工艺总体方案Checklist
工艺总体方案
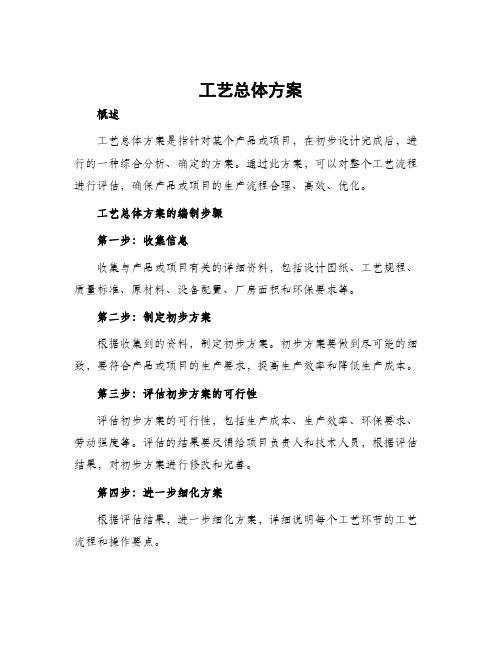
工艺总体方案概述工艺总体方案是指针对某个产品或项目,在初步设计完成后,进行的一种综合分析、确定的方案。
通过此方案,可以对整个工艺流程进行评估,确保产品或项目的生产流程合理、高效、优化。
工艺总体方案的编制步骤第一步:收集信息收集与产品或项目有关的详细资料,包括设计图纸、工艺规程、质量标准、原材料、设备配置、厂房面积和环保要求等。
第二步:制定初步方案根据收集到的资料,制定初步方案。
初步方案要做到尽可能的细致,要符合产品或项目的生产要求,提高生产效率和降低生产成本。
第三步:评估初步方案的可行性评估初步方案的可行性,包括生产成本、生产效率、环保要求、劳动强度等。
评估的结果要反馈给项目负责人和技术人员,根据评估结果,对初步方案进行修改和完善。
第四步:进一步细化方案根据评估结果,进一步细化方案,详细说明每个工艺环节的工艺流程和操作要点。
第五步:制定工艺标准依据细化出的工艺方案,制定出工艺标准,为生产提供技术依据。
第六步:进行生产实践在制定出的工艺标准的基础上,进行生产实践,检验工艺总体方案的正确性和可操作性。
工艺总体方案的优势工艺总体方案是工业生产过程中非常关键的一环。
它不仅可以确保产品的质量,还可以使企业在生产领域获得如下优势:降低生产成本通过对整个工艺流程的评估和优化,可以合理地利用设备和人力,大幅降低生产成本。
提高生产效率通过分析和研究每个工艺环节,找到生产过程中的瓶颈点,进而优化工艺流程,提高生产效率。
优化产品质量通过对整个工艺流程的把控,可以确保产品的质量稳定可靠,提高产品市场竞争力。
环保要求通过对整个工艺流程的评估和优化,可以降低废弃物的排放,达到环保要求,保护环境。
总结制定出正确、高效、合理的工艺总体方案,在企业生产中起到了举足轻重的作用。
在进行工艺总体方案编制的过程中,需要收集详尽的资料,制定初步方案,评估可行性,进一步细化方案,制定工艺标准和进行生产实践。
通过工艺总体方案的优化,可以降低生产成本、提高生产效率和优化产品质量,达到环保要求。
工艺总体方案
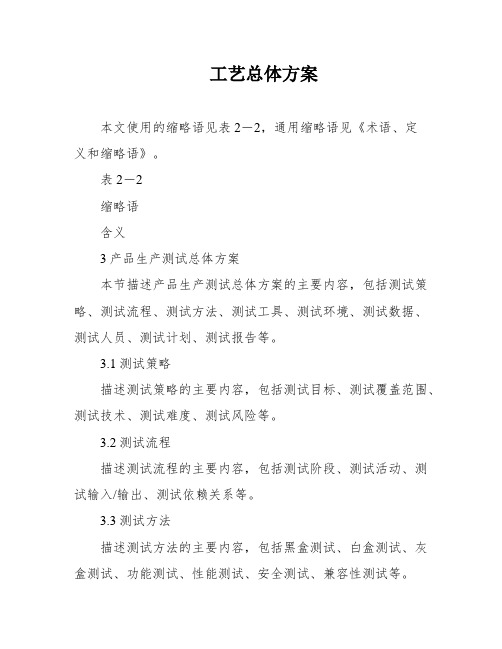
工艺总体方案本文使用的缩略语见表2-2,通用缩略语见《术语、定义和缩略语》。
表2-2缩略语含义3产品生产测试总体方案本节描述产品生产测试总体方案的主要内容,包括测试策略、测试流程、测试方法、测试工具、测试环境、测试数据、测试人员、测试计划、测试报告等。
3.1测试策略描述测试策略的主要内容,包括测试目标、测试覆盖范围、测试技术、测试难度、测试风险等。
3.2测试流程描述测试流程的主要内容,包括测试阶段、测试活动、测试输入/输出、测试依赖关系等。
3.3测试方法描述测试方法的主要内容,包括黑盒测试、白盒测试、灰盒测试、功能测试、性能测试、安全测试、兼容性测试等。
3.4测试工具描述测试工具的主要内容,包括测试管理工具、测试执行工具、测试自动化工具、测试仿真工具等。
3.5测试环境描述测试环境的主要内容,包括测试硬件、测试软件、测试网络、测试数据等。
3.6测试数据描述测试数据的主要内容,包括测试用例、测试输入、测试输出、测试数据生成方法等。
3.7测试人员描述测试人员的主要内容,包括测试人员的数量、资质、分工、培训、管理等。
3.8测试计划描述测试计划的主要内容,包括测试时间、测试资源、测试进度、测试质量、测试风险等。
3.9测试报告描述测试报告的主要内容,包括测试结果、测试问题、测试建议、测试评估等。
4工艺总体方案本节描述工艺总体方案的主要内容,包括工艺流程、工艺参数、工艺设备、工艺材料、工艺人员、工艺计划、工艺报告等。
4.1工艺流程描述工艺流程的主要内容,包括工艺步骤、工艺输入/输出、工艺依赖关系等。
4.2工艺参数描述工艺参数的主要内容,包括工艺温度、工艺压力、工艺速度、工艺时间等。
4.3工艺设备描述工艺设备的主要内容,包括工艺设备的种类、数量、规格、性能等。
4.4工艺材料描述工艺材料的主要内容,包括工艺材料的种类、数量、规格、性能等。
4.5工艺人员描述工艺人员的主要内容,包括工艺人员的数量、资质、分工、培训、管理等。
