涡流阵列检测技术的研究进展现状分析
多频涡流检查技术的研究分析

4多频涡流检查技术地研究对蒸汽发生器传热管进行涡流检查时,除了传热管地缺陷信号外,还有结构、管材加工、沉积物,以及它们之间不同地组合,会产生大量地畸变信号,从而引起误判或漏检,对正确分析缺陷带来一定困难.为此,必须对涡流检查技术进行研究,包括引进和掌握先进地多频涡流检查装置.4. 1 MIZ-18多频涡流检查装置蒸汽发生器传热管地涡流检查采用了美国Zetec公司生产地M IZ-18多频涡流检查装置,如图2所示.该装置具有下列功能:M IZ-18数据采集系统是用来采集和记录涡流检查数据,它与S M -10定位器和4D探头推拔器联合使用,其检查地全部过程由HP9836计算机控制.S M -10定位器是自动定位装置,远控检测探头定位于管端.安装这种定位器时,检查人员不需要进入高放射性地水室,而是将定位器从人孔插入,固定在人孔地螺栓孔上.4D探头推拔器是远距离操作地双速探头驱动机构,由主机控制,驱动探头进入传热管或从管中拉出地最大速率为12m/ s,最慢速率为0. 03m/ s.检查前将速率设置好,检查期间保持不变.M IZ-18数据分析系统提供分析涡流数据地能力,包括混频、相位分析、信号图形打印和最终报告地形成.M IZ-18数据处理系统提供对己完成地检查数据进行汇总、统计和分类,并对分析结果进行统计.4. 2多频涡流检查技术(1)在涡流检查中确定了4种检测频率.550kHz为主检测频率,是判伤地主要依据,确保标定管上伤深为壁厚10%地外伤有足够地检测灵敏度及信噪比;标定管上地通孔与10%外伤地涡流信号相位差在50度至135度之间,以提高判伤地准确性.100k H z为辅助检测频率,主要用于消除支撑板干扰信号,与主频通道混频,在混频通道上消除支撑板信号,用于支撑板信号处地判伤分析.同时,用于弯管区地信号分析.900kHz为胀管轮廓曲线分析频率,能提高胀管内径地测量精度.20kHz为管板定位及沉积物检测频率,由于管板及沉积物均邻近外壁,采用较低频率.(2)检测探头选择.检查较大弯头U形管时,选择填充系数较大、使用寿命较长地ULC探头,它有可仲缩地脚使探头在管内对中,能使尺寸偏小地探头维持与管子同心.检查小弯头U形竹时则需选择BJF探头,它地头部极软,能穿过小曲率U形管.如果被测管子具有磁性,要选择具有磁饱和特性地探头.一般每台蒸汽发生器有磁导率偏差影响地管子小于10% ,该磁偏效应可畸变或产生类似缺陷地信号,增加分析困难.为此,采用磁饱和探头对那些带磁地管子进行重复检查,以消除磁偏效应.旋转式探头比普通轴向探头可给出缺陷地类别、尺寸及方向等更详细地信息,但检查速度较慢,一般用于对缺陷进行定性定量分析和对管子复杂区域进行补充检查,以发现轴向探头可能漏检地缺陷.( 3)掌握和应用胀管区轮廓曲线地分析技术.利用由美国Zetec公司引进地“远控涡流数据采集分析系统”和“管板轮廓曲线分析程序”,开展对胀管区轮廓曲线分析技术地研究.一般作图通道地频率越高,分析出地轮廓曲线误差越小.这是因为频率越高,涡流地趋肤效应越显著,渗透深度也越小.在测量传热管内径地微小变化时,为了减少管板及管板端面对轮廓曲线分析地影响,选择900kHz地第6绝对通道为作图通道.通过对每根传热竹地涡流信号分析,可以绘出管壁轮廓曲线,来检验管子地欠胀或过胀地状况.4)提高检测缺陷地灵敏度.经研究,对Φ0. 3mm地通孔及Φ0.5mmx 60%壁厚地平底孔能准确判伤;轴向及周向相对定位误差均可《士lmm;采用多频涡流及其混频技术来消除干扰信号,例如管板上泥渣,支撑板、流量分配板、防振条等处地干扰信号,检测出真正地缺陷信号;利用DDA-4分析软件可在屏慕上显示X,Y分量长条图及局部扩展图,显示通道可任意选择,可显示频率、组态、时间、相位角、幅值及伤深、伤位等参数,利用MRPC显示软件可显示出缺陷特征及胀管形状等.版权申明本文部分内容,包括文字、图片、以及设计等在网上搜集整理.版权为个人所有This article includes some parts, including text, pictures, and design. Copyright is personal ownership.Zzz6Z。
2024年涡流探伤机市场发展现状
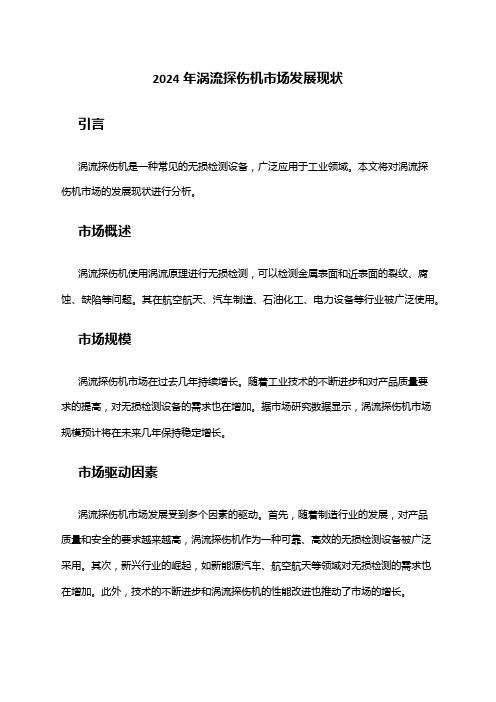
2024年涡流探伤机市场发展现状引言涡流探伤机是一种常见的无损检测设备,广泛应用于工业领域。
本文将对涡流探伤机市场的发展现状进行分析。
市场概述涡流探伤机使用涡流原理进行无损检测,可以检测金属表面和近表面的裂纹、腐蚀、缺陷等问题。
其在航空航天、汽车制造、石油化工、电力设备等行业被广泛使用。
市场规模涡流探伤机市场在过去几年持续增长。
随着工业技术的不断进步和对产品质量要求的提高,对无损检测设备的需求也在增加。
据市场研究数据显示,涡流探伤机市场规模预计将在未来几年保持稳定增长。
市场驱动因素涡流探伤机市场发展受到多个因素的驱动。
首先,随着制造行业的发展,对产品质量和安全的要求越来越高,涡流探伤机作为一种可靠、高效的无损检测设备被广泛采用。
其次,新兴行业的崛起,如新能源汽车、航空航天等领域对无损检测的需求也在增加。
此外,技术的不断进步和涡流探伤机的性能改进也推动了市场的增长。
市场竞争格局涡流探伤机市场存在着竞争激烈的格局。
市场上有多家国内外知名厂商提供涡流探伤机产品,这些厂商通过技术创新、产品质量和价格等方面展开竞争。
其中,国际大型公司在技术研发和市场渠道方面具有一定的优势,而国内厂商则借助技术改进和本土市场的需求来提升竞争力。
市场趋势未来涡流探伤机市场有几个明显的趋势。
首先,随着技术的不断进步,涡流探伤机的性能将得到进一步提升,能够更准确地检测和分析缺陷。
其次,市场将呈现出不断多元化的需求,例如对更小型化、便携化的涡流探伤机的需求将增加。
另外,随着人工智能和大数据技术的发展,涡流探伤机可能会与这些技术相结合,进一步提高检测效率和准确性。
持续进步的机遇涡流探伤机市场的持续进步为厂商和投资者带来了机遇。
首先,市场的发展为厂商提供了更大的销售空间和利润空间。
其次,技术的不断改进和创新为厂商提供了产品优化和差异化的机会。
另外,涡流探伤机市场的增长也为投资者提供了投资增长的机会,具有一定的投资潜力。
结论在未来的市场环境中,涡流探伤机市场将继续保持稳定的增长。
涡流无损检测

1无损检测(Nondestructive Testing, NDT)是一门涉及多学科的综合性应用技术,它以不损害被检对象的内部结构和使用性能为前提,应用多种物理原理和化学现象,对各种工程材料、零部件、结构件进行有效地检验和测试,检测被检对象中是否存在缺陷或不均匀性,进而评价它们的连续性、完整性、安全可靠性及某些物理性能【1-6]。
无损检测技术是现代工业发展必不可少的有效工具,在一定程度上反应了一个国家的工业发展水平,其重要性己得到世界范围内广泛公认。
