轴瓦检验规范概诉
发动机轴瓦
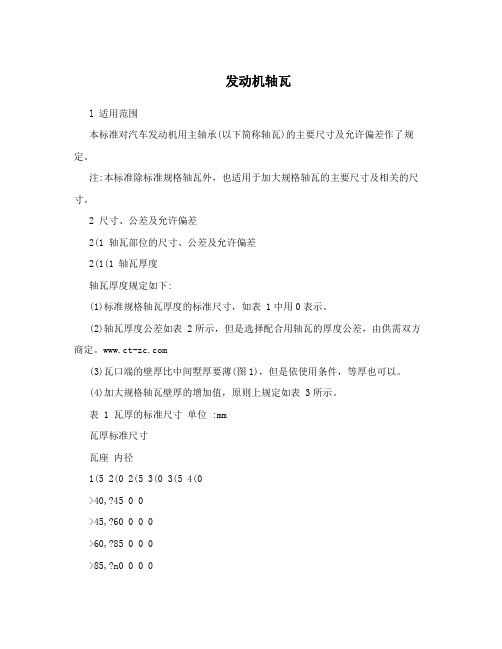
发动机轴瓦l 适用范围本标准对汽车发动机用主轴承(以下简称轴瓦)的主要尺寸及允许偏差作了规定。
注:本标准除标准规格轴瓦外,也适用于加大规格轴瓦的主要尺寸及相关的尺寸。
2 尺寸、公差及允许偏差2(1 轴瓦部位的尺寸、公差及允许偏差2(1(1 轴瓦厚度轴瓦厚度规定如下:(1)标准规格轴瓦厚度的标准尺寸,如表 1中用0表示。
(2)轴瓦厚度公差如表 2所示,但是选择配合用轴瓦的厚度公差,由供需双方商定。
(3)瓦口端的壁厚比中间墅厚要薄(图1),但是依使用条件,等厚也可以。
(4)加大规格轴瓦壁厚的增加值,原则上规定如表 3所示。
表 1 瓦厚的标准尺寸单位 :mm瓦厚标准尺寸瓦座内径1(5 2(0 2(5 3(0 3(5 4(0>40,?45 0 0>45,?60 0 0 0>60,?85 0 0 0>85,?n0 0 0 0>n0,?125 0 0 0>125,?150 0 0图 1 瓦口端壁厚表2 瓦厚公差单位 :mm 表3 加大规格轴瓦壁厚增加值单位:mm 瓦厚公差加大轴瓦规格壁厚增加值瓦座内径无表面镀层带表面镀层 0(25 0(125>40,?60 0(008 0(012 0(50 0(250>60,?n0 0(010 0(015 0,75 0(375>n0,?150 0(015 0(022 1(00 0(5O0----------------------- Page 2-----------------------维普资讯2(1(2 轴瓦定位唇尺寸及轴瓦座孔定位槽的尺寸轴瓦定位唇尺寸及轴瓦座孔定位槽的尺寸规定如下:(1)轴瓦定位唇的尺寸及允许偏差原则上如表4所示。
表4 轴瓦定位唇尺寸及允许偏差单位:mm轴瓦宽度(A) 高度(No) 长度(B)壁厚标准允许标准允许标准允许尺寸偏差尺寸偏差尺寸偏差1(5 3(O 1(0 4(02(0 4(0 1(4 5(62(5 5(0 O 1(4 O 5(6 O3(O 6(O —O(1 1(7 一O(25 8(7 ——0(83(5 6(0 1(7 8(74(0 6(0 1(7 8(7(2)轴瓦定位唇的边距(H),由于加工上的限制,边距应大于瓦厚的 1(5倍(即H?1(5×瓦厚),而且边距不得小于3mm(即H?3mm)。
轴瓦检修Microsoft PowerPoint 演示文稿剖析
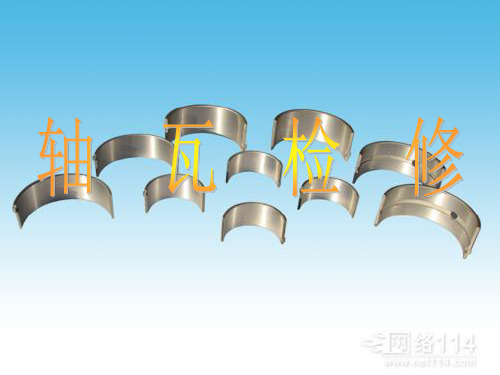
四、轴瓦研刮
轴不易被顶起,轴瓦合金与轴颈稍有摩擦时油池被破坏。 油池太深会影响润滑油膜的形成。油池的面积不能太大也 不能太小,因油池的本身就影响压力油膜的连续性。面积 太大,将使油膜浮力不够,破坏油膜,如果面积太小,又 顶不起轴颈 椭圆形轴瓦的接触角比圆筒型轴瓦的接触角略小,一 般为45°~50°。
二、轴瓦检修工艺
d:轴承间隙测量
使用塞尺测量下半轴承与轴颈两侧间隙,塞尺插入 的深度约为轴颈的1/12~1/10,塞尺厚度从0.03mm开始, 直到赛不进为之,此时塞尺的厚度即为两侧油间隙。
用压铅丝的方法测量(圆筒瓦及椭圆瓦)轴瓦顶部 间隙。将上半轴承吊开,在轴颈上放两条直径大于顶部间 隙的铅丝(轴承两端),扣上上半轴承并紧固轴承对口螺 栓。用塞尺检查水平接合面有无间隙,当用0.03mm塞尺 不入时可松开对口螺栓,吊开上半轴承,取出铅丝,用外 径千分尺测量铅丝的厚度取平均值,便是轴承的顶部间隙 值。
三、轴瓦检修标准及方法
对于轴径值在400mm及一下的可倾瓦,其标准间隙为轴 径值的1.3‰;对于轴径值在400mm以上的可倾瓦,其标 准间隙为轴径值的1.5 ‰,最大允许间隙为轴径值的 2 ‰ 可倾瓦的瓦块与轴径的油间隙值可通过调整瓦块背 部的调整块内的垫片来调整,当瓦块与轴颈的间隙超出标 准时,应更换轴承的瓦块。
五、轴承垫铁与轴承座洼窝间隙标准
