磷化钢丝的生产和质量控制
钢丝绳磷化涂层技术
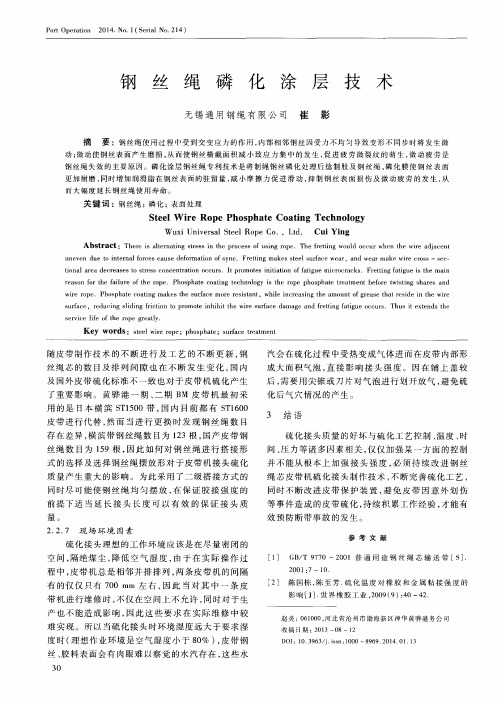
r e a s o n f o r t h e f a i l ur e o f t h e r o p e. Ph o s ph a t e c o a t i n g t e c h n o l o g y i s t h e r o pe p ho s p ha t e t r e a t me n t be f o r e t wi s t i n g s h a r e s a n d
s u r f a c e,r e d u c i n g s l i di ng f r i c t i o n t o p r o mo t e i n hi b i t t he wi r e s ur f a c e d a ma g e a n d re f t t i n g f a t i g u e O C C U R S . Th us i t e x t e n d s t h e
皮带 进行 代替 , 然 而 当进 行 更 换 时 发 现 钢丝 绳 数 目 存在 差异 , 横滨 带钢 丝绳 数 目为 1 2 3根 , 国产皮 带 钢 丝绳 数 目为 1 5 9根 , 因 此如 何 对钢 丝绳 进行 搭 接 形 式 的选择 及选 择钢 丝绳 摆放 形对 于皮 带机 接头 硫化 质量 产生 重 大 的影 响 。为此 采用 了二 级搭 接方 式 的 同时尽可 能使 钢 丝绳 均 匀 摆 放 , 在 保 证 胶接 强 度 的 前提 下适 当延 长 接 头 长 度 可 以有l a r e a d e c r e a s e s t o s t r e s s c o n c e n t r a t i o n o c c ur s .I t p r o mo t e s i ni t i a t i o n o f f a t i g u e mi c r o c r a e k s .F r e t t i ng f a t i g ue i s t he ma i n
常见磷化和喷塑质量问题及解决方法
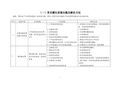
(一)常见磷化质量问题及解决方法摘要:磷化生产中经常会遇到一些质量问题,现将一些常见的问题和产生的原因及解决方法总结归纳。
序号质量外观外观现象产生原因解决方法1 无磷化膜或磷化膜不易形成工件整体或局部无磷化膜,有时发蓝或有空白片1.工件表面有硬化层2.总酸度不够3.处理温度低4.游离酸太低5.脱脂不净或磷化时间偏短6.工件表面聚齐氢气7.磷化槽液比例失调,如P2O5含量过低8.工件重叠或工件之间发生接触1.改进加工方法或用酸洗、喷砂去除硬化层,达到表面处理要求2.补加磷化剂3.升高磷化槽液温度。
4.补加磷化剂5.加强脱脂或延长磷化时间6.翻动工件或改变工件位置7.调整或更换磷化槽液8.注意增大工件间间隙,避免接触2 磷化膜过薄磷化膜太薄,结晶过细或无明显结晶,抗蚀性能差1.总酸度过高2.磷化时间不够3.处理温度过低4.促进剂浓度高5.工件表面有硬化层6.亚铁离子含量低7.表调效果差或表调失效1.加水稀释磷化槽液2.延长磷化时间3.升高处理温度4.停止添加促进剂5.用酸洗或喷砂清理,达到表面处理要求6.插入铁板,并检测总酸度或游离酸度变化情况7.更换或添加表调剂1序号质量外观外观现象产生原因解决方法3磷化膜结晶粗大磷化膜结晶粗大、疏松、多孔、表面有水锈1.工件未清洗干净2.工件在磷化前生锈3.亚铁离子含量偏低4.游离酸度偏低5.磷化温度低6.工件表面产生过腐蚀现象1.强磷化前工件的表面预处理2.除锈水洗后减少工件在空气中的暴露时间3.提高亚铁离子的含量,如补充磷酸二氢铁4.加入磷酸等,提高游离酸度5.提高槽液温度6.控制除锈时间或更换除锈剂4 磷化膜挂灰磷化膜干燥后表面有白色粉末1.槽液含渣量过大2.酸比太高3.处理温度过高4.槽液沉渣浮起,黏附在工件上5.工件表面氧化物未除净6.溶液氧化剂含量过高,总酸度过高1.清除槽底残渣,并定期过滤2.补加磷化剂3.降低磷化处理温度4.静置磷化槽液,并翻槽5.加强酸洗并充分水洗6.停加氧化剂,调整酸的比值5磷化膜发花磷化膜不均匀,有明显流挂痕迹1.除油不干净2.表调剂效果不佳或已失效3.磷化槽液喷淋不均匀4.工件表面钝化5.磷化温度低1.强脱脂或更换脱脂剂2.更换或补充表调剂3.检查并调整喷嘴4.加强酸洗或喷砂5.提高磷化温度2序号质量外观外观现象产生原因解决方法6 磷化膜发黑局部呈黑条状,膜黑且粗糙1.促进剂浓度太低2.酸洗过度1.加促进剂2.控制酸洗时间7磷化表面生锈磷化后工件表面产生黄色锈斑或锈点1.磷化膜晶粒过粗或过细,使耐蚀性降低2.游离酸含量过高3.工件表面过过腐蚀4.溶液中磷酸盐含量不足5.工件表面有残酸6.磷化槽沉淀多,已堵塞喷嘴7.处理温度低8.设备原因,如喷淋的压力过大、喷嘴方向等1.调整游离酸度与总酸度的比例2.降低游离酸含量,可加氧化锌或氢氧化锌3.控制酸洗过程4.补充磷酸二氢盐5.加强中和水洗6.检查喷嘴并进行清理,检查磷化槽沉淀量7.提高处理温度8.逐一检查设备是否运行正常8 磷化膜发红磷化膜红但不是锈1.铜离子渗入磷化液2.酸洗液中的铁渣附着1.注意不用铜挂具,用铁屑置换除去或用硫化处理,调整酸度2.加强酸洗过程的质量控制9 膜呈彩虹花斑用指甲划过无划痕,对光观察呈彩虹色1.促进剂浓度过高2.促进剂分布不均匀3.除油不彻底1.停加促进剂2.充分搅拌,使之均匀3.补加脱脂剂3序号质量外观外观现象产生原因解决方法10 磷化槽液变黑磷化槽液变黑浑浊1.槽液温度低于规定温度2.溶液中亚铁离子过量3.