平板表层缺陷检测涡流阵列传感器的设计
涡流探伤仪设计方案. (2)

涡流探伤仪设计方案.涡流探伤仪是一种用于检测金属材料表面裂纹和缺陷的设备。
它利用涡流原理,通过产生和感应涡流来检测材料表面的变化。
下面是一个设计涡流探伤仪的方案。
1. 设计原理:涡流探伤仪主要包括两个主要部分:激励线圈和接收线圈。
激励线圈通过通电产生交变电磁场,而接收线圈用于接收由材料表面缺陷引起的涡流感应。
通过分析接收线圈中感应到的信号,可以确定材料表面是否存在缺陷。
2. 硬件设计:涡流探伤仪的硬件设计主要包括电源电路、激励线圈、接收线圈和信号处理电路。
电源电路提供所需的电能,激励线圈产生交变电磁场,接收线圈用于感应并接收信号,信号处理电路对接收到的信号进行放大和解析。
3. 激励线圈设计:激励线圈是涡流探伤仪中最重要的部分之一。
它应根据被测材料的大小和形状进行设计。
激励线圈通常采用多匝线圈,可以根据需要进行调节和控制。
4. 接收线圈设计:接收线圈应该与激励线圈相对称放置,以便更好地感应到材料表面的涡流信号。
接收线圈通常采用细线制成,以提高感应灵敏度。
5. 信号处理电路设计:接收到的信号通常需要进行放大和滤波处理,以便进一步分析和识别。
信号处理电路应设计成能够满足这些需要的功能。
6. 控制模块设计:涡流探伤仪通常还需要一个控制模块来控制和显示检测结果。
控制模块应能够根据实际需求选择合适的参数,并将结果显示在监测器上。
7. 安全设计:涡流探伤仪的安全设计非常重要。
应采取必要的措施,以确保操作者和设备的安全。
例如,在通电前应进行安全检查,并配备过载保护装置。
总之,设计涡流探伤仪需要考虑到电路设计、线圈设计、信号处理、控制以及安全等方面的要求。
根据具体应用需求,可以进行相应的优化和改进。
无损检测----涡流阵列检测技术典型应用
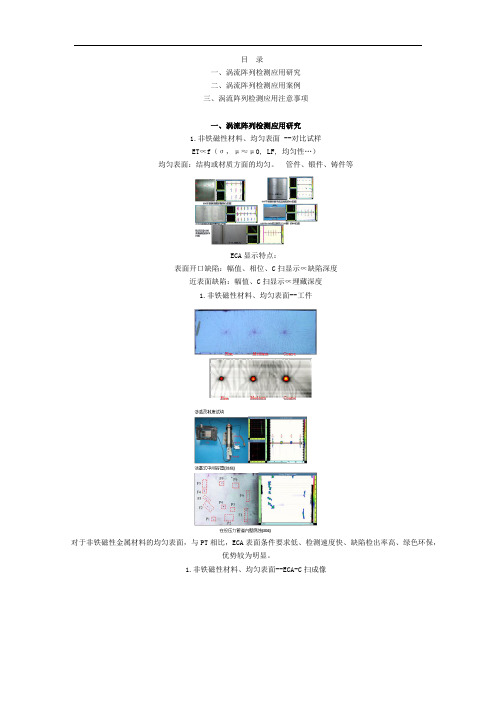
目录一、涡流阵列检测应用研究二、涡流阵列检测应用案例三、涡流阵列检测应用注意事项一、涡流阵列检测应用研究1.非铁磁性材料、均匀表面 --对比试样ET∝f(σ,μ≈μ0, LF, 均匀性…)均匀表面:结构或材质方面的均匀。
管件、锻件、铸件等ECA显示特点:表面开口缺陷:幅值、相位、C扫显示∝缺陷深度近表面缺陷:幅值、C扫显示∝埋藏深度1.非铁磁性材料、均匀表面--工件对于非铁磁性金属材料的均匀表面,与PT相比,ECA表面条件要求低、检测速度快、缺陷检出率高、绿色环保,优势较为明显。
1.非铁磁性材料、均匀表面--ECA-C扫成像绝对桥式阵列、小的线圈尺寸、多的阵列排数更有利于涡流阵列C扫成像。
均匀表面表面开口缺陷ECA-C扫成像可在一定程度上定性2.非铁磁性材料、非均匀表面--对比试块ET∝f(σ, LF, μ≈μ0, 均匀性…)对接接头:局部表面出现结构或材质不均匀。
2.非铁磁性材料、非均匀表面--模拟试块表面的不均匀性,在一定程度上影响ECA-C成像效果,直观性受到影响。
焊纹也会降低检测灵敏度。
2.非铁磁性材料、非均匀平面--工件3.铁磁性材料、均匀表面--对比试样ET∝f(σ, LF, μ, 均匀性…)管件、锻件、铸件等4.铁磁性材料、非均匀表面--动态提离补偿技术ECA C-scan Image对接接头:局部表面出现结构或材质不均匀。
4.铁磁性材料、非均匀表面--对比试样5.高温奥氏体不锈钢刻槽试板高温检测实验(300℃)6.低温低温情况下,PT无法实施,可考虑ECA。
二、涡流阵列检测典型案例——奥氏体不锈钢对接接头1.表面开口缺陷ECA可以比PT更容易发现缺陷。
2.近表面缺陷ECA可以在一定程度上检出近表面缺陷。
在线不打磨检测--动态提离补偿动态提离补偿技术,实现了碳钢对接接头的在线不打磨表面缺陷检测。
三、涡流阵列检测注意事项a)了解检测对象b)选探头c)选对比试样d)确定灵敏度e)扫查f)数据判读g)验证。
平板导体深层缺陷定量检测仿真研究
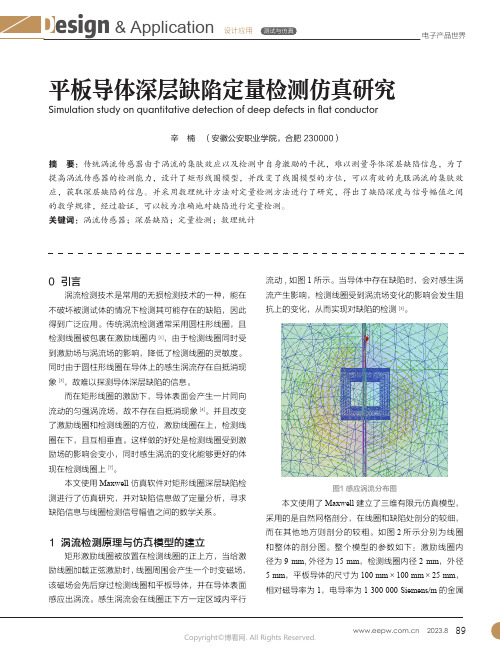
平板导体深层缺陷定量检测仿真研究Simulation study on quantitative detection of deep defects in flat conductor辛 楠 (安徽公安职业学院,合肥 230000)摘 要:传统涡流传感器由于涡流的集肤效应以及检测中自身激励的干扰,难以测量导体深层缺陷信息,为了提高涡流传感器的检测能力,设计了矩形线圈模型,并改变了线圈模型的方位,可以有效的克服涡流的集肤效应,获取深层缺陷的信息。
并采用数理统计方法对定量检测方法进行了研究,得出了缺陷深度与信号幅值之间的数学规律,经过验证,可以较为准确地对缺陷进行定量检测。
关键词:涡流传感器;深层缺陷;定量检测;数理统计0 引言涡流检测技术是常用的无损检测技术的一种,能在不破坏被测试体的情况下检测其可能存在的缺陷,因此得到广泛应用。
