甲醇-水精馏塔化工原理课程设计
化工原理课程设计,甲醇和水的分离精馏塔的设计
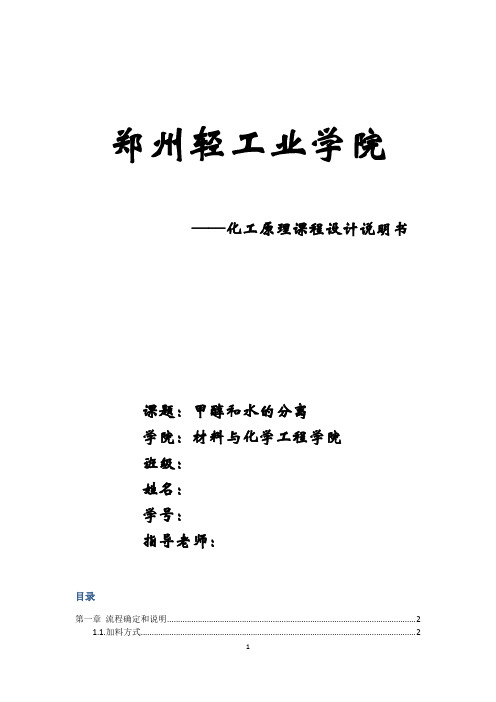
郑州轻工业学院——化工原理课程设计说明书课题:甲醇和水的分离学院:材料与化学工程学院班级:姓名:学号:指导老师:目录第一章流程确定和说明 (2)1.1.加料方式 (2)1.2.进料状况 (2)1.3.塔型的选择 (2)1.4.塔顶的冷凝方式 (2)1.5.回流方式 (3)1.6.加热方式 (3)第二章板式精馏塔的工艺计算 (3)2.1物料衡算 (3)2.3 塔板数的确定及实际塔板数的求取 (5)2.3.1理论板数的计算 (5)2.3.2求塔的气液相负荷 (5)2.3.3温度组成图与液体平均粘度的计算 (6)2.3.4 实际板数 (7)2.3.5试差法求塔顶、塔底、进料板温度 (7)第三章精馏塔的工艺条件及物性参数的计算 (9)3.1 平均分子量的确定 (9)3.2平均密度的确定 (10)3.3. 液体平均比表面积张力的计算 (11)第四章精馏塔的工艺尺寸计算 (12)4.1气液相体积流率 (12)4.1.1 精馏段气液相体积流率: (12)4.1.2提馏段的气液相体积流率: (13)第五章塔板主要工艺尺寸的计算 (14)5.1 溢流装置的计算 (14)5.1.1 堰长 (14)5.1.2溢流堰高度: (15)5.1.3弓形降液管宽度 (15)5.1.4 降液管底隙高度 (16)5.1.5 塔板位置及浮阀数目与排列 (16)第六章板式塔得结构与附属设备 (24)6.1附件的计算 (24)6.1.1接管 (24)6.1.2 冷凝器 (27)6.1.3再沸器 (28)第七章参考书录 (28)第八章设计心得体会 (29)第一章流程确定和说明1.1.加料方式加料方式有两种:高位槽加料和泵直接加料。
采用高位槽加料,通过控制液位高度,可以得到稳定的流速和流量,通过重力加料,可以节省一笔动力费用,但由于多了高位槽,建设费用相应增加;采用泵加料,受泵的影响,流量不太稳定,流速不太稳定,流速不太稳定,从而影响了传质效率,但结构简单,安装方便。
甲醇水精馏塔化工原理课程设计

甲醇水精馏塔化工原理课程设计本文将介绍一门关于“甲醇水精馏塔化工原理课程设计”的学习内容,该课程设计将涉及到许多重要的化工原理和技术应用方面。
本文将主要从以下几个方面进行介绍:一、课程设计背景甲醇和水是常见的有机溶剂和溶媒,广泛应用于化学工业、食品工业、医药工业等诸多领域。
但甲醇和水的相互溶解度较低,难以用简单的混合物方法来进行分离。
因此,需要采用精馏技术对甲醇水混合物进行分离与提纯,而甲醇水精馏塔就是典型的精馏设备。
本课程设计就是为了让学生深入了解甲醇水精馏塔的化工原理和工艺操作,并掌握甲醇水分离的关键技术。
二、课程设计内容本课程设计的主要内容包括理论学习和实验操作两部分。
具体来说,理论学习将介绍甲醇水混合物的化学性质、相图、相平衡、相接触、塔、节流和板面效应等理论基础知识,并通过相应的实验操作来加深学生的理解。
实验操作将包括设备组装、实验前检查、实验过程控制和实验后数据处理等环节,以培养学生的实验技能和实际操作能力。
三、课程设计任务本课程设计的主要任务是让学生了解甲醇水精馏塔的化工原理和工艺操作,在此基础上能够独立设计和操作精馏设备,实现甲醇和水混合物的高效分离和提纯。
具体而言,学生需要完成以下任务:1. 研究甲醇水混合物的相图,掌握不同温度下甲醇和水的相互溶解度和相变情况;2. 根据甲醇水混合物的相平衡数据,设计合适的塔板数和塔壳直径,以实现甲醇和水的有效分离;3. 设计甲醇水精馏塔的流程图和操作流程,确保操作步骤合理且安全;4. 根据实验数据,计算塔效和塔效影响因素,并分析其影响和解决方法;5. 总结课程设计过程中遇到的问题和方法,撰写相关实验报告和课程设计论文。
四、课程设计意义本课程设计不仅能够深入学习甲醇和水的化学性质和相互关系,也可以了解甲醇水精馏塔的精细操作技术和机理原理,从而加深对化工实践的理解和认识。
同时,学生还可以在实验操作中培养实际能力和团队配合能力,为今后从事化工实践和科研工作奠定坚实基础。
甲醇-水精馏课程设计—化工原理课程设计

甲醇-水分离过程板式精馏塔的设计1.设计方案的确定本设计任务为分离甲醇和水混合物。
对于二元混合物的分离,应采用连续精馏流程。
设计中采用泡点进料,将原料液通过预热器加热至泡点后送入精馏塔内。
塔顶上升蒸气采用全凝器冷凝,冷凝液在泡点下一部分回流至塔内,其余部分经产品冷凝冷却后送至储罐。
该物系属易分离物系,最小回流比较小,故操作回流比取最小回流比的1.8倍。
塔釜采用间接蒸汽加热①。
2.精馏塔的物料衡算2.1.原料液及塔顶、塔顶产品的摩尔分率甲醇的摩尔质量M A=32.04kg/kmol水的摩尔质量M B=18.02 kg/kmolx F=0.46/32.040.324 0.46/32.040.54/18.02=+x D=0.95/32.040.914 0.95/32.040.05/18.02=+x W=0.03/32.040.0171 0.03/32.040.97/18.02=+2.2.原料液及塔顶、塔底产品的平均摩尔质量M F=0.324*32.04(10.324)*18.0222.56+-=kg/kmol M D=0.914*32.04(10.914)*18.0230.83-=kg/kmol M W=0.0171*32.04(10.0171)*18.0218.26+-=kg/kmol 2.3.物料衡算原料处理量F=30000*1000184.724*300*22.56=kmol/h总物料衡算184.7=D+W甲醇物料衡算184.7*0.324=0.914D+0.0171W 联立解得D=63.21 kmol/hW=121.49 kmol/h3.塔板数的确定3.1.理论塔板层数N T的求取3.1.1.由手册查的甲醇-水物系的气液平衡数据温度饱和蒸汽压(甲醇)kPa 饱和蒸汽压(水)kPa 64.5 101.3 25.00370 125.1458 31.15775 150.8157 38.54480 180.667 47.34385 215.19957.80890 254.946970.09595 300.48384.513100 352.4169101.3由上数据可绘出x-y图和t-x(y)图。
甲醇-水精馏化工原理课程设计