总酸度过低1.停止磷化,升高槽液温度至沸点,保持1-2h,并用空气搅拌,直至灰色原色2.氧化剂,如高锰酸钾等3.补充硝酸锌,提高总酸度11 磷化膜发蓝磷化膜部分表面产生紫蓝色彩表调剂的PH值不在工艺范围2.表调与磷化间隔区的水务喷嘴堵塞3.磷化槽液的锌离子含量不足4.磷化槽液的促进剂含量不够1.补加表调剂或补加Na2CO3,以提高PH值2.检查、清扫水务喷嘴3.补加磷化液或硝酸锌4.补加促进剂12 涂膜气泡涂装后,涂膜发生起泡现象1.磷化后水洗不充分2.清洗水被污染3.纯水的水质不好4.吊架或传送带上滴落水1.检查喷嘴或水洗方法2.增加供水量,控制清洗水的电导率在150μS/cm以下3.控制纯水的电导率在5μS/cm以下4.消除这类滴水4(二)喷塑常见问题一览表问题点主要原因解决措施1)针孔①板面锈蚀;②镀锌底材含氢离子;③磷化前处理后发黄;④工件磷化后,水洗不干净,尤其在工件四周表现为圈状针孔;⑤阴阳离子交换树脂脱盐水呈酸性;⑥粉末质量。
磷化质量控制及检测方法 磷化后的工件
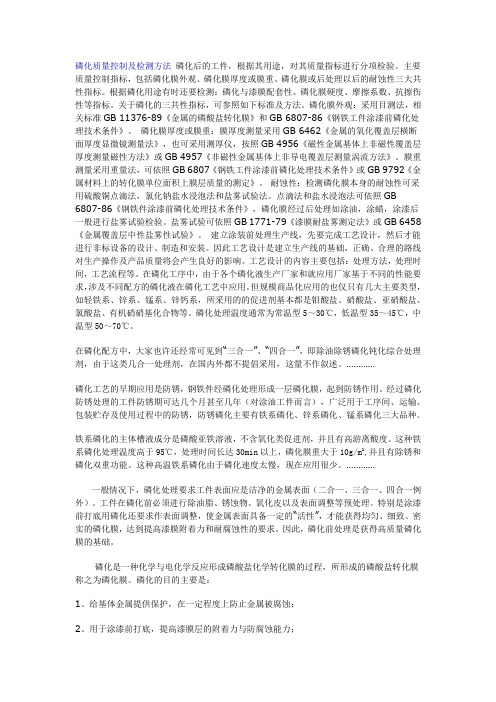
磷化质量控制及检测方法磷化后的工件,根据其用途,对其质量指标进行分项检验。
主要质量控制指标,包括磷化膜外观、磷化膜厚度或膜重、磷化膜或后处理以后的耐蚀性三大共性指标。
根据磷化用途有时还要检测:磷化与漆膜配套性、磷化膜硬度、摩擦系数、抗擦伤性等指标。
关于磷化的三共性指标,可参照如下标准及方法。
磷化膜外观:采用目测法,相关标准GB 11376-89《金属的磷酸盐转化膜》和GB 6807-86《钢铁工件涂漆前磷化处理技术条件》。
磷化膜厚度或膜重:膜厚度测量采用GB 6462《金属的氧化覆盖层横断面厚度显微镜测量法》,也可采用测厚仪,按照GB 4956《磁性金属基体上非磁性覆盖层厚度测量磁性方法》或GB 4957《非磁性金属基体上非导电覆盖层测量涡流方法》。
膜重测量采用重量法,可依照GB 6807《钢铁工件涂漆前磷化处理技术条件》或GB 9792《金属材料上的转化膜单位面积上膜层质量的测定》。
耐蚀性:检测磷化膜本身的耐蚀性可采用硫酸铜点滴法,氯化钠盐水浸泡法和盐雾试验法。
点滴法和盐水浸泡法可依照GB 6807-86《钢铁件涂漆前磷化处理技术条件》,磷化膜经过后处理如涂油,涂蜡,涂漆后一般进行盐雾试验检验。
盐雾试验可依照GB 1771-79《漆膜耐盐雾测定法》或GB 6458《金属覆盖层中性盐雾性试验》。
建立涂装前处理生产线,先要完成工艺设计,然后才能进行非标设备的设计、制造和安装。
因此工艺设计是建立生产线的基础,正确、合理的路线对生产操作及产品质量将会产生良好的影响。
工艺设计的内容主要包括:处理方法,处理时间,工艺流程等。
在磷化工序中,由于各个磷化液生产厂家和就应用厂家基于不同的性能要求,涉及不同配方的磷化液在磷化工艺中应用。
但规模商品化应用的也仅只有几大主要类型,如轻铁系、锌系、锰系、锌钙系,所采用的的促进剂基本都是钼酸盐、硝酸盐、亚硝酸盐、氯酸盐、有机硝硝基化合物等。
磷化处理温度通常为常温型5~30℃,低温型35~45℃,中温型50~70℃。
磷化钢丝工艺技术

磷化钢丝工艺技术磷化钢丝工艺技术是一种将钢丝表面进行磷化处理的工艺技术。
磷化是指将金属表面与磷酸盐接触,在一定的温度和时间下,形成一层磷酸盐溶液相互作用形成的稳定、致密、均匀的磷化膜。
磷化钢丝工艺技术主要应用于防腐蚀和改善钢丝表面性能的领域。
磷化膜具有良好的耐磨、耐蚀以及润滑性能,可以提高钢丝的使用寿命和磨损性能。
同时,磷化膜还能增加钢丝表面的摩擦系数,提高抗剪切性能。
磷化钢丝工艺技术包含以下几个步骤:1. 清洗:将钢丝表面的油污、锈蚀物等杂质进行清除。
清洗可以采用物理方法如水冲洗、超声波清洗等,也可以采用化学方法如酸洗、碱洗等。
2. 酸洗:将钢丝浸泡于稀酸溶液中进行酸洗。
酸洗有助于去除钢丝表面的氧化皮、锈蚀物等有害物质,并为后续的磷化处理做好准备。
3. 磷化:将酸洗后的钢丝浸泡于磷酸盐溶液中进行磷化处理。
磷化处理的温度、酸性度以及时间等参数需要根据钢丝材料的不同进行调控,以获得最佳的磷化效果。
4. 中和:将磷化完成后的钢丝浸泡于碱性中和溶液中进行中和处理。
中和可以中和磷酸盐和酸洗液残留在钢丝表面的残余酸性物质,防止对钢丝表面产生侵蚀。
5. 比重检查:使用比重计测定中和液的比重,以确保中和液的酸碱度达到要求,从而保证钢丝表面的磷化膜质量。
磷化钢丝工艺技术的优点是成本低、工艺简单、环境友好。
相比于其他表面处理工艺如镀锌、热处理等,磷化工艺不需要高温、高压条件,能够在常温常压下进行。
同时,磷化膜均匀致密,不易掉落,具有很好的抗腐蚀性能。
然而,磷化钢丝工艺技术也存在一些问题和挑战。
首先,磷化膜的成膜速度较慢,需要较长的处理时间。
其次,磷化膜对于一些强酸、强碱等腐蚀性物质的抵抗能力相对较低,容易受到腐蚀破坏。
此外,磷化膜的硬度较低,不能满足一些特殊领域对于硬度要求较高的应用。
总的来说,磷化钢丝工艺技术是一种有效的表面处理方法,在钢丝的防腐蚀、摩擦性能提升等方面具有广泛应用前景。
随着科技的发展和工艺技术的创新,磷化钢丝工艺技术有望进一步改进和完善,以满足不同行业对于钢丝产品质量的需求。
关于磷化工序的浅解
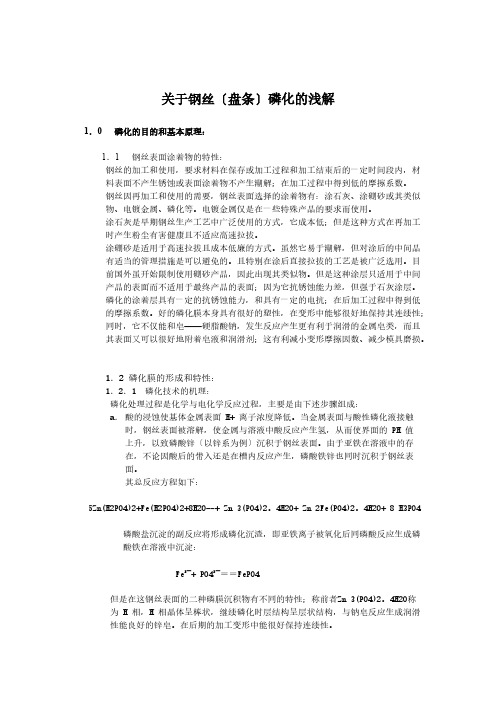
关于钢丝〔盘条〕磷化的浅解1.0磷化的目的和基本原理:1.1钢丝表面涂着物的特性:钢丝的加工和使用,要求材料在保存或加工过程和加工结束后的一定时间段内,材料表面不产生锈蚀或表面涂着物不产生潮解;在加工过程中得到低的摩擦系数。
钢丝因再加工和使用的需要,钢丝表面选择的涂着物有:涂石灰、涂硼砂或其类似物、电镀金属、磷化等。
