高固体分环氧海洋防腐蚀涂料的研究进展
环氧涂料已成为汽车涂装上发展最快的涂料

: 资
i
; =
田、炼油厂及石化厂等。
选 择 环 氧树 脂 作 为成 膜 剂 还
P G都在进 一步开发汽 车用粉末涂 料 ,年增长 率在1 %以上 ,其 中增 P 2
海洋涂料成为海上作业设备的保护伞
由于海 洋本身是一个 复杂的腐蚀性环境 。海水本
身就 是一种很强 的腐蚀 介质 。同时波 、浪 、潮、流又
保养 。另外 与修补漆配套也是重 要因素 。同时要符 合
环保及安全要求。2 世纪9 年代初 。宝马开始对 普遍 0 0 使用的清漆体 系进行分析 、评价 和筛选 ,最终选用环 氧丙烯酸粉末 清漆 ,原 因在 于它的经久耐用和粉末 涂
迹象 。
o ;
2;
胶、皮革 、陶瓷 、纤维等都有 良好
的粘接力。 固化后 的环 氧树脂 。具
有优 良的耐化学腐蚀性、耐热性 、
耐 酸碱 性 及 良好 的 电绝 缘 性 。用
它来 配 制的 防火 涂 料 具 有 良好 的 附着力 、防腐蚀性 和机械 强度。
一嬲 市 垮 撷
其次 ,环氧防火涂料具有极佳 的封闭性 。阻燃成分不会迁移到涂
料的诸 多优点 。选择环氧丙烯酸 树脂作为汽 车粉 末清
对金 属构 件产生低频往 复应力和冲击 ,加上海洋微 生 物、附着生物及 它们 的代 谢产物等都对腐蚀过 程产 生
直接或 间接 的加速 作用。而在海水 中作业 的船舶、潜
艇 、石油钻井等设 备 ,因常年与这种高腐蚀 的海 水接
触 。表面构件很容 易出现微生物腐蚀 、电偶腐蚀 、点
海洋环境混凝土防腐涂料研究及发展趋势

0 引言
近年来,随着沿海地区经济建设的推进,一大批海洋 工程陆续涌现。目前我国已建有 200 多个海上石油平台, 厦门翔安海底隧道和胶州湾海底隧道已经建成通车。与此 同时,跨海、临海大桥工程也在我国如火如荼的进行。然而, 由于海洋苛刻的腐蚀环境,处于海洋环境中的钢筋混凝土 结构常因混凝土腐蚀和钢筋锈蚀而过早发生耐久性失效 乃至破坏,这些问题给我国带来了巨大的经济损失。如果 对海洋钢筋混凝土工程采取有效的防腐措施,就可以大大 地降低因腐蚀而造成的损失。
(2)聚氨酯涂料。以聚氨酯树脂为主要成膜物质组成 的涂料,称为聚氨酯涂料,通常可以分为双组分聚氨酯涂 料和单组分聚氨酯涂料。双组分聚氨酯涂料一般是由含异 氰酸酯的预聚物和含羟基的树脂两部分组成,按含羟基的 不同可分为:丙烯酸聚氨酯、醇酸聚氨酯、环氧聚氨酯等[5]。 单组分是利用混合聚醚进行脱水,加入二异氰酸酯与各种 助剂进行环氧改性制成。聚氨酯树脂涂料在应用中具有以 下优点:涂层的透水性和透气性小,防腐蚀性能优良;通过 调节配合比,涂膜既可以做成刚性涂料,也可以做成柔性 涂料;可与多种树脂混合或改性制备成各种特色的防腐蚀涂 料;可以在低温潮湿的环境下固化;良好的机械性能、水解稳 定性、耐生物污损性和耐温性。由于耐候性优异、装饰性强, 聚氨酯涂料是目前常用的一类面漆涂料。M.H.F.Medeiros 和 P.Helene 通过对几种常用涂料的性能试验后表明,聚氨酯 的抗氯离子渗透性明显好于斥水性涂料和丙烯酸涂料,而 且它降低氯离子扩散系数达 86%[6]。但是这种涂料的缺点是 涂膜易变黄、粉化褪色;固化反应慢;附着力相对较小。
Abstract: In the marine environment,the reinforced concrete structure may occur durability failure prematurely or even destruction due to the marine environment corrosion and thus bring huge economic losses.If effective protective measures were taken to the marine engi- neering,it could effectively extend the service life of the structure and greatly reduce the economic losses caused by corrosion.To the pro- tective methods of using anti-corrosion coatings for reinforced concrete,the types and main performances of the anti-corrosion coatings of the concrete under the marine environment were introduced and the trend of the research and development of the anti-corrosion coatings for marine application were indicated.It provided a reference for the selection of anti-corrosion coatings. Key words: marine environment;concrete;anti-corrosion coating
高固体分涂料的硬度与韧性研究
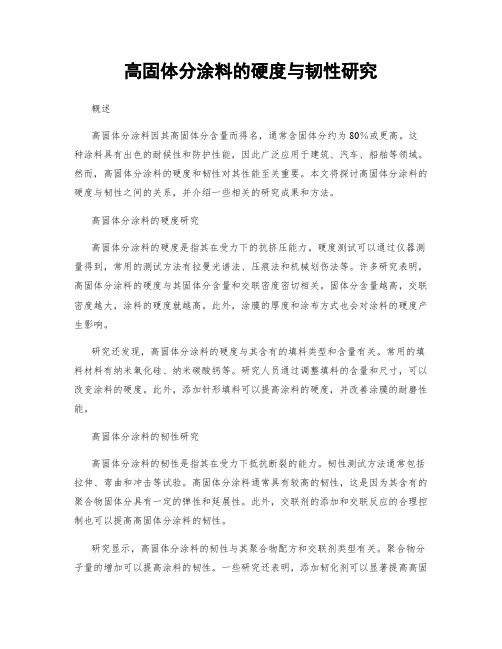
高固体分涂料的硬度与韧性研究概述高固体分涂料因其高固体分含量而得名,通常含固体分约为80%或更高。
这种涂料具有出色的耐候性和防护性能,因此广泛应用于建筑、汽车、船舶等领域。
然而,高固体分涂料的硬度和韧性对其性能至关重要。
本文将探讨高固体分涂料的硬度与韧性之间的关系,并介绍一些相关的研究成果和方法。
高固体分涂料的硬度研究高固体分涂料的硬度是指其在受力下的抗挤压能力。
硬度测试可以通过仪器测量得到,常用的测试方法有拉曼光谱法、压痕法和机械划伤法等。
许多研究表明,高固体分涂料的硬度与其固体分含量和交联密度密切相关。
固体分含量越高,交联密度越大,涂料的硬度就越高。
此外,涂膜的厚度和涂布方式也会对涂料的硬度产生影响。
研究还发现,高固体分涂料的硬度与其含有的填料类型和含量有关。
常用的填料材料有纳米氧化硅、纳米碳酸钙等。
研究人员通过调整填料的含量和尺寸,可以改变涂料的硬度。
此外,添加针形填料可以提高涂料的硬度,并改善涂膜的耐磨性能。
高固体分涂料的韧性研究高固体分涂料的韧性是指其在受力下抵抗断裂的能力。
韧性测试方法通常包括拉伸、弯曲和冲击等试验。
