6SIGMA--DMAIC方法案例
质量管理学教学案例二:将6σ管理作为持续改进的突破性策略

质量管理学教学案例二:将6σ管理作为持续改进的突破性策略教学案例二:将6σ管理作为持续改进的突破性策略1. 引言一家成立仅五年,投资仅5000万美元的汽车零部件生产型企业,奇迹般地以每年平均50%的业务量增幅跨跃式发展,2002年销售额已高达22亿元,一跃而为国内最大汽车座椅总成的专业供应商。
国内市场拓展顺利,海外业务更是蒸蒸日上,2002年以出口超亿美金的佳绩,名列上海市出口百强第55位,并以其出色的供货表现,荣获美国江森自控(Johnson Controls)总部授与的全球质量奥林匹克金奖。
这就是上海延锋江森座椅有限公司—上海汽车工业(集团)总公司属下的延锋伟世通汽车饰件有限公司和美国江森自控国际有限公司共同投资的年轻的合资企业。
是什么使上海延锋江森座椅有限公司能诞生不久就蓬勃发展,取得如此辉煌的成功?天时、地利、人和?成功的成因也许是多方面的,但更与该公司管理层的一个英明决策和一个不懈追求有关,这就是走中西合璧的卓越之路:推行6σ管理,建设零缺陷文化。
6σ首先是由美国摩托罗拉公司于80年代中期提出的,主要用于生产制造过程的质量管理。
该公司在分析产品售后服务数据中发现,发生故障的产品大都是在生产制造过程中曾经返修或返工的产品,或采用曾经返工或返修过的零件的产品。
所以,该公司提出6σ理论,要求使每一操作过程都达到6σ的要求,力求在制造过程中做到不返修不返工,从根本上杜绝返工报废的浪费。
通过6σ管理理论的实施,摩托罗拉公司的质量缺陷减少了99.7%,节约了110亿美元的资金,并因此于1988年获得美国波多里奇国家质量奖。
美国江森自控于1999年引进了6σ这一理念和机制,并由最高领导层自上而下在全球范围内数百家江森的工厂中全面推行。
上海延锋江森座椅有限公司作为江森公司的合资公司,于1999年12月引入推行6σ。
2. 6σ质量战略σ是一个希腊字母,在统计学上用来表示任何程序或过程中变量偏离其均值的程度。
六西格玛流程DMAIC方法论

Step1 : 项目 选定
Big Y 导出
潜在 项目 发掘 潜在 项目 选定
Measure
Step4 : Y’s 确认
项目 CTQ 导出
Analyze
Step7 : Data 收集
必要 Data 掌握 收集计划树立
Improve
Step 10 : 改善 战略 建立
X 特性 掌握
Control
六西格玛方法论-10-
Analyze 阶段 X Data
单个X变数
X Data 计数型 计量型
多个X 变数
X Data 计数型 计量型
1个的 Y 变数
计数型
Chi-Square 卡方
对数回归 Y Data
计数型
多重回归
多重对数回归
Y Data
Y Data
计量型
计量型
One-way ANOVA 平均值/ 中值检验
S1A1T2. 课题选定 适合性 检讨
问题定义 S2A2T1. Y(缺陷)的 O.D
登录程序(Sigma Park)
推进方法论确认 S1A2T1. 方法论确认
DMAIC DMADOV
S2A2T2. Y的B/L、Goal
S2A2T3. 课题范围
课题输入/选定 S1A3T1.课题概要陈述
S2A2T4. 期待效果计算
“ቤተ መጻሕፍቲ ባይዱ”
具体性原则 要体现绩效目标之间的因 果关系,针对关键成功因 素具体阐述所衡量的关键 业绩指标
时效性原则
确保在需要的 时候能够得到 所需的数据
“T”
“M”
可衡量原则 可定期收集所需的准确、 完整的数据,定量指标可 以量化计算,定性指标可 以用双方都能理解的标准 (阶段目标、阶段效果、 时间节点等)衡量
六西格玛6sigma培训教材:DMAIC 案例培训教程

顾客满意 6σ 质量水准
改进 IMPROVE
分析 ANALYZE
定义(define)
识别客户要求:确定影响客户满意度的关键因素
主要工作任务:
预期财务成果与成本 商业案情 -解释为什么要实施这个项目 团队组织 -人员、期望、责任 项目问题描述 项目日程 项目范围 -实现目标的关键步骤和日期 -流程和产品牵涉到的方面、 可利用的资源 顾客及CTQ 最后形成“项目注册表” Y及缺陷定义 目的及目标阐述
•
1. 2. 3. • •
为成功地完成项目
明确项目领导和队员的职责,分清业务队员要熟悉相应工序的作业人员 必要时邀请团队以外的人给予协助,并得到倡导者承认和支持 沟通计划:总结过去,计划未来,交流沟通 六西格玛黑带考试48个复习要点(6sigma黑带) /thread-1-1-3.html
3.避免选择怎样的项目
• • • • • • 已经掌握解决对策的 因异常原因突发的 一次要解决很多 范围太广 起点太低 没有可测定的Y,好坏没有衡量指标
4.项目选择方向
• • • • • •
•
从VOC出发 聚焦品质 与企业战略相联系 团队之间有可能实施的项目 考虑项目的优先顺序(BB项目,GB项目,一般改进项目等) 确保项目具备S.M.A.R.T化
总结
从顾客观点上导出的 项目
CTQ
Critical to Quality
CCR
Critical Customer Requirement
VOC
Voice of Customer
VOB
Voice of Business
CBR
Critical Business Requirement
6sigma经典案例
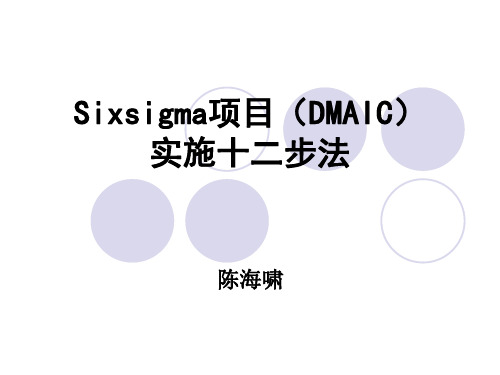
主要工具: 客户需求,查询设计文件及图纸
第2步 : 定义关键质量特性的绩效标准
开始前的提问:
1) 客户的需求是怎么来量化和衡量的? 2) 我是否需要对哪个特定变量进行测量?