《化工原理课程设计》报告10000kg/h 甲醇~水精馏装置设计一、概述 (3)1.1 设计依据 (3)1.2 技术来源 (3)1.3 设计任务及要求 (3)二、计算过程 (4)1 设计方案及设计工艺的确定 (4)1.1 设计方案 (4)1.2.设计工艺的确定 (4)1.3、工艺流程简介 (4)2. 塔型选择 (5)3. 操作条件的确定 (5)3.1 操作压力 (5)3.2 进料状态 (5)3.3加热方式的确定 (6)3.4 热能利用 (6)4. 有关的工艺计算 (6)4.1精馏塔的物料衡算 (9)4.1.1 原料液及塔顶、塔底产品的摩尔分率 (9)4.1.2 原料液及塔顶、塔底产品的平均摩尔质量 (10)4.1.3物料衡算 (10)4.2 塔板数的确定 (10)4.2.1 理论板层数NT的求取 (10)4.2.3 热量衡算 (12)4.3 精馏塔的工艺条件及有关物性数据的计算 (14)4.3.1 操作压力的计算 (14)4.3.2 操作温度的计算 (14)4.3.3 平均摩尔质量的计算 (15)4.3.4 平均密度的计算 (15)4.3.5 液相平均表面张力的计算 (16)4.3.6 液体平均粘度的计算 (17)4.4 精馏塔的塔底工艺尺寸计算 (18)4.4.1塔径的计算 (18)4.4.2 精馏塔有效高度的计 (19)4.5 塔板主要工艺尺寸的计算 (19)4.5.1溢流装置的计算 (19)4.5.2 塔板布置 (21)4.6 筛板的流体力学验算 (24)4.6.1 塔板压降 (24)4.6.2 液面落差 (25)4.6.3 液沫夹带 (26)4.6.4 漏液 (26)4.6.5 液泛 (27)4.7 塔板负荷性能图 (27)4.7.1、液漏线 (27)4.7.2、液沫夹带线 (28)4.7.3、液相负荷下限线 (29)4.7.4、液相负荷上限线 (29)4.7.5、液泛线 (29)5.热量衡算 (32)5.1塔顶换热器的热量衡算 (33)5.2塔底的热量计算 (33)5.3、热泵的选型 (36)5.4、塔底料液和热蒸气预热进料液 (36)5.5、水蒸汽加热进料液 (37)三、辅助设备的计算及选型 (38)(一)、管径的选择 (38)1、加料管的管径 (38)2、塔顶蒸汽管的管径 (38)3、回流管管径 (38)4、料液排出管径 (39)(二)、泵的选型 (39)1、原料液进入精馏塔时的泵的选型 (39)2、塔顶液体回流所用泵的型号 (39)(三)、储罐选择 (40)1、原料储槽 (40)2、塔底产品储槽 (40)3、塔顶产品储槽 (40)四、费用的计算 (41)(一)设备费用的计算 (41)1、换热器费用的计算 (41)2、精馏塔的费用计算 (42)泵的费用 (42)储槽费用 (42)输送管道费用 (43)分液槽费用 (44)(二)操作费用的计算 (44)1、热蒸汽的费用 (44)2、冷却水的费用 (44)3、泵所用的电费 (44)4、总费用 (44)参考文献 (45)主要符号说明 (46)对本设计的评述 (49)一、概述塔设备是最常采用的精馏装置,无论是填料塔还是板式塔都在化工生产过程中得到了广泛的应用,在此我们作板式塔的设计以熟悉单元操作设备的设计流程和应注意的事项是非常必要的。
化工原理课程设计甲醇和水的分离精馏塔的设计

郑州轻工业学院——化工原理课程设计说明书课题:甲醇和水的分离学院:材料与化学工程学院班级:姓名:学号:指导老师:目录第一章流程确定和说明 (2)1.1.加料方式 (2)1.2.进料状况 (2)1.3.塔型的选择 (2)1.4.塔顶的冷凝方式 (2)1.5.回流方式 (3)1.6.加热方式 (3)第二章板式精馏塔的工艺计算 (3)2.1物料衡算 (3)2.3 塔板数的确定及实际塔板数的求取 (5)2.3.1理论板数的计算 (5)2.3.2求塔的气液相负荷 (5)2.3.3温度组成图与液体平均粘度的计算 (6)2.3.4 实际板数 (7)2.3.5试差法求塔顶、塔底、进料板温度 (7)第三章精馏塔的工艺条件及物性参数的计算 (9)3.1 平均分子量的确定 (9)3.2平均密度的确定 (10)3.3. 液体平均比表面积张力的计算 (11)第四章精馏塔的工艺尺寸计算 (12)4.1气液相体积流率 (12)4.1.1 精馏段气液相体积流率: (12)4.1.2提馏段的气液相体积流率: (13)第五章塔板主要工艺尺寸的计算 (14)5.1 溢流装置的计算 (14)5.1.1 堰长 (14)5.1.2溢流堰高度: (15)5.1.3弓形降液管宽度 (15)5.1.4 降液管底隙高度 (16)5.1.5 塔板位置及浮阀数目与排列 (16)第六章板式塔得结构与附属设备 (24)6.1附件的计算 (24)6.1.1接管 (24)6.1.2 冷凝器 (27)6.1.3再沸器 (28)第七章参考书录 (28)第八章设计心得体会 (29)第一章流程确定和说明1.1.加料方式加料方式有两种:高位槽加料和泵直接加料。
采用高位槽加料,通过控制液位高度,可以得到稳定的流速和流量,通过重力加料,可以节省一笔动力费用,但由于多了高位槽,建设费用相应增加;采用泵加料,受泵的影响,流量不太稳定,流速不太稳定,流速不太稳定,从而影响了传质效率,但结构简单,安装方便。
甲醇—水精馏分离板式塔设计

3.3.5 提馏段平均摩尔质量
MVm 25.67 18.08 2 21.88 Kg mol
M
Lm
20.1118.01
2 19.06 Kg
mol
4.精馏塔的塔体工艺尺寸
4.1 精馏段塔径的计算
由上面可知精馏段 L 45 Kmol h V 68 Kmol h
精馏段的气、液相体积流率为
Vs VMVm 3600 Vm 68 28.73 3600 1.01 1.481 m3 s
根据回收率: xD D xF F 99%
则有:
D 23 Kmol h
由总物料衡算: F D W
以及:
xF F xD D W xW
容易得出: W 94 Kmol h , xW 0.0012
2.塔板数的确定
2.1 逐板计算法求取理论板层数 NT
甲醇-水汽液平衡数据:
x
y
x
y
3600 Af
HT Lh
3600 0.0448 0.40 3600 0.0084
21.31s5s 其中 HT 即为板间距
0.40m, Lh 即为每小时的体积流量
验证结果为降液管设计符合要求。 5.1.1.4 降液管底隙高度 ho
10
ho Lh 3600 lw uo 取 uo 0.07 m s ho 0.0084 3600 3600 0.6 0.07 0.020024 m0.02m
故精馏塔有效高度为 Z Z精 Z提 0.8 10.4m
5.塔板主要工艺尺寸
5.1 精馏段塔板工艺尺寸计算
5.1.1 溢流装置计算
9
因塔径
,
所以可选取单溢流弓形降液管,采用凹形受液盘。( 此种溢流方式液体流径较长, 塔板效率较高,塔板结构简单,加工方便,在直径小于 2.2m 的塔中被广泛使用。) 各项计算如下:
化工原理甲醇-水板式精馏塔设计

(1)生产能力:3万吨/年,年开工300天
(2) 进料组成:甲醇含量65%(质量分数)
(3) 采用间接蒸汽加热并且加热蒸汽压力:0.3MPa
(4) 进料温度:采用泡点进料
(5) 塔顶馏出液甲醇含量99%(质量分数)
(6) 塔底轻组分的浓度≤1%(本设计取0.01)
(7) 塔顶压强常压
11.171
49
11.745
50
12.344
51
12.97
52
13.623
53
14.303
54
15.012
55
15.752
56
16.522
57
17.324
58
18.159
59
19.028
60
19.932
61
