客户抱怨8D处理报告表
8D报告实例样板(铁壳变形)

Report No:Product Name : (品名)S1206R-B01Sell Qty : (销货数量)pcs 客诉单号客户Sample Qty : (抽样数量)统计中Failure Rate :统计中Shipping No. : (销货单号)异常发生处 :Shipping Date: (销货日期)处理时效客诉日期Date receive by EL:4D回覆日期4D sent out:8D回覆日期8D sent out:第一次修改1st revised:第二次修改2st revised:结束日期Closed bycustomer2019/11/82019/11/82019/11/8Defect Domain:Convenor(召集人):Team Members:小组成员DefectDomain:2019/11/8Completion Date:superintendent2019/11/8D4 DIAGNOSE ROOTCAUSE(S):真因分析Completion Date:superintende ntCompletion Date:superintendentCompletion Date:superintendent2019/11/8Completion Date:superintendent2019/11/82019/11/82019/11/81.现我司针对此USB铁壳变形异常,对制程作业人员进行培训教育,要求后续生产过程中,如有产品落地立即拣起,并对拣此产品以标准母座进行测试,预防此变形异常再次发生。
2.流出原因:现已经将客户的最新判断标准纳入制程管控,并将此次客户抱怨外观异常,在早会时对作业员/检验员进行进行倡导,预防再次流出(现已完成)。
Closed by:Date closed:1.对不良测量数据及实物进行分析,确认为五金壳轻微变形造成.2.现针对此款,我司制程评估分析确认为,因生产作业过程中,部分产品落地导致碰压到造成此变形异常。
客诉根因解决之8D报告

8D中的误区
缺乏意识,未有效固化经验。 真正能从系统的角度去考虑和预防问题的发生,总结经验教训,固化经验,
而不是流于形式。
感谢您的聆听
1.8D的基本概念 2.8D的开展步骤 3. 8D的应用误区
8D中的误区
公司任何质量异常均用8D方法予以解决。使得8D在公司上下成为一种形式 对于复杂的、影响严重的问题,才使用8D的方法解决,如:客户投诉、内部
批量质量问题、停线问题等
指定一个人完成一项8D任务 8D是以团队为导向的问题解决方法,即依靠跨部门的横向功能小组来解决问
为了避免此问题或类似问题发生,修改管理系统、实务及流程等标准 (未发生的不发生)
怎么才算合格的8D
通过确认8D报告来决定这些问题是否已经回答:
①对零件的知识进行了充分论证 ②完全确认了根本原因并聚焦于原因 ③遗漏点已经被识别 ④确定与根本相匹配的纠正措施 ⑤纠正措施计划的验证已经被确认(包括了实施纠正措施的时间计划) ⑥有证据显示供方将把纠正措施纳入整个系统
8D报告
8D report
1.8D的基本概念 2.8D的开展步骤 3. 8D的应用误区
什么是8D
8D的原名叫做 8 Disciplines,又称团队导向问题解决方 法、8D问题求解法(8D Problem Solving)是福特公司处理 问题的一种方法,亦适用于制程能力指数低於其应有值时有关问 题的解决,它提供了一套符合逻辑的解决问题的方法,同时对於统 计制程管制与实际的品质提升架起了一座桥梁。现在8D已经成 为许多大公司用这个方便而有效的方法解决品质问题。目前, 8D已经成为一个固定而有共识的标准化问题解决步骤。
为什么推行8D
确定根本问题
认清根本原因
消除根本原因
异常处理单(8D报告)

