超声波传感器在波纹板折线焊缝跟踪中的应用
电磁超声技术在焊缝检测中的应用
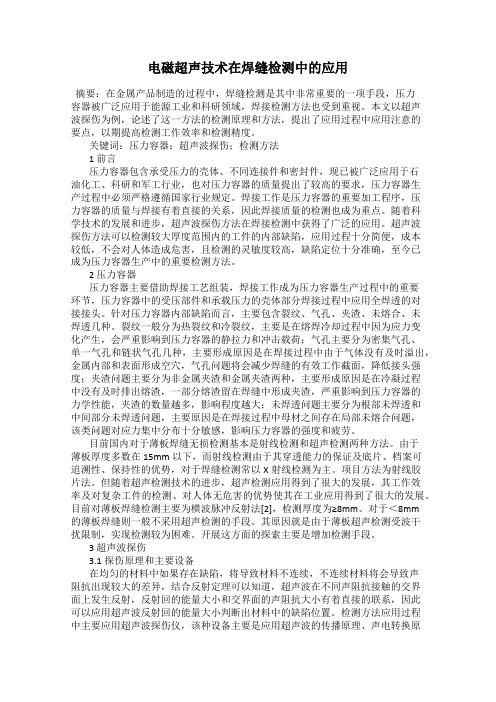
电磁超声技术在焊缝检测中的应用摘要:在金属产品制造的过程中,焊缝检测是其中非常重要的一项手段,压力容器被广泛应用于能源工业和科研领域,焊接检测方法也受到重视。
本文以超声波探伤为例,论述了这一方法的检测原理和方法,提出了应用过程中应用注意的要点,以期提高检测工作效率和检测精度。
关键词:压力容器;超声波探伤;检测方法1 前言压力容器包含承受压力的壳体、不同连接件和密封件,现已被广泛应用于石油化工、科研和军工行业,也对压力容器的质量提出了较高的要求,压力容器生产过程中必须严格遵循国家行业规定。
焊接工作是压力容器的重要加工程序,压力容器的质量与焊接有着直接的关系,因此焊接质量的检测也成为重点。
随着科学技术的发展和进步,超声波探伤方法在焊接检测中获得了广泛的应用。
超声波探伤方法可以检测较大厚度范围内的工件的内部缺陷,应用过程十分简便,成本较低,不会对人体造成危害,且检测的灵敏度较高,缺陷定位十分准确,至今已成为压力容器生产中的重要检测方法。
2 压力容器压力容器主要借助焊接工艺组装,焊接工作成为压力容器生产过程中的重要环节,压力容器中的受压部件和承载压力的壳体部分焊接过程中应用全焊透的对接接头。
针对压力容器内部缺陷而言,主要包含裂纹、气孔、夹渣、未熔合、未焊透几种。
裂纹一般分为热裂纹和冷裂纹,主要是在熔焊冷却过程中因为应力变化产生,会严重影响到压力容器的静拉力和冲击载荷;气孔主要分为密集气孔、单一气孔和链状气孔几种,主要形成原因是在焊接过程中由于气体没有及时溢出,金属内部和表面形成空穴,气孔问题将会减少焊缝的有效工作截面,降低接头强度;夹渣问题主要分为非金属夹渣和金属夹渣两种,主要形成原因是在冷凝过程中没有及时排出熔渣,一部分熔渣留在焊缝中形成夹渣,严重影响到压力容器的力学性能,夹渣的数量越多,影响程度越大;未焊透问题主要分为根部未焊透和中间部分未焊透问题,主要原因是在焊接过程中母材之间存在局部未熔合问题,该类问题对应力集中分布十分敏感,影响压力容器的强度和疲劳。
弯曲及折线焊缝的自动跟踪
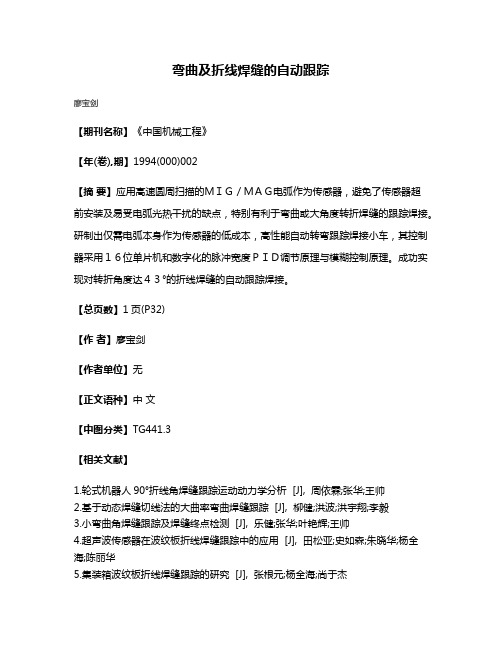
弯曲及折线焊缝的自动跟踪
廖宝剑
【期刊名称】《中国机械工程》
【年(卷),期】1994(000)002
【摘要】应用高速圆周扫描的MIG/MAG电弧作为传感器,避免了传感器超
前安装及易受电弧光热干扰的缺点,特别有利于弯曲或大角度转折焊缝的跟踪焊接。
研制出仅需电弧本身作为传感器的低成本,高性能自动转弯跟踪焊接小车,其控制器采用16位单片机和数字化的脉冲宽度PID调节原理与模糊控制原理。
成功实现对转折角度达43°的折线焊缝的自动跟踪焊接。
【总页数】1页(P32)
【作者】廖宝剑
【作者单位】无
【正文语种】中文
【中图分类】TG441.3
【相关文献】
1.轮式机器人90°折线角焊缝跟踪运动动力学分析 [J], 周依霖;张华;王帅
2.基于动态焊缝切线法的大曲率弯曲焊缝跟踪 [J], 柳健;洪波;洪宇翔;李毅
3.小弯曲角焊缝跟踪及焊缝终点检测 [J], 乐健;张华;叶艳辉;王帅
4.超声波传感器在波纹板折线焊缝跟踪中的应用 [J], 田松亚;史如森;朱晓华;杨全海;陈丽华
5.集装箱波纹板折线焊缝跟踪的研究 [J], 张根元;杨全海;尚于杰
因版权原因,仅展示原文概要,查看原文内容请购买。
超声波检测传感器的设计与应用研究
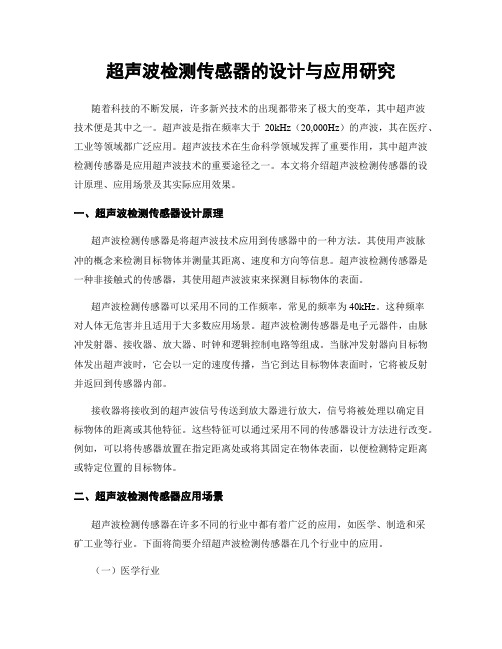
超声波检测传感器的设计与应用研究随着科技的不断发展,许多新兴技术的出现都带来了极大的变革,其中超声波技术便是其中之一。
超声波是指在频率大于20kHz(20,000Hz)的声波,其在医疗、工业等领域都广泛应用。
超声波技术在生命科学领域发挥了重要作用,其中超声波检测传感器是应用超声波技术的重要途径之一。
本文将介绍超声波检测传感器的设计原理、应用场景及其实际应用效果。
一、超声波检测传感器设计原理超声波检测传感器是将超声波技术应用到传感器中的一种方法。
其使用声波脉冲的概念来检测目标物体并测量其距离、速度和方向等信息。
超声波检测传感器是一种非接触式的传感器,其使用超声波波束来探测目标物体的表面。
超声波检测传感器可以采用不同的工作频率,常见的频率为40kHz。
这种频率对人体无危害并且适用于大多数应用场景。
超声波检测传感器是电子元器件,由脉冲发射器、接收器、放大器、时钟和逻辑控制电路等组成。
当脉冲发射器向目标物体发出超声波时,它会以一定的速度传播,当它到达目标物体表面时,它将被反射并返回到传感器内部。
接收器将接收到的超声波信号传送到放大器进行放大,信号将被处理以确定目标物体的距离或其他特征。
这些特征可以通过采用不同的传感器设计方法进行改变。
例如,可以将传感器放置在指定距离处或将其固定在物体表面,以便检测特定距离或特定位置的目标物体。
二、超声波检测传感器应用场景超声波检测传感器在许多不同的行业中都有着广泛的应用,如医学、制造和采矿工业等行业。
下面将简要介绍超声波检测传感器在几个行业中的应用。