20.873
62
21.851
63
22.868
64
23.925
65
25.022
66
26.163
67
即:
同理可以求得
如此重复,直至
此后,改用提馏段操作线方程,
即: ,求出
同理可得:
如此重复计算,直至计算到
计算结果见下表:
逐板计算法的理论塔板数
y y的值
x x的值
y1
0.982
Xd
0.982
y2
0.960182532
x2
0.935523207y3 Nhomakorabea0.922159507
x3
0.865110198
y4
0.864902729
式中:D——塔径,m
——气体体积流量,
化工原理课程设计--甲醇-水连续精馏塔的设计

化工原理课程设计题目:甲醇-水连续精馏塔的设计姓名学号年级 2011级专业化学工程与工艺系(院)化学化工学院指导教师2013年 12月目录一、概述 (4)1.精馏操作对塔设备的要求 (4)2.板式塔类型 (4)3.精馏塔的设计步骤 (5)二、精馏塔的物料衡算 (5)三、塔板数的确定 (6)四、精馏塔的工艺条件及有关物性数据数据的计算 (6)五、精馏塔的塔体工艺尺寸计算 (10)六、塔板主要工艺尺寸的计算 (12)七、筛板的流体力学验算 (15)八、塔板负荷性能图 (18)九、筛板塔设计计算结果 (23)十、辅助设备的计算及选型 (24)⒈原料贮罐 (24)2.产品贮罐 (25)3.原料预热器 (25)4.塔顶全凝器 (26)5.塔底再沸器 (26)6.产品冷凝器 (27)7.精馏塔 (27)8.管径的设计 (28)9.泵的计算及选型 (29)10.参考文献 (29)11.设计评述 (29)12.操作流程图 (30)13.符号说明 (31)精馏塔设计任务书(一)设计题目甲醇-水连续精馏塔的设计(二)计任务及操作条件1) 进精馏塔的料液含甲醇30%(质量分数,下同),其余为水;2) 产品的甲醇含量不得低于95%;3) 残液中甲醇含量不得高于0.6%;4) 每年实际生产时间:7200小时/年,处理量:54000吨/年;5) 操作条件a) 塔顶压力:常压 b) 进料热状态:饱和液体进料 (或自选)c) 回流比: R=2.0Rmin d) 加热方式:直接蒸汽 e) 单板压降:≤0.7kPa (三)板类型筛板塔(四)厂址临沂地区(五)设计内容1、设计说明书的内容1) 精馏塔的物料衡算;2) 塔板数的确定;3) 精馏塔的工艺条件及有关物性数据的计算;4) 精馏塔的塔体工艺尺寸计算;5) 塔板主要工艺尺寸的计算;6) 塔板的流体力学验算;7) 塔板负荷性能图;8) 精馏塔接管尺寸计算;9)设计结果汇总10) 对设计过程的评述和有关问题的讨论。
甲醇-水精馏塔化工原理课程设计报告

南京工业大学《化工原理》课程设计设计题目 常压甲醇-水筛板精馏塔设计学生姓名 陈献富 班级、学号 化工070313指导教师姓名 刘晓勤、王晓东课程设计时间2010年6月14日-2010年6月25日课程设计成绩指导教师签字化学化工学院课程名称化工原理课程设计设计题目常压甲醇-水筛板精馏塔设计学生姓名周佳佳专业化学工程与工艺班级学号 1001090605设计日期 2010 年 6 月 14 日至 2009 年 6 月 25日设计条件及任务:设计体系:甲醇-水体系设计条件:进料量:F= 200 kmol/h进料浓度:Z F= 0.35 (摩尔量分数)进料状态:q= 1.08操作条件:塔顶压强为4kPa(表压),单板压降不大于0.7kPa。
塔顶冷凝水采用深井水,温度t=12℃;塔釜加热方式:间接蒸汽加热,采用3kgf/cm2(表压)水蒸汽全塔效率:E T = 52%分离要求:X D= 0.995(质量分数);X W= 0.002(质量分数);回流比:R/R min =1.6指导教师刘晓勤、王晓东2010年6月11日目录绪论 (1)1.精馏简介 (1)2.塔设备简介 (1)3.体系介绍 (2)4.设计要求 (2)第一节概述 (3)1.1精馏操求作对塔设备的要求 (3)1.2板式塔类型 (3)1.2.1筛板塔 (3)1.2.2浮阀塔 (3)1.2.3泡罩塔 (3)1.3设计单元操作方案简介 (4)1.4精馏塔的设计简介 (4)1.4.1 筛板塔设计须知 (4)1.4.2 筛板塔的设计程序 (4)第二节设计方案的初步确定 (5)2.1操作条件的确定 (5)2.1.1操作压力 (5)2.1.2进料状态 (5)2.1.3加热方式 (5)2.1.4冷却剂与出口温度 (5)2.1.5回流比 (6)2.1.6热能的利用 (6)2.2确定设计方案的原则 (6)2.3操作流程简图 (7)第三节板式精馏塔的工艺参数计算 (8)3.1 物料衡算与操作线方程 (8)3.2 理论塔板数的计算与实际板数的确定 (10)3.2.1理论板数的计算 (10)3.2.1实际板数的确定 (11)3.3操作压强的计算 (11)3.4操作温度的计算 (11)3.5塔内物料平均分子量、张力、流量及密度的计算 (12)3.5.1密度及流量 (12)3.5.2液相表面张力的确定: (13)3.5.3液体平均粘度计算 (13)第四节板式塔主要尺寸的设计计算 (14)4.1塔的有效高度和板间距的初选 (14)4.1.1塔有效高度 (14)4.2 塔径 (14)第五节板式塔的结构 (16)5.1 塔的总体结构 (16)5.2 总塔高度 (16)5.2.1塔顶空间H D (16)5.2.2塔底空间 (16)5.2.3整体塔高 (16)5.2.4人孔数 (16)5.3 塔板结构 (16)5.3.1溢流装置 (16)5.3.2弓形降液管宽度W d和面积A f (17)h (18)5.3.3降液管底隙高度5.3.4塔板布置及筛孔数目与排列 (18)5.4.筛板的力学检验 (19)5.4.1塔板压降 (19)5.4.2液面落差 (20)5.4.3液沫夹带 (20)5.4.4漏液 (21)5.4.5液泛 (21)5.5.塔板负荷性能图 (21)5.5.1漏液线 (21)5.5.2液沫夹带线 (22)5.5.3液相负荷下限线 (23)5.5.4液相负荷上限线 (23)5.5.5液泛线 (23)5.5.6操作弹性 (24)第六节设计结果汇总 (26)第七节精馏装置的附属设备 (28)7.1 管壳式换热器的设计与选型 (28)7.1.1塔顶冷凝器(列管式换热器) (28)7.1.2进料预热器 (31)7.2 再沸器 (32)7.3 管件 (33)7.3.1塔釜残液出料管 (33)7.3.2塔顶回流液管 (33)7.3.4塔釜再沸器蒸汽进口管 (33)7.3.5塔顶蒸汽进冷凝器进口管 (34)7.3.6塔顶冷凝水管 (34)7.4冷凝水泵的选择 (34)7.5除沫器 (35)7.6裙座 (35)附表 (36)1、常压下甲醇-水气液平衡组成与温度关系 (36)2、理论塔板数计算(MATLAB程序): (36)3、进料、塔顶及塔釜温度—组成的插值计算(MATLAB程序) (37)4、史密斯关联图 (38)参考文献及设计手册 (38)设计感想 (39)感谢 (40)绪论1.精馏简介蒸馏是分离液体混合物的一种方法,是一种属于传质分离的单元操作。
