球化剂在铸铁中起什么作用
铸造球化技术

铸造球化技术
铸造球化技术是一种常用的金属加工技术,常见于铸铁制造过程中。
该技术的主要目的是通过控制铸造工艺参数,使铸铁中的石墨以球形形态存在,从而提高铸铁的塑性和韧性,降低其脆性和断裂风险。
铸造球化技术的核心是控制铸造过程中的冷却速度和添加合适的球化剂。
其中,冷却速度影响石墨的成长和形态,高速冷却可促进石墨的球形化,以及提高铸件的硬度,而低速冷却则容易形成薄片状石墨,导致铸件脆性增加。
球化剂的添加可以促进石墨的球形化,常用的球化剂包括钙、硅、铝等元素,它们可以与石墨形成化合物,并在冷却过程中释放出大量热量,促进石墨的球形化。
铸造球化技术的应用范围广泛,可以应用于铸造车轮、曲轴、滚筒等各种机械零部件制造过程中。
该技术可以提高铸件的力学性能和耐磨性,延长设备的使用寿命,同时也可以减少铸造缺陷和不良品率,提高生产效率和制造质量。
球墨铸铁铸造成本-概述说明以及解释

球墨铸铁铸造成本-概述说明以及解释1.引言1.1 概述概述本文将深入探讨球墨铸铁铸造的成本问题。
球墨铸铁是一种重要的工程材料,广泛应用于汽车、机械设备、建筑等领域。
而球墨铸铁的成本是影响其应用范围和市场竞争力的重要因素之一。
球墨铸铁铸造的成本主要包括原材料、能源消耗、人工成本等多个方面。
在球墨铸铁生产过程中,原材料的选择对产品质量和成本起着关键作用。
同时,铸造过程中的耗能问题也需要引起重视,尤其是在当今提倡节能减排的社会环境下。
此外,人工成本也是影响成本的重要因素之一,包括生产工人的工资待遇、培训成本等。
文章将从球墨铸铁铸造的基本过程入手,详细介绍球墨铸铁的成本因素。
首先,我们将阐述球墨铸铁铸造的基本过程,包括模具制作、熔铁、注液、凝固、清理等环节。
然后,我们将着重分析球墨铸铁铸造的成本因素,包括原材料成本、能源消耗、人工成本等。
通过对球墨铸铁铸造成本的深入了解,我们可以更好地把握其成本控制的关键点,提高生产效率,降低成本。
而对于企业来说,控制成本意味着提升市场竞争力,实现可持续发展。
本文旨在通过对球墨铸铁铸造成本的研究,为相关行业提供有益的参考,帮助企业更好地管理和控制成本,提高产品质量和市场竞争力。
同时,也是对球墨铸铁铸造成本问题的一次深入剖析和总结。
希望本文对读者能够有所启发,并为相关研究提供一定的参考价值。
文章结构部分的内容可以从以下几个方面进行撰写:文章结构的重要性:在撰写一篇长文之前,建立清晰且有组织的文章结构非常重要。
良好的文章结构可以帮助读者更好地理解文章的脉络,使文章更易于阅读和理解。
同时,清晰的结构还可以使作者更有条理地表达观点,使文章更具说服力。
文章结构的要素:一个良好的文章结构通常包含以下要素:1. 引言部分(Introduction):引言部分主要介绍文章的背景和主题,概述文章的目的和重要性,并引起读者的兴趣和注意。
2. 正文部分(Main Body):正文部分是文章的核心部分,包含作者要表达的主要观点、论据和证据。
球墨铸铁用稀土硅镁球化剂
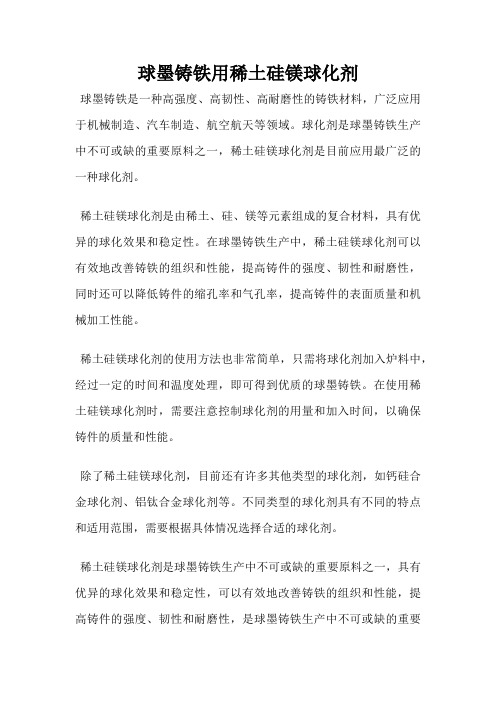
球墨铸铁用稀土硅镁球化剂
球墨铸铁是一种高强度、高韧性、高耐磨性的铸铁材料,广泛应用于机械制造、汽车制造、航空航天等领域。
球化剂是球墨铸铁生产中不可或缺的重要原料之一,稀土硅镁球化剂是目前应用最广泛的一种球化剂。
稀土硅镁球化剂是由稀土、硅、镁等元素组成的复合材料,具有优异的球化效果和稳定性。
在球墨铸铁生产中,稀土硅镁球化剂可以有效地改善铸铁的组织和性能,提高铸件的强度、韧性和耐磨性,同时还可以降低铸件的缩孔率和气孔率,提高铸件的表面质量和机械加工性能。
稀土硅镁球化剂的使用方法也非常简单,只需将球化剂加入炉料中,经过一定的时间和温度处理,即可得到优质的球墨铸铁。
在使用稀土硅镁球化剂时,需要注意控制球化剂的用量和加入时间,以确保铸件的质量和性能。
除了稀土硅镁球化剂,目前还有许多其他类型的球化剂,如钙硅合金球化剂、铝钛合金球化剂等。
不同类型的球化剂具有不同的特点和适用范围,需要根据具体情况选择合适的球化剂。
稀土硅镁球化剂是球墨铸铁生产中不可或缺的重要原料之一,具有优异的球化效果和稳定性,可以有效地改善铸铁的组织和性能,提高铸件的强度、韧性和耐磨性,是球墨铸铁生产中不可或缺的重要
原料之一。
球铁球化率的作用
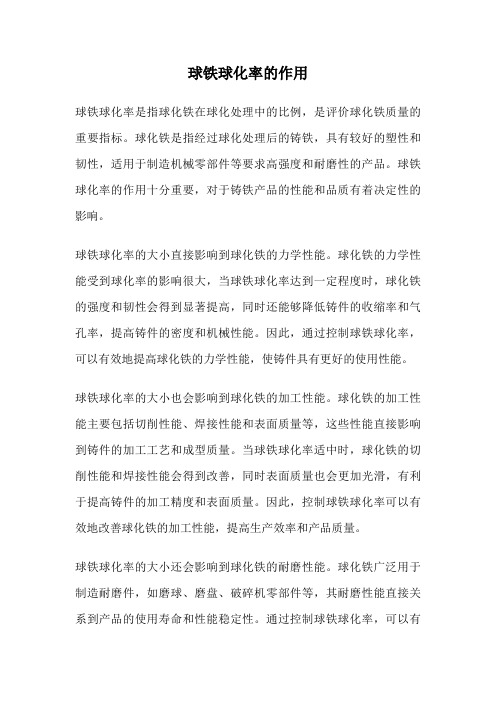
