钢铁生产工艺流程ppt
合集下载
钢铁生产流程课堂PPT
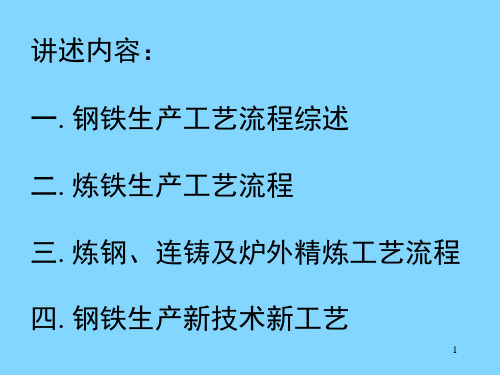
52
(6)切割装置 ·作用:定尺、切割。 ·方式:火焰、机械 ·火焰切割 -设备轻,不受断面限制,切口齐,
有金属损耗; ·机械切割: - 切割速度快 -无金属损耗 -操作安全可靠 -设备投资大,重量较大。
53
连铸机的生产能力
1)连铸机的作业率 指一年的生产时间(含准备时间)占 一年的日历时间的百分数。 y = (C+P)/ D ×100% 其中:y:作业率 C:年浇铸时间 P:年准备时间 D:年日历时间
6.渣铁处理系统 出铁场、渣铁沟、泥炮、开口机、炉前天车、水渣池、渣铁罐车
16
17
7.喷吹系统 煤粉制备、储煤罐、喷吹罐、混合器、喷枪
18
高炉生产技术经济指标
19
20
21
三、炼钢生产工艺流程 •转炉炼钢工艺; •铁水预处理工艺; •钢水炉外精炼处理工艺。
22
钢与生铁的区别:
首先是碳的含量,理论上一般把碳含量 小于2.11%称之钢,它的熔点在14501500℃,而生铁的熔点在1100-1200℃。
31
32
连铸机的种类
连铸机的机型及其特点 2.1.1 连铸机的机型 (1) 按外形分类;
33
(2)按铸坯断面分类:
机型
最大断面 mm×mm
最小断面 mm×mm
经常浇注断面 mm×mm
板坯
300×2640 310×2500
130×250
180×700~ 300×200
大方坯 小方坯
圆坯
600×600 160×160
·要求全凝固矫直,限制了生产率。
37
(3)多点弯曲立弯式连铸机
- 有垂直段,夹杂物容易上浮,具有立
弯
式连铸机的优点;
(6)切割装置 ·作用:定尺、切割。 ·方式:火焰、机械 ·火焰切割 -设备轻,不受断面限制,切口齐,
有金属损耗; ·机械切割: - 切割速度快 -无金属损耗 -操作安全可靠 -设备投资大,重量较大。
53
连铸机的生产能力
1)连铸机的作业率 指一年的生产时间(含准备时间)占 一年的日历时间的百分数。 y = (C+P)/ D ×100% 其中:y:作业率 C:年浇铸时间 P:年准备时间 D:年日历时间
6.渣铁处理系统 出铁场、渣铁沟、泥炮、开口机、炉前天车、水渣池、渣铁罐车
16
17
7.喷吹系统 煤粉制备、储煤罐、喷吹罐、混合器、喷枪
18
高炉生产技术经济指标
19
20
21
三、炼钢生产工艺流程 •转炉炼钢工艺; •铁水预处理工艺; •钢水炉外精炼处理工艺。
22
钢与生铁的区别:
首先是碳的含量,理论上一般把碳含量 小于2.11%称之钢,它的熔点在14501500℃,而生铁的熔点在1100-1200℃。
31
32
连铸机的种类
连铸机的机型及其特点 2.1.1 连铸机的机型 (1) 按外形分类;
33
(2)按铸坯断面分类:
机型
最大断面 mm×mm
最小断面 mm×mm
经常浇注断面 mm×mm
板坯
300×2640 310×2500
130×250
180×700~ 300×200
大方坯 小方坯
圆坯
600×600 160×160
·要求全凝固矫直,限制了生产率。
37
(3)多点弯曲立弯式连铸机
- 有垂直段,夹杂物容易上浮,具有立
弯
式连铸机的优点;
钢铁冶炼过程PPT课件

—氮气在钢铁厂的应用主要是用作保护气,如轧钢、镀锌、镀铬、热处理(尤为薄钢片)连续铸 造等都要用氮气作保护气,而且氮气纯度要求99.99%以上。
—氩气在炼钢过程的作用:如向熔融的钢水中吹入氩气,使成份均匀,钢液净化,并可除掉溶解 在钢水中的氢、氧、氮等杂质,提高钢坯质量。吹氩还可以取消还原期,缩短冶炼时间,提高产 量,节约电能等。氩气吹炼和保护是提高钢材质量的重要途径。
自学互学共同学习一起成才生铁和钢铁的合金生铁含碳的质量分数2430032杂质硅锰较多硫磷较多硅锰适量硫磷较多机械加工可铸不可锻可铸可锻可压延机械性能硬而韧有弹性生铁和钢的比较球墨生铁合金生铁碳素钢低碳钢中碳钢高碳钢炼钢生铁白口铁铸造生铁灰口铁合金钢炼铁
Objectives:
1。重温炼铁和炼钢的基础知识 2。了解炼铁和炼钢的流程和设备 3。通过学习加深对我们用户的了解 4。自学,互学,共同学习,一起成才
原料 设备
铁矿石、石灰石、焦碳、空气 炼铁高炉
生铁(废钢)、纯氧、氧化钙 转炉、平炉、电炉
13
第13页/共29页
ห้องสมุดไป่ตู้
炼钢
转炉结构图
14
第14页/共29页
转炉炼钢:
15
第15页/共29页
电炉炼钢:
16
第16页/共29页
平炉炼钢示意图:
17
第17页/共29页
18
第18页/共29页
19
第19页/共29页
硫、磷杂质与生石灰作用形成炉渣被除去。
④脱氧: Si+2FeO=SiO2+2Fe (脱氧剂:硅铁,锰铁) 调节合金元素
12
第12页/共29页
炼铁和炼钢
炼铁和炼钢的比较
炼铁
炼钢
—氩气在炼钢过程的作用:如向熔融的钢水中吹入氩气,使成份均匀,钢液净化,并可除掉溶解 在钢水中的氢、氧、氮等杂质,提高钢坯质量。吹氩还可以取消还原期,缩短冶炼时间,提高产 量,节约电能等。氩气吹炼和保护是提高钢材质量的重要途径。
自学互学共同学习一起成才生铁和钢铁的合金生铁含碳的质量分数2430032杂质硅锰较多硫磷较多硅锰适量硫磷较多机械加工可铸不可锻可铸可锻可压延机械性能硬而韧有弹性生铁和钢的比较球墨生铁合金生铁碳素钢低碳钢中碳钢高碳钢炼钢生铁白口铁铸造生铁灰口铁合金钢炼铁
