故障假设分析法
故障假设分析法解释与运用事例

(教材P103,112~118) PPt 2-2-007、017插件一、故障假设分析法【知识要求】1.目的故障假设分析的目的是识别危险有害因素并提出由此可能产生的意想不到的结果(具体事故事件)。
通常由经验丰富的人员完成并根据存在的安全措施等条件提出降低危险性的建议(对识别出的潜在事故状况不进行分级,不能定量化)。
该方法包括检查设计、安装、技改或操作过程中可能产生的偏差。
要求评价人员对工艺规程熟知,并对可能导致事故的设计偏差进行整合。
2.评价的方法和结果故障假设分析过程简单,首先提出一系列问题,然后回答这些问题。
一般采用表格形式完成。
表格的主要内容包括:提出的问题,回答可能的后果、安全措施、降低或消除危险性的安全措施(具体方法或方案等)。
(这种方法其实是用一种故障假设的思路原理,即以经验丰富的专业人员针对评价对象(设备、系统、工艺过程)的某些环节、因素、部位、时段等,假设性的提出可能发生那些故障,以识别危险有害因素可能导致的后果,采取相应的防范对策措施。
)3.所需要的资料和条件要求由于故障假设分析方法较为灵活,它可以用于工程、系统的任何阶段,因此,与工艺过程有关的资料都有可能用到,对工艺的具体过程,一般2~3名评价人员即可完成。
对复杂工艺,可将工艺分成若干部分,分块处理。
二、通过案例学会使用故障假设分析法…【能力要求】P112~118对某化工企业的“氯乙烯单体产品的生产进行安全评价”。
故障假设分析法的分析评价过程:1.项目基本情况简介(教材P112)(应给参加的专家发资料) “·············对氯乙烯单体产品的生产进行安全评价。
”2.生产工艺简介(教材P113)工艺过程、工艺方法概述性简介。
(介绍资料中应有工艺流程图和主要设备设施的概述性介绍)原资料有以下内容:·生产工艺过程(该事例的原资料有以下内容):乙烯氯气 图: VCM 生产工艺流程图·氯乙烯VCM 主要原料、中间体和产品:(教材P113,表2-12) ·氯乙烯单体生产中使用化学品主要特性(P113~114,表2-13) ·另外,还应准备一些必要的参考资料(如化学工程手册、危险物品消防手册···等)3.研究准备(教材P114)(1)组织评价小组。
安全工程师《生产管理》:常用安全评价方法全考点

安全工程师《生产管理》:常用安全评价方法全考点(-)按安全评价结果的量化程度分类法按安全评价结果的量化程度,安全评价方法可分为定性安全评价方法和定量安全评价方法。
1 .定性安全评价方法属于定性安全评价方法的有安全检查表、专家现场询问观察法、因素图分析法、事故引发和发展分析、作业条件危险性评价法(格雷厄姆-金尼法或1EC法)、故障类型和影响分析、危险可操作性研究等。
2 .定量安全评价方法按照安全评价给出的定量结果的类别不同,定量安全评价方法还可以分为:概率风险评价法、伤害(或破坏)范围评价法、危险指数评价法。
二、常用的安全评价方法(一)安全检查表方法(SCA)(1)安全检查表主要有以下优点:①检查项日系统、完整,可以做到丕遗逼任何能导致危险的关键因素,避免传统的安全检蛰中的易发生的疏忽、遗漏等弊端,因而能保证安全检查的质量。
②可以根据已有的规章制度、标准、规程等,检查执行情况,得出准确的评价。
③安全检查表可采用提问的方式,有问有答,给人的印象深刻,能使人知道如何做才是正确的,因而可起到安全教育的作用。
④编制安全检查表的过程本身就是一个系统安全分析的过程,可使检查人员对系统的认识更深刻,更便于发现危险因素。
⑤对不同的检查对象、检查目的有不同的检蛰表,应用范围Γo (2)安全检查表缺点:针对不同的需要,须事先编制大量的检查表,工作量大且安全检查表的质量受编制人员的知识水平和经验影响。
(二)危险指数方法(RR)危险指数评价可以运用在工程项目的各个阶段(可行性研究、设计、运行等),可以在详细的设计方案完成之前运用,也可以在现有装置危险分析计划制定之前运用;也可用于在役装置,作为确定工艺及操作危险性的依据。
(三)预先危险分析方法(PHA)预先危险分析方法是一项实现系统安全危害分析的初步或初始工作,在设计、施工和生产前,首先对系统中存在的危险性类别、出现条件、导致事故的后果进行分析,目的是识别系统中的潜在危险,确定危险等级,防止危险发展成事故。
故障假设分析方

故障假设分析方在实际的软件开发、维护和运维过程中,故障难以避免。
正确认识和处理故障,对于尽快恢复系统功能,提高系统的可靠性和可维护性具有非常重要的意义。
而故障假设分析方案则是一种有效的故障分析方法,能够帮助系统管理员和开发人员对故障进行深层次的分析和定位,并提出高效的解决方案。
什么是故障假设分析故障假设分析是一种常用的故障分析方法,它通过对系统中各种可能会造成故障的情况进行假设,然后根据实际情况来验证假设的有效性,最终找到故障的原因。
在实际的系统开发和维护中,故障假设分析通常要结合日志分析、监控数据分析、系统架构分析等各种分析方法。
故障假设分析可以较为全面地对系统功能进行分析,帮助我们预测故障、发现故障,并可以进行较为精准的定位和处理。
同时,故障假设分析还可以有效地帮助我们改进系统设计和优化系统架构。
故障假设分析的步骤故障假设分析通常需要分为以下几个步骤:1.收集故障信息:在故障发生后,首先要及时收集相关的故障信息,包括故障现象、故障日志、错误代码、系统监控数据等。
2.列出可能的故障假设:根据故障信息,列出一系列可能的故障假设,并进行分类和优先级排序。
3.根据假设逐一验证:针对每一个故障假设,进行相应的验证和测试,目的是找到故障的真正原因。
4.找到故障原因:通过不断的验证和测试,最终找到故障的原因,并进行相应的处理和修复。
5.总结故障分析过程:对故障分析过程进行总结和归纳,总结故障分析的经验和教训,以便今后遇到类似问题时能够更加快速地解决。
故障假设分析的优缺点故障假设分析的优点主要包括:•能够对系统进行全面的分析,能够找到隐藏的故障;•能够提高系统的可靠性和可维护性,避免故障的反复出现;•能够对系统进行改进和优化,提高系统性能和健壮性。
故障假设分析的缺点主要包括:•故障假设分析需要一定的技术实力和经验,需要对系统的结构和机制有较为深入的了解;•故障假设分析需要大量的时间和人力投入,需要进行跨部门的合作和协同;•故障假设分析需要较为系统的故障分析流程和方法,需要进行规范化的管理和标准化的实施。
安全评价方法有哪些

安全评价方法有哪些任何一项工作都讲究方法,那么安全评价的方法有哪些呢?我们一起来了解了解!1 安全检查方法(Safety Review,SR)安全检查方法可以说是第一个安全评价方法,它有时也称为工艺安全审查或“设计审查”及“损失预防审查”。
它可以用于建设项目的任何阶段。
对现有装置(在役装置)进行评价时,传统的安全检查主要包括巡视检查、正规日常检查或安全检查。
(例如,如果工艺尚处于设计阶段,设计项目小组可以对一套图纸进行审查。
)安全检查方法的目的是辨识可能导致事故、引起伤害、重要财产损失或对公共环境产生重大影响的装置条件或操作规程。
一般安全检查人员主要包括与装置有关的人员,即操作人员、人员、工程师、管理人员、安全员等等,具体视工厂的组织情况而定。
安全检查目的是为了提高整个装置的安全操作度,而不是干扰正常操作或对发现的问题进行处罚。
完成了安全检查后,评价人员对亟待改进的地方应提出具体的措施、建议。
2 安全检查表方法(Safety Checklist Analysis,SCA)为了查找工程、系统中各种设备设施、物料、工件、操作、管理和组织措施中的危险、有害因素,事先把检查对象加以分解,将大系统分割成若干小的子系统,以提问或打分的形式,将检查项目列表逐项检查,避免遗漏,这种表称为安全检查表。
3 危险指数方法(Risk Rank,RR)危险指数方法是一种评价方法。
通过评价人员对几种工艺现状及运行的固有属性(以作业现场危险度、事故几率和事故严重度为基础,对不同作业现场的危险性进行鉴别)进行比较计算,确定工艺危险特性重要性大小,并根据评价结果,确定进一步评价的对象。
危险指数评价可以运用在工程项目的各个阶段(可行性研究、设计、运行等),或在详细的设计方案完成之前,或在现有装置危险分析计划制定之前。
当然它也可用于在役装置,作为确定工艺及操作危险性的依据。
目前已有好几种危险等级方法得到广泛的应用。
此方法使用起来可繁可简,形式多样,既可定性,又可定量。
常用安全风险评估方式方法

