铸铝转子制造工艺精编
铸铝转子质量的工艺分析及措施

铸铝转子质量的工艺分析及措施转子质量问题专题调查分析如下:铸铝转子质量问题,最突出的表现就是转子内部存在的气孔的问题,其次就是转子内部的笼条细条、断条、夹渣以及端环部分的缩孔、冷裂、热裂、缺肉等。
这些问题的产生,最终导致整机的电气性能下降、转速不够、效率降低。
1、转子片间存油未去除:这是转子产生气孔的一个主要原因,由于转子铸铝是在高温、高压、瞬间形成的一个过程,在铝液刚刚充满转子型腔,高温铝还是液态而与转子片间的油类发生反应时,生成气体,这种气体有些被逸出,有些被铝液包围,然而铝液迅速固化,被包围的气体跑不出去,因此这些气体以气泡的形式残留在转子的笼条和端环中,呈不规则分布状态。
解决的办法为:铸铝前的转子铁芯应进行脱油处理,具体做法为:转子铁芯可用工业清洗剂冷态脱油,自来水冲洗,电炉烘干。
烘干温度以不破坏冲片表面保护膜为准,烘干时间以目测干透为准。
我们在5月19日已经做过96个转子脱油的实验,用拉上同型号转子和实验品转子各10个,装入同型号定子各10台,由抽查室做负载对比检查,结果装有实验品转子的电机比拉上同型号电机的转速平均提高2.5%以上。
2、铝液的清化问题:这个问题也是铸铝转子产生气孔的一个主要问题,铝锭及回炉铝在加热熔解过程中,与空气中的水蒸气接触时(尤其是多雨季节),一方面生成氧化铝沉于铝液底部,另一方面分解出氢气,同时氢气也渗入铝水中。
含有气体的铝水压铸出来的转子质量很差,因为铝水在压铸成型的瞬间,铝水迅速固化,一部分气体还未来得及逸出而被固化的铝包围,从而留在铸件内造成气孔。
另外就是铝液表面上的浮渣、铝液底部的沉渣以及留在铝液中间的其它杂物对转子的质量来说也是一个很大的隐患,一旦将这些渣滓和杂物压入转子内部,它们会使转子造成夹渣、形成冷隔(电阻系数增加)、热裂和冷裂的现象,热裂和冷裂严重时造成转子笼条断路。
为了解决上述问题,加入清化剂(氯盐:一般为NaCl 、ZnCl)可以较好的解决这一问题。
转子离心铸铝

转子离心铸铝王江波离心铸铝工艺简介(一)开启熔解炉电源,打开燃气阀门,按下点火开关点燃熔解炉,炉温升到400℃以后将铝料投入熔解炉内(熔解炉第一次使用时,先用小伙缓慢升温两小时后在用大火升温。
铝料要事先预热保温,完全去除铝料中的水气),当铝温达到750-780℃将表面渣子消除干净,浇铸时温度控制在760-780℃。
(二)按照车间下发的任务单准备好转子冲片,假轴,针座,模具。
按生产单子换好卸转子的卸座和标识。
(三)开启预热炉电源,升温,开启传送带,调整温度和传送速度。
(四)根据需要选择相应模具,安装在铸铝机旋转组件的上旋转磁盘和移动磁盘上,打开离心铸铝机的控制系统有专人设置参数。
(五)将料勺和探针涂上料勺被覆剂,涂擦要均匀。
(六)手动时检查离心铸铝机的旋转磁盘上下移动和旋转是否正常,每次是否回到原点;机械手控制系统与离心铸铝机是否联机,手动检查机械手运转是否正常,一切正常后进入自动操作状态。
(七)开启冷却传送机电源,运转传送链。
(八)人工将假轴用液压机插入铁芯放到预热机的送带上,假轴有拉伤的必须挑出,经过预热炉预热后,到达预热炉出口,由人工放到离心铸铝机上,放置时位置要正。
(九)按下启动开关,离心铸铝机升降系统移动磁盘上升,将铁芯移动到上磁盘夹具内,然后高速旋转,机器人从溶解炉里舀出铝液,从装夹好转子铁芯的旋转浇铸口浇筑进去。
铝液在离心力作用下充满型腔,制冷空气循环冷却铸件,离心机停止旋转,移动托盘下移至原位,完成工作后工件由人工取下,放到冷却传送机上,安启动开关退顶料。
两个工位循环往复。
(十)工件冷却后由人工取下,退出假轴。
(十一)检查工件一.熔铝准备1.坩埚准备1.1对坩埚进行焙烧,充分去除坩埚表面的水分,控制温度缓慢上升,约4-5小时候达到400℃,开始装料熔炼。
1.2熔炼工具准备,凡是与铝液接触的捞渣勺,搅拌棒,铝勺都要进行预热刷涂料,以防被铝液腐蚀、增加铝液中的含铁量。
1.3铝料要进行充分预热,去除铝料中的水分。
电动机转子铸铝工艺原理