无损检测技术的应用范围十分广泛,遍布工业发展的各个领域,在机械、建筑、冶金、电力、石油、造船、汽车、宇航、核能、铁路等行业中被普遍采用,成为不可或缺的质量保证手段,其在产品设计、生产和使用的各个环节中己被卓有成效的运用[4,7-16]。
2以德国科学家伦琴1895年发现X射线为标志,无损检测作为应用型技术学科己有一百多年的历史[l7]0 1900年,法国海关开始应用X射线检验物品;1922年,美国建立了世界第一个工业射线实验室,用X射线检查铸件质量,以后在军事工业和机械制造业等领域得到了广泛应用,射线检测技术至今仍然是许多工业产品质量控制的重要手段。
1912年,超声波检测技术最早在航海中用于探查海面上的冰山;1929年,将其应用于产品缺陷的检测,目前仍是锅炉压力容器、铁轨等重要机械产品的主要检测手段。
1930年后,开始采用磁粉检测方法来检测车辆的曲柄等关键部件,以后在钢结构上广泛应用磁粉探伤方法,使磁粉检测得以普及到各种铁磁性材料的表面检测。
毛细管现象是土壤水分蒸发的一种常见现象,随着工业化大生产的出现,将“毛细管现象”成功地应用于金属和非金属材料开口缺陷的检测,其灵敏度与磁粉检测相当,它的最大好处是可以检测非铁磁性物质。
经典的电磁感应定律和涡流趋肤效应的发现,促进了现代导电材料涡流检测方法的产生。
1935年,第一台涡流探测仪器研究成功。
到了二十世纪中期,建立了以射线检测(Radiographic Testing, RT、超声检测(Ultrasonic Testing, UT、磁粉检测(Magnetic Testing, MT、渗透检测(Penetrant Testing, PT)和涡流检测(Eddy Current Test, ECT五大常规检测技术为代表的无损检测体系【‘“]。
无损检测---涡流阵列检测技术基本原理

目录一、什么是涡流阵列检测技术?二、涡流检测基础知识三、涡流阵列检测技术工作原理四、涡流阵列检测技术特点五、涡流阵列检测技术的国内外现状一、什么是涡流阵列检测技术?“涡流阵列",又叫“阵列涡流”,英文名称“Eddy Current Array (简称ECA)JB/T 11780-2011无损检测仪器涡流阵列检测仪性能和检验阵列涡流检测具有按一定方式排布、且独立工作的多个检测线圈,能够一次性完成大面积扫查及成像的涡流检测技术。
C扫相关显示与缺陷形状像不像?并能形成直观性C扫图二、涡流检测基础知识1. ET工作原理一电磁感应①激励,悬空(电。
一磁0 )空载阻抗Z=Z0区0 = & +及卬涡流线圈M一互感系数〜提离R2一电涡流短路环负载〜路径几何尺寸,。
2L2—电涡流短路环自感系数〜路径几何尺寸,U22.影响放理式线圈阻抗的因素W" +黑:焉死)+ j9”-“R:短㈤a)提离b)边缘效应c)电导率d)磁导率e)工件几何尺寸f)缺陷g)表面状况h)检测频率影响阻抗变化的因素太多,限制r涡流探伤的应用!3.放置式涡流探头的分类4.绝对式探头和差分式探头的对比绝对式每个缺陷产生1个闭路(半8字):对于小缺陷、长缺陷和渐变缺陷敏感:可用于测殳材料性能差异.可能需要参考线圈执行系统平衡:对提离非常敏感。
差分式信号来自2个感应线圈的减法。
.每个缺陷产生2个闭路(8字)对小缺陷特别敏感,但渐变缺陷不敏感:对于小缺陷具有更好的信噪比:对于提离不太鼓感。
检测前,应该根据用途、被检1:件状况等确定探头的工作模式和信号响应模式!5.常规涡流检测技术的特点优点■适用于各种导电材质的试件探伤:■可以检出表面和近表面缺陷:■检测结果以电信号输出,容易实现自动化:■由于采用非接触式检测,所以检测速度快:■无需耦合剂,环保。
缺点・不能检测非导电材料:■形状更杂的工件很难检测:■各种干扰检测的因素较多,容易引起杂乱信号:■无法检出埋藏较深的缺陷:■ 一次覆盖范围小,检测效率低:■检测结果不直观,不能叔示缺陷图形,无法缺陷定性。
探究涡流检测技术在质量控制方面的总结

探究涡流检测技术在质量控制方面的总结。
在过去的几十年中,涡流检测技术已经得到了广泛的应用和研究。
随着科技的不断发展和进步,涡流检测技术也不断更新和改进。
目前,涡流检测技术已经发展成为一个具有系统性、灵活性和高效性的测试方法。
涡流检测技术的基本原理是利用交变的电流在导体中产生的磁场和导体内涡流引起的反磁场的相互作用来检测导体中的缺陷。
直流电流和交变电流都可以用于产生磁场,但是在实际应用中,交变电流被广泛地采用。
涡流检测技术可以检测表面的裂纹、缺陷、腐蚀和疲劳裂纹等,并且可以定量地测量它们的尺寸和深度。
涡流检测技术可以分类为两类:同轴涡流检测技术和平面涡流检测技术。
同轴涡流检测技术是利用导电材料的自感和与探头之间的耦合效应来检测材料的缺陷。
平面涡流检测技术是利用感应线圈中的交流电源来产生涡流场。
平面涡流检测技术可以检测导体的表面和近表面的缺陷和裂纹。
涡流检测技术在质量控制方面的应用非常广泛。
在汽车工业中,涡流检测技术可以应用于发动机缸体和曲轴等零部件的检测和评估。
在核电站中,由于涡流检测技术不产生辐射,因此可以用于检测反应堆的压力容器壁和管道的缺陷。
在航空航天领域中,涡流检测技术可以用于检测飞机的蒙皮、机翼、转子叶片和发动机零部件的质量和缺陷。
除以上领域外,涡流检测技术还可以应用于其它行业中。
比如,在工业管道中,涡流检测技术可以用于检测管道的内壁,以检测管道内部的缺陷、腐蚀和疲劳裂纹。
在电力行业中,涡流检测技术可以用于检测发电机转子的缺陷和质量。
涡流检测技术在质量控制方面的应用非常广泛,不仅能够提高产品质量,而且可以提高产效率和安全性。
但是,在涡流检测技术的应用中,还需要进一步发展和完善,以满足不同工业领域的需求。
涡流无损检测技术研究进展

涡流无损检测技术研究进展作者:宋倩张思全徐浩军陈刚来源:《中国科技博览》2015年第20期[摘要]随着人类科技的不断发展和进步,工业化程度持续提高,对检测材料和产品缺陷的精度的要求也不断提高。
涡流检测是一种常规的电磁无损检测方法,被广泛的应用于管道腐蚀、裂纹,机械损伤等工程问题。
常规涡流检测技术自身存在的一些局限性,如具有提离效应、探测深度小、检测速度慢等。
针对这些问题,逐渐发展出了一些新的涡流检测技术。
阐述了涡流检测的特点及这些新技术的原理和研究重点,分析了涡流检测技术今后的研究方向和发展趋势。
[关键词]电磁无损检测;涡流检测;检测精度中图分类号:TG115.28 文献标识码:A 文章编号:1009-914X(2015)20-0209-011 涡流无损检测基本原理根据法拉第电磁感应原理,当金属导体被在变化的磁场中,导体会不断地切割磁力线,从而产生感应电动势,形成一个电流的闭合回路。
这个电流我们就称之为涡流,以上现象称为涡流效应。
如图1.1所示,当通着交变电流的线圈靠近金属工件时,因为电磁感应的存在,工件中会产生涡流。
而涡流的分布、大小等情况都与金属工件的状况有关。
当工件有缺陷或者它的磁导率、电导率等物理特性有变化时,金属工件中的涡流就会随之产生变化。
同时,涡流产生的磁场会反作用于线圈,使得线圈阻抗产生变化。
