轧钢车间设计总论
年产万吨热轧带钢车间设计
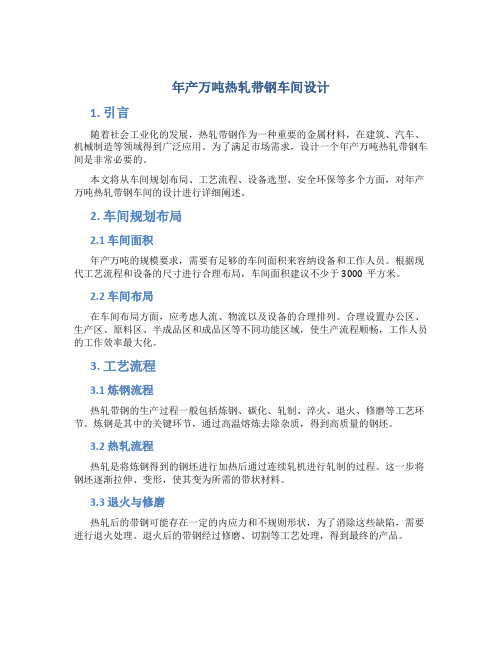
年产万吨热轧带钢车间设计1. 引言随着社会工业化的发展,热轧带钢作为一种重要的金属材料,在建筑、汽车、机械制造等领域得到广泛应用。
为了满足市场需求,设计一个年产万吨热轧带钢车间是非常必要的。
本文将从车间规划布局、工艺流程、设备选型、安全环保等多个方面,对年产万吨热轧带钢车间的设计进行详细阐述。
2. 车间规划布局2.1 车间面积年产万吨的规模要求,需要有足够的车间面积来容纳设备和工作人员。
根据现代工艺流程和设备的尺寸进行合理布局,车间面积建议不少于3000平方米。
2.2 车间布局在车间布局方面,应考虑人流、物流以及设备的合理排列。
合理设置办公区、生产区、原料区、半成品区和成品区等不同功能区域,使生产流程顺畅,工作人员的工作效率最大化。
3. 工艺流程3.1 炼钢流程热轧带钢的生产过程一般包括炼钢、碳化、轧制、淬火、退火、修磨等工艺环节。
炼钢是其中的关键环节,通过高温熔炼去除杂质,得到高质量的钢坯。
3.2 热轧流程热轧是将炼钢得到的钢坯进行加热后通过连续轧机进行轧制的过程。
这一步将钢坯逐渐拉伸、变形,使其变为所需的带状材料。
3.3 退火与修磨热轧后的带钢可能存在一定的内应力和不规则形状,为了消除这些缺陷,需要进行退火处理。
退火后的带钢经过修磨、切割等工艺处理,得到最终的产品。
4. 设备选型4.1 炼钢设备炼钢设备是热轧带钢车间中的核心设备,包括炉子、转炉、炼钢机等。
选购时应考虑设备的稳定性、生产能力以及能耗方面的因素。
4.2 轧机设备轧机设备是热轧过程中的关键设备,主要包括脱碳设备、轧机机组和辊道设备等。
选型时需综合考虑轧制能力、稳定性以及安全工作性能。
4.3 退火设备退火设备用于对经过轧制后的钢带进行退火处理,消除内应力和恢复材料的塑性。
选择设备时需考虑工艺要求、退火温度和速度的控制以及能耗方面的因素。
5. 安全环保在车间设计中,安全环保是至关重要的。
应设计合理的消防设施,安装可靠的烟雾和气体检测系统,确保生产过程中的安全。
热连轧带钢车间工艺设计论文(DOCX 124页)

西安建筑科技大学本科毕业设计(论文)题目年产240万吨1580mm热连轧带钢车间工艺设计学生姓名柳旭辉学号 4院(系)冶金工程学院专业材料成型及控制工程指导教师陈小林时间2017年6月10日设计总说明板带钢是钢铁产品的主要品种之一,广泛应用于工业,农业,交通运输和建筑业。
近年来,世界各国都在注重研制和使用新技术和新设备来生产板带钢,例如采用超快速冷却技术生产双相钢。
本设计是年产240万吨1580mm热轧带钢车间工艺设计。
产品规格为:(~)× (850~1500)mm,所用钢种为:低碳钢,低合金钢。
论文主要内容包括:典型产品的选择和原料的选择,主要设备和辅助设备的选择,生产工艺的制定,典型产品的计算,并对主要设备(轧辊和电机)的计和规划。
本设计达到了预期要求,实际产量为260万吨。
关键词:热连轧,带钢,工艺计算,典型产品,设备Design DescriptionStrip is one of steel and iron products. It plays an important role in the industry,agriculture,transportation and construction. In recent years, many new technologies and equipments, such as ultra-fast cooling are developed toproduce the duplex steel in the various countries.This design is the annual output of million tons of sheet strip workshop process design. Its product specifications range from ~×(850~1550)mm , which uses steels of carbon steel,low alloy steel.The thesis mainly includes the selection of tppical production and raw material ,the selection of subsidiary equipments and main equipments, formulation of production technology,technology calculation of the typical