甲醇水筛板精馏塔课程设计报告
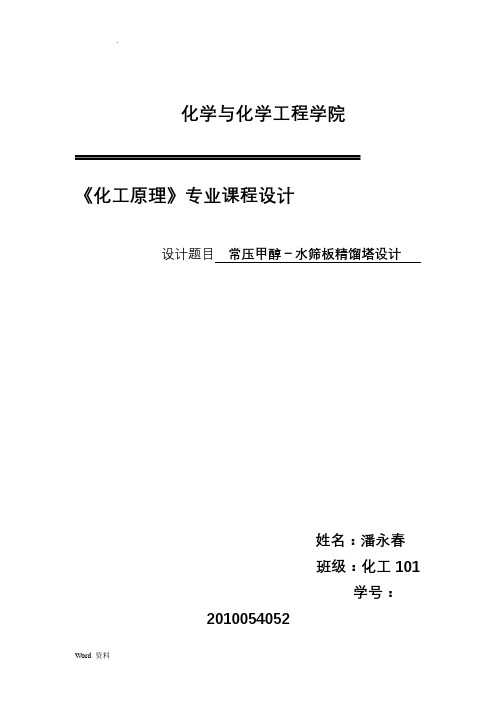
化学与化学工程学院《化工原理》专业课程设计设计题目常压甲醇-水筛板精馏塔设计姓名:潘永春班级:化工101学号:2010054052指导教师:朱宪荣课程设计时间2013、6、8——2013、6、20化工原理课程设计任务书专业:化学与化学工程学院:化工101 姓名:潘永春学号20100054052 指导教师朱宪荣设计日期:2013 年6月8日至2013年6月20日一、设计题目:甲醇-水精馏塔的设计二、设计任务及操作条件:1、设计任务生产能力(进料)413.34Kmol/hr操作周期8000小时/年进料组成甲醇0.4634 水0.5366(质量分率下同)进料密度233.9Kg/m3 平均分子量22.65塔顶产品组成>99%塔底产品组成<0.04%2、操作条件操作压力 1.45bar (表压)进料热状态汽液混合物液相分率98%冷却水20℃直接蒸汽加热低压水蒸气塔顶为全凝器,中间汽液混合物进料,连续精馏。
3、设备形式筛板式或浮阀塔4、厂址齐齐哈尔地区三、图纸要求1、计算说明书(含草稿)2、精馏塔装配图(1号图,含草稿)一.前言 51.精馏与塔设备简介 52.体系介绍 53.筛板塔的特点 64.设计要求: 6二、设计说明书7三.设计计算书8 1.设计参数的确定81.1进料热状态81.2加热方式81.3回流比(R)的选择81.4 塔顶冷凝水的选择82.流程简介及流程图82.1流程简介83.理论塔板数的计算与实际板数的确定93.1理论板数计算93.1.1物料衡算93.1.2 q线方程93.1.3平衡线方程103.1.4 Rmin和R的确定103.1.5精馏段操作线方程的确定103.1.6精馏段和提馏段气液流量的确定 103.1.7提馏段操作线方程的确定103.1.8逐板计算103.1.9图解法求解理论板数如下图: 123.2实际板层数的确定124精馏塔工艺条件计算124.1操作压强的选择 124.2操作温度的计算 134.3塔内物料平均分子量、张力、流量及密度的计算 134.3.1 密度及流量 134.3.2液相表面张力的确定:144.3.3 液体平均粘度计算154.4塔径的确定154.4.1精馏段154.4.2提馏段174.5塔有效高度174.6整体塔高175.塔板主要工艺参数确定185.1溢流装置185.1.1堰长lw 185.1.2出口堰高hw 185.1.3弓形降液管宽度Wd和面积Af 185.1.4降液管底隙高度h0195.2塔板布置及筛孔数目与排列195.2.1塔板的分块195.2.2边缘区宽度确定 195.2.3开孔区面积Aa计算195.2.4筛孔计算及其排列206.筛板的力学检验206.1塔板压降206.1.1干板阻力h c计算 206.1.2气体通过液层的阻力Hl计算 216.1.4气体通过每层塔板的液柱高h p21 6.2 筛板塔液面落差可忽略216.3液沫夹带216.4漏液226.5液泛227.塔板负荷性能图227.1漏液线227.2液沫夹带线237.3液相负荷下限线 247.4液相负荷上限线 247.5液泛线247.6操作弹性258. 辅助设备及零件设计268.1塔顶冷凝器(列管式换热器)268.1.1方案Ⅰ:垂直管 268.1.2方案Ⅱ:水平管 298.2各种管尺寸的确定308.2.1进料管308.2.2釜残液出料管308.2.3回流液管318.2.4再沸器蒸汽进口管318.2.5 塔顶蒸汽进冷凝器出口管318.2.6冷凝水管328.3冷凝水泵329.设计结果汇总3310. 参考文献及设计手册35四.设计感想35一.前言1.精馏与塔设备简介蒸馏是分离液体混合物的一种方法,是传质过程中最重要的单元操作之一,蒸馏的理论依据是利用溶液中各组分蒸汽压的差异,即各组分在相同的压力、温度下,其探发性能不同(或沸点不同)来实现分离目的。
化工原理甲醇—水精馏塔设计说明

沈阳化工大学化工原理课程设计说明书专业:制药工程班级:制药1102学生姓名:黄奎兴学号:11220223指导老师:王国胜设计时间:2014.5.20----2014620成绩:____________化工原理课程设计任务书设计题目:分离甲醇-水混合液的填料精馏塔二原始数据及条件生产能力:年生产量甲醇1万吨(年开工300天)原料:甲醇含量为30% (质量百分数,下同)的常温液体分离要求:塔顶甲醇含量不低于95%,塔底甲醇含量不高于0.3%。
建厂地区:沈阳三设计要求(一)•一份精馏塔设计说明书,主要内容要求:(1)•前言(2).流程确定和说明(3)•生产条件确定和说明(4)•精馏塔设计计算(5)•主要附属设备及附件选型计算(6)•设计结果列表专业•专注(7).设计结果的自我总结与评价(8).注明参考和试用的设计资料(9).结束语(二)•绘制一份带控制点工艺流程图。
(三)•制一份精馏塔设备条件图四.设计日期:2013年5月20日至6月20日、八、,刖言精馏塔分为板式塔和填料塔两大类。
填料塔又分为散堆填料和规整填料两种。
板式塔虽然结构较简单,适应性强,宜于放大,在空分设备中被广泛采用。
但是,随着气液传热、传质技术的发展,对高效规整填料的研究,一些效率高、压降小、持液量小的规整填料的开发,在近十多年内,有逐步替代筛板塔的趋势。
实际生产中,在精馏柱及精馏塔中精馏时,上述部分气化和部分冷凝是同时进行的。
对理想液态混合物精馏时,最后得到的馏液(气相冷却而成)是沸点低的B 物质,而残液是沸点高的A 物质,精馏是多次简单蒸馏的组合o精馏塔底部是加热区,温度最高;塔顶温度最低。
精馏结果,塔顶冷凝收集的是纯低沸点组分,纯高沸点组分则留在塔底。
精馏塔的优点:归纳起来,规整填料塔与板式塔相比,有以下优点:1)压降非常小。
气相在填料中的液相膜表面进行对流传热、传质,不存在塔板上清液层及筛孔的阻力。
在正常情况下,规整填料的阻力只有相应筛板塔阻力的1/5 〜1/6 ; 2)热、质交换充分,分离效率高,使产品的提取率提高;3)操作弹性大,不产生液泛或漏液,所以负荷调节范围大,适应性强。
化工原理课程设计甲醇和水筛板精馏塔分离

设计计算<一>设计方案的确定本设计任务为分离甲醇-水混合物。
对于二元混合物的分离,应采用连续精馏流程。
设计中采用泡点进料,将原料液通过预加热器至泡点后送入精馏塔内。
塔顶上升蒸汽采用全凝器冷凝,冷凝液在泡点下一部分回流至塔内,其余部分经产品冷却器冷却后送至储罐。
该物系属易分离系,最小回流比,故操作回流比取最小回流比的2倍。
塔釜采用间接蒸汽加热,塔底产品经冷却后送至储罐。