因此,阻抗分析方法是一个经典的处理涡流信号的方法。
2 涡流无损检测技术的特点涡流检测技术不但可以检测出铁磁性和非铁磁性材料的腐蚀、裂纹及其它缺陷,而且还可以对其进行对其无损评价。
涡流无损检测技术具有如下特点:2.1 非接触检测,易于实现自动化涡流检测线圈被激励后所形成的电磁场的本质是一种电磁波,具有波动性和粒子性,所以检测时传感器并不需要接触到工件本身,也不需要填充耦合剂。
检测速度较快,易于实现自动化检测。
2.2 能在高温的状态下进行检测高温下的导电试件具有导电性质,可以对导体进行涡流检测。
涡流无损检测技术的研究

涡流无损检测技术的研究涡流无损检测技术是现代材料检测领域中广泛应用的一种技术,它是一种利用电磁感应原理的无损检测技术。
该技术利用涡流感应效应,在电磁场的作用下,材料中会产生交变电流,当被检测材料内部存在缺陷或异物时,会对电磁场产生影响,从而产生信号。
该技术具有高精度、高灵敏度、高速度和非破坏性等优点,因此在航空、铁路、军工、电子、汽车等领域得到了广泛的应用。
涡流无损检测技术的原理是利用交流磁场诱导材料内部涡流,涡流大小与材料导电性及交变电磁场频率有关,涡流异常即可反映材料缺陷的位置、尺寸和形态等信息。
该技术适用于检测导电性好的金属材料和导体内部缺陷,不仅可以检测表面缺陷,还可以检测材料内部缺陷,如裂纹、疲劳、腐蚀、脆性断裂、异物等。
由于该技术不需要破坏性取样,同时具有高速度和高准确度,因此被广泛应用于工业产品的无损检测和质量控制。
从技术原理上来看,涡流无损检测技术的检测效果与涡流激励场、被检测材料的电磁属性、探测器的性能和杂波等因素密切相关。
为了达到更高的检测精度和检测速度,需要针对不同应用场景选择合适的技术方案和合适的参数,同时还需要进行优化和改进。
近年来,随着科技的发展和需求的不断增加,涡流无损检测技术不断得到改进和优化,例如采用数字化信号处理技术、引入声学辅助技术、结合多种检测技术等,这些技术的应用大大提高了涡流无损检测技术的检测精度和可靠性。
目前市场上出现了许多涡流无损检测设备,这些设备不仅可以检测金属材料,还可以检测非金属材料,并且可以根据不同行业的应用需求进行优化和改进,比如建筑行业的混凝土结构检测、铁路行业的铁轨裂纹检测、航空行业的发动机叶片检测等。
总之,涡流无损检测技术是一种高精度、高灵敏度、高速度和非破坏性的检测技术,它已经广泛应用于工业领域的产品无损检测和质量控制。
随着科技的不断发展和需求的不断增加,涡流无损检测技术还将继续得到改进和优化,为不同行业的应用提供更加精确、高效和可靠的检测服务。
涡流阵列无损检测中裂纹参数估计和成像方法研究
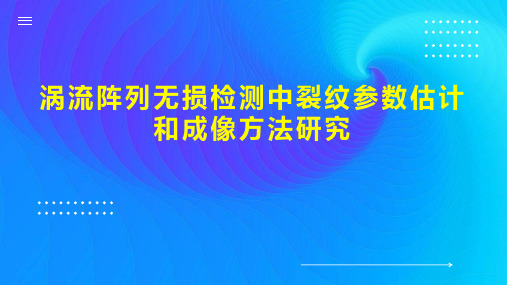
研究背景
涡流阵列无损检测技术自20世纪80年代问世以来,已广泛应用于各种材料和 构件的检测。在裂纹检测方面,涡流阵列技术具有高精度和高效率等优势,但是 对于裂纹参数估计和成像方法的研究仍然存在一定的挑战。特别是在复杂形状和 材料条件下,裂纹参数估计的准确性以及成像方法的可靠性仍需进一步研究。
研究方法
实验结果与分析
通过实验,我们获取了大量裂纹信号的数据,并采用先进的分析方法对其进 行了处理。结果显示,基于涡流阵列技术的裂纹参数估计具有较高的准确性,能 够在不同材料和形状条件下对裂纹进行有效的检测和识别。此外,成像方法的应 用也使得裂纹形态的展示更加直观清晰,为后续的损伤评估和修复提供了便利。
本次演示采用的研究方法主要包括实验设计、数据采集、参数估计和成像方 法等。首先,根据实际应用场景设计涡流阵列检测实验,包括试件制作、实验设 备搭建和实验方案制定。其次,利用高精度测量仪器进行数据采集,获取裂纹的 信号特征。然后,采用模式识别和机器学习算法对裂纹信号进行分析,提取裂纹 参数,如长度、深度、方向等。最后,运用图像处理技术对裂纹进行成像,直观 地展示裂纹的分布和形态。
在分析实验结果的基础上,我们发现涡流阵列无损检测技术在裂纹参数估计 和成像方面具有以下优点:
1、高灵敏度:涡流阵列技术对裂纹信号的捕捉能力强,能够快速准确地检 测到微小裂纹。
2、抗干扰能力强:该技术不易受材料表面粗糙度、缺陷等因素的干扰,提 高了裂纹参数估计的准确性。
3、多角度检测:涡流阵列可以在同一工件上进行多角度检测,从而实现裂 纹完整形态的还原。
涡流阵列无损检测中裂纹参数估计 和成像方法研究
01 引言
03 研究方法 05 结论与展望
目录
02 研究背景 04 实验结果与分析
关于对涡流检测的研究

关于对涡流检测的研究罗攀(哈尔滨工业大学材料科学与工程学院,哈尔滨150001)摘要:本文主要介绍一种重要的无损检测——涡流检测,先介绍有关无损检测的的相关信息,再简要介绍涡电流的现象原理,然后从原理、应用、优缺点等方面来介绍涡流检测,让大家对涡流检测有一个比较全面的认识,同时认识到我国的目前的涡流检测在国际中的水平。
关键词:无损检测;涡流检测;涡电流;应用;优缺点无损检测是工业发展必不可少的有效工具,在一定程度上反映了一个国家的工业发展水平,无损检测其重要性已得到公认。
涡流检测作为五大常规无损检测技术之一,尤其近年来无论仪器和检测技术都得到了长足的进步,在石化、电力、冶金等各个工业领域发挥了越来越重要的作用。
涡流检测与其它几种方法相比,它具有检测速度快,可以实现无接触检测,对表面及近表面缺陷非常敏感,特别适合检测薄件金属物体。
1无损检测技术无损检测,是以不损害被检验对象的使用性能为前提,应用多种物理原理和化学现象,对各工程材料、零部件和组织结构等进行有效地检验和测试的一种技术。
从而通过无损检测能够了解和评价材料、产品、设备构件直至生物等的性质、状态或内部结构等等。
无损检测有着非破坏性、互容性、动态性、严格性以及检验结果的分歧性等特点。
无损检测学科几乎涉及到了物理科学中的光学、电磁学、声学、原子物理学以及计算机、数据通讯等学科,在冶金机械、石油化工、航空航天等各个领域有着广泛的应用。
在现代科学技术应用领域中,没有那种技术能象无损检测那样具有如此广泛的科学基础和应用领域。
作为现代工业的基础技术之一,无损检测在保证产品和工程质量上发挥着愈来愈重要的作用,其“质量卫士”的美誉已得到工业界的普遍认同。
目前,无损检测技术通常的方法有以下几种:(1)液体渗透检测Penetrant Testing;(2)磁粉检测Magnetic particle Testing;(3)射线检测Radiographic Testing;(4)超声检测Ultrasonic Testing;(5)涡流检测Eddy current Testing。
涡流检测文献综述

摘要:涡流无损检测是以电磁感应原理为基础的一种常规无损检测方法,在现代工业中有着广泛的应用。
脉冲涡流无损检测是在涡流无损检测技术上发展起来的一种新技术。
相对于传统的涡流无损检测方法,脉冲涡流具有包含的频率分量丰富、检测信号信息量大、时域分析方便等优点,因此具有广阔的应用前景。
