金属材料短流程、近终形的生产工艺
轧钢技术工艺流程连续化和紧凑化

轧钢技术工艺流程连续化和紧凑化短流程、上下游工序的连续化和紧凑化的轧钢技术发展趋势,表现在以下方面:(1)短流程技术的发展近终形连铸的开发,使传统的轧钢工艺流程发生了巨大变革,使轧钢工艺流程简化和缩短,全连铸的发展导致初轧工序的消亡。
连铸坯直接轧制成材,连铸连轧工艺技术的不断成熟,热送热装和直接轧制技术的进展,最终将实现无需补热的直接轧制技术,使轧制工序成为不需补热的“零”热能工序,达到最低热能消耗。
薄带钢连铸的工业化,将成为首先取消热轧工序的带钢生产线。
(2)连续轧制和无头轧制技术得到发展年代初冷轧带钢实现无头轧制后,相继实现了酸洗与冷轧,冷轧与连续退火、平整全连续生产的冷连轧机。
年代中期,热轧带钢也实现了无头轧制。
以后相继又开发了棒、线材无头轧制技术;薄板坯连铸连轧已实现了长坯料轧制(半无头轧制),并正在向无头轧制迈进。
这些新技术的应用明显提高了成材率,降低了切头切尾损耗,减少了废品,提高了尺寸精度。
例如,热连轧机实现无头轧制后,可使热轧带钢全长的达到厚差在以内(常规生产仅能达到全长的),而且可使成材率提高,产量提高约。
全连续轧制的实现,还将改变传统的冷、热轧机生产规格的分工,如的热轧带钢可替代同规格的冷轧产品。
这样,相对低成本的热轧产品可取代一部分相对高成本的冷轧产品,从而大大提高了热轧产品的市场竞争力。
棒线材的无头轧制技术和小规格产品也已投入工业生产;线材轧机的高精度机架减定径机组的应用,除可达到提高轧制精度、速度和性能目的外,还可生产小于规格的产品,据称,可为规格轧制创造条件。
连续化生产流程的推进,可大大提高钢材轧制成材率,使成材率接近,并逐步实现金属“零”损耗。
由于连续化轧制工艺的高效率、低成本,将使其继续得到多种形式的发展。
例如,美国钢厂已建成世界上第个连续式中厚板生产厂。
这表明连续化工艺的应用已由带钢向中厚板生产发展。
高成本、低成材率的间隙式和周期式的轧制生产方式将被淘汰,我国横列式中小型和线材轧机、叠轧薄板轧机的加速淘汰就是例证。
短流程镍冶炼技术
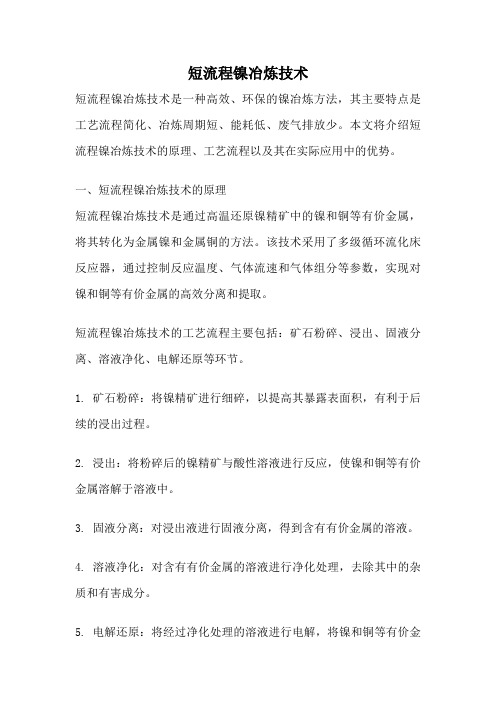
短流程镍冶炼技术短流程镍冶炼技术是一种高效、环保的镍冶炼方法,其主要特点是工艺流程简化、冶炼周期短、能耗低、废气排放少。
本文将介绍短流程镍冶炼技术的原理、工艺流程以及其在实际应用中的优势。
一、短流程镍冶炼技术的原理短流程镍冶炼技术是通过高温还原镍精矿中的镍和铜等有价金属,将其转化为金属镍和金属铜的方法。
该技术采用了多级循环流化床反应器,通过控制反应温度、气体流速和气体组分等参数,实现对镍和铜等有价金属的高效分离和提取。
短流程镍冶炼技术的工艺流程主要包括:矿石粉碎、浸出、固液分离、溶液净化、电解还原等环节。
1. 矿石粉碎:将镍精矿进行细碎,以提高其暴露表面积,有利于后续的浸出过程。
2. 浸出:将粉碎后的镍精矿与酸性溶液进行反应,使镍和铜等有价金属溶解于溶液中。
3. 固液分离:对浸出液进行固液分离,得到含有有价金属的溶液。
4. 溶液净化:对含有有价金属的溶液进行净化处理,去除其中的杂质和有害成分。
5. 电解还原:将经过净化处理的溶液进行电解,将镍和铜等有价金属电积出来,得到金属镍和金属铜。
三、短流程镍冶炼技术的优势相比传统的镍冶炼方法,短流程镍冶炼技术具有以下优势:1. 工艺流程简化:相比传统的镍冶炼方法,短流程镍冶炼技术的工艺流程更为简化,减少了中间环节和设备投资,提高了生产效率。
2. 冶炼周期短:短流程镍冶炼技术采用了高效的循环流化床反应器,使得冶炼周期大大缩短,提高了生产效率。
3. 能耗低:短流程镍冶炼技术通过优化工艺参数和设备结构,降低了能耗,减少了能源消耗,降低了生产成本。
4. 废气排放少:短流程镍冶炼技术通过合理设计反应器和采用高效的气体净化设备,减少了废气的排放量,降低了对环境的污染。
5. 提高资源利用率:短流程镍冶炼技术能够高效提取镍和铜等有价金属,提高了资源的利用率,减少了资源的浪费。
6. 环保节能:短流程镍冶炼技术采用了先进的工艺和设备,减少了对环境的污染,符合现代绿色冶金的要求。
金属材料生产工艺
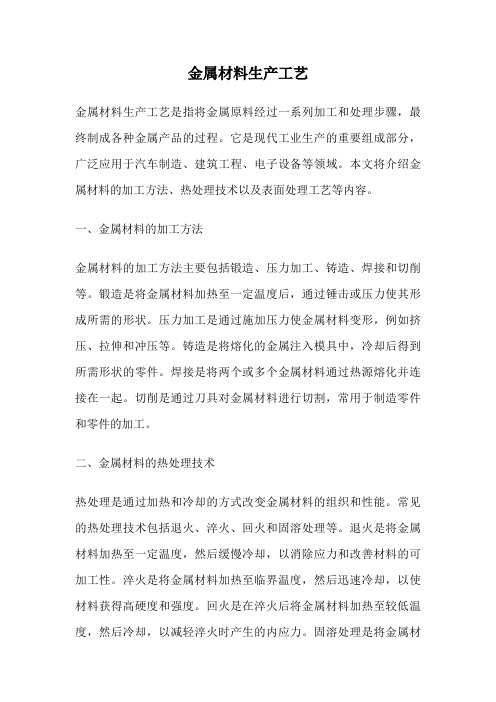
金属材料生产工艺金属材料生产工艺是指将金属原料经过一系列加工和处理步骤,最终制成各种金属产品的过程。
它是现代工业生产的重要组成部分,广泛应用于汽车制造、建筑工程、电子设备等领域。
本文将介绍金属材料的加工方法、热处理技术以及表面处理工艺等内容。
一、金属材料的加工方法金属材料的加工方法主要包括锻造、压力加工、铸造、焊接和切削等。
锻造是将金属材料加热至一定温度后,通过锤击或压力使其形成所需的形状。
压力加工是通过施加压力使金属材料变形,例如挤压、拉伸和冲压等。
铸造是将熔化的金属注入模具中,冷却后得到所需形状的零件。
焊接是将两个或多个金属材料通过热源熔化并连接在一起。
切削是通过刀具对金属材料进行切割,常用于制造零件和零件的加工。
二、金属材料的热处理技术热处理是通过加热和冷却的方式改变金属材料的组织和性能。
常见的热处理技术包括退火、淬火、回火和固溶处理等。
退火是将金属材料加热至一定温度,然后缓慢冷却,以消除应力和改善材料的可加工性。
淬火是将金属材料加热至临界温度,然后迅速冷却,以使材料获得高硬度和强度。
回火是在淬火后将金属材料加热至较低温度,然后冷却,以减轻淬火时产生的内应力。
固溶处理是将金属材料加热至固溶温度,然后快速冷却,以改善材料的硬度和强度。
三、金属材料的表面处理工艺金属材料的表面处理工艺主要包括防锈处理、电镀和喷涂等。
防锈处理是通过涂覆防锈剂或进行化学处理,以保护金属材料免受氧化和腐蚀。
电镀是将金属材料浸入电解液中,通过电流的作用,在材料表面形成一层金属镀层,以增加材料的耐腐蚀性和美观性。