电动机转子铸铝工艺原理——铸铝转子工艺简单的说,三相异步电动机主要由定子和转子两大部分组成,定子部分主要包括定子铁心、定子绕组和机座等,转子部分主要有转子铁心、转子绕组和转轴,而我们转子铸铝工序主要完成的就是它的转子绕组部分。
为什么说转子铸铝工序是特殊工序呢?ISO9000:2000标准中告诉我们,“凡是对形成的产品是否合格不易或不能经济地进行验收的过程”即为特殊过程或特殊工序,我们公司确定转子铸铝、浸漆和电磁线漆包烘干为特殊工序,所以必须对特殊工序按人、机、料、法、环这五个方面进行确认,只有这五个方面都合格了,才能确保这些过程实现所策划结果的能力。
而且标准中还强调对特殊工序人员要定期进行设备和工艺方面的培训,要求每年最少两次,所以这也是本次培训开设的主要目的,去年大家也都参加过有关铸铝专业知识方面的学习,这里我们再就一些重点内容强调一下。
一、电机工作原理及转子绕组的种类首先我们来了解一下交流三相异步电动机的工作原理,可以帮助我们来理解为什么转子断条、细条等会使电阻增大,要尽量避免,以及为什么转子两端要用短路环短接等。
工作原理:当电动机的定子绕组通以三相对称交流电时,在定子和转子间便产生以转速n s旋转的旋转磁场(电能生磁),由于转子开始时是静止的,所以转子导体将被旋转磁场切割,根据相对运动的原理,我们也可以把磁场看成不动,而转子导体相对磁场旋转切割磁力线从而产生感生电动势(即1831年法拉第发现的电磁感现象也称“动磁生电”),由于转子导体两端已被短路环短接,导体已构成闭合回路,所以转子导体内也相应产生感生电流。
有感生电流的转子导体即为通电导体,通电导体在磁场中就会受到电磁力的作用(电磁生力),产生电磁力矩最终带动转子旋转,而且我们还可以根据左手定则判断出转子导体的旋转方向,与旋转磁场的方向是相同的,只不过是以略小于旋转磁场转速n s的速度运转的,这也是异步电动机名称的由来。
所以说转子绕组的主要作用就是产生感生电动势和电流,并在旋转磁场的作用下产生电磁力矩而使转子转动,所以要求转子绕组的导电性能比较好(铝的电阻率为2.9×10-8m2/m,铜的电阻率为1.78×10-8Ωm2/m)。
转子压力铸铝工艺守则

浙江巨龙电机有限公司
共3页
第1页
1使用范围
1.1本守则适用于所有系列电机转子压力铸铝工艺。
2材料
2.1铝锭、铝浇口AL-1(含铝AL99.5%)。
2.2清化剂、氯化物(氯化锌、氯化钠、氯化铵)。
2.3石棉纸。
3设备与工具
3.1压铸机(300T、200T、50T、30T)。
3.2蓄压器。
资料来源
编制
校对
标准化
提出部门
审定
标记
处数
更改文件号
签字
日期
批准文号
批准
转子压力铸铝工艺守则
浙江巨龙电机有限公司
共3页
第2页
4.17槽形应整齐,用槽斜度,样板和槽形棒检查。
4.18当15%铝块和浇冒口溶化后放入铝锭,如是火焰炉应鼓风加速熔化。
4.19熔铝温度为690-710℃。
4.20清化处理。当铝温在600℃左右时,投放氯化物进行铝液清化,同时进行搅拌,当气泡由铝液中析出来以后,清化即告结束,除去表面上的渣子。
5.2.2浇注温度可控制在680-700℃压入时浇注温度可低些。
5.3压射:铝液倒入压射室后,用手动或自动送模到位后,手动关防护门,迅速掀下操纵箱手柄。
5.3.1压射后,压射活塞应停留3-5S.
5.4切断浇口,松开操作箱手柄,压射活塞回到上面位置,同时在压铸机下活塞缸自动操纵箱的
作用下,压射室下活塞上升切断浇口,然后顶出料饼。
6.10平衡柱残缺不得大于1/4平衡柱高度,每端残缺的数目不得超过平衡柱数目的1/4。
6.11转子浇口浇铝不足或低陷不得超过槽口高度。
7注意事项
7.1铝锭、盛铝桶、热电偶测温仪应径预热后方可投入铝液中。
谈转子离心铸铝的工艺方法

2 0 1 4
速 农机
AN N O N GJ FUJI I
谈转子 离心铸铝 的工艺方法
陈玉 宇
( 福建 南 电股份 有 限公 司 , 福建 南平 3 5 3 0 0 1 )
摘
要: 为 了保证电动机转子铸铝 的质量 , 对转子铸铝熔铝设备、 离心铸铝的工艺参数、 离心铸铝模 的结构