本文围绕涡流无损检测技术研究现状及其发展趋势,和脉冲涡流无损检测技术研究现状及其发展趋势展开综述分析,最终确定将深层缺陷脉冲涡流无损检测电磁场理论与实验研究作为研究课题。
本文由以下两部分组成:第一部分包括:1)涡流无损检测电磁场理论的研究现状和发展趋势;2)涡流无损检测技术的研究现状和发展趋势;3)涡流无损检测的实验研究和应用;4)深层缺陷涡流无损检测技术的研究现状和发展趋势。
第二部分包括:1)脉冲涡流无损检测电磁场理论的研究现状和发展趋势;2)脉冲涡流无损检测技术的研究现状和发展趋势;3)脉冲涡流无损检测中的信号处理;4)脉冲涡流无损检测的实验研究和应用。
通过以上综述分析,确定了将脉冲涡流无损检测作为研究课题,采用聚焦线圈与GMR(Giant MagnetoRestance)传感器相结合的脉冲涡流无损检测方法来实现深层缺陷检测。
关键词:脉冲涡流;深层缺陷;聚焦线圈;GMR传感器Abstracts:Eddy current non-destructive testing is a conventional non-destructive testing method based on the electromagnetic theory, which has wide applications in modern industries. Pulsed Eddy Current Testing(PECT) is a new technique developed on the basis of eddy current testing. In contrast to conventional eddy current excitation, PEC has a lot of advantages, such as rich frequency components and informations, convenient time-domain analysis, so it has wide potential applications. Through analysis for research and development of eddy current testing and PECT, the research will focus on the theory and experiment of pulsed eddy current testing for deep-seated flaws.The paper has two parts: the first part includes: 1) the theory research and development trends of eddy current non-destructive testing.2)the technology research and development trends of eddy current non-destructive testing. 3) the experimental research and application of eddy current non-destructive testing.4)the research and development trends of deep-seated flaws.the second part include:1) the theory research and development trends of PECT.2) the technology research and development trends of PECT.3) the signal processing of PECT.4) the experimental research and application of PECT. Summary of the above analysis, WE determine to take the pulse eddy current non-destructive testing as the research topic, using the pulsed eddy current non-destructive testing methods to detect deep-seated flaws with combination of Figure-8-shaped coil coil and GMR (Giant MagnetoRestance) sensor.Key words:PEC; deep-seated flaws; Figure-8-shaped coil coil; GMR sensor文献概述涡流无损检测理论研究是涡流无损检测技术的基础,在涡流无损检测理论研究方面,无缺陷状态的涡流电磁场解析解被推导出,采用数值计算软件,有缺陷状态的涡流电磁场各场量被计算出;为了实际应用的快速方便,还从“路”的角度得出了涡流电磁场的简化等效变压器模型,并且研究了该模型的适用范围。
涡流阵列检测技术的研究进展现状分析

图 1 加拿大 Eddyfi 公司研制的柔性阵列式涡流探头
图 2 加拿大 Eddyfi 公司的试样和检测结果
此外ꎬ还有各种新型原理的阵列传感器方案ꎬ如基于 SQUID 效应 的 阵 列 传 感 器[2] 、 基 于 MWM 的 阵 列 传 感 器[3] 、霍尔 元 件 阵 列 传 感 器[4] 、 GMR 阵 列 传 感 器 等[5] ꎮ
Keywords:testingꎻ eddy current sensorꎻ array testing systemꎻ research status
0 引言
涡流阵列传感器检测技术ꎬ亦属于涡流传感器技术新 兴发展方向之一ꎮ 因为这种检测技术既有涡流检测技术 非接触、在实际检测中便于应用的优势ꎬ又有阵列传感器 检测大型工件效率高的特点ꎬ在检测零件表面损伤研究方 面ꎬ具有独特优 势ꎬ 是 一 种 结 合 计 算 机 技 术、 自 动 控 制 技 术、多传感器融合技术、智能信号处理技术的综合技术ꎬ目 前虽不够成熟、稳定、在检测实践中应用也不多ꎬ但无碍于 这种技术的发展ꎮ
由 Matrix 公司在国内负责销售ꎬ检测效果较好ꎬ适应于各 种曲面零件的检测ꎬ但价格较高ꎬ用户不多ꎮ 2004 年ꎬCO ̄ DECI 传感器 问 世ꎬ 该 传 感 器 将 阵 列 排 布 的 线 圈 单 元 和 CCD 结合ꎬ能检测各种导电材料的表面缺陷ꎬ是阵列传感 技术的重要进展ꎮ
1 涡流阵列检测技术的研究进展
Present Situation Analysis and Research Progress of Eddy Current Array Testing Technology
