轧钢生产工艺简介
轧钢工艺简介ppt课件
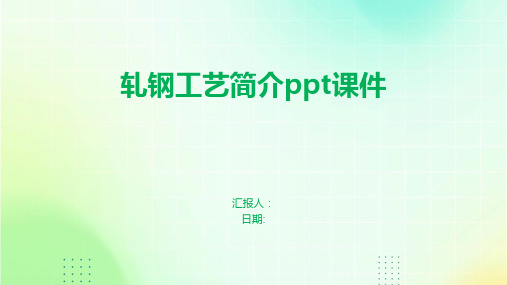
采用隔声、吸声等措施,降低噪声对周围环境的影响。
绿色轧钢工艺的发展趋势
短流程生产
采用短流程生产方式,减少中间环节,降低能源消耗和环境污染 。
智能化控制
引入智能化控制系统,实现生产过程的自动化和智能化,提高生产 效率和环保性能。
低碳环保
积极推广低碳环保技术,如新能源、清洁能源等,降低碳排放,实 现绿色可持续发展。
精轧
对粗轧后的钢材进行精细轧制,使 其形状、尺寸更加符合要求。
尺寸控制
通过调整轧制参数和控制冷却速度 ,控制钢材的厚度、宽度和长度等 尺寸。
精整
矫直
将轧制后的钢材进行矫直,消除 应力并改善其平直度。
表面处理
根据需要,对钢材表面进行抛光 、涂层或镀层等处理。
分级和包装
根据钢材的质量、尺寸和用途进 行分级,并进行包装,便于后续
纵轧机
主要用于加工板材和带材,其优点是产量高、品 种多。
斜轧机
主要用于加工锥形断面的金属材料,其优点是能 够实现高速、高效的生产。
轧机的工作原理
金属材料进入轧机后,受到轧 辊的压缩和变形,使其形状和 尺寸发生变化。
通过调整轧辊之间的距离,可 以控制金属材料的变形程度, 从而达到所需的形状和尺寸。
在轧制过程中,还需对金属材 料进行冷却和润滑,以降低摩 擦和温度,提高产品质量。
挑战
随着全球市场竞争的加剧,轧钢工艺面临着节能减排、降低成本、提高产品质 量的挑战。同时,由于环保政策的加强,如何减少轧钢生产过程中的环境污染 和废弃物排放也成为亟待解决的问题。
新技术对轧钢工艺的影响与推动
新技术应用
数字化轧钢、智能制造、新材料技术等新技术的应用,使得轧钢生产过程更加高 效、精准和可控。例如,通过数字化技术,可以实现轧钢生产过程的实时监控和 优化控制,提高产品质量和生产效率。
轧钢生产工艺
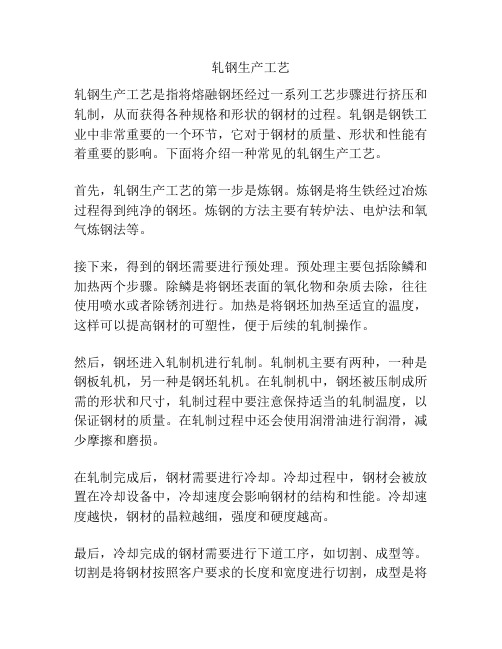
轧钢生产工艺
轧钢生产工艺是指将熔融钢坯经过一系列工艺步骤进行挤压和轧制,从而获得各种规格和形状的钢材的过程。
轧钢是钢铁工业中非常重要的一个环节,它对于钢材的质量、形状和性能有着重要的影响。
下面将介绍一种常见的轧钢生产工艺。
首先,轧钢生产工艺的第一步是炼钢。
炼钢是将生铁经过冶炼过程得到纯净的钢坯。
炼钢的方法主要有转炉法、电炉法和氧气炼钢法等。
接下来,得到的钢坯需要进行预处理。
预处理主要包括除鳞和加热两个步骤。
除鳞是将钢坯表面的氧化物和杂质去除,往往使用喷水或者除锈剂进行。
加热是将钢坯加热至适宜的温度,这样可以提高钢材的可塑性,便于后续的轧制操作。
然后,钢坯进入轧制机进行轧制。
轧制机主要有两种,一种是钢板轧机,另一种是钢坯轧机。
