压铸模的表面处理
锌合金压铸件表面处理

锌合金压铸件表面处理1. 简介锌合金压铸件是一种常见的金属零件,具有很高的强度和耐腐蚀性。
然而,其表面通常需要进行处理以提高外观和性能。
本文将详细介绍锌合金压铸件表面处理的方法和技术。
2. 表面处理方法2.1 机械处理机械处理是锌合金压铸件表面处理的基本方法之一。
它包括去毛刺、抛光和打磨等步骤。
去毛刺可以通过机械切削或研磨来完成,以去除零件表面的毛刺和尖锐边缘。
抛光和打磨则可以提高零件表面的光洁度和平整度。
2.2 化学处理化学处理是锌合金压铸件表面处理的另一种常用方法。
它主要包括酸洗、电镀和化学转化膜等过程。
酸洗可以去除锌合金表面的氧化物和污垢,提供一个干净的表面用于后续处理。
电镀可以在锌合金表面形成一层金属镀层,提高其外观和耐腐蚀性。
化学转化膜则可以在锌合金表面形成一层化学转化膜,提高其耐磨性和耐腐蚀性。
2.3 热处理热处理是一种常用的锌合金压铸件表面处理方法。
它包括热处理和热喷涂两种方式。
热处理可以改变锌合金的组织结构和性能,提高其硬度和强度。
热喷涂则可以在锌合金表面形成一层涂层,提高其耐磨性和耐腐蚀性。
3. 表面处理技术3.1 硅溶胶处理硅溶胶处理是一种常用的锌合金压铸件表面处理技术。
它通过在锌合金表面形成一层硅溶胶膜来提高其耐腐蚀性和耐磨性。
硅溶胶处理可以在常温下进行,具有成本低、工艺简单和效果显著的优点。
3.2 电化学抛光电化学抛光是一种通过电化学方法去除锌合金表面的氧化物和污垢的技术。
它可以提高锌合金表面的光洁度和平整度,使其具有更好的外观和耐腐蚀性。
3.3 电镀技术电镀技术是一种常用的锌合金压铸件表面处理技术。
它可以在锌合金表面形成一层金属镀层,如镍、铬或锌等,以提高其外观和耐腐蚀性。
电镀技术可以根据需要选择不同的金属镀层,以满足不同的要求。
3.4 化学转化膜技术化学转化膜技术是一种通过化学反应在锌合金表面形成一层转化膜的技术。
转化膜可以提高锌合金表面的耐磨性和耐腐蚀性,同时保持其原有的外观。
铝合金压铸件表面处理方法
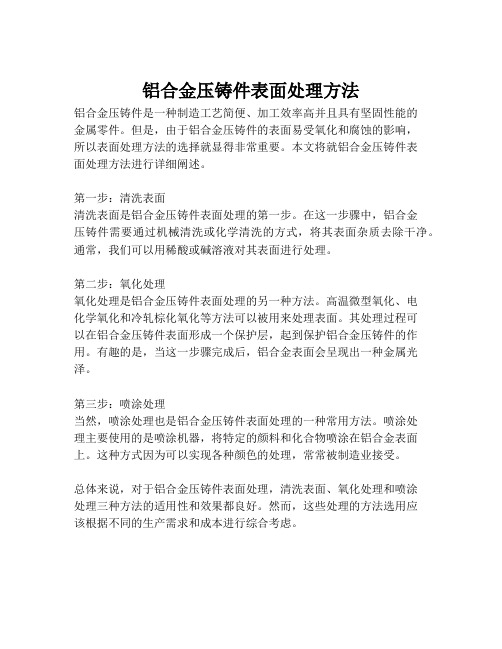
铝合金压铸件表面处理方法
铝合金压铸件是一种制造工艺简便、加工效率高并且具有坚固性能的
金属零件。
但是,由于铝合金压铸件的表面易受氧化和腐蚀的影响,
所以表面处理方法的选择就显得非常重要。
本文将就铝合金压铸件表
面处理方法进行详细阐述。
第一步:清洗表面
清洗表面是铝合金压铸件表面处理的第一步。
在这一步骤中,铝合金
压铸件需要通过机械清洗或化学清洗的方式,将其表面杂质去除干净。
通常,我们可以用稀酸或碱溶液对其表面进行处理。
第二步:氧化处理
氧化处理是铝合金压铸件表面处理的另一种方法。
高温微型氧化、电
化学氧化和冷轧棕化氧化等方法可以被用来处理表面。
其处理过程可
以在铝合金压铸件表面形成一个保护层,起到保护铝合金压铸件的作用。
有趣的是,当这一步骤完成后,铝合金表面会呈现出一种金属光泽。
第三步:喷涂处理
当然,喷涂处理也是铝合金压铸件表面处理的一种常用方法。
喷涂处
理主要使用的是喷涂机器,将特定的颜料和化合物喷涂在铝合金表面上。
这种方式因为可以实现各种颜色的处理,常常被制造业接受。
总体来说,对于铝合金压铸件表面处理,清洗表面、氧化处理和喷涂
处理三种方法的适用性和效果都良好。
然而,这些处理的方法选用应
该根据不同的生产需求和成本进行综合考虑。
压铸模具表面处理工艺

压铸模具表面处理工艺嘿,朋友们!今天咱就来唠唠压铸模具表面处理工艺这档子事儿。
咱先说说这压铸模具啊,那可是生产各种零部件的大功臣呢!但要让它更好地发挥作用,这表面处理可就相当重要啦。