非球面垫铁与轴承座洼窝间隙标准 每块垫铁应承重均匀,垫铁与轴承座洼窝的接触痕迹 应占垫铁总面积的75%以上,且接触点应均匀分布。带有 油孔的垫铁,油孔周围接触一定要严密,以防止润滑油外 泄。轴瓦在承重的状态下,垫铁与轴承座洼窝间隙0.03mm 塞尺应塞不进。抬起转子后,最下部垫铁应有0.03~ 0.07mm间隙,两侧垫铁用0.03mm塞尺应塞不进。如不符合 要求,应翻出下瓦,检查垫铁接触情况,并进行研刮。 1:首先在下部垫铁内加一片0.05mm厚的垫片,然后将下半 轴瓦和转子安装就位,在轴瓦水平接合面处拧固两个
瓦检作业操作规程
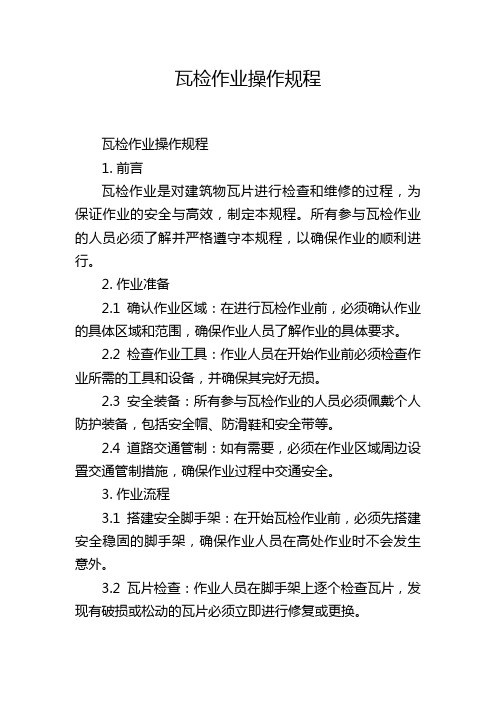
瓦检作业操作规程瓦检作业操作规程1. 前言瓦检作业是对建筑物瓦片进行检查和维修的过程,为保证作业的安全与高效,制定本规程。
所有参与瓦检作业的人员必须了解并严格遵守本规程,以确保作业的顺利进行。
2. 作业准备2.1 确认作业区域:在进行瓦检作业前,必须确认作业的具体区域和范围,确保作业人员了解作业的具体要求。
2.2 检查作业工具:作业人员在开始作业前必须检查作业所需的工具和设备,并确保其完好无损。
2.3 安全装备:所有参与瓦检作业的人员必须佩戴个人防护装备,包括安全帽、防滑鞋和安全带等。
2.4 道路交通管制:如有需要,必须在作业区域周边设置交通管制措施,确保作业过程中交通安全。
3. 作业流程3.1 搭建安全脚手架:在开始瓦检作业前,必须先搭建安全稳固的脚手架,确保作业人员在高处作业时不会发生意外。
3.2 瓦片检查:作业人员在脚手架上逐个检查瓦片,发现有破损或松动的瓦片必须立即进行修复或更换。
3.3 妥善保管材料:在作业过程中,作业人员必须合理安排材料的存放位置,防止材料滚落或损坏。
3.4 高处安全:作业人员在高处作业时必须站稳脚跟,保持平衡,不得随意移动或晃动脚手架。
3.5 防止交叉作业:在同一作业区域内,不得同时进行多个作业任务,以避免发生碰撞或意外伤害。
4. 安全注意事项4.1 严禁酒后作业:作业人员在进行瓦检作业前,不得饮酒或受酒精等物质的影响,严禁酒后作业。
4.2 注意天气状况:在恶劣的天气条件下,如大风、雨雪等,必须暂停作业,确保作业人员的人身安全。
4.3 注意观察周围环境:作业人员在高处作业时,必须时刻注意观察周围环境,防止因外界干扰或其他因素而发生意外。
4.4 禁止腾空作业:作业人员严禁腾空作业,即站在不稳固的支撑物上进行作业。
5. 应急措施5.1 作业人员伤害:如作业人员在作业过程中发生伤害,必须立即停止作业,并及时寻求医疗救助。
5.2 火灾事故:如发生火灾事故,必须立即报警并按照单位应急预案进行逃生和灭火。
发电机大修项目及质量标准
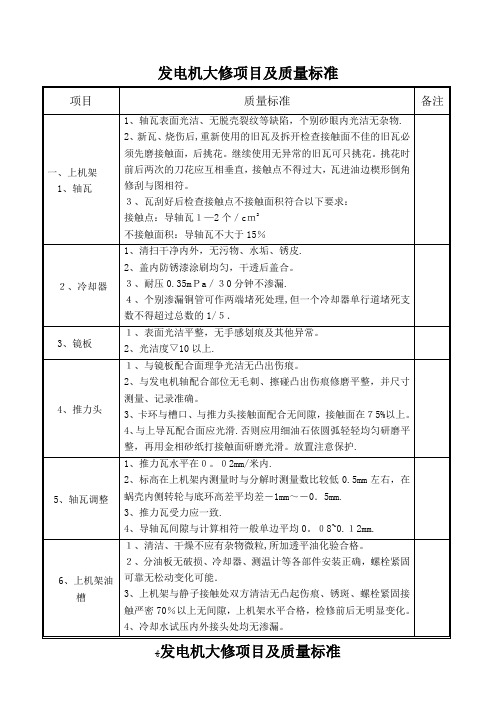
1、表面光洁平整,无手感划痕及其他异常。
2、光洁度▽10以上.
4、推力头
1、与镜板配合面理争光洁无凸出伤痕。
2、与发电机轴配合部位无毛刺、擦碰凸出伤痕修磨平整,并尺寸测量、记录准确。
3、卡环与槽口、与推力头接触面配合无间隙,接触面在75%以上。
4、与上导瓦配合面应光滑.否则应用细油石依圆弧轻轻均匀研磨平整,再用金相砂纸打接触面研磨光滑。放置注意保护.
七、定子检查
1、静子各部无不应有的杂物线圈无伤损。
2、消防水管等固定牢固无松动开裂.定子喷漆时注意喷水孔不能堵塞。
3、上下挡风板螺栓齐全无松动开裂。
4、基础板及静子与基础板、上机架接触部位应清洁无锈蚀及凸出伤痕接触严密70%以上无间隙。
5、气隙最大与最小不大于(或小于)平均气隙的10%。
八、机组轴线处理
5、总装初调
1、导叶50%开度时各杆件应基本水平符合图纸要求。
2、开度限制机构指示偏差全行程不大于2%。
3、压紧行程2-4mm.
4、回复机构死行程不大于接力器全行程的0.2%。
5、残留值按要求整定,记录于检修记录.
