过程审核提问评分表
审核提问表

6.1.5
是否对量产过程中的产品或者过程变更开展了跟踪和记录? * 关注以下要求:
BIQS-12 变更管理
6.2 过程管理
6.2.1
控制计划的要求是否完整并得到有效落实? 关注以下要求: BIQS-5 屏蔽/偏差管理 BIQS-11 标准化作业
3.4
策划?
3.5
针对产品和过程开发,是否考虑到了必要的资源?
4
产品和过程开发的实现
产品和过程开发计划中的活动是否得到落实? 关注以下要求: 4.1 * BIQS-3 过程失效模式和后果分析 BIQS-5屏蔽/偏差管理
4.2
人力资源是否到位并且具备资质以确保批量生产启动?
4.3
物质资源是否到位并且使用,以确保批量生产启动?
效性? * BIQS-8 快速响应问题解决流程
关注以下要求:
BIQS-9 团队合作解决问题的流程
6.5.4
是否对过程和产品定期开展审核? 关注以下要求: BIQS-2 分层审核 BIQS-4 风险降低和年度回顾
6.6 过程结果(输出)
6.6.1 是否根据需要确定产量/生产批量,并且有目的地运往下道工序?
4.4 * 是否获得了针对产品和过程开发所要求的批准和放行?
4.5
是否已制定并落实了产品与过程开发的制造和检验规范?
4.6
是否在量产条件下,为量产批准进行了能力测试?
是否为确保顾客关怀/顾客满意/顾客服务和使用现场失效分析建立了过
4.7
程?
4.8 * 针对将项目从开发阶段移交至批量生产,是否已进行了规定?
过程审核提问表(VDA6.3 2016 )
审核内容
VDA6.3过程审核评分矩阵表(标准模板)

当前程度
6.1.2 E P6 #DIV/0!
6.1.3
6.1.4
6.2.4
6.2.5
6.6.1
6.6.2
6.6.3
###### ###### ###### ###### ######
###### ###### ###### ###### ###### ######
###### ###### ######
6.1.2
6.1.3
6.1.4
6.2.4
6.2.5
6.6.1
6.6.2
6.6.3
过程分析中的子要素的分析评估(1-n的平均数) 6.1.1 6.1.2
当前程度
6.1.3
目标程度
6.1.4
最高程度
6.1.5
当前程度
6.2.1
6.2.2
6.2.3
当前程度
6.2.4
目标程度
6.2.5
最高程度
6.2.6
当前程度 当前程度
n.e. 当前程度 目标程度 最高程度 当前程度
#DIV/0!
######
EPzR
######
5.2
5.3
5.4*
5.5*
5.6
5.7
n.e.
当前程度
目标程度
最高程度
当前程度
E P5
#DIV/0!
工序落实程度[%]
运输和零部件处置
E1 #DIV/0! E2 #DIV/0! E3 #DIV/0! E4 #DIV/0! E5 #DIV/0! E6 #DIV/0! E7 #DIV/0! E8 #DIV/0! E9 #DIV/0! E10 #DIV/0!
###### ###### ###### ######
制造过程审核评审提问表 模板

质量管理体系、产品和过程方面的要求是否得到满足? 是否对顾客关怀提供了必要的保障? * 是否保障了供货? * 针对投诉是否开展了失效分析,并且有效地落实了纠正措施? 针对各具体的任务,相关的人员是否具备资质,是否定义了责权关系?
n.a. 评分 n.a. n.a. n.a. n.a. n.a. n.a. n.a. 评分
必须回答问题:5,回答问题:7/7 工序1-10:100%(26/26)
6.3.3 P6.4 6.4.1 6.4.2 6.4.3 6.4.4 6.4.5 P6.5 6.5.1 6.5.2 6.5.3 6.5.4 P6.6 6.6.1 6.6.2 6.6.3 6.6.4 P7 7.1 7.2 7.3 7.4 7.5
是否具备必要的人力资源? 100% 通过哪些资源落实了过程?(物质资源)
* 使用的生产设备是否可以满足顾客对产品的特定要求? 生产设备/工具的维护保养是否受控?
* 通过使用的测量和试验设备,是否能够有效地监控质量要求? 加工工位以及检验工位是否满足具体的要求? 是否根据要求,正确的存放工具、装置和检验工具?
* 产品和过程开发是否具有所要求的认可批准?
产品
过程
4.5
是否基于产品和过程开发制定生产和检验规范并加以实施?
产品
过程
4.6
是否在量产条件下开展了效能测试,以便获得批量生产批准/放行?
过程
4.7
是否建立流程以便确保顾客关怀/顾客满意/顾客服务以及现场失效分析的实施?
过程
4.8
* 是否对项目从开发移交至批量生产开展了控制管理?
3.1
针对产品和过程的具体要求是否已明确?
VDA6.3-2016审核评分表

NO 工序6 工序7 工序8 工序9 工序10 6.3.3 工序1 工序2 工序3 工序4 工序5 工序6 工序7 工序8 工序9 工序10 P6.4 6.4.1 工序1 工序2 工序3 工序4 工序5 工序6 工序7 工序8 工序9
类别
评审提问表 工序6 工序7 工序8 工序9 工序10 是否具备必要的人力资源? 注塑 冲压 电镀 装配 包装 工序6 工序7 工序8 工序9 工序10 10 10 10 10 10 n.a. n.a. n.a. n.a. n.a. n.a. n.a. n.a. n.a. n.a.
