铸钢件生产工艺流程 PPT
《铸造生产工艺》课件

质量控制
原材料控制
确保使用的原材料质量合格,无杂质 且成分稳定。
模具设计与制造
采用先进的模具设计技术,确保模具 精度和寿命,减少铸件缺陷。
工艺参数优化
通过调整金属液的浇注温度、模具温 度等工艺参数,提高铸件质量。
后处理与检验
对铸件进行必要的后处理,如热处理 、机加工等,并进行严格的质量检验 ,确保产品合格。
铸造设备的组成
铸造设备通常由熔炼设备、浇注设备、造型设备 、清理设备和检测设备等组成。
铸造设备的特点
铸造设备具有高效、自动化和环保等特点,能够 提高铸件的质量和生产效率,降低生产成本和能 耗。
03 铸造生产工艺流程
CHAPTER
造型
01
造型是铸造生产流程的起始阶段,主要任务是根据产品需求和 工艺要求,制作出符合要求的铸型。
根据铸件的使用要求和工艺要 求,选择合适的铸造材料,以
保证铸件的质量和性能。
铸造设备
铸造设备的分类
根据其用途和功能,铸造设备可分为砂型铸造设 备、特种铸造设备和造型设备等。
铸造设备的工作原理
熔炼设备将金属材料熔化为液态,浇注设备将液 态金属注入模具中,造型设备将砂型或模具中的 金属液凝固成为铸件,清理设备则对铸件进行表 面处理和清理。
02
铸造生产工艺是机械制造行业中 的重要基础工艺之一,广泛应用 于汽车、船舶、航空、农业机械 、电力、化工等各个行业。
铸造生产工艺的流程
铸造生产工艺流程包括
浇注
熔炼、浇注、冷却、落砂、清理和后 处理等步骤。
将熔融态的金属注入铸型中,形成所 需形状的铸件。
熔炼
将金属材料加热至熔融状态,并加入 必要的合金元素,以获得所需的化学 成分和物理性能。
钢铁厂生产工分艺流程介绍PPT钢铁生产流程
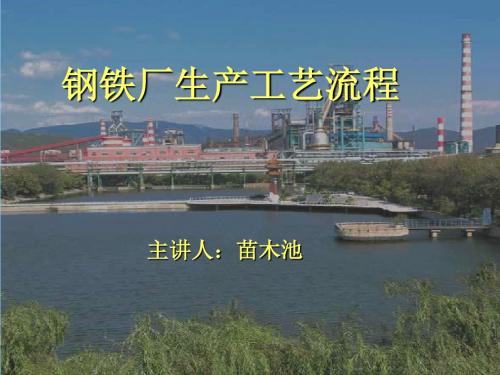
(3)结晶器及其振动装置
- 结晶器:
在连铸生产中,高拉速条件下保证
有
均匀的坯壳厚度而不致拉漏。
-良好的导热性
-钢液和内壁不粘结
-有一定刚度
-结构简单,重量轻
类型有:整体型、管式、组合式结晶器
薄板坯连铸结 晶器
- 振动装置 ·作用: - 防止初生坯壳金额结晶器壁粘结 - 避免拉漏坯壳 - 改善表面质量
铁水预处理与 钢水炉外精炼处理工艺
连铸工艺与设备
1 现代炼钢技术的发展(连铸技术的作用) (1) 1947年-1974年: 技术特点:转炉、高炉的大型化;以模铸-初 轧为核心,生产外延扩大。 (2) 1974年-1989年: 技术特点:全连铸工艺,以连铸机为核心。 (3) 1989年-现在:
技术特点:连铸-连轧工艺,以薄板 坯,连铸-连轧为代表,钢厂向紧凑化发展。
紧凑式连续化的专业生产线