球铁球化率的作用球铁球化率是指球化铁在球化处理中的比例,是评价球化铁质量的重要指标。
球化铁是指经过球化处理后的铸铁,具有较好的塑性和韧性,适用于制造机械零部件等要求高强度和耐磨性的产品。
球铁球化率的作用十分重要,对于铸铁产品的性能和品质有着决定性的影响。
球铁球化率的大小直接影响到球化铁的力学性能。
球化铁的力学性能受到球化率的影响很大,当球铁球化率达到一定程度时,球化铁的强度和韧性会得到显著提高,同时还能够降低铸件的收缩率和气孔率,提高铸件的密度和机械性能。
因此,通过控制球铁球化率,可以有效地提高球化铁的力学性能,使铸件具有更好的使用性能。
球铁球化率的大小也会影响到球化铁的加工性能。
球化铁的加工性能主要包括切削性能、焊接性能和表面质量等,这些性能直接影响到铸件的加工工艺和成型质量。
当球铁球化率适中时,球化铁的切削性能和焊接性能会得到改善,同时表面质量也会更加光滑,有利于提高铸件的加工精度和表面质量。
因此,控制球铁球化率可以有效地改善球化铁的加工性能,提高生产效率和产品质量。
球铁球化率的大小还会影响到球化铁的耐磨性能。
球化铁广泛用于制造耐磨件,如磨球、磨盘、破碎机零部件等,其耐磨性能直接关系到产品的使用寿命和性能稳定性。
通过控制球铁球化率,可以有效地改善球化铁的耐磨性能,提高产品的耐磨性和抗疲劳性能,延长产品的使用寿命,降低维护成本。
总的来说,球铁球化率在球化铁生产和应用中起着至关重要的作用。
通过科学合理地控制球铁球化率,可以有效地改善球化铁的力学性能、加工性能和耐磨性能,提高产品的质量和性能,满足不同工程领域对铸铁产品的需求。
因此,加强对球铁球化率的控制和研究,对于提高球化铁的品质和竞争力具有重要意义。
希望通过不断的技术创新和工艺改进,进一步提高球铁球化率,推动球化铁产业的发展,为我国制造业的升级和转型做出贡献。
球墨铸铁用球化剂

球墨铸铁用球化剂
球墨铸铁是一种具有优异性能的铸铁,其强度和延展性能相对于普通铸铁更出色,这得益于它所使用的球化剂。
球化剂是一种能够促进球墨铸铁球化反应的添加剂。
通过球化剂的作用,将铸铁中的碳以球状分布,从而使合金铸铁增加韧性、塑性和强度,降低铸铁的脆性,提高其机械性能。
球化剂种类繁多,每种球化剂所发挥的作用也各有不同。
其中几种常见的球化剂包括钉形铁素体晶核剂、钒铁铝、锰硅合金等。
这些球化剂大都含有一定量的铝、钛、锰、硅、钒等元素,这些元素通常能够形成稳定的化合物,促进碳的球化反应。
在使用球化剂时,还需要控制其加入时机、用量和温度等因素,以确保其球化效果达到最佳。
同时,在球化剂的选择上,还要根据不同铸铁的特点和使用要求进行选择。
总之,球化剂在球墨铸铁生产过程中起着非常重要的作用。
它们能够大大提高合金铸铁的机械性能和使用寿命,同时使得球墨铸铁在机械制造、汽车制造等领域得到广泛应用。
铸造用球化剂

铸造用球化剂
铸造用球化剂是一种能够在铸造过程中改善铸件内部组织结构
的化学物质。
球化剂的主要成分是镁和铝等金属元素,其作用是通过与铁和碳等元素反应,使其形成球状颗粒,从而改善铸件的力学性能和加工性能。
球化剂广泛应用于铸铁、球墨铸铁、铜合金等铸造材料的生产中。
经过球化处理的铸件具有较好的韧性、耐磨性和抗拉强度等性能,能够有效地提高铸件的质量和使用寿命。
在使用球化剂进行铸造时,需要按照一定的配比和工艺流程进行操作,以确保球化效果的稳定性和一致性。
同时,球化剂的用量和质量也会影响铸件的质量和性能,因此需要严格控制其使用量和质量。
总的来说,铸造用球化剂是铸造行业中非常重要的一种材料,其能够显著提高铸件的性能和质量,为铸造生产带来了巨大的经济和社会效益。
- 1 -。
球化剂的用途

球化剂在铸铁中起什么作用2010-01-09 15:54球墨铸铁问世至今已有52年,其发展迅速之快令人惊讶,即使在经济不景气的情况下,球铁仍然有所发展,有人称球墨铸铁为不适当退却中的胜利者,指出:球墨铸铁由于其高强度、高韧性和低价格,所以在材料市场上仍占有重要的地位,尽管几年来钢铁铸造总产量有所下降,但球铁产量并未下降,奥——贝球铁的出现增强了球铁的竞争地位。
1.球铁的生产和研究现状 1. 1常规球铁目前常规球铁——即以铁素体和珠光体为基体的球铁仍占球铁产量中的绝大部分比例,因此注意提高常规球铁的性能和质量,在保持球铁的竞争地位中起了重要的作用。
1.1. 1对影响球铁质量的因素加强控制球铁的组织与性能取决于铸铁的成份和结晶条件以及所用球化剂的质量,研究认为为了确保球铁的机械性能,必须针对铸件具体壁厚、浇注温度、所用球化剂、球化处理工艺、冷却参数的优化以及有效的排渣措施进行严格控制,而适当的降低碳当量,合金化和热处理是改善球铁的有效措施。