3.3
是否具有产品和过程开发事项的详细计划? 产品 过程 n.a. n.a.
3.4
顾客关怀/顾客满意/顾客服务以及现场失效分析方面的事项是否具有相应计划? 产品 过程 n.a. n.a.
3.5
是否对产品和过程开发所需的资源进行策划? 产品 过程 100% n.a. n.a. 产品 产品和过程开发的实现 必须回答问题:4,回答问题:6/6
NO 工序2 工序3 工序4 工序5 工序6 工序7 工序8 工序9 工序10 P6.3 6.3.1 工序1 工序2 工序3 工序4 工序5 工序6 工序7 工序8 工序9 工序10 6.3.2 工序1 工序2 工序3 工序4 工序5
类别
评审提问表 冲压 电镀 装配 包装 工序6 工序7 工序8 工序9 工序10 8 8 10 10 n.a. n.a. n.a. n.a. n.a.
类别
评审提问表 工序10 是否对来料进行适当的仓储,所使用的运输工具/包装设备是否适合来料的特殊特 性? 注塑 冲压 电镀 装配 包装 工序6 工序7 工序8 工序9 工序10 必要的标识/记录/放行是否具备,并且适当地体现在来料上? 注塑 冲压 电镀 装配 包装 工序6 工序7 工序8 工序9 工序10 8 10 10 10 10 n.a. n.a. n.a. n.a. n.a. 8 10 10 10 10 n.a. n.a. n.a. n.a. n.a. n.a.
过程审核-2010 检查表-评分矩阵-中英文版

注意:当审核到自己的工作时, 审核小组内灵活调整。
审核内容(提问项目) //
CTS//(Zhongshan)Technology Co.,Ltd
CTS(Zhongshan)Technology Co.,Ltd
审核日期
2012 年 审核流程计划内容 审核日期/时间
所要审核的产品/过程 首次会议
受审部 门
ALL
审核员 ALL
审核内容(提问项目) //
CTS(Zhongshan)Technology Co.,Ltd
备注:新产品部份:应当规 划在量产前或量产时,以确认 过程是否符合需求。
既有产品部份:每年 至少应规划一次,对公司的各 项工序进行过程审核,以发现 是否有过程的缺失存在。 编制/日期:
末次会议
ALL
ALL
审核/日期:
// 批准/日期:
CTS(Zhongshan)Technology Co.,Ltd 评价。 计以外的所有的过程及工序、顾客满意度 准则(Formel Q 第五版)。
CTS(Zhongshan)Technology Co.,Ltd
过程审核计划表
审核目的
为使现行质量管理体系的质量保证能力得到巩固和提高而进行评价。
审核范围
从原材料直至交付过程中的所有的影响质量的活动。除产品设计以外的所有的过程及工序、顾
审核依据
VDA6.3过程审核标准; 德国大众汽车集团 供应商质量能力评定准则(Formel Q 第五版)。
最新VDA6.3过程审核检查表及评分标准
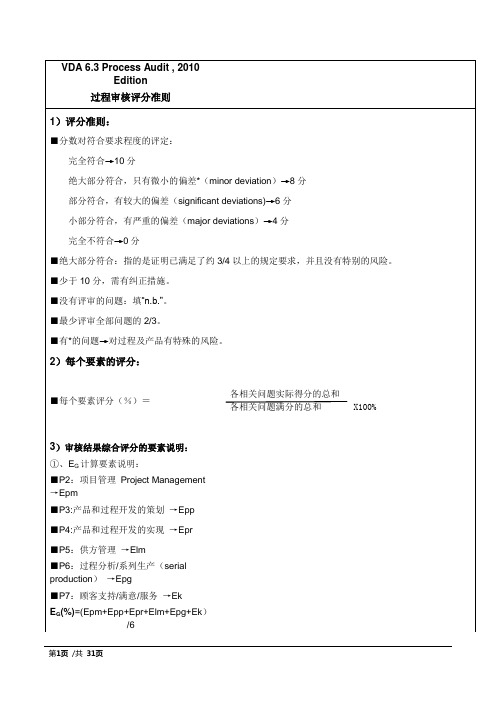
■项目计划=>关键路径则(critical path)
■质量管理计划(QM plan) :项目计划的组成部分。
P2.4
项目组织是否在项目进程中提供了可靠的变更管理?考虑要点,如:
■变更管理需要满足特定的顾客要求。
■变更的可行性检验(manufacturing feasibility check)
EG(%)=(Epm+Epp+Epr+Elm+Epg+Ek)/6
②、过程分析/管理—乌龟图(P6:生产)各要素说明:
■Eu1:输入
■Eu1:工作内容
■Eu3:支持过程
■Eu4:材料、资源
■Eu5:效率
■Eu6:输出/结果
■Eu7:零件运输(Transport/Parts Handling)
4)审核结果的综合评分Overall Assessment:
VDA 6.3 Process Audit , 2010 Ed分数对符合要求程度的评定:
完全符合→10分
绝大部分符合,只有微小的偏差*(minor deviation)→8分
部分符合,有较大的偏差(significant deviations)→6分
小部分符合,有严重的偏差(major deviations)→4分
:记录
■定义的过程[记录所有变更]
■说明变更(highlight)
■和顾客协商沟通、评价
■影响到产品质量的变更=>风险评价
■供方(关键群体)参与
■对变更停止的时间点:明确的定义、遵守
■如果不能遵守,则在顾客和供方之间必须以书面形式加以记录。
■SOP之前的变更时间段:不会影响到产品质量。
过程审核评分准则

既无规定又未执行--------扣3分
分值计算:
2*被评估项目数-总扣分数
分值(%)=×100%
2*被评估项目数
等级划分:
A级-------分值:≥90%
B级-------分值:≥80%,<90%
C级------分值:≥70%,<80%
D级------分值:<70%
目录
1、产品定义7条
2、外协件质量保证9条
3、生产管理32条
4、成品检验和试验7条
5、成品包装、储存、运输6条
过程审核评分准则
过程审核提问表
本评定标准分为五个章节共61个条款。依据企业规模或所采取的技术及所处的阶段,有些项目可不作评审,但பைடு நூலகம்求有足够的理由。本提问表采取项目扣分制,扣分原则如下:
合适--------扣0分
程序文件没规定但执行的较好--------扣1分
程序文件有规定但执行的不好但对产品质量无直接影响-------扣1分
10版vda6.3-过程审核提问表(审核案例)

x 查:检验标准并与批产控制计划比对,核对检验记录
x
x 查:首检记录、工艺参数监控记录、首件检验记录等
x
查:设备保养计划、保养记录、维修记录,关注设备精度的 确认及产能确认。
6.2.4* 是否在生产中控制住了重要特性?