6、动特性试验
1、空载扰动
(1)扰动量±8%
(2)通过试验选配至最佳参数其标志是:
转速最大超调量不大于扰动量的30%,超调量次数不超过2次。
4、解体、检查及修理蜗壳排水阀、尾水管排水阀、技术供水阀;
阀门开、关动作自如,不费劲,无渗漏现象;
5、清扫、检查测量表计管路;
无堵塞、渗漏现象;
6、对引水钢管、蜗壳进行防腐;
除锈、打磨干净,刷防锈漆并进行干燥处理
五、大轴补气阀
对吸力真空阀进行解体、清扫及试验调整;
无锈蚀,密封面良好,动作正常(真空度为0.2MPa时应动作补气);
GJB319398装甲车辆柴油机主轴瓦及连杆轴瓦规范

中华人民共和国国家军用标准 F L2815GJB 3193-98装甲车辆柴油机主轴瓦及连杆轴瓦规范Specification of main bearings and connecting rodbearings for armoured vehicle diesel engine1998-03-16发布1998-09-01实施国防科学技术工业委员会批准目次1 范围 (1)1.1 主题内容 (1)1.2 适用范围 (1)2 引用文件 (1)3 要求 (1)3.1 合格鉴定 (1)3.2 可靠性 (1)3.3 材料 (1)3.4 设计 (2)3.5 结构 (2)3.6 性能 (6)3.7 维修性 (6)3.8 尺寸与形位公差 (6)3.9 表面状况 (10)3.10 产品的标志和代号 (10)3.11 外观质量 (10)4 质量保证规定 (11)4.1 检验责任 (11)4.2 检验分类 (11)4.3 检验条件 (11)4.4 鉴定检验(定型检验) (11)4.5 质量一致性检验 (11)4.6 包装检验 (13)4.7 检验方法 (14)5 交货准备 (17)5.1 封存和包装 (17)5.2 运输和贮存 (17)5.3 标志 (17)6 说明事项 (18)6.1 订货文件内容 (18)6.2 定义 (18)中华人民共和国国家军用标准装甲车辆柴油机主轴瓦GJB 3193-98及连杆轴瓦规范Specification of main bearings and connecting rodbearings for armoured vehicle diesel engine1 范围1.1 主题内容本规范规定了装甲车辆柴油机用主轴瓦及连杆轴瓦(以下简称轴瓦)的技术要求、质量保证规定和交货准备等内容。
1.2 适用范围本规范适用于装甲车辆柴油机用轴瓦的设计、制造和验收。
其它军用柴油机的轴瓦亦可参照使用。
轴瓦判定准则

2500Km以下出现烧瓦,责任:装配厂。2500Km以上:供应商。
脱落
止推瓦脱落
止推片松脱
1、检查每挡主轴孔的两端面是否有受轴向推力痕迹。
1、属于受轴向力原因造成。
更换止推瓦及相关故障件
1、100%汽车厂
2、检查油质。
2、油质原因引起。
2、100%用户。
更换轴瓦及相关故障件
1、轴瓦供应商(没受高温现象的剥落)
穴蚀
轴瓦工作表面呈现麻点,瓦面发黑
穴蚀
1、检查轴瓦各档是否都有穴蚀情况。
1、机油原因引起。
更换轴瓦及相关故障件
1、如不是用玉柴机油的,责任:用户。
2、如机油是用玉柴的,责任:润滑油公司与轴瓦供应商各1/2。
龟裂
轴瓦工作面(内表面)出现细裂纹
龟裂
烧坏
轴瓦工作面(内表面)、钢背烧伤
烧瓦
1、油质(机油是否严重发黑、有杂质等现象)。
3、属于油质原因引起。
1、更换相关件后装上源机油泵如机油压力低的
2、更换轴
瓦
1、用户
2、检查油量(检查项)。
2、油量不足,属缺油导致烧瓦。
2、用户
3、检查轴瓦是否有严重剥落,或抱死曲轴现象;
3轴瓦合金层剥落原因造成烧瓦,属于轴瓦质量问题。
3.轴瓦供应商。
4、检查机油泵:1)换轴瓦后,检查机油压力是否能达技术要求。2)检查机油泵是否明显损坏、松动。3)如无以上两点情况。
4、1)如果机油压力不达技术要求,则烧瓦是机油泵原因引起。
如果机油泵有明显损坏或松动现象,则是机油泵原因造成烧瓦。
4、1)100%机油泵责任。
2)100%机油泵责任。
瓦检作业操作规程

瓦检作业操作规程
《瓦检作业操作规程》
一、目的与范围
本操作规程适用于瓦检作业的实施,旨在规范作业流程,确保作业安全和质量。
二、作业前准备
1. 设立作业区域,确保工作环境清洁整洁。
2. 准备必要的工具和设备,包括瓦片、瓦检工具等。
3. 确认作业人员已经接受过相关培训并具有必要的操作证书。
三、作业流程
1. 检查要进行瓦检的瓦片,排除是否有破损、裂缝或其它质量问题。
2. 使用专用工具进行瓦检,确保每一块瓦片都经过了质量的检验。
3. 将经过检验的瓦片进行分类,分为合格品和次品。
4. 对次品瓦片进行记录和标记,以备后续处理。
四、作业安全
1. 在进行瓦检作业时,作业人员必须佩戴好相关的安全防护用具,如手套、护目镜等。
2. 在搬运和操作瓦片时,要注意轻拿轻放,防止瓦片破损或伤到人员。
五、作业结束
1. 做好作业区域的清理和整理工作。
2. 对次品瓦片进行处理,可以选择返工或废弃。
3. 对作业流程中出现的问题和不良情况进行总结和反馈。
六、相关控制
1. 确保作业区域的整洁和安全。
2. 定期对瓦检工具和设备进行检查和维护。
3. 结合实际情况,不断优化和改进瓦检作业流程。
以上即为《瓦检作业操作规程》的内容,希望能够对瓦检作业的实施提供指导和规范。
柴油机连杆轴瓦常见损伤原因与检验方法
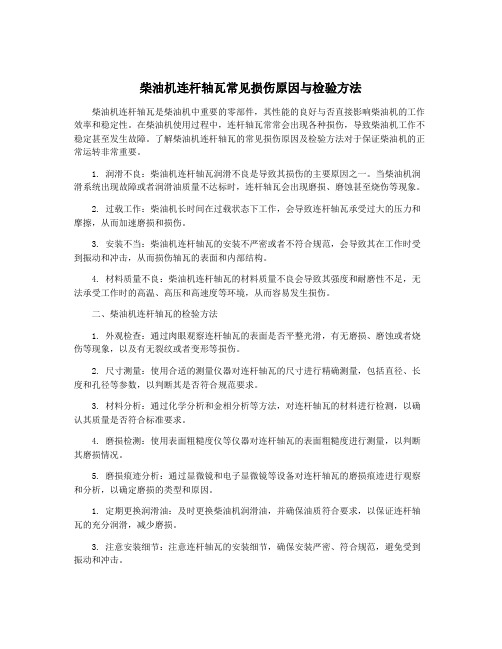
柴油机连杆轴瓦常见损伤原因与检验方法柴油机连杆轴瓦是柴油机中重要的零部件,其性能的良好与否直接影响柴油机的工作效率和稳定性。
在柴油机使用过程中,连杆轴瓦常常会出现各种损伤,导致柴油机工作不稳定甚至发生故障。
