为发动机最大转矩(Temax=165 N • m) ; h为变速器一挡传动比(i-6.02) ; n为变速器传动效率,取96%本设计中,取K A=9.0O将数值代入公式,算得A=88.5849mm故初取A=89mm三、变速器的轴向尺寸影响变速器壳体轴向尺寸的因素有挡数、换挡机构形式以及齿轮形式。
设计时可根据中心距A的尺寸参照下列经验关系初选:五挡货车变速器壳体轴向尺寸:(2.7-3.0) A=239.18mm-265.75mm选用壳体轴向尺寸为260mm四、齿轮参数(1 )齿轮模数变速器齿轮模数:货车最大总质量在1.8〜140的货车为2.0-3.5mm齿轮模数由齿轮的弯曲疲劳强度或最大载荷下的静强度所决定。
当增大尺宽而减小模数时将降低变速器的噪声,增大模数并减小尺宽和中心距将减小变速器的质量。
对于斜齿轮m n-K {"Temax式中m n........... 齿轮横数mmK m——为模数系数,一般K m=0.28-0.37o本设计中取K m=0.35o将数值代入计算得mn=1.919mm5取g =2。
对于直齿轮m=Kn 3 J式中m ........... —挡齿轮模数mmK m i ------------ 挡齿轮模数系数,一般K m i =0.28-0.37o本设计中取K m i =0.30Tl --------- 挡输出转矩,Tl=Temax*i 1i 1 --------- 挡传动比当数值代入计算得m=2.993 mm取m=3参考国标(GB1357-87规定的第一系列模数:一档和倒挡的模数:m= 3mm二,三,四,五挡的模数:叫=2mm;(2) 压力角齿轮压力角较小时,重合度较大并降低了轮齿刚度,为此能减少进入啮合和退出啮合时的动载荷,使传动平稳,有利于降低噪声;压力角增大时,可提高齿轮的抗弯强度和表面接触强度。
变速箱计算

第四节变速器的设计与计算一、齿轮的损坏形式变速器齿轮的损坏形式主要有三种:轮齿折断,齿面疲劳剥落(点蚀),移动换挡齿轮端部破坏。
轮齿折断发生在两种情况下:轮齿受到足够大的冲击载荷作用,造成轮齿弯曲折断;轮齿在重复载荷作用下,齿根产生疲劳裂纹,裂纹扩展深度逐渐加大,然后出现弯曲折断。
前者在变速器中出现得极少,而后者出现得多些。
轮齿工作时,一对齿轮相互啮合,齿面相互挤压,这时存在于齿面细小裂缝中的润滑油,油压升高,并导致裂缝扩展,然后齿面表层出现块状剥落而形成小麻点,称之为齿面点蚀。
它使齿形误差加大,产生动载荷,并可能导致轮齿折断。
用移动齿轮的方法完成换挡的低挡和倒挡齿轮,由于换挡时两个进入啮合的齿轮存在角速度差,换挡瞬间在轮齿端部产生冲击载荷,并造成损坏。
二、轮齿强度计算与其它机械行业比较,不同用途汽车的变速器齿轮使用条件仍是相似的。
此外,汽车变速器齿轮用的材料、热处理方法、加工方法、精度级别、支承方式也基本一致。
如汽车变速器齿轮用低碳合金钢制作,采用剃齿或磨齿精加工,齿轮表面采用渗碳淬火热处理工艺,齿轮精度为JBl79—83,6级和7级。
因此,用于计算通用齿轮强度公式更为简化一些的计算公式来计算汽车齿轮,同样可以获得较为准确的结果。
下面介绍的是计算汽车变速器齿轮强度用的简化计算公式。
1、轮齿弯曲强度计算 (1)直齿轮弯曲应力wσbtyK K F fw σ=σ1(3--11)式中,wσ为弯曲应力(N /mm ²);1F 为圆周力(N),1F =2gT/d ;gT 为计算载荷(N·mm);d 为节圆直径(mm);σK 为应力集中系数,可近似取σK =1.65;fK 为摩擦力影响系数,主、从动齿轮在啮合点上的摩擦力方向不同,对弯曲应力的影响也不同:主动齿轮fK =1.1,从动齿轮fK =O.9;b 为齿宽(mm),b=cK m ;t 为端面齿距(mm),t=πm ;m 为模数(mm);y 为齿形系数,见图3-14。
课程设计--- 变速器的设计计算

设计说明书题目:货车机械变速器学号:姓名:变速器的设计计算1.1 变速器的选择变速器的种类很多,按前进档位的不同可分为三、四、五和多档变速器,根据轴的型式的不同,又有固定轴式和旋转轴式(常配合行星齿轮传动)两类。
固定轴式又有两轴式、中间轴式、双中间轴式和多中间轴式变速器。
固定轴式应用广泛,其中两轴式变速器多用于发动机前置前轮驱动的汽车上,中间轴式变速器多用于发动机前置后轮驱动的汽车上。
旋转轴式主要用于液力机械式变速器。
2-1-1 中间轴式变速器从结构外形看中间轴式变速器有三根轴:一轴和二轴在一条中心线上。
将它们连接即为直接档,此时,齿轮、轴承不承受载荷而只传递转矩,故而传动效率高,而且摩损小,寿命长,噪音也较小。
而在其他档位上,经过两对连续齿轮传动,传动效率稍低。
由于本设计中的汽车为重型货车,且档位多,传动比大,故本设计采用这种型式。
2-1-2 变速器齿轮型式变速器中的齿轮一般只有两种:直尺圆柱齿轮和斜齿圆柱齿轮。
直齿圆柱齿轮多用为滑动式,故使用在一档和倒档的较多,它们的结构简单,制造容易。
但是在换档时齿轮端部产生冲击,噪声很大,从而加剧端部磨损,使齿轮的寿命降低,而且由于噪声大,容易造成驾驶员的疲劳。
斜齿圆柱齿轮传动平稳,噪声很小,磨损小,寿命长。
唯一的缺点是工作时有轴向力的产生,而且结构复杂,这个缺点可以在进行轴的载荷计算时予以平衡。
通过比较两种型式齿轮的优缺点,本设计中,倒档采用直齿圆柱齿轮,这是考虑到倒档的使用率较低,综合衡量经济性和便利性而定的,其余各档全部采用斜齿圆柱齿轮传动,这样充分发挥其传动平稳,噪声小等优点。
2-1-3变速器的换档结构变速器的换档机构形式有以下几种:直齿滑动齿轮、啮合套和同步器换档。
(1) 直齿滑动齿轮换档该结构形式制造容易,结构简单。
但缺点较多:汽车行驶时各档齿轮有不同的角速度,因此用轴向滑动直齿齿轮的方式换档,会在轮齿端面产生冲击,并伴随有噪声。
这使齿轮端部磨损加剧并过早损坏,造成汽车的行驶安全性降低,同时使驾驶员精神紧张,而换档产生的噪声又会使乘坐舒适应大大的降低。
汽车变速器计算参考共17页