高固体分涂料通常具有较高的韧性,这是因为其含有的聚合物固体分具有一定的弹性和延展性。
此外,交联剂的添加和交联反应的合理控制也可以提高高固体分涂料的韧性。
研究显示,高固体分涂料的韧性与其聚合物配方和交联剂类型有关。
聚合物分子量的增加可以提高涂料的韧性。
一些研究还表明,添加韧化剂可以显著提高高固体分涂料的韧性。
韧化剂可以增强聚合物的分子间结合力,从而提高涂料的抗冲击性能。
高固体分涂料的硬度与韧性的关系研究高固体分涂料的硬度和韧性是两个截然不同的性能指标,但它们之间存在一定的关联关系。
一般来说,高固体分涂料的硬度越高,其韧性相对较低;而硬度较低的涂料往往具有较高的韧性。
硬度和韧性之间的关系与涂料的聚合物体系、固体分含量、填料类型等因素相关。
一项研究中发现涂料中添加纳米碳酸钙和碳纳米管可以提高其硬度,但会降低涂料的韧性。
我国防腐涂料的现状及发展趋势

我国防腐涂料的现状及发展趋势我国防腐涂料的现状及发展趋势摘要:本文分析了国内防腐涂料发展现状及我国防腐涂料行业存在的问题,指出了我国防腐涂料行业的发展趋势。
关键词:防腐涂料;发展趋势;存在问题1 引言在国民经济中腐蚀造成了大量的资源和能源浪费,全世界每年因腐蚀造成的经济损失约为10000亿美元,是火灾、风灾和地震造成损失的总和。
防腐涂料作为最有效、最经济、应用最普遍的防腐方法,受到国内外广泛地关注和重视。
防腐涂料是现代工业、交通、能源、海洋工程等部门应用极为广泛的一种涂料。
按其涂料膜层的耐腐蚀程度和使用要求, 通常将防腐蚀涂料分为通用型和重防腐型两类。
根据使用环境腐蚀介质的情况选用不同类型的防腐蚀涂料。
在一般大气环境的腐蚀条件下, 如机床、汽车、铁路车辆、工程机械等行业, 常采用通用型防腐蚀涂料, 此时还要求涂层具有较高的装饰功能; 在工业或海洋性大气腐蚀环境条件下, 如化工、石油化工、冶金、海洋工程等行业, 多采用重防腐蚀涂料。
防腐涂料在我国涂料工业中占有重要地位,在涂料工业中所占的比例已经位居前列。
近年来,我国在建筑、交通运输、石化、水电以及海洋工程等众多领域,都出现了飞速增长,进而带动了相关配套产品需求的快速增长,我国防腐涂料市场也出现了喜人的局面,市场规模已经仅次于建筑涂料而位居第二位。
本文将就我国防腐涂料的发展现状、发展趋势以及存在的问题进行探讨。
2 我国防腐涂料发展现状2. 1 主要品种据不完全统计, 我国防腐蚀涂料品种有1000 余种, 传统的按树脂分类有环氧、沥青、氯化橡胶、氯磺化聚乙烯、聚氯乙烯、过氯乙烯、高氯化聚乙烯、丙烯酸、聚氨酯、酚醛、醇酸漆等。
上世纪90年代开始,新一代防腐涂料体系陆续占据了市场研究和应用的主流,其中包括水性环氧涂料、水性丙烯酸涂料、水性无机硅酸富锌涂料、聚硅氧烷涂料、粉末涂料、氟碳涂料、聚脲涂料、鳞片涂料、导电聚苯胺涂料以及钛纳米聚合物涂料等。
涂料品种已经由单一向多功能化发展。
自修复环氧防腐涂层的研究进展

自修复环氧防腐涂层的研究进展目录1. 内容综述 (2)1.1 研究背景与意义 (3)1.2 国内外研究现状概述 (4)2. 自修复环氧防腐涂层材料的设计与制备 (5)2.1 材料选择与改进 (6)2.2 涂层制备方法与优化 (8)2.3 涂层性能评价标准建立 (8)3. 自修复环氧防腐涂层的机理研究 (9)3.1 自修复机制的探究 (10)3.2 防腐效果的评估方法 (12)3.3 涂层与基材的界面结合分析 (13)4. 自修复环氧防腐涂层在典型环境中的应用 (14)4.1 在金属腐蚀环境中的应用 (15)4.2 在化工环境污染环境中的应用 (17)4.3 在海洋工程防腐环境中的应用 (18)5. 自修复环氧防腐涂层的性能改进与优化 (18)5.1 提高耐磨性、耐腐蚀性和耐候性 (20)5.2 优化涂层结构与成分以提高整体性能 (21)5.3 涂层的多功能化与集成化研究 (22)6. 实际应用案例分析 (23)6.1 工程实例介绍 (25)6.2 应用效果与评价 (26)6.3 经验教训与发展建议 (27)7. 结论与展望 (28)7.1 研究成果总结 (29)7.2 存在问题与挑战 (31)7.3 未来发展方向与前景展望 (32)1. 内容综述随着科技的不断发展,自修复环氧防腐涂层作为一种新型环保型涂料,逐渐受到人们的关注和重视。
自修复环氧防腐涂层具有优异的耐磨、耐腐蚀、抗老化等性能,能够有效地延长物体的使用寿命,降低维修成本,减少对环境的污染。
国内外学者在自修复环氧防腐涂层的研究方面取得了一系列重要进展。
自修复环氧防腐涂层的制备工艺得到了不断的优化,研究人员通过采用不同的成膜基料、添加剂和分散剂等,成功地实现了不同类型自修复环氧防腐涂层的制备。
还研究了纳米颗粒、微米级颗粒等特殊功能填料在自修复环氧防腐涂层中的应用,进一步提高了涂层的性能。
自修复环氧防腐涂层的性能研究取得了显著成果,研究人员通过对不同种类的自修复环氧防腐涂层进行对比试验,发现其具有较高的抗划伤性、耐磨性和耐腐蚀性,能够有效抵抗各种恶劣环境的侵蚀。
环氧树脂防腐性能研究进展
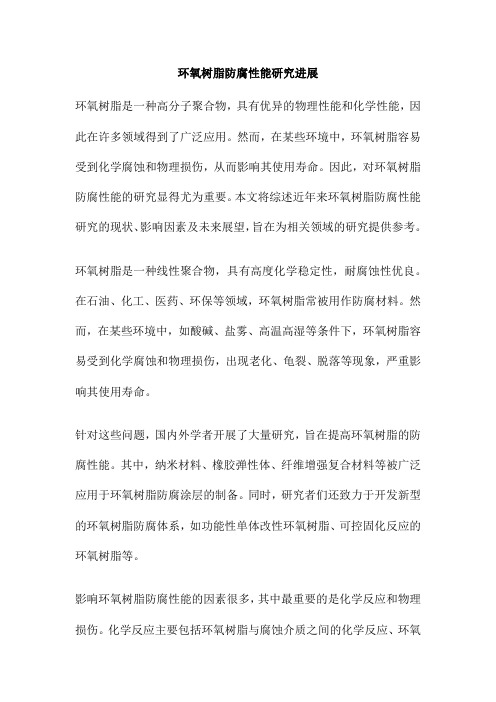
环氧树脂防腐性能研究进展环氧树脂是一种高分子聚合物,具有优异的物理性能和化学性能,因此在许多领域得到了广泛应用。
然而,在某些环境中,环氧树脂容易受到化学腐蚀和物理损伤,从而影响其使用寿命。
因此,对环氧树脂防腐性能的研究显得尤为重要。
本文将综述近年来环氧树脂防腐性能研究的现状、影响因素及未来展望,旨在为相关领域的研究提供参考。
环氧树脂是一种线性聚合物,具有高度化学稳定性,耐腐蚀性优良。
在石油、化工、医药、环保等领域,环氧树脂常被用作防腐材料。
然而,在某些环境中,如酸碱、盐雾、高温高湿等条件下,环氧树脂容易受到化学腐蚀和物理损伤,出现老化、龟裂、脱落等现象,严重影响其使用寿命。
针对这些问题,国内外学者开展了大量研究,旨在提高环氧树脂的防腐性能。
其中,纳米材料、橡胶弹性体、纤维增强复合材料等被广泛应用于环氧树脂防腐涂层的制备。
同时,研究者们还致力于开发新型的环氧树脂防腐体系,如功能性单体改性环氧树脂、可控固化反应的环氧树脂等。
影响环氧树脂防腐性能的因素很多,其中最重要的是化学反应和物理损伤。
化学反应主要包括环氧树脂与腐蚀介质之间的化学反应、环氧树脂本身的化学反应。
物理损伤主要包括环氧树脂的机械强度、耐磨性、抗冲击性等。
这些因素之间相互作用,共同影响着环氧树脂的防腐性能。
未来,环氧树脂防腐性能的研究将朝着多功能化、智能化、绿色化等方向发展。
