复合材料模压成型模具结构及分类
复合材料成型工艺与设备之模压设备(PPT 36页)

5.1 概述
5.1.1 模具的作用 要求
模压成型的主要工艺设备,使能 制造出一定形状、尺寸、外观及各 种性能均满足设计要求的制品。
(1) 能承受20一80MPa的高压; (2) 能耐成型时模塑料对模具的摩擦;
(3) 在175—200℃温度时,其硬度应无显著下降; (4) 能耐模塑料及脱模剂的化学腐蚀; (5) 表面光滑; (6) 尺寸符合制品要求; (7) 在结构上要有利于模压料的流动及制品的取出,并能 满足工艺操作上的要求。
•
30、如果你相信自己,你可以做任何事 。
•
31、天空黑暗到一定程度,星辰就会熠 熠生辉 。
•
32、时间顺流而下,生活逆水行舟。
•
33、生活充满了选择,而生活的态度就 是一切 。
•
34、人各有志,自己的路自己走。
•
35、别人的话只能作为一种参考,是不 能左右 自己的 。
•
36、成功来自使我们成功的信念。
一个水平分型面敞 开式压模
两个水平分型面闭 合式压模
为减少溢料量,密合面应光滑平整。为了减薄毛边 厚度,密合面面积不宜太大,可设计成紧围在制品周边 的环形。
24
不溢式压模配合形式:凸凹 模之间不存在挤压面,凸凹模之 间需要留有一定的间隙(0.025~ 0.075mm),便于气体排出和溢 料,并有利于开模。
29
使用液压系统的另外一个好处就是能使力量成倍的增加。在液压系 统中只需要改变一个活塞和液压缸的尺寸。
30
分类
A 以控制方式分类
(1) 手控式
采用手动方法控制液压系统中的阀及启 闭各种电器装置来实现操作。
(2)半自动式
除了加料及取出制品外,其 余有关压力操作加压、保压、泄 压,制品顶出及温度、压力、时 间的控制都自动进行。
常见模具的分类及结构模具的装配
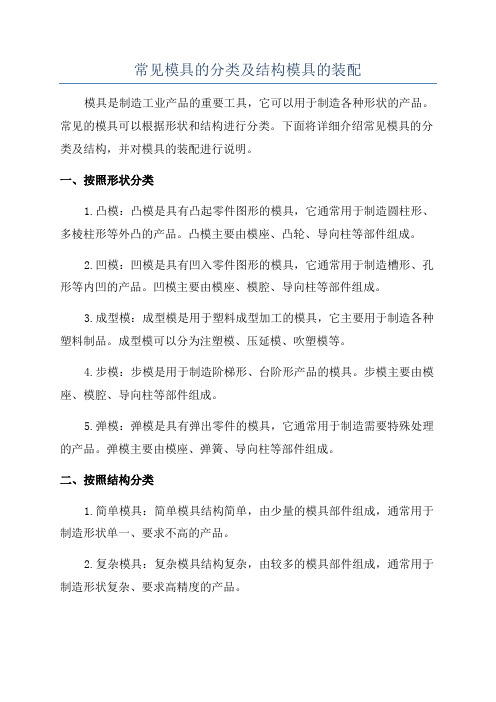
常见模具的分类及结构模具的装配模具是制造工业产品的重要工具,它可以用于制造各种形状的产品。
常见的模具可以根据形状和结构进行分类。
下面将详细介绍常见模具的分类及结构,并对模具的装配进行说明。
一、按照形状分类1.凸模:凸模是具有凸起零件图形的模具,它通常用于制造圆柱形、多棱柱形等外凸的产品。
凸模主要由模座、凸轮、导向柱等部件组成。
2.凹模:凹模是具有凹入零件图形的模具,它通常用于制造槽形、孔形等内凹的产品。
凹模主要由模座、模腔、导向柱等部件组成。
3.成型模:成型模是用于塑料成型加工的模具,它主要用于制造各种塑料制品。
成型模可以分为注塑模、压延模、吹塑模等。
4.步模:步模是用于制造阶梯形、台阶形产品的模具。
步模主要由模座、模腔、导向柱等部件组成。
5.弹模:弹模是具有弹出零件的模具,它通常用于制造需要特殊处理的产品。
弹模主要由模座、弹簧、导向柱等部件组成。
二、按照结构分类1.简单模具:简单模具结构简单,由少量的模具部件组成,通常用于制造形状单一、要求不高的产品。
2.复杂模具:复杂模具结构复杂,由较多的模具部件组成,通常用于制造形状复杂、要求高精度的产品。
3.组合模具:组合模具由多个模具部件组合而成,可以根据不同产品的要求进行组合和调整。
组合模具可以用于制造多种形状的产品。
4.附加模具:附加模具是用于辅助模具操作和加工的附属工具,它主要包括模模切割刀、导向柱、模间距调节器等。
模具的装配是将各个模具部件按照一定顺序进行组合和安装,使其构成一个完整的模具系统。
模具的装配需要遵循以下几个步骤:1.准备工作:对于新的模具部件,需要进行清洗和润滑处理,以确保其表面干净平整,并且能够顺利运动。
2.分析设计图纸:根据模具的设计图纸,分析各个模具部件的规格、尺寸和相对位置,确定正确的装配顺序和方法。