ZHANG Weiminꎬ YUE Mingmingꎬ PANG Weihanꎬ XU Mindongꎬ CHEN Guolong ( School of Mechanical Engineeringꎬ Beijing Institute of Technologyꎬ Beijing 100081ꎬ China) Abstract:This paper briefly introduces the research progress and application of the eddy current array testing technologyꎬ and points
涡流检测技术及进展

检测方法 。如 图 l ,已知法 拉第 电磁 感应定律 ,在 检测线 圈上接通交流 电,产 生垂直 于工件 的交变磁 场 。检 测 线 圈靠 近 被 检 工 件 时 …,该 工 件 表 面 感 应
出 涡 流 同 时 产 生 与 原 磁 场 方 向相 反 的 磁 场 ,部 分抵
l 引言
涡流 检 测 是 建 立 在 电磁 感 应 原 理 基 础 上 的无 损
换 能器 的设计是 由确 定线 圈形状 、横截 面、尺
寸 、 结 构 等 参 数 制 造 的换 能 器 。 常 用 设 计 方 法 为 : 实 验 型 、解 析 型 及 数 值 型 等 设 计 【。 2 】
寸 或 要 求 由 公 式 计 算 线 圈 阻 抗 ,称 解 析 型 设 计 。而
消原磁场 ,导致检测线 圈电阻和 电感变化 。若金属 工 件 存 在 缺 陷 ,将 改 变 涡 流 场 的 强度 及 分 布 ,使 线 圈阻抗发生变化 ,检测该变化 可判 断有无缺 陷。
数值 型设计 始于数值求解 与线 圈响应有 关的解 析积 分表达式和 实现对换 能器性 能的模拟 。 每种 设计 方法有各 自优 点和局 限,通 常将 这三 种方法 结合起 来设计 涡流 换能器 ,以达 到优化设计
i sr me ta d S n T ed sg f a s u e e d o i ai n o x e i n y e r s l to y e a d n me i a y e a d n tu n n O o . h e i n o n d c r e sc mb n t f p rme tt p , e o u i n t p n u r t n o e rc l p , n t e d u r n r n d c r C l b d c o d n o t e c is a a e e s s c s s a e r s e to d y c re tt a s u e al e ma e a c r i g t h o l p r m t r u h a h p 。c o s s c i n,sz n tu t r . i e a d s r c u e
脉冲涡流检测技术研究及其应用的
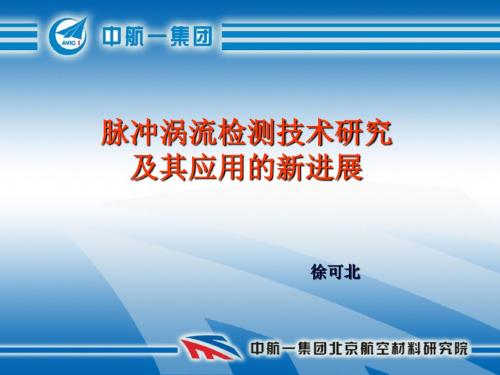
脉冲涡流检测技术研究及其应用的新进展
5 结束语
任何一项无损检测技术的生命力都在于其技术原理存在着有 别于其它技术的特殊性,同时每一项无损检测技术又都存在各自 的局限性; 脉冲涡流不仅在检测深度上比常规涡流具有较大突破,而且 其响应信号中包含有可深入挖掘和广泛利用的丰富信息; 脉冲涡流频谱中终究是以低频涡流成分为主,因此难以克服 低频涡流检测技术的一些局限性:① 激励线圈尺寸较大,不利 于小的形状较复杂的机械零件上缺陷的检测,② 对于表面微小 缺陷的检测能力偏低; 对于脉冲涡流检测技术的研究,不论是理论分析方面,还是 实际应用方面,只有正确把握这样一种辩证关系,才有利于更快、 更有效地推进该项技术的研究与发展。
p
其中,Vp为理想点线圈的感应电压,其 表达式为:
Vp A B ds ( A ) ds dl.......... .......... ..(2) t t t l
脉冲涡流检测技术研究及其应用的新进展
涡流检测发展趋势总结

涡流检测是一种无损检测技术,其发展趋势主要体现在以下几个方面:
1. 智能化和自动化:随着人工智能和机器学习技术的发展,涡流检测技术正朝着智能化和自动化的方向发展。
通过引入人工智能技术,可以实现自动识别缺陷、自动分类缺陷等功能,提高检测的准确性和可靠性。
2. 高精度和超高清成像:随着图像处理技术的发展,涡流检测技术正朝着高精度和超高清成像的方向发展。
通过高精度和超高清成像技术,可以更加清晰地呈现被检测物体的内部结构和缺陷,提高检测的分辨率和清晰度。
3. 多模式多频段检测:涡流检测技术正朝着多模式多频段检测的方向发展。
通过采用不同的检测模式和频率,可以更加全面地检测各种不同类型的材料和缺陷,提高检测的适应性和可靠性。
4. 快速检测:随着涡流检测技术的发展,其检测速度也在不断提高。
通过采用先进的信号处理技术和算法,可以实现快速检测,提高检测效率。
5. 集成化和便携化:随着工业生产和维修保养的需求,涡流检测设备正朝着集成化和便携化的方向发展。
集成化可以提高设备的可靠性和稳定性,便携化则方便设备的携带和使用。
6. 定制化服务:针对不同行业和不同需求,提供定制化的涡流检测服务也是未来的发展趋势之一。
通过深入了解客户需求,可以提供更加贴合客户需求的解决方案,提高客户满意度。
总之,涡流检测技术的发展趋势是多方面的,涵盖了智能化、自动化、高精度、超高清成像、多模式多频段检测、快速检测、集成化、便携化和定制化服务等方向。
这些技术的发展将有助于提高涡流检测的准确性和可靠性,满足工业生产和维修保养的需求。
涡流检测实验报告总结(3篇)
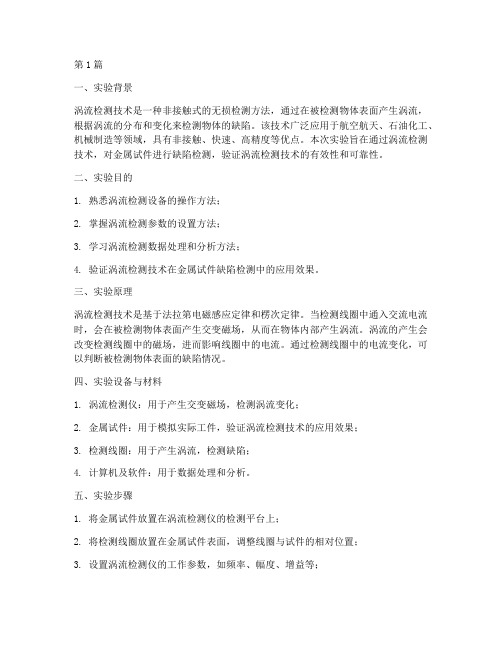
第1篇一、实验背景涡流检测技术是一种非接触式的无损检测方法,通过在被检测物体表面产生涡流,根据涡流的分布和变化来检测物体的缺陷。
该技术广泛应用于航空航天、石油化工、机械制造等领域,具有非接触、快速、高精度等优点。
本次实验旨在通过涡流检测技术,对金属试件进行缺陷检测,验证涡流检测技术的有效性和可靠性。
二、实验目的1. 熟悉涡流检测设备的操作方法;2. 掌握涡流检测参数的设置方法;3. 学习涡流检测数据处理和分析方法;4. 验证涡流检测技术在金属试件缺陷检测中的应用效果。
三、实验原理涡流检测技术是基于法拉第电磁感应定律和楞次定律。
当检测线圈中通入交流电流时,会在被检测物体表面产生交变磁场,从而在物体内部产生涡流。
涡流的产生会改变检测线圈中的磁场,进而影响线圈中的电流。
通过检测线圈中的电流变化,可以判断被检测物体表面的缺陷情况。
四、实验设备与材料1. 涡流检测仪:用于产生交变磁场,检测涡流变化;2. 金属试件:用于模拟实际工件,验证涡流检测技术的应用效果;3. 检测线圈:用于产生涡流,检测缺陷;4. 计算机及软件:用于数据处理和分析。
五、实验步骤1. 将金属试件放置在涡流检测仪的检测平台上;2. 将检测线圈放置在金属试件表面,调整线圈与试件的相对位置;3. 设置涡流检测仪的工作参数,如频率、幅度、增益等;4. 启动涡流检测仪,观察检测线圈中的电流变化;5. 分析电流变化,判断金属试件表面的缺陷情况;6. 改变检测参数,观察电流变化,验证参数对检测结果的影响;7. 记录实验数据,进行数据处理和分析。
