轧钢车间设计
【完整版】轧钢车间主体工程施工组织设计

山东莱钢永锋钢铁有限公司轧钢车间主体工程施工组织设计中国十三冶山东分公司2002. 6. 6一、工程概况二、组织机构三、施工准备四、进度网络计划五、主要施工方法5.1 土方工程5.2钢筋砼工程5.3钢结构制作工程5.4钢结构安装工程5.5围护结构工程六、质量保证措施七、安全文明施工措施八、冬雨季施工措施一、工程概况本工程系大型冶金建筑安装工程,建筑面积23668 〃,施工工期计划为4个月完成车间主体及车间内设备基础及地面的施工(2002年10月18 日),我们据此安排了施工网络计划,结合我公司多年来承担类似工程的施工经验和采取一系列有效措施,可以保证按时建成。
本工程任务重、工期紧、质量要求高。
在整个施工过程中,我们将认真贯彻IS09002标准及公司质量方针(即:管理科学、质量第一;信守合同、顾客满意。
),确保按期交付生产。
钢结构制作安装与土建基础施工同时施工,钢结构安装与车间封闭交叉作业,充分利用车间平面、空间和时间,组织平行流水和立体交叉作业,按总网络计划组织施工。
最大限度地利用机械化的优势,缩短施工工期。
1.工程范围1.1 土建施工:1.1.1轧钢车间柱基础、设备基础。
1.1.2车间地面及1.2m围墙砌体施工1.2钢结构制作安装:1.2.1屋架系统、钢吊梁系统、车间钢柱、围护系统制作安装。
1.2.2墙皮、屋面的安装。
二、施工组织管理机构见附图一:三、施工进度计划网络见附图二:四、施工准备4.1三通一平轧钢车间的三通一平工作在开工前必须基本结束,水、电及道路基本形成,具备进场条件。
4.2生产、大临设施4.2.1砼搅拌站拟建二座30m ;大面积回填土施工,米用土方车运土,人工配合推土机整平,压路机压实。
小面积回填土施工,采用人工运土、整平,蛙式打夯机夯实。
基础深度超过6m,要做基坑支护。
基础较深时,基础四周卸荷,卸荷宽度和深度均为4~ 5m如果基础很深时,如10m左右,则采用内支撑,基坑深度小于6m时,不作支护。
年产万吨热轧带钢车间设计
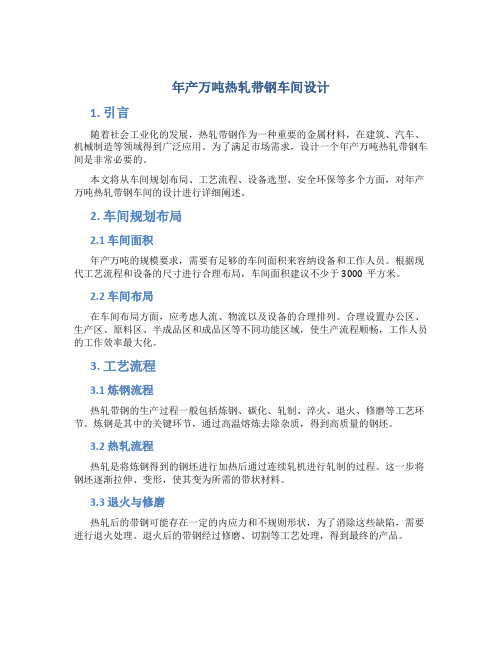
年产万吨热轧带钢车间设计1. 引言随着社会工业化的发展,热轧带钢作为一种重要的金属材料,在建筑、汽车、机械制造等领域得到广泛应用。
为了满足市场需求,设计一个年产万吨热轧带钢车间是非常必要的。
本文将从车间规划布局、工艺流程、设备选型、安全环保等多个方面,对年产万吨热轧带钢车间的设计进行详细阐述。
2. 车间规划布局2.1 车间面积年产万吨的规模要求,需要有足够的车间面积来容纳设备和工作人员。
根据现代工艺流程和设备的尺寸进行合理布局,车间面积建议不少于3000平方米。
2.2 车间布局在车间布局方面,应考虑人流、物流以及设备的合理排列。
合理设置办公区、生产区、原料区、半成品区和成品区等不同功能区域,使生产流程顺畅,工作人员的工作效率最大化。
3. 工艺流程3.1 炼钢流程热轧带钢的生产过程一般包括炼钢、碳化、轧制、淬火、退火、修磨等工艺环节。
炼钢是其中的关键环节,通过高温熔炼去除杂质,得到高质量的钢坯。
3.2 热轧流程热轧是将炼钢得到的钢坯进行加热后通过连续轧机进行轧制的过程。
这一步将钢坯逐渐拉伸、变形,使其变为所需的带状材料。
3.3 退火与修磨热轧后的带钢可能存在一定的内应力和不规则形状,为了消除这些缺陷,需要进行退火处理。
退火后的带钢经过修磨、切割等工艺处理,得到最终的产品。
4. 设备选型4.1 炼钢设备炼钢设备是热轧带钢车间中的核心设备,包括炉子、转炉、炼钢机等。