products,and check the capacity of main equipments (including rolling mills and the electric motors). Setting about the products design it plans exactly the main economic index of the workshop and its arrangement,environmentproduction and so on.The design achieves the desired requirements with the annual output of million tons.Key Words:hot rolling, srip, technology calculate, typical product, equipment.目录1文献综述 ...................................................................................................... 错误!未定义书签。
轧钢车间设计

车间设计任务书是依据,由有关上级部门下达。设计任务书的基本内容包 括:
1. 车间的生产规模、品种 2. 生产方案 3. 建厂地址,厂区范围,资源利用状况、各种材料供应、运输等 4. 要求达到的技术水平,经济及社会效益 5. 投资及劳动定员的控制数字。 6. 环保要求
6
2 生产方案与产品方案制定
8
一. 板带钢生产:~0.2 薄带箔材,0.2~0.4 薄板,4~中厚板 1. 中厚板生产:单机四辊可逆式,双机架(2+4 或 4+4)可逆式;半连 轧连轧 2. 热轧薄板带钢:全连续式,半连续式、3/4 连续式 2.0~12mm→0.8mm 3. 冷轧带钢:单机可逆、连轧(3 机架 4 机架 5 机架 6 机架)0.1~2.0mm 二. 型钢生产 1. 横列布置普通轧法 2. 万能轧法 3. 型钢连轧 4. 热及冷弯型钢 5. 挤压法 三. 管材生产 1. 热轧法:自动轧管机、连轧管机、两辊斜轧穿孔、三辊斜轧穿孔、菌 式穿孔机、张力减径机、皮格尔轧管、狭舍尔轧管机 2. 热挤压 3. 焊接:直缝焊、螺旋焊 4. 冷加工:冷轧 冷拔、冷旋压 四. 线材生产 以下成卷交货 一般断面为圆形 1. 横列式(二辊轧机) 2. 半连续式(三辊轧机) 3. 连续式(二辊+45°无钮式或二辊+Y 型无钮)(单线或三线)
影响产品的产量、质量,因此选择轧机时应以生产方案和产品方案为依据进行
52.5
普通及深冲用低碳
0.2~0.3 600~1500
卷
钢带
22.5 22.5
7
镀锌钢板
0.25~0.55 700~1500 1000~6000 13.5 13.5
镀锌钢带
0.25~0.55 700~1500
毕业设计年产420万吨热轧带钢车间设计
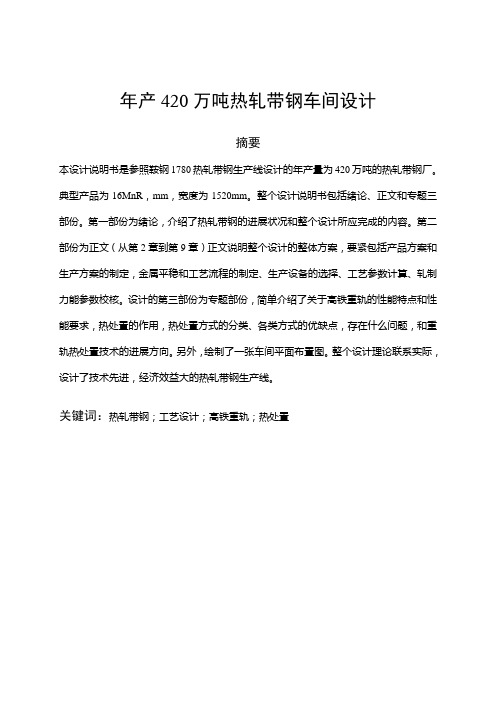
年产420万吨热轧带钢车间设计摘要本设计说明书是参照鞍钢1780热轧带钢生产线设计的年产量为420万吨的热轧带钢厂。
典型产品为16MnR,mm,宽度为1520mm。
整个设计说明书包括绪论、正文和专题三部份。
第一部份为绪论,介绍了热轧带钢的进展状况和整个设计所应完成的内容。
第二部份为正文(从第2章到第9章)正文说明整个设计的整体方案,要紧包括产品方案和生产方案的制定,金属平稳和工艺流程的制定、生产设备的选择、工艺参数计算、轧制力能参数校核。
设计的第三部份为专题部份,简单介绍了关于高铁重轨的性能特点和性能要求,热处置的作用,热处置方式的分类、各类方式的优缺点,存在什么问题,和重轨热处置技术的进展方向。
另外,绘制了一张车间平面布置图。
整个设计理论联系实际,设计了技术先进,经济效益大的热轧带钢生产线。
关键词:热轧带钢;工艺设计;高铁重轨;热处置AbstractThis specification refers to anshan Steel’s 1780 strip line design for the production of hot rolling strip steel factory 420 million tons. Typical products for 16MnR, products for 2.5 mm thickness and width for 1520mm. The design manual includes three parts: introduction, text and topic .The first part is introduction, introduces