了解柴油机连杆轴瓦的常见损伤原因及检验方法对于保证柴油机的正常运转非常重要。
1. 润滑不良:柴油机连杆轴瓦润滑不良是导致其损伤的主要原因之一。
当柴油机润滑系统出现故障或者润滑油质量不达标时,连杆轴瓦会出现磨损、磨蚀甚至烧伤等现象。
2. 过载工作:柴油机长时间在过载状态下工作,会导致连杆轴瓦承受过大的压力和摩擦,从而加速磨损和损伤。
3. 安装不当:柴油机连杆轴瓦的安装不严密或者不符合规范,会导致其在工作时受到振动和冲击,从而损伤轴瓦的表面和内部结构。
4. 材料质量不良:柴油机连杆轴瓦的材料质量不良会导致其强度和耐磨性不足,无法承受工作时的高温、高压和高速度等环境,从而容易发生损伤。
二、柴油机连杆轴瓦的检验方法1. 外观检查:通过肉眼观察连杆轴瓦的表面是否平整光滑,有无磨损、磨蚀或者烧伤等现象,以及有无裂纹或者变形等损伤。
2. 尺寸测量:使用合适的测量仪器对连杆轴瓦的尺寸进行精确测量,包括直径、长度和孔径等参数,以判断其是否符合规范要求。
3. 材料分析:通过化学分析和金相分析等方法,对连杆轴瓦的材料进行检测,以确认其质量是否符合标准要求。
4. 磨损检测:使用表面粗糙度仪等仪器对连杆轴瓦的表面粗糙度进行测量,以判断其磨损情况。
5. 磨损痕迹分析:通过显微镜和电子显微镜等设备对连杆轴瓦的磨损痕迹进行观察和分析,以确定磨损的类型和原因。
1. 定期更换润滑油:及时更换柴油机润滑油,并确保油质符合要求,以保证连杆轴瓦的充分润滑,减少磨损。
3. 注意安装细节:注意连杆轴瓦的安装细节,确保安装严密、符合规范,避免受到振动和冲击。
4. 选择优质材料:在更换连杆轴瓦时,选择优质的材料和工艺加工,以提高连杆轴瓦的强度和耐磨性。
轴瓦式高压电机检修项目及标准
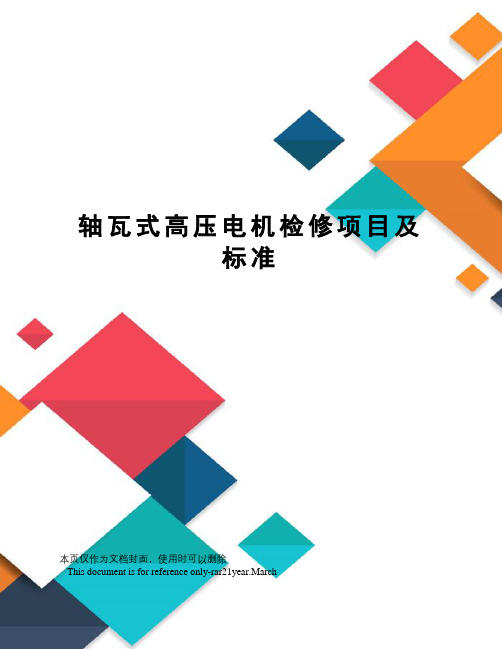
1.试运两小时
2.振动、温度、声音、电流、转向符合要求
2.定子铁芯在机壳上焊接或固定良好
3.转子铁芯在转轴上固定良好
12
楔检查
槽楔紧固
14
定子引出线检查
引出线绝缘良好,固定良好,引出线接头焊接良好
15
转子绕组检修
鼠笼条无断裂、开焊
16
转子风扇及平衡块检查
风扇及平衡块固定螺栓紧固
17
装转子
定、转子无损伤
18
电机复位
1.无人身伤害及设备损坏
2.电机定子所落位置与原标记相符
19
复测定、转子间隙
四周间隙四周均匀不超过平均值的10%
20
复装电机端盖
电机端盖与转轴间隙四周均匀5S
21
电机接线
1.带电部位之间及带电部分与接线盒之间安全净距符合要求
2.电缆头无损伤
3.电缆与接线盒直接接触部位应加绝缘皮加以保护
22
5
电机起吊并运至检修场地
无人身伤害及设备损坏
6
拔对轮风扇
1.对轮风扇无损坏
2.难拔的对轮用两套气割加热,不得硬拔,防止损坏
7
做好标记后解体
标记清晰正确,各零部件妥善保管
8
抽转子
定、转子完好无碰伤
9
定、转子清扫
定、转子通风孔及绕组清洁无异物、赃物
10
空冷器清洗、水压试验
11
定、转子铁芯检修
1.铁芯无松散、锈蚀、过热
轴瓦式高压电机检修项目及标准
高压电机检修(一)
序号
项目
质量标准
责任人
时间
备注
1
拆电缆接头
1.电缆头无碰伤或损坏
质量工艺手册(轴瓦检修)

安全质量标准化
—轴瓦检修关键工艺
1、轴瓦的检查:
关键质量工艺要求:
1
对所检修的轴瓦首先进行外观检查,是否存在气孔、裂纹等缺陷,并进行详细的记录。
2
检查轴瓦尺寸是否正确,轴瓦乌金是否脱胎或局部脱落(可浸煤油实验、超声波探伤等方法)。
3
乌金面上轴颈磨擦痕迹所占的位置是否正确,该处的刮研刀花是否被磨亮,有无划伤,损坏和磨蚀。
4
垫铁承力面或球面上有无磨损和磨蚀,垫铁螺钉是否松动以及垫铁是否完好。
5 检查轴承各部份间隙是否符合要求,如轴瓦处有磨得发
亮,变硬,要进行修刮,以免损伤轴颈。
6 检查轴颈有无损伤,并用金相砂纸打磨轴颈。
检查轴瓦是
否存在脱
胎、气孔等
缺陷 乌金磨擦痕
迹所占位置
是否正确 打磨轴颈,检查有无损
伤
2、更换轴瓦所进行的检查:
关键质量工艺要求:
1 新的轴瓦首先进行外观检查,是否存在气孔、裂纹等缺陷,并进行详细的记录。
2 检查轴瓦尺寸是否正确,轴瓦乌金是否脱胎或局部脱落(可浸煤油实验、超声波探伤等方法)。
3 对新轴瓦进行初步修刮,使轴与轴瓦之间出现部分间隙,但一般不超过正常间隙的2/3。
3、下轴瓦的初步修刮:
4、下轴瓦的精刮:
5、上轴瓦的研刮:。
拔轴瓦检修工艺和质量标准

轴瓦检修工艺和质量标准一、各轴瓦质量标准1、各轴瓦质量标准如下表:单位:mm一)主轴承1、主轴承的解体1)拆除轴承盖上的测振元件等附件。
2)拆除轴承盖结合面螺丝,拔出定位销、吊走瓦盖。
3)拆瓦枕结合面螺丝,用铜棒将销子螺丝向下打,吊走上枕瓦,注意结合面是否有垫片,取下结合面处销饼。
4)取出轴承室靠近轴瓦处的下油挡,放入专用顶转子工具,将转子顶起。
顶起前应装上两块千分表,测量顶起高度及左右移动,顶起高度不易太高,以防顶坏汽封齿,一般顶至0.5mm左右,拆顶轴油管及测点,测点引出线接头。
5)拆轴瓦结合面螺丝,将轴瓦结合面转至水平,用铜棒打下销子螺丝,吊走上瓦,注意结合面是否有垫片。
6)如揭缸,待转子吊出后,可将下瓦及下瓦枕分别吊出,如不揭缸只检查轴瓦须先将下瓦转出下瓦枕再吊出,3,4,5,瓦顺序用专用吊轴瓦用的杠杆工具将下瓦吊出,下瓦或下瓦枕吊出后用胶布将进油孔封闭,以防杂物进入。
2、清理检查:1)将轴瓦各部清理干净,进油管及轴瓦油槽中无杂物,轴承盖结合面如涂的漆片,应用刮刀,砂布清理干净。
2)检查轴瓦应无裂纹,损伤,钨金无剥落,气孔槽道裂纹等情况。
检查钨金有无脱胎情况,作好记录,检查顶轴油管是否畅通。