选购时应考虑设备的稳定性、生产能力以及能耗方面的因素。
4.2 轧机设备轧机设备是热轧过程中的关键设备,主要包括脱碳设备、轧机机组和辊道设备等。
选型时需综合考虑轧制能力、稳定性以及安全工作性能。
4.3 退火设备退火设备用于对经过轧制后的钢带进行退火处理,消除内应力和恢复材料的塑性。
选择设备时需考虑工艺要求、退火温度和速度的控制以及能耗方面的因素。
5. 安全环保在车间设计中,安全环保是至关重要的。
应设计合理的消防设施,安装可靠的烟雾和气体检测系统,确保生产过程中的安全。
热轧带钢生产车间布置设计分析

热轧带钢生产车间布置设计分析热轧带钢简介以板坯或钢锭为原料用热轧方式生产各种中厚钢板、薄钢板和带钢的轧钢车间设计。
热轧板带钢车间设计范围包括中厚板车间设计、连续热轧宽带钢车间设计、施特克尔(炉卷)带钢轧钢车间设计和热轧窄带钢车间设计。
除了以上四类板带轧钢车间外,尚有叠轧薄板车间和行星轧板车间。
工艺流程热轧宽带钢主要生产工艺流程是板坯经加热后由粗轧机组及精轧机组制成带钢。
从精轧最后一架轧机出来的热钢带通过层流冷却到设定温度,由卷取机卷成钢带卷,冷却后的钢带卷,根据用户的不同需求,经过不同的精整作业线加工而成为钢板、平整卷及纵切钢带产品的过程。
设备构成主体、加热炉、推钢机、出钢机、粗轧机组(四机架)、飞剪、精轧机组(七机架连轧)、卷取机、吊车、精整机组(开卷机、矫直机、剪切机、张力卷取机等)。
在进行车间设计时主要是轧机型式和轧机组成的选择,同时从设备的可靠性、产品质量、维修方便、设备结构、外形和机组重量等因素进行比较和选择。
主要轧钢机有中厚钢板轧机、热轧宽带钢轧机、施特克尔(炉卷)带钢轧机和热轧窄带钢轧机。
(1)中厚钢板轧机。
有二辊式、三辊劳特式、四辊式。
轧机布置型式主要有单机架、双机架型式。
现代的中厚板车间设计均采用四辊式轧机,按产品和产量的不同选用单机架或双机架组成,最佳型式是粗轧机和精轧机,均为四辊轧机并顺列布置。
(2)热轧宽带钢轧机。
指辊身长度不小于1000mm的热轧带钢轧机,世界上建设最多的为1500~1800mm和2000~2300mm热轧带钢轧机,最大的达2690mm。
按粗轧机的型式和组成有半连续式、3/4连续式和连续式三种热轧宽带钢轧机。
(3)施特克尔带钢轧机。
主要用于轧制不锈钢、硅钢等难变形金属。
该轧机的特点是在轧机入口和出口设有带卷筒的加热保温炉,用以保持带钢轧制温度,因此在中国称炉卷轧机。
现代的施特克尔带钢车间,一般由一架四辊式可逆式万能粗轧机和一架四辊可逆式精轧机组成。
轧机后设有带钢冷却设备、卷取机和钢板剪切设备。
轧钢车间设计

车间设计任务书是依据,由有关上级部门下达。设计任务书的基本内容包 括:
1. 车间的生产规模、品种 2. 生产方案 3. 建厂地址,厂区范围,资源利用状况、各种材料供应、运输等 4. 要求达到的技术水平,经济及社会效益 5. 投资及劳动定员的控制数字。 6. 环保要求
6
2 生产方案与产品方案制定
8
一. 板带钢生产:~0.2 薄带箔材,0.2~0.4 薄板,4~中厚板 1. 中厚板生产:单机四辊可逆式,双机架(2+4 或 4+4)可逆式;半连 轧连轧 2. 热轧薄板带钢:全连续式,半连续式、3/4 连续式 2.0~12mm→0.8mm 3. 冷轧带钢:单机可逆、连轧(3 机架 4 机架 5 机架 6 机架)0.1~2.0mm 二. 型钢生产 1. 横列布置普通轧法 2. 万能轧法 3. 型钢连轧 4. 热及冷弯型钢 5. 挤压法 三. 管材生产 1. 热轧法:自动轧管机、连轧管机、两辊斜轧穿孔、三辊斜轧穿孔、菌 式穿孔机、张力减径机、皮格尔轧管、狭舍尔轧管机 2. 热挤压 3. 焊接:直缝焊、螺旋焊 4. 冷加工:冷轧 冷拔、冷旋压 四. 线材生产 以下成卷交货 一般断面为圆形 1. 横列式(二辊轧机) 2. 半连续式(三辊轧机) 3. 连续式(二辊+45°无钮式或二辊+Y 型无钮)(单线或三线)