3.定位安装:根据设计要求,将模座固定在加工设备的工作台上,并使用夹具或螺丝将模具部件正确的定位和固定。
4.组合装配:根据装配图纸或指导书,按照正确的顺序和方法,将各个模具部件进行组合和安装。
模具结构形式
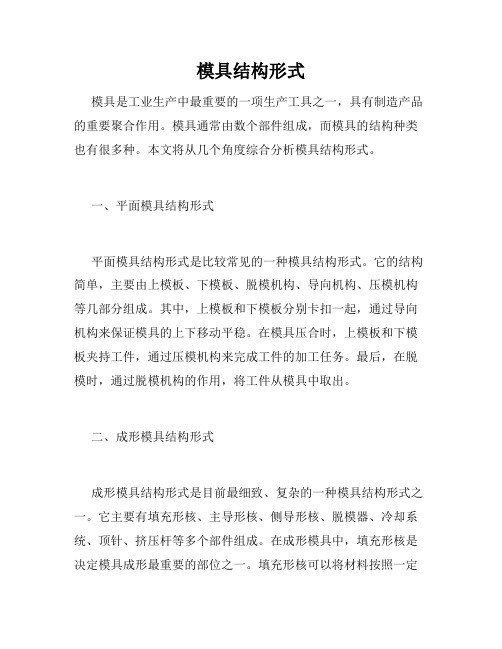
模具结构形式模具是工业生产中最重要的一项生产工具之一,具有制造产品的重要聚合作用。
模具通常由数个部件组成,而模具的结构种类也有很多种。
本文将从几个角度综合分析模具结构形式。
一、平面模具结构形式平面模具结构形式是比较常见的一种模具结构形式。
它的结构简单,主要由上模板、下模板、脱模机构、导向机构、压模机构等几部分组成。
其中,上模板和下模板分别卡扣一起,通过导向机构来保证模具的上下移动平稳。
在模具压合时,上模板和下模板夹持工件,通过压模机构来完成工件的加工任务。
最后,在脱模时,通过脱模机构的作用,将工件从模具中取出。
二、成形模具结构形式成形模具结构形式是目前最细致、复杂的一种模具结构形式之一。
它主要有填充形核、主导形核、侧导形核、脱模器、冷却系统、顶针、挤压杆等多个部件组成。
在成形模具中,填充形核是决定模具成形最重要的部位之一。
填充形核可以将材料按照一定的比例和形状填充到模具内。
主导形核辅助填充形核完成模具内的填充任务。
脱模器则是要将填充材料取出来,而冷却系统、顶针、挤压杆则是更好的完成了填充材料的加工任务。
三、复合模具结构形式复合模具的结构形式比较多,主要分两部分:连续成型模具和异型模具。
连续成型模具是利用一款模具完成多个加工任务的模具。
它主要包括钢带模、防水卷材模、塑料大件模、不锈钢卷材模等。
异形模具则是针对一些非规则形状产品进行开发设计的模具,这种模具的结构比较复杂,通常需要根据不同的需求来组合不同的部件。
四、注塑模具结构形式注塑模具结构形式也比较广泛,主要分为单面形心式模具、双面形心式模具、移动式模具等多种。
单面形心式模具因结构简单,加工成本低而在注塑领域中占据重要地位。
双面形心式模具则是用于注塑工艺比较复杂的产品,可以减少在共入口注塑过程中对产生的二次加工,提高模具的生产效率。
总结综上所述,模具结构形式多种多样,不同的模具结构形式适用于不同的产品制造过程。
在模具制作中,需要根据实际生产需求来选取模具的结构形式,以便更好地完成加工任务,提高生产效率。
模具结构基础知识
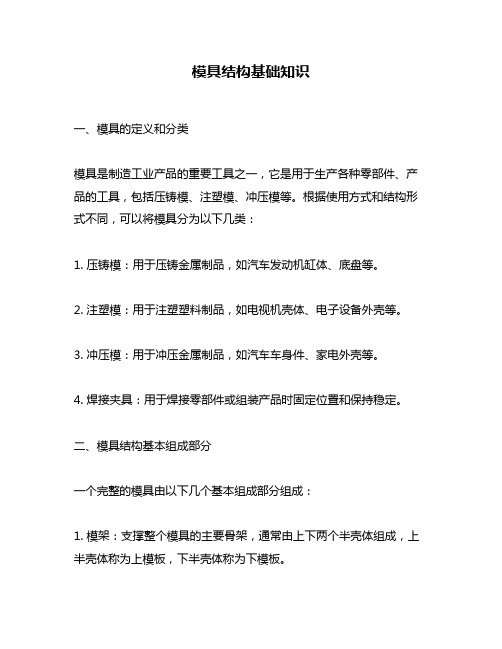
模具结构基础知识一、模具的定义和分类模具是制造工业产品的重要工具之一,它是用于生产各种零部件、产品的工具,包括压铸模、注塑模、冲压模等。
根据使用方式和结构形式不同,可以将模具分为以下几类:1. 压铸模:用于压铸金属制品,如汽车发动机缸体、底盘等。
2. 注塑模:用于注塑塑料制品,如电视机壳体、电子设备外壳等。
3. 冲压模:用于冲压金属制品,如汽车车身件、家电外壳等。
4. 焊接夹具:用于焊接零部件或组装产品时固定位置和保持稳定。
二、模具结构基本组成部分一个完整的模具由以下几个基本组成部分组成:1. 模架:支撑整个模具的主要骨架,通常由上下两个半壳体组成,上半壳体称为上模板,下半壳体称为下模板。
2. 模腔:用于成形产品的空间,在上下两个半壳体中间形成。
根据不同的产品形状和尺寸需求,可以设计出不同形状和尺寸的模腔。
3. 模仁:用于成形产品的核心部分,通常安装在上模板上,与模腔配合使用。
4. 引导柱和导套:引导柱是固定在上下两个半壳体中间,用于保持模具的位置和稳定性;导套则是安装在引导柱上,用于保持引导柱与半壳体之间的间隙,以便半壳体之间的移动。
5. 凸模和凹模:凸模是安装在下模板上的零件,用于成形产品表面;凹模则是安装在上模板上的零件,用于成形产品内部和底部。