上瓦吊走转子未吊出前,应用桥规进行测量,并与前次检查作比较,以确定轴瓦钨金磨损情况。
3)检查轴颈与钨金接触情况,沿轴应均匀接触。
4)检查瓦枕垫铁接触的情况,在轴承洼窝内涂上红丹粉少许,将瓦枕放入,轻转动研磨,吊出查看痕迹。
底部不应接触,应有0.03—0.05的间隙。
如接触不良应修刮,研磨修刮面应在底部垫铁下加0.05mm垫片,然后进行研磨修刮。
直至三块铁接触均匀,接触面〉70%为止。
然后取出底部0.05mm垫片。
5)检查球面与洼窝之间接触情况,应光滑、平整,无毛刺,接触分布均匀,接触面积〉70%。
3、油档的检修:(1)轴承室前后油档卸下后清扫干净,将结合面园周安装部分的漆片刮净,回油孔用铁丝通畅通。
(2)检查铜油档片是否有裂纹,弯曲卷边现象,如有应进行修整。
29轴瓦验收标准[1]
![29轴瓦验收标准[1]](https://img.taocdn.com/s3/m/04fc3eb5fd0a79563c1e724b.png)
轴瓦验收标准页 次 第 1 页 , 共 2 页
1范围
本标准规定了本公司所采购的轴瓦进厂验收项目,验收规则及验收要求。
本标准适用于本公司的轴瓦进厂检验。
2 验收项目及规则
a.产品合格证
合格证上必须注明产品名称、规格、材质、数量、检验员及检验日期。
b.外观质量
轴瓦表面不允许有锐角、毛刺、锈蚀、裂纹、黑皮,各端面及配合面不允许有缺陷及严重磕碰伤。
c.标识检验
每付轴瓦的上下轴瓦相对应字母或数字必须一致。
对应钢印位置在轴瓦的上或下端面。
d.粗糙度检验
轴瓦配合表面和端面的表面粗糙度根据规格型号找出相对应的公司技术图纸文件规定进行检验。
粗糙度用表面粗糙度测量仪或粗糙度样块比较法检验。
e.尺寸检验
轴瓦各尺寸根据规格型号找出相对应的公司技术图纸文件进行检验。
f.检验规则
轴瓦进厂时每批次检验项目按a、b、c、d、e项检验,每批次按20%的抽样比例检验,抽样数不少于2套。
抽样过程中,如有一套不合格,采取加倍抽检,加倍抽检100%合格则判定批合格,若仍有不合格则整批拒收或采取全数检验。
附加说明:
本规范由质量管理办公室提出并归口管理
本规范由五分厂负责起草
轴瓦验收标准页 次 第 2 页 , 共 2 页本规范起草人:张杰
本规范由唐亮审核
本规范由李爱学批准。
轴瓦选配与检修要点(3)

51轴瓦选配与检修要点(3)阮天林(上接2021年第3期)整体式曲轴通过正常检修,其轴颈与轴瓦进行配对研磨和抛光,难免有研磨剂液体渗入曲轴润滑油道内。
对此,应设法去掉主油道油塞,使用专用铰刀或压缩空气进行高压清洗,清洗干净后,重新拧紧油塞。
部分车型的整体式曲轴没有油塞结构,其油孔主要利用钢球作工艺堵塞,可用冲子小心将工艺钢球冲出,然后用不低于5.0kg/cm 3的高压空气反复吹洗、清理润滑油油道,并用清洁汽油(至少二次)将润滑油主油道清洗干净,确认曲轴主油道内没有任何异物杂质后,再将工艺钢球装入主油道工艺孔内,最后用专用工具将装入的工艺钢球沿圆周冲铆紧,防止其在曲轴运转过程中脱落,而导致润滑油意外流失。
在曲轴连杆机构中,连杆大小头孔轴线应保证在同一平面内,并互相平行。
发动机工作时,有可能出现超负荷运行或爆震以及拆装时操作不慎重等原因,使连杆受力较大,造成连杆弯曲或扭曲。
若连杆产生弯曲或扭曲,不仅降低了连杆本身的强度,变形后的连杆在发动机工作时,还会使活塞与气缸的配合关系发生变化,使活塞、活塞环、气缸出现单侧受力过大,加重活塞和气缸的过量磨损或偏磨,导致活塞环漏气和窜机油等不良现象。
因此,发动机大修时(尤其是运行里程超过30 000km 以上的车辆),必须对连杆是否存在弯曲或扭曲现象进行检查,并视情予以矫正。
a )连杆杆身弯曲和扭曲。
主要有以下三种:1)连杆在曲轴中心线平面内的弯曲;2)连杆在垂直于曲轴平面内的弯曲变形;3)连杆扭曲变形。
这三种弯曲和扭曲变形,以连杆在曲轴中心线平面内的弯曲最为严重,它会使连杆大小头孔的平行度超差,造成活塞、活塞环与气缸内壁产生偏磨,是极其有害的变形,应认真进行检测。
b )连杆的扭曲测量:用两块等高V 形铁分别支撑连杆大头芯轴,将连杆小头及芯轴搁在方铁块上,用磁性百分表在同一平板上先校测连杆大头芯轴两边,使之与平板面保持平行(平行度不超过0.005mm ),然后再测量连杆图33小头芯轴两边的差值,即可计算出连杆的扭曲量(连杆大小头中心线空间偏扭度应≤0.06 mm )。
轴瓦垫铁研磨标准依据
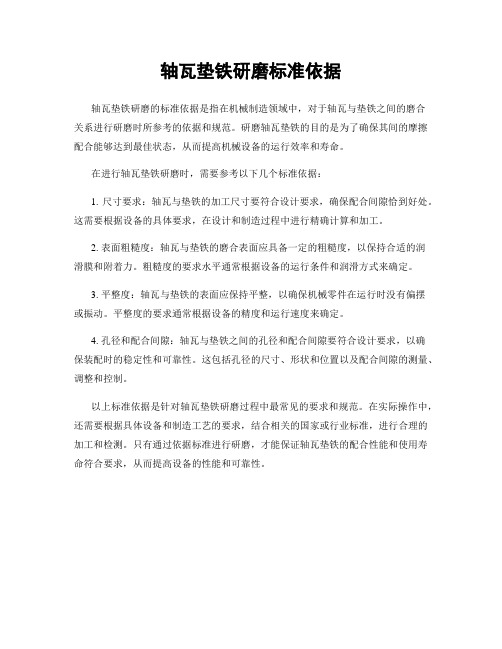
轴瓦垫铁研磨标准依据
轴瓦垫铁研磨的标准依据是指在机械制造领域中,对于轴瓦与垫铁之间的磨合
关系进行研磨时所参考的依据和规范。
研磨轴瓦垫铁的目的是为了确保其间的摩擦配合能够达到最佳状态,从而提高机械设备的运行效率和寿命。
在进行轴瓦垫铁研磨时,需要参考以下几个标准依据:
1. 尺寸要求:轴瓦与垫铁的加工尺寸要符合设计要求,确保配合间隙恰到好处。
这需要根据设备的具体要求,在设计和制造过程中进行精确计算和加工。
2. 表面粗糙度:轴瓦与垫铁的磨合表面应具备一定的粗糙度,以保持合适的润
滑膜和附着力。
粗糙度的要求水平通常根据设备的运行条件和润滑方式来确定。
3. 平整度:轴瓦与垫铁的表面应保持平整,以确保机械零件在运行时没有偏摆
或振动。
平整度的要求通常根据设备的精度和运行速度来确定。
4. 孔径和配合间隙:轴瓦与垫铁之间的孔径和配合间隙要符合设计要求,以确
保装配时的稳定性和可靠性。
这包括孔径的尺寸、形状和位置以及配合间隙的测量、调整和控制。
以上标准依据是针对轴瓦垫铁研磨过程中最常见的要求和规范。
在实际操作中,还需要根据具体设备和制造工艺的要求,结合相关的国家或行业标准,进行合理的加工和检测。