常用安全风险评估方式方法一、定性评估法。
也称经验评估法,是按生产系统或生产工艺过程,对系统中存在的各种危险危害因素进行定性的分析、研究、评估,得出定性评估结论的评估方法。
本方法通常采用安全评估表,根据经验将需要检查评估的内容以列表的方式逐项列出,现场逐条对应评估。
安全评估表内容还可根据项目危险程度,将评估项目内容划分为安全否决项(不可控危险)和可控项(中等或可控危险)两部分,存在否决项时,停止评估,向上一级管理层报告;不存在否决项时,对可控项进行赋值,得分不低于规定的临界值,定性为具备安全建设条件;可控项得分低于临界值,停止作业,制定措施进行整改,整改完毕后再进行重新评估。
本方法适用于简单系统、大型装备,工作条件和环境相对稳定的区队开工和岗位的评估。
二、专业评估法。
是指集体检查分析、专业综合评估或两者相结合的评估方式,依据现场条件、检测结果、临界指标,运用类比分析等方法,对系统运行环境、设备设施、工艺和人员技术能力、安全措施、制度、管理水平等方面进行评估的方法。
本方法适用于复杂的系统、工艺、装置以及“四新”试验应用等方面的评估。
三、危险与可操作性分析法。
是通过分析生产运行过程中工艺状态参数的变动和操作控制中可能出现的偏差,以及这些变动与偏差对系统的影响及可能导致的后果,找出出现变动及偏差的原因,明确装置或系统内及建设过程中存在的主要危险、危害因素,并针对变动与偏差产生的后果提出应对安全措施的评估方法。
本方法主要分析步骤是:1.建立研究组,确定任务、研究对象。
一是建立一个有多方面专业组成的研究组,研究组的人员应包括设计、管理、使用和监察等各方面人员。
二是明确研究组的任务,如研究的最终目的是解决系统安全问题,还是产品问题、环境问题,或者是综合问题。
三是充分了解分析对象,准备有关资料。
2.划分单元,明确功能。
将分析对象划分为若干单元,明确各单元的功能,说明其运行状态和过程。
在连续过程中单元应以管道为主,在间歇过程中单元应以设备为主。
危害因素的辨识与风险评价

辩识方法辩识危害因素的辨识方法采取一种或结合多种评估方法。
主要的评价方法有询问交谈、现场勘查、查阅有关记录、获取外部信息、平安检查〔SCL〕、工作危险源分析〔JHA〕、预先危害因素分析〔PHA〕、故障假说分析〔WI〕、失效模式与影响分析〔FMEA〕、危害与可操作性研究〔HAZOP〕。
危害因素辩识方法第一类危险源第一类危险源:系统中存在的、可能发生意外释放的各种能量或危险物质。
1、危险物质辨识:如氢气、原油、天然气、液化气、汽油、乙决、甲烷、煤油等可燃物质;硫化氢、一氧化碳、氯、氨、二氧化碳、氮气二氧化硫、甲醇等有毒物质;生产过程中使用的危险化学品。
2、能量辨识:辨识产生、供应能量和能量的载体。
包括以下几个方面:a.具的动能的各类机械运动部件、工件和人体及产生的机械性、动力性等振动部件。
b.具有势能的平台及坑、井、沟口处等场所上的人体和物体。
c.带电体的电能,包括雷电、静电;d.高温设备和管线的热外表、高温介质及剧烈热反响工艺装置的热能及低温介质所具有的冷量。
e.盛装具有能量的介质的压力容器。
f.机械性、动力性等噪声的声能。
g.化学反响的化学能。
h.紫外线、激光射频辐射,超高压电场等非电离辐射等。
第二类危险源第二类危险源:对第一类危险源控制设施和措施失控的状态和行为。
主要包括以下几个方面:1、控制设施和措施缺陷。
无控制设施和措施或控制设施不符合法律、法规、标准和设计标准等要求。
控制措施不好,起不到应有的作用。
2、人员失误:人的不平安行为中产生不良后果的行为。
3、管理缺陷:缺少规章制度、操作规程、工作职责不明确;组织不全;缺乏协调或协调不当、检查不及时、不到位;奖惩不清楚;培训不到位等。
4、作业环境和场所不良:引起设备故障或人员失误的温度、温度、风雨雪、照明、视野、噪声、扰动、通风换气,色彩、作业区环境不良等环境因素。
危险源识别方法简介一、工作危险源分析〔JHA〕:是一种较细致地分析工作过程中存在危险源的方法,把一项工作活动分解成几个步骤,识别每一步骤中的危险源和可能的事故,设法消除危险源。
故障假设分析方

故障假设分析方故障假设分析,也被称为故障树分析或故障模式和效果分析,是一种系统性的方法,用于评估可能的故障以及它们对系统的影响。
故障假设分析主要是通过构建逻辑树状结构来分析故障,并提供可行的解决方案来防止故障的发生或恢复已经发生的故障。
以下是故障假设分析的详细解释。
1. 确定故障在故障假设分析中,首先需要识别系统的故障点。
可以通过检查设备的技术手册、设备记录和运行数据来确定系统中的故障点。
这些信息还可以帮助识别故障的类型,例如设备故障、人为操作错误、设计缺陷等。
2. 构建逻辑树确定故障后,需要构建逻辑树状结构。
逻辑树是一种决策树状结构,它可以帮助分析人员归纳系统内的所有可能的故障因素。
例如,如果一个设备停止工作,则可能存在许多原因,例如电源故障、系统软件错误或传感器故障等。
每个可能原因都是逻辑树的一个节点,系统内的所有其他因素均被连接到该节点。
这个过程将建立一个完整的故障树,展示系统中每个可能的故障因素。
3. 分析故障假设一旦故障树建立完成,需要对每个故障假设进行详细分析。
针对每个假设,需要考虑它是否是合理的,是否可能发生,并且必须考虑可能导致故障的所有因素。
如果该假设是合理的,则将其标记为“绿色”,如果它不切实际或不可能,将其标记为“红色”。
如果假设可能存在,但是需要进一步分析来确定其可能性,则将其标记为“黄色”。
4. 制定解决方案完成故障分析后,需要制定解决方案来预防未来的故障或解决当前的问题。
这些解决方案应包括进行预防性维护、设计更好的系统组件、更宽泛的培训教育等。
通过实施这些解决方案,可以减少出现故障的机率,降低系统维护成本以及提高整个系统的可靠性。
总之,故障假设分析是一种有助于分析系统故障原因和制定解决方案的强有力方法。
通过构建故障树和分析可能的故障原因,可以帮助维护团队寻找设置预防性措施的最佳方案。
关于故障假设分析

关于故障假设分析1方法概述故障假设分析(What…If Analysis)方法是对某一生产过程或工艺过程的创造性分析方法。
使用该方法时,要求人员应对工艺熟悉,通过提出一系列“如果……怎么办?”的问题,来发现可能和潜在的事故隐患从而对系统进行彻底检查的一种方法。
故障假设分析通常对工艺过程进行审查,一般要求评价人员用“What…If”作为开头对有关问题进行考虑,从进料开始沿着流程直到工艺过程结束。
任何与工艺有关的问题,即使它与之不太相关也可以提出加以讨论。
故障假设分析结果将找出暗含在分析组所提出的问题和争论中的可能事故情况。
这些问题和争论常常指出了故障发生的原因。
通常要将所有的问题记录下来,然后进行分类。
该方法包括检查设计、安装、技改或操作过程中可能产生的偏差。
要求评价人员对工艺规程熟知,并对可能导致事故的设计偏差进行整合。
2故障假设分析步骤故障假设分析很简单,它首先提出一系列问题,然后再回答这些问题。
评价结果一般以表格的形式显示,主要内容包括:提出的问题,回答可能的后果,降低或消除危险性的安全措施。
故障假设分析法由三个步骤组成,即分析准备、完成分析、编制结果文件。
(1)分析准备①人员组成。
进行该分析应由2~3名专业人员组成小组。
要求成员要熟悉生产工艺,有评价危险经验。
②确定分析目标。
首先要考虑的是取什么样的结果作为目标,目标又可以进一步加以限定。
目标确定后就要确定分析哪些系统。
在分析某一系统时应注意与其他系统的相互作用,避免遗漏掉危险因素。
③资料准备。
进行分析时,(2)完成分析①了解情况,准备故障假设问题。
分析会议开始应该首先由熟悉整个装置和工艺的人员阐述生产情况和工艺过程,包括原有的安全设备及措施。
参加人员还应该说明装置的安全防范、安全设备、卫生控制规程。
分析人员要向现场操作人员提问,然后对所分析的过程提出有关安全方面的问题。
有两种会议方式可以采用。
一种是列出所有的安全项目和问题,然后进行分析;另一种是提出一个问题讨论一个问题,即对所提出的某个问题的各个方面进行分析后再对分析组提出的下一个问题(分析对象)进行讨论。
故障假设分析法