铁水 铁口 铁水罐 钢厂(铸铁机); 炉渣 渣口 渣罐 (水渣池); 煤气从炉顶导出,经煤气净化系统处理后作为燃料,其中40 %用来加热热风炉。
高炉工艺设备的组成
高炉工艺设备主要由7大部分组成: 1.高炉本体 炉基、炉壳、炉衬、冷却设备、 炉体框架和支柱。 高炉炉型:高炉内部工作空间形状 高炉炉体分为5段: 炉喉、炉身、炉腰、炉腹、炉缸。
(4)近终型连铸新技术 ·薄板坯连铸技术 ·薄带坯连铸技术
钢铁生产新技术新工艺
一.现代炼铁重大技术 1.非高炉炼铁技术 2.短流程的物流传递-(铁水一包到底技术)
二.现代转炉炼钢的重大技术
1.转炉大型化技术
装备技术 工艺控制技术 节能与环保技术
合理的 H/D,合理的炉容比 全悬挂倾动机构,水冷托圈、耳轴、炉帽、汽水冷却 上料,称量与下料程序控制 下渣检查与有效的渣铁分离装置 多孔水冷拉瓦尔氧枪、兼顾二次燃烧、化渣、脱碳与搅 拌功能 灵活可控的炉底供气系统、长寿喷嘴与大气量调节强化 搅拌功能 炉渣、炉气与钢液的在线动态检测 全自动吹炼控制与信息管理系统 除尘与煤气回收,二次除尘设施,尽可能采取干法系统 炉口微压差控制与余热锅炉 炉衬厚度检测与炉体维护设施 拆、砌炉机械
制造铸钢件的工艺流程

制造铸钢件的工艺流程
铸钢的机械性能比铸铁高,但其铸造性能却比铸铁差。
因为铸钢的熔点较高,钢液易氧化、钢水的流动性差、收缩大,其体收缩率为10~14%,线收缩为 1.8~2.5%。
为防止铸钢件产生浇不足、冷隔、缩孔和缩松、裂纹及粘砂等缺陷,必须采取比铸铁复杂的工艺措施:
1、由于钢液的流动性差,为防止铸钢件产生冷隔和浇不足,铸钢件的壁厚不能小于8mm;浇注系统的结构力求简单、且截面尺寸比铸铁的大;采用干铸型或热铸型;适当提高浇注温度,一般为1520°~1600℃,因为浇注温度高,钢水的过热度大、保持液态的时间长,流动性可得到改善。
但是浇温过高,会引起晶粒粗大、热裂、气孔和粘砂等缺陷。
因此一般小型、薄壁及形状复杂的铸件,其浇注温度约为钢的熔点温度+150℃;大型、厚壁铸件的浇注温度比其熔点高出100℃左右。
2、由于铸钢的收缩大大超过铸铁,为防止铸件出现缩孔、缩松缺陷,在铸造工艺上大都采用冒口和、冷铁和补贴等措施,以实现顺序凝固。
此外,为防止铸钢件产生缩孔、缩松、气孔和裂纹缺陷,应使其壁厚均匀、避免尖角和直角结构、在铸型用型砂中加锯末、在型芯中加焦炭、以及采用空心型芯和油砂芯等来改善砂型或型芯的退让性和透气性。
铸钢件生产工艺流程
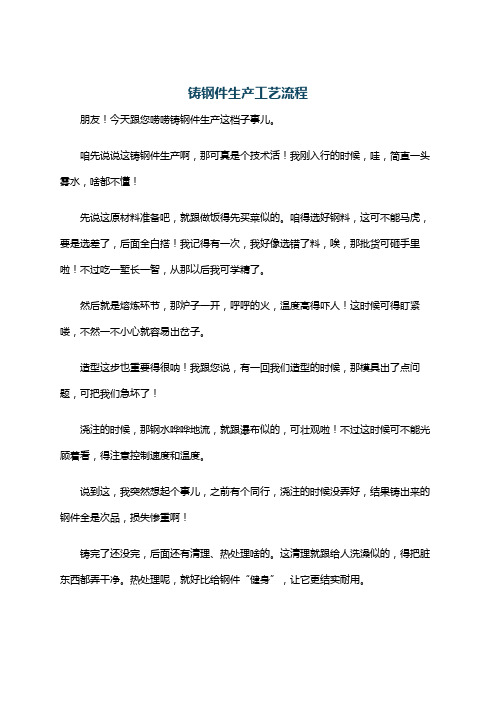
铸钢件生产工艺流程
朋友!今天跟您唠唠铸钢件生产这档子事儿。
咱先说说这铸钢件生产啊,那可真是个技术活!我刚入行的时候,哇,简直一头雾水,啥都不懂!