汽车变速器计算参考共17页§2.1 变速器主要参数的选择一、档数和传动比近年来,为了降低油耗,变速器的档数有增加的趋势。
目前,乘用车一般用4~5个档位的变速器。
本设计也采用5个档位。
选择最低档传动比时,应根据汽车最大爬坡度、驱动轮与路面的附着力、汽车的最低稳定车速以及主减速比和驱动轮的滚动半径等来综合考虑、确定。
汽车爬陡坡时车速不高,空气阻力可忽略,则最大驱动力用于克服轮胎与路面间的滚动阻力及爬坡阻力。
故有则由最大爬坡度要求的变速器Ⅰ档传动比为(2-1)式中m----汽车总质量;g----重力加速度;ψmax----道路最大阻力系数;r r----驱动轮的滚动半径;T emax----发动机最大转矩;i0----主减速比;η----汽车传动系的传动效率。
根据驱动车轮与路面的附着条件求得的变速器I档传动比为:(2-2)式中G2----汽车满载静止于水平路面时驱动桥给路面的载荷;φ----路面的附着系数,计算时取φ=0.5~0.6。
由已知条件:满载质量 1800kg;r r=337.25mm;T e max=170Nm;i0=4.782;η=0.95。
根据公式(2-2)可得:i gI =3.85。
超速档的的传动比一般为0.7~0.8,本设计去五档传动比i=0.75。
gⅤ中间档的传动比理论上按公比为:(2-3)的等比数列,实际上与理论上略有出入,因齿数为整数且常用档位间的公比宜小些,另外还要考虑与发动机参数的合理匹配。
根据上式可的出:q=1.51。
故有:二、中心距中心距对变速器的尺寸及质量有直接影响,所选的中心距、应能保证齿轮的强度。
三轴式变速器的中心局A(mm)可根据对已有变速器的统计而得出的经验公式初定:(2-4)式中K A----中心距系数。
对轿车,K A=8.9~9.3;对货车,K A=8.6~9.6;对多档主变速器,K A =9.5~11;T I max ----变速器处于一档时的输出扭矩:T I max=T e max i g I η =628.3N﹒m故可得出初始中心距A=77.08mm。
变速器的设计与计算
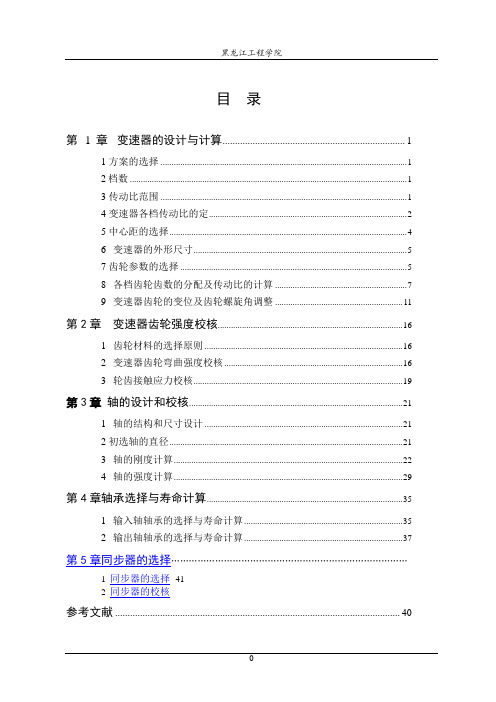
目录第1章变速器的设计与计算 (1)1方案的选择 (1)2档数 (1)3传动比范围 (1)4变速器各档传动比的定 (2)5中心距的选择 (4)6变速器的外形尺寸 (5)7齿轮参数的选择 (5)8各档齿轮齿数的分配及传动比的计算 (7)9变速器齿轮的变位及齿轮螺旋角调整 (11)第2章变速器齿轮强度校核 (16)1齿轮材料的选择原则 (16)2变速器齿轮弯曲强度校核 (16)3轮齿接触应力校核 (19)第3章轴的设计和校核 (21)1轴的结构和尺寸设计 (21)2初选轴的直径 (21)3轴的刚度计算 (22)4轴的强度计算 (29)第4章轴承选择与寿命计算 (35)1输入轴轴承的选择与寿命计算 (35)2输出轴轴承的选择与寿命计算 (37)第5章同步器的选择………………………………………………………………………1 同步器的选择412 同步器的校核参考文献 (40)第1章变速器的设计与计算1 方案的选择最高车速 150 Km/h整车总质量 1200 Kg最大功率 65 Kw最大转矩 145 N·m最大转矩转速 5500 r/min前轮胎规格165/60 R142 档数近年来,为了降低油耗,变速器的档数有增加的趋势。
目前,乘用车一般用5~6个档位的变速器。
发动机排量大的乘用车变速器多用6个档。
商用车变速器采用4~5个档或多档。
载质量在2.0~3.5t的货车采用五档变速器,载质量在4.0~8.0t的货车采用六档变速器。
多档变速器多用于总质量大些的货车和越野汽车上。
档数选择的要求:1、相邻档位之间的传动比比值在1.8以下。
2、高档区相邻档位之间的传动比比值要比低档区相邻档位之间的比值小。
因此,本次设计的变速器为5档变速器。
3 传动比范围变速器传动比范围是指变速器最高档与最低档传动比的比值。
最高档通常是直接档,传动比为1.0;有的变速器最高档是超速档,传动比为0.7~0.8。
影响最低档传动比选取的因素有:发动机的最大转矩和最低稳定转速所要求的汽车最大爬坡能力、驱动轮与路面间的附着力、主减速比和驱动轮的滚动半径以及所要求达到的最低稳定行驶车速等。
变速器标准值计算公式

变速器标准值计算公式变速器是汽车传动系统中的重要组成部分,它能够根据车速和发动机转速的变化,使车辆在不同工况下保持合适的转速和扭矩输出,从而保证车辆的动力性能和燃油经济性。
在变速器设计和优化过程中,需要对其性能进行评估和计算,以确定合适的参数和工作范围。
在这个过程中,变速器标准值计算公式是一个重要的工具,它可以帮助工程师们快速准确地计算出变速器的各项性能指标,为变速器的设计和优化提供参考。
变速器的性能指标包括传动效率、传动比、换挡时间等多个方面,其中传动效率是变速器性能的关键指标之一。
传动效率是指变速器在传递动力时的能量损失,它直接影响着车辆的燃油经济性和动力性能。
传动效率的计算公式可以表示为:η = (Pout / Pin) 100%。
其中,η表示传动效率,Pout表示输出功率,Pin表示输入功率。
通过这个公式,可以快速计算出变速器的传动效率,从而评估其性能和优化设计。
除了传动效率,传动比也是变速器设计中的一个重要参数。
传动比是指变速器输入轴和输出轴的转速比,它直接影响着车辆的加速性能和燃油经济性。
传动比的计算公式可以表示为:i = Nout / Nin。
其中,i表示传动比,Nout表示输出轴转速,Nin表示输入轴转速。
通过这个公式,可以快速计算出变速器的传动比,从而评估其对车辆动力性能的影响。
此外,换挡时间也是变速器设计中需要考虑的重要参数。
换挡时间是指变速器在进行换挡操作时所需的时间,它直接影响着车辆的驾驶舒适性和动力输出。
换挡时间的计算公式可以表示为:t = (θ 60) / (2 π N)。
其中,t表示换挡时间,θ表示换挡角度,N表示发动机转速。
通过这个公式,可以快速计算出变速器的换挡时间,从而评估其对车辆驾驶舒适性的影响。