生产全流程分析与改进CHECKLIST
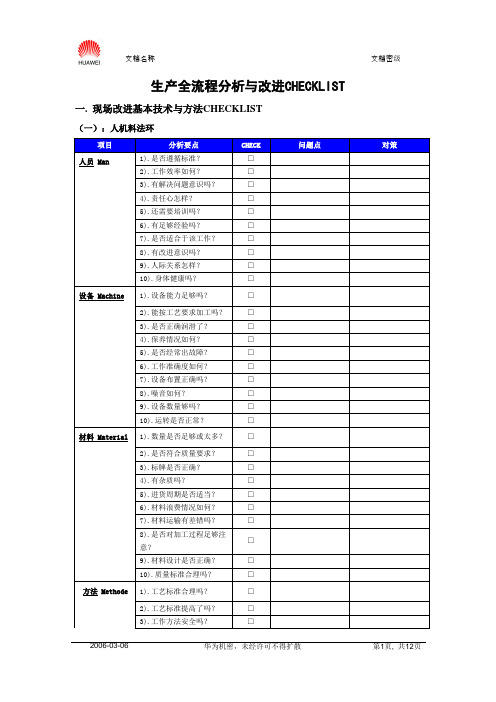
生产全流程分析与改进CHECKLIST 一.现场改进基本技术与方法CHECKLIST(一):人机料法环(二):5W2H(三):消除浪费对策二. 现场改进流程CHECKLIST1. 全流程程序分析分析要点:工序关系,物流次序、瓶颈工序、关键工序(控制评审点) 关键方法:ECRS 四大原则、五个方面、程序分析、5W2H (结合使用) 1) ECRS 原则2)五个方面3)程序分析2.全流程操作分析分析要点:整理工序操作流程;消除工序操作中不经济、停滞现象;工序操作中作业进行优化,消除不经济现象关键方法:人机操作分析;联合操作分析;双手操作分析1)人机操作分析目的:在机器的工作过程中,调查、了解在操作周期内,人与机的相互联系,以充分调动人与机的能量及平衡操作的分析。
要点:•人力作业时序分布•机器作业时序分布•合理分布人机时序•优化人机时序分布•提高人机工作效率2)联合操作分析定义:在生产现场,对常有两个或两个以上的操作员同时对一台机器(一项工作),进行工作,对其进行作业分析。
目的:取消或減少空閒或等待時間,以達到縮短工期要点:•发掘空闲时间•平衡人机工作•减少工作周期•合理分配人机•提高设备效率3)双手操作分析定义:调查、了解生产现场工人如何用双手进行实际操作的情况,称双手操作分析。
目的:雙手動作規範、平穩,去除無效動作,改變不合理的物料、工具、設備位置。
要点:•双手操作情况•用6W方式提问•有无优化动作•实施简化合并操作分析检讨点:3. 全流程动作分析分析要点:(1)了解操作者身体部位的动作顺序和方法;(2)了解以两手为中心的人体各部位是否能尽可能同时动作,是否相互联系; (3)明确各种动作的目的,动作过程中的必要动作和不必要动作; (4)了解必要的作业动作中两手的平衡。
关键方法:目视动作观察法(动素分析;双手操作分析);影像动作观察法主要工具:Right ans left hand charts (左右手分析法)/Simo charts ;Process chart (流程图);Operation process chart (操作流程图) 1) 动素分析定义:动素分析把动作分类归纳成 18 种基本的最小动作单位,可以分成以下三 大类动素。
很全面的PCB_checklist_表格
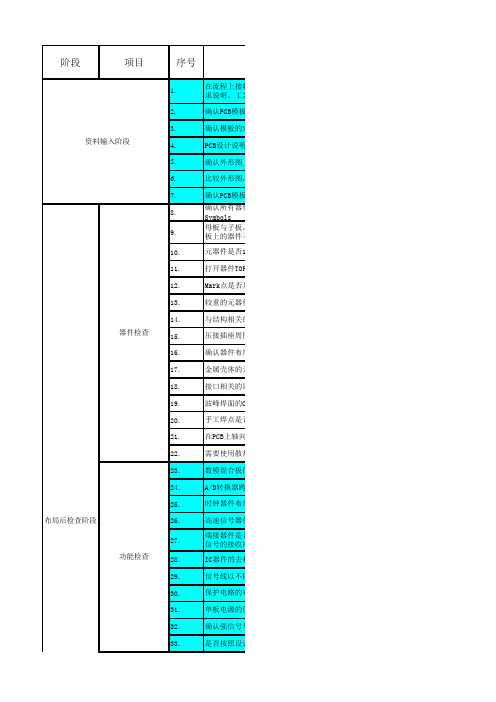
5.
确认外形图上的禁止布放器件和布线区已在PCB模板上体现
6.
比较外形图,确认PCB所标注尺寸及公差无误, 金属化孔和非金属化孔定义准确
7.
确认PCB模板准确无误后最好锁定该结构文件,以免误操作被移动位置
8.
确认所有器件封装是否与公司统一库一致,是否已更新封装库(用viewlog检查运行结果) Symbols
0805及其以下封装求的丝印添加是否正确置有防静电和射频板标识射频板使用的插板方向标识是否对应确标识了槽位名槽位号端口名称护套方向否遗漏位置是否能正确标识器件否符合公司标准要求管脚排列顺序第1脚标志器件的极性标志连接器的方向标识的正确性盘安装的chip元件0805及其以下封装如电阻电容与其焊盘连接的印制线最好从焊盘中心位置对与焊盘连接的印制线必须具有一样的宽度对于线宽小于03mm12mil的引出线可以不考虑此条规定从soicplccqfpsot等器件的焊盘的两端引出板边推荐为大于2mm最小为05mm皮到板边12mm最小为05mm孔径最好不小于板厚的110是否100布通率是否100没有达到100的需要在备注中说明测试点的网络都是经确认可以进行精简的时应该尽量避免出现没有网络连接的死铜孤岛还需注意是否有非法连线未报告的drcottom上的大面积铜箔如无特殊的需要应用网格铜单板用斜网背板用正交网线宽03mm12距05mm20mil区的元件焊盘应设计成花焊盘以免虚焊
29.
信号线以不同电平的平面作为参考平面,当跨越平面分割区域时,参考平面间的连接电容
30.
保护电路的布局是否合理,是否利于分割
31.
单板电源的保险丝是否放置在连接器附近,且前面没有任何电路元件
32.