6. 夹具和顶针:夹具是用于固定原材料或成品,保持其位置稳定;顶针则是用于将成品从模腔中顶出来。
三、常见的模具结构类型1. 平面式结构:适合制造平面形状、简单结构的产品。
由一个平面型下模板和一个平面型上模板组成。
2. 拉伸式结构:适合制造长条状、管状等拉伸型产品。
由一个拉伸型下模板和一个拉伸型上模板组成。
3. 斜侧式结构:适合制造斜侧形状、倾斜角度较大的产品。
由一个斜侧型下模板和一个斜侧型上模板组成。
4. 旋转式结构:适合制造圆柱形、球形等旋转型产品。
由一个圆柱型下模板和一个圆柱型上模板组成。
四、常见的模具材料1. 铝合金:轻质、导热性能好,适用于制造小批量生产的零件或产品。
复合模模具结构

复合模模具结构复合模具结构是一种常见的模具结构形式,也是模具行业中技术含量较高的一种。
复合模具结构是指模具由多个独立部件组成,每个部件都具有独立的功能,通过相互组合形成完整的模具。
这种模具结构相比传统的单一结构模具,具有更高的灵活性和可变性,并且可以适应不同形状和尺寸的工件加工需求。
复合模具结构的主要组成部分包括定位部件、顶出部件和工作部件。
定位部件主要用于确保工件在模具中的位置准确,包括定位销、定位块等。
顶出部件主要用于将加工完成的工件顶出模具,包括顶出销、顶针等。
工作部件是模具的主要部分,用于实现对工件的加工,包括模板、芯片、侧滑块等。
复合模具结构的优点在于可以根据不同工件的加工需求进行灵活组合,实现多工位、多工序的加工。
比如,通过更换不同的工作部件,可以实现对不同形状的工件进行加工。
这种灵活性使得复合模具结构在多品种、小批量生产的情况下更加适用。
另外,复合模具结构的使用还可以提高模具的使用寿命和经济效益。
由于模具的各个部件都是独立的,如果某个部件损坏或磨损,可以只更换该部件,而无需更换整个模具,降低了成本。
同时,由于工作部件可以根据需要进行组合,可以减少模具的数量和占地面积,节约了资源。
当然,复合模具结构的设计和制造也需要更高的技术要求。
各个部件之间的配合精度要求较高,需要保证定位精度和工作精度。
因此,在制造复合模具时,需要注意材料的选择、加工工艺的控制以及检测手段的完善,以确保模具的质量和可靠性。
总的来说,复合模具结构作为一种新型的模具结构形式,在模具行业发展中具有重要意义。
其灵活性、可变性和经济效益使得它在多品种、小批量生产中具有广泛应用前景。
然而,要与时俱进,不断提高设计和制造水平,以满足不断变化的市场需求。
复合材料的模压成型技术

复合材料的模压成型技术复合材料是由两种或两种以上的不同材料组成的材料,具有比单一材料更优越的性能。
模压成型是一种常用的复合材料制备技术,通过在模具中对复合材料进行加热和压力处理,使其固化成特定形状的产品。
下面将详细介绍复合材料的模压成型技术。
模压成型技术是一种传统且成熟的复合材料制备方法,适用于各种复材的生产。
其基本工艺包括:制备模具、预热模具、预切制复材、层堆压、模热固化、冷却脱模、再加工等步骤。
下面将分别介绍每个步骤的具体操作方法。
首先是制备模具。
模具是模压成型技术中非常重要的一部分,其质量和精度会直接影响最终产品的质量。
制备模具时,需要根据产品的要求设计和制造成型模具,通常采用金属材料制作,如铝合金、钢材等。
接下来是预热模具。
模具在使用前需要对其进行预热处理,以提高产品成型效果和减少模具损耗。
预热温度一般根据复合材料的热固化温度来确定,通常在50-100摄氏度之间。
然后是预切制复材。
复合材料通常是由纤维增强材料和树脂基体组成的,为了方便模压成型,需要将复材事先切成与产品形状相近的形状。
预切制复材时要注意保持纤维的方向和层间粘接质量,以确保最终产品的强度和性能。
层堆压是模压成型的核心步骤,也是影响成型质量的关键环节。
层堆压时,将预切制好的复材层叠放在模具中,注意纤维方向和树脂基体的均匀分布。