参数、 离心浇注的工艺方法及 离心力大小、 操作程序的具体实施步骤进行剖析介绍, 总结 了一套可用于指导生 产实际的离心铸铝转子生产工艺。
关键词: 转子; 铸铝 ; 坩锅; 涂料 ; 离心力; 温度 ; 速度
由于铸 铝转 子具有结构对称 、 紧凑 , 外形美观 , 易 于达到机械平衡 ; 槽形设计不受 铜条或铝条形 状
铝 过程 中最 容易产 生 的气体 , 在铝 中的溶解 度 随着温 度升高而增加 ( 见图2 ) 。 当铝 温 到 达 8 0 0  ̄ C 时, 由于
3 转子铁芯和铸铝模 的预热炉
预 热炉 必 须保 证 转 子铁 芯 预 热 温度 5 0 0 ℃左右 、
铸铝模预热温度 3 5 0  ̄ C 左右 , 而且温度均匀。 目前大
升随之提高 。所以铸铁坩埚使用前的处理就显得更 为 重要 。新 坩埚 必须 除净 铁锈 , 然后 加 热到 1 5 0 ~
的限制 , 可 以任 意选择能改善 电机性能 的理想槽形 ; 转子风叶、 笼条端环 以及平衡柱可同时铸出 , 槽满率 几乎达 1 0 0 %, 提高了散热效率 ; 生产周期短 、 成本低 、
都 采用反 射 炉或 电阻炉 等 。
4 离心铸铝模
离心铸铝模 由上 、 中、 下模 , 分流器 , 假轴等几部 分组成 。各种铸铝方法所用模具虽有不 同, 但其结构
电动机转子铸铝工艺原理

正确进行清化除理;
浇注速度过快;
适当控制浇注速度;
转子铁心预热温度低,油渍没 正确控制转子铁心预
有烧去即进行浇注;
热温度和时间;
下模排气孔小。
放大排气孔。
转子铁心预热温度低,导条先 凝固,铝水补充不下去;
正确控制转子预热温 度;
下模预热温度高或预热温度 低。
正确控制下模预热温 度。
铝水温度过低;
适当提高铝水温度;
我公司所采用的转子铸铝方法主要有离心铸铝和压力铸铝两种。 下面分别来看一下这两种铸铝方法的工作原理和特点。 (一)压力铸铝
工作原理是用压力将融化好的金属铝液注入型腔,待冷却凝固 成铸件。其特点有: (1)在压铸过程的始终,压力起着主要作用。 (2)压铸时,金属液在高速冲型过程中,如果型腔中的气体来不及 排出,就会被卷入金属内产生气孔。 (3)由于金属液充型过程是在压力作用下进行的,转子铁心可在冷 态下压铸。 (4)生产效率高,易实现机械化、自动化,从而可减轻劳动强度。 (二)离心铸铝
3
序 缺陷名 号称 1 断条
2 细条
3
端环 裂纹
4
上端环 裂纹
5 气孔
6
下端环 缩孔
7 浇不足
铸铝转子培训教材————————版权所有
产生原因
防止措施
转子铁心叠压过紧,铸铝后 有过大的压力加在铝条上,将 铝条拉断铸铝后脱模中,铝水 未凝固好,铝条由于脱模敲打 而断裂。
控制叠压压力小于 3Mpa 铸铝后等铝水完全凝 固后再脱模。
6
铸铝转子培训教材————————版权所有
温度数显仪上下限温度设定,上限温度应比铸造温度高 500C,上下 限温差 1000C. 4.4 坩埚连续工作时,铝液高度应不低于坩埚高度的 1/3. 4.5 当铝块熔化后应将预热后的铝锭陆续推入坩埚内,动作应缓慢, 切不可“抛入”。 4.6 铝液的净化处理
铸铝转子工艺

铸铝转子工艺(铸铝工序)一、转子铸铝方法我公司所采用的转子铸铝方法主要有离心铸铝和压力铸铝两种。
下面分别来看一下这两种铸铝方法的工作原理和特点。
(一)压力铸铝工作原理是用压力将融化好的金属铝液注入型腔,待冷却凝固成铸件。
其特点有:(1)在压铸过程的始终,压力起着主要作用。
(2)压铸时,金属液在高速冲型过程中,如果型腔中的气体来不及排出,就会被卷入金属内产生气孔。
(3)由于金属液充型过程是在压力作用下进行的,转子铁心可在冷态下压铸。
(4)生产效率高,易实现机械化、自动化,从而可减轻劳动强度。
(二)离心铸铝工作原理是将融化好的金属铝液注入旋转着的铝模中,使之在离心力的作用下充满型腔,并凝固。
其特点有:(1)离心力对铸件的成型和金属结晶过程有重要影响,它有助于金属液中的气体和非金属杂物(比金属轻)的排出。
更重要的是影响到金属结晶过程,起到加强补缩和结晶细化的作用。
