第三章 有杆泵采油
第03章有杆泵采油-2讲解

B
Bl
一、柱塞冲程
第四节 泵效计算
交变载荷作用
抽油杆柱和油管柱的弹性伸缩
柱塞冲程小于光杆冲程
液柱载荷交替地由油管转移到抽油杆柱和由抽油杆柱
(一)静载荷作用下的柱塞冲程
转移到油管,使杆柱和管柱发生交替地伸长和缩短。
一、柱塞冲程
上冲程中:抽油杆加载,油管卸载。 1) A B驴头上 行,游动阀关闭, 抽 油杆加载W’ l ,杆伸 长λr 。 2) B B’与此同 时,管卸载W’ l ,缩 短λt ,活塞与衬套无 相对位移,吸入阀关 闭。 3)B’ C吸入阀 打开,B’C=Sp =S(λr + λt )=S-λ
一、柱塞冲程
API方法:
抽油杆柱振
动对柱塞冲
程的影响存 在着冲次、 冲程配合的 有利与不利 区域。
二、气体和充不满的影响
通常: P泵入口 Pb 气体进泵减少 V液进泵
气锁:由于气体在泵内的压缩和膨胀,使得吸入 阀无法打开而抽不出油,这种现象称为“气锁”。 充满系数:是指每冲次吸入泵内的原油(或液体)的 体积 Vo 与活塞让出容积 V p 之比,即
Vo V p Vs 1 Rgo
Vo ' Vo Vs
Vp Vs 1 Rgo
Vs
Vp Vs Rgo 1 Rgo
1 K s Rgo 1 Rgo
Vo ' V p Vs Rgo 1 Vp 1 Rgo V p
Vs 1 Rgo Vp 1 Rgo
若油层能量低或 o高,造成冲不满,可以 采用:加深泵挂,增加 沉没度,实施增产措 施,优选抽汲参数,若 为稠油,可以降粘。
Rgo
( R p Rs )(1 f w ) pi 0.1
延大采油工程实验指导03有杆泵与抽油原理

实验三有杆泵与抽油原理一.实验目的1. 观察抽油机、抽油泵的结构和工作过程(机杆泵四连杆机构)。
2.掌握有杆泵抽汲原理熟悉游梁式抽油机主要部件组成、各部件名称结构及工作原理。
3. 观察气锚的分气效果。
4.观察模拟泵在井筒内的工作状况。
二.实验内容1.抽油机工作原理有杆泵抽油是三大采油方法之一。
本实验装置由抽油机和井筒两大部分组成,见图1。
电动机的高速旋转运动通过皮带轮和减速箱减速,传递给曲柄轴,带动曲柄作低速旋转运动,经曲柄、连杆、横梁带动油梁作上下摆动,挂在游梁驴头上的悬绳器便带动抽油杆柱做上下往复运动,从而带动泵柱塞做上下往复运动。
图1 抽油机的实验装置组成示意图2.抽油泵工作原理有杆泵是由泵筒、衬套、柱塞、游动阀、固定阀组成。
泵的工作由三个基本环节组成,即柱塞在泵内让出容积,液体进泵和从泵内排出液体。
在理想的情况下,柱塞上下一次进入和排出的液体等于柱塞让出的容积。
上冲程,抽油机带动抽油杆连接柱塞一起向上运动,柱塞上的游动阀受柱塞上油管液柱压力作用而关闭,与此同时,泵腔内由于柱塞上行让出容积而压力降低,固定阀在油套环形空间液柱压力作用下被冲开,液体被吸入泵腔内,上冲程为泵吸液而油井排液过程。
下冲程,柱塞下行,固定阀关闭,泵腔内压力增高,当泵内压力大于柱塞以上液柱压力时,游动阀被冲开,泵腔内液体通过游动阀排入井筒中,见图2。
柱塞上下一次为一个冲程,在一个冲程内完成一次进液和排液的过程。
图2 泵的工作原理图3.气锚分离原理气锚是井下油气分离装置,其基本原理是建立在油气密度不同而起油气分离作用的。
气锚可分为旋转式、沉降式,其结构图见3.3。
气锚安装在抽油泵的末端。
沉降式气锚当柱塞上行时,由于抽吸和管外液柱压力作用,油和气进入锚内,由于油气密度的差异气体大部分上浮于气锚的上端,而液体则沉降于气锚的下端;当柱塞下行时,由于泵的阀被关闭,气锚内液体处于静止状态,气体上浮自锚上端的排气孔抛出,进入管外油套环形空间,而脱气原油自气锚中心管的下口被吸入到泵腔内,从而达到防止气体进泵,提高泵效的目的。
第3章有杆泵采油
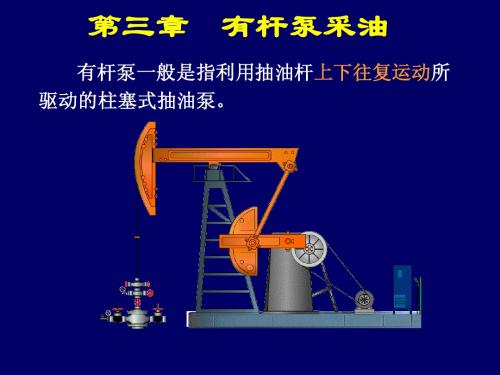
总阀门: 总阀门:控制着油气 流入采油树的通道。 流入采油树的通道。 正常生产是打开, 正常生产是打开,需 要关 井时关闭。 井时关闭。
第四节
抽油机平衡计算
一、平衡方式及其原理