1.1.2有效控制铁素体球铁和球光体球铁的生产[2] 控制球铁基体的主要因素有铸铁的成份、所用球化剂、孕育剂的类型,加入方法以及冷却条件等。
铸态铁素体球铁的成份控制微过共晶成份,其中碳稍高,但不出现石墨漂浮,含硅稍低,孕育剂硅量应少于3%,锰越低越好,应使Mn<0.04%,硫、磷应低,使S≤0.02%、P≤0.02%,这是因为硅可改善球铁组织和相应的塑性,Si=3.0~3.5%可得到全部铁素体组织。
有研究指出,Si=2.6~2.8%时,铸铁具有最高的延伸率和冲击韧性,但硅在铁中的显微偏析随着含磷量的增加,这种偏析越严重,并对机械性能有不良影响,特别是当温度低于零度时影响更大,而含硫低可以选用低镁低稀土球化剂球化,并减少“黑斑”缺陷的产生,而“黑斑”主要是镁、铈硫化物和氧化物的聚集物,此外也要用低硅球化剂以保证可以进行多次孕育。
对珠光体球铁而言,在生产时铸铁成份中锰可提高至0.8~1.0%,有些铸件如果是用作耐磨性曲轴时,锰可提高至1.2~1.35%,生产铸态珠光体元素铜。
球墨铸铁的焊接

球墨铸铁是在熔炼过程中加入一定量的球化剂,使石墨以球状存在,从而使力学性能明显提高。
1. 球墨铸铁的焊接性球墨铸铁焊接性与灰铸铁有相同的一面,但又有其自身的一些特点。
这主要表现在两方面。
(1)球墨铸铁的白口化倾向及淬硬倾向比灰铸铁大,这是因为球化剂(当其加入量已可稳定获得球状石墨时)有阻碍石墨化及提高淬硬临界冷却速度的作用,所以,在焊接球墨铸铁时,同质焊缝及半熔化区更易形成白口,奥氏体区更易出现马氏体组织。
(2) 由于球铁的强度、塑性与韧性比灰铸铁高,故对焊接接头的力学性能要求也相应提高,常要求与各强度等级球墨铸铁母材相匹配。
2. 球墨铸铁电弧补焊球墨铸铁电弧补焊采用同质及异质焊条,同质焊条又有钢芯与铸芯之别。
异质焊条则采用镍基焊条(Z408)及高钒焊条,对于不重要的部位也可以采用低碳钢焊条,如J506、J422等。
球墨铸铁通常应用于比较重要的场合,采用同质焊条焊接时应保证焊缝球化,力学性能达到规定的指标,应尽量降低白口倾向,提高抗裂性。
(1) Z238焊条电弧热焊。
Z238焊条为低碳钢焊芯,药皮中加入球化剂及石墨化剂,在一定工艺条件下,焊缝中的石墨可成为球状,能够得到较好的力学性能。
由于电弧温度较高,球化元素氧化、蒸发严重,给焊缝的稳定球化带来困难,力学性能很难达到指标。
采用Z238焊条,白口倾向较大,因此,焊接时通常进行400~700℃预热,必要时焊后要进行退火或正火处理。
(2)钢芯石墨球化通用铸铁焊条补焊。
该种类焊条采用钢芯,药皮中加入脱氧元素、孕育剂及少量的球化剂。
这种焊条对水分、空气、铁锈等不敏感,球化稳定性很高,白口倾向低,焊缝的塑性及抗裂性都较好。
对于刚性较小的部位,可以采用冷焊工艺补焊较长的焊缝或较大的面积,但是,刚性较大的部位应进行预热或采用加热减应区法,焊缝的力学性能较好。
接头正火后,抗拉强度约为650MPa,伸长率约为5%。
接头退火后的抗拉强度一般大于420MPa,伸长率大于10%,最高可达20%以上。
铸铁球化剂
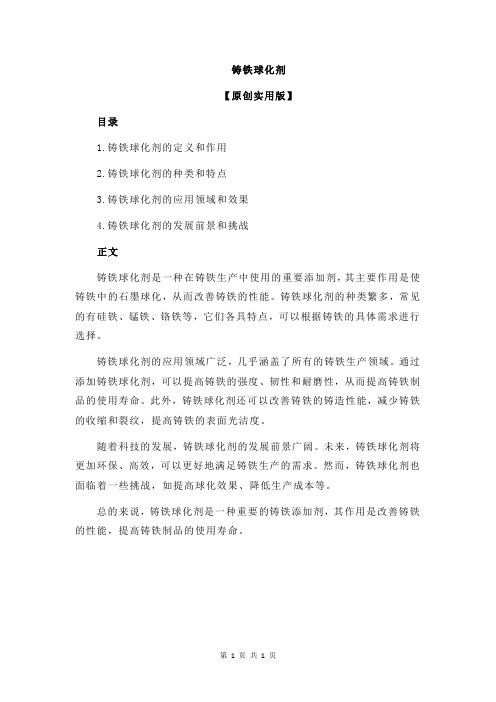
铸铁球化剂
【原创实用版】
目录
1.铸铁球化剂的定义和作用
2.铸铁球化剂的种类和特点
3.铸铁球化剂的应用领域和效果
4.铸铁球化剂的发展前景和挑战
正文
铸铁球化剂是一种在铸铁生产中使用的重要添加剂,其主要作用是使铸铁中的石墨球化,从而改善铸铁的性能。
铸铁球化剂的种类繁多,常见的有硅铁、锰铁、铬铁等,它们各具特点,可以根据铸铁的具体需求进行选择。
铸铁球化剂的应用领域广泛,几乎涵盖了所有的铸铁生产领域。
通过添加铸铁球化剂,可以提高铸铁的强度、韧性和耐磨性,从而提高铸铁制品的使用寿命。
此外,铸铁球化剂还可以改善铸铁的铸造性能,减少铸铁的收缩和裂纹,提高铸铁的表面光洁度。
随着科技的发展,铸铁球化剂的发展前景广阔。
未来,铸铁球化剂将更加环保、高效,可以更好地满足铸铁生产的需求。
然而,铸铁球化剂也面临着一些挑战,如提高球化效果、降低生产成本等。
总的来说,铸铁球化剂是一种重要的铸铁添加剂,其作用是改善铸铁的性能,提高铸铁制品的使用寿命。
第1页共1页。
铸造课堂:球化剂在球墨铸铁生产中的作用,如何准确使用球化剂以达到提高铸件质量,防止缺陷的发生!