只有通过依据标准进行研磨,才能保证轴瓦垫铁的配合性能和使用寿命符合要求,从而提高设备的性能和可靠性。
铝基轴瓦金相标准

铝基轴瓦金相标准如下:
1.宏观检查:轴瓦基体应无气孔、砂眼、疏松等铸造缺陷。
2.显微组织检查:轴瓦基体应具有致密的、均匀分布的、无宏观偏析的显微
组织。
3.晶粒度检查:轴瓦基体的晶粒度应符合要求,晶粒应细小、均匀。
4.夹杂物检查:轴瓦基体中不得有大于0.05mm的夹杂物存在。
5.硬度检查:轴瓦基体的硬度应符合要求。
6.耐磨性试验:通过摩擦试验,检查轴瓦基体的耐磨性能。
7.疲劳性能试验:通过疲劳试验,检查轴瓦基体的疲劳性能。
8.抗腐蚀性能试验:通过盐雾试验、浸渍试验等方法,检查轴瓦基体的抗腐
蚀性能。
9.金相组织观察:通过金相显微镜观察,分析轴瓦基体的金相组织结构。
10.其他特殊要求:根据具体使用条件和性能要求,可制定其他特殊的金相标
准。
以上是铝基轴瓦的一般金相标准,具体标准可能会因产品类型、使用条件等因素而有所不同。
混凝土瓦检验实施细则
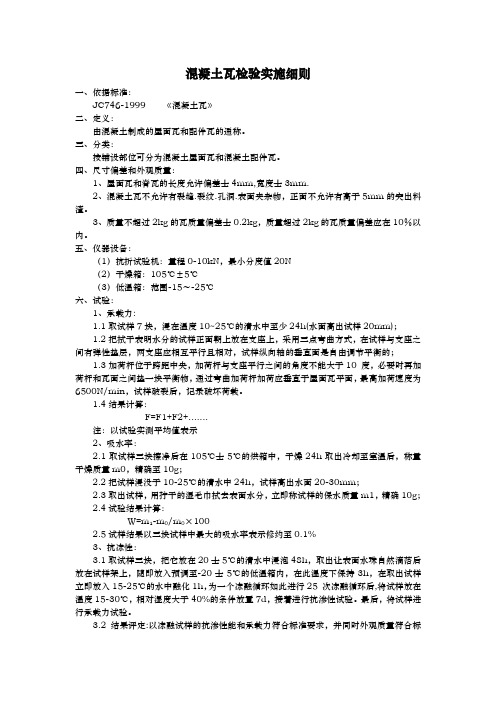
混凝土瓦检验实施细则一、依据标准:JC746-1999 《混凝土瓦》二、定义:由混凝土制成的屋面瓦和配件瓦的通称。
三、分类:按铺设部位可分为混凝土屋面瓦和混凝土配件瓦。
四、尺寸偏差和外观质量:1、屋面瓦和脊瓦的长度允许偏差士4mm,宽度士3mm.2、混凝土瓦不允许有裂缝.裂纹.孔洞.表面夹杂物,正面不允许有高于5mm的突出料渣。
3、质量不超过2kg的瓦质量偏差士0.2kg,质量超过2kg的瓦质量偏差应在10%以内。
五、仪器设备:(1)抗折试验机:量程0-10kN,最小分度值20N(2)干燥箱:105℃±5℃(3)低温箱:范围-15~-25℃六、试验:1、承载力:1.1取试样7块,浸在温度10~25℃的清水中至少24h(水面高出试样20mm);1.2把拭干表明水分的试样正面朝上放在支座上,采用三点弯曲方式,在试样与支座之间有弹性垫层,两支座应相互平行且相对,试样纵向轴的垂直面是自由调节平衡的;1.3加荷杆位于跨距中央,加荷杆与支座平行之间的角度不能大于10 度,必要时再加荷杆和瓦面之间垫一块平衡物,通过弯曲加荷杆加荷应垂直于屋面瓦平面,最高加荷速度为6500N/min,试样破裂后,记录破坏荷载。
1.4结果计算:F=F1+F2+.......注:以试验实测平均值表示2、吸水率:2.1取试样三块擦净后在105℃士5℃的烘箱中,干燥24h取出冷却至室温后,称量干燥质量m0,精确至10g;2.2把试样浸没于10-25℃的清水中24h,试样高出水面20-30mm;2.3取出试样,用拧干的湿毛巾拭去表面水分,立即称试样的保水质量m1,精确10g;2.4试验结果计算:W=m1-m0/m0×1002.5试样结果以三块试样中最大的吸水率表示修约至0.1%3、抗冻性:3.1取试样三块,把它放在20士5℃的清水中浸泡48h,取出让表面水珠自然滴落后放在试样架上,随即放入预调至-20士5℃的低温箱内,在此温度下保持3h,在取出试样立即放入15-25℃的水中融化1h,为一个冻融循环如此进行25 次冻融循环后,将试样放在温度15-30℃,相对湿度大于40%的条件放置7d,接着进行抗渗性试验。
轴的检修工艺标准

轴的检修工艺标准1.1.1.1.1 在轴瓦处的轴表面必须光滑,不得有斑痕及凸起处。
1.1.1.1.2 轴在静止状态下的垂直度不宜超过0.2mm。
1.1.1.1.3 轴的弯曲允许值不应超过0.03mm~0.08mm。
1.1.1.1.4 在轴瓦处的轴颈椭圆度及锥度不应超过0.05mm。
1.1.1.1.5 轴的水平差,每公尺轴差不应超过0.05mm。
1.1.1.1.6 轴颈磨损时采用下述方法进行处理:——镶套:当轴颈磨损严重时采用;——焊后进行退火处理再加工到需要尺寸;——喷镀:当轴颈磨损轻微时(在0.2mm内)所采用的方法。
1.1.1.1.7 固定端轴承与轴肩间的轴向间隙总和(a+b)不得大于0.3mm~0.4mm,自由端轴承与轴承间隙膛得小于轴的热膨胀伸长量:1.1.1.1.8 轴的热膨胀伸长量如下表4:表1 轴的热膨胀伸长量温度(℃) 0~100100~200200~300轴长的伸长量(mm) 1.2 2.51 3.921.2 键与键槽检修工艺标准1.2.1.1.1 键与键槽与修研至面部光滑,无棱角变形。
1.2.1.1.2 键与键槽的尺寸应符合技术要求。
1.2.1.1.3 键与键槽应先进行试装,尺寸要吻合,不得在键槽内加垫片。
1.2.1.1.4 平键、平园键与键槽配合后其工作面应紧密贴合,不得松动,其顶部应留间隙,当配合不紧密时,不得增大键的厚度来增加紧力。
1.2.1.1.5 楔键与槽两侧面均不得接触。
1.2.1.1.6 楔键装配后其键头与轮之间应留有间隙,以便拆卸。
1.2.1.1.7 导向平键的固定丝应埋入键内,不得高出键的顶面。
1.2.1.1.8 比原尺寸小至5%时,应该更换。
1.3 定位销检修工艺标准1.3.1.1.1 装定位销时,应将两连接件的销孔对准,检查确无不同心和不同径的偏差后,方可将定位销装入。
1.3.1.1.2 装定位销时,应轻轻推入,其深度应达到图纸要求,销与销孔应接触良好。
轴瓦轴衬设备安全操作规程
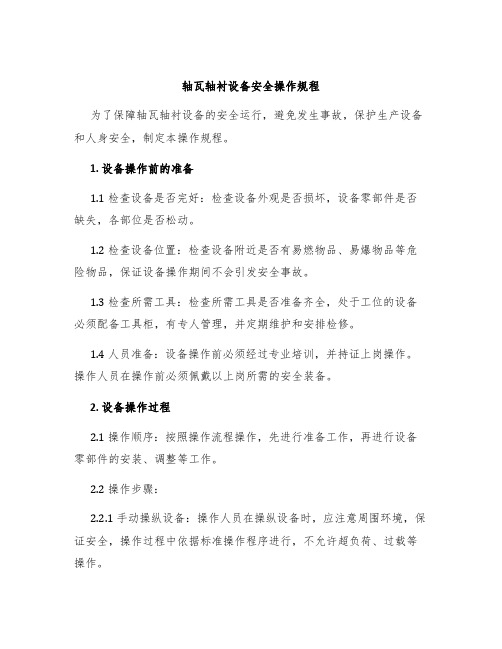
轴瓦轴衬设备安全操作规程
为了保障轴瓦轴衬设备的安全运行,避免发生事故,保护生产设备和人身安全,制定本操作规程。
1. 设备操作前的准备
1.1 检查设备是否完好:检查设备外观是否损坏,设备零部件是否缺失,各部位是否松动。
1.2 检查设备位置:检查设备附近是否有易燃物品、易爆物品等危险物品,保证设备操作期间不会引发安全事故。