在轧制机中,钢坯被压制成所需的形状和尺寸,轧制过程中要注意保持适当的轧制温度,以保证钢材的质量。
在轧制过程中还会使用润滑油进行润滑,减少摩擦和磨损。
在轧制完成后,钢材需要进行冷却。
冷却过程中,钢材会被放置在冷却设备中,冷却速度会影响钢材的结构和性能。
冷却速度越快,钢材的晶粒越细,强度和硬度越高。
最后,冷却完成的钢材需要进行下道工序,如切割、成型等。
切割是将钢材按照客户要求的长度和宽度进行切割,成型是将
钢材制作成特定的形状,如角钢、型钢等。
综上所述,轧钢生产工艺主要包括炼钢、预处理、轧制、冷却和后续加工等步骤。
每个环节都需要严格控制工艺参数,以确保最终钢材的质量和性能。
随着技术的进步,现代轧钢生产工艺越来越高效和智能化,为产业发展带来了更多的便利和机遇。
轧钢的工艺流程

轧钢的工艺流程
轧钢是一种将钢坯通过一系列工艺步骤加工成各种规格钢材的生产过程。
下面是轧钢的典型工艺流程。
1. 炼钢:首先,将原料如铁矿石、废钢等投入高炉或电弧炉中进行冶炼,产生熔融的钢液。
2. 连铸:从炼钢炉中得到的钢液经过脱氧、温度调节等处理后,通过连铸机连续浇铸成钢坯,得到粗钢。
3. 精炼:将粗钢进行精炼,其中包括脱硫、脱磷、脱氮等工艺,以提高钢的质量。
4. 预热:在开始轧制之前,将钢坯进行预热,以提高钢坯的塑性和可加工性。
5. 轧制:将预热后的钢坯送入轧机,经过多次高压轧制、冷却和拉伸等工序,使钢坯逐渐减小断面,得到所需的钢材形状。
6. 酸洗:为了去除钢表面的氧化物和锈蚀物质,对轧制后的钢材进行酸洗。
7. 表面处理:根据需要,对钢材进行镀锌、镀铬、涂层等表面处理,以提高钢的耐腐蚀性能。
8. 成品检验:对生产的钢材进行各项检测,包括化学成分、力学性能、外观质量等,确保钢材符合相关标准和要求。
9. 包装和出厂:经过检验合格的钢材进行包装,并按要求进行存放和运输,最终出厂供应给客户使用。
以上是轧钢的典型工艺流程,不同钢材的生产过程可能会有所差异,具体工艺参数也会根据不同钢材的特性进行调整。
轧钢工艺过程
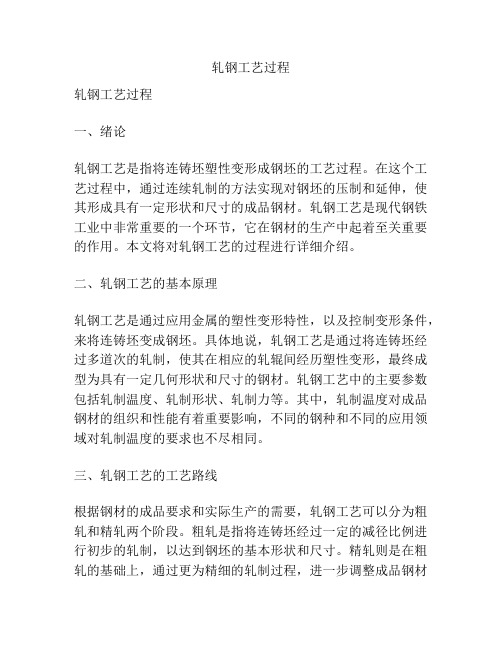
轧钢工艺过程轧钢工艺过程一、绪论轧钢工艺是指将连铸坯塑性变形成钢坯的工艺过程。
在这个工艺过程中,通过连续轧制的方法实现对钢坯的压制和延伸,使其形成具有一定形状和尺寸的成品钢材。
轧钢工艺是现代钢铁工业中非常重要的一个环节,它在钢材的生产中起着至关重要的作用。
本文将对轧钢工艺的过程进行详细介绍。
二、轧钢工艺的基本原理轧钢工艺是通过应用金属的塑性变形特性,以及控制变形条件,来将连铸坯变成钢坯。
具体地说,轧钢工艺是通过将连铸坯经过多道次的轧制,使其在相应的轧辊间经历塑性变形,最终成型为具有一定几何形状和尺寸的钢材。