铸造课堂:球化剂在球墨铸铁生产中的作用,如何准确使用球化剂以达到提高铸件质量,防止缺陷的发生!1.球化剂及球化元素在球墨铸铁生产中的作用内容导读:尽管国内外球化剂的种类很多,但在我们国内目前应用最多的还是稀土镁类合金,现主要论述该类合金及其球化元素的作用。
1.1球化元素及反球化元素1.1.1球化元素的作用所谓球化元素是指那些能够促进石墨球状化、使石墨球生成或增加的元素。
球化元素一般有以下共同性质:(1)元素最外电子层上有一个或两个价电子,次内层有8个电子。
这种电子结构使元素与硫、氧和碳有较强的亲和力,反映产物稳定,能显著减少贴水中的硫和氧。
(2)元素在铁水中溶解度低,凝固过程中有显著偏析倾向。
(3)虽然和碳有一定亲和力,但在石墨晶格内溶解度低。
根据以上特点,Mg,Ce,Y,Ca属于有效球化元素。
一是在铁水中蒸气压力高,使铁水佛腾。
镁的原子量和密度比铁水小,熔点650度,沸点1108度,在铁水的处理温度下,镁产生的蒸气压力很高(超过1Mpa).镁的熔解热为21J/g,蒸发潜热为406J/g。
因此,镁加入铁水时,要产生汽化,使铁水翻腾。
二是与硫、氧有很强的亲和力。
所生成的MgO和MgS熔点高,密度也远小于铁,容易与铁水分离,因此镁处理后的铁水,硫和羊的含量都很低;三是在铁水凝固过程中有偏析于石墨的倾向,当其在铁水中的残留量超过0.035%时,使末就可以球化,但当镁残留量超过0.07%时,一部分镁偏析于晶界,并于晶界中的碳、磷等发生放热反应,生成MgC2、Mg2C3、Mg3P2等。
残留镁量更多时,晶间碳化物增多。
稀土族元素对石墨球化有显著作用的是轻稀土元素中的铈和重稀土中的钇。
一是稀土元素的沸点均比镁高,加入铁水中时,不会引起铁水的翻腾和喷溅;二是铈和钇基稀土元素有比镁更强的脱硫脱氧能力,生成的硫化稀土、氧化稀土等化合物熔点高、稳定性好;三是,稀土元素与铁水中的球化干扰元素也能形成稳定的化合物,因此含稀土的球化剂比镁球化剂的抗干扰能力强。
镧系球化剂在球墨铸铁件生产中的应用

镧系球化剂在球墨铸铁件生产中的应用
镧系球化剂在球墨铸铁件生产中广泛应用。
球墨铸铁是一种强度高、韧性好、耐磨、耐腐蚀的铸造材料,其主要成分为铁、碳和硅。
为了提高球墨铸铁的机械性能,需要在生产过程中将铸铁中的石墨化为球状,这就需要使用球化剂。
镧系球化剂是一种非常有效的球化剂,主要成分是镧和其他合金元素。
将镧系球化剂添加到熔融的铸铁中,可以促使石墨球化为球状,从而提高铸铁的塑性和韧性。
与其他球化剂相比,镧系球化剂具有以下优点:
1. 高效性:镧系球化剂可以在相对较低的添加量下实现良好的球化效果,能够在短时间内将大部分石墨球化。
2. 稳定性:镧系球化剂在高温下稳定性较好,不易氧化和蒸发,可以保持较长时间的球化效果。
3. 均匀性:镧系球化剂的分散均匀,可以保证铸铁中石墨球化的均匀性,避免出现孤立的石墨片。
4. 经济性:镧系球化剂是价格相对较低的球化剂之一,能够在铸铁生产过程中实现节约成本。
因此,镧系球化剂在球墨铸铁件生产中得到了广泛的应用,提
高了球墨铸铁的机械性能和工艺性能,推动了球墨铸铁行业的发展。
球化剂对球铁影响

球化剂对球铁影响
球化剂对球铁的影响主要体现在以下几个方面:
1. 促使铸件中的碳以球状石墨的形式出现:球化剂能够在液态铁中引入一定的稳定元素,如钡、镁等。
稳定元素在处理过程中与铁中的碳结合,形成球状石墨,从而增强了铸件的塑性和韧性。
球状石墨的形成还能够提高铸件的高温稳定性和抗疲劳性能。
2. 改善铸件的表面质量:球化剂能够促使铁水中的夹杂物形成球状而不是片状。
片状夹杂物容易导致铸件的表面粗糙和气孔,而球状夹杂物能够减少这些缺陷,提高铸件的表面质量。
3. 提高铸件的机械性能:球化剂能够改善铸件的力学性能,如降低铸件的脆性,提高抗拉强度和屈服强度。
这是因为球状石墨的形成能够提高铸件的塑性和韧性,使其更能耐受拉伸和冲击载荷。
4. 优化铁水的凝固组织:球化剂能够改善铁水的凝固组织,使其凝固过程更加均匀和稳定。
这有助于减少铸件内部的缩孔和偏析,提高铸件的综合性能和铸造工艺的稳定性。
需要注意的是,球化剂的种类和添加量等因素对球铁的影响也会有差异,具体效果需根据铸造工艺和应用要求进行选择和调整。
球墨铸铁球化机理

球墨铸铁球化机理
球墨铸铁是一种高性能铸铁,其独特的球状石墨形态使其具有出色的韧性、强度和耐磨性,成为各种工业领域中的首选材料。
而球化是球墨铸铁制造过程中不可或缺的步骤,其目的是将灰口铸铁中的石墨球化成球墨石墨,以提高材料的力学性能。
球化机理主要包括两个方面,即球化剂的作用和铸造工艺的影响。
球化剂是实现球化的关键,其作用是在铁液中形成稳定的球墨石墨结构。
常用的球化剂有镁、稀土等元素。
镁作为球化剂时,可以在铁液中与硫、氧等元素反应,生成稳定的球墨石墨结构。
稀土元素可以通过改变石墨的形态和大小来促进球化。
除了球化剂的作用外,铸造工艺也对球化效果有重要影响。
铸造温度、浇注速度、浇注压力等因素都会影响球化效果。
一般来说,较高的铸造温度、合适的浇注速度和压力可以提高球化效果。
总之,球墨铸铁的球化机理是一个复杂的过程,需要综合考虑球化剂和铸造工艺等多种因素,才能获得优良的球墨铸铁材料。
- 1 -。