具体来说,研究者们将致力于开发具有自修复能力、耐高温高湿、抗紫外老化等功能的环氧树脂防腐体系;利用智能材料和传感器技术,实现环氧树脂防腐涂层的智能监测和预警;还将在保证环氧树脂防腐性能的前提下,降低其生产和使用过程中的能耗和排放,实现绿色可持续发展。
环氧树脂防腐性能的研究对于提高其在各领域的应用效果具有重要意义。
通过深入探究影响环氧树脂防腐性能的因素及作用机制,合理设计并制备高性能的环氧树脂防腐材料,有助于解决环氧树脂在复杂环境下的腐蚀问题,延长其使用寿命。
随着科学技术的发展,环氧树脂防腐性能的研究将不断取得突破性进展,为相关领域的发展提供有力支持。
高固体分环氧涂料的制备与研究

高固体分环氧涂料的制备与研究康瑞瑞;李陈郭;李至秦;杨名亮;苏雅丽;方大庆【摘要】以自制低黏度二聚酸改性环氧树脂(HEH)、双酚A环氧树脂和低黏度固化剂开发出VOC含量为79.2g/L的高固体分环氧涂料.采用盐雾试验、3.5%NaC1溶液和10%NaOH溶液浸泡试验、阴极剥离试验研究了HEH用量、颜料体积浓度(PVC)以及固化剂对涂层防腐性能的影响.采用SEM、EIS和DSC对涂层性能进行了表征.结果表明:HEH与E51按质量比1∶1复配,PVC=0.30且使用脂环胺固化剂时,涂层孔隙率小,致密性好,防腐性能优异.%A high solid epoxy coating with VOC of 79.2 g/L was developed by using self-prepared low viscosity epoxy resin (HEH) modified by dimer acid,bisphenol A epoxy resin and low viscosity curing agent.The effects of the amount of self-prepared resin,the PVC of coatings and the curing agents on the corrosion resistance of the coating were studied by salt spray test,3.5% NaCl (aq) and 10% NaOH (aq) soaking test and cathodic stripping test.The coatings were also characterized by SEM,EIS and DSC.The results showed that when HEH and E51 were blended at with a mass ratio of 1 ∶ 1,PVC =0.30 and the curing agent was alicyclic amine,the cured coating exhibited small porosity,good density and excellent corrosion resistance.【期刊名称】《涂料工业》【年(卷),期】2017(047)012【总页数】6页(P36-41)【关键词】改性环氧树脂;高固体分涂料;防腐;VOC【作者】康瑞瑞;李陈郭;李至秦;杨名亮;苏雅丽;方大庆【作者单位】厦门双瑞船舶涂料有限公司,福建厦门361101;厦门双瑞船舶涂料有限公司,福建厦门361101;厦门双瑞船舶涂料有限公司,福建厦门361101;厦门双瑞船舶涂料有限公司,福建厦门361101;厦门双瑞船舶涂料有限公司,福建厦门361101;厦门双瑞船舶涂料有限公司,福建厦门361101【正文语种】中文【中图分类】TQ637.85海洋环境具有强烈的腐蚀破坏性,船舶与海洋工程结构长期处于恶劣的海洋环境下,腐蚀非常严重。
海洋环境中的防腐蚀涂层技术及发展_刘晓建

5
结语
随着世界海洋工业的迅速发展和环境保护法对海 洋涂料工业的影响,海洋防腐蚀涂层也向高性能及环 保型方向发展。 研究和推广海洋防腐蚀涂层的新品种、 新技术, 提高其防腐蚀效果和质量, 减轻有毒物质对海 洋环境的污染, 降低有害物质对海洋管道、 平台钢结构 等工程设施的腐蚀破坏,具有十分重要的现实意义和 经济意义。 参考文献:
1
引言
随着海上运输、 深海采矿、 港口码头、 油气开发、 海 洋生物技术等新兴海洋产业的兴起,加上近年来深海 开发中的油气勘探和生产活动的大大增加,人类对海 洋的开发利用规模不断扩大, 逐步从传统走向深入。 正 是由于海洋经济和海洋产业对人类社会的发展起着极 为重要的作用,因此海洋环境中各类设备装置的防腐 蚀涂层及其技术的开发将成为研究的重点。
21
2010 年 4 月 第 13 卷第 4 期
Apr.2010 Vol.13 No.4
⑷外部面漆必须具有优异的耐候性、耐紫外线照 射和保光保色性; ⑸与电化学保护系统相容性好; ⑹符合健康、 安全、 环保的要求。 目前海洋平台中各设备的防腐蚀涂层主要用在大 气区, 其配套体系有如下几种: 环氧富锌底漆 2 层+环氧中间漆 2 层+环氧面漆 3 层; 环氧富锌底漆 2 层+乙烯基中间漆 3 层+乙烯基丙 烯涂层 2 层; 无机富锌底漆 3 层+环氧中间漆 2 层+聚 氨酯面漆 3 层。 其中富锌底漆要求含锌粉比例高,且与基材附着 力强; 中间漆要求综合防腐蚀能力强; 面漆是为底漆 、 中间漆提供保护层, 减少和限制水汽、 氧及化学活性离 子的渗入。 4.2 锌加防腐蚀保护技术 锌加保护技术与传统有机涂料相比,具有更强的 阴极保护作用和涂层保护双重作用,其耐腐蚀能力高 于常规的富锌底漆 5 ~ 6 倍,防腐蚀保护年限可达到 25 ~ 30 年。 用于钢结构防腐蚀保护的锌加涂料是由电解锌粉 (纯度高于 99.995% ) 、有机树脂和挥发性溶剂 3 部分 配制而成的单组分系列产品。 由于含锌量高, 锌加干膜 含有 96%以上的纯锌, 足以为钢结构材料提供较好的 阴极保护, 当锌加涂层被氧化时, 会在锌加涂层表面缓 慢产生一层锌盐层来提供屏障保护,同时锌加涂料中 的黏结剂能提供一层附加的屏障保护,从而减缓锌的 氧化。锌加涂层与钢结构表面具有优良的机械结合和 化学结合, 即使受到磨损破坏, 锌加涂层也不会剥落。 经国内外海洋平台的工程证明,锌加保护涂层技 术的防腐蚀性能十分优异。1988 年, 日本濑户大桥采 用锌加涂料作为底漆, 使用至今未发现任何锈蚀。 2000 年锌加保护技术被应用在深圳蛇口海上钻井平台和东 海平湖油田海上钻井平台的局部维修上,修复的锌加 涂层至今未发现锈蚀, 防腐性能良好[8-9]。 4.3 聚氨酯重防腐涂料保护 100% 固体含量的长效刚性聚氨酯防腐蚀涂 料 (RPU ) 不含溶剂、 利于环保, RPU 膜中除含有氨基甲酸 酯键外, 还含有部分脲键等, 其它基本为惰性的碳链结 构。基于以上特点, RPU 具有多种优异的性能, 如优良 的物理机械性能, 涂膜坚硬 、 柔韧 、 光亮, 尤其是耐磨 性、 黏附力特别好; 水解稳定性及耐生物污损性优异; 耐温性能好, 可制成高温涂料, 也可制成-70 ℃下使用 的低温涂料; 另有耐腐蚀、 寿命长 (可适应工程 50 年 ) 、 施工性能优良等优点。 RPU 涂料已先后应用于上海国际航运中心洋山