the development status of strip and whole design should complete content. The second part (from chapter 2 text to chapter 9) is the text. The body of the whole design of the overall program description, including product and production plan formulation, metal balance and process, production equipment, process parameter calculation, rolling force. The third part of the design for the projects section, introduced the characteristics and performance requireents of GaoTieChong rail . It also induces the heat treatment, heat treatment methods of function of classification, the advantages , disadvantages of various methods, the existing problems, and what the heavy rail heat treatment technology development direction. In addition, draw a workshop layout. The whole design linkes theory and practice together. It also designs the advanced technology and economic benefit of strip line.Key words:hot rolling strip steel;high-speed railway rails; heat treatment目录1文献综述 (1)热轧带钢进展历史 (1)热轧带钢的种类及用途 (2)热轧一般带钢 (2)热轧优质带钢 (3)热轧带钢生产工艺 (4)几种新技术简介 (5)中间坯保温技术和边部感应加热技术 (5)组织性能操纵与铁素体区轧制新技术 (6)自由程序轧制技术 (7)热轧带钢进展中孕育的问题 (7)热轧工艺润滑技术问题 (7)热轧进程中产生氧化铁皮的问题 (8)小结 (9)2 产品方案与金属平稳 (10)产品方案的确信 (10)2.1.1 热轧产品品种及产品钢号标准 (10)2.1.2 产品品种规格及代表尺寸 (11)2.1.3 年打算产量及所占比例 (12)2.2金属平稳 (13)2.3 原料的选择 (14)2.3.1 原料种类及规格 (14)板坯技术条件 (14)2.3.3 年需坯数量 (15)3 轧制工艺进程及轧制制度的制定 (17)生产工艺流程 (17)3.1.1 典型产品生产工艺流程示用意 (17)3.1.2 生产工艺流程简介 (18)轧制制度的制定 (19)3.2.1 加热制度 (19)3.2.2 压下制度 (21)3.2.3 速度制度 (23)温度制度 (27)辊型制度 (30)厚度制度 (31)轧机工作图表 (32)4 设备参数的选择 (33)加热区设备的选择 (33)粗轧区设备选择 (34)4.2.1 板坯高压水除鳞装置 (34)粗轧机组 (35)4.2.3 粗轧机小立辊 (35)保温罩 (35)4.3 精轧区设备选择 (36)4.3.1 飞剪 (36)精轧除鳞箱 (36)4.3.3 精轧机组 (37)4.3.4 精轧区其他设备 (38)4.4 冷却装置 (39)4.5 卷取区 (40)5 轧制力与轧制力矩计算 (41)5.1 轧制力计算 (41)5.1.1 计算公式 (41)5.1.2 轧制力计算结果 (42)轧制力矩的计算 (43)轧制力矩计算公式 (43)轧制力矩计算结果 (44)6 设备能力参数校核 (44)轧制力能参数 (44)6.2 轧辊强度校核 (45)6.2.1 参数计算 (45)6.2.2 R1轧辊强度校核 (47)咬入角校核 (50)6.4 加热炉能力校核 (51)6.5 电机功率校核 (51)7 轧机生产能力校核 (53)7.1 年产量计算 (53)7.1.1 工作制度与工作时刻 (54)轧机生产能力校核 (54)8 车间技术经济指标 (56)概述 (56)8.2 车间各项技术经济指标分析及制定 (57)9 节能与环境爱惜 (61)9.1 绿化布置 (61)9.2 污染物处置 (62)9.2.1 水处置 (62)9.2.2 废气处置 (62)9.2.3 热轧润滑油处置 (63)9.3 噪声处置 (63)9.4 废弃物处置 (63)9.5 现场节能技术与方法 (63)高铁重轨热处置技术的进展 (64)1.