球墨铸铁中的碳化物
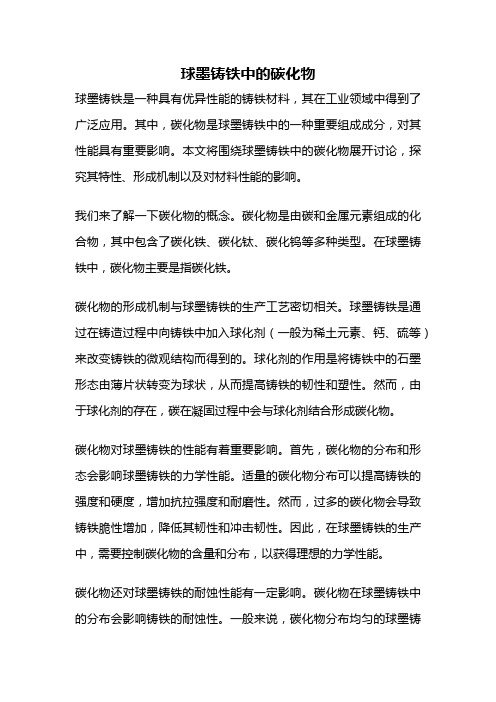
球墨铸铁中的碳化物球墨铸铁是一种具有优异性能的铸铁材料,其在工业领域中得到了广泛应用。
其中,碳化物是球墨铸铁中的一种重要组成成分,对其性能具有重要影响。
本文将围绕球墨铸铁中的碳化物展开讨论,探究其特性、形成机制以及对材料性能的影响。
我们来了解一下碳化物的概念。
碳化物是由碳和金属元素组成的化合物,其中包含了碳化铁、碳化钛、碳化钨等多种类型。
在球墨铸铁中,碳化物主要是指碳化铁。
碳化物的形成机制与球墨铸铁的生产工艺密切相关。
球墨铸铁是通过在铸造过程中向铸铁中加入球化剂(一般为稀土元素、钙、硫等)来改变铸铁的微观结构而得到的。
球化剂的作用是将铸铁中的石墨形态由薄片状转变为球状,从而提高铸铁的韧性和塑性。
然而,由于球化剂的存在,碳在凝固过程中会与球化剂结合形成碳化物。
碳化物对球墨铸铁的性能有着重要影响。
首先,碳化物的分布和形态会影响球墨铸铁的力学性能。
适量的碳化物分布可以提高铸铁的强度和硬度,增加抗拉强度和耐磨性。
然而,过多的碳化物会导致铸铁脆性增加,降低其韧性和冲击韧性。
因此,在球墨铸铁的生产中,需要控制碳化物的含量和分布,以获得理想的力学性能。
碳化物还对球墨铸铁的耐蚀性能有一定影响。
碳化物在球墨铸铁中的分布会影响铸铁的耐蚀性。
一般来说,碳化物分布均匀的球墨铸铁具有较好的耐蚀性能。
然而,如果碳化物分布不均匀或过多,会导致局部腐蚀的发生,降低铸铁的耐蚀性能。
因此,在球墨铸铁的制备中,需要合理控制碳化物的分布,以提高其耐蚀性。
碳化物还对球墨铸铁的热处理性能有一定影响。
在球墨铸铁的热处理过程中,碳化物的存在会影响材料的相变行为和组织结构。
碳化物的形态和分布会影响铸铁的回火性能和热处理硬化性能。
因此,在球墨铸铁的热处理过程中,需要考虑碳化物的存在对材料性能的影响,采取适当的热处理工艺控制碳化物的形态和分布,以获得所需的材料性能。
碳化物作为球墨铸铁中的重要组成成分,对材料性能具有重要影响。
通过合理控制碳化物的含量和分布,可以获得理想的力学性能、耐蚀性能和热处理性能。
球墨铸铁用稀土球化剂

球墨铸铁用稀土球化剂
球墨铸铁用稀土球化剂是一种用于球墨铸铁生产中的添加剂。
稀土球化剂可以促进球墨铸铁中的碳素球化,从而提高铁件的力学性能和耐磨性能。
稀土球化剂通常由氧化物或氯化物制成,其中包括氧化镧、氧化钕、氧化铈等稀土元素。
稀土球化剂的加入量通常为球墨铸铁总重量的0.05-0.1%,具体的加入量要根据生产工艺和铸件性能要求而定。
加入稀土球化剂后,球墨铸铁的微观组织结构将得到改善,碳素球的数量和尺寸将得到控制,从而提高铁件的力学性能和耐磨性能。
稀土球化剂的使用具有以下优点:一是球化效果好,可以在较短时间内完成碳素球化过程;二是球化均匀性好,可以得到均匀细小的碳素球;三是稀土元素可以与铁中的硫化物结合形成稳定的硫化物,从而减少了铁水中的硫含量,有利于减少铁件的缺陷率。
总之,稀土球化剂是球墨铸铁生产中必不可少的一种添加剂,可以提高铁件的性能和质量,推动球墨铸铁生产技术的发展和进步。
- 1 -。
球墨铸铁的工艺原理
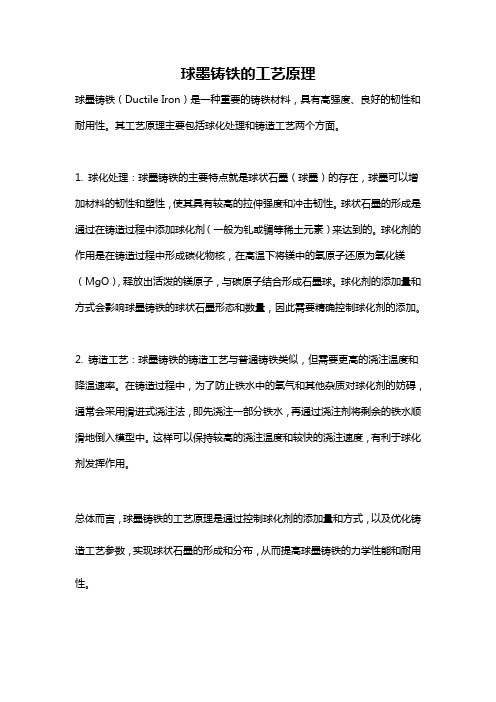
球墨铸铁的工艺原理
球墨铸铁(Ductile Iron)是一种重要的铸铁材料,具有高强度、良好的韧性和耐用性。
其工艺原理主要包括球化处理和铸造工艺两个方面。
1. 球化处理:球墨铸铁的主要特点就是球状石墨(球墨)的存在,球墨可以增加材料的韧性和塑性,使其具有较高的拉伸强度和冲击韧性。
球状石墨的形成是通过在铸造过程中添加球化剂(一般为钆或镧等稀土元素)来达到的。
球化剂的作用是在铸造过程中形成碳化物核,在高温下将镁中的氧原子还原为氧化镁(MgO),释放出活泼的镁原子,与碳原子结合形成石墨球。
球化剂的添加量和方式会影响球墨铸铁的球状石墨形态和数量,因此需要精确控制球化剂的添加。
2. 铸造工艺:球墨铸铁的铸造工艺与普通铸铁类似,但需要更高的浇注温度和降温速率。
在铸造过程中,为了防止铁水中的氧气和其他杂质对球化剂的妨碍,通常会采用滑进式浇注法,即先浇注一部分铁水,再通过浇注剂将剩余的铁水顺滑地倒入模型中。
这样可以保持较高的浇注温度和较快的浇注速度,有利于球化剂发挥作用。
总体而言,球墨铸铁的工艺原理是通过控制球化剂的添加量和方式,以及优化铸造工艺参数,实现球状石墨的形成和分布,从而提高球墨铸铁的力学性能和耐用性。
球墨铸铁生产球化剂作用汇总

球墨铸铁生产球化剂作用汇总铸造工业网昨天1.球铁的生产和研究现状1. 1常规球铁目前常规球铁——即以铁素体和珠光体为基体的球铁仍占球铁产量中的绝大部分比例,因此注意提高常规球铁的性能和质量,在保持球铁的竞争地位中起了重要的作用。
1.1. 1对影响球铁质量的因素加强控制球铁的组织与性能取决于铸铁的成份和结晶条件以及所用球化剂的质量,研究认为为了确保球铁的机械性能,必须针对铸件具体壁厚、浇注温度、所用球化剂、球化处理工艺、冷却参数的优化以及有效的排渣措施进行严格控制,而适当的降低碳当量,合金化和热处理是改善球铁的有效措施。
1.1.2有效控制铁素体球铁和球光体球铁的生产控制球铁基体的主要因素有铸铁的成份、所用球化剂、孕育剂的类型,加入方法以及冷却条件等。