六、实验结果与分析1. 在实验过程中,发现金属试件表面存在明显的缺陷,涡流检测仪能够准确检测出缺陷的位置和大小;2. 通过调整涡流检测仪的工作参数,发现参数对检测结果有显著影响。
适当调整参数,可以提高检测精度和灵敏度;3. 实验结果表明,涡流检测技术在金属试件缺陷检测中具有较好的应用效果,可以满足实际工程需求。
涡流检波器市场分析报告

涡流检波器市场分析报告1.引言1.1 概述涡流检测器是一种用于非接触式检测导体表面缺陷和材料性能的传感器设备。
随着工业自动化的发展和质量控制要求的提高,涡流检测器市场需求不断增长。
本文将对涡流检测器市场进行深入分析,探讨市场概况、发展趋势和竞争格局,并对市场的前景展望进行展望。
通过对关键市场因素的分析,同时给出建议,为相关行业提供决策参考。
1.2 文章结构文章结构包括三个主要部分:引言、正文和结论。
引言部分包括概述、文章结构、目的和总结。
在概述中介绍了涡流检测器市场的重要性和现状,文章结构部分介绍了本文所采用的结构和框架,目的是指出本文的写作目标和意义,而总结则是对整篇文章的内容和结论进行概述。
正文部分包括涡流检测器市场概况、涡流检测器市场发展趋势和涡流检测器市场竞争格局。
在涡流检测器市场概况中,介绍了市场规模、市场份额和市场发展历程;发展趋势部分分析了市场发展的预期方向和潜在机会;竞争格局部分分析了市场上的主要竞争者和市场竞争态势。
结论部分包括市场前景展望、关键市场因素分析和建议与展望。
在市场前景展望中,对涡流检测器市场未来发展进行了预测和展望;关键市场因素分析部分分析了影响市场发展的关键因素;建议与展望部分提出了对市场发展的建议和展望。
1.3 目的:本报告的目的是对涡流检测器市场进行全面分析,以便了解当前市场状况和发展趋势。
通过对市场概况、发展趋势和竞争格局的分析,我们旨在为相关企业和投资者提供可靠的市场情报和决策参考。
同时,我们也希望通过对市场前景展望和关键市场因素分析的总结,为行业发展提出建议和展望,促进涡流检测器市场的健康发展。
最终,我们期望本报告能够为行业相关方向的决策提供参考,为市场参与者创造更多的商机和增长机会。
1.4 总结总结部分:通过本报告的分析,我们可以得出以下几点结论:1. 涡流检测器市场具有较大的发展潜力,受到了广泛的关注和重视。
2. 随着科技的不断进步和应用领域的不断拓展,涡流检测器市场将持续保持稳定增长。
2024年涡流检测设备市场发展现状

涡流检测设备市场发展现状引言涡流检测是一种非破坏性检测技术,可以用于检测金属表面的缺陷和损伤。
涡流检测设备市场在过去几年中取得了快速的发展,在各个领域都得到了广泛的应用。
本文将对涡流检测设备市场的发展现状进行全面分析。
涡流检测设备市场概述涡流检测是一种通过电磁感应原理进行的检测技术。
涡流检测设备主要由探头、仪器和显示器组成。
市场上的涡流检测设备种类繁多,涵盖了各种规模和功能的设备,可以满足不同行业的需求。
涡流检测设备市场驱动因素涡流检测设备市场的发展受到多种因素的驱动。
首先,随着制造业的发展,对产品质量和安全性的要求不断提高,涡流检测设备作为一种有效的质量控制手段得到了广泛应用。
其次,涡流检测设备在航空、航天、石油化工等高端领域的应用需求也在不断增长。
此外,随着技术的进步和成本的降低,涡流检测设备的市场需求也在不断扩大。
涡流检测设备市场应用领域涡流检测设备在各个行业都有广泛的应用。
首先,航空航天行业是涡流检测设备的主要应用领域之一。
涡流检测设备可以检测飞机发动机叶片和机身表面的缺陷,保障飞行安全。
其次,石油化工行业也是涡流检测设备的重要应用领域。
涡流检测设备可以用于检测石油管道和化工设备的缺陷,预防泄露事故的发生。
此外,涡流检测设备还在汽车制造、机械制造、电力行业等领域有着广泛应用。
涡流检测设备市场竞争格局目前,涡流检测设备市场竞争格局较为激烈。
市场上存在着众多的涡流检测设备供应商,产品种类繁多。
国内外知名企业在涡流检测设备市场占据主导地位,它们通过技术创新和产品优势来提升市场份额。
此外,新兴企业也在不断涌现,它们通过研发具有竞争力的产品,寻求突破。
涡流检测设备市场发展趋势未来涡流检测设备市场具有较大的发展潜力。
首先,随着制造业智能化的推进,涡流检测设备将更加自动化和智能化,提高检测效率和准确性。
其次,涡流检测设备的便携性将得到进一步提升,可以满足现场检测的需求。
此外,涡流检测设备将会向多功能、高精度的方向发展,以满足不同行业的需求。
涡流检测技术总结质量控制_工作质量自我总结
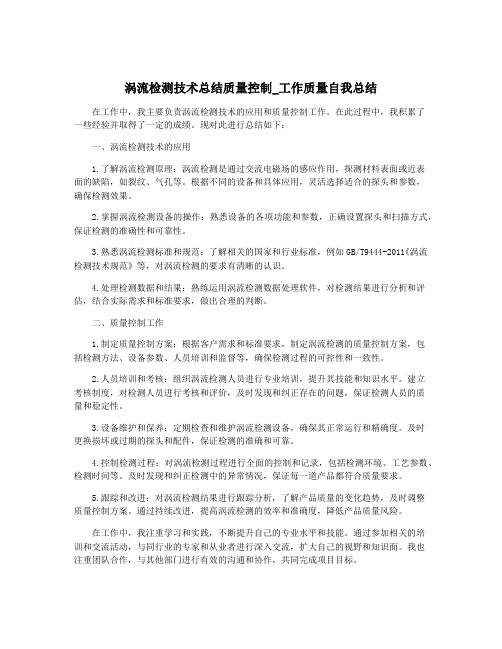
涡流检测技术总结质量控制_工作质量自我总结在工作中,我主要负责涡流检测技术的应用和质量控制工作。
在此过程中,我积累了一些经验并取得了一定的成绩。
现对此进行总结如下:一、涡流检测技术的应用1.了解涡流检测原理:涡流检测是通过交流电磁场的感应作用,探测材料表面或近表面的缺陷,如裂纹、气孔等。
根据不同的设备和具体应用,灵活选择适合的探头和参数,确保检测效果。
2.掌握涡流检测设备的操作:熟悉设备的各项功能和参数,正确设置探头和扫描方式,保证检测的准确性和可靠性。
3.熟悉涡流检测标准和规范:了解相关的国家和行业标准,例如GB/T9444-2011《涡流检测技术规范》等,对涡流检测的要求有清晰的认识。
4.处理检测数据和结果:熟练运用涡流检测数据处理软件,对检测结果进行分析和评估,结合实际需求和标准要求,做出合理的判断。
二、质量控制工作1.制定质量控制方案:根据客户需求和标准要求,制定涡流检测的质量控制方案,包括检测方法、设备参数、人员培训和监督等,确保检测过程的可控性和一致性。
2.人员培训和考核:组织涡流检测人员进行专业培训,提升其技能和知识水平。
建立考核制度,对检测人员进行考核和评价,及时发现和纠正存在的问题,保证检测人员的质量和稳定性。
3.设备维护和保养:定期检查和维护涡流检测设备,确保其正常运行和精确度。
及时更换损坏或过期的探头和配件,保证检测的准确和可靠。
4.控制检测过程:对涡流检测过程进行全面的控制和记录,包括检测环境、工艺参数、检测时间等。
及时发现和纠正检测中的异常情况,保证每一道产品都符合质量要求。
5.跟踪和改进:对涡流检测结果进行跟踪分析,了解产品质量的变化趋势,及时调整质量控制方案。
通过持续改进,提高涡流检测的效率和准确度,降低产品质量风险。
在工作中,我注重学习和实践,不断提升自己的专业水平和技能。
通过参加相关的培训和交流活动,与同行业的专家和从业者进行深入交流,扩大自己的视野和知识面。
我也注重团队合作,与其他部门进行有效的沟通和协作,共同完成项目目标。
非铁磁性传热管阵列涡流检测研究

科学技术创新2021.07非铁磁性传热管阵列涡流检测研究谷昊(辽宁红沿河核电有限公司,辽宁大连116300)1概述对于非铁磁性传热管,一般采用常规涡流检测方法(Bobbin )对其运行状况进行检查。