影响产品的产量、质量,因此选择轧机时应以生产方案和产品方案为依据进行
52.5
普通及深冲用低碳
0.2~0.3 600~1500
卷
钢带
22.5 22.5
7
镀锌钢板
0.25~0.55 700~1500 1000~6000 13.5 13.5
镀锌钢带
0.25~0.55 700~1500
热轧H型钢轧钢车间设计

热轧H型钢轧钢车间设计(design of hot H-beam mill)以连铸坯、热轧坯为原料,经加热和万能轧机轧制,生产热轧H型钢产品的车间设计。
H型钢过去称为宽边工字钢,属于经济断面型钢。
它与工字钢相比,其断面特点是翼缘(腿)可更宽、腹板(腰)可更高,而壁较薄;在相同断面面积时,H型钢的截面抵抗矩、惯性矩等力学性能都比工字钢高,可获得优良的抗弯能力和稳定性;腿部内外侧平行,呈直角,故拼装连接方便;形状美观。
H型钢主要用于制作高层民用建筑的构件,工业厂房的梁、柱和桩,桥梁钢结构件,重型车辆桥架及各种机械的构件和机座等。
H型钢用在建筑结构上可减轻重量30%~40%,做拼装组合构件可减少焊接、铆接工作量达25%。
在工业发达国家,目前热轧H型钢产量约占热轧钢材产量的2%~6%,占型钢产量的30%~60%。
H型钢产品按翼缘宽度分为宽翼缘H型钢(HK)、窄翼缘H型钢(HZ)和H型钢桩(HU)三大类。
中国国家标准规定的H型钢产品规格范围见表1。
目前国外生产的H型钢断面最大高度达1200mm,最大翼缘宽度达530mm。
H型钢的材质,主要有碳素钢和低合金结构钢,少量为含低镍、低铬的低温用钢和海洋用钢。
热轧H型钢轧钢车间设计的原则和方法见轧钢厂设计。
简史 1867年德国哈哥•萨克(Huge Sack)发明带立辊的万能轧机,1901年卢森堡阿尔贝德一迪弗当日(Arbed-Differdange)厂建成了由万能机架和轧边机架组成的格雷式(Grey)H型钢轧机,德国和美国等国也相继建成了此类轧机,但在20世纪前半个世纪建成甚少。
直至20世纪60年代,由于建筑业的高速发展,市场对H型钢的需求量增加,加快了H型钢轧机的发展,特别是轧钢技术和电控技术的进步,使其向多品种、自动化、中型轧机的连续化方向发展。
1985年联邦德国西马克(SMS)公司开发了由两架万能机架和一架二辊轧边机架组成的串列式万能轧机,轧出了H型钢,使串列式万能轧机向经济型方向发展。
线材轧钢工程车间平面布置

线材轧钢工程车间平面布置
一、一般规定
1、总图布置应考虑轧钢车间与上游连铸车间的衔接,宜采用辊道运输的方式输送连铸坯,紧凑布置。
2、车间工艺布置应满足生产工艺要求,流程畅通,布局合理,操作方便;对预留发展的车间,应预留设备、设施的布置场地。
二、主车间布置
1、设备布置宜紧凑,应留有设备安装、操作、检修空间和安全通道等。
2、主轧线设备应采用高架平台布置。
高架平台布置相对于车间±0.0m地坪,平台标高宜为+5.0m。
平台下应用于设置液压润滑站等设施。
3、主厂房起重机的轨面标高及起重量应按设备高度、设备检修要求、坯料成品的堆放能力和运输条件等确定。