<二>精馏塔的物料衡算1、原料液及塔顶、塔底产品的摩尔分率甲醇的摩尔质量 M 甲醇=32.04kg/ kmol 水的摩尔质量 M 水=18.02kg/kmolX F =0.432.04=0.2730.40.6+32.0418.02X D =0.999732.04=0.99470.99970.0003+32.0418.02X W =0.00532.04=0.0028180.0050.995+32.0418.022、原料液及塔顶、塔底产品的平均摩尔质量M F =0.273×32.04+(1—0.273)×18.02=21.85kg/kmol M D =0.9947×32.04+(1—0.9947)×18.02=31.96kg/kmol M W =0.002818×32.04+(1—0.002818)×18.02=18.06kg/kmol 3、物料衡算 原料处理量:F=210000000=115.573302421.85⨯⨯⨯kmol/h总物料衡算:F=D+W 115.57=D+W甲醇物料衡算:FX F =DX D +WX W 115.57×0.273=D×0.9947+W×0.002818 联立解得 D=31.48kmol/h w=84.09kmol/h <三>塔板数的确定 1、理论板数的求取 ①由 y=1+(-1)xxαα及甲醇—水在不同温度下的汽—液平衡组成温度 液相 气相 a 温度 液相 气相 a 92.9 0.0531 0.2834 7.05 81.6 0.2083 0.6273 6.4 90.3 0.0767 0.4001 8.03 80.2 0.2319 0.6485 6.11 88.9 0.0926 0.4353 7.55 78 0.2818 0.6775 5.35 86.6 0.1257 0.4831 6.5 77.8 0.2909 0.6801 5.18 85 0.1315 0.5455 7.93 76.7 0.3333 0.6918 4.49 83.2 0.1674 0.5586 6.29 76.2 0.3513 0.7347 5.11 82.3 0.1818 0.5775 6.15 73.8 0.462 0.7756 4.02 72.7 0.5292 0.7971 3.49 68 0.7701 0.8962 2.57 71.3 0.5937 0.8183 3.08 66.9 0.8741 0.9194 1.6470 0.6849 0.8492 2.59am=1919......3.2.1a a a a =4.83 得到相平衡方程 y=4.83=1+(-1)x 1+3.83x xxαα因为泡点进料,所以q=1 且Xq=XF=0.273 且q 点过相平衡线 则y q=4.83=0.6451+3.83qqx x =0.645Rmin=D q q qx y y x --=0.94取操作回流比 min 2.0 1.88R R ==2、求精馏塔的气液相负荷==RD L 1.88×31.48=59.18kmol/h V=(R+1)D =2.88×31.48=90.66kmol/h =L+F=59.18+115.57=174.75kmol/h=V=90.66kmol/h 3、求操作线方程精馏段操作线方程 1n y +=1RR ++1D x R +=0.6528Xn+0.3454提馏段操作线方程 1W n n Wx Ly x V V+=-=1.927Xn-2.614×10-35、逐板计算法求理论板数因为塔顶为全凝器 10.9947D y X == 通过相平衡方程求 X 1=11=0.97494.83-3.83y y再通过精馏段操作线方程 y 2=0.6528X 1+0.3454=0.9818 ,如此反复得当X 6<Xq后,改用相平衡方程与提馏段操作方程yn+1=1.927Xn-12.614×10-3计算.如此反y 12=7.88×10-3x 12=1.64×10-3<0.002818可得到进料板位置 N F=6总理论板数N T =12<包括再沸器> 2、实际板层数的求取精馏段实际板层数:N 精=50.6=8.3≈9 提馏段实际板层数:N 提=60.6≈10(不包括再沸器)<四>精馏塔工艺条件及有关物性数据的计算 1、 操作压力计算塔顶操作压力 P D =101.3+4=105.3KPa 每层塔板压力降 P=0.7KPa进料板压力 P F =105.3+0.7×9=111.6KPa 塔底压力 Pw=P F +0.7×10=118.6KPa精馏段平均压力 Pm=105.3+111.6=108.452KPa提馏段平均压力 P m ′=111.6+120=115.12KPa2、 操作温度计算(内插法得)根据甲醇-水的气-液平衡组成表,再通过内插法得: 塔顶温度 t D =64.79℃ 进料板温度 t F =78.3℃ 塔釜温度 t w =99.6℃精馏段平均温度 t m =+64.79+78.3==71.5422D F t t ℃ 提馏段平均温度 t m ′=+78.3+99.6==88.9522F W t t ℃3、 平均摩尔质量的计算塔顶平均摩尔质量计算由X D =y 1=0.9947 通过相平衡方程求得 X 1=0.9749M VDM =y 1M 甲+(1-y 1)M 水=0.9947×32.04+(1-0.9947) ×18.02=31.97Kg/Kmol M LOM =X 1M 甲+(1-X 1)M 水=0.9749×32.04+(1-0.9749) ×18.02=31.69 Kg/Kmol 进料板平均摩尔质量计算通过逐板计算得进料板y F =0.5603,再通过相平衡方程得X F =0.2087 M VFM = y F M 甲+(1-y F )M 水=0.5603×32.04+(1-0.5603)×18.02=25.87Kg/Kmol M LFM =X F M 甲+(1-X F )M 水=0.2087×32.04+(1-0.2087×18.02)=20.95Kg/Kmol塔釜平均摩尔质量的计算由X w =0.002818 查平衡曲线得 y w =0.01346M VWM =y w M 甲+(1-y w )M 水=0.01346×32.04+(1-0.01346)×18.02=18.21Kg/Kmol M LWM =X W X 甲+(1-X W )M 水=0.002818×32.04+(1-0.002818)×18.02=18.06Kg/Kmol 精馏段平均摩尔质量M VM =VDM VFM (M +M )31.97+25.87==28.92/22Kg KmolM LM =LDM LFM (M +M )31.69+20.95==26.32/22Kg Kmol提馏段平均摩尔质量M VM ′=VDM VFM (M +M )25.87+18.21==22.04/22Kg KmolM LM ′=LFM LWM (M +M )20.95+18.06==19.50/22Kg Kmol4、平均密度计算⑴气相平均密度计算由理想气体状态方程计算 即 精馏段VM =m vm P M 108.4528.92==1.0948.314(71.54+273.15)m RT ⨯⨯Kg/m提馏段vm ′=m vm P M 115.122.04==0.84278.314(88.95+273.15)m RT ''⨯'⨯ ⑵液相平均密度计算 液相平均密度按下式计算 即i 1a =m