游梁式抽油机平衡采用气动平衡和机械平衡两种方式。 其中,机械平衡又分为: 1)游梁平衡(beam balance) ; 2)曲柄平衡(crank balance); 3) 复合平衡(combined balance)。 平衡的基本原理: 平衡的基本原理:下冲程过程中以某种方式把抽油杆柱所 放出的能量、电动机提供的能量储存起来, 放出的能量、电动机提供的能量储存起来,到上冲程时再 释放出来帮助电动机做功。 释放出来帮助电动机做功。
皮带式抽油机
链传式抽油机
天轮式抽油机
直线往复式抽油机
一、抽油机
主要组成: 主要组成:
游梁—连杆 曲柄 四连杆) 游梁 连杆—曲柄(四连杆)机构 连杆 曲柄( 减速机构(减速器) 减速机构(减速器) 动力设备(电动机) 动力设备(电动机) 辅助装置等四部分 游梁式抽油机工作原理: 游梁式抽油机工作原理:
达到平衡所需要的曲柄平衡半径为
F:复合平衡 Y:游梁平衡 平衡方式代号 B:曲柄平衡 Q:气动平衡 减速箱齿轮形代号, 减速箱齿轮形代号 , H 为点啮合双 圆弧齿轮, 圆弧齿轮,省略渐开线人字齿轮 减速箱曲柄轴最大允许扭矩,kN.m 减速箱曲柄轴最大允许扭矩,kN.m
B
光杆最大冲程, 光杆最大冲程,m 悬点最大载荷, 悬点最大载荷,10 kN 游梁式抽油机系列代号
(3-1)
;
3. 抽油泵类型和结构
• 按抽油泵在油管中的固定方式分为:
管式泵和杆式泵两大类型。
• 按抽油泵泵筒结构又分为
采油机械——有杆泵采油
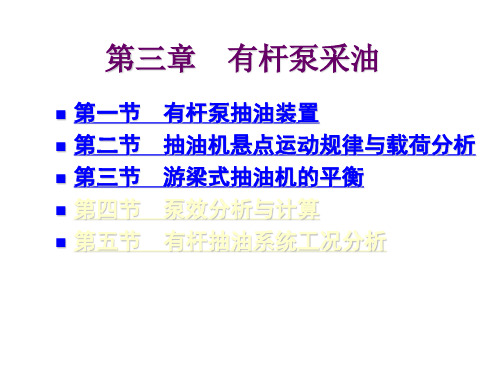
(2)游梁
游梁的作用:游梁安装在支 架轴承上,作用是绕支点 轴承作摇摆运动来传递动 力,同时也是承受负荷的 主要构件。
游梁安装的要求:为了校准 驴头中心与井口中心一致, 往往在游梁上焊上2—4个 顶丝,并且将游梁上的 “U”型卡子的孔开成长方 形的。亦有在抽油机支架 上焊上2—4个顶丝,用来 调节小轴的轴承位置。
安装时要注意曲柄孔、曲柄孔 键槽、锥形套和键等应有良 好的配合,否则易滚键或断 曲柄销。
(5)曲柄
曲柄的位置:曲柄安装在 减速器输出轴两端共 两个。
曲柄的结构:曲柄上有 4—8 个 圆 孔 , 调 节 冲 程时可将曲柄销子固 定在任何一个适当的 孔里。图为曲柄和平 衡块的安装图。
(5)曲柄
曲柄的安装:曲柄一端有开口 的大孔,是用它把曲柄安装 在减速器的输出轴上。安 装时键槽孔要对正,然后将 键打入键槽,再将孔旁的差 动螺丝或T型螺丝上紧。曲 柄两侧的两个大铁块叫平 衡块,平衡块是用T型螺丝 与曲柄紧固在一起。平衡 块上面标的箭头处是平衡 块的中心线,它是供调平 衡时应用的。
(3)横梁
横梁的作用:是连接连杆 与游梁之间的桥梁,动 力经过横梁才能带动游 梁作摇摆运动
横梁的形式: 一般有三种, 一种是直形横梁,另一 种是船形横梁,还有一 种是翼形横梁。
横梁结构:多采用型钢焊 接结构,如船形横梁 ( 图 a) , 也 有 少 数 铸 造 横梁,如翼形横梁(图b)
第4堂开始
普通式抽油机结构简图
2.游梁式抽油机的结构:
(1)驴头
驴头的安装形式: 驴头是装在游梁近
井口端的一个带弧面构 件,由钢板或三角铁焊 接制成。 驴头的作用:
在游梁摆动的情况 下保证光杆始终对准井 口中心位置。
驴头的类型:
延大采油工程习题集及答案03有杆泵采油

第三章 有杆泵采油一、名词解释1、有杆泵: 利用抽油杆驱动的井下抽油泵。
2、静载荷: 由抽油杆柱重力、液柱重力、沉没压力、井口回压在悬点上产生的载荷。
3、动载荷: 抽油杆柱运动时由于振动、惯性以及摩擦在悬点上产生的载荷。
4、扭矩曲线:反映曲柄轴扭矩随曲柄转角的变化曲线称之为曲柄轴扭矩曲线,简称扭矩 曲线。
5、泵效: 在抽油井生产过程中, 泵的实际排量与理论排量的比值称为泵效, 亦称泵的容 积效率。
= QQ t ,6、充满程度:每冲次吸入泵内的原油(或液体)的体积与活塞让出体积的比值。
β =V 07、系统效率:有效功率与电机输入功率的比值。
= H e V p 9、气动平衡:通过游梁带动的活塞压缩气包中的气体,把下冲程中做的功储存成为气体 的压缩能。
在上冲程中被压缩的气体膨胀,将储存的压缩能转换成膨胀能帮助电动机做功。
10、机械平衡:以增加平衡重块的位能来储存能量, 而在上冲程中平衡重降低位能来帮助 电动机做功的平衡方式。
11 、理论排量: 在一个冲程内, 排出的液体体积为,Vp 的s 排量为: Q t = 1440f p sn 每日的排量就成为理论排量。