结束时的提问:
1)是否可以连续测量? 是否可以观察到偏差的情况? 2)测量的变量是否反映了客户的需求? 3)这一测量的缺点在哪里? 它该如何操作?
要点:
1) 始终用Z值和DPMO来量化你的过程能力。 2) 在正态图上多花些时间---你过程中的所有信息可能都隐藏在其 中 3) 取样时要包含所有数据---而不是主观的挑选数据
第4步..…建立 Y (取药率) 的过程能力
如何实施? • 正常条件下取药情况 • 取药率
# 等级数
目标 = 90% 缺陷 <86%
结束时的提问:
1)你的客户是否同意你所列出的关键质量特性? 2)你是否最先解决客户最大的问题? 3)你所使用的数据和信息来自哪里? 4)你目前内部是如何测量和跟踪的?
要点:
1) 接受你目前的状态-- 投入你的精力和热情去做得更好! 2) 验证你的设想--不管它看上去多么显而易见。
A - 确定有待改进的产品或流程
• 疗效
Y = ? !!
第2步 : 定义关键质量特性的绩效标准
“如何衡量需要改进的产品性能?”
目标
定义能反映客户需求的输出变量,同时,明确如何去衡量它? 客户要我达到什么标准?
•在真实的世界里, 所有影响输出变量的x必须是可记录、可衡量的。
•为了理解这些x并提高它,你的输出变量也必须通过测量来记录和衡量。
要点:
1)测量客户所能“看到”和所期望的每一个行动。 2)不要仅限于现有的测量和数据。 3)在这一步化一些时间 -- 你将会知道你要测量什么。
六西格玛之DMAIC工具改善质量成本管理的案例分析
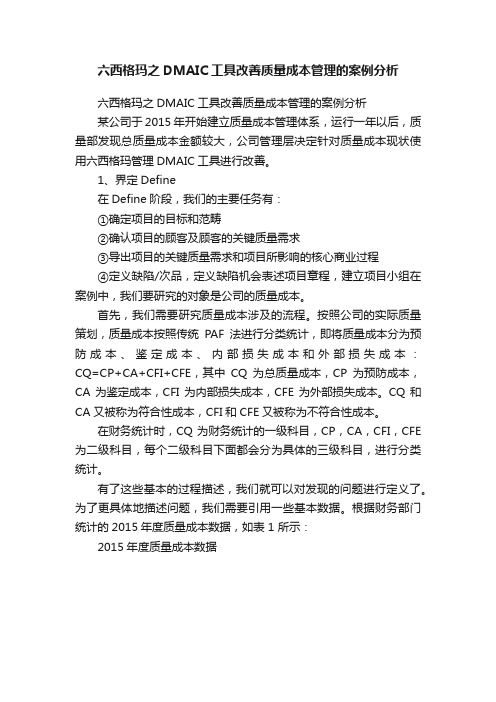
六西格玛之DMAIC工具改善质量成本管理的案例分析六西格玛之DMAIC工具改善质量成本管理的案例分析某公司于2015年开始建立质量成本管理体系,运行一年以后,质量部发现总质量成本金额较大,公司管理层决定针对质量成本现状使用六西格玛管理DMAIC工具进行改善。
1、界定Define在Define阶段,我们的主要任务有:①确定项目的目标和范畴②确认项目的顾客及顾客的关键质量需求③导出项目的关键质量需求和项目所影响的核心商业过程④定义缺陷/次品,定义缺陷机会表述项目章程,建立项目小组在案例中,我们要研究的对象是公司的质量成本。
首先,我们需要研究质量成本涉及的流程。
按照公司的实际质量策划,质量成本按照传统PAF法进行分类统计,即将质量成本分为预防成本、鉴定成本、内部损失成本和外部损失成本:CQ=CP+CA+CFI+CFE,其中CQ为总质量成本,CP为预防成本,CA为鉴定成本,CFI为内部损失成本,CFE为外部损失成本。
CQ和CA又被称为符合性成本,CFI和CFE又被称为不符合性成本。
在财务统计时,CQ为财务统计的一级科目,CP,CA,CFI,CFE 为二级科目,每个二级科目下面都会分为具体的三级科目,进行分类统计。
有了这些基本的过程描述,我们就可以对发现的问题进行定义了。
为了更具体地描述问题,我们需要引用一些基本数据。
根据财务部门统计的2015年度质量成本数据,如表 1 所示:2015年度质量成本数据从这些数据本身,我们不能发现哪里有问题,因为好与坏的标准并不能从这些数据中直接看出来。
这里,我们选取行业平均质量水平作为参照。
据了解,某公司所在行业总质量成本占销售额(S)的比例平均水平为3%。
在综合了各位专家的意见及行业情况,我们初步将质量成本构成比例基准设定为CP∶CA∶CFI∶CFE=1∶4∶3∶2。
对比这些目标数据,我们发现某公司的CQ占销售额比例5.8%,远远超过行业平均3%的水平,质量成本构成比例大约为CP∶CA∶CFI∶CFE=1.5:2.5:1:5,与基准之间也有不小的差距。
(六西格玛管理)案例编写济钢测量设备的六西格玛管理
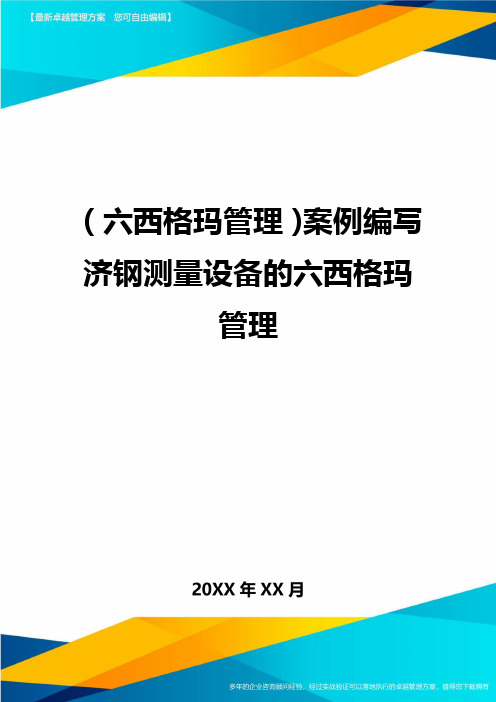
(六西格玛管理)案例编写济钢测量设备的六西格玛管理济钢六西格玛测量设备管理项目壹、济南钢铁集团(股份)公司的发展简介济南钢铁集团(股份)公司(以下简称:济钢)始建于1958年,现有职工42032人,占地面积21214亩,各类测量设备37424台(套),资产总额350亿元,已形成年产1000万吨钢的生产能力的特大型钢铁联合企业,规模位居全国6位,销售收入400多亿,2005年获得全国质量大奖,设有专门的组织机构对于公司内测量设备进行管理,对于公司壹、二级结算和生产重要质量控制点的测量设备实行职能、专业化管理,主要生产工艺有焦化、烧结、球团、炼铁、炼钢、轧钢等。
主要产品有中厚板、圆钢、螺纹钢、角钢、槽钢、球墨铸管、化产品等,现有产品品种187个,产品规格3800个。