轧钢工艺中的主要参数包括轧制温度、轧制形状、轧制力等。
其中,轧制温度对成品钢材的组织和性能有着重要影响,不同的钢种和不同的应用领域对轧制温度的要求也不尽相同。
三、轧钢工艺的工艺路线根据钢材的成品要求和实际生产的需要,轧钢工艺可以分为粗轧和精轧两个阶段。
粗轧是指将连铸坯经过一定的减径比例进行初步的轧制,以达到钢坯的基本形状和尺寸。
精轧则是在粗轧的基础上,通过更为精细的轧制过程,进一步调整成品钢材的形状和尺寸,并改善其组织和性能。
具体的轧钢工艺路线根据不同的产品和钢种有所差异,但一般都包括了传统的粗轧和精轧两个阶段。
四、粗轧工艺过程粗轧是轧钢工艺的第一个阶段,其目的是将连铸坯塑性变形成钢坯的初始形状和尺寸。
粗轧过程中采用的轧机一般为大型的热轧机、中宽带轧机等。
具体的粗轧工艺过程包括以下几个步骤:1. 进炉:将连铸坯送入粗轧轧机的加热炉中进行预热处理。
预热的目的是提高钢坯的塑性和表面质量,便于后续的轧制过程。
2. 加热:预热后的连铸坯由加热炉送入轧机的工作台。
工作台上的传动装置和轧辊开始运转,连铸坯在轧辊的压制下产生塑性变形。
同时,轧机通过喷水冷却系统对加热炉中的连铸坯进行降温。
3. 挤压:连铸坯经过轧机的上轧辊和下轧辊间的压制,实现了钢坯的初始塑性变形。
这一过程被称为挤压,其目的是将连铸坯轧制成大致规定形状和尺寸的钢坯。
1轧钢热轧冷轧工艺介绍

连铸机
结 晶 器
隧道式 感应加 加热炉 热炉
粗轧机 温度 控制器
精轧机
层流冷却 卷取机
摆动剪
除鳞箱
除鳞箱
飞剪
3.冷轧板带钢生产
1)冷轧的含义 金属学说法:加工温度低于该钢种在特定变形条件下的
再结晶温度的压力加工称为“冷加工”; 工业上的习惯:坯料事先不经过再加热的常温轧制过
程。
2)冷轧的工艺特点 (1)冷轧中的加工硬化; (2)冷轧中的工艺冷却和润滑; (3)冷轧中的张力轧制。
(3)中厚板生产的工艺流程
原料
加热
除鳞
轧制
冷矫
冷床
热矫
层流冷却
冷床
剪切
喷印
包装
轧制
中厚板的轧制过程大致可分为粗轧和精轧。
(1)全纵轧法 当板坯宽度大于或等于钢板宽度时,即可不用展宽而直接纵轧成
成品。 (2)横轧-纵轧法或综合轧制法
先进行横轧将板坯展宽至所需宽度以后再转90°进行纵轧完成。 (3)角轧-纵轧法
层流冷却
圆盘式 卷取机
③FTSRQ工艺(Flexible Thin Slab Rolling for Quality)
FTSRQ工艺后改为FTSC,称之为生产高质量产品的灵活性薄板坯轧制, 是由意大利达涅利公司开发出的又一种薄板坯连铸连轧工艺。
加拿大安大略省的阿尔戈马钢铁公司建成投产了产量为200万t/a的双流铸 机FTSR生产线。世界上已经建成7条。我国唐钢、本钢和通钢薄板坯连铸连轧 生产线即是采用该工艺。