海洋工程重防腐技术
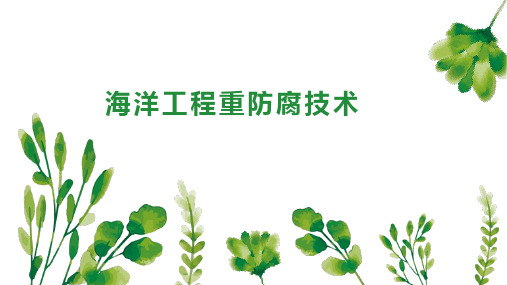
结论
本次演示介绍了海洋工程重防腐涂料的应用技术现状及发展分析。目前,海 洋工程重防腐涂料已广泛应用于船舶、港口设施、海洋平台等领域,并取得了良 好的防腐效果。然而,随着环保、节能和可持续发展的要求不断提高,海洋工程 重防腐涂料的应用技术仍需不断进步和创新。未来,开发环保、高性能、低能耗 的海洋工程重防腐涂料将成为研究的重要方向。
海洋工程重防腐技术
目录
01 引言
03
重防腐技术的定义和 原理
02 防腐技术的重要性 04 参考内容
引言
海洋工程是指利用海洋资源和环境条件,为人类开发、利用和保护海洋而开 展的一系列工程和技术活动。然而,海洋环境中的腐蚀问题一直是制约海洋工程 长期稳定发展的关键因素之一。因此,本次演示将重点探讨海洋工程重防腐技术 的重要性和未来发展趋势,以期为相关领域的研究和实践提供参考。
2、研究方向与进展
目前,国内外针对海洋工程重防腐涂料的研究主要集中在以下几个方面:
(1)高性能涂料研发:研究开发耐候性、耐腐蚀性、耐生物侵蚀性更强的 涂料,以提高海洋工程设施的防腐寿命。
(2)涂层固化技术:探究更快速、更环保的涂层固化技术,以提高涂层的 施工效率和降低能耗。
(3)涂层维护与修复:研究涂层的维护与修复技术,以提高涂层的耐用性 和降低维护成本。
防腐技术的重要性
海洋工程中,防腐技术具有极其重要的作用。首先,海洋环境中的高盐、富 氧等条件使得钢铁等材料容易发生电化学腐蚀,进而影响结构物的安全性和稳定 性。其次,海洋工程中大量使用的石油、化工、天然气等设施也需要面对严重的 腐蚀问题,一旦发生泄漏将对环境造成严重危害。因此,防腐技术的合理应用对 于保障海洋工程的安全性和稳定性具有重要意义。
方法
海洋工程防腐系统优化设计的方法包括以下几个方面:
高固体分环氧防腐涂料的制备

性 吸 季 性’ 成盐涂 ,漆离多 霸 j 季,层泛影膜胺, 嚣 。抗 篡 擎 游较易 面 防能潮 腐 稍 … 一
面理 ,高、温能好固 蔷篓求高在温低都很地化 W 处要
腰 果壳 油衍 生物 都 是 以 带 有 不 饱 和 双 键 的 C 直 链取 i
下 ,漆膜固化的效果较差 ;改性脂肪胺做 固化剂 出现 的弊 病较多 ,影响漆膜的防腐 能。而腰果壳油改性酚醛胺 固 生 化环氧体系 ,不仅在使用条件上不受环境 的限制 ,而且有 着优异的防腐保护 能 。在常温下 ,环氧树脂通常只能达 生 到 9% 0 的交联度。当 7 % 5 以上的环氧基 团交联时 ,涂料性 的环氧体系 ,在 5 c 时,3 d左右就可达到基本完全 固化 C
王 秀娟 ,李敏 ,马胜 军 中海油 常州涂料 化工研 究院 ,常y 2 0 ) 、 1 1 3 6 1
性涂料 在施工的过程中极易引起闪锈 ,而且成膜后其防 12 性能 技术指 标 .
腐蚀性能与溶剂型涂料相 比还是有一定的差距 ,不能用于 按照比例配漆制板 ,依据国家标 准对高 固体分环氧涂 具有高防腐蚀要 求的钢结构表面涂装。而高 固体分环氧涂 料进行性能的测试 ,检验 的具体性能结果如表 2 所示 。
耐 盐 水 性 (%NC) 6 漆 3 a I,90h
D
通过 45 7
G/ 2241 06 B 6 .—2O T0 G/ 96一 l8 B 24 98 T
, G / 8 4 2 8 B7 1 3 0 0 0
—
氧 涂 料 属 于 厚 浆 型 涂 料 。 若 涂 料 施 工 表 干 时 间较 长 ,则 有 机 颜 料 易 产 生 浮 色 、 发 花 等 问 题 , 因而 宜 选 用 耐 化 学 介 质
高固体分环氧海洋防腐蚀涂料的研究进展

高固体分环氧海洋防腐蚀涂料的研究进展1·前言防腐蚀涂料的防护作用主要有3 种: 漆膜与片层颜料的屏蔽作用、碱性或氧化性颜料的缓蚀钝化作用以及锌粉的电化学保护作用。
其中,能把水、氧以及离子等腐蚀介质隔绝的屏蔽作用最为关键。
目前常用的海洋重防腐涂料多为溶剂型涂料。
在其成膜过程中,溶剂挥发留下的针孔,会使腐蚀介质渗至膜下造成腐蚀。
所得腐蚀产物膨胀挤破涂层,使腐蚀介质得以扩散,终使涂层成片脱落失效。
需要指出的是,防护涂层即使无裂纹和针孔空隙等缺陷,腐蚀介质仍然能在一定程度上渗透涂层到达金属表面。
因此,必须提高涂膜的致密性与厚度以延长介质的渗透时间[1 - 3]。
海洋钢铁设施中常用的重防腐涂层总厚度一般要求300 ~500 μm,有的甚至要求更厚。
然而,溶剂型涂料的单道涂层仅为一百多微米,需要多道涂装才能达到规定膜厚,这就增加了施工成本,而且溶剂对工人的身体健康有损害。
面对溶剂型涂料的种种问题,科研人员正在努力开发新型防腐蚀涂料[4 - 5]。
其中,高固体分环氧涂料受到极大重视。
高固体分环氧涂料多为双组分反应固化型防腐涂料[6]。
低分子量环氧树脂、颜料、活性稀释剂及各种助剂经高速分散、研磨后,制成漆料组分,可满足特定场合需要的改性胺作固化剂组分。
环氧树脂用作成膜物质的优点是: 由于它含有大量的羟基与醚基等强极性基团,使其与底材的附着力非常好; 固化时不产生小分子副产物,体积收缩很小,因而具有良好的成膜致密性;优异的机械性能、耐化学品性能和耐腐蚀性能。
采用低分子量的树脂与活性稀释剂是为了降低施工粘度,以提高涂膜平整性与致密性。
高固体分是指: 制备与施工无需或很少量使用有机溶剂; 涂料的固含量很高,甚至达100%。
回避了有机溶剂就消除了针孔现象,提高了涂膜的抗渗性,免除了溶剂毒害。
固含量高使得单道涂层的厚度增大,适用于厚涂,从而减少了涂装费用与时间。
高固体分环氧涂料综合了高固体分与环氧树脂的优点,高固体分环氧涂料是实现厚膜化要求的最简单有效的方法,已经成为防腐涂料的研究热点,是海洋重防腐涂料的发展趋势。
高温慢固化高固体分环氧涂料的研制
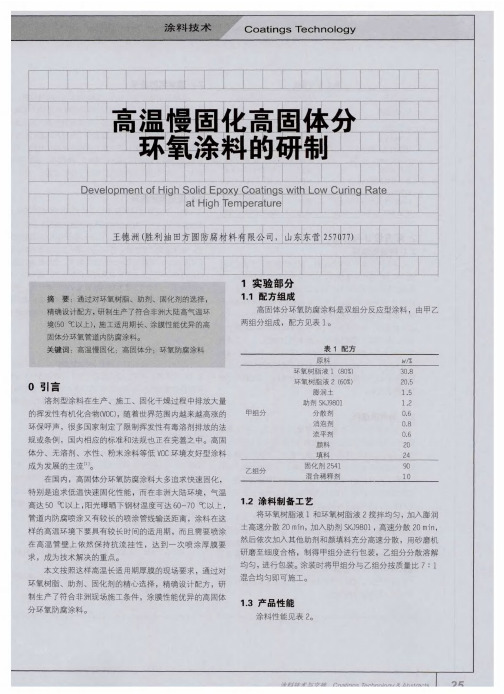
表 2 涂料性 能
23 颜填 料 的选 择 .