1. 方法概述故障假设分析(What…If Analysis)方法是对某一生产过程或工艺过程的创造性分析方法。
使用该方法时,要求人员应对工艺熟悉,通过提出一系列“如果……怎么办?”的问题,来发现可能和潜在的事故隐患从而对系统进行彻底检查的一种方法。
故障假设分析通常对工艺过程进行审查,一般要求评价人员用“What…If”作为开头对有关问题进行考虑,从进料开始沿着流程直到工艺过程结束。
任何与工艺有关的问题,即使它与之不太相关也可以提出加以讨论。
故障假设分析结果将找出暗含在分析组所提出的问题和争论中的可能事故情况。
这些问题和争论常常指出了故障发生的原因。
通常要将所有的问题记录下来,然后进行分类。
该方法包括检查设计、安装、技改或操作过程中可能产生的偏差。
要求评价人员对工艺规程熟知,并对可能导致事故的设计偏差进行整合。
2故障假设分析步骤故障假设分析很简单,它首先提出一系列问题,然后再回答这些问题。
评价结果一般以表格的形式显示,主要内容包括:提出的问题,回答可能的后果,降低或消除危险性的安全措施。
故障假设分析法由三个步骤组成,即分析准备、完成分析、编制结果文件。
(1)分析准备①人员组成。
进行该分析应由2~3名专业人员组成小组。
要求成员要熟悉生产工艺,有评价危险经验。
②确定分析目标。
首先要考虑的是取什么样的结果作为目标,目标又可以进一步加以限定。
目标确定后就要确定分析哪些系统。
在分析某一系统时应注意与其他系统的相互作用,避免遗漏掉危险因素。
③资料准备。
进行分析时,(2)完成分析①了解情况,准备故障假设问题。
分析会议开始应该首先由熟悉整个装置和工艺的人员阐述生产情况和工艺过程,包括原有的安全设备及措施。
参加人员还应该说明装置的安全防范、安全设备、卫生控制规程。
分析人员要向现场操作人员提问,然后对所分析的过程提出有关安全方面的问题。
有两种会议方式可以采用。
一种是列出所有的安全项目和问题,然后进行分析;另一种是提出一个问题讨论一个问题,即对所提出的某个问题的各个方面进行分析后再对分析组提出的下一个问题(分析对象)进行讨论。
常用安全风险评估方式方法

常用安全风险评估方式方法一、定性评估法。
也称经验评估法,是按生产系统或生产工艺过程,对系统中存在的各种危险危害因素进行定性的分析、研究、评估,得出定性评估结论的评估方法。
本方法通常采用安全评估表,根据经验将需要检查评估的内容以列表的方式逐项列出,现场逐条对应评估。
安全评估表内容还可根据项目危险程度,将评估项目内容划分为安全否决项(不可控危险)和可控项(中等或可控危险)两部分,存在否决项时,停止评估,向上一级管理层报告;不存在否决项时,对可控项进行赋值,得分不低于规定的临界值,定性为具备安全建设条件;可控项得分低于临界值,停止作业,制定措施进行整改,整改完毕后再进行重新评估。
本方法适用于简单系统、大型装备,工作条件和环境相对稳定的区队开工和岗位的评估。
二、专业评估法。
是指集体检查分析、专业综合评估或两者相结合的评估方式,依据现场条件、检测结果、临界指标,运用类比分析等方法,对系统运行环境、设备设施、工艺和人员技术能力、安全措施、制度、管理水平等方面进行评估的方法。
本方法适用于复杂的系统、工艺、装置以及“四新”试验应用等方面的评估。
三、危险与可操作性分析法。
是通过分析生产运行过程中工艺状态参数的变动和操作控制中可能出现的偏差,以及这些变动与偏差对系统的影响及可能导致的后果,找出出现变动及偏差的原因,明确装置或系统内及建设过程中存在的主要危险、危害因素,并针对变动与偏差产生的后果提出应对安全措施的评估方法。
本方法主要分析步骤是:1.建立研究组,确定任务、研究对象。
一是建立一个有多方面专业组成的研究组,研究组的人员应包括设计、管理、使用和监察等各方面人员。
二是明确研究组的任务,如研究的最终目的是解决系统安全问题,还是产品问题、环境问题,或者是综合问题。
三是充分了解分析对象,准备有关资料。
2.划分单元,明确功能。
将分析对象划分为若干单元,明确各单元的功能,说明其运行状态和过程。
在连续过程中单元应以管道为主,在间歇过程中单元应以设备为主。
危险源辨识方法

危险源辨识方法工作危险源分析是一种常用的危险源辨识方法,适用于日常作业活动、设备、设施、关键生产工艺过程、新建、扩建、改建及检维修、设备拆除等方面。
它主要采用询问交谈、现场观察、查阅有关记录等方式来辨识危险源。
二、预先危害因素分析(PHA):预先危害因素分析是一种适用于新建、扩建、改建等方面的危险源辨识方法。
它主要采用SCL、HAZOP、FMEA等方式来辨识危险源。
三、故障假说分析(WI):故障假说分析是一种适用于设备、设施方面的危险源辨识方法。
它主要采用现场勘查、查阅有关记录、WI等方式来辨识危险源。
四、失效模式与影响分析(FMEA):失效模式与影响分析是一种适用于设备、设施方面的危险源辨识方法。
它主要采用查阅有关记录、FMEA等方式来辨识危险源。
五、危害与可操作性研究(HAZOP):危害与可操作性研究是一种适用于关键生产工艺过程方面的危险源辨识方法。
它主要采用SCL、HAZOP等方式来辨识危险源。
六、第一类危险源:第一类危险源包括各种能量或危险物质,如可燃物质、有毒物质、危险化学品等。
能量方面包括动能、势能、电能、热能、化学能、非电离辐射等。
七、第二类危险源:第二类危险源包括对第一类危险源控制设施和措施失控的状态和行为,如控制设施和措施缺陷、人员失误、管理缺陷、作业环境和场所不良等。
危险源分析是一种详细分析工作过程中可能存在的危险源的方法。
该方法将工作活动分解成几个主要步骤,并识别每一步骤中的危险源和可能的事故,并设法消除危险源。
分析步骤包括观察工作、与操作者一起讨论研究、运用自己对这一项工作的知识以及结合上述三条。
对于每一步骤,需要问可能发生什么事故,并识别每一步骤的主要危险源后果。
然后识别现有安全控制措施,进行风险评价,并建议安全工作步骤。
安全检查表分析是一种基于经验的方法,用于识别与一般工艺设备和操作有关的已知类型的危险源、设计缺陷以及事故隐患。
分析步骤包括建立安全检查表,从有关渠道选择合适的安全检查表,如果无法获取相关的安全检查表,则需要运用自己的经验和可靠的参考资料制定检查表。
13种常用安全评价方法介绍.