喷涂是将涂料喷洒在金属材料表面,形成一层保护层,以增加材料的耐候性和装饰效果。
总结金属材料生产工艺是现代工业生产的重要环节。
通过锻造、压力加工、铸造、焊接和切削等加工方法,可以将金属材料制成各种形状的零件和产品。
通过热处理技术,可以改变金属材料的组织和性能,以满足不同的工程要求。
通过表面处理工艺,可以保护金属材料免受腐蚀和氧化,并增加其美观性和装饰效果。
金属零件生产工艺流程

金属零件生产工艺流程金属零件生产工艺流程金属零件是工业生产中常见的一种零部件,广泛应用于汽车、航空航天、机械制造等领域。
本文将对金属零件的生产工艺流程进行详细介绍。
一、工艺准备在开始生产金属零件之前,首先需要进行工艺准备。
包括确定产品的设计要求、制定生产工艺、选择合适的材料和设备等。
根据产品的尺寸、形状和用途等要求,选择适当的金属材料,如钢、铝、铜等。
根据产品的具体要求,确定生产工艺,包括加工方式、工艺路线和加工参数等。
同时,还需要选择和购置合适的设备,如车床、铣床、钻床等。
二、图纸设计根据产品的设计要求,制作相应的图纸。
图纸应包括产品的外形尺寸和形状,各部件的加工要求和装配要求等。
图纸设计完成后,需要进行复核和审查,确保图纸的准确性和合理性。
三、材料准备根据产品的材料要求,准备相应的金属材料。
材料应符合产品的需求,如强度要求、耐腐蚀性能等。
材料需要进行质量检验,确保质量合格后才能使用。
四、加工制造1.下料根据产品的尺寸要求,将金属材料进行下料。
通常采用锯床或切割机进行下料,保证尺寸精度和形状要求。
2.粗加工粗加工主要是对材料进行基本的加工处理,以使其接近最终形状。
常见的粗加工方式有车削、铣削、钻孔等,通过切削和去除多余材料,使得材料逐渐接近产品的形状和尺寸要求。
在粗加工过程中,需要根据产品的具体要求,进行多道次的加工和调整。
3.热处理对于某些金属材料,需要进行热处理以改变其组织结构和性能。
常见的热处理方式有退火、淬火、回火等。
通过加热和冷却的控制,使得材料达到理想的硬度、强度和韧性等性能。
4.精加工精加工是在粗加工的基础上进一步加工和修整,以满足产品的精度和表面质量要求。
常见的精加工方式有研磨、刨削、拋光等,通过去除表面的毛刺和不平整,使得产品的表面更加光滑,达到要求的工艺和装配要求。
5.组装对于需要多个部件的金属零件,需要进行组装。
组装时需要注意各部件之间的配合和装配顺序,保证产品的功能和性能要求。
通用的金属材料生产工艺
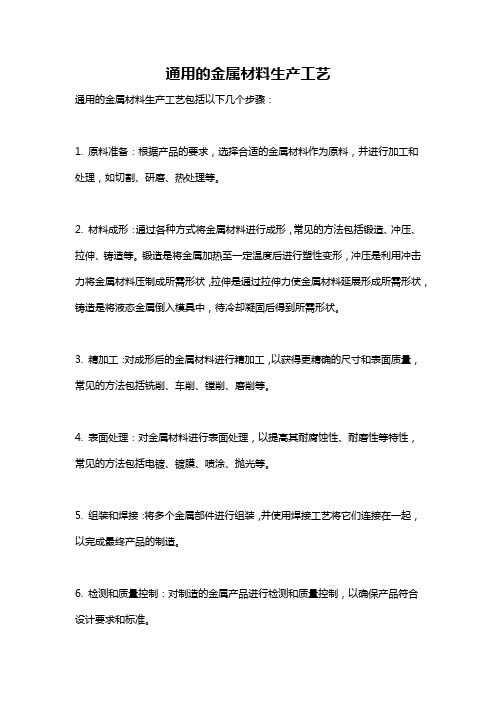
通用的金属材料生产工艺
通用的金属材料生产工艺包括以下几个步骤:
1. 原料准备:根据产品的要求,选择合适的金属材料作为原料,并进行加工和处理,如切割、研磨、热处理等。
2. 材料成形:通过各种方式将金属材料进行成形,常见的方法包括锻造、冲压、拉伸、铸造等。
锻造是将金属加热至一定温度后进行塑性变形,冲压是利用冲击力将金属材料压制成所需形状,拉伸是通过拉伸力使金属材料延展形成所需形状,铸造是将液态金属倒入模具中,待冷却凝固后得到所需形状。
3. 精加工:对成形后的金属材料进行精加工,以获得更精确的尺寸和表面质量,常见的方法包括铣削、车削、镗削、磨削等。
4. 表面处理:对金属材料进行表面处理,以提高其耐腐蚀性、耐磨性等特性,常见的方法包括电镀、镀膜、喷涂、抛光等。
5. 组装和焊接:将多个金属部件进行组装,并使用焊接工艺将它们连接在一起,以完成最终产品的制造。
6. 检测和质量控制:对制造的金属产品进行检测和质量控制,以确保产品符合设计要求和标准。
这些是金属材料生产的一般工艺步骤,具体的工艺可能会根据不同的材料和产品类型而有所不同。
金属材料短流程、近终形的生产工艺

金属材料短流程、近终形的生产工艺多个进程(如凝固与成形)的综合化,称短流程化,如喷射成形技术、半固态加工技术和持续铸轧技术等。
打破传统的材料成形与加工模式,缩短生产工艺流程,简化工艺环节,实现近终形、短流程的持续化生产,提高生产效率。
近终型、短流程的成形加工技术具有高效、节能等特点,在技术上突出的特点是缩短加工周期,尽可能减少变形量或后续加工环节,由金属熔体直接取得所需的制品或近似的制品,同时,这些制品还具有现有加工方式所生产制品的性能和组织,这可大大减少后续挤压、轧制和压铸等耗能大、投资大、用工多的加工进程。
例如,半固态成形、持续铸轧和持续铸挤等是将凝固与成形两个进程合而为一,实行精准控制,形成以节能、降耗、高效和优质为主要特征的新技术和新工艺。
1半固态成型金属材料的半固态成型是在半液半固的两相状态下进行的,所以与全液体成型或全固体成型相较,具有许多长处。
首先,在凝固进程中有固液两相,同时存在的合金系都可进行半固态成型。
半固态材料浆的粘度比熔融金属的粘度高得多,因此成型时可形成层流,也能更均匀地填充模型。
金属浆的成型温度较低,与常规铸造工艺相较:可节约35%左右的能源;可以延长模型寿命;凝固时间较短;可缩短生产周期;由于有固体存在和温度较低,零件在模内的收缩较小。
用金属浆生产的零件内的宏观气孔与显微疏松比常规铸件中的少得多。
半固态材料填充模型时,材料前端呈层流充满型腔,比熔融金属的流动平稳得多,不会卷入气体。
半固态成型零件的尺寸可与成品零件的相等或几乎相等,极大地减少了机械加工量与切削量,既节约了材料,又可以生产形状复杂的零件或难于加工的薄壁零件。
半固态模锻件与压铸件表面平整滑腻,内部组织致密,晶粒细小,力学性能高。
2近终形轧制技术(1)热连轧技术热连轧技术是将均热后的坯锭同时在几个机架中产生塑形变形的持续轧制进程。
与单机架轧制相较较,热连轧技术具有工艺流程短,生产率高,产品质量高和生产本钱低等长处。
短流程近终型
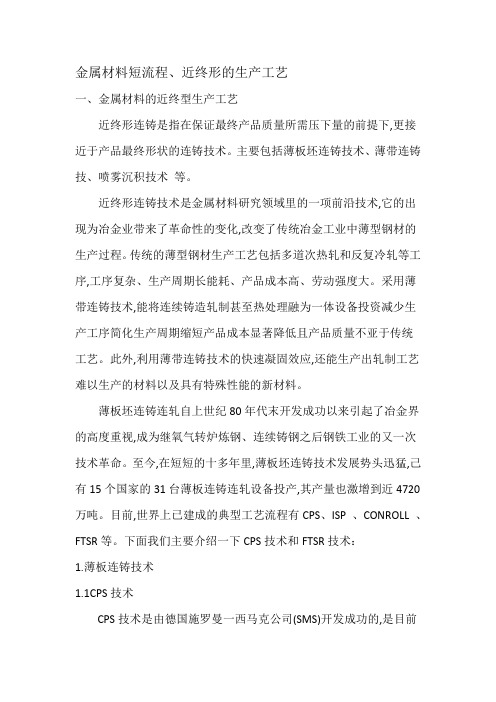
金属材料短流程、近终形的生产工艺一、金属材料的近终型生产工艺近终形连铸是指在保证最终产品质量所需压下量的前提下,更接近于产品最终形状的连铸技术。