x
6.2.5
是否对报废、返工和调整件进行了隔离及标 识?
xx
6.2.6
是否确保了物料/零件的流向,以防止混料/错 料的产生?
x
6.4.2*
通过使用的测试、检验和测量设备,是否能有 效地监察质量要求?
x
6.4.3 生产工位和测试/检验区域是否满足要求?
x
x
6.4.4
工装、设施和测试/禁言设备是否被正确地存 放?
x
x
6.5 过程实现的效果如何?(有效性、效率、减少浪费)
x
查:各类文件的特殊特性标识的一致性,现场检查这些特性 的符合性。
x
x
6.3 哪些功能为过程提供支持?(人力资源)
6.3.1
是否向员工授予了职责和权限,以监察产品和 过程的质量?
x
6.3.2*
员工是否适合完成下达的任务,并且其资质是 否保持更新?
x
x
6.3.3 是否有人力资源安排计划?
6.4 通过哪些资源实现了过程?(物质资源)
6.4.1 生产设施/工装的维护及保养是否受控?
x
6.5.2
对收集到的质量和过程数据是否可以进行评 审?
6.5.3*
当与产品和过程的要求有偏差时,是否进行了 原因分析,并检查了纠正措施的有效性?
x
6.5.4* 是否定期进行了过程和产品审核?
x
6.6 过程应该产出什么?(过程结果/输出)
VDA6.3-2016版-过程审核提问检查表

- 退回概念包含在产品和过程创新中。 - 为交付而策划零公里和现场追回分析过程。为失效分析考虑顾客要求。
P3.5
是否为产品和过程开 发考虑了必要的资 源?
-- 当 实介 现绍 确新 定技 资术 源和 的产 过品 程、 。员工培训和必要基础设施的建立也要提供给顾客服务。 - 资源的决定参考了人员资质、预算、如建筑物/测试设备(软件和硬件)/实验设备/机器和设备这样的 基础设施的可用性。 - 必须策划和考虑原型技术、原型制作、试生产、生产测试和连续生产的实现能力。
情况?
- 资源策划特别考虑了关键路径。
- 策划和批准了人员和设备的必要项目预算(如:测试和实验设备)。 - 项目策划满足特定的顾客要求
- 所有内部和顾客定义的里程碑完整的合并在项目策划里。
- 执行项目策划里定义的里程碑评审以检查所有执行的活动与完成成熟度的要求。
是否有项目计划,并 - 若法定授权产品的程序特殊要求,该程序持续期包含在项目策划中。 P2.3 与顾客进行了协商确 - 当项目策划变更时确保内部沟通,与顾客协调项目策划变更对顾客的影响。
P3产品和过程开发的策划- 弱国风险识别包含技术、供应商或供应国,事态升级管理中应考虑这些风险。
项目
提问概述
有关评估的最低要求
- 知道所有有关开发的产品要求。
- 对于嵌入式软件产品,定义软件和硬件之间的借口要求。为这些实施需求管理。
- 组织必须决定有必要满足顾客特殊要求的产品相关的物流要求和法律法规要求。
- 变更(由顾客、内部或客户发起)必须被评估。如需要,项目计划应进行修改。评估必须包含产品质
P2.6
项目组织是否确保了 项目中的变更管理?