13种常用安全评价方法介绍1 安全检查方法(Safety Review,SR安全检查方法可以说是第一个安全评价方法,它有时也称为工艺安全审查或“设计审查”及“损失预防审查”。
它可以用于建设项目的任何阶段。
对现有装置(在役装置进行评价时,传统的安全检查主要包括巡视检查、正规日常检查或安全检查。
(例如,如果工艺尚处于设计阶段,设计项目小组可以对一套图纸进行审查。
安全检查方法的目的是辨识可能导致事故、引起伤害、重要财产损失或对公共环境产生重大影响的装置条件或操作规程。
一般安全检查人员主要包括与装置有关的人员,即操作人员、维修人员、工程师、管理人员、安全员等等,具体视工厂的组织情况而定。
安全检查目的是为了提高整个装置的安全操作度,而不是干扰正常操作或对发现的问题进行处罚。
完成了安全检查后,评价人员对亟待改进的地方应提出具体的措施、建议。
2 安全检查表方法(Safety Checklist Analysis,SCA为了查找工程、系统中各种设备设施、物料、工件、操作、管理和组织措施中的危险、有害因素,事先把检查对象加以分解,将大系统分割成若干小的子系统,以提问或打分的形式,将检查项目列表逐项检查,避免遗漏,这种表称为安全检查表。
3 危险指数方法(Risk Rank,RR危险指数方法是一种评价方法。
通过评价人员对几种工艺现状及运行的固有属性(以作业现场危险度、事故几率和事故严重度为基础,对不同作业现场的危险性进行鉴别进行比较计算,确定工艺危险特性重要性大小,并根据评价结果,确定进一步评价的对象。
危险指数评价可以运用在工程项目的各个阶段(可行性研究、设计、运行等,或在详细的设计方案完成之前,或在现有装置危险分析计划制定之前。
当然它也可用于在役装置,作为确定工艺及操作危险性的依据。
目前已有好几种危险等级方法得到广泛的应用。
此方法使用起来可繁可简,形式多样,既可定性,又可定量。
例如,评价者可依据作业现场危险度、事故几率、事故严重度的定性评估,对现场进行简单分级,或者,较为复杂的,通过对工艺特性赋予一定的数值组成数值图表,可用此表计算数值化的分级因子,常用评价方法有:①危险度评价;②道化学火灾、爆炸危险指数法;③蒙德法;④化工厂危险等级指数法;⑤其他的危险等级评价法。
13种常用安全评价方法介绍
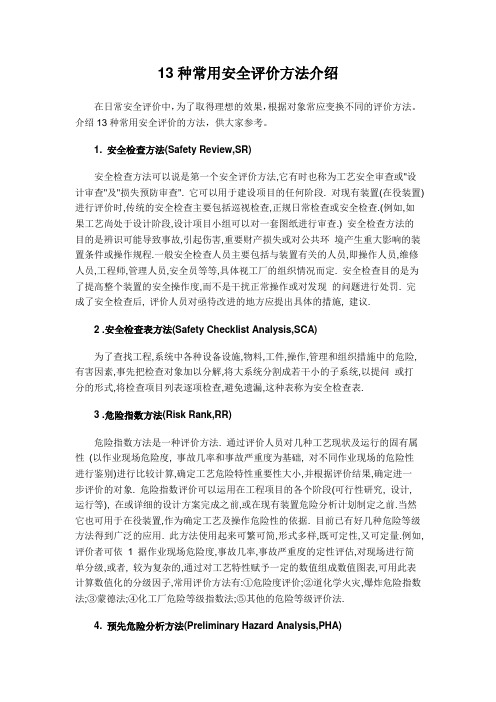
13种常用安全评价方法介绍在日常安全评价中,为了取得理想的效果,根据对象常应变换不同的评价方法。
介绍13种常用安全评价的方法,供大家参考。
1. 安全检查方法(Safety Review,SR)安全检查方法可以说是第一个安全评价方法,它有时也称为工艺安全审查或"设计审查"及"损失预防审查". 它可以用于建设项目的任何阶段. 对现有装置(在役装置)进行评价时,传统的安全检查主要包括巡视检查,正规日常检查或安全检查.(例如,如果工艺尚处于设计阶段,设计项目小组可以对一套图纸进行审查.) 安全检查方法的目的是辨识可能导致事故,引起伤害,重要财产损失或对公共环境产生重大影响的装置条件或操作规程.一般安全检查人员主要包括与装置有关的人员,即操作人员,维修人员,工程师,管理人员,安全员等等,具体视工厂的组织情况而定. 安全检查目的是为了提高整个装置的安全操作度,而不是干扰正常操作或对发现的问题进行处罚. 完成了安全检查后, 评价人员对亟待改进的地方应提出具体的措施, 建议.2 .安全检查表方法(Safety Checklist Analysis,SCA)为了查找工程,系统中各种设备设施,物料,工件,操作,管理和组织措施中的危险,有害因素,事先把检查对象加以分解,将大系统分割成若干小的子系统,以提问或打分的形式,将检查项目列表逐项检查,避免遗漏,这种表称为安全检查表.3 .危险指数方法(Risk Rank,RR)危险指数方法是一种评价方法. 通过评价人员对几种工艺现状及运行的固有属性(以作业现场危险度, 事故几率和事故严重度为基础, 对不同作业现场的危险性进行鉴别)进行比较计算,确定工艺危险特性重要性大小,并根据评价结果,确定进一步评价的对象. 危险指数评价可以运用在工程项目的各个阶段(可行性研究, 设计, 运行等), 在或详细的设计方案完成之前,或在现有装置危险分析计划制定之前.当然它也可用于在役装置,作为确定工艺及操作危险性的依据. 目前已有好几种危险等级方法得到广泛的应用. 此方法使用起来可繁可简,形式多样,既可定性,又可定量.例如,评价者可依1 据作业现场危险度,事故几率,事故严重度的定性评估,对现场进行简单分级,或者, 较为复杂的,通过对工艺特性赋予一定的数值组成数值图表,可用此表计算数值化的分级因子,常用评价方法有:①危险度评价;②道化学火灾,爆炸危险指数法;③蒙德法;④化工厂危险等级指数法;⑤其他的危险等级评价法.4. 预先危险分析方法(Preliminary Hazard Analysis,PHA)预先危险分析方法是一种起源于美国军用标准安全计划要求方法.主要用于对危险物质和装置的主要区域等进行分析,包括设计,施工和生产前,首先对系统中存在的危险性类别,出现条件,导致事故的后果进行分析,其目的是识别系统中的潜在危险,确定其危险等级,防止危险发展成事故. 预先危险分析可以达到以下4个目的:①大体识别与系统有关的主要危险;②鉴别产生危险原因;③预测事故发生对人员和系统的影响;④判别危险等级,并提出消除或控制危险性的对策措施. 预先危险分析方法通常用于对潜在危险了解较少和无法凭经验觉察的工艺项目的初期阶段.通常用于初步设计或工艺装置的R&D(研究和开发),当分析一个庞大现有装置或当环境无法使用更为系统的方法时,常优先考虑PHA 法.5 .故障假设分析方法(What…If,W1)故障假设分析方法是一种对系统工艺过程或操作过程的创造性分析方法.使用该方法的人员应对工艺熟悉, 通过提问(故障假设)的方式来发现可能的潜在的事故隐患(实际上是假想系统中一旦发生严重的事故, 找出促成事故的有潜在因素, 在最坏的条件下,这些导致事故的可能性). 与其他方法不同的是,要求评价人员了解基本概念并用于具体的问题中,有关故障假设分析方法及应用的资料甚少,但是它在工程项目发展的各个阶段都可能经常采用. 故障假设分析方法一般要求评价人员用"What…if"作为开头,对有关问题进行考虑.任何与工艺安全有关的问题,即使它与之不太相关,也可提出加以讨论.例如: 提供的原料不对,如何处理? 如果在开车时泵停止运转,怎么办? 如果操作工打开阀B 而不是阀A,怎么办? 2 通常,将所有的问题都记录下来,然后将问题分门别类,例如:按照电气安全,消防,人员安全等问题分类,分头进行讨论.对正在运行的现役装置,则与操作人员进行交谈,所提出的问题要考虑到任何与装置有关的不正常的生产条件,而不仅仅是设备故障或工艺参数数的变化.6 .故障假设分析/检查表分析方法(What…If/Checklist Analysis,W1/CA)故障假设分析方法/检查表分析方法是由具有创造性的假设分析方法与安全检查表分析方法组合而成的,它弥补了单独使用时各自的不足. 例如:安全检查表分析方法是一种以经验为主的方法,用它进行安全评价时,成功与否很大程度取决于检查表编制人员的经验水平. 如果检查表编制的不完整, 评价人员就很难对危险性状况作有效的分析.而故障假设分析方法鼓励评价人员思考潜在的事故和后果,它弥补了检查表编制时可能存在的经验不足;相反,检查表这部分把故障假设分析方法更系统化. 故障假设分析/检查表分析方法可用于工艺项目的任何阶段. 与其他大多数的评价方法相类似, 这种方法同样需要有丰富工艺经验的人员完成, 常用于分析工艺中存在的最普遍的危险.虽然它也能够用来评价所有层次的事故隐患, 但故障假设分析/检查表分析一般主要对过程危险初步分析, 然后可用其他方法进行更详细的评价.7. 危险和可操作性研究(Hazard and Operability Study,HAZOP) HAZOP是一种定性的安全评价方法,基本过程以引导词为引导,找出过程中工艺状态的变化(即偏差),然后分析找出偏差的原因,后果及可采取的对策. 危险和可操作性研究技术是基于这样一种原理,即,背景各异的专家们若在一起工作,就能够在创造性,系统性和风格上互相影响和启发,能够发现和鉴别更多的问题,要比他们独立工作并分别提供工作结果更为有效.虽然危险和可操作性研究技术起初是专门为评价新设计和新工艺而开发的,但是这一技术同样可以用于整个工程, 系统项目生命周期的各个阶段. 