曹翊
2016/11/11
8-D 效果追踪(Effectiveness Verification)
负责人
日期 (Due Date)
后续交货跟踪情况Impoved shipments follow up
第一批
1st
第二批
第三批
shipment
2nd shipment
3rd shipment
抱怨改善状况Effect of improvement
核准 (Approved by):
黄庆
2-D 相关责任单位(Relative Dept) :
审核 (Reviewed by):
毕永强
承办 (Prepared
by):
禹明超
制造部、品质部
3-D 原因分析( Root Cause)
1,外观不良:①,外观出现压伤、变形、缺料、裂痕、脏污、批锋不良,产品在成型过程中由 于作业不规范,对产品外观及环境不够重视,致使不良品流入。②孔径异常,产品在成型过程中 由于模具磨损致使孔径出现披锋,作业员没能及时反馈,造成不良品流入。 2,检测:品质部在检验过程中未按正常检验标准进行作业,致使不良流入。
调查(Prepared by): 禹明超
以永久对策平行展开到贵司所有产品,把永久对策以文件形式规定下来,便于后续产品的质量管 控
毕永强
2016/11/11
7-D 标准修订(Standard recension) 对作业指导书HSM-SOP-0001~0030文件进行修订,让作业程序更详细化
责任人
日期
(Followed by) (Due Date)
异常时积极和客户勾通,不可擅自决定,未经客人同意的异常产品不可出货。
8D报告(样本)
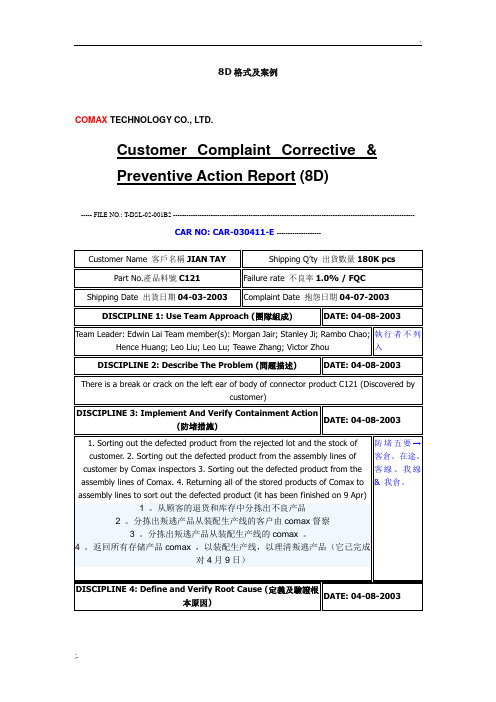
Shipping Q’ty出貨數量180K pcs
Part No.產品料號C121
Failure rate不良率1.0% / FQC
Shipping Date出貨日期04-03-2003
Complaint Date抱怨日期04-07-2003
DISCIPLINE 1: Use Team Approach (團隊組成)
DATE: 04-08-2003
Team Leader: Edwin Lai Team member(s): Morgan Jair; Stanley Ji; Rambo Chao; Hence Huang; Leo Liu; Leo Lu; Teawe Zhang; Victor Zhou
執行者不列入
DISCIPLINE 3: Implement And Verify Containment Action (防堵措施)
DATE: 04-08-2003
1. Sorting out the defected product from the rejected lot and the stock of customer. 2. Sorting out the defected product from the assembly lines of customer by Comax inspectors 3. Sorting out the defected product from the assembly lines of Comax. 4. Returning all of the stored products of Comax to assembly lines to sort out the defected product (it has been finished on 9 Apr)
8D报告(中英文)

Team Member/小组成员:
Approvl/核准:
Root Cause/根本原因:(description of technical or logistical background/技术或内在联系)
Analysis/分析:Approvl/核准:
Containment Action(s)/补救措施:
Define Problem/问题描述:(all relevant data like failure description, failure rate, line or incoming failure - filled-in by customer)
(所有相关数据比如缺陷描述,缺陷比率,在线或进料缺陷-客户提供)
公司LOGO
公司英文名称
公司中文名称
Date/日期:
Complaint No./客诉编号:
8D Report(Customer Complaint)/ 8D报告(客户抱怨)
Company/公司:Linkman/联系人:
Model Name/机型名称:Complaint Date/抱怨日期:
Purchase Order No./定单号:Delivery ./出货日期:
Fill in/填写:Approvl/核准:Send/发送:
Corrective Action/纠正措施:(short-term and mid-term actions/短期及中期预防措施)
Fill in/填写:Approvl/核准:Send/发送:
Verify Corrective Actions/确认纠正措施:(indication that corrective actions are covering the defined problem/
8D报告模板

作业指导书
检验指导书
控制计划
图纸
过程FMEA
Claim qualified (Yes / No): __所有因延迟罚款无须通知厂家,直接在货款里扣除_____
8D-Report
零件号 零件名称
重要等级
客户/供应商
厂商批号:
抱怨号:
Date: 送货批号
导致结果
要求回复日期
抱怨来源 (生产 /进料 ):
造成不良的责任者:
责任方:
生产投入日期
1.供应商分析小组名单:
问题描述: 3. 应急对策:
Date
L&V采取对策:
行动内容 Name Date
是否退货 (Yes/No): 确认结果 日期
此项请在收到FAX后24小时内回复,否则将以延迟一天按RMB100.00元罚款,格式不够时,可以附加页说明 4. 根本原因分析:
5. 采取纠正对策:
Date
Action
Name
date
确认结果
日期
6. 恒久对策(防止再发生对策):
7. 恒久对策(防止再流出对策): 8. 预防措施(相同产品的对策开展): 此5项请在收到FAX后一周内回复,否则将以延迟一天按RMB200.00元罚款,格式不够时可以附加页作出说明.
8D报告以和案例分析