Bobbin 目前已经是一种比较成熟的无损检测方法,检测效率高、信号可记录、重复性好,尤其适合传热管的在役检测。
但是Bobbin 检测方法同时也存在不足之处,检测信号比较抽象、图像显示不够直观、不能区分开同一个圆周截面的多个缺陷、对于纵向的缓慢变形的长缺陷不够敏感、对信号显示的判伤较依赖分析人员的经验。
因此,采取合适的检测方法对Bobbin 进行补充很有必要。
旋转探头虽然检测效果良好,但检测速度慢、检验装置复杂且造价高、探头损耗严重、经济效益低[1]。
寻找一种既经济方便,又对非铁磁性传热管具有良好检测效果的涡流探伤新方法就成为当前的研究重点,本文介绍了非铁磁性传热管阵列涡流检测的试验过程与试验结果。
2传热管阵列涡流检测原理阵列涡流探头的常见激发方式主要分为绝对式及激励-接收式两种。
绝对式是指阵列涡流线圈中每个线圈既用于激发涡流,又用来接收感应的涡流信号。
当阵列涡流探头处于此种激发模式时,检测效果即可等同于若干个点式探头同时扫查,提高了检测效率。
然而,因为此种激发方式使检测探头的提离信号影响较大,不利于检测的实施,所以,阵列涡流更多采用激励-接受式的激发方式。
激励-接受式激发方式基本原理为:一个线圈针对工件激发感应涡流,另外一个或若干的线圈接收感应涡流产生的信号。
当被检工件存在电磁特性的不连续时,激励的涡流会被这种不连续干扰,进而被接收线圈接收到。
一对激励-接受组合的线圈会因缺陷方向的不同而产生不同的检测灵敏度。
当缺陷方向与涡流流动方向垂直时,缺陷干扰涡流的流动检出效果好;当缺陷方向与涡流方向相同时,缺陷对涡流的干扰较小,检测效果较差。
密布的线圈按照预先设计的激发顺序依次交替运行,在电磁场和涡流场发生高速旋转的同时,检测的焦点也发生高速旋转,以此达到对传热管内表面旋转扫查的目的,其效果近似于旋转探头的机械旋转。
- 1、下载文档前请自行甄别文档内容的完整性,平台不提供额外的编辑、内容补充、找答案等附加服务。
- 2、"仅部分预览"的文档,不可在线预览部分如存在完整性等问题,可反馈申请退款(可完整预览的文档不适用该条件!)。
- 3、如文档侵犯您的权益,请联系客服反馈,我们会尽快为您处理(人工客服工作时间:9:00-18:30)。
涡流阵列检测技术的研究进展现状分析张卫民;岳明明;庞炜涵;徐民东;陈国龙【摘要】简要介绍了阵列涡流检测技术研究进展和应用情况,指出阵列涡流传感器是涡流检测技术的一个新的发展方向,在重要机械零部件和关键结构监测中具有广泛应用前景.提出了一种检测小曲率曲面零件的新型阵列式检测技术方案和结构设计方案.%This paper briefly introduces the research progress and application of the eddy current array testing technology,and points out a new development direction that the eddy current array sensor is applied to its testing technology.It has a wide application pros-pect in monitoring the important mechanical parts. A new array testing technology and the system design scheme are proposed to test the small curved surface parts.【期刊名称】《机械制造与自动化》【年(卷),期】2018(000)001【总页数】3页(P181-183)【关键词】检测;涡流传感器;阵列式检测结构;研究现状【作者】张卫民;岳明明;庞炜涵;徐民东;陈国龙【作者单位】北京理工大学机械与车辆学院北京100081;北京理工大学机械与车辆学院北京100081;北京理工大学机械与车辆学院北京100081;北京理工大学机械与车辆学院北京100081;北京理工大学机械与车辆学院北京100081【正文语种】中文【中图分类】TP274+.50 引言涡流阵列传感器检测技术,亦属于涡流传感器技术新兴发展方向之一。
因为这种检测技术既有涡流检测技术非接触、在实际检测中便于应用的优势,又有阵列传感器检测大型工件效率高的特点,在检测零件表面损伤研究方面,具有独特优势,是一种结合计算机技术、自动控制技术、多传感器融合技术、智能信号处理技术的综合技术,目前虽不够成熟、稳定、在检测实践中应用也不多,但无碍于这种技术的发展。
1 涡流阵列检测技术的研究进展国际上,最初的涡流阵列传感器由绕制的线圈单元构成。
1988年,Krampfner和Johnson将印制电路板技术用于涡流阵列传感器的设计,巧妙解决了人工绕制线圈一致性较差的问题[1]。
2009年,加拿大Eddyfi公司开发出各种结构柔性阵列涡流检测传感器(如图1、图2所示),并由Matrix公司在国内负责销售,检测效果较好,适应于各种曲面零件的检测,但价格较高,用户不多。
2004年,CODECI传感器问世,该传感器将阵列排布的线圈单元和CCD结合,能检测各种导电材料的表面缺陷,是阵列传感技术的重要进展。
图1 加拿大Eddyfi公司研制的柔性阵列式涡流探头图2 加拿大Eddyfi公司的试样和检测结果此外,还有各种新型原理的阵列传感器方案,如基于SQUID效应的阵列传感器[2]、基于MWM的阵列传感器[3]、霍尔元件阵列传感器[4]、GMR阵列传感器等[5]。
但这些传感器由于受到各种条件限制,都没有线圈式阵列传感器在实践中应用广泛。
国内关于涡流阵列传感器研究较早的是清华大学陈祥林、丁天怀等人,采用柔性印刷电路板工艺研制了一种新型接近式电涡流传感器及测试系统,可以实现大面积曲面间微小间隙的实时监测[6],在阵列传感器方面进行过较深入研究的是长沙国防科技大的刘波、罗飞路等人[7],刘波对涡流阵列检测技术的理论和实验都进行了深入、系统的研究。
西安交通大学、北京航空航天大学、华中理工大学、吉林大学、南昌航空大学、中国石油大学、中国民航大学、北京航空材料研究院、上海材料研究所、上海飞机设计研究所等多家单位,也先后开展了涡流阵列检测技术研究,并各自推出了传感器结构方案,解决了一些实际问题[8-10]。
2 涡流阵列检测技术的应用现状涡流阵列传感器的实际应用之一是用于重要机械结构的疲劳损伤在位监测。
值得注意的是,用于损伤发展在位监测的一种新型平面电涡流传感器结构,可用于螺栓孔附近疲劳裂纹发展监测[11]。
激励线圈从中心圆处呈辐射状向四周螺旋展开,在激励线圈的螺旋线间隔内分布着环状感应线圈,激励线圈中通以激励电流,在传感器监测空间内产生激励磁场,环状感应线圈用于感应激励磁场在监测空间内的反射场,而反射场跟传感器监测空间内的电磁特性和空间边界条件紧密相关,结构损伤伴随结构电磁特性参数和边界条件的改变,引起传感器输出特性变化。
某研究组针对该结构进行了深入的理论和实验研究[12],此后类似研究尚不多见。
