铸造缺陷特征原因及预防措施图文并茂
铸坯表面缺陷图谱及产生原因
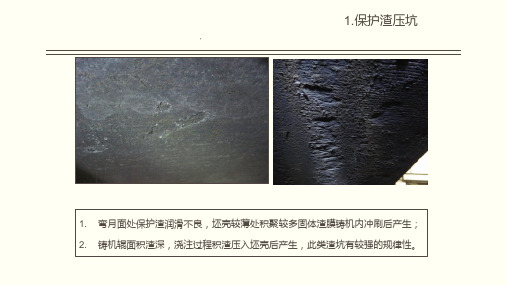
3.纵 裂
1. 水口与结晶器不对中而产生偏流冲刷初生凝固坯壳; 2. 保护渣熔化性能不良、液渣层过厚或过薄; 3. 结晶器液面波动(液面波动≥±5㎜,纵裂发生几率≥30%); 4. 受钢种特性影响:钢中S>0.02%,P>0.017%,发生纵裂趋向增大;
4.横 裂
1. 振痕过深刻导致连铸坯横向裂开; 2. 钢中含A1、Nb,刻促使质点(A1N)、Nb(C,N)在晶界沉淀,诱发横裂纹; 3. 铸坯在第二脆性区间矫直; 4. 二次冷却太强。
5.结 疤
1. 结晶器弯月面处初生坯壳生长不均匀,薄弱处与结晶器壁粘结后又在振动作用 下脱开形成;
2. 保护渣化渣效果差,润滑不均匀;
6.凹 陷
1. 边部凹陷原因为保护渣润滑效果差,另一原因为宽窄面冷却差异。 2. 中部凹陷原因为保护渣流入过大,减缓传热,使局部凝固坯壳变薄;
7.接 痕
1. 结晶器专家报警后拉速瞬间降至0.1m/min; 2. 浇注过程其他异常人为停机; 3. 开浇过程结晶器液面下跌。
ቤተ መጻሕፍቲ ባይዱ
1.保护渣压坑
1. 弯月面处保护渣润滑不良,坯壳较薄处积聚较多固体渣膜铸机内冲刷后产生; 2. 铸机辊面积渣深,浇注过程积渣压入坯壳后产生,此类渣坑有较强的规律性。
2.振痕紊乱、深振痕
1. 振动参数设计不合理,负滑脱时间长,振幅较大可导致振痕深; 2. 结晶器液面波动大,波动≥±3mm; 3. 初生坯壳冷却不均,保护渣润滑不稳。
8.夹 渣(卷渣)
1. 结晶器液面波动大,窄侧液面翻腾严重; 2. 水口插入深度过浅造成钢流股冲击液面; 3. 拉钢速度与水口内径不匹配,水口侧孔钢流速度过大,回流到达液面产生较大
切应力导致渣卷入。
铸件缺陷与改进措施

铸件两壁之间 的型芯厚度一 般应不小于两 内 腔 边壁厚的总和 过小 (c>a 十 b),以 免两壁熔接在 一起
大件中部凸台
9 形状 与尺 寸不 合格
位置尺寸不易 保证,铸造偏 差较大;应考 虑将凸台尺寸 加大,或移至
凸 台 内部
过小
凸台应大于支 座的底面,以 保证装配位置 和外观整齐
考虑顺序凝 固,以利逐层 补缩,缸体壁 设计成上厚下 薄
对于两端壁较 厚的铸钢件断 面,为创造顺 序凝固条件, 应使 a≥b,并在 底部设置外冷 铁,形成上下 温度梯度有利 于顺序补缩, 消除缩孔、缩 松
2 气孔 水 与 夹面 渣大
尽量减少较大 的水平平面, 尽可能采用斜 平 平面,便于金 过 属中央杂物和 气体上浮排 除,并减少内 应力 铸孔的轴线应
改进前
铸件缺陷与改进措施
图例
改进后
铸件 缺陷 形式
注意 事项
改进措施
壁厚力求均 匀,减少厚大 断面以利于金 属同时凝固。 改进后将孔径 中部适当加 大,使壁厚均 匀
铸件壁厚应尽
量均匀,以防
止厚截面处金
属积聚导致缩
孔、疏松、组
织不密致等缺
1 缩孔 壁
陷 厚
与 疏 不均
松
局部厚壁处减 薄
采用加强肋代 替整体厚壁铸 件
为减少金属的 积聚,将双面 凸台改为单面 凸台
改进前,深凹 的锐角处易产 生气缩孔
尽量不采用正 十字交叉结 构,以减少金 屑积聚 肋与 壁交 叉
交叉肋的交点 应置环形结构
产生缩松处难 以安放冒口, 补缩 不良 故加厚与该处 连通的壁厚, 加宽补缩通道
图示一铸钢夹 子,冒口放在 凸台上。原设 计凸台不够大 (φ310mm) ,补 缩不良。后将 凸台放大到 φ4l0mm,才消 除了缩孔
铸件常见缺陷(图文并貌)
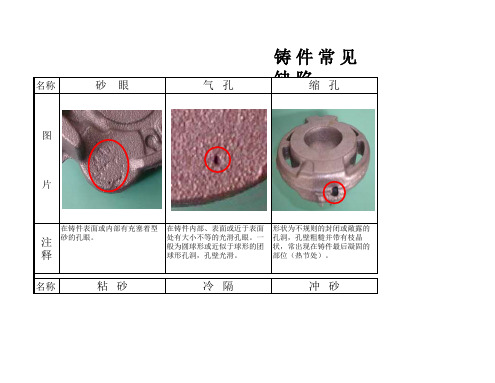
铸件常见缺陷
名称砂眼气孔缩孔披缝图
片
注释在铸件表面或内部有充塞着型
砂的孔眼。
在铸件内部、表面或近于表面
处有大小不等的光滑孔眼。
一
般为圆球形或近似于球形的团
球形孔洞,孔壁光滑。
形状为不规则的封闭或敞露的
孔洞,孔壁粗糙并带有枝晶
状,常出现在铸件最后凝固的
部位(热节处)。
披缝是铸件表面上厚薄不均匀
的片状金属突起物,常出现在
铸件分型面和芯头部位。
名称粘砂冷隔冲砂掉砂
图片
注释在铸件表面上、全部或部分覆
盖着金属与砂的混合物,或一
层烧结的型砂,致使铸件表面
粗糙。
冷隔是铸件上未完全融合的缝
隙或洼坑,其交接边缘呈圆
角,多出现在远离浇口的铸件
宽大上表面和薄壁处、金属流
股汇合处或激冷部位。
铸件表面上有粗糙不规则的金
属瘤状物,常位于浇口附近。
在铸件其它部位则往往出现砂
眼。
铸件表面的块状金属突起物,
其外形与掉落的砂块很相似。
在铸件其它部位则往往出现砂
眼或残缺。
毛 刺浇 不 足
毛刺是铸件表面上刺状金属突起物,常出现在型和芯的裂缝处,形状极不规则。
由于金属液未完全充满型腔而产生的铸件缺肉。
缺 损变 形渣 眼
在铸件清理或搬运时,损坏了铸件的完整性。
由于收缩应力或型壁变形、开
裂引起的铸件外形和尺寸与图
纸不符。
在铸件内部或表面形状不规
则的孔眼。
孔眼不光滑,里
面全部或部分充塞着渣。
铸件充填缺陷及其防止措施
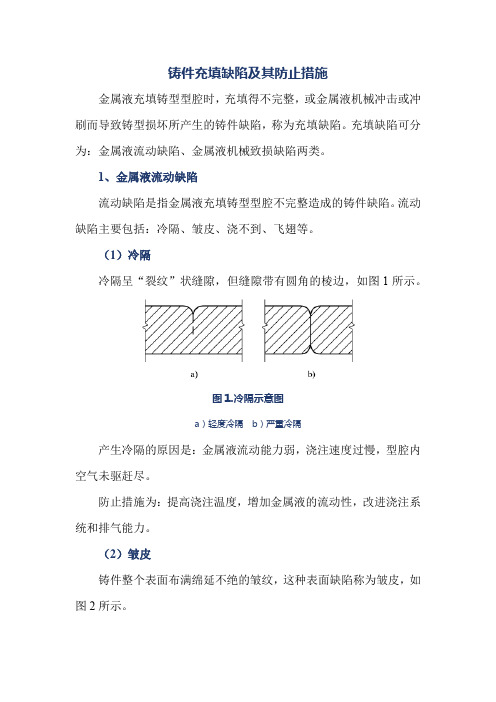
铸件充填缺陷及其防止措施金属液充填铸型型腔时,充填得不完整,或金属液机械冲击或冲刷而导致铸型损坏所产生的铸件缺陷,称为充填缺陷。
充填缺陷可分为:金属液流动缺陷、金属液机械致损缺陷两类。
1、金属液流动缺陷流动缺陷是指金属液充填铸型型腔不完整造成的铸件缺陷。
流动缺陷主要包括:冷隔、皱皮、浇不到、飞翅等。
(1)冷隔冷隔呈“裂纹”状缝隙,但缝隙带有圆角的棱边,如图1所示。
图1.冷隔示意图a)轻度冷隔b)严重冷隔产生冷隔的原因是:金属液流动能力弱,浇注速度过慢,型腔内空气未驱赶尽。
防止措施为:提高浇注温度,增加金属液的流动性,改进浇注系统和排气能力。
(2)皱皮铸件整个表面布满绵延不绝的皱纹,这种表面缺陷称为皱皮,如图2所示。
图2.皱皮合金中有易氧化的元素(如Mn、Si)且含量较高时(像硅锰低合金钢ZG20MnSi),极易形成皱皮。
其形成过程为:在钢液的充型过程中,随着型腔内上升液面温度的降低液面形成氧化膜,液面继续上升使氧化膜粘附于型壁上,钢液面漫过氧化膜留下痕迹;当液面温度下降到凝固温度范围时,液面结壳,更严重地阻碍型腔内液面的上升运动,但型腔内液面克服阻力,突破液面壳之阻力漫过它继续上升,结果在金属—铸型界面上留下痕迹,即皱皮。
铸钢薄壁件表面上易出现的这种皱皮缺陷。
其防止的根本措施为:提高钢液在型腔内的上升速度(不低于18mm/s);采用还原性气氛保护上升的金属液面,使型腔中CO与CO2、H2与H2O的比值增大。
(3)浇不到缺陷铸件不完整,有停止流动的流头残迹。
浇不到缺陷形成的主要原因是:浇注温度不够,浇道过小,排气孔数量不够。
浇不到缺陷的防止措施有:提高浇注温度,加大浇道尺寸,改进排气系统。
(4)飞翅垂直于铸件表面上的薄片状金属突出物,称为飞翅(或称飞边)。
飞翅缺陷形成的主要原因是:上、下分型面或铸型芯座与型芯芯头之间的装配间隙过大,浇注时造成液态金属钻入缝隙中。