量的风险评定和截至日期。 - 供方(关键供方)应积极参与变更管理。
过程审核的评分标准

0
--产品上有缺陷(不能满足功能性,产品的 --机器/设备/工装不适用,不完整或者完全没有 使用受到严重限制,顾客对其不能开展进一 到位 步的制造) --在接下来的过程/检验中不能发现缺陷,从 --涉及顾客的特性的制造不能满足过程可靠性 而也就不能加以筛选或者返工
--没有提供相关的检查,检验和测量工具,从而 对涉及顾客的特性开展监控 --零部件搬运过程中会引起涉及顾客的特性的受 --产品应用对接下来的用户而言构成一种风险 损 --企业内部或者发货过程中会导致零部件混淆, 从而影响到顾客那里的进一步制造
--没有为人员提供必要的资格培训 --于有关要求的落实情况不足,导致顾客那里 发生功能缺陷
--会出现投诉以及现场失效的情况
过程审核的评分风险评分表
评分 10 产品风险
--产品没有任何缺陷,满足技术要求 --产品上有缺陷(但不影响到功能,使用或者在 过程中的进一步制造),需要加以改进
过程风险
--满足了技术要求/产品和过程的技术规范要求 --生产流程中存在轻度的故障 --过程中存在薄弱环节,但被及时发现和排除
质量管理体系相关性
8
6
--产品上有缺陷(但不影响到功能,缺陷会导致 使用时或者在过程中的进一步制造时发生故障) --没有满足过程能力要求(特殊特性) --在接下来的过程中将对缺陷加以返工 --检验时发现缺陷,有缺要求,但特殊 特性仍满足技术规范要求 --对特殊特性没有开展系统的监控 --需要开展筛选行动 --需要开展返工 --零部件有受到损伤的风险 --整个材料流转过程中存在过程风险 --检验和测量工具不适用于发现缺陷 --员工的培训不够 --产品的生产不能满足过程可靠性的要求,特殊 特性部分超差 --对特殊特性没有开展系统的监控 --需要开展筛选行动 --需要开展返工 --零部件有受到损伤的风险 --零部件混合/错误的安装导致过程故障 --用于发现缺陷的检验和测量工具不适用 --员工一方面接受的培训不足,另一方面对故障 模式也不了解
VDA6.3-2016版-过程审核提问检查表
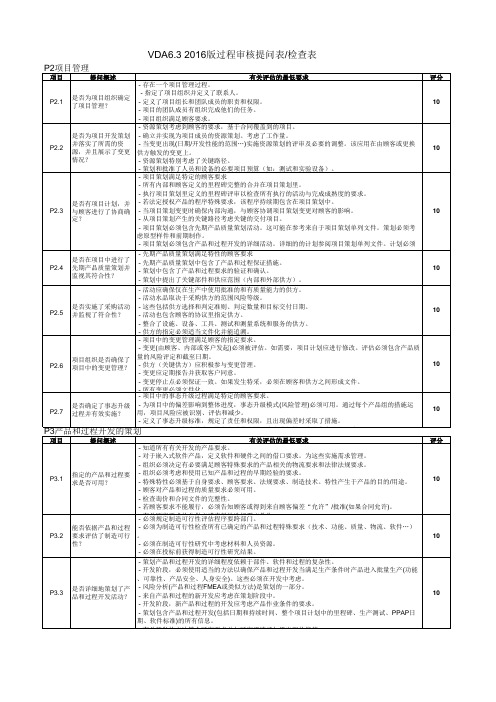
P2项目管理
项目
提问概述
有关评估的最低要求
- 存在一个项目管理过程。
P2.1
是否为项目组织确定 了项目管理?
- 指定了项目组织并定义了联系人。 - 定义了项目组长和团队成员的职责和权限。 - 项目的团队成员有组织完成他们的任务。
- 项目组织满足顾客要求。
产品控制方法是否从 P4.7 开发转移到连续生
产?
P5供方管理
项目
提问概述
P5.1
是否只使用批准和质 量能力的供方?
P5.2 P5.3 P5.4
是否在供应链内考虑 了顾客要求?
是否就供方绩效的目 标协议达成一致并落 外包产品和服务必要 的放行/批准是否可
P5.5
是否确保了外包产品工作结果的过程。 - 文件化集成软件产品开发的结果(包含中间结果和其文件)。 - 项目交付的先决条件是成功的内部PPAP过程,连续交付放行的先决条件是成功的顾客批准。及时 坨屎内部或外部产生的措施。 - 能力证明能展示所有的特殊特性。 - 按照策划,人力资源可用并有资质。 - 物质资源包含建筑物、测量装置、实验装置、设备装置等。这些资源可用并被批准。 - 采购量的释放是可用的。
系列的启动?
- 评估实现原型和样品的有资格人才资源。策划试生产、生产、启动和连续生产的人力资源并且人
员的资质与项目要求一致。
- 也 建要 立考 决虑 定被 资外 源包 的的 过过 程程 。。
- 资源的确定参考测试设备、实验室设备、机器、设备和机器和设备利用可用性。必须考虑支持过
材料资源是否可用? 程。
定?
- 从项目策划产生的关键路径考虑关键的交付项目。
- 项目策划必须包含先期产品质量策划活动。这可能在参考来自于项目策划单列文件。策划必须考
VDA 过程审核检查表及评分标准

审核结果记录
评分
第5页 共17页
序号 P4.6
审核项目/内容
是否在不同阶段应用了生产控制计划,并由此编制出了生 产、测试和检验文件?考虑要点,如: ■生产控制计划Production control plan 包括:
⊙构件 ⊙组件 ⊙部件 ⊙零件和材料 ⊙与产品相关的生产过程。 ■生产控制计划(control plan) : ⊙原型件阶段(如果顾客提出要求的话)prototype ⊙试生产阶段pilot run ⊙系列生产阶段serial production 本问题与产品开发无关!