传统涡流检测通常采用圆柱形线圈,且检测线圈被包裹在激励线圈内[1],由于检测线圈同时受到激励场与涡流场的影响,降低了检测线圈的灵敏度。
同时由于圆柱形线圈在导体上的感生涡流存在自抵消现象[5],故难以探测导体深层缺陷的信息。
而在矩形线圈的激励下,导体表面会产生一片同向流动的匀强涡流场,故不存在自抵消现象[4]。
并且改变了激励线圈和检测线圈的方位,激励线圈在上,检测线圈在下,且互相垂直。
这样做的好处是检测线圈受到激励场的影响会变小,同时感生涡流的变化能够更好的体现在检测线圈上[7]。
本文使用Maxwell仿真软件对矩形线圈深层缺陷检测进行了仿真研究,并对缺陷信息做了定量分析,寻求缺陷信息与线圈检测信号幅值之间的数学关系。
1 涡流检测原理与仿真模型的建立矩形激励线圈被放置在检测线圈的正上方,当给激励线圈加载正弦激励时,线圈周围会产生一个时变磁场,该磁场会先后穿过检测线圈和平板导体,并在导体表面感应出涡流。
感生涡流会在线圈正下方一定区域内平行流动,如图1所示。
当导体中存在缺陷时,会对感生涡流产生影响,检测线圈受到涡流场变化的影响会发生阻抗上的变化,从而实现对缺陷的检测[3]。
平板表层缺陷检测涡流阵列传感器的设计
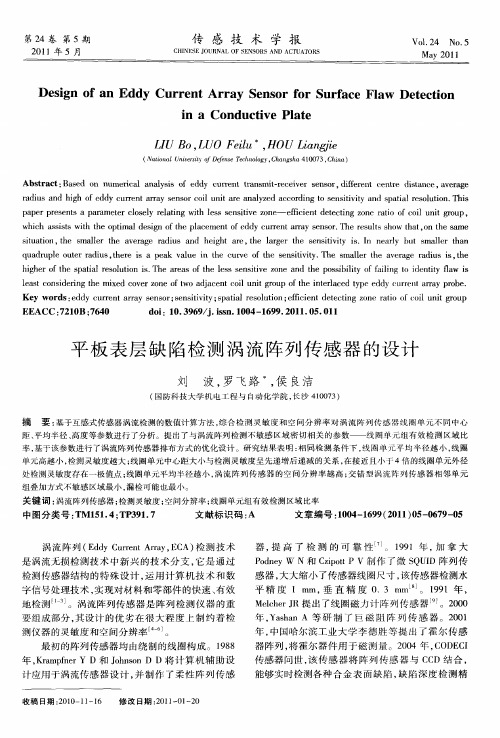
wh c sit t h pt ld sg ft e p a e n fe d u e ta a e s r Th e u t h w h t o h a l ih a ssswih te o i e in o h lc me to d y c r n r y s n o . e rs lss o t a , n t e s ne ma
E AC 7 1 B;6 0 E C:2 0 7 4
d i 1 .9 9 j i n 1 0 — 6 9 2 1 .5 0 1 o : 0 3 6 / . s . 04 1 9 . 0 1 0 . 1 s
平 板 表 层 缺 陷检测 涡 流 阵列 传 感 器 的设 计
刘 波 , 飞路 , 良洁 罗 侯
( 国防 科 技 大 学 机 电 工 程 与 自动 化 学 院 , 沙 4 0 7 ) 长 103
摘 要 : 基于互感式传感器涡流检测的数值计算方法, 综合检测灵敏度和空间分辨率对涡流阵列传感器线圈单元不同中心
距 、 均 半 径 、 度 等 参 数 进 行 了分 析 。提 出 了与 涡 流 阵 列 检 测 不 敏 感 区 域 密 切 相 关 的 参 数 —— 线 圈 单 元 组 有 效 检 测 区域 比 平 高 率 , 于 该 参 数 进 行 了 涡 流 阵 列 传 感 器 排 布 方 式 的 优 化设 计 。 研 究结 果 表 明 : 同 检 测 条 件 下 , 圈 单 元 平 均 半 径 越 小 , 圈 基 相 线 线 单 元 高越 小 , 测 灵 敏 度 越 大 ; 圈单 元 中心 距 大 小 与 检 测 灵 敏 度 呈 先 递 增 后 递 减 的关 系 , 检 线 在接 近 且小 于 4倍 的 线 圈单 元 外 径
涡流探伤仪设计方案. (3)

涡流探伤仪设计方案1. 引言涡流探伤是一种常用的非破坏性检测方法,广泛应用于工业生产中对金属材料表面缺陷的检测。
为了提高涡流探伤的效率和准确性,本文设计了一套涡流探伤仪。
2. 设计原理涡流探伤的原理是基于法拉第电磁感应定律,当通过金属材料表面的导电体时,由于磁通变化引起的感应电流在导电体内形成涡流。
通过检测涡流的变化,可以判断出金属材料表面是否存在缺陷。
3. 设计方案涡流探伤仪主要由以下几个部分组成:3.1 发射线圈发射线圈是涡流探伤仪的核心部件,用于产生磁场。
发射线圈由绕组和磁芯组成,通过电流激励绕组产生磁场,并将磁场集中在待检测部位。
3.2 接收线圈接收线圈用于检测待检测部位产生的涡流,它由绕组和磁芯组成。
当待检测部位存在缺陷时,涡流的强度和方向会发生变化,接收线圈可以将这种变化转换为电信号。
3.3 信号处理器信号处理器用于接收和处理接收线圈产生的电信号,它通过放大、滤波和模数转换等处理,将电信号转换为数字信号,并进行相关算法分析,以实现对待检测部位缺陷的判断和定位。
3.4 控制系统控制系统用于控制涡流探伤仪的运行,包括发射线圈和接收线圈的电流控制、信号处理器的工作状态控制等。
控制系统还可以实现对检测参数的设置和调整。
4. 设计优化为了提高涡流探伤仪的性能,可以从以下几个方面进行优化:4.1 发射线圈优化优化发射线圈的设计和制造工艺,提高发射线圈的发磁效果和耐磨性,减小能量损耗,并增加线圈的寿命。
4.2 接收线圈优化优化接收线圈的设计和制造工艺,提高接收线圈的灵敏度和信噪比,减小线圈的尺寸和重量,便于操作和移动。