2005年全公司生产钢1015万吨、实现销售收入360亿元、利税30亿元、利润18亿元。
长期以来,特别是改革开放以来,济钢坚持以市场为导向,和时俱进,创新发展,制定实施了低成本战略、可持续发展战略、精品战略、出口带动战略、人才战略、信息化推进战略六大战略,加强物质文明建设和精神文明建设,提高核心竞争力,使济钢走上了壹条持续、快速、健康发展的道路。
于企业提高管理水平、确保产品质量、降低能源消耗、做好安全防护及运营管理等工作中,测量设备发挥了重要作用。
二、济钢六西格玛测量设备管理项目的提出1、济钢测量设备管理现状分析济钢现有测量设备五万多台件,设有计量管理处对全厂的测量设备行使管理职能,且负责全公司壹二级测量设备的管理,总公司各二级单位由设备管理部门对所属的三级测量设备进行管理。
于完备的组织体系之下,建立完善了文件化管理体系,形成了大量的三级作业文件和作业指导书,如测量设备点检作业指导书、测量设备确认作业指导书、测量设备维修作业指导书等,明确点检、抢修和日常维修的管理流程,细化了每壹项作业内容和标准。
为确保文件的执行,建立了测量设备运行考核机制,对测量设备按照重要程度不同,规定了具体量化的考核指标,从设备的配备率、运行完好率、故障率和故障时间等进行多维度监督控制。
6SIGMA__DMAIC方法案例
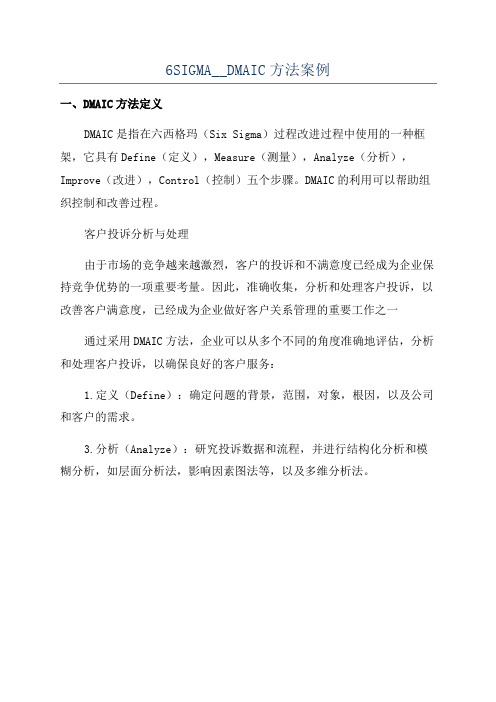
6SIGMA__DMAIC方法案例
一、DMAIC方法定义
DMAIC是指在六西格玛(Six Sigma)过程改进过程中使用的一种框架,它具有Define(定义),Measure(测量),Analyze(分析),Improve(改进),Control(控制)五个步骤。
DMAIC的利用可以帮助组织控制和改善过程。
客户投诉分析与处理
由于市场的竞争越来越激烈,客户的投诉和不满意度已经成为企业保持竞争优势的一项重要考量。
因此,准确收集,分析和处理客户投诉,以改善客户满意度,已经成为企业做好客户关系管理的重要工作之一通过采用DMAIC方法,企业可以从多个不同的角度准确地评估,分析和处理客户投诉,以确保良好的客户服务:
1.定义(Define):确定问题的背景,范围,对象,根因,以及公司和客户的需求。
3.分析(Analyze):研究投诉数据和流程,并进行结构化分析和模糊分析,如层面分析法,影响因素图法等,以及多维分析法。
六西格玛DMAIC案例

D-4: 项目范围
DMAI C
宏观流程图
原砂 树脂
制芯
浸涂 烘干
造型
浇注
水套芯
与项目密切相关的流程
钻孔
整芯
浸涂
铲车 转运
烘房
流程均在项目组可控范围内
铲车 转运
造型
D-5: Y及缺陷定义
Y 定义
小Y 定义
缺陷 定义
DMAI C
D-6: 基线及目标陈述
Baseline
<30%
0.0008640 0.005184 2.91 0.67
测量者 0.0008640 0.005184 2.91
部件结间 论0:.本028测840量6 0.173043 97.08 合计变系异统可0.0信297赖085 0.178251 100.00
M-1: Y的测量系统分析(连续型) D M A I C
测量内容:气缸体水套芯紧实率测试(连续数据) ★[样本数量]:共8个 ★[测量机器]:台秤 ★[测 量 者]:王慧勇、江晓明、彭国江 ★[记 录 者]:何帅伟 ★[测量方法]:用台秤分别对8个样品测试两次并记录结果。 ★[判定基准]: %P/TV≤30%、%P/T ≤30% 、明显分类数≥5
可区分的类别数 = 12
≥5
M-1: Y的测量系统分析(连续型) D M A I C
测量内容:气缸体冷芯盒水套芯常温强度测试(连续数据) ★[样本数量]:共10个
★[测量机器]:液压式万能强度试验仪
★[测 量 者]:沈林粉、陈红铭、白丽娜
★[记 录 者]:江贤波
★[测量方法]:用液压式万能强度仪分别对10个样品测试两次并记录结果
缸体报废数为813个,平均每年有407个,气缸 体
6SIGMA--DMAIC方法案例
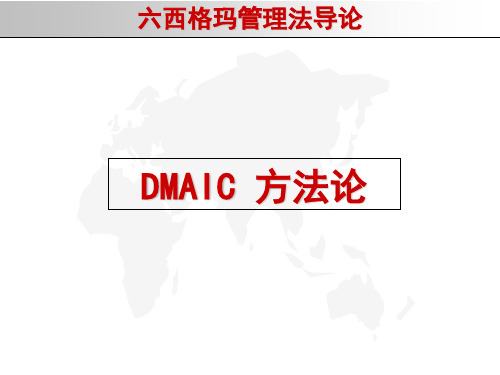
-40 -30 -20 -10 0 10 20 30 40 50 60
Actual (LT) Potential (ST)
Process Demographics
Date: Reported by: Pro j e ct: Department: Process: Ch a ra cte ri sti c: Un i ts: Upper Spec: 20 Lower Spec: -10 No m i n a l : Op p o rtu n i ty:
项目Y(5)的表现标准