电镀金属仅是在一些特殊产品的要求而使用。
涂石灰是早期钢丝生产工艺中广泛使用的方式,它成本低;但是这种方式在再加工时产生粉尘有害健康且不适应高速拉拔。
涂硼砂是适用于高速拉拔且成本低廉的方式。
虽然它易于潮解,但对涂后的中间品有适当的管理措施是可以避免的。
且特别在涂后直接拉拔的工艺是被广泛选用。
目前国外虽开始限制使用硼砂产品,因此出现其类似物。
但是这种涂层只适用于中间产品的表面而不适用于最终产品的表面;因为它抗锈蚀能力差,但强于石灰涂层。
磷化的涂着层具有一定的抗锈蚀能力,和具有一定的电抗;在后加工过程中得到低的摩擦系数。
好的磷化膜本身具有很好的塑性,在变形中能够很好地保持其连续性;同时,它不仅能和皂——硬脂酸钠,发生反应产生更有利于润滑的金属皂类,而且其表面又可以很好地附着皂液和润滑剂;这有利减小变形摩擦因数、减少模具磨损。
1.2 磷化膜的形成和特性:1.2.1 磷化技术的机理:磷化处理过程是化学与电化学反应过程,主要是由下述步骤组成:a.酸的浸蚀使基体金属表面 H+ 离子浓度降低。
当金属表面与酸性磷化液接触时,钢丝表面被溶解,使金属与溶液中酸反应产生氢,从而使界面的 PH 值上升,以致磷酸锌〔以锌系为例〕沉积于钢丝表面。
由于亚铁在溶液中的存在,不论因酸后的带入还是在槽内反应产生,磷酸铁锌也同时沉积于钢丝表面。
其总反应方程如下:5Zn(H2P04)2+Fe(H2P04)2+8H20--+ Zn 3(P04)2。
4H20+ Zn 2Fe(P04)2。
4H20+ 8 H3P04磷酸盐沉淀的副反应将形成磷化沉渣,即亚铁离子被氧化后同磷酸反应生成磷酸铁在溶液中沉淀:Fe³¯+ P04³¯==FeP04但是在这钢丝表面的二种磷膜沉积物有不同的特性;称前者Zn 3(P04)2。
钢丝拉拔磷化技术研究
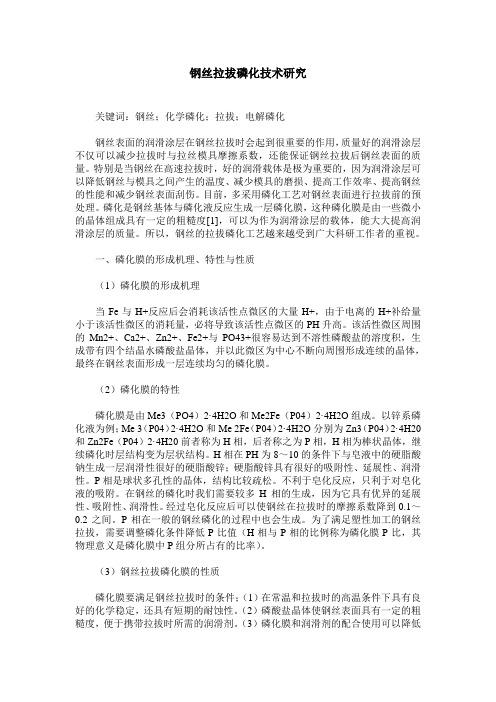
钢丝拉拔磷化技术研究关键词:钢丝;化学磷化;拉拔;电解磷化钢丝表面的润滑涂层在钢丝拉拔时会起到很重要的作用,质量好的润滑涂层不仅可以减少拉拔时与拉丝模具摩擦系数,还能保证钢丝拉拔后钢丝表面的质量。
特别是当钢丝在高速拉拔时,好的润滑载体是极为重要的,因为润滑涂层可以降低钢丝与模具之间产生的温度、减少模具的磨损、提高工作效率、提高钢丝的性能和减少钢丝表面刮伤。
目前,多采用磷化工艺对钢丝表面进行拉拔前的预处理。
磷化是钢丝基体与磷化液反应生成一层磷化膜,这种磷化膜是由一些微小的晶体组成具有一定的粗糙度[1],可以为作为润滑涂层的载体,能大大提高润滑涂层的质量。
所以,钢丝的拉拔磷化工艺越来越受到广大科研工作者的重视。
一、磷化膜的形成机理、特性与性质(1)磷化膜的形成机理当Fe与H+反应后会消耗该活性点微区的大量H+,由于电离的H+补给量小于该活性微区的消耗量,必将导致该活性点微区的PH升高。
该活性微区周围的Mn2+、Ca2+、Zn2+、Fe2+与PO43+很容易达到不溶性磷酸盐的溶度积,生成带有四个结晶水磷酸盐晶体,并以此微区为中心不断向周围形成连续的晶体,最终在钢丝表面形成一层连续均匀的磷化膜。
(2)磷化膜的特性磷化膜是由Me3(PO4)2·4H2O和Me2Fe(P04)2·4H2O组成。
以锌系磷化液为例;Me 3(P04)2·4H2O和Me 2Fe(P04)2·4H2O分别为Zn3(P04)2·4H20和Zn2Fe(P04)2·4H20前者称为H相,后者称之为P相,H相为棒状晶体,继续磷化时层结构变为层状结构。
H相在PH为8~10的条件下与皂液中的硬脂酸钠生成一层润滑性很好的硬脂酸锌;硬脂酸锌具有很好的吸附性、延展性、润滑性。
P相是球状多孔性的晶体,结构比较疏松。
不利于皂化反应,只利于对皂化液的吸附。
在钢丝的磷化时我们需要较多H相的生成,因为它具有优异的延展性、吸附性、润滑性。
关于磷化工序的浅解

关于钢丝〔盘条〕磷化的浅解1.0磷化的目的和基本原理:1.1钢丝表面涂着物的特性:钢丝的加工和使用,要求材料在保存或加工过程和加工结束后的一定时间段内,材料表面不产生锈蚀或表面涂着物不产生潮解;在加工过程中得到低的摩擦系数。
钢丝因再加工和使用的需要,钢丝表面选择的涂着物有:涂石灰、涂硼砂或其类似物、电镀金属、磷化等。
电镀金属仅是在一些特殊产品的要求而使用。
涂石灰是早期钢丝生产工艺中广泛使用的方式,它成本低;但是这种方式在再加工时产生粉尘有害健康且不适应高速拉拔。
涂硼砂是适用于高速拉拔且成本低廉的方式。
虽然它易于潮解,但对涂后的中间品有适当的管理措施是可以避免的。
且特别在涂后直接拉拔的工艺是被广泛选用。
目前国外虽开始限制使用硼砂产品,因此出现其类似物。
但是这种涂层只适用于中间产品的表面而不适用于最终产品的表面;因为它抗锈蚀能力差,但强于石灰涂层。
磷化的涂着层具有一定的抗锈蚀能力,和具有一定的电抗;在后加工过程中得到低的摩擦系数。
好的磷化膜本身具有很好的塑性,在变形中能够很好地保持其连续性;同时,它不仅能和皂——硬脂酸钠,发生反应产生更有利于润滑的金属皂类,而且其表面又可以很好地附着皂液和润滑剂;这有利减小变形摩擦因数、减少模具磨损。
1.2 磷化膜的形成和特性:1.2.1 磷化技术的机理:磷化处理过程是化学与电化学反应过程,主要是由下述步骤组成:a.酸的浸蚀使基体金属表面 H+ 离子浓度降低。
当金属表面与酸性磷化液接触时,钢丝表面被溶解,使金属与溶液中酸反应产生氢,从而使界面的 PH 值上升,以致磷酸锌〔以锌系为例〕沉积于钢丝表面。
由于亚铁在溶液中的存在,不论因酸后的带入还是在槽内反应产生,磷酸铁锌也同时沉积于钢丝表面。
其总反应方程如下:5Zn(H2P04)2+Fe(H2P04)2+8H20--+ Zn 3(P04)2。