4.3 信号处理器优化优化信号处理器的算法和硬件设计,提高信号处理的速度和精度,增加数据存储和传输的能力,以适应各种检测场景的需求。
4.4 控制系统优化优化控制系统的设计和软件开发,简化操作界面和操作流程,提高控制系统的稳定性和可靠性,减少故障率。
5. 总结本文设计了一套涡流探伤仪的方案,通过优化发射线圈、接收线圈、信号处理器和控制系统等部分,提高涡流探伤仪的性能和可靠性。
介绍涡流检测技术的原理和实施步骤
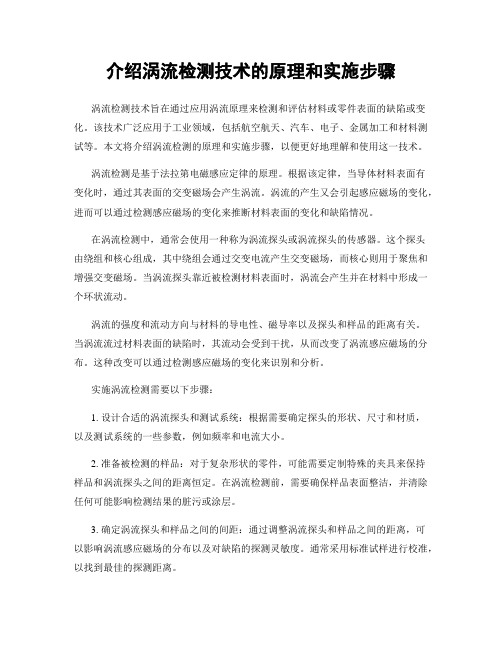
介绍涡流检测技术的原理和实施步骤涡流检测技术旨在通过应用涡流原理来检测和评估材料或零件表面的缺陷或变化。
该技术广泛应用于工业领域,包括航空航天、汽车、电子、金属加工和材料测试等。
本文将介绍涡流检测的原理和实施步骤,以便更好地理解和使用这一技术。
涡流检测是基于法拉第电磁感应定律的原理。
根据该定律,当导体材料表面有变化时,通过其表面的交变磁场会产生涡流。
涡流的产生又会引起感应磁场的变化,进而可以通过检测感应磁场的变化来推断材料表面的变化和缺陷情况。
在涡流检测中,通常会使用一种称为涡流探头或涡流探头的传感器。
这个探头由绕组和核心组成,其中绕组会通过交变电流产生交变磁场,而核心则用于聚焦和增强交变磁场。
当涡流探头靠近被检测材料表面时,涡流会产生并在材料中形成一个环状流动。
涡流的强度和流动方向与材料的导电性、磁导率以及探头和样品的距离有关。
当涡流流过材料表面的缺陷时,其流动会受到干扰,从而改变了涡流感应磁场的分布。
这种改变可以通过检测感应磁场的变化来识别和分析。
实施涡流检测需要以下步骤:1. 设计合适的涡流探头和测试系统:根据需要确定探头的形状、尺寸和材质,以及测试系统的一些参数,例如频率和电流大小。
2. 准备被检测的样品:对于复杂形状的零件,可能需要定制特殊的夹具来保持样品和涡流探头之间的距离恒定。
在涡流检测前,需要确保样品表面整洁,并清除任何可能影响检测结果的脏污或涂层。
3. 确定涡流探头和样品之间的间距:通过调整涡流探头和样品之间的距离,可以影响涡流感应磁场的分布以及对缺陷的探测灵敏度。
通常采用标准试样进行校准,以找到最佳的探测距离。
4. 进行涡流检测:将涡流探头放置在被检测材料的表面,并施加适当的交变电流。
通过检测感应磁场的变化,可以确定任何存在的缺陷或变化。
传统上,可以使用示波器、磁通计或涡流图像系统等设备来记录和分析感应磁场数据。
5. 分析和解释检测结果:根据涡流检测得到的数据,可以准确识别样品表面的缺陷或变化,并进行定性和定量评估。
无损检测技术中的涡流检测方法详解
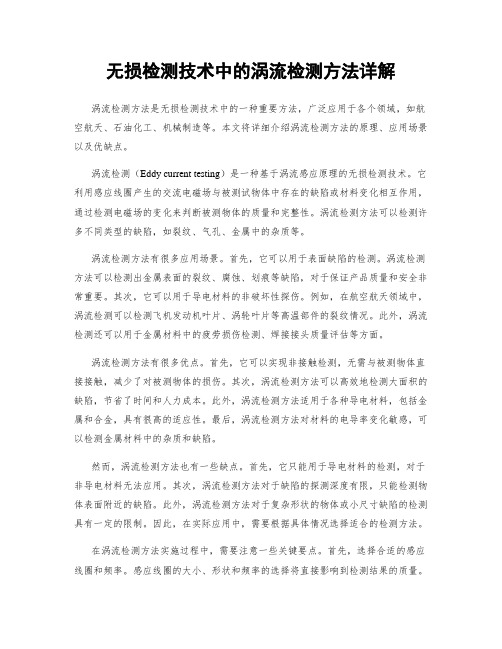
无损检测技术中的涡流检测方法详解涡流检测方法是无损检测技术中的一种重要方法,广泛应用于各个领域,如航空航天、石油化工、机械制造等。
本文将详细介绍涡流检测方法的原理、应用场景以及优缺点。
涡流检测(Eddy current testing)是一种基于涡流感应原理的无损检测技术。
它利用感应线圈产生的交流电磁场与被测试物体中存在的缺陷或材料变化相互作用,通过检测电磁场的变化来判断被测物体的质量和完整性。
涡流检测方法可以检测许多不同类型的缺陷,如裂纹、气孔、金属中的杂质等。
涡流检测方法有很多应用场景。
首先,它可以用于表面缺陷的检测。
涡流检测方法可以检测出金属表面的裂纹、腐蚀、划痕等缺陷,对于保证产品质量和安全非常重要。
其次,它可以用于导电材料的非破坏性探伤。
例如,在航空航天领域中,涡流检测可以检测飞机发动机叶片、涡轮叶片等高温部件的裂纹情况。
此外,涡流检测还可以用于金属材料中的疲劳损伤检测、焊接接头质量评估等方面。
涡流检测方法有很多优点。
首先,它可以实现非接触检测,无需与被测物体直接接触,减少了对被测物体的损伤。
其次,涡流检测方法可以高效地检测大面积的缺陷,节省了时间和人力成本。
此外,涡流检测方法适用于各种导电材料,包括金属和合金,具有很高的适应性。
最后,涡流检测方法对材料的电导率变化敏感,可以检测金属材料中的杂质和缺陷。
然而,涡流检测方法也有一些缺点。
首先,它只能用于导电材料的检测,对于非导电材料无法应用。
其次,涡流检测方法对于缺陷的探测深度有限,只能检测物体表面附近的缺陷。
此外,涡流检测方法对于复杂形状的物体或小尺寸缺陷的检测具有一定的限制。
因此,在实际应用中,需要根据具体情况选择适合的检测方法。
在涡流检测方法实施过程中,需要注意一些关键要点。
首先,选择合适的感应线圈和频率。
感应线圈的大小、形状和频率的选择将直接影响到检测结果的质量。
其次,设置合理的检测参数。
检测参数包括检测速度、灵敏度等,需要根据具体情况进行调整。
涡流阵列检测原理
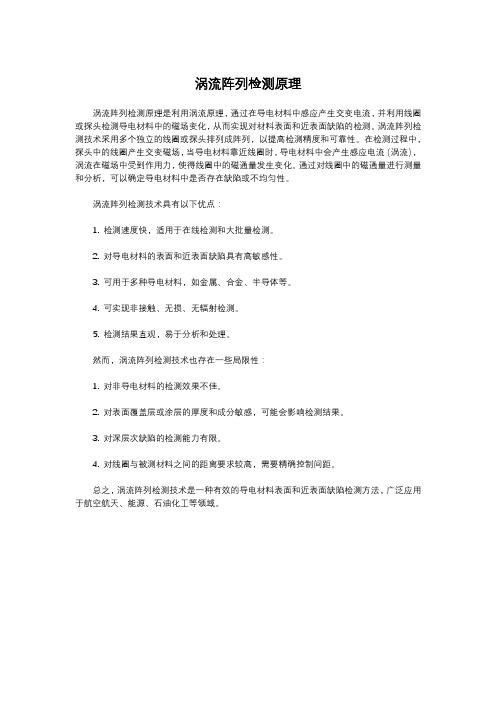
涡流阵列检测原理