1.3 检查所需工具:检查所需工具是否准备齐全,处于工位的设备必须配备工具柜,有专人管理,并定期维护和安排检修。
1.4 人员准备:设备操作前必须经过专业培训,并持证上岗操作。
操作人员在操作前必须佩戴以上岗所需的安全装备。
2. 设备操作过程
2.1 操作顺序:按照操作流程操作,先进行准备工作,再进行设备零部件的安装、调整等工作。
2.2 操作步骤:
2.2.1 手动操纵设备:操作人员在操纵设备时,应注意周围环境,保证安全,操作过程中依据标准操作程序进行,不允许超负荷、过载等操作。
- 1、下载文档前请自行甄别文档内容的完整性,平台不提供额外的编辑、内容补充、找答案等附加服务。
- 2、"仅部分预览"的文档,不可在线预览部分如存在完整性等问题,可反馈申请退款(可完整预览的文档不适用该条件!)。
- 3、如文档侵犯您的权益,请联系客服反馈,我们会尽快为您处理(人工客服工作时间:9:00-18:30)。
文件名称:轴瓦系列产品检验规范文件编号:Q/AD Q31.TD04版本/版次:A/0页数:第1页共3页受控状态:分发号:发布日期:2006年02月25日实施日期:2006年03月01日编制:审核:批准:1.目的:对产品进行有效的检测,保证产品质量,预防质量事故。
2.范围:适用于本公司生产的主轴瓦及连杆瓦在制造过程中及最终的成品检验。
3.引用标准:GB/T 7308—1987 《滑动轴承薄壁滑动轴承用金属多层材料》QC/T 516—99 《汽车发动机主轴瓦锡基和铅基合金金相标准》QC/T 281—1999 《汽车发动机轴瓦铜铅合金金相标准》QC/T 280—1999 《汽车发动机主轴瓦及连杆瓦技术条件》QC/T 282—1999 《汽车发动机主轴止推片技术条件》GB/T 7308—1987 《滑动轴承薄壁翻边轴瓦尺寸、公差及检验方法》GB/T 12613.1—2002 《滑动轴承卷制轴套第一部分:尺寸》GB/T 12613.2—2002 《滑动轴承卷制轴套第二部分:外径和内径的检测数据》GB/T 12613.3—2002 《滑动轴承卷制轴套第三部分:润滑油孔、润滑油槽和润滑油穴》GB/T 12613.4—2002 《滑动轴承卷制轴套第四部分:材料》JB/T 7920—1995 《滑动轴承薄壁轴瓦周长的检验方法》GB/T 18330—2001 《滑动轴承薄壁轴瓦和薄壁轴套的壁厚测量》GB/T 18331.1—2001 《滑动轴承卷制轴套外经的检测》4.目录:第一部分:材料检验规范第二部分:过程检验规范第三部分:成品检验规范5.内容:第一部分材料检验规范一.铜铅合金双金属带1.钢背材料:(选用钢板必须符合GB699-1999的要求)1.1钢背牌号钢背材料可选用:10F、15F、10、15优质碳素结构钢或St37-2G、SPCC、SPHC、St37-2、SS400。
1.2化学成分:必须满足C 0.06~0.17%;Si ≤0.05%;Mn 0.25~0.90%;P ≤0.035%;S ≤0.030%。
1.3机械性能:1.3.1轴瓦材料为360~510MPa;衬套材料>270 MPa。
1.3.2轴瓦材料≥215 MPa;衬套材料>185MPa。
1.3.3延伸率(长80mm)≥20%。
1.3.4钢背硬度:连杆瓦、主轴瓦和止推片为HB120~HB160;翻边瓦和衬套为HB100~HB130。
同一批次的材料,钢背硬度差不得大于HB10。
2.合金层材料2.1合金层化学成分及表面硬度应符合表1之规定。
表1 合金层化学成分及表面硬度表:说明:翻边瓦和衬套的合金硬度应比标准要求低HB10~HB15。
同一批次的材料,合金硬度差不得大于HB5。
2.3合金层金相组织:2.3.1 轴瓦合金层中铅的分布形态为树状时,按表2评定,其中1~5级为合格,6级为不合格。
表2 合金层中铅的分布形态为树状评定表2.3.2轴瓦合金层中铅的分布形态为点、块状时,按表3评定,其中1~5级为合格,6级为不合格。
表3 合金层中铅的分布形态为点、块状评定表2.3.3轴瓦合金层中铅的分布形态为网状时,按表4评定,其中1~4级为合格,5级为不合格。
表4 合金层中铅的分布形态为网状评定表2.3.4轴瓦合金层中铅的分布形态为点及不规则的块状时,按表5评定,其中1~4级为合格,5级为不合格。
表5 合金层中铅的分布形态点及不规则的块状评定表2.3.5 合金与钢背结合情况,按表6评定,其中1~2级为合格,3级为不合格。
表6合金与钢背结合情况评定表注:①在每个视场中,单个氧化物和硫化物的最大边长不得大于50µm,其总面积不得大于8000µm2。
②不允许有硬质硼化物存在。
③合金层中单个最大的铅块面积不得大于8000µm2。
3.钢带表面质量3.1钢背表面粗糙度Ra0.8。
3.2合金表面粗糙度Ra1.6。
3.3钢背表面必须镀铜且应光洁、均匀平滑,不得有斑点、锈蚀、擦伤、划伤等缺陷。
3.4合金层不允许有砂眼、气孔、夹杂物、裂缝及疏松等缺陷。
4.钢带几何尺寸和形位质量4.1 几何尺寸4.1.1 名义尺寸:按材料规格检验。
4.1.2 尺寸公差:总厚度公差+0.05 0,钢背厚度公差:0 -0.05,宽度公差:±0.5,长度公差:+15 0。
4.1.3形位公差4.1.3.1长边相对于短边的垂直度为0.5。
4.1.3.2毛边(烧结粉末坡度)对称度为1。
4.1.3.3镰刀弯(即两长边的直线度)≤3/1000。
5. 检验方法5.1 金相组织5.1.1 取样大小:在钢带中截取试样,其长度10~30,宽4~8。
5.1.2 试样制作:采用镶嵌法制作试样。
5.1.3 检查部位:对铅的分布,在规定的工作面和结合层的整个磨面上进行检查评级。
5.1.4 试样浸蚀方法:用2~4%的硝酸酒精溶液浸蚀3~6秒钟。