有一次啊,我和几个同行凑一块儿聊天。
我就说:“你们说这压铸模具表面处理就像给它化个妆,让它变得更漂亮更耐用。
”一个朋友立马接话:“可不是嘛,就跟咱人出门得拾掇得精神点儿一个道理。
”另一个朋友也笑着说:“对对对,处理好了,这模具工作起来也更带劲!”咱常见的表面处理方法有好几种呢。
比如说氮化处理,这就好比给模具穿上一层坚固的铠甲,让它更耐磨、更耐腐蚀。
还有电镀,这就像给模具披上一层闪亮的外衣,不仅好看还实用。
我记得有一次在工厂里,师傅正在给一个压铸模具做表面处理。
我好奇地凑过去问:“师傅,这氮化处理有啥讲究不?”师傅一边忙活着一边说:“小子,这讲究可大了去了。
温度、时间都得把握好,不然效果可就差远喽。
”我似懂非懂地点点头。
还有一次,看到一个经过电镀处理的模具,那表面亮闪闪的,我忍不住伸手摸了摸,旁边的工人大哥笑着说:“嘿,可别乱摸,这可是宝贝呢!”我赶忙缩回手,嘿嘿笑了。
除了这些,还有好多其他的表面处理工艺呢,每一种都有它独特的作用和好处。
就拿热喷涂来说吧,这能让模具的表面具备特殊的性能,就像给它加了个超级技能。
总之啊,压铸模具表面处理工艺那是相当重要。
咱可不能小瞧了它,得认真对待,选对方法,让咱的模具发挥出最大的价值。
就像咱人一样,好好打扮打扮自己,才能更自信地面对生活和工作嘛。
所以啊,朋友们,一定要重视这压铸模具表面处理工艺哦!这就是我的看法,咱就这么着吧!。
压铸模的表面处理
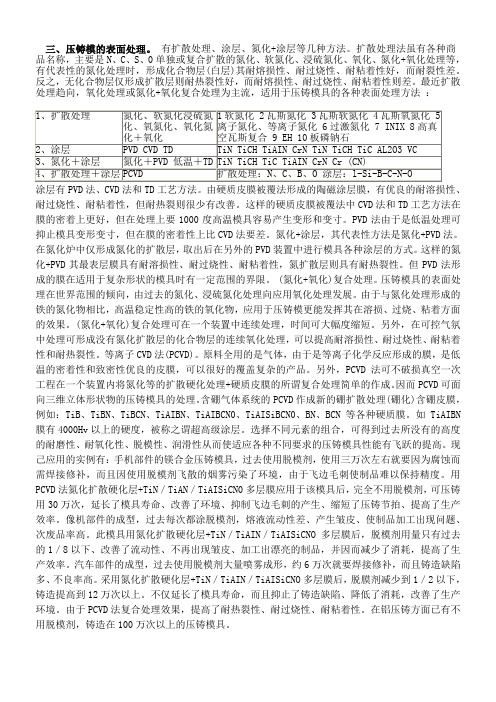
三、压铸模的表面处理。
有扩散处理、涂层、氮化+涂层等几种方法。
扩散处理法虽有各种商品名称,主要是N、C、S、0单独或复合扩散的氮化、软氮化、浸硫氮化、氧化、氮化+氧化处理等,有代表性的氮化处理时,形成化合物层(白层)其耐熔损性、耐过烧性、耐粘着性好,而耐裂性差。
反之,无化合物层仅形成扩散层则耐热裂性好,而耐熔损性、耐过烧性、耐粘着性则差。
最近扩散处理趋向,氧化处理或氮化+氧化复合处理为主流,适用于压铸模具的各种表面处理方法:涂层有PVD法、CVD法和TD工艺方法。
由硬质皮膜被覆法形成的陶磁涂层膜,有优良的耐溶损性、耐过烧性、耐粘着性,但耐热裂则很少有改善。
这样的硬质皮膜被覆法中CVD法和TD工艺方法在膜的密着上更好,但在处理上要1000度高温模具容易产生变形和变寸。
PVD法由于是低温处理可抑止模具变形变寸,但在膜的密着性上比CVD法要差。
氮化+涂层,其代表性方法是氮化+PVD法。
在氮化炉中仅形成氮化的扩散层,取出后在另外的PVD装置中进行模具各种涂层的方式。
这样的氮化+PVD其最表层膜具有耐溶损性、耐过烧性、耐粘着性,氮扩散层则具有耐热裂性。
但PVD法形成的膜在适用于复杂形状的模具时有一定范围的界限。
(氮化+氧化)复合处理。
压铸模具的表面处理在世界范围的倾向,由过去的氮化、浸硫氮化处理向应用氧化处理发展。
由于与氮化处理形成的铁的氮化物相比,高温稳定性高的铁的氧化物,应用于压铸模更能发挥其在溶损、过烧、粘着方面的效果。
(氮化+氧化)复合处理可在一个装置中连续处理,时间可大幅度缩短。
另外,在可控气氛中处理可形成没有氮化扩散层的化合物层的连续氧化处理,可以提高耐溶损性、耐过烧性、耐粘着性和耐热裂性。
等离子CVD法(PCVD)。
原料全用的是气体,由于是等离子化学反应形成的膜,是低温的密着性和致密性优良的皮膜,可以很好的覆盖复杂的产品。
另外,PCVD法可不破损真空一次工程在一个装置内将氮化等的扩散硬化处理+硬质皮膜的所谓复合处理简单的作成。
压铸件的表面处理.