Objectives:
1。重温炼铁和炼钢的基础知识 2。了解炼铁和炼钢的流程和设备 3。通过学习加深对我们用户的了解 4。自学,互学,共同学习,一起成才
原料 设备
铁矿石、石灰石、焦碳、空气 炼铁高炉
生铁(废钢)、纯氧、氧化钙 转炉、平炉、电炉
13
第13页/共29页
ห้องสมุดไป่ตู้
炼钢
转炉结构图
14
第14页/共29页
转炉炼钢:
15
第15页/共29页
电炉炼钢:
16
第16页/共29页
平炉炼钢示意图:
17
第17页/共29页
18
第18页/共29页
19
第19页/共29页
硫、磷杂质与生石灰作用形成炉渣被除去。
④脱氧: Si+2FeO=SiO2+2Fe (脱氧剂:硅铁,锰铁) 调节合金元素
12
第12页/共29页
炼铁和炼钢
炼铁和炼钢的比较
炼铁
炼钢
钢板生产工艺流程PPT(29张)

• 常用牌号:SPHC、SPHD、SPHE、SAPH370、SAPH440、
8
镀锌钢板
• 主要分为电镀锌钢板和热镀锌钢板,目前 XX公司用的镀锌钢板都是热镀锌钢板,原 因是热镀锌的成本比较低。是镀纯锌的。 镀纯锌的耐蚀性好。
• 热镀锌钢板的成本要比基板的价格高出800 元/吨。热镀锌钢板的镀层又分为纯锌和锌铁合金。镀锌钢板对焊接性能有较大影响。
• 常用的牌号;B140H1、B180H1
5
双相钢
双相钢是由铁素体和马氏体两相组织构成 的钢板,马氏体弥散分布在铁素体基体上, 马氏体的体积百分比一般不超过20%。钢 板的强度主要由马氏体的体积百分比的多 少决定。 常用的牌号:DP600、DP800。
6
低合金高强钢
• 低合金高强度钢是在低碳钢中添加少量的 Ni或Ti等合金元素(总量不超过3%),使其与 C、N等元素形成碳化物、氮化物并在铁素 体基体上析出从而提高钢的强度。这种钢 具有良好的成形性能和较高的强度,主要 用于汽车座椅表示材料在外载荷下抵抗弹性变形的能
力。钢铁的弹性模量一般为210GPa,不同 类型的材料,其弹性模量可以差别很大。材料的 弹性模量主要取决于结合键的本性和原子间的结 合力,改变材料的成分和组织会对材料的强度(如 屈服强度、抗拉强度)有显著影响,但对材料的刚 度影响不大。 • 例如铁(钢)的弹性模量为210GPa,是铝(铝合金)的 三倍(EAl≈70GPa)。弹性模量是和材料的熔点成正 比的,越是难熔的材料弹性模量也越高。
9
车身钢材的性能指标
• 车身钢材常用的基本性能指标有: • 屈服强度、抗拉强度、伸长率、应变强化
指数n,即加工硬化指数 • 塑性应变比r值,即宽度方向和厚度方向的
变化比值 • 弹性模量E • 硬度
8
镀锌钢板
• 主要分为电镀锌钢板和热镀锌钢板,目前 XX公司用的镀锌钢板都是热镀锌钢板,原 因是热镀锌的成本比较低。是镀纯锌的。 镀纯锌的耐蚀性好。
• 热镀锌钢板的成本要比基板的价格高出800 元/吨。热镀锌钢板的镀层又分为纯锌和锌铁合金。镀锌钢板对焊接性能有较大影响。
• 常用的牌号;B140H1、B180H1
5
双相钢
双相钢是由铁素体和马氏体两相组织构成 的钢板,马氏体弥散分布在铁素体基体上, 马氏体的体积百分比一般不超过20%。钢 板的强度主要由马氏体的体积百分比的多 少决定。 常用的牌号:DP600、DP800。
6
低合金高强钢
• 低合金高强度钢是在低碳钢中添加少量的 Ni或Ti等合金元素(总量不超过3%),使其与 C、N等元素形成碳化物、氮化物并在铁素 体基体上析出从而提高钢的强度。这种钢 具有良好的成形性能和较高的强度,主要 用于汽车座椅表示材料在外载荷下抵抗弹性变形的能
力。钢铁的弹性模量一般为210GPa,不同 类型的材料,其弹性模量可以差别很大。材料的 弹性模量主要取决于结合键的本性和原子间的结 合力,改变材料的成分和组织会对材料的强度(如 屈服强度、抗拉强度)有显著影响,但对材料的刚 度影响不大。 • 例如铁(钢)的弹性模量为210GPa,是铝(铝合金)的 三倍(EAl≈70GPa)。弹性模量是和材料的熔点成正 比的,越是难熔的材料弹性模量也越高。
9
车身钢材的性能指标
• 车身钢材常用的基本性能指标有: • 屈服强度、抗拉强度、伸长率、应变强化
指数n,即加工硬化指数 • 塑性应变比r值,即宽度方向和厚度方向的
变化比值 • 弹性模量E • 硬度
钢铁冶炼与冶金工艺培训ppt

04
工作环境改善
优化工作环境,降低噪声和振动 的影响,为员工创造一个良好的
工作条件。
06
实践操作与案例分析
钢铁冶炼实践操作
钢铁原料准备
了解和掌握各种钢铁原料的 性质、用途和加工方法,以 及合理配比和优化原料的实 践操作。
高炉炼铁工艺
通过实践操作掌握高炉炼铁 的工艺流程、技术参数和操 作要点,包括原料加工、烧 结、高炉炼铁等环节。
无缝钢管轧制技术
无缝钢管轧制技术是生产无缝钢管的主要方法,通过精确 控制轧制温度、压力和变形量得到高质量的无缝钢管。
04
钢铁冶炼环境保护与节能 减排
钢铁冶炼的环境影响
01
02
03
空气污染
钢铁冶炼过程中会产生大 量的烟尘和有害气体,如 硫化物、氮氧化物等,对 空气质量造成严重影响。
水污染
钢铁冶炼过程中产生的废 水含有多种有害物质,如 重金属离子、酸碱物质等 ,对水体造成严重污染。
电炉炼钢技术