(2)转子铁心必须预热。
铁心加热后,在槽型断面上得到氧化,有利于降低电机的杂散损耗。
(3)转子离心铸铝用的设备比较简单。
但在浇铸过程中有不少手工操作,劳动强度较大。
二、离心铸铝和压力铸铝的优缺点及其常见的缺陷和防止措施1.离心铸铝优缺点离心铸铝所得到的铸件,金属组织比较紧密,质量比较好,所用设备不太复杂,操作技术比较简单,与压力铸铝相比较杂散损耗比较小,不过其生产率不高,劳动条件较差,劳动强度较高。
2.压力铸铝优缺点压力铸铝时,铝水压射到转子槽和型腔中的速度极高,其充填速度可达10~25m/s。
压铸时,不象离心铸铝那样铝水有一段流动时间,而是瞬间完成的,因此铁心和模具均可不必预热。
铁心和模具不预热,这就大大减化了操作工艺,改善了劳动条件。
此外由于没有离心铸铝那样复杂的凝固补缩过程,铸铝转子质量稳定,一次合格率达99%以上。
3.压力铸铝的质量,目前存在以下一些问题:(1)由于压力很大,铝水充满型腔的速度很高,原来在型腔中得空气难以排尽,会在铸件中产生气孔。
19-53转子铁芯铸铝压铸工艺守则
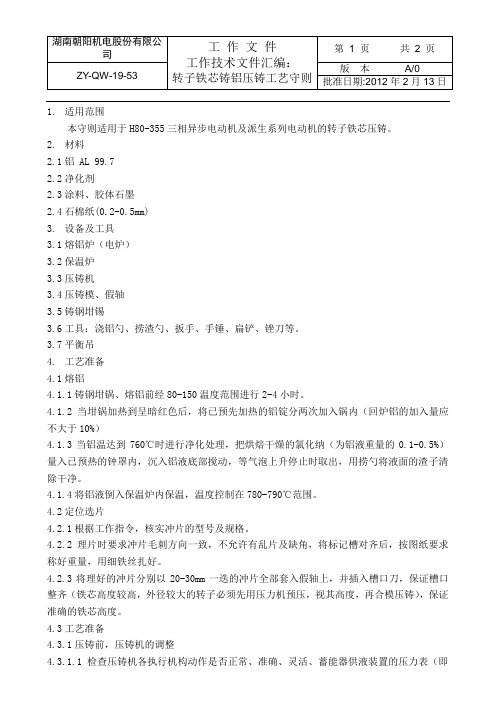
1.适用范围本守则适用于H80-355三相异步电动机及派生系列电动机的转子铁芯压铸。
2.材料2.1铝 AL 99.72.2净化剂2.3涂料、胶体石墨2.4石棉纸(0.2-0.5mm)3.设备及工具3.1熔铝炉(电炉)3.2保温炉3.3压铸机3.4压铸模、假轴3.5铸钢坩锡3.6工具:浇铝勺、捞渣勺、扳手、手锤、扁铲、锉刀等。
3.7平衡吊4.工艺准备4.1熔铝4.1.1铸钢坩锅、熔铝前经80-150温度范围进行2-4小时。
4.1.2当坩锅加热到呈暗红色后,将已预先加热的铝锭分两次加入锅内(回炉铝的加入量应不大于10%)4.1.3当铝温达到760℃时进行净化处理,把烘焙干燥的氯化纳(为铝液重量的0.1-0.5%)量入已预热的钟罩内,沉入铝液底部搅动,等气泡上升停止时取出,用捞勺将液面的渣子清除干净。
4.1.4将铝液倒入保温炉内保温,温度控制在780-790℃范围。
4.2定位选片4.2.1根据工作指令,核实冲片的型号及规格。
4.2.2理片时要求冲片毛刺方向一致,不允许有乱片及缺角,将标记槽对齐后,按图纸要求称好重量,用细铁丝扎好。
4.2.3将理好的冲片分别以20-30mm一迭的冲片全部套入假轴上,并插入槽口刀,保证槽口整齐(铁芯高度较高,外径较大的转子必须先用压力机预压,视其高度,再合模压铸),保证准确的铁芯高度。
4.3工艺准备4.3.1压铸前,压铸机的调整4.3.1.1检查压铸机各执行机构动作是否正常、准确、灵活、蓄能器供液装置的压力表(即氮气的压力表9-10kg)指示压力是否符合要求。
4.3.1.2根据被压转子的规格来调整内浇口速度(10-15M/S),压射比压(15-20MPa)开模行程及各行程开关的位置。
4.3.2压铸模的安装调整4.3.2.1检查模具有无损坏,风叶、平衡柱、排气通道是否有堵塞。
4.3.2.2将压铸模下模安装在辅机的拖板上,上模通过T型槽螺栓与活动横梁坚固,并均匀涂刷石墨油剂。
铸铝转子工艺

首先我们来了解一下交流三相异步电动机的工作原理,可以帮助 我们来理解为什么转子断条、细条等会使电阻增大,要尽量避免,以 及为什么转子两端要用短路环短接等。
工作原理:当电动机的定子绕组通以三相对称交流电时,在定子 和转子间便产生以转速ns旋转的旋转磁场(电能生磁),由于转子开始 时是静止的,所以转子导体将被旋转磁场切割,根据相对运动的原 理,我们也可以把磁场看成不动,而转子导体相对磁场旋转切割磁力 线从而产生感生电动势(即1831年法拉第发现的电磁感现象也称“动 磁生电”),由于转子导体两端已被短路环短接,导体已构成闭合回 路,所以转子导体内也相应产生感生电流。有感生电流的转子导体即 为通电导体,通电导体在磁场中就会受到电磁力的作用(电磁生 力),产生电磁力矩最终带动转子旋转,而且我们还可以根据左手定 则判断出转子导体的旋转方向,与旋转磁场的方向是相同的,只不过 是以略小于旋转磁场转速ns的速度运转的,这也是异步电动机名称的 由来。