⊙生产计划 ⊙负责生产的厂区 ■特殊特性(SCs) ⊙在FMEA中 ⊙通过措施进行了保障。 ■证明(evidence) : 措施的有效性
审核结果记录
评分
第4页 共17页
序号 P4.2
审核项目/内容
产品和过程开发计划中确定的事项是否得到了有效实现? 考虑要点,如: ■考虑产品的使用条件(English version : installation requirement) ■产品开发的方法(e.g. QFD, DOE, FMEA …) 得到了应用
⊙包括那些顾客没有明确说明的要求(例如法律法 规要求) ■考虑: ⊙经验(教训) ⊙未来的期望 ■规范: 报价审批过程 ⊙相关负责/参与的部门确认顾客要求的可行性
△采购 △开发 △生产计划 △生产 △质量管理策划 △物流... ■报价阶段: 考虑产能(capacity) ■必须考虑到来自P7“顾客支持/顾客满意度/服务”的要 求
VDA 6.3 Process Audit , 2010 Edition
过程审核检查表
序号 P2:项目 管理
P2.1
审核项目/内容
过程审核评分矩阵

EZ
93
90
8
8
8
10 10 88
8
8 10 10 8 87
8
10 10 10 8 Eu3(%) 92
8
8 10 8 Eu4(%)
8
8
.5
10 10 89
.6 .7
过程审核评分矩阵
评价的提问/满足率
WKQ-03-4-01-02
A/0
A
产品诞生过程
1 产品开发(设计)
.1 .2 .3 .4 .5 .6 .7 1、 策划 2、 落实 .1 .2 .3 .4 .5 .6 .7 1、 策划 2、 落实 .1 .2 .3 .4 .5 .6 .7 .8 .9 10 8 10 10 10 8 8 10 10 .1 .2 .3 .4 .5 .6 .7 EPE #### .1 .2 .3 .4 .5 .6 EDE #### 符合率 (%)
2 过程开发
B
Байду номын сангаас
批量生产
1 分供方 / 原材料 2 生产(评价每道工序)
人员/素质 1.1 .2 .3 .4 .5 工序1 焊接 8 8 8 10 10 生产设备/工装模具 2.1 .2 .3 .4 .5 .6 8 8 10 10 10 10 运输/搬运 3.1 .2 .3 .4 .5 10 10 10 8 8 缺陷分析/纠正措施/持续改进 4.1 .2 .3 .4 .5 .6 .7 E1 8 10 8 8 8 10 10 E2 #### E3 #### E4 E5 E6 E7 E8 E9 E10 要素B2中与质量管理体系有关的评价(工序1-n的平均值)
VDA6.3-2016版-过程审核提问表检查表
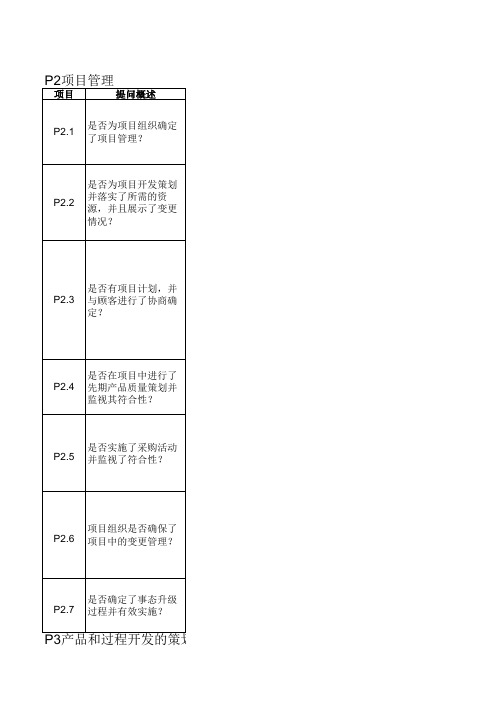
必要的标识/记录/放 P6.1.4 行是否可用并适当地 分配给了进厂材料?
是否跟踪和文件化了 P6.1.5 连续生产的产品和过 程变更?
P6.2 是否所有的生产过程都受控?(过程顺序)
控制计划的要求是否 P6.2.1 完整并有效的予以实 施?
P6.2.2
是否重复了制造过程 的放行?
P6.2.3
是否在生产中管理了 特殊特性?
P5.2 P5.3
P5.4
P5.5
外包产品和服务必要 的放行/批准是否可 用? 是否确保了外包产品 和服务的质量?
P5.6
进料是否被合适的储 存?
P5.7
各项工作的人员是否 有资格并定义了职 责?
P6生产分析过程
P6.1 什么进入过程?过程输入 项目 提问概述
项目是否从开发转移 P6.1.1 到了批量生产并保证 可靠启动? 进料需要的数量/产 品批量是否可用并在 P6.1.2 约定时间到达正确的 仓库/工作站? 进料是否适当储存且 P6.1.3 运输方式/包装装置 的方法适合于进料的 特殊特性?
P2.3
P2.4
P2.5
是否实施了采购活动 并监视了符合性?
P2.6
项目组织是否确保了 项目中的变更管理?
P2.7
是否确定了事态升级 过程并有效实施?
P3产品和过程开发的策划
项目 提问概述
P3.1
指定的产品和过程要 求是否可用?
P3.2
能否依据产品和过程 要求评估了制造可行 性? 是否详细地策划了产 品和过程开发活动? 是否为顾客支持/顾 客满意/各科服务策 划了活动?
P4.5
制造和检验规范是否 来源于产品与过程开 发并实现?
P4.6
是否在连续放行的连 续条件下执行性能测 试?
