湿式钙法、镁法、双碱法的比较
双碱法脱硫工艺简介
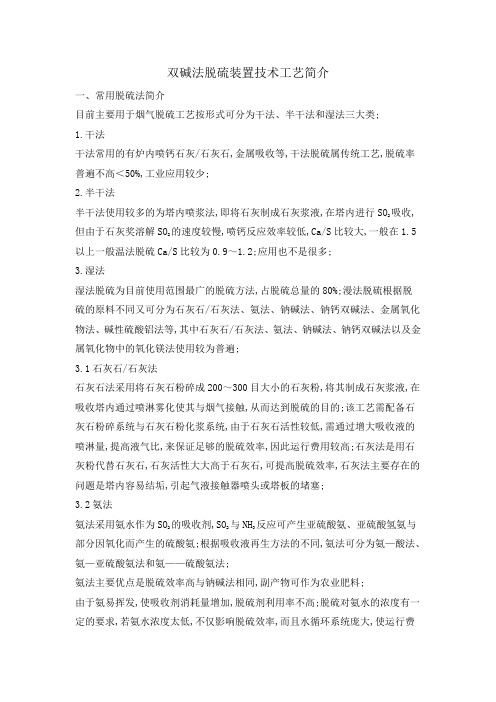
双碱法脱硫装置技术工艺简介一、常用脱硫法简介目前主要用于烟气脱硫工艺按形式可分为干法、半干法和湿法三大类;1.干法干法常用的有炉内喷钙石灰/石灰石,金属吸收等,干法脱硫属传统工艺,脱硫率普遍不高<50%,工业应用较少;2.半干法半干法使用较多的为塔内喷浆法,即将石灰制成石灰浆液,在塔内进行SO2吸收,但由于石灰奖溶解SO2的速度较慢,喷钙反应效率较低,Ca/S比较大,一般在1.5以上一般温法脱硫Ca/S比较为0.9~1.2;应用也不是很多;3.湿法湿法脱硫为目前使用范围最广的脱硫方法,占脱硫总量的80%;漫法脱硫根据脱硫的原料不同又可分为石灰石/石灰法、氨法、钠碱法、钠钙双碱法、金属氧化物法、碱性硫酸铝法等,其中石灰石/石灰法、氨法、钠碱法、钠钙双碱法以及金属氧化物中的氧化镁法使用较为普遍;3.1石灰石/石灰法石灰石法采用将石灰石粉碎成200~300目大小的石灰粉,将其制成石灰浆液,在吸收塔内通过喷淋雾化使其与烟气接触,从而达到脱硫的目的;该工艺需配备石灰石粉碎系统与石灰石粉化浆系统,由于石灰石活性较低,需通过增大吸收液的喷淋量,提高液气比,来保证足够的脱硫效率,因此运行费用较高;石灰法是用石灰粉代替石灰石,石灰活性大大高于石灰石,可提高脱硫效率,石灰法主要存在的问题是塔内容易结垢,引起气液接触器喷头或塔板的堵塞;3.2氨法氨法采用氨水作为SO2的吸收剂,SO2与NH3反应可产生亚硫酸氨、亚硫酸氢氨与部分因氧化而产生的硫酸氨;根据吸收液再生方法的不同,氨法可分为氨—酸法、氨—亚硫酸氨法和氨——硫酸氨法;氨法主要优点是脱硫效率高与钠碱法相同,副产物可作为农业肥料;由于氨易挥发,使吸收剂消耗量增加,脱硫剂利用率不高;脱硫对氨水的浓度有一定的要求,若氨水浓度太低,不仅影响脱硫效率,而且水循环系统庞大,使运行费用增大;浓度增大,势必导致蒸发量的增大,对工作环境产生影响,而且氨易与净化后烟气中的SO2反应,形成气溶胶,使得烟气无法达标排放;氨法的回收过程也是较为困难的,投资费用较高,需配备制酸系统或结晶回收装置需配备中和器、结晶器、脱水机、干燥机等,系统复杂,设各繁多,管理维护要求高;3.4金属氧化物法常用的金属氧化物法是氧化镁法,氧化镁与SO2反应得到亚硫酸镁与硫酸镁,它们通过锻烧可重新分解处氧化镁,同时回收较纯净的SO2气体,脱硫剂可循环使用;由于氧化镁活性比石灰水高,脱硫效率也较石灰法高;它的缺点是氧化镁回收过程需锻烧,工艺较复杂,但若直接采用抛弃法,镁盐会导致二次污染,总体运行费用也较高;3.5钠钙双碱法二、双碱法脱硫工艺1、什么是双碱法脱硫双碱法脱硫是指采用NaOH和石灰氢氧化钙两种碱性物质做脱硫剂的脱硫方法; 2、双碱法脱硫工艺原理主要工艺过程是:清水池一次性加入氢氧化钠溶剂制成氢氧化钠脱硫液循环水,用泵打入脱硫除尘器进行脱硫;3种生成物均溶于水;在脱硫过程中,烟气夹杂的烟道灰同时被循环水湿润而捕集进入循环水,从脱硫除尘器排出的循环水变为灰水稀灰浆;一起流入沉淀池,烟道灰经沉淀定期清除,回收利用,如制内燃砖等;上清液溢流进入反应池与投加的石灰进行反应,置换出的氢氧化钠溶解在循环水中,同时生成难溶解的亚硫酸钙、硫酸钙和碳酸钙等,可通过沉淀清除;可以回收,是制水泥的良好原料;因此可做到废物综合利用,降低运行费用;用NaOH脱硫,循环水基本上是NaOH的水溶液;在循环过程中对水泵、管道、设备均无腐蚀与堵塞现象,便于设备运行与保养;为保证脱硫除尘器正常运行,烟气排放稳定达标,确保脱硫剂有足够使用量是一个关键问题;脱硫剂用量计算如下:脱硫反应中,NaOH的消耗量是SO2和CO2与其反应的消耗量;用量需要过量5%以上按5%计算;前面计算的10 t/h锅炉烟气中SO2排放量为42 kg/h,CO2排放是为2 161 kg/h;SO2和CO2中和反应用氢氧化钠量为:80×42÷64+80×2 161÷44×105%=4 180 kg脱硫过程由于NaOH的转换实际消耗是石灰;折算成生石灰消耗量56×4180÷80=2 926 kg生石灰日消耗量为70 224 kg综上所述,脱硫过程的碱消耗量是很大的;但要保证脱硫效率,就必须要保证碱的用量,通过比较双碱法脱硫可以实现脱硫效率高,运行费用相对比较低,操作方便,无二次污染,废渣可综合利用;所以改进后的双碱法脱硫工艺是值得推荐和推广应用的;3、优势钠钙双碱法Na2CO3/CaOH2是在石灰法基础上结合钠碱法,利用钠盐易溶于水,在吸收塔内部采用钠碱吸收SO2,吸收后的脱硫液在再生池内利用较廉价的石灰进行再生,从而使得钠离子循环吸收利用;该工艺综合石灰法与钠碱法的特点,解决了石灰法的塔内易结垢的问题,又具备钠碱法吸收效率高的优点;脱硫副产物为亚硫酸钙或硫酸钙氧化后;亚硫酸钙配以合成树脂可生产一种称为钙塑的新型复合材料;或将其氧化后制成石膏;或者直接将其与粉煤灰混合,可增加粉煤灰的塑性,增加粉煤灰作为铺路底层垫层材料的强度;与氧化镁法相比,钙盐不具污染性,因此不产生废渣二次污染;双碱法烟气脱硫技术是为了克服石灰石—石灰法容易结垢的缺点而发展起来的;传统的石灰石/石灰—石膏法烟气脱硫工艺采用钙基脱硫剂吸收二氧化硫后生成的亚硫酸钙、硫酸钙,由于其溶解度较小,极易在脱硫塔内及管道内形成结垢、堵塞现象;结垢堵塞问题严重影响脱硫系统的正常运行,更甚者严重影响锅炉系统的正常运行;为了尽量避免用钙基脱硫剂的不利因素,钙法脱硫工艺大都需要配备相应的强制氧化系统曝气系统,从而增加初投资及运行费用,用廉价的脱硫剂而易造成结垢堵塞问题,单纯采用钠基脱硫剂运行费用太高而且脱硫产物不易处理,二者矛盾相互凸现,双碱法烟气脱硫工艺应运而生,该工艺较好的解决了上述矛盾问题;石灰石/石膏法的原理是:将石灰石粉加水或石灰石磨制为石灰石浆制成浆液作为吸收剂泵入吸收塔与烟气充分接触混合,烟气中的二氧化硫与浆液中的碳酸钙以及从塔下部鼓入的空气进行氧化反应生成硫酸钙,硫酸钙达到一定饱和度后,结晶形成二水石膏;经洗涤脱出二氧化硫的烟气经加热或不加热由烟囱排入大气;氨法脱硫工艺是以氨水为吸收剂,副产硫酸铵化肥;锅炉排出的烟气经烟气换热器降温到90-100℃,进入预洗涤器经洗涤后除去HCI和HF,洗涤后的烟气经过液滴分离器除去水滴进入前置洗涤器中;在前置洗涤器中,氨水自塔顶喷淋洗涤烟气,烟气中的SO2被洗涤吸收除去,经洗涤的烟气排出后经液滴分离器除去携带的水滴,进入脱硫洗涤器;在该洗涤器中烟气进一步被洗涤,经洗涤塔顶的除雾器除去雾滴,进入脱硫洗涤器;再经烟气换热器加热后经烟囱排放;洗涤工艺中产生的浓度约30%的硫酸铵溶液排出洗涤塔,可以送到化肥厂进一步处理或直接作为液体氮肥出售,也可以把这种溶液进一步浓缩蒸发干燥加工成颗粒、晶体或块状化肥出售;烟气循环流化床脱硫工艺由吸收剂制备、吸收塔、脱硫灰再循环、除尘器及控制系统等部分组成;该工艺一般采用干态的消石灰粉作为吸收剂,也可采用其它对二氧化硫有吸收反应能力的干粉或浆液作为吸收剂;由锅炉排出的未经处理的烟气从吸收塔即流化床底部进入;吸收塔底部为一个文丘里装置,烟气流经文丘里管后速度加快,并在此与很细的吸收剂粉末互相混合,颗粒之间、气体与颗粒之间剧烈摩擦,形成流化床,在喷入均匀水雾降低烟温的条件下,吸收剂与烟气中的二氧化硫反应生成CaSO3 和CaSO4;脱硫后携带大量固体颗粒的烟气从吸收塔顶部排出,进入再循环除尘器,被分离出来的颗粒经中间灰仓返回吸收塔,由于固体颗粒反复循环达百次之多,故吸收剂利用率较高;双碱法脱硫是指采用NaOH和石灰氢氧化钙两种碱性物质做脱硫剂的脱硫方法;双碱法脱硫一般只有一个循环水池,NaOH、石灰与除尘脱硫过程中捕集下来的烟灰同在一个循环池内混合,在清除循环水池内的灰渣时烟灰、反应生成物亚硫酸钙、硫酸钙及石灰渣和未完全反应的石灰同时被清除,清出的灰渣是一种混合物不易被利用而形成废渣;主要工艺过程是:清水池一次性加入氢氧化钠溶剂制成氢氧化钠脱硫液循环水,用泵打入脱硫除尘器进行脱硫;3种生成物均溶于水;在脱硫过程中,烟气夹杂的烟道灰同时被循环水湿润而捕集进入循环水,从脱硫除尘器排出的循环水变为灰水稀灰浆;一起流入沉淀池,烟道灰经沉淀定期清除,回收利用,如制内燃砖等;上清液溢流进入反应池与投加的石灰进行反应,置换出的氢氧化钠溶解在循环水中,同时生成难溶解的亚硫酸钙、硫酸钙和碳酸钙等,可通过沉淀清除;可以回收,是制水泥的良好原料;脱硫的方法其实有很多,主要的方法有,石灰石——石膏湿法CaCO3、石灰法也就市氧化钙法CaO、氨法NH3、双碱法NaOH/CaCO3、氧化镁法MgO;生石灰是CaO 