先说这原材料准备吧,就跟做饭得先买菜似的。
咱得选好钢料,这可不能马虎,要是选差了,后面全白搭!我记得有一次,我好像选错了料,唉,那批货可砸手里啦!不过吃一堑长一智,从那以后我可学精了。
然后就是熔炼环节,那炉子一开,呼呼的火,温度高得吓人!这时候可得盯紧喽,不然一不小心就容易出岔子。
造型这步也重要得很呐!我跟您说,有一回我们造型的时候,那模具出了点问题,可把我们急坏了!
浇注的时候,那钢水哗哗地流,就跟瀑布似的,可壮观啦!不过这时候可不能光顾着看,得注意控制速度和温度。
说到这,我突然想起个事儿,之前有个同行,浇注的时候没弄好,结果铸出来的钢件全是次品,损失惨重啊!
铸完了还没完,后面还有清理、热处理啥的。
这清理就跟给人洗澡似的,得把脏东西都弄干净。
热处理呢,就好比给钢件“健身”,让它更结实耐用。
我在这行干了 20 多年啦,中间犯过不少错,也学到了不少东西。
这工艺啊,也是不断在进步,以前觉得难的,现在可能都不算啥了。
就像现在流行的那些新技术,我有时候都还搞不太明白呢,还得继续学习。
不知道您听我这么一说,心里有没有点谱啦?要是您有啥想法,赶紧跟我交流交流!我这又扯远啦,反正大概就是这么个流程,您自个儿琢磨琢磨!。
《铸造工艺流程》课件
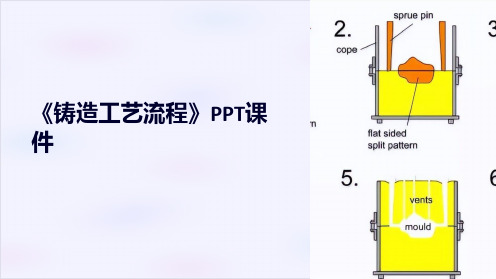
蜡型铸造
使用蜡模制造复杂形状的铸 件,然后将蜡模浸入耐火材 料中进行铸造。
铸造工艺流程的步骤
1
熔化金属
2
将合金料或金属材料加热至熔化状态,
以便于后续浇注。
3
模具制备
根据产品形状制作合适的模具,包括 砂型、金属型或蜡型等。
浇注
将熔化的金属倒入模具中,填充整个 空腔,等待冷却凝固。
铸造工艺流程的常见问题
1 气孔
2 缩孔和收缩
在铸件中形成气体孔隙, 影响铸件的机械性能。
由于熔铸过程中金属的 凝固收缩导致的缩孔和 表面缺陷。
3 夹杂物
杂质或不洁净物质被困 在铸件内部,影响铸件 的强度和质量。
铸造工艺流程的优点和局限性
优点
可制造复杂形状的金属制品、生产效率高、成 用于某些高温合金。
《铸造工艺流程》PPT课 件
铸造工艺流程的定义
铸造工艺流程是将熔化的金属或合金倒入型腔中,经过冷却凝固、浇注除砂获得所需几何形状的金属制 品的一系列工艺程序。
铸造工艺流程的分类
砂型铸造
通过在铸品外表面上涂敷一 层专用砂浆,然后铸造。常 用于制造大型铸件。
金属型铸造
制造出金属制品,通过在金 属模具中注入熔融金属,使 其凝固形成所需铸件。
铸造工艺流程的发展趋势
自动化
引入自动化设备和机器人,提高生产效率和 质量。
数字化技术
应用计算机仿真、数据分析等技术,优化工 艺流程和产品质量。
材料创新
研发新型材料,如高温合金、复合材料,扩 大铸造工艺的应用范围。
环保
减少能源消耗和废物产生,推动可持续发展。
铸造工艺流程的应用范围
铸造工艺广泛应用于制造业,包括汽车、航空航天、能源、机械制造等领域。