i∑ρL ρ塔顶液相平均密度的计算 由t D =64.79℃ 查手册得 甲=747.168Kg/m水=980.613Kg/mLPM =11==747.70.9970.003++746.168980.613甲水D wωωρρKg/m进料板液相平均密度计算 由t F =78.3℃ 查手册得 甲=735.53 Kg/m 水=972.82 Kg/m进料板液相的质量分率F x 0.208732.04===0.3192x +(1-x )M 0.208732.04+0.791318.02F F M aA M ⨯⨯⨯甲甲水LFM =11==881.91-0.31920.6808++735.53972.82甲水A A ααρρKg/m提馏段液相平均密度计算 由t w =99.6℃ 查手册得 甲=716.36Kg/m 水=958.176Kg/mLWM =11==957.061-0.0050.995++716.36958.676甲水w w ωωρρKg/m精馏段液相平均密度为LM =747.7881.91814.822LDM LFM ρ+ρ+==Kg/m 提馏段液相平均密度LM′=881.91+957.06919.4822LFM LWM ρ+ρ==Kg/m 5、液体平均表面张力的计算 液相平均表面张力依下式计算 即LM =X ii塔顶液相平均表面张力的计算 由t D =64.79℃查手册得甲=18.31mN/m水=65.29Mn/mLOM =X D甲+(1-X D )水=0.9947×18.31+0.0053×65.29=18.56mN/m进料板液相平均表面张力的计算 由t F =78.3℃ 查手册得 甲=17.0647mN/m水=62.889mN/mLFM =X F甲+(1-X F )水=0.2087×17.0647+0.7913×62.889=53.32mN/m塔釜液相平均表面张力的计算 由tw=99.6℃ 查手册得 甲=14.93mN/m 水=58.9mN/mLWM =X w甲+(1-X w )水=0.002818×14.93+(1-0.2087)×62.889=53.32mN/m精馏段液相平均表面张力为LM =18.5653.3235.9422L LFM OM δ+δ+==mN/m提馏段液相平均表面张力为L M′=53.3258.7856.0522LFM LW M δ+δ+==mN/m 6、液体平均粘度计算 液相平均粘度以下式计算,即LM=X i i塔顶液相平均粘度计算 由t D =64.79℃查手册得甲=0.3289mpa.s水=0.4479mpa.sLDM =X D甲+(1-X D )水=0.9947g (0.3289)+(1-0.9947)(0.4479)= —0.4825LDM =0.3292mpa.s进料板液相平均粘度计算 由t F =78.3℃查手册得甲=0.28193mpa.s水=0.37084mpa.sLFM =X F甲+(1-X F )水=0.2087(0.28193)+(1-0.2087)(0.37084)=—0.4557LFM =0.35mpa.s由t w =99.6℃ 查手册得甲=0.226mpa.s 水=0.289mpa.sLWM =X w 甲+(1-X w )水=0.002818lg(0.226)+(1-0.002818)(0.289)=-0.5394LWM =0.2888mpa.s精馏段液相平均黏度为LM =+0.32920.350.339722LDM LFM μμ+==mpa.s 提馏段液相平均黏度为L M′=0.28880.350.319422LFM LW M μ+μ+==mpa.s <五>精馏塔的塔体工艺尺寸计算1、 塔径的计算精馏段的气液相体积流率为 Vs=90.6628.92==0.665736003600 1.094vm vm VM ⨯⨯ρm/sLs=59.1826.32==0.00053136003600814.8lm lm LM ⨯⨯ρm/s提馏段的气液相体积流率为V s ′=90.6622.04==0.6586360036000.8427vm vm VM '⨯'⨯ρm /sL s ′=174.7519.50==1.02936003600919.48lm lm LM '⨯'⨯ρ×10-3 精馏段 u max =-L VVc ρρρ式中C 由C 20求取,C 20可通过查图(P 129页)筛板塔的泛点关联图的横坐标 0.000531814.8=0.6657 1.094sL sV L V ρρ 取板间距H T =0.35m (通过筛板塔的的泛点关联图)(书P 129 图10-42)得到C 20=0.068 C=C 20(20dL )0.2=0.068×(35.9420) 0.2=0.07646 最大空塔气速u max =-814.8-1.094=0.0746=2.085/1.094L V V cm s ρρρ 取安全系数为0.8,则空塔气速u=0.8u max =0.8×2.085=1.668m/s 440.6657==0.7133.14 1.668s V m u π⨯⨯ 按标准塔径圆整后 D=0.8m (据书P 129 表10-1)塔截面积为A T = 3.140.8==0.502444D π⨯²²m ² 实际空塔气速 u=0.6657==1.325/0.5024s T V m s Amax 1.325==0.632.085u u 实(安全系数在允许范围内,符合设计要求) 提馏段同理查阅得C201.0291030.6586⨯-=0.05161查表得H T =0.35m C 20′=0.07 C ′=C20′(20L δ')0.2=0.07(56.0520)0.2=0.08602 Umax ′=C同上取安全系数0.8 u ′=0.8Umax ′=0.8×2.84=2.272m/s D ′=圆整取D ′=0.8m 同上A T ′=0.5024㎡ 实际空塔气速u ′=T 0.65861.313A 0.5024s V '==' max 1.313==0.462.84u U ''(符合安全系数范围,设计合理)2、精馏塔有效高度的计算精馏段有效高度为Z 精=(N 精-1)H T =(9-1)×0.35=2.8m 提馏段有效高度为Z 提=(N 提-1)H T =(10-1)×0.35=3.15m 在加料板上设一人孔,其高度为0.7m故精馏塔的有效高度为Z=Z 精+Z 提+0.7=2.8+3.15+0.7=6.65m <六>塔板主要工艺尺寸的计算 1、溢流装置计算因塔径D=0.8,可选用单溢流弓形降液管,采用凹形受液盘 ⑴堰长l w 取l w=0.6D=0.48m ⑵溢流堰高度h w 由h w =h L —h ow选用平直堰,堰上液层高度h ow =2.84()/31000hwL E l ² 取E=1.03 h ow =2.840.00053136001.03()/3=7.3510000.48⨯⨯⨯²mmh ow ′=2.840.00102936001.03()/3=11.3110000.48⨯⨯⨯²mm 取板上清液高度为h L =60mm h w =60-7,35=0.05265m h w ′=60-11.31=0.04869m ⑶弓形降液管宽度w d 和截面积A f 由=0.6lw D 查图(P127页 弓形降液管的宽度与面积图)得=0.052f T A A =0.1d w D所以A f =0.052A T =0.052×0.5024=0.02612㎡W d =0.1D=0.1×0.8=0.08m所以依式计算液体在降液管中的停留时间精馏段:=360036000.026120.35==17.2170.0005313600f T h A H s L ⨯⨯⨯> 3~5s (故设计合理) 提馏段:′=360036000.026120.35==8.8840.0010293600f T h A H s L '⨯⨯'⨯ >3~5s(故设计合理)⑷降液管低隙高度h 。