4H20+ Zn 2Fe(P04)2。
4H20+ 8 H3P04磷酸盐沉淀的副反应将形成磷化沉渣,即亚铁离子被氧化后同磷酸反应生成磷酸铁在溶液中沉淀:Fe³¯+ P04³¯==FeP04但是在这钢丝表面的二种磷膜沉积物有不同的特性;称前者Zn 3(P04)2。
磷化 质量控制及检测方法
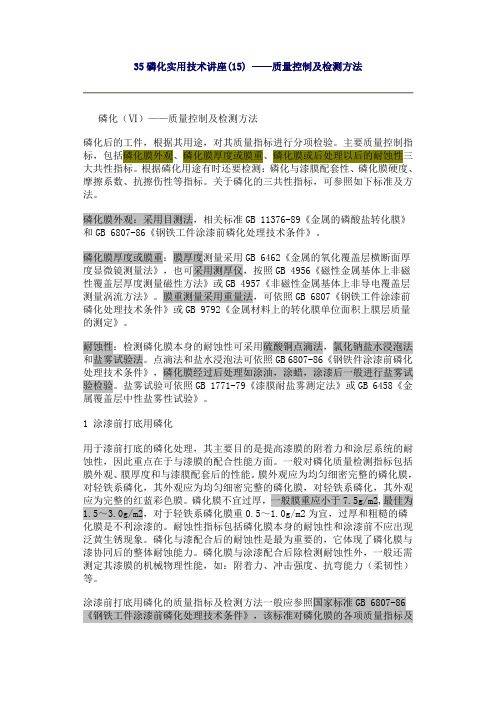
35磷化实用技术讲座(15) ——质量控制及检测方法磷化(Ⅵ)——质量控制及检测方法磷化后的工件,根据其用途,对其质量指标进行分项检验。
主要质量控制指标,包括磷化膜外观、磷化膜厚度或膜重、磷化膜或后处理以后的耐蚀性三大共性指标。
根据磷化用途有时还要检测:磷化与漆膜配套性、磷化膜硬度、摩擦系数、抗擦伤性等指标。
关于磷化的三共性指标,可参照如下标准及方法。
磷化膜外观:采用目测法,相关标准GB 11376-89《金属的磷酸盐转化膜》和GB 6807-86《钢铁工件涂漆前磷化处理技术条件》。
磷化膜厚度或膜重:膜厚度测量采用GB 6462《金属的氧化覆盖层横断面厚度显微镜测量法》,也可采用测厚仪,按照GB 4956《磁性金属基体上非磁性覆盖层厚度测量磁性方法》或GB 4957《非磁性金属基体上非导电覆盖层测量涡流方法》。
膜重测量采用重量法,可依照GB 6807《钢铁工件涂漆前磷化处理技术条件》或GB 9792《金属材料上的转化膜单位面积上膜层质量的测定》。
耐蚀性:检测磷化膜本身的耐蚀性可采用硫酸铜点滴法,氯化钠盐水浸泡法和盐雾试验法。
点滴法和盐水浸泡法可依照GB 6807-86《钢铁件涂漆前磷化处理技术条件》,磷化膜经过后处理如涂油,涂蜡,涂漆后一般进行盐雾试验检验。
盐雾试验可依照GB 1771-79《漆膜耐盐雾测定法》或GB 6458《金属覆盖层中性盐雾性试验》。
1 涂漆前打底用磷化用于漆前打底的磷化处理,其主要目的是提高漆膜的附着力和涂层系统的耐蚀性,因此重点在于与漆膜的配合性能方面。
一般对磷化质量检测指标包括膜外观、膜厚度和与漆膜配套后的性能。
膜外观应为均匀细密完整的磷化膜,对轻铁系磷化,其外观应为均匀细密完整的磷化膜,对轻铁系磷化,其外观应为完整的红蓝彩色膜。
磷化膜不宜过厚,一般膜重应小于7.5g/m2,最佳为1.5~3.0g/m2,对于轻铁系磷化膜重0.5~1.0g/m2为宜,过厚和粗糙的磷化膜是不利涂漆的。
磷化处理管理要点

磷化处理管理要点磷酸盐处理虽然稳定,但对于产品质量管理来说,却是药剂生产厂家与用户必须协调配合。
为了让用户能更深刻地理解皮膜生成的原理、工艺目的、母材、设备、处理液的管理,特作解释如下。
一、前言一般认为含电镀钢材在内的涂装前的磷化处理是比较稳定的。
可是工艺管理就未必那么简单。
尽管因磷化处理不当而引起涂装不良的现象较少,但认真做好磷化处理的管理工作是保证质量、降低成本的一个重要方面。
然而对于工程服务不可缺少的厂家来说,希望能有很好的管理工作。
在本文中,阐述了对采用使用较为广泛的碱性脱脂、胶钛的表面调整,以磷酸锌工艺为主的生产线的各个管理点和磷化不良时的对应措施。
二、磷化处理的原理一般磷化处理的作用被轻视的原因,是由于原理难以理解,加之生成的皮膜被涂膜遮盖,难以认识其真正作用。
在脱脂、表面调整后的磷化工艺、母材的界面与磷化液进行反应,具有1~10um 的厚度,并带灰白色~灰黑色的绝缘性,析出无机质的细微结晶性皮膜。
皮膜的耐蚀性并不是其单独显现出来的。
但涂装时,磷化膜表现出来的粘附性、耐蚀性的效果就非常大。
下面简单叙述各工艺的原理:1 碱性脱脂使用含界面活性剂的碱性脱脂剂,目的是去除附着在母材上、妨碍磷化的防锈油和污物,使其成为亲水性的表面。
2 表面调整胶态状的特殊Ti化合物一吸附在表面,即迅速生成微细的结晶皮膜。
3 皮膜磷化(1)皮膜生成的反应(以Fe原材料为例)在PH为3左右的磷酸二氢锌饱和溶液中,母材的表面被溶解[1式]。
在其界面的处理液因失去游离磷酸而成为磷酸二锌的过饱和溶液。
一旦过饱和溶液。
一旦过饱和,在水里的不溶性的结晶皮膜即析出在母材表面[2式]。
Fe+2H3PO4→Fe(H2PO4)2+2H+ ………………[1式]Zn(H2PO4)2+Fe(H2PO4)2→Zn2Fe(PO4)2•4H2O+Zn3(PO4)2•4H2O…… [2式](P hosphopillite皮膜)(H opeite皮膜)P比值=P/(P+H)(2)残渣产生磷化处理的最大缺点是出现残渣,其中有铁的化合物{FePO4•2H2O},皮膜的副生成物{Zn3(PO4)2•4H2O}产生,附着在物品上并引起配管堵塞。
磷化钢丝标准

磷化钢丝标准一、磷化钢丝简介磷化钢丝是一种经过特殊处理的高强度钢丝,具有优异的防腐蚀性能和机械性能。
它广泛应用于制造各种高强度、耐腐蚀的机械零件和构件,如弹簧、链条、齿轮等。
二、磷化钢丝标准概述磷化钢丝标准是对磷化钢丝的生产、检验、使用等方面的规定和指导性文件。
标准规定了磷化钢丝的分类、技术要求、试验方法、检验规则、包装、运输和贮存等方面的内容。
三、磷化钢丝分类根据使用要求和应用场景的不同,磷化钢丝可分为以下几类:1.按用途分类:可分为磷化弹簧钢丝、磷化链条钢丝、磷化齿轮钢丝等。
2.按表面状态分类:可分为磷化涂层钢丝和裸丝。
3.按磷化膜层厚度分类:可分为薄层磷化钢丝和厚层磷化钢丝。
4.按磷化液成分分类:可分为锌系磷化钢丝、锰系磷化钢丝、锌锰系磷化钢丝等。
四、磷化钢丝技术要求磷化钢丝的技术要求包括以下几个方面:1.化学成分:磷化钢丝应采用低碳钢作为原料,其化学成分应符合相关国家标准的规定。
2.外观质量:磷化钢丝的外观应光滑、无明显缺陷,如裂纹、折叠、结疤等。
3.尺寸及允许偏差:磷化钢丝的尺寸及允许偏差应符合相关国家标准的规定。