主要包括薄板坯连铸技术、薄带连铸技、喷雾沉积技术等。
近终形连铸技术是金属材料研究领域里的一项前沿技术,它的出现为冶金业带来了革命性的变化,改变了传统冶金工业中薄型钢材的生产过程。
传统的薄型钢材生产工艺包括多道次热轧和反复冷轧等工序,工序复杂、生产周期长能耗、产品成本高、劳动强度大。
采用薄带连铸技术,能将连续铸造轧制甚至热处理融为一体设备投资减少生产工序简化生产周期缩短产品成本显著降低且产品质量不亚于传统工艺。
此外,利用薄带连铸技术的快速凝固效应,还能生产出轧制工艺难以生产的材料以及具有特殊性能的新材料。
薄板坯连铸连轧自上世纪80年代末开发成功以来引起了冶金界的高度重视,成为继氧气转炉炼钢、连续铸钢之后钢铁工业的又一次技术革命。
至今,在短短的十多年里,薄板坯连铸技术发展势头迅猛,己有15个国家的31台薄板连铸连轧设备投产,其产量也激增到近4720万吨。
目前,世界上已建成的典型工艺流程有CPS、ISP 、CONROLL 、FTSR等。
下面我们主要介绍一下CPS技术和FTSR技术:1.薄板连铸技术1.1CPS技术CPS技术是由德国施罗曼一西马克公司(SMS)开发成功的,是目前应用最广泛的薄板坯连铸连轧工艺,已有19条生产线成功地投入了工业生产。
CPS的工艺过程为:采用立弯式连铸机生产厚50mm~60mm的铸坯,经分段剪后,送入辊底式均热炉(120~185m)进行加热、均热。
薄板坯经加热炉入口段、加热段和均热段加速到20~30m/min进入轧制工序。
六机架精轧机组将厚50mm~60mm的铸坯轧制成1.2~12.7mm的带材,经层流水帘冷却后卷取。
生产线全长约270m。
优点:流程短、生产稳定、产品质量好等。
缺点:对钢水质量要求高、难以生产很宽或较厚的钢板、均热炉设备尚未定型化等。
高效连铸和近终型连铸生产技术
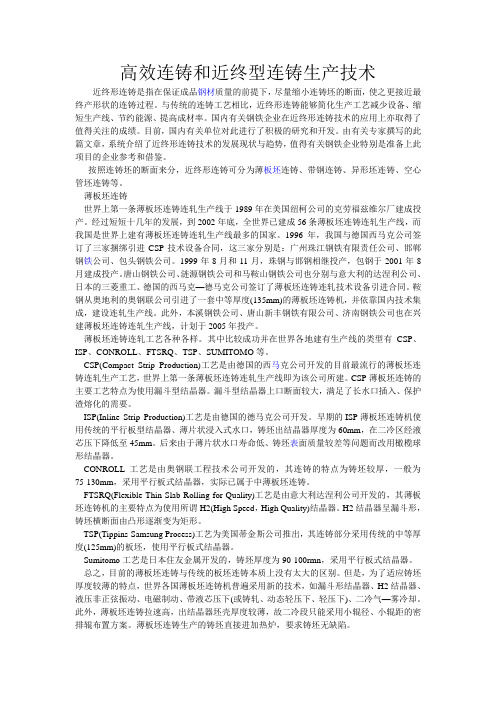
高效连铸和近终型连铸生产技术近终形连铸是指在保证成品钢材质量的前提下,尽量缩小连铸坯的断面,使之更接近最终产形状的连铸过程。
与传统的连铸工艺相比,近终形连铸能够简化生产工艺减少设备、缩短生产线、节约能源、提高成材率。
国内有关钢铁企业在近终形连铸技术的应用上亦取得了值得关注的成绩。
目前,国内有关单位对此进行了积极的研究和开发。
由有关专家撰写的此篇文章,系统介绍了近终形连铸技术的发展现状与趋势,值得有关钢铁企业特别是准备上此项目的企业参考和借鉴。
按照连铸坯的断面来分,近终形连铸可分为薄板坯连铸、带钢连铸、异形坯连铸、空心管坯连铸等。
薄板坯连铸世界上第一条薄板坯连铸连轧生产线于1989年在美国纽柯公司的克劳福兹维尔厂建成投产。
经过短短十几年的发展,到2002年底,全世界已建成56条薄板坯连铸连轧生产线,而我国是世界上建有薄板坯连铸连轧生产线最多的国家。
1996年,我国与德国西马克公司签订了三家捆绑引进CSP技术设备合同,这三家分别是:广州珠江钢铁有限责任公司、邯郸钢铁公司、包头钢铁公司。
1999年8月和11月,珠钢与邯钢相继投产,包钢于2001年8月建成投产。
唐山钢铁公司、涟源钢铁公司和马鞍山钢铁公司也分别与意大利的达涅利公司、日本的三菱重工、德国的西马克—德马克公司签订了薄板坯连铸连轧技术设备引进合同。
鞍钢从奥地利的奥钢联公司引进了一套中等厚度(135mm)的薄板坯连铸机,并依靠国内技术集成,建设连轧生产线。
此外,本溪钢铁公司、唐山新丰钢铁有限公司、济南钢铁公司也在兴建薄板坯连铸连轧生产线,计划于2005年投产。
薄板坯连铸连轧工艺各种各样。
其中比较成功并在世界各地建有生产线的类型有CSP、ISP、CONROLL、FTSRQ、TSP、SUMITOMO等。
CSP(Compact Strip Production)工艺是由德国的西马克公司开发的目前最流行的薄板坯连铸连轧生产工艺,世界上第一条薄板坯连铸连轧生产线即为该公司所建。
金属材料的成型加工工艺

砂型铸造
• 砂型铸造俗称翻砂,用砂粒制造铸型进行 铸造的方法。
• 主要工序有:制造铸模,制造砂铸型(即砂 型),浇注金属液,落砂,清理等。
• 砂型铸造适应性强,几乎不受铸件形状、 尺寸、重量及所பைடு நூலகம்金属种类的限制,工艺 设备简单,成本低,为铸造业广泛使用。
砂型铸造工艺流程
型砂
铸
铸
模型
型
落
零
造
件
工
图
艺
熔化 浇注
合 冷却 箱 凝固
砂 、 清
检 验
铸 件
图
芯盒
型
理
芯砂
芯
熔模铸造
热轧是将材料加热到再结晶温度以上进行轧制,热轧变形抗力小,变形量大,生产效率高,适合轧制较大断面尺寸,塑性较差或变形 量较大的材料。
• 熔模铸造又称失蜡铸造,为精密铸造方法之 熔模铸造过程分为:制作母模---制作压型---制作蜡模---制作型壳---脱蜡---焙烧和造型---浇注---脱壳。
金属材料的成型加工工艺
金属材料及其成型工艺
• 金属材料是金属及其合金的总祢。 在钢、 铁和合金为代表的现代工业社会,金属材 料以其优良的力学性能、加工性能和独特 的表面特性,成为现代产品设计中的一大 主流材质。
• 金属的成型方法可区分为铸造、塑性加工、 切削加工、焊接与粉末冶金五类。
一、铸造
• 将熔融态金属浇入铸型后,冷却凝固成为 具有一定形状铸件的工艺方法。铸造是生 产金属零件毛坯的主要工艺方法之一,与 其他工艺方法相比,铸造成型生产成本低, 工艺灵活性大,适应性强,适合生产不同 材料、形状和重量的铸件,并适合于批量 生产。但它的缺点是公差较大,容易产生 内部缺陷。铸造按铸型所用材料及浇注方 式分为砂型铸造、熔模铸造、金属型铸造、 压力铸造以及离心铸造等。
金属生产工艺

金属生产工艺金属生产工艺是指将金属原料经过一系列加工和处理的过程,转化为各种金属制品的方法和技术。
金属生产工艺涵盖了金属的提取、熔炼、铸造、锻造、焊接、冲压、表面处理等多个环节。
以下将简要介绍金属生产工艺的主要环节和工艺流程。