二、转子铸铝方法
我公司所采用的转子铸铝方法主要有离心铸铝和压力铸铝两种。下面 分别来看一下这两种铸铝方法的工作原理和特点。 (一)压力铸铝
工作原理是用压力将融化好的金属铝液注入型腔,待冷却凝固成铸 件。其特点有: (1)在压铸过程的始终,压力起着主要作用。 (2)压铸时,金属液在高速冲型过程中,如果型腔中的气体来不及排 出,就会被卷入金属内产生气孔。 (3)由于金属液充型过程是在压力作用下进行的,转子铁心可在冷态 下压铸。 (4)生产效率高,易实现机械化、自动化,从而可减轻劳动强度。 (二)离心铸铝
正确进行清化除理; 适当控制浇注速度; 正确控制转子铁心预热温度 和时间; 放大排气孔。
正确控制转子预热温度;
正确控制下模预热温度。
铸铝转子工艺.doc

铸铝转子工艺(铸铝工序)一、转子铸铝方法我公司所采用的转子铸铝方法主要有离心铸铝和压力铸铝两种。
下面分别来看一下这两种铸铝方法的工作原理和特点。
(一)压力铸铝工作原理是用压力将融化好的金属铝液注入型腔,待冷却凝固成铸件。
其特点有:(1)在压铸过程的始终,压力起着主要作用。
(2)压铸时,金属液在高速冲型过程中,如果型腔中的气体来不及排出,就会被卷入金属内产生气孔。
(3)由于金属液充型过程是在压力作用下进行的,转子铁心可在冷态下压铸。
(4)生产效率高,易实现机械化、自动化,从而可减轻劳动强度。
(二)离心铸铝工作原理是将融化好的金属铝液注入旋转着的铝模中,使之在离心力的作用下充满型腔,并凝固。
其特点有:(1)离心力对铸件的成型和金属结晶过程有重要影响,它有助于金属液中的气体和非金属杂物(比金属轻)的排出。
更重要的是影响到金属结晶过程,起到加强补缩和结晶细化的作用。
(2)转子铁心必须预热。
铁心加热后,在槽型断面上得到氧化,有利于降低电机的杂散损耗。
(3)转子离心铸铝用的设备比较简单。
但在浇铸过程中有不少手工操作,劳动强度较大。
二、离心铸铝和压力铸铝的优缺点及其常见的缺陷和防止措施1.离心铸铝优缺点离心铸铝所得到的铸件,金属组织比较紧密,质量比较好,所用设备不太复杂,操作技术比较简单,与压力铸铝相比较杂散损耗比较小,不过其生产率不高,劳动条件较差,劳动强度较高。
2.压力铸铝优缺点压力铸铝时,铝水压射到转子槽和型腔中的速度极高,其充填速度可达10~25m/s。
压铸时,不象离心铸铝那样铝水有一段流动时间,而是瞬间完成的,因此铁心和模具均可不必预热。
铁心和模具不预热,这就大大减化了操作工艺,改善了劳动条件。
此外由于没有离心铸铝那样复杂的凝固补缩过程,铸铝转子质量稳定,一次合格率达99%以上。
3.压力铸铝的质量,目前存在以下一些问题:(1)由于压力很大,铝水充满型腔的速度很高,原来在型腔中得空气难以排尽,会在铸件中产生气孔。
铸铝转子工艺

简单的说,三相异步电动机主要由定子和转子两大部分组成,定子部 分主要包括定子铁心、定子绕组和机座等,转子部分主要有转子铁心、 转子绕组和转轴,而我们转子铸铝工序主要完成的就是它的转子绕组部 分。为什么说转子铸铝工序是特殊工序呢?ISO9000:2000标准中告诉 我们,“凡是对形成的产品是否合格不易或不能经济地进行验收的过 程”即为特殊过程或特殊工序,我们公司确定转子铸铝、浸漆和电磁线 漆包烘干为特殊工序,所以必须对特殊工序按人、机、料、法、环这五 个方面进行确认,只有这五个方面都合格了,才能确保这些过程实现所 策划结果的能力。而且标准中还强调对特殊工序人员要定期进行设备和 工艺方面的培训,要求每年最少两次,所以这也是本次培训开设的主要 目的,去年大家也都参加过有关铸铝专业知识方面的学习,这里我们再 就一些重点内容强调一下。
7 浇不足
8
抛空
9
冷隔
转子冲片个别槽孔漏冲; 铝条中有气孔; 浇注时中途停顿; 铁心温度太低。
离心机转速太高,离心力太大; 转子槽孔过小,使铝水浇不足;
转子外圆斜线不直,槽不齐。
铝水含铁硅等杂质多; 铝水铁硅比小; 铝水温度过高,晶粒变粗; 风叶、平衡柱和端环连接处圆脚小