12 、光杆示功图:反映悬点载荷随其位移变化规律的图形。
实际抽油井的光杆(地面)示 功图由动力仪测得。
二、叙述题1 、有杆泵分为哪几类:答案要点:分为常规有杆泵和地面驱动螺杆泵。
2 、常规型游梁式抽油机的工作原理是什么:答案要点 091:动力机将高速旋转运动经皮带传递给减速箱,经减速箱减速后, 再由曲 柄连杆机构将旋转运动变为游梁的上下摆动,挂在驴头上的悬绳器带动抽油杆做上下往复运 动。
3 、管式泵的特点是什么?答案要点:结构简单、成本低; 泵径大, 排量大; 检泵时需起出油管,修井工作量大。
1 、 杆式泵的特点:答案要点:检泵不需起出油管, 检泵方便;结构复杂,制造成本高;排量小。
2 、 抽油机平衡方式:答案要点:分为气动平衡和机械平衡。
第三章 有杆泵采油

(3)横梁 (3)横梁 横梁的作用:是连接连杆 与游梁之间的桥梁,动 力经过横梁才能带动游 梁作摇摆运动 横梁的形式一般有三种: 一种是直形横梁,另一 种是船形—横梁,还有 一种是翼形横梁。 横梁结构:多采用型钢焊 接结构,如船形横梁 (图a),也有少数铸造 横梁,如翼形横梁(图b)
(4)连杆 (4)连杆 连杆与横梁连接(如图所示): 在连杆的上部焊有接头,连 杆与横梁用销轴铰接,下接 头靠曲柄销4与曲柄连接,曲 柄销与连杆连接的一端装有 双列自位滚珠轴承,另一端 与锥形套配合固定在曲柄销 孔内,用冕形螺帽6固紧,并 加开口销锁住。
变型抽油机为适 应长冲程做成前 臂长,驴头端重
普通式抽油机结构简图
2.游梁式抽油机的结构: (1)驴头 驴头是装在游梁近井 口端的一个带弧面构件, 由钢板或三角铁焊接制成。 驴头的作用:是在游梁 摆动的情况下保证光杆始 终对准井口中心位置。
(2)游梁 (2)游梁 游梁的作用:游梁安装在 支架轴承上,作用是绕支点 轴承作摇摆运动来传递动 力,同时也是承受负荷的主 要构件。 游梁安装的要求:为了校 准驴头中心与井口中心一致, 往往在游梁上焊上2—4个顶 丝,并且将游梁上的“U”型 卡 子的孔开成长方形的。
每分钟排量为: 每日体积排量为: 每日质量排量为: 式中:
Vm = f P sn
Qt = 1440 f P sn
Qm = 1440 f P snρ l
Qt -泵的体积理论排量,m3/d;
Qm-
泵的质量理论排量,t/d;
三、抽油杆
抽油杆的作用:在抽油装置中抽油杆是中间部分, 起连接抽油机与抽油泵,并把抽油机的动力传递给抽 油泵的作用。 抽油杆的类型: (1)根据化学成份,抽油杆可分为碳钢抽油杆、 合金钢抽油杆及玻璃钢抽油杆等类型。 (2)根据抽油杆在杆柱中起的作用,抽油杆又可 分为光杆、普通抽油杆和加重杆。
采油工程第三章有杆泵采油5-6.ppt

为了求出声波在环形空间中传播的速度,在距离井口一 定深度 L1 处安装音标。
液面深度
L L1 t t1
用双频回声仪测得的液面曲线。
在这种液面曲线上量取10个油管接箍反射波之间的纸带 长度作为 t1 ,量取从井口波到液面波之间的纸带长度作
为t,以10根油管的长度作为 L1, 也可求出液面深度为
Pf o gH f o g(H L f )
沉没度 hS :泵的吸入口沉没在动液面以下的深度。
油井的采油指数为: J Q
Q
Q
Pe Pf o g(H S H f ) o g(L f LS )
令
K
Jo g
HS
Q H
f
Q L f LS
,则油井的流动方程可表达为:
Q K (H S H f ) K (L f LS )
二、
(一)地层方面的措施
1.对于注水开发的油田,加强注水,保持油层能量高, 液面高。 2.采取有效的防砂措施。
(二) 井筒方面的措施
1. 在保证泵的理论排量不变,即 f P、s、n的乘积不变,改变各个参数的
大小时,泵效也改变,如果选用合理的参数,泵效可提高。
一般选用大冲程、小冲数、适当的泵径
2、确定合理的下泵深度和合理的沉没度 下泵深度越小,冲程损失越小,泵效越高; 下泵深度越大即沉没度越大,沉没压力越高,气体影响越小。
式中 Q —— 油井产量,t /d; K —— 称为米采油指数,t /(d·m)。
米采油指数 K 和采油指数 J 一样,也表示单位生产压差 下的原油日产量,只是这时的生产压差是用液柱高度差或液 面深度差表示。