确认强信号与弱信号(功率相差30dB)电路分开布设
ESI结构工艺评审点检表(checklist)[空白模板]
![ESI结构工艺评审点检表(checklist)[空白模板]](https://img.taocdn.com/s3/m/c3ac82dfb90d6c85ed3ac6a9.png)
序号类型点检项目点检人不符合项原因分析建议措施责任单位/责任人跟进反馈关闭状态改善完成时间复查情况1客户信息、项目简况、评审时间是否明确。
23D图档、CMF、工艺标准等资料客户是否提供。
3产品材质、胚料重量是否确定。
4客户特殊加工要求是否明确,是否满足我司技术能力。
5整体工艺方案和加工顺序是否合理,夹数是否过多,部分夹位能否合并。
6材料余量预留是否合理,能否进一步减少。
7定位基准是否合理可靠,尽可能避免多次转换基准,夹持方式是否牢固。
8刀具选型是否合理,有无特殊要求,刀具加工参数和寿命评估是否合理。
9工序3D有无接刀问题,如何避免接刀风险,同一夹台阶光刀尽可能用一 把刀完成。
10产品变形风险评估,如何有效解决产品加工变形导致的尺寸不稳问题。
11定位孔是否已考虑防呆,定位孔直径公差及深度是否合理,有没有考虑加倒角,加工方式是否合理,大批量生产是否可靠。
12有无放大偏位特征,如何避免。
13加工冷却方式有无特殊要求。
14外观有无特殊要求,外观面不允许出现接刀,外观刀材质选择是否合理。
15容易出现毛刺的特征如何解决毛刺问题,有没有加专门去毛刺刀具刀路。
16进刀位和退刀位是否合理,有无撞刀风险。
17是否需要断刀检测,探头,探点位选择是否合理,探点数量是否合理,变量选择是否正确。
18是否需要记版本号和机台号。
19每次飞面厚度0.30mm,飞面光刀后,接刀纹要控制在0.02以内。
20裙边宽度定义D6销钉+4mm+7mm为准,外侧壁优先考虑分夹加工;外侧壁合夹加工的裙边留料定义D6销钉+4mm+外侧壁刀具过刀直径+1.0mm。
21宽度方向以注塑前半成品尺寸(铝挤面)单边+0.5mm,长度方向以注塑前半成品尺寸(锯切面)单边+1.0mm。
22CNC1飞面,并加工一组定位孔只给CNC2使用,定位孔直径D5,方便后工序二次使用时扩孔。
23CNC2或CNC3加工内腔的工序需同时在产品内腔及外裙边加工两组定位孔作为后工序直至外侧壁工序的定位。
精密设备加工组装Checklist

精密设备加工组装Checklist精密设备加工组装Checklist设备编码:序号类别检查条款检查标准检查工具评审级别自检状况自检结果抽检结果备注(若不涉及请备注)1来料标准件、外购件来料标准件须和BOM完全一致,所有外购件收货必须检查检验合格证,且零件分开包装运输。
关键外购件要保留出厂检验报告。
目检 AOK□NO□OK□NO□2 机加来料机加件收货时要求保留出厂检验报告,所有机加件形位公差、粗糙度、表面处理应符合图纸要求。
并对零部件关键尺寸使用三坐标进行入厂检验,并保留检验记录。
三坐标AOK□NO□OK□NO□3精密零件、模组来料1.精密零件及外购组件来料尺寸,外观,颜色等均符合图纸要求,并保留检验记录。
三坐标ANO□OK□NO□4 2.在检时需用酒精、清洁油等对表面清洁干净,严禁中转途中碰伤,划伤等。
目检 BOK□NO□OK□NO□5 装配环境及装配人员要求装配环境及装配人员要求1.车间温度、湿度、5S等符合相关要求;整机装配平面干净,且过程必须保证机台底座水平。
水平仪AOK□NO□NO□6 2.装配人员要求有精密设备装配经验。
目检 AOK□NO□OK□NO□7设备整体要求外观1.外观整体造型讲究、美观、协调,设备尺寸和外观颜色与技术要求一致。
目检 AOK□NO□OK□NO□8 2.外观表面平整光滑、缝隙均匀,无以下明显缺陷(如凹凸、无尖锐凸台,无撞伤,划伤人员风险、无掉漆、锈蚀等)。
设备主体架构及其它各部件均需进行防锈处理。
目检 AOK□NO□OK□9 3.设备铭牌格式符合技术要求书要求,信息填写完整,并已安装目检 BOK□NO□OK□NO□于设备上。
10装配过程要求部件、组件、零件等装配过程1.所有组件部件在装配过程中必须使用相关检测设备对精度进行把控。
千分表AOK□NO□OK□NO□11 2.零件有掉落、撞击、划伤等异常情况必须送检验室从新检验经检验员签字后方可继续使用。
目检 AOK□OK□NO□12 3.严禁设备,组件,部件上存在零件有划伤,撞伤等不良品装配使用。
制程认证CHECKLIST模板

制程认证 结论:
部门
品质 工程 生产
审核人
版本
自检认证结 果
是
是
是 是 是 是 是 否 是 是 是 是 是 否 不涉及 不涉及 不涉及 不涉及 不涉及 不涉及 不涉及 不涉及
不涉及 否 是 是 是 是
是 否 是
是
是
确认人
是 是 否 不涉及 不涉及 不涉及
不涉及
是 是 是 是 是 是 是 是
是
自评审核时间
包装方案是否得到客人认可
是否还有其他风险
必开模具数量(模具清单)
所有必开模具是否均开模完成并验收合格,若无,请记录最新状况
开模总数量 3、模具检具 所有模具是否均已加工完成并验收合格,若未完成需记入最新状况( 必开模
具中已列的不和格项不需要再列)
工装/检具数量
所有工装检具是否都已通过验收并统一编号管理
喷涂保护工装是否得到有效验证。
直通率是否大于90%
是否还有其他风险
组装
SOP/SIP是否合格,需要包含质量控制计划中的所有内容,需要跟线验证, SOP需要和实际作业一致
工装、检具是否充足并验收合格,依照《工装检具管理》验收
是否有相似物料,是否有做防混料检具。
气密测试工装是否有验证OK
直通率是否大于90%
直通率是否大于95%
是否还有其他风险
丝印
丝印工装数量是否充足并验收合格 2.工艺 SOP/SIP是否合格,需要包质量控制计划中的所有内容。
工装、检具是否已经充分验证OK
直通率是否大于95%
是否还有其他风险
喷涂
是否明确上挂悬挂点和典型喷涂参数
线速、炉温设置是否符合工艺条件要求
前处理槽液是否例行监控并记录保存完整
新供应商考察checklist

24 25 26 27 28 29 30 31 32 33 34 35 36 37 38 39 40