电炉炼钢技术是一种节能环保的炼钢方法,通过电能将废钢或生铁熔 化,再加入合金元素来得到不同品质的钢。
炉外精炼技术
炉外精炼技术是在传统的炼钢工艺基础上发展起来的一种新型技术, 通过在钢包中加入各种精炼剂来进一步优化钢的成分和性能。
连铸技术的发展
传统连铸技术
传统的连铸技术是将液态钢倒 入固定模子中,形成钢坯后进 行切割和轧制。
影响。
安全管理与操作规程
建立健全安全管理制度
制定并执行安全生产责任制、安全检查 制度等,确保各项安全工作有序开展。
安全设施配备
配备齐全的安全设施,如防护罩、防 护栏、报警装置等,确保员工在工作
过程中得到有效保护。
操作规程培训
钢铁制造流程脱硫工艺(PPT49页)

有: Na2CO3 CaC2 CaO Mg等
及以其为基础的复合脱硫剂。
3.铁水预处理常用脱硫剂及其特性比较
3.1 Na2CO3基钠系脱硫剂 Na2CO3有很强的脱硫能力,我国在20世纪50年代
就采用洒入高炉出铁沟脱硫的方法; 脱硫反应式:
(Na2CO3 )+〔S〕+2〔C〕=(Na2S)+ 3CO 由于在1250℃以上易挥发形成大量白色浓雾,腐蚀性 强,污染环境。 Na2CO3分解吸热量大, 生成的Na2O进入渣中使渣 变稀,不易扒渣,除渣困难; 价格相对较高,所以已不单独作为脱硫剂使用,仅用 于某些复合脱硫剂的辅助成分。
2. 不同含硫量控制方式的特点与比较
2.6产品含硫量控制成本 研究表明:钢铁制造流程各工序脱除单位质量
硫的成本高低顺序为: 钢冶炼(转炉)﹥二次精炼(钢包炉)﹥炼铁 (高炉)﹥铁水预处理 结论:现代化钢铁制造流程中,都配备有功能 完备的铁水炉外预处理(脱硫)手段
3.铁水预处理常用脱硫剂及其特性比较
部分国家炼钢用石灰技术指标
美国 日本 英国 德国 俄罗斯 中国
成 分 w/%
CaO
SiO2
S
>96
<1 0.035
>92
<2
<0.02 0
>95
<1
<0.05 0
>87~95
<0.05
>90~92 >90
<2 <0.04
<3
<0.10/ 0.05
烧减/% <20 <30 <25 <30 <20 <4
铁水预处理脱硫主要是铁水的炉外脱硫
脱硫原理:使用与硫的亲和力比铁与硫的亲和 力大的元素或化合物(脱硫剂),施以一定的 能量以获得反应的动力学条件,将硫化铁中的 硫转变为更稳定的、极少溶解或完全不溶于铁 液的化合物 (高含硫渣),并将其尽可能完全 地除净。
及以其为基础的复合脱硫剂。
3.铁水预处理常用脱硫剂及其特性比较
3.1 Na2CO3基钠系脱硫剂 Na2CO3有很强的脱硫能力,我国在20世纪50年代
就采用洒入高炉出铁沟脱硫的方法; 脱硫反应式:
(Na2CO3 )+〔S〕+2〔C〕=(Na2S)+ 3CO 由于在1250℃以上易挥发形成大量白色浓雾,腐蚀性 强,污染环境。 Na2CO3分解吸热量大, 生成的Na2O进入渣中使渣 变稀,不易扒渣,除渣困难; 价格相对较高,所以已不单独作为脱硫剂使用,仅用 于某些复合脱硫剂的辅助成分。
2. 不同含硫量控制方式的特点与比较
2.6产品含硫量控制成本 研究表明:钢铁制造流程各工序脱除单位质量
硫的成本高低顺序为: 钢冶炼(转炉)﹥二次精炼(钢包炉)﹥炼铁 (高炉)﹥铁水预处理 结论:现代化钢铁制造流程中,都配备有功能 完备的铁水炉外预处理(脱硫)手段
3.铁水预处理常用脱硫剂及其特性比较
部分国家炼钢用石灰技术指标
美国 日本 英国 德国 俄罗斯 中国
成 分 w/%
CaO
SiO2
S
>96
<1 0.035
>92
<2
<0.02 0
>95
<1
<0.05 0
>87~95
<0.05
>90~92 >90
<2 <0.04
<3
<0.10/ 0.05
烧减/% <20 <30 <25 <30 <20 <4
铁水预处理脱硫主要是铁水的炉外脱硫
脱硫原理:使用与硫的亲和力比铁与硫的亲和 力大的元素或化合物(脱硫剂),施以一定的 能量以获得反应的动力学条件,将硫化铁中的 硫转变为更稳定的、极少溶解或完全不溶于铁 液的化合物 (高含硫渣),并将其尽可能完全 地除净。
某钢铁集团生产工艺流程介绍(PPT 47页)
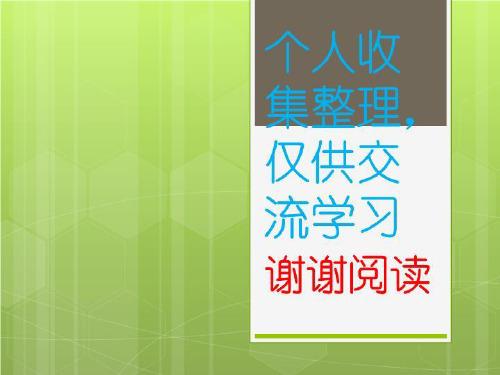
烧结生产的第一道工序是配料,即根 据烧结矿质量标准,把各种原燃料按照相 应比例搭配在一起。配料采用先进的重量 法,就是圆盘给料机加电子皮带称进行配 料。
将配合好的原料运送至混合室,混合 最常用的是圆筒混合机。通过圆筒混合机 不停地转动,各种成份不同的原料逐渐混 匀变成一种化学成分均匀的烧结混合料 (混合料二),圆筒混合机的另一个作用 是通过添加适量的水,在转动作用下使烧 结混合料从粉状变成许多小粒粒状,从而 为下道工序烧结打下良好基础。由于混合 要起到混匀,造粒的作用,所以一般至少 采用二次混合作业,甚至三次、四次的。
烧结工序是整个生产环节中最重要,
最关键的一环,主要将烧结混合料通过燃 料燃烧产生的高温发生许多复杂的物理化 学反应,最终成为烧结矿。烧结过程是在 烧结机台车上进行的,但和烧结机密切配 合的是烧结主抽风机(主抽风机二),抽 风机从烧结机台车下面不间断地抽走燃烧 产生的废气,而使空气源源不断从台车表 层进入混合料,而保证台车上烧结混合料 中的燃料从上而下一直延续下去,才能像 上面说的最终生成烧结矿。烧结过程所用 的设备叫烧结机,主要是带式烧结机,还 有一种步进式平面烧结机。