压铸件的表面处理 对压铸件进行表面处理就是要改善压铸件的表面状态,增厚表面氧化 膜或者形成新的表面模,以提高压铸件表面的耐蚀性、装饰性或达到
其它学要的特性。
压铸件常用的表面处理方法有化学转化处理、阳极氧化处理、电 镀和涂装等。为了获得满意的表面处理效果,需在处理之前对压铸件
进行预处理,包括机械预处理(磨光、抛光、喷砂等)和化学预处理
(脱脂、酸洗和碱洗). 铝合金压铸件的电镀可以改善压铸件装饰性、提高表面硬度和耐磨 性、改善润滑性以及提高表面导电性和反光率等。实际生产中除非有 特殊要求时,铝合金压铸件一般很少采用电镀处理。
材料工程学院材料成型教研室
压铸模具表面处理的最新方法

压铸模具表面处理的最新方法压铸模具是模具在一个大的类。
随着中国汽车摩托车产业的快速发展,铸造业,迎来了一个新的发展时期。
同时,也压铸模具,生活,并提出了更高的要求的机械性能。
为了满足日益增长的性能需求仅仅依靠新的模具材料的应用仍然很难满足,必须适用于各种表面处理技术的压铸模具压铸模具能达到较高的表面处理效率,高精度和高寿命。
在各种模具中,压铸模具是更苛刻的工作条件。
压力铸造是使熔融金属在高压和高速下压力铸造模具腔内充满的,当然他们的工作,多次与热金属接触,因此要求较高的耐热耐压铸模具的疲劳,导热磨损,耐腐蚀的性质,冲击韧性,红硬性,良好的脱模等。
因此,压铸模具表面处理技术要求近年来,各种压铸模具表面处理新技术不断涌现,但大体上可分为以下三大类:(1)改善传统的热处理工艺技术;(2)表面改性技术,包括表面热膨胀渗透处理,表面相变强化,增强技术的火花;(3)镀膜技术,包括化学镀等。
一个传统的散热改进的技术处理过程压铸模具传统的热处理工艺是淬火 - 回火,后来发展了表面处理技术。
由于可作为压铸模具使用的多种材料,相同的表面处理技术,并在不同的材料使用过程会产生不同的结果。
马尔可夫近代历史上对模具基体材料和表面处理技术,的基材预处理技术,在传统工艺,根据不同的模具材料,提出相应的处理技术,以提高模具性能,提高模具寿命。
另一个热处理技术提高的发展方向是传统的热处理工艺和先进的表面处理工艺相结合,提高压铸模具的使用寿命。
如果化学热处理碳氮共渗,与常规淬火,回火过程相结合的NQN的治疗方法(即碳氮共渗 - 淬火 - 碳氮共渗)复合材料的加强,不仅具有较高的表面硬度和有效硬化层深度的增加,硬度梯度分布层是合理的,回火稳定性和耐蚀性提高,从而以压铸模具在获得良好的心脏,而物业部,表面质量和性能大大提高。
2.表面改性技术2.1表面的热膨胀渗透这种类型的,包括渗碳,渗氮,碳氮共渗硼,硫碳氮共渗,等。
2 1 1渗碳和碳氮共渗渗碳工艺,冷,热和塑料模具表面强化中使用,可以提高模具寿命。
压铸件表面处理的常用工艺

温馨小提示:本文主要介绍的是关于压铸件表面处理的常用工艺的文章,文章是由本店铺通过查阅资料,经过精心整理撰写而成。
文章的内容不一定符合大家的期望需求,还请各位根据自己的需求进行下载。
本文档下载后可以根据自己的实际情况进行任意改写,从而已达到各位的需求。
愿本篇压铸件表面处理的常用工艺能真实确切的帮助各位。
本店铺将会继续努力、改进、创新,给大家提供更加优质符合大家需求的文档。
感谢支持!(Thank you for downloading and checking it out!)压铸件表面处理的常用工艺一、压铸件表面处理概述压铸件表面处理的定义:压铸件表面处理是指对压铸件表面进行的一系列加工处理,以改善其表面质量、提高外观装饰效果、增强防护性能和满足使用要求的过程。
它主要包括去除铸件表面的缺陷、污垢、氧化皮等,以及进行各种表面涂覆、抛光、防锈等处理。
压铸件表面处理的目的和意义:压铸件表面处理的目的主要是为了提高铸件的表面质量,使其满足客户对产品外观和性能的要求。
表面处理的意义在于:提高铸件的装饰效果,增强产品的市场竞争力;提高铸件的防护性能,延长产品的使用寿命;提高铸件的机械性能,增强其耐磨、耐腐蚀等性能;满足特殊使用要求,如航空、汽车等行业的严苛环境。
压铸件表面处理的分类:压铸件表面处理主要包括以下几类:去披锋、抛光、喷漆、电镀、阳极氧化、喷塑、防锈处理等。
去披锋主要是去除铸件表面的尖角、毛刺等缺陷,保证铸件表面的光滑度;抛光则是通过机械或化学方法使铸件表面达到更高的光洁度;喷漆和喷塑是在铸件表面形成一层保护膜,起到防锈、美化等作用;电镀和阳极氧化则是在铸件表面形成一层耐磨、耐腐蚀的金属或氧化膜,提高其防护性能;防锈处理则是针对铸件的防锈、防腐蚀处理,延长其使用寿命。
二、常用压铸件表面处理工艺在压铸件生产过程中,为了提高其表面质量和使用性能,常常需要进行一系列的表面处理工艺。
这些工艺主要包括机械处理、化学处理、电化学处理、热处理和表面涂装等。
压铸件清理及表面处理新技术研讨

压铸件清理及表面处理新技术研讨第二章压铸件清理及表面处理新技术第一节压铸件清理清理的口的:①去除毛刺;②去除表面流痕;③去除表面附着涂料;④获得表面均匀的光滑度。
一、去除浇口、飞边的方法1)手T.作业:利用木槌、键刀、钳子等简单工具敲打去除铸件浇注系统等多余部分,优点是方便、简单、快捷;缺点是切口不整齐,易损伤铸件及变形,对浇口厚的件、复杂件、大的铸件不适用。
2)机械作业:采用切边机、冲床和冲模、带锯机等机械设备。
优点是切口整齐,对于大、中型铸件清理效率高。
图2- 1为用下落式冲模去除浇口。
3)抛光:根据铸件要求选择钢砂轮、尼龙轮、布轮、t翼轮、研磨轮等进行打磨处理。
4)清理过程自动化:采用机器人进行铸件清理,完成去除匕边、打磨、修整等工作。