铸态铁素体球铁的成份控制微过共晶成份,其中碳稍高,但不出现石墨漂浮,含硅稍低,孕育剂硅量应少于3%,锰越低越好,应使Mn<0.4%,硫、磷应低,使S≤0.02%、P≤0.02%,这是因为硅可改善球铁组织和相应的塑性,Si=3.0~3.5%可得到全部铁素体组织。
有研究指出,Si=2.6~2.8%时,铸铁具有最高的延伸率和冲击韧性,但硅在铁中的显微偏析随着含磷量的增加,这种偏析越严重,并对机械性能有不良影响,特别是当温度低于零度时影响更大,而含硫低可以选用低镁低稀土球化剂球化,并减少“黑斑”缺陷的产生,而“黑斑”主要是镁、铈硫化物和氧化物的聚集物,此外也要用低硅球化剂以保证可以进行多次孕育。
对珠光体球铁而言,在生产时铸铁成份中锰可提高至0.8~1.0%,有些铸件如果是用作耐磨性曲轴时,锰可提高至1.2~1.35%,生产铸态珠光体元素铜。
加入量大于1.8%时,它阻碍石墨球化,但促进基体完全珠光体化,一般球铁中铜含量应小于1.5%,锡是强烈的珠光体化元素,其对硬度的影响大于铜和锰,但Sn≥0.1%时使石墨畸变,因此其含量应限制在0.08%以下。
1.1.3 稀土在球铁中的作用稀土能促进镁合金的球化效果(球化率和球的圆整度),它对壁厚球铁件中防止球状石墨畸变的效果受到了重视,这也是国内外球化剂中都包含稀土的主要原因之一。
铸铁中孕育剂的作用

铸铁中孕育剂的作用
铸造中的孕育和球化处理一般是针对球铁而言的,球铁是用灰铁成分的铁液经球化处理和孕育处理得到的。
将球化剂加入铁水的操作过程叫球化处理。
我国常用的球化剂有镁、稀土或稀土硅镁合金。
纯镁的球化作用很强,球化率高,容易获得完整的石墨。
但是纯镁又是很强的阻碍石墨化的元素,有增大铸铁白口化的倾向。
由于纯镁的沸点远低于铁水温度,因此纯镁加入铁水中沸腾飞溅、烧损严重,需要采用压力加镁办法,处理工艺和设备较为复杂。
而且铸件的收缩、疏松夹渣、皮下气泡等缺陷较为严重。
因此镁及稀土元素都强烈组织石墨化,铁水经球化处理后容易出现白口,难以产生石墨核心。
因此,球化处理的同时,必须进行孕育处理。
孕育剂必须含有强烈促进石墨化的元素,通常采用含硅量是75%的硅铁和硅钙合金。
经孕育处理后的球铁,石墨球铁量增加,球径减小,形状圆整,分布均匀,从而显著改善了球铁的机械性能。
镧系球化剂在球墨铸铁件生产中的应用

镧系球化剂在球墨铸铁件生产中的应用柯志敏;何良荣;陈永成【摘要】介绍镧系球化剂在使用安全要求较高的球墨铸铁件生产中的应用。
生产实践表明:使用镧系球化剂球化处理后,不仅可以提高球墨铸铁件内在质量,如提高球化率,增加石墨球数,消除碎块状石墨,减少缩松倾向等,而且可以降低生产成本,具有显著的经济效益。
%This paper mainly introduced the applicationof La based FSM (nodulizer) in safety-critical components ductile iron castings. The production practice proved: through using La basedFSM(nodulizer), it can improve the inner quality of the castings, such as high the nodularity, increase the nodule counts, removing the chunky graphite, reduce the tendency of shrinkage, and reduce the production cost, it have obvious economic beneift.【期刊名称】《中国铸造装备与技术》【年(卷),期】2016(000)001【总页数】3页(P16-18)【关键词】镧;球化剂;球墨铸铁件;球化率;缩松【作者】柯志敏;何良荣;陈永成【作者单位】中天创展球铁有限公司,广东顺德528313;中天创展球铁有限公司,广东顺德 528313;中天创展球铁有限公司,广东顺德 528313【正文语种】中文【中图分类】TG255随着球墨铸铁技术的发展,其性能的不断提高,优质廉价的球墨铸铁已在注塑机械、工程机械等领域得到充分应用。
- 1、下载文档前请自行甄别文档内容的完整性,平台不提供额外的编辑、内容补充、找答案等附加服务。
- 2、"仅部分预览"的文档,不可在线预览部分如存在完整性等问题,可反馈申请退款(可完整预览的文档不适用该条件!)。
- 3、如文档侵犯您的权益,请联系客服反馈,我们会尽快为您处理(人工客服工作时间:9:00-18:30)。
球化剂在铸铁中起什么作用球墨铸铁问世至今已有52年,其发展迅速之快令人惊讶,即使在经济不景气的情况下,球铁仍然有所发展,有人称球墨铸铁为不适当退却中的胜利者,指出:球墨铸铁由于其高强度、高韧性和低价格,所以在材料市场上仍占有重要的地位,尽管几年来钢铁铸造总产量有所下降,但球铁产量并未下降,奥——贝球铁的出现增强了球铁的竞争地位。
1.球铁的生产和研究现状1. 1常规球铁目前常规球铁——即以铁素体和珠光体为基体的球铁仍占球铁产量中的绝大部分比例,因此注意提高常规球铁的性能和质量,在保持球铁的竞争地位中起了重要的作用。