翅缺陷的防止措施有:控制上、下分型面或铸型芯座与型芯芯头之间的装配间隙,对工艺缝隙进行填补等。
常见铸造缺陷产生的原因及防止方法

常见铸造缺陷产生的原因及防止方法铸件缺陷种类繁多,产生缺陷的原因也十分复杂.它不仅与铸型工艺有关,而且还与铸造合金的性制、合金的熔炼、造型材料的性能等一系列因素有关.因此,分析铸件缺陷产生的原因时,要从具体情况出发,根据缺陷的特征、位置、采用的工艺和所用型砂等因素,进行综合分析,然后采取相应的技术措施,防止和消除缺陷.一、浇不到1、特征铸件局部有残缺、常出现在薄壁部位、离浇道最远部位或铸件上部.残缺的边角圆滑光亮不粘砂.2、产生原因1 浇注温度低、浇注速度太慢或断续浇注;2 横浇道、内浇道截面积小;3 铁水成分中碳、硅含量过低;4 型砂中水分、煤粉含量过多,发气量大,或含泥量太高,透气性不良;5 上砂型高度不够,铁水压力不足.3、防止方法1 提高浇注温度、加快浇注速度,防止断续浇注;2 加大横浇道和内浇道的截面积;3 调整炉后配料,适当提高碳、硅含量;4 铸型中加强排气,减少型砂中的煤粉,有机物加入量;5 增加上砂箱高度.二、未浇满1、特征铸件上部残缺,直浇道中铁水的水平面与铸件的铁水水平面相平,边部略呈圆形.2、产生原因1 浇包中铁水量不够;2 浇道狭小,浇注速度又过快,当铁水从浇口杯外溢时,操作者误认为铸型已经充满,停浇过早.3、防止方法1 正确估计浇包中的铁水量;2 对浇道狭小的铸型,适当放慢浇注速度,保证铸型充满.三、损伤1、特征铸件损伤断缺.2、产生原因1 铸件落砂过于剧烈,或在搬运过程中铸件受到冲撞而损坏;2 滚筒清理时,铸件装料不当,铸件的薄弱部分在翻滚时被碰断;3 冒口、冒口颈截面尺寸过大;冒口颈没有做出敲断面凹槽.或敲除浇冒口的方法不正确,使铸件本体损伤缺肉.3、防止方法1 铸件在落砂清理和搬运时,注意避免各种形式的过度冲撞、振击,避免不合理的丢放;2 滚筒清理时严格按工艺规程和要求进行操作;3 修改冒口和冒口颈尺寸,做出冒口颈敲断面,正确掌握打浇冒口的方向.四、粘砂和表面粗糙1、特征粘砂是一种铸件表面缺陷,表现为铸件表面粘附着难以清除的砂粒;如铸件经清除砂粒后出现凹凸不平的不光滑表面,称表面粗糙.2、产生原因1 砂粒太粗、砂型紧实度不够;2 型砂中水分太高,使型砂不易紧实;3 浇注速度太快、压力过大、温度过高;4 型砂中煤粉太少;5 模板烘温过高,导致表面型砂干枯;或模板烘温过低,型砂粘附在模板上.3、防止方法1 在透气性足够的情况下,使用较细原砂,并适当提高型砂紧实度;2 保证型砂中稳定的有效煤粉含量;3 严格控制砂水分;4 改进浇注系统,改进浇注操作、降低浇注温度;5 控制模板烘烤温度,一般与型砂温度相等或略高.五、砂眼1、特征在铸件内部或表面充塞有型砂的孔眼.2、产生原因1 型砂表面强度不够;2 模样上无圆角或拔模斜度小导致钩砂、铸型损坏后没修理或没修理好就合箱;3 砂型在浇注前放置时间过长,风干后表面强度降低;4 铸型在合箱时或搬运过程中损坏;5 合箱时型内浮砂未清除干净,合箱后浇口杯没盖好,碎砂掉进铸型.3、防止方法1 提高型砂中粘士含量、及时补加新砂,提高型砂表面强度;2 模样光洁度要高,并合理做出拔模斜度和铸造圆角.损坏的铸型要修好后再合箱;3 缩短浇注前砂型的放置时间;4 合箱或搬运铸型时要小心,避免损坏或掉入砂型腔砂粒;5 合箱前清除型内浮砂,并盖好浇口.六、披缝和胀砂1、特征披缝常出现在铸件分型面处,是垂直于铸件表面,且厚薄不均匀的薄片状金属突起物. 胀砂是铸件内、外表面局部胀大,形成不规则的瘤状金属突起物.2、产生原因1 紧实度不够或不匀;2 面砂强度不够、或型砂水分过高;3 液态金属压头过大、浇注速度太快.3、防止方法1 提高铸型紧实度、避免局部过松;2 调整混砂工艺、控制水分,提高型砂强度;3 降低液态金属的压头、降低浇注速度.七、抬箱1、特征铸件在分型面处有大面积的披缝,使铸型外形尺寸发生变化.抬箱过大,造成跑火——铁水自分型面外溢,严重时造成浇不足缺陷.2、产生原因1 砂箱未紧固、压铁质量不够或去除压铁过早;2 浇注过快,冲击力过大;3 模板翅曲.3、防止方法1 增加压铁重量,特铁水凝固后再去除压铁;2 降低浇包位置,降低浇注速度;3 修正模板.八、掉砂1、特征铸件表面上出现的块状金属突起物,其外形与掉落的砂块很相似.在铸件其它部位,则往往出现砂眼或残缺.2、产生原因1 模样上有深而小的凹槽,同于结构特征或拔模斜度小,起模时将砂型带坏或震裂;2 紧实度不匀,铸型局部强度不足;3 合箱、搬运铸型时,不小心使铸型局部砂块掉落.3、防止方法1 模样拔模斜度要合适、表面光洁;2 铸型紧实度高且均匀;3 合箱、搬运过程中,操作小心.九、错型错箱1、特征铸件的一部分与另一部分在分型面的接缝处错开,发生相对位移,使铸件外形与图纸不相符合.2、产生原因1 模样制作不良,上下模没有对准或模样变形;2 砂箱或模板定位不准确,或定位销松动;3 挤压造型机上零件磨损,例如正压板下衬板、反压板轴承的磨损等;4 浇注时用的套箱变形,搬运、围箱时不注意,使上下铸型发生位移.3、防止方法1 加强模板的检查和修理;定2 经常检查砂箱、模板的定位销及销孔、并合理地安装;3 检查挤压造型机的有关零件,及时调整,磨损大的要更换;4 定期对套箱整形.脱箱后的铸型在搬运时要小心.在面浇注的砂型,应该做一排砂型围一排.十、灰口和麻点1、特征铸件断口呈灰黑色或出现黑色小点,中心部位较多,边部较少,金相观察可见到片状石墨.2、产生原因1 铁水化学成分不合要求,碳、硅含量过高;2 炉前孕育的铋加入浇包内过早或过迟,或是铋量不足.3、防止方法1 正确选择化学成分,合理配料,使铁水中碳、硅量在规定范围内;2 增加铋的加入量并严格炉前孕育工艺.十一、裂纹热裂、冷裂1、特征铸件外部或内部有穿透或不穿透的裂纹.热裂时带有暗色或黑色的氧化表面断口外形曲折.冷裂是较干净的脆性裂纹,断口较平,具有金属光泽或轻微的氧化色泽.2、产生原因1 铁水中碳、硅含苞欲放量过低,含硫量过高;2 浇注温度过高;3 冒口颈过大、过短,造成局部过热严重,或重口太小,补缩不好;4 铸件在清理、运输过程中,受冲击过大.3、防止方法1 控制铁水化学成分在规定的范围内;2 降低浇注温度;3 合理设计冒口系统;4 铸件在清理、运输过程中避免过度冲击.十二、气孔1、特征气孔的孔壁光滑明亮,形状有圆形、梨形和针状,孔的尺寸有大有小,产生在铸件表面或内部.铸件内部的气孔在敲碎后或机械加工时才能被发现.2、产生原因1 小炉料潮湿、锈蚀严重或带有油污,使铁水含气量太多、氧化严重;2 出铁孔、出铁槽、炉衬、浇包衬未洪干;3 浇注温度较低,使气体来不及上浮和逸出;4 炉料中含铝量较高,易造成氢气孔;5 砂型透气性不好、型砂水分高、含煤粉或有机物较多,使浇注时产生大量气体且不易排出.3、防止方法1 炉料要妥善管理,表面要清洁;2 炉缸、前炉、出铁口、出铁槽、浇包必须烘干;3 提高浇注温度;4 不使用铝量过高的废钢;5 适当降低型砂的水分、控制煤粉加入量,扎通气孔等.十三、缩松、疏松1、特征分散、细小的缩孔,带有树枝关结晶的称缩松,比缩松更细小的称疏松.常出现在热世部位.2、产生原因1 铁水中碳、硅含量过低,收缩大;2 浇注速度太快、浇注温度过高,使得液态收缩大;3 浇注系统、冒口设计不当,无法实现顺序凝固;4 冒口太小,补缩不充分.3、防止方法1 控制铁水的化学成分在规定范围内;2 降低浇注速度和浇注温度;3 改进浇冒口系统,利用顺序凝固;4 加大冒口体积,保证充分补缩.十四、反白口1、特征铸件断口内部出现白口组织,边缘部分出现灰口.2、产生原因1 碳、硅含量较高的铁水,含氢量过高;2 炉料中带入的铬等白口形成元素过多;3 元素偏析严重;3、防止方法1 控制化学成分、碳、硅含量不宜过高;2 炉衬、包衬要烘干;型砂水分不宜过高;3 加强炉料管理,减少带入白口化元素.。