并在每一层复材之间涂上树脂胶水,以增强层间粘接力。
接着是模热固化。
层堆压好的复材在模具中进行加热和压力处理,以使树脂基体固化成型。
模具的温度和压力要根据树脂基体的热固化曲线和产品要求来确定。
一般情况下,模具温度在120-180摄氏度之间,压力在0.5-2.0MPa之间。
冷却脱模是使产品从模具中取出的最后一个步骤。
脱模时要注意避免产品变形和破损,可以采用自然冷却或水冷却的方法。
同时,也可以根据产品的要求进行一些后续处理,如修磨、修边、打孔等工艺。
最后是再加工。
模压成型的产品可能会因为形状和尺寸的要求不完全符合而需要进行一些再加工。
模压成型工艺
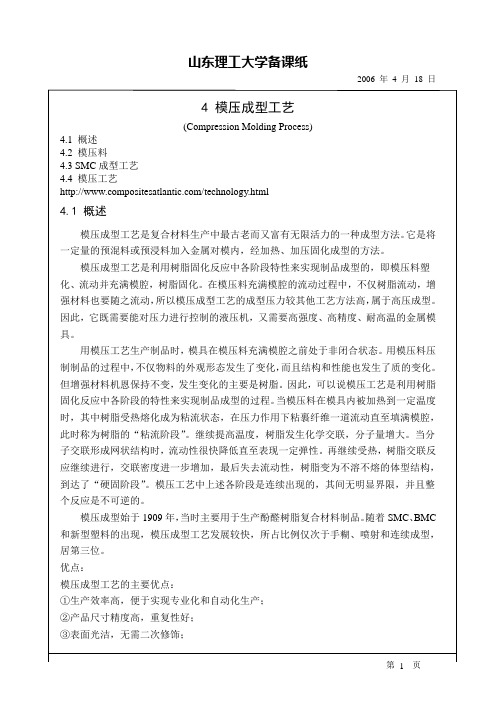
4 模压成型工艺(Compression Molding Process)4.1 概述4.2 模压料4.3 SMC成型工艺4.4 模压工艺/technology.html4.1 概述模压成型工艺是复合材料生产中最古老而又富有无限活力的一种成型方法。
它是将一定量的预混料或预浸料加入金属对模内,经加热、加压固化成型的方法。
模压成型工艺是利用树脂固化反应中各阶段特性来实现制品成型的,即模压料塑化、流动并充满模腔,树脂固化。
在模压料充满模腔的流动过程中,不仅树脂流动,增强材料也要随之流动,所以模压成型工艺的成型压力较其他工艺方法高,属于高压成型。
因此,它既需要能对压力进行控制的液压机,又需要高强度、高精度、耐高温的金属模具。
用模压工艺生产制品时,模具在模压料充满模腔之前处于非闭合状态。
用模压料压制制品的过程中,不仅物料的外观形态发生了变化,而且结构和性能也发生了质的变化。
但增强材料机恩保持不变,发生变化的主要是树脂。
因此,可以说模压工艺是利用树脂固化反应中各阶段的特性来实现制品成型的过程。
当模压料在模具内被加热到一定温度时,其中树脂受热熔化成为粘流状态,在压力作用下粘裹纤维一道流动直至填满模腔,此时称为树脂的“粘流阶段”。
继续提高温度,树脂发生化学交联,分子量增大。
当分子交联形成网状结构时,流动性很快降低直至表现一定弹性。
再继续受热,树脂交联反应继续进行,交联密度进一步增加,最后失去流动性,树脂变为不溶不熔的体型结构,到达了“硬固阶段”。
模压工艺中上述各阶段是连续出现的,其间无明显界限,并且整个反应是不可逆的。
模压成型始于1909年,当时主要用于生产酚醛树脂复合材料制品。
随着SMC、BMC 和新型塑料的出现,模压成型工艺发展较快,所占比例仅次于手糊、喷射和连续成型,居第三位。
优点:模压成型工艺的主要优点:①生产效率高,便于实现专业化和自动化生产;②产品尺寸精度高,重复性好;③表面光洁,无需二次修饰;④能一次成型结构复杂的制品;⑤因为批量生产,价格相对低廉。
复合材料芯模结构
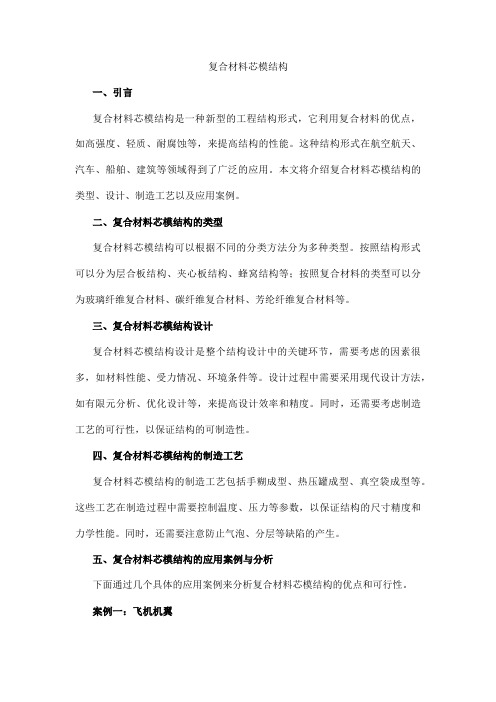
复合材料芯模结构一、引言复合材料芯模结构是一种新型的工程结构形式,它利用复合材料的优点,如高强度、轻质、耐腐蚀等,来提高结构的性能。
这种结构形式在航空航天、汽车、船舶、建筑等领域得到了广泛的应用。
本文将介绍复合材料芯模结构的类型、设计、制造工艺以及应用案例。
二、复合材料芯模结构的类型复合材料芯模结构可以根据不同的分类方法分为多种类型。
按照结构形式可以分为层合板结构、夹心板结构、蜂窝结构等;按照复合材料的类型可以分为玻璃纤维复合材料、碳纤维复合材料、芳纶纤维复合材料等。
三、复合材料芯模结构设计复合材料芯模结构设计是整个结构设计中的关键环节,需要考虑的因素很多,如材料性能、受力情况、环境条件等。
设计过程中需要采用现代设计方法,如有限元分析、优化设计等,来提高设计效率和精度。
同时,还需要考虑制造工艺的可行性,以保证结构的可制造性。