高铁重轨的性能特点和性能要求 (65)高铁重轨的概念 (65)高铁重轨的性能特点 (65)高铁重轨的性能要求 (65)2 高铁重轨的热处置技术 (66)高铁重轨热处置的作用 (66)2.2 高铁重轨热处置方式的分类及其优缺点 (67)高铁重轨热处置存在的问题 (68)3重轨热处置技术的进展方向 (68)环保节能是近代重轨热处置技术进展的主题 (69)3.2 贝氏体重轨热处置工艺 (69)4 小结 (70)结论 (71)致谢 (71)参考文献 (72)1文献综述1.1热轧带钢进展历史热轧带钢是在带钢热轧机上生产厚度为 1.2~8mm成卷带钢的工艺。
重钢1780mm热轧带钢车间工艺设计毕业论文

重钢1780mm热轧带钢车间工艺设计毕业论文目录摘要 (I)ABSTRACT (II)引言 (1)1车间投资分析 (2)1.1本设计的目的和意义 (2)1.2厂址的选择 (2)1.3原料及产品的市场分析 (3)1.4技术经济分析 (3)2年产量及产品大纲的制定 (5)2.1产品方案的编制 (5)2.1.1产品方案 (5)2.1.2编制产品方案的原则及方法 (5)2.1.3选择计算产品 (5)2.1.4确定产品大纲 (5)3生产方案 (7)3.1选择生产方案的依据 (7)4生产工艺流程制定 (8)4.1制定生产工艺流程的主要依据 (8)4.2主要生产工艺过程简述 (9)4.2.1板坯库工艺技术流程 (9)4.2.2加热炉工艺技术流程 (9)4.2.3粗轧区工艺技术流程 (10)4.2.4热卷箱、飞剪工艺技术流程 (10)4.2.5精轧区工艺流程 (11)5轧机选择 (12)5.1轧钢机选择的原则 (12)5.2轧钢机机架布置及数目的确定 (12)5.2.1E1立辊轧机 (12)5.2.2四辊粗轧机 (14)5.2.3F1E立辊轧机 (15)5.2.4F1~F7四辊精轧机组 (15)6辅助设备的选择 (17)6.1加热及热处理设备选择 (17)6.1.1炉型确定 (17)6.1.2步进梁及运动机构 (17)6.1.3加热炉 (18)6.3热卷箱 (19)6.4层流冷却 (21)7典型产品工艺计算 (24)7.1确定粗轧机组的轧制规程 (24)7.1.1板坯尺寸 (24)7.1.2粗轧机组压下量分配原则及其道次变形量的分配 (24)7.1.3校核咬入能力 (25)7.1.4粗轧机组的速度制定 (25)7.1.5确定轧件在各道次中的轧制时间 (26)7.1.6确定轧件在各道次中的轧制温度 (28)7.1.7确定轧件在各道次的平均变形速度 (30)7.1.8确定轧件在各道次的轧制力 (31)7.1.9确定轧件在各道次的轧制力矩 (33)7.2精轧阶段工艺计算 (38)7.2.1压下规程的分配 (38)7.2.2精轧机组速度制度的制定 (39)7.2.3轧制时间的确定 (40)7.2.4轧制温度的确定 (40)7.2.5计算各道的平均变形速度 (41)7.2.6计算各道平均单位压力 (42)7.2.7计算各道的传动力矩 (44)8电机能力校核 (48)8.1粗轧电机能力校核 (48)8.1.1等效力矩计算 (48)8.1.2电机温升校核 (49)8.1.3电机的过载校核 (49)8.2精轧机电机能力校核 (49)8.2.1等效力矩计算 (49)8.2.2电机温升校核 (49)8.2.3电机的过载校核 (49)9轧辊强度校核 (50)9.1R1强度校核 (50)9.1.1辊身强度校核 (50)9.1.2辊颈弯曲应力和扭转应力计算 (51)9.1.3辊头扭转强度计算 (51)9.1.4接触应力计算 (52)9.2F1~F4精轧机强度校核 (52)9.2.1支承辊弯曲力矩校核 (52)9.2.2辊颈弯曲应力和扭转应力校核 (53)9.2.3辊头扭转强度计算 (53)9.2.4接触应力计算 (53)9.3F5~F7精轧机强度校核 (53)9.3.1支承辊弯曲力矩校核 (53)9.3.2辊颈弯曲应力和扭转应力校核 (54)9.3.3辊头扭转强度计算 (54)9.3.4接触应力计算 (54)10轧钢机产量计算 (55)10.1典型产品的工作图表 (55)10.2典型产品小时产量计算 (55)10.3厂年产量计算 (55)11车间平面布置 (57)11.1平面布置的原则 (57)11.2金属流程线的确定 (57)11.3设备间距的确定 (58)11.3.1加热炉及其前后设备间距 (58)11.3.2其它设备之间的距离 (58)11.3.3车间跨度大小及柱距大小 (58)11.4仓库面积的确定 (59)11.4.1原料仓库面积的计算 (59)11.4.2中间仓库面积的计算 (60)11.4.3成品仓库面积的计算 (60)11.5车间运输量的确定 (60)12劳动组织及车间经济技术指标 (62)12.1车间劳动组织 (62)12.1.1劳动定额 (62)12.1.2劳动定员 (62)12.2车间技术经济指标 (63)12.2.1金属消耗 (63)12.2.2其它消耗 (63)12.3车间概算 (63)12.3.1车间设计指标 (63)12.3.2车间投资概算 (64)12.3.3成本概算 (64)12.3.4钢板销售收入 (64)12.3.5年利润及投资回收期 (64)13轧钢车间环境保护设计与废水处理 (64)13.1环保对车间设计的要求 (65)13.2环保的容与对策 (65)13.3热轧废水的治理 (66)13.3.1直接冷却废水的处理 (66)13.3.2间接冷却废水的处理 (66)13.3.3层流冷却废水的处理 (66)参考文献 (67)致谢 (69)1车间投资分析1.1本设计的目的和意义本设计是重钢1780热轧板带钢车间工艺设计。
轧钢车间设计3
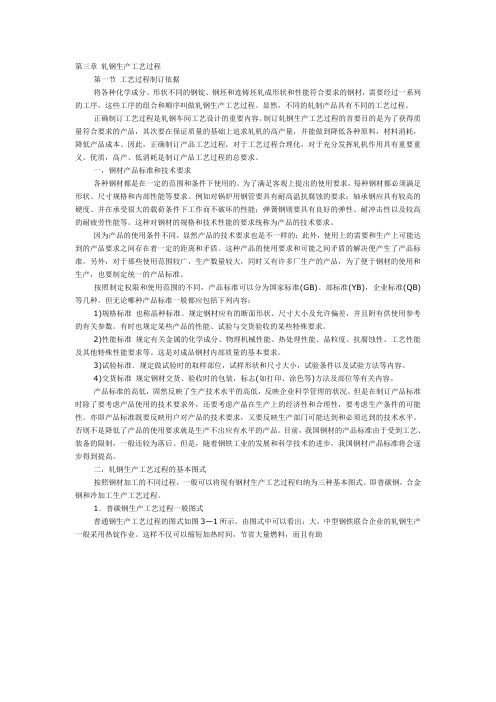
第三章轧钢生产工艺过程第一节工艺过程制订依据将各种化学成分、形状不同的钢锭、钢坯和连铸坯轧成形状和性能符合要求的钢材,需要经过一系列的工序,这些工序的组合和顺序叫做轧钢生产工艺过程。
显然,不同的轧制产品具有不同的工艺过程。
正确制订工艺过程是轧钢车间工艺设计的重要内容。
制订轧钢生产工艺过程的首要目的是为了获得质量符合要求的产品,其次要在保证质量的基础上追求轧机的高产量,并能做到降低各种原料,材料消耗,降低产品成本。
因此,正确制订产品工艺过程,对于工艺过程合理化,对于充分发挥轧机作用具有重要童义。
优质,高产、低消耗是制订产品工艺过程的总要求。
一,钢材产品标准和技术要求各种钢材都是在一定的范围和条件下使用的。
为了满足客观上提出的使用要求,每种钢材都必须满足形状、尺寸规格和内部性能等要求。
例如对锅炉用钢管要具有耐高温抗腐蚀的要求;轴承钢应具有较高的硬度、并在承受很大的载荷条件下工作而不破坏的性能;弹簧钢则要具有良好的弹性、耐冲击性以及较高的耐疲劳性能等。
这种对钢材的规格和技术性能的要求统称为产品的技术要求。
因为产品的使用条件不同,显然产品的技术要求也是不一样的;此外,使用上的需要和生产上可能达到的产品要求之间存在着一定的距离和矛盾。
这种产品的使用要求和可能之间矛盾的解决便产生了产品标准。
另外,对于那些使用范围较广,生产数量较大,同时又有许多厂生产的产品,为了便于钢材的使用和生产,也要制定统一的产品标准。
按照制定权限和使用范围的不同,产品标准可以分为国家标准(GB)、部标准(YB),企业标准(QB)等几种。
但无论哪种产品标准一般都应包括下列内容:1)规格标准也称晶种标准。
规定钢材应有的断面形状、尺寸大小及允许偏差,并且附有供使用参考的有关参数。
有时也规定某些产品的性能、试验与交货验收的某些特殊要求。
2)性能标准规定有关金属的化学成分、物理机械性能、热处理性能、晶粒度、抗腐蚀性、工艺性能及其他特殊性能要求等。
冷轧车间设计教案
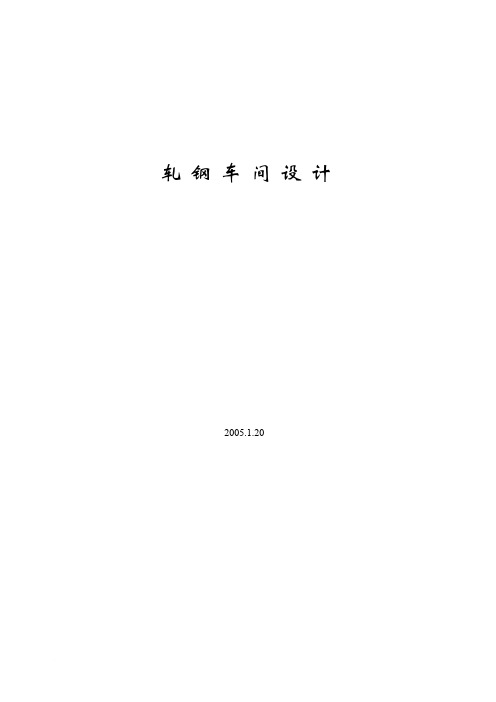
车间设计的基本程序
一般经过三个阶段:初步设计、技术设计、施工设计。但目前一般按:可 行性研究、初步设计、施工设计进行。 1.2.1 可行性研究 是对所提工程项目从各有关方面进行调查和综合论证、为拟建项目提供科 重点掌握可 学依据、从而保证所建项目能生产出高质低耗产品,以最少投入获得最大利润。 行性研究的 一. 可行性研究的主要内容 主要内容
重点理解: 产品方案、生 产方案的定 义、制定的方 法、目的。
600~1500 1000~6000 600~1500 卷
普通及深冲用低碳 0.2~0.3 钢带 镀锌钢板 镀锌钢带 镀锡钢板 镀锡钢带 合计 2.1.4
0.25~0.55 700~1500 1000~6000 0.25~0.55 700~1500 0.15~0.55 520~1050 0.15~0.55 520~1050 卷 400~1000 卷
教 内
案
用 容
纸 重点、要点
1. 车间设Βιβλιοθήκη 总论摘要:本章主要讲两个大问题,即车间设计(工艺设计)的主要内容和车间 设计的基本程序,通过对这两个问题的掌握使学生对轧钢车间有一个总体认识, 为毕业设计打基础。
1.1 车间设计的基本内容