过程审核提问记录表【精选】

过程审核提问记录表要素审核提问和提问内容提问记录评分1.1是否允许已认可的且有质量能力的供方供货?公司采购是在经评审具有资格的合格分供方进行采购,包括:1.初选:在确定供方之前,必须有质量管理体系的评价结果(认证/审核)→生产件批准→合格供方名单;2.每月进行采购的业绩评定;3.检查采购合同、到货台账证明均在合格供方采购;4.检查供方供货质量台账及进货检验证明均符合要求;5.每年进行对分供方进行过程审核,促进其质量能力的提高101.2是否确保供方所供产品的质量达到供货协议要求?1.有按要求配置的实验室,并经需方认可,执行实验室控制程序;2.根据图纸/技术标准、技术质量协议、检验规程实施检测;3.材料检验执行进货检验计划,并达到质量规定要求;4.本公司与对分供方签定质量保证协议,按质量保证书中的项目由工厂进行验证检查,对工厂无法验证检查项目在检查指导书中规定委托认可试验室作验证101.3是否评价供货实物质量?与要求有偏差时是否采取措施?每批原材料进行进厂检查、判定。
采购部建立供货质量业绩档案(质量/成本/服务),每月进行的进货质量统计,业绩评定。
在绩效不佳时制订能力提高计划;出现与要求有偏差时,要求分供方立即采取改进措施,本公司再进行跟踪验证(包括改进后的实物质量的检验/测量记录)。
特殊情况停止供货、限期整改101 供方/原材料1.4是否与供方就产品与过程的持续改进商定了质量目标并付之落实?“防止缺陷、减少变差、持续改进”是公司永恒的主题,每年把原材料进货检验结果反馈给分供方并提出改进要求/目标,并落实。
813 216。
过程审核评分表

必须定义和规范质量数据和过程参数(设定值),这些数据对于证明产品一致性来说是必要的。
记录实际数据(实际值),用于展示对目标要求的符合性。
这些数据必须确保可用以评价。
对异常情况进行记录(班次日志/设备日志)。
收集的数据要与产品和过程相关,数据来源是实际的、易获取的、可查的、可存档的。
要考虑追溯性要求。
对收集的数据进行分析,并启动相应的改进措施。
潜在的改进必须根据质量、成本、服务的先前问题来持续开展。
导致过程或产品发生偏离的事件,及其相关措施,被体现在相应的风险分析(例如FMEA)当中。
●缺陷收集卡
●控制图
●特殊特性
●过程参数(温度,时间,压力...)
●生产数据采集
●故障信号(例如停线,断电,程序故障报警)●参数变化
●失效类型/失效频率
●失效成本(不符合)
●报废/返工
●隔离通知/拣选行动
●节拍时间,周期时间
●SPC●柏拉图分析
●因果图
●风险分析(FMEA、FTA…)。
过程审核检查表、计划表
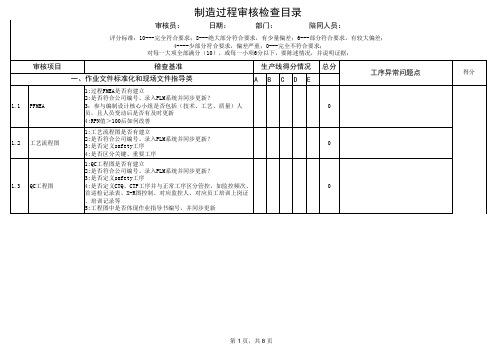
0
测量的需求
测量工具是否有合
6.2 6.3 6.4
格标识,测量工具 完好、准确? 作业员\检查员是 否按规定频率和样 本数量使用指定工 具检查? 测量记录完整,准 确、有效?
1:满足测量工具按需配置, 2:量具在制定的校检期内, 3:测试工具完好无损, 4:测试记录应保持齐全完整, 5:对于关键的控制点,按要求进行测量,并做过程能力分析控制 图
0
验证数据、不回用的处理流程节点责任人
得分
0
第 3 页,共 8 页
审核项目
制造过程审核检查目录
审核员:
日期:
部门:
陪同人员:
评分标准:10---完全符合要求;8---绝大部分符合要求,有少量偏差;6---部分符合要求,有较大偏差; 4----少部分符合要求,偏差严重;0---完全不符合要求;
对每一大项全部满分(10),或每一小项6分以下,要陈述情况,并说明证据;
三、生产设备、工装、夹具、封样件
A B C D E 总分
工序异常问题点
3.1
设备、工装定期点 检保养,检验器具 定期校验、封样件 校验记录
1:设备是否定期进行保养(记录) 2:设备是否有相关的点检保养制度,以及相关的操作流程 3:点检记录的规范以及完整性 4:工装是否定期检定,并且在有效检定期内使用 5:计量器具、封样件是否在有效期内、是否有校验记录
对每一大项全部满分(10),或每一小项6分以下,要陈述情况,并说明证据;
审核项目
稽查基准
是否有措施保证标 1:班组是否有明确的要求规定巡检频率 1.10 准化作业的执行? 2:过程巡检工作班组是否有专人执行,
(如过程监查) 3:过程检查是否按规定检查,并留有记录
过程审核提问表

过程审核提问表附录2:过程审核要素的评分标准1 提问和过程要素的单项评分对每项提问都要根据各自要求及其是否一贯符合以及过程是否可靠等情况来评分,每个问题的得分可分为:0、4、6、8、10。
符合要求的程度作为评分标准。
“绝大部分”应理解为3/4以上的规定都被证明有效且无特别风险。
计算单项评分的符合率E E的公式如下:E E=各项实得分之和×100%各项满分之和2 过程审核的总评分一个产品组的评分是由下列部分组成:a)在产品诞生过程中过程单元产品/过程开发(E DE; E PE)在产品诞生过程中,如果在批量生产中根本没有或没有类似的过程/产品。
过程单元产品/过程开发和三个在批量生产中类似的过程在产品诞生过程中,如果在批量生产中具有类似的过程/产品。