金属的提取是金属生产的第一步。
金属常见的提取方法有开采法和冶炼法。
开采法是通过采矿、选矿和预处理等步骤,将含有金属矿石中的金属元素提取出来。
冶炼法则是将金属矿石经过高温熔炼,分离金属和非金属成分。
熔炼是将金属矿石加热至高温,使其熔融,并分离出金属和非金属的过程。
熔炼方法主要有火法和湿法两种。
火法熔炼是利用高温燃烧将矿石中的金属分离出来,常见的火法熔炼方法有焙烧、电炉炼铁、高炉冶炼等。
湿法熔炼则是通过化学反应将金属溶解在液体中,并通过萃取、电解等方法将金属分离出来。
铸造是将金属熔融后,倒入预先准备好的铸型中,冷却凝固,得到所需形状的金属制品的过程。
铸造方法根据铸型材料的不同可分为砂型铸造、金属型铸造和陶瓷型铸造等。
砂型铸造是最常见的铸造方法,通过将金属熔液倒入砂型中,凝固后取出并清理,得到所需的铸件。
锻造是将金属加热到一定温度后,放入压力机或锤击机中,通过机械力使金属发生塑性变形,得到所需形状的金属制品的过程。
锻造方法根据金属的变形方式可以分为冷锻、热锻和温锻等。
锻造可以使金属的内部结构得到改善,增加金属的强度和韧性。
焊接是将金属零件通过加热使其部分或全部熔化,然后冷却凝固,使其连接为整体的工艺。
焊接方法根据焊接材料的不同可分为电弧焊接、气焊、激光焊接、等离子焊接等。
焊接可以在不改变金属物理性质的情况下,将两个或多个金属零件连接在一起,起到加强连接和密封的作用。
冲压是利用冲压设备将金属板材经过模具的压力变形,以实现所需形状和尺寸的工艺。
冲压方法包括剪切、冲孔、弯曲、拉伸等。
冲压工艺可以高效地生产大量形状复杂的金属零件,具有工艺稳定性高、生产效率高的特点。
表面处理是对金属制品进行涂镀或喷涂,以增加金属的耐腐蚀性、装饰性和使用寿命的方法。
金属材料生产工艺

金属材料生产工艺一、引言金属材料生产工艺是指通过一系列加工和处理过程将金属原料转化为具有特定形状、结构和性能的金属制品的过程。
金属材料广泛应用于各个领域,如建筑、汽车、机械、电子等。
本文将介绍金属材料生产工艺的一些常见方法和技术。
二、铸造铸造是最常见的金属材料生产工艺之一。
它是将金属原料加热至熔化状态,然后借助模具将熔融金属注入,并在冷却固化后得到所需形状的工艺。
铸造方法包括砂型铸造、金属型铸造、压力铸造等。
其中,砂型铸造是最为传统和常用的方法,它适用于各种复杂形状的制品。
三、锻造锻造是通过加热金属原料至一定温度后,将其放置于模具之间,然后施加压力使金属发生塑性变形,最终得到所需形状制品的工艺。
锻造方法包括自由锻造、冷锻造、热锻造等。
锻造可以提高金属的内部结构和力学性能,广泛应用于航空航天、造船、军工等领域。
四、焊接焊接是将两个或多个金属部件通过热源加热至熔化状态,然后使其相互结合的工艺。
焊接方法包括电弧焊、气体焊、激光焊等。
焊接可以实现金属部件的连接,广泛应用于制造业、建筑业等领域。
五、切削加工切削加工是通过切削工具对金属进行削减,从而得到所需形状的工艺。
常见的切削加工方法包括车削、铣削、钻削等。
切削加工可以实现高精度加工,广泛应用于制造业、机械加工等领域。
六、表面处理金属制品在生产过程中常需要进行表面处理,以提高其耐腐蚀性、耐磨性和美观性。
常见的表面处理方法包括镀层、喷涂、阳极氧化等。
表面处理可以改善金属制品的性能和外观,广泛应用于建筑、家具、电子等领域。
七、热处理热处理是通过加热和冷却的方式改变金属的组织结构和性能的工艺。
常见的热处理方法包括退火、淬火、回火等。
热处理可以提高金属的硬度、强度和耐磨性,广泛应用于机械、工具等领域。
八、总结金属材料生产工艺是将金属原料转化为具有特定形状、结构和性能的金属制品的过程。
铸造、锻造、焊接、切削加工、表面处理和热处理是常见的金属材料生产工艺方法。
通过合理选择和应用这些工艺方法,可以满足不同领域对金属制品的需求,推动工业发展和技术进步。
金属材料冶炼的生产流程
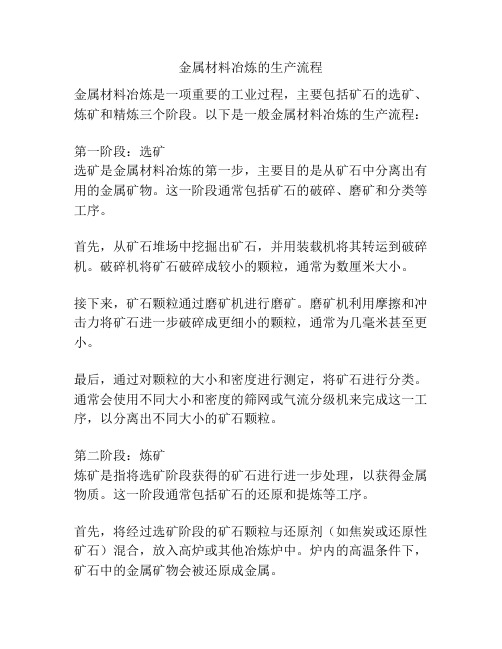
金属材料冶炼的生产流程金属材料冶炼是一项重要的工业过程,主要包括矿石的选矿、炼矿和精炼三个阶段。
以下是一般金属材料冶炼的生产流程:第一阶段:选矿选矿是金属材料冶炼的第一步,主要目的是从矿石中分离出有用的金属矿物。
这一阶段通常包括矿石的破碎、磨矿和分类等工序。
首先,从矿石堆场中挖掘出矿石,并用装载机将其转运到破碎机。
破碎机将矿石破碎成较小的颗粒,通常为数厘米大小。
接下来,矿石颗粒通过磨矿机进行磨矿。
磨矿机利用摩擦和冲击力将矿石进一步破碎成更细小的颗粒,通常为几毫米甚至更小。
最后,通过对颗粒的大小和密度进行测定,将矿石进行分类。
通常会使用不同大小和密度的筛网或气流分级机来完成这一工序,以分离出不同大小的矿石颗粒。
第二阶段:炼矿炼矿是指将选矿阶段获得的矿石进行进一步处理,以获得金属物质。
这一阶段通常包括矿石的还原和提炼等工序。
首先,将经过选矿阶段的矿石颗粒与还原剂(如焦炭或还原性矿石)混合,放入高炉或其他冶炼炉中。
炉内的高温条件下,矿石中的金属矿物会被还原成金属。
接下来,金属物质通过冶炼炉底部的排渣口流出,形成初级金属产品,如生铁、铜精矿等。
同时,炉顶部的烟气会经过除尘等处理,以减少对环境的污染。
第三阶段:精炼精炼是指对初级金属产品进行进一步的提纯和处理,以得到高纯度的金属材料。
这一阶段通常包括铁矿石的炼铁、铜矿石的炼铜、铝矿石的电解精炼等过程。
在炼铁过程中,将初级金属产品与炼铁炉料混合,并通过高炉进行冶炼。
在高炉中,通过加入石灰石和其他辅助剂,除去混入的杂质,提高铁的纯度。
在炼铜过程中,铜精矿经过浮选等处理后,通过加热熔炼,并通过电解等方法分离出铜金属和其他杂质。
在铝电解精炼过程中,熔化铝矿石后,将其注入电解槽,通过电解分离出纯铝金属。
精炼过程通常还包括其他辅助工序,如水洗、溶解、析出等。
最终,经过精炼的金属材料可以通过浇铸、轧制、拉制等方式制成各种形状和规格的金属制品。