1.1.1 轧钢车间设计的基本内容 通常由生产工艺设计、机械设备设计、厂房与基础设计、供水与排水,热力 (供气)与电力,通风与照明,运输等设计所组成。 其中车间生产工艺设计是整个轧钢车间设计的总体部分。 主要任务是根据设 计任务书,确定生产工艺过程,确定轧机组成,选择所需各种设备,画出车间工 艺平面布置图,最后对水、电、动力、热力、通风照明、厂房建筑等设计提出要 求。最后形成文件即车间设计说明书。 1.1.2 轧钢车间工艺设计(车间设计说明书)的主要内容 一. 总论(前言、综述、概况) (对该产品生产有一全面了解) 1. 车间年产量、产品品种规格等 2. 原材料、动力、燃料的来源及市场情况 3. 本设计与同类企业相比具有的特点 4. 目前建设的内容与远景规划 5. 车间的劳动组织、建设投资、经济与社会效益 6. 遗留问题与解决意见 7. 若扩建需说明现状、 扩建理由, 并提出充分利用现有设备及构筑物挖潜 革新的措施 8. 其它要说明的问题 注:对毕业设计综述应从以下几个方面论述、阐述: 1.品名称、品种、规格、用途、生产方法等 2.xxxx 产品生产的发展历史 (主要指生产方法重要的工艺变革及设备改进 等) 3.目前的生产状况、主要指生产该产品目前采用的新工艺、新设备等技术 生产展望,发展方向、对未来的预测(提出那里应改进,应向何方向发展)
年产360万吨热连轧车间工艺设计毕业论文
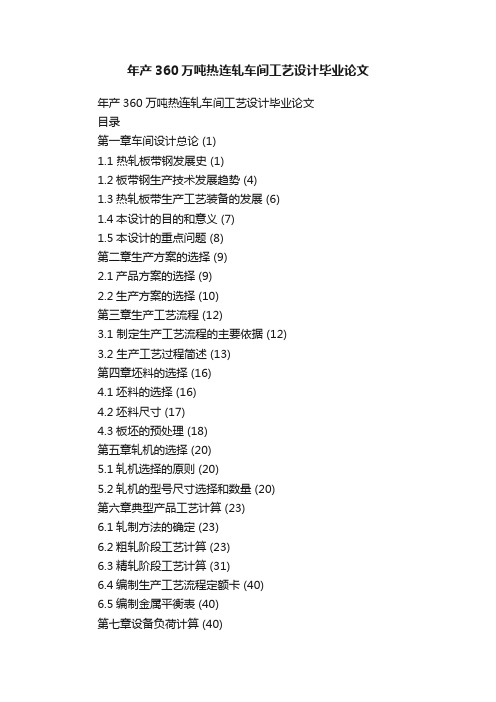
年产360万吨热连轧车间工艺设计毕业论文年产360万吨热连轧车间工艺设计毕业论文目录第一章车间设计总论 (1)1.1 热轧板带钢发展史 (1)1.2板带钢生产技术发展趋势 (4)1.3热轧板带生产工艺装备的发展 (6)1.4本设计的目的和意义 (7)1.5本设计的重点问题 (8)第二章生产方案的选择 (9)2.1产品方案的选择 (9)2.2生产方案的选择 (10)第三章生产工艺流程 (12)3.1 制定生产工艺流程的主要依据 (12)3.2 生产工艺过程简述 (13)第四章坯料的选择 (16)4.1坯料的选择 (16)4.2坯料尺寸 (17)4.3板坯的预处理 (18)第五章轧机的选择 (20)5.1轧机选择的原则 (20)5.2轧机的型号尺寸选择和数量 (20)第六章典型产品工艺计算 (23)6.1轧制方法的确定 (23)6.2粗轧阶段工艺计算 (23)6.3精轧阶段工艺计算 (31)6.4编制生产工艺流程定额卡 (40)6.5编制金属平衡表 (40)第七章设备负荷计算 (40)7.1工作制度与年工作台时的确定 (40) 7.2设备负荷能力计算 (40)7.3车间设备负荷率的确定 (40)7.4提高设备产量途径 (40)第八章电机能力校核 (43)8.1粗轧机电机能力校核 (46)8.2精轧机组电机能力的校核 (47)第九章轧辊强度的校核 (49)9.1粗轧机轧辊强度的校核 (49)9.2 F1~F5精轧机轧辊强度校核 (51) 9.3 F6~F7精轧机轧辊强度校核 (52) 第十章辅助设备的选择 (53)10.1加热炉的选择 (53)10.2起重运输设备的选择 (55)10.3除磷设备的选择 (56)10.4保温装置的选择 (57)10.5剪切设备的选择 (57)10.6冷却设备的选择 (58)10.7卷取机的选择 (58)第十一章车间平面布置和立面尺寸 (60) 11.1车间平面布置 (60)11.2仓库面积的确定 (62)11.3车间立面尺寸 (63)第十二章劳动组织与技术经济指标 (64) 12.1车间劳动组织 (64)12.2车间技术经济指标 (66)12.3投资概算 (66)12.4流动资金定额的概算 (68)12.5产品成本概算 (69)第十三章环境保护与综合利用 (72)13.1环保对车间设计的要求 (69)13.2环保的容与对策 (69)参考文献 (74)第一章车间设计总论1.1 热轧板带钢发展史热轧带钢是重要的钢材品种,对整个钢铁工业的技术进步和经济效益有着重要影响。
- 1、下载文档前请自行甄别文档内容的完整性,平台不提供额外的编辑、内容补充、找答案等附加服务。
- 2、"仅部分预览"的文档,不可在线预览部分如存在完整性等问题,可反馈申请退款(可完整预览的文档不适用该条件!)。
- 3、如文档侵犯您的权益,请联系客服反馈,我们会尽快为您处理(人工客服工作时间:9:00-18:30)。
3.2 金属平衡计算
是指生产车间在一定时期内(通常为一年)生产产品的收支情况,即投入
与产出情况。编制金属平衡表目的是确定出为完成年计划产量所需的投料量。
主要工作是计算产品的成材率、然后编制金属平衡表。
3.2.1 计算成品(材)率(金属消耗系数) 1. 成材率定义:指成品重量与投料之比的百分数,亦即一吨原料能够生
2.1 产品技术方案的编制
2.1.1 产品技术方案定义