在变速器设计和优化过程中,变速器标准值计算公式是一个重要的工具,它可以帮助工程师们快速准确地评估变速器的性能指标,为变速器的设计和优化提供参考。
通过对传动效率、传动比、换挡时间等多个方面的计算,可以全面了解变速器的性能特点,从而为其优化设计提供有力支持。
汽车变速器齿轮强度计算方法
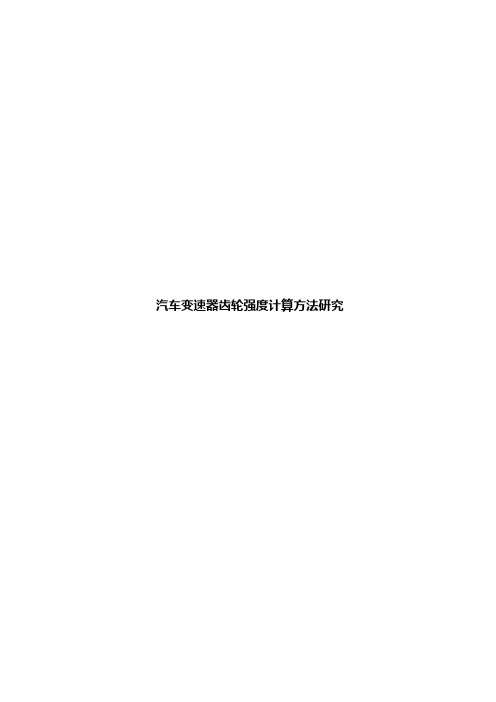
汽车变速器齿轮强度计算方法研究摘要汽车变速器齿轮强度的计算比较复杂,有些参数需通过多次选取和计算,才能达到设计要求,需要耗费大量的时间。
通过学习研究一些国外变速器的齿轮计算方法,通过VB6.0编程实现计算机辅助汽车变速器齿轮强度计算,找到一种简便的、快速的计算方法。
同时使用S-N曲线对计算后的齿轮强度进行校核。
Solidworks是法国达索公司开发的集三维建模、运动模拟及有限元分析为一体的,功能强大且操作简单的机械设计软件。
可对齿轮进行快速建模,并应用集成cosmosworks 对啮合齿轮进行有限元分析,为设计提供依据。
本文以某六档机械式汽车变速器为实例进行设计计算。
关键词:汽车变速器,齿轮强度计算,cosmosworks,VB汽车变速器齿轮的强度计算和校核1.1 齿轮强度计算1.1.1 变速箱齿轮的失效形式通常变速箱齿轮损坏有三种形式:轮齿折断、齿面点蚀、齿面胶合。
齿轮在啮合过程中,轮齿表面将承受集中载荷的作用。
轮齿相当于悬臂梁,根部弯曲应力很大,过渡圆角处又有应力集中,故轮齿根部很容易发生断裂。
折断有两种情况:一是轮齿受足够大的突然载荷冲击作用导致发生断裂;二是受多次重复载荷的作用,齿根受拉面的最大应力区出现疲劳裂缝,裂缝逐渐扩展到一定深度,轮齿突然折断。
变速箱齿轮折断多数是疲劳破坏。
齿面点蚀是闭式齿轮传动常出现的一种损坏形式。
因闭式齿轮传动的齿轮在润滑油中工作,齿面长期受到脉动的接触应力作用,会逐渐产生大量与齿面成尖角的小裂缝。
而裂缝中充满了润滑油,啮合时由于齿面互相挤压,裂缝中油压升高,使裂缝继续扩展,最后导致齿面表层一块块剥落,齿面出现大量扇形小麻点,此即齿面点蚀。
理论上靠近节圆的根部齿面处要较靠近节圆顶部齿面处点蚀更严重;互相啮合的齿轮副中,主动的小齿轮点蚀较严重。
在变速箱齿轮中,齿面胶核损坏的情况不多,故一般设计计算无须校核齿面胶合的情况。
齿轮计算载荷的确定在齿轮强度计算中占据至关重要的地位,而影响轮齿载荷的因素却有很多,也比较复杂,目前在国际上的各种齿轮强度计算方法的主要区别,就是对载荷影响因素的计算方法的不同。
五档手动变速器计算参考
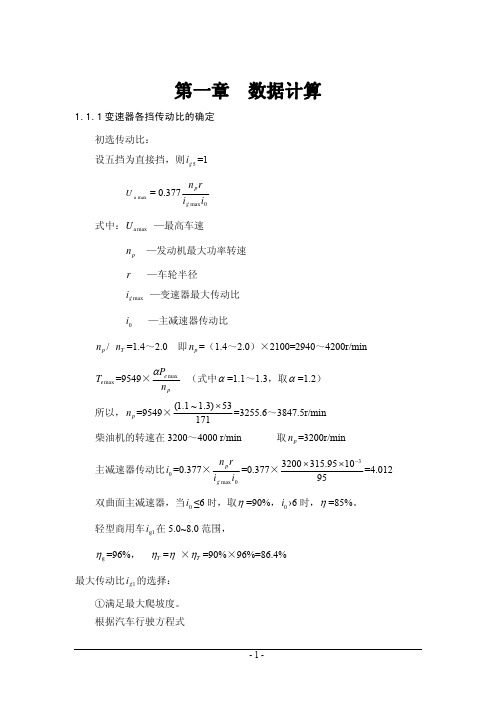
1.1.1 变速器各挡传动比的确定
初选传动比: 设五挡为直接挡,则 ig5 =1
U
a max
=
0.377
npr ig maxi0
式中:Ua max —最高车速
np —发动机最大功率转速 r —车轮半径 ig max —变速器最大传动比
i0 —主减速器传动比
np / nT =1.4~2.0 即 np =(1.4~2.0)×2100=2940~4200r/min
=
1 2
d1'0
=
27.18mm
3、确定常啮合传动齿轮副的齿数
由式(1.3)求出常啮合传动齿轮的传动比
Z2 Z1
= ig1
Z10 Z9
(1.6)
-6-
= 5.8 × 13 =2.43 31
常啮合传动齿轮的中心距与一挡齿轮的中心距相等,初选 β1−2 = 20° ,即
A = mn (Z1 + Z2 )
=5.87≈
ig1
=5.8
对常啮合齿轮进行角度变位:
理论中心距
Ao
=
mn (Z1 + Z2
2cos β1−2
)
=
4× (13 + 32)
2cos 20°
=95.79mm
端面压力角
tanαt =tanα n /cos β1−2
αt =21.18°
端面啮合角
cos
α
, t
=
Ao A
cos
α
t
=
95 .79 94
Te
max
=9549×
αPe max np
(式中α =1.1~1.3,取α =1.2)
变速器主要参数
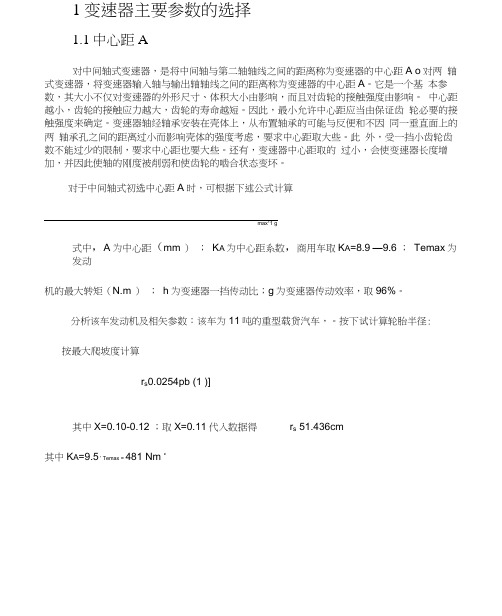
1变速器主要参数的选择1.1中心距A对中间轴式变速器,是将中间轴与第二轴轴线之间的距离称为变速器的中心距A o对两轴式变速器,将变速器输入轴与输出轴轴线之间的距离称为变速器的中心距A。
它是一个基本参数,其大小不仅对变速器的外形尺寸、体积大小由影响,而且对齿轮的接触强度由影响。
中心距越小,齿轮的接触应力越大,齿轮的寿命越短。
因此,最小允许中心距应当由保证齿轮必要的接触强度来确定。
变速器轴经轴承安装在壳体上,从布置轴承的可能与反便和不因同一垂直面上的两轴承孔之间的距离过小而影响壳体的强度考虑,要求中心距取大些。
此外,受一挡小齿轮齿数不能过少的限制,要求中心距也要大些。
还有,变速器中心距取的过小,会使变速器长度增加,并因此使轴的刚度被削弱和使齿轮的啮合状态变坏。
对于中间轴式初选中心距A时,可根据下述公式计算max11 g式中,A为中心距(mm );K A为中心距系数,商用车取K A=8.9—9.6 ;Temax为发动机的最大转矩(N.m );h为变速器一挡传动比;g为变速器传动效率,取96%。
分析该车发动机及相矢参数:该车为11吨的重型载货汽车,。
按下试计算轮胎半径: 按最大爬坡度计算r s0.0254pb (1 )]r s 51.436cm其中X=0.10-0.12 ;取X=0.11代入数据得其中K A=9.5 ' Temax = 481 Nm ‘挡传动比: 参考同类车型:取主减速器传动比为i。
=4.654,取F|T=0.85; ITIQ. maxTslgi>Te max'试中:m为汽车重质量m=11000Kg,g为重力加速度g=9.8N/Kg,Tmax为发动机最大转矩Temax=481N.m,i。
为主减速器传动比等于4.654, Tmax为道路最大阻力系数等于0.2533,rs为驱动轮滚动半径,r| T为汽车传动系效率。