第三章 球团
我厂建设有2座10平方米竖炉,设计年 产成品球团矿100万吨,于2006年1月份建 成投产,从几个生产实际来看,现已达到 年产120万吨的能力。在这里结合我厂情况, 介绍一下竖炉球团的生产工艺流程。
铁精矿
膨润土
配
料
干
燥
润
磨
高 炉 煤 气
电除尘
竖炉风机
造
球
筛
分
<8m m 烧 结 厂 或 返 回 配 料
焙烧过程通常可分为干燥、预热、焙烧、 均热、冷却(球团带冷机尾部图)5个阶段, 最后经由齿辊破碎机破碎可能粘结的大块 后排出。
将配合好的原料运送至混合室,混合 最常用的是圆筒混合机。通过圆筒混合机 不停地转动,各种成份不同的原料逐渐混 匀变成一种化学成分均匀的烧结混合料 (混合料二),圆筒混合机的另一个作用 是通过添加适量的水,在转动作用下使烧 结混合料从粉状变成许多小粒粒状,从而 为下道工序烧结打下良好基础。由于混合 要起到混匀,造粒的作用,所以一般至少 采用二次混合作业,甚至三次、四次的。
烧结工序是整个生产环节中最重要,
最关键的一环,主要将烧结混合料通过燃 料燃烧产生的高温发生许多复杂的物理化 学反应,最终成为烧结矿。烧结过程是在 烧结机台车上进行的,但和烧结机密切配 合的是烧结主抽风机(主抽风机二),抽 风机从烧结机台车下面不间断地抽走燃烧 产生的废气,而使空气源源不断从台车表 层进入混合料,而保证台车上烧结混合料 中的燃料从上而下一直延续下去,才能像 上面说的最终生成烧结矿。烧结过程所用 的设备叫烧结机,主要是带式烧结机,还 有一种步进式平面烧结机。
第三章 球团
我厂建设有2座10平方米竖炉,设计年 产成品球团矿100万吨,于2006年1月份建 成投产,从几个生产实际来看,现已达到 年产120万吨的能力。在这里结合我厂情况, 介绍一下竖炉球团的生产工艺流程。
铁精矿
膨润土
配
料
干
燥
润
磨
高 炉 煤 气
电除尘
竖炉风机
造
球
筛
分
<8m m 烧 结 厂 或 返 回 配 料
焙烧过程通常可分为干燥、预热、焙烧、 均热、冷却(球团带冷机尾部图)5个阶段, 最后经由齿辊破碎机破碎可能粘结的大块 后排出。
钢铁制造流程脱硫工艺.ppt

4.1 当前主流铁水预处理脱硫的工艺方法 鱼雷罐喷吹法
脱硫剂:CaC2基;CaO基; 铁水包喷吹法
脱硫剂:CaC2基;CaO基;Mg+CaO;Mg; 机械搅拌法
脱硫剂:CaO基(CaO+CaF2或Na2CO3);
4.2当前最新建成的铁水脱硫设施工艺、装备分析比较 机械搅拌法
KR法(CaO基) 铁水包喷吹法
2.4铁水预处理脱硫 铁水脱硫相对于钢水脱硫有利的因素:
◆含有较高的C、Si、P等元素,提高了 铁水中硫的活度系数;
◆铁水中氧含量低,提高渣铁之间硫分 配比,脱硫效率高;
◆铁水含氧量低,因而可以使用强脱硫 剂强化脱硫而不会造成强烈氧化损失;
◆脱硫过程对最终钢的成分及性能不会
铁水脱硫相对于钢水脱硫的不利因素 ◆由于后续炼钢的氧化过程,铁水脱硫后
美国 日本 英国 德国 俄罗斯 中国
成 分 w/%
CaO
SiO2
S
>96
<1 0.035
>92
<2
<0.02 0
>95
<1
<0.05 0
>87~95
<0.05
>90~92 >90
<2 <0.04
Байду номын сангаас
<3
<0.10/ 0.05
烧减/% <20 <30 <25 <30 <20 <4
块度/㎜
7~30 4~30 7~40 8~40 8~30 5~40
(1)
2CaO(S) +2[S] +[Si]=2[Fe] +2CaS(S)+SiO2 (S) (2)
钢铁生产流程PPT演示课件

φ 450
200×200 55×55 φ 100
250×250~ 450×450 240×280~ 400×560
90×90~ 150×150
φ 200~φ 300
异性坯
工字型 460×460×120
中空坯 φ 450/6100
椭圆型 120×140
35
(3)按钢液压头分类
表2-2各种机型按钢水静压头分类特征
高炉一代寿命——炉龄 (10~15年,现要求20年以上)
11
2.高炉上料系统
上料系统——炉料料仓 筛分
称量
料罐 皮带机 ( 斜桥料车)
12
3.装料系统
装料系统: 受料斗 布料装置
探尺 均压、 放散阀
钟式炉顶
无料钟炉顶
13
4.送风系统
高炉鼓风机、热风炉、热风总管、热风支管、风口设备 国内热风炉有三种形式:内燃式、外燃式、顶燃式
26
铁水预处理与 钢水炉外精炼处理工艺
27
连铸工艺与设备
1 现代炼钢技术的发展(连铸技术的作用) (1) 1947年-1974年: 技术特点:转炉、高炉的大型化;以模铸-初 轧为核心,生产外延扩大。 (2) 1974年-1989年: 技术特点:全连铸工艺,以连铸机为核心。 (3) 1989年-现在:
技术特点:连铸-连轧工艺,以薄板 坯,连铸-连轧为代表,钢厂向紧凑化发展。
28
连续铸钢的技术特点
· 高效凝固 · 优化成型 · 化学冶金 · 物理冶金 · 节能
29
凝固理论
30
31
连续铸钢的工艺特点 (1)提高综合成材率:模铸从钢水到成坯的收 得 率大约84~88%,连铸为95~96%; (2)降低能耗:连铸节能主要是省去了开坯工序, 以及提高成材率。生产一吨钢坯比模铸可以节能 627~1046kJ,相当于21.4~35.7kg标准煤。加上综 合成材率的提高, 可以节能约130kg标准煤; (3)连铸产品的均一性好,质量好; (4)易于实现机械化和自动化。