涡流阵列检测原理是利用涡流原理,通过在导电材料中感应产生交变电流,并利用线圈或探头检测导电材料中的磁场变化,从而实现对材料表面和近表面缺陷的检测。
涡流阵列检测技术采用多个独立的线圈或探头排列成阵列,以提高检测精度和可靠性。
在检测过程中,探头中的线圈产生交变磁场,当导电材料靠近线圈时,导电材料中会产生感应电流(涡流),涡流在磁场中受到作用力,使得线圈中的磁通量发生变化。
通过对线圈中的磁通量进行测量和分析,可以确定导电材料中是否存在缺陷或不均匀性。
涡流阵列检测技术具有以下优点:
1. 检测速度快,适用于在线检测和大批量检测。
2. 对导电材料的表面和近表面缺陷具有高敏感性。
3. 可用于多种导电材料,如金属、合金、半导体等。
4. 可实现非接触、无损、无辐射检测。
5. 检测结果直观,易于分析和处理。
然而,涡流阵列检测技术也存在一些局限性:
1. 对非导电材料的检测效果不佳。
2. 对表面覆盖层或涂层的厚度和成分敏感,可能会影响检测结果。
3. 对深层次缺陷的检测能力有限。
4. 对线圈与被测材料之间的距离要求较高,需要精确控制间距。
总之,涡流阵列检测技术是一种有效的导电材料表面和近表面缺陷检测方法,广泛应用于航空航天、能源、石油化工等领域。
新型电涡流传感器测量电路设计

新型电涡流传感器测量电路设计电涡流传感器是一种能够将金属中的涡流效应转换为电信号的传感器,广泛应用于工业领域的位移、速度和金属表面缺陷等测量。
而新型电涡流传感器测量电路设计则是针对传感器测量信号处理的核心部分,其设计的好坏直接关系到传感器测量精度和稳定性。
这篇文章将从深度和广度的角度,全面评估新型电涡流传感器测量电路设计的关键要素,并探讨其在工业应用中的重要性。
1. 传感器原理及特点在进行新型电涡流传感器测量电路设计之前,首先需要了解传感器的工作原理和特点。
电涡流传感器利用涡流效应来检测金属表面的缺陷或测量金属零件的尺寸、形状等参数。
其工作原理是当金属表面被感应线圈的交变磁场影响时,会在金属内部产生涡流,并产生一个感应电动势,感应线圈测量出这个电动势,从而实现对金属的测量。
而新型电涡流传感器相比传统传感器具有更高的灵敏度、更快的响应速度和更广的测量范围。
2. 传感器测量电路设计要求在进行新型电涡流传感器测量电路设计时,需要考虑的关键要素包括信号放大、滤波、AD转换、数字信号处理等。
对于传感器的微弱信号,需要进行有效的放大处理,以提高信噪比和测量灵敏度;由于传感器信号可能存在噪声等干扰,需要设计合适的滤波电路来滤除杂散干扰,保证信号质量;另外,为了实现对信号的数字化处理和后续数据处理,还需要进行AD转换和数字信号处理的设计;对于工业现场的使用,还需要考虑电涡流传感器测量电路的稳定性和抗干扰能力。
3. 设计方案及优化在新型电涡流传感器测量电路设计中,可以采用多种电路设计方案来实现对传感器信号的高精度采集和处理。
常见的方案包括差动放大电路、滤波电路、高速AD转换电路等。
对于特定应用场景,可以根据实际需求选取合适的电路方案,并通过仿真、实验等手段对电路进行优化。
在差动放大电路中,可以采用低噪声、低偏置电流的运算放大器来实现微弱信号的放大,提高测量精度;在滤波电路中,可以采用低通滤波器来滤除高频噪声,保证信号的准确性。
涡流检测在铝板超声缺陷检测盲区中的应用研究
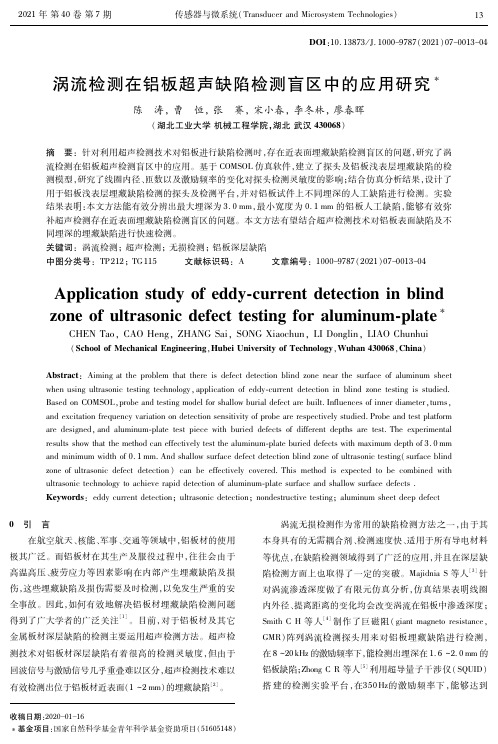
收稿日期:2020—01—16 基金项目:国家自然科学基金青年科学基金资助项目(51605148)
14 传 感 器 与 微 系 统 第 40卷
4.2mm铝板的检测深度;周德强等人[6]针对平板导体深层 缺陷检测问题,分别研究了反射式、透射式涡流检测中激励 频率及探头尺寸对检测灵敏度的影响,得到透射式探头对 深层缺陷 的 检 测 效 果 优 于 反 射 式 探 头 的 结 论;邹 国 辉 等 人[7]设计了一种双激励线圈结构的探头,使用隧道磁电阻 (tunnelingmagnetoresistance,TMR)作 为 检 测,通 过 实 验 对 探头参数进行优化,实现了对飞机铆钉周围埋藏缺陷的检 测;杨宾峰等人[8]利用脉冲涡流法对飞机多层结构中的裂 纹缺陷、腐蚀缺陷进行了检测和定量识别研究,对探头提离 的影响进行了深入研究。何泽等人[9]通过提取快速傅里 叶变换幅值谱中频率分量进行分析,实现了多层导电结构 中埋藏缺陷的检测与识别。虽然,涡流用于深层缺陷的检 测已经取得了一定的进展,但用涡流检测技术弥补超声检 测技术在铝板材近表面埋深缺陷检测中存在检测盲区缺陷 的问题的文献还很鲜见。
场的渗透 深 度 约 为 1mm,1kHz电 磁 场 的 渗 透 深 度 约 为
3mm,因此想要实现对最大埋深 3mm的铝板材深层缺陷的
检测,必须降低涡流线圈激励信号频率为 1kHz左右。控制