(二)液面位置的测量 原理:利用回声仪测量声波从井口传播到液面再返回到井 口所用的时间t,再求出声波在环形空间中传播的速度,则 液面深度为:
第三章 有杆泵采油

第三章有杆泵采油机械采油:通过给井中原油补充机械能将油采到地面的方法称为机械采油。
分类:机械采油法分为有杆泵采油和无杆泵采油等方法。
第一节有杆泵抽油装置有杆泵抽油系统的基本组成:由抽油机、抽油泵和抽油杆三大部分组成游梁式抽油机-深井泵抽油装置(见图3-1所示):用油管把深井泵下入到井内液面以下,在泵筒下部装有只能向上打开的吸入阀,用抽油杆把柱塞下入泵筒内,柱塞上装有只能向上打开的排出阀,通过抽油杆柱把抽油机驴头悬点产生的上下往复运动传递给抽油泵向上抽油。
一、抽油机(一)游梁式抽油机游梁式抽油机的基本组成:1)换向机构:游梁-连杆-曲柄机构(四连杆)2)减速机构:由皮带轮、皮带、减速器组成。
3)动力设备:电动机或内燃机。
4)辅助装置:杀车装置、底座等工作原理:电动机通过传动皮带将高速旋转运动传递给减速器输入轴,经减速后由低旋转的曲柄通过四连杆机构带动游梁作上下往复摆动。
游梁前端圆弧状的驴头经悬绳器带动抽油杆作上下往复直线运动。
游梁式抽油机类的类型:(1)普通式:①基本型:抽油机的前臂和后臂接近等长(见图3-2)②变型:前臂长,可适应长冲程(2)前置式:其结构与普通式相同(见图3-3),只是支架轴和横梁轴互换了位置;上冲程曲柄转角为195°,下冲程为165°;当驴头在右侧时,曲柄顺时针转动;上冲程比下冲程慢,使抽油机承载能力强。
游梁式抽油的结构:(1)驴头驴头是装在游梁近井口端的一个带弧面构件,由钢板或三角铁焊接制成。
驴头的作用:是在游梁摆动的情况下保证光杆始终对准井口中心位置。
驴头的类型:根据移开井口的方式可分为,上翻式,可拆卸式和侧转式三种,如前图前所示。
上翻式(图a):修井时可把驴头上翻到游梁上。
这种驴头由于修井作业时可以用大钩提放,较为方便迅速,但缺点是笨重、不安全;侧转式驴头(图c)俗称歪脖子,由于移开井口操作时不需爬上游梁,故安全可靠,但缺点是不灵活,侧转费力;可拆卸的驴头(b)一般只用于小型抽油机。
有杆泵采油装置
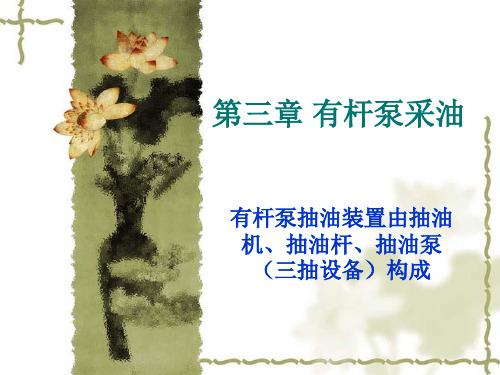
基本型抽油机
❖ 基本型抽油机游梁旳前臂和后臂接近等长, 驴头在左曲 柄顺时针旋转为正传,但正转和反转效果相同。
变型抽油机
❖ 前长变型抽油机为适应长冲程做成前臂长,驴头端重。 ❖ 异相变型抽油机又称曲柄偏置抽油机,它旳平衡重中心线与曲柄中心线有一
5—内泵筒;6—固定阀
二、抽油泵
❖ 1.管式泵
❖ (1)管式泵旳构造及下井方式
❖ (2)管式泵旳特点是构造简朴,成本低, 在相同油管直径下允许下入旳泵径较 杆式泵大,因而排量大。但检泵时必 须起下管柱,修井工作量大,故合用 于下泵深度不大,产量较高旳,含气 量较小,含砂量较大旳浅井。
图3-5 抽油泵示意图 a. 管式泵 b.杆式泵
经过井口密封盘根,上端经过悬绳器和绳辫子与抽油机驴头
相连。驴头在下死点时,光杆伸入盘根盒下列旳长度称为方
入,盘根盒以上到悬绳器之间光杆旳长度称为方余,光杆旳
方入要不小于光杆冲程。
❖ 2. 抽油杆
❖ 3. 加重杆
图3-6-2 抽油杆示意图
3.悬绳器——悬点
❖
悬绳器是连接光杆与绳辫
子旳工具,由上下两块扼板构
抽油泵构造简朴,便于起下,制造泵旳
材料耐磨,抗腐蚀性能好,使用寿命长,
加工安装质量高,降低使用故障率。
❖
抽油泵主要由泵筒、吸入阀、活塞、 排出阀四大部分构成。按照抽油泵在井
图3-5 抽油泵示意图 a. 管式泵 b.杆式泵
1—油管;2—游动阀;
下旳固定方式,可分为管式泵和杆式泵。 3—卡簧;4—活塞;
游梁式抽油机型号代号
(二)链条式抽油机
❖ 链条式抽油机旳构造主要 由
第3章有杆泵采油-采油概论

二、平衡计算
下冲程-存储能量 存储能量=电机所做功+抽油杆下落悬点所做功 Aw=Amd+Ad 上冲程-释放能量 释放能量+电机所做功=悬点提升所做功 Aw+Amu= Au Amd=Amu
基本公式:
(3-54)
二、平衡计算
只考虑静载荷,惯性力在上下冲程中所作功为0
悬点上冲程做功: 悬点下冲程做功:
二、泵的充满程度
条件:
P P in b
余隙比: K Vs / V p 充满系数:
Vl
'
1 K 1 R
K
1 KR 1 R
Vp
气体对冲满程度的影响
气锁:抽汲时由于气体在泵内压缩和膨胀,吸入和排出阀无 法打开,出现抽不出油的现象。
二、泵的充满程度
泵充满程度的影响因素分析:
前置式气动平衡抽油机结构简图 后置式抽油机结构简图
③运动规律不同—后置式上、 下冲程的时间基本相等;前 置式上冲程较下冲程慢。
我国游梁式抽油机型号表示法
例:CYJ8-3-37HB
CYJ
8 – 3 – 37 H
B
F:复合平衡
Y:游梁平衡 平衡方式代号 B:曲柄平衡 Q:气动平衡 减速箱齿轮形代号,H为点啮合双 圆弧齿轮,省略渐开线人字齿轮 减速箱曲柄轴最大允许扭矩,kN.m 光杆最大冲程,m 悬点最大载荷,10 kN 游梁式抽油机系列代号
松的防脱器等。
4、井口装置-采油树
节流器:控制 自喷井产量
清蜡闸门:其上方可 连接清蜡方喷管等, 清蜡时才打开。
生产阀门:控制油气 流向出油管线,正常 生产时打开,更换检 查油 嘴或油井停产时 关闭
总阀门:控制着油气 流入采油树的通道。 正常生产是打开,需 要关 井时关闭。
采油工程第3章有杆泵采油

②抽油井工作制度与含水的变化关系
采油工程原理与设计
当油层和水层压力相同(或油水同层)时,油井含水不随工作 制度而改变;
当出油层压力高于出水层压力时,增大总采液量(降流压), 将引起油井含水量的上升;
当水层压力高于油层压力时,加大总采液量,将使油井含 水量下降。
S
i
S(1 Wr N 2L )
1790 fr E
采油工程原理与设计
(三)抽油杆柱的振动对柱塞冲程的影响
液柱载荷交变作用 抽油杆柱变速运动
抽油杆柱振动
抽油杆柱变形
理论分析和实验研究表明:抽油杆柱本身振动的相位在上 下冲程中几乎是对称的,即如果上冲程末抽油杆柱伸长,则下 冲程末抽油杆柱缩短。因此,抽油杆振动引起的伸缩对柱塞冲 程的影响是一致 ,即要增加都增加,要减小都减小。其增减 情况取决于抽油杆柱自由振动与悬点摆动引起的强迫振动的相 位配合。
图3-30 有气体影响的示功图
②充不满影响的示功图
采油工程原理与设计
充不满现象:地层产液在上冲程末未充满泵筒的现象。
图3-31 充不满的示功图
液击现象:泵充不满生产时,柱塞与泵内液面撞击引 起抽油设备受力急剧变化的现象。
2.漏失对示功图的影响 ① 排出部分的漏失
图3-32 泵排出部分漏失
采油工程原理与设计
V L1 t1 / 2
图3-26 声波反射曲线
L
L1
t t1
图3-25 静液面与动液面的位置
2.无音标井
采油工程原理与设计
根据波动理论和声学原理,声波在气体中的传播速度为:
V KP
利用气体状态方程确定气体密度:PV
第三章 有杆泵采油new4-6-2013 (1)
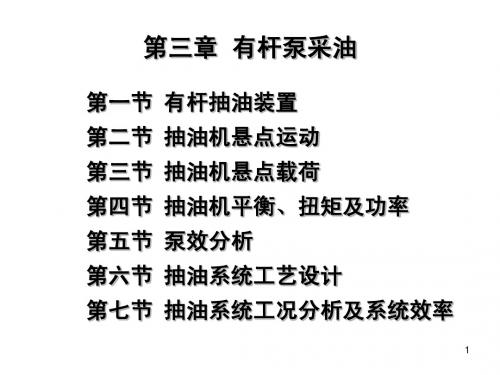
泵内条件下(p<pb)的气液比可表示为
R Vg VL (1 f w )(Rp Rs )Bg BL
Rs Rp pi pb
1
充满系数可表示为泵吸入压力的函数
Z g Tpsc 1 1 1 R p 1 f w p Tsc BL pb i
2
0
1 n 2 M ( ) d M i 2 i 1
2
17
抽油机曲柄轴的等值扭矩与最大扭矩之间 存在一定关系,可近似表示为
M e kM max
当抽油机的运动视为简谐运动k=0.7;回归分 析结果k=0.54;根据理论分析和实践资料的计算 结果,并考虑到不平衡等因素,建议k取0.6。
第三章 有杆泵采油
第一节 有杆抽油装置 第二节 抽油机悬点运动
第三节 抽油机悬点载荷
第四节 抽油机平衡、扭矩及功率
第五节 泵效分析
第六节 抽油系统工艺设计
第七节 抽油系统工况分析及系统效率
1
第四节 抽油机平衡、扭矩及功率一、 Nhomakorabea油机平衡计算
抽油机不平衡运转 上冲程: Pu Wr WL 电机对驴头作功 A (W W )S u r L 下冲程: P W 驴头对电机作功 Ad WrS
min(M max1 , M max2 ) max(M max1 , M max2 )
当Ψ≥0.7时认为基本达到平衡。
按SY/T5266-1996, I下 I上 100% Ψ =80~110%为合格!