Y 连续数据测量系统R&R,检 数据收集计划和MSA(6),项 验/再检验,属性数据的R&R 目数据Y(7)
Y 能力指标
项目Y(8)的流程能力
Y 团队、属性参照
项目Y(9)改善目标
X 流程分析、图像分析、 所有Xs的优先列表(10) 假设检验
六西格玛管理法导论
DMAIC 12步
与要求时间的差异 每个部件的运输费用
材料成本 平均首次故障时间
0
10
20
30
40
50
六西格玛管理法导论
导出项目的关键性质量要素,项目所影响的核心商 业过程
• 问题所关注的测量特征可转化为: • 实际到货时间与客户要求到货时间的差值 • 这就要求了解客户所认可的标准(客户所能容忍的最大限
度?)
• 定义缺陷/次品,定义缺陷机会 通过进一步了解与客户,可了解到客户所能容忍的最大限度是: 早到10天;晚到20天. (即在要求时间10天前到,和要求时间20天后到都为缺陷.)
17
18
19
95% Confidence Interval for Median
6西格玛改善案例解析
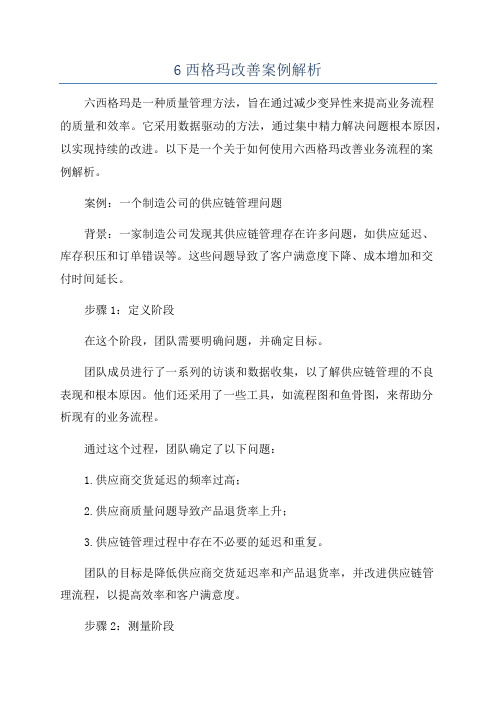
6西格玛改善案例解析六西格玛是一种质量管理方法,旨在通过减少变异性来提高业务流程的质量和效率。
它采用数据驱动的方法,通过集中精力解决问题根本原因,以实现持续的改进。
以下是一个关于如何使用六西格玛改善业务流程的案例解析。
案例:一个制造公司的供应链管理问题背景:一家制造公司发现其供应链管理存在许多问题,如供应延迟、库存积压和订单错误等。
这些问题导致了客户满意度下降、成本增加和交付时间延长。
步骤1:定义阶段在这个阶段,团队需要明确问题,并确定目标。
团队成员进行了一系列的访谈和数据收集,以了解供应链管理的不良表现和根本原因。
他们还采用了一些工具,如流程图和鱼骨图,来帮助分析现有的业务流程。
通过这个过程,团队确定了以下问题:1.供应商交货延迟的频率过高;2.供应商质量问题导致产品退货率上升;3.供应链管理过程中存在不必要的延迟和重复。
团队的目标是降低供应商交货延迟率和产品退货率,并改进供应链管理流程,以提高效率和客户满意度。
步骤2:测量阶段在这个阶段,团队需要收集关于问题的数据,并量化问题的影响。
团队成员收集并分析了供应商交货延迟率和产品退货率的数据,并确定了相关的指标和测量方式。
通过数据分析,团队发现供应商交货延迟率为10%,产品退货率为5%。
步骤3:分析阶段在这个阶段,团队使用统计工具和质量工具来分析问题的原因。
团队使用了流程图和鱼骨图来分析供应链管理的问题。
他们还使用了直方图、散点图和控制图等统计工具来确定问题的原因。
通过分析,团队发现供应商交货延迟的主要原因是缺乏有效的供应商评估和监控机制,产品退货率的主要原因是供应商质量问题。
步骤4:改进阶段在这个阶段,团队需要提出解决问题的解决方案,并实施改进措施。
团队提出以下改进方案:1.建立供应商评估和监控机制,定期对供应商进行评估,并设置合理的交货期限。
2.加强供应商质量管理,与供应商建立更紧密的合作关系,并提供培训和支持,以改进他们的生产流程和质量控制。
精选6sigmaDMAIC步骤
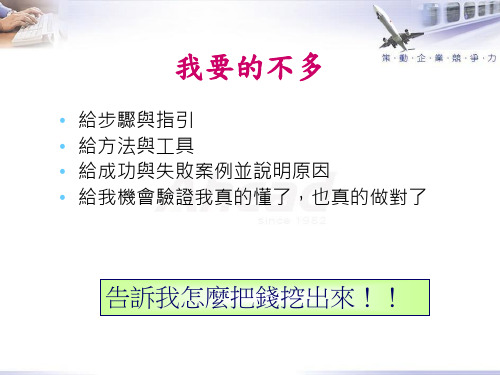
M3 發展數據收集工具
M2 Ys數據層別化
M4 發展操作性定義
M5 進行MSA
M6 數據收集計劃展
M8 計數值製程能力
M7 數據收集
M9 製程能力分析
M10 Sigma水準 (Z值)
計算計數值製程能力DPMO需要定義缺點機會並收集總缺點數
DPMO =
缺點總數Total Number of Defects
設計作業
輸入 KPIV外觀機能光學
輸出KPOV外觀檢查規格畫面閃動、無畫面機能檢查規格畫面亮點光學測定規格輝度,色度
下料作業(原料)
生產作業(LCD組立)
生產作業(LCM組立)
輸入 KPIV外觀機能光學
人員機器設備材料量測方法
人員機器設備材料組立方法
人員機器設備檢驗好的LCD檢驗好的材料組立方法
檢驗好的原材
D1:發展高階問題陳述
D2:成立專案小組
D3:確認客戶
D4:轉換VOC成CTQ
D5:發展操作性定義/衡量尺度
D6:發展缺點定義
D7:確認專案範圍
D8:預估顧客滿意/ COPQ
主要客戶究竟是誰?(作為後續訪談對象)
D4:轉換VOC成CTQ
Color STN顯示器外觀機能光學
D1:發展高階問題陳述
D2:成立專案小組
KPIV
D6:發展缺點定義
D7:確認專案範圍
D8:預估顧客滿意/ COPQ
專案範圍在QALCD PDLCM PD三部門生產作業。
D8 :預估顧客滿意/ COPQ
劣質成本(COPQ)影響不良報廢損失重工工時客戶抱怨處理賠償損失