5.1.5 显微组织评级方法:试样在100倍显微镜下选取5个最差的视场分别进行评级。
若5个视场中有3个视场为不合格级或有1个视场超出不合格级,则判为不合格。
5.2 结合强度5.2.1 金相显微法5.2.1.1取样大小:在钢带中截取试样,其长度10~30,宽4~8。
5.2.1.2试样制作:采用镶嵌法制作试样。
5.2.1.3检查部位:在试样长边截面上检查评级。
5.2.1.4试样浸蚀方法:用2~4%的硝酸酒精溶液浸蚀3~6秒钟。
5.2.1.5 显微组织评级方法:试样在100倍显微镜下选取最差的视场作为评级的依据。
5.2.2 破坏试验法5.2.2.1取样大小:在钢带中截取试样,其长度100~120mm,宽10~15mm。
5.2.2.2 检查部位:在试样弯曲裂开的合金与钢背的结合出检查评定。
5.2.2.3 试样制作:将试样沿长度方向,合金面向外弯曲成180°,使得钢背面与钢背面相互贴紧,弯曲半径等于试样的总厚度。
5.2.2.4 评定方法:5.2.2.4.1 裂纹状态:合金层厚度在总厚的20%以下时,裂纹应为细网状,不允许有粗大的或直线裂纹;合金层厚度在总厚的20~35%时,允许有粗大的或直线裂纹;合金层厚度在总厚的35%以上时,允许有直线翘开裂纹,但底部应呈毛绒状。
5.2.2.4.2 合金层断口颜色:合金层断口颜色应为灰白色,灰白颜色程度随含铅量的多少而不同。
含铅量越高颜色越深,含铅量月高颜色越浅。
5.2.2.4.3 结合面:合金层与钢背层结合面上应附有灰白色合金粉末。
5.3 钢背/合金硬度5.3.1取样大小:在钢带中截取试样,其长度10~30mm,宽4~8mm。
5.3.2试样制作:采用镶嵌法制作试样。
5.3.3检查部位:在试样长边截面上检查评级。
5.3.4 评定方法:在布洛维硬度机上检测。
5.4 几何尺寸5.4.1 长度尺寸:用卷尺测量。
5.4.2 宽度尺寸:用0~200游标卡尺测量。
5.4.3 总厚度尺寸:用0~25千分尺测量。
5.4.4 钢背厚度尺寸:用涂覆层测厚仪检测。
5.5 形位公差5.5.1 毛边对称度用0~150游标卡尺测量。
5.5.2镰刀弯:将钢带侧放在大于1000的检验平板上,用塞规检查其弯曲的最大高度。
5.5.3 垂直度用角尺测量。
5.6 钢背/合金成份:采用能谱分析,钢背也可采取化学分析法。
二.铝锡合金双金属带5.钢背材料:(选用钢板必须符合GB699-1999的要求)1.1钢背牌号钢背材料可选用:08F、10F、15F、08、10、15优质碳素结构钢或St37-2G、SPCC、SPHC、St32-2。
1.2化学成分:必须满足C:0.08~0.12%;Si≤0.05%;Mn:0.25~0.60%;P:≤0.035%;S:≤0.035%。
1.3机械性能:1.3.1抗拉强度360~510MPa。
1.3.2屈服强度≥215 MPa。
1.3.3延伸率(长80)≥20%。
1.3.4钢背硬度:连杆瓦、主轴瓦、止推片为HB160~HB220。
翻边瓦为HB140~HB180。
卷制轴套为HB140~HB180。
同一批次的材料,钢背硬度差不得大于HB10。
6.合金层材料2.1合金层化学成分及表面硬度应符合表1之规定。
表1 合金层化学成分及表面硬度表:说明:翻边瓦和衬套的合金硬度应比标准要求低HB10~HB15。
同一批次的材料,合金硬度差不得大于HB5。
2.3合金层金相组织:2.3.1 轴瓦合金层中锡的分布形态为树状时,按表2评定,其中1~5级为合格,6级为不合格。
2.3.2轴瓦合金层中锡的分布形态为点、块状时,按表3评定,其中1~5级为合格,6级为不合格。
表3 合金层中锡的分布形态为点、块状评定表2.3.3轴瓦合金层中锡的分布形态为网状时,按表4评定,其中1~4级为合格,5级为不合格。
表4 合金层中锡的分布形态为网状评定表2.3.4轴瓦合金层中锡的分布形态为点及不规则的块状时,按表5评定,其中1~4级为合格,5级为不合格。
表5 合金层中锡的分布形态点及不规则的块状评定表2.3.5 合金与钢背结合情况,按表6评定,其中1~2级为合格,3级为不合格。
表6合金与钢背结合情况评定表注:①在每个视场中,单个氧化物和硫化物的最大边长不得大于50µm,其总面积不得大于8000µm2。
②不允许有硬质硼化物存在。
③合金层中单个最大的铅块面积不得大于8000µm2。
3. 钢带表面质量3.1钢背表面粗糙度Ra0.8。
3.2合金表面粗糙度Ra1.6。
3.3钢背表面颜色应均匀光洁,不得有斑点、锈蚀、擦伤、划伤等缺陷。
3.4合金层不允许有砂眼、气孔、气泡、夹杂物、裂缝及疏松等缺陷。
4.钢带几何尺寸和形位质量4.1 几何尺寸4.1.1 名义尺寸:按材料规格检验。
4.1.2 尺寸公差:总厚度公差+0.10 0,钢背厚度公差:0 -010.,宽度公差:±0.5,长度公差:+5 0;4.1.3形位公差4.1.3.1长边相对于短边的垂直度≤0.5。
4.1.3.2镰刀弯(即两长边的直线度)≤1.5/1000。
5. 检验方法5.1 金相组织5.1.1 取样大小:在钢带中截取试样,其长度10~30,宽4~8。
5.1.2 试样制作:采用镶嵌法制作试样。
5.1.3 检查部位:对铅的分布,在规定的工作面和结合层的整个磨面上进行检查评级。
5.1.4 试样浸蚀方法:用2~4%的硝酸酒精溶液浸蚀3~6秒钟。
5.1.5 显微组织评级方法:试样在100倍显微镜下选取5个最差的视场分别进行评级。
若5个视场中有3个视场为不合格级或有1个视场超出不合格级,则判为不合格。
5.2 结合强度5.2.1 金相显微法5.2.1.1取样大小:在钢带中截取试样,其长度10~30,宽4~8。
5.2.1.2试样制作:采用镶嵌法制作试样。