熟石灰是CaOH2 石灰石主要成分是CaCO3CaO+H2O=CaOH2CaOH2+CO2=CaCO3+H2OCaCO3=CaO+CO2 反应条件是高温主要工艺过程是:清水池一次性加入氢氧化钠溶剂制成氢氧化钠脱硫液循环水,用泵打入脱硫除尘器进行脱硫;3种生成物均溶于水;在脱硫过程中,烟气夹杂的烟道灰同时被循环水湿润而捕集进入循环水,从脱硫除尘器排出的循环水变为灰水稀灰浆;一起流入沉淀池,烟道灰经沉淀定期清除,回收利用,如制内燃砖等;上清液溢流进入反应池与投加的石灰进行反应,置换出的氢氧化钠溶解在循环水中,同时生成难溶解的亚硫酸钙、硫酸钙和碳酸钙等,可通过沉淀清除;可以回收,是制水泥的良好原料;因此可做到废物综合利用,降低运行费用;用NaOH脱硫,循环水基本上是NaOH的水溶液;在循环过程中对水泵、管道、设备均无腐蚀与堵塞现象,便于设备运行与保养;为保证脱硫除尘器正常运行,烟气排放稳定达标,确保脱硫剂有足够使用量是一个关键问题;脱硫剂用量计算如下:脱硫反应中,NaOH的消耗量是SO2和CO2与其反应的消耗量;用量需要过量5%以上按5%计算;前面计算的10 t/h锅炉烟气中SO2排放量为42 kg/h,CO2排放是为2 161 kg/h; SO2和CO2中和反应用氢氧化钠量为:80×42÷64+80×2 161÷44×105%=4 180 kg脱硫过程由于NaOH的转换实际消耗是石灰;折算成生石灰消耗量56×4180÷80=2 926 kg生石灰日消耗量为70 224 kg综上所述,脱硫过程的碱消耗量是很大的;但要保证脱硫效率,就必须要保证碱的用量,通过比较双碱法脱硫可以实现脱硫效率高,运行费用相对比较低,操作方便,无二次污染,废渣可综合利用;所以改进后的双碱法脱硫工艺是值得推荐和推广应用的;物料就是氢氧化钠和氧化钙白灰;双碱法是采用钠基脱硫剂进行塔内脱硫,由于钠基脱硫剂碱性强,吸收二氧化硫后反应产物溶解度大,不会造成过饱和结晶,造成结垢堵塞问题;另一方面脱硫产物被排入再生池内用氢氧化钙进行还原再生,再生出的钠基脱硫剂再被打回脱硫塔循环使用;双碱法脱硫工艺降低了投资及运行费用,比较适用于中小型锅炉进行脱硫改造;双碱法烟气脱硫技术是利用氢氧化钠溶液作为启动脱硫剂,配制好的氢氧化钠溶液直接打入脱硫塔洗涤脱除烟气中SO2来达到烟气脱硫的目的,然后脱硫产物经脱硫剂再生池还原成氢氧化钠再打回脱硫塔内循环使用;脱硫工艺主要包括5个部分:1吸收剂制备与补充;2吸收剂浆液喷淋;3塔内雾滴与烟气接触混合;4再生池浆液还原钠基碱;5石膏脱水处理;双碱法烟气脱硫工艺同石灰石/石灰等其他湿法脱硫反应机理类似,主要反应为烟气中的SO2先溶解于吸收液中,然后离解成H+和HSO3-;SO2g= SO2lSO2aq+H2Ol = H++HSO3-=2H++SO32-;式1为慢反应,是速度控制过程之一;然后H+与溶液中的OH-中和反应,生成盐和水,促进SO不断被吸收溶解;具体反应2方程式如下:2NaOH + SO2 → Na2SO3 + H2ONa2SO3 + SO2 + H2O → 2NaHSO3脱硫后的反应产物进入再生池内用另一种碱,一般是CaOH2进行再生,再生反应过程如下:CaOH2 + Na2SO3 → 2 NaOH + CaSO3CaOH2 + 2NaHSO3 → Na2SO3 + CaSO3·1/2H2O +1/2H2O存在氧气的条件下,还会发生以下反应:CaOH2 + Na2SO3 + 1/2O2 + 2 H2O → 2 NaOH + CaSO4·H2O脱下的硫以亚硫酸钙、硫酸钙的形式析出,然后将其用泵打入石膏脱水处理系统或直接堆放、抛弃;再生的NaOH可以循环使用;工艺流程介绍来自锅炉的烟气先经过除尘器除尘,然后烟气经烟道从塔底进入脱硫塔;在脱硫塔内布置若干层根据具体情况定旋流板的方式,旋流板塔具有良好的气液接触条件,从塔顶喷下的碱液在旋流板上进行雾化使得烟气中的SO2与喷淋的碱液充分吸收、反应;经脱硫洗涤后的净烟气经过除雾器脱水后进入换热器,升温后的烟气经引风机通过烟囱排入大气;双碱法脱硫工艺流程图:最初的双碱法一般只有一个循环水池,NaOH、石灰和脱硫过程中捕集的飞灰同在一个循环池内混合;在清除循环池内的灰渣时,烟灰、反应生成物亚硫酸钙、硫酸钙及石灰渣和未反应的石灰同时被清除,清出的混合物不易综合利用而成为废渣;为克服传统双碱法的缺点,对其进行了改进;主要工艺过程是,清水池一次性加入氢氧化钠制成脱硫液,用泵打入吸收塔进行脱硫;三种生成物均溶于水,在脱硫过程中,烟气夹杂的飞灰同时被循环液湿润而捕集,从吸收塔排出的循环浆液流入沉淀池;灰渣经沉淀定期清除,可回收利用,如制砖等;上清液溢流进入反应池与投加的石灰进行反应,置换出的氢氧化钠溶解在循环水中,同时生成难溶解的亚硫酸钙、硫酸钙和碳酸钙等,可通过沉淀清除;3、工艺流程说明双碱法烟气脱硫工艺主要包括吸收剂制备和补充系统,烟气系统,SO2吸收系统,脱硫石膏脱水处理系统和电气与控制系统五部分组成;吸收剂制备及补充系统脱硫装置启动时用氢氧化钠作为吸收剂,氢氧化钠干粉料加入碱液罐中,加水配制成氢氧化钠碱液,碱液被打入返料水池中,由泵打入脱硫塔内进行脱硫,为了将用钠基脱硫剂脱硫后的脱硫产物进行再生还原,需用一个制浆罐;制浆罐中加入的是石灰粉,加水后配成石灰浆液,将石灰浆液打到再生池内,与亚硫酸钠、硫酸钠发生反应;在整个运行过程中,脱硫产生的很多固体残渣等颗粒物经渣浆泵打入石膏脱水处理系统;由于排走的残渣中会损失部分氢氧化钠,所以,在碱液罐中可以定期进行氢氧化钠的补充,以保证整个脱硫系统的正常运行及烟气的达标排放;为避免再生生成的亚硫酸钙、硫酸钙也被打入脱硫塔内容易造成管道及塔内发生结垢、堵塞现象,可以加装瀑气装置进行强制氧化或特将水池做大,再生后的脱硫剂溶液经三级沉淀池充分沉淀保证大的颗粒物不被打回塔体;另外,还可在循环泵前加装过滤器,过滤掉大颗粒物质和液体杂质;烟气系统, 锅炉烟气经烟道进入除尘器进行除尘后进入脱硫塔,洗涤脱硫后的低温烟气经两级除雾器除去雾滴后进入主烟道,经过烟气再热后由烟囱排入大气;当脱硫系统出现故障或检修停运时,系统关闭进出口挡板门,烟气经锅炉原烟道旁路进入烟囱排放;SO2吸收系统烟气进入吸收塔内向上流动,与向下喷淋的石灰石浆液以逆流方式洗涤,气液充分接触;脱硫塔采用内置若干层旋流板的方式,塔内最上层脱硫旋流板上布置一根喷管;喷淋的氢氧化钠溶液通过喷浆层喷射到旋流板中轴的布水器上,然后碱液均匀布开,在旋流板的导流作用下,烟气旋转上升,与均匀布在旋流板上的碱液相切,进一步将碱液雾化,充分吸收SO2、SO3、HCl和HF等酸性气体,生成NaSO3、NaHSO3,同时消耗了作为吸收剂的氢氧化钠;用作补给而添加的氢氧化钠碱液进入返料水池与被石灰再生过的氢氧化钠溶液一起经循环泵打入吸收塔循环吸收SO2;在吸收塔出口处装有两级旋流板或折流板除雾器,用来除去烟气在洗涤过程中带出的水雾;在此过程中,烟气携带的烟尘和其它固体颗粒也被除雾器捕获,两级除雾器都设有水冲洗喷嘴,定时对其进行冲洗,避免除雾器堵塞;脱硫产物处理系统&电气与控制系统脱硫系统的最终脱硫产物仍然是石膏浆固体含量约20%,具体成分为CaSO3、CaSO4,还有部分被氧化后的钠盐NaSO4;从沉淀池底部排浆管排出,由排浆泵送入水力旋流器;由于固体产物中掺杂有各种灰分及NaSO4,严重影响了石膏品质,所以一般以抛弃为主;在水力旋流器内,石膏浆被浓缩固体含量约40%之后用泵打到渣处理场,溢流液回流入再生池内;电气与控制系统脱硫装置动力电源自电厂配电盘引出,经高压动力电缆接入脱硫电气控制室配电盘;在脱硫电气控制室,电源分为两路,一回经由配电盘、控制开关柜直接与高压电机浆液循环泵相连接;另一回接脱硫变压器,其输出端经配电盘、控制开关柜与低压电器相连接,低压配电采用动力中心电动机控制中心供电方式;系统配备有低压直流电源为电动控制部分提供电源;脱硫系统的脱硫剂加料设备和旋流分离器实行现场控制,其它实行控制室内脱硫控制盘集中控制,亦可实现就地手动操作;正常运行时,由立式控制盘自动控制各个调节阀,控制脱硫系统石灰供应量和氢氧化钠补给量,要在锅炉负荷变动时能自动予以调节;烟气量的控制是根据锅炉排烟量,由引风机入口挡板通过锅炉负荷信号转换为烟气量与实际引入脱硫装置的烟气量反馈信号控制;吸收剂浆液流量的控制是通过进入脱硫装置的SO2量以及循环浆池中浆液的PH值来控制的;副产品浆液供给量通过吸收剂浆液的流量来控制;除雾装置清洗水的流量、吸收室入口冲洗水的压力以及脱水机排出液流