D1:發展高階問題陳述
六西格玛DMAIC方法分析Fisher & Paykel企业生产环节问题
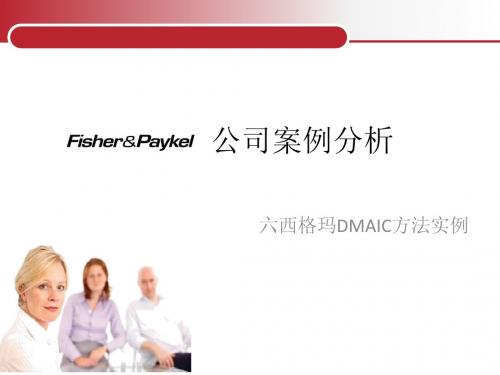
• 组建改进团队、组织结构和自责分工:
戴艾伦
电冰箱生产部门 采购员
珍妮
沃尔顿公司
蒂基•杜阿庞
真空成形制造部 门
尼尔•利斯
澳大利亚工厂在 奥克兰库管
约翰•格雷哈姆
冰箱生产线上小 组
约翰•吉布斯
质量统计
• 界定要改进的流程、起始结束点:
开始:蒸发器密封垫需求预测, 到蒸发器密封垫交付工厂作为备件 11
1. 生产计划确 认 2. 设备缓冲 3. 设备维护及 维修 4. 包装、入库 储备
打孔加工
1. 打孔质量控制 2. 包装、入库储 备 3. 设备维护及维 修 4. 设备转型
质量检验
1.检验标准 2.检验器械 3. 质量报告
交付工厂
1.物流运输 2.检验器械 3. 质量报告
C 可控输入变量:X可以改变来观察对Y的影响 S 标准操作流程SOP:运行流程中制定的标准程序 N 噪声输入:输入变量X变化时影响输出变量Y,但 是很难或者不可能控制这些因素 X 关键输入:通过数据统计看出输入X对输出Y的可 变性有主要影响
六西格玛DMAIC过程
Control
控
Improve
阶
改进阶
Define Analyze Measure
义阶
阶
测
阶
8
六西格玛DMAIC 目 录 DMAIC 六西格玛
DMAIC主要内容
D阶段 阶段 M阶段 阶段 A阶段 阶段 I阶段 阶段 C阶段 阶段
•界定项目 范围 、目 标及财务 收益 •确定项目 组织结构 •制定项目 计划 •完成SIPOC 流程图
目 录
公司案例分析
六西格玛DMAIC方法实例
六西格玛案例分析

表7 试验设计的因子和水平表
表8 试验设计表
Page
16
4.改进阶段箱线图
不良品 的箱线图
2 8 3
不良品 的箱线图
1 8 2
7
7
不良品
不良品
6
6
5
5
4
4
3 组块变量: 绕丝机档位
3 组块变量: 绕丝机
不良品 的箱线图
1 8 7 2 8
不良品 的箱线图
7
不良品
5
不良品
6
6
5
4
4
3 3 组块变量: 绕丝方向
DMAIC各个阶段中数据分析的需求,使得Minitab软件在六西 格玛管理中占据着重要的位置,它为使用者提供了准确、实用的 实现工具,帮助使用者进行质量控制、实验设计以及常用统计分 析等在六西格玛管理中不可缺少的分析。它已经成为六西格玛管 理技术进行实施的主要工具。下面就结合Minitab,运用六西格 玛改进分析,提高质量水平,达到改进目的,对节能灯装配过程 进行研究。
Page
2
1.定义阶段
(1)问题阐述
节能灯装配生产线需要经过插件和整灯两个主要 环节,由许多工序组成,运用六西格玛改进方式对其进行 分析研究可以根据当前状况设计出能够提高节能灯装配一 次性合格率的方案并进行有效地实施。
另外,提高了节能灯装配生产线的一次性合格率,不仅 可以使生产过程中出现的缺陷数减少,而且可以减少资源 的浪费,降低成本。
Page
3
1.定义阶段
(2)装配生产线一次性合格率现状 以四月份整灯二组为例,抽样统计结果见下表1。从下表统计中我们 可以看出:整灯二组在4月份生产过程中生产了40302支节能灯,其中 不良品合计1046支,合格率达到97.40%;
六西格玛DMAIC面包案例

2 3 4 5 6 7
“好面包”烘烤过程
最佳竞争者
需提高的间距
百万缺陷数
西格玛值
Freihofer WONDER Pepperidge Farm Sunbeam
还有..…不断的用数据绘图
FLOUR
“Brand C”
354 353 352 351 350 349 348
1 3 5 7 9 11 13 15 17 19 21 23 25
控制
讨论: 案例对我们的启发--结合各组的项目
控制
6 概述
第11步..…明确关键变量Xs的控制能力
如何实施? 检查所有烤箱温度 实时监控温度 关注过程能力 查找波动的程度
波动不错,但是…平均值偏高( 算法需检查)
30
345
# 烤箱号
温度
346
357
347
348
349
350
顾客看重的是什么? 蓬松度 软硬度 香味 新鲜 口味
Y = 口味!!
6 概述
测量
第2步..…对CTQs or Y定义绩效标准
或许5 过程是足够的!
1,000,000 - 100,000 - ............................. 10,000 - ............................. 1,000 - ............................. 100 - ............................. 10 - ............................. 1 -