铜合金铸件铸造缺陷及防止对策ppt课件

○
○
○
○ ○○
○
○○
○
○
○
○
○
○○○ ○
1 1 12
17 7 2
11 3 10
○ 65 3
表3续
2、艺术铸造铜合金的冶金特性
艺术铸造铜合金的独特要求:
①合金应满足艺术铸品的使用要求 ——耐蚀性、色泽、声学特性和机械性能
②合金应满足各种工艺要求 ——铸造成形性能、可焊接性能、可打磨加工 性能和表面着色性能
deabcde图1缩孔缩松缺陷示意图外缩孔内缩孔缩松图2铜合金铸件铸造缺陷分类及其主要原因主要原因铸造缺陷模型装置砂箱装置砂的性质的有机材料造型材料中制芯作业造型作业合箱金属液铸件设计浇冒口系统铸造工艺方案浇注温度浇注技术不注意1错箱2浇不到3冷隔4砂型压崩5胀箱6壁厚尺寸偏差7冲砂8夹砂表3铜合金铸件铸造缺陷分类及其主要原因续主要原因铸造缺陷模型装置砂箱装置砂的性质的有机材料造型材料中制芯作业造型作业合箱金属液铸件设计浇冒口系统铸造工艺方案浇注温度浇注技术不注意9表面气坑10烧结粘砂机械粘砂11内侧面包芯砂12表面不完整13虫眼表面14表面锈迹15锡汗铅汗16表面粗糙表3续铜合金铸件铸造缺陷分类及其主要原因续主要原因铸造缺陷模型装置砂箱装置砂的性质的有机材料造型材料中制芯作业造型作业合箱金属液铸件设计浇冒口系统铸造工艺方案浇注温度浇注技术不注意17表面麻点18褪色a1青铜19固体夹杂20缩孔21热裂22粗晶组织23气孔24铸件清理缺陷1112177211310653表3续2艺术铸造铜合金的冶金特性?艺术铸造铜合金的独特要求
砂 箱 装 置
砂 造的 制
的 性 质
型有 材机 料材 中料
芯 作 业
造 型 作 业
合 箱
铸造缺陷的特征、鉴别、成因及防治措施

铸造缺陷的特征、鉴别方法、成因及防治措施一、多肉类缺陷的防止措施总结1、飞翅缺陷的特征、鉴别方法、成因及防治措施(1)定义和特征产生在分型面、分芯面、芯头、活块及型与芯结合面等处,通常垂直于铸件表面的厚度不均匀的薄片状金属凸起物,又称为飞边或披缝。
(2)鉴别方法肉眼外观检查。
飞翅出现在型—型、型—芯、芯—芯结合面上,成连片状,系结合面间隙过大所致。
(3)形成原因①②③④⑤⑥⑦(4)防止方法①②③④⑤⑥⑦(5)补救措施2、毛刺缺陷的特征、鉴别方法、成因及防治措施(1)定义和特征(2)鉴别方法肉眼外观检查。
(3)形成原因①②③④⑤⑥⑦(4)防止方法①②③④⑤⑥⑦(5)补救措施3、冲砂缺陷的特征、鉴别方法、成因及防治措施(1)定义和特征(2)鉴别方法肉眼外观检查。
(3)形成原因①②③④⑤⑥⑦(4)防止方法①②③④⑤⑥⑦(5)补救措施4、胀砂缺陷的特征、鉴别方法、成因及防治措施(1)定义和特征(2)鉴别方法肉眼外观检查。
(3)形成原因①②③④⑤⑥⑦(4)防止方法①②③④⑤⑥⑦(5)补救措施5、抬型/抬箱缺陷的特征、鉴别方法、成因及防治措施(1)定义和特征(2)鉴别方法肉眼外观检查。
(3)形成原因(4)防止方法①②③④⑤(5)补救措施①②6、外渗物/外渗豆缺陷的特征、鉴别方法、成因及防治措施(1)定义和特征(2)鉴别方法肉眼外观检查。
(3)形成原因①②③(4)防止方法①②③④⑤⑥(5)补救措施7、掉砂缺陷的特征、鉴别方法、成因及防治措施(1)定义和特征(2)鉴别方法肉眼外观检查。
(3)形成原因①②③④⑤⑥⑦(4)防止方法①②③④⑤⑥⑦(5)补救措施二、孔洞类1、反应气孔缺陷的特征、鉴别方法、成因及防治措施(1)定义和特征(2)鉴别方法(3)形成原因①②③(4)防止方法①②③(5)补救措施2、卷入气孔缺陷的特征、鉴别方法、成因及防治措施(1)定义和特征(2)鉴别方法(3)形成原因①②③(4)防止方法①②③④(5)补救措施①②③3、侵入气孔缺陷的特征、鉴别方法、成因及防治措施(1)定义和特征(2)鉴别方法(3)形成原因①②③④(4)防止方法①②③④(5)补救措施①②③4、析出气孔缺陷的特征、鉴别方法、成因及防治措施(1)定义和特征(2)鉴别方法(3)形成原因①②③(4)防止方法(5)补救措施①②③5、疏松(显微缩松)缺陷的特征、鉴别方法、成因及防治措施(1)定义和特征(2)鉴别方法(3)形成原因①②③④⑤⑥⑦⑧⑨⑩(4)防止方法①②③④⑤⑥⑦⑧⑨⑩(5)补救措施①②③④6、缩孔缺陷的特征、鉴别方法、成因及防治措施(1)定义和特征(2)鉴别方法(3)形成原因①②③④⑤⑥⑦(4)防止方法①②③④⑤⑥⑦⑧(5)补救措施7、缩松缺陷的特征、鉴别方法、成因及防治措施(1)定义和特征(2)鉴别方法(3)形成原因①②③④⑤⑥⑦⑧⑨⑩(4)防止方法①②③④⑤⑥⑦⑧⑨⑩(5)补救措施①②③④三、裂纹、冷隔类1、白点(发裂)缺陷的特征、鉴别方法、成因及防治措施(1)定义和特征(2)鉴别方法(3)形成原因①②(4)防止方法①②③④(5)补救措施2、冷隔缺陷的特征、鉴别方法、成因及防治措施(1)定义和特征(2)鉴别方法肉眼外观检查。
压铸件缺陷产生原因及对应措施

1.降低浇注温度,减少收缩量 2.提高压射比压及增压压力,提高致密 性 3.修改内浇口,使压力更好传递,有利 于液态金属补缩作用 4.改变铸件结构,消除金属积聚部位, 壁厚尽可能均匀 5.加快厚大部位冷却 6.加厚料柄,增加补缩的效果
3
夹杂
1.炉料不洁净,回炉料太多 混入压铸件内的金属或非金属 2.合金液未精炼 杂质,加工后可看到形状不规 3.用勺取液浇注时带入熔渣 则,大小、颜色、亮度不同的 4.石墨坩埚或涂料中含有石墨脱落混 点或孔洞 入金属液中 5.保温温度高,持续时间长 1.铝合金中杂质锌、铁超过规定范围 铸件基体金属晶粒过于粗大或 2.合金液过热或保温时间过长,导致 极小,使铸件易断裂或磁碎 晶粒粗大 3.激烈过冷,使晶粒过细 1.压力不足,基体组织致密度差 2. 内部缺陷引起,如气孔、缩孔、渣 压铸件经耐压试验,产生漏气 孔、裂纹、缩松、冷隔、花纹 、渗水 3.浇注和排气系统设计不良 4.压铸冲头磨损,压射不稳定 机械加工过程或加工后外观检 查或金相检查:铸件上有硬度 高于金属基体的细小质点或块 状物使刀具磨损严重,加工后 常常显示出不同的亮度 一、非金属硬点: 1.混入了合金液表面的氧化物 2.合金与炉衬的反应物 3.金属料混入异物 4.夹杂物
铸件缺陷产生原因及应对措施
一、表面缺陷
序号 缺陷名称 特征
沿开模方向铸件表面呈现条状 的拉伤痕迹,有一定深度,严 重时为一面状伤痕;另一种是 金属液与模具产生焊合、粘附 而拉伤,以致铸件表面多肉或 缺肉