有无收入检查标准书(程序书),标准是否适 用 检查程序书中SAMPLING方法及检查点是否 明确 有无无检查产品的品质保证方法 检查记录是否可以按照LOT或日期确认检查明 细,并判定合格/不合格 收入/外驻检查对不合格品的处理程序是否明 收入检 确,对策收取及改善是否有实施 查 各业体是否定期反馈品质状况,并进行改善中 外驻生产是否按照检查标准进行检查中 是否有特殊物品使用的程序及分类管理的体系 特殊采购物品使用发生问题时处理规定是否有 明文规定 是否有上述特殊采购物品使用的内部运用标准 是否有指定主要管理工程,检查项目是否明确 检查项目的合格/不合格判定标准要明确,需 要时否有限度样板 不合格品识别,维修后是否有检查 工厂检 各工序制作检查日报,是否按层进行中 查 是否有主要工艺不良的原因分析及改善对策的 树立,实施 生产计划设立标准及目标的管理有无及合理库 存管理体系 月生产能力及最近3个月产线利用率 合计
0~5分 0~5分 0~5分 0~5分 0~5分 0~5分 0~5分 0~5分 0~5分 0~5分 0~5分 0~5分 0~5分 0~5分 0~5分 0~5分 0~5分
工程管 具备完整的作业指导书,包括在作业时使用设 理 备的Spec 重要工序(CTQ工序,顾客不满工序,特殊工序, 不良多发工序等)有明确管理 作业指导书对员工起到指导作用,按照标准操 作并熟知 工程发生时有处理流程,通过内部检测分析类 型并树立对策 所有工序使用合理的设备及JIG 为生产良品对装备及JIG定期进行检查及校正, 并有计划的实行中 为提高生产效率,有导入及运用自动化设备 对特殊工序有设备及工序的管理条件,并实行 对备用设备进行日常及定期管理,管理记录良 好 各设备的运用及履历管理 需设立作业品质基准的工序有明确设立标准 品质标准确定困难是采用限度样板的方式 工程品质Data整理管理,并持续积极的改善 操作员熟知品质标准,并运用于实际操作中 有明确判定良,不良品的标示,不良品有处理 流程并遵守中 工程发生时有处理流程,通过内部检测分析类 型并树立对策 在需保护装备的工序中为安全及清洁是否着装 良好 设计变更(ECO/修模)的履历管理 重要工序4M(Man, Machine, Material, Method)变更时,根据管理标准,及时培训 管理 工程Control Plan管理/监督,通过定期的工 程审核管理及遵守有无
PCB_xxxxxxxx.x+设计布局Checklist(工艺)

XXXX有限公司中试工艺组PCB设计布局CHECK LISTPCB名称.版本: MA31GAMU.1项目内容结果备注1 PCB的尺寸长/宽/厚(含孔)是否符合结构要素图要求?是[■]否[ ]免[ ]2 所有器件的封装是否正确?是[ ]否[ ]免[ ]3 TOP&BOTTOM面宽边板边5mm内是否没有SMD器件影响传送?是[ ]否[ ]免[ ]4 条码的位置是否已经预留?是[ ]否[ ]免[ ]5 SMD器件之间的距离时候足够?是[ ]否[ ]免[ ]6 SMD器件和插件之间的距离足够?是[ ]否[ ]免[ ]7 插座、插针的插拔空间是否预留出?是[ ]否[ ]免[ ]8 内存条、扣板的插拔空间是否预留出?是[ ]否[ ]免[ ]9 波峰焊的距离要求是否优先考虑?是[ ]否[ ]免[ ]10 插件元件焊盘和SMD元件距离是否大于1.27mm?是[ ]否[ ]免[ ]11 压接器周围的禁布区(3mm)内是否没有器件?是[ ]否[ ]免[ ]12 是否有特殊封装器件(例如底部带焊盘的)?是[ ]否[ ]免[ ]13 BGA的禁布区是否已经预留出?是[ ]否[ ]免[ ]14 带散热器的器件散热器的位置是否预留出?是[ ]否[ ]免[ ]15 TOP&BOTTOM面的器件高度没有超出要素图的要求?是[ ]否[ ]免[ ]16 拉手条的安装区域内没有器件干涉?是[ ]否[ ]免[ ]17 扣板位置是否没有超高器件干涉?是[ ]否[ ]免[ ]18 螺钉安装孔的周围禁布区是否足够?(注意BOTTOM面与接手条支柱接触区)是[ ]否[ ]免[ ]19 TOP&BOTTOM面的器件是否没有二次回流掉件的问题是[ ]否[ ]免[ ]20 热敏感器件是否远离高热器件?是[ ]否[ ]免[ ]21 背板是否考虑SMD元件在一面布局?是[ ]否[ ]免[ ]22 背板上的连接器是否优先考虑压接?是[ ]否[ ]免[ ]23 有方向的插件器件是否按照同一方向布局?是[ ]否[ ]免[ ]24 结构要素图中禁布区内是否无器件?是[ ]否[ ]免[ ]25 背板中连接器卡扣朝下是[ ]否[ ]免[ ]26 正反面的BGA是否相对是[ ]否[ ]免[ ] 存在的其它问题:检查人签名:日期:。
QPA工艺审核

3、追溯管理
是否可以追溯到原材料的相关资料?并对涉及的范围进行调查处理?(记录) 1)是否对异常发生原因进行分析?
2 2 2 2
4、纠正与预防
2)是否建立纠正与预防再次发生的对策? 3)是否对纠正与预防再次发生的对策进行检定与确认效果?
QPA 过程质量工艺审核checklist
项 目 检 查 清 单 得分 备 注
四、生产制造标准 1)是否有零件、部位及组装顺序的“工艺流程图”? 2)流程图、控制计划、作业指导书是否明确制订部门、制订者、制订日期等? 1、作业标准 3)每个工位的作业指导书上的内容是否与作业员实际操作相一致? 4)“流程图”或“作业指导书”中,是否明确注明有ESD措施要求? 5)“流程图”或“作业指导书”中,是否明确注明有安全的工位? 1)流水线上是否标示有工程名称(与工艺流程图描述一致)? 2 2 2 2 2 2 有,在产品开发阶段制定“过程流程图”,见:30017498产品过 程流程图 在《产品质量先期策划指导书》/ZD-22中规定了流程图、控制计 划、作业指导书制定者和日期;见《产品质量先期策划指导书》 一致,见30017498工艺卡与实际工艺及记录 N/A 不涉及“ESD”
2)是否有证据证明产品项目已确实得到保障(指导书规格明确,作业员能记住并确实作业)?
2
3)是否对控制计划、作业指导书中的参数是否明确?对作业参数是否点检及实验记录?