200×200 55×55 φ 100
250×250~ 450×450 240×280~ 400×560
90×90~ 150×150
φ 200~φ 300
异性坯
工字型 460×460×120
中空坯 φ 450/6100
椭圆型 120×140
35
(3)按钢液压头分类
表2-2各种机型按钢水静压头分类特征
高炉一代寿命——炉龄 (10~15年,现要求20年以上)
11
2.高炉上料系统
上料系统——炉料料仓 筛分
称量
料罐 皮带机 ( 斜桥料车)
12
3.装料系统
装料系统: 受料斗 布料装置
探尺 均压、 放散阀
钟式炉顶
无料钟炉顶
13
4.送风系统
高炉鼓风机、热风炉、热风总管、热风支管、风口设备 国内热风炉有三种形式:内燃式、外燃式、顶燃式
26
铁水预处理与 钢水炉外精炼处理工艺
27
连铸工艺与设备
1 现代炼钢技术的发展(连铸技术的作用) (1) 1947年-1974年: 技术特点:转炉、高炉的大型化;以模铸-初 轧为核心,生产外延扩大。 (2) 1974年-1989年: 技术特点:全连铸工艺,以连铸机为核心。 (3) 1989年-现在:
技术特点:连铸-连轧工艺,以薄板 坯,连铸-连轧为代表,钢厂向紧凑化发展。
28
连续铸钢的技术特点
· 高效凝固 · 优化成型 · 化学冶金 · 物理冶金 · 节能
29
凝固理论
30
31
连续铸钢的工艺特点 (1)提高综合成材率:模铸从钢水到成坯的收 得 率大约84~88%,连铸为95~96%; (2)降低能耗:连铸节能主要是省去了开坯工序, 以及提高成材率。生产一吨钢坯比模铸可以节能 627~1046kJ,相当于21.4~35.7kg标准煤。加上综 合成材率的提高, 可以节能约130kg标准煤; (3)连铸产品的均一性好,质量好; (4)易于实现机械化和自动化。
最全钢铁企业制造流程

§1970年开发顶底复合吹炼转炉;
§1964年我国第1家氧气顶吹转炉炼钢厂在首钢建成投产,与 此同时我国太钢从奥钢联引进了2台50 t氧气顶吹转炉,使我 国的氧气顶吹转炉炼钢进入了发展的初始阶段。
PPT文档演模板
2020/11/17
最全钢铁企业制造流程
转炉炼钢
PPT文档演模板
2020/11/17
最全钢铁企业制造流程
将高温钢液连续地浇铸到一个或多个强制水冷的金属型腔内。凝 固成形后,再经二次冷却,使之凝固,且成一定形状(规格)铸坯的 工艺方法,其典型特征是生产过程的连续化。
PPT文档演模板
2020/11/17
最全钢铁企业制造流程
连铸工艺——设备
PPT文档演模板
2020/11/17
最全钢铁企业制造流程
连铸工艺——相关技术
– 振动装置 采用小振幅高频率的结晶器振动,一般频率可达0~360次/min, 振幅<10mm(有的为±4mm)。
– 二冷控制 精确控制二次喷水冷却。按不同钢种、不同拉速自动调节,均 匀冷却。尽管气-水雾冷却会增加控制上的困难、价格较高,但对特殊钢 连铸来说仍是十分必要的。
– 自动控制 采用计算机控制对稳定铸坯质量非常重要。
§看炉口的火,听声音。看火亮度--加第二批(渣料)--提 枪化渣,控制“返干”。
§降枪控制终点(FeO),倒炉取样测温,出钢。 §技术水平高的炉长,一次命中率高。50%。(宝钢是付枪)
根据分析取样结果--决定出钢(或补吹)--脱氧、合金化。
不要补吹的就是通常说的一次命中。
PPT文档演模板
2020/11/17
§ 铁水脱硫预处理的工艺方法
– 投掷法: 将脱硫剂投入铁水中 – 喷吹法: 将脱硫剂喷入铁水中 – 搅拌法(KB法): 将通过中空机械搅拌器向铁水内加入脱硫剂,搅拌脱硫。
§1964年我国第1家氧气顶吹转炉炼钢厂在首钢建成投产,与 此同时我国太钢从奥钢联引进了2台50 t氧气顶吹转炉,使我 国的氧气顶吹转炉炼钢进入了发展的初始阶段。
PPT文档演模板
2020/11/17
最全钢铁企业制造流程
转炉炼钢
PPT文档演模板
2020/11/17
最全钢铁企业制造流程
将高温钢液连续地浇铸到一个或多个强制水冷的金属型腔内。凝 固成形后,再经二次冷却,使之凝固,且成一定形状(规格)铸坯的 工艺方法,其典型特征是生产过程的连续化。
PPT文档演模板
2020/11/17
最全钢铁企业制造流程
连铸工艺——设备
PPT文档演模板
2020/11/17
最全钢铁企业制造流程
连铸工艺——相关技术
– 振动装置 采用小振幅高频率的结晶器振动,一般频率可达0~360次/min, 振幅<10mm(有的为±4mm)。
– 二冷控制 精确控制二次喷水冷却。按不同钢种、不同拉速自动调节,均 匀冷却。尽管气-水雾冷却会增加控制上的困难、价格较高,但对特殊钢 连铸来说仍是十分必要的。
– 自动控制 采用计算机控制对稳定铸坯质量非常重要。
§看炉口的火,听声音。看火亮度--加第二批(渣料)--提 枪化渣,控制“返干”。
§降枪控制终点(FeO),倒炉取样测温,出钢。 §技术水平高的炉长,一次命中率高。50%。(宝钢是付枪)
根据分析取样结果--决定出钢(或补吹)--脱氧、合金化。
不要补吹的就是通常说的一次命中。
PPT文档演模板
2020/11/17
§ 铁水脱硫预处理的工艺方法