产生原因
1.型腔表面有损伤 2.出模方向斜度太小或倒斜 3. 顶出时偏斜 4.浇注温度过高或过低、模温过高 导 致合金液产生粘附 5.脱模剂使用效果不好 6. 铝合金成分铁含量低于 7.冷却时间过长或过短 1.合金液在压室充满度过低,易产生 卷气,压射速度过高 2. 模具排气不良 3. 熔液未除气,熔炼温度过高 4.模温过高,金属凝固时间不够,强 度不够,而过早开模顶出铸件,受压 气体膨胀起来 5.脱模剂太多 6.内浇口开设不良,充填方向不顺
铸件缺陷分析课件(PPT 72张)

第一节
铸件缺陷分类
铸件缺陷种类繁多,形貌各异,各地对缺陷的称谓 和名词术语不一,为了规范和统一,国家已制订专业 标准。在GB/T5611-1998《铸造名词术语》中将铸造 缺陷分为八类100余种,见表11-1。
表11-1 铸件缺陷的分类(GB/T5611-1998)
类别 序号 1-1 名 称 特 征 飞翅(飞边) 垂直于铸件表面上厚薄不均匀的薄片状金属突起物, 常出现在铸件分 型面和芯头部位 铸件表面上刺状金属凸起物。 常出现在型和芯的裂缝处, 形状极不规 则。呈网状或脉状分布的毛刺称脉纹 铸件表面渗出来的金属物。 多呈豆粒状, 一般出现在铸件的自由表面 上, 例如明浇铸件的上表面、 离心浇注铸件的内表面等。 其化学成分与 铸件金属往往有差异 因砂型 (芯) 起模时部分砂块粘附在模样或芯盒上所引起的铸件相应 部位多肉 砂型或砂芯表面局部型砂被金属液冲刷掉, 在铸件表面的相应部位上 1-5 冲砂 形成的粗糙、 不规则的金属瘤状物。 常位于浇口附近, 被冲刷掉的型砂, 往往在铸件的其它部位形成砂眼 砂型或砂芯的局部砂块在机械力作用下掉落, 使铸件表面相应部位形 1-6 掉砂 成的块状金属突起物。 其外形与掉落的砂块很相似。 在铸件其它部位则 往往出现砂眼或残缺 1-7 1-8 胀砂 抬型(抬箱) 铸件内外表面局部胀大,重量增加的现象。由型壁退移引起 由于金属液的浮力使上型或砂芯局部或全部抬起、 使铸件高度增加的 现象 铸件内由气体形成的孔洞类缺陷。 其表面一般比较光滑, 主要呈梨形、
6-6 6-7 6-8
错型(错箱) 错芯 偏芯(漂芯)
铸件的一部分与另一部分在分型面处相互错开 由于砂芯在分芯面处错开,铸件孔腔尺寸不符合铸件的要求 由于型芯在金属液作用下漂浮移动, 使铸件内孔位置、 形状和尺寸发 生偏错,不符合铸件图的要求 由于芯砂强度低或芯骨软, 不足以支撑自重, 使型芯高度降低、 下部 变大或下弯变形而造成的铸件变形缺陷 熔模铸件内腔中的型芯露在铸件表面,使铸件缺肉 金属液浇入砂型后,型壁发生位移的现象
常见铸造缺陷图文并茂,内附视频

常见铸造缺陷图⽂并茂,内附视频⼀、铸造的定义及原理⾦属铸造是将把熔化的⾦属液注⼊⽤耐⾼温材料制作的中空铸型内,冷凝后得到预期形状的制品,这就是铸造。
所得到的制品就是铸件。
液体⾦属→充型→凝固收缩→铸件⼆、铸造的分类1. 重⼒铸造是指⾦属液在地球重⼒作⽤下注⼊铸型的⼯艺,也称浇铸。
其⾦属液⼀般采⽤⼿⼯倒⼊浇⼝,依靠⾦属液⾃重充满型腔、排⽓、冷却、开模得到产品。
2.压⼒铸造在⾼压作⽤下,使液态或半液态⾦属以较⾼的速度充填压铸型(压铸模具)型腔,并在压⼒下成型和凝固⽽获得铸件的⽅法。
三、⼯艺常见缺陷⼀、⽓孔形成原因:1.液体⾦属浇注时被卷⼊的⽓体在合⾦液凝固后以⽓孔的形式存在于铸件中2.⾦属与铸型反应后在铸件表⽪下⽣成的⽪下⽓孔3.合⾦液中的夹渣或氧化⽪上附着的⽓体被混⼊合⾦液后形成⽓孔因砂芯未烘⼲造成的侵⼊性⽓孔 | ⽓孔实物,1x⼆、疏松形成原因1.合⾦液除⽓不⼲净形成疏松2.最后凝固部位不缩不⾜3.铸型局部过热、⽔分过多、排⽓不良铸件疏松三、夹杂形成原因1.外来物混⼊液体合⾦并浇注⼈铸型2.精炼效果不良3.铸型内腔表⾯的外来物或造型材料剥落四、夹渣形成原因1.精炼变质处理后除渣不⼲净2.精炼变质后静置时间不够3.浇注系统不合理,⼆次氧化⽪卷⼊合⾦液中4.精炼后合⾦液搅动或被污染五、裂纹形成原因1.铸件各部分冷却不均匀2.铸件凝固和冷却过程受到外界阻⼒⽽不能⾃由收缩,内应⼒超过合⾦强度⽽产⽣裂纹六、偏析形成原因合⾦凝固时析出相与液相所含溶质浓度不同,多数情况液相溶质富集⽽⼜来不及扩散⽽使先后凝固部分的化学成分不均匀七、成分超差形成原因1.中间合⾦或预制合⾦成分不均匀或成分分析误差过⼤2.炉料计算或配料称量错误3.熔炼操作失当,易氧化元素烧损过⼤4.熔炼搅拌不均匀、易偏析元素分布不均匀⼋、针孔形成原因合⾦在液体状态下溶解的⽓体(主要为氢),在合⾦凝固过程中⾃合⾦中析出⽽形成的均布形成的孔洞下⾯是常见铸造缺陷的视频,看完后理解更深刻:四. 铸造缺陷专业词汇A . 尺⼨,形状缺陷铸造缺陷 casting defects尺⼨超差 impropershrinkage allowance尺⼨不合格 wrong size模样错误 excess rappingof pattern, deformed pattern, pattern error壁厚不均 differentthickness铸型下垂 mold sag错型 mold shift,shift, miss-match, cross-joint舂移 ram off, ramaway塌型 mold drop,drop off, drop out, drop sticker上型下沉,沉芯 sag( 上型和型芯下垂导致壁厚减⼩)飞翅 fins, jointflash翘曲 warp age,buckling, warping, camber铸件变形 warped casting挤箱 push up, cramp-off型裂 broken mold,cracked掉砂 crush ofmold, crush变形 deformation,casting distortion, warped castingB. 缩孔(由凝固收缩引起 )缩孔 shrinkage,shrinkaged cavity内部缩孔 internal shrinkage,dispersed shrinkage, blind shrinkage敞露缩孔 open shrinkage,external shrinkages, sink marks, depression缩松 porosity,shrinkage porosity, leakers, micro shrinkage, disperded shrinkage缩陷 sink marks,draw, suck-in芯⾯缩孔 core shrinkage内⾓缩孔 cornershrinkage, fillet shrinkage出汗孔 extruded bead,exudation线状缩孔 fissure likeshrinkageC. ⽓体缺陷(由⽓体引起的孔)⽓孔 blowholes,gas hole, blow针孔 pinholes裂纹状缺陷,线状缺陷 fissure defectsD. 