危险和可操作性分析的本质,就是通过系列会议对工艺流程图和操作规程进行分析, 由各种专业人员按照规定的方法对偏离设计的工艺条件进行过程危险和可操作性研究, 是帝国化学工业公司(ICI, 英国)最早确定要由一个多方面人员组成的小组执行3 危险和可操作性研究工作的.鉴于此,虽然某一个人也可能单独使用危险与可操作性分析方法,但这绝不能称为危险和可操作性分析.所以,危险和可操作性分析技术与其他安全评价方法的明显不同之处是其他方法可由某人单独去做, 而危险和可操作性分析则必须由一个多方面的,专业的,熟练的人员组成的小组来完成.8 .故障类型和影响分析(Failure Mode Effects Analysis,FMEA)故障类型和影响分析(FMEA)是系统安全工程的一种方法,根据系统可以划分为子系统,设备和元件的特点,按实际需要将系统进行分割,然后分析各自可能发生的故障类型及其产生的影响,以便采取相应的对策,提高系统的安全可靠性. (1)故障.元件,子系统,系统在运行时,达不到设计规定的要求,因而完不成规定的任务或完成的不好.(2)故障类型系统, 子系统或元件发生的每一种故障的形式称为故障类型. 例如: 一个阀门故障可以有 4 种故障类型,即内漏,外漏,打不开,关不严. (3)故障等级. 根据故障类型对系统或子系统影响的程度不同而划分的等级称为故障等级. 列出设备的所有故障类型对一个系统或装置的影响因素,这些故障模式对设备故障进行描述(开启,关闭,泄漏等),故障类型的影响由对设备故障有系统影响确定. FMEA 辨识可直接导致事故或对事故有重要影响的单一故障模式.在FMEA中不直接确定人的影响因素,但像人失误操作影响通常作为一设备故障模式表示出来.一个FMEA 不能有效地辨识引起事故的详尽的设备故障组合.9 .故障树分析(Fault Tree Analysis,FTA)故障树(Fault Tree)是一种描述事故因果关系的有方向的"树",是安全系统工程中的重要的分析方法之一.它能对各种系统的危险性进行识别评价,既适用于定性分析,又能进行定量分析.具有简明,形象化的特点,体现了以系统工程方法研究安全问题的系统性,准确性和预测性.FTA 作为安全分析评价和事故预测的一种先进的科学方法,已得到国内外的公认和广泛采用. 20世纪60 年代初期美国贝尔电话研究所为研究民兵式导弹发射控制系统的安全性问题开始对故障树进行开发研究, 为解决导弹系统偶然事件的预测问题作出了贡献. 随之波音公司的科研人员进一步发展了FTA 方法, 使之在航空航天工业方面得到应用. 4 60 年代中期,FTA 由航空航天工业发展到以原子能工业为中心的其他产业部门.1974 年美国原子能委员会发表了关于核电站灾害性危险性评价报告——拉斯姆逊报告,对FTA 作了大量和有效的应用,引起了全世界广泛的关注,目前此种方法已在许多工业部门得到运用. FTA 不仅能分析出事故的直接原因,而且能深入提示事故的潜在原因,因此在工程或设备的设计阶段, 在事故查询或编制新的操作方法时, 都可以使用FTA 对它们的安全性作出评价. 日本劳动省积极推广FTA 方法, 并要求安全干部学会使用该种方法. 从1978 年起,我国开始了FTA 的研究和运用工作.实践证明FTA 适合我国国情, 应该在我国得到普遍推广使用.10 .事件树分析(Event Tree Analysis,ETA)事件树分析是用来分析普诵设备故障或过程波动(称为初始事件)导致事故发生的可能性. 事故是典型设备故障或工艺异常(称为初始事件)引发的结果. 与故障树分析不同, 事件树分析是使用归纳法(而不是演绎法), 事件树可提供记录事故后果的系统性的方法,并能确定导致事件后果事件与初始事件的关系. 事件树分析适合被用来分析那些产生不同后果的初始事件. 事件树强调的是事故可能发生的初始原因以及初始事件对事件后果的影响,事件树的每一个分支都表示一个独立的事故序列,对一个初始事件而言,每一独立事故序列都清楚地界定了安全功能之间的功能关系.11. 人员可靠性分析(Human Reiliability Analysis,HRA)人员可靠性行为是人机系统成功的必要条件, 人的行为受很多因素影响. 这些"行为成因要素" (Performance Shoping Factors PSFs)可以是人的内在属性,比如紧张, 情绪,教养和经验;也可以是外在因素,比如工作间,环境,监督者的举动,工艺规程和硬件界面等.影响人员行为的PSFs 数不胜数.尽管有些PSFs 是不能控制的,许多却是可以控制的,可以对一个过程或一项操作的成功或失败产生明显的影响. 例如: 评价人员可以把人为失误考虑进故障树之中去, 一项"如果……怎么办"/ 检查表分析可以考虑这种情况——在异常状况下,操作人员可能将本应关闭的阀门打开了.典型的危险和可操作性研究(HAZOP)通常也把操作人员失误作为工艺失常(偏差) 5 的原因考虑进去. 尽管这些安全评价技术可以用来寻找常见的人为失误, 但它们还是主要集中于引发事故的硬件方面.当工艺过程中手工操作很多时,或者当人一机界面很复杂,难以用标准的安全评价技术评价人为失误时,就需要特定的方法去评估这些人为因素. 人为因素是研究机器设计,操作,作业环境以及它们与人的能力,局限和需求如何协调一致的学科.有许多不同的方法可供人为因素专家用来评估工作情况.一种常用的方法叫做"作业安全分析"(Job Safety Analysis,JSA),但该方法的重点是作业人员的个人安全.JSA 是一个良好的开端,但就工艺安全分析而言,人员可靠性分析方法更为有用.人员可靠性分析技术可被用来识别和改进PSFs,从而减少人为失误的机会.这种技术分析的是系统,工艺过程和操作人员的特性,识别失误的源头. 不与整个系统的分析相结合而单独使用HRA 技术的话,似乎是太突出人的行为而忽视了设备特性的影响.如果上述系统是一个已知易于由人为失误引起事故的系统, 这样做就不合适了.所以,在大多数情况下,建议将HRA 方法与其他安全评价方法结合使用.一般来说,HRA 技术应该在其他评价技术(如HAZOP,FMEA,FTA)之后使用, 识别出具体的,有严重后果的人为失误.12. 作业条件危险性评价法(Job Risk Analysis,LEC)美国的KJ格雷厄姆(Keneth.J.Graham)和GF金尼(Gilbert.F.Kinney) 研究了人们在具有潜在危险环境中作业的危险性,提出了以所评价的环境与某些作为参考环境的对比为基础,将作业条件的危险性作因变量(D),事故或危险事件发生的可能性(L),暴露于危险环境的频率(正)及危险严重程度(C)为自变量,确定了它们之间的函数式.根据实际经验,他们给出了3 个自变量的各种不同情况的分数值,采取对所评价的对象根据情况进行"打分"的办法, 然后根据公式计算出其危险性分数值, 再在按经验将危险性分数值划分的危险程度等级表或图上查出其危险程度的一种评价方法.这是一种简单易行的评价作业条件危险性的方法.13 .定量风险评价法(Quantity Risk Analysis,QRA)在识别危险分析方面, 定性和半定量的评价是非常有价值的, 但是这些方法仅是定性的,不能提供足够的定量化,特别是不能对复杂的并存在危险的工业流程等提供决策的依据和足够的信息,在这种情况下,必须能够提供完全的定量的计算和评价.6 定量风险评价可以将风险的大小完全量化,风险可以表征为事故发生的频率和事故的后果的乘积.QRA 对这两方面均进行评价,并提供足够的信息,为业主,投资者,政府管理者提供有利的定量化的决策依据. 对于事故后果模拟分析,国内外有很多研究成果,如美国,英国,德国等发达国家,早在20 世纪80 年代初便完成了以Burro,Coyote,Thorney Island 为代表的一系列大规模现场泄漏扩散实验. 到了90 年代, 又针对毒性物质的泄漏扩散进行了现场实验研究.迄今为止,已经形成了数以百计的事故后果模型,如著名的DEGADIS, ALOHA,SLAB,TRACE,ARCHIE等.基于事故模型的实际应用也取得了发展,如DNV 公司的SAFETY Ⅱ软件是一种多功能的定量风险分析和危险评价软件包,包含多种事故模型,可用于工厂的选址,区域和土地使用决策,运输方案选择,优化设计,提供可接受的安全标准.Shell Global Solution 公司提供的Shell FRED,Shell SCOPE 和Shell Shepherd 3 个序列的模拟软件涉及泄漏,火灾,爆炸和扩散等方面的危险风险评价软件.这些软件都是建立在大量实验的基础上得出的数学模型,有着很强的可信度. 评价的结果用数字或图形的方式显示事故影响区域, 以及个人和社会承担的风险. 可根据风险的严重程度对可能发生的事故进行分级,有助于制定降低风险的措施.。
常用的安全评价方法