量单独控制;脱硫塔底部的液位亦属于单独控制,即通过补给水量来控制;吸收剂浆池浓度的控制由补给水量调节给料器的转速以控制石灰加入量,继而达到控制浓度的目的;吸收室出口除雾器的清洗是按一定的时间间隔开关喷水阀用补充给水进行冲洗;二次污染的解决问题:采用氢氧化钠作为脱硫剂,在脱硫塔内吸收二氧化硫反应速率快,脱硫效率高,但脱硫的产物Na2SO4很难进行处理,极易造成严重的二次污染问题;采用双碱法烟气脱硫工艺,用氢氧化钠吸收二氧化硫后的产物用石灰来再生,只有少量的Na2SO4被带入石膏浆液中,这些掺杂了少量Na2SO4的石膏浆液用泵打入旋流分离器中进行固液分离,分离的大量的含水率较低的固体残渣被打到渣场进行堆放,溶液流回再生池继续使用,因此不会造成二次污染;5、工艺特点与石灰石或石灰湿法脱硫工艺相比,双碱法原则上有以下优点1用NaOH脱硫,循环水基本上是NaOH的水溶液,在循环过程中对水泵、管道、设备均无腐蚀与堵塞现象,便于设备运行与保养2吸收剂的再生和脱硫渣的沉淀发生在塔外,这样避免了塔内堵塞和磨损,提高了运行的可靠性,降低了操作费用;同时可以用高效的板式塔或填料塔代替空塔,使系统更紧凑,且可提高脱硫效率;3钠基吸收液吸收SO2速度快,故可用较小的液气比,达到较高的脱硫效率,一般在90%以上;对脱硫除尘一体化技术而言,可提高石灰的利用率;缺点是:NaSO3氧化副反应产物Na2SO4较难再生,需不断的补充NaOH或Na2CO3而增加碱的消耗量;另外,Na2SO4的存在也将降低石膏的质量双碱法脱硫技术是国内外运用的成熟技术,是一种特别适合中小型锅炉烟气脱硫技术,具有广泛的市场前景;3、工艺设备双碱法工艺系统主要由除尘装置、脱硫塔、供液系统、制浆系统、再生系统、水处理系统五部分组成;除尘装置与脱硫塔可采用我公司脱硫除尘一体化设备脱硫除尘一次完成;供液系统工艺水系统主要由工艺水管在路组成,根据实际情况需要配置工艺水泵及工艺水箱,可由厂区自来水管网引入;制浆系统脱硫剂配制系统包括斗式提升机、石灰料仓、螺旋输送机、石灰消化池、纯碱制备罐等;生石灰粉通过斗式提升机送入石灰料仓储存,再由螺旋输送机送入石灰消化池溶解后溢流至再生反应池,供脱硫液再生使用;螺旋输送机配变频器,可调节石灰投量;由于系统产生石膏沉淀带走水份中含有钠离子,系统需要补充少量纯碱;纯碱在制备罐中充分溶解后通过阀门调节投入至再生液池;脱硫剂主要为石灰和纯碱;纯碱为市卖98%工业纯碱,石灰粉粒径200目,CaO含量80%;纯碱启动时一次添加,以后少量补充随脱硫渣带走的部分,通过监测废液pH值的高低,控制电磁阀门对纯碱投量进行控制;再生系统再生反应系统包括再生反应池、搅拌器等;废液泵将部分废液输送入再生反应池,同时制备好的石灰浆液也加入到再生反应池,在池内发生再生反应,池内进行充分的机械搅拌;在再生反应中产生了可供脱硫的再生液,同时也生成大量的亚硫酸钙沉淀,再生反应池出口溢流入沉淀池;沉淀池上清液流入再生液储存池,由再生液输送泵输送至吸收塔循环水池;水处理系统废水处理系统包括沉淀池、刮泥机、PAC、PAM制备灌、压滤机、压滤机给料泵等;由再生反应池排入的浑浊浆液进入沉淀池,沉淀池为竖沉池;沉淀池底部安装刮泥机,沉淀物在此沉淀后由压滤机给料泵打入压滤机中;压滤机清水返回至再生反应池,泥饼的主要成分为亚硫酸钙与硫酸钙;泥饼含水率低,利于外运,泥饼可用于铺路或作为水泥添加剂;刮泥机用于浓缩池中的机械排泥;污水经池中心导流筒均匀流向池四周,随着流速的降低,污水中的悬浮物质沉淀于池底,池底刮泥机将沉淀污泥刮集到中心泥坑中,将沉降在池底上污泥刮集至积泥坑;特点:结构简单、重量轻;由于采用箱形结构,比传统机构重量大大减轻;维护简单方便,运行费用低;新型的传动机械,减速机采用行星减速机,安装方便、结构简单紧凑、效率高;电气元件均采用户外型,安全可靠,可随机控制或远程控制;。
氨法、镁法、钙法和双碱湿法脱硫方案比较
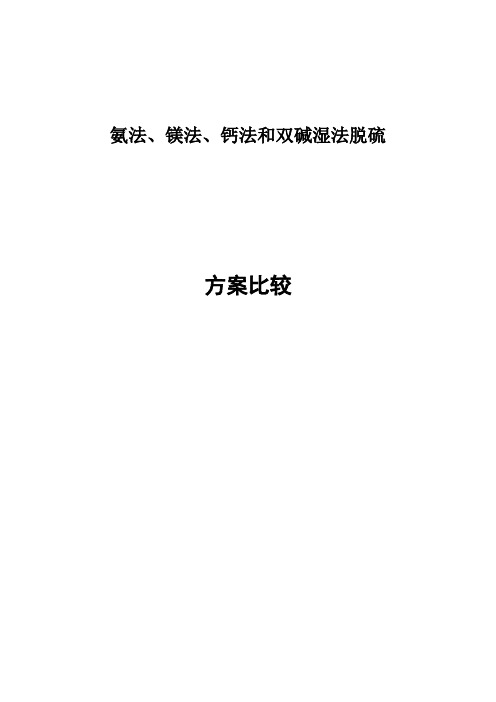
氨法、镁法、钙法和双碱湿法脱硫方案比较1. 湿法脱硫技术比较当前我国环境形势相当严峻,在新颁布的国家标准《火电厂大气污染物排放排放提出了更严格的要求,必须采用标准》(GB13223-2011)中,对电厂的SO2的排放浓度满足环保要求。
湿法脱硫技术,才能使SO2湿法工艺是指脱硫剂以液浆形式喷入反应器,而脱硫产品也以液浆形式排出的系统。
适用于中小型锅炉烟气脱硫技术,依采用的脱硫剂不同,常用的主要有石灰(石)法、氧化镁法、双碱法、氨法等几类。
湿法脱硫因其脱硫效率高、适应范围广而得到广泛运用,市场占有率为85%以上。
中小型脱硫产物的处理国内外多采用抛弃法处理。
A、石灰(石)/石膏湿法脱硫工艺石灰(石)/石膏湿法脱硫工艺是采用石灰石(CaCO3)或石灰(CaO)作脱硫吸收剂原料,经消化处理后加水搅拌制成氢氧化钙(Ca(OH)2)作为脱硫吸收浆。
石灰或吸收剂浆液喷入吸收塔,吸附其中的SO2气体,产生亚硫酸钙,进而氧化为硫酸钙(石膏)副产品。
该工艺的优点主要是:(1)脱硫效率高,在Ca/S比小于1.1的时候,脱硫效率可高达90%以上;(2)吸收剂利用率高,可达到90%;(3)吸收剂资源广泛,价格低廉;(4)适用于高硫燃料,尤其适用于大容量电站锅炉的烟气处理;(5)副产品为石膏,高品位石膏可用于建筑材料。
该工艺的缺点是:(1)系统复杂,占地面积大;(2)造价高,一次性投资大;(在美国,单位一般造价在$150— 200/kW;在中国,重庆珞璜电厂一期烟气脱硫工程2×360MW脱硫装置占电厂总投资的11.15%,太原第一热电厂高速平流简易湿式300MW机组的600000m3/h 脱硫装置的单位造价约RMB650元/kW,杭州半山电厂2×125MW和北京第一热电厂2×410t/h锅炉脱硫装置单位造价更高达RMB 1600/KW);(3)运行问题较多——由于副产品CaSO4易沉积和粘结,所以,容易造成系统积垢,堵塞和磨损;(而双减法在系统内产物是NaSO3,不会造成堵塞和积垢)(4)运行费用高,高液/气比所带来的电、水循环和耗量非常大;(5)副产品处理问题——目前,世界上对该副产品处理,主要采用抛弃和再利用两种方法:西欧和日本因缺乏石膏资源,所以用此副产品做建筑用石膏板,与此同时,当地建筑规范也为该产品的推广使用提供了方便。
[世界五百强企业绝密文件]脱硫对比9
![[世界五百强企业绝密文件]脱硫对比9](https://img.taocdn.com/s3/m/cd04f370a88271fe910ef12d2af90242a895ab76.png)
几种脱硫方案的对比1、烧结机各种烟气处理工艺方案比选目前世界上烟气脱硫工艺技术(FGD)有上百种,但是具有实用价值的仅十几种,它们分别适用于不同的场合和要求。
按脱硫过程及产物的干湿形态,烟气脱硫技术可分为湿法、半干法和干法等工艺。
干法/半干法烟气脱硫技术主要有旋转喷雾干燥法、炉内喷钙尾部烟气增湿法、循环流化床烟气脱硫技术、循环悬浮式半干法等,由于其副产品(脱硫灰)与粉煤灰在理化性质上的不同,只能得到低级的利用,因此通常把这些技术都归属于抛弃法的范畴。
传统的干法/半干法烟气脱硫技术的脱硫剂利用率较低,相对湿法脱硫技术,干法/半干法的脱硫效率较低,一般为70%左右,对于SO2排放标准较严的地区适用性较差。
湿法烟气脱硫技术为目前使用范围较广泛的方法,占脱硫设施总量的80%以上,它具有脱硫效率高、吸收剂利用率高等优点。
由于碱性吸收剂的不同,又可细分为石灰石/石灰-石膏法、氧化镁法、氨法等。
1.1常用烟气脱硫技术简介1、石灰石/石灰-石膏湿法石灰石/石灰-石膏法湿法脱硫工艺是目前世界上实用业绩最多、运行状况比较稳定的脱硫技术,占目前全世界烟气脱硫装置总量的36.7%,其脱硫效率最高可达到95%。
石灰-石膏法是用石灰粉代替石灰石,石灰活性大大高于石灰石,可提高脱硫效率。
大机组多采用石灰石-石膏湿法脱硫工艺,其特点是技术成熟,吸收剂来源广泛,适用于各种煤种,该法的缺点在于设备易腐蚀、磨损,系统易发生结垢、堵塞等长期存在的技术难点还没有得到较为满意的解决,其建设投资和运行费用较高。
此外,副产品脱硫石膏的产生量较大,目前还没有需要量大而又稳定的用户,我国是一个天然石膏藏量丰富的国家,脱硫石膏与它缺乏竞争上的优势,这也是不得不把它列为抛弃法的原因。
具体的工艺如下:从电除尘器出来的烟气通过增压风机(BUF)进入换热器(GGH),烟气被冷却后进入吸收塔(Abs),并与石灰石浆液相混合。
浆液中的部分水份蒸发掉,烟气进一步冷却。
脱硫和脱销工艺介绍