b)在批量生产中过程要素原材料/外购件(E Z),生产(E PG)和售后服务/顾客满意(E K)。
开始批量生产(SOP)后,产品诞生过程结束。
要素E DE, E PE,E Z和E K与各生产工序相反,它们是独立评分的。
在生产这个要素中,由于各个产品组的过程中的各道工序各不相同,因此,必须将每个产品组的有关工序综合起来(E PG)。
为了确保各个单元同等重要,这样做也是必要的。
因此,在生产这个大组中,对各具体的产品组来说,由于工序是选定的,故得到的符合率也不相同。
每个产品组的平均值E PG 是由以下公式算出的:E PG=∑(E1-E n)%已评分的工序数其中,E1为各产品组生产的第一道工序,E n为各产品组生产的最后一道工序。
过程审核符合率E P的总评分,在兼顾a)和b)情况下,根据以下公式计算:E P=E DE+E PE+E Z+E PG+E K×100%已评分的要素数作为评分过程单元的补充,下列重点内容,如:E S1人员/人员素质E S2设备/工位器具E S3运输/零件的搬运、放置/贮存/包装E S4缺陷分析/纠正措施/持续改进在生产单元中分开进行评价、分析并表示出来。
- 1、下载文档前请自行甄别文档内容的完整性,平台不提供额外的编辑、内容补充、找答案等附加服务。
- 2、"仅部分预览"的文档,不可在线预览部分如存在完整性等问题,可反馈申请退款(可完整预览的文档不适用该条件!)。
- 3、如文档侵犯您的权益,请联系客服反馈,我们会尽快为您处理(人工客服工作时间:9:00-18:30)。
该物料存在条件为RH≤70%,温度25±5%,改工位的管控条件为RH≤60%,温度 25±5%符合要求;运输设备与原材料的特殊特性相适应。 6月23日查看原材料外箱标识与原材料一致。
8
8
6
8
8
8
8
8
8 n.b.
6.1.5
6
6
6
6
6
6
6
6
6 n.b.
查核CP-65185253C-A0与CP-65185253C-C1(现行版本)的铝膜成型工序无差 异,未进行任何变更。
n.b. n.b. n.b. n.b. n.b.
n.b.
8 8 10 8 8 10
4.6 不能用于产品开发
DFMEA风险优先度及变更未有效进行评评审并形成记录 产品过程检测/放错及验证的落实未实现有效的策划及形成记录 没有弱点被确定 针对基础设施及资源的策划未完善,区域设备机器策划不合理 产品实验/生产测试/产能研究不完整,未能形成有效评审并记录 没有弱点被确定
4.2 4.3 4.4 4.5 x
31
4.6
32
4.7
33 34 35
4.8 4.9
是否在量产条件下开展了试生产,以便获得批量生产 n.b. 放行? 采购方面的计划任务是否得到有效的落实? n.b. 为了对正式投产提供保障,是否对项目交接进行了控 n.b. 制管理?
6 10 8
4.7不能用于产品开发
针对产品和过程是否制定了目标要求? 对收集的质量和过程数据是否可以开展评价? 一旦与产品和过程要求不符,是否对原因进行了分 析,并且检验了整改措施的有效性?
6.5.1 6.5.2 6.5.3 x
10 6 8
10 6 8
10 6 8
10 6 8
10 6 8
10 6 8
10 6 8
10 6 8
10 n.b. 6 n.b. 8 n.b.
8
8
8
10
8
8
8
8
8 n.b.
在《首检记录表FM-65185253-SOP147》中按SOP要求记录产品进行首件检验记 录及确认,在《铝膜成型检验品质记录表FM-65185253C-SIP012A0》按SIP要求 进行首检和巡检记录及确认。
53
I,
1 8 9 10
2
3
4
5
6
7
8
9
10
11
12
13
14
压延/冲 切 模切/干 燥 层叠/焊 接 铝膜/成 型 包装/打 码 注液/预 封 静置/化 成 老化/组 装 检查/出 货
42
5.7
43 44
针对各具体的任务,相关的人员是否具备资质,是否 定义了责权关系?
10
P6
6.1
过程分析 / 生产
混料/ 涂布
什么将被输入到过程中? 过程输入 / Input
查看现场工序目标为98.5%,6月23日《生产日报表》中良率为99.2%达标。 对采集数据实时记录至EV-65185253C组装品质检验记录清单中,并统计分析 CPK、PPK等指标。 查看《5月EV品质月报》,报告中的针对不良进行系统的原因分析、并制定改 善措施等
70 71 72
混料/ 涂布
压延/ 冲切
2.2 x
14
2.3
15
2.4
16
2.5 x
17
2.6
18
2.7 x
19 20 21 22
P3
3.1 3.2 x 3.3
生产和过程开发的规划
针对具体产品和过程的要求是否已经到位? n.b. 在为产品和过程确定的要求的基础上,是否从跨部门 n.b. 的可行性展开了评价? 是否为产品和过程开发编制了相关的计划? n.b. 针对产品和过程开发,是否考虑到了所需的资源? 针对采购对象,是否编制了相关的质量管理计划? n.b. n.b. 产品 过程
10 10
10 10
10 n.b. 10 n.b.