四、复合材料芯模结构的制造工艺复合材料芯模结构的制造工艺包括手糊成型、热压罐成型、真空袋成型等。
这些工艺在制造过程中需要控制温度、压力等参数,以保证结构的尺寸精度和力学性能。
同时,还需要注意防止气泡、分层等缺陷的产生。
五、复合材料芯模结构的应用案例与分析下面通过几个具体的应用案例来分析复合材料芯模结构的优点和可行性。
案例一:飞机机翼飞机机翼是复合材料芯模结构应用的重要领域之一。
传统的金属机翼重量大、刚度低,而复合材料芯模结构的机翼则具有重量轻、强度高、抗疲劳性能好等优点。
在飞机机翼中采用复合材料芯模结构可以减轻机翼重量,提高飞行性能和燃油效率。
同时,还可以减少机翼的维护和维修成本。
因此,复合材料芯模结构在飞机机翼中得到了广泛应用。
案例二:汽车车身汽车车身是复合材料芯模结构应用的另一个重要领域。
传统的汽车车身重量大、刚度低,而复合材料芯模结构的汽车车身则具有重量轻、强度高、抗冲击性能好等优点。
在汽车车身中采用复合材料芯模结构可以提高汽车的燃油效率,减少排放,同时还可以提高汽车的碰撞安全性。
复合材料成型工艺与设备之模压设备
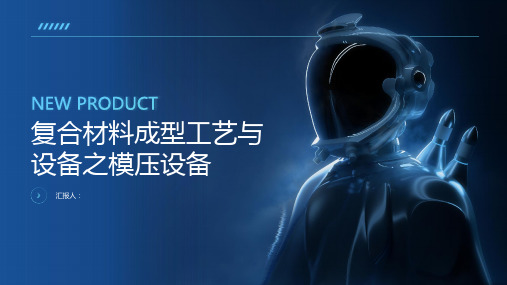
பைடு நூலகம் 复合材料模压设备 结构与特点
主机结构:主要包括加热系统、压 力系统、控制系统等
压力系统:采用液压或气压传动, 实现压力的精确控制和快速响应
添加标题
添加标题
添加标题
添加标题
加热系统:采用电加热或蒸汽加热, 实现快速升温和精确控温
控制系统:采用PLC或计算机控制, 实现自动化生产,提高生产效率和 质量稳定性。
市场需求持续增长:随着复合材料在汽 车、航空、建筑等领域的应用越来越广 泛,模压设备的市场需求将持续增长。
技术升级:随着科技的发展,模压设备将 不断升级,提高生产效率和降低生产成本。
市场竞争加剧:随着市场的扩大,越来越 多的企业进入模压设备市场,市场竞争将 加剧。
环保要求提高:随着环保意识的提高,模 压设备生产企业需要更加注重环保问题, 提高设备的环保性能。
准备材料:将复合材料按照配方进行混合,并准备模具 预热模具:将模具加热至一定温度,使材料在模具中充分流动 填充材料:将混合好的材料倒入模具中,并使材料在模具中均匀分布 加压成型:在模具上加压,使材料在压力作用下充分流动并固化 冷却脱模:将成型好的复合材料从模具中取出,并进行冷却处理 后处理:对成型好的复合材料进行打磨、抛光等处理,使其达到使用要
19世纪初: 模压设备 开始出现, 主要用于 生产橡胶 制品
20世纪初: 模压设备 开始应用 于塑料制 品生产
20世纪50 年代:模 压设备开 始应用于 复合材料 生产
20世纪70 年代:模压 设备开始采 用计算机控 制,提高了 生产效率和 质量
20世纪90 年代:模压 设备开始采 用自动化生 产线,提高 了生产效率 和降低了生 产成本
21世纪初: 模压设备开 始采用环保 材料和节能 技术,提高 了环保性能 和节能效果
模具基本结构及分类
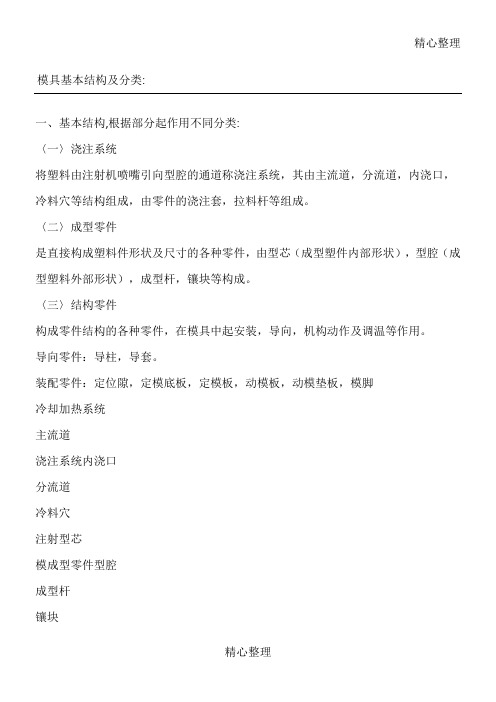
它是指构成模具结构的各种零件,包括:导向、脱模、抽芯以及分型的各种零件。如前后夹板、前后扣模板、承压板、承压柱、导向柱、脱模板、脱模杆及回程杆等。
1.导向部件
为了确保动模和定模在合模时能准确对中,在模具中必须设置导向部件。在注塑模中通常采用四组导柱与导套来组成导向不见,有时还需在动模和定模上分别设置互相吻合的内、外锥面来辅助定位。
4.浇口
它是接通主流道(或分流道)与型腔的通道。通道的截面积可以与主流道(或分流道)相等,但通常都是缩小的。所以它是整个流道系统中截面积最小的部分。浇口的形状和尺寸对制品质量影响很大。
浇口的作用是:
A、控制料流速度:.