起重机数量应根据车间生产能力确定。
4、单线轧制的线材车间主轧跨跨度宜为24m,双线轧制的线材车间主轧跨跨度宜为27m~30m。
5、坯料库、中间库和成品库的面积应保证正常生产需要。
坯料库存放量根据车间的热装热送率宜为2d~5d,没有全厂性成品仓库的线材车间,成品库存放量不宜少于7d。
三、辅助设施布置
1、主电室宜布置在轧机传动侧,生产线较长或设施分散时,可分区布置若干电气室。
2、轧辊间应靠近主轧跨,宜布置在轧机操作侧。
3、水处理设施应靠近车间集中布置。
中厚板轧钢车间设计

中厚板轧钢车间设计创建时间:2008-08-02中厚板轧钢车间设计 (design of plate mill)以板坯或扁锭为原料,经加热轧制生产中厚钢板的车间设计。
中国规定,钢板厚度大于4~20mm 的为中板,厚度大于20~60mm的为厚板,厚度大于60mm的为特厚板,统称为中厚板,中厚钢板主要用于造船、建筑、机器制造、交通运输以及军事工业等部门,还可用作制造螺旋焊管,UOE焊管与焊接钢梁的原料。
在工业发达国家,中厚钢板的产量占钢材总产量的10%~20%。
厚度为4~25.4mm的中厚钢板也可以在带钢热轧机上生产。
车间设计的原则及方法见轧钢厂设计。
简史 18世纪初,西欧开始用二辊轧机轧制出小块中厚钢板。
1854年欧洲建成用蒸汽机传动的二辊可逆式中厚板轧机。
1864年美国建成三辊劳特式中厚板轧机。
1891年美国建成世界上第一台四辊可逆式中厚板轧机,1918年美国又建成主要生产装甲钢板,其辊身长5000mm以上的宽厚板轧机。
以后,世界上又陆续出现了双机架、半连续式、连续式中厚板轧机。
20世纪70年代是中厚板车间建设得最多的时期,不少轧机是4000~5500mm的双机架宽厚板轧机。
1871年中国福州船政局已开始轧制造船板,1907年汉冶萍公司建设了2440mm中板轧机。
1936年在鞍山建成了第一套2300mm三辊劳特式中板轧机。
1958年及1966年鞍山钢铁公司和武汉钢铁公司分别建成了2800mm中厚板轧机,其粗轧机为二辊式、精轧机为四辊式。
1978年设计建成了舞阳钢铁公司4200mm宽厚板车间,1990年上海第三钢铁厂的4200/3300mm厚板车间投产。
坯料选择有扁锭、初轧板坯、连铸板坯和锻坯。
在满足轧制压缩比的条件下,尽可能采用连铸板坯为原料。
某些特殊钢种,根据需要采用锻坯。
设计规模和产品方案设计规模主要取决于轧机和辅机性能、设备组成、市场需求和坯料条件等。
轧机尺寸、组成与设计规模的关系见表1。
轧钢车间设计3
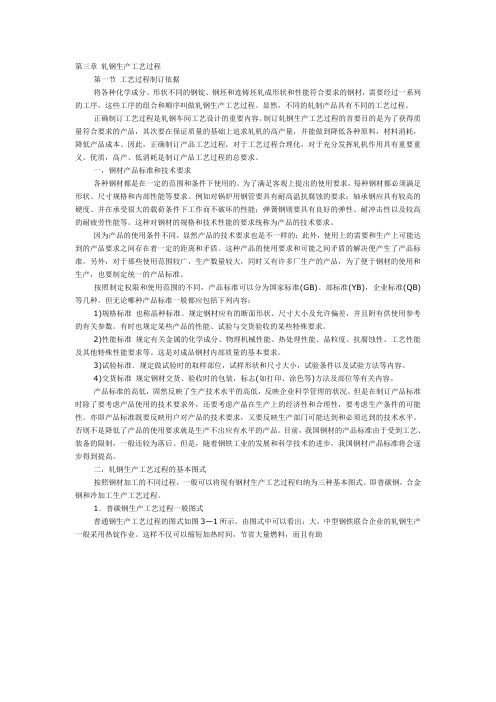
第三章轧钢生产工艺过程第一节工艺过程制订依据将各种化学成分、形状不同的钢锭、钢坯和连铸坯轧成形状和性能符合要求的钢材,需要经过一系列的工序,这些工序的组合和顺序叫做轧钢生产工艺过程。
显然,不同的轧制产品具有不同的工艺过程。
正确制订工艺过程是轧钢车间工艺设计的重要内容。
制订轧钢生产工艺过程的首要目的是为了获得质量符合要求的产品,其次要在保证质量的基础上追求轧机的高产量,并能做到降低各种原料,材料消耗,降低产品成本。
因此,正确制订产品工艺过程,对于工艺过程合理化,对于充分发挥轧机作用具有重要童义。
优质,高产、低消耗是制订产品工艺过程的总要求。
一,钢材产品标准和技术要求各种钢材都是在一定的范围和条件下使用的。
为了满足客观上提出的使用要求,每种钢材都必须满足形状、尺寸规格和内部性能等要求。