M max1 M max2 R Wcb (sin1 sin 2 )
拉玛扎诺夫(1957)最大扭矩公式(SI单位制)
延大采油工程原理与设计课件03有杆泵采油

Chapter 4
第一节 抽油设备及其工作原理
抽油设备: 抽油机、抽油杆柱和抽油泵,即“三抽”设备
一、抽油机
1. 游梁式抽油机 (1)分类
抽油机
游梁式抽油机 无游梁式抽油机
游梁式抽油机
常规型(普通型) 前置型 变型
基本型
Chapter 4 (2)结构
第一节 抽油设备及其工作原理
由游梁—连杆—曲柄机构、减速箱、动力设备和 辅助装置四大部分构成
斜直井型
Chapter 4
第一节 抽油设备及其工作原理
(一)抽油机的结构组成
Chapter 4
第一节 抽油设备及其工作原理
(二)抽油机各组成部件的作用
(1)刹车装置:刹车也叫制动器,它是由手柄、刹车中间座、拉杆、锁死弹簧、 刹车轮、刹车片等部件组成。刹车片与刹车轮接触时发生摩擦而起到制动作用。
(2)电动机:电机是动力的来源,一般采用感应式三相交流电动机。它固定在电 机座上由皮带传递动力至减速器大皮带轮。前后对角上有两条顶丝可调节皮带的松 紧度。
(9)游梁:它安装在支架轴承上,绕支架轴承作上下摆动,尾端通过尾轴承与横梁 连接在一起,前端装有驴头,游梁可前后移动调节,以便使驴头始终对准井口。在 复合平衡的机型中,游梁尾部可挂有尾平衡板。
(10)驴头:它装在游梁最前端驴头为弧面,它的弧线是以支架轴承为圆心,以游 梁前臂长为半径画孤而得到的。它保证了抽油时光杆始终对正井口中心。驴头担负 着井内抽油杆、泵摩擦阻力及液柱的重量。
(3)曲柄:它是由铸铁铸就的一个部件,装在减速器输出轴上。曲柄上开有大小 冲程的孔眼叫冲程孔,专门为调节冲程所用。两侧外缘有牙槽并有刻度标记。侧面 开有凹槽是装配重块所用,内侧两边缘为平面,尾部有一吊孔。曲柄头部与输出轴 的连接,头部为叉型,中间开有与减速器输出轴直径相匹配的孔,并开有键槽。叉 型部分由两条拉紧螺栓固定。
采油工程-第03章有杆泵采油
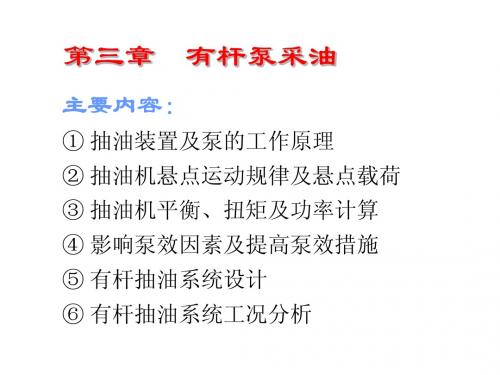
•动液面---生产时的环空 液面深度Lf •静液面---关井时的环空 液面深度Ls •沉没度---生产时的环空 液面距泵口距离hf
二、泵的工作原理 1)上冲程
(一)泵的抽汲过程
抽油杆柱带着柱塞向上运动,
柱塞上的游动阀受管内液柱压力而
关闭。 泵内压力降低,固定阀在环形 空间液柱压力(沉没压力)与泵内压 力之差的作用下被打开。 泵内吸入液体、井口排出液体。 泵吸入的条件:泵内压力(吸入压力) 低于沉没压力。
采油方法-螺杆泵采油
(五)发展趋势
1)为提高排量和扬程,国外各公司在单螺 杆泵结构优化的同时,积极研究多头螺杆 泵。
2)为提高螺杆泵的综合性能和使用寿命, 国外各公司在优化定子橡胶的配方和增强 转子的耐磨、抗腐蚀的同时,还探索使用 金属定子、非金属转子。
采油方法-螺杆泵采油
(五)发展趋势
3)为降低螺杆泵的制造成本,以提高经济效益, 国外各公司在普遍从采用圆钢毛坯加工成型转 子向采用热轧成型转子方向发展的同时,积极 发展钢管热轧成型转子。
(2) 地面驱动螺杆泵采油:井口驱动 头的旋转运动通过抽油杆传递给井下 螺杆泵。
常规有杆泵采油是目前我国应用最 广泛的采油方式,我国机械采油井
占总井数的90%以上,其中有杆泵
占机采井的90%以上。全国产液量
的60%、产油量的75%靠有杆抽油
采出。
采油方法-螺杆泵采油
螺杆泵是一种新型的机械采油设备。 苏联于1973年首先研制成功采油用井下 单螺杆泵,之后,美国、加拿大、法国 等一些国家也相继研制和应用了螺杆泵 采油。我国从1986年开始引进和使用螺 杆泵采油。
设备。
(2)抽油泵: 机械能转化为流体压能的设备
主要组成
工作筒(外筒和衬套)、柱塞及游动阀 (排出阀)和固定阀(吸入阀)
- 1、下载文档前请自行甄别文档内容的完整性,平台不提供额外的编辑、内容补充、找答案等附加服务。
- 2、"仅部分预览"的文档,不可在线预览部分如存在完整性等问题,可反馈申请退款(可完整预览的文档不适用该条件!)。
- 3、如文档侵犯您的权益,请联系客服反馈,我们会尽快为您处理(人工客服工作时间:9:00-18:30)。
第三章有杆泵采油有杆泵一般是指利用抽油杆上下往复运动所驱动的柱塞式抽油泵。
有杆泵采油具有结构简单、适应性强和寿命长的特点,是目前国内外应用最广泛的机械采油方式。
本章将系统地介绍游梁式抽油机有杆抽油装置、采油原理、工艺设计及油井工况分析方法。
第一节有杆抽油装置典型的有杆抽油装置主要由三部分组成,如图3-1所示。
一是地面驱动设备即抽油机;二是安装在油管柱下部的抽油泵;三是抽油杆柱,它把地面设备的运动和动力传递给井下抽油泵柱塞使其上下往复运动,使油管柱中的液体增压,将油层产液抽汲至地面。
就整个有杆抽油生产系统而言,还包括供给流体的油层、用于悬挂抽油泵并作为举升流体通道的油管柱、井下器具(油管锚、气锚、砂锚等)、油套管环形空间及井口装置等。