代入数据得igi>7.39o根据车轮与路面附着条件确定一档传动比:G2 rsTe m ax's为汽车满载时静止于水平路面驱动桥给路面的载荷G2=mg 66.5%=11000 10 66.5%=73150Kg,为道路附着系数‘计算时取=0.5-0.8 ‘ 在此取0.8。
第四节 变速器的设计与计算
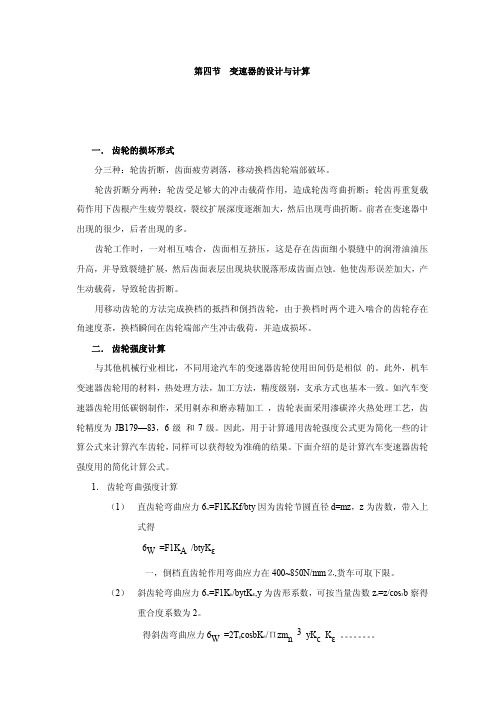
f c 和 f s 分别表示轴在垂直面和水平面的挠度,则轴的全挠度 f 为
f
f c2 f s2
≤0.2mm。
轴在垂直面和水平面挠度的允许值为 齿轮所在平面的转角不应超过0.002rad。
f c =0.05—0.10mm,/, f s =0.10—0.15mm。
与中间轴齿轮常啮合的第二轴上的齿轮,常通过青铜衬套或滚针轴承装在轴上,也有的 省去衬套或滚针轴承直接装在轴上,这就能够增大轴的直径,因而使轴的刚度增加。 作用在齿轮上的径向力和轴向力,使轴在垂直面内弯曲变形,而圆周力使轴在水平面内 弯曲变形。在求取支点的垂直面和水平面内的支反力Fc和Fs之后,计算相应的弯矩Mc、Ms。 轴在转矩Tn和弯矩同时作用下,其应力为
三. 轴的强度计算 变速器工作时,由于齿轮上有圆周力、径向力和轴向力作用,其轴要承受转矩和弯矩。 变速器的轴应有足够的刚度和强度。 因为刚度不足的轴会产生弯曲变形, 破坏了齿轮的正确 啮合,对齿轮的强度、耐磨性和工作噪声等均有不利影响。所以设计变速器轴时,其刚度大 小应以保证齿轮能实现正确的啮合为前提条件。 对齿轮工作影响最大的是轴在垂直面内产生的挠度和轴在水平面内的转角。前者使齿轮 中心距发生变化,破坏了齿轮的正确啮合;后者使齿轮相互歪斜,如图3—15所示,致使沿 齿长方向的压力分布不均匀。
第四节 变速器的设计与计算
一. 齿轮的损坏形式 分三种:轮齿折断,齿面疲劳剥落,移动换档齿轮端部破坏。 轮齿折断分两种:轮齿受足够大的冲击载荷作用,造成轮齿弯曲折断;轮齿再重复载 荷作用下齿根产生疲劳裂纹,裂纹扩展深度逐渐加大,然后出现弯曲折断。前者在变速器中 出现的很少,后者出现的多。 齿轮工作时,一对相互啮合,齿面相互挤压,这是存在齿面细小裂缝中的润滑油油压 升高,并导致裂缝扩展,然后齿面表层出现块状脱落形成齿面点蚀。他使齿形误差加大,产 生动载荷,导致轮齿折断。 用移动齿轮的方法完成换档的抵挡和倒挡齿轮,由于换档时两个进入啮合的齿轮存在 角速度茶,换档瞬间在齿轮端部产生冲击载荷,并造成损坏。 二. 齿轮强度计算 与其他机械行业相比,不同用途汽车的变速器齿轮使用田间仍是相似 的。此外,机车 变速器齿轮用的材料,热处理方法,加工方法,精度级别,支承方式也基本一致。如汽车变 速器齿轮用低碳钢制作,采用剃赤和磨赤精加工 ,齿轮表面采用渗碳淬火热处理工艺,齿 轮精度为 JB179—83,6 级 和 7 级。因此,用于计算通用齿轮强度公式更为简化一些的计 算公式来计算汽车齿轮, 同样可以获得较为准确的结果。 下面介绍的是计算汽车变速器齿轮 强度用的简化计算公式。 1. 齿轮弯曲强度计算 (1) 直齿轮弯曲应力 6w=F1K6Kf/bty 因为齿轮节圆直径 d=mz ,z 为齿数,带入上 式得 6W =F1KA /btyKε 一,倒档直齿轮作用弯曲应力在 400~850N/mm⒉,货车可取下限。 (2) 斜齿轮弯曲应力 6w=F1K6/bytKE,y 为齿形系数,可按当量齿数 zn=z/cos3b 察得 重合度系数为 2。 得斜齿弯曲应力 6W =2TgcosbK6/Πzmn 3 yKc Kε 。 。 。 。 。 。 。 。
变速器传动比的计算方法及其原理

变速器传动比的计算方法及其原理传动比是指变速器输出轴的转速与输入轴的转速之比,是汽车变速器的重要性能指标。
它决定了汽车在不同速度下的运行状态和动力输出情况。
为了实现高效、平稳的行驶,驾驶员需要了解变速器传动比的计算方法及其原理。
本文将介绍变速器传动比的计算方法和相关原理。
一、传动比的定义传动比是通过变速器来调节输出轴转速与输入轴转速之间的比值。
以手动变速器为例,传动比由使用者通过操纵换挡杆控制。
不同挡位会导致不同的传动比,进而实现不同的车速。
二、传动比的计算方法传动比的计算方法根据变速器的设计和构造不同而异。
下面将介绍两种常见的传动比计算方法。
1. 简单计算法对于一些简单的变速器结构,可以通过输出轴转速与输入轴转速之比直接计算传动比。
传动比 = 输出轴转速 / 输入轴转速例如,一台汽车变速器的输出轴转速为4000转/分钟,输入轴转速为2000转/分钟,则传动比为:传动比 = 4000 / 2000 = 22. 齿轮比法对于复杂的齿轮传动系统,传动比的计算可以通过齿轮比来实现。
变速器中齿轮的设计决定了传动比的变化。
传动比 = Z2 / Z1其中,Z2为输出轴上的齿轮的齿数,Z1为输入轴上的齿轮的齿数。
例如,一台汽车变速器的输出轴上的齿轮齿数为30,输入轴上的齿轮齿数为15,则传动比为:传动比 = 30 / 15 = 2三、传动比的原理传动比的原理是通过不同齿轮组合或输入输出轴间的直接比例关系实现的。
1. 齿轮传动原理在齿轮传动中,通过不同大小的齿轮组合来改变传动比。
齿轮的齿数与直径成反比,因此齿轮半径越大,齿数越小,传动比越大。
2. 偏心齿轮原理在偏心齿轮传动中,通过离心力的作用,使齿轮在轴上产生偏心运动,从而改变传动比。
通过调整齿轮的偏心程度,可以实现不同的传动比。
3. 液力变速器原理在液力变速器中,通过油流的流动和涡轮的转动来改变传动比。
液力变速器根据需要自动调整液压传动比,从而实现平稳的变速。
自动变速器速比计算
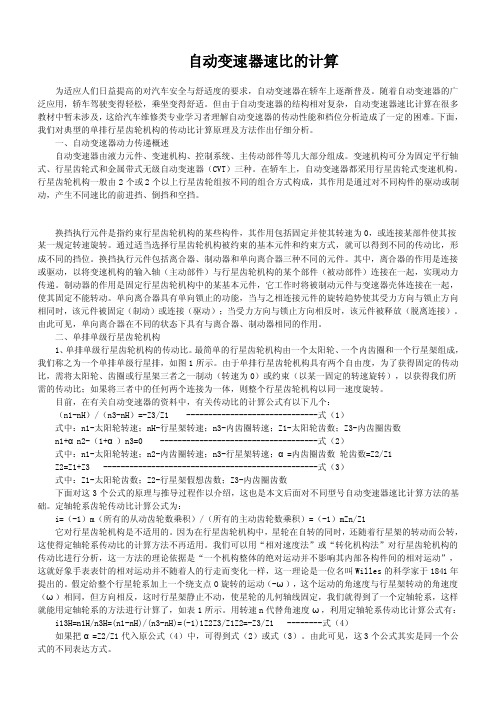
自动变速器速比的计算为适应人们日益提高的对汽车安全与舒适度的要求,自动变速器在轿车上逐渐普及。
随着自动变速器的广泛应用,轿车驾驶变得轻松,乘坐变得舒适。
但由于自动变速器的结构相对复杂,自动变速器速比计算在很多教材中暂未涉及,这给汽车维修类专业学习者理解自动变速器的传动性能和档位分析造成了一定的困难。