例如对锅炉用钢管要具有耐高温抗腐蚀的要求;轴承钢应具有较高的硬度、并在承受很大的载荷条件下工作而不破坏的性能;弹簧钢则要具有良好的弹性、耐冲击性以及较高的耐疲劳性能等。
这种对钢材的规格和技术性能的要求统称为产品的技术要求。
因为产品的使用条件不同,显然产品的技术要求也是不一样的;此外,使用上的需要和生产上可能达到的产品要求之间存在着一定的距离和矛盾。
这种产品的使用要求和可能之间矛盾的解决便产生了产品标准。
另外,对于那些使用范围较广,生产数量较大,同时又有许多厂生产的产品,为了便于钢材的使用和生产,也要制定统一的产品标准。
按照制定权限和使用范围的不同,产品标准可以分为国家标准(GB)、部标准(YB),企业标准(QB)等几种。
但无论哪种产品标准一般都应包括下列内容:1)规格标准也称晶种标准。
规定钢材应有的断面形状、尺寸大小及允许偏差,并且附有供使用参考的有关参数。
有时也规定某些产品的性能、试验与交货验收的某些特殊要求。
2)性能标准规定有关金属的化学成分、物理机械性能、热处理性能、晶粒度、抗腐蚀性、工艺性能及其他特殊性能要求等。
- 1、下载文档前请自行甄别文档内容的完整性,平台不提供额外的编辑、内容补充、找答案等附加服务。
- 2、"仅部分预览"的文档,不可在线预览部分如存在完整性等问题,可反馈申请退款(可完整预览的文档不适用该条件!)。
- 3、如文档侵犯您的权益,请联系客服反馈,我们会尽快为您处理(人工客服工作时间:9:00-18:30)。
2.1 产品方案的编制
2.1.1 产品方案定义 产品方案是指所设计的工厂式车间拟生产的产品名称、品种、规格、状态
以及年计划产量。 产品方案一段在设计任务书中加以规定。产品方案是进行车间设计的主要
依据,根据产品方案可以确定生产方案(工艺)及选择设备。 2.1.2 编制产品方案依据
重点理解: 产品方案、生 产方案的定 义、制定的方 法、目的。
等) 3.目前的生产状况、主要指生产该产品目前采用的新工艺、新设备等技术 生产展望,发展方向、对未来的预测(提出那里应改进,应向何方向发展)
深入理解车 间工艺设计 的步骤及其 内容。
2
二. 产品方案与生产方案制定 1. 产品方案编制:选择典型(计算)产品,编制产品方案 2. 生产方案选择制定:选择工艺方案 三. 生产工艺流程制定及金属平衡计算 1. 根据生产方案,以计算产品为依据列出工艺流程表 2. 依据工艺流程计算金属平衡,算出投料量 四. 设备选择(初选、精选、确定) 1. 主轧机选择、型式、吨位 2. 其它设备选择 五. 工艺参数计算 工艺规程制定与计算;温度制度;速度制度;张力制度;辊型制度;压力 计算;冷却制度 六. 设备校核 1. 主要设备校核:轧辊校核;电机校核;机架强度校核等 2. 辅助设备校核: 包括加热炉产量校核、剪切机能力校核、矫直机能力 校核 七. 车间年产量计算 1. 轧机工作图表绘制 2. 轧机小时产量计算 3. 轧机年产量计算 八. 车间平面布置 1. 金属流程线的确定 2. 设备组成及设备间距的确定 3. 仓库及辅助设施面积计算 4. 厂房设计:车间跨距、柱距、总长度、轨顶标高及总面积 5. 内部运输 6. 其它指标:通风、采暖、电源 7. 绘制车间平面布置图 九. 各项技术经济指标
能够生产出的合格产品重量的百分数。用公式表示为
A=
QW Q
100%
3.1
式中、A─成材率%
重点理解
金属平衡的 制定方法及 意义、影响 成品率的主 要因素
Q─投料量
W─损失料量
成品率的倒数就是金属消耗系数。
成品率是车间生产中的一项重要指标、它的高低反映了生产管理和工艺技