铸钢件生产工艺流程(精)

C.其他 砂箱,芯骨,冷铁等。
(4)造型制芯的基本要求:紧、光、通。
-4-
2.烘烤和上涂料
(1)任务(目的) 对制备好的砂型和砂芯烘烤,上涂料,防止铸件出现 气孔,防止粘砂、冲刷,提高铸件表面光洁度。
(2)重要性 对提高铸件表面光洁度,防止粘砂、冲砂,防止气孔起很大
的甚至是决定性的作用。 (3)涂料 我公司用锆英粉醇基涂料,涂料的基本组成(骨料)是锆英粉,
8.热处理后的抛丸:
(1)任务 去除热处理时生成的氧化皮 (2)重要性(注意事项) 使铸件表面光泽均匀一致,钢丸要 细一些,抛丸时间要短一些,尽量避免表皮缺陷的重新出现。 9.精整 (1)任务 修复出现的表面缺陷 (2)重要性(注意事项) 此时的精整最后决定铸件的表面质 量和外观轮廓,因此一定要注意,尽量少焊补,少打磨,打磨 后保证铸件的形状和尺寸。 -14-
A.砌包; B.清理钢包; C.装塞杆; D.烘包;
E.撒除渣剂、保温剂。
-8-
三. 后道工序 1.开箱落砂 (1)任务 打开浇注后的铸型,取出铸件,打碎已浇注后的铸型,取出 铸件。是后道工序的第一步,是砂再生处理的第一步; (2)重要性 (注意事项) 及时开箱,保证砂箱的流转,浇出来的铸件 及时进入下道工序,防止铸件出现裂纹和震坏。 2.清砂 (1)任务 将铸件表面、内腔残留的型砂清除掉,去除芯骨和铸件表面 的冷铁。 (2)重要性(注意事项) 为割除浇冒口创造条件,为后续的抛丸,清 除、修复缺陷创造条件,要避免损坏铸件表面。 -9-
避免涂料堆集,影响铸件尺寸,过厚的涂料层不易烘干,会造成铸件气
孔。 -5-
3.合箱(配模) (1)任务(内容)将制备好的砂型和砂芯装配起来,准备浇注。有时要放内 冷铁和芯撑。
连续铸钢生产课件汇总全套ppt完整版课件最全教学教程整套课件全书电子教案

由于钢包容量与出钢温降有关,出钢温降是随 钢包容量的增大而减少的。经验数字表明,大容量 的钢包出钢温降大约为20~40℃;中等容量的钢包 大约为30~60℃;小容量的钢包则通常为40~80℃, 甚至更高。
B.出完钢到钢包精炼开始前的温降分析 钢水在这一阶段的热损失主要表现为钢包包衬吸
E.钢水从钢包注入中间包的温降分析与控制 这一过程的钢水热损失与出钢相似,即主要表现
为钢流辐射热损失,对流热损失及中间包吸热的损失。 此过程的温降主要与钢流保护状况、中间包形式(冷 包、热包)、中间包钢水覆盖及中间包热负荷有关。
减少钢水从钢包注入中间包过程的温降措施: (1)钢流必须保护,通常采用长水口,这不仅为 了减少温降,同时也是防止钢水二次氧化、保证钢水 清洁度的必不可少的手段; (2)尽量减少浇注时间,严格遵循工序匹配的原 则,即炼钢周期与浇注周期的优化设计,同时要在保 证质量的前提下,尽可能采用高拉速技术;
(1)冶炼过程的控制(如铁水成分、废钢、新、 老炉等);
(2)出钢口要打好,用大孔径出钢,以缩短出 钢时间;