线圈内径及匝数不变,通过改变激励信号频率,研究在铝板
第 7期 陈 涛,等:涡流检测在铝板超声缺陷检测盲区中的应用研究
匝数条件下,线圈扫查铝板缺陷时的灵敏度 S
S=(Vbroken -Vnormal)/Vnormal×100%
(1)
式中 Vnormal为 铝 板 上 无 缺 陷 时,检 测 线 圈 的 输 出 电 压 值,
铁磁性平板构件腐蚀缺陷的脉冲涡流检测
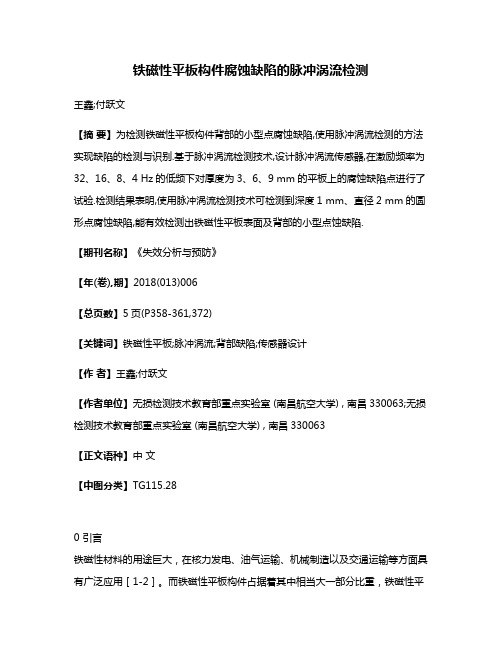
铁磁性平板构件腐蚀缺陷的脉冲涡流检测王鑫;付跃文【摘要】为检测铁磁性平板构件背部的小型点腐蚀缺陷,使用脉冲涡流检测的方法实现缺陷的检测与识别.基于脉冲涡流检测技术,设计脉冲涡流传感器,在激励频率为32、16、8、4 Hz的低频下对厚度为3、6、9 mm的平板上的腐蚀缺陷点进行了试验.检测结果表明,使用脉冲涡流检测技术可检测到深度1 mm、直径2 mm的圆形点腐蚀缺陷,能有效检测出铁磁性平板表面及背部的小型点蚀缺陷.【期刊名称】《失效分析与预防》【年(卷),期】2018(013)006【总页数】5页(P358-361,372)【关键词】铁磁性平板;脉冲涡流;背部缺陷;传感器设计【作者】王鑫;付跃文【作者单位】无损检测技术教育部重点实验室 (南昌航空大学) , 南昌330063;无损检测技术教育部重点实验室 (南昌航空大学) , 南昌330063【正文语种】中文【中图分类】TG115.280 引言铁磁性材料的用途巨大,在核力发电、油气运输、机械制造以及交通运输等方面具有广泛应用[1-2]。
而铁磁性平板构件占据着其中相当大一部分比重,铁磁性平板在长期使用过程中易产生疲劳裂纹和腐蚀缺陷,对人类的生命财产安全产生巨大的威胁。
为了避免此类故障的发生,需要对铁磁性平板件进行无损探伤。
近年来脉冲涡流(Pulsed Eddy Current,PEC)技术发展迅速,相比于传统涡流技术(Eddy Current)而言,PEC技术具有信号频谱丰富、响应速度快、可以承受较大的激励能量、检测信号信息含量高等优点[3-4],其丰富的频谱特性使得它不仅可以检测试件表面,也可以有效地检出试件内部缺陷。
Alicia Romero Ramirez等[5]使用漏磁检测技术(Magnetic Flux Leakage,MFL)对区分储罐底板顶部缺陷与底部缺陷进行了研究。
实验表明,MFL检测技术对于储罐底板的顶部缺陷以及底部缺陷都有着良好的识别能力。
基于涡流技术的管道表面缺陷探测系统
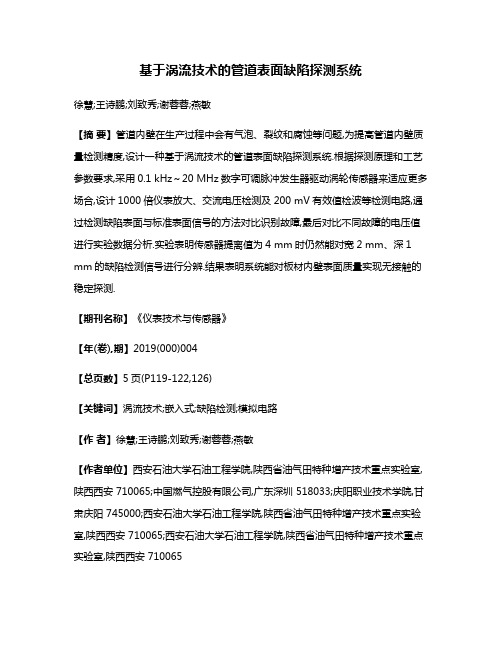
基于涡流技术的管道表面缺陷探测系统徐慧;王诗鹏;刘致秀;谢蓉蓉;燕敏【摘要】管道内壁在生产过程中会有气泡、裂纹和腐蚀等问题,为提高管道内壁质量检测精度,设计一种基于涡流技术的管道表面缺陷探测系统.根据探测原理和工艺参数要求,采用0.1 kHz~20 MHz数字可调脉冲发生器驱动涡轮传感器来适应更多场合,设计1000倍仪表放大、交流电压检测及200 mV有效值检波等检测电路,通过检测缺陷表面与标准表面信号的方法对比识别故障,最后对比不同故障的电压值进行实验数据分析.实验表明传感器提离值为4 mm时仍然能对宽2 mm、深1 mm的缺陷检测信号进行分辨.结果表明系统能对板材内壁表面质量实现无接触的稳定探测.【期刊名称】《仪表技术与传感器》【年(卷),期】2019(000)004【总页数】5页(P119-122,126)【关键词】涡流技术;嵌入式;缺陷检测;模拟电路【作者】徐慧;王诗鹏;刘致秀;谢蓉蓉;燕敏【作者单位】西安石油大学石油工程学院,陕西省油气田特种增产技术重点实验室,陕西西安 710065;中国燃气控股有限公司,广东深圳 518033;庆阳职业技术学院,甘肃庆阳 745000;西安石油大学石油工程学院,陕西省油气田特种增产技术重点实验室,陕西西安 710065;西安石油大学石油工程学院,陕西省油气田特种增产技术重点实验室,陕西西安 710065【正文语种】中文【中图分类】TG1150 引言油气储运过程中需要用到大量金属管道,如果管道内壁表面存在气泡裂痕等问题,会影响管道使用寿命,严重时还会发生油气泄漏、爆炸等问题,可能造成重大人身和财产损失[1]。
因此对管道内壁表面质量的检测显得非常重要。
目前,在生产过程中,人工进行内壁检测不仅效率低下而且可靠性不高,在生产完成后只能是通过敲击声测等接触式检测方式[2]。
由于钢管材质为金属,采用电涡流传感器搭建电流检测更加方便且可靠。
设计一种便携式的电涡流检测仪器,利用电桥式涡流检测技术实现内壁缺陷的检测识别,通过优化涡流传感器发射电路、设计桥式电路、激励放大和有效值检测电路等提取内部缺陷信号,通过标准信号与缺陷信号的对比进行系统验证试验。
表面缺陷的涡流检测
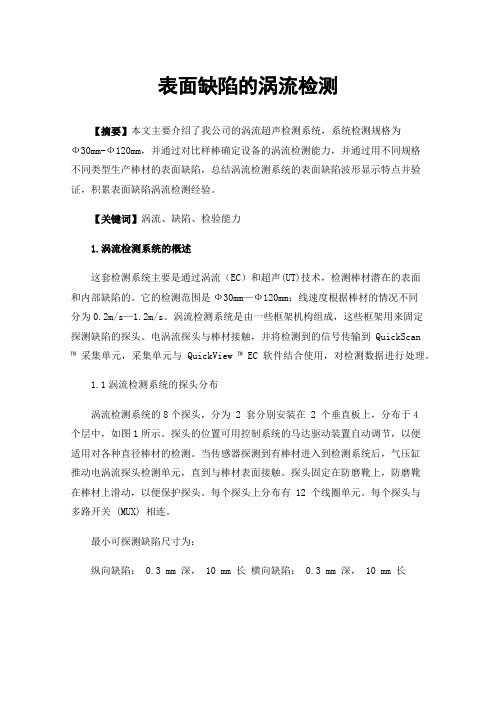