从而实现清洁、高效率的生产。
二、抛丸清理(1)作用1)去除铸件表面氧化皮及杂质,去除毛刺,去除表面涂层。
图2-1下落式冲模日2)表面毛化,表面清理,表面精整,表面强化。
(2)原理弹丸在抛丸轮的作用下,以很高的速度射向铸件,见图2-2。
撞击铸件表面, 使其吸收高速运动弹丸的动能后产生塑性变形,呈现残余压应力,从而提高铸件表面强度,抗疲劳强度和抗腐蚀能力。
达到清理和强化的目的。
(3)获得良好清理效果的条件1)选择合适的弹丸:俾丸的材质、性能(硬度)、尺寸。
当抛射速度一定时,大的弹丸动能大,有利于撞击去除大的杂质,清理效果好,但铸件表面质量不够好; 小的弹丸动能小,可用于去除小的杂质,铸件表面质量好,但清理效率低。
锌、铝合金压铸件可采用不锈钢丸,弹丸尺寸可选择0.14〜Irnm不等,抛出产品表面光亮、纹理细致、不变色、抗腐蚀能力强、涂装附着力好。
2)抛射速度和抛射生:弹丸具仃足够的能量,才能清理铸件。
山公式E = 加/〃可知,弹丸动能£的大小取决于弹丸的质量机和抛射速度z,。
皿。
厂而式中:r为弹丸速度(m/s), n为抛丸轮传速(r/min), 〃为抛丸轮直径(m)。
浅析压铸模具防损伤表面处理技术
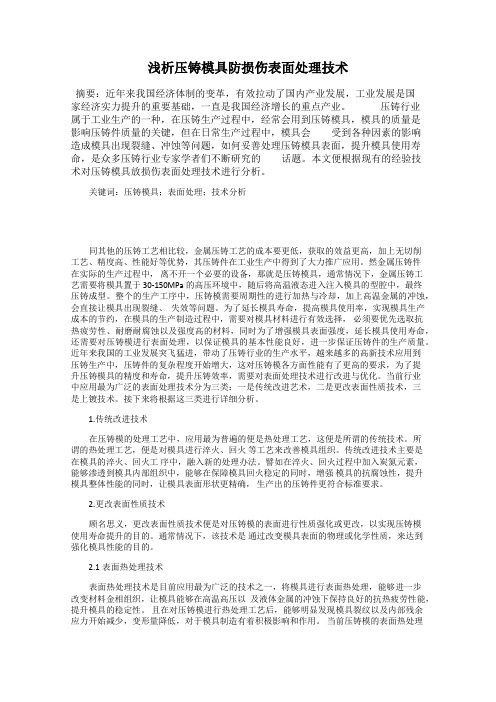
浅析压铸模具防损伤表面处理技术摘要:近年来我国经济体制的变革,有效拉动了国内产业发展,工业发展是国家经济实力提升的重要基础,一直是我国经济增长的重点产业。
压铸行业属于工业生产的一种,在压铸生产过程中,经常会用到压铸模具,模具的质量是影响压铸件质量的关键,但在日常生产过程中,模具会受到各种因素的影响造成模具出现裂缝、冲蚀等问题,如何妥善处理压铸模具表面,提升模具使用寿命,是众多压铸行业专家学者们不断研究的话题。
本文便根据现有的经验技术对压铸模具放损伤表面处理技术进行分析。
关键词:压铸模具;表面处理;技术分析同其他的压铸工艺相比较,金属压铸工艺的成本要更低,获取的效益更高,加上无切削工艺、精度高、性能好等优势,其压铸件在工业生产中得到了大力推广应用。
然金属压铸件在实际的生产过程中,离不开一个必要的设备,那就是压铸模具,通常情况下,金属压铸工艺需要将模具置于 30-150MPa 的高压环境中,随后将高温液态进入注入模具的型腔中,最终压铸成型。
整个的生产工序中,压铸模需要周期性的进行加热与冷却,加上高温金属的冲蚀,会直接让模具出现裂缝、失效等问题。
为了延长模具寿命,提高模具使用率,实现模具生产成本的节约,在模具的生产制造过程中,需要对模具材料进行有效选择,必须要优先选取抗热疲劳性、耐磨耐腐蚀以及强度高的材料,同时为了增强模具表面强度,延长模具使用寿命,还需要对压铸模进行表面处理,以保证模具的基本性能良好,进一步保证压铸件的生产质量。
近年来我国的工业发展突飞猛进,带动了压铸行业的生产水平,越来越多的高新技术应用到压铸生产中,压铸件的复杂程度开始增大,这对压铸模各方面性能有了更高的要求,为了提升压铸模具的精度和寿命,提升压铸效率,需要对表面处理技术进行改进与优化。
当前行业中应用最为广泛的表面处理技术分为三类:一是传统改进艺术,二是更改表面性质技术,三是上镀技术。
接下来将根据这三类进行详细分析。
1.传统改进技术在压铸模的处理工艺中,应用最为普遍的便是热处理工艺,这便是所谓的传统技术。
铝合金压铸制品常见表面处理
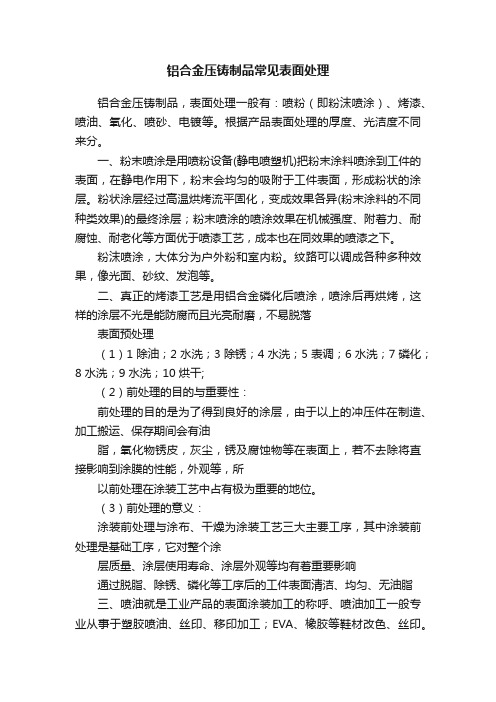
铝合金压铸制品常见表面处理铝合金压铸制品,表面处理一般有:喷粉(即粉沫喷涂)、烤漆、喷油、氧化、喷砂、电镀等。
根据产品表面处理的厚度、光洁度不同来分。
一、粉末喷涂是用喷粉设备(静电喷塑机)把粉末涂料喷涂到工件的表面,在静电作用下,粉末会均匀的吸附于工件表面,形成粉状的涂层。
粉状涂层经过高温烘烤流平固化,变成效果各异(粉末涂料的不同种类效果)的最终涂层;粉末喷涂的喷涂效果在机械强度、附着力、耐腐蚀、耐老化等方面优于喷漆工艺,成本也在同效果的喷漆之下。
粉沫喷涂,大体分为户外粉和室内粉。
纹路可以调成各种多种效果,像光面、砂纹、发泡等。
二、真正的烤漆工艺是用铝合金磷化后喷涂,喷涂后再烘烤,这样的涂层不光是能防腐而且光亮耐磨,不易脱落表面预处理(1)1 除油;2 水洗;3 除锈;4 水洗;5 表调;6 水洗;7 磷化;8 水洗;9 水洗;10 烘干;(2)前处理的目的与重要性:前处理的目的是为了得到良好的涂层,由于以上的冲压件在制造、加工搬运、保存期间会有油脂,氧化物锈皮,灰尘,锈及腐蚀物等在表面上,若不去除将直接影响到涂膜的性能,外观等,所以前处理在涂装工艺中占有极为重要的地位。
(3)前处理的意义:涂装前处理与涂布、干燥为涂装工艺三大主要工序,其中涂装前处理是基础工序,它对整个涂层质量、涂层使用寿命、涂层外观等均有着重要影响通过脱脂、除锈、磷化等工序后的工件表面清洁、均匀、无油脂三、喷油就是工业产品的表面涂装加工的称呼、喷油加工一般专业从事于塑胶喷油、丝印、移印加工;EVA、橡胶等鞋材改色、丝印。
拥有喷涂线、丝印线、移印机等设备,并可根据客户要求,生产耐高温、耐摩擦、耐紫外、耐酒精、耐汽油等产品。
加工范围:电子产品:普通喷漆、PU漆、橡胶漆(手感漆)、(如:U盘、MP3、摄像头、网络周边产品及其它电子产品。
),可喷涂注塑加工遇到的难以解决的问题,如气纹、熔接缝等,具有喷涂橡胶漆(手感漆)经验,具备手感漆返工技术。
压铸模具表面处理

压铸模具表面处理在压铸模具的制造过程中,表面处理是至关重要的一个环节。