颜填料的选用很大程度 上影响着涂层 的最终性 能,适 合 的颜 填料不 仅能提 高涂层 的物理机 械性 能和耐 化学 介 质性能 ,而且对施 工性能 、储存性能也有改善。本方案作 为底 面合一的厚膜 管道 内防腐涂料 ,颜料 以防腐 性能优异 的氧 化铁 红、云母氧化铁为主 ,填料选用以云母粉、石英 粉为主 , 同时添加功能性防锈填料三聚磷酸 铝、 磷酸锌等 , 提高了涂膜 的抗介质渗透性 ,降低 了涂料成本。
婚
》
高 固体分环氧防腐涂料 由于黏度大 ,流平性欠佳 ,需 取得 了非 常好 的效果。 添加适量流平剂 ,降低 体系的表 面张 力,避免涂膜表面缺
陷。而为 了使颜填料在涂料体 系中更好地分散 ,提高高速 分散和研磨 的效率 ,还需添加适量的分散 剂。添加适量有 效 的消泡剂 ,可消除涂料在 生产制备和施工过程 中卷入 空 气形成 的气泡。多种助剂的加入大大改善 了高 固体分涂料
本研究生产制备的高固体分环氧防腐涂料 ,在 非洲 大
陆 5 C O c 高温 环境 下 ,应 用 自控调频无气喷涂步行车对各 种管径 的管道 内壁进行防腐施工 ,其施 工进度 、施 工便利 性 ( 长适用期) 较 、一次成膜 干膜 厚度( 5 ≥2 0啪 ) 、涂膜性 能等都达到甚至超越了设计 要求。
的性能 ,使涂膜平整光滑。
婚
参考 文 献
[ ] 王秀娟 ,李敏 ,马胜军 .高固体分环氧防腐涂料 的制备[] 1 J. 涂料技术与文摘 ,2 1 ,3 (O 8 l . 0 0 11 ) - 0
[] 朱能杰,潘神燕 ,蓝席建 ,等. 2 钢结构高 固体分防腐蚀环氧
高固体分抗冲击耐蚀涂料的研制

期“ 能性 涂料 ” 辑 , 珊 专
以飧 读 者 。
D M 配制的 IN涂料的综 合性 能最好 。 D P 关键 词 : 环氧树脂 ; 聚丙烯酸醇 ; 互穿聚合物网络 ; 防腐涂料
22 1 潦料 的配制 .. 将环 氧树脂 与 D M 按 当量 比 1 1 合 , 上 述 D :混 按 混合 物质 量的 2 % ~3 %添加 H D 0 o D A和适 量 B O。 P
2 22 样 板 的 制 备 ..
制备 的 防腐涂料 因其交联 密度 高 , 具 有更好 的耐 热 而
《 , 满足 各 领 域 的 特 切 以 }殊要求。 为 了反 映我 国
功 能 性 涂 料 的 技 术 水
郑耀 臣 ( 南京 工 业走学材料 学院 ,1 0 ) 20 9 0 ( 山东省威海 市油漆 厂技 术 开发 部 ,620 240 )
要: 以低分子量环氧树脂 、 芳族胺 固化剂 44 一二氨基二苯 甲烷( D 与 ,’ D M)
1 前
言
44 一二 氨 基二 苯 甲烷 ( D , ,’ D M)化学 纯 , 海 三 爱 思 上 试剂 有 限公 司 ;, 16一己二 醇 二丙 烯 酸酯 ( D A)工 HD ,
业品 , C U B公 司 ; 氧化 二 苯 甲酰 ( P , 学 纯 , 过 B O) 化 上 海 中利化 工厂 。
维普资讯
・
试验研究 ・
《 编者按 ] 涂料 具有保 [
《 装饰 、 护、 标志和其他特 《
》 功 能 作 用。 随 着Fra bibliotek我 国 殊 竺 ,
高固体分涂料的涂装工艺研究

高固体分涂料的涂装工艺研究高固体分涂料是一种广泛应用于汽车、航空航天、建筑等领域的重要涂装材料。
其具有较高的固体含量和低的溶剂含量,能够提供出色的涂料覆盖性能和耐候性能。
本文将重点研究高固体分涂料的涂装工艺,包括前处理、涂装操作、固化和涂膜性能评价等方面。
首先,前处理是高固体分涂料涂装工艺的关键步骤之一。
前处理的目的是清洁、去除表面污染物、增强涂层与基材之间的附着力,以确保涂装效果的质量。
常见的前处理方法包括机械除锈、化学除锈、表面活化等。
机械除锈通过砂纸、刷洗等方法去除基材表面的锈蚀物,化学除锈使用酸、碱等化学药品溶解锈蚀物,表面活化则是通过改变表面的化学性质来增强涂层与基材的附着力。
在进行涂装操作时,需要注意控制涂料的均匀性和涂料的流变性。
高固体分涂料因其高固体含量,粘度较高,容易出现涂装不均匀、流平性差的问题。
因此,在涂装时需要选择合适的喷涂设备和增稠剂,调整涂料的流变性,以提高涂布均匀性和流平性。
同时,合理控制喷涂参数,如压力、喷嘴大小等也是确保涂装质量的关键。
当高固体分涂料完成涂装后,需要进行固化以形成坚固的涂膜。
固化的方法有烘干固化、烤漆固化和紫外光固化等。
烘干固化主要适用于溶剂型涂料,通过加热使溶剂挥发,从而固化涂料。
烤漆固化则是通过将涂层暴露在高温环境中,使涂料中的反应物质发生反应,形成固化后的涂膜。
紫外光固化是将涂层暴露在特定的紫外光下,通过紫外线的能量来促使涂料固化。
根据涂料的特性和涂装的环境,选择合适的固化方法非常重要。
最后,需要对涂膜性能进行评价。
涂膜性能评价包括附着力、硬度、耐磨性、耐腐蚀性、耐候性等指标。
附着力是评价涂层与基材的结合力,可以通过剥离实验来测试。
硬度是评价涂膜表面硬度的指标,可以通过铅笔硬度测试来进行评价。
耐磨性、耐腐蚀性、耐候性等性能可以通过相关的物理性能测试仪器进行实验评价。
这些评价指标的操作方法和标准应根据不同领域和应用需求进行选择,以保证涂膜性能满足要求。
我国海洋防腐涂料现状及未来发展趋势
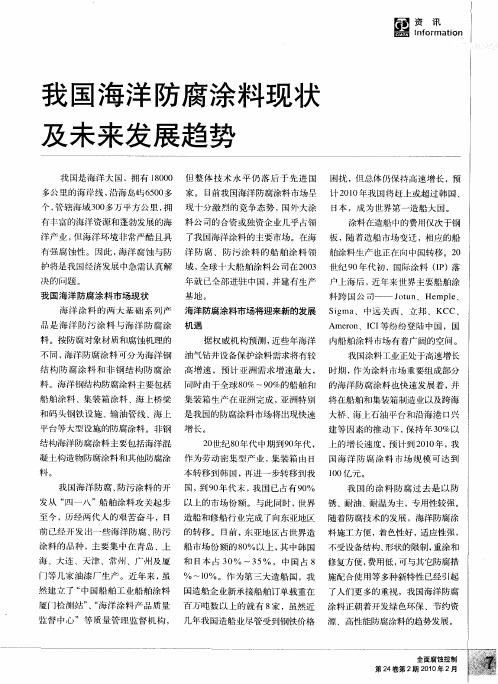
不同 , 海洋防腐涂料可分 为海 洋钢 油气钻井设 备保护涂料需求将有较
结 构 防腐 涂料 和 非钢 结 构防 腐 涂 高增速 ,预计 亚洲需求 增速最大 , 时期 , 作为涂料市场重要组成部分 料 。海洋钢结构防腐涂料主要 包括 同时 由于全球 8 %~9 %的船舶和 的海洋防腐涂料也快速发展 着, 0 0 并 船舶涂料 、集装箱涂料 、海上桥梁 集装箱生产在亚洲完成 , 亚洲特别 将在船舶和集装箱制造业以及跨海
海 洋涂 料 的两 大基 础 系列 产 海洋防腐涂料市场将迎来新的发展 S g 、中远 关西 、立 邦 、KC ima C、 品是 海 洋防 污涂 料 与海 洋 防腐 涂 机遇 料 。按防腐对象材 质和腐蚀机理的 Am rn C 等纷纷登陆 中国 ,国 eo 、I I