– 投掷法: 将脱硫剂投入铁水中 – 喷吹法: 将脱硫剂喷入铁水中 – 搅拌法(KB法): 将通过中空机械搅拌器向铁水内加入脱硫剂,搅拌脱硫。
钢铁厂生产工艺流程介绍PPT钢铁生产流程
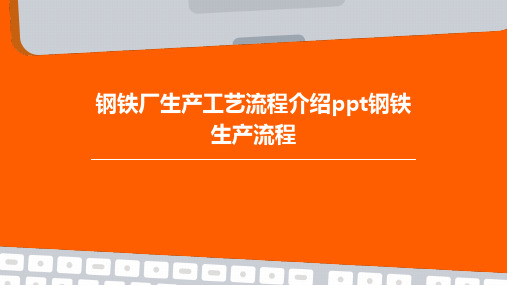
钢材切割与焊接总结词
钢材切割与焊接是钢铁生产中的重要环节, 通过切割与焊接工艺将钢材加工成各种形状 和尺寸的零件或结构件。
详细描述
切割工艺包括火焰切割、激光切割和等离子 切割等多种方式,根据不同的材料和切割要 求选择合适的切割方式。焊接工艺则通过熔 融的焊料将钢材连接在一起,常用的焊接方 法有电弧焊、气体保护焊和激光焊等。
钢材表面处理
总结词
钢材表面处理是钢铁生产中的重要环节,通过表面处理工艺提高钢材的耐腐蚀性和美观 度。
详细描述
表面处理工艺包括喷涂、电镀、热浸镀和化学镀等多种方式。喷涂工艺通过喷涂涂料或 油漆在钢材表面形成保护膜,提高耐腐蚀性和美观度。电镀和热浸镀工艺则是通过在钢 材表面沉积金属或合金层,提高耐腐蚀性和耐磨性。化学镀则是通过化学反应在钢材表
焦炭燃烧
焦炭在炉内燃烧,产生高温和 一氧化碳还原剂。
熔融状态
铁矿石在高温下熔化成铁水, 从炉底排出。
矿石与焦炭装入
将准备好的铁矿石和焦炭装入 高炉炉顶的料仓。
矿石还原
一氧化碳与铁矿石中的氧反应, 将铁元素从矿石中还原出来。
炉渣形成
未还原的杂质和熔剂形成炉渣, 与铁水分离。
其他炼铁方法
直接还原法
氧气转炉法
面形成金属或合金镀层,提高美观度和性能。
06
钢铁生产中的环境保护 与节能减排
废气处理与排放控制
废气处理
钢铁厂在生产过程中会产生大量的废气,包 括烧结、炼铁、炼钢等工序产生的烟气和粉 尘。这些废气需要进行处理,以减少对环境 的污染。常见的废气处理方法包括除尘、脱 硫、脱硝等。
排放控制
钢铁厂的废气排放需要符合国家和地方的相 关标准,对于超标排放的企业将会受到相应 的处罚。因此,钢铁厂需要采取有效的排放
钢材切割与焊接是钢铁生产中的重要环节, 通过切割与焊接工艺将钢材加工成各种形状 和尺寸的零件或结构件。
详细描述
切割工艺包括火焰切割、激光切割和等离子 切割等多种方式,根据不同的材料和切割要 求选择合适的切割方式。焊接工艺则通过熔 融的焊料将钢材连接在一起,常用的焊接方 法有电弧焊、气体保护焊和激光焊等。
钢材表面处理
总结词
钢材表面处理是钢铁生产中的重要环节,通过表面处理工艺提高钢材的耐腐蚀性和美观 度。
详细描述
表面处理工艺包括喷涂、电镀、热浸镀和化学镀等多种方式。喷涂工艺通过喷涂涂料或 油漆在钢材表面形成保护膜,提高耐腐蚀性和美观度。电镀和热浸镀工艺则是通过在钢 材表面沉积金属或合金层,提高耐腐蚀性和耐磨性。化学镀则是通过化学反应在钢材表
焦炭燃烧
焦炭在炉内燃烧,产生高温和 一氧化碳还原剂。
熔融状态
铁矿石在高温下熔化成铁水, 从炉底排出。
矿石与焦炭装入
将准备好的铁矿石和焦炭装入 高炉炉顶的料仓。
矿石还原
一氧化碳与铁矿石中的氧反应, 将铁元素从矿石中还原出来。
炉渣形成
未还原的杂质和熔剂形成炉渣, 与铁水分离。
其他炼铁方法
直接还原法
氧气转炉法
面形成金属或合金镀层,提高美观度和性能。
06
钢铁生产中的环境保护 与节能减排
废气处理与排放控制
废气处理
钢铁厂在生产过程中会产生大量的废气,包 括烧结、炼铁、炼钢等工序产生的烟气和粉 尘。这些废气需要进行处理,以减少对环境 的污染。常见的废气处理方法包括除尘、脱 硫、脱硝等。
排放控制
钢铁厂的废气排放需要符合国家和地方的相 关标准,对于超标排放的企业将会受到相应 的处罚。因此,钢铁厂需要采取有效的排放
- 1、下载文档前请自行甄别文档内容的完整性,平台不提供额外的编辑、内容补充、找答案等附加服务。
- 2、"仅部分预览"的文档,不可在线预览部分如存在完整性等问题,可反馈申请退款(可完整预览的文档不适用该条件!)。
- 3、如文档侵犯您的权益,请联系客服反馈,我们会尽快为您处理(人工客服工作时间:9:00-18:30)。
蓬勃兴起。30多年来,先后有阿姆科(Armco)法、普罗费尔
非高炉炼铁
转底炉直接还原技术(RHF)是铁矿粉(或红土镍矿、钒钛磁铁矿、硫酸渣或 冶金粉尘、除尘灰、炼钢污泥等)经配料、混料、制球和干燥后的含碳球团加 入到具有环形炉膛和可转动的炉底的转底炉中,在1350 ℃ 左右炉膛温度下, 在随着炉底旋转一周的过程中,铁矿被碳还原。当铁矿粉含铁品位在67%以上, 采用转底炉直接还原工艺,产品为金属化球团供电炉使用;当矿粉含铁品位低 于62%时,采用转底炉——熔分炉的熔融还原铁工艺,产品为铁水供炼钢使用。
4300t/-d。
转炉炼钢
转炉生产流程:炼钢厂先将熔铣送前处理站作脱硫脱磷处理,经转炉吹炼后, 再依订单钢种特性及品质需求,送二次精炼处理站(RH真空脱气处理站、
Ladle Injection盛桶吹射处理站、VOD真空吹氧脱碳处理站、STN搅拌站等)进 行各种处理,调整钢液成份,最后送大钢胚及扁钢胚连续铸造机,浇铸成红 热钢胚半成品,经检验、研磨或烧除表面缺陷,或直接送下游轧制成条钢、
-
冷轧
酸洗冷轧 第一酸洗冷轧线:第一酸洗冷轧线接收热轧钢卷,经过解卷、 焊接、整平、盐酸酸洗、裁边之后,再经由串列式冷轧机轧延 成厚度较薄之冷轧钢卷。
通常金属化率可达80%以上,- 金属化球团可作为高炉原料。
非高炉炼铁