正确的表面处理能够保证模具的质量、寿命和生产效率。
本文将介绍压铸模具表面处理的基本流程和方法。
表面处理流程对于压铸模具的表面处理流程,一般可以分为以下几个步骤:去毛刺在模具的制造过程中,如果不对模具进行去毛刺处理,那么产生的毛刺将会影响模具的精度和表面质量。
因此,在模具生产完成后,必须进行去毛刺处理。
去毛刺的方法可以是手动去毛刺、机械去毛刺或者化学去毛刺等。
具体选择哪种去毛刺方法,需要根据模具的材料和形状来做出合理的选择。
打磨和抛光模具表面的打磨和抛光是为了提高模具的表面质量和减小模具表面的粗糙度,从而使产品的表面更加光滑。
打磨和抛光的方法可以是手动或者机械。
镀膜镀膜是为了保护模具表面和提高模具的使用寿命,在模具表面涂上一层特殊的化合物,可以起到抗磨、防腐、隔热、抗氧化等作用。
有许多种镀膜方法,比较常见的是电镀、喷涂和真空镀膜。
表面处理方法针对不同的材料、用途和形状,压铸模具的表面处理方法也会有所不同,下面将介绍一些常见的表面处理方法:氮气淬火氮气淬火是在模具表面形成一层硬度高、膜厚薄的氮化层,可以提高模具表面的硬度和耐磨性,从而延长模具的使用寿命。
氮化氮化是一种常见的表面处理方法,通过吸入氨气,让模具表面形成具有高硬度、耐磨性和耐腐蚀性的硬化层,可以提高模具的使用寿命和表面质量。
等离子氧化等离子氧化是一种将金属表面氧化并形成带有多孔结构的新表面的方法,可以形成均匀、致密和硬度高的氧化膜,适用于铝合金呈现良好的抗磨性、耐腐蚀性和美观性。
离子镀膜离子镀膜是一种高精度的表面处理方法,通过向金属表面喷发一层金属离子,使其在低温下甚至在室温下形成硬度极高的保护层,保障模具表面的深层和表层质量,适用于高要求的模具表面处理。
结论合理的表面处理方法可以有效地提高压铸模具的使用寿命和表面质量,增强产品的生产效率。
在具体选择表面处理方法时,需要考虑材料、形状、用途等因素,从而选出最适合的表面处理方法。
压铸件的表面处理,你不能不知
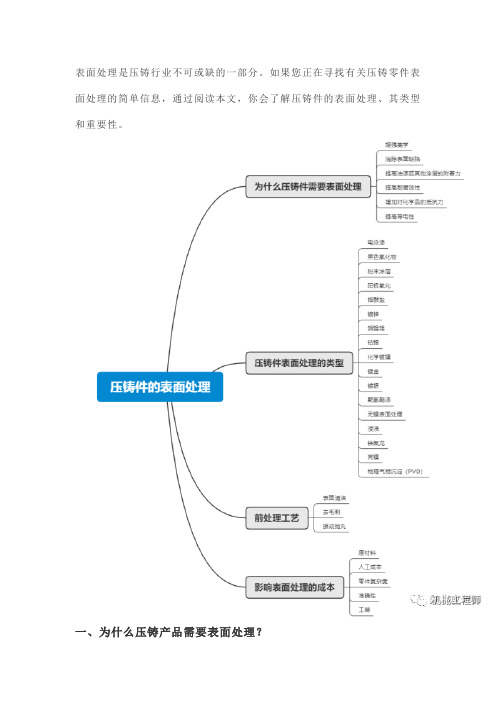
表面处理是压铸行业不可或缺的一部分。
如果您正在寻找有关压铸零件表面处理的简单信息,通过阅读本文,你会了解压铸件的表面处理、其类型和重要性。
一、为什么压铸产品需要表面处理?表面处理对于压铸表面很重要,因为它使最终产品看起来更精细,美观、使用寿命更长。
压铸件表面处理后获得的其他好处包括:1、增强美学压铸件表面处理有助于消除制造过程中产生的缺陷,从而使表面看起来干净、美观。
一些用于表面处理的方法可以使压铸件具有漂亮颜色和细腻的手感,增加了表面的审美价值。
2、消除表面缺陷各种表面处理工艺包括圆化尖角和从表面刮掉多余的残留物,表面打磨是常用的,这对于刮除制造过程中产生的所有缺陷最为有效。
3、提高油漆和其他涂料的附着力压铸件经过适当的表面处理后可降低粗糙度并使其光滑,这增加了表面吸收油漆和涂层的能力,从而形成更坚硬的层。
4、提高耐腐蚀性一些金属对水分具有高度反应性,暴露在大气中时会腐蚀,在涂饰过程中使用非腐蚀性涂层有助于防止金属腐蚀,从而提高它们的耐用性。
不同的表面光洁度也会产生不同的表面粗糙度,与光滑表面相比,较粗糙的表面更容易受到局部腐蚀形式的影响,例如点蚀和缝隙腐蚀。
5、增加对化学品的抵抗力表面装饰涉及用坚韧和高抗性材料覆盖表面,这使它们具有抵抗化学物质的能力。
6、提高导电性电镀通过增强其电性能来帮助提高原始零件的导电性,它会影响可焊性、耐用性和接触电阻。
在以电导率为至关重要的应用设计时,应该选择表面光洁度,以便电导率值适合应用。
二、表面处理的类型虽然有许多表面处理可供选择,但以下是最常用的表面处理。
1、电泳漆E-coat,也称为油漆沉积,是一种利用电力将油漆产品吸引到金属表面的过程。
它通常单独使用,因为它具有出色的覆盖率,但也可用作其他涂层(如粉末涂层)的底涂层。
传统上,它被用于保护等功能目的,而不是真正用于装饰目的。
诸如透明复合工艺之类的 E-coats 用于涂层广泛的消费品,包括珠宝、硬件、礼品、眼镜框等。
压铸模具的表面处理(完整版)

黏着的机理
• 黏着是指压铸产品与模具之间粘合,造成产 品和模具的表面损伤. A,原因 1,脱模剂没有均匀附着模具表面. 2,模具表面受到损伤 3,模具表面硬度偏低
黏着
B,解决方案 1,模具表面要有一定粗糙度,以利于脱模剂 的均匀附着.(ABP处理) 2,增加表面硬度和表面强度。(ASN处理)
ASSAB表面强化处理的定义
镁压铸模
AfterASN
AfterASO
ASN+ASO Case Study
Component : 电加热水壶 Tool type: Zn 压铸 Work material: 3# Zn 合金 Die Casting Type: Hot Chamber Working Load:150 T
Original Tool steel Hardness Surface treatment performance Failure due to 8407 50 HRC 使用早期发生侵 蚀 侵蚀 Replacement 8407 50HRC ASN+ASO 60,000 Still use
处理方法: 焊接+ ABP+ ASO 结果 : 20,000 模后发生侵蚀
NINGBO
ASN+ASO的应用
• ASN+ASO 搭配(特殊浅层氮化与蒸汽氧化)处理,既达 到了氮化的耐磨性,又有氧化膜隔离铝液。 从而提高模具抵抗冲蚀,侵蚀能力。(氮 化深层约3-5丝,氧化层3-5um.)