(3)钢包和中间包均采用绝热性能良好的耐火 材料,使包衬温降到最低值;
(4)钢包、中间包加覆盖剂和盖子; (5)利用红包出钢和滑动水口; (6)分批加入块度合适的铁合金块; (7)钢包传递时间不要耽误等。
是确保连铸钢厂生产顺行、质量稳定的重要环节。 a.建立温度制度的前提条件 建立温度制度的前提条件如下: (1)对钢水温降的每一个过程进行全面的调查,并
对收集到的大量数据进行统计分析,得出平均温降及分 布状况。
(2)计算出每一个钢种的液相线温度。 (3)确定每一个钢种的过热度。
b. 温度制度的编制原则 1) 确定每一个过程的目标温度,通常要确定以下5个 温度值。
铸钢件生产工艺流程
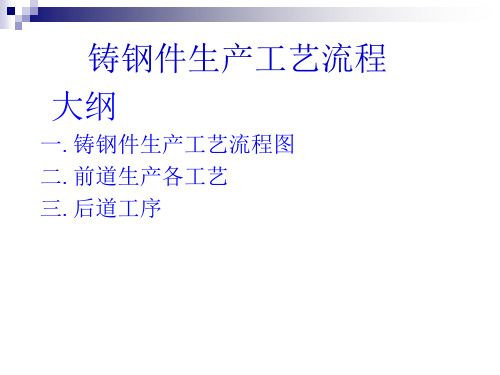
再次烘烤; 清除表面浮砂; 检查砂型、砂芯型腔,特别是出气孔道; 下砂芯; 扣上箱; 放浇口杯; 夹紧。
-6-
4.熔炼
(1)任务 得到化学成分合格,脱氧好,夹杂物和气体含量 少,有一定温度、流动性好的液体合金。
(2)重要性 液体合金凝固、冷却后形成铸件,它的成分、 组织、纯净度直接决定了铸件的性能。
铸钢件生产工艺流程
大纲
一.铸钢件生产工艺流程图 二.前道生产各工艺 三.后道工序
一.铸钢件生产工艺流程图
二.前道生产各工艺 1.造型和制芯 (1)任务(内容) 制备形成铸件的模型。 (2)重要性(地位)是砂型铸造生产的主要或者说是基本工序,往往以
该道工序来衡量/计算铸造生产能力、劳动生产率(效率)、生产技术 的先进性。 (3)支持配合的工序 A.模型 模型对铸件的尺寸精度起决定性的影响;
以上,锆英粉的特点是耐火度高,化学稳定性好,高温下热膨胀系数小,
能有效地防粘砂、冲砂、夹砂等缺陷,涂料中有一些挥发物,高温下有
较大的发气量,会带来铸件的皮下气孔,因此刷涂料后要烘干,过高的
烘烤温度有损于醇基涂料中的粘结剂,削弱了涂料层,要避免(一般控
制在200°C以下)。涂料中有一定量的醇类物质,在使用过程中因醇类
-14-
10.入库前的抛丸: (1)碳钢,中低合金钢铸件的最后一道工序,决定了铸件的外
观质量。 (2)对于不锈钢铸件,为最后一次钝化做准备,一定要将缺陷
彻底暴露。
11.防锈处理 (1)碳钢不锈钢铸件在表面质量合格并抛丸后应立即刷防锈油,
入库 (2)不锈钢铸件在表面质量合格抛丸后,酸洗钝化处理入库。
-11-
- 1、下载文档前请自行甄别文档内容的完整性,平台不提供额外的编辑、内容补充、找答案等附加服务。
- 2、"仅部分预览"的文档,不可在线预览部分如存在完整性等问题,可反馈申请退款(可完整预览的文档不适用该条件!)。
- 3、如文档侵犯您的权益,请联系客服反馈,我们会尽快为您处理(人工客服工作时间:9:00-18:30)。
一.铸钢件生产工艺流程图
二.前道生产各工艺 1.造型和制芯 (1)任务(内容) 制备形成铸件的模型。 (2)重要性(地位)是砂型铸造生产的主要或者说是基本工序,往往以