主要反应方程 (1) SO2+H2O→H2SO3 (2) CaCO3+2H2SO3→Ca(HSO3)2+CO2+H2O (3) Ca(HSO3)2+O2+2H2O→CaSO4·2H2O+H2SO4 (4) CaCO3+H2SO4+H2O→CaSO4·2H2O+CO2
主要优点为:a.脱硫效率高(脱硫效率大于90%); b.吸收剂利用率高,可大于90%; c.设备运转率高(可达90%以上)。
-
基本原理 氧化镁脱硫工艺是以氧化镁(MgO)为原料,经熟化 生成氢氧化镁(Mg(0H)2)作为脱硫剂,其主要的化学反 应有: 熟化制浆: MgO + H20 Mg(OH)2 脱硫吸收: Mg(OH)2 + S02 MgS03 + H20 氧 化: MgS03 + 1/202 MgS04 最后形成的副产物中含有MgS03·3H20、 MgS03·6H20、MgS04·7 H20、 Mg(HS03)2等多种成分 ,经脱水后得到以MgS03为主要成份的副产品,含水量 <1 O%。副产品可以作为肥料综合利用或经过再生生成 MgO循环使用,同时将分解出的S02制硫酸。
脱硫和脱销工艺介绍
通过对国内外脱硫技术以及国内电力行业引进脱 硫工艺试点厂情况的分析研究,目前脱硫方法一般可 划分为燃烧前脱硫、燃烧中脱硫和燃烧后脱硫等3类。
其中燃烧后脱硫,又称烟气脱硫(Flue gas desulfurization,简称FGD),在FGD技术中,按脱硫剂 的种类划分,可分为以下五种方法:以CaCO3(石灰石) 为基础的钙法,以MgO为基础的镁法,以Na2SO3为 基础的钠法,以NH3为基础的氨法,以有机碱为基础 的有机碱法。
-
干法脱硫 工艺 干法FGD技术的脱硫吸收和产物处理均在
各脱硫工艺简介及对比
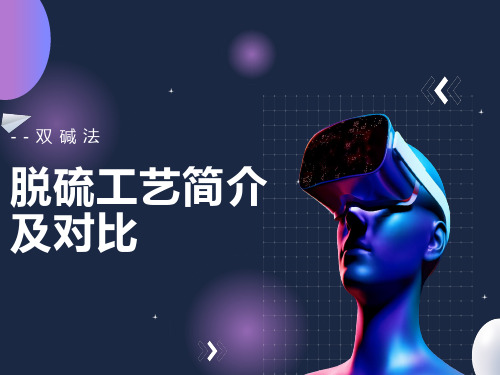
(4)石膏脱水系统
工艺水系统 工艺水系统负责提供FGD足够的水量,补充系统运行期间水的散失,以保证FGD系统的正常功能。工艺水通常采用循环水排水作为水源,一般设置两台工艺水泵(一用一备),一个工艺水箱。 工艺水的主要用水如下: 系统的补充水,主要有:除雾器冲洗水、石灰浆液补充水、泵的循环水等。 不定期对系统的一些管路进行冲洗,水量不定。主要有:循环管路冲洗水、石灰浆液管路冲洗水,石膏排放管路冲洗水、污泥管路冲洗水等。
3、脱硫系统说明
脱硫系统的工艺流程图见下页图。 整套系统由六大部分组成: 烟气系统;(2)SO2吸收系统;(3)吸收剂制备及供给系统;(4)石膏脱水系统;(5)工艺水系统;(6)电控系统。
(1)烟气系统
烟气从锅炉引风机后的烟道上引出,进入吸收塔。在吸收塔内脱硫净化,经除雾器除去水雾,送入锅炉引风机后的总烟道,经然后烟囱排入大气。在烟道上设一段旁路烟道,并设置旁路挡板门,当锅炉启动、进入FGD的烟气超温和FGD装置故障停运时,烟气由旁路挡板经烟囱排放。 烟气系统主要包括FGD进出口烟道,进出口挡板门,旁路挡板门以及与挡板门配套的执行机构。
脱硫工艺简介及对比
--双碱法
一、脱硫工艺
不同脱硫工艺之间的比较 ,具体见下表。
双碱法脱硫工艺介绍
烟气脱硫原理 湿式石灰/石灰石法技术工成熟,脱硫率高,但其主要缺点之一是容易结垢造成吸收系统的堵塞,而双碱法则是先用可溶性的碱性清液作为吸收剂吸收SO2,然后再用电石渣或石灰浆液对吸收液进行再生,由于在吸收和吸收液处理中,使用了两种不同类型的碱,故称为双碱法。双碱法的明显优点是,由于采用液相吸收,从而不存在结垢和浆料堵塞等问题。 针对公司的实际情况,因此本工程选用钠-钙双碱法工艺。
(6)电控系统
燃煤电厂各种干法半干法湿法脱硫技术及优缺点汇总

燃煤电厂各种干法、半干法、湿法脱硫技术及优缺点汇总目前,湿法烟气脱硫技术最为成熟,已得到大规模工业化应用,但由于投资成本高还需对工艺和设备开展优化;干法烟气脱硫技术不存在腐蚀和结露等问题,但脱硫率远低于湿法脱硫技术,一般单想电厂都不会选用,须进一步开发基于新脱硫原理的干法脱硫工艺;半干法脱硫技术脱硫率高,但不适合大容量燃烧设备。
不同的工况选择最符合的脱硫方法才会得到最大的经济效益,接下来根据电厂脱硫技术的选择原则来分析各种工艺的优缺点、适用条件。
电厂脱硫技术的选择原则:1、脱硫技术相对成熟,脱硫效率高,能到达环保控制要求,已经得到推广与应用。
2、脱硫成本比较经济合理,包括前期投资和后期运营。
3、脱硫所产生的副产品是否好处理,最好不造成二次污染,或者具有可回收利用价值。
4、对发电燃煤煤质不受影响,及对硫含量适用范围广。
5、脱硫剂的能够长期的供给,且价格要低廉一、干法脱硫干法脱硫工艺工艺用于电厂烟气脱硫始于20世纪80年代初。
传统的干法脱硫工艺主要有干法喷钙脱硫工艺、荷电干法吸收剂喷射脱硫法、电子束照射法、吸附法等。
传统的干法脱硫技术有工艺简单投资少,设备简占地面积小且不存在腐蚀和结露,副产品是固态无二次污染等优点,在缺水地区优势明显。
但是脱硫效率很低,一般脱硫效率只能到达70%左右,难以满足排放要求。
干法喷钙脱硫工艺工艺介绍磨细的石灰石粉通过气力方式喷人锅炉炉膛中温度为900〜1250。
C的区域在炉内发生的化学反应包括石灰石的分解和煨烧,S02和SO3与生成的Cao之间的反应。
颗粒状的反应产物与飞灰的混合物被烟气流带人活化塔中;剩余的CaO与水反应,在活化塔内生成Ca(OH)2,而Ca(OH)2很快与S02反应生成CaSo3,其中部分CaSO3被氧化成CaSo4;脱硫产物呈干粉状,大部分与飞灰一起被电除尘器收集下来,其余的从活化塔底部分离出来从电除尘器和活化塔底部收集到的部分飞灰通过再循环返回活化塔中。
双碱法与氧化镁法比较
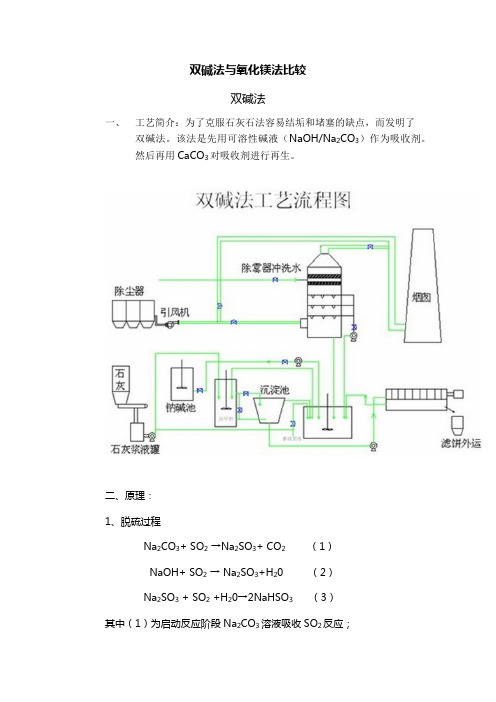
双碱法与氧化镁法比较双碱法一、工艺简介:为了克服石灰石法容易结垢和堵塞的缺点,而发明了双碱法。
该法是先用可溶性碱液(NaOH/Na2CO3)作为吸收剂。
然后再用CaCO3对吸收剂进行再生。
二、原理:1、脱硫过程Na2CO3+ SO2→Na2SO3+ CO2(1)NaOH+ SO2→ Na2SO3+H20 (2)Na2SO3 + SO2 +H20→2NaHSO3(3)其中(1)为启动反应阶段Na2CO3溶液吸收SO2反应;(2)为再生液PH较高时(PH>9)溶液吸收SO2的主反应;(3)为溶液PH值较低(PH为5-9)的主反应。
2、氧化过程(副反应)Na2SO3+1/2O2→Na2SO4(4)NaHSO3+1/2O2→NaHSO4(5)由于Na2SO4 与Ca(OH)2很难反应,所以(4)氧化后的产物很难再生。
导致NaOH消耗量大大增加。
3、再生过程NaHSO3+ Ca(OH)2→ CaCO3+NaOH+H2O (6)Na2SO3+ Ca(OH)2→2NaOH+CaCO3(7)(6)为第一步反应再生反应。
(7)为再生至PH>9以后继续发生的主反应。
三、双碱法系统的组成:整个工艺大致由四大部分组成:1 、脱硫剂制备过程由成品CaCO3(粒径小于10mm)运至厂内加入石灰仓中进行消化。
消化后再流入再生池与NaCO3进行再生反应。
钠碱由运至厂内加入给料塔,并与工艺水混合从而达到所需浓度的碱液。
当再生池的钠浓度低于标准的时候加至再生池中。
2、烟气系统热烟气自锅炉出来后进入吸收塔,向上流动穿过喷淋层,烟气被冷却到饱和温度,烟气中的SO2等污染物被碱液吸收。
洗涤后干净的烟气经除雾器出去水雾后,排入烟囱。
从锅炉出口到脱硫塔进口之间烟道设置膨胀节。
并根据需求设置旁路系统和挡板系统,以便脱硫系统事故时旁路运行。
3、SO2吸收系统在吸收塔内,脱硫液中的NaOH与烟气中的SO2、SO3 、 HF 、 HCl等发生中和反应并生成Na2SO3和NaHSO3等物质脱离烟气落入再生池中。
双碱法优点、对比及案例
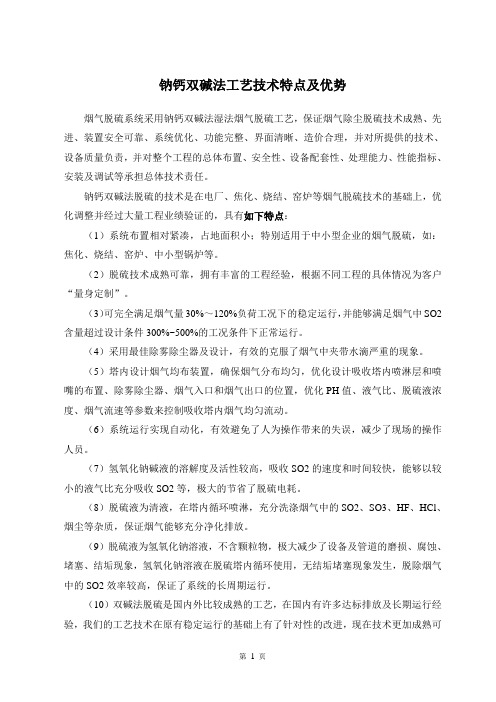
钠钙双碱法工艺技术特点及优势烟气脱硫系统采用钠钙双碱法湿法烟气脱硫工艺,保证烟气除尘脱硫技术成熟、先进、装置安全可靠、系统优化、功能完整、界面清晰、造价合理,并对所提供的技术、设备质量负责,并对整个工程的总体布置、安全性、设备配套性、处理能力、性能指标、安装及调试等承担总体技术责任。
钠钙双碱法脱硫的技术是在电厂、焦化、烧结、窑炉等烟气脱硫技术的基础上,优化调整并经过大量工程业绩验证的,具有如下特点:(1)系统布置相对紧凑,占地面积小;特别适用于中小型企业的烟气脱硫,如:焦化、烧结、窑炉、中小型锅炉等。