常用的安全评价方法(1)安全检查表方法(Safety Checklist Analysis,SCA)为了查找工程、系统中各种设备设施、物料、工件、操作、管理和组织措施中的危险、有害因素、事先把检查对象加以分解,将大系统分割成若干小的子系统,以提问或打分的形式,将检查项目列表逐项检查,避免遗漏,这种表称为安全检查表,用安全检查表进行安全检查的方法称为安全检查表方法。
安全检查项目依据相关的标准、规范,以及工程、系统中已知的危险类别、设计缺陷、一般工艺设备、操作、管理有关的潜在危险性和有害性进行设置。
为了避免检查项目遗漏、事先把检查对象分割成若干系统,以提问或打分的形式,将检查项目列表。
安全检查表是系统安全工程的一种最基础、最简便、广泛应用的系统危险性评价方法。
安全检查表在我国不仅用于查找系统中各种潜在的事故隐患,还对各检查项目给予量化,用于进行系统安全评价。
(二)危险指数方法(Risk Bank,RR)危险指数方法是通过对几种工艺现状及运行的固有属性(以作业现场危险度、事故概率和事故严重度为基础,对不同作业现场的危险性进行鉴别)进行比较计算,确定工艺危险特性、重要性,并根据评价结果,确定需要进一步评价的对象的安全评价方法。
危险指数评价可以运用在工程项目的各个阶段(可行性研究、设计、运行等),可以在详细的设计方案完成之前运用,也可以在现有装置危险分析计划制定之前运用;也可用于在役装置,作为确定工艺及操作危险性的依据。
目前已有许多种危险指数方法得到广泛的应用,如危险度评价法、道化学公司的火灾、爆炸危险指数法,帝国化学工业公司(ICI)的蒙德法,日本化工企业六阶段评价法、化工厂危险等级指数法等。
(三)预先危险分析法(Preliminary Hazard Analysis,PHA)预先危险分析又称初步危险分析。
预先危险分析方法是一项实现系统安全危害分析的初步或初始工作,在设计、施工和生产前,首先对系统中存在的危险性类别、出现条件、导致事故的后果进行分析、目的是识别系统中的潜在危险、确定危险等级,防止危险发展成事故。
几种常见的安全评价方法
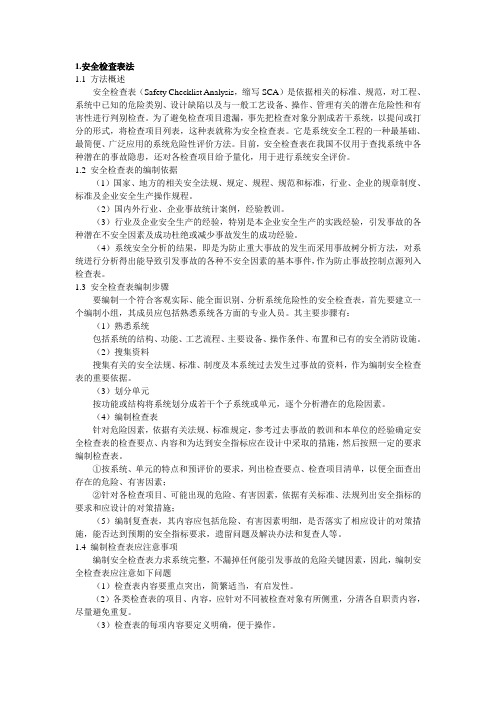
1.安全检查表法1.1 方法概述安全检查表(Safety Checklist Analysis,缩写SCA)是依据相关的标准、规范,对工程、系统中已知的危险类别、设计缺陷以及与一般工艺设备、操作、管理有关的潜在危险性和有害性进行判别检查。
为了避免检查项目遗漏,事先把检查对象分割成若干系统,以提问或打分的形式,将检查项目列表,这种表就称为安全检查表。
它是系统安全工程的一种最基础、最简便、广泛应用的系统危险性评价方法。
目前,安全检查表在我国不仅用于查找系统中各种潜在的事故隐患,还对各检查项目给予量化,用于进行系统安全评价。
1.2 安全检查表的编制依据(1)国家、地方的相关安全法规、规定、规程、规范和标准,行业、企业的规章制度、标准及企业安全生产操作规程。
(2)国内外行业、企业事故统计案例,经验教训。
(3)行业及企业安全生产的经验,特别是本企业安全生产的实践经验,引发事故的各种潜在不安全因素及成功杜绝或减少事故发生的成功经验。
(4)系统安全分析的结果,即是为防止重大事故的发生而采用事故树分析方法,对系统迸行分析得出能导致引发事故的各种不安全因素的基本事件,作为防止事故控制点源列入检查表。
1.3 安全检查表编制步骤要编制一个符合客观实际、能全面识别、分析系统危险性的安全检查表,首先要建立一个编制小组,其成员应包括熟悉系统各方面的专业人员。
其主要步骤有:(1)熟悉系统包括系统的结构、功能、工艺流程、主要设备、操作条件、布置和已有的安全消防设施。
(2)搜集资料搜集有关的安全法规、标准、制度及本系统过去发生过事故的资料,作为编制安全检查表的重要依据。
(3)划分单元按功能或结构将系统划分成若干个子系统或单元,逐个分析潜在的危险因素。
(4)编制检查表针对危险因素,依据有关法规、标准规定,参考过去事故的教训和本单位的经验确定安全检查表的检查要点、内容和为达到安全指标应在设计中采取的措施,然后按照一定的要求编制检查表。
故障假设分析