B、在注射中可因存于这部分的熔料早凝而防止倒流:
C、使通过的熔料受到较强的剪切而升高温度,从而降低表观粘度以提高流动性:
浇注系统是指塑料从射嘴进入型腔前的流道部分,包括主流道、冷料穴、分流道和浇口等。成型零件是指构成制品形状的各种零件,包括动模、定模和型腔、型芯、成型杆以及排气口等。典型塑模结构如图示。
一.浇注系统
浇注系统又称流道系统,它是将塑料熔体由注射机喷嘴引向型腔的一组进料通道,通常由主流道、分流道、浇口和冷料穴组成。它直接关系到塑料制品的成型质量和生产效率。
2.推出机构
在开模过程中,需要有推出机构将塑料制品及其在流道内的凝料推出或拉出。推出固定板和推板用以夹持推杆。在推杆中一般还固定有复位杆,复位杆在动、定模合模时使推板复位。
3.侧抽芯机构
有些带有侧凹或侧孔地塑料制品,在被推出以前必须先进行侧向分型,抽出侧向型芯后方能顺利脱模,此时需要在模具中设置侧抽芯机构。
2、点浇口脱出模具(三板式模具)
3、带横向轴芯的分型模具
4、自动卸螺纹注射成型模具
试析复合材料的模具设计制造工艺
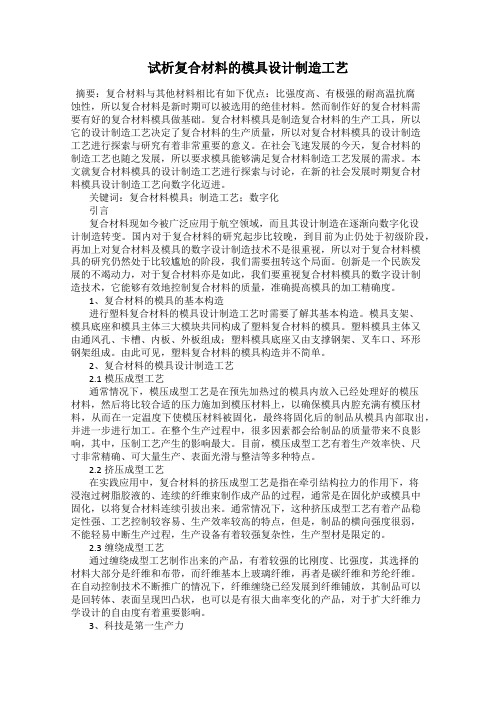
试析复合材料的模具设计制造工艺摘要:复合材料与其他材料相比有如下优点:比强度高、有极强的耐高温抗腐蚀性,所以复合材料是新时期可以被选用的绝佳材料。
然而制作好的复合材料需要有好的复合材料模具做基础。
复合材料模具是制造复合材料的生产工具,所以它的设计制造工艺决定了复合材料的生产质量,所以对复合材料模具的设计制造工艺进行探索与研究有着非常重要的意义。
在社会飞速发展的今天,复合材料的制造工艺也随之发展,所以要求模具能够满足复合材料制造工艺发展的需求。
本文就复合材料模具的设计制造工艺进行探索与讨论,在新的社会发展时期复合材料模具设计制造工艺向数字化迈进。
关键词:复合材料模具;制造工艺;数字化引言复合材料现如今被广泛应用于航空领域,而且其设计制造在逐渐向数字化设计制造转变。
国内对于复合材料的研究起步比较晚,到目前为止仍处于初级阶段,再加上对复合材料及模具的数字设计制造技术不是很重视,所以对于复合材料模具的研究仍然处于比较尴尬的阶段,我们需要扭转这个局面。
创新是一个民族发展的不竭动力,对于复合材料亦是如此,我们要重视复合材料模具的数字设计制造技术,它能够有效地控制复合材料的质量,准确提高模具的加工精确度。
1、复合材料的模具的基本构造进行塑料复合材料的模具设计制造工艺时需要了解其基本构造。
模具支架、模具底座和模具主体三大模块共同构成了塑料复合材料的模具。
塑料模具主体又由通风孔、卡槽、内板、外板组成;塑料模具底座又由支撑钢架、叉车口、环形钢架组成。
由此可见,塑料复合材料的模具构造并不简单。
2、复合材料的模具设计制造工艺2.1模压成型工艺通常情况下,模压成型工艺是在预先加热过的模具内放入已经处理好的模压材料,然后将比较合适的压力施加到模压材料上,以确保模具内腔充满有模压材料,从而在一定温度下使模压材料被固化,最终将固化后的制品从模具内部取出,并进一步进行加工。
在整个生产过程中,很多因素都会给制品的质量带来不良影响,其中,压制工艺产生的影响最大。
模具基本结构及分类
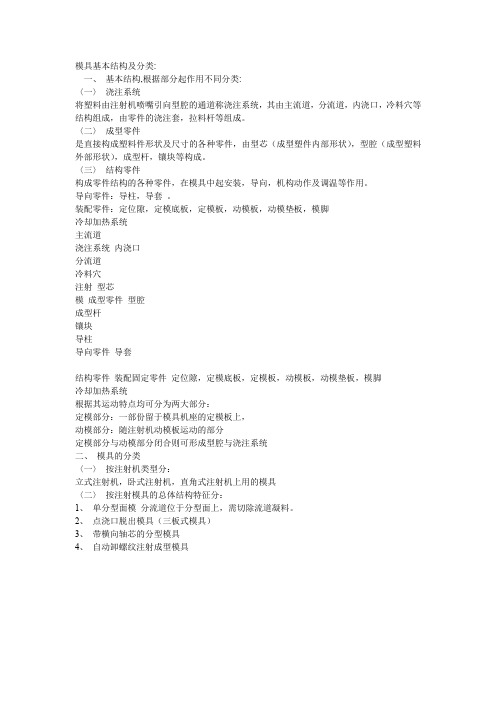
它是指构成模具结构的各种零件,包括:导向、脱模、抽芯以及分型的各种零件。如前后夹板、前后扣模板、承压板、承压柱、导向柱、脱模板、脱模杆及回程杆等。
1.导向部件
为了确保动模和定模在合模时能准确对中,在模具中必须设置导向部件。在注塑模中通常采用四组导柱与导套来组成导向不见,有时还需在动模和定模上分别设置互相吻合的内、外锥面来辅助定位。
D、便于制品与流道系统分离。浇口形状、尺寸和位置的设计取决于塑料的性质、制品的大小和结构。一般浇口的截面形状为矩形或圆形,截面积宜小而长度宜短,这不仅基于上述作用,还因为小浇口变大较容易,而大浇口缩小则很困难。浇口位置一般应选在制品最厚而又不影响外观的地方。浇口尺寸的设计应考虑到塑料熔体的性质。型腔它是模具中成型塑料制品的空间。用作构成型腔的组件统称为成型零件。各个成型零件常有专用名称。构成制品外形的成型零件称为凹模(又称阴模),构成制品内部形状(如孔、槽等)的称为型芯或凸模(又称阳模)。设计成型零件时首先要根据塑料的性能、制品的几何形状、尺寸公差和使用要求来确定型腔的总体结构。其次是根据确定的结构选择分型面、浇口和排气孔的位置以及脱模方式。最后则按控制品尺寸进行各零件的设计及确定各零件之间的组合方式。塑料熔体进入型腔时具有很高的压力,故成型零件要进行合理地选材及强度和刚度的校核。为保证塑料制品表面的光洁美观和容易脱模,凡与塑料接触的表面,其粗糙度Ra>0.32um,而且要耐腐蚀。成型零件一般都通过热处理来提高硬度,并选用耐腐蚀的钢材制造。