(2)脱硫技术成熟可靠,拥有丰富的工程经验,根据不同工程的具体情况为客户“量身定制”。
(3)可完全满足烟气量30%~120%负荷工况下的稳定运行,并能够满足烟气中SO2含量超过设计条件300%~500%的工况条件下正常运行。
(4)采用最佳除雾除尘器及设计,有效的克服了烟气中夹带水滴严重的现象。
(5)塔内设计烟气均布装置,确保烟气分布均匀,优化设计吸收塔内喷淋层和喷嘴的布置、除雾除尘器、烟气入口和烟气出口的位置,优化PH值、液气比、脱硫液浓度、烟气流速等参数来控制吸收塔内烟气均匀流动。
(6)系统运行实现自动化,有效避免了人为操作带来的失误,减少了现场的操作人员。
(7)氢氧化钠碱液的溶解度及活性较高,吸收SO2的速度和时间较快,能够以较小的液气比充分吸收SO2等,极大的节省了脱硫电耗。
(8)脱硫液为清液,在塔内循环喷淋,充分洗涤烟气中的SO2、SO3、HF、HCl、烟尘等杂质,保证烟气能够充分净化排放。
(9)脱硫液为氢氧化钠溶液,不含颗粒物,极大减少了设备及管道的磨损、腐蚀、堵塞、结垢现象,氢氧化钠溶液在脱硫塔内循环使用,无结垢堵塞现象发生,脱除烟气中的SO2效率较高,保证了系统的长周期运行。
(10)双碱法脱硫是国内外比较成熟的工艺,在国内有许多达标排放及长期运行经验,我们的工艺技术在原有稳定运行的基础上有了针对性的改进,现在技术更加成熟可靠,可在项目实施中少走弯路。
双碱法优点对比及案例
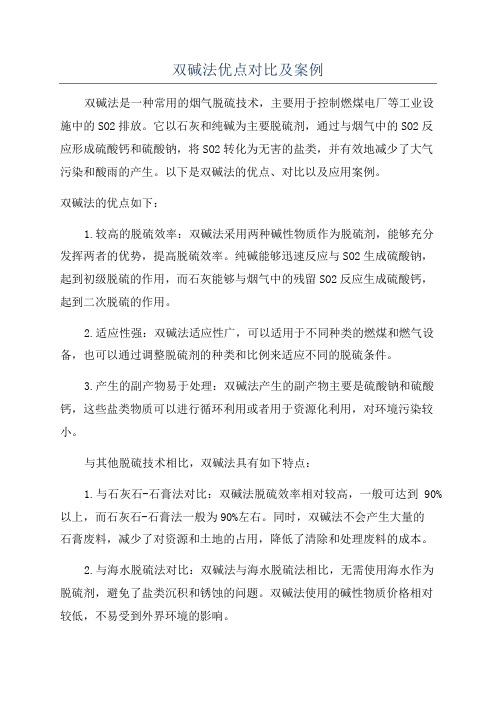
双碱法优点对比及案例双碱法是一种常用的烟气脱硫技术,主要用于控制燃煤电厂等工业设施中的SO2排放。
它以石灰和纯碱为主要脱硫剂,通过与烟气中的SO2反应形成硫酸钙和硫酸钠,将SO2转化为无害的盐类,并有效地减少了大气污染和酸雨的产生。
以下是双碱法的优点、对比以及应用案例。
双碱法的优点如下:1.较高的脱硫效率:双碱法采用两种碱性物质作为脱硫剂,能够充分发挥两者的优势,提高脱硫效率。
纯碱能够迅速反应与SO2生成硫酸钠,起到初级脱硫的作用,而石灰能够与烟气中的残留SO2反应生成硫酸钙,起到二次脱硫的作用。
2.适应性强:双碱法适应性广,可以适用于不同种类的燃煤和燃气设备,也可以通过调整脱硫剂的种类和比例来适应不同的脱硫条件。
3.产生的副产物易于处理:双碱法产生的副产物主要是硫酸钠和硫酸钙,这些盐类物质可以进行循环利用或者用于资源化利用,对环境污染较小。
与其他脱硫技术相比,双碱法具有如下特点:1.与石灰石-石膏法对比:双碱法脱硫效率相对较高,一般可达到90%以上,而石灰石-石膏法一般为90%左右。
同时,双碱法不会产生大量的石膏废料,减少了对资源和土地的占用,降低了清除和处理废料的成本。
2.与海水脱硫法对比:双碱法与海水脱硫法相比,无需使用海水作为脱硫剂,避免了盐类沉积和锈蚀的问题。
双碱法使用的碱性物质价格相对较低,不易受到外界环境的影响。
现实中,双碱法已经在多个国家和地区得到了广泛应用。
以下是一些应用案例:1.美国爱达荷州莱文沙槽二号电厂:该电厂采用双碱法进行烟气脱硫,运行效果良好。
该电厂使用石灰和纯碱作为脱硫剂,脱硫效率可达到90%以上,大大降低了SO2排放量,减少了酸雨的形成。
2.中国山西热电厂:该热电厂采用双碱法进行烟气脱硫,成功地实现了大气污染物的减排。
该电厂使用石灰和纯碱作为脱硫剂,通过脱硫工艺,将煤烟气中的SO2转化为硫酸钠和硫酸钙并进行收集处理。
3.德国霍尔茨门热电厂:该热电厂采用双碱法进行烟气脱硫,将SO2排放控制在环境法规要求以下。
火电厂脱硫脱硝技术优缺点
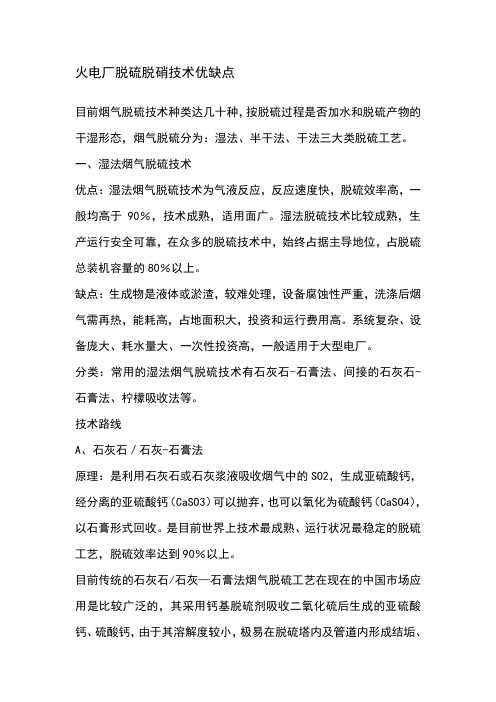
火电厂脱硫脱硝技术优缺点目前烟气脱硫技术种类达几十种,按脱硫过程是否加水和脱硫产物的干湿形态,烟气脱硫分为:湿法、半干法、干法三大类脱硫工艺。
一、湿法烟气脱硫技术优点:湿法烟气脱硫技术为气液反应,反应速度快,脱硫效率高,一般均高于90%,技术成熟,适用面广。
湿法脱硫技术比较成熟,生产运行安全可靠,在众多的脱硫技术中,始终占据主导地位,占脱硫总装机容量的80%以上。
缺点:生成物是液体或淤渣,较难处理,设备腐蚀性严重,洗涤后烟气需再热,能耗高,占地面积大,投资和运行费用高。
系统复杂、设备庞大、耗水量大、一次性投资高,一般适用于大型电厂。
分类:常用的湿法烟气脱硫技术有石灰石-石膏法、间接的石灰石-石膏法、柠檬吸收法等。
技术路线A、石灰石/石灰-石膏法原理:是利用石灰石或石灰浆液吸收烟气中的SO2,生成亚硫酸钙,经分离的亚硫酸钙(CaSO3)可以抛弃,也可以氧化为硫酸钙(CaSO4),以石膏形式回收。
是目前世界上技术最成熟、运行状况最稳定的脱硫工艺,脱硫效率达到90%以上。
目前传统的石灰石/石灰—石膏法烟气脱硫工艺在现在的中国市场应用是比较广泛的,其采用钙基脱硫剂吸收二氧化硫后生成的亚硫酸钙、硫酸钙,由于其溶解度较小,极易在脱硫塔内及管道内形成结垢、堵塞现象。
对比石灰石法脱硫技术,双碱法烟气脱硫技术则克服了石灰石—石灰法容易结垢的缺点。
B 、间接石灰石-石膏法:优常见的间接石灰石-石膏法有:钠碱双碱法、碱性硫酸铝法和稀硫酸吸收法等。
原理:钠碱、碱性氧化铝(Al2O3·nH2O)或稀硫酸(H2SO4)吸收SO2,生成的吸收液与石灰石反应而得以再生,并生成石膏。
该法操作简单,二次污染少,无结垢和堵塞问题,脱硫效率高,但是生成的石膏产品质量较差。
C、柠檬吸收法:原理:柠檬酸(H3C6H5O7·H2O)溶液具有较好的缓冲性能,当SO2气体通过柠檬酸盐液体时,烟气中的SO2与水中H发生反应生成H2SO3络合物,SO2吸收率在99%以上。
湿式钙法、镁法、双碱法的比较

脱硫除尘工艺的比较湿法烟气脱硫工艺,技术比较成熟。
该技术根据吸收剂种类的不同,又可分为:石灰(石)-石膏法(使用最多)、双碱法、氧化镁法、氨法、海水法、钠碱法等,由于海水法、双碱法、氨法、钠碱法等受到地理位置、脱硫副产品处理、脱硫剂来源及价格等因素影响,常常应用在区域性较强、烟量相对较小或工艺要求简单的脱硫工程中。
石灰(石)-石膏法则因其成熟的工艺技术,在工业锅炉和大型电厂的脱硫工程中得到广泛应用。
而镁法脱硫技术,近些年来我国临近镁矿产地地区(山东、东北、天津、北京等地区)也得到一些应用。
1.3.1 化学反应机理比较(1)湿式钙法脱硫湿式钙法脱硫的脱硫剂可采用石灰石(CaCO3)或石灰(CaO),所以化学反应也因脱硫剂的不同而略有不同。
湿式钙法脱硫多采用石灰-石膏法。
CaO+H2O →Ca(HO) 2消化SO2 + H2O → H2SO3吸收Ca(HO) 2 + H2SO3→ CaSO3 + 2H2O 中和CaSO3 + 1/2 O2→ CaSO4氧化CaSO3 + 1/2 H2O → CaSO3•1/2H2O 结晶CaSO4 + 2H2O → CaSO4•2H2O 结晶(2)湿式镁法脱硫以普通工业氧化镁粉(纯度约85%~90%)浆液作吸收剂,与烟气反应生成亚硫酸镁,如亚硫酸镁进一步氧化,可生成硫酸镁。
MgO+H2O→Mg(OH)2 (悬浮乳液) 熟化SO2+ H2O→H2SO3 吸收Mg(OH)2+ H2SO3→MgSO3+2H2O 中和MgSO3+ H2SO3→Mg(HSO3)2 中和生成的亚硫酸镁一部分又作为吸收剂循环使用,同时未使用的另一部分可排放或进一步利用。
MgSO 3+1/2O 2→MgSO 4(溶解状态) 氧化此外,在Mg(OH)2相对SO 2不足时则会:MgSO 3+SO 2+H 2O→Mg(HSO 3)2补足Mg(OH)2时Mg (HSO 3)2+Mg (OH )2→2MgSO 3↓+2H 2O当副产品亚硫酸镁采用焙烧方法制成氧化镁和硫酸回收时,则其化学过程如下(焙烧温度控制在850℃以下,如温度达到1200℃,氧化镁会被烧结,不能作为脱硫剂使用),该工艺复杂,投资大,我国脱硫过程尚无常用:MgSO 3 →MgO +SO 2MgSO 4→MgO +SO 3Mg(HSO 3)2→MgO +H 2O +2SO 2SO 2+1/2O 2→SO 3SO 3+H 2O→H 2SO 4一般,我国氧化镁脱硫,脱硫副产品采用抛弃法。
五种常用的烟气脱硫技术
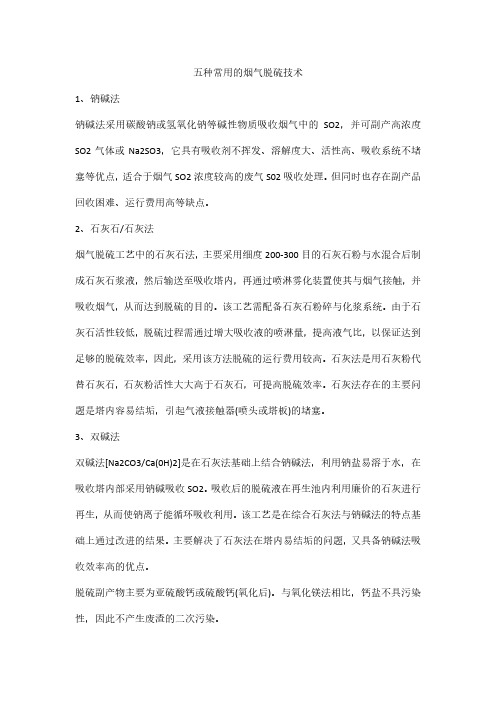
五种常用的烟气脱硫技术1、钠碱法钠碱法采用碳酸钠或氢氧化钠等碱性物质吸收烟气中的SO2,并可副产高浓度SO2气体或Na2SO3,它具有吸收剂不挥发、溶解度大、活性高、吸收系统不堵塞等优点,适合于烟气SO2浓度较高的废气S02吸收处理。