(一)医学行业医学行业是超声波技术的主要应用领域之一。
医生们使用超声波检测传感器来检查身体内部,了解病患的内部情况。
在妇科等领域,这种传感器可以用于卵巢癌的早期检测。
此外,它还可以用于检查肝脏、胰腺和血管等器官的状况。
(二)制造业在制造行业中,超声波检测传感器主要应用于检测材料缺陷、尺寸和位置等。
这种传感器可以用于检测金属薄片、塑料件、纺织品等产品的质量。
电磁超声技术在焊缝检测中的应用

图3 激光拼焊板样品以及人工缺陷照片
表1 缺陷几何形状参数缺陷 形状 几何参数1 孔 φ1mm 2 孔 φ1mm×0.5mm(深)3 孔 φ2mm 4 孔 φ0.3mm 5 孔 φ1mm 6 孔 φ1.5mm 7 槽 25.4mm(长)×0.25mm(深)8 槽 25.4mm(长)×0.25mm(深)9 槽 25.4mm(长)×0.5mm(深)
图8 电磁超声相控阵仪器及探头照片
4 结论
电磁超声技术(EMAT)作为一种新型的超声无损检测技术,近年来已经由实验室研究阶段进入工业生产的实际应用阶段。介绍了电磁超声的基本原理、电磁超声较传统压电超声检测技术的优缺点。重点介绍了由Innerspec公司开发研制的三套针对焊缝检测的代表性电磁超声系统,包括薄板激光焊缝的检测、电阻焊钢管检测以及奥氏体不锈钢焊缝的检测。电磁超声传感技术与超声导波技术的结合,适用于从<1mm的薄板,到12mm的厚板以及管件中焊缝的检测。对于超过12mm厚的材料,电磁超声斜入射体波检测可以达到很好的效果。总之,电磁超声技术的发展扩展了超声波检测的应用范围。电磁超声为很多需要非接触检测、快速高效检测、超高低温环境以及需要水平横波检测的应用领域提供了一系列有效的解决方案。
3 电磁超声SH波相控阵检测பைடு நூலகம்氏体不锈钢焊缝
由于奥氏体不锈钢的强抗腐蚀性,它在核工业、石油化工以及高温处理工业中得到了广泛应用。因此,奥氏体焊缝在这些应用领域也非常常见。由于奥氏体焊缝具有很特殊的长条形晶粒结构,超声波在奥氏体焊缝中会受到明显的散射以及方向偏转,给奥氏体不锈钢焊缝的检测带来很大的困难。理论研究表明,最常用于检测常规焊缝的斜入射垂直横波受到的影响尤其剧烈,而最理想的检测波形是水平横波。然而,由于压电换能器不易于激发和耦合水平横波,现有的方法是使用纵波检测,但是由于纵波经过表面反射后会发生波型转换,给信号的判读带来一定的难度。通常用纵波对奥氏体不锈钢焊缝检测都需要将焊缝表面修平,而且焊缝的两侧都必须可以放置探头。
电磁超声技术在焊缝检测中的应用_高会栋
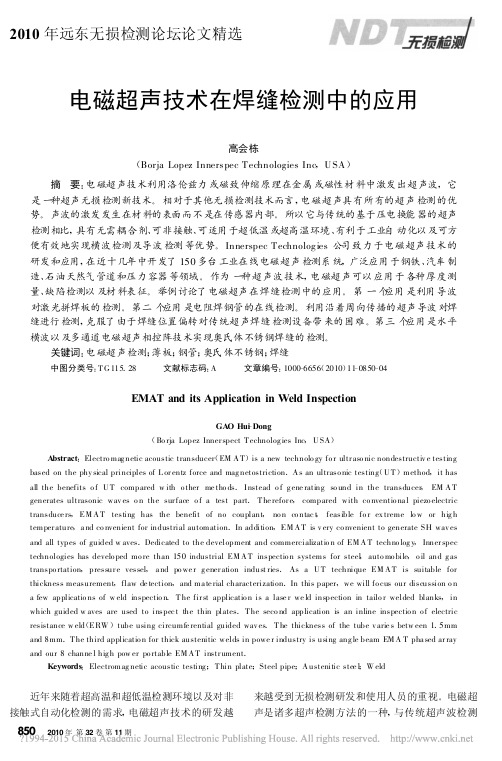
2010年远东无损检测论坛论文精选 2010年第32卷第11期电磁超声技术在焊缝检测中的应用高会栋(Borja Lopez Innerspec Technologies Inc ,USA )摘 要:电磁超声技术利用洛伦兹力或磁致伸缩原理在金属或磁性材料中激发出超声波,它是一种超声无损检测新技术。
相对于其他无损检测技术而言,电磁超声具有所有的超声检测的优势。
声波的激发发生在材料的表面而不是在传感器内部。
所以它与传统的基于压电换能器的超声检测相比,具有无需耦合剂、可非接触、可适用于超低温或超高温环境、有利于工业自动化以及可方便有效地实现横波检测及导波检测等优势。
Innerspec Technolog ies 公司致力于电磁超声技术的研发和应用,在近十几年中开发了150多台工业在线电磁超声检测系统,广泛应用于钢铁、汽车制造、石油天然气管道和压力容器等领域。
作为一种超声波技术,电磁超声可以应用于各种厚度测量、缺陷检测以及材料表征。
举例讨论了电磁超声在焊缝检测中的应用。
第一个应用是利用导波对激光拼焊板的检测。
第二个应用是电阻焊钢管的在线检测。
利用沿着周向传播的超声导波对焊缝进行检测,克服了由于焊缝位置偏转对传统超声焊缝检测设备带来的困难。
第三个应用是水平横波以及多通道电磁超声相控阵技术实现奥氏体不锈钢焊缝的检测。
关键词:电磁超声检测;薄板;钢管;奥氏体不锈钢;焊缝 中图分类号:T G 115.28 文献标志码:A 文章编号:1000-6656(2010)11-0850-04EMAT and its Application in Weld InspectionGA O Hui -Dong(Bo rja Lopez Inner spect T echnolog ies Inc ,U SA )A bstract :Electro mag netic acoustic transducer (EM A T )is a new technolo gy fo r ultr aso nic nondestructiv e testing based on the phy sical principles of L or entz force and mag netostriction .A s an ultraso nic testing (U T )method ,it has all the benefits o f U T compared w ith o ther me tho ds .I