术设备等各方面的水平,直接影响企业的生产成本。因此产前必须对其进行正
3.2.3 编制金属平衡表 将钢种、各项消耗指标、年产量、成材率、需坯量列在以下表格中,即为
金属平衡表。
表 3.1 冷轧薄板钢金属平衡表
序 钢种
号
坯料 规格 /mm
溶损 t%
消 耗 /% 烧损 切损 t%t%
工艺 损失 t%
年产 量 /万吨
成品 率 /%
需坯 量
/万吨
1
2
3
4 ∶
∶
9
4 设备选择
主要内容是确定出车间设备的种类、型式、结构、规格、数量及能力。包
0.25~0.55 700~1500 1000~6000 13.5
13.5
镀锌钢带
0.25~0.55 700~1500
卷
1.5
1.5
镀锡钢板
0.15~0.55 520~1050 400~1000 9.0
9.0
镀锡钢带
0.15~0.55 520~1050
卷
1.0
1.0
合计
100
100
2.1.4 产品标准与技术要求
晶粒度、性能及其它特殊性能等); 实验标准(取样部位、试样形状尺
寸、试验条件及实验方法); 交货标准(交货验收时的包装、标志、方
法及部位等)。
5
2.2 生产方案的选择
2.2.1 生产方案定义
是指为完成任务书中规定的产品的生产任务而采取的生产方法。选择生产
方案时,应考虑设计规模、产品质量及技术经济指标的要求。
2.2.2 选择生产方案的依据
1.金属与合金的品种、规格、状态及质量要求。
2.年产量大小
3.投资多少、建设速度、机械化的程度及将来发展。 4.经济效果、工艺的成熟条件等。 2.2.3 钢材的生产方案
一. 板带钢生产:~0.2 薄带箔材,0.2~0.4 薄板,4~中厚 板 1. 中厚板生产:单机四辊可逆式,双机架(2+4 或 4+4)可逆式;半连
学依据、从而保证所建项目能生产出高质低耗产品,以最少投入获得最大利润。
重点掌握可 行性研究的
一. 可行性研究的主要内容
主要内容
3
1. 市场销售情况研究:销售利润——建设规模及生产方案产品方案 2. 经济效果研究:综合考虑分析投资回收率、近期、远期利润、原料政 策、投资风险程度等、资金(固定及流动资金)来源、利息、折旧等。 3. 工艺技术研究:工艺技术及设备 4. 工程条件研究:资源储量、原料来源、厂址气象、水文地址、交通运 输、水电动力、建筑材料、协作区域、文化生活设施、环保(三废处理)等, 进行综合分析比较。 二. 其它方面:劳动力来源、费用、人员培训、建设进度、工厂组织机构 体制可行性研究步骤 1. 调查研究收集资料:市场研究、相关企业调研。——调研报告。 2. 对资料进行客观分析、预测、判断、提出方案。 3. 方案比选:几个方案、各述利弊、分析比较、选择最佳方案。 4. 编制可行性研究报告:项目名称;主办单位;主要技术负责人与经济 负责人;项目审批文件;承办企业的情况与条件;生产规划;物料供应;厂址 选择;技术与设备;建设资金;项目实施与进度;人员培训;经济效益评价等。 1.2.2 初步设计(技术设计) 按设计任务书给定的条件,在可行性研究的基础上进行的设计,最后形成 设计说明书。其中初步设计是基础设计,技术设计则更详尽严密。 1.2.3 施工设计 是设计的最后阶段,任务是为制造设备、厂房基础、其它构筑物的施工提 供依据。内容包括:车间的土建设计;设备施工图纸;各项施工文件及说明。
产品等列成表,如表 2.1 所示。
表 2.1 某冷连轧厂(车间)产品方案
产品名称
产 品 规 格 /mm
厚
宽
长
产量 所占比例
/万吨
/%
普通及深冲用低碳
钢板