该道工序来衡量/计算铸造生产能力、劳动生产率(效率)、生产技术 的先进性。 (3)支持配合的工序 A.模型 模型对铸件的尺寸精度起决定性的影响; 模型直接影响着整个铸造厂的操作方法,生产效率; 模型的生产管理; 有关模型的技术标准; 可以说模型影响着整个铸造厂(车间)的生产。
65%以上,锆英粉的特点是耐火度高,化学稳定性好,高温下热膨胀系
数小,能有效地防粘砂、冲砂、夹砂等缺陷,涂料中有一些挥发物,高
温下有较大的发气量,会带来铸件的皮下气孔,因此刷涂料后要烘干,
过高的烘烤温度有损于醇基涂料中的粘结剂,削弱了涂料层,要避免
(一般控制在200°C以下)。涂料中有一定量的醇类物质,在使用过程
-4-
2.烘烤和上涂料
(1)任务(目的) 对制备好的砂型和砂芯烘烤,上涂料,防止铸件出现气 孔,防止粘砂、冲刷,提高铸件表面光洁度。
(2)重要性 对提高铸件表面光洁度,防止粘砂、冲砂,防止气孔起很大 的甚至是决定性的作用。
(3)涂料 我公司用锆英粉醇基涂料,涂料的基本组成(骨料)是锆英粉,
化学结构式是ZrO2·SiO2, ZrO2含量越高越好,铸钢生产要求含ZrO2
中因醇类物质的挥发涂料变粘度,影响涂刷,用工业无水酒精稀释。刷
涂料时要避免涂料堆集,影响铸件尺寸,过厚的涂料层不易烘干,会造
成铸件气孔。
-5-
3.合箱(配模) (1)任务(内容)将制备好的砂型和砂芯装配起来,准备浇注。有时要放内
冷铁和芯撑。 (2)重要性 是制备铸件模型的最后一道工序,决定铸件尺寸,形状,铸件
5.浇注 (1)任务 将钢水浇入铸型中。 (2)重要性 是直接形成铸件的一道工序。 (3)支持配合的工作: A.砌包; B.清理钢包; C.装塞杆; D.烘包; E.撒除渣剂、保温剂。
-8-
三. 后道工序 1.开箱落砂 (1)任务 打开浇注后的铸型,取出铸件,打碎已浇注后的铸型,取出
铸件。是后道工序的第一步,是砂再生处理的第一步; (2)重要性 (注意事项) 及时开箱,保证砂箱流转,浇出来的铸件-11-
5.焊补 (1)任务 焊补缺陷 (2)重要性和注意事项
A.铸钢件生产中的一道关键性工序。铸钢件在生产过程中避免不了焊补, 焊补后铸件的机械性能、化学成分、组织状况、应力情况、是否有气孔、 夹渣、裂纹等直接影响铸件质量。 B.焊条有严格规定(包括焊条牌号、直径、保管、烘烤、保温等) C.中低合金钢焊前要予热,焊后除应。 D.焊后要打磨至铸件原始的形状和尺寸。
-3-
B.型砂 ※型砂直接影响着造型、制芯的生产操作,影响或者说决定生 产节奏和效率。 ※型砂对铸件质量起着极大的影响,液体合金充型,在型砂中 流动、冷却、凝固、再冷却。在整个过程中有自身的、合金与 铸型的以及合金与空气的物理变化和化学反应。铸件的大多数 缺陷都与型砂直接或间接的有关,如粘砂、夹砂、气孔、裂纹、 折皱等等,还直接影响表面质量。 ※型砂直接影响劳动条件和环境。 ※型砂对生产成本的影响很大,有些砂种占成本的比例很大。 C.其他 砂箱,芯骨,冷铁等。 (4)造型制芯的基本要求:紧、光、通。