模具基本结构及分类:
一、基本结构,根据部分起作用不同分类:
〈一〉浇注系统
将塑料由注射机喷嘴引向型腔的通道称浇注系统,其由主流道,分流道,内浇口,冷料穴等结构组成,由零件的浇注套,拉料杆等组成。
复合材料成型工艺与设备之模压设备

复合材料成型工艺与设备之模压设备一、引言模压是一种常用的复合材料成型工艺,通过模压设备可以将复合材料加工成各种形状和尺寸的制品。
模压设备在复合材料制造行业中具有重要的作用,有效地提高了生产效率和产品质量。
本文将介绍复合材料模压设备的原理、分类和应用。
二、模压设备的原理模压设备是通过将预浸料(或干预浸料)放置在模具中,然后施加压力和温度,使其固化而成为制品。
模具是模压设备的关键组成部分,根据制品的形状和尺寸,选择不同的模具设计。
模具通常分为开放式模具和闭合式模具两种类型。
在模压过程中,可以通过施加一定的压力来减小材料的毛孔和缩孔,提高制品的密实性和强度。
同时,温度也起到促进固化反应的作用,加快制品的硬化速度。
模压设备通常配备了控制系统,可以精确地控制压力和温度的参数,以确保最佳的模压效果。
三、模压设备的分类根据模压设备的压力来源和结构形式,可以将其分为以下几类:1. 机械式模压设备机械式模压设备通过机械传动或液压系统施加压力。
它们通常由柱式压力机、液压机或板式压力机组成。
机械式模压设备结构简单、成本低廉,适用于小批量生产。
2. 液压式模压设备液压式模压设备通过液压系统施加压力。
它们可以提供更大的压力范围和更稳定的压力控制,适用于中大批量生产。
液压式模压设备通常具有更复杂的结构和控制系统。
3. 热压模压设备热压模压设备在施加压力的同时,提供高温环境,用于加速材料的固化反应。
它们通常由热压机和热板组成。
热压模压设备适用于热固性树脂复合材料的制造。
4. 真空模压设备真空模压设备在模压过程中提供真空环境,去除材料中的气体和空气。
它们通常由真空袋、真空吸附装置和真空泵组成。
真空模压设备适用于复合材料的脱气和密实性要求较高的制品。
四、模压设备的应用模压设备广泛应用于航空航天、汽车、船舶、电子、建筑等领域的复合材料制造。
具体应用包括但不限于以下几个方面:1. 航空航天领域模压设备在航空航天领域中用于制造飞机、直升机、卫星等复合材料结构件。
复合材料成型模具的知识
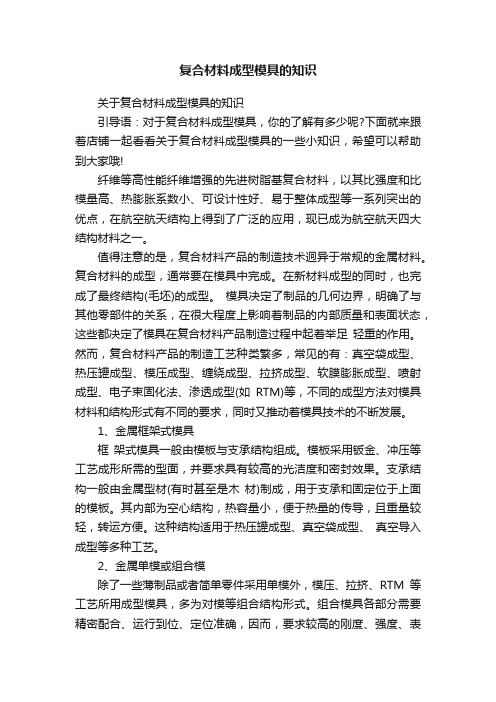
复合材料成型模具的知识关于复合材料成型模具的知识引导语:对于复合材料成型模具,你的了解有多少呢?下面就来跟着店铺一起看看关于复合材料成型模具的一些小知识,希望可以帮助到大家哦!纤维等高性能纤维增强的先进树脂基复合材料,以其比强度和比模量高、热膨胀系数小、可设计性好、易于整体成型等一系列突出的优点,在航空航天结构上得到了广泛的应用,现已成为航空航天四大结构材料之一。
值得注意的是,复合材料产品的制造技术迥异于常规的金属材料。
复合材料的成型,通常要在模具中完成。
在新材料成型的同时,也完成了最终结构(毛坯)的成型。
模具决定了制品的几何边界,明确了与其他零部件的关系,在很大程度上影响着制品的内部质量和表面状态,这些都决定了模具在复合材料产品制造过程中起着举足轻重的作用。
然而,复合材料产品的制造工艺种类繁多,常见的有:真空袋成型、热压罐成型、模压成型、缠绕成型、拉挤成型、软膜膨胀成型、喷射成型、电子束固化法、渗透成型(如RTM)等,不同的成型方法对模具材料和结构形式有不同的要求,同时又推动着模具技术的不断发展。
1、金属框架式模具框架式模具一般由模板与支承结构组成。
模板采用钣金、冲压等工艺成形所需的型面,并要求具有较高的光洁度和密封效果。
支承结构一般由金属型材(有时甚至是木材)制成,用于支承和固定位于上面的模板。
其内部为空心结构,热容量小,便于热量的传导,且重量较轻,转运方便。
这种结构适用于热压罐成型、真空袋成型、真空导入成型等多种工艺。
2、金属单模或组合模除了一些薄制品或者简单零件采用单模外,模压、拉挤、RTM等工艺所用成型模具,多为对模等组合结构形式。