4.力学性能:磷化钢丝的抗拉强度、弹性模量、伸长率等力学性能应符合相关国家标准的规定。
5.耐腐蚀性能:磷化钢丝具有良好的耐腐蚀性能,可适应各种恶劣环境下的长期使用。
6.涂层质量:对于磷化涂层钢丝,其涂层应均匀、致密,与基体结合牢固,无起皮、脱落等现象。
7.包装、标志和标签:磷化钢丝的包装、标志和标签应符合相关国家标准的规定,确保产品信息的准确性和可追溯性。
8.其他要求:根据具体使用场景和特殊要求,可对磷化钢丝提出其他特定的技术要求,如高温性能、低温性能等。
五、磷化钢丝试验方法为了检验磷化钢丝是否符合标准要求,通常需要进行以下试验方法:1.化学成分分析:通过对磷化钢丝的化学成分进行分析,确定其成分是否符合标准要求。
2.外观检查:观察磷化钢丝的表面质量,检查是否存在裂纹、折叠、结疤等缺陷。
钢丝磷化的作用

钢丝磷化的作用钢丝磷化的作用什么是钢丝磷化钢丝磷化是一种用于改善钢丝表面性能的表面处理技术。
通过在钢丝表面形成一层磷化物膜,可以提高钢丝的耐磨性、耐蚀性和抗疲劳性,同时还能改善钢丝与其他材料之间的黏附性。
钢丝磷化的作用•提高耐磨性:钢丝磷化后表面形成的磷化物膜具有很高的硬度,可以有效提高钢丝的耐磨性,延长使用寿命。
•提高耐蚀性:钢丝磷化处理后,表面生成的磷化物膜可以阻隔外界氧气和水分的接触,从而起到抗氧化和防腐蚀的作用。
•改善抗疲劳性:钢丝经过磷化处理后,表面形成的磷化物膜能够增强钢丝的抗疲劳性能,降低因疲劳引起的断裂风险。
•提高黏附性:钢丝磷化处理后,磷化物膜能够提供更多的活性位点,增加涂层材料与钢丝的黏附强度,降低涂层脱落的可能性。
•降低摩擦系数:磷化后钢丝表面光滑度增加,可以有效降低钢丝与其他材料之间的摩擦系数,减少能量损耗和磨损。
•改善外观:钢丝磷化处理后,表面形成的磷化物膜可以改善钢丝的外观,提高产品的质量和美观度。
如何进行钢丝磷化处理1.表面清洁:首先要对钢丝表面进行彻底清洁,去除油脂、氧化物等杂质,可以采用溶剂清洗、机械打磨等方法。
2.酸洗处理:将清洁后的钢丝浸泡在酸性溶液中,如盐酸溶液,进行酸洗处理,可以去除钢丝表面的氧化物,提高磷化的效果。
3.磷化处理:将酸洗后的钢丝放入含有磷化剂的溶液中,经过一定的时间进行磷化处理。
常用的磷化剂有锌盐、铁盐和锰盐等。
4.中和处理:磷化后的钢丝需经过中和处理,可用碱性溶液中和残留的酸性物质,以避免对钢丝产生腐蚀。
5.保护处理:磷化后钢丝需进行保护处理,可以通过涂覆或浸泡等方式,形成一层保护性的膜,增加耐腐蚀能力和耐磨性。
小结钢丝磷化作为一种常用的表面处理技术,可以显著提升钢丝的性能并增加其使用寿命。
通过改善钢丝的耐磨性、耐蚀性、抗疲劳性和黏附性等方面,钢丝磷化在各个领域都有广泛的应用。
应用领域•汽车制造:钢丝磷化处理后的钢丝可以用于汽车轮胎钢丝、线材、弹簧等零部件的制造,提高汽车零部件的耐蚀性和耐磨性。
磷化工艺指导及质量检验标准
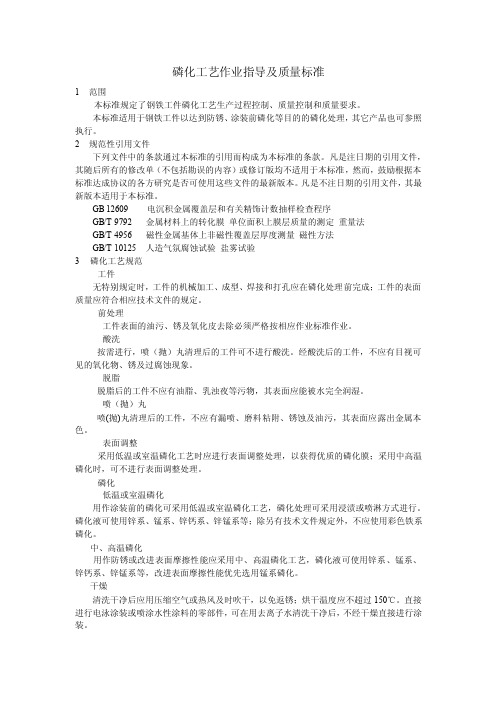
磷化工艺作业指导及质量标准1 范围本标准规定了钢铁工件磷化工艺生产过程控制、质量控制和质量要求。
本标准适用于钢铁工件以达到防锈、涂装前磷化等目的的磷化处理,其它产品也可参照执行。
2 规范性引用文件下列文件中的条款通过本标准的引用而构成为本标准的条款。
凡是注日期的引用文件,其随后所有的修改单(不包括勘误的内容)或修订版均不适用于本标准,然而,鼓励根据本标准达成协议的各方研究是否可使用这些文件的最新版本。
凡是不注日期的引用文件,其最新版本适用于本标准。
GB 12609 电沉积金属覆盖层和有关精饰计数抽样检查程序GB/T 9792 金属材料上的转化膜单位面积上膜层质量的测定重量法GB/T 4956 磁性金属基体上非磁性覆盖层厚度测量磁性方法GB/T 10125 人造气氛腐蚀试验盐雾试验3磷化工艺规范工件无特别规定时,工件的机械加工、成型、焊接和打孔应在磷化处理前完成;工件的表面质量应符合相应技术文件的规定。
前处理工件表面的油污、锈及氧化皮去除必须严格按相应作业标准作业。
酸洗按需进行,喷(抛)丸清理后的工件可不进行酸洗。
经酸洗后的工件,不应有目视可见的氧化物、锈及过腐蚀现象。
脱脂脱脂后的工件不应有油脂、乳浊夜等污物,其表面应能被水完全润湿。
喷(抛)丸喷(抛)丸清理后的工件,不应有漏喷、磨料粘附、锈蚀及油污,其表面应露出金属本色。
表面调整采用低温或室温磷化工艺时应进行表面调整处理,以获得优质的磷化膜;采用中高温磷化时,可不进行表面调整处理。
磷化低温或室温磷化用作涂装前的磷化可采用低温或室温磷化工艺,磷化处理可采用浸渍或喷淋方式进行。
磷化液可使用锌系、锰系、锌钙系、锌锰系等;除另有技术文件规定外,不应使用彩色铁系磷化。
中、高温磷化用作防锈或改进表面摩擦性能应采用中、高温磷化工艺,磷化液可使用锌系、锰系、锌钙系、锌锰系等,改进表面摩擦性能优先选用锰系磷化。
干燥清洗干净后应用压缩空气或热风及时吹干,以免返锈;烘干温度应不超过150℃。
磷化质量要求

磷化质量要求
Phosphating
范围:
本规范规定了基体材料为冷轧钢或镀锌钢板的工件喷涂前磷化处理的工艺要求及其质量要求。
本规范适用于工艺评审和批生产质量检验
简介:
磷化是钢铁零件喷涂有机涂层前的前处理工艺,其主要目的是加强有机涂层与金属基材之间的结合力。磷化膜本身对钢铁表面的防腐蚀作用很微弱,所以有必要控制磷化后至喷涂前的时间间隔。本文对磷化膜的质量作了规定,同时对工艺操作过程中的关键质量因素作了说明。
注示:
注1:试片可由华为技术有限公司完成并提供给被鉴定工厂。
注2:所有试片必须同时进行处理。
注3:试验报告的发出者必须是华为技术有限公司认可的试验室或机构
1.4.