总结起来,金属材料冶炼的生产流程主要包括选矿、炼矿和精炼三个阶段。
短流程镍冶炼技术

短流程镍冶炼技术短流程镍冶炼技术是一种现代化的镍冶炼技术,它是指将含镍废料或者精矿直接还原成纯镍的技术。
在这种技术中,尽可能减少了传统镍冶炼过程中的工序和用量,从而达到节能、减排、降本的目的。
一般来说,短流程镍冶炼技术采用了先进的物理化学反应原理和设备技术,通过短流程的方式将精矿中的金属氧化物还原成纯金属。
这种技术基本上将含镍废料或者精矿加热到很高的温度,然后用气体进行还原,从而将金属氧化物还原成纯金属。
在短流程镍冶炼技术中,关键的是还原反应,这个反应需要掌握严格的温度、时间、气体流量等参数。
为了控制好这些参数,一般采用计算机控制和实时监控技术,确保反应可以稳定进行。
短流程镍冶炼的主要优点是:1. 节能减排:短流程镍冶炼技术中省去了矿物选矿和烧结这两个繁琐的步骤,不需要大规模的矿山建设,从而减少了能源消耗和大量工业废气的排放,符合现代环保要求。
2. 高效节省:短流程镍冶炼工艺节省了原材料、电能、水、劳动力等成本,降低了生产成本,提高了企业经济效益。
3. 快速反应:短流程镍冶炼技术可以达到很高的温度,反应速度快,反应时间短,可以做到实时控制。
4. 灵活可靠:短流程镍冶炼技术的设备和生产线比较灵活、可靠,可以根据实际需要随时更改生产情况,适应市场变化。
短流程镍冶炼技术具有一定的市场前景和发展空间,不过它也存在一些缺陷,例如:1. 技术门槛较高:短流程镍冶炼技术需要较高的技术水平,设备复杂,对人员的要求较高。
3. 行业标准不统一:短流程镍冶炼技术还没有行业标准,不同企业生产工艺略有不同,技术导向和技术指标也不尽相同。
总的来说,短流程镍冶炼技术是一种具有一定优势和发展空间的现代化技术,随着技术的不断进步和完善,相信会在未来的镍冶炼过程中发挥越来越重要的作用。
金属材料加工工艺流程

金属材料加工工艺流程一、开篇聊聊金属材料的魅力嘿,朋友们,今儿咱们得聊聊那闪闪发亮的金属材料,那可是工业界的明星,日常生活的贴心小伙伴。
想象一下,从家里的水龙头到高楼大厦的骨架,从汽车的心脏发动机到手机那薄薄的机身,哪儿都离不开金属的身影。
它们不仅硬朗耐用,还能玩出各种花样,真是让人爱不释手,欲罢不能啊!二、走进金属材料加工的世界1.选材:挑个好的开始要想加工出好货,选材可是头一遭。
就像做饭得选好食材一样,咱们得根据需求,挑那合适的金属材料。
有的金属硬得像石头,适合干重活;有的轻如鸿毛,适合做精细活。
挑好了材料,就等于给作品打了个好基础。
2.切割:一刀两断的艺术接下来,就是切割环节了。
这活儿可得精细,一刀下去,得恰到好处,多了少了都不行。
工人们手握切割机,就像大厨挥刀切菜一样,嗖嗖几下,就把大块头变成了小块头。
那火花四溅的场面,简直就是一场视觉盛宴,让人看得直呼过瘾。
3.塑形:打造完美身材切割好了,就得给金属塑形了。
这塑形啊,就像是给金属做美容,得根据设计图,一点点地打磨、弯曲、拉伸。
有时候,还得用上模具,把金属压成各种形状。
经过这一番折腾,金属就像变魔术一样,变成了我们想要的样子。
4.热处理:火中取宝塑形完了,还得来点火候。
热处理啊,就是让金属在火中烤一烤,变得更加坚韧或者柔软。
这火候可得掌握得恰到好处,火候大了容易烤焦,火候小了又不起作用。
经过热处理的金属啊,就像是经过千锤百炼的战士一样,更加可靠耐用。
5.表面处理:穿上漂亮的衣服最后一步就是表面处理了。
这就像是给金属穿上漂亮的衣服一样重要。
通过喷漆、电镀等方式啊,可以让金属表面变得光滑亮丽、耐腐蚀、防氧化。
这样一来啊,金属作品就更加美观大方、经久耐用了。
三、结尾:感受金属的魅力与温度朋友们啊,经过这一番加工流程啊,原本冷冰冰的金属啊就变得有温度、有情感了。
它们不再只是简单的物质存在啊,而是融入了我们的智慧和汗水啊成为了我们生活中的一部分啊。
金属材料生产工艺

金属材料生产工艺一、导言金属材料生产工艺是指将金属矿石经过一系列工艺流程转化为制品的过程。
在工艺中,需要考虑金属的提取、熔炼、净化、成形和加工等环节。
二、金属矿石提取金属矿石提取是生产金属材料的第一步。
主要的金属矿石有铁矿石、铜矿石、铝矿石等。
金属矿石提取的方法有地下开采和露天开采两种。
2.1 地下开采地下开采是指通过井道或洞穴进入地下矿脉,将矿石运送上来。
地下开采相对而言更为复杂和危险,但通常能够得到更高品质的矿石。
2.2 露天开采露天开采是指直接在地表挖掘矿石。
这种方法通常适用于矿脉较浅的矿区。
虽然效率较高,但由于露天开采会对环境造成一定损害,因此需要合理处理挖掘废料。
三、金属矿石的熔炼金属矿石提取后,需要进行熔炼,并将其转化为金属合金。
熔炼的目的是将矿石中的金属元素分离出来,并去除杂质。
3.1 熔炼的步骤•矿石预处理:将矿石破碎、磨细,以提高熔炼效果。
•矿石还原:通过高温反应使金属与氧化物发生还原反应,从而得到金属。
•熔融和精炼:将金属矿石和还原剂加热到高温,使其熔化。
随后通过注气、除杂等工艺,去除熔融金属中的杂质。
•合金化:根据需要掺入其他金属元素,以改变金属的性能。
3.2 熔炼中的技术要点•温度控制:熔炼过程中需要精确控制温度,以保证金属的质量。
•杂质控制:通过加入适量的氧化剂和还原剂,控制金属中的杂质含量。
•熔炼剂选择:根据金属特性选择合适的熔炼剂,以提高熔炼效率和质量。
四、金属材料的净化熔炼后得到的金属含有一定的杂质,需要进行净化处理,以提高金属的纯度和性能。
4.1 电解精炼电解精炼是常用的净化方法之一。
通过将金属浸入电解液中,利用电解作用使金属离子迁移,从而去除杂质。
4.2 氧化反应净化氧化反应净化是利用氧化反应将杂质氧化成易挥发的氧化物,再通过加热或其他方法除去。
五、金属材料的成形和加工净化后的金属材料需要通过成形和加工来满足不同的工程需求。
5.1 成形成形是将金属材料通过加热和外力作用,使其变形成所需形状的过程。