下面,我们对典型的单排行星齿轮机构的传动比计算原理及方法作出仔细分析。
一、自动变速器动力传递概述自动变速器由液力元件、变速机构、控制系统、主传动部件等几大部分组成。
变速机构可分为固定平行轴式、行星齿轮式和金属带式无级自动变速器(CVT)三种。
在轿车上,自动变速器都采用行星齿轮式变速机构。
行星齿轮机构一般由2个或2个以上行星齿轮组按不同的组合方式构成,其作用是通过对不同构件的驱动或制动,产生不同速比的前进挡、倒挡和空挡。
换挡执行元件是指约束行星齿轮机构的某些构件,其作用包括固定并使其转速为0,或连接某部件使其按某一规定转速旋转。
通过适当选择行星齿轮机构被约束的基本元件和约束方式,就可以得到不同的传动比,形成不同的挡位。
换挡执行元件包括离合器、制动器和单向离合器三种不同的元件。
其中,离合器的作用是连接或驱动,以将变速机构的输入轴(主动部件)与行星齿轮机构的某个部件(被动部件)连接在一起,实现动力传递。
制动器的作用是固定行星齿轮机构中的某基本元件,它工作时将被制动元件与变速器壳体连接在一起,使其固定不能转动。
单向离合器具有单向锁止的功能,当与之相连接元件的旋转趋势使其受力方向与锁止方向相同时,该元件被固定(制动)或连接(驱动);当受力方向与锁止方向相反时,该元件被释放(脱离连接)。
由此可见,单向离合器在不同的状态下具有与离合器、制动器相同的作用。
二、单排单级行星齿轮机构1、单排单级行星齿轮机构的传动比。
最简单的行星齿轮机构由一个太阳轮、一个内齿圈和一个行星架组成,我们称之为一个单排单级行星排,如图1所示。
由于单排行星齿轮机构具有两个自由度,为了获得固定的传动比,需将太阳轮、齿圈或行星架三者之一制动(转速为0)或约束(以某一固定的转速旋转),以获得我们所需的传动比;如果将三者中的任何两个连接为一体,则整个行星齿轮机构以同一速度旋转。
(整理)变速器设计参数.
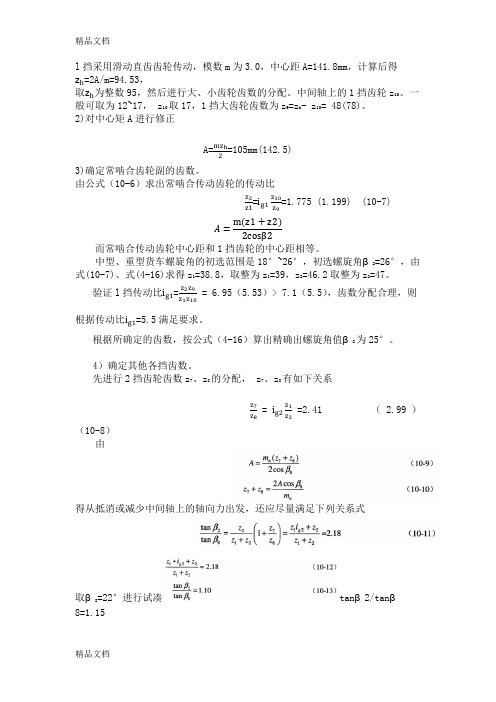
l挡采用滑动直齿齿轮传动,模数m为3.0,中心距A=141.8mm,计算后得=2A/m=94.53,取为整数95,然后进行大、小齿轮齿数的分配。
中间轴上的1挡齿轮z10。
一般可取为12~17, z10取17,1挡大齿轮齿数为z9=zh- z10= 48(78)。
2)对中心矩A进行修正A==105mm(142.5)3)确定常啮合齿轮副的齿数。
由公式(10-6)求出常啮合传动齿轮的传动比==1.775 (1.199) (10-7)而常啮合传动齿轮中心距和1挡齿轮的中心距相等。
中型、重型货车螺旋角的初选范围是18°~26°,初选螺旋角β2=26°,由式(10-7)、式(4-16)求得z1=38.8,取整为z1=39,z2=46.2取整为z2=47。
验证l挡传动比= = 6.95(5.53)> 7.1(5.5),齿数分配合理,则根据传动比=5.5满足要求。
根据所确定的齿数,按公式(4-16)算出精确出螺旋角值β2为25°。
4)确定其他各挡齿数。
先进行2挡齿轮齿数z7、z8的分配, z7、z8有如下关系==2.41 (2.99)(10-8)由得从抵消或减少中间轴上的轴向力出发,还应尽量满足下列关系式取β8=22°进行试凑tanβ2/tanβ8=1.15相差较多,为尽量缩小差距,取β8=18。
,已是极限值。
将数据代入式( 10-8) ~式(10-13)求得,z8=22.6取整为23,z7=67.8取整为68,验证传动比为=3.56,齿数分配不合适。
进行齿数调整,令z1=23,z2=69,则根据传动比=3.62满足要求。
根据所确定的齿数,按式(10-10)算出精确的螺旋角β8值为20.6°。
同样方法求得β6=19。
,z6=27,z5=51,验证传动比为=2.43,满足要求,精确的螺旋角β2值为20.5°;取β4=20°,z4=36,z3=32,验证传动比为=1.61,满足要求;根据所确定的齿数,按式(4-16)算出精确的螺旋角值β4为21°。
变速器的计算
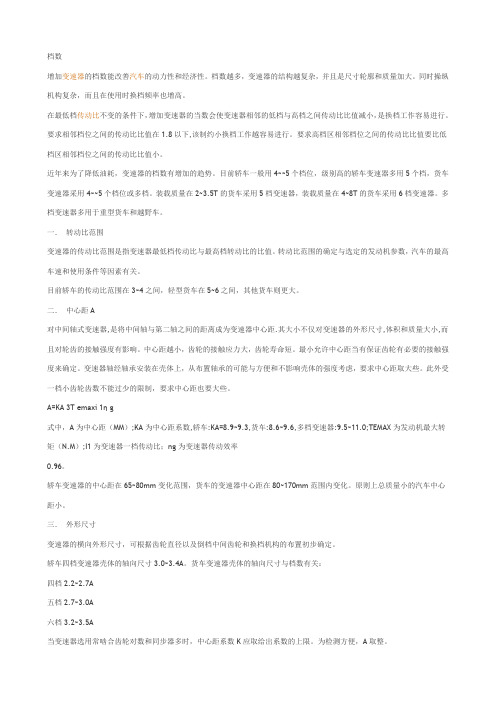
档数增加变速器的档数能改善汽车的动力性和经济性。
档数越多,变速器的结构越复杂,并且是尺寸轮廓和质量加大。
同时操纵机构复杂,而且在使用时换档频率也增高。
在最低档传动比不变的条件下,增加变速器的当数会使变速器相邻的低档与高档之间传动比比值减小,是换档工作容易进行。
要求相邻档位之间的传动比比值在1.8以下,该制约小换档工作越容易进行。
要求高档区相邻档位之间的传动比比值要比低档区相邻档位之间的传动比比值小。
近年来为了降低油耗,变速器的档数有增加的趋势。
目前轿车一般用4~~5个档位,级别高的轿车变速器多用5个档,货车变速器采用4~~5个档位或多档。
装载质量在2~3.5T的货车采用5档变速器,装载质量在4~8T的货车采用6档变速器。
多档变速器多用于重型货车和越野车。
一.转动比范围变速器的传动比范围是指变速器最低档传动比与最高档转动比的比值。
转动比范围的确定与选定的发动机参数,汽车的最高车速和使用条件等因素有关。
目前轿车的传动比范围在3~4之间,轻型货车在5~6之间,其他货车则更大。
二.中心距A对中间轴式变速器,是将中间轴与第二轴之间的距离成为变速器中心距.其大小不仅对变速器的外形尺寸,体积和质量大小,而且对轮齿的接触强度有影响。
中心距越小,齿轮的接触应力大,齿轮寿命短。
最小允许中心距当有保证齿轮有必要的接触强度来确定。
变速器轴经轴承安装在壳体上,从布置轴承的可能与方便和不影响壳体的强度考虑,要求中心距取大些。
此外受一档小齿轮齿数不能过少的限制,要求中心距也要大些。
A=KA 3T emaxi 1η g式中,A为中心距(MM);KA为中心距系数,轿车:KA=8.9~9.3,货车:8.6~9.6,多档变速器:9.5~11.0;TEMAX为发动机最大转矩(N.M);I1为变速器一档传动比;ng为变速器传动效率0.96。