nstead o f g ene rating so und in the transducer ,EM A T generates ultrasonic wav es o n the sur face o f a test part .T he refor e ,compared with co nventio na l piezo electric transduce rs ,EM A T testing has the benefit of no couplant ,no n co ntac t ,feasible fo r ex treme lo w or hig h temper ature ,a nd co nvenient for industrial automation .In addition ,EM A T is v ery co nvenient to generate SH wav es and all types of guided w aves .Dedicated to the development and commercializatio n of EM A T techno log y ,Inner spec technologies has develo ped mo re than 150industrial EM A T inspectio n systems for steel ,auto mo bile ,o il and g as transpo rtation ,pressur e vessel ,a nd po we r g ener ation indust ries .As a U T technique EM A T is suitable for thickness measurement ,flaw de tection ,and ma te rial characterization .In this paper ,we will fo cus our discussion o n a few applicatio ns of w eld inspectio n .T he fir st applicatio n is a lase r we ld inspection in tailo r welded blanks ,in which guided w aves are used to inspec t the thin plates .T he seco nd application is an inline inspectio n o f electric resistance w eld (ERW )tube using circumfe rential guided wav es .T he thickness of the tube v arie s betw een 1.5mm and 8mm .T he third applicatio n for thick austenitic welds in powe r industry is using ang le beam EM A T pha sed ar ray and our 8channe l hig h pow er po rtable EM A T instr ument .Keywords :Electromag netic acoustic testing ;T hin plate ;Steel pipe ;A ustenitic stee l ;W eld 近年来随着超高温和超低温检测环境以及对非接触式自动化检测的需求,电磁超声技术的研发越来越受到无损检测研发和使用人员的重视。
集装箱波纹板折线焊缝跟踪的研究
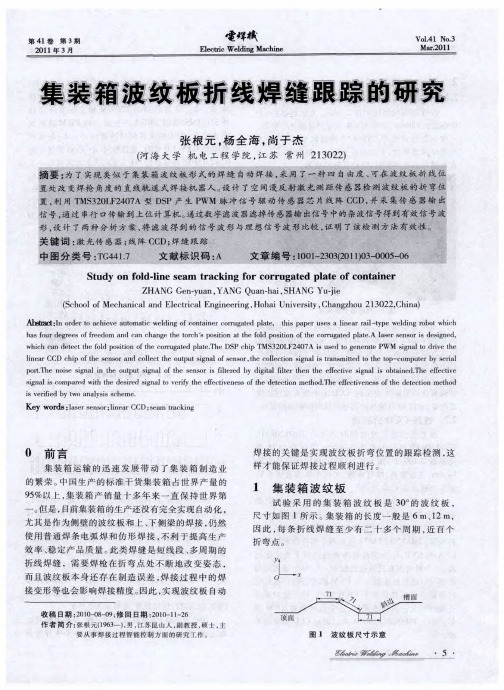
C D有 多种 驱动方 式 , 中一种是采 用 D P驱 C 其 S 动。 S D P不 仅可 以产生 C D所需 的驱动 脉冲 , C 还可
以 利 用 D P强 大 的 计 算 能 力对 C D 的 输 } 信 号 进 S C } I 行 处 理 。 MS 2 L 2 0 A 包 括 两 个 事 件 管 理 器 模 块 T 3OF 47 E A 和 E B, 个 事 件 管 理 器 包 括 两 个 通 用 定 时 V V 每 器 , 个 带 可 编 程 死 区 的 比较 单 元 每 个 通 用 定 时 三 。 器都可 以独立 地提供 一个 P WM 输 出 , 因此 , 用 定 通 时 器 最 多 可 以 提 供 四 个 P M 输 出 。 个 比较 单 元 W 每
有 效消 除弧光 的影 响 ; 位 孔和 接收器 。 限
210个 ( ( 6 b 或
周期同 所 以 , , 综合 考虑取 P WM1 、
P 2的 频 率 为 4 0k zT P WM 0 H ,2 WM 的 频 率 为 14H 。 7 z
图 3中 1号线 为 T P 2 wM( S , 即 H)2号线 为 P WM2
焊 设 接备
2 激 光 传 感 器 系 统
21 传 感器 结 构 和 原 理 .