但同时也存在副产品回收困难、运行费用高等缺点。
2、石灰石/石灰法烟气脱硫工艺中的石灰石法,主要采用细度200-300目的石灰石粉与水混合后制成石灰石浆液,然后输送至吸收塔内,再通过喷淋雾化装置使其与烟气接触,并吸收烟气,从而达到脱硫的目的。
该工艺需配备石灰石粉碎与化浆系统。
由于石灰石活性较低,脱硫过程需通过增大吸收液的喷淋量,提高液气比,以保证达到足够的脱硫效率,因此,采用该方法脱硫的运行费用较高。
石灰法是用石灰粉代替石灰石,石灰粉活性大大高于石灰石,可提高脱硫效率。
石灰法存在的主要问题是塔内容易结垢,引起气液接触器(喷头或塔板)的堵塞。
3、双碱法双碱法[Na2CO3/Ca(0H)2]是在石灰法基础上结合钠碱法,利用钠盐易溶于水,在吸收塔内部采用钠碱吸收SO2。
吸收后的脱硫液在再生池内利用廉价的石灰进行再生,从而使钠离子能循环吸收利用。
该工艺是在综合石灰法与钠碱法的特点基础上通过改进的结果。
主要解决了石灰法在塔内易结垢的问题,又具备钠碱法吸收效率高的优点。
脱硫副产物主要为亚硫酸钙或硫酸钙(氧化后)。
与氧化镁法相比,钙盐不具污染性,因此不产生废渣的二次污染。
4、氧化镁法氧化镁法采用氧化镁与SO2反应得到亚硫酸镁与硫酸镁,它们通过煅烧可重新分解出氧化镁,同时回收较纯净的SO2气体,脱硫剂可循环使用。
由于氧化镁活性比石灰水高,脱硫效率也较石灰法高。
它的缺点是氧化镁回收过程需煅烧,工艺较复杂,但若直接采用抛弃法,镁盐会导致二次污染,总体运行费用也较高。
5、氨法氨法采用氨水作为SO2的吸收剂,SO2与NH3反应可产生亚硫酸氨、亚硫酸氢氨与部分因氧化而产生的硫酸氨。
根据吸收液再生方法的不同,氨法可分为氨—酸法、氨—亚硫酸氨法和氨—硫酸氨法。
双碱法与氧化镁法工艺比较.doc
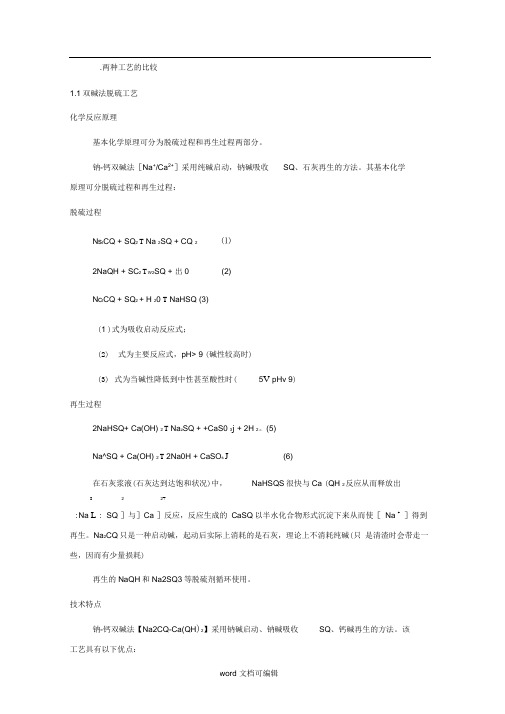
.两种工艺的比较1.1双碱法脱硫工艺化学反应原理基本化学原理可分为脱硫过程和再生过程两部分。
钠-钙双碱法[Na+/Ca2+]采用纯碱启动,钠碱吸收SQ、石灰再生的方法。
其基本化学原理可分脱硫过程和再生过程:脱硫过程Ns t CQ + SQ2 T Na 2SQ + CQ 2 ⑴2NaQH + SC2 T W2SQ + 出0 (2)Nc t CQ + SQ2 + H 20 T NaHSQ (3)(1 )式为吸收启动反应式;(2)式为主要反应式,pH> 9 (碱性较高时)(3)式为当碱性降低到中性甚至酸性时( 5V pHv 9)再生过程2NaHSQ+ Ca(OH) 2 T Na z SQ + +CaS0 3j + 2H 2。
(5)Na^SQ + Ca(OH) 2 T 2Na0H + CaSO s J (6)在石灰浆液(石灰达到达饱和状况)中,NaHSQS很快与Ca (QH 2反应从而释放出I 2 2+:Na L : SQ ]与]Ca ]反应,反应生成的CaSQ以半水化合物形式沉淀下来从而使[Na +]得到再生。
Na2CQ只是一种启动碱,起动后实际上消耗的是石灰,理论上不消耗纯碱(只是清渣时会带走一些,因而有少量损耗)再生的NaQH和Na2SQ3等脱硫剂循环使用。
技术特点钠-钙双碱法【Na2CQ-Ca(QH)2】采用钠碱启动、钠碱吸收SQ、钙碱再生的方法。
该工艺具有以下优点:1投资省、脱硫效率高。
与传统的双碱法脱硫相比较,钠碱吸收剂较钙碱的反应活性高、吸收速度快,可大大降低脱硫吸收的液气比,从而降低吸收液循环泵的功率和投资,而脱硫效率达80%以上,除尘脱硫后的烟气确保完全满足环保排放要求;2 该工艺在多个燃煤锅炉的除尘脱硫项目中运行效果良好,技术成熟,运行可靠性高,烟气除尘脱硫装置投入率为95%以上,系统主要设备很少发生故障,因此不会因除尘脱硫设备故障影响主设备的安全运行;3 对操作弹性大,对燃烧煤种含硫量的变化适应性强。
镁法与钙法的比较

一、镁法与钙法脱硫方案比较比较项目镁法脱硫钙法脱硫脱硫效率达99%以上约95%安全投运结垢、堵塞系统反应生成硫酸镁,易溶于水,纯液态浆液,无结垢堵塞系统反应生成硫酸钙(石膏),微溶于水,导致系统结垢堵塞情况严重腐蚀系统运行的PH值为6.5左右,接近中性的运行环境,腐蚀性很小系统的运行PH值为5.4左右,为酸性的运行环境,腐蚀严重磨损脱硫剂氧化镁粒度为200目左右,磨损小自运行企业采用的石灰粉粒度较大,磨损严重运行成本相对循环水量液气比4-5,循环水量少液气比8-15,循环水量大相对电耗脱硫系统运行阻力在600-800Pa左右,运行无需增压风机,耗电量小脱硫系统运行阻力需要2000Pa以上,运行需要加装增压风机,耗电量大维修成本设备磨损小,维修费低设备磨损大,维修费高脱硫副产品产出高品质七水硫酸镁,经济效益高基本抛弃,易造成二次污染对长期国家环保政策的适应性强,有单独的资金补贴:有清洁能源生产及循环经济法治污2项奖励政策弱,无对应奖励政策。
同时《国务院关于化解产能严重过剩矛盾的指导意见》中明确到2015年淘汰1亿吨水泥产能。
该政策将会对钙法脱硫剂的价格及少数回收的副产品(石膏)的去向造成重大影响。
增加CO2排放无每减排1吨SO2释放0.7吨CO2脱硝采用物化络合吸收法,可实现一塔内同时脱硫脱硝。
不能脱硝,如脱硝需另行立项,增加设备及投资,对原有系统改动大,效率低。
脱重金属可脱除重金属不能脱重金属。
湿式钙法、镁法、双碱法的比较
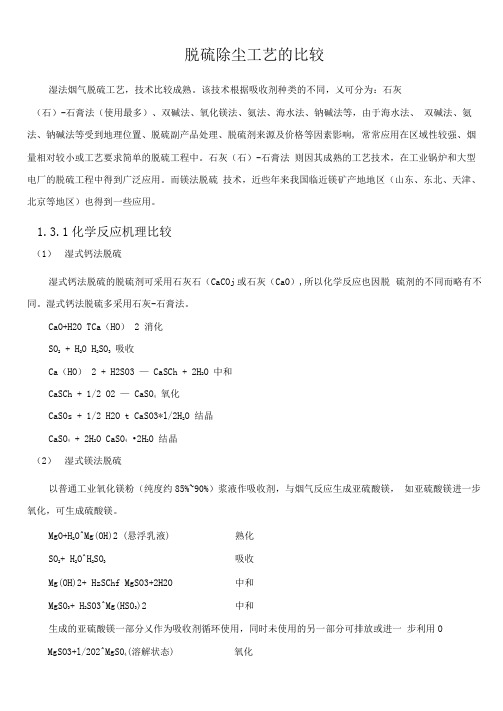
脱硫除尘工艺的比较湿法烟气脱硫工艺,技术比较成熟。
该技术根据吸收剂种类的不同,乂可分为:石灰(石)-石膏法(使用最多)、双碱法、氧化镁法、氨法、海水法、钠碱法等,由于海水法、双碱法、氨法、钠碱法等受到地理位置、脱硫副产品处理、脱硫剂来源及价格等因素影响, 常常应用在区域性较强、烟量相对较小或工艺要求简单的脱硫工程中。
石灰(石)-石膏法则因其成熟的工艺技术,在工业锅炉和大型电厂的脱硫工程中得到广泛应用。
而镁法脱硫技术,近些年来我国临近镁矿产地地区(山东、东北、天津、北京等地区)也得到一些应用。
1.3.1化学反应机理比较(1)湿式钙法脱硫湿式钙法脱硫的脱硫剂可采用石灰石(CaCOj或石灰(CaO),所以化学反应也因脱硫剂的不同而略有不同。
湿式钙法脱硫多采用石灰-石膏法。
CaO+H2O TCa(HO) 2 消化SO2 + H2O H2SO3吸收Ca(HO) 2 + H2SO3 — CaSCh + 2H2O 中和CaSCh + 1/2 O2 — CaSO4氧化CaSOs + 1/2 H2O t CaSO3*l/2H2O 结晶CaSO4 + 2H2O CaSO4•2H2O 结晶(2)湿式镁法脱硫以普通工业氧化镁粉(纯度约85%~90%)浆液作吸收剂,与烟气反应生成亚硫酸镁,如亚硫酸镁进一步氧化,可生成硫酸镁。
MgO+H2O^Mg(OH)2 (悬浮乳液) 熟化SO2+ H2O^H2SO3吸收Mg(OH)2+ HzSChf MgSO3+2H2O 中和MgSO3+ H2SO3^Mg(HSO3)2 中和生成的亚硫酸镁一部分乂作为吸收剂循环使用,同时未使用的另一部分可排放或进一步利用OMgSO3+l/2O2^MgSO4(溶解状态) 氧化此外,在Mg(OH)2相对SO2不足时则会:MgSO3+SO2+H2O^Mg(HSO3)2补足Mg(OH)2时Mg (HSOs) 2+Mg (OH) 2T2MgSOg+2H2O当副产品亚硫酸镁采用焙烧方法制成氧化镁和硫酸回收时,则其化学过程如下(焙烧温度控制在850C以下,如温度达到1200c C,氧化镁会被烧结,工艺复杂,投资大,我国脱硫过程尚无常用:不能作为脱硫剂使用),该MgSOs^MgO+SOzMgSO4->MgO + SO3Mg(HSO3)2^MgO + H2O + 2SO2SO2+I/2O2TSO3SO3+H2OTH2SO4一般,我国氧化镁脱硫,脱硫副产品采用抛弃法。
基于钙法、镁法、双碱法、氨法脱硫技术比较分析
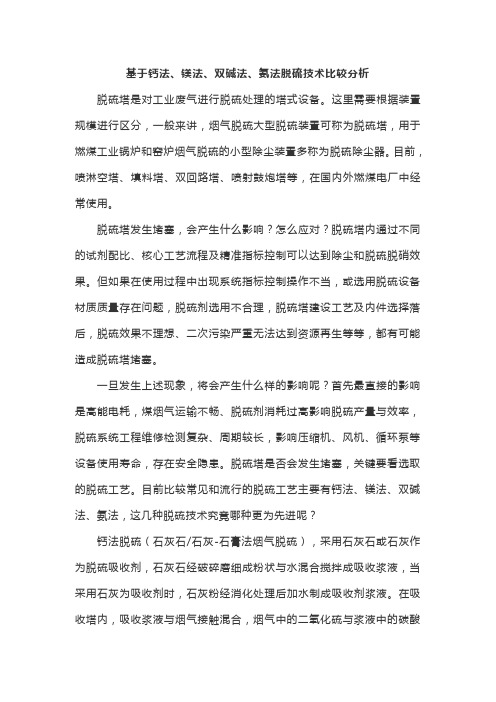
基于钙法、镁法、双碱法、氨法脱硫技术比较分析脱硫塔是对工业废气进行脱硫处理的塔式设备。
这里需要根据装置规模进行区分,一般来讲,烟气脱硫大型脱硫装置可称为脱硫塔,用于燃煤工业锅炉和窑炉烟气脱硫的小型除尘装置多称为脱硫除尘器。
目前,喷淋空塔、填料塔、双回路塔、喷射鼓炮塔等,在国内外燃煤电厂中经常使用。
脱硫塔发生堵塞,会产生什么影响?怎么应对?脱硫塔内通过不同的试剂配比、核心工艺流程及精准指标控制可以达到除尘和脱硫脱硝效果。