1.4.1.
材料:冷轧钢板
尺寸:80×125×1~4 (mm)
表面粗糙度:Ra≤1 mm
表面处理:锌系磷化;
根据生产的产品要求选择后处理喷漆或喷粉(注意喷涂必须在磷化完成后24小时以内进行)
Table of Contents
List ofTables
磷化质量要求
Phosphating
Scope
This specification defines the process requirements and quality requirements of thephosphatingbefore coating on the part made with cold-rolled steel or galvanized steel.
2.2.2.
在工件上按GB4956测量磷化膜厚度,要求其平均膜厚为2~3μm。对预镀锌钢板不要求膜厚检测。
2.2.3.
耐蚀性检查按IEC 60068-2-11在试片上进行中性盐雾试验。
钢丝的磷化
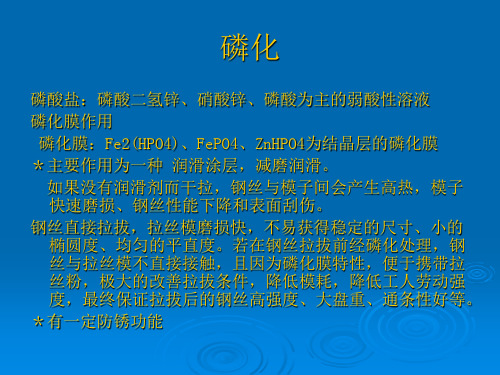
日常检查控制
槽液浓度: 温度: 液位:所有钢丝浸入溶液 钢丝位置:不交叉、不重叠 蒸汽:开启正常 添加水:正常、合适 磷化液自动添加:按设定(若存在自动添加) 擦液棒及分线梳:不大量结垢
磷化槽保养程序
穿戴好劳保用品, 穿戴好劳保用品,准备好使用工具 安全点:高温溶液,小心烫伤 安全点:高温溶液,小心烫伤 有一定的腐蚀性,注意保护 开启开关把槽内磷化液打入备用储液罐。 回液结束后,清理,疏通槽子所有管路, 回液结束后,清理,疏通槽子所有管路,清理废渣并 放入准备好的空筒内 清理槽内及场地周围垃圾, 清理槽内及场地周围垃圾,清理磷化槽内外表面 整理周围现场,废渣入库, 整理周围现场,废渣入库,工具清理后放回原位 待储液罐沉淀后,将磷化液放回磷化池中。
磷化质量控制
磷化质量与磷化液成分、温度、浸渍时间有关,需进行跟 踪监测,控制在合适范围。 磷化后需用纯水阶梯式冲洗,冲洗不好会生锈 因磷化是在酸性溶液中进行,因此后续有必要采用硼砂或 石灰来中和
工艺控制
磷化浴工艺参数
总酸度:SL: 总酸度:SL: TA,WL: TA 游离酸度:总酸度的1/5~ 游离酸度:总酸度的1/5~1/7.5 槽液量: 温度:℃ 温度:℃
磷化前酸洗作用
除锈、除污染 获得一定程度的表面粗糙度 活化钢丝表面
影响磷化质量因素
磷化液种类、质量 温度控制:温度升高加速磷化反应速度,提高磷化膜牢固 度,缩度慢。一般中温控制(70-85) 低则反应速度慢。一般中温控制(70-85) 浓度控制(总酸度TA和游离酸度FA) 浓度控制(总酸度TA和游离酸度FA):总酸度高则加速磷 TA FA 化反应速度,晶粒生成速度快,磷化层薄而致密,但过高 将使磷与铁的反应减弱,反而不易生成磷化膜。总酸度低 时,磷化速度慢,磷化膜结晶粗糙疏松。游离酸过高则结 晶困难,磷化膜结晶粗糙疏松,和钢丝表面结合力减弱并 引起溶液中沉淀增多。游离酸过低同样会使反应速度慢, 磷化膜薄而易破,生成量少,色泽不好且不好拉拔。 TA:120±40,FA:1/5TA:120±40,FA:1/5-1/7.5
钢丝磷化工艺技术研究
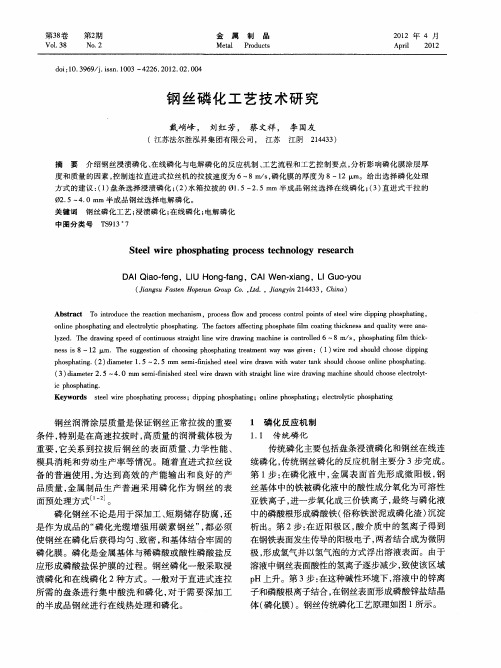
性能。
( ) 压 性 , 承 受 拉 拔 的压 力 , 被 挤 掉 或 1耐 可 不
破坏 。
1 2 电解磷 化 .
电解 磷 化 是 通过 给磷 化液 施 加 电流 , 钢 丝表 在 面沉 积形 成磷 化膜 的反 应过 程 。在 施加 电流 的 电解 磷 化槽 中 , 丝作 为 阴极 , 用一种 不参 与成 膜 的惰 钢 使 性 导体作 为 阳极 , 主要 反应 机制分 2步完 成 。首先 , 给 电解磷 酸槽 液通 电 , 钢丝 作为 阴极 , 性导 体作 为 惰 阳极 , 化液 自动 发生 水解 反应 , 阴极 表 面产 生氢 磷 在
所 需 的盘 条进 行 集 中 酸洗 和磷 化 , 于需 要 深 加 工 对
的半 成 品钢 丝进行 在 线热 处理 和磷 化 。
・
1 ・ 6
金
属
制
品
第3 8卷
利 于携带 润滑 剂 。 ( ) 拔 时 可 与 钢 丝 一起 延 伸 变 形 , 参 与 钢 3拉 还 丝 与拉 丝模模 壁 的辅助 分 离 。改 善 拉 拔 条件 , 高 提 拉拔 速度 。 ( ) 防锈 剂 有 很 强 的吸 收 性 , 防锈 油 配合 4对 与 可 极大 地增加 防锈 性能 。
(in s at oeu ru o ,t. J nyn2 43 , hn ) JaguF s nH psnGopC .Ld , i g i 14 3 C i e a a
Ab t a t T n rd c h e ci n me h n s ,p o e sf w n rc s o t l on so t e w r ip n h s h t g sr c o ito u e t e r a t c a i o m r c s o a d p o e sc n r it f e l i d p ig p o p ai , l op s e n o l e p o p ai ga d ee t lt h s h t g h c o safc ig p o p aef m o t gt ik e sa d q a i e e a a n i h s h t n l cr y i p o p ai .T e f tr f t h s h t l c ai hc n s n u l y w r n — n n o c n a e n i n t lzd y e .T e d a i g s e d o o t u u t i h i ewi rwi g ma h n s c n r l d6 —8 m ,p o p ai g f m hc — h r w n p e fc n i o s sr g t n r d a n c i e i o t l n a l e oe /s h s h t l t i k n i
磷化钢丝绳生产技术论证
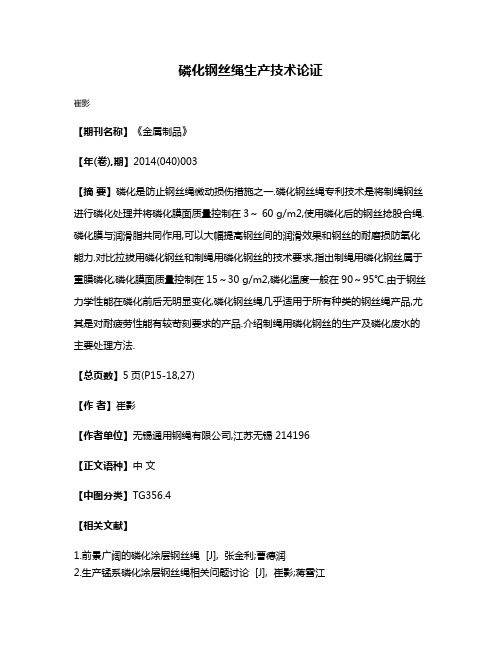
磷化钢丝绳生产技术论证
崔影
【期刊名称】《金属制品》
【年(卷),期】2014(040)003
【摘要】磷化是防止钢丝绳微动损伤措施之一.磷化钢丝绳专利技术是将制绳钢丝进行磷化处理并将磷化膜面质量控制在3~ 60 g/m2,使用磷化后的钢丝捻股合绳.磷化膜与润滑脂共同作用,可以大幅提高钢丝间的润滑效果和钢丝的耐磨损防氧化能力.对比拉拔用磷化钢丝和制绳用磷化钢丝的技术要求,指出制绳用磷化钢丝属于重膜磷化,磷化膜面质量控制在15~30 g/m2,磷化温度一般在90~95℃.由于钢丝力学性能在磷化前后无明显变化,磷化钢丝绳几乎适用于所有种类的钢丝绳产品,尤其是对耐疲劳性能有较苛刻要求的产品.介绍制绳用磷化钢丝的生产及磷化废水的主要处理方法.