组合模具各部分需要精密配合、运行到位、定位准确,因而,要求较高的刚度、强度、表面硬度、形位精度等,通常采用碳钢或铝合金材料。
虽然钢和铝表面光滑、致密、硬度大、易于脱模,清理模具时不易损坏,并且耐温性能好,但存在着和复合材料热膨胀系数不匹配的问题(钢的膨胀系数约为12×10-6/℃,铝的膨胀系数约为24×10-6/℃,碳纤维复合材料的膨胀系数一般都低于3.5×10-6/℃),导致制件型面精度不高,尺寸误差大、固化应力较大。
- 1、下载文档前请自行甄别文档内容的完整性,平台不提供额外的编辑、内容补充、找答案等附加服务。
- 2、"仅部分预览"的文档,不可在线预览部分如存在完整性等问题,可反馈申请退款(可完整预览的文档不适用该条件!)。
- 3、如文档侵犯您的权益,请联系客服反馈,我们会尽快为您处理(人工客服工作时间:9:00-18:30)。
复合材料模压成型模具结构及分类模具在压制过程中具有重要作用,典型模具由上模和下模两部分组成,上下模闭合使装于型腔内的模压料受热受压变为熔融态充满整个型腔。
当制品固化成型后上下模打开利用顶出装置顶出制品件。
压模可进一步分为如下各部件:型腔、加料室、导向机构、侧向分型抽心机构、脱模机构和加热系统。
一、模具结构
典型模具结构如图3.21所示。
它是由上模和下模两部分组成。
上、下模闭合使装于加料室和型腔中的模压料受热受压,变为熔融状态充满整个型腔。
当制品固化成型后,上、下模打开,利用顶出装置顶出制品。
模具可进一步分为如下各个部件。
复合材料模压成型的模具结构及分类
①型腔直接成“制品的部位。
图示的模具型腔由上凸模 3、下凸模8、凹模4构成。
②加料室指凹模4的上半部。
③导向机构由布置在模具上模周边的四根导柱6和装有导向套10的导柱孔组成。
④侧向分型抽芯机构模压带有侧孔和侧凹的制品,模具必须设有各种侧向分型抽芯机构,制品才能脱出。
⑤脱模机构由顶出板17、顶出杆11等零件组成。
⑥加热系统一般热固性模压成型需要在较高的温度下进行,因此,模具必须加热。
复合材料模压成型模具常见加热方式有:模温机加热、电加热、蒸汽加热等。
复合材料模压成型控温模温机
二、复合材料模压成型模具分类
(一) 根据与压机连接方式分类
①移动式模具属于外装卸模具。
模具不固定在压机上。
一般情况下,模具的分模、装料、闭合及成型后制品从模具中取出均在机外进行。
模具本身不带加热装置。
这种模具适用于压制批量不大的中小型制品。
移动式模具结构简单,制造周期短,造价低。
但是加料、开模、取件等工序均为手工操作,劳动强度大,生产效率低。
②固定式模具属于机内装卸的模具。
它固定在压机上,且本身带有加热装置。
整个生产过程即分模、装料、闭合、成型及顶出产品都在压机上进行。
固定式模具使用寿命长,适于生产批量大,尺寸较大的制品。
③半固定式模具这种模具介于上述两者之间,一般为上模固定在压机上,下模可以沿着导轨移动,用定位块定位。
(二)按分型面特征分类
分型面的作用是将已经成型好的制品从型腔中取出或者为满足安装嵌件及排气等成型的需要。
①水平分型面分型面平行于压机的工作台面。
②垂直分型面分型面垂直于压机的工作台面。
③复合分型面分型面既有平行于压机的工作台面的,也有垂直于压机的工作台面的。
(三)按上、下模闭合形式分
复合材料模压成型的模具结构
①敞开式模具如图3.22 (1)所示,该模具特点是没有加料室。
此类模具结构简单,造价低,耐用,易脱模,安装嵌件方便。
②密闭式模具如图 3.22(3)所示。
模具的加料室为型腔上部的延续部分,无挤压面。
压机所施加的压力全部作用在制品上。
模压料的溢出量非常少。
制品的密实性好,机械强度较高,且飞边在垂直
方向,易于去除。
这种模具适合成型形状复杂、薄壁、长流程的制品,也适用于流动性小、单位压力大,密度大的模压料。
其缺点是:加料量必须准确控制;模具凸模与加料室边壁摩擦,边壁容易损伤,在顶出时带有有损伤痕迹的加料室壁又容易将制品表面损伤。
③半密闭式模具如图3.22(3)所示。
该种模具型腔上有加料室,型腔内有挤出环,制品的密实性比敞开式模具成型的制品好,且易于保证高度方向尺寸精度,脱模时可以避免擦伤制品。
模具在压制过程中具有重要作用,典型模具由上模和下模两部分组成,上下模闭合使装于型腔内的模压料受热受压变为熔融态充满整个型腔。
当制品固化成型后上下模打开利用顶出装置顶出制品件。
压模可进一步分为如下各部件:型腔、加料室、导向机构、侧向分型抽心机构、脱模机构和加热系统。