产品技术方案是指所设计的工厂式车间拟生产的产品名称、品种、规格、 重点理解:
状态以及年计划产量。
产品技术方
产品技术方案一段在设计任务书中加以规定。产品技术方案是进行车间设
案、生产技术 方案的定义、
计的主要依据,根据产品技术方案可以确定生产技术方案(工艺)及选择设备。 制定的方法、
轧钢车间设计
2005.1.20
教案用纸
内
容
重点、要点
1. 车间设计总论
摘要:本章主要讲两个大问题,即车间设计(工艺设计)的主要内容和车间 设计的基本程序,通过对这两个问题的掌握使学生对轧钢车间有一个总体认识, 为毕业设计打基础。
1.1 车间设计的基本内容
1.1.1 轧钢车间设计的基本内容 通常由生产工艺设计、机械设备设计、厂房与基础设计、供水与排水,热力
学依据、从而保证所建工程能生产出高质低耗产品,以最少投入获得最大利润。
重点掌握可 行性研究的
一. 可行性研究的主要内容
主要内容
1. 市场销售情况研究:销售利润——建设规模及生产技术方案产品技术 方案
2. 经济效果研究:综合考虑分析投资回收率、近期、远期利润、原料政 策、投资风险程度等、资金(固定及流动资金)来源、利息、折旧等。
产出的合格产品重量的百分数。用公式表示为
A=
QW Q
100%
3.1
式中、A─成材率%
重点理解
金属平衡的 制定方法及 意义、影响 成品率的主 要因素
Q─投料量
W─损失料量
成品率的倒数就是金属消耗系数。
成品率是车间生产中的一项重要指标、它的高低反映了生产经管和工艺技
术设备等各方面的水平,直接影响企业的生产成本。因此产前必须对其进行正
成分、物化性能、机械力学性能、热处理性能、晶粒度、性能及其它特殊性能
等); 实验规范(取样部位、试样形状尺寸、实验条件及实验方法); 交货规
范(交货验收时的包装、标志、方法及部位等)。
2.2 生产技术方案的选择
2.2.1 生产技术方案定义
是指为完成任务书中规定的产品的生产任务而采取的生产方法。选择生产
1.3 车间设计的依据
车间设计任务书是依据,由有关上级部门下达。设计任务书的基本内容包 括:
1. 车间的生产规模、品种 2. 生产技术方案 3. 建厂地址,厂区范围,资源利用状况、各种材料供应、运输等 4. 要求达到的技术水平,经济及社会效益 5. 投资及劳动定员的控制数字。 6. 环保要求
2 生产技术方案与产品技术方案制定
金属平衡表。
表 3.1 冷轧薄板钢金属平衡表
序 钢种
号
坯料 规格 /mm
溶损 t%
消 耗 /% 烧损 切损 t%t%
工艺 损失 t%
年产 量 /万吨
成品 率 /%
需坯 量
/万吨
1
2
3
4 ∶
∶
4 设备选择
主要内容是确定出车间设备的种类、型式、结构、规格、数量及能力。包 括主要设备和辅助设备。对主要设备应在预选基础上进行必要的设备负荷计算。 对重要部件进行强度校核。对辅助设备可依经验选取不进行验算。设备选择一 般原则是:
技术方案时,应考虑设计规模、产品质量及技术经济指标的要求。
2.2.2 选择生产技术方案的依据
1. 金属与合金的品种、规格、状态及质量要求。
2. 年产量大小
3. 投资多少、建设速度、机械化的程度及将来发展。
4. 经济效果、工艺的成熟条件等。
2.2.3 钢材的生产技术方案
一. 板带钢生产:~0.2 薄带箔材,0.2~0.4 薄板,4~中厚板 1. 中厚板生产:单机四辊可逆式,双机架(2+4 或 4+4)可逆式;半连轧 连轧 2. 热轧薄板带钢:全连续式,半连续式、3/4 连续式 2.0~12mm→0.8mm 3. 冷轧带钢:单机可逆、连轧(3 机架 4 机架 5 机架 6 机架)0.1~2.0mm
包括金属消耗、燃料消耗、电耗、水耗、设备消耗 其它内容:参考文献
附表附图:车间平面布置图、孔型图、程序、外文翻译、专题撰写。
1.2 车间设计的基本程序
一般经过三个阶段:初步设计、技术设计、施工设计。但目前一般按:可
行性研究、初步设计、施工设计进行。
1.2.1 可行性研究
是对所提工程工程从各有关方面进行调查和综合论证、为拟建工程提供科
卷
1.0
1.0
合计
100
100
2.1.4 产品规范与技术要求
1. 技术要求:指产品的牌号、规格、表面质量及组织性能等方面的要求。 2. 产品规范分为国标(GB)部标(YB) 企标(QB),它是根据产品使
用上的技术要求和生产部门可能达到的技术水平而制定的。产品规范一般包括:
规格规范(产品牌号、形状、尺寸、表面质量及相关参数); 性能规范(化学