内浇口截面过小,补缩不足; 上模温度低,内浇口先凝固; 分流器过高。
开始浇注时离心机转速过高
浇注时断浇 有渣子隔开
加强各级检查; 一次浇完不能停顿; 一次浇完不能停顿; 适当提高铁心温度。
控制离心机转速; 适当提高转子预热温度; 转子铁心叠压时用合格的槽 样棒。
控制铁硅含量; 控制铁硅含量; 控制温度在740~7600C间 增大圆角
适当增大内浇口; 提高上模预热温度; 适当降低分流器高度。
铸铝转子制造工艺精编

铸铝转子制造工艺精编 Document number:WTT-LKK-GBB-08921-EIGG-22986铸铝转子制造工艺Y2、Y3系列三相异步电动机全部采用铸铝转子。
转子铸铝用一级重熔用铝锭,牌号为A1 或(GB1196),其电阻率在20℃时为~Ωmm/m,铝的纯度不小于%,其杂质含量不得大于表3-7的规定。
表3-7 的杂质含量注:含量均指质量分数。
转子铸铝时,在已经装入转子铁心的铸铝模中,注入熔化铝液,铸成由导条和端环组成的整体铝笼及端环上的风叶和平衡柱。
铸铝转子的主要质量要求是:(1)铝笼的含铁量应不大于%。
(2)铸铝转子铁心长度公差为+(L<160mm);+(L≥160mm)。
(3)端环的尺寸公差应符合图样规定。
(4)端环及风叶上的毛刺披锋和铁心外圆上的残铝必须清理干净。
(5)转子外圆表面斜槽线平直,无明显曲折形。
(6)转子槽口浇铝不足或低陷不得超过槽口高度规定的尺寸。
(7)转子导条应无断条、细条现象。
(8)端环和风叶不得有裂纹、弯曲现象和明显缩孔、缺陷等。
常用转子铸铝方法为压力铸造和离心铸造两种。
其工作原理和特点见表3-8.表3-8 几种转子铸铝方法的工作原理和特点在转子铸铝前,必须做好铝料的熔化工作。
采用铸铁坩埚熔铝时,必须先在坩埚内腔涂刷一层保护涂料。
保护涂料一般采用“高温涂料,它由超微粒锆、矾土、矾土水泥和硼酸等组成。
在涂刷高温涂料前,坩埚内表面需清砂、防锈、清理干净,并预热到100~200℃。
涂料的调配为:每千克涂料配以~水玻璃和~的开水,调成糊状,分几次涂刷到规定厚度。
涂刷是坩埚应在炉上保持温度,刷好后升温加热,坩埚内壁呈暗红色,干结即可。
浇口料加入量不得大于15%,以控制铝液的纯度。
在熔炼时,需进行铝水的清化,以达到排气排渣的目的。
铝水清化常用的方法是加氯盐(如氯化钠),加入量为铝液的%~%。
转子压力铸铝采用冷室压铸机,按其压射室位置不同分为全立式、立式和卧式三种。
转子压铸机主要参数为:压射力(N)、压射速度(m/s)、合型力(N)、压射比压(Pa)和铝的最大浇注量(kg)等。
转子铸铝后的热套轴工艺

转子铸铝后的热套轴工艺中小型异步电动机铸铝转子和轴的联结,以前多采用滚花轴或键联结的“冷压法”。
早在六十年代,一些电机厂就开始了“热套法”的试验工作。
H280机座以下的铸铝转子几乎全部采用“热套法”。
冷压法的轴直径大于40毫米时,转轴上的键槽,会降低了轴的强度。
对于直径小于40毫米的滚花轴,压入时常发生弯曲变形,这些问题在采用热套法时均可避免。
Ms.参今天就谈谈热套轴。
热套轴的方法铸铝转子热套轴工艺是在转子浇注后,利用转子铸铝时的余热,立即将轴装入铁心轴孔;对于成批生产的电机,为了保证热套轴的位置,提高工效,宜采用专门热套轴工具。
热套后,常发现轴顺冲片毛刺方向移动,严重时会出现明显的锅底问题,在设计模具应时,应充分考虑这些问题。
轴穿入轴孔,可垂直插入或水平插入。
当垂直插入轴孔时,铸铝转子需要一个个翻转放到垫盘上。
水平插入轴时,应注意核对轴伸尺寸,在转子冷却前,切勿触动转子和轴,以防尺寸变动。
当轴具有铁心定位的轴肩时,将轴肩紧靠铁心,即可保证轴伸尺寸。
经预热后浇注的转子,利用其余热即可进行套轴。
压力铸铝转子由于未经预热,浇注后温度较低,须再经加热后方可套轴。
大、中型电机铸铝转子,热套轴虽是一常较为简便的工艺方法,但热套失败将造成重大损失,因此,在进行操作时,必须严格遵守以下工工艺规定。
套轴前的准备工作● 转子的放置应保证轴穿入时不受阻碍,且倾斜度不超过每米1毫米;● 检查轴及轴孔,核对配合紧量;●对带键轴,键应打入健槽内,检查其宽度和槽深方向高度,不能有尖角;●检查轴与键中心线是否一致,轴与键中心线不一致,热套事故的主要原因。