轿车变速器的中心距在65~80mm变化范围,货车的变速器中心距在80~170mm范围内变化。
原则上总质量小的汽车中心距小。
变速箱计算

第四节变速器的设计与计算一、齿轮的损坏形式变速器齿轮的损坏形式主要有三种:轮齿折断,齿面疲劳剥落(点蚀),移动换挡齿轮端部破坏。
轮齿折断发生在两种情况下:轮齿受到足够大的冲击载荷作用,造成轮齿弯曲折断;轮齿在重复载荷作用下,齿根产生疲劳裂纹,裂纹扩展深度逐渐加大,然后出现弯曲折断。
前者在变速器中出现得极少,而后者出现得多些。
轮齿工作时,一对齿轮相互啮合,齿面相互挤压,这时存在于齿面细小裂缝中的润滑油,油压升高,并导致裂缝扩展,然后齿面表层出现块状剥落而形成小麻点,称之为齿面点蚀。
它使齿形误差加大,产生动载荷,并可能导致轮齿折断。
用移动齿轮的方法完成换挡的低挡和倒挡齿轮,由于换挡时两个进入啮合的齿轮存在角速度差,换挡瞬间在轮齿端部产生冲击载荷,并造成损坏。
二、轮齿强度计算与其它机械行业比较,不同用途汽车的变速器齿轮使用条件仍是相似的。
此外,汽车变速器齿轮用的材料、热处理方法、加工方法、精度级别、支承方式也基本一致。
如汽车变速器齿轮用低碳合金钢制作,采用剃齿或磨齿精加工,齿轮表面采用渗碳淬火热处理工艺,齿轮精度为JBl79—83,6级和7级。
因此,用于计算通用齿轮强度公式更为简化一些的计算公式来计算汽车齿轮,同样可以获得较为准确的结果。
下面介绍的是计算汽车变速器齿轮强度用的简化计算公式。
1、轮齿弯曲强度计算 (1)直齿轮弯曲应力wσbtyK K F fw σ=σ1(3--11)式中,wσ为弯曲应力(N /mm ²);1F 为圆周力(N),1F =2gT/d ;gT 为计算载荷(N·mm);d 为节圆直径(mm);σK 为应力集中系数,可近似取σK =1.65;fK 为摩擦力影响系数,主、从动齿轮在啮合点上的摩擦力方向不同,对弯曲应力的影响也不同:主动齿轮fK =1.1,从动齿轮fK =O.9;b 为齿宽(mm),b=cK m ;t 为端面齿距(mm),t=πm ;m 为模数(mm);y 为齿形系数,见图3-14。
变速器设计说明书 正文

第1章 变速器主要参数的计算及校核学号:15最高车速:m ax a U =113Km/h 发动机功率:m ax e P =65.5KW 转矩:max e T =206.5Nm 总质量:m a =4123Kg转矩转速:n T =2200r/min 车轮:R16(选6.00R16LT )1.1设计的初始数据表1.1已知基本数据车轮:R16(选6.00R16LT ) 查GB/T2977-2008 r=337mm1.2变速器传动比的确定确定Ι档传动比:汽车爬坡时车速不高,空气阻力可忽略,则最大驱动力用于克服轮胎与路面间的滚动阻力及爬坡阻力。
故有:ααηsin cos 0emax G Gf ri i T Tg +==max ψmg (1.1)式中:G ----作用在汽车上的重力,mg G =;m ----汽车质量;g ----重力加速度,41239.840405.4G mg N ==⨯=;max e T —发动机最大转矩,m N T e ⋅=174max ;0i —主减速器传动比,0 4.36i =;T η—传动系效率,%4.86=T η;r —车轮半径,0.337r m =;f —滚动阻力系数,对于货车取02.0=f ;α—爬坡度,30%换算为16.7α=。
则由最大爬坡度要求的变速器I 档传动比为:Te r g i T mgr i η0max max 1ψ≥=41239.80.2940.3375.17206.5 4.3686.4%⨯⨯⨯=⨯⨯ (1.2) 驱动轮与路面的附着条件:≤rTg r i i T η01emax φ2G (1.3)2G ----汽车满载静止于水平路面时驱动桥给地面的载荷;8.0~7.0=ϕ取75.0=ϕ1g i ≤2max 00.641239.80.750.3377.9206.5 4.3686.4%r e T G r T i φη⨯⨯⨯⨯==⨯⨯综上可知:15.177.9g i ≤≤ 取1 5.8g i = 其他各档传动比的确定: 按等比级数分配原则:q i i i i i i i i g g g g g g g g ====54433221 (1.4)式中:q —常数,也就是各挡之间的公比;因此,各挡的传动比为:41q i g =,32q i g =,23q i g =,q i g =4 1n 1-=g i q1.55=高档使用率比较高,低档使用率比较低,所以可使高档传动比较小,所以取其他各挡传动比分别为:2g i =3 3.7q =;23 2.4g i q ==;4 1.55g i q ==1.3中心距A可根据下述经验公式31max g e A i T K A η= (1.5)式中:A —变速器中心距(mm );A K —中心距系数,商用车:6.96.8-=A K ; max e T —发动机最大转矩(N.m );1i —变速器一挡传动比,8.51g =i ;g η—变速器传动效率,取96% ;max e T —发动机最大转矩,max 206.5e T N m =⋅。
变速器设计参数word资料4页

l 挡采用滑动直齿齿轮传动,模数m 为3.0,中心距A=141.8mm ,计算后得zh=2A/m=94.53,取z h 为整数95,然后进行大、小齿轮齿数的分配。
中间轴上的1挡齿轮z 10。
一般可取为12~17, z 10取17,1挡大齿轮齿数为z 9=z h - z 10= 48(78)。
2)对中心矩A 进行修正A=mz h2=105mm(142.5) 3)确定常啮合齿轮副的齿数。
由公式(10-6)求出常啮合传动齿轮的传动比z2z1=i g1z 10z 9=1.775 (1.199) (10-7) A =m (z1+z2)2cosβ2而常啮合传动齿轮中心距和1挡齿轮的中心距相等。
中型、重型货车螺旋角的初选范围是18°~26°,初选螺旋角β2=26°,由式(10-7)、式(4-16)求得z 1=38.8,取整为z 1=39,z 2=46.2取整为z 2=47。