2
2、现场实施
4)要求定期检查的测定保证项目是否定期检查?(烙铁温度,电/风批力度,ESD记录等) 5)成品检查处(或检查区域)是6
能充分保证产品运转、存放的空间,通道畅通无占用、堵塞现 象,详见附件 《化学品管理规定》化学品基本按需采购,入库单及领用单的记 录,脱模剂的入库单及领料单 装卸模具过程中电动葫芦的使用,1、员工持证上岗2、《电动葫 芦的安全操作规程》,3、相关的检查记录 有醒目的标识,在发生异常状况时,可及时按下紧急停止开关 配电间, 车间柱子等有警示标识
设计和项目checklist

项目周会 Check List(草案)
投模决策 模具制造
ESL1 ESL2
小批 pilot 量产
项目周会 Check List(草案)
市场调研、成本分析 项目研究计划表:设计工程师研究计划(样机研究,标准研究,功能结构评估) 专利搜索报告 标准研究计划表:品质工程师标准研究计划(标准释放,对比,解读,培训)、 测试资源评估清单:测试资源评估表准备(测试工装,仪器,设备,耗材) 可行性分析报告释放计划 意向书:明确 目标市场/目标成本/目标客户/主要性能参数/项目计划 客户流程确认(CPA,KFPS,各阶段样机需求计划) 实验大纲编制,讨论,释放计划
意向书 实验汇总表 拆机分析报告
ESL2物料到料清单:ESL2物料监控,到料测量确认 项目改进计划表更新:整机装配问题汇总,改善计划表更新执行监控 项目改进计划表更新:Artwork及ID参与确认相关外观及造型的问题点recheck. 装配工艺表:装配工装,检具,设备改善结果验证 测试设备清单:测试资源改善验证 ESL1品质评估报告:ESL1品质评估计划,测试情况监控跟踪(特别关注:使用,耐久,寿 命,温升,EMC) 项目改进计划表更新:ESL1阶段问题点改善结果确认 小批申请单释放 认证摸底,认证样机准备(特别关注:噪音,温升,耐久) FFU摸底,客户特殊测试要求摸底,FFU样机准备 小批检指,图纸发行计划,检具移交IQC计划 BOM进系统计划(物料清单爆炸图释放计划,商务档案释放计划) 试制完成2天内将包装样机安排寄出
PM
投模决策后5个工作日
包装 投模决策前5个工作日
RD
投模决策后5个工作日
RD
EOS后3个工作日
QA
工艺总方案模板

工艺总方案模板篇一:工艺方案模板一零件的工艺分析和毛坯的选择1. 零件工艺性分析(1)审查工程图(2)主要尺寸精度分析和表面质量分析(3)形位公差分析(4)结构工艺分析二制定机械加工工艺方案 1.确定审查类型根据样机制造要求,仅需单件生产。
2. 确定毛坯(1)(铝或45#)的切削性能分析(2)毛坯的选择分析3.拟定工艺路线(1)确定工件的定位基准(2)选择加工方法(3)拟定工艺路线三加工工序设计 1选用加工设备(主要写写机床型号。
工作台尺寸,行程是否足够空间加工)2选择工艺装备(1)装夹方式(2)刀具选择及对应加工位置(简略描述)(3)量具选择及测量位置、尺寸(一定程度的分析描述)四.填写工艺文件(1)工量具表(2)各工序卡篇二:工艺总体方案模板生产测试和工艺总体方案(仅供内部使用)编制:审核:会签:批准:修订记录文件的版本号由“V ×.×”组成,其中:a)小数点前面的×为主版本号,取值范围为“0~9”。
文件进行重大修订时主版本号递增1; b)小数点后面的×为次版本号,取值为“0~9,a~z”。
文件每修改一次时次版本号递增1;主版本号发生改变时,次版本号重新置0;c)未批准发布的文件版本号为V0.×版,批准发布时为版。
当主版本号发生改变时,前面只有次版本号不同的修订记录可以删除。
目录1引言 ................................................ ................................................... ................................................... .. 4 2编写目的................................................. ................................................... ............................. 4 预期的读者和阅读建议 ................................................ ................................................... (4)术语、定义和缩略语 ................................................ ................................................... (4)术语、定义................................................. ................................................... ......................... 4 缩略语 ................................................ ................................................... (4)3 4产品概述 ................................................ ................................................... ............................................. 5 工艺 ................................................ ................................................... ................................................... .. 5工艺分析................................................. ................................................... ............................. 5 工艺路................................................... ............................. 5 工艺流程................................................. ................................................... ............................. 5 工艺防护要求 ................................................ ................................................... . (5)环境要求 ................................................ ................................................... ...................... 5 操作要求 ................................................ ................................................... . (5)加工控制................................................. ................................................... .. (5)外协................................................... ......................... 