雹珲钗
第 1 4卷
将 事 件 管 理 器 E A 的 比较 单 元 1 生 的 P V 产 WM1
和P WM2作 为 C D 的 复位 脉 冲 R C S和移位 时钟 脉
冲 、I , 2定 时 器 的 T P M 输 出 作 为 转 移 脉 (:T ) 2W 、 的 频 率 冲 S T 3 0 F 4 7 产 生 的 三 路 P M 波 形 如 H。 MS 2 L 2 0 A W 图 3所 示 。 为 两 相 移 位 时 钟 脉 冲 因 范 同 是 01 ~ . MHz 复 位 脉 冲 R . 1 5 0 , S的 频 率 范 围 是 0 ~ .MH , 移 脉 冲 S 为 低 电平 的 时 间 应 不 小 于 . 2 z转 3 0 H
超声波传感器及其应用
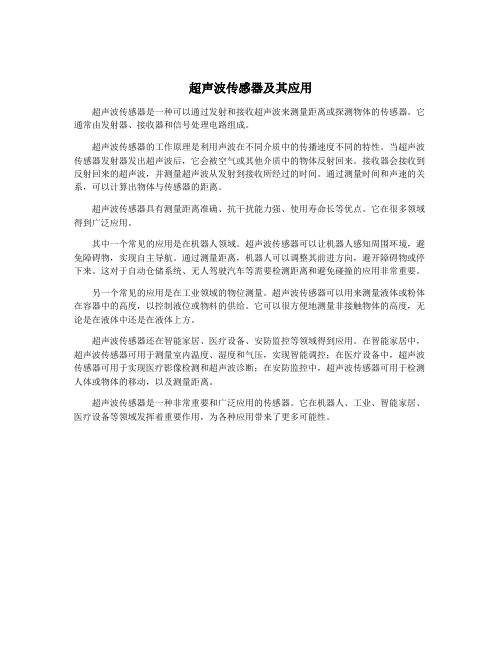
超声波传感器及其应用
超声波传感器是一种可以通过发射和接收超声波来测量距离或探测物体的传感器。
它通常由发射器、接收器和信号处理电路组成。
超声波传感器的工作原理是利用声波在不同介质中的传播速度不同的特性。
当超声波传感器发射器发出超声波后,它会被空气或其他介质中的物体反射回来。
接收器会接收到反射回来的超声波,并测量超声波从发射到接收所经过的时间。
通过测量时间和声速的关系,可以计算出物体与传感器的距离。
超声波传感器具有测量距离准确、抗干扰能力强、使用寿命长等优点。
它在很多领域得到广泛应用。
其中一个常见的应用是在机器人领域。
超声波传感器可以让机器人感知周围环境,避免障碍物,实现自主导航。
通过测量距离,机器人可以调整其前进方向,避开障碍物或停下来。
这对于自动仓储系统、无人驾驶汽车等需要检测距离和避免碰撞的应用非常重要。
另一个常见的应用是在工业领域的物位测量。
超声波传感器可以用来测量液体或粉体在容器中的高度,以控制液位或物料的供给。
它可以很方便地测量非接触物体的高度,无论是在液体中还是在液体上方。
超声波传感器还在智能家居、医疗设备、安防监控等领域得到应用。
在智能家居中,超声波传感器可用于测量室内温度、湿度和气压,实现智能调控;在医疗设备中,超声波传感器可用于实现医疗影像检测和超声波诊断;在安防监控中,超声波传感器可用于检测人体或物体的移动,以及测量距离。
超声波传感器是一种非常重要和广泛应用的传感器。
它在机器人、工业、智能家居、医疗设备等领域发挥着重要作用,为各种应用带来了更多可能性。
超声波在焊缝检测中的应用

超声波在焊缝检测中的应用文章结合实际超声波检测过程,介绍了焊缝中的各个类型缺陷在超声波检测中的波形特点,以及实际检测中的一些实用方法。
标签:焊缝;超声波检测;波形特点;实用方法超声波检测是目前应用最广泛的无损检测方法之一,它具有穿透力强、缺陷定位较准确、对面积型缺陷的检出率高、灵敏度高、检测成本低、速度块、设备轻便、对人体及环境无害、现场使用方便等优点。
由于超声波穿透力强的特点,所以检测厚度较厚的焊缝。
对于埋藏较深的缺陷,只要超声波能较垂直摄入缺陷面,就能得到很高的缺陷回波。
因此超声波对焊缝中的未熔合、未焊透和裂纹等危害性缺陷的检出率很高。
1 焊缝中不同类型缺陷的波形特点一般都焊缝中常见的缺陷有:气孔、夹渣、未熔合、未焊透和裂纹等。
到目前为止还没有一个成熟的方法对缺陷的性质进行准确的评判,只是根据荧光屏上得到的缺陷波的形状和放射波的高低的变化结合缺陷的位置和焊接工艺对缺陷进行综合估判。
1.1 气孔單个气孔:由于气孔中的气体声阻抗小,得到的反射波也陡直尖锐。
从各个方向探测,得到的回波高度大致相同,单稍微移动探头,回波就消失。
密集气孔:会得到一簇反射波,波高随气孔的大小而不同,若有几个气孔紧挨着,会得到一个较宽而且反射波特别高的回波。
当探头作定点转动时,会出现此起彼落的现象。
这里得和裂纹进行区别了,密集气孔从不同方向探,回波差距不大,裂纹就相差较大了。
1.2 夹渣点状夹渣回波信号和单个气孔的信号类似,不同之处在于,夹渣的声阻抗较气孔大,得到的反射回波较低。
又由于夹渣面粗糙,所以波形较宽,呈锯齿形。
1.3 咬边表面缺陷,一般用肉眼即可发现。
一般出现在板厚位置,焊缝两侧检测都能发现,用手蘸油轻轻拍打缺陷处,反射波有明显的起伏。
1.4 未焊透出现在根部位置,波幅较高。
探头平拉时,波形稳定,焊缝两侧探测,波高相似。
1.5 未熔合较多出现在波口位置,用探头单侧平拉时,波形较稳定,两侧检测时,波幅有明显不同,甚至有时候,只能从单侧发现。
浅谈超声波检测在钢结构焊接质量检验中的应用

浅谈超声波检测在钢结构焊接质量检验中的应用(中国二冶钢结构公司无损检测室张军)在厂房建设及设备安装中大量使用钢结构,钢结构的焊接质量十分重要,无损检测是保证钢结构焊接质量的重要方法。
一、钢结构焊缝无损检测技术简介无损检测是在不损坏工件或原材料工作状态的前提下,以物理或化学方法为手段,借助先进的技术和设备器材,对试件的内部及表面的结构,性质,状态进行检查和测试的方法。
钢结构焊缝无损检测技术主要有超声波检测、射线检测以及磁粉检测。
超声波检测是目前应用最广泛的无损探伤方法之一,该法采用高频超声波穿过被检焊缝,当遇到缺陷时超声波反射,通过反射波的幅度和位置判断缺陷性质、位置及大小。
射线检测技术是采用X 射线透照被检焊缝,焊缝内部的缺陷对X 射线的反射、吸收使之在底片上留下影像,通过底片上的影像即可判断焊缝内部缺陷。
磁粉检测技术是一种表面探伤技术,其原理是材料或焊缝表面缺陷造成表面材质的不连续,当外加磁场在该处时,其表面磁场分布与无缺陷处不同,利用磁粉指示出磁场分布,即可判断材料或焊缝的表面缺陷。
二、超声波无损检测技术的物理基础及适用范围(一)超声波检测的物理特点超声波是超声振动在介质中的传播,它的实质是以波动形式在弹性介质中传播的机械振动,其频率在20KHz以上。
超声波检测可探测厚度较大的材料,且具有检测速度快,费用低并能对缺陷进行定位和定量,对人体无害以及对危害性较大的面积型缺陷的检测灵敏度较高等优点。
因此,超声波检测已经发展成一种很重要的无损检测方法,在生产实践中得到了广泛的应用。
超声波被用于无损检测,主要有以下几个特性:(1)波在介质中传播时,遇到界面会发生反射;(2)波指向性好。
频率愈高,指向性愈好;(3)传播能量大,对各种材料的穿透力都较强;(4)超声波的声速、衰减、阻抗和散射等特性,为超声波的应用提供了丰富的信息,并且成为超声波广泛应用的条件。