【总页数】5页(P15-18,27)
【作者】崔影
【作者单位】无锡通用钢绳有限公司,江苏无锡214196
【正文语种】中文
【中图分类】TG356.4
【相关文献】
1.前景广阔的磷化涂层钢丝绳 [J], 张金利;曹德润
2.生产锰系磷化涂层钢丝绳相关问题讨论 [J], 崔影;蒋雪江
3.钢丝绳磷化涂层技术 [J], 崔影
4.磷化电梯钢丝绳的生产与使用 [J], 崔影
5.钢丝绳酸洗磷化废水处理工艺改进 [J], 黄海啸
因版权原因,仅展示原文概要,查看原文内容请购买。
钢丝磷化工艺研究
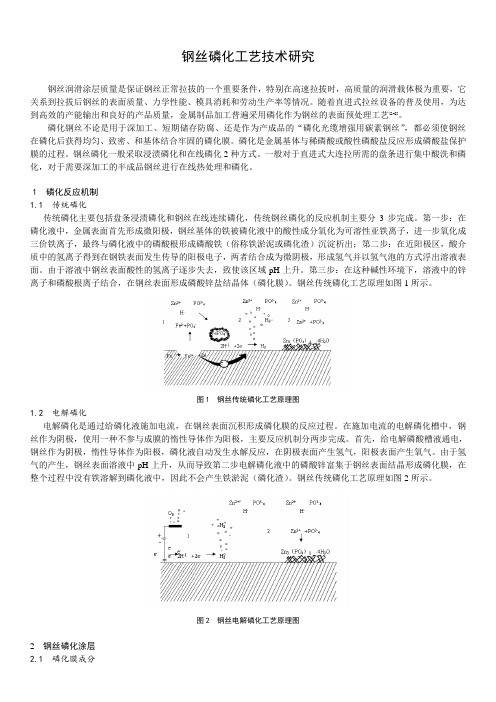
钢丝磷化工艺技术研究钢丝润滑涂层质量是保证钢丝正常拉拔的一个重要条件,特别在高速拉拔时,高质量的润滑载体极为重要,它关系到拉拔后钢丝的表面质量、力学性能、模具消耗和劳动生产率等情况。
随着直进式拉丝设备的普及使用,为达到高效的产能输出和良好的产品质量,金属制品加工普遍采用磷化作为钢丝的表面预处理工艺[1-2]。
磷化钢丝不论是用于深加工、短期储存防腐、还是作为产成品的“磷化光缆增强用碳素钢丝”,都必须使钢丝在磷化后获得均匀、致密、和基体结合牢固的磷化膜。
磷化是金属基体与稀磷酸或酸性磷酸盐反应形成磷酸盐保护膜的过程。
钢丝磷化一般采取浸渍磷化和在线磷化2种方式。
一般对于直进式大连拉所需的盘条进行集中酸洗和磷化,对于需要深加工的半成品钢丝进行在线热处理和磷化。
1 磷化反应机制1.1 传统磷化传统磷化主要包括盘条浸渍磷化和钢丝在线连续磷化,传统钢丝磷化的反应机制主要分3步完成。
第一步:在磷化液中,金属表面首先形成微阳极,钢丝基体的铁被磷化液中的酸性成分氧化为可溶性亚铁离子,进一步氧化成三价铁离子,最终与磷化液中的磷酸根形成磷酸铁(俗称铁淤泥或磷化渣)沉淀析出;第二步:在近阳极区,酸介质中的氢离子得到在钢铁表面发生传导的阳极电子,两者结合成为微阴极,形成氢气并以氢气泡的方式浮出溶液表面。
由于溶液中钢丝表面酸性的氢离子逐步失去,致使该区域pH上升。
第三步:在这种碱性环境下,溶液中的锌离子和磷酸根离子结合,在钢丝表面形成磷酸锌盐结晶体(磷化膜)。
钢丝传统磷化工艺原理如图1所示。
图1 钢丝传统磷化工艺原理图1.2 电解磷化电解磷化是通过给磷化液施加电流,在钢丝表面沉积形成磷化膜的反应过程。
在施加电流的电解磷化槽中,钢丝作为阴极,使用一种不参与成膜的惰性导体作为阳极,主要反应机制分两步完成。
首先,给电解磷酸槽液通电,钢丝作为阴极,惰性导体作为阳极,磷化液自动发生水解反应,在阴极表面产生氢气,阳极表面产生氧气。
由于氢气的产生,钢丝表面溶液中pH上升,从而导致第二步电解磷化液中的磷酸锌富集于钢丝表面结晶形成磷化膜,在整个过程中没有铁溶解到磷化液中,因此不会产生铁淤泥(磷化渣)。
一种钢丝磷化槽
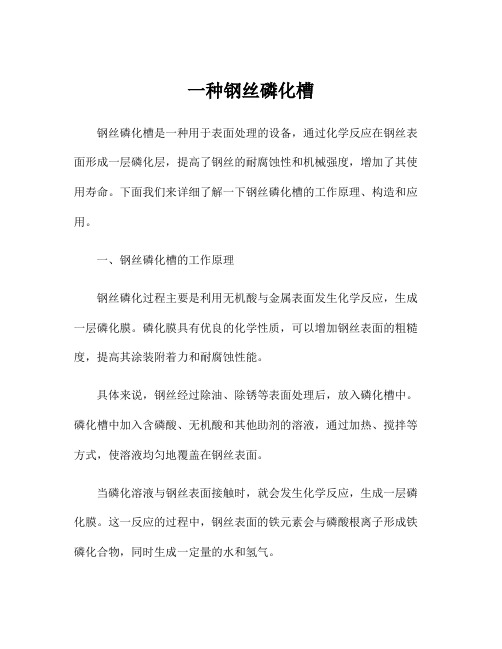
一种钢丝磷化槽钢丝磷化槽是一种用于表面处理的设备,通过化学反应在钢丝表面形成一层磷化层,提高了钢丝的耐腐蚀性和机械强度,增加了其使用寿命。
下面我们来详细了解一下钢丝磷化槽的工作原理、构造和应用。
一、钢丝磷化槽的工作原理钢丝磷化过程主要是利用无机酸与金属表面发生化学反应,生成一层磷化膜。
磷化膜具有优良的化学性质,可以增加钢丝表面的粗糙度,提高其涂装附着力和耐腐蚀性能。
具体来说,钢丝经过除油、除锈等表面处理后,放入磷化槽中。
磷化槽中加入含磷酸、无机酸和其他助剂的溶液,通过加热、搅拌等方式,使溶液均匀地覆盖在钢丝表面。
当磷化溶液与钢丝表面接触时,就会发生化学反应,生成一层磷化膜。
这一反应的过程中,钢丝表面的铁元素会与磷酸根离子形成铁磷化合物,同时生成一定量的水和氢气。
磷化膜的生成是一个自催化过程,即磷化膜生成后会加速磷化反应的继续进行。
磷化反应的时间和温度往往会影响磷化膜的厚度和质量,一般情况下需要进行实验确定最适宜的参数。
二、钢丝磷化槽的构造钢丝磷化槽一般由槽体、加热装置、搅拌装置、自动控制装置和其他辅助设备组成。
下面我们来一一介绍这些构造部分的作用和特点。
1.槽体槽体是钢丝磷化槽的主体部分,一般用不锈钢和耐酸碱材料制成。
槽体的大小和形状一般根据客户的需求进行设计,常见的大小有1m*1m*1m、1m*1.5m*1.5m等。
槽体需要具有较高的耐腐蚀性和加热效率,能够承受高温高压的环境,还需要具有较高的密封性能,防止半成品及制品溢出。
2.加热装置加热装置是将工艺液加热至适宜的温度,促进磷化反应的进行。
加热方式一般是采用电加热、蒸汽、燃气等方式,也可以根据客户要求进行设计。
加热装置需要具备平衡加热、节能、温度控制精度高等特点。
3.搅拌装置搅拌装置是将工艺液搅拌均匀,提高钢丝表面的反应均匀性。
搅拌方式主要有机械搅拌和气体搅拌两种,也可以结合采用。
搅拌装置需要具备搅拌效率高、噪音小、清洗方便等特点。
4.自动控制装置自动控制装置是为了提高设备的自动化程度和控制精度,使工艺过程更加平稳可靠。
- 1、下载文档前请自行甄别文档内容的完整性,平台不提供额外的编辑、内容补充、找答案等附加服务。
- 2、"仅部分预览"的文档,不可在线预览部分如存在完整性等问题,可反馈申请退款(可完整预览的文档不适用该条件!)。