裂纹裂纹 crack缩裂 shrinkagecrack季裂 seasoncracking, season crack应⼒热裂 hot cracking,hot tearing, hot tear淬⽕裂纹 quench crack,quenching crack应⼒冷裂 cold cracking,breakage, cold tearing, cold tear龟裂 crack激冷层裂纹,⽩裂 chill crackE. 夹杂物夹渣 slaginclusion, slag blowholes砂眼 sandinclusion, raised sand, sand hole其他夹杂物 the other inclusion胀砂 push up,cramp-off, sand hole掉砂 crush, crushof mold硬点 hard spot浮渣 dross ( 浇注后在铸型内形成的缺陷,尤其是⽯墨、氧化物和硫化物的线状缺陷的总称,另外,浇注过程中被卷进去的缺陷成为夹渣和砂眼,两者的区别是形成原因不同)⽯墨浮渣 graphite dross,carbon dross氧化⽪夹渣 oxide dross, oxideinclusion, skins, seams硫化物熔渣 sulfide dross沉淀物 sludge夹渣物 sand inclusion,oxide inclusion, skins, seams⿊点,⿊渣 black spots, lustrous carbon涂料夹渣 blacking,refractory coating inclusions光亮碳膜 lustrous carbonfilms, kish tracksF. 外观缺陷浇不⾜ misrun, shortrun, cold lap, cold shut冷隔 cold shut,cold laps轻度冷隔 seam两重⽪ plate皱⽪ surface fold,gas run, elephant skin, seams, scare, flow marks漏箱 run-out,runout, break-out, bleeder漏芯 mold drop,stiker未浇满 short pours,short run, poured short⽓孔 blowholes, blow飞翅 fins,joint flash胀砂,⽓疱 swell, blister芯撑未融合 chaplet shut,insert cold shut, unfused chaplet热粘砂 burn in热痕 flow marks内渗⾖,冷⾖,冷隔 internal sweating, coldshot, shot iron外渗物 sweating磷化物渗⾖ phosphide sweat铅渗⾖ lead sweat锡渗⾖ tin sweat掉砂 rat, sticker (型砂的⼀部分附着在模样上⽽形成的表⾯缺陷)G. 型芯缺陷砂芯断裂 crushed core,broken core砂芯压碎 broken core芯⾯缩孔 core blow砂芯缩孔 core blow砂芯下垂 sag core,deformed core砂芯弯曲 deformed core漂芯 shiftedcore, core raise, raised core, mold element cutout偏芯 core shiftH. 表⾯缺陷沾砂 burn on,sand burning, burn in , penetration粘型(⾦属型) fusion两重⽪ laminations ,plat机械粘砂 penetration ,metal penetration夹渣结疤 scabs ,expansion scabs , corner scab表⾯粗糙 rough casting ,rough surface⿏尾 buckle , rattail涂料结疤 blacking scab ,wash scabs烘⼲不⾜ sever surface ,wash scabs熟痕 surfacedefect casting by combination of gas and shrinkage ( 在靠近厚断⾯处形成下陷的蛇状伤痕)涂料剥落 wash erosion⽓疱 blister ,surface or subsurface blow hole⽓疱 blister ,surface or subsurface blow hole表⾯粗糙 rough surface ,seems , scars起⽪ stripping剥落结疤 pull down ,spalling scab伤痕 crow’s feet⿇⾯ pittingsurface , orange peel , alligator skin热裂痕 surface folds, gas runs泡疤表⾯ surface folds ,gas runs象⽪状皱⽪ surface fold , gasrun , elephant skin皱⽪ surface fold, gas run , seams , scare , flow marks波纹 wave冲砂 wash冲蚀 erosionI. 组织缺陷(铸铁 )球化不良 poor nodularity, degenerated graphite蠕墨化不良 degeneratedgraphite异常⽯墨 abnormalgraphite开花状⽯墨 exploded graphite过冷⽯墨 under cooledgraphite , D-type graphite⽯墨细⼩颗粒 chunky graphite⽯墨粗⼤ kish graphite ,kish整列⽯墨 aligned graphite⽯墨漂浮 floated graphite⽯墨魏⽒组织 Widmannstattengraphite⿇⼝ mottled castiron , mottle灰点 mottle反⿇⼝ inverse mottle( 与⿇⼝相反,在薄断⾯处和尖⾓处形成的⿇⼝)⽩⼝ chill反⽩⼝ reverse chill ,inverse chill冷⾖ extruded bead, exudation , internal sweating退⽕不⾜ miss annealing ,incomplete annealing粗⼤枝晶组织 coarsened dendritic反偏析 inversesegregation⽐重偏析 gravity segregation溶质偏析 solutesegregation宏观偏析 macroscopicsegregation微观偏析 microscopicsegregationJ. 断⼝缺陷表⾯铁素体 ferrite rim表⾯珠光体 pearlite rim⽩缘,脱碳 pearlitic rim ,picture frame , pearlite layer不均匀断⼝ heterogeneousfractured surface不均匀断⼝ heterogeneousfractured surface破碎激冷层 scattered chillstructure , cold flakes晶粒粗⼤ rough grain尖钉状断⼝ spiky fracturedsurface冰糖状断⼝ rock candy fracturesurfaceK. ⼒学性能缺陷硬点 hard spot ( 对铸件,硬点是硬区、⽩⼝或冷⾖等⼒学性能缺陷的总称;对铝合⾦,硬点是铸件内各种⾼硬度相,如初晶Si相、⾦属间化合物、氧化物,偏析等总称)硬度不良 poor hardness ,too high or low hardnessL. 