0.2~0.3 600~1500 1000~6000 52.5
52.5
普通及深冲用低碳
钢带
0.2~0.3 600~1500
卷
பைடு நூலகம்
22.5
22.5
镀锌钢板
包括金属消耗、燃料消耗、电耗、水耗、设备消耗 其它内容:参考文献
附表附图:车间平面布置图、孔型图、程序、外文翻译、专题撰写。
1.2 车间设计的基本程序
一般经过三个阶段:初步设计、技术设计、施工设计。但目前一般按:可
行性研究、初步设计、施工设计进行。
1.2.1 可行性研究
是对所提工程项目从各有关方面进行调查和综合论证、为拟建项目提供科
确估算。
3.2.2 影响成品率的主要因素
凡是造成废品的生产及销售因素都是影响成品率的因素。
(1) 烧损:氧化烧损 1~5% 一般表面积愈大、加热时间越长、
温度越高、气氛氧化性越强则烧损越大。
(2) 溶损:在酸、碱或化学处理等过程中的损失。0.1~1.0%
(3) 几何损失:切头、切尾、切边残屑消理(车皮、锯切、铲)
3.2 金属平衡计算
是指生产车间在一定时期内(通常为一年)生产产品的收支情况,即投入
与产出情况。编制金属平衡表目的是确定出为完成年计划产量所需的投料量。
主要工作是计算产品的成材率、然后编制金属平衡表。
3.2.1 计算成品(材)率(金属消耗系数) 1. 成材率定义:指成品重量与投料之比的百分数,亦即一吨原料
一. 总论(前言、综述、概况)(对该产品生产有一全面了解) 1. 车间年产量、产品品种规格等 2. 原材料、动力、燃料的来源及市场情况 3. 本设计与同类企业相比具有的特点 4. 目前建设的内容与远景规划 5. 车间的劳动组织、建设投资、经济与社会效益 6. 遗留问题与解决意见 7. 若扩建需说明现状、扩建理由,并提出充分利用现有设备及构筑物挖潜 革新的措施 8. 其它要说明的问题 注:对毕业设计综述应从以下几个方面论述、阐述: 1.品名称、品种、规格、用途、生产方法等 2.xxxx 产品生产的发展历史(主要指生产方法重要的工艺变革及设备改进
5. 挤压法
三. 管材生产
1. 热轧法:自动轧管机、连轧管机、两辊斜轧穿孔、三辊斜轧穿孔、
菌式穿孔机、张力减径机、皮格尔轧管、狭舍尔轧管机
2. 热挤压
3. 焊接:直缝焊、螺旋焊
4. 冷加工:冷轧 冷拔、冷旋压
四. 线材生产 以下成卷交货 一般断面为圆形
1. 横列式(二辊轧机)
2. 半连续式(三辊轧机)
8
1~10% (4) 工艺损失:技术损失、各工序由于设备、工具、技术操作及
表面介质等问题造成的质量不合要求的产品。如诈漏、轧断、轧卡、卡
钢、 超差、浪形、轧扭、腰薄、耳子、性能不合格等。
由于成品率直接影响生产成本,因此实际生产中应尽可能采取措施提高成
材率,主要应从工艺、设备、原料、管理(操作)四个方面入手。
重点理解:
型、板、管、 线材的生产 中最佳方 案。
轧连轧
2. 热轧薄板带钢:全连续式,半连续式、3/4 连续式 2.0~12mm→0.8mm
3. 冷轧带钢:单机可逆、连轧(3 机架 4 机架 5 机架 6 机架)0.1~2.0mm
二. 型钢生产
1. 横列布置普通轧法
2. 万能轧法
3. 型钢连轧
4. 热及冷弯型钢
轧钢车间设计
课程教案
井玉安 2005.1.20
1
教案用纸
内
容
重点、要点
1. 车间设计总论
摘要:本章主要讲两个大问题,即车间设计(工艺设计)的主要内容和车间 设计的基本程序,通过对这两个问题的掌握使学生对轧钢车间有一个总体认识, 为毕业设计打基础。
1.1 车间设计的基本内容