1.1. 1对影响球铁质量的因素加强控制球铁的组织与性能取决于铸铁的成份和结晶条件以及所用球化剂的质量,研究认为为了确保球铁的机械性能,必须针对铸件具体壁厚、浇注温度、所用球化剂、球化处理工艺、冷却参数的优化以及有效的排渣措施进行严格控制,而适当的降低碳当量,合金化和热处理是改善球铁的有效措施。
1.1.2有效控制铁素体球铁和球光体球铁的生产[2]控制球铁基体的主要因素有铸铁的成份、所用球化剂、孕育剂的类型,加入方法以及冷却条件等。
铸态铁素体球铁的成份控制微过共晶成份,其中碳稍高,但不出现石墨漂浮,含硅稍低,孕育剂硅量应少于3%,锰越低越好,应使Mn<0.04%,硫、磷应低,使S≤0.02%、P≤0.02%,这是因为硅可改善球铁组织和相应的塑性,Si=3.0~3.5%可得到全部铁素体组织。
有研究指出,Si=2.6~2.8%时,铸铁具有最高的延伸率和冲击韧性,但硅在铁中的显微偏析随着含磷量的增加,这种偏析越严重,并对机械性能有不良影响,特别是当温度低于零度时影响更大,而含硫低可以选用低镁低稀土球化剂球化,并减少“黑斑”缺陷的产生,而“黑斑”主要是镁、铈硫化物和氧化物的聚集物,此外也要用低硅球化剂以保证可以进行多次孕育。
对珠光体球铁而言,在生产时铸铁成份中锰可提高至0.8~1.0%,有些铸件如果是用作耐磨性曲轴时,锰可提高至1.2~1.35%,生产铸态珠光体元素铜。
加入量大于 1.8%时,它阻碍石墨球化,但促进基体完全珠光体化,一般球铁中铜含量应小于 1.5%,锡是强烈的珠光体化元素,其对硬度的影响大于铜和锰,但Sn≥1.0%时使石墨畸变,因此其含量应限制在0.08%以下。
1.1.3 稀土在球铁中的作用稀土能促进镁合金的球化效果(球化率和球的圆整度),它对壁厚球铁件中防止球状石墨畸变的效果受到了重视,这也是国内外球化剂中都包含稀土的主要原因之一。
在铸件中有些元素能破坏和阻碍石墨球化,这些元素即所谓的球化干扰元素,干扰元素分为两类,一是消耗球化元素型干扰元素,它们与镁、稀土生成MgS、MgO、MgSe、RE2O3、RE2S3、RE2Te3等,使球化元素降低从而破坏了球状石墨形成;另一类是晶间偏析型干扰元素,包括锡、锑、砷、铜、钛、铝等在共晶结晶时,这些元素富集在晶界,促进使碳在共晶后期形成畸形的枝晶状石墨,球化干扰元素原子量越大,其干扰作用越强,现在许多研究都已找到了干扰元素在铸铁中的临界含量,当这些元素含量小于临界含量时,并不能形成畸变石墨。
在有干扰元素的铸铁中,加入稀土可消除其干扰作用,有研究报告指出在铸铁中干扰元素之和应小于0.10%即z=Ti+Cr+Sb+V+As+Pb+Zn+…<0.10% 有研究指出,中和铁水中的Al、Sb、TI、Pb、Bi、等只要分别加入0.005~0.04%Ce即可,例如,中和Ti、Pb、Sb、Al等只要分别加入0.005~0.007%、0.014%、0.15%和0.008%的Ce即可。
干扰元素在铸件壁厚,冷却速度慢的情况下破坏作用更大。
干扰元素对球铁基体也有影响,Te、B强烈促进白口形成,Cr、As、Sn、Sb、Pb、Bi稳定珠光体,Al、Zr促进铁素体。
值得注意的是,目前正在发展一些球化元素与干扰元素复合球化剂,以改善大断面球铁的处理效果及石墨球的圆整度。
1.1. 4球铁检测加强球铁检测是保证其质量的重要措施,目前正在研究发展线分析,即产品在生产过程中进行分析,以确定其质量,已有不少单位在大批量生产条件下利用超声波对铸件质量进行分析。
在利用超声波测定铸铁组织时,片状石墨的声速为4500m/s、蠕墨铸铁为5400m/s、球墨铸铁5600m/s,此外在铸铁中高频衰减率的变化也可判断铸铁类型,球铁中心频率为5MHz而片状铸铁仅为1.5MHz。
目前还有单位正在用超声波作球化级别的测定,已可测定合格的球化级别和不合格的产品(3级和4级之间),但还不能进行更细分级测定,此方法正在完善中。
1.2奥——贝球铁世纪70年代,荷兰、中国、美国彼此独立地,几乎是同时宣布各自研究成功了贝氏体球铁,中国研究成功的是下贝氏体,美国为下贝氏体+马氏体,荷兰为上贝氏体+奥氏体,荷兰成果最具代表性,即现在所称的奥——贝球铁。
1977年M.Jokason宣布荷兰的Kgmi Kgmmene公司所属的karkkila铸造厂开发了一种特性优异的新型铸铁,即奥——贝球铁,并在1978年召开第45届国际年会上宣读了有关论文,此一发明在美、英、法、加等13个国家申请了专利(美国专利号:3860457,荷兰专利1996/72,原西德专利2852870),引起了各国重视,被誉为近几十年来铸铁冶金中的重大成就之一。
奥——贝球铁兼备高强度、高韧性和高耐磨性。
如英国的标准有NE-GJS-800-8,EN-GJS-1000-5,EN-GJS-1400-1。
奥——贝球铁成份与常规球铁成份相同,球化剂和处理工艺也相同,其差别是必须进行等温淬火处理,等温淬火温度不同时可分别获得上贝氏体+奥氏体,下贝氏+奥氏体,下贝氏+马氏体等不同基体。
这种铸铁成本高、生产难度较大,目前应用面虽在不断扩大,但其总量并不大,被人们称之为21世纪材料。