故障假设分析Company Document number:WTUT-WT88Y-W8BBGB-BWYTT-19998故障假设分析1 目的故障假设分析的目的是识别危险性、危险情况或可能产生的意想不到的结果的事故事件。
通常由经验丰富的人员识别可能发生的事故的情况、结果,提出降低危险性的安全措施。
(对识别出的潜在事故状况不进行分级,不能定量化) 该方法包括检查设计、安装、技改或操作过程中可能产生的偏差。
要求评价人员对工艺规程熟知,并对可能导致事故的设计偏差进行整合。
2 评价的结果故障假设分析很简单,它首先提出一系列问题,然后再回答这些问题。
评价结果一般以表格的形式显示,主要内容包括:提出的问题,回答可能的后果、安全措施、降低或消除危险性的安全措施。
3 所需要的资料和条件要求由于故障假设分析方法较为灵活,它可以用于工程、系统的任何阶段,因此与工艺过程有关的资料都有可能用到。
对工艺的具体过程进行分析,一般有2至3名评价人员即可完成。
对—个复杂工艺进行分析时,需尽可能的将复杂的工艺问题分解成若干个小块。
4 故障假设分析方法事例以下故障假设分析方法是参考美国化学工程师学会(CCPS)《危害评价过程指南》中有关故障假设分析方法的事例。
1)工艺中风险问题的提出背景下面是假定公司和装置的基本情况,并简单介绍了氯乙烯单体的生产工艺。
(1)公司和装置的基本情况。
某化工有限公司是美国一家大型联合化工企业,生产氯、烧碱、硫酸、盐酸等化学品。
某公司享有极高的安全信誉,在过去的59年里,始终保持安全生产。
某公司的许多技术人员都是国际上公认的化工产品生产和加工方面的专家。
基于众多原因,某公司决定将氯乙烯单体的生产能力扩大。
某公司决定在美国Anyuhere厂建一条工艺生产状况具有世界先进水平的VC朋生产线。
公司专门成立一个职能部门(筹建处)负责这项带有风险的三年投资计划。
作为公司安全生产管理的一部分,该公司将在适当的时间内,组织完成该装置的操作的安全评价研究工作。
常用安全风险评估方式方法2017.6
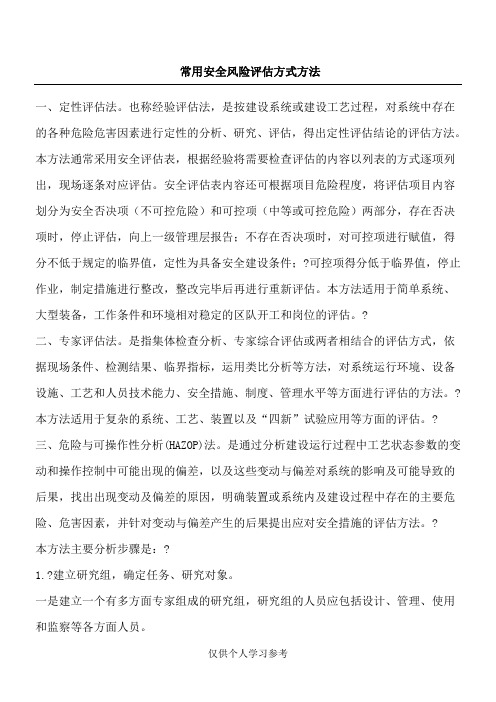
常用安全风险评估方式方法一、定性评估法。
也称经验评估法,是按建设系统或建设工艺过程,对系统中存在的各种危险危害因素进行定性的分析、研究、评估,得出定性评估结论的评估方法。
本方法通常采用安全评估表,根据经验将需要检查评估的内容以列表的方式逐项列出,现场逐条对应评估。
安全评估表内容还可根据项目危险程度,将评估项目内容??险、危害因素,并针对变动与偏差产生的后果提出应对安全措施的评估方法。
?本方法主要分析步骤是:?1.?建立研究组,确定任务、研究对象。
一是建立一个有多方面专家组成的研究组,研究组的人员应包括设计、管理、使用和监察等各方面人员。
二是明确研究组的任务,如研究的最终目的是解决系统安全问题,还是产品问题、环境问题,或者是综合问题。
三是充分了解分析对象,准备有关资料。
?2.?划分单元,明确功能。
将分析对象划分为若干单元,明确各单元的功能,说明其运行状态和过程。
在连续过程中单元应以管道为主,在间歇过程中单元应以设备为主。
?3.?4.?5.?1.2.?3.?4.??5.?制定预防事故发生的安全对策措施。
?本方法适用于固有系统中采取新的方法,接触新的物料、设备和设施的危险性评估。
?五、故障假设分析法(WI)。
是由熟悉工艺的人员对系统工艺过程或操作过程,通过提问(故障假设)的方式来发现可能的潜在的事故隐患(实际上是假想系统中一旦发生严重的事故,找出促成事故的潜在因素,在最坏的条件下,这些因素导致事故的可能性)的分析评估法。
?本方法适用于工程项目的各个阶段的评估。
?六、“五步”评估法。
是作业人员按照“停、想、评、定、做”五个步骤,对本岗位职责范围内的环境、设备、设施和自身上岗条件进行安全评估的方法。
本方法中。
07故障假设分析安全检查表分析1