图3-1 典型的有杆抽油生产系统1-吸入阀;2-泵筒;3-排出阀;4-柱塞;5-抽油杆;6-动液面;7-油管;8-套管;9-三通;10-盘根盒;11-光杆;12-驴头;13-游梁;14-连杆;15-曲柄;16-减速器;17-动力机(电动机)一、抽油机抽油机(pumping unit)是有杆抽油的地面驱动设备。
按其基本结构抽油机可分为游梁式和无游梁式两大类,目前国内外应用最为广泛的是游梁式抽油机(俗称磕头机)。
游梁式抽油机主要由游梁—连杆—曲柄(四连杆)机构、减速机构(减速器)、动力设备(电动机)和辅助装置等四部分组成,如图3-2所示。
游梁式抽油机工作时,传动皮带将电机的高速旋转运动传递给减速器的输入轴,经减速后由低速旋转的曲柄通过四连杆机构带动游梁作上下往复摆动。
游梁前端圆弧状的驴头经悬绳器带动抽油杆柱作上下往复直线运动。
根据结构形式不同游梁式抽油机分为常规型(普通型),异相型、前置型和异型等类型。
常规型和前置型是游梁式抽油机的两种基本型式。
1.常规型抽油机常规型游梁抽油机如图3-2所示。
它是目前油田使用最广的一种抽油机。
其结构特点是:支架位于游梁的中部,驴头和曲柄连杆分别位于游梁的两端,曲柄轴中心基本位于游梁尾轴承的正下方,上下冲程运行时间相等。
图3-2 常规型游梁式抽油机结构1-刹车装置;2-电动机;3-减速器皮带轮;4-减速器;5-输入轴;6-中间轴;7-输出轴;8-曲柄;9-连杆轴;10-支架;11-曲柄平衡块;12-连杆;13-横船轴;14-横船;15-游梁平衡块;16-游梁;17-支架轴;18-驴头;19-悬绳器;20-底座2. 异相型抽油机异相型抽油机是上世纪七十年代发展起来的一种性能较好的抽油机,如图3-3所示。
从外形上看,它与常规型抽油机并无显著差别,故常规型与异相型也称后置型抽油机。
其结构特点是:曲柄轴中心与游梁尾轴承存在一定的水平距离;曲柄平衡重臂中心线与曲柄中心线存在偏移角(曲柄平衡相位角)。
使得上冲程的曲柄转角明显大于下冲程,从而降低了上冲程的运行速度、加速度和动载荷,达到减小抽油机载荷、延长抽油杆寿命和节能的目的。
图3-3 异相型游梁式抽油机结构1-刹车装置;2-电动机;3-减速器皮带轮;4-减速器;5-曲柄;6-曲柄平衡块;7-支架;8-曲柄平衡重臂;9-连杆;10-游梁;11-驴头;12-悬绳器;13-底座3.前置型抽油机前置型抽油机(mark II pumping unit)如图3-4所示。
其结构特点是:支架位于游梁的一端,驴头和曲柄连杆同位于另一端。
在相同曲柄半径下,前置型的冲程长度明显大于常规型,抽油机的规格尺寸较常规型小巧。
这种抽油机上冲程运行时间长于下冲程运行时间,从而降低了上冲程的运行速度、加速度和动载荷。
前置型多为重型长冲程抽油机,除采用机械平衡方式外,还有采用气动平衡方式。
图3-4 前置型游梁式抽油机结构1-驴头;2-游梁;3-横梁;4-连杆;5-减速器;6-悬挂器;7-曲柄销;8-支架;9-曲柄;10-底座;11-电动机;12-刹车装置我国游梁式抽油机型号表示法如下:例如:规格代号为8-3-37的常规型游梁式抽油机,减速器采用点啮合双圆弧齿轮,平衡方式为曲柄平衡,型号为CYJ8-3-37HB。
表示抽油机的额定悬点载荷为80kN,光杆悬点最大冲程为3m,减速器额定扭矩为37kN·m。
为了增大冲程、节能及改善抽油机的结构特性和受力状态,国内外还发展了许多变形游梁式抽油机,如双驴头、旋转驴头、调径变矩、下偏杠铃以及斜井游梁式抽油机等。
为了扩大有杆抽油方式的适用范围,改善其技术经济指标,国内外还发展了许多不同类型的无游梁抽油机(特别超长冲程抽油机),如链条式、增距式和宽带式抽油机等,多为长冲程和慢冲次,以适应深井和稠油的特殊需要。
二、抽油泵抽油泵(有杆泵sucker rod pump)是有杆抽油系统的井下关键设备,安装在油管柱的下部,沉没在井液中,通过抽油机、抽油杆传递的动力抽汲井内的液体。
它所抽汲的液体中常会含有蜡、砂、气、水及腐蚀性物质,在数百米到上千米的井下工作,泵内压力会高达20MPa 以上。
为了使抽油泵能适应井下复杂的工作环境和恶劣的条件,对抽油泵基本要求是:结构简单、强度高;工作可靠,使用寿命长;便于起下而且规格类型能满足不同油田的采油工艺需要。
1.泵的工作原理抽油泵主要由泵筒、柱塞、固定阀和游动阀四部分组成。
泵筒即为缸套,其内装有带游动阀的柱塞。
柱塞与泵筒形成密封,用于从泵筒内排出液体。
固定阀(standing valve)为泵的吸入阀(intake valve),一般为球座型单流阀,抽油过程中该阀位置固定。
游动阀(traveling valve)为泵的排出阀(exhaust valve),它随柱塞运动。
柱塞上下运动一次称一个冲程,也称一个抽汲周期,其间完成泵进液和排液过程,如图3-5所示。