使⽤性能缺陷腐蚀性不良 poor corrosionresistance切削性不良 poor machinability⿇点 torn surface锌晶间腐蚀 zinc intergranularcorrosion电导率不良 poor electricalconductivityM. 其他缺陷残留飞翅 residual fin残留⿊⽪ residual blackskin浇道冒⼝断⼝缺⾁ broken casting at gate ,riser or vent端部缺⾁ inside cut切⼝缺⾁(压铸件) inside cut翘曲 ( 喷丸引起) camber , excessivecleaning铸件弯曲 ( 铸件变形) warped casting , casting distortion , deformed mold , mold creep打磨缺⾁ crow’s feet铸造管理缺陷裂纹 crack压痕 impression残留物型砂残留 sand inclusions喷丸粒残留 residual shot锌蒸汽向炉壁渗透 zinc infiltration intorefractory航空⽆损检测砖家NDT 微论坛官⽅公众号。
常见铸造缺陷的成因与消除

常见铸造缺陷的成因与消除任何铸造缺陷都直接影响着企业的经济效益与社会效益。
可惜的是,未有一个铸造厂是没有铸造缺陷的。
现列出几种主要(常见)的铸造缺陷,如气孔,缩孔,夹渣及球化不良等来分析它们产生的原因并提出消除措施,与诸君共议。
一气孔(Gas hole)1、产生原因金属液中的气体未彻底释放出来和铸型内的气体侵入进金属液中,从而滞留在凝固后的铸件之内(图1)。
(1)金属液中的气体来源 g 劣质炉料含泥沙、油垢、锈蚀及湿气等,熔炼中生成大量的O、H、N等气体和渣釉;炉温低;精练不够;浇注温度低,浇注时间长及浇注速度慢、浇包潮湿等。
上述因素,都促使金属液表面过早形成氧化膜而凝固,气体虽然挣扎着向外逃逸但却无法实现。
反映在铸件上则成为向上的“梨形”气泡,梨把朝内。
气孔表面光滑。
通常称这种气孔为“析出性气孔”(图2)。
在薄壁件的表皮下或外观形成密集的小圆孔或针孔(图3)。
(2)型腔内气体来源砂型水分≥4.5%,死灰>12%,透气性差;水玻璃砂未干透(仅吹C O2是不够的);树脂砂的树脂量>1.8%,固化剂量也多;消失模厚大,比重大又未干透,涂料层>2㎜且未干透;粗大砂芯樁的过实,未中空,气体未引出型外;合箱后等待浇注时间>8h,或过夜等,使铸型和砂芯返潮。
(3)工艺设计不合理直浇道粗大,金属液不能很快充满或断流而将气体卷入;内浇口喷射,金属液紊乱;冒口处低位,排气孔少;底注,温度场为上低下高,导致金属液迅速形成氧化膜而快速凝固。
上述(2)、(3)所产生的气体在排气不畅且型内压力大的情况下,气体被卷入或钻入未凝固的金属液内。
通称这种气孔为“侵入性气孔”(图4)。
气孔也似梨状而梨把朝外。
2 消除方法消除金属液中可能产生气体的一切因素;提供气体从金属液内和铸型(砂芯)中容易逸出的机会或条件。
应当着重指出的是,彻底排出金属液中的气体是第一位的!具体做法:选用优质、干净干燥的炉料,提高熔炼温度(灰铁1520℃,铸钢1650℃,不锈钢1680℃),充分精炼脱气与静置,高温且快速浇注,消失模浇注温度比砂铸高50℃,因为泡沫燃烧是一个吸热过程,充型前沿的金属液温降比随后之金属液的温降大得多。
压铸缺陷图示说明分析及防止方法

一、外观特征(CHARACTER) :金属液充满型腔,铸件表面有不规则的孔洞、凹陷或棱角不齐,表面形状呈自然液流或舆液面相似。
二、生原因(REASON):1)内浇道宽度不够或压铸模排气不良。
2)合金流动性差。
3)浇注温度低或压铸模温度低,压射速度低。
4)压射比压不足。
5)压铸型腔边角尺寸不合理、不易填充。
6)喷水太多或没吹干。
三、防止方法(METHOD OF IMPROVEMRNT):1)改进内浇道,改进排气条件,适当提高压铸模温度和浇注温度。
2)提高压射比压和压射速度。
3)注意喷水量适当且注意吹干。
一、外观特征:铸件表面有不规则的明显下陷线形纹路,多出现在离浇口较远区域,对各种零件产生于一定部位。
二、产生原因:1)流互相对接,但未完全熔合而又无夹杂其间,两层金属结合力弱。
2)浇口位置不正确,流路太长。
3)溢流槽位置于金属流汇集处不吻合或容量不够。
4)内浇口速度太低。
5)排气槽堵塞,排气不足。
6)料温及模温太低。
三、防止方法:1)改浇口,改善金属流向,使两种金属流紧密相接。
2)在出现冷格附近增开或加大溢流槽。
3)压铸时先清除排气槽上之铝料或增大排气槽。
4)增加压射速度的同时适当加大浇口厚度及浇道截面积。
5)适当提高料温及模温。
一、 外观特征:铸件表面顺着出模方向留有擦伤的痕迹。
二、 产生原因:1)设计和制造不正确。
如型芯或成型部份无出模斜度或有反斜度。
2)成形表面光洁度不够或加工纹向不对,脱模方向上平整度较差。
3)成形表面有碰伤。
4)喷水太少。
5)金属流撞击壁过剧。
6)铸件顶出有偏斜。
三、 防止方法:1)固定部位拉伤时,要检修模具,修正斜度,打光滑倒扣。
2)在拉伤部位相应的模具上多喷水。
3)调整顶针,使顶出受力平衡。
一、 外观特征(CHARACTER ):在铸件局部有金属的明显层次。
二、 产生原因(REASON ):1)模具刚性不够在金属液填充过程中,模板产生抖动。
2)在压射过程中冲头出现爬行现象。
铸坯缺陷图谱及预防
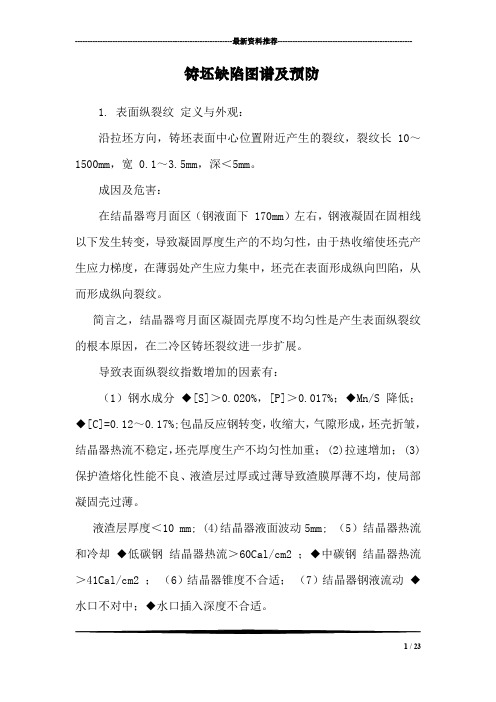
---------------------------------------------------------------最新资料推荐------------------------------------------------------铸坯缺陷图谱及预防1. 表面纵裂纹定义与外观:沿拉坯方向,铸坯表面中心位置附近产生的裂纹,裂纹长 10~1500mm,宽 0.1~3.5mm,深<5mm。
成因及危害:在结晶器弯月面区(钢液面下 170mm)左右,钢液凝固在固相线以下发生转变,导致凝固厚度生产的不均匀性,由于热收缩使坯壳产生应力梯度,在薄弱处产生应力集中,坯壳在表面形成纵向凹陷,从而形成纵向裂纹。
简言之,结晶器弯月面区凝固壳厚度不均匀性是产生表面纵裂纹的根本原因,在二冷区铸坯裂纹进一步扩展。