验证l 挡传动比i g1=z 2z9z 1z 10= 6.95(5.53)> 7.1(5.5),齿数分配合理,则根据传动比i g1=5.5满足要求。
根据所确定的齿数,按公式(4-16)算出精确出螺旋角值β2为25°。
4)确定其他各挡齿数。
先进行2挡齿轮齿数z 7、z 8的分配, z 7、z 8有如下关系z7z 8=i g2z1z 2=2.41 (2.99) (10-8)由得从抵消或减少中间轴上的轴向力出发,还应尽量满足下列关系式取β8=22°进行试凑tan β2/tan β8=1.15相差较多,为尽量缩小差距,取β8=18。
,已是极限值。
将数据代入式( 10-8) ~式(10-13)求得,z 8=22.6取整为23,z 7=67.8取整为68,验证传动比为i g2=3.56,齿数分配不合适。
进行齿数调整,令z 1=23,z 2=69,则根据传动比i g2=3.62满足要求。
根据所确定的齿数,按式(10-10)算出精确的螺旋角β8值 为20.6°。
- 1、下载文档前请自行甄别文档内容的完整性,平台不提供额外的编辑、内容补充、找答案等附加服务。
- 2、"仅部分预览"的文档,不可在线预览部分如存在完整性等问题,可反馈申请退款(可完整预览的文档不适用该条件!)。
- 3、如文档侵犯您的权益,请联系客服反馈,我们会尽快为您处理(人工客服工作时间:9:00-18:30)。
§2.1 变速器主要参数的选择一、档数和传动比近年来,为了降低油耗,变速器的档数有增加的趋势。
目前,乘用车一般用4~5个档位的变速器。
本设计也采用5个档位。
选择最低档传动比时,应根据汽车最大爬坡度、驱动轮与路面的附着力、汽车的最低稳定车速以及主减速比和驱动轮的滚动半径等来综合考虑、确定。
汽车爬陡坡时车速不高,空气阻力可忽略,则最大驱动力用于克服轮胎与路面间的滚动阻力及爬坡阻力。
故有则由最大爬坡度要求的变速器Ⅰ档传动比为(2-1)式中m----汽车总质量;g----重力加速度;ψmax----道路最大阻力系数;r r----驱动轮的滚动半径;T emax----发动机最大转矩;i0----主减速比;η----汽车传动系的传动效率。
根据驱动车轮与路面的附着条件求得的变速器I档传动比为:(2-2)式中G2----汽车满载静止于水平路面时驱动桥给路面的载荷;φ----路面的附着系数,计算时取φ=0.5~0.6。
由已知条件:满载质量 1800kg;r r=337.25mm;T e max=170Nm;i0=4.782;η=0.95。
根据公式(2-2)可得:i gI =3.85。
超速档的的传动比一般为0.7~0.8,本设计去五档传动比i=0.75。
gⅤ中间档的传动比理论上按公比为:(2-3)的等比数列,实际上与理论上略有出入,因齿数为整数且常用档位间的公比宜小些,另外还要考虑与发动机参数的合理匹配。
根据上式可的出:q=1.51。
故有:二、中心距中心距对变速器的尺寸及质量有直接影响,所选的中心距、应能保证齿轮的强度。
三轴式变速器的中心局A(mm)可根据对已有变速器的统计而得出的经验公式初定:(2-4)式中K A----中心距系数。
对轿车,K A=8.9~9.3;对货车,K A=8.6~9.6;对多档主变速器,K A =9.5~11;T I max ----变速器处于一档时的输出扭矩:T I max=T e max i g I η =628.3N﹒m故可得出初始中心距A=77.08mm。
三、轴向尺寸变速器的横向外形尺寸,可根据齿轮直径以及倒档中间齿轮和换档机构的布置初步确定。
轿车四档变速器壳体的轴向尺寸 3.0~3.4A。
货车变速器壳体的轴向尺寸与档数有关:四档(2.2~2.7)A五档(2.7~3.0)A六档(3.2~3.5)A当变速器选用常啮合齿轮对数和同步器多时,中心距系数K A应取给出系数的上限。
为检测方便,A取整。
本次设计采用5+1手动挡变速器,其壳体的轴向尺寸是3⨯77.08mm=231.24mm,变速器壳体的最终轴向尺寸应由变速器总图的结构尺寸链确定。
四、齿轮参数(1)齿轮模数建议用下列各式选取齿轮模数,所选取的模数大小应符合JB111-60规定的标准值。
第一轴常啮合斜齿轮的法向模数m nm=n(2-5)其中T=170Nm,可得出m n=2.5。
emax一档直齿轮的模数mm=(2-6)通过计算m=3。
同步器和啮合套的接合大都采用渐开线齿形。
由于制造工艺上的原因,同一变速器中的结合套模数都去相同,轿车和轻型货车取2~3.5。
本设计取2.5。
(2)齿形、压力角α、螺旋角β和齿宽b汽车变速器齿轮的齿形、压力角、及螺旋角按表2-1选取。
表2-1 汽车变速器齿轮的齿形、压力角与螺旋角压力角较小时,重合度大,传动平稳,噪声低;较大时可提高轮齿的抗弯强度和表面接触强度。
对轿车,为加大重合度已降低噪声,取小些;对货车,为提高齿轮承载力,取大些。
在本设计中变速器齿轮压力角α取20°,啮合套或同步器取30°;斜齿轮螺旋角β取30°。
应该注意的是选择斜齿轮的螺旋角时应力求使中间轴上是轴向力相互抵消。
为此,中间轴上的全部齿轮一律去右旋,而第一轴和第二轴上的的斜齿轮去左旋,其轴向力经轴承盖由壳体承受。
齿轮宽度b的大小直接影响着齿轮的承载能力,b加大,齿的承载能力增高。
但试验表明,在齿宽增大到一定数值后,由于载荷分配不均匀,反而使齿轮的承载能力降低。
所以,在保证齿轮的强度条件下,尽量选取较小的齿宽,以有利于减轻变速器的重量和缩短其轴向尺寸。
通常根据齿轮模数的大小来选定齿宽:直齿 b=(4.5~8.0)m,mm斜齿 b=(6.0~8.5)m,mm第一轴常啮合齿轮副齿宽的系数值可取大一些,使接触线长度增加,接触应力降低,以提高传动的平稳性和齿轮寿命。
§2.2各档传动比及其齿轮齿数的确定在初选了中心距、齿轮的模数和螺旋角后,可根据预先确定的变速器档数、传动比和结构方案来分配各档齿轮的齿数。
下面结合本设计来说明分配各档齿数的方法。