表面缺陷的涡流检测【摘要】本文主要介绍了我公司的涡流超声检测系统,系统检测规格为Ф30mm-Ф120mm,并通过对比样棒确定设备的涡流检测能力,并通过用不同规格不同类型生产棒材的表面缺陷,总结涡流检测系统的表面缺陷波形显示特点并验证,积累表面缺陷涡流检测经验。
【关键词】涡流、缺陷、检验能力1.涡流检测系统的概述这套检测系统主要是通过涡流(EC)和超声(UT)技术,检测棒材潜在的表面和内部缺陷的。
它的检测范围是Ф30mm—Ф120mm;线速度根据棒材的情况不同分为0.2m/s—1.2m/s。
涡流检测系统是由一些框架机构组成,这些框架用来固定探测缺陷的探头。
电涡流探头与棒材接触,并将检测到的信号传输到 QuickScan ™ 采集单元,采集单元与QuickView ™ EC 软件结合使用,对检测数据进行处理。
1.1涡流检测系统的探头分布涡流检测系统的8个探头,分为 2 套分别安装在 2 个垂直板上,分布于4个层中,如图1所示。
探头的位置可用控制系统的马达驱动装置自动调节,以便适用对各种直径棒材的检测。
当传感器探测到有棒材进入到检测系统后,气压缸推动电涡流探头检测单元,直到与棒材表面接触。
探头固定在防磨靴上,防磨靴在棒材上滑动,以便保护探头。
每个探头上分布有 12 个线圈单元。
每个探头与多路开关 (MUX) 相连。
最小可探测缺陷尺寸为:纵向缺陷: 0.3 mm 深, 10 mm 长横向缺陷: 0.3 mm 深, 10 mm 长图1涡流检测系统的探头分布2.涡流检测系统综合能力测试用φ60mm对比样棒对涡流系统进行综合性能测试,包括误报率、漏报率、盲区、信噪比、稳定性,通过测试结果判断涡流检测系统是否满足YB/T4083标准要求。
表1 φ60mm对比样棒信息表2.1对比样棒缺陷检测φ60mm对比样棒包含两种缺陷,分别是纵向槽和环形伤,具体分布如图2所示;经过检测,其中缺陷D1可以被相邻探头层同时发现,如图3所示。
铝薄板模拟分层缺陷的阵列涡流检测仿真
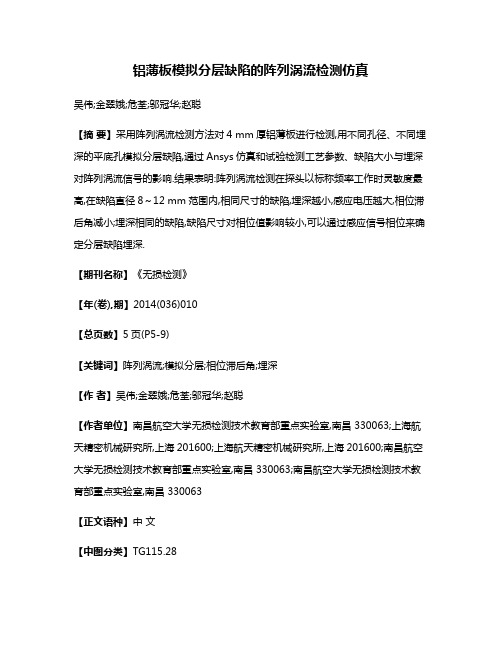
铝薄板模拟分层缺陷的阵列涡流检测仿真吴伟;金翠娥;危荃;邬冠华;赵聪【摘要】采用阵列涡流检测方法对4 mm厚铝薄板进行检测,用不同孔径、不同埋深的平底孔模拟分层缺陷,通过Ansys仿真和试验检测工艺参数、缺陷大小与埋深对阵列涡流信号的影响.结果表明:阵列涡流检测在探头以标称频率工作时灵敏度最高,在缺陷直径8~12 mm范围内,相同尺寸的缺陷,埋深越小,感应电压越大,相位滞后角减小;埋深相同的缺陷,缺陷尺寸对相位值影响较小,可以通过感应信号相位来确定分层缺陷埋深.【期刊名称】《无损检测》【年(卷),期】2014(036)010【总页数】5页(P5-9)【关键词】阵列涡流;模拟分层;相位滞后角;埋深【作者】吴伟;金翠娥;危荃;邬冠华;赵聪【作者单位】南昌航空大学无损检测技术教育部重点实验室,南昌 330063;上海航天精密机械研究所,上海201600;上海航天精密机械研究所,上海201600;南昌航空大学无损检测技术教育部重点实验室,南昌 330063;南昌航空大学无损检测技术教育部重点实验室,南昌 330063【正文语种】中文【中图分类】TG115.28冷轧薄板因具有良好的冲压成型、抗疲劳、抗腐蚀、高强度、高塑性等优势,在汽车、家电等行业的应用越来越广泛。
薄板在加工过程中,可能会产生裂纹和分层等缺陷,表面裂纹类缺陷会在薄板反复冲压加工过程中生长最终导致薄板断裂[1],分层类缺陷如冷扎钢板分层缺陷在实际检测中占总缺陷的50%[2]。
钢板分层类缺陷降低了承受载荷的有效厚度,特别是降低了钢板分层同方向的承载能力和该处薄板的抗弯曲性能;分层缺陷的边缘尖锐,对应力作用敏感,会引起严重的应力集中,在使用过程中造成应力疲劳[3]。
国内外很多学者在薄板类工件无损检测方面进行了研究。
吴永桥等对薄板类工件进行模态分析,通过模态分析对薄板类工件进行检测[4]。
吴时红等利用超声板波对钢薄板分层进行检测,发现超声板波对平行于表面的分层缺陷有较好的检出率[5]。
- 1、下载文档前请自行甄别文档内容的完整性,平台不提供额外的编辑、内容补充、找答案等附加服务。
- 2、"仅部分预览"的文档,不可在线预览部分如存在完整性等问题,可反馈申请退款(可完整预览的文档不适用该条件!)。
- 3、如文档侵犯您的权益,请联系客服反馈,我们会尽快为您处理(人工客服工作时间:9:00-18:30)。
义为线圈单元的检测灵敏度。
S
=
|
Vd -Vn Vn
|
(1)
其中,Vd 为检测线圈单元通过缺陷的感应电压,Vn
为检测线圈单元在无缺陷处的感应电压。 下面对线
圈单元中心距、线圈单元平均半径、线圈单元高对检
测灵敏度的影响进行研究。
(1) 线圈单元中心距