2. 轧钢机
1)轧钢机的基本组成: 轧制钢材的设备称为轧钢机。
轧钢机由轧辊、工作机架、齿轮机座、联 接轴和联轴节、主电机等组成。
2) 轧钢机的分类:
轧钢工艺基础知识

轧钢工艺基础知识目录一、轧钢工艺概述 (2)1.1 轧钢定义及发展历程 (3)1.2 轧钢工艺分类及特点 (4)二、轧钢设备 (6)2.1 轧机设备 (7)2.2 辅助设备 (8)2.3 控制系统 (9)三、轧钢基本原理 (11)3.1 金属的塑性变形 (11)3.2 剪切应力与剪切力 (12)3.3 影响轧制过程的主要因素 (14)四、轧钢工艺流程 (15)4.1 钢的熔炼与铸造 (16)4.2 热轧工艺 (18)4.3 冷轧工艺 (19)4.4 后处理工艺 (21)五、轧制质量控制 (22)5.1 影响轧制质量的因素 (23)5.2 质量检测方法与标准 (24)六、轧钢安全生产与环保 (25)6.1 安全生产操作规程 (27)6.2 环保设施与要求 (28)七、轧钢工艺发展趋势 (29)7.1 新技术应用 (30)7.2 节能减排与可持续发展 (32)一、轧钢工艺概述轧钢工艺定义与目的:轧钢工艺是指通过旋转轧辊对加热后的钢坯进行压力加工,使其塑性变形,从而获得所需形状和尺寸的钢材。
其目的是提高钢材的力学性能和表面质量,满足不同的使用需求。
原料准备:包括铁水预处理、转炉冶炼、连铸或模铸等工序,以获取所需的钢坯。
钢坯加热:将钢坯加热至适宜的温度,以提高其塑性,便于后续的轧制过程。
轧制过程:在轧机的作用下,通过轧辊的旋转和挤压,使钢坯逐渐变形,达到所需的形状和尺寸。
产品后处理:包括冷却、矫直、切割、热处理等工序,以提高钢材的性能和表面质量。
轧钢工艺的重要性:轧钢工艺是钢铁生产过程中的关键环节,对于提高钢材质量、降低能耗、提高生产效率具有重要意义。
掌握轧钢工艺基础知识对于从事钢铁行业的工作人员来说至关重要。
轧钢工艺的发展趋势:随着科技的发展,轧钢工艺不断进行创新和改进,如连轧技术的广泛应用、高精度轧制技术的研发等。
环保和可持续发展也成为轧钢工艺发展的重要方向,如节能减排、资源循环利用等。
轧钢工艺是钢铁生产过程中不可或缺的一环,对于提高钢材质量、满足市场需求具有重要意义。
轧钢工艺流程简介
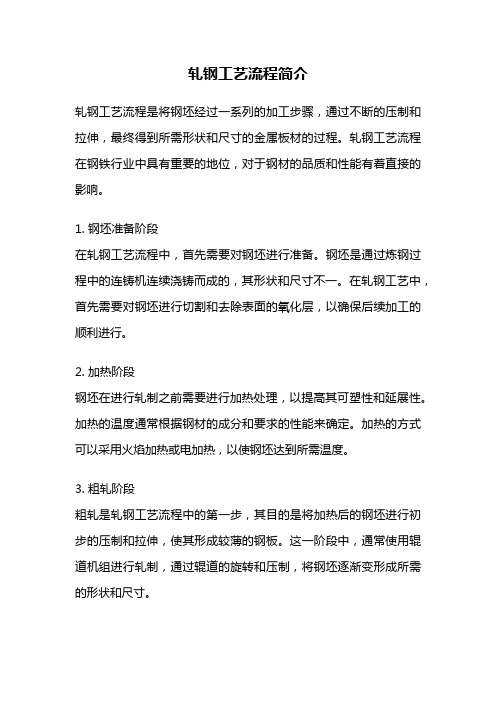
轧钢工艺流程简介轧钢工艺流程是将钢坯经过一系列的加工步骤,通过不断的压制和拉伸,最终得到所需形状和尺寸的金属板材的过程。
轧钢工艺流程在钢铁行业中具有重要的地位,对于钢材的品质和性能有着直接的影响。
1. 钢坯准备阶段在轧钢工艺流程中,首先需要对钢坯进行准备。
钢坯是通过炼钢过程中的连铸机连续浇铸而成的,其形状和尺寸不一。