分析程序
关键词
原因
与基准状态的偏差
结果
对策
故障树的顶
28
分析步骤
• (1)建立研究小组确定任务.研究对象 (群体分析方式)
• 首先应成立一个由设备、工艺、仪表控 制等工程技术人员、安全工作者、操作 工人等各方面专家组成的研究小组,并 确定一名具有丰富经验且掌握分析方法 的人员作为组长,以便确定分析点,引 导大家深人讨论。
4
故障假设分析方法(What…IF,WI)
• 分析步骤
• 1、分析准备 • ①人员组成: • ②确定分析目标: • ③资料准备 • ④为故障假设分析准备—些基本问
题,它们是分析会议的“种子”。
5
①人员组成
• 对工艺的具体过程进行分析,一般有2至3 名评价人员即可完成。
②确定分析目标
对—个复杂工艺进行分析时,需尽可能 的将复杂的工艺问题分解成若干个小块。
补短弥补各自单独使用时的不足。
10
§4.2 常用的安全评价方法
• 五、故障假设分析方法 (What…IF,WI)
• 举例分析: 生产磷酸氢二铵
(DAP)安全评价
•
在该工艺过程中,将磷酸溶
液与氨水溶液加入到带夹套的搅
拌反应釜中,使磷酸与氨反应生
成DAP。DAP是无任何危险的产品。
所 生 成 的 DAP 放 入 一 敞 开 储 槽 中 。
•
此法是一种定性的安全评价方法。其基本
过程是以关键词为引导,找出过程中工艺状态的
变化(即偏差),然后分析偏差产生的原因、后果
及可采取的对策。
23
分析原理
• 背景各异的专家们如若在一起工作,就能 够在创造性、系统性和风格上互相影响和 启发,能够发现和鉴别更多的问题,要比 他们独立工作并分别提供工作结果更为有 效。
- 1、下载文档前请自行甄别文档内容的完整性,平台不提供额外的编辑、内容补充、找答案等附加服务。
- 2、"仅部分预览"的文档,不可在线预览部分如存在完整性等问题,可反馈申请退款(可完整预览的文档不适用该条件!)。
- 3、如文档侵犯您的权益,请联系客服反馈,我们会尽快为您处理(人工客服工作时间:9:00-18:30)。
故障假设分析法1 概念定性分析。
是识别危险有害因素,并提出由此可能产生的意想不到的结果。
通常由经验丰富的人员完成,并根据存在的安全措施等条件提出降低危险性的建议。
2 基本方法介绍它首先提出一系列问题,然后再回答这些问题。
评价结果一般以表格的形式显示,主要内容包括:提出的问题,回答可能的后果,降低或消除危险性的安全措施。
故障假设分析法由三个步骤组成,即分析准备、完成分析、编制结果文件。
1)分析准备①人员组成。
进行该分析应由2〜3名专业人员组成小组。
要求成员要熟悉生产工艺,有评价危险经验。
② 确定分析目标。
首先要考虑的是取什么样的结果作为目标,目标又可以进一步加以限定。
目标确定后就要确定分析哪些系统。
在分析某一系统时应注意与其他系统的相互作用,避免遗漏掉危险因素。
③ 资料准备。
进行分析时,2)完成分析① 了解情况,准备故障假设问题。
分析会议开始应该首先由熟悉整个装置和工艺的人员阐述生产情况和工艺过程,包括原有的安全设备及措施。
参加人员还应该说明装置的安全防范、安全设备、卫生控制规程。
分析人员要向现场操作人员提问,然后对所分析的过程提出有关安全方面的问题。
有两种会议方式可以采用。
一种是列出所有的安全项目和问题,然后进行分析;另一种是提出一个问题讨论一个问题,即对所提出的某个问题的各 个方面进行分析后再对分析组提出的下一个问题(分析对象)进行讨论。
两种 方式都可以,但是通常最好是在分析之前列出所有的问题以免打断分析组的 “创 造性思维 ”。
② 按照准备好的问题,从工艺进料开始,一直进行到成品产出为止,逐一 提出如果发生那种情况,操作人员应该怎么办?分别得出正确答案。
3)编制结果文件3 适用范围故障假设分析法适用范围很广,可用于设备设计和操作的各个方面(比 如:建筑物、动力系统、原料、中间体、产品 ...)。
4 实例以下故障假设分析方法是参考美国化学工程师学会 (CCPS 《) 危害评价过程指 南》中有关故障假设分析方法的事例。
1)工艺中风险问题的提出背景由于故障假设分析不需要氯乙烯单体装置设计的详细资料,并且有识别和评价危险的显著活性,所以小组推荐采用故障假设分析技术。
评价小组由如下专家组成:作为氯气专家,已经主持或参与过多个不同的危险评价,包括故障化学专家 ——为帮助识别有害物和潜在化学品的相互影响,需要一位熟悉 氯气、盐酸、乙烯、二氯化乙烯、氯乙烯单体某化学品的专家。
A 先生将担任 这一职务。
氯气专家 ——氯气专家必须有生产氯气方面的经验。
来自某公司本地氯气装置的E 女士,已有10年的丰富经验,将担任这一职务。
安全专家 ——必须帮助了解与新项目相关的实际安全要求。
安全专家 (以及 其他小组A 先生, 被选定为组长。
A 先生, 某公司本地氯气装置的安全和紧急情况协调员。
B 先生, 主持故障假设分析。
B 先生, 假设分析。
成员)应熟知与氯乙烯单体项目有关的过去的事故、近期的事故和安全改进。
B先生将担任这一职务。
B 先生将主持故障假设分析会议。
根据由评价小组收集到的资料,此项目刚刚开始的事实,B先生估计分析将花费一天到二天的时间。
安排了会议,选择一个适宜的场所一一当地工厂的培训教室。
在开会前二周,B先生送给每位成员一份氯乙烯单体生产过程的摘要和由研究小组收集的有关此项目的资料。
B先生编制了在会议中要使用的故障假设分析检查表(表3)。
该表应能让小组成员畅所欲言地表达他们的安全观点。
B先生已发现,用少数问题作球状滚动”提问,是非常有帮助的。
(3)分析说明。
两周以后,在周一9:00 时,危险评价小组在当地工厂的培训教室集合开会。
首先,B 先生要求评价组人员互相介绍自己;然后,B先生说明了一天的安排, B 先生简单回顾了氯乙烯单体风险项目的基本情况、化学进展和为什么要进行故障假设分析。
在开始检查之前, B 先生概述了下面的基本原则:① 所有小组成员都将平等发言;② 任何一个观点,无论它多么无意义,都是合理的提议;③所有小组成员都要出一份力;④ 由初始故障假设分析产生的疑问和想法在继续前进以前,给予优先权;⑤ 不需对疑问或想法进行详细分析和鉴别;⑥检查重点主要集中在识别危险上检查的结论将由A先生和他本人写成文件,通过小组检查,然后作为正式的报告交给业务小组。
(B先生此时不能确定小组召集在一起检查这份报告,还是仅仅送一个报告给他自己。
)面是故障假设分析小组会议讨论的摘录:在生产过程的这一阶段,提出这样的一般性事件是有意义的。
故障假设分析重点放在该公司没有经验的领域。
由小组提出的实际事件包括下述内容:B 先生:让我们从检查生产氯乙烯单体的化学基本原理开始。
哪位有问题可以提问?(适当地停顿)如果送到生产过程中的乙烯供料有杂质,怎么办?E女士:杂质是什么?P先生:在乙烯中主要的杂质是轻油,少数情况有水存在。
A 先生:从最初的实验和文献中我们了解到,油和氯气会激烈地反应,这可能是个问题,提供的原料乙烯含有多少杂质?P 先生:这虽然取决于乙烯的供料方式。
假如乙烯是通过管道供料的,那么,在乙烯供料中将可能仅仅只有微量的杂质。
如果你同意,我将就这一问题进行检查。
B先生:我想我们能做到。
我们要知道,如果杂质存在,会有几种反应?Mr. Chemist你的会议记录能告诉我们吗?A 先生:好吧。
对于少量的油,我认为在反应器中的大容积的氯气、乙烯和二氯乙烯将有可能抑制油和氯气的反应。
但我将注意核实这一点。
B 先生:有新的疑问吗?(停顿)A 先生:如果氯气供料有杂质怎么办?E女士:在氯气中的主要杂质是水。
然而,我们了解到如果氯气装置中的氯气有水,那是在氯气供给该生产过程之前就有的。
任何微量的水形成的盐酸都能显著地毁坏设备和管道。
B 先生:是的。
但是我们能否认为水是由乙烯供料带来的?这也是氯乙烯单体生产过程形成盐酸的一个方面。
相信我们能够对乙烯杂质进行更好的检查。
A 先生:我同意。
我认为少量的水将不会引起任何问题,但我将就这方面进行检查。
E 女士:如果一条供料管线破裂怎么办?P先生:是的,如果乙烯管道破裂,在周围就会有大量的燃烧或易燃蒸汽,如果是氯气管道破裂,就会有有毒性气体逸出的问题。
B 先生:因为我们有设备、人员和专门知识去解决这个问题,因此我认为我们能控制氯气管线问题。
乙烯管线则是不同的情况。
另外。
供给的氯气是液体还是气体?A 先生:我同意。
我认为少量的水将不会引起任何问题,但我将就这方面进行检查。
E女士:如果一条供料管线破裂怎么办?P先生:是的,如果乙烯管道破裂,在周围就会有大量的燃烧或易燃蒸汽。
如果是氯气管道破裂,就会有毒性气体逸出的问题。
B 先生:因为我们有设备、人员和专门知识去解决这个问题,因此我认为我们能控制氯气管线问题。
乙烯管线则是不同的情况。
另外,供给的氯气是液体还是气体?A 先生:正好我们在讨论液氯的供给。
我赞同你的想法——如果管线破裂,气体供料会引起大量的氯气逸出。
我将组织研究小组查证这种可能性。
如果乙烯管道破裂怎么办?P先生:我认为无论乙烯是否被良好地控制,有些事情你们公司必须考虑。
当然,许多公司每日都安全地控制着乙烯。
有许多防止和减轻逸出的事情你们能做,如安装少量的实用隔离阀门。
然而,你们公司确定在这—领域有了一些经验和必需的防火设备后,才能做这些事情。
B先生:必须注意这—点, A 先生管理部门必须落实这种情况。
你采用我们的意见吗?A先生:不,你能重复一下刚才的建议吗?B 先生:重复一下A 先生:我将关注这一问题,目前我们暂时放下,留待初步设计时考虑。
B 先生:很好,但我认为,能否直接消耗掉氯化反应器中的全部氯气,从而避免这一问题。
Mr. Chemist ----- 在理论上是可行的。
但实际上做不到,这一问题将留到后面接续研究。
在一天的时间内,一直以这种方式继续着。
所有小组成员都提出问题和回答问题。
回答一直继续,直到小组没有其他问题或要回答的疑问涉及以前相同的情况时才结束。
(4)结果讨论。
分析结果被以表格形式列出(表4)。
表中内容有:疑问提问,小组成员对疑问的回答,还有小组提出来的对策。
在该公司的表格中,还包括为对策的执行和执行活动的情况。
而该公司的表格中没有说明如何执行对策的决议栏。
在有关人员被指定决定对策的时候,填写这一栏目。
由小组提出的许多疑问在会议中迅速解决,没有迅速解决的疑问指定了各小组成员在分析会议以夕随行调查,被指定的小组成员要对分析报告中包括的这些疑问作出调查结论,要向小组领导汇报。
有关检查中提出的疑问或获得的答案、对策要落实。
分析期间, A 先生继续关注有关问题的提出,后来他集中精力为业务小组打印一份正式报告。
他在报告中包括了小组成员对在会议中遗留下来的疑问进行调查的结论和建议。
(5)评价小结。
故障假设分析小组对小组每位成员和某公司员工提出的对策负有落实的责任。
协调氯乙烯项目的一位业务小组成员——A 先生,已同意会晤某公司员工并保证这些对策被落实, B 先生认为不需要为之后的工作再召开一次会议。
落实对策的结果被合并到故障假设分析结果中,并且作为递送业务小组的报告资料。
(6)结论和报告。
故障假设分析方法非常成功的原因是:负责人经验十分丰富,分析过程按部就班进行,较好完成任务;② 参加评价人员选择合理,人员水平较高;③ 分析组不是把所有的问题都解决,而是有重点地解决。
5 优缺点故障假设分析法鼓励创造性思维思考潜在的事故和后果,它弥补了基于经验的安全检查表法的编制时的经验不足,相反检查表可以吧故障假设分析方法更加系统化。
因此出现了安全检查表分析和故障假设分析组合使用的分析方法,互相取长补短。