本文作者在博士点基金、自然科学基金、国防预研基金资助下,针对实际裂纹走向呈随机性分布、而普通差动式涡流传感器[13]、方向性涡流传感器检测时存在盲区的问题,提出了利用旋转涡流场的十字交叉激励新型结构。
所谓十字交叉激励,即采用两个十字交叉导线激励和阿基米德螺线接收线圈接收方式,组成电涡流传感器平面结构。
在十字交叉导线上分别通以相位相差90°的正余弦交流电,则会在试件上产生一强度均匀,方向旋转的方向性电磁场。
与传统的常规圆柱型涡流探头相比,由于这种结构具有瞬时方向性,更有利于集中瞬时能量,用于检测各向异性性质的残余应力等物理量,由于方向是均匀旋转的,则对方向随机分布的裂纹,均有较好的检测灵敏度。
目前研究成果已投寄国际权威杂志,引起业内专家的兴趣与注意。
几乎就在提出十字交叉激励等新结构同时已申请专利。
国际权威杂志NDT&E International,2015 年70卷29-37页上发表了Lius S和Telmo G等人的论文“,“A new dual driver planar eddy current probe with dynamically controlled induction patte rn”[14],文中所提结构和本课题新装置或派生结构十分相似,有异曲同工之妙,如图3所示。
这也从一个侧面说明,本研究确有先进性,且应刻不容缓开展研究。
图3 两种结构对比计划在下一步开展基于阵列传感器研究,届时不仅可以监测到疲劳裂纹产生程度,而且对位置也可以监测到。
图4是作者设想的一种结构,用于监测焊缝处疲劳裂纹,激励线圈有两条导线,交叉处形成旋转磁场,监测线圈是独立的,不仅可以检测到疲劳裂纹的出现,还可以检测到疲劳裂纹的位置。
图4 新型电磁在位监测机构3 一种可用于小曲率曲面零件表面损伤的涡流阵列检测技术的研制该装置由柔性阵列式检测涡流探头、气囊式装置、步进电机、多通道信号采集装置、计算机组成。
柔性阵列涡流传感器由30组刚性线圈等间距固定在柔性橡胶垫上制成,每个单元线圈结构都是一致的。
橡胶垫具有一定柔性,可以满足小曲率曲面零件的检测需求。
检测时气囊式装置充气,将阵列式涡流探头压紧在零件表面上,步进电机驱动则可保证装置在任何地方实现检测。
多通道信号采集装置最多可采集48路信号,在计算机中进行成像处理。
整个实验装置如图5所示。
检测时,充气气囊将传感器线圈紧压在被测零件表面上,这种结构对小曲率曲面零件也有一定适应性,步进电机将传感器结构送到需要检测位置,从而实现检测。
这种结构对检测微小损伤未必有什么明显优势,其主要特点是检测效率高,发挥了阵列探头优点。
实验中选用一铝合金小曲率曲面零件,在上面用机械方法加工出尺寸为(长×宽×深)10mm×2mm×3mm较大的裂纹状缺陷,如图6所示。
图5 涡流阵列检测实验装置图6 裂纹状缺陷将阵列传感器移动至缺陷位置,在缺陷位置可观测到信号幅值发生突变,将信号通过低通滤波器等进一步处理,即可清晰提取出缺陷信号,如图7所示,裂纹缺陷信号为图中黑色部分。
图7 缺陷信号4 结语分析了目前阵列涡流传感器技术的研究和应用现状,指出阵列涡流传感器技术是涡流检测技术的一个新的发展方向。
回顾了国内外研制现状,提出了一种新型阵列涡流传感器结构方案。
参考文献:[1] Y.D.KramPfner,D.D.Johnson.Flexible Substrate Eddy Current Coil Arrays[C]. NewYork: ReviewoProgressin Quantitative NDE: 1988,7:471-478.[2] w.N.podney,p.V.Czipott.An electromagnetic Microscope forEddyCurrentEvaluationofMaterials[J]. IEEETransactionsonMagnetics,1991,27(2):3241-3244.[3] N.J.Goldfine,J.R.Melcher.MagnetometerHavingperiodic Winding Structure And Material Pro Perty Estimator[P]. USPatentNtlmber:5453689,1995-9-26.[4] H.Y.Sun,R.Ali,M.Johnson,etal.Enhanced Flaw Detection Usingan EddyCurrent Probewitha Linear Array of Hall Sensors[C]. NewYork:Review of Progressin Quantitative NDE, 2004,23:516-522.[5] A.Bluschke,U.schmucker. 一种用于检测金属物体轮廓和材料性能的新型传感器)涡流阵列[J]. 无损检测,1995,17(6):177-175.[6] Mark Lin,Amrita Kumar,Xinlin Qing. Advances in utilization of structurally integrated sensor networks for healthmonitoring in commercial applications[A]. Smart structures and materials, Proceeding of SP IE, 2002,4701: 167-176.[7] 刘波. 涡流阵列无损检测中裂纹参数估计和成像方法研究[D]. 长沙:长沙国防科技大学,2011.[8] 蒋齐密,史海滨,康宜华,等. 基于涡流传感器阵列的火车轮在役自动检测系统设计[J]. 机械与电子,2000,(6):26-27.[9] 高印寒,杨柳松,杨晓璐,等. 含交错层叠电涡流传感器阵列的成像定位仪的研究[J]. 无损检测,2005,27(10):505-505.[10] 杨宾峰,罗飞路,曹雄恒,等. 脉冲涡流腐蚀成像阵列传感器应用研究[J]. 传感技术学报,2005,18(1):112-115.[11] 丁华,何宇廷,杜金强,等. 花萼状涡流传感器及其飞机金属结构疲劳损伤监测试验研究[J]. 机械工程学报,2013,149 (2):1-7.[12] 丁华,何宇廷,焦胜博,等. 花萼状涡流传感器的损伤监测正向等效模型构建[J]. 中国电机工程学报,2013, 133(9):167-175.[13] 张卫民,曾卫琴,杨秀江,等. 基于平面线圈阵列传感器的铝板材料裂纹电涡流检测[J]. 北京理工大学学报,2014,34(11):110-114.[14] Luis S.Rosado,TelmoG.Santos,PedroM.Ramosetal.A new dual driver planar eddy current probe with dynamically controlled induction pattern[J].NDT&E International,2015, 70:29-37.。