COREX法是由原联邦德国KORF公司和奥地利VOEST-ALPINE公司联合开发的 一种无焦炼铁的熔融还原炼铁工艺。原名KR法,是在KORF工程公司拥有的
米德莱克斯(Midrex)竖炉直接还原法基础上发展起来的。
-
非高炉炼铁
Finex是一种直接用粉矿和非炼焦煤粉冶炼铁水的新工艺。 Finex工艺的关键技术是在主流化床反应器内将铁矿粉还原成粉状DRI(直接 还原铁),DRI经热压成形后,利用熔融气化炉将DRI热压铁块熔融还原为铁 水。与传统的高炉炼铁工艺相比,Finex炼铁工艺省去了炼焦和烧结过程,生 产的铁水质量可以与高炉及Corex工艺相媲美。目前,世界上唯一一座Finex工 艺装备(年产150万t铁水)已于2007年4月10日在浦项点火投产,设计产能
-
热轧 第二热轧生产流程
热连轧 热轧生产流程>第二热轧钢带生产流程:热轧钢带工场主要制 程是将扁钢胚加热后,经粗轧机及精轧机轧延成钢带,并以层流 冷却系统喷水冷却至适当温度,再由盘卷机卷成粗钢卷。
-
热轧 调质
热轧生产流程>三号,四号调质重卷线布置图:主要功能为将 原料钢卷上线解卷、调质轧延、分切、重卷及包装为成品 H.R COIL 或 H.R BAND〔HR BAND 未调质轧延〕。
线材、钢板、钢卷及钢片等成品。
-
电炉炼钢
电炉炼钢主要利用电弧热,在电弧作用区,温度高达4000℃。冶炼过程一般分为 熔化期、氧化期和还原期,在炉内不仅能造成氧化气氛,还能造成还原气氛,因
此脱磷、脱硫的效率很高。 以电为能源的炼钢过程。 此类炼钢炉即电炉种类有电弧炉、感应电炉、电渣炉、电子束炉、自耗电弧炉等。 通常说的电炉钢是用碱性电弧炉生产的钢。 电炉钢多用来生产优质碳素结构钢、工具- 钢和合金钢等。这类钢质量良、性能
胚,板状形即为扁钢胚。此半成品视需要经钢胚表面处理后,再送轧钢厂轧延。
-
热轧
-
第一热轧生产流程
热连轧 热轧生产流程>第一热轧钢带生产流程:热轧钢带工场主要制 程是将扁钢胚加热后,经粗轧机及精轧机轧延成钢带,并以层流 冷却系统喷水冷却至适当温度,再由盘卷机卷成粗钢卷。
-
热轧 开平剪切
热轧生产流程>热轧板剪切线布置图:主要功能为将原料钢卷 上线解卷、切边、切片、整平、堆叠、及包装为成品钢板叠 (HR PLATE)。
炼焦炉内经干馏后产生热焦碳及粗焦炉气之制程。
-
烧结
烧结生产流程:烧结作业系将粉铁矿,各类助熔剂及细 焦炭经由混拌、造粒后,经由布料系统加入烧结机,由 点火炉点燃细焦炭 ,经由抽气风车抽风完成烧结反应, 高热之烧结矿经破碎冷却、筛- 选后,送往高炉作为冶炼
球团
篦机-回转窑-环冷机球团生产工艺过程主要包括以下几个部分:制煤 系统、原料系统、干配系统、造球焙烧系统、润磨系统。球团生产过 程可概述为:将准备好的原料(细磨精矿和添加剂等),按一定比例 经过干配混匀后,进入造球系统造- 球,然后进入链篦机-回转窑-环冷 机进行干燥、高温焙烧、冷却,直至送入成品系统。其中回转窑高温
-
热轧 调质
热轧生产流程>一号,二号调质重卷线布置图:主要功能为将 原料钢卷上线解卷、调质轧延、分切、重卷及包装为成品 H.R COIL 或 H.R BAND〔HR BAND 未调质轧延〕。
-
热轧 酸洗涂油
热轧生产流程>酸洗涂油线设备布置图:主要功能为将原料钢 卷上线解卷、焊接、整平、酸洗、调质轧延、切边、涂油、 分切及包装为成品酸洗钢卷。
钢铁生产工艺流程
占世界黑色冶金工业产能80%以上的钢 铁企业,都是采用传统“烧结——炼 铁——炼钢——轧制”长流程生产工艺, 它具有高效率、大批量生产钢材的优点, 远超使用电炉炼钢及直接还原铁工艺的
产量。 下面我们以某厂的生产工艺流程来了解 了解钢材生产
-
炼焦
炼焦生产流程:炼焦作业是将焦煤经混合,破碎后加入
高炉炼铁
高炉生产流程:高炉作业是将铁矿石、焦炭及助熔剂由高炉顶部加 入炉内,再由炉下部鼓风嘴 鼓入高温热风,产生还原气体,还原铁
矿石,产生熔融铁水与熔渣之炼铁制程。
-
非高炉炼铁
在竖炉中用高温还原气或固体还原剂还原铁矿石的直接还原炼铁方 法。该法是1932年由马丁·韦伯(Wiberg)发明的在瑞典建成了第一 座生产装置,称维伯尔法(Wiberg Soderfors process)。此法开始是 用木炭制造还原气。后因经济上的原因,改用焦炭制气。60年代, 随着石油、天然气工业的发展,以- 天然气为能源的竖炉直接还原法
连铸制坯
连铸生产流程:连续铸造作业乃是将钢液转变成钢胚之过程。上游处理完成之钢液, 以盛钢桶运送到转台,经由钢液分配器分成数股,分别注入特定形状之铸模内,开始 冷却凝固成形,生成外为凝固壳、内为钢液之铸胚,接着铸胚被引拔到弧状铸道中, 经二次冷却继续凝固到完全凝固。经矫直后再依订单长度切割成块,方块形即为大钢
非高炉炼铁
转底炉直接还原技术(RHF)是铁矿粉(或红土镍矿、钒钛磁铁矿、硫酸渣或 冶金粉尘、除尘灰、炼钢污泥等)经配料、混料、制球和干燥后的含碳球团加 入到具有环形炉膛和可转动的炉底的转底炉中,在1350 ℃ 左右炉膛温度下, 在随着炉底旋转一周的过程中,铁矿被碳还原。当铁矿粉含铁品位在67%以上, 采用转底炉直接还原工艺,产品为金属化球团供电炉使用;当矿粉含铁品位低 于62%时,采用转底炉——熔分炉的熔融还原铁工艺,产品为铁水供炼钢使用。
4300t/-d。
转炉炼钢
转炉生产流程:炼钢厂先将熔铣送前处理站作脱硫脱磷处理,经转炉吹炼后, 再依订单钢种特性及品质需求,送二次精炼处理站(RH真空脱气处理站、