2.球化剂的现状球化剂是目前获得球铁的主要手段之一,在志包钢稀土一厂共同完成国家攻关课题“稀土三剂系列化”时,我校课题组对世界上100多个球化剂生产厂,国内主要合金生产进行调研,取得了英、美、法、德、日、前苏联、印度等十几个国家50多家合金生产厂的产品样本及国内主要球化剂生产厂的产品样本,为对比国内外球化剂性能及今后球化剂生产改进提供了依据。
2.1球化剂的类型按生产方式分有下述几种(1)球化剂的类型包括镁硅系合金、稀土镁硅系合金、钙系合金(日本用的较多),镍镁系合金、纯镁合金、稀土合金。
上述合金中目前世界上用的最为广泛的是稀土镁硅铁合金,但中国合金中RE/Mg的比值范围大(0.5~2.2),国外的合金RE/Mg的比值范围小(0.1~0.3)。
中国合金中稀土大于等于镁含量的占多数,小于镁含量的占少数,而国外(除前苏联一些合金外)球化剂合金中的稀土含量几乎都小于镁含量,因此稀土三剂系列化课题组建议除保留FeSlMg8E18外(此合金是效果优良的蠕化剂),其它全部球化剂中RE/Mg≤1,随后修订的国家标准中采纳了这个建议。
钙镁球化剂主要是日本生产和应用,如日本信越(SHIN—ETSU)生产的钙系合金NC5、NCl0、NCl5、NC20、NC25中镁含量从4~28%变动,但钙含量变化较小,其变化范围为20~31%;此类合金白口倾向小,但要求处理温度高,处理后渣量大。
镍镁合金在美洲、欧洲均有应用,美国国际镍公司生产的镍镁合金最高达82~85%,其中Mg、Ca分别为13~16,及20,镍最低的57~61%(其中Mg4.0~4.5%,Ca<2.5,Fe32~36)。
德国金属化学公司生产的镍镁合金中Ni47~51%,Mgl5~17%,C1.0%Si28~32%,RE1.0%余Fe。
这些合金的优点是比重大,反映平稳,镍可起合金化作用,其特点是价格贵,这种合金在中国基本没有应用。
镍硅系合金目前在中国基本上已不用。
纯镁合金处理时要用专用的压力加镁包,镁的吸收率高,但处理安全措施要极为严格,生产中应用比例较小。
稀土是发明球铁时使用的球化剂,它的发现推进了球铁工业应用的进程。
但价格高,白口倾向大,过量会使石墨变态,现在己不作为球化剂单独使用,仅作为辅助球化元素。
(2)压块状球化剂用镁粉和铁粉及所设计的硅含量直接加压成型,这种球化剂中含硅很低,通常称为低硅压块状球化剂,因而为后续的孕育提供了大的余地,有利于生产铸态球铁,但这种合金易漂浮,处理效果波动大,处理时最好跟块状球化剂混合使用。
(3)包芯线型球化剂将镁粉、铁粉包覆在薄钢板或钢板中,将其快速送入铁水中达到球化目的,这种球化剂较贵,且设备投资大,但处理时合金吸收率高,因此处理球铁的总成本几乎没有提高。
(4)粉状球化剂这种球化剂是俄罗斯的一个专利,使用时将镁粉与抑制剂混合放入包内,并使铁水从合金表面上流过,逐层与合金反映达到球化效果,这种专门工艺称之为MC。
2.2球化剂的应用目前国内外在球铁生产中主要应用火法冶炼的合金,压块球化剂、包芯线球化剂、粉状球化剂应用的很少,火法冶炼的球化剂在生产中应用占90%以上,目前这类合金中增加Ba、Ca、Cu、Ni等以达到控制基体目的,对合金中的氧化镁含量已有限量指标。
现对中国33个典型工厂和美国77个工厂生产球铁工厂进行对比分析。
中国33个工厂的基本情况是:33个工厂总计有36个熔炉,其中电炉(中频、工频、电弧炉)9个占25%,冲天炉22个占61%,冲天炉一电炉双联熔炼厂4个占11%,高炉1个占3%,球铁处理温度大于1500℃,4个占11%,1450~1500℃,20个占56%,1350~1400℃,6个占16.7%,1300~1350℃,2个占5.6%;大于1270℃1个占2.7%;铁水含硫量小于等于0.03%占20%;处理方法中冲入法占94%,喷吹法占3%,压力加镁法3%,用量最大的6#合金Mg8RE8占46%,其次为Mg8RE5占37%,Mg9RE5占11%。
美国77个工厂的基本情况是:熔化设备冲天炉占30%,感应电炉占63%,球化处理温度1482~1538℃占75%;原铁水在球化处理前有50%工厂采用预脱硫工艺,有90%的工厂S小于0.025%,球化处理方法中在美国大工厂中冲入法占36%,而小厂(小于200吨/周)冲入法仅占22%,压入法、多孔塞法、型内处理法、Tundish盖包法、压力加镁法则占绝大部分比重,使用的球化剂中含镁大于%的占8.2%Mg4~6%占63.3,含镁小于4%占16.4%纯镁占5%,其它的镁合金占8.2%。
资料表明中国生产球铁方面还有不小的差距,美国生产的电炉可保证球化处理所需要的高温,一般经预脱硫,含硫量低,质量要优于我国处理球铁的质量,因此处理球铁可用低镁、低稀土球化剂,而且质量控制也严格,包括使用衰退时间控制器。
我国从90年到现在球化剂生产已有了很大变化,稀土镁合金国家标准经过修订,对合金中的RE作了重大调整,除保留Mg8RE18以外,其它合金中Mg/Re 均大于1,工厂使用的合金中稀土量有所下降,Mg8RE5—7的合金应用大量增加,电炉也增加了不少,但原铁水中的含硫量变化不大,预脱硫工艺未有效地推广,因此我国球化剂中Mg、BE仍处在较高的水平上,新的球化处理工艺在我国推广不多,如在美国占有很大比例的Tundish盖包法在我国几乎还未得到应用,这些都是我国球铁生产厂待解决的问题。