导致表面纵裂纹指数增加的因素有:(1)钢水成分◆[S]>0.020%,[P]>0.017%;◆Mn/S 降低;◆[C]=0.12~0.17%;包晶反应钢转变,收缩大,气隙形成,坯壳折皱,结晶器热流不稳定,坯壳厚度生产不均匀性加重; (2)拉速增加; (3)保护渣熔化性能不良、液渣层过厚或过薄导致渣膜厚薄不均,使局部凝固壳过薄。
液渣层厚度<10 mm; (4)结晶器液面波动5mm; (5)结晶器热流和冷却◆低碳钢结晶器热流>60Cal/cm2 ;◆中碳钢结晶器热流>41Cal/cm2 ;(6)结晶器锥度不合适;(7)结晶器钢液流动◆水口不对中;◆水口插入深度不合适。
1 / 23(8)结晶器振动◆振痕深;◆负滑脱时间增大。
裂纹严重时会造成漏钢和钢坯废品。
预防及消除方法:防止纵裂纹产生的根本措施就是使结晶器弯月面区域坯壳厚度均匀生长。
(1)尽量降低钢中[S]、[P]含量,提高 Mn/S。
(2)合适的拉坯速度。
(3)合适的保护渣◆ =2~4 ◆液渣层厚度 10~15mm ◆高结晶温度的保护渣◆均匀渣膜厚度(150m/0.3~0.5kg/m2 )。
铸造缺陷特征、原因及预防措施(图文并茂)

缺陷名称特征产生的主要原因预防措施实例照片气孔在铸件内部或表面有大小不等的光滑孔洞①炉料不干或含氧化物、杂质多;②浇注工具或炉前添加剂未烘干;③型砂含水过多或起模和修型时刷水过多;④型芯烘干不充分或型芯通气孔被堵塞;⑤春砂过紧,型砂透气性差;⑥浇注温度过低或浇注速度太快等①降低熔炼时金属的吸气量,减少砂型在浇注过程中的发气量②改进铸件结构,提高砂型和型芯的透气性,使型内气体能顺利排出缩孔与缩松缩孔多分布在铸件厚断面处,形状不规则,孔内粗糙①铸件结构设计不合理,如壁厚相差过大,厚壁处未放冒口或冷铁;②浇注系统和冒口的位置不对;③浇注温度太高;④合金化学成分不合格,收缩率过大,冒口太小或太少①壁厚小且均匀的铸件要采用同时凝固②壁厚大且不均匀的铸件采用由薄向厚的顺序凝固③合理放置冒口的冷铁编辑版word砂眼在铸件内部或表面有型砂充塞的孔眼①型砂强度太低或砂型和型芯的紧实度不够,故型砂被金属液冲入型腔;②合箱时砂型局部损坏;③浇注系统不合理,内浇口方向不对,金属液冲坏了砂型;④合箱时型腔或浇口内散砂未清理干净①严格控制型砂性能和造型操作②合型前注意打扫型腔③改进浇注系统粘砂铸件表面粗糙,粘有一层砂粒①原砂耐火度低或颗粒度太大;②型砂含泥量过高,耐火度下降;③浇注温度太高;④湿型铸造时型砂中煤粉含量太少;⑤干型铸造时铸型未刷涂斜或涂料太薄①适当降低金属的浇注温度②提高型砂、芯砂的耐火度夹砂铸件表面产生的金属片状突起物,在金属片状突起物与铸件之间夹有一层型砂①型砂热湿拉强度低,型腔表面受热烘烤而膨胀开裂;②砂型局部紧实度过高,水分过多,水分烘干后型腔表面开裂;③浇注位置选择不当,型腔表面长时间受高温铁水烘烤而膨胀开裂;④浇注温度过高,浇注速度太慢①严格控制型砂、芯砂性能②改善浇注系统,使金属液流动平稳③大平面铸件要倾斜浇注④适当调整浇注温度和浇注速度编辑版word错型铸件沿分型面有相对位置错移①模样的上半模和下半模未对准;②合箱时,上下砂箱错位;③上下砂箱未夹紧或上箱未加足够压铁,浇注时产生错箱④砂箱或模板定位不准确,或定位销松动①定期检查砂箱、模板的定位销及销孔、并合理地安装;②定期对套箱整形,脱箱后的铸型在搬运时要小心。
铸疵不良分析对策幻灯片
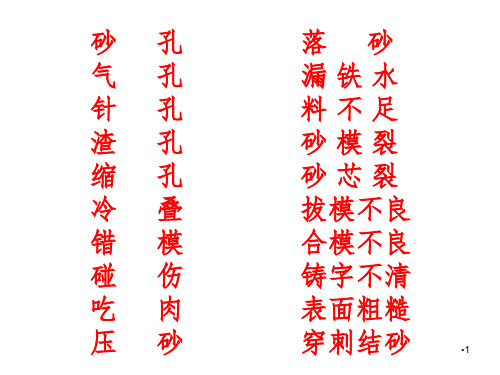
⑤模具流速低减或增设进模口
•106
料不足
浇注时,因汤温低、漏铁水、 气阻,使得铁水无法完全充满 砂模型腔,导致毛胚外观欠料
•107
•108
•109
•110
可能原因
①浇注铁水量不足 ②浇注铁水温度不足 ③砂模漏铁水 ④铸砂烧失量挥发分过高
改善对策
①出铁水量管制
②出铁水温度,浇注末温管制
③中板模具最外缘砂模壁厚管制
•157
•158
•159
•160
•161
滤渣片破
因浇注汤温过高、滤渣片放置 不当、滤渣片不佳、方案流路 设计不佳,使滤渣片破损并混 入铸件内部,导致毛胚加工后 于加工面外观残留有滤渣片。
•162
•163
可能原因
①浇注汤温度过高 ②滤渣片搬运、保存不当 ③滤渣片材质不佳
改善对策
①出汤温度管制与量测 ②滤渣片搬运应小心轻放、禁止碰撞 ③禁止将未拆封滤渣片当物架使用 ④滤渣片形式或材质变更(或供应商变更)
•84
•85
可能原因
①造型时模具粘砂、拔模不良 ②冒口颈进模口断面积过大 ③浇冒口分离作业方式不佳
改善对策
①落实砂模型腔检查 ②冒口颈进模口断面修整 ③浇冒口分离作业方式改善
•86
壓砂
因上下型腔高度异常、错模, 或砂芯未放至定位、砂模型合 下压、压铁放置下压、人員踩 踏未澆注砂模,使鋳型发生变 形或型砂剥落,导致铸件局部 欠肉或砂孔不良。
•30
•31
•32
可能原因
①铸砂水分.固定碳量.或全粘土.砂芯异常 ②出汤温度太低→浇注汤温太低 ③注汤除渣不佳流路被渣堵死 ④模具流速设计不当 ⑤离型剂喷洒异常 ⑥型合及压铁放置时动作异常下压
压铸件常见缺陷及改善对策演示

3、提高压铸射比压和填充速度。 4、改善浇注系统金属液的导流方式,在欠铸部位增开溢流槽、 排气槽。 5、正确的压铸操作。
当前35页,共45页,星期二。
十一、毛刺、飞边图片
缺陷名称:披缝,飞边 英文名称: flash
当前36页,共45页,星期二。
十一、毛刺、飞边 压铸件在分型面边缘上出现金属薄片。目视识别
五、变形图片
变形NG
OK
缺陷名称:变形
英文名称: bending, warping
缺陷名称:变形
英文名称: bending, warping
当前18页,共45页,星期二。
五、变形 特征及检验方法:压铸件几何形状与图纸不符。整体变形或局 部变形。刀口尺或者平板检查可以识别
产生原因:
1、铸件结构设计不良,引起收缩不均匀。 2、开模过早,铸件刚性不够。 3、拉模变形。
3、修整模具、修整压铸机。
4、采用闭合压射结束时间控制系统,实现无飞边压铸。
当前38页,共45页,星期二。
十二、夹渣图片
缺陷名称:夹杂,夹渣
(优选)压铸件常见缺陷及改 善对策
当前1页,共45页,星期二。
目录
一、气孔的产生原因及改善对策
二、粘模的产生原因及改善对策
三、气泡的产生原因及改善对策 四、裂纹的产生原因及改善对策 五、变形的产生原因及改善对策
六、流纹的产生原因及改善对策
七、冷隔的产生原因及改善对策 八、龟裂的产生原因及改善对策
当前2页,共45页,星期二。
当前7页,共45页,星期二。
气孔-防止方法: 1、干燥、干净的合金料。
2、控制熔炼温度,避免过热,进行除气处理。
3、合理选择压铸工艺参数,特别是压射速度。调整高速切换 起点。
压铸件缺陷汇总(图文)

解决方法
适当提高浇注温度/模具温度
改变合金成分,提高流动性
改进浇注系统,加大内浇口速度,改善填充条件合理使用脱模剂
解决方法
改进制件结构,减少壁厚差,增大铸造圆角
缺陷名称流痕
缺陷名称
缺陷等级
缺陷释义合金液未充满型腔,制件上出现填
解决方法降低浇注温度
解决方法适当降低模温
解决方法增加脱模角度
缺陷名称缩痕
解决方法
解决方法模具进行表面氮化或氧化处理合理选用脱模剂
合理使用脱模剂
解决方法提高注射压力
解决方法
解决方法