3. 工艺技术研究:工艺技术及设备 4. 工程条件研究:资源储量、原料来源、厂址气象、水文地址、交通运 输、水电动力、建筑材料、协作区域、文化生活设施、环保(三废处理)等, 进行综合分析比较。 二. 其它方面:劳动力来源、费用、人员培训、建设进度、工厂组织机构 体制可行性研究步骤 1. 调查研究收集资料:市场研究、相关企业调研。——调研报告。 2. 对资料进行客观分析、预测、判断、提出技术方案。 3. 技术方案比选:几个技术方案、各述利弊、分析比较、选择最佳技术 方案。 4. 编制可行性研究报告:工程名称;主办单位;主要技术负责人与经济 负责人;工程审批文件;承办企业的情况与条件;生产规划;物料供应;厂址 选择;技术与设备;建设资金;工程实施与进度;人员培训;经济效益评价等。 1.2.2 初步设计(技术设计) 按设计任务书给定的条件,在可行性研究的基础上进行的设计,最后形成 设计说明书。其中初步设计是基础设计,技术设计则更详尽严密。 1.2.3 施工设计 是设计的最后阶段,任务是为制造设备、厂房基础、其它构筑物的施工提 供依据。内容包括:车间的土建设计;设备施工图纸;各项施工文件及说明。
产品技术方案与计算产品确定后,按产品名称、合金牌号、状态、规格范
围、产品等列成表,如表 2.1 所示。
表 2.1 某冷连轧厂(车间)产品技术方案
产品名称
产 品 规 格 /mm
厚
宽
长
产量 所占比例
/万吨
/%
普通及深冲用低碳
钢板
0.2~0.3 600~1500 1000~6000 52.5
52.5
普通及深冲用低碳
6. 热送热装直轧
3 生产工艺流程制定及金属平衡计算
3.1 工艺流程制定
一. 热轧板带 连铸坯 →清理→(补偿)加热→轧制→冷却→精整→检查验收→入库 轧制分粗轧和精轧,冷却为层流冷却,精整主要包括矫直、横切、纵切。 二. 冷轧板带 热轧卷→柱矫→酸洗→切边→轧制→卷取→退火(退火分光亮退火和黑退 火)→平整→精整(矫直、纵切分条横切)→检查包装→入库 三. 热轧型钢 方坯(型坯)→清理→(补偿)加热→轧制→剪锯切→冷却→矫直 四. 无缝管材 圆坯→穿孔→轧制→均整→张力减径 →冷却→精整(矫直、切头尾、检查、 车丝)→包装→入库 五. 线材 方坯→ 加热 →轧制(粗中、预精、精轧)→冷却(水冷、风冷)→集卷 →打捆→检查→入库
4. 冷加工:冷轧 冷拔、冷旋压
四. 线材生产 以下成卷交货 一般断面为圆形
1. 横列式(二辊轧机)
2. 半连续式(三辊轧机)
3. 连续式(二辊+45°无钮式或二辊+Y 型无钮)(单线或三线)
2.3 轧钢生产中的先进生产工艺
1.连铸连轧紧凑式机组 2.以热代冷 3.低温大压下控轧超强控冷(轧机电位大、冷床超强冷却) 4.柔性轧制技术 5.连铸型管坯
2.1.2 编制产品技术方案依据
目的。
主要依据是:国民经济发展对产品的要求;产品在全国的平衡;建厂地区
的资源条件、自然条件、投资等。
2.1.3 计算(典型)产品的选择
计算产品定义:用做进行车间设计依据的产品。
选择依据:有代表性(产量大、有代表性);通过所以工序;要与实际相接
近,要保留一定的调整余量。
重点理解:
型、板、管、 线材的生产 中最佳技术 方案。
二. 型钢生产
1. 横列布置普通轧法
2. 万能轧法
3. 型钢连轧
4. 热及冷弯型钢
5. 挤压法
三. 管材生产
1. 热轧法:自动轧管机、连轧管机、两辊斜轧穿孔、三辊斜轧穿孔、菌
式穿孔机、张力减径机、皮格尔轧管、狭舍尔轧管机
2. 热挤压
3. 焊接:直缝焊、螺旋焊
➢ 要满足产品技术方案的要求,保证高质量的产品。 ➢ 要满足生产技术方案及生产工艺流程的要求。 ➢ 要注意设备的先进性和经济性的合理性(性价比)
等) 3.目前的生产状况、主要指生产该产品目前采用的新工艺、新设备等技术 生产展望,发展方向、对未来的预测(提出那里应改进,应向何方向发展)
深入理解车 间工艺设计 的步骤及其 内容。
二. 产品技术方案与生产技术方案制定 1. 产品技术方案编制:选择典型(计算)产品,编制产品技术方案 2. 生产技术方案选择制定:选择工艺技术方案 三. 生产工艺流程制定及金属平衡计算 1. 根据生产技术方案,以计算产品为依据列出工艺流程表 2. 依据工艺流程计算金属平衡,算出投料量 四. 设备选择(初选、精选、确定) 1. 主轧机选择、型式、吨位 2. 其它设备选择 五. 工艺参数计算 工艺规程制定与计算;温度制度;速度制度;张力制度;辊型制度;压力 计算;冷却制度 六. 设备校核 1. 主要设备校核:轧辊校核;电机校核;机架强度校核等 2. 辅助设备校核: 包括加热炉产量校核、剪切机能力校核、矫直机能力 校核 七. 车间年产量计算 1. 轧机工作图表绘制 2. 轧机小时产量计算 3. 轧机年产量计算 八. 车间平面布置 1. 金属流程线的确定 2. 设备组成及设备间距的确定 3. 仓库及辅助设施面积计算 4. 厂房设计:车间跨距、柱距、总长度、轨顶标高及总面积 5. 内部运输 6. 其它指标:通风、采暖、电源 7. 绘制车间平面布置图 九. 各项技术经济指标