(二)超声波检测的基本原理超声波探伤仪每秒输出数十至数千个高频脉冲电压信号,通过特殊电缆施加于压电换能器(俗成探头) ,并完成电—机转换,产生高频机械振动;高频机械波在探伤人员或机械装置的规范影响下,通过中间介质导入被检测对象——焊缝;焊缝本身的形状、结构或内部缺陷的声学特性对超声波传播的影响时效反馈至换能器进行机—电转换,转换后的电脉冲信号经检波过程显示在探伤仪荧光屏上;探伤人员(或模拟的自动化机械识别装置)根据荧光屏上有无信号、信号的位置、信号的幅度、信号的形态判断焊缝中有无缺陷、缺陷的位置、缺陷的大小和性质,并以此综合信息对焊缝质量进行评价。
相控阵超声波检测技术在焊缝检测中的应用分析
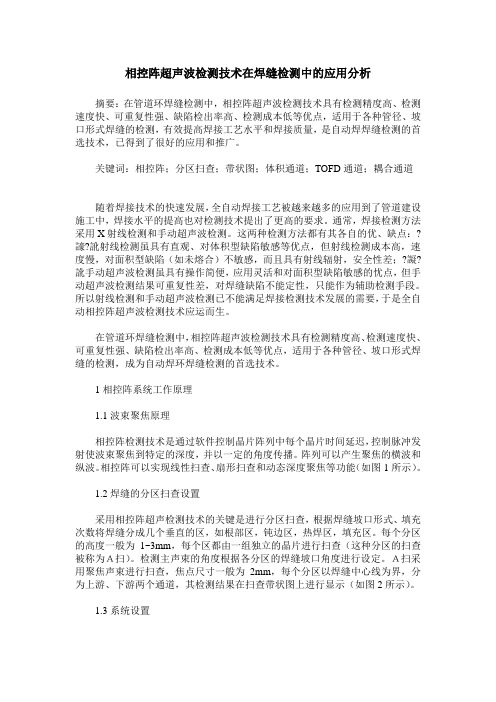
相控阵超声波检测技术在焊缝检测中的应用分析摘要:在管道环焊缝检测中,相控阵超声波检测技术具有检测精度高、检测速度快、可重复性强、缺陷检出率高、检测成本低等优点,适用于各种管径、坡口形式焊缝的检测,有效提高焊接工艺水平和焊接质量,是自动焊焊缝检测的首选技术,已得到了很好的应用和推广。
关键词:相控阵;分区扫查;带状图;体积通道;TOFD通道;耦合通道随着焊接技术的快速发展,全自动焊接工艺被越来越多的应用到了管道建设施工中,焊接水平的提高也对检测技术提出了更高的要求。
通常,焊接检测方法采用X射线检测和手动超声波检测。
这两种检测方法都有其各自的优、缺点:?譹?訛射线检测虽具有直观、对体积型缺陷敏感等优点,但射线检测成本高,速度慢,对面积型缺陷(如未熔合)不敏感,而且具有射线辐射,安全性差;?譺?訛手动超声波检测虽具有操作简便,应用灵活和对面积型缺陷敏感的忧点,但手动超声波检测结果可重复性差,对焊缝缺陷不能定性,只能作为辅助检测手段。
所以射线检测和手动超声波检测已不能满足焊接检测技术发展的需要,于是全自动相控阵超声波检测技术应运而生。
在管道环焊缝检测中,相控阵超声波检测技术具有检测精度高、检测速度快、可重复性强、缺陷检出率高、检测成本低等优点,适用于各种管径、坡口形式焊缝的检测,成为自动焊环焊缝检测的首选技术。
1相控阵系统工作原理1.1波束聚焦原理相控阵检测技术是通过软件控制晶片阵列中每个晶片时间延迟,控制脉冲发射使波束聚焦到特定的深度,并以一定的角度传播。
阵列可以产生聚焦的横波和纵波。
相控阵可以实现线性扫查、扇形扫查和动态深度聚焦等功能(如图1所示)。
1.2焊缝的分区扫查设置采用相控阵超声检测技术的关键是进行分区扫查,根据焊缝坡口形式、填充次数将焊缝分成几个垂直的区,如根部区,钝边区,热焊区,填充区。
每个分区的高度一般为1~3mm,每个区都由一组独立的晶片进行扫查(这种分区的扫查被称为A扫)。
检测主声束的角度根据各分区的焊缝坡口角度进行设定。
超声波在焊缝跟踪中的应用

叶建雄:超声波传感器在焊缝跟踪中的应用超声波传感器在焊缝跟踪中的应用叶建雄(南昌大学机器人与焊接自动化实验室330029)摘要:介绍了超声波的特点及将在焊接自动化领域的应用。
将超声波传感器应用于焊缝自动跟踪的关键是距离的测量。
文章从减小回波损失,缩小检测盲区,保持回波强度和判断回波到达时刻四个方面论述了利用超声波传感器实现高精度距离测量的方法,对传感器在焊接中的应用方式和焊枪控制的方法进行了说明,最后对超声波传感器在焊接中的应用前景和趋势进行了展望。
关键词:超声波;传感器;焊缝跟踪1 简介超声波是一种振动频率高于声波的机械波,具有频率高、波长短、方向性好、可以定向发射和调制等特点;超声波是由压电体产生的,压电体又称换能器,是超声波传感器的核心部件,具有正压电效应和逆压电效应,通过压电体的逆压电效应可以获得超声波,利用压电体的正压电效应可以由超声波得到相应的脉动电压,从而实现声能与电能的相互转换。
超声波传感器按工作方式可分为发射型(电——声转换)、接收型(声——电转换)、发射——接收复合型三种形式,由于这类传感器具有使用灵活,原理简单,成本低、安装方便等优点,被广泛应用于距离检测,压力测量,流量/流速测定、空间智能定位、厚度控制等领域[1-4],超声波的安全性和非接触测量的优点,非常适合工作在重污染、高危险及人类难以进入的地区。
2 焊缝跟踪的意义焊接被广泛应用于机械制造、造船、海洋开发、汽车制造、石油化工、航天技术、原子能、电力、电子技术及建筑等部门,在金属制造业中,焊接已成为仅次于装配和机械加工的第三大产业。
在工业发达国家,每年钢铁产量的45%左右要通过焊接才能转化为最终的产品。
为了保证焊接产品质量的稳定性和提高劳动生产率,改善焊接工人工作条件,人们不断地提高焊接自动化的水平,主要内容之一就是发展焊缝自动跟踪技术。
焊缝跟踪是一项多学科交叉技术,包括电子技术、计算机、焊接、结构、材料,流体、光学、电磁等学科,国内外众多研究工作者投入到这一领域进行研究,从示教型焊接机器到程序控制焊接系统,再到移动式自动焊缝跟踪技术,焊接自动化的每一次进步,不仅大大降低了对工件加工精度和装配精度的要求,而且降低了焊前准备时间,显著提高了生产效率。
超声波检测在钢结构焊缝中的应用

超声波检测在钢结构焊缝中的应用目前现代化钢结构厂房的运用越来越多,它涉及大量立柱、横梁、吊车梁和焊接工字梁的制造及安装,按照图样技术的条件以及规范要求,钢结构件的翼板和腹板采用角焊接的焊缝形式,重要部位焊缝务必焊透。
针对需要焊透的焊缝按照技术条件以及规范要求来实行检测,以确保角焊缝内不存在未焊透缺陷。
GB50205-2001《钢结构工程施工及验收规范》明确要求用超声波检测方法对角焊缝整个截面进行检测。
焊接接头内部缺陷分级应符合现行国家标准GB11345—1989《钢焊缝手工超声波探伤方法和探伤结果的分级》的规定,焊缝质量等级及缺陷分级见表1。
在对钢结构件T形接头焊缝进行超声波检测过程中,一般采用三种检测方法,笔者进行了比较,并总结出较好的超声波探伤方法,供参考。
1超声波检测在钢结构焊缝中的运用钢结构中的立柱、Z字形大梁和吊车梁的材料一般为Q235A16Mn钢,翼板厚度一般为12 ~24mm,腹板厚度t一般为6~14mm,钢结构件的长度不等。
T形接头焊缝大部分采用手工电弧焊与埋弧焊,一般结构焊脚尺寸定为腹板的t/4,重级工作制和超重量>50t的中级工作制吊车梁腹板与翼缘的焊脚尺寸为t/2,且≯10mm。
GB 50205将焊缝质量等级分为一、二、三级。
一、二级焊缝需要进行焊缝内部缺陷检测,应符合GB 11345标准对应的,级质量等级。
超声波检测等级采用B级。
探伤比例分别为100%和20%(按每条焊缝长度的百分数计且≮200mm)。
原则上采用斜探头在焊缝单面两侧对整个焊缝截面进行探测,以防二维(片状)缺陷漏检。