但如果在使用过程中出现系统指标控制操作不当,或选用脱硫设备材质质量存在问题,脱硫剂选用不合理,脱硫塔建设工艺及内件选择落后,脱硫效果不理想、二次污染严重无法达到资源再生等等,都有可能造成脱硫塔堵塞。
一旦发生上述现象,将会产生什么样的影响呢?首先最直接的影响是高能电耗,煤烟气运输不畅、脱硫剂消耗过高影响脱硫产量与效率,脱硫系统工程维修检测复杂、周期较长,影响压缩机、风机、循环泵等设备使用寿命,存在安全隐患。
脱硫塔是否会发生堵塞,关键要看选取的脱硫工艺。
目前比较常见和流行的脱硫工艺主要有钙法、镁法、双碱法、氨法,这几种脱硫技术究竟哪种更为先进呢?钙法脱硫(石灰石/石灰-石膏法烟气脱硫),采用石灰石或石灰作为脱硫吸收剂,石灰石经破碎磨细成粉状与水混合搅拌成吸收浆液,当采用石灰为吸收剂时,石灰粉经消化处理后加水制成吸收剂浆液。
在吸收塔内,吸收浆液与烟气接触混合,烟气中的二氧化硫与浆液中的碳酸钙以及鼓入的氧化空气进行化学反应从而被脱除,最终反应产物为石膏。
目前该工艺技术比较成熟,对烟气负荷、煤种变化适应性好,脱硫效率高。
但系统结构相对复杂,占地面积大,投资费用较高。
液气比高循环液量大,耗电量较高。
由于脱硫原料及产物溶解度小,易造成设备的堵塞、结垢和磨损。
脱硫副产品为石膏,品质差,系统排放大量高氯盐水,产量过剩,二次污染比较严重。
烟囱需要进行防腐处理。
镁法脱硫(氧化镁湿法脱硫工艺),以氧化镁为原料,经熟化生成氢氧化镁作为脱硫剂,在吸收塔内,吸收浆液与烟气接触混合,烟气中的二氧化硫与浆液中的氢氧化镁进行化学反应从而被脱除,最终反应产物为亚硫酸镁和硫酸镁混合物。
有图有真相,干法、半干法、湿法脱硫,太详细
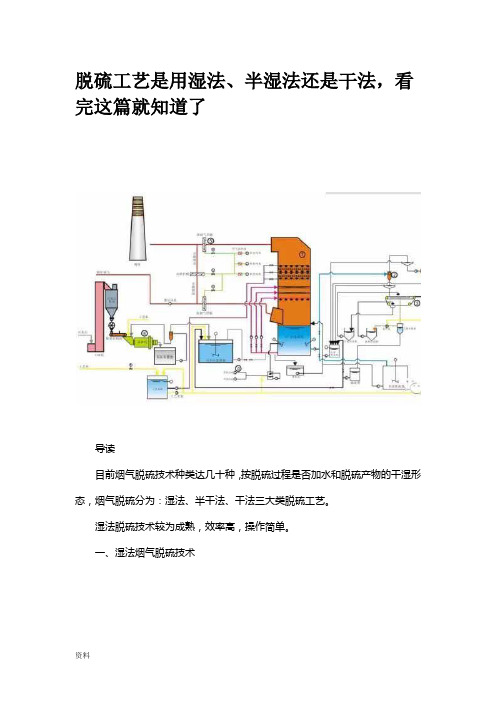
脱硫工艺是用湿法、半湿法还是干法,看完这篇就知道了导读目前烟气脱硫技术种类达几十种,按脱硫过程是否加水和脱硫产物的干湿形态,烟气脱硫分为:湿法、半干法、干法三大类脱硫工艺。
湿法脱硫技术较为成熟,效率高,操作简单。
一、湿法烟气脱硫技术优点:湿法烟气脱硫技术为气液反应,反应速度快,脱硫效率高,一般均高于90%,技术成熟,适用面广。
湿法脱硫技术比较成熟,生产运行安全可靠,在众多的脱硫技术中,始终占据主导地位,占脱硫总装机容量的80%以上。
缺点:生成物是液体或淤渣,较难处理,设备腐蚀性严重,洗涤后烟气需再热,能耗高,占地面积大,投资和运行费用高。
系统复杂、设备庞大、耗水量大、一次性投资高,一般适用于大型电厂。
分类:常用的湿法烟气脱硫技术有石灰石-石膏法、间接的石灰石-石膏法、柠檬吸收法等。
技术路线A、石灰石/石灰-石膏法原理:是利用石灰石或石灰浆液吸收烟气中的SO2,生成亚硫酸钙,经分离的亚硫酸钙(CaSO3)可以抛弃,也可以氧化为硫酸钙(CaSO4),以石膏形式回收。
是目前世界上技术最成熟、运行状况最稳定的脱硫工艺,脱硫效率达到90%以上。
目前传统的石灰石/石灰—石膏法烟气脱硫工艺在现在的中国市场应用是比较广泛的,其采用钙基脱硫剂吸收二氧化硫后生成的亚硫酸钙、硫酸钙,由于其溶解度较小,极易在脱硫塔内及管道内形成结垢、堵塞现象。
对比石灰石法脱硫技术,双碱法烟气脱硫技术则克服了石灰石—石灰法容易结垢的缺点。
B 、间接石灰石-石膏法:常见的间接石灰石-石膏法有:钠碱双碱法、碱性硫酸铝法和稀硫酸吸收法等。
原理:钠碱、碱性氧化铝(Al2O3·nH2O)或稀硫酸(H2SO4)吸收SO2,生成的吸收液与石灰石反应而得以再生,并生成石膏。
该法操作简单,二次污染少,无结垢和堵塞问题,脱硫效率高,但是生成的石膏产品质量较差。
C、柠檬吸收法:原理:柠檬酸(H3C6H5O7·H2O)溶液具有较好的缓冲性能,当SO2气体通过柠檬酸盐液体时,烟气中的SO2与水中H发生反应生成H2SO3络合物,SO2吸收率在99%以上。
湿式石灰石膏法与双碱法在烟气脱硫中的对比
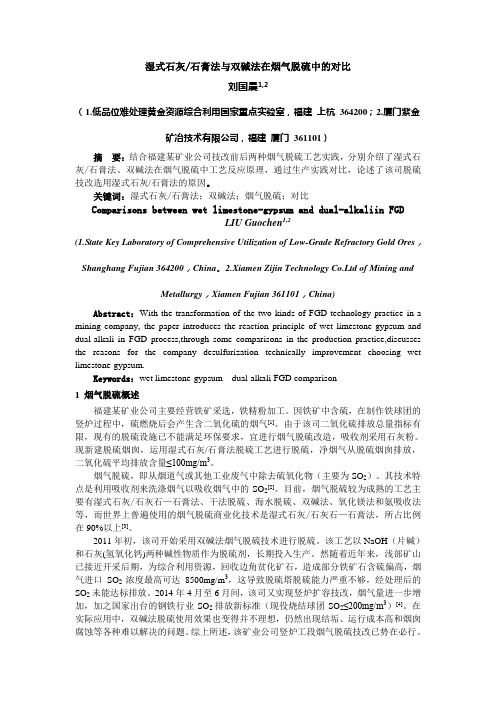
湿式石灰/石膏法与双碱法在烟气脱硫中的对比刘国晨1,2(1.低品位难处理黄金资源综合利用国家重点实验室,福建上杭364200;2.厦门紫金矿冶技术有限公司,福建厦门361101)摘要:结合福建某矿业公司技改前后两种烟气脱硫工艺实践,分别介绍了湿式石灰/石膏法、双碱法在烟气脱硫中工艺反应原理,通过生产实践对比,论述了该司脱硫技改选用湿式石灰/石膏法的原因。
关键词:湿式石灰/石膏法;双碱法;烟气脱硫;对比Comparisons between wet limestone-gypsum and dual-alkaliin FGDLIU Guochen1,2(1.State Key Laboratory of Comprehensive Utilization of Low-Grade Refractory Gold Ores,Shanghang Fujian 364200,China。
2.Xiamen Zijin Technology Co.Ltd of Mining andMetallurgy,Xiamen Fujian 361101,China)Abstract:With the transformation of the two kinds of FGD technology practice in a mining company, the paper introduces the reaction principle of wet limestone-gypsum and dual-alkali in FGD process,through some comparisons in the production practice,discusses the reasons for the company desulfurization technically improvement choosing wet limestone-gypsum.Keywords:wet limestone-gypsum dual-alkali FGD comparison1 烟气脱硫概述福建某矿业公司主要经营铁矿采选,铁精粉加工。
- 1、下载文档前请自行甄别文档内容的完整性,平台不提供额外的编辑、内容补充、找答案等附加服务。
- 2、"仅部分预览"的文档,不可在线预览部分如存在完整性等问题,可反馈申请退款(可完整预览的文档不适用该条件!)。
- 3、如文档侵犯您的权益,请联系客服反馈,我们会尽快为您处理(人工客服工作时间:9:00-18:30)。
脱硫除尘工艺的比较湿法烟气脱硫工艺,技术比较成熟。
该技术根据吸收剂种类的不同,又可分为:石灰(石)-石膏法(使用最多)、双碱法、氧化镁法、氨法、海水法、钠碱法等,由于海水法、双碱法、氨法、钠碱法等受到地理位置、脱硫副产品处理、脱硫剂来源及价格等因素影响,常常应用在区域性较强、烟量相对较小或工艺要求简单的脱硫工程中。
石灰(石)-石膏法则因其成熟的工艺技术,在工业锅炉和大型电厂的脱硫工程中得到广泛应用。
而镁法脱硫技术,近些年来我国临近镁矿产地地区(山东、东北、天津、北京等地区)也得到一些应用。
1.3.1 化学反应机理比较(1)湿式钙法脱硫湿式钙法脱硫的脱硫剂可采用石灰石(CaCO3)或石灰(CaO),所以化学反应也因脱硫剂的不同而略有不同。
湿式钙法脱硫多采用石灰-石膏法。
CaO+H2O →Ca(HO) 2消化SO2 + H2O → H2SO3吸收Ca(HO) 2 + H2SO3→ CaSO3 + 2H2O 中和CaSO3 + 1/2 O2→ CaSO4氧化CaSO3 + 1/2 H2O → CaSO3•1/2H2O 结晶CaSO4 + 2H2O → CaSO4•2H2O 结晶(2)湿式镁法脱硫以普通工业氧化镁粉(纯度约85%~90%)浆液作吸收剂,与烟气反应生成亚硫酸镁,如亚硫酸镁进一步氧化,可生成硫酸镁。
MgO+H2O→Mg(OH)2 (悬浮乳液) 熟化SO2+ H2O→H2SO3 吸收Mg(OH)2+ H2SO3→MgSO3+2H2O 中和MgSO3+ H2SO3→Mg(HSO3)2 中和生成的亚硫酸镁一部分又作为吸收剂循环使用,同时未使用的另一部分可排放或进一步利用。