在轧钢工艺中,首先需要对钢坯进行切割和去除表面的氧化层,以确保后续加工的顺利进行。
2. 加热阶段钢坯在进行轧制之前需要进行加热处理,以提高其可塑性和延展性。
加热的温度通常根据钢材的成分和要求的性能来确定。
加热的方式可以采用火焰加热或电加热,以使钢坯达到所需温度。
3. 粗轧阶段粗轧是轧钢工艺流程中的第一步,其目的是将加热后的钢坯进行初步的压制和拉伸,使其形成较薄的钢板。
这一阶段中,通常使用辊道机组进行轧制,通过辊道的旋转和压制,将钢坯逐渐变形成所需的形状和尺寸。
4. 中轧阶段中轧是对粗轧后的钢板进行进一步的压制和拉伸,以得到更加细薄的钢板。
在中轧阶段中,使用的轧机通常比粗轧阶段中的轧机更加先进和精密。
通过更高的压力和更精细的控制,中轧阶段可以使钢板的尺寸和形状达到更高的精度要求。
5. 精轧阶段精轧是轧钢工艺流程中的最后一道工序,其目的是对中轧后的钢板进行最后的压制和拉伸,使其达到最终的厚度和尺寸。
在精轧阶段中,使用的轧机通常更加精密和灵活,可以对钢板进行微调和修整,以确保其尺寸的一致性和平整度。
6. 冷却和整平阶段在精轧后,钢板需要进行冷却和整平,以恢复其原有的力学性能和平整度。
冷却可以采用水冷或空冷的方式,根据钢材的特性和要求来确定。
整平则是通过机械或液压的方式对钢板进行拉伸和修整,使其达到所需的平整度和表面质量。
7. 检验和包装阶段经过轧钢工艺流程的钢板需要进行严格的检验,以确保其质量和性能符合要求。
检验包括尺寸、表面质量、力学性能等方面的测试。
合格的钢板经过检验后,会进行包装和标识,以便于储运和使用。
轧钢工艺简介

❖ 2.热轧/冷轧
❖
热轧就是在奥氏体再结晶温度以上进行轧制,
冷轧即轧件不经过加热,直接轧制。
❖ 3 .高压水除鳞
❖
利用高压水的机械冲击力来除去氧化铁皮
轧钢工艺简介
❖ 4.层流冷却
❖ 层流就是使低水头的水从水箱或集水管 中通过弯曲管的作用形成一无旋和无脉动的 流股,这种流股从外观上看如同透明的棒一 样,液体质点无任何混杂现象。这样的层流 态的水从一定高度降落到钢板表面上会平稳 地向四周流去,从而扩大了冷却水同板材的 有效接触,大大提高了冷却效率。
轧钢工艺流程简介
轧钢工艺简介
内容摘要
❖ 目录 ❖ 1.名词解释 ❖ 2.板带轧制工艺流程 ❖ 3.轧钢机械设备 ❖ 4.板带轧制常见缺陷及产生原因 ❖ 5.轧钢新技术
轧钢工艺简介
高 炉
连铸
转炉
加热炉 轧制
轧钢工艺简介
除鳞 1 除鳞 2 大立辊 切头剪 除鳞 3 卷取机 1 卷取机 2
中厚板坯 连铸连轧 设备布置
2#加热炉 1#加热炉
加热炉 R1
F1 F2 F3 F4 F5 F6 F7 精轧机
层流冷却系统
板坯:厚度180/200mm 宽度670~1050mm 长度7~10m 成品:厚度1.4~25mm 宽度650~1050mm