据权 威机 构预测 , 近些年海洋 内船 舶涂料 市场 有着广阔的空间。 我国涂料工业正处于高速增长
门等几家油漆厂生 产 。近年来 , 虽 % ~1% 。作为第 三大造船 国 ,我 施配合使用等多种新特性 已经引起 0 然建立 了 “ I 工业船舶涂料 国造船企业新承接船舶订单载 重在 了人们更多的重视 ,我国海洋 防腐 中匡船舶
厦门检测站 ” “ 、 海洋涂料 产品质量 百 万吨数以上 的就 有 8 ,虽然近 涂料正朝着开发绿 色环保 、节 约资 家
凝土构造物防腐涂料和其他防腐涂 作为劳动密集型产业 , 集装箱 由 日 国海 洋 防腐 涂料 市 场规 模可 达 到 料。 本转移 到韩国 , 再进一步转移 到我 10亿元 。 0
我 国海洋 防腐 、 防污涂料 的开 国 , 0 到9 年代末 , 国 已占有 9 % 我 0
我 国的 涂料 防 腐过去 是 以防
和码头钢铁 设施 、 输油管 线、海上 是我国的防腐涂料市场将 出现快速 大桥 、 上石油平台和沿海港 口兴 海
海洋工程重防腐涂料的应用技术现状及发展分析

海洋工程重防腐涂料的应用技术现状及发展分析黄红雨,宋雪曙 (上海振华重工(集团)股份有限公司,上海 200125)【摘要】摘要:针对海洋腐蚀对海洋工程的影响及防腐蚀的意义,详细论述了海洋防腐涂料的种类、性能、要求,国际海工防腐标准对涂层配套的技术要求和试验指标,对当前长寿命、低表面处理、高固体分、无溶剂、水性化、环保低毒等海洋防腐涂料的研究重点及进展进行了介绍,分析了海洋防腐涂料应用现状及存在的问题,探讨了长寿命防腐涂料和高耐久复合涂层体系,提出了同寿命涂层设计理念。
针对与国外的差距,提出了我国应加强基础性研究以及人才培养的建议。
【期刊名称】涂料工业【年(卷),期】2012(042)008【总页数】4【关键词】关键词:海洋腐蚀;海洋防腐涂料;涂装技术;分析海洋防腐蚀是海洋工程的关键技术之一,金属在海洋中腐蚀导致的应力腐蚀断裂(SCC)、氢脆(HE)、腐蚀疲劳(CF)、晶间腐蚀(IC)等会使海工钢结构发生突然断裂,导致海洋环境生态灾难,造成巨大损失。
此外,海工产品防腐涂层的提前失效和涂层维修带来的停工损失也相当大。
因此,必须采取合适的防腐蚀技术予以解决。
近年来国内外对海洋腐蚀与防护日趋重视,虽然各种耐海水腐蚀材料不断推出,各种防腐蚀施工技术也大有发展,但仍远不能满足实际需求。
我国对海洋工程结构设施的防腐蚀研究与国外发达国家有明显的差距,一些关键技术尚未解决,没有形成具有我国自主知识产权的技术,而且缺少相应的防腐规范和标准,这些都严重影响了海洋工程结构的设计、建造和安全运行。
因此,针对我国重点海域和重大海洋工程所面临的共性和关键防腐蚀问题,开展海洋工程结构设施的长效防腐蚀关键技术研究,不但可以防止腐蚀发生,避免或减少后期服役的维修、维护费用和因维修造成的经济损失,减少重大恶性事故的发生,而且能够使海工设施的安全性大大提高,具有重大意义。
1 海洋防腐涂料的要求海洋防腐涂料是指在海洋环境中使用的防腐蚀涂料。
海洋工程材料防腐蚀技术应用与发展趋势

海洋工程材料防腐蚀技术应用与发展趋势随着海洋工程的不断发展,海洋工程材料的防腐蚀技术也越来越重要。
在海洋环境中,海水中的氯离子、海盐、海藻等物质以及气候环境等各种因素都会造成海洋结构材料的损坏腐蚀,防腐蚀技术的应用和研究将对海洋工程的可靠性和寿命产生重要影响。
本文将从防腐蚀技术的应用和发展趋势两方面来探讨海洋工程材料防腐蚀技术的现状以及未来的趋势。
一、防腐蚀技术的应用1.金属涂层对于海洋结构的防腐蚀,金属涂层是一种常用的方法。
金属涂层的主要作用是防止海水中的氯离子、海盐等物质侵蚀结构表面。
常用的金属涂层包括锌涂层、铝涂层、不锈钢涂层等。
在实践中,锌涂层是最为常见的防腐蚀涂层,其主要原因是锌具有较高的电化学电位并且易于镀制成薄膜。
2.有机涂层有机涂层是另一种常用的海洋工程材料防腐蚀技术。
有机涂层可以覆盖在结构表面上形成一层保护膜,使其对海水等外界物质的侵蚀具有一定的防护作用。
有机涂层的主要材料包括有机硅涂料、环氧涂料、聚氨酯涂料等。
有机涂层的优点是粘附力强,可起到密封作用,但其寿命较短。
3.玻璃纤维增强塑料玻璃纤维增强塑料是目前应用较为广泛的一种防腐蚀材料。
该材料不仅具有轻质、高强度等优点,还能耐受环境的侵蚀,长期使用不会出现腐蚀损坏。
同时,玻璃纤维增强塑料还容易加工,成型灵活,可以制作成各种不同形状的部件。
这在海洋大型结构的制造中有一定的优势。
二、发展趋势1.功能性涂层传统的涂层材料主要是为了对海水侵蚀起到保护作用,而对于一些海洋结构来说,单单的防护作用已经不能满足需求。
因此,未来的发展方向将会是研究开发具有更多功能性的涂层材料,如自修复、自洁、抗污等特点,以满足海洋工程的更高要求。
2.新型防腐材料随着海洋工程的发展,新型防腐材料的研究将成为未来的一个重点。
这些材料不仅要具有优越的防腐蚀性能,还需要具备轻质、高强度、耐高温等功能,以更好地适应未来海洋工程的需求。
3.先进的材料制造技术先进的材料制造技术是未来海洋工程材料防腐蚀技术的重要保障。
高固体分防腐涂料开发与产品推广应用趋势
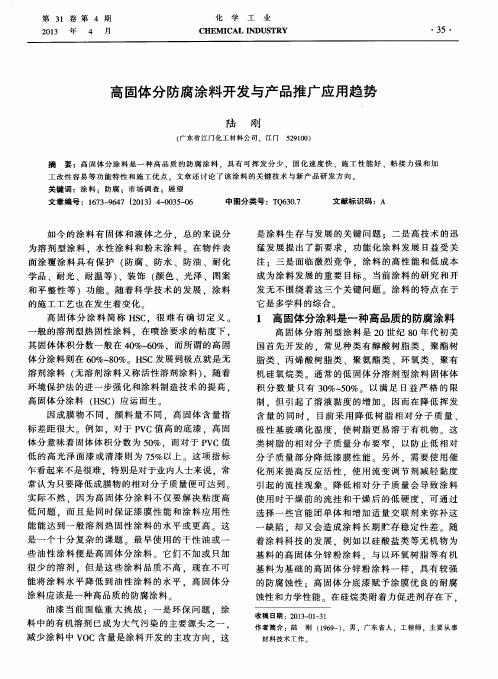
环境 保护 法 的进 一 步强 化 和涂 料制 造技 术 的 提高 . 高 固体分 涂料 ( HS C)应 运而 生 。 因成 膜 物 不 同 .颜 料 量 不 同 .高 固体 含 量指 标 差 距很 大 。例 如 ,对 于 P V C值 高 的底 漆 .高 固
体 分 意 味着 固体 体 积分 数 为 5 0 %.而 对 于 P V C值
面 涂 覆涂 料 具 有 保 护 ( 防腐 、 防水 、 防油 、耐 化
学 品 、耐光 、耐 温 等 ) 、装 饰 ( 颜 色 、光 泽 、 图案 和平 整性 等 )功 能 。随着 科 学 技 术 的发 展 , 一 涂 料
的施 工 工艺也 在 发生 着变 化 。
成 为 涂料 发 展 的 重要 目标 当前 涂 料 的研 究 和开 发 无不 围绕 着 这 三个 关 键 问 题 涂 料 的 特点 在 于
般 的溶 剂 型热 固性 涂 料 .在 喷涂 要 求 的粘 度下 .