金属材料短流程

阐述金属材料短流程、近终形的生产工艺1. 引言人类在探索新材料的过程中,也在不断地探索和完善材料的制备技术。
近几十年来,随着高新技术在冶金领域的应用,金属材料近终成形技术得到了很快的发展。
金属材料的近终成形是集金属合成、精炼、凝固、成形于一道工序的一次成形技术,它实现了减少工序,缩短生产周期,提高金属利用率,提高金属性能。
目前已使用的金属近终成形技术有近终形连铸、粉末冶金、喷射沉积成形、电渣转注、电磁铸造、金属泥成形等。
近终形连铸技术已成为现代材料工业,尤其是钢铁工业最主要的技术之一。
西方发达国家钢生产中的连铸比已达90%,我国的连铸比也接近60%。
作为取代模铸的一种新工艺,连铸已带来巨大的经济效益。
但传统的连铸坯仍需要多道加工工序才能制成最终的产品,因此造成大规模的设备投资和很大的能耗。
为了减少投资,降低能耗,提高产品质量,各种近终形连铸相继出现。
近终型连铸的优点:(1)可省去开坯、初轧,甚至可免去整个热轧工序,使设备投资和过程能耗大为降低;(2)因断面尺寸接近成品,总轧制变形量减小,减少了机架数量,进而降低基建投资;(3)应用薄板坯连铸生产热轧带钢,已使生产带卷的成本大大降低,正在研究中的薄带连铸的工业应用,将会带来进一步的革命性变化,这其中之一将是取消热连轧机组。
近终形连铸技术是近20年来最为瞩目的成就之一,它包括薄板坯连铸和薄带坯连铸两种。
目前,薄板坯连铸技术已经进入工业化生产,而大多数薄带坯连铸技术仍主要处于实验室研究阶段,一些技术难点和缺陷还有待进一步解决。
日本预测,到2020年,在连铸技术领域,传统连铸占40%,薄板坯连铸占50%,薄带坯连铸占10%。
2. 薄板坯连铸技术2.1 薄板坯连铸技术简介薄板坯连铸是介于传统连铸和薄带连铸之间的一种工艺。
世界上第一台薄板坯连铸机于1989年在美国Nucor公司的Crawfordsville工厂投产。
进入90年代以来,薄板坯连铸连轧工艺迅猛发展。
快速发展中的近终形连铸技术

&’ 薄板坯连铸连轧带钢; !’ 中等厚度板坯连铸连轧中厚钢板新工艺; (’ 薄带连铸; )’ 钢梁异型坯连铸连轧工艺。薄。由初始阶段最小厚度为 &’!00改
)*
科技进步 的生产线能力可达到 !"#$!%# 万 & ’ ( 。 为生产薄带钢和产能的需要, 精轧机出口最大速度由原 来的 )!* ’ +左右提高到 !!* ’ +, 采用升速轧制。 由于采用了前述先进技术,在产品质量上有所提高, 产 品范围有所扩大, 除传统产品外, 铁素体不锈钢、 工具钢、 汽 车用钢( 面板在外) 等均可在薄板坯连铸连轧生产线上成批 生产。 经过十余年的发展, 薄板坯连铸连轧生产线出现了多种 工艺,开始用得较多的是德国西马克公司的 ,-.型和德马克 随着两公司的合并, 吸收 /-. 工艺优点后, 新公 公司的 /-. 型, 司继续推广 ,-.薄板坯连铸连轧生产线,在全世界已建成的 生产线中占大多数。其后意大利达涅利公司推出颇有特点的 首先在加拿大阿尔戈马公司得到成功 01-,型薄板坯连铸机, 应用, 特别是在改造世界第一台美国纽柯公司克劳福兹维尔 厂铸机时, 01-,型铸机显示其优越性,接着在伊朗伊斯法罕 厂、 唐钢、 埃及 20- 厂、 意大利 34- 厂和本钢先后得到采用, 在 数量上占第二位。奥钢联的 ,567588工艺、 美国梯平斯公司 的 1-.工艺也有所建树。 !##) 年我国投产了拥有我国自主知 识产权的 3-.工艺中的薄板坯连铸连轧生产线。这些工艺都 各有优缺点, 既相互竞争也相互渗透, 采用或变相采用对方 的长处, 需要结合具体情况选择采用。 早在十九世纪中就有科学家提出薄带连铸的设想, 即将 钢水直接浇铸成薄带钢。经过 )## 多年若干代人的努力, 终于 从 !# 世纪 9# 年代开始陆续有 > 台商业规模的带钢连铸机投入 生产, 其概况是: 生产率, 二是有利于轧制薄规格中厚板, 三是由于热装温度 和热装率高, 节约能源。 新工艺推广很快, 特别是 )99@ 年美国伊 9#年代中期以来, 普斯科公司蒙特利埃厂第一条中等厚度板坯连铸连轧中厚板 生产线投产并取得成功后, 接着进行第二条生产线建设, 泰国 美国俄勒冈公司、 特斯卡洛沙公司和加拿 8.6钢板轧机公司、 大-&ABCD公司等改造工程也相继投入生产。我国南京钢铁集团 公司、 安阳钢铁集团公司、 韶关钢铁集团公司也在建设中等厚 度板坯连铸连轧中厚板生产线, 将在近年内投入生产。 由于 中等厚度板坯连铸机浇铸板坯厚度为 )##$)"#**, 压缩比的限制, 生产中厚板厚度最大 为 =# ** 左 右 , 宽度为 在宽度和厚度方面都有一定限制。 >)##**左右,
金属生产工艺流程

金属生产工艺流程一、金属矿石开采。
金属生产嘛,第一步肯定得把含有金属的矿石从地底下挖出来呀。
这可不是个简单事儿,工人们要先勘探,看看哪里有丰富的矿石资源。
就像寻宝一样,到处找线索呢。
找到合适的地方之后,就开始用各种大型机械挖掘,那些挖掘机、装载机啥的可壮观了。
矿石开采的时候还得注意安全哦,毕竟地下的情况很复杂,一不小心就可能有危险。
而且开采也不能乱采,得按照一定的规划来,这样才能保证资源不被浪费。
二、矿石精选。
把矿石挖出来还不行,里面还混着好多没用的石头和杂质呢。
这时候就要进行精选啦。
就像是从一堆沙子里挑出珍珠一样。
有很多方法来精选矿石哦。
比如说浮选法,这就像让矿石在水里“游泳比赛”,有用的矿石就会浮起来,没用的就沉下去啦。
还有重选法,根据矿石和杂质的重量不一样,把它们分开。
这一步可重要了,如果精选不好,后面生产出来的金属质量就不好啦。
三、冶炼。
矿石精选好了,就到了冶炼这一步。
这可是个超级酷的过程。
就拿炼铁来说吧,要把精选后的铁矿石放进高炉里。
高炉就像一个超级大的热锅,里面温度超高的。
然后加入焦炭和石灰石。
焦炭就像是给这个热锅加燃料,让它一直热乎着。