6 概述
如何测量口味 (Y)? 品尝小组 从1 到10划分等级 目标: 平均为 8级 期望:不要低于7,即 低于7级为缺陷
六西格玛方法论:DMAIC步骤详解与案例分析

定
• 定期检查过程,及时发现新的问题和改
进点
02
成果巩固
• 对改进成果进行量化评估,确保改进目
标的实现
• 将改进成果纳入标准流程,实现成果的
长期巩固
04
六西格玛方法论的案例分
析
案例一:某制造企业生产流程优
化
问题识别与目标设定
• 通过数据分析,发现生产过程中的缺陷
和浪费
• 确定改进目标,提高生产效率和降低生
方法论的推广和执行
的典范,激发员工的参与热情
员工的培训与激励机制
激励机制
• 设计激励机制,如奖金、晋升和表彰等,鼓励员工参与六西格玛改进活动
• 通过公平和透明的激励机制,激发员工的积极性和创造力
员工培训
• 提供六西格玛方法论培训,使员工掌握改进方法和工具
• 提供技能培训,提高员工的岗位能力和综合素质
• 六西格玛的核心理念是追求极致,通过不断地改进和优化过程,实现高质量、高效率的运营
六西格玛方法论的发展历程
• 20世纪80年代,摩托罗拉公司首次提出六西格玛概念
• 90年代,通用电气公司推广六西格玛,使其成为全球范围内的质量管理方法
• 21世纪初,六西格玛方法论逐渐应用于非制造行业,如服务业和软件开发等
问题识别与目标设定
解决方案制定与实施
控制阶段
• 通过数据分析,发现项目开
• 提出改进方案,包括项目管
• 建立控制计划,定期检查项
发过程中的延误和资源浪费
理优化、开发流程改进和团队
目进度,确保改进成果的持续
• 确定改进目标,缩短项目周
协作提升
稳定
期和提高项目成功率
• 制定实施计划,分阶段实施
六西格玛成功(6sigma)案例学习[优秀范文五篇]
![六西格玛成功(6sigma)案例学习[优秀范文五篇]](https://img.taocdn.com/s3/m/51b2a8e3c0c708a1284ac850ad02de80d5d80658.png)
六西格玛成功(6sigma)案例学习[优秀范文五篇]第一篇:六西格玛成功(6sigma)案例学习6sigma成功案例**电子:步伐稳健行走于6σ之路2000年12月,第十届台湾品质奖的颁奖典礼上,在评审“品质不折不扣”的理念下,**电子以多年来致力追求品质的决心与成就,脱颖而出,获得台湾品质奖。
细察**电子追求品质的努力、实践品质的过程,得以知道这个奖得来实至名归。
**电子自1994年起,就在董事长许胜雄的领导下,努力实践6σ(Six Sigma)的品质策略。
何谓6σ?σ在字面上的定义是为统计学上的标准差,简单来说,σ是一个测量品质的标准工具,它代表一种绩效目标,也是一种品质改善的观念。
达到6σ表示每百万次中只会出现3.4个错误,几乎等于零缺点。
σ曾经协助许多世界级企业展现惊人的成绩,它曾经使通用电气(GE)公司迈向营运的高峰,被杰克韦尔奇称许为通用所采用的过最重要的管理措施;也是西方企业力抗日本企业反败为胜的法宝。
提起**电子导入6 σ的原由,**电子副总经理陈乃源表示:“起源于为了满足顾客对品质的要求。
”在未实行6 σ前,**电子所生产的产品错误率颇高,无法达到客户满意,除容易引起顾客的抱怨,相对也缺乏竞争力。
为了提高竞争力,**电子决定导入6 σ。
当时**电子派遣了一批人员到美国接受6σ的训练课程,其中成员包含总经理、数位副总及相关人员,陈乃源也是其中之一。
受训回国后,陈乃源全心投入**电子执行6 σ的架构规划。
陈乃源指出:“实践6 σ的基本原则,是以顾客需求为出发点,一切改善都必须以顾客需求为主,它讲求从制造过程开始改进,而不是看产品产出最后的结果,因为产品事后的修补往往要花费更多的成本。
品质改善最重要的是要从根源做起,也就是在设计时就减少错误的机会。
尤其是在产品生命周期急速缩短的今天,已没有时间让你尝试错误了,也无法再像过去一样等生产过程结束后再统计错误,必须在设计的时候就减少错误的发生,把线上的制程能力及零件的制造能力都计算、考虑进去,让产品合于标准,将制造流程改善,一次就做好,使得后续不至于有错误发生。
- 1、下载文档前请自行甄别文档内容的完整性,平台不提供额外的编辑、内容补充、找答案等附加服务。
- 2、"仅部分预览"的文档,不可在线预览部分如存在完整性等问题,可反馈申请退款(可完整预览的文档不适用该条件!)。
- 3、如文档侵犯您的权益,请联系客服反馈,我们会尽快为您处理(人工客服工作时间:9:00-18:30)。
11.9492
13.0450