5 自加工................................................. ................................................... . (5)5关键工序控制 ................................................ ................................................... ...................... 6 工装 ................................................ ................................................... . (6)生产测试 ................................................ ................................................... (6)生产测试分析 ................................................ ......................................................................... 6 测试要求及装备 ................................................ ................................................... .................. 6 首件鉴定................................................. ................................................... .. (6)6 7产能分析 ................................................ ................................................... ............错误!未定义书签。
产线设备和工艺验收checklist(浓缩版)

工序项目裁剪房温湿度裁剪尺寸开孔焊接参数焊接外观拉托力层压机EL EL图片直角焊接间距返工区域层压参数温度偏差剥离力真空度交联率接线盒打胶非自动益胶补胶的胶量自动溢胶的总胶量接线盒焊接温度AB胶配比rate of A and B inweight 自动串焊机裁剪层压机叠层装框标准温度范围为23+/-3℃,湿度小于30~70RH%;3mmfollow作业指导书无锡珠、毛刺,表面清洁,无明显助焊剂;无空焊、虚焊、侧焊、过焊、破片;焊带与电池片主栅线错位≤0.5mm≥2N-焊接标准见作业指导书见60和72pcs间距要求,和胶带贴方式串焊返工不良区域均需要有吸盘实测温度与设定温度的误差-1℃~+2℃以内 ;±3℃EVA和背板≥40NEVA和玻璃≥40N120s内真空度达到100pa以下80~95%接头处预留5~7mm,400+/-15℃AB胶配比标准,回天5299W-S,质量比A:B为5:1,质量比值范围4.8~5.2;天山1533,质量比A:B为5.5:1,质量比值范围5.3~5.7;天辰HT6360/AB,质量比A:B为5.5:1,质量比值范围5.3~5.7 ;要求Y/N备注温湿度要求24h均达到分别记录裁剪样品量50pcs,按照点检表单以样品为准,无毛刺,光滑满足作业指导书中焊接温度等参数要求工废建议值≤0.2%正反面EL图片清晰可见要求员工熟练要求层压后无间距不良(此为重点关注)要求员工手不能拿电池片在层压要求的范围内,满足要求,I区域: A≤2mm2,Q≤2E区域: A≤2mm2,Q≤3距玻璃边沿5mm,距电池片边缘0.3mm,电池片上,都不允许有气泡,无鼓包;不允许有尖锐物造成之穿刺性凹坑,无破损、孔洞及任何尺寸的带电体伸出背板,无污迹、硅胶、EVA、纸屑等残留,无水印;分别是使用长杆和多路测温仪进行温度监控层压机4个位置均要做层压机4个位置的交联率均要做按照接线盒轨迹设定好程序型材内框打胶两侧空留≤5mm;底部铺满,总胶量≥65ml;边框型材打胶,平铺槽底深度2-3mm拆框后型材底部均有胶量,并且四周均匀益胶要求灌胶设备能打达到上述参数要求。
(最新)汽车内外饰工艺数据checklist
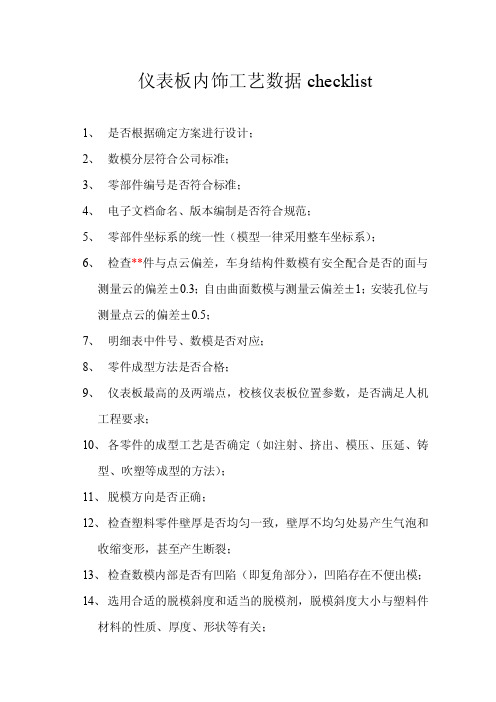
仪表板内饰工艺数据checklist1、是否根据确定方案进行设计;2、数模分层符合公司标准;3、零部件编号是否符合标准;4、电子文档命名、版本编制是否符合规范;5、零部件坐标系的统一性(模型一律采用整车坐标系);6、检查**件与点云偏差,车身结构件数模有安全配合是否的面与测量云的偏差±0.3;自由曲面数模与测量云偏差±1;安装孔位与测量点云的偏差±0.5;7、明细表中件号、数模是否对应;8、零件成型方法是否合格;9、仪表板最高的及两端点,校核仪表板位置参数,是否满足人机工程要求;10、各零件的成型工艺是否确定(如注射、挤出、模压、压延、铸型、吹塑等成型的方法);11、脱模方向是否正确;12、检查塑料零件壁厚是否均匀一致,壁厚不均匀处易产生气泡和收缩变形,甚至产生断裂;13、检查数模内部是否有凹陷(即复角部分),凹陷存在不便出模;14、选用合适的脱模斜度和适当的脱模剂,脱模斜度大小与塑料件材料的性质、厚度、形状等有关;15、载塑料零件上,是否避免锐角及直角过渡;16、安装方式是否正确;17、正确的选择定位尺寸基准,应尽可能使设计基准和工艺基准重合,避免装配过程中,误差的积累过大;18、经常所装的零部件,为了更换方便,应以螺栓成自攻螺钉和簧片螺母配合紧固连接;19、明确安装工具,预留所需的被动空间;20、在安装过程中,需要进行装配调整的零部件要考虑孔位的合理布置及适当地预留间隙调整;21、考虑到仪表板内线束的固定,明确线卡固定点及固定方式,钣金上的线束的过孔是否加以保护套成翻边结构;22、检查保险杆外表面在X方向是否有负面保证模具成型后外表面的完整和美观;23、检查外表面面与面的偏差是否超标;24、检查外表面可增厚性;25、检查零件的强度是否适当,是否有强度薄弱的区域(薄弱的区域需增加加强筋);26、检查零件的材料选用是否适当(如毛面需要镀铬地零件应选用同ABS等可镀铬材料,不能选用PP难镀的材料;27、在塑料件结构设计中,为避免转角处应刀集中,应采用圆弧过渡,这对于模具制造及使用寿命足很有利的;28、对于保险杆要进行相关国家法规的检查(接近角、离车角等);29、检查零件开孔的合理性,孔一般设计成通孔,避免¢5以下盲孔,盲孔底部应设计成半球面或圆锥面,以利物料流动、孔径与深度比一般为1∶2或1∶3 ;30、检查前保险杆与翼子板的间隙是否合适(与翼子板间隙,轿车1—3mm);31、检查前保险杆与前大灯的间隙【与前大灯的间隙:2.5(下限为2.5大小)—4mm】;32、检查前保险杆与发动机舱盖间隙(与发动机舱盖间隙:8—15mm);33、检查保险杆与雾灯的间隙(与雾灯的间隙:2—3mm);34、检查结构设计完成的外饰件的周边与车身的间隙是否与外表面上所给的间隙一致;35、检查数模是否已经装配好,并且装配是根据明细表来装配,是否已经装了标准件,装配数模中是否有多余的点、线、面(装配数模中不允许有的参数);36、剖断面检查总成内部零件装配是否可靠,间隙是否合理适当,是否有干涉现象(安装点的位置及零件间搭接部位是重点剖吻得部位);37、在外饰上很对筋除加强的作用外,有的还起到了支撑外面的作用,检查这些筋与钣金的合理间隙;38、检查保险杆两端与挡泥板连接的翻边是否太长,原则上满足安装点的空间就可以了,太宽了对模具不利;39、检查加强筋的宽度是都适当,表面是否出现缩痕的危险;40、检查外饰件在车身的安装点是否对应,装配面是否贴合,安装孔的开孔方式是否合理(该开腰形孔的不能开圆孔);41、检查外饰件在车身的安装点是否合理,总体强度是否足够,与车身的装配是否合理;对于安装点,安装时人手的可接近性是否好,气枪或套筒扳手是否有空间;42、对于零件总成(如保险杠),检查总成内零件的装配是否合理,零件间是否靠谱,定位是否准确;43、检查外饰件表面是否有足够高的弧高,尤其装饰条等零件,其表面弧高要66车身外表面大;44、检查通风盖板与发动机盖内外板的间隙大小是否合理,间隙是否均匀;45、检查通风盖板与风窗玻璃的关系是否合理;46、检查通风盖板与风刮的关系是否合理,检查雨刮在两个极限位置时是否与通风盖板干涉;47、检查通风盖板两端与发动机白色铰链的关系是否合理,是否有干涉;48、对于车身表面的装饰条,如果是粘接上的,检查粘接面大小是否足够,粘接间隙是否留出;49、检查通风盖板两侧与发动机舱两端的关系是否合理,是否有干涉;50、检查挡泥板与轮胎包络线的间隙是否合理;51、检查挡泥板与车身及悬架等零件是否存在干涉,与车身是否有很好的贴近性;52、检查散热器的功能性,设计时要考虑散热器前面开口面积,风扇倾斜带来的空气流入量的变化及前面看时发动机室内部的遮蔽性;53、散热器罩通常表面需要镀铬,镀铬与非镀铬表面有明显的分界,检查部门镀铬地可能性;54、检查后保险杠与排气管的间隙是否合理;55、检查后保险杠与后行李盖的间隙(通常为:8—15mm ,应多测量一些车,取平均值);56、检查保险杠与倒车雷达装配是否合理可靠,倒车雷达分布是否合理;57、检查保险杠与防撞杆的关系是否合理;58、检查保险杠上牌照空间是否足够,以及牌照安装孔是否对称;59、检查零件通用性,能对称尽量做对称件,能合并一个件尽量合并一个件;60、外饰件孔径尺寸要调整,边缘要光顺;61、筋的壁厚要小于料厚的二分之一,表面做皮纹件拔横角大于5°;62、A柱护板与前风挡玻璃间隙3—4mm(轿车),6—8mm(MPV、SUV等);63、A柱护板材料:PP、P/E等,料厚:2.5—3mm ;64、A柱护板与A柱内板之间,应留足够线束(或洗涤液管)通过的空间一般留有16*14的截面空间;65、A柱护板在前门柜处通过密封条压住,A柱护板允许密封条压入留间隙0.5—1mm ;66、A柱护板压在密封条下,为使密封条对A柱护板有一定的压力,A柱护柱侧面斜角应该大于密封条压边自然状态下的角度,约20度左右;67、A柱护板通过卡口连接到A柱内板上,A柱内板应该起凸坑,其过孔表面法向于卡扣中心轴线平行,卡扣弹性球面回弹量0.5mm ;68、A柱护板在上部,压在顶蓬上,不留间隙,压边重叠宽度应大于20mm ;69、A柱护板在上部,压在仪表板上,仪表板若为注塑件,两者之间间隙1—2mm ,若为发泡件,应根据发泡件压缩量计算间隙;70、B柱护板材料:PP、P/E、PE等,料厚一般为:2.5—3mm ;71、B柱护板成型方式:一般为注塑;72、B柱上护板5B柱内板之间,应留足前座椅安全带升降器总成的空间,B柱下护板与B柱加强板之间安装安全带卷缩器,B柱下护板与B柱内板距离16—18mm ,B柱下护板与B柱加强板距离18—22mm ;73、B柱护板在门柜处,通过密封条压住,B柱护板应允许密封条压入留间隙0.5—1mm ;74、为使密封条对B柱护板有一定压力,B柱护板侧面斜条应大于密封条压边白丝状态下角度20度左右;75、B柱上护板压在顶蓬上,不留间隙,压边重叠宽度应大于20mm ;76、C柱护板材料:PP、P/E、PE等,料厚:2.5—3mm ;77、C柱护板与三角窗玻璃(后风挡玻璃)之间间隙3—4mm (轿车),6—8mm(MPV、SUV),多测一些车,取一个平均值;78、C柱护板与C柱内板及加强板之间不小于5mm ;79、C柱护板通过卡扣装到C柱内板上,C柱内板上立起凸台(凹坑),凸台平面法线与卡扣中心线方向平行,卡扣弹性球面回弹量0.5mm ,侧位压缩量0.75mm ;80、C柱护板压在顶蓬上,不留间隙,压边重叠宽度大于20mm ;81、前门内护板总成材料,前门装饰板材料一般为:PP、ABS、PE、麻毡+PBM发泡+PVC表皮等,料厚:2.5—3mm ;前门三角护板材料:PP、ABS、PE等,料厚:2.5—3mm ;扶手材料:PP、DA 等,前门地图袋、前门喇叭材料一般为:PP、ABS等,料厚2.5—3mm ;82、前门内护板周边到前门门柜密封条间隙,6—8mm ,周边间隙均匀,在前门槛处可略大(该间隙处不可见区,略大的间隙可消除制造误差对装配的影响;83、前门内护板周边翻边压在门内板面上,不留间隙;84、前门内护板通过卡扣拉紧在门内板上,卡扣轴向回弹量0.5mm ,侧面压入压缩量0.75mm ,常用过孔¢8(¢5)卡扣压入端,大径¢9.5(¢8),括号内尺寸为推荐使用的变形补偿卡扣;85、前门内护板内有防水膜,在防水膜粘胶区,内护板应保持均匀间隙4—5mm ;86、在内板上若留有内护板压槽,内护板翻边与槽边缘应有均匀间隙;87、前门内护板与仪表板配合处间隙6—8mm ,要求间隙均匀;88、前门内护板与前座椅之间距离不小于16mm ,应多测一些车,取平均值;89、前门内护板与门内板之间最小间隙大于4mm ;90、门内开拉手、车门把手及门窗玻璃升降器按钮位置需要经过人机校核;91、门内开拉手、车门把手均需要螺钉(或螺栓)紧固件固定在门内板上,以手受拉力;92、后门内护板周边与后门柜密封条间隙6—8mm ,周边要求间隙均匀,在后门槛处间隙可略大(此处为不可见区,大间隙可消除制造误差对装配的影响;93、后门内护板周边翻边压在门内板面上,不留间隙;94、后门内护板通过卡扣拉紧在门内板面上,卡扣轴向压缩量0.5mm ,侧面压入压缩量0.75mm ;95、后门内护板有防水膜,在防水膜的粘胶区,内护板与内板应保持均匀间隙4—5mm ;96、后门内护板与后座椅之间间隙不小于16mm ,应多测一些汽车,取平均值;97、后门内护板与门内间隙常最小处应大于4mm ;98、背内护板材料:后门装饰板材料一般为:PP、ABS、PE等,料厚:2.5—3mm ;99、背门内板周边到后背门门柜密封条,以背门槛护板之间间隙8—10mm ,周边要求间隙均匀;100、背门内护板周边到后背门内板间距最小应大于5mm ,与后雨刮器机构间隙应大于6mm ;101、背门通过卡扣拉紧在背门内板面上,卡扣轴向球面压缩量0.5mm ,侧面压入压缩量0.75mm ;102、前门槛护板可压在背门门柜密封条上,也可压在前门柜密封条下,后者应允许密封条在门槛装好后压入,间隙0.5—1mm ;103、前门槛护板与内饰之间应留足线束通过空间,一般大于20mm ;104、顶蓬固定方式:卡扣和螺钉连接,卡扣主要用在后部起拉紧固定作用,螺钉主要在安全拉手处;105、顶棚大面大体与顶盖大面呈偏差关系(正向设计),距离12—16mm ;106、顶棚在附件位置处(如拉手、遮阳板、阅读灯等)应与内板保持3—4mm间隙,顶蓬在门柜处压在门柜密封条下,允许密封条压入,留间隙1—2mm ;107、顶棚在位于横梁处,要求与横梁表面保持3mm间隙,在其余位置顶棚与内板间隙应为12—16mm ,顶棚与侧面内板间隙大于10mm,允许线束通过,顶棚与顶盖横梁处于钣金距离3—5mm ;(安装点零距离贴合)108、在顶蓬与A、B、C柱的搭接部位应有支撑件,且支撑件要不影响线束通过;109、在前、后风挡玻璃处,顶蓬有两种连接方式,分别为粘接和密封条连接,其连接方式为密封条连接时,应注意顶蓬卡在距钣金卡槽中心位置6mm处,并存在20度夹角关系;110、地毯通过侧面护板,前后门槛板压在地板上,其压缩量为2mm ,与护板重叠部分宽度为20mm ;111、通过地毯的运动件部分用开孔,孔边界与运动件极限位置间隙5mm 。
PCB工艺设计CheckList

6 7 8 9 10 11 12
BGA、CSP器件的贴装面的背面是否有其它 BGA、CSP器件的背面不允许贴装器件,以防止其影响到BGA、CSP器件的X-RAY检测。 器件贴装? 大型器件四周是否留有一定的维修空隙? 应留出SMD返修设备加热透能够进行操作的尺寸,较矮小的器件不应被高大的器件围住。 密脚器件(引脚间距≤0.5mm)布局是否合 1.不能布置在离板边10mm范围内; 理? 2.钢网需局部加厚的器件8mm范围内禁布密脚器件。 器件兼容设计是否符合要求? 焊盘设计是否符合要求? 器件高度是否满足要求? 1.不允许两个器件共用一个焊盘; 2.不允许两个表面贴装的异型引脚器件重叠。 PCB焊盘与器件封装要一致,具体参考IPC-SM-782A。 除结构有特殊要求之外,THD器件都必须放置在正面;背面贴片器件高度≦5mm。
丝印方向
TOP面上,优先水平放置。
丝印外形
丝印位号 丝印批号 丝印过板方向 留空间
锡焊盘、阴影效应。
m二维码空间。
局部Mark点
路丝印处,放置完器件后应可见。
整板Mark点数为3
整板Mark点数为2
刷设备的能力。太小刮刀无法板自动刷
钢网的尺寸厚度
测试点设置 四个角倒45°R角
PCB下流。
炉等过程中碰损元器件。
引脚阻焊是否有做桥位?