热套时应注意事项●用卡板测量加热后的轴孔尺寸以保证轴能顺利通过;●转子停止加热到插入轴的时间应尽量缩短,一般不应超过15分钟;●如套轴不能到位时,应立即退出。
套轴后的注意事项●检查轴向尺寸是否正确;●带支架铁心冷缩时和轴肩可能离缝,可用锤敲打支架或轴使其靠紧。
热套轴的工艺参数●热套轴工艺主要是掌握热套温度及轴孔与轴的配合公差。
转子离心铸铝

转子离心铸铝王江波离心铸铝工艺简介(一)开启熔解炉电源,打开燃气阀门,按下点火开关点燃熔解炉,炉温升到400℃以后将铝料投入熔解炉内(熔解炉第一次使用时,先用小伙缓慢升温两小时后在用大火升温。
铝料要事先预热保温,完全去除铝料中的水气),当铝温达到750-780℃将表面渣子消除干净,浇铸时温度控制在760-780℃。
(二)按照车间下发的任务单准备好转子冲片,假轴,针座,模具。
按生产单子换好卸转子的卸座和标识。
(三)开启预热炉电源,升温,开启传送带,调整温度和传送速度。
(四)根据需要选择相应模具,安装在铸铝机旋转组件的上旋转磁盘和移动磁盘上,打开离心铸铝机的控制系统有专人设置参数。
(五)将料勺和探针涂上料勺被覆剂,涂擦要均匀。
(六)手动时检查离心铸铝机的旋转磁盘上下移动和旋转是否正常,每次是否回到原点;机械手控制系统与离心铸铝机是否联机,手动检查机械手运转是否正常,一切正常后进入自动操作状态。
(七)开启冷却传送机电源,运转传送链。
(八)人工将假轴用液压机插入铁芯放到预热机的送带上,假轴有拉伤的必须挑出,经过预热炉预热后,到达预热炉出口,由人工放到离心铸铝机上,放置时位置要正。
(九)按下启动开关,离心铸铝机升降系统移动磁盘上升,将铁芯移动到上磁盘夹具内,然后高速旋转,机器人从溶解炉里舀出铝液,从装夹好转子铁芯的旋转浇铸口浇筑进去。
铝液在离心力作用下充满型腔,制冷空气循环冷却铸件,离心机停止旋转,移动托盘下移至原位,完成工作后工件由人工取下,放到冷却传送机上,安启动开关退顶料。
两个工位循环往复。
(十)工件冷却后由人工取下,退出假轴。
(十一)检查工件一.熔铝准备1.坩埚准备1.1对坩埚进行焙烧,充分去除坩埚表面的水分,控制温度缓慢上升,约4-5小时候达到400℃,开始装料熔炼。
1.2熔炼工具准备,凡是与铝液接触的捞渣勺,搅拌棒,铝勺都要进行预热刷涂料,以防被铝液腐蚀、增加铝液中的含铁量。
1.3铝料要进行充分预热,去除铝料中的水分。
- 1、下载文档前请自行甄别文档内容的完整性,平台不提供额外的编辑、内容补充、找答案等附加服务。
- 2、"仅部分预览"的文档,不可在线预览部分如存在完整性等问题,可反馈申请退款(可完整预览的文档不适用该条件!)。
- 3、如文档侵犯您的权益,请联系客服反馈,我们会尽快为您处理(人工客服工作时间:9:00-18:30)。
铸铝转子制造工艺精编 Document number:WTT-LKK-GBB-08921-EIGG-22986
铸铝转子制造工艺
Y2、Y3系列三相异步电动机全部采用铸铝转子。
转子铸铝用一级重熔用铝锭,牌号为A1 或(GB1196),其电阻率在20℃时为~Ωmm/m,铝的纯度不小于%,其杂质含量不得大于表3-7的规定。
表3-7 的杂质含量
注:含量均指质量分数。
转子铸铝时,在已经装入转子铁心的铸铝模中,注入熔化铝液,铸成由导条和端环组成的整体铝笼及端环上的风叶和平衡柱。
铸铝转子的主要质量要求是:
(1)铝笼的含铁量应不大于%。
(2)铸铝转子铁心长度公差为+(L<160mm);+(L≥160mm)。
(3)端环的尺寸公差应符合图样规定。
(4)端环及风叶上的毛刺披锋和铁心外圆上的残铝必须清理干净。
(5)转子外圆表面斜槽线平直,无明显曲折形。
(6)转子槽口浇铝不足或低陷不得超过槽口高度规定的尺寸。
(7)转子导条应无断条、细条现象。
(8)端环和风叶不得有裂纹、弯曲现象和明显缩孔、缺陷等。
常用转子铸铝方法为压力铸造和离心铸造两种。
其工作原理和特点见表3-8.