石灰石呢,就像是个小助手,能把矿石里的杂质去除掉。
在高温下,铁矿石里的铁就慢慢被还原出来了,变成液态的铁水。
这铁水就像火红的岩浆一样,特别壮观。
其他金属的冶炼也有各自的方法,但总体上都是要通过高温或者化学反应把金属从矿石里提取出来。
四、精炼。
冶炼出来的金属可能还不是很纯呢,里面可能还有一些小杂质。
这时候就需要精炼啦。
精炼就像是给金属做个美容,让它变得更完美。
比如说电解精炼,把粗金属当成阳极,纯金属当成阴极,然后通上电,杂质就会被留在电解液里,纯金属就会在阴极上越来越多。
精炼后的金属质量就超级棒啦,可以用于各种高级的地方,像制造飞机、汽车啥的。
五、加工成型。
金属精炼好了之后,就可以根据不同的需求进行加工成型啦。
可以把金属拉成丝,就像把面团拉成面条一样,不过这个“面条”可是金属的哦。
- 1、下载文档前请自行甄别文档内容的完整性,平台不提供额外的编辑、内容补充、找答案等附加服务。
- 2、"仅部分预览"的文档,不可在线预览部分如存在完整性等问题,可反馈申请退款(可完整预览的文档不适用该条件!)。
- 3、如文档侵犯您的权益,请联系客服反馈,我们会尽快为您处理(人工客服工作时间:9:00-18:30)。
金属材料短流程、近终形的生产工艺金属材料短流程、近终形的生产工艺连铸近终形连铸(Near-Net-Shape Continuous Casting)是指使连铸坯的断面尺寸在保证钢材性能、质量的前提下,尽量接近最终钢材断面的形状、尺寸。
近终形生产工艺打破了传统的材料成形与加工模式,缩短了生产工艺流程,简化了工艺环节,实现近终形、短流程的连续化生产,提高生产效率。
近终型、短流程的成形加工技术具有高效、节能等特点,在技术上突出的特点是缩短加工周期,尽量减少变形量或者后续加工环节,由金属熔体直接得到所需的制品或近似的制品,同时,这些制品还具有现有加工方法所生产制品的性能和组织,这可大大减少后续挤压、轧制和压铸等耗能大、投资大、用工多的加工过程。
近终形连铸技术是金属材料研究领域里的一项前沿技术,它的出现为冶金业带来了革命性的变化,改变了传统冶金工业中薄型钢材的生产过程。
它主要包括薄板坯连铸技术、薄带连铸技、喷雾沉积技术等。
目前,薄板坯连铸技术已经进入工业化生产,而大多数薄带坯连铸技术仍主要处于实验室研究阶段,一些技术难点和缺陷还有待进一步解决。
日本预测,到2020年,在连铸技术领域,传统连铸占40%,薄板坯连铸占50%,薄带坯连铸占10%。
1 薄板坯连铸技术薄板坯连铸是介于传统连铸和薄带连铸之间的一种工艺。
世界上第一台薄板坯连铸机于1989年在美国Nucor公司的Crawfordsville工厂投产。
薄板坯的厚度通常为40-50mm,是传统连铸板坯厚度的1/3-l/6。
因此,生产过程中可取消粗轧机而直接进入精轧机。
普通连铸的吨钢投资为800-1200美元,而薄板坯连铸的吨钢投资只有300-500美元,经济效益十分巨大。
1984年,原联邦德国sehloemansiemagsMS公司在高度保密的情况下,着手开始研究薄板坯连铸技术,1986年取得重大进展,1989年第一条薄板坯连铸生产线在美国Nucor公司正式投产。
几年内,薄板坯连铸技术席卷全世界,有几十条薄板连铸生产线已投入工业化生产。
就北美而言,就有11条生产线于1995年和1996年正式投入工业生产。
其中,NorthSta:steel/BHP于1995联合企业投资4亿美元,建一条年产150万吨钢的生产线;IPSCO公司将投资3.6亿美元,建一条年产100万吨钢的生产线,于1996年投产。
目前世界上已开展的薄板坯连铸连轧工艺有:①由德国西马克公司开发的CSP工艺;②由德国德马克公司开发的ISP工艺;③由德国西马克公司、蒂森公司和法国的于齐诺尔公司一起开发的CPR工艺;④意大利达涅利公司开发的薄板坯连铸连轧工艺等。
此外,美国蒂平斯公司和韩国三星重工公司共同开发的TSP技术都陆续被采用,各种技术在竞争中发展迅速。
薄板坯连铸连轧工艺今年来在中国也有很大的发展,北京钢铁研究总院也研制了我国第一台薄板坯连铸机,安装在兰州钢铁集团公司。
1999年8月26日,我国引进的第一条薄板坯连铸连轧生产线(CSP)在广州珠江钢铁有限责任公司投产。
整个生产过程采用计算机控制,从废钢入炉到热轧成板只需2.5h,与需要28h的传统工艺相比,具有明显的竞争优势。
薄板坯连铸连轧工艺生产带钢的成本(从钢水到热带)较传统工艺约低50美元/吨。
薄板坯连铸连轧工艺因总多单位参与研究与开发,形成了各具特色的生产工艺,如:CSP技术、ISP技术、CONROLL技术、FTSR技术、QSP技术、TSP 技术、CPR技术等。
其中应用推广最多的是CSP工艺技术,由西马克.德马格公司开发。
1.1CSP(CompaetstripProduetion)工艺CSP工艺又称为紧凑式热带生产工艺,是由德国施罗曼-西马克公司开发成功的,是目前应用最广泛的薄板坯连铸连轧工艺。
这是目前应用最广泛的薄板坯连铸技术。
1989年7月世界上第一座CSP工厂在Nucor开始投产,经过22个月完全达到设计要求。
由于CSP生产线投产后取得了显著的经济效益,Nucor公司于1990年开始建立第二条CSP生产线。
因为有了第一条CSP生产线的操作经验,Nucor的第二条CSP生产线在投产后8个月就达产了。
1994年4月这两台新建的CSP连铸机也投产。
目前Nucor公司已具有年产热轧卷3-4百万吨的能力。
Nucor公司使用CSP技术成功的经验,促进了CSP技术的推广,1993年美国、墨西哥、韩国的许多钢厂分别与SMS公司签订了购买CSP技术的合同。
目前已有22条生产线32流铸机(包括我国在内)成功地投入了工业生产。
CSP的工艺过程为:采用立弯式连铸机生产厚50-60 mm的铸坯,经分段剪切后,送入辊底式均热炉(120-185 m)进行加热、均热。