ist
评审日期
评审结果 回流焊≤255℃ 波峰焊≤265℃
不符合说明
改善建议
℃,3s(一般235~255℃); 良(浮起、立碑等);过波峰焊时不能
优先SMD件 编带 异性器件带吸附面
吸附面的封装;
绿油覆盖
般是≤0.4pitch; 加阻焊漆
间距为2.54mm。
直径一般≥1.4mm
SMT车间生产工艺checklist

验证内容:口SMT□其它
产品型号
编码
日期
拉长
技术员
IPQC
SMT
基本
资料
序号
项目
有
无
说明
1
PCB光板。
2
成品样板。
3
元件位置图。
4
PCB的Gerber File或SMT编程文件。
5
客户BOM。
6
公司清单。
7
工位图(仅中试产品)。
8
特殊元件安装说明。
辅料
要求
1
锡膏/红胶。
2
助焊剂/锡丝。
PCB
评估
4
是否有细间距IC等要求较高元件。
5
为防止元件被碰坏,培训、定位、拿板和装箱。
6
是否有无法克服的品质问题,培训、定位。
补焊
1
有无金手指等要求特殊的地方,培训、定位。
2
使用工具是否符合要求。
3
工具是否按要求工艺参数进行使用。
4
后焊时有无大焊盘,能否符合工艺要求参数。
5
是否要做工装夹具(后焊)。
3
是否可用分板机进行分板。
1
PCB是否为喷锡板。
2
IC管脚料盘喷锡是否均匀。
3
PCB是否为真空包装。
4
PCB焊盘是否符合IPC标准。
5
PCB是否有Mark点。
6
钢网厚度/锡膏厚度/开口大小。
材料
评估
1
最小的元件是什么,机器能否贴。
2
最大的元件是什么,机器能否贴。
3
最高的元件是什么,机器能否贴。4Βιβλιοθήκη 最小的间距是多少,机器能否贴。
工艺总体设计方案

工艺总体设计方案修订记录目录1产品概述 (5)2 单板方案 (5)2.1.1 继承产品及同类产品工艺分析 (5)2.1.2 竞争对手工艺分析 (5)2.1.3 单板工艺特点分析 (5)2.1.3.1 产品结构分析 (5)2.1.3.2PCB及关键器件工艺特点分析 (5)2.1.4 单板热设计 (6)2.1.5 单板装配 (6)2.1.6 工艺路线设计 (6)2.2工艺能力分析及关键工序及其质量控制方案 (6)2.2.1 器件工艺难点分析: (7)2.2.2 单板组装工艺难点分析及质量控制方案 (7)2.3制造瓶颈分析 (7)2.4 平台工具/工装选用和新工具/工装 (7)3 整机方案 (8)3.1 BOM结构分层方案 (8)3.2 工序设计 (8)3.3 关键工序及其质量控制方案 (8)3.3.1 装配保证产品外观质量 (8)3.3.2 装配保证产品互连互配要求 (8)3.3.3 装配保证产品防护要求 (8)3.3.4 装配保证其它要求 (8)3.4 生产安全要求 (8)3.5 制造瓶颈分析 (8)3.6 工具/工装方案(加个表:序号\工装名称\工装目的) (8)3.7 新工艺和特殊工艺技术分析 (8)4 环保设计要求 (9)4.1 单板环保设计要求 (9)4.2 整机设计环保要求 (9)XX工艺总体设计方案关键词:摘要:缩略语清单:<对本文所用缩略语进行说明,要求提供每个缩略语的英文全名和中文解释。
>1产品概述产品基本情况介绍,对产品的网络地位,运行环境、产品配置、系统功耗、结构特点、产品结构框图(包括机柜、插框、单板名称、数量)、各单板在产品中的位置进行介绍。
2 单板方案2.1 生产方式确定和工序设计(依照现有的成熟的制造模式,结合各单板的特点(尺寸、板材、关键元器件、元器件种类数、元器件数量、结构设计要求、估计产量等)确定并列出各单板的加工工艺流程;分析各单板对工艺流程中各个工序的关键影响因素,有针对性地设计各工序合理的解决方法)2.1.1 继承产品及同类产品工艺分析分析继承产品、同类产品单板的工艺路线,工艺难点,品质水平,市场工艺返修率,关键器件缺陷率,热设计,故障检测方式等。
- 1、下载文档前请自行甄别文档内容的完整性,平台不提供额外的编辑、内容补充、找答案等附加服务。
- 2、"仅部分预览"的文档,不可在线预览部分如存在完整性等问题,可反馈申请退款(可完整预览的文档不适用该条件!)。
- 3、如文档侵犯您的权益,请联系客服反馈,我们会尽快为您处理(人工客服工作时间:9:00-18:30)。
强制 强制 强制 强制 强制
根据《PCB可制造性设计指南》、《元器件工艺技术规范》、PCB及关键器件 9 工艺特点已分析
10 所有单板的初步工艺路线已经确定 11 各种工艺路线已经分析,包括PCB尺寸、焊点密度、复杂度、器件封装等 12 器件工艺难点已经分析 13 单板组装工艺难点已经分析 14 根据《单板试制工艺操作指导书》,单板组装工艺难点已有质量控制方案 15 单板工艺设计风险点已经全面分析
被审核文档 质量检查结果
分类/编号 1 2 3
工艺设计 4 5
产品工艺总体方案评审要素表(工艺)
强制不满足数大于等于1,则不通过
检查项 产品概述包含运行环境、网络层次、产品结构框图、单板在产品中的位置、 公司同类产品分析,给出借鉴的经验和教训,给出本产品的可借鉴点; 对友商同类别产品的设计进行分析,给出本产品的可借鉴点; 已根据公司/友商同类产品的分析,给出可制造性现状、追赶目标及解决方 案; 根据《单板DFR设计指南》,进行产品环境适应性分析
16 已对各种制造瓶颈工序进制 强制 强制 强制 强制
强制
已根据单板加工各个工序所用工装/夹具进行全面分析,借用和需要新设计的
17 工装已经明确
强制
18 新工艺应用技术已确定 19 新工艺技术需求、开发进度和输出要求已经明确 20 对环保设计产品其元器件进行全面分析,包括RoHS、无铅等 21 对环保设计产品其加工过程中使用到的辅料进行分析 22 PCB环保设计要求已分析
审核人(姓名) 审核工作量(小
强制总数 涉及的强制数 不涉及的强制数 强制不满足数
检查/审 级别 计对象 强制 强制 强制
强制
强制
6 根据工艺规范要求,单板结构件种类及可装配性分析
强制
工艺能力 分析及质
量控制
制造瓶颈 分析 工装夹具
新工艺 环保设计
7 扣板、扩展板、光模块、光纤、拉手条、导向组件等装配方案已明确 8 单板/背板连接器型号、导向、插拔力要求已分析