岗位说明书中明确规定员工的职责和权限,以确保监察产品和过程的质量。6 月2日,查看该工序检验员李玲有该品质检验岗位上岗证,技能级别为A,查看 该员工档案确认进行有效考核,且实际操作与SIP相符。 6月2日,查看该工序操作员陆中孟有该岗位上岗证,技能级别为B,查看该员 工档案确认进行有效考核。 依据产能要求进行人员配置,人员离职或扩产时会根据相关岗位的招聘周期提 前进行人员增补申请,并保证有效的培训,保障人力资源。
每年至少进行1次年度过程和产品审核
6
6
6
6
6
6
6
6
6 n.b.
顾客无特定要求,产品和过程满足产品设计要求。
50 混料/ 涂布 压延/ 冲切 模切/ 干燥 层叠/ 焊接 铝膜/ 成型 包装/ 打码 注液/ 预封 静置/ 化成 老化/ 组装 51 检查/ 出货
6.2 6.2.1 x
工作内容 / 流程 (所有的生产过程是否被规范?)
在生产控制计划表的基础上,是否在具体的生产和检 验文件中完整的给出了所有相关重要的信息?
64 65 66
6.4.3 6.4.4 6.5
8 8 混料/ 涂布Biblioteka 8 8压延/冲 切
8 8
模切/干 燥
8 8
层叠/焊 接
8 8
铝膜/成 型
8 8
包装/打 码
8 8
注液/预 封
8 8
静置/化 成
8 n.b. 8 n.b.
老化/组 装 检查/出 货
67 68 69
如何有效的落实过程? 效果?效率?以及集成的避 免浪费措施)
23 24 25 26
3.4 3.5
P4
4.1
27 28 29 30
生产和过程开发的实施
是否编制了产品-FMEA/过程-FMEA,并在项目进行 过程中进行了更新,同时确定了整改措施? 产品和过程开发计划中确定的事项是否得到落实? 人力资源是否到位并且具备资质? 基础实施(产品的和过程的)是否落实并且是适用 的? 针对各个具体的阶段,是否在要求的基础上取得了必 要的能力证明以及批准? 是否针对各个具体的阶段应用了生产控制计划,是否 在这些计划的基础上编制了具体的生产和检验文件?
得分 编号 问题 存在的弱点/建议的措施, 论断
11
6.2.3 x
使用的生产设备是否可以满足客户对具体产品提出的 要求?
8
8
8
8
6
8
8
8
8 n.b.
顾客无特定要求,所使用的生产设施满足产品设计要求。
54 55 56
6.2.4 x 6.2.5 6.2.6
57 58
在生产环节是否对特殊的特性进行了控制管理? 对于报废零部件、返工零部件以及设置用零部件,是 否单独放置并且相应加以了标记? 是否采取了措施,防止在材料/零部件流转的过程 中,发生混合/搞错的情况? 混料/ 涂布
61
混料/ 涂布
压延/ 冲切
模切/ 干燥
层叠/ 焊接
铝膜/ 成型
包装/ 打码
注液/ 预封
静置/ 化成
老化/ 组装
62 63
6.4 6.4.1 6.4.2 x
物质资源
生产设备/工具的维护及保养是否受控? 通过使用的测量和检验装置,是否能够有效地监控质 量要求? 加工工位以及检验工位是否满足具体的要求? 是否根据要求,正确的存放工具,装置和检验工具?
8 8 8
8 8 8
压延/ 冲切
8 8 8
模切/ 干燥
8 8 8
层叠/ 焊接
8 8 8
铝膜/ 成型
8 8 8
包装/ 打码
8 8 8
注液/ 预封
8 8 8
静置/ 化成
8 n.b. 8 n.b. 8 n.b.
老化/ 组装 检查/ 出货
查核CP,该工序重要特性为铝膜成型深度,针对该特性进行SPC管控。 现场对产品进行状态标识,合格品、不合格品、报废品等,但未进行区域隔离 。 《现品票》明确标识产品数量、状态、型号信息以及检验结果。
6
6
6
6
6
6
6
6
6 n.b.
《65185253C铝膜成型作业指导书SOP-EV-65185253C-0190》相关参数以及《 65185253C铝膜成型检验指导书SIP-EV-65185C-011》相关标准与控制计划一 致,并罗列齐全。
52
6.2.2
对生产工艺流程是否进行了放行,并且对设置数据进 行了采集?
6.3 6.3.1
过程支持 / 人力资源
在监控产品/过程质量方面,是否将相关的责权和权 限委托给了员工? 员工是否有适合完成委托的任务,其资质是否始终保 持? 是否编制了员工上岗计划
8
8
8
8
8
8
8
8
8 n.b.
59 60
6.3.2 x 6.3.3
10 10
10 10
10 10
10 10
10 10
10 10
是否在研发和批量生产之间进行了项目交接? 在约定的时间,所需数量/生产订单的原材料是否能 够被送至指定的仓库/工位?
45 46
6.1.1 x 6.1.2
8 6
8 8
8 8
8 8
8 8
8 8
8 8
8 8
8 n.b. 该项目为65185253C-5P9S,查核项目资料,阶段2至阶段3资料齐全 10 查看铝塑膜放置区域明确标识,原材料外箱标签中明确标识材料的数量、批次 6 已经检验状态。
1 1 2 3 4 5 6 7 8 9 10
2
3
4
5
6
7
8
9