超声波探伤仅适用于全熔透焊缝。
1.1在翼板上用直探头检测角焊缝由于在翼板上探伤时看不到焊缝(图1),必须以翼板边缘为准找出焊缝中心,画出一条基准线。
采用5N10,5N12窄脉冲直探头,扫描比例为1∶1,使Ф2mm平底孔当量不漏检,利用钢板大平底来调整探伤灵敏度(因窄脉冲探头对近场区有较高的分辨力),在此灵敏度下层状撕裂很容易探出。
焊缝的超声波探伤资料讲解

超声波的反射、折射、波形转换
在有机玻璃与钢的介面:
第一临界角为α=27.2°,βS=33.3° 第二临界角为α=56.7°,βS=90°
用于焊缝检测的超声波斜探头的入射 角必须大于第一临界角而小于第二临 界角。 我国习惯:斜探头的横波折射角用横 波折射角度的正切值表 示,如K=2
超声波探伤用试块
CSK-IA
超声波探伤用试块
调节:探头的前沿、K值、声速
超声波探伤用试块
CSK-IIIA
距离-波幅(DAC)曲线绘制
三条曲线生成后,按“增益”键,使用方向键调节曲线的高底,使 判废线达到屏幕的80%高度,进入探伤界面,进行探伤检测。
探测灵敏度的选定
➢ 探测灵敏度决定了检测缺陷的能力 灵敏度高,检测缺陷的能力大,探伤时反射的杂波太多,影响缺陷波的
GB11345-89标准规定:检验频率f一般在2-5MHz范围内选 择,
推荐选用2-2.5MHz公称频率检验。
检验等级
•A级检验
采用一种角度的探头在焊缝的单面单侧进行检验,只对允许扫 查到的焊缝截面进行探测.一般不要求作横向缺陷的检验.母材厚度 大于50mm时,不得采用A级检验。
检验等级
• B级检验
➢ 采用二次波探伤,探测面修整宽度为:
S ≥ 2KT+50 (mm)
➢ 采用一次波探伤,探测面修整宽度为:
S≥KT+50 (mm) 式中: K----探头的K值;
T----工件厚度。
P
P
二次波探伤
一次波探伤
耦合剂的选用
超声波检测在厚板对接焊缝中的应用
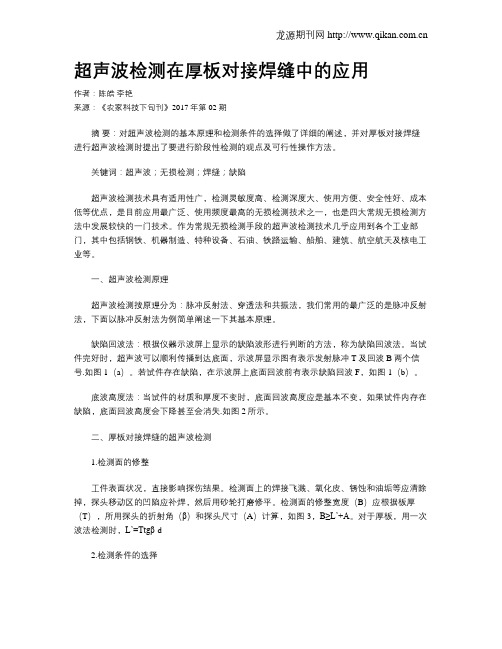
超声波检测在厚板对接焊缝中的应用作者:陈皓李艳来源:《农家科技下旬刊》2017年第02期摘要:对超声波检测的基本原理和检测条件的选择做了详细的阐述,并对厚板对接焊缝进行超声波检测时提出了要进行阶段性检测的观点及可行性操作方法。
关键词:超声波;无损检测;焊缝;缺陷超声波检测技术具有适用性广,检测灵敏度高、检测深度大、使用方便、安全性好、成本低等优点,是目前应用最广泛、使用频度最高的无损检测技术之一,也是四大常规无损检测方法中发展较快的一门技术。
作为常规无损检测手段的超声波检测技术几乎应用到各个工业部门,其中包括钢铁、机器制造、特种设备、石油、铁路运输、船舶、建筑、航空航天及核电工业等。
一、超声波检测原理超声波检测按原理分为:脉冲反射法、穿透法和共振法,我们常用的最广泛的是脉冲反射法,下面以脉冲反射法为例简单阐述一下其基本原理。
缺陷回波法:根据仪器示波屏上显示的缺陷波形进行判断的方法,称为缺陷回波法。
当试件完好时,超声波可以顺利传播到达底面,示波屏显示图有表示发射脉冲T及回波B两个信号.如图1(a)。
若试件存在缺陷,在示波屏上底面回波前有表示缺陷回波F,如图1(b)。
底波高度法:当试件的材质和厚度不变时,底面回波高度应是基本不变,如果试件内存在缺陷,底面回波高度会下降甚至会消失.如图2所示。
二、厚板对接焊缝的超声波检测1.检测面的修整工件表面状况,直接影响探伤结果。
检测面上的焊接飞溅、氧化皮、锈蚀和油垢等应清除掉,探头移动区的凹陷应补焊,然后用砂轮打磨修平。
检测面的修整宽度(B)应根据板厚(T),所用探头的折射角(β)和探头尺寸(A)计算,如图3,B≥L’+A。
对于厚板,用一次波法检测时,L’=Ttgβ-d2.检测条件的选择焊缝的晶粒比较细小,可选用较高的频率探伤,一般为2.5~5MHZ,对于板厚较小的焊缝,可采用较高的频率,对于板厚较大、衰减明显的焊缝,应选择较低的频率。
对于厚板对接焊缝,探头频率一般采用2.5MHZ,就能满足检测要求。
钢板焊缝的接触法超声波检测

钢板焊缝的接触法超声波检测钢板焊缝的接触法超声波检测【摘要】采用超声横波检测焊缝在工业应用中是一种非常成熟的技术,在压力容器和船舶的焊缝检测中应用广泛。
本文主要探讨了超声波检测焊缝时,反射波的埋深、水平距离及条件,分析了辨别方法,对提高超检声波检测准确性有很重要作用。
本论文主要介绍超声波检测技术的原理,超声检测的优缺点,探伤仪器的结构和性能,影响检测结果的因素,以及对中厚板对接焊缝检测的基本过程。
关键字:无损检测;超声波检测;探伤仪器;焊缝Abstract welds using ultrasonic wave detection in industrial applications is a very mature technology, pressure vessels and ships in the weld inspection is widely used. This article discusses the ultrasonic weld inspection, the reflected wave depth, horizontal distance and conditions of the identification method to improve the detection accuracy of ultra-sonic inspection is an important role. This paper introduces the principle of ultrasonic detection technology, the advantages and disadvantages of ultrasonic testing, flaw of the structure and performance of the factors that affect the test results, as well as the basic plate butt weld inspection process.Keywords: NDT; ultrasonic testing; flaw detector; weld钢板焊缝的接触法超声波检测目录1压力容器用钢板 (4)2检测方法的选择 (4)2.1无损检测的应用特点 (4)2.2超声波检测原理 (5)2.2.1脉冲反射法 (5)2.3接触法焊缝超声波检测的特点 (5)3检测仪器设备 (6)3.1超声波检测仪 (6)3.1.1 产品简介 (7)3.2超声波探头 (10)3.3耦合剂 (12)3.4试块 (12)4焊缝超声检测工艺卡 (15)5焊缝检测过程 (15)5.1目视检测面 (15)5.2.