线圈 单 元 内 半 径 r1 = 0. 75 mm, 外 半 径 r2 = 3. 5 mm,高 h = 3. 0 mm,提离 l1 = 1. 0 mm,检测频率 f = 5 kHz。 激励线圈单元和检测线圈单元中心距 D
LIU Bo,LUO Feilu*,HOU Liangjie
( National University of Defense Technology,Changsha 410073,China)
Abstract:Based on numerical analysis of eddy current transmit鄄receiver sensor, different centre distance, average radius and high of eddy current array sensor coil unit are analyzed according to sensitivity and spatial resolution. This paper presents a parameter closely relating with less sensitive zone—efficient detecting zone ratio of coil unit group, which assists with the optimal design of the placement of eddy current array sensor. The results show that,on the same situation, the smaller the average radius and height are, the larger the sensitivity is. In nearly but smaller than quadruple outer radius,there is a peak value in the curve of the sensitivity. The smaller the average radius is,the higher of the spatial resolution is. The areas of the less sensitive zone and the possibility of failing to identity flaw is least considering the mixed cover zone of two adjacent coil unit group of the interlaced type eddy current array probe. Key words:eddy current array sensor;sensitivity;spatial resolution;efficient detecting zone ratio of coil unit group EEACC:7210B;7640摇 摇 摇 摇 doi: 10. 3969 / j. issn. 1004-1699. 2011. 05. 011
关键词:涡流阵列传感器;检测灵敏度;空间分辨率;线圈单元组有效检测区域比率 中图分类号:TM151. 4;TP391. 7摇 摇 摇 摇 文献标识码:A摇 摇 摇 摇 文章编号:1004-1699(2011)05-0679-05
摇 摇 涡流阵列( Eddy Current Array,ECA) 检测技术 是涡流无损检测技术中新兴的技术分支,它是通过 检测传感器结构的特殊设计,运用计算机技术和数 字信号处理技术,实现对材料和零部件的快速、有效 地检测[1-3] 。 涡流阵列传感器是阵列检测仪器的重 要组成部分,其设计的优劣在很大程度上制约着检 测仪器的灵敏度和空间分辨率[4-6] 。
在涡流 阵 列 传 感 器 设 计 理 论 研 究 方 面,2003 年,日本学者 Huang H 运用数值计算方法对核电站 蒸汽管道检测用涡流阵列传感器的线圈单元参数进 行了优化[11] 。 2008 年,Zaoui A 应用简化的体积分 法对阵列电磁场展开了研究,有效地缩短了缺陷检 测正问题、逆问题的数值计算时间,解决了有限元、 三维体积分法对阵列传感器仿真中的关键问题-划 分单元、节点太多,计算非常耗时,为阵列传感器的 设计提供了理论依据[12] 。
第 24 卷 第 5 期 2011 年 5 月
传感技术学报
CHINESE JOURNAL OF SENSORS AND ACTUATORS
Vol. 24摇 No. 5 May 2011
Design of an Eddy Current Array Sensor for Surface Flaw Detection in a Conductive Plate