ASN+ASO
压铸模具表面强化处理
目录
一、模具的失效方式及解决方案 二、ABP: 提高模具抗热疲劳龟裂的表面处理 三、 ASO: 提高模具抗侵蚀性能的表面处理 四、ASN: 提高模具抗冲蚀性能的表面处理 五、ABP+ASN ABP+ASO ASN+ASO 套餐应用 六、未来计划
压铸件及表面处理零件外观检验标准

外观检验标准WI/DQ JS -07 A01.目的:规范统一压铸件及表面处理零件外观标准。
2.范围:适用于公司所生产的所有压铸件、表面处理零件产品,客户特别规定的除外。
3.权责:本标准由技术部编制,运用于判定产品外观缺陷及接收标准。
4.定义4.1压铸件、表面处理等级一级:产品外露表面即装饰表面,表面处理为抛光+电镀零件。
如执手、面板产品等。
二级:安装前可见的表面,壳体内表面等。
三级:结构件,非外露表面或零件。
4.2压铸件表面缺陷描述流痕:在表面出现波浪或条纹,原因为流入模具内的熔汤熔融状态不充分。
充填不良:由于模具充填不充分而导致零件部分缺省。
裂缝:由于外力产生微小的裂纹。
原因为铸件凝固收缩,或脱模时包紧力过大。
缩限:材料有像火山口一样的凹陷。
原因为铸件在肉厚处的收缩。
起泡:铸件表面的气孔,有像水泡或肿块凸起,为铸件开模或热处理时表面气体膨胀。
积炭:熔汤熔着模具表面,使得铸件表面产生缺肉或粗糙的现象。
模裂纹:模具表面有热裂纹的伤痕时使得铸件表面产生同样形状的伤痕。
冲蚀:熔汤高温高速冲蚀模具,使得铸件产生与模具相同的伤痕。
脱皮:铸件表面部分剥离的现象,最易发生在表面光滑的铸件上。
针孔:氢气导致针状细小的砂孔,因除气不彻底产生的内部缺陷。
擦伤:由于磨损使表面不理想,有比较长的痕迹。
缩孔:因熔汤凝固收缩而产生的内部砂孔。
气孔:因卷入气体或空气导致铸件内部存在的砂孔。
玷污:其它材料或其它材料的加入使表面变色,如机器润滑油,离型剂等。
隔层:铸件层剥皮。
变形:产品收缩应力或顶出变形。
凹陷:由于不同的材料的结合度和收缩率不同,引起表面凹陷。
拉伤:铸件表面的磨损或磨擦使得表面不理想。
腐蚀:在材质表面有不连续的痕迹,由氧化引起。
凹痕:由于挤压或撞击而产生的凹坑。
毛刺:在孔或边有粗糙和锋利的棱角(相对于材料的厚度和凸起的高度)。
冷隔:在两处或更多的材料融合点有线条(并且终止了结合或流动)分模线:在模具的两块或镶块之间有一条明显的线,例如:如果模具安装不当,在模具的主要部分能明显的看到明显的看到微小的凸起的线条。
压铸件表面处理工艺

压铸件表面处理工艺压铸件表面处理是指对压铸件的表面进行处理,以改善其外观和性能。
压铸件表面处理工艺的选择和施工是保证产品质量的重要环节。
本文将从压铸件表面处理的意义、常用的表面处理工艺以及工艺选择的考虑因素等方面进行介绍。
一、压铸件表面处理的意义压铸件表面处理的主要目的有以下几点:一是改善产品的外观质量,使其外观更加美观、光亮;二是提高产品的耐腐蚀性能,增加其使用寿命;三是改善产品的机械性能,提高其强度和硬度;四是为后续的涂装、镀铬等工艺提供良好的基础。
二、常用的表面处理工艺1. 除锈除氧化工艺:由于压铸件在生产过程中容易产生氧化皮和锈蚀,因此需要进行除锈除氧化处理。
常用的方法有机械除锈、化学除锈、电化学除锈等。
2. 去毛刺工艺:压铸件在冷却后会产生毛刺,影响产品的外观和性能。
去毛刺的方法有手工去毛刺、喷砂去毛刺、机械去毛刺等。
3. 改善表面粗糙度工艺:压铸件的表面粗糙度对产品的性能和使用寿命有一定影响。
常用的改善表面粗糙度的方法有抛光、镜面处理、喷丸等。
4. 表面涂层工艺:表面涂层可以提高产品的耐腐蚀性能、耐磨性能和美观度。
常用的表面涂层工艺有电泳涂装、喷涂、浸塑等。
5. 陶瓷涂层工艺:陶瓷涂层可以提高产品的耐磨性、耐腐蚀性和耐高温性能。
常用的陶瓷涂层工艺有热喷涂、电化学沉积等。
三、工艺选择的考虑因素在选择压铸件表面处理工艺时,需要考虑以下几个因素:1. 压铸件的材质:不同材质的压铸件适合不同的表面处理工艺。
例如,铝合金压铸件适合电泳涂装、阳极氧化等工艺;镁合金压铸件适合电化学沉积等工艺。
2. 产品的用途:根据产品的用途和工作环境,选择适合的表面处理工艺。
例如,汽车零部件需要具有良好的耐腐蚀性能和耐磨性能,因此适合进行镀铬、喷涂等工艺。