图3-5 泵的工作原理(a )上冲程(吸液进泵); (b )下冲程(排液出泵)1)上冲程在理想情况下,抽油杆柱向上拉动柱塞,如图3-5(a )所示。
柱塞上的游动阀受油管内液柱压力一开始就关闭。
此时,泵内(柱塞下面的)容积增大,压力降低,固定阀在油套环空液柱压力(沉没压力)与泵内压力之差的作用下被打开,原油被吸入泵内。
与此同时,如果油管内已逐渐被液体所充满,柱塞上面的一段液体将沿油管排到地面。
所以,上冲程是泵内吸入液体,井口排出液体的过程。
造成吸液进泵的条件是泵内压力(吸入压力)低于沉没压力。
2)下冲程抽油杆柱向下推动柱塞,如图3-5(b )所示。
固定阀一开始就关闭,柱塞挤压固定阀和游动阀之间的液体,使泵内压力增高。
当泵内压力增加到大于柱塞以上液体压力时,游动阀被顶开,柱塞下面的液体通过游动阀进入柱塞上面,使泵排出液体。
由于有相当于冲程长度的一段光杆从井外进入油管,井口将排挤出相当于这段光杆体积的液体。
所以,下冲程是泵向油管内排液的过程,造成泵排出液体的条件是泵内压力高于柱塞以上的液柱压力。
2.泵的理论排量泵的工作过程是由三个基本环节组成:柱塞在泵内让出容积、原油进泵和从泵内排出原油。
在理想情况下,柱塞上下一次吸入和排出的液体体积相等,即等于柱塞在上行时走过的几何体积A P S 。
所以,泵的理论排量(pump displacement )为Sn A Q p t 1440 (3-1) 式中 Q t ——泵的理论体积排量,m 3/d ;A p ——柱塞截面积(πD 2/4),m 2;D ——泵径,m ;S ——光杆冲程,m ;n ——冲次,min -1。
3. 抽油泵类型和结构按抽油泵在油管中的固定方式分为管式泵和杆式泵两大类型。
通常对于符合抽油泵标准设计和制造的抽油泵称为常规泵;而具有专门用途,如稠油泵、防气泵、防砂卡泵等,与标准结构不同的泵称为特殊泵或专用泵。
抽油泵又分为整筒泵和组合泵(衬套泵)。
组合泵的外筒内装有多节衬套组成泵筒,并与金属柱塞配套;而整筒泵没有衬套;与软密封柱塞配套。
SYS5059-91标准抽油泵的基本型式如图3-6所示。
图3-6 抽油泵基本型式1—定筒式杆式泵;厚壁泵筒,顶部定位,组合泵筒,顶部定位2—定筒式杆式泵;薄壁泵筒,顶部定位,薄壁泵筒,顶部定位,软密封柱塞3—定筒式杆式泵;厚壁泵筒,底部定位,组合泵筒,底部定位4—定筒式杆式泵;薄壁泵筒,底部定位,薄合泵筒,底部定位,软密封柱塞5—动筒式杆式泵;厚壁泵筒,底部定位,组合泵筒,底部定位6—动筒式杆式泵;薄壁泵筒,底部定位,薄合泵筒,底部定位,软密封柱塞7—厚壁泵筒或组合泵筒管式泵8—厚壁泵筒管式泵,软密封柱塞1)管式泵图3-6中7和8为管式泵(tubing pump)的结构图。
管式泵一般将泵筒在地面组装好后由油管接箍直接连接在油管下部下入到设计的泵挂深度处,然后投入可打捞的固定阀装置,最后把柱塞连接在抽油杆柱下端下入泵筒内。
检泵打捞固定阀时,通常采用两种方法:一种是利用柱塞下部的卡扣或丝扣起抽油杆柱时捞上来;另一种是柱塞下部无打捞装置,在起出抽油杆柱和柱塞后,用绞车、钢丝绳下入专门的打捞工具将固定阀捞出。
管式泵的结构简单、成本低,在相同油管直径下允许下入的泵径较杆式泵大,因而排量大。
但起下泵作业时,需要起下全部油管,且修井作业时间长,费用高。
故管式泵适用于下入深度不大,产量较高的油井。
2)杆式泵杆式泵(insert pump)是将整个泵在地面组装成套后,随抽油杆柱插入油管内的预定位置固定,故又称为“插入式泵”。
杆式泵又按其固定方式分为以下三种:(1)定筒式顶部固定杆式泵。
其柱塞经阀杆与抽油杆连接,并作上下运动。
由泵顶部的固定支承装置将泵筒固定在油管内的预定位置上,如图3-6中1、2所示。
(2)定筒式底部固定杆式泵。
其柱塞与抽油杆柱连接,并作上下运动。
由泵的底部锁紧装置将泵筒固定在油管内的预定位置上,如图3-6中3、4所示。
(3)动筒式底部固定杆式泵。
其泵筒与抽油杆柱连接,并作上下运动。
柱塞通过拉管及底部锁紧装置固定在油管内预定位置的支承套上,如图3-6中5、6所示。
杆式泵与管式泵相比结构复杂,制造成本高。
在相同油管直径下允许下入的泵径较管式泵小。
但杆式泵是整泵通过油管下井,泵内各精密部件得到良好保护,不易损伤柱塞;起下泵时无需起下油管,检泵方便;可用于深井。
另外,它还有形式多样,选择余地大等优点。
在国外,大部分有杆泵井都使用杆式泵,目前我国也正在逐步推广使用。
3 ) 组合泵为了减少磨损、防止砂卡,国内常用带环状槽的金属柱塞。
金属柱塞与其相配合的衬管其加工要求高,制造不便,易于磨损。
为了便于加工和保证质量,衬管分段加工,然后组装在泵筒内,这类泵称为衬管泵或组合泵。
这类泵在长途运输和使用中易发生“错缸”即衬管错位。
4 ) 整筒泵(软密封柱塞泵)前面介绍的都是金属柱塞泵。
软密封柱塞泵只是柱塞与金属柱塞不同,其余结构与金属柱塞泵相同。
软密封柱塞泵具有在压力作用下能扩大直径和材质较软的特点,柱塞与泵筒内表面可以不经表面硬化处理。