他圆环的感 应 电 压; 最 后, 叠 加 所 有 圆 环 的 感 应 电 压,求得检测线圈单元的总的感应电压。
2摇 检测灵敏度
检测灵敏度是衡量涡流传感器检测性能的重要
指标之一,能够较好地反映传感器对于缺陷的检出
率。 设定仿真物理模型:假定待测试件的电导率滓 =
3. 82伊107 S / m,相对磁导率 滋r = 1,厚度 d = 3. 0 mm, 包含长 lc = 12 mm,宽 wc = 1. 0 mm,深 dc = 1. 2 mm 的 表面缺陷,其电导率 滓 = 0,相对磁导率 滋r = 1。 将由 缺陷引起的检测线圈单元感应电压的相对变化 S 定
最初的阵列传感器均由绕制的线圈构成。 1988 年,Krampfner Y D 和 Johnson D D 将计算机辅助设 计应用于涡流传感器设计,并制作了柔性阵列传感
器, 提 高 了 检 测 的 可 靠 性[7] 。 1991 年, 加 拿 大 Podney W N 和 Czipott P V 制作了微 SQUID 阵列传 感器,大大缩小了传感器线圈尺寸,该传感器检测水 平 精 度 1 mm, 垂 直 精 度 0. 3 mm[8] 。 1991 年, Melcher JR 提出了线圈磁力计阵列传感器[9] 。 2000 年,Yashan A 等 研 制 了 巨 磁 阻 阵 列 传 感 器。 2001 年,中国哈尔滨工业大学李德胜等提出了霍尔传感 器阵列,将霍尔器件用于磁测量。 2004 年,CODECI 传感器问世,该传感器将阵列传感器与 CCD 结合, 能够实时检测各种合金表面缺陷,缺陷深度检测精
第5 期
刘摇 波,罗飞路等:平板表层缺陷检测涡流阵列传感器的设计
6摇 81
变化越接近,两个缺陷越难于识别。 因此,线圈单元 平均半径越大,涡流阵列传感器的空间分辨率越小。
图 2摇 检测灵敏度与线圈单元平均半径的关系曲线
(3) 线圈单元高 线圈 单 元 内 半 径 r1 = 0. 75 mm, 外 半 径 r2 = 3. 5 mm,提离 l1 = 1. 0 mm,检测频率 f = 5 kHz。 激励 线圈单元和检测线圈单元中心距 D = 14. 0 mm,高 h 从 1. 0 mm 增加到 5. 0 mm。 线圈单元检测灵敏度 S 与高 h 的关系曲线如图 3 所示。 由图 2 可知,随着 线圈单元高度的增大,检测线圈单元感应电压幅值 变化单调递增,检测灵敏度单调递减。
收稿日期:2010-11-16摇 摇 修改日期:2011-01-20
传摇 感摇 技摇 术摇 学摇 报
680
www. chinatransducers. com
第 24 卷
度可达 0. 2 mm[10] 。 CODECI 传感器开启了阵列传 感器与其他检测方法在信息获取层的集成,代表了 阵列传感器发展的最高水平。
图 3摇 检测灵敏度与线圈单元高度的关系曲线
3摇 空间分辨率
空间分辨率( Spatial Resolution) 是反映涡流阵 列传感器对于邻近的多个缺陷的检出能力的一项指 标。 平板、缺陷和线圈单元参数如第 2 节所述,缺陷 1 和缺陷 2 距离 6 mm,在线圈单元匝数密度不变的 情况下,改变线圈平均半径。 扫描路径如图 4 所示, 记扫描路径为 X 轴线,两缺陷沿 X 轴的中心点位坐 标原点,检测线圈单元感应电压幅值变化如图 5 所 示。 由图 5 可知,线圈单元平均半径越大,缺陷处电 压幅值变化与两缺陷中心处( 即原点) 的电压幅值
从 8. 0 mm 增加到 16. 0 mm。 线圈单元检测灵敏度
S 与两线圈单元中心距 D 的关系曲线如图 1 所示。
观察图 1 可知,随着中心距的增大,检测线圈单元感
应电压幅值变化单调递减,检测灵敏度先增后减,在
中心距大约为 12. 8 mm 时达到最大。
图 1摇 检测灵敏度与线圈单元中心距的关系曲线
本文采用有限元数值计算方法,以检测灵敏度、 空间分辨率和线圈单元组有效检测区域比率等评价 指标为依据,对平板表层缺陷检测涡流阵列传感器 线圈单元内径、外径、高度等参数,线圈单元中心距, 线圈单元排布方式进行了设计。
1摇 理论基础
涡流传感器按感应方式分类,可分为自感式传感 器(或称参量式传感器) 和互感式传感器( 或称变压 器式传感器) ,按照检测比较方式可分为绝对式传感 器和差动式传感器。 涡流阵列传感器所有线圈单元 覆盖面积较大,且根据受检对象形状排布各异,仅含 一个激励线圈以产生适宜涡流检测的激励பைடு நூலகம்难度很 大、成本昂贵,因此现有的阵列传感器大多为所有线 圈单元采用同一尺寸,既可为激励线圈又可为检测线 圈。 另外,互感式传感器在检测灵敏度和信噪比优于 自感式传感器[13] 。 在检测比较方式上,由于考虑到差 动式传感器对受检件长而平缓的缺陷可能漏检,且易 产生难以解释的信号,因此大多采用绝对式传感器。