- 3、如文档侵犯您的权益,请联系客服反馈,我们会尽快为您处理(人工客服工作时间:9:00-18:30)。
磷化钢丝的生产和质量控制
南通帅龙钢丝绳有限公司虞建宏、凌桂庭、明志光
目前光缆中使用的钢丝基本上已用磷化钢丝替代过去的镀锌钢丝。
本文介绍了磷化钢丝的基本要求,分析了连续式生产线和分段式生产线这二种生产工艺对磷化钢丝质量的影响。
磷化钢丝、生产、质量
加强件是光缆的基本构件之一,而钢丝加强件在我国的光缆中又估有极大的份额。
它的质量好坏直接影响到光缆的寿命。
随着光缆的技术进步,钢丝的材质和制造技术也在不断的更新和提高。
目前光缆中使用的钢丝基本上已用磷化钢丝替代过去的镀锌钢丝,本公司是国内主要的磷化钢丝生产厂家之一,现将我们对磷化钢丝生产中的一些看法叙述如后。
二、磷化钢丝的基本要求
磷化钢丝是光纤光缆增强用材料,表面要做到无水、污、油、锈蚀、毛刺、裂纹、折弯等缺陷,磷化膜连续、均匀、光亮、不脱落、磷化膜重量应大于等于2.5g/m。
,外径圆整、通条性好、无应力,剪6米长自然放地上应平直,不成“s”形,矢高不得大于5厘米,弹性模量≥190GPa,永久伸长率≤0.10,强度根据用户需要,有1370MPa、1470MPa、1570 MPa、1670MPa、1770 MPa、1870 MPa等。
三、生产T艺方面对磷化钢丝质量的影响
我们都知道,要生产出合格的磷化钢丝,关键在于选用好的母材,采取合理的开坯、热处理、酸洗磷化及拉拔工艺。
关于母材,选用国产宝钢72A或72B的材料,其各项指标完全能满足生产磷化钢丝的需要,无须从国外高价进口原材料。
因此磷化钢丝的质量主要还是取决于它的生产工艺。
目前,国内外生产磷化钢丝有二种工艺:
1、连续式生产线;
2、分段式生产线
下面我们就这两种生产工艺来具体谈一下它对磷化钢丝质量的影响。
1、连续式生产线
此为国内外大多光缆钢丝生产厂家采取的生产工艺,其较突出的优点为:生产速度快,产量高;其缺点如下:
(1)投资大,生产成本高;
连续式生产线大多是进口或仿进口的设备,故投资很大,造成了生产成本的增加,从而抬高了成品钢丝的价格。
(2)磷化层薄且易脱落;
首先,我想谈一下磷化层对磷化钢丝的作用。
大家都知道,钢丝在潮湿的空气或水中容易发生原电池反应,钢丝表面很快就会锈蚀,而磷化膜就起到了将钢丝与外界空气相隔绝即防锈的作用。
因此,磷化层的厚薄决定了钢丝受外界侵害的程度。
当然,磷化膜的防锈作用也不是万能的,因为磷化膜表面成鱼磷状,存在一定的空隙,要防止钢丝生锈,还取决于钢丝的贮存环境,钢丝不能暴露在潮湿的空气中,磷化层厚度受钢丝与磷化液反应条件限止,不可能达到过厚。
一般磷化层厚度大于等于2.5g /m2为最佳。
要想得到致密牢固的磷化膜,关键在于对钢丝表面的处理及合理的磷化时间。
连续式生产线因受拉丝速度的影响,酸洗、磷化的时间很短。
酸洗时间短,表面杂质去除不干净,势必造成磷化膜在钢丝表面吸附不牢,以至于在后面拉拔过程中脱落,再加上随着磷化液的消耗而磷化时间不能改变,势必造成磷化膜过薄,达不到磷化钢丝的要求。
(3)钢丝力学性能不稳定。
我们都知道,钢丝的力学性能取决于母材、热处理和拉拔工艺,由于连续式生产工艺受拉拔速度和热处理设备本身影响,热处理后钢丝坯料强度不可能达到一样,势必会造成钢丝强度高、韧性差或强度低、韧性好。
(4)做不到100%无焊接;
连续式生产线生产时一捆材料(2吨左右)用完后必定要将第二捆(2吨左右)材料用焊接的方法连接起来继续生产,焊接部位的强度肯定达不到材料的原始强度,因此成品钢丝就存在断裂的隐患。
2、分段式生产线
优点如下:
(1)投资少,生产成本低;
设备投资一般用国产的干式拉丝机,投入较低,故成本不会很高。
(2)磷化层厚且不易脱落;
分段式生产的酸洗、磷化、拉丝都是独立的,故它有足够的时间在酸洗时清除原料表面的杂质,磷化时能够与磷化液充分地结合,因此生产出来的钢丝表面磷化膜厚且不脱落。
(3)钢丝力学性能稳定
分段式生产工艺可以根据热处理后坯料强度分等级,根据不同等级的坯料来改变拉拔工艺,使钢丝的力学性能达到光缆钢丝的要求。
(4)能做到100%无焊接。
开坯根据成品的需要定坯料长度,这样就可以做到100%无焊接,剩余零头钢丝做其它产品,这样即不浪费又能杜绝钢丝断裂隐患。
缺点:生产速度慢,产量低。
当然,生产速度的快慢和产量的高低只是相对而言的。
如在一定的时间对磷化钢丝的需求量在较适中的范围内,分段式生产线就有了它明显的优势。
无论在质量上,还是在价格上,都有连续式生产线不可比拟的地方。
四、用“在线检测"提高磷化钢丝的质量控制水平
“在线检测’’是成品拉丝过程中加一个在线检测设备,如某一部位的钢丝不能达到预定的抗拉强度就会自行断裂,此设备确保了光缆生产厂家生产光缆时钢丝无断裂隐患。
据了解,目前只有我厂使用此设备。
另外,磷化钢丝的平直度、平整度也是关键,故生产磷化钢丝厂家的调直设备和操作工的技术水平是致关重要的。
上述的种种因素决定了磷化钢丝的质量水平。
当然,影响光缆钢丝的因素远不止这些,我们还在进行深入的探讨和研究,不断提高磷化钢丝的质量水平。
参考文献 (略)。