3. 加工工艺要求:根据产品的加工工艺要求,选择适合的表面处理工艺。
例如,需要进行后续的涂装工艺的产品,需要选择适合涂装的表面处理工艺。
4. 成本和效益:考虑表面处理工艺的成本和效益,选择经济实用的工艺。
压铸模具的表面处理新技术111
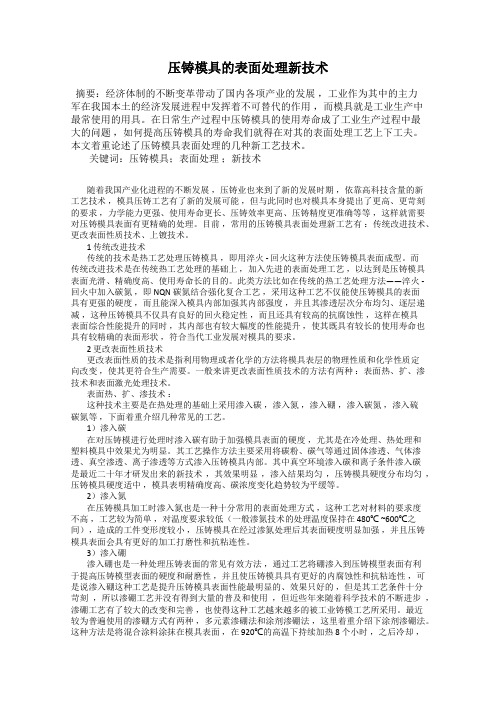
压铸模具的表面处理新技术摘要:经济体制的不断变革带动了国内各项产业的发展,工业作为其中的主力军在我国本土的经济发展进程中发挥着不可替代的作用,而模具就是工业生产中最常使用的用具。
在日常生产过程中压铸模具的使用寿命成了工业生产过程中最大的问题,如何提高压铸模具的寿命我们就得在对其的表面处理工艺上下工夫。
本文着重论述了压铸模具表面处理的几种新工艺技术。
关键词:压铸模具;表面处理;新技术随着我国产业化进程的不断发展,压铸业也来到了新的发展时期,依靠高科技含量的新工艺技术,模具压铸工艺有了新的发展可能,但与此同时也对模具本身提出了更高、更苛刻的要求,力学能力更强、使用寿命更长、压铸效率更高、压铸精度更准确等等,这样就需要对压铸模具表面有更精确的处理。
目前,常用的压铸模具表面处理新工艺有:传统改进技术、更改表面性质技术、上镀技术。
1 传统改进技术传统的技术是热工艺处理压铸模具,即用淬火 - 回火这种方法使压铸模具表面成型。
而传统改进技术是在传统热工艺处理的基础上,加入先进的表面处理工艺,以达到是压铸模具表面光滑、精确度高、使用寿命长的目的。
此类方法比如在传统的热工艺处理方法——淬火 - 回火中加入碳氮,即 NQN 碳氮结合强化复合工艺,采用这种工艺不仅能使压铸模具的表面具有更强的硬度,而且能深入模具内部加强其内部强度,并且其渗透层次分布均匀、逐层递减,这种压铸模具不仅具有良好的回火稳定性,而且还具有较高的抗腐蚀性,这样在模具表面综合性能提升的同时,其内部也有较大幅度的性能提升,使其既具有较长的使用寿命也具有较精确的表面形状,符合当代工业发展对模具的要求。
2 更改表面性质技术更改表面性质的技术是指利用物理或者化学的方法将模具表层的物理性质和化学性质定向改变,使其更符合生产需要。
一般来讲更改表面性质技术的方法有两种:表面热、扩、渗技术和表面激光处理技术。
表面热、扩、渗技术:这种技术主要是在热处理的基础上采用渗入碳,渗入氮,渗入硼,渗入碳氮,渗入硫碳氮等,下面着重介绍几种常见的工艺。
压铸模具的表面处理新技术 李红玉
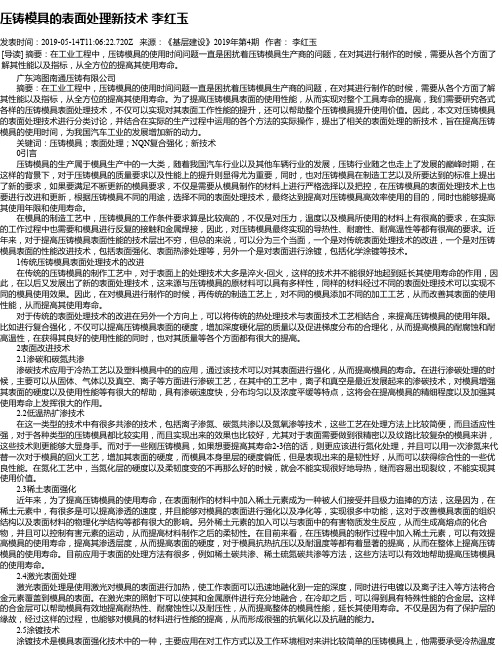
压铸模具的表面处理新技术李红玉发表时间:2019-05-14T11:06:22.720Z 来源:《基层建设》2019年第4期作者:李红玉[导读] 摘要:在工业工程中,压铸模具的使用时间问题一直是困扰着压铸模具生产商的问题,在对其进行制作的时候,需要从各个方面了解其性能以及指标,从全方位的提高其使用寿命。
广东鸿图南通压铸有限公司摘要:在工业工程中,压铸模具的使用时间问题一直是困扰着压铸模具生产商的问题,在对其进行制作的时候,需要从各个方面了解其性能以及指标,从全方位的提高其使用寿命。
为了提高压铸模具表面的使用性能,从而实现对整个工具寿命的提高,我们需要研究各式各样的压铸模具表面处理技术,不仅可以实现对其表面工作性能的提升,还可以帮助整个压铸模具提升使用价值。
因此,本文对压铸模具的表面处理技术进行分类讨论,并结合在实际的生产过程中运用的各个方法的实际操作,提出了相关的表面处理的新技术,旨在提高压铸模具的使用时间,为我国汽车工业的发展增加新的动力。
关键词:压铸模具;表面处理;NQN复合强化;新技术0引言压铸模具的生产属于模具生产中的一大类,随着我国汽车行业以及其他车辆行业的发展,压铸行业随之也走上了发展的巅峰时期,在这样的背景下,对于压铸模具的质量要求以及性能上的提升则显得尤为重要,同时,也对压铸模具在制造工艺以及所要达到的标准上提出了新的要求,如果要满足不断更新的模具要求,不仅是需要从模具制作的材料上进行严格选择以及把控,在压铸模具的表面处理技术上也要进行改进和更新,根据压铸模具不同的用途,选择不同的表面处理技术,最终达到提高对压铸模具高效率使用的目的,同时也能够提高其使用年限和使用寿命。