轧钢工艺简介
1.基本定义及特点
轧钢工艺简介
1.1名词解释
❖ 1.轧钢
❖ 轧钢就是采用高速旋转的轧辊将轧件拖入辊缝 中,并将轧件轧制成所需要的形状的过程。
❖ 3. 可弯曲、焊接成各类断面的型钢、钢管、大型工 字钢、槽钢等结构件,故称为 “万能钢材” 。
轧钢工艺简介
1.3板带钢轧制的生产特点
❖ 板、带材的生产具有以下特点: ❖ 1. 板、带材是用平辊轧出,故改变产品规格较简单
- 1、下载文档前请自行甄别文档内容的完整性,平台不提供额外的编辑、内容补充、找答案等附加服务。
- 2、"仅部分预览"的文档,不可在线预览部分如存在完整性等问题,可反馈申请退款(可完整预览的文档不适用该条件!)。
- 3、如文档侵犯您的权益,请联系客服反馈,我们会尽快为您处理(人工客服工作时间:9:00-18:30)。
39
优质圆钢
螺纹钢
40
成品发货
成品仓库
41
生产操作控制中心
42
自动化中央控制室
43
2
高速线材厂生产简介
自1999年投产以来,经过不断完善、加 强生产管理和提高操作技术水平,于2005年 实际年产量已达到70万吨,2006年预计将超 过75万吨。 80
60 40 20 0 ê ú ¿ Ä ² Á (Í ¶ £ ò Ö ©
2000
2001
2002
2003
2004
2005
2006
3
高速线材生产工艺流程
29
ø610粗轧 机组六机 架连轧, 每机架轧 制一次。
水平轧机 立式轧机
30
1#飞剪
31
1#飞剪
1#飞剪在生产的过程中用于剪切掉头、尾部 不合格的红坯,当生产线发生故障时,该飞剪将 处理未轧制完的轧件。
32
ø420中轧机 组六机架连 轧,每机架 轧制一次。
中轧机组
33
精轧机组
ø370精轧机组六架轧机连轧,每机架轧制一次。
12
精轧机组
13
预精轧二中轧输送过来的红 坯,在预精轧机组轧制四道次, 然后切头进入精轧机组。
14
吐丝机
15
高温下的线材成品经由吐丝 机,均匀地分布在散冷运输辊道 上,经冷却后进入收集装置。
16
PF钩式运输机
集卷
17
收集成卷后的成品,其温度 还在300º C左右,在PF钩式盘卷 运输和继续冷却的过程中,经过 检验、打包、称重、入库。
27
双蓄热推钢式加热炉
该加热炉有效尺寸39000X6500m/m, 加热能力90t/h。燃料为高炉煤气,采用节 能环保型蓄热式烧嘴加热钢坯。原料进入加 热炉后加热至1100º C~1150 º C,由推钢机 推出炉进入轧制生产线。
28
根据合金钢生产的要求,采用高压水除鳞装置,除 去加热后钢坯表面的氧化铁皮。
– 原料 150X150X6000m/m; – 成品 ø10~ø25m/m螺纹钢;ø25~ø50园钢 – 钢种 普通碳素结构钢、低合金钢、优质碳素结构钢