1.确定一档齿轮的齿数一档传动比(2-7)为了确定Z9和Z10的齿数,先求其齿数和∑Z:(2-8)其中A =77.08mm、m =3;故有4.51=∑Z。
图2-1 五档变速器示意图当轿车三轴式的变速器9.3~5.3=gI i 时,则范围内选择可在17~1510Z ,此处取10Z =16,则可得出9Z =35。
上面根据初选的A 及m 计算出的∑Z 可能不是整数,将其调整为整数后,从式(2-8)看出中心距有了变化,这时应从∑Z 及齿轮变位系数反过来计算中心距A ,再以这个修正后的中心距作为以后计算的依据。
这里∑Z 修正为51,则根据式(2-8)反推出A =76.5mm 。
2.确定常啮合齿轮副的齿数由式(2-7)求出常啮合齿轮的传动比(2-9)由已经得出的数据可确定 ①而常啮合齿轮的中心距与一档齿轮的中心距相等(2-10)由此可得:(2-11)而根据已求得的数据可计算出:5321=+Z Z 。
②① 与②联立可得:1Z =19、2Z =34。
则根据式(2-7)可计算出一档实际传动比为: 。
3.确定其他档位的齿数二档传动比(2-12)而 ,故有:对于斜齿轮,(2-13)故有:5387=+Z Z ④③ 联立④得:223187==Z Z 、。
按同样的方法可分别计算出:三档齿轮 272665==Z Z 、;四档齿轮4.确定倒档齿轮的齿数一般情况下,倒档传动比与一档传动比较为接近,在本设计中倒档传动比gr i 取3.7。
中间轴上倒档传动齿轮的齿数比一档主动齿轮10略小,取1312=Z 。
而通常情况下,倒档轴齿轮13Z 取21~23,此处取13Z =23。
由(2-14)可计算出2711=Z 。
故可得出中间轴与倒档轴的中心距A′ =(2-15) =50mm而倒档轴与第二轴的中心:(2-16)=72.5mm 。
§2.3 齿轮变位系数的选择齿轮的变位是齿轮设计中一个非常重要的环节。
采用变位齿轮,除为了避免齿轮产生根切和配凑中心距以外,它还影响齿轮的强度,使用平稳性,耐磨性、抗胶合能力及齿轮的啮合噪声。
变位齿轮主要有两类:高度变位和角度变位。
高度变位齿轮副的一对啮合齿轮的变位系数的和为零。
高度变位可增加小齿轮的齿根强度,使它达到和大齿轮强度想接近的程度。
高度变位齿轮副的缺点是不能同时增加一对齿轮的强度,也很难降低噪声。
角度变位齿轮副的变位系数之和不等于零。
角度变位既具有高度变位的优点,有避免了其缺点。
有几对齿轮安装在中间轴和第二轴上组合并构成的变速器,会因保证各档传动比的需要,使各相互啮合齿轮副的齿数和不同。
为保证各对齿轮有相同的中心距,此时应对齿轮进行变位。
当齿数和多的齿轮副采用标准齿轮传动或高度变位时,则对齿数和少些的齿轮副应采用正角度变位。
由于角度变位可获得良好的啮合性能及传动质量指标,故采用的较多。
对斜齿轮传动,还可通过选择合适的螺旋角来达到中心距相同的要求。
变速器齿轮是在承受循环负荷的条件下工作,有时还承受冲击负荷。
对于高档齿轮,其主要损坏形势是齿面疲劳剥落,因此应按保证最大接触强度和抗胶合剂耐磨损最有利的原则选择变位系数。
为提高接触强度,应使总变位系数尽可能取大一些,这样两齿轮的齿轮渐开线离基圆较远,以增大齿廓曲率半径,减小接触应力。
对于低档齿轮,由于小齿轮的齿根强度较低,加之传递载荷较大,小齿轮可能出现齿根弯曲断裂的现象。
总变位系数越小,一对齿轮齿更总厚度越薄,齿根越弱,抗弯强度越低。
但是由于轮齿的刚度较小,易于吸收冲击振动,故噪声要小些。
根据上述理由,为降低噪声,变速器中除去一、二档和倒档以外的其他各档齿轮的总变位系数要选用较小的一些数值,以便获得低噪声传动。
〈17,因此一档齿轮需要变位。
其中,一档主动齿轮10的齿数Z10变位系数(2-17)式中Z为要变位的齿轮齿数。
第三章变速器齿轮的强度计算与材料的选择§3.1 齿轮的损坏原因及形式齿轮的损坏形式分三种:轮齿折断、齿面疲劳剥落和移动换档齿轮端部破坏。
轮齿折断分两种:轮齿受足够大的冲击载荷作用,造成轮齿弯曲折断;轮齿再重复载荷作用下齿根产生疲劳裂纹,裂纹扩展深度逐渐加大,然后出现弯曲折断。
前者在变速器中出现的很少,后者出现的多。
齿轮工作时,一对相互啮合,齿面相互挤压,这是存在齿面细小裂缝中的润滑油油压升高,并导致裂缝扩展,然后齿面表层出现块状脱落形成齿面点蚀。
他使齿形误差加大,产生动载荷,导致轮齿折断。
用移动齿轮的方法完成换档的抵挡和倒挡齿轮,由于换档时两个进入啮合的齿轮存在角速度茶,换档瞬间在齿轮端部产生冲击载荷,并造成损坏。
§3.2 齿轮的强度计算与校核与其他机械设备使用的变速器比较,不同用途汽车的变速器齿轮使用条件仍是相似的。
此外,汽车变速器齿轮所用的材料、热处理方法、加工方法、精度等级、支撑方式也基本一致。
如汽车变速器齿轮用低碳合金钢制造,采用剃齿或齿轮精加工,齿轮表面采用渗碳淬火热处理工艺,齿轮精度不低于7级。
因此,比用于计算通用齿轮强度公式更为简化一些的计算公式来计算汽车齿轮,同样、可以获得较为准确的结果。
在这里所选择的齿轮材料为40Cr。
1.齿轮弯曲强度计算σ(1)直齿轮弯曲应力W(3-1)式中,σ----弯曲应力(MPa);WF----一档齿轮10的圆周t10力(N),;其中为计算载荷(N·mm),d为节圆直径。
----应力集中系数,可近似取1.65;K----摩擦力影响系数,f主动齿轮取1.1,从动齿轮取0.9;b----齿宽(mm),取20t----端面齿距(mm);y----齿形系数,如图3-1所示。
图3-1 齿形系数图当处于一档时,中间轴上的计算扭矩为:(3-2)=170⨯1000⨯2.18⨯1.78=659668Nm故由可以得出F;再将所得出的数据代入式(3-1)可得10t当计算载荷取作用到变速器第一轴上的最大扭矩max e T 时,一档直齿轮的弯曲应力在400~850MPa 之间。
(2) 斜齿轮弯曲应力(3-3)式中 K ε为重合度影响系数,取 2.0;其他参数均与式(3-1)注释相同,1.50K σ=,选择齿形系数y 时,按当量模数3/cos n z z β=在图(3-1)中查得。