MgSO 3+1/2O 2→MgSO 4(溶解状态) 氧化此外,在Mg(OH)2相对SO 2不足时则会:MgSO 3+SO 2+H 2O→Mg(HSO 3)2补足Mg(OH)2时Mg (HSO 3)2+Mg (OH )2→2MgSO 3↓+2H 2O当副产品亚硫酸镁采用焙烧方法制成氧化镁和硫酸回收时,则其化学过程如下(焙烧温度控制在850℃以下,如温度达到1200℃,氧化镁会被烧结,不能作为脱硫剂使用),该工艺复杂,投资大,我国脱硫过程尚无常用:MgSO 3 →MgO +SO 2MgSO 4→MgO +SO 3Mg(HSO 3)2→MgO +H 2O +2SO 2SO 2+1/2O 2→SO 3SO 3+H 2O→H 2SO 4一般,我国氧化镁脱硫,脱硫副产品采用抛弃法。
(3)钠钙双碱法钠钙双碱法 利用氢氧化钠钠盐易溶于水,在吸收塔内部采用钠碱吸收SO 2,吸收后的脱硫液在再生池内利用廉价的石灰作为第二碱处理吸收液,进行再生,生成亚硫酸钙和硫酸钙的少量沉淀物,从而使得钠离子循环吸收利用。
其法本化学原理可分为SO 2吸收过程、脱硫过程、再生过程、氧化过程。
气相SO 2被液相吸收脱硫反应过程:↑+⇒+232232CO SO Na SO CO Na(1) 22322NaOH SO Na SO H O+⇒+ (2) 322322NaHSO O H SO SO Na ⇔++ (3)以上三式视吸收液酸碱度不同而异:碱性较高时(PH >9),(2)式为主要反应;碱性)()()()(42233222l SO H O H g SO l SO H O H g SO ↔+↔+较低时,(1)式为主要反应;碱性为中性甚至酸性时(5<PH <9),则(3)式为主要反应。
由于烟气中含氧,所以会有以下副反应:4223221SO Na O SO Na ⇒+ (4)42321NaHSO O NaHSO ⇒+ (5)再生过程(石灰乳置换再生): 3223322132()22NaHSO Ca OH Na SO CaSO H O H O •+⇔++ (6)2323()2Na SO Ca OH NaOH CaSO +⇒+ (7)氧化反应(不稳定的亚硫酸钙氧化成稳定的硫酸钙):O H CaSO O H O O H CaSO 2422232232•→++• (8)在石灰乳液(石灰水达到饱和状况)中,中性的Na 2HSO 3跟石灰反应从而释放出Na +,随后生成的SO 32-又继续跟石灰反应,反应生成物以半水化合物形式慢慢沉淀下来,从而使钠法得到再生。
1.3.2 主要工艺系统比较(1)湿式钙法脱硫石灰-石膏湿法脱硫工艺系统主要有:烟气系统、浆液制备系统、吸收系统、氧化系统、石膏脱水系统、公用系统组成。
典型工艺流程为浓缩罐→过滤机↑脱硫剂→螺旋加灰机→石灰乳液罐→石灰乳泵→脱硫循环池←罗茨风机脱硫后浆液↑↓脱硫循环泵锅炉烟气→除尘器→引风机→烟道→湿法脱硫塔→烟道→烟囱经除尘后的烟气靠引风机的动力进入脱硫塔脱硫,经均气降温层均气降温后,在脱硫塔内与脱硫浆液进行充分的传质、吸收,吸收烟气中的大部分SO 2并继续脱除剩余的细尘,之后烟气经脱水除雾后,进入烟囱达标排放。
脱硫过程生成的亚硫酸钙和硫酸钙浆液进入脱硫循环池(塔内或塔外),并在其中进行曝气氧化。
之后,大部分浆液经循环泵循环用于脱硫(脱硫浆液的pH值通过控制循环池中新鲜石灰乳的加入量进行调控),小部分浓浆液有控制地排入副产物处理系统,由脱水系统过滤出固态脱硫渣。
(2)湿式镁法脱硫氧化镁湿法脱硫工艺系统主要有:烟气系统、水镁浆制备系统、吸收系统、氧化系统、脱硫浆液后处理系统、公用系统组成。
典型工艺流程为烟气→除尘器→引风机→湿式脱硫塔→烟道→烟囱排放循环泵↑↓MgO粉→制浆池→制浆泵→供浆池→供浆泵→塔底循环反应池→浓缩池→脱水系统→固态渣。
同时滤液经曝气氧化后作为系统补水,小部分外排。
以上是我公司的氧化镁处理工艺。
但很多公司脱硫浆液后处理系统中采取在循环池(或沉淀池中) 将反应生产的亚硫酸镁直接氧化成溶解度很大的硫酸镁,这样系统脱硫产物只能以硫酸镁溶液形式外排到市政管道。
工艺说明:脱硫塔采用正压运行,经除尘后的烟气经引风机送出后,通过进口烟道下斜10度左右进入脱硫塔。
在脱硫塔内,烟气中的SO2与脱硫浆液进行碰撞、吸收和反应,进行脱硫。
经过一定的反应时间后,达标烟气经两层高效折板除雾器除雾后,由烟道进入烟囱排放。
完成脱硫后的浆液进入脱硫循环池,池内大部分浆液经由脱硫循环泵送至脱硫塔内循环用于脱硫,小部分浆液输送至浓缩池进行浓缩,浓缩后底部35%左右的浓相(大部分为亚硫酸镁)进入皮带式脱水系统进行过滤,滤渣可同锅炉渣一同处理,也可综合利用。
滤液则排至滤液池,在滤液池内进行氧化曝气将绝大部分亚硫酸镁、亚硫酸氢镁氧化为硫酸镁后用于脱硫塔入口喷淋降温。
(3)钠钙双碱法脱硫钠钙双碱法脱硫工艺系统主要有:烟气系统、浆液制备系统、吸收系统、钠碱再生系统、氧化系统、脱硫浆液后处理系统、公用系统组成。
烟气净化流程:烟气→除尘器→引风机→湿式脱硫塔→烟道→烟囱排放脱硫液循环流程:↓钠-钙置换及脱硫产物处理工艺流程:↓(底部浓相)↓脱硫塔采用正压运行,除尘后的烟气经引风机送出后,通过进口烟道下斜10-15度进入脱硫塔,经脱硫塔内均气降温层均气降温后,到达XP-Ⅱ型高效流化脱硫除尘部件时,与来自上层喷淋装置的脱硫浆液进行充分的传质、吸收,吸收烟气中的大部分SO2并继续脱除剩余的细尘,之后烟气经两级折板除雾器脱水除雾后,由公共烟道进入烟囱达标排放。
完成脱硫后的部分脱硫液(主要含:NaHSO 3、Na 2SO 3、NaSO 4)进入置换池置,在池中与来自石灰乳制备系统的石灰乳液反应,置换、再生得到NaOH 和CaSO 3等,CaSO 3等自流进入浓缩池浓缩。
浓缩后的上清液流至综合调节池,用火碱或纯碱调整到设定的Ph 值后,用循环泵送入脱硫塔重新参与脱硫。
浓缩池底部的浓相(主要含:CaSO 3·1/2H 2O )由浓浆泵输送至真空过滤机进行过滤,过滤出固态渣,滤渣可同锅炉渣一同处理。
滤液则排至综合调节池回用。
1.3.3 系统主要特点比较(1)湿式钙法脱硫主要优点:① 技术最成熟,运行稳定,应用最多,技术可靠性好。
② 运行费用低。
石灰资源丰富,价格便宜,目前市场售价约为280元/吨左右。
③ 石灰较易溶解,石灰乳制备系统较为简单且运行稳定。
④ 脱硫效率达95~98%。
⑤对煤种变化、负荷变化的适应性强。
⑥产物为石膏,易于过滤,是所用脱硫产物中最易处理的。
主要缺点:液气比相对较高,为3~5.5L/m3,循环水量较大,耗电量较高。
(2)湿式镁法脱硫主要优点:①技术相对成熟。
我国部分地区已经有了应用的业绩。
②我国镁资源丰富,但主要分布在辽宁、山东等省。
③氧化镁化学反应活性强,反应速度快,脱硫效率达95~98%。
主要缺点:①轻烧氧化镁市场价格比石灰价格高,运行费用高。
②氧化镁相对难溶,浆液制备系统需消化(制浆)、供浆两步进行,系统较为复杂,如果直接采用工艺水制浆,氧化镁消化温度不够,将导致氧化镁在脱硫过程中反应不彻底,系统的镁硫比将远大于 1.1(北京某供热厂采用氧化镁脱硫时,实际氧化镁投加量高出设计理论量的20%以上)。
③氧化镁产地主要分布于辽东半岛和山东半岛,来源主要集中在几个大公司,对将来氧化镁粉采购带来相当难度。
从近几年北京市场看,氧化镁价格从最初的300多元每吨上涨到现今810元每吨(80%纯度),并且还有进一步上涨的趋势。
④产物亚硫酸镁过滤难度较大,含水率较高。
而产物硫酸镁为可溶性盐,不能过滤,只有以硫酸镁溶液的形式外排,导致脱硫系统外排污水量大(外排水量将在石灰法的10倍以上),相应补水量也大大超过钙法脱硫。
并且外排水还存在二次污染(可溶性盐超标)。
(3)钠钙双碱脱硫主要优点:①钠盐活性强,反应速度快,脱硫效率达95~98%。
②液气比相对较低。
③理论上,参与脱硫的为钠盐,溶解度大不易结垢。
主要缺点:①运行稳定性较差钠钙双碱法为上世纪八十年代初,因石灰石(石灰)-石膏技术不成熟的时候出现的一种折中技术,八十年代末,石灰石(石灰)-石膏技术成熟后,这种技术国外早已不再使用。
钠钙双碱法从理论上讲,先用钠碱性溶液作为吸收剂,然后将吸收SO2后的脱硫液用石灰石或石灰进行再生,再生后吸收液可循环使用,这样脱硫是清液,不会出现钙法脱硫过程中亚硫酸钙和硫酸钙不溶物的结垢现象。
但在实际工程中,部分参数很难控制,特别是置换过程中亚硫酸钙和硫酸钙的沉淀分离过程。
事实上置换过程生成亚硫酸钙结晶颗粒粒径相当小,大部分在10um以下,很难用简单沉淀法将其分离下来。
并且要求浓缩池排渣设施必须非常可靠,保证系统脱硫生成产物及时排出,防止上清夜钙离子超过饱和度。
实际上双碱法脱硫很难做到脱硫液为清液(不含钙质),所以钠钙双碱法运行中结垢情况还是比较普遍的。
同时,双碱法工艺流程较为复杂,需控制的关键参数较多,较严格,特别是置换过程的pH值控制。