23
棒材生产工艺特点
该生产线工艺特点为:以生产小规格螺 纹钢为主,采用先进的切分轧制新工艺,全 线18架轧机,按平立交替无扭轧制布置, 产品产量高、成本低、质量好。
6
Ø650轧机
7
由加热炉出来的红坯,经输 送辊道进入粗轧机,在ø650轧 机轧制三道次。
8
中轧机组
双线轧制
9
由ø650粗轧机输送过来 的红坯,经中轧机组连轧十 道次,然后分为二线进入预精
轧机组。
10
预精轧机组
11
由中轧机组输送过来的红坯, 在预精轧机组轧制四道次,然后 切头进入精轧机组。
ቤተ መጻሕፍቲ ባይዱ34
精轧机组出 口处设有控 制水冷箱, 轧件经过水 水冷系统的 冷却处理, 以提高钢材 的综合机械 性能。
控制水冷箱
35
倍尺飞剪 夹送辊
根据成品定尺要求及冷床的长度,由倍尺飞剪将轧 36 件剪成倍尺长度。
步进齿条式冷床
37
定尺冷剪机将冷却后的轧件,剪成用户所需要的长 度。
38
检验、收集
打捆、入库
原料准备 一中轧 3#飞剪 双蓄热加热炉 2#飞剪 精轧机组 二中轧 水冷线 Ø650粗轧机 分二线 吐丝机 压紧打捆 1#热剪 预精轧 风冷线 盘卷称重
散卷收集 入库
PF运输线
4
推钢式 加热炉
5
加热炉有效尺寸39000X6500m/m, 加热能力100t/h。燃料为高炉煤气,采 用节能环保型蓄热式烧嘴加热钢坯。原 料进入加热炉后加热至1100º C~1150 º C, 由推钢机推出炉,进入轧制生产线。
18
压紧打捆
成品发货
19
自动化中央控制室
20
高线厂自动化控制系统,是基 于德国西门子PLC控制器和直流调 速传动等技术的全集成自动化系统。
21
生产操作控制中心
22
棒材生产工艺简介
棒材厂始建于2004年6月,于2005年9月投 产。设计年产量50万吨,成品线速度14m/s。 产品工艺方案
24
棒材生产工艺流程
连铸坯 高压水除鳞 2#飞剪 步进冷床 打捆挂牌 上料台架 粗轧机组 精轧机组 定尺冷剪 称重 入炉辊道 1#飞剪 控制水冷 检验台架 入库
25
双蓄热加热炉 中轧机组 倍尺飞剪 计数收集
液压推钢机 上料辊道
炉区上料系统由上料台架、上料辊道、入炉液压推 26 钢机组成。
双蓄热式加热炉
轧钢工艺简介
1、高速线材生产工艺 2、棒材生产工艺
高速线材生产工艺简介
高速线材厂于1998年8月开工建设,1999年 4月底投产。设计年产量50万吨,精轧机组采用 美国摩根45º 高速无扭精轧机组,成品线速度 75m/s。 产品工艺方案
– 原料 150X150X6000m/m;180X180X3000m/m – 成品 ø6.5~ø12m/m光园盘条;ø8~ø10螺纹钢盘条 – 钢种 普通碳素结构钢、低合金钢、优质碳素结构钢