设定仪器的工作状态 (16)5.3测定探头的前沿距离及K值 (16)5.3.1 前沿测定 (16)5.3.2K值测定 (16)5.4、调节扫描速度 (16)5.4.1水平调节法 (17)5.4.2深度调节法 (17)5.5校验扫描速度 (17)5.6绘制距离波幅曲线 (18)5.7检测灵敏度的调节 (19)5.8扫查 (19)5.9清理现场 (20)钢板焊缝的接触法超声波检测6.超声检测结果 (21)结束语 ..................................................................................................................................... 错误!未定义书签。
- 1、下载文档前请自行甄别文档内容的完整性,平台不提供额外的编辑、内容补充、找答案等附加服务。
- 2、"仅部分预览"的文档,不可在线预览部分如存在完整性等问题,可反馈申请退款(可完整预览的文档不适用该条件!)。
- 3、如文档侵犯您的权益,请联系客服反馈,我们会尽快为您处理(人工客服工作时间:9:00-18:30)。
2 超声波传感器和焊接机构
2 . 1 超声波传感器 试验使用美国 Banner公司生产的模拟量输出高 精度超声波传 感器 Q45UR3L I U 64C 71005 , 测量范 围内 ( 80~ 150 mm ) 信号输出单调递增 ( 0~ 10 V ). 2 . 2 焊接机构 焊接机构采用的是自行研制的轨道式波纹板专 用焊接小车, 采用 4 台步进电机驱动 . 1 号电机控制 小车本体在焊缝方向 x 轴 ( 图 2 ) 上直线运动 , 2 号 电机控制焊枪在 y 轴方向随焊缝跟进, 3 号电机控 制焊枪在 z 轴 ( 垂直方向 ) 随动 , 4 号电机控制焊枪
1
杨全海 ,
1
陈丽华
2
(1 . 河海大学 机电工程学院 , 江苏 常州
213022; 2. 常州机电职业技术学院 , 江苏 常州
213022)
要 : 采用 Banner公司生产的超声波传感器 , 分别 在 3 种 速度下 跟踪波纹 板一个 波
纹周期 , 通过 TM S320LF2407A 对传感器输出信号进 行采样 . 采用快速 傅里叶变 换 ( fast four ier transfor m, FFT ) 分析采样数据 , 获取目标信号和干扰 信号频率范 围 . 设 计了 Bu t ter w orth 数字滤波器 , 经滤波后发现 , 3 种速度下波形一致 , 且 在波纹 板槽面与 斜边交 接 处的折弯位置信号变化明显 , 而在顶面与斜边 交接处 的折弯 位置信 号变化会 出现延 迟 或超前现象 . 根据超声波的传 播特性 分析 这一现 象 , 选择 前者 为检测 对象 . 在 500 脉 冲 / s 的速度下从固定起始点重复跟踪该折 弯位置 . 结果 表明 , 信号 突变点即 对应折 弯 位置 , 检测误差范围为 - 0 . 60~ - 0. 04 mm. 关键词 : 超声波传感器 ; 折线焊缝跟踪 ; 快速傅里叶变换 ; 数字滤波 中图分类号: TG 151 文献标识码 : A 文章编号 : 0253- 360X ( 2010) 12- 0097- 04
3. 4 数字滤波 通过 M atlab 设计了巴特沃兹滤波器. 巴特沃兹 滤波器的特点是具有通带内最大平坦的振幅特性 , 而且随着频率的升高而单调下降. 以 500 cts / s为例 , 巴特沃兹滤波器设计如下. 采样频率 f s = 500 H z, 通带边界频率 W p = 2 H z, 阻带边界频率 W s = 5 H z. 通带波动设置为 0 . 1 dB, 最小阻带衰减设置为 25 dB. 滤波器系数为 b = 10
X ( k ) = DFT [ x ( n ) ] =
! x ( n)W
n= 0
kn N
, ( 1)
k = 0 , 1, ∀N - 1
kn N
式中 : W 为傅里叶算子 ; DFT 算法为离散信号的分 析从理论上提供了变换信息 , 但由于 DFT 算法运算 量大 ( 计算量与变化区间长度 N 的平方成正比 ), 运 算时间长 , 很难实现 . FFT 的出现使 DFT 的运算效 率提高 1~ 2个数量级, 为数字信号处理技术应用于 各种信号的实时处理创造了条件 . FFT 算法形式基本上可以分为两大类, 即时间 抽取法和频率抽取法 , 算法思想基本一致 . 取采样 范围长度 N 为 2 的 整数次方, 采样数不足补零 , 根 据 DFT 的 性质, 可以将 N 点 DFT 分解为两个 N /2 点的 DFT. N / 2点的 DFT 又可以再分解成两个 N /4 点的 DFT 变换, 一直分解下去 , 最后 获得 N / 2 个 2 点的 DFT 变换. 3 . 3 . 2 采样数据的 FFT 处理 FFT 可以通过 M atlab 实现 . 采用 M atlab 对 3 个 速度下的传感器输出信号进行 FFT 处理得到的频 谱图如图 4 所示. 由图 4 可以看出, 500 脉冲 / s 速 度下功率谱密度最大的频率均在 0 . 1 H z附近 , 即为 目标信号 , 而 其它杂波信号的 功率谱密度都较 小. 同样处理 800脉冲 / s和 1 000 脉冲 / s速度下的采样 信号 , 目标信号频率非常接近 , 但影响较大的杂波信 号随着速度的提高频率也在提高 . 指令速度为 500 , 800 , 1 000 脉冲 / s时 , 影响较大的杂波信号频率分 别为 5 864 , 9 . 383 , 11 . 42 H z , 这些杂波信号的频率 与速度的大小近似成正比关系, 这说明该杂波信号
1 波纹板
试验采用的波纹板为 30 波纹板, 其具体尺寸
收稿日期 : 2009- 07- 21
98
焊
接
学
报
第 31 卷
在扇形导轨上转动. 整个运动过程中 , 超声波传感 器只沿 x 轴方向运动 . x 轴的驱动采用步进电机驱 动齿轮齿条 . 步进电动机的步进角为 1 . 8 , 电机细 分数为 40 . 电机的控制采用 PMAC2 PC I . 试验测 得焊接小车 在 x 轴上 运动 1 mm 平均 需要 53 ( 脉 冲 ).