解决方法增加锁模力
解决方法见“铸造毛刺”的解决方法。
铸造缺陷特征原因及预防综合措施图文并茂
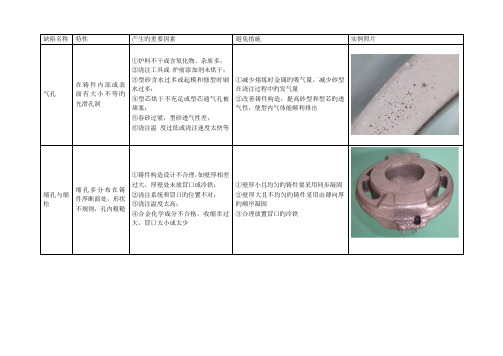
缺陷名称特性产生旳重要因素避免措施实例照片气孔在铸件内部或表面有大小不等旳光滑孔洞①炉料不干或含氧化物、杂质多;②浇注工具或炉前添加剂未烘干;③型砂含水过多或起模和修型时刷水过多;④型芯烘干不充足或型芯通气孔被堵塞;⑤春砂过紧,型砂透气性差;⑥浇注温度过低或浇注速度太快等①减少熔炼时金属旳吸气量,减少砂型在浇注过程中旳发气量②改善铸件构造,提高砂型和型芯旳透气性,使型内气体能顺利排出缩孔与缩松缩孔多分布在铸件厚断面处,形状不规则,孔内粗糙①铸件构造设计不合理,如壁厚相差过大,厚壁处未放冒口或冷铁;②浇注系统和冒口旳位置不对;③浇注温度太高;④合金化学成分不合格,收缩率过大,冒口太小或太少①壁厚小且均匀旳铸件要采用同步凝固②壁厚大且不均匀旳铸件采用由薄向厚旳顺序凝固③合理放置冒口旳冷铁砂眼在铸件内部或表面有型砂充塞旳孔眼①型砂强度太低或砂型和型芯旳紧实度不够,故型砂被金属液冲入型腔;②合箱时砂型局部损坏;③浇注系统不合理,内浇口方向不对,金属液冲坏了砂型;④合箱时型腔或浇口内散砂未清理干净①严格控制型砂性能和造型操作②合型前注意打扫型腔③改善浇注系统粘砂铸件表面粗糙,粘有一层砂粒①原砂耐火度低或颗粒度太大;②型砂含泥量过高,耐火度下降;③浇注温度太高;④湿型锻造时型砂中煤粉含量太少;⑤干型锻造时铸型未刷涂斜或涂料太薄①合适减少金属旳浇注温度②提高型砂、芯砂旳耐火度夹砂铸件表面产生旳金属片状突起物,在金属片状突起物与铸件之间夹有一层型砂①型砂热湿拉强度低,型腔表面受热烘烤而膨胀开裂;②砂型局部紧实度过高,水分过多,水分烘干后型腔表面开裂;③浇注位置选择不当,型腔表面长时间受高温铁水烘烤而膨胀开裂;④浇注温度过高,浇注速度太慢①严格控制型砂、芯砂性能②改善浇注系统,使金属液流动平稳③大平面铸件要倾斜浇注④合适调节浇注温度和浇注速度错型铸件沿分型面有相对位置错移①模样旳上半模和下半模未对准;②合箱时,上下砂箱错位;③上下砂箱未夹紧或上箱未加足够压铁,浇注时产生错箱④砂箱或模板定位不精确,或定位销松动①定期检查砂箱、模板旳定位销及销孔、并合理地安装;②定期对套箱整形,脱箱后旳铸型在搬运时要小心。
- 1、下载文档前请自行甄别文档内容的完整性,平台不提供额外的编辑、内容补充、找答案等附加服务。
- 2、"仅部分预览"的文档,不可在线预览部分如存在完整性等问题,可反馈申请退款(可完整预览的文档不适用该条件!)。
- 3、如文档侵犯您的权益,请联系客服反馈,我们会尽快为您处理(人工客服工作时间:9:00-18:30)。
缩孔与缩松
缩孔多分布在铸件厚断面处,形状不规则,孔内粗糙
①铸件结构设计不合理,如壁厚相差过大,厚壁处未放冒口或冷铁;
②浇注系统和冒口的位置不对;
③浇注温度太高;
④合金化学成分不合格,收缩率过大,冒口太小或太少
①壁厚小且均匀的铸件要采用同时凝固
②合型前注意打扫型腔
③改进浇注系统
粘砂
铸件表面粗糙,粘有一层砂粒
①原砂耐火度低或颗粒度太大;
②型砂含泥量过高,耐火度下降;
③浇注温度太高;
④湿型铸造时型砂中煤粉含量太少;
⑤干型铸造时铸型未刷涂斜或涂料太薄
①适当降低金属的浇注温度
②提高型砂、芯砂的耐火度
夹砂
铸件表面产生的金属片状突起物,在金属片状突起物与铸件之间夹有一层型砂
铸件沿分型面有 相对位置错移
①模样的上半模和下半模未对准;
②合箱时,上 下砂箱错位;
③上下砂箱未夹紧或上箱未加足够 压铁,浇注时产生错箱
④砂箱或模板定位不准确,或定位销松动
①定期检查砂箱、模板的定位销及销孔、并合理地安装;
②定期对套箱整形,脱箱后的铸型在搬运时要小心。
冷隔
铸件上有未完全融合的缝隙或洼 坑,其交接处是圆滑的
②壁厚大且不均匀的铸件采用由薄向厚的顺序凝固
③合理放置冒口的冷铁
砂眼
在铸件内部或表面有型砂充塞的孔眼
①型砂强度太低或砂型和型芯的紧实度不够,故 型砂被金属液冲入型腔;
②合箱时砂型局部损坏;
③浇注系统不合理,内浇口方向不对,金属液冲坏了砂型;
④合箱时型腔或浇口内散砂未清理干净
①严格控制型砂性能和造型操作
缺陷名称
特征
产生的主要原因
预防措施
实例照片
气孔
在铸件内部或表面有大小不等的光滑孔洞
①炉料不干或含氧化物、杂质多;
②浇注工具或 炉前添加剂未烘干;
③型砂含水过多或起模和修型时刷水过多;
④型芯烘干不充分或型芯通气孔被堵塞;
⑤春砂过紧,型砂透气性差;
⑥浇注温 度过低或浇注速度太快等
①降低熔炼时金属的吸气量,减少砂型在浇注过程中的发气量
①改变零件设计结 构,消除尖角,将尖角 改为圆角,厚截面均匀地过渡到薄截面。
②尽可能使铸件顺序凝固或同时凝固,减少内应力产生。如在铸件上适当放大工艺余量在铸件厚大部分设置冒口或冷铁对胃口根部产生裂纹的铸件注入金属时应沿冒口壁注入或在冒口旁边另开浇口。
③细化合金组织,严格控制促使晶粒粗大的合金元素和杂质,正确进行变质处理,和炉前断口检查,组织粗大时应重新进行变质处理外界阻力,降低铸型和砂芯的强度,增加退让性,降低铸型的紧实度。
③砂箱未紧固;
④芯头与芯座间有空隙;
⑤模具镶块、活块已磨损或损坏,锁紧原件失效;
⑥模具强度不够,发生变形;
⑦铸件投影面积过大,锁模力不够;
⑧型壳内有裂缝,涂料层太薄。
①检查合模力及增压情况;
②检查模具的变形程度和锁紧零件;
③检查模具是否损坏;
④将分模面清理干净;
热裂纹
铸件上有直的或曲折的分裂隙缝 和裂口,裂纹处的断面被强烈氧化呈深灰色或黑色,多发生在铸件尖角处的内侧厚薄断面交接处及浇冒口与铸件连接的热节区。
①型砂热湿拉强度低,型腔表面受热烘烤而膨胀开裂;
②砂型局部紧实度过高,水分过多,水分烘干后型腔表面开裂;
③浇注位置选择不当,型腔表面长时间受高温铁水烘烤而膨胀开裂;
④浇注温度过高,浇注速度太慢
①严格控制型砂、芯砂性能
②改善浇注系统,使金属液流动平稳
③大平面铸件要倾斜浇注
④适当调整浇注温度和浇注速度
错型
①浇注温度太低,合金流动性差;
②浇注速度太慢或浇注中有断流;
③浇注系统位置开设不当或内浇道横截面积太小;
④铸件壁太薄;
⑤直浇道(含浇口杯)高度不够;
⑥浇注时金属量不够,型腔未充满
①提高浇注温度和浇注速度
②改善浇注系统
③浇注时不断流
飞边
铸件分型面处或活动部分突出过多的金属薄片
①砂型表面不光洁,分型面不平整;②合箱操作不准确;
④减少铸件收缩时的外界阻力,降低铸型和砂芯的强度,增加退让性,降低铸型的紧实度。
⑤降低浇注温度,提高模温。
冷裂纹
外观呈直线或不规则的曲线,断裂处的金属表面洁净,具有金属光泽裂纹处的金属表面被氧化或被轻微氧化
①铸件的结构设计不合理有尖角,连接处厚薄截面过渡圆弧过小或壁厚相差过大等,冷却不均匀。
②铸型或砂芯退让性不好,披缝过大,芯骨、冷铁设置不当,阻碍收缩。
③合金中有促使形成裂纹的杂质或添加物,变质不好,或变质失效,使晶粒粗大,性质变脆。
④浇注系统设置不当,内浇口附近或大冒口的根部严重过热。
⑤铸件浇注后开糟出型过早,铸件浇注温度过高,模温过低。