化工原理甲醇—水精馏塔设计
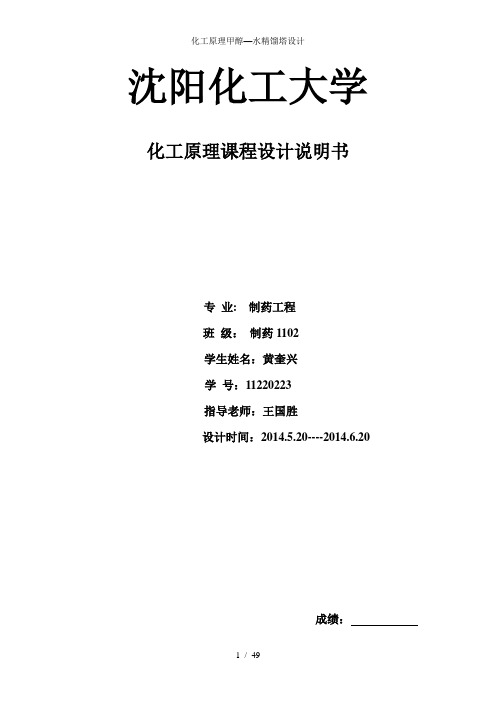
沈阳化工大学化工原理课程设计说明书专业: 制药工程班级:制药1102学号:设计时间:2014.5.20----2014.6.20成绩:化工原理课程设计任务书设计题目:分离甲醇-水混合液的填料精馏塔二原始数据及条件生产能力:年生产量甲醇1万吨(年开工300天)原料:甲醇含量为30%(质量百分数,下同)的常温液体分离要求:塔顶甲醇含量不低于95%,塔底甲醇含量不高于0.3%。
建厂地区:沈阳三设计要求(一).一份精馏塔设计说明书,主要内容要求:(1).前言(2).流程确定和说明(3).生产条件确定和说明(4).精馏塔设计计算(5).主要附属设备及附件选型计算(6).设计结果列表(7).设计结果的自我总结与评价(8).注明参考和试用的设计资料(9).结束语(二).绘制一份带控制点工艺流程图。
(三).制一份精馏塔设备条件图四.设计日期:2013年5月20日至6月20日前言精馏塔分为板式塔和填料塔两大类。
填料塔又分为散堆填料和规整填料两种。
板式塔虽然结构较简单,适应性强,宜于放大,在空分设备中被广泛采用。
但是,随着气液传热、传质技术的发展,对高效规整填料的研究,一些效率高、压降小、持液量小的规整填料的开发,在近十多年内,有逐步替代筛板塔的趋势。
实际生产中,在精馏柱及精馏塔中精馏时,上述部分气化和部分冷凝是同时进行的。
对理想液态混合物精馏时,最后得到的馏液(气相冷却而成)是沸点低的B物质,而残液是沸点高的A物质,精馏是多次简单蒸馏的组合。
精馏塔底部是加热区,温度最高;塔顶温度最低。
精馏结果,塔顶冷凝收集的是纯低沸点组分,纯高沸点组分则留在塔底。
精馏塔的优点:归纳起来,规整填料塔与板式塔相比,有以下优点:1)压降非常小。
气相在填料中的液相膜表面进行对流传热、传质,不存在塔板上清液层及筛孔的阻力。
在正常情况下,规整填料的阻力只有相应筛板塔阻力的1/5~1/6;2)热、质交换充分,分离效率高,使产品的提取率提高;3)操作弹性大,不产生液泛或漏液,所以负荷调节范围大,适应性强。
- 1、下载文档前请自行甄别文档内容的完整性,平台不提供额外的编辑、内容补充、找答案等附加服务。
- 2、"仅部分预览"的文档,不可在线预览部分如存在完整性等问题,可反馈申请退款(可完整预览的文档不适用该条件!)。
- 3、如文档侵犯您的权益,请联系客服反馈,我们会尽快为您处理(人工客服工作时间:9:00-18:30)。
南京工业大学《化工原理》课程设计设计题目 常压甲醇-水筛板精馏塔设计学生姓名 陈献富 班级、学号 化工070313指导教师姓名 刘晓勤、王晓东课程设计时间2010年6月14日-2010年6月25日课程设计成绩指导教师签字化学化工学院课程名称化工原理课程设计设计题目常压甲醇-水筛板精馏塔设计学生姓名周佳佳专业化学工程与工艺班级学号1001090605设计日期2010 年6 月14 日至2009 年6 月25日设计条件及任务:设计体系:甲醇-水体系设计条件:进料量:F= 200 kmol/h进料浓度:Z F= 0.35 (摩尔量分数)进料状态:q= 1.08操作条件:塔顶压强为4kPa(表压),单板压降不大于0.7kPa。
塔顶冷凝水采用深井水,温度t=12℃;塔釜加热方式:间接蒸汽加热,采用3kgf/cm2(表压)水蒸汽全塔效率:E T = 52%分离要求:X D= 0.995(质量分数);X W= 0.002(质量分数);回流比:R/R min =1.6指导教师刘晓勤、王晓东2010年6月11日目录绪论1.精馏简介蒸馏是分离液体混合物的一种方法,是一种属于传质分离的。
广泛应用于炼油、、轻工等领域。
蒸馏的理论依据是利用溶液中各组分蒸汽压的差异,即各组分在相同的压力、温度下,其挥发性能不同(或沸点不同)来实现分离目的。
以本设计所选取的甲醇-水体系为例,加热甲醇(沸点64.5℃)和水(沸点100.0℃)的混合物时,由于甲醇的沸点较低(即挥发度较高),所以甲醇易从液相中汽化出来。
若将汽化的蒸汽全部冷凝,即可得到甲醇组成高于原料的产品,依此进行多次汽化及冷凝过程,即可将甲醇和水分离。
经过多次部分汽化部分冷凝,最终在汽相中得到较纯的易挥发组分,而在液相中得到较纯的难挥发组分,这就是精馏。
在工业精馏设备中,使部分汽化的液相与部分冷凝的气相直接接触,以进行气液相际传质,结果是气相中的难挥发组分部分转入液相,中的易挥发组分部分转入气相,也即同时实现了液相的部分汽化和气相的部分冷凝。
蒸馏按操作可分为简单蒸馏、平衡蒸馏、精馏、特殊精馏等多种方式。
按原料中所含组分数目可分为双组分蒸馏及多组分蒸馏。
按操作压力则可分为常压蒸馏、加压蒸馏、减压(真空)蒸馏。
此外,按操作是否连续蒸馏和间歇蒸馏。
工业中的蒸馏多为多组分精馏,从石油工业、酒精工业直至焦油分离,基本有机合成,空气分离等等,特别是大规模的生产中精馏的应用更为广泛。
本设计着重讨论常压下甲醇-水双组分体系精馏。
2.塔设备简介塔设备是炼油、化工、石油化工等生产中广泛应用的气液传质设备。
根据塔内气液接触件的结构型式,可分为板式塔和填料塔两大类。
板式塔内设置一定数量踏板,气体以鼓泡活喷射形式穿过板上液层进行质、热传递,气液相组成成阶梯变化,属逐级接触逆流操作过程。
填料塔内有定高度的填料层,液体自塔顶沿填料表面下流,气体逆流而上(也有并流向下者)与液相接触进行质、热传递,气相组成沿塔高连续变化,属微分接触操作过程。
工业上对塔设备的主要要求:(1)生产能力大;(2)传质、传热效率高;(3)气流的摩擦阻力小;(4)操作稳定,适应性强,操作弹性大;(5)结构简单,材料消耗少;(6)制造安装容易,操作维修方便。
此外还要求不易堵塞、耐腐蚀等。
实际上,任何塔设备都难以满足上述所有要求,因此,设计者应根据塔型特点、物系性质、生产工艺条件、操作方式、设备投资、操作与维修费用等技术经济评价以及设计经验等因素,依矛盾的主次,综合考虑,选择适宜的塔型。
在化学工业和石油工业中广泛应用的诸如吸收,解吸,精馏,萃取等单元操作中,气液传质设备必不可少。