其 固体 体积 分 数一 般 在 4 0 %~ 6 0 % .而 所谓 的高 固 体 分 涂料 则在 6 0 %~ 8 0 % H S C发 展 到极 点就 是无
溶 剂 涂料 ( 无 溶 剂涂 料 又称 活 性溶 剂 涂料 ) .随着
使 用 时 干燥 前 的流 挂 和 干燥 后 的低 硬 度 .可 通 过 选 择 一 些 官 能 团单 体 和增 加适 量 交 联 剂 来 弥 补这
一
Байду номын сангаас
缺 陷 .却 又 会 造 成 涂料 长期 贮 存 稳 定 性 差 。 随
是 一 个 十分 复 杂 的课 题 最 早 使 用 的干 性 油 或 一
制 .但 引 起 了 溶液 黏 度 的 增 加 因而 在 降低 挥 发
防腐蚀领域新突破--喷涂聚脲弹性体技术

防腐蚀领域新突破——喷涂聚脲弹性体技术黄微波陈酒姜王宝柱刘培礼刘东晖 (海洋化工研究院青岛266071)摘要“喷涂聚脲弹性体”(Spray Polyurea Elastomer 以下简称SPUA)技术是国外近十年来,继高固体份涂料、水性涂料、光固化涂料、粉末涂料等低(无)污染涂装技术之后,为适应环保需求而研制、开发的一种新型无溶剂、无污染的绿色施工技术,在我国研发成功后,以其优异的综合性能和先进的施工工艺,引起了国内材料界和工程界的极大关注。
本文从发展简史、化学原理、材料性能、应用领域等方面,较系统、全面地介绍该技术的发展过程以及在防腐蚀领域中的独特优势。
关键词: 喷涂、聚脲、聚氨酯、弹性体、防腐蚀前言喷涂聚脲弹性体(Spray Polyurea Elastomer 以下简称SPUA)技术是国外近十年来,继高固体份涂料、水性涂料、光固化涂料、粉末涂料等低(或无)污染涂装技术之后,为适应环保需求而研制、开发的一种新型无溶剂、无污染的绿色施工技术,与传统的低(或无)污染涂装及喷涂聚氨酯技术相比(见表1)。
表1. 环保型施工技术之比较SPUA技术具有以下优点:1.不含催化剂,快速固化,可在任意曲面、斜面及垂直面上喷涂成型,不产生流挂现象,5秒钟凝胶,1分钟即可达到步行强度。
2.对水分、湿气不敏感,施工时不受环境温度、湿度的影响。
3.双组分,100%固含量,对环境友好;可以1:1体积比进行喷涂或浇注,一次施工达到厚度要求,克服了以往多层施工的弊病。
4.优异的物理性能,如抗张强度、柔韧性、耐磨性等。
5.具有良好的热稳定性,可在150℃下长期使用,可承受350℃的短时热冲击。
6.可加入各种颜、填料,制成不同颜色的制品。
7.配方体系任意可调,手感从软橡皮(邵A30)到硬弹性体(邵D65)。
8.使用成套喷涂、浇注设备,施工方便,效率高。
可以这样讲:SPUA技术是一种新型“万能”(国外称之为versatile)涂装技术,它全面突破了传统环保型涂装技术的局限,因此,使得该技术一问世,便得到了迅猛的发展。
- 1、下载文档前请自行甄别文档内容的完整性,平台不提供额外的编辑、内容补充、找答案等附加服务。
- 2、"仅部分预览"的文档,不可在线预览部分如存在完整性等问题,可反馈申请退款(可完整预览的文档不适用该条件!)。
- 3、如文档侵犯您的权益,请联系客服反馈,我们会尽快为您处理(人工客服工作时间:9:00-18:30)。
1·前言防腐蚀涂料的防护作用主要有3 种: 漆膜与片层颜料的屏蔽作用、碱性或氧化性颜料的缓蚀钝化作用以及锌粉的电化学保护作用。
其中,能把水、氧以及离子等腐蚀介质隔绝的屏蔽作用最为关键。
目前常用的海洋重防腐涂料多为溶剂型涂料。
在其成膜过程中,溶剂挥发留下的针孔,会使腐蚀介质渗至膜下造成腐蚀。
所得腐蚀产物膨胀挤破涂层,使腐蚀介质得以扩散,终使涂层成片脱落失效。
需要指出的是,防护涂层即使无裂纹和针孔空隙等缺陷,腐蚀介质仍然能在一定程度上渗透涂层到达金属表面。
因此,必须提高涂膜的致密性与厚度以延长介质的渗透时间[1 - 3]。
海洋钢铁设施中常用的重防腐涂层总厚度一般要求300 ~ 500 μm,有的甚至要求更厚。
然而,溶剂型涂料的单道涂层仅为一百多微米,需要多道涂装才能达到规定膜厚,这就增加了施工成本,而且溶剂对工人的身体健康有损害。
面对溶剂型涂料的种种问题,科研人员正在努力开发新型防腐蚀涂料[4 - 5]。
其中,高固体分环氧涂料受到极大重视。
高固体分环氧涂料多为双组分反应固化型防腐涂料[6]。
低分子量环氧树脂、颜料、活性稀释剂及各种助剂经高速分散、研磨后,制成漆料组分,可满足特定场合需要的改性胺作固化剂组分。
环氧树脂用作成膜物质的优点是: 由于它含有大量的羟基与醚基等强极性基团,使其与底材的附着力非常好; 固化时不产生小分子副产物,体积收缩很小,因而具有良好的成膜致密性;优异的机械性能、耐化学品性能和耐腐蚀性能。
采用低分子量的树脂与活性稀释剂是为了降低施工粘度,以提高涂膜平整性与致密性。
高固体分是指: 制备与施工无需或很少量使用有机溶剂; 涂料的固含量很高,甚至达100%。
回避了有机溶剂就消除了针孔现象,提高了涂膜的抗渗性,免除了溶剂毒害。
固含量高使得单道涂层的厚度增大,适用于厚涂,从而减少了涂装费用与时间。
高固体分环氧涂料综合了高固体分与环氧树脂的优点,高固体分环氧涂料是实现厚膜化要求的最简单有效的方法,已经成为防腐涂料的研究热点,是海洋重防腐涂料的发展趋势。
2·高固体分环氧防腐涂料研究现状国际油漆( International) 、亚美龙( Ameron) 、式玛卡龙( sigmakalon) 、青岛725 所和海洋化工研究院等涂料公司都有无溶剂涂料的生产,并取得了优异的防腐效果。
杜建伟、张静[7]等研制了一种在球墨铸铁管管道及配件管道内壁水泥砂浆表层用的超厚膜环氧涂料,该涂料是以环氧树脂与特定固化剂反应而得的双组分常温固化型防腐蚀涂料,一次喷涂可达500 μm,双组份固化形成网状立体结构,具有良好的防腐效果。
王秀娟、李敏[8]等人采用腰果壳油改性的酚醛胺作为固化剂制备的高固体分环氧树脂,在低温下能实现快速固化,并保持良好的防腐性能。
与脂肪族的聚酰胺和改性脂肪胺类固化剂相比,该固化剂中的苯环结构与双酚 A 型环氧树脂具有更好的相容性,从而可进一步的降低体系的黏度,提高主剂和固化剂的兼容性。
同时长直链不仅给体系提供了良好的内增韧效果,而且对体系的固化反应有初始的空间位阻效应,使得体系特别是高固体含量的体系在快速固化时仍有良好的操作期。
郭晓军、白晶[9]等人开发了一种以低黏度双酚F 环氧树脂为基料,添加片状高耐磨颜填料及助剂等,以改性脂肪胺为固化剂的无溶剂环氧防腐涂料。
双酚F 环氧树脂除具有双酚A 环氧树脂的所有优良特性外,其黏度远低于双酚A 环氧树脂,因此在使用过程中不需要加入溶剂或活性稀释剂,操作更方便,固化后漆膜的力学性能更佳,具有更好的耐溶剂性,避免了由于加入溶剂或稀释剂使得漆膜出现针孔、脆性大等弊病。
但双酚F 环氧树脂价格要比双酚A 环氧树脂高,综合考虑涂料成本与性能,经过试验确定双酚F 环氧树脂含量占总量的35% ~ 50% 时,性价比最高。