0 序
言
如图 1 所示. 波纹板一般长数十米, 每条折线焊缝 有数十个周期 , 近两百个折弯点 . 冲模和板料送进 都存在误差, 如果不进行跟踪 , 折弯位置必然出现偏 差, 使焊缝偏移焊接位置 .
波纹板广泛应用于集装箱、 工业厂房、 展厅屋顶 等 , 但波纹板的焊接主要为焊条电弧焊. 提高波纹 板焊接自动化程度的关键是折线焊缝的跟踪 . 焊缝 跟踪常用传感器主要有电弧、 光学、 声学、 力学传感 器等. 南昌大学江西省焊接机器人重点实验室
第 12 期
田松亚, 等 : 超声波传感器在波纹板折线焊缝跟踪中的应用
99
是由驱动部分振动产生的机械波信号, 完全可以通 过数字滤波器滤去.
4 试验结果与分析
由于波纹板折线焊缝属于短线段、 多周期、 长焊 缝, 考虑到检测所有折弯点的计算量较大, 基于焊缝 折弯位置的周期性 , 每个波纹周期只检测一个折弯 位置 , 通过其几何尺寸推算另 3 个折弯位置, 这样可 以大大降低计算量 . 结合图 3 与图 5 , 可以看出超声 波信号在波纹板斜边与槽面形成的折弯处变化较为 明显 , 而在斜边与顶面形成的折弯处变化比较平缓. 造成这一现象的原因主要为波纹板是冲压成的, 折 弯位置实际上是圆角过渡 . 超声波指向性好, 界面
图 3 指令速度 500脉冲 /s 采样数据波形 Fi g 3 Samp le da ta wave form
3 . 3 快速傅里叶变换 ( FFT) 3 . 3 . 1 FFT 算法思想 离散 傅 里 叶 变 换 ( discrete fourier transfor m,
图 2 焊接机构示意m
第 3 1卷第 12 期 2 0 1 0 年 1 2月
焊
接
学
报
V o. l 3 1 No. 12 December 2010
TRANSACT IONS OF THE CH I NA W ELDING I N ST ITUT ION
超声波传感器在波纹板折线焊缝跟踪中的应用
田松亚 ,
摘
1
史如森 ,
1
朱晓华 ,
DFT )定义为 : 设 x ( n) 是一个长度为 n 的有限序列, 则 x ( n ) 的 N 点离散傅里叶变换为
N- 1
3 试验与分析
3. 1 数据采集过程 数据采集采用 T I 公司的 TM S320LF2407A 试验 板 . 该试验板 CPU 频率为 40 MH z , 有两个时间管理 模块 ( EV) , 每个时间管理模块有两个计数器 ( Tx ) , 数模转换模块 ( ADC ) , 可以 方便的实现模数转换 . 试验采用 T 1 计时器 , 128分频, 连续增计数模式 , 每 中断一次进行一次采样 , 采样频率与驱动速度相匹 配 , 为 1 脉冲距 离采 样一次 , 采样 分辨率 为 0 . 019 mm. ADC 接入超声波传感器输出模拟信号 , 采用级 连模式 , 预定标系数为 9 , 即 500 ns. 超声波传感器 信号输出采用电压模式, 由于 DSP 的最高允许电压 为 3. 3 V, 因此对 DSP输入端接收信号进行分压 , 最 大为 2 . 8 V. 3. 2 采集的数据 在指令速度分别为 500 , 800 , 1 000 脉冲 / s 3 种 情况下 , 使小车从指定位置开始沿 x 轴方向运动 , 位 移超过一个周期, 采用超声波传感器进行跟踪. 每 个速度下重复采样 5次 . 对采集的试验数据绘制波 形图, 通过对比这些波形图可以发现 , 试验重复性效 果良好 . 3 种速度下的试验数据波形 图基本一致 , 其中指令速度为 500 脉冲 / s 数据波形图如图 3 所 示 . 由图 3 可知, 采样数据波形与波纹板的形状相 似 , 但是整个波形中杂波较多, 掩盖了折弯点信息 , 必须进行滤波处理. 首先要分析有效信号和干扰信 号的频率特征.
图 4 指令速度 500脉冲 /s 采样信号频谱图 F ig 4 Freq uency spectrog ram of samp l e da ta a t 500 cts
反射遵循波的反射原理 , 检测斜边时形成盲区, 但由 于波纹板表面并不是一个理想镜面 , 所以实际上斜 边处会有部分超声波发生散射而被传感器检测到, 使得检测信号不断跳变 . 顶面与斜边交接处圆角是 一个凸面 , 超声波传播到该凸面时 , 会被凸面散射, 使得可接收反射信号的范围增大 , 并且声压分布比 较均匀, 所以超声波传感器检测该折弯位置时信号 跳变会延迟发生, 表现为折弯位置处信号缓慢增大; 槽边和斜边的交接处圆角是一个凹面 , 超声波传播 到凹面反射时 , 会被凹面聚焦 , 从而使得可接收反射 信号的范围减小 , 并且聚焦点处声压最大 . 所以选 择从槽面到斜边处的折弯位置进行检测 . 以所选折弯位置为对象, 选择一个包含该折弯 位置的范围, 进行超声波传感器数据采样, 分析波形 的跳变与折弯位置的关系. 由前述试验结果分析可 知, 速度对信号采集的影响主要表现在驱动部分振 动产生的机械波的频率上, 焊接速度越大, 该机械波 的频率越高. 考虑到目标波形频率在 0 . 1 H z左右, 远低于 500 脉冲 / s时的机械波频率. 实际焊接时的 焊接速度为 1 . 2 ~ 1. 5 m /m in, 即 1 062 ~ 1 328 脉 冲 / s. 因此, 为了尽可能多的采集细节信号 , 试验选 择指令速度为 500 脉冲 / s时 , 超声波传感器从指定 起点前进 2 770 脉冲 . 重复采集 5 组试验数据 . 按 照上面的滤波方法对数据滤波. 试验数据重复度较 好, 其中一 组数据 波形图 和滤 波后 数据 波形图 如 图 6 所示. 为了表述方便, 图 6b 中, 波形从平缓突 变下降的点称为跳变点. 5 组试验数据滤波后的跳 变点横坐标数值分别为 1 421 , 1 423 , 1 440 , 1 452 , 1 425 . 试验测得采样的开始点到折 弯位置的位移为 27 . 4 mm, 采样总位移为 52 . 2 mm, 如图 7 所示 . 则 折弯位置对应的采样点为