表3-8 几种转子铸铝方法的工作原理和特点
在转子铸铝前,必须做好铝料的熔化工作。
采用铸铁坩埚熔铝时,必须先在坩埚内腔涂刷一层保护涂料。
保护涂料一般采用“高温涂料,它由超微粒锆、矾土、矾土水泥和硼酸等组成。
在涂刷高温涂料前,坩埚内表面需清砂、防锈、清理干净,并预热到100~200℃。
涂料的调配为:每千克涂料配以~水玻璃和~的开水,调成糊状,分几次涂刷到规定厚度。
涂刷是坩埚应在炉上保持温度,刷好后升温加热,坩埚内壁呈暗红色,干结即可。
浇口料加入量不得大于15%,以控制铝液的纯度。
在熔炼时,需进行铝水的清化,以达到排气排渣的目的。
铝水清化常用的方法是加氯盐(如氯化钠),加入量为铝液的%~%。
转子压力铸铝采用冷室压铸机,按其压射室位置不同分为全立式、立式和卧式三种。
转子压铸机主要参数为:压射力(N)、压射速度(m/s)、合型力(N)、压射比压(Pa)和铝的最大浇注量(kg)等。
压铸机是由床身、压射机构、合型机构和液压及电气控制装置等组成。
压射机构是实现压射的关键部件,它的结构和正确使用时决定压铸件质量的主要因素。
压射机构一般采用二级和三级压射系统,目前生产中使用的压铸机大多采用三级压射。
在压铸机上配备定量浇注装置和工件装卸机构,便能实现压铸生产自动化。
转子压力铸铝用的压铸模系将转子铁心作为一个嵌件,其槽形是构成型腔的一个主要部分,起到上下模之间的通道作用。
对不同压铸机应配置相应的压铸模,全立式的压铸模结构较简单。
转子压铸模的进铝方式主要有中心浇注和风叶(或平衡柱)端面浇注。
卧式而和立式压铸机用压铸模一般采用中心浇注,由直浇道从数个分支内浇口引入型腔。
内浇口的进口置于壁厚的端环处,以利于铝液的补偿。
全立式压铸机大多配置风叶端面浇注的压铸模。
由于压铸过程中铝液充型时间较短,必须开设足够的排气槽,使腔内空气有次序滴尽快排出。
转子压力铸铝工艺中,根据铝液的流动性较差,铸件的形状不太复杂且壁厚等特点,合理地选取压铸工艺参数,压射比压应高些,而充型速度应尽量低些。
表3-9所列数据为小型电机常用的转子压铸工艺参数。
表 3-9 小型电机常用的转子压铸工艺一般参数
在压铸过程中,压射比压、充型速度、压铸温度、压铸模温度等工艺参数之间有一定的关系,可通过试模来进行调整,以达到最佳效果。
在采用风叶端面浇注时,压铸过程中压力损失较小,压射比可略低些。
铸铝模采用中心浇注,它的浇注系统与压铸模大致相同。
在对铝液补缩要求较高情况下,如2极电机转子,通常采用环形内浇口。
在转子离心铸铝工艺中,铝液温度一般控制在720~780℃。
铸铝温度为450~550℃,铸铝模的上、下模预热温度为300~350℃,中模预热温度为150~200℃。
离心铸铝时,离心机的额定转速n由以下公式决定:
式中 K ——修正系数(一般取~);
r1 ——转子端环外圆半径(m);
r2 ——转子端环外圆半径(m);
离心机得额度转速也可根据生产工艺的实际情况而定。
铸铝转子铁心技术条件
1 主题内容与使用范围
本技术条件规定了低压异步电动机铸铝转子铁心的技术要求、检验方法。
本技术条件适用于Y2、Y3三相异步电动机及其对转子铸铝无特殊要求的派生系列电动机的压力铸铝转子(以下简称铸铝转子)。
2 技术要求
转子铸铝使用的铝锭
转子铸铝采用一级重熔用铝锭,牌号为A/或A/(GB1196-1980),其电阻在20℃时为~Ωmm2/m,铝锭的化学成分应符合表1的规定。
表1
①此表化学成分均为质量分数。
铝锭熔化后,铝液含铁量允许高于表1的规定值,但不得大于%,杂质总和不大于1%,且电阻率仍应符合条件中的规定。
每班生产前,一般坩埚中的铝液必须进行取样进行化验。
转子冲片在铸铝前必须进行检查。
冲片毛刺不得大于图样的规定值,冲片表面不得有油污及锈迹。
铁心齿部必须平整。
铸废的转子允许回炉重铸一次,回炉两次的冲片不得再用。
熔炉温度一般控制在720-780℃。
要根据具体的工件来保持相应的铝液温度。
铸铝心轴的磨损极限值不大于表2的规定。
表2
3质量检查
铸铝转子铁心长度公差见表3。
表 3
铸铝转子铁心斜槽线应平直,无明显曲折,其斜槽尺寸应符合图样规定。
端环及风叶上的毛刺披锋和铁心外圆上的残铝必须清理干净。
铸铝转子的冲片之间,轴孔内不得夹铝和粘铝。
铸态表面质量要求
端环缩孔允许有三处,其深度小于3mm,直径小于5mm。
端环及风叶不得有裂纹、弯曲、夹渣、碰伤等现象,风叶冷隔不得超过风叶长度的四分之一,叶形残缺不超过3mm。
平衡柱无裂纹,残缺不得大于平衡柱高的五分之一,每端残缺不得超过该端总数的四分之一。
端环尺寸公差应符合图样的规定,端环外圆与铁心外圆的同轴度公差应符合GB1184-1980《形状和公差未注公差的规定》的D级规定。
铸铝转子槽内不允许有断条和细条现象,铸铝转子应逐台进行断条检查,检查可采用电流摆动比较法,按下式计算的电流摆动量不得超过3%。
转子槽口浇注不足或低陷不得超过槽口规定的尺寸。
铸铝转子铁心外圆伤痕深度不得超过外圆精车尺寸。