95% Confidence Interval for Median
17.1454
18.8434
Report 1: Executive Summary
Process Performance
Actual (LT) Potential (ST)
LSL
USL
1,000,000 100,000
开发流程数据收集计划。确定缺陷和度量的类型.
• Zst = 0.72, ppm = 446,887,st.Dev=12.47 • 进一步与客户沟通,我们设定目标值为Z=2.0. • 即标准偏差为7.5 天.
10,000 1000 100 10 1 0
Process Benchmarks
Actual (LT) Potential (ST)
Sigma
(Z.Bench)
0.13 0.72
PPM 446887 236002
500
1000
过程能力显示当前的西格玛值为 Zst = 0.72 .
六西格玛管理法导论
六西格玛管理法导论
改进方法
DMAIC • 评估 • 导出对业务流程质量的影响点和具体要求 • 根据这些流程标准来评估现有的核心业务流程能力。
找出差距 • 开发流程数据收集计划。确定缺陷和度量的类型 • 找出造成这些缺陷的所有可能的原因
六西格玛管理法导论
导出对业务流程质量的影响点和具体要求
流程图
供应商发货
接收 清洁 检测
加工
清 洁 检 查 运输
步骤 1
步骤 2
步骤 3
六西格玛管理法导论
根据这些流程标准来评估现有的核心业务流程能力,找出差距
Descriptive Statistics
Variable: C1
-22.5 -10.0 2.5 15.0 27.5 40.0 52.5
95% Confidence Interval for Mu
小 时
//
/
年年
千
瓦
63 38 57 99 36 27
方向 越多越好 越少越好 固定量
关系 ◎强烈-9 ○适中-3 △微弱-1
六西格玛管理法导论
项目要求
客 户
需 质量之 求屋
#1
主要流程
项 目
要 质量之 求屋
#2
关键项目要求
主要流程步骤
服务领域应用
主要任务
主
要
流 质量之
程
屋
步
骤 #3
主要任务
六西格玛管理法导论
没有意识到 技术的存在
企业没有利 用高科技减 少差旅费用
软件没有得到 安装和调试
六西格玛管理法导论
柏拉图法则:PARETO CHART
1. 根据意大利经济学家柏拉图的理论命名的,他指出社会重等收 入分配是不均匀的。即80%的财富由20%的人所掌握。同样的 在流程中大部分的缺陷经常是由相对较少的原因造成的。
六西格玛管理法导论
核心方法论
DMAIC ❖测量
导出对业务流程质量的影响点和具体要求 根据这些流程标准来评估现有的核心业务流程能力、找出差距 开发流程数据收集计划、确定缺陷和度量的类型 找出造成这些缺陷的所有可能的原因
六西格玛管理法导论
核心方法论
DMAIC ❖分析
分析收集的数据和流程图、决定造成缺陷的根本原因
六西格玛管理法导论
QFD:质量功能展开
鉴别客户需求,将其量化并排序,并体现到产品、服务及 流程设计中
使用步骤: 1.归纳客户需求、将其变成产品及服务特征 2.将服务特征量化、变成可评估性需求 3.将评估标准变成流程设计特征 4.将流程设计特征变成流程绩效标准
六西格玛管理法导论
◎强烈正相关 ○正相关 ×负相关 ※强烈负相关
2. 造成缺陷的原因可能很多,可以改进的也很多但是知道从哪里 入手做好并不容易,而可以帮助你分类并隔离出最重要的因素。
六西格玛管理法导论
柏拉图法则:PARETO CHART
六西格玛管理法导论
失败模式和影响分析(FMEA)
1、FMEA是一种为避免失误发生而做出计划的战略。 FMEA鉴别潜在的风险模式,并分配以权重级别 FMEA对于事故的发生原因和探测事故发生可能性的能力给出客观的评价 FMEA对有缺陷的产品或流程进行排序并着重于测的清除隐患
六西格玛管理法导论
DMAIC 方法论
六西格玛管理法导论
六西格玛(DMAIC)项目实施步骤
定义
测评
分析
改进
控制
Define Measure
Analyze
Improve
Control
六西格玛管理法导论
应用统计学解决问题
实际问题 统计问题 统计方案
实际方案
偏离目标值 隔离关键X
六西格玛管理法导论
DMAIC 12步
与要求时间的差异 每个部件的运输费用
材料成本 平均首次故障时间
0
10
20
30
40
50
六西格玛管理法导论
导出项目的关键性质量要素,项目所影响的核心商 业过程
• 问题所关注的测量特征可转化为: • 实际到货时间与客户要求到货时间的差值 • 这就要求了解客户所认可的标准(客户所能容忍的最大限
度?)