塔设备就是使气液成两相通过紧密接触达到相际传质和传热目的的气液传质设备之一。
3.体系介绍本设计的体系为甲醇-水体系。
101.325kPa下,甲醇-水体系汽液平衡数据如下:温度t(℃) 液相组成x 气相组成y 温度t(℃) 液相组成x 气相组成y100 0 0 75 0.4 0.796 0.02 0.1 73 0.5 0.894 0.04 0.2 71 0.6 0.891 0.06 0.3 69 0.7 0.989 0.08 0.4 68 0.8 0.988 0.1 0.4 66 0.9 184 0.15 0.5 65 1 182 0.2 0.6 65 1 178 0.3 0.7注:x、y分别为气液两相中甲醇的摩尔分数4.设计要求设计条件:体系:甲醇-水体系已知:进料量F=200 kmol/h进料浓度ZF= 0.35(摩尔分数)进料状态:q= 1.08操作条件:塔顶压强为4 kPa(表压),单板压降不大于0.7kPa。
塔顶冷凝水采用深井水,温度t=12℃;塔釜加热方式:间接蒸汽加热全塔效率ET= 52%分离要求: XD = 0.995(质量分数);XW= 0.002(质量分数); R/Rmin=1.6 。
第一节概述1.1精馏操求作对塔设备的要求工业上对塔设备的主要要求:(1)生产能力大;(2)传质、传热效率高;(3)气流的摩擦阻力小;(4)操作稳定,适应性强,操作弹性大;(5)结构简单,材料消耗少;(6)制造安装容易,操作维修方便。
此外还要求不易堵塞、耐腐蚀等。
1.2板式塔类型塔设备大致可以分为两类,一类是有降液管的塔板,如泡罩、浮阀、筛板、导向筛板、舌形、S形、多降液管塔板等;另一类是无降液管塔板,如传流式筛板(栅板)、穿流式波纹板等。
工业上应用较多的是有降液管的浮阀、筛板和泡罩塔板等。
1.2.1筛板塔筛板塔板简称筛板,结构持点为塔板上开有许多均匀的小孔。
根据孔径的大小,分为小孔径筛板(孔径为3—8mm)和大孔径筛板(孔径为10—25mm)两类。
工业应用小以小孔径筛板为主,大孔径筛板多用于某些特殊场合(如分离粘度大、易结焦的物系)。
筛板的优点是结构简单,造价低;板上液面落差小,气体压降低,生产能力较大;气体分散均匀,传质效率较高。
筛板塔和泡罩塔相比较具有下列特点:生产能力大于10.5%,板效率提高产量15%左右;而压降可降低30%左右;另外筛板塔结构简单,塔板的造价可减少40%左右;安装容易,也便于清理检修。
但其缺点是筛孔易堵塞,不宜处理易结焦、粘度大的物料。
值得说明的是,尽管筛板传质效率高,但若设计和操作不当,易产生漏液,使得操作弹性减小,传质效率下降。
然而近年来,由于设计和控制水平的不断提高,可使筛板的操作非常精确,弥补了上述不足,故应用日趋广泛。
综合考虑利弊,对于甲醇-水体系,本设计选用筛板塔。
1.2.2浮阀塔浮阀广泛应用于精馏、吸收和解析等过程。
其主要特点是在塔板的开孔上装有可浮动懂得浮阀,气流从浮阀周边以稳定的速度水平地进入塔板上液层进行两相接触。
浮阀可以根据气流量的大小而上下浮动,自行调节。
浮阀的主要优点是生产能力大,操作弹性大,分离效率高,塔板结构较泡罩塔简单。
1.2.3泡罩塔泡罩塔是最早使用的板式塔,其主要构件是泡罩、升气管及降液管。
泡罩的种类很多,国内用较多的是圆形泡罩。
泡罩的主要优点是操作弹性较大,液气比范围大,适用于多种介质,操作稳定可靠;但其结构复杂、造价高、安装维修不方便,气相压降较大。
现虽已为新型塔板取代,但鉴于其某些优点,仍有使用。
1.3设计单元操作方案简介蒸馏过程按操作方式的不同,分为连续蒸馏和间歇蒸馏两种流程。
连续蒸馏具有生产能力大,产品质量稳定等优点,工业生产中以连续蒸馏为主。
间歇蒸馏具有操作灵活、适应性强等优点,但适合于小规模、多品种或多组分物系的初步分离。
故分离苯-甲苯混合物体系应采用连续精馏过程。
蒸馏是通过物料在塔内的多次部分气化与多次部分冷凝实现分离的,热量自塔釜输入,由冷凝器和冷却剂中的冷却介质将余热带走。
塔顶冷凝装置可采用全凝器、分凝器-全凝器两种不同的设置。
工业上以采用全凝器为主,以便准确控制回流比。
本设计中采用全凝器。
1.4精馏塔的设计简介1.4.1 筛板塔设计须知(1)筛板塔设计是在有关工艺计算已完成的基础上进行的。
对于气、液恒摩尔流的塔段,只需任选其中一块塔板进行设计,并可将该设计结果用于此塔段中。
例如,全塔最上面一段塔段,通常选上面第一块塔板进行设计;全塔最下面一段塔段,通常选最下面一块塔板进行设计。
这样计算便于查取气液相物性数据。
(2)若不同塔段的塔板结构差别不大,可考虑采用同一塔径,若不同塔段塔板的可能有差异。
对筛孔少、塔径大的塔段,为减少筛孔数、空心距与筛孔直径之比t/d进塔壁处液体“短路”,可在近塔壁处设置挡板。
只有当不同塔段的塔径相差较大时才考虑采用不同塔径,即异径塔。
1.4.2 筛板塔的设计程序⑴确定设计方案;⑵平衡级计算和理论塔板的确定;⑶塔板的选择;⑷实际板数的确定;⑸塔体流体力学计算;⑹管路及附属设备的计算与选型;⑺撰写设计说明书和绘图。
第二节设计方案的初步确定2.1操作条件的确定2.1.1操作压力塔内操作压力的选择不仅牵涉到分离问题,而且与塔顶和塔底温度的选取有关。
根据所处理的物料性质,兼顾技术上的可行性和经济上的合理性来综合考虑,一般有下列原则:⑴压力增加可提高塔的处理能力,但会增加塔身的壁厚,导致设备费用增加;压力增加,组分间的相对挥发度降低,回流比或塔高增加,导致操作费用或设备费用增加。
因此如果在常压下操作时,塔顶蒸汽可以用普通冷却水进行冷却,一般不采用加压操作。
操作压力大于1.6MPa才能使普通冷却水冷却塔顶蒸汽时,应对低压、冷冻剂冷却和高压、冷却水冷却的方案进行比较后,确定适宜的操作方式。
⑵考虑利用较高温度的蒸汽冷凝热,或可利用较低品位的冷源使蒸气冷凝,且压力提高后不致引起操作上的其他问题和设备费用的增加,可以使用加压操作。
⑶真空操作不仅需要增加真空设备的投资和操作费用,而且由于真空下气体体积增大,需要的塔径增加,因此塔设备费用增加。
综合考虑以上因素本设计采用常压精馏。
2.1.2进料状态泡点进料时,塔的操作易于控制,不受环境影响。
饱和液体进料时进料温度不受季节、气温变化和前段工序波动的影响,塔的操作比较容易控制。
此外,泡点进料,提馏段和精馏段塔径大致相同,在设备制造上比较方便。
冷液进塔虽可减少理论板数,使塔高降低,但精馏釜及提馏段塔径增大,有不利之处。
所以根据设计要求,选择泡点进料,q=1。
2.1.3加热方式精馏塔的设计中多在塔底加一个再沸器以采用间接蒸汽加热以保证塔内有足够的热量供应;由于甲醇-水体系中,甲醇是轻组分由塔顶冷凝器冷凝得到,水为重组分由塔底排出。
所以本设计应采用再沸器提供热量,采用3kgf/cm2(温度130℃)间接水蒸汽加热。
2.1.4冷却剂与出口温度本设计中采用的冷却剂为深井水,深井水水温较江河水水温稳定(如:南京地区深井水水温常年维持在12℃),易于操作条件的控制。
冷却水出口温度过高,则冷却效果不佳;反之,如果温度过低,冷却水用量较大,增加了成本。