Ladle Injection盛桶吹射处理站、VOD真空吹氧脱碳处理站、STN搅拌站等)进 行各种处理,调整钢液成份,最后送大钢胚及扁钢胚连续铸造机,浇铸成红 热钢胚半成品,经检验、研磨或烧除表面缺陷,或直接送下游轧制成条钢、
-
冷轧
酸洗冷轧 第一酸洗冷轧线:第一酸洗冷轧线接收热轧钢卷,经过解卷、 焊接、整平、盐酸酸洗、裁边之后,再经由串列式冷轧机轧延 成厚度较薄之冷轧钢卷。
通常金属化率可达80%以上,- 金属化球团可作为高炉原料。
非高炉炼铁
COREX法是由原联邦德国KORF公司和奥地利VOEST-ALPINE公司联合开发的 一种无焦炼铁的熔融还原炼铁工艺。原名KR法,是在KORF工程公司拥有的
米德莱克斯(Midrex)竖炉直接还原法基础上发展起来的。
-
非高炉炼铁
Finex是一种直接用粉矿和非炼焦煤粉冶炼铁水的新工艺。 Finex工艺的关键技术是在主流化床反应器内将铁矿粉还原成粉状DRI(直接 还原铁),DRI经热压成形后,利用熔融气化炉将DRI热压铁块熔融还原为铁 水。与传统的高炉炼铁工艺相比,Finex炼铁工艺省去了炼焦和烧结过程,生 产的铁水质量可以与高炉及Corex工艺相媲美。目前,世界上唯一一座Finex工 艺装备(年产150万t铁水)已于2007年4月10日在浦项点火投产,设计产能
-
热轧 第二热轧生产流程
热连轧 热轧生产流程>第二热轧钢带生产流程:热轧钢带工场主要制 程是将扁钢胚加热后,经粗轧机及精轧机轧延成钢带,并以层流 冷却系统喷水冷却至适当温度,再由盘卷机卷成粗钢卷。
-
热轧 调质
热轧生产流程>三号,四号调质重卷线布置图:主要功能为将 原料钢卷上线解卷、调质轧延、分切、重卷及包装为成品 H.R COIL 或 H.R BAND〔HR BAND 未调质轧延〕。
线材、钢板、钢卷及钢片等成品。
-
电炉炼钢
电炉炼钢主要利用电弧热,在电弧作用区,温度高达4000℃。冶炼过程一般分为 熔化期、氧化期和还原期,在炉内不仅能造成氧化气氛,还能造成还原气氛,因
此脱磷、脱硫的效率很高。 以电为能源的炼钢过程。 此类炼钢炉即电炉种类有电弧炉、感应电炉、电渣炉、电子束炉、自耗电弧炉等。 通常说的电炉钢是用碱性电弧炉生产的钢。 电炉钢多用来生产优质碳素结构钢、工具- 钢和合金钢等。这类钢质量良、性能
胚,板状形即为扁钢胚。此半成品视需要经钢胚表面处理后,再送轧钢厂轧延。
-
热轧
-
第一热轧生产流程
热连轧 热轧生产流程>第一热轧钢带生产流程:热轧钢带工场主要制 程是将扁钢胚加热后,经粗轧机及精轧机轧延成钢带,并以层流 冷却系统喷水冷却至适当温度,再由盘卷机卷成粗钢卷。
-
热轧 开平剪切
热轧生产流程>热轧板剪切线布置图:主要功能为将原料钢卷 上线解卷、切边、切片、整平、堆叠、及包装为成品钢板叠 (HR PLATE)。
炼焦炉内经干馏后产生热焦碳及粗焦炉气之制程。
-
烧结
烧结生产流程:烧结作业系将粉铁矿,各类助熔剂及细 焦炭经由混拌、造粒后,经由布料系统加入烧结机,由 点火炉点燃细焦炭 ,经由抽气风车抽风完成烧结反应, 高热之烧结矿经破碎冷却、筛- 选后,送往高炉作为冶炼
球团
篦机-回转窑-环冷机球团生产工艺过程主要包括以下几个部分:制煤 系统、原料系统、干配系统、造球焙烧系统、润磨系统。球团生产过 程可概述为:将准备好的原料(细磨精矿和添加剂等),按一定比例 经过干配混匀后,进入造球系统造- 球,然后进入链篦机-回转窑-环冷 机进行干燥、高温焙烧、冷却,直至送入成品系统。其中回转窑高温
-
热轧 调质
热轧生产流程>一号,二号调质重卷线布置图:主要功能为将 原料钢卷上线解卷、调质轧延、分切、重卷及包装为成品 H.R COIL 或 H.R BAND〔HR BAND 未调质轧延〕。
-
热轧 酸洗涂油
热轧生产流程>酸洗涂油线设备布置图:主要功能为将原料钢 卷上线解卷、焊接、整平、酸洗、调质轧延、切边、涂油、 分切及包装为成品酸洗钢卷。
钢铁生产工艺流程
占世界黑色冶金工业产能80%以上的钢 铁企业,都是采用传统“烧结——炼 铁——炼钢——轧制”长流程生产工艺, 它具有高效率、大批量生产钢材的优点, 远超使用电炉炼钢及直接还原铁工艺的
产量。 下面我们以某厂的生产工艺流程来了解 了解钢材生产
-
炼焦
炼焦生产流程:炼焦作业是将焦煤经混合,破碎后加入
高炉炼铁
高炉生产流程:高炉作业是将铁矿石、焦炭及助熔剂由高炉顶部加 入炉内,再由炉下部鼓风嘴 鼓入高温热风,产生还原气体,还原铁
矿石,产生熔融铁水与熔渣之炼铁制程。
-
非高炉炼铁
在竖炉中用高温还原气或固体还原剂还原铁矿石的直接还原炼铁方 法。该法是1932年由马丁·韦伯(Wiberg)发明的在瑞典建成了第一 座生产装置,称维伯尔法(Wiberg Soderfors process)。此法开始是 用木炭制造还原气。后因经济上的原因,改用焦炭制气。60年代, 随着石油、天然气工业的发展,以- 天然气为能源的竖炉直接还原法
连铸制坯
连铸生产流程:连续铸造作业乃是将钢液转变成钢胚之过程。上游处理完成之钢液, 以盛钢桶运送到转台,经由钢液分配器分成数股,分别注入特定形状之铸模内,开始 冷却凝固成形,生成外为凝固壳、内为钢液之铸胚,接着铸胚被引拔到弧状铸道中, 经二次冷却继续凝固到完全凝固。经矫直后再依订单长度切割成块,方块形即为大钢