薄板坯经加热炉入口段、加热段和均热段加速到20-30 m/min进入轧制工序。
六机架精轧机组将厚50-60 mm的铸坯轧制成1.2-12.7 mm的带材,经层流水帘冷却后卷取。
生产线全长约270 m。
优点:流程短、生产简便、稳定、产品质量好、成本低、有很强的市场竞争力等。
缺点:对钢水质量要求高、难以生产很宽或较厚的钢板等。
1.2 ISP(InlinestripProduetion)工艺ISP工艺也称作在线热带钢生产工艺,是由德国曼内斯曼-德马克公司1989年开发成功的,是世界上第一个在工业条件下采用固液铸轧技术的生产工艺,也被称为无头轧制工艺。
第一家ArvediISP工厂建在意大利的克雷莫纳(Cremona)。
经过两年半的准备和建设,于1992年1月投产。
投产后15个月产量就达到40万吨/年。
ArvdeiISP工厂的设计能力为50万吨/年,1993年9月产量达到了设计水平。
到1994年2月,共生产了55万吨热轧带卷和8万吨厚板。
目前,世界上有6条ISP生产线在运行中。
ISP的工艺过程为:钢包车→中间罐→薄片状浸入式水口→结晶器→铸轧段(厚约40 mm)→大压下量粗轧机(厚约20 mm)→剪切机→感应加热炉→克日莫那炉→精轧机→层流冷却→地下卷取。
生产线全长约175 m。
优点:生产线布置紧凑、生产能耗少等。
缺点:感应加热炉设备较复杂且维修困难、薄片形水口寿命较短等。
1.3 CPR(CastingPressingRolling)工艺CPR工艺即铸压轧工艺,用于生产厚度小于25mm的合金钢和普碳钢热轧带材。
它利用浇铸后的大压下(60%的极限压下量),仅用一组轧机,最终可生产厚度为6mm的薄带卷,也可生产低碳钢、管线钢、铁素体和奥氏体不锈钢及高硅电工钢等。
该生产线包括一台连铸机、一台感应炉、除磷机、一台四辊轧机。
工艺流程示意为:电炉或转炉炼钢→刚爆精炼炉→薄板坯铸压轧→感应加热炉→旋转式高压水除磷机→精轧机→层流冷却→卷取机。
CPR工艺目前已成功进行了半工业实验生产。
第一期半工业实验是1992年12月底前在西马克公司Buschhutten半工业实验工厂进行的,并取得了成功。
这期实验进行的是铸压实验。
在第二期半工业实验中加上了随后的轧制工序。
第二期CSP实验厂从1993年底开始运行,到目前为止已实现了铸、压、轧在线生产,其结果非常令人满意。
CPR的生产能力是CSP的生产能力的40-60%。
年产50万吨热轧卷,厚度为5-25mm,宽度为1500mm,设备总投资为1.5亿马克,每吨钢投资为300马克。
除了以上所说的工艺以为,还有FTSR工艺技术、QSP工艺技术、TSP工艺技术、CONROLL工艺技术等。
2 薄带连铸技术作为生产扁平材的近终形连铸技术,带钢连铸工艺生产的钢带较之薄板坯连铸更接近于最终产品的形状,也就是连铸带钢更薄一些。
它可将钢水直接浇铸出1-10mm厚的钢带,不经热轧或稍经热轧(1-2个机架),即可进行冷轧,而产品的性能和质量仍可与常规生产的产品相媲美。
薄带连铸能大大降低基建投资和生产成本,是当今钢铁工业令人关注的新工艺,也是最热门的研究课题之一。
薄带连铸技术工艺方案因结晶器的不同分为带式、辊式、辊带式等,其中研究得最多、进展最快、最有发展前途的当属双辊薄带连铸技术。
该技术在生产0.7-2 mm厚的薄钢带方面具有独特的优越性,其工艺原理是由两个铸辊和端面侧封板构成钢水池,钢水经浸入式浇铸系统控制,送入辊口,薄带坯厚度通过调节辊缝的大小来控制。
双辊铸机依两辊辊径的不同分为同径双辊铸机和异径双辊铸机,其中尤以同径双辊铸机发展最快,已接近工业规模生产的水平。
由于双辊连铸实现的是双面冷却,其冷却速率较单辊连铸的大,浇铸的薄带坯厚度可大些。
国外的新日铁与三菱重工合作,于1985年开始双辊铸轧不锈钢薄带技术的研究,所建立的铸轧试验机可以生产宽800mm、长1330mm的带卷。
生产的带卷表面无裂纹且组织结构均匀,力学性能和抗腐蚀性能达到或超过用传统工艺生产的带钢。
他们目前已达到工业试验阶段。
此后,澳大利亚的BHP公司、意大利的AST公司、法国的Usinor公司和韩国的浦项钢铁公司也相继进行了双辊铸轧技术的研究,都取得了一定的研究成果。
国内的技术发展也十分迅速,国内东北大学自1958年开始进行薄带钢铸轧方面的研究,在自制的连续铸轧试验机上铸轧出了1-2mm厚、260mm宽的球墨铸铁板和变压器硅钢带。
1983年建立了1号异径双辊式铸轧机。
1990年3月又建成了2号异径双辊式薄带铸轧机,采用直流电机驱动,速度可调,配有磨辊装置,等离子切割机和小型热轧机等。
成功铸轧出2mm×207mm的高速钢薄带。
铸轧出的薄带坯经小变形量的热轧,可做切口铣刀和下料机的锯条,使用性能良好。
1998年,东北大学轧制技术及连轧自动化国家重点实验室的双辊铸轧研究又被列为国家自然科学基金委重大项目。
除了双辊薄带连铸技术以为,还有单辊连铸、双辊连铸、辊带连铸等。
现简单介绍如下:单辊法又称为熔-拖法,原理是钢水从中间包流出,直接浇到旋转辊上,由于铸辊的冷却作用使其凝固,形成薄带。
其缺点是单面凝固会造成产品内部结构不均匀,且长度方向厚度也可能不均匀。
另外,带钢的宽度也不易控制。
辊带连铸工艺中,钢水由中间包浇到活动带上,活动带由安装在下部冷却箱内的喷嘴喷水冷却,铸坯表面由上辊压平。
升起上辊,可进行左右表面连铸操作,铸机后部还安装了一对拉坯辊。
瑞典的梅福斯公司和德国的曼内斯曼·德马克公司合作对这一技术进行了开发试验。
但辊带技术工艺控制复杂,且宽度不能调节,钢液的喂入也很困难。
因此,应有也不如双辊薄带连铸技术广泛。
3 铝合金哈兹列特连铸连轧工艺我国铝加工业存在中低端铝板带材产品过多,生产能力相对过剩,产品竞争激烈,企业效益空间相对变小的局面。
而高附加值、高技术含量的高端铝板带材如电子工业用电子铝箔、罐用深冲铝板、汽车、飞机用铝板等,由于技术上的原因仍主要依赖进口,这严重制约了我国相关产业的发展。