• 定义缺陷/次品,定义缺陷机会 通过进一步了解与客户,可了解到客户所能容忍的最大限度是: 早到10天;晚到20天. (即在要求时间10天前到,和要求时间20天后到都为缺陷.)
步骤
描述
改善
7 筛选滞在原因
8 发现变量关系
9 建立操作关系 控制
10 定义并验证实际应用 中的X测量系统
11 确定流程能力 12 实施流程控制
重点
X X Y、X
Y、X
Y、X X
工具
SSQC的结果
DOE-筛选 因子设计 模拟
关键少数Xs(11)的列 建议解决方案(13) 试验方案(14)
连续数据测量系统R&R, 检验/再检验,属性数据的 R&R
2、FMEA的类型 系统FMEA:在系统的概念形成早期对系统及子系统进行分析。 设计FMEA:在某产品/服务投入生产之前进行的分析 流程FMEA:用于分析生产、装配和交易型的流程分析
六西格玛管理法导论
6西格玛实践寻宝图
范围与文件
培训
测量
明确希望的后果 分析现状
前期工作 与项目选定
定义
形成团队与 界定项目
项目要求
客 户
需 质量之 求屋
#1
主要流程
功 能
要 质量之 求屋
#2
关键性功能要求
关键组件特征
产品领域应用
主要任务
组
建
特 质量之
征
屋
#3
关键生产流程
主要任务
生
产
流 质量之
程
屋
#4
关键流程变量
六西格玛管理法导论
鱼骨形图/因果图:CAUSE & EFFECT DIAGRAM
对效果根源进行鉴别,分类及排序的方法 由40年代早期日本川崎(Kawasaki)钢厂的石川首创 使用步骤:
1、确认主要原因类型:机器、人员、方法、测量、材料、环境 2、利用头脑风暴法对每类原因进行细分 3、对每个原因的重要性加以权重评定
六西格玛管理法导论
鱼骨形图/因果图:CAUSE & EFFECT DIAGRAM
技术 环境
人员
协调作业技 术不成熟
公司的系统 环境不允许 公司内部网 速度太慢
软件
对软件不熟悉
项目Y(5)的表现标准
Y 连续数据测量系统R&R,检 数据收集计划和MSA(6),项 验/再检验,属性数据的R&R 目数据Y(7)
Y 能力指标
项目Y(8)的流程能力
Y 团队、属性参照
项目Y(9)改善目标
X 流程分析、图像分析、 所有Xs的优先列表(10) 假设检验
六西格玛管理法导论
DMAIC 12步
不仅是一个分类的工具,在流程 改善中确定每一步如何操作,可 以想像当每个人都使用同种方 法时会产生较大协同效应.
六西格玛管理法导论
六西格玛重要应用工具
质量功能展开(QUALITY FUNTIONAL DEPLOYMENT) 鱼骨型图/因果图(CAUSE & EFFECT DIAGRAM) 柏拉图法则(PARETO CHART) 失败模式和影响分析(FMEA) 统计流程控制(SPC) 防错法(MISTAKE PROOFING)
1000
Minimum 1st Quartile Median 3rd Quartile Maximum
-22.8825 9.9619
17.9801 26.6543 56.9202
95% Confidence Interval for Mu
17.3369
18.8849
95% Confidence Interval for Sigma
能力参数
控制图, FMEA
MSA
流程能力Y、X 持续的解决方案(15) 文献(16)
六西格玛管理法导论
改进方法
DMAIC ❖定义
要确定项目的目标和范畴; 确认项目中顾客和顾客的关键性质量要素(CTQ); 导出项目的关键性质量要素,项目所影响的核心商业过程; 定义缺陷/次品,定义缺陷机会; 表述项目章程,建立项目小组;
• 但你们的交货期却有很大问题! 你们经常迟发货. 如果你们过早的发货同样会给我们带来很大麻烦.我 们实在没有能力去处理此类事情.
如果我们不按客户制定日期发货,我们的客户会选择其他的供应商.
所以准时发货是当前最关键的问题. 然后是成本, 再是可靠性.