在模具的制造工艺中,压铸模具的工作条件要求算是比较高的,不仅是对压力,温度以及模具所使用的材料上有很高的要求,在实际的工作过程中也需要和模具进行反复的接触和金属焊接,因此,对压铸模具最终实现的导热性、耐磨性、耐高温性等都有很高的要求。
- 1、下载文档前请自行甄别文档内容的完整性,平台不提供额外的编辑、内容补充、找答案等附加服务。
- 2、"仅部分预览"的文档,不可在线预览部分如存在完整性等问题,可反馈申请退款(可完整预览的文档不适用该条件!)。
- 3、如文档侵犯您的权益,请联系客服反馈,我们会尽快为您处理(人工客服工作时间:9:00-18:30)。
三、压铸模的表面处理。
有扩散处理、涂层、氮化+涂层等几种方法。
扩散处理法虽有各种商品名称,主要是N、C、S、0单独或复合扩散的氮化、软氮化、浸硫氮化、氧化、氮化+氧化处理等,有代表性的氮化处理时,形成化合物层(白层)其耐熔损性、耐过烧性、耐粘着性好,而耐裂性差。
反之,无化合物层仅形成扩散层则耐热裂性好,而耐熔损性、耐过烧性、耐粘着性则差。
最近扩散处理趋向,氧化处理或氮化+氧化复合处理为主流,适用于压铸模具的各种表面处理方法:
涂层有PVD法、CVD法和TD工艺方法。
由硬质皮膜被覆法形成的陶磁涂层膜,有优良的耐溶损性、耐过烧性、耐粘着性,但耐热裂则很少有改善。
这样的硬质皮膜被覆法中CVD法和TD工艺方法在膜的密着上更好,但在处理上要1000度高温模具容易产生变形和变寸。
PVD法由于是低温处理可抑止模具变形变寸,但在膜的密着性上比CVD法要差。
氮化+涂层,其代表性方法是氮化+PVD法。
在氮化炉中仅形成氮化的扩散层,取出后在另外的PVD装置中进行模具各种涂层的方式。
这样的氮化+PVD其最表层膜具有耐溶损性、耐过烧性、耐粘着性,氮扩散层则具有耐热裂性。
但PVD法形成的膜在适用于复杂形状的模具时有一定范围的界限。
(氮化+氧化)复合处理。
压铸模具的表面处理在世界范围的倾向,由过去的氮化、浸硫氮化处理向应用氧化处理发展。
由于与氮化处理形成的铁的氮化物相比,高温稳定性高的铁的氧化物,应用于压铸模更能发挥其在溶损、过烧、粘着方面的效果。
(氮化+氧化)复合处理可在一个装置中连续处理,时间可大幅度缩短。
另外,在可控气氛中处理可形成没有氮化扩散层的化合物层的连续氧化处理,可以提高耐溶损性、耐过烧性、耐粘着性和耐热裂性。
等离子CVD法(PCVD)。
原料全用的是气体,由于是等离子化学反应形成的膜,是低温的密着性和致密性优良的皮膜,可以很好的覆盖复杂的产品。
另外,PCVD法可不破损真空一次工程在一个装置内将氮化等的扩散硬化处理+硬质皮膜的所谓复合处理简单的作成。
因而PCVD可面向三维立体形状物的压铸模具的处理。
含硼气体系统的PCVD作成新的硼扩散处理(硼化)含硼皮膜,例如:TiB、TiBN、TiBCN、TiAIBN、TiAIBCN0、TiAISiBCN0、BN、BCN等各种硬质膜。
如TiAIBN 膜有4000Hv以上的硬度,被称之谓超高级涂层。
选择不同元素的组合,可得到过去所没有的高度的耐磨性、耐氧化性、脱模性、润滑性从而使适应各种不同要求的压铸模具性能有飞跃的提高。
现己应用的实例有:手机部件的镁合金压铸模具,过去使用脱模剂,使用三万次左右就要因为腐蚀而需焊接修补,而且因使用脱模剂飞散的烟雾污染了环境,由于飞边毛刺使制品难以保持精度。
用PCVD法氮化扩散硬化层+TiN/TiAN/TiAISiCN0多层膜应用于该模具后,完全不用脱模剂,可压铸用30万次,延长了模具寿命、改善了环境、抑制飞边毛刺的产生、缩短了压铸节拍、提高了生产效率。
像机部件的成型,过去每次都涂脱模剂,熔液流动性差、产生皱皮、使制品加工出现问题、次废品率高。
此模具用氮化扩散硬化层+TiN/TiAIN/TiAISiCNO多层膜后,脱模剂用量只有过去的1/8以下、改善了流动性、不再出现皱皮、加工出漂亮的制品,并因而减少了消耗,提高了生产效率。
汽车部件的成型,过去使用脱模剂大量喷雾成形,约6万次就要焊接修补,而且铸造缺陷多、不良率高。
采用氮化扩散硬化层+TiN/TiAIN/TiAISiCNO多层膜后,脱膜剂减少到1/2以下,铸造提高到12万次以上。
不仅延长了模具寿命,而且抑止了铸造缺陷、降低了消耗,改善了生产环境。
由于PCVD法复合处理效果,提高了耐热裂性、耐过烧性、耐粘着性。
在铝压铸方面已有不用脱模剂,铸造在100万次以上的压铸模具。