(3)具体操作 将废钢、各种合金材料通过熔化、精炼、去除有 害元素、去除夹杂物、脱氧、除气调整化学成分,最后获得 合格的钢水。
(4)支持、配合的工作(工序) A.筑炉; B.备料(废钢、合金、增碳剂、脱氧剂、氧气、矿石、造渣材料 等); C.化学分析。 -7-
大家有疑问的,可以询问和交流
可以互相讨论下,但要小声点
边,出气通道。 (2)注意事项 A.冒口根部残留量不能大,也不能割入铸件内部; B.注意区
别铸筋和铸件上的搭子和结构筋;C.中低合金钢气割前要热处理及预热。 4.抛丸 (1)任务 进一步清除铸件表面的粘砂,暴露铸件的表面(表皮)缺陷。 (2)重要性(注意事项) 彻底暴露铸件的表面(表皮)缺陷,尽量在热处
-12-
7.热处理: 通过热加工制度(加热、保温、冷却)改变铸件性能的加工方法 (1)任务 改变金相组织,消除应力,获得所需要的工艺性能(机加工)和使 用性能(机械性能和化学性能等) (2)重要性 铸件仅化学成分合格还不能满足用户的使用要求或工艺要求,还需 要通过热处理来使铸件满足这些要求,通过热处理可以: ※满足用户需要的机械性能;※满足用户需要的耐腐蚀性能; ※满足用户需要的工艺性能;※消除应力,稳定尺寸等。 (3)常见的热处理方法有:退火,正火,淬火,回火。 (4)设备:热处理炉,冷却水池。
理之前修补缺陷,大大缩短生产周期,避免在抛丸—修补缺陷两个环节往 返,注意要在第一次抛丸时尽量用粗粒抛丸(直径在2~2.5㎜)抛丸时间长 (15分钟左右)
-10-
5.碳刨(挖凿缺陷) (1)任务 将缺陷挖除干净,准备焊补 (2)注意事项
A.缺陷一定要挖除干净才能焊补,必要时要用渗透探伤来 检查。
B.重大焊补(焊补深度超过壁厚的20%或深度超过一英寸, 或焊补面积超过65㎝2)要做记录,要用渗透探伤来检查 缺陷是否清除干净。 C.中低合金钢碳刨前要予热,碳刨后要保温,要及时除应。
及时进入下道工序,防止铸件出现裂纹和震坏。 2.清砂 (1)任务 将铸件表面、内腔残留的型砂清除掉,去除芯骨和铸件表面的
冷铁。 (2)重要性(注意事项) 为割除浇冒口创造条件,为后续的抛丸,清除、
修复缺陷创造条件,要避免损坏铸件表面。 -9-
3.气割 (1)任务 割除浇冒口,冒口补贴,不需要保留的铸筋已经厚大飞
是否有砂孔、冲砂、气孔等,是铸造生产中最要的工序之一。 (3)具体操作内容:
再次烘烤; 清除表面浮砂; 检查砂型、砂芯型腔,特别是出气孔道; 下砂芯; 扣上箱; 放浇口杯; 夹紧。
-6-
4.熔炼
(1)任务 得到化学成分合格,脱氧好,夹杂物和气体含量 少,有一定温度、流动性好的液体合金。
(2)重要性 液体合金凝固、冷却后形成铸件,它的成分、 组织、纯净度直接决定了铸件的性能。