鉴于厚膜防腐涂料在海洋防腐领域的突出表现,超厚膜涂料也渐渐成为重防腐涂料领域的新宠。
超厚膜涂料是指喷涂一道漆的干膜厚度大于1 mm,甚至更厚的涂料,一般是无溶剂型,100% 固含量的涂料,能达到长期使用、无需维修的效果,具有更优异的防腐性能[10]。
1972 年美国亚美龙公司率先把超厚膜涂料推向市场进行实用考核,将其Tideguard171 涂在墨西哥海湾一钻井平台腐蚀条件最严酷的脚架部位。
10 年后检查,漆层没有裂纹、脱落、泛锈迹现象,仅是褐色表面褪色。
根据其优良的使用效果,超厚膜涂料Tideguard171被各大石油公司广泛用于钻井平台的甲板、钻井房、走道、直升机甲板、打桩工程、码头、防波设备及浅海的原油管的支撑钢构上[10]。
之后,很多大涂料公司,如国际油漆、亚美龙、式玛卡龙、日本迪恩特也纷纷研制及推出超厚膜涂料,先后应用于石油化工产品等有特殊要求的贮罐内壁、输送管道内壁、污水处理厂、管道和贮罐外壁防腐、水利工程钢结构的防腐等工程。
我国20 世纪90 年代开始了对超厚膜重防腐涂料的研究,青岛725 所和海洋化工研究院都在尝试超厚膜重防腐涂料的研究,并取得了一定的成果。
海洋化工研究院姜秀杰、崔显林[11]等人研制出的海洋浪溅区钢结构超厚膜环氧涂料,一道涂料施工干膜厚度达1 000 μm,缩短了工程时间,降低了施工成本,不存在多次喷涂的层间附着力不佳问题,且使用时间长,并且通过合成EPU 改性环氧树脂有效地提高了涂层的抗冲击性能和耐磨损的特点。
蒋健明、陈正涛[12]研究了不同环氧树脂、环氧固化剂、颜料、助剂等的特性,制备了厚膜型无溶剂环氧涂料,并进行了各项性能的检测,结果表明,该涂料具有极低的VOC 含量,符合环保要求,适于要求长效防腐的钢构件。
中国科学院海洋研究所与日本DNT 公司联合开发了性能优异的海洋钢结构用超厚膜环氧防腐涂料[13],一次涂装能达到1. 2 mm 以上。
该涂层具有收缩率低、抗渗透性好、抗冲击性优异、附着力好、耐海水及耐酸碱介质性能优良的特点,寿命长,是一款综合性能优异的重防腐涂料。
高固体分涂料虽具有众多优点,但也存在一些缩孔多与出现流挂的不足。
缩孔是因为高固体分涂料中的大多数低聚物都需要比较高的官能团含量,同时采用较高极性和高表面张力的溶剂以获得低黏度,造成涂料的表面张力比传统溶剂型涂料高。
要解决缩孔,必须在配方设计时添加调整表面张力的助剂( 流平剂) 使其表面张力接近同类传统涂料的表面张力,同时,在施工时要对被涂底材进行严格的表面处理。
流挂是由于高固体分涂料的施工黏度较小与干燥较慢造成的。
针对这一现象,除了加入防流挂剂,还可以采用热喷涂技术,特别是双组分喷涂设备。
在施工前,将涂料加热至一定的温度以降低黏度,而非采用稀释剂来降低黏度。
3 ·高固体分环氧涂料主要成膜物质研究现状高固体分环氧涂料的核心问题是设法降低成膜物质的相对分子质量、降低黏度、提高溶解性能,而通过在成膜过程中有效的交联反应保证完美的涂层质量。
高固体分环氧涂料配方中,应该充分的掌握各组分的特性和涂料对各组分的要求,其中成膜物质环氧树脂跟其固化剂的性能对涂料体系的性能起到最关键的作用。
3. 1 环氧树脂发展状况高固体分环氧涂料对环氧树脂选择时,应该满足低黏度、高交联密度、漆膜内极性化学键及基团少等要求。
一般选用低分子量的液体环氧树脂E51 或E44 作为基料,从而导致漆膜柔韧性不佳,因此环氧树脂的研究主要集中在对其进行增韧改性,生产具有柔韧性的树脂。
利用弹性体增韧环氧树脂的工作早在20 世纪60 年代就已进行,其增韧原理可用经典的海岛结构理论解释。
根据弹性体海岛结构在树脂分散相的形成先后不同,可分为添加法与原位生成法。
所采用的弹性体主要有丁腈橡胶,近年来,除丁腈橡胶外,聚氨酯、有机硅等弹性体都有采用。
采用液体丁腈橡胶( CTBN) 增韧环氧树脂比较让人注目[14 - 16]。
环氧树脂与液体丁腈橡胶先进行预反应,少量丁腈橡胶的加入不会形成两相结构,只有当丁腈橡胶含量达到一定的限度时形成具有海岛结构的相分离[17]。
这既能满足未固化前橡胶与环氧树脂良好混溶,低粘度特性,又可以再固化后能析出橡胶相,产生微观相分离,提高耐冲击性能。
除了端羧基丁腈橡胶外,端羟基、端胺基、端乙烯基丁腈橡胶增韧,近年也有报道[18 - 19],其都能在一定程度上提高环氧树脂的冲击强度,但由于端基基团的差异,形成的两相结构在微观结构上有少许的差异。
聚氨酯增韧环氧树脂目前研究较多的是以聚氨酯和环氧树脂形成半互穿网络( SIPN) 和互穿网络( IPN) 聚合物,SIPN 与IPN 结构可取“强迫互容”与“协同作用”使聚氨酯的高弹性与环氧树脂的良好耐热性与粘接性有机地结合在一起,取得良好的增韧效果[20]。
加入有机硅既能降低环氧树脂内应力,又能改善环氧树脂韧性、耐高温性等性能,使用这种方法改性环氧树脂是近年来发展起来的新途径[21]。
其中最大困难是二者相容性差,解决相容性是增韧的关键。
洪晓斌等[22]合成3,3,3″-三羟基苯氧基硅烷三缩水甘油醚,当其含量为4% 时,可使环氧树脂的拉伸强度、弯曲强度分别提高10. 4% 及53. 6% ,线胀系数降低18. 8% ,抗开裂指数提高52. 2%。
苏倩倩等人[23]用聚甲基三乙氧基硅烷( PTS) 改性环氧树脂体系,固化物的拉伸强度从48. 94 MPa 增加到58. 36 MPa,断裂伸长率增加了4. 1% ,达到11. 65% , Tg 从152. 53 ℃增加到169. 82 ℃。
这种改性方法既提高了固化物的力学性能,又提高了固化物的热性能,目前国内外所报道的各种有机硅改性环氧方法很少有达到此种效果的。
弹性体改性环氧树脂国内已经有一些商品面市,但是其综合性能在高固体分环氧树脂的应用上还有很大的差距。
国外已有系列化产品,主要生产商有日本ACR、东都化成、韩国国都化学、台湾南亚等。
以韩国国都化学产品较具代表性。
与此同时,也出现新型柔韧性环氧树脂,其在很大程度上弥补了上述弹性体增韧环氧的不足。
其种类主要有缩水甘油醚与缩水甘油酯类环氧树脂。
缩水甘油酯型柔韧性环氧树脂主要品种有二聚酸的缩水甘油酯以及二聚酸与环氧树脂的部分加成物。
二聚酸的缩水甘油酯的合成方法与经典的缩水甘油酯型环氧树脂合成方法基本相同。
通常是由二聚酸与环氧氯丙烷在催化剂作用下反应形成氯醇物,然后在碱作用下脱氯化氢形成缩水甘油酯。
二聚酸缩水甘油酯及其改性环氧树脂的固化物具有较好弹性,又称为可挠性环氧树脂。
在日本东都化成、韩国国都、台湾南亚等公司都有此类产品。
采用长链脂肪醇或在刚性酚类结构中引入柔性长链脂肪醇,可合成出不同柔性的缩水甘油醚型环氧树脂。
这类环氧树脂具有粘度低,色泽浅,增柔效果好等特点。
特别是刚性与柔性链共聚物的缩水甘油醚,可通过共聚比列的调节,达到不同的柔韧性。
国外直链型脂肪族柔韧性环氧树脂代表物为美国陶氏公司的的DER-732 与DER- 736,性能见表1。