字模冲子修模时 未依图面配置
跳屑造成迭料
模具
字模高度设计 安全系数尺寸 偏低
字模磨损
材料
材料厚度 0.3±0.01
三. 临时对策:
3.1.对嫌疑品全部重工
在途物流 厂内
sorting日期 11/23 11/24 11/24
不良率 52/18,000= 0.28% 40/9,000= 0.44% 22/61,300 =0.03%
D2: 问题描述
• 从客户观点来描述问题,他们看到什么? 照片or 寄 不良样品回来分析 .
• 阐明全部客户提供之数据. • 涵盖范围 ? Lot No?批号?Date Code?制造日期? • 问题有多严重 ? 不良数?不良率? • 是制造还是设计旳问题 ? 层别法 - 模号? • 阐明规格之要求. • 阐明电子,机械验证,及任何失效分析之成果. • 所报告旳问题是真正旳问题吗?连续问5次为何. 重工, 全检 ,报废 .若要 重工或全检 , 有执行旳原则吗 ?
• 详述检验措施, 措施可行吗?有作有效性验 证吗?
• 紧急对策引起其他问题吗?
• 紧急对策进行中?已完毕? 注意时效.
• 检验/测试/分析成果阐明. 详列检验数,不良 数,不良率.
D4:原因分析
• 详列永久对策旳运营时间表.
D6:效果验证
• 验证紧急对策及永久对策之有效性,应以 量化表达验证成果(如:Cpk值可达1.33, 或不良发生率降至 0 等).
• 在永久对策验证有效之前,应连续进行紧 急对策.
• 追踪永久对策执行后之品质推移情况. • 在没有完全把握问题已彻底处理之前 , 不
要轻率旳结案 .
不良品生产日期
11/4 11/7 11/19,11/20
8D回复详细报告

8D回复详细报告D1-第一步骤:建立解决问题小组----由品质部召集相关人员若问题无法独立解决,通知你认为有关的人员组成团队。
团队的成员必需有能力执行,例如调整机器或懂得改变制程条件,或能指挥作筛选等。
备注:执行者不列入。
D2-第二步骤:描述问题----由品质部收集,并向小组人员传达向团队说明何时、何地、发生了什么事、严重程度、目前状态、如何紧急处理、以及展示照片和收集到的证物。
想象你是FBI 的办案人员,将证物、细节描述越清楚,团队解决问题将越快。
D3-第三步骤:执行暂时对策---由小组人员负责执行若真正原因还未找到,暂时用什么方法可以最快地防止问题?如全检、筛选、将自动改为手动、库存清查等。
暂时对策决定后,即立刻交由团队成员带回执行。
备注:为了防止遗漏,纠正措施五要→客户仓库、在途、客户生产线、工厂生产线&工厂仓库。
D4-第四步骤:找出问题真正原因----由小组人员讨论后确定找问题真正原因时,最好不要盲目地动手改变目前的生产状态,先动动脑。
您第一件事是要先观察、分析、比较。
列出您所知道的所有生产条件(即鱼骨图),逐一观察,看看是否有些条件走样,还是最近有些什么异动?换了夹具吗?换了作业员?换了供应商?换了运输商?修过电源供应器?流程改过?或比较良品与不良品的检查结果,看看哪个数据有很大的差异?尺寸?重量?电压值?CPK?耐电压?等等不良的发生,总是有原因,资料分析常常可以看出蛛丝马迹。
这样的分析,可以帮助您缩小范围,越来越接近问题核心。
当分析完成,列出您认为最有可能的几项,再逐一动手作些调整改变,并且观察哪些改变可使品质回复正常及影响变异的程度,进而找到问题真正的原因。
这就是著名田口式方法最简单而实际的运用。
D5-第五步骤:选择永久对策----由小组人员讨论后确定找到造成问题的主要原因后,即可开始拟出对策的方法。
对策的方法也许有好几种,例如修理或更新模具。
试试对可能的选择列出其优缺点,要花多少钱?多少人力?能持续多久?再对可能的方法作一最佳的选择,并且确认这样的对策方法不会产生其它副作用。
客户8D报告

D4:Permanent Corrective Action/永久性的纠正措施
责任人:监督:执行日期:
D5:Action Effectiveness Verification/措施检验
Customer (客户名称) :
Open date (收件日):
CustomerRef(客户客诉编号):
Sample Qty : (样本数)
Customer Part No.(客户料号):
Lot No. : (批号)
Part No. : (品名)
Lot Size : (批量)
Date Code : (制造日期码)
深圳市硕凌电子科技有限公司
8D
CORRECTIVE ACTION REPORT
(客户抱怨改善报告)
CUSTOMER (客户):
PART NO.(品名):
REPORT NO.(編号):
REPORTDATE(日期):
承认
确认
制作
8D CORRECTIVE ACTION REPORT
Part 1 : Applicant Information (客诉资料)
Approved By:批准
Checked By:检查
Prepared By:承办
SL-QP-QA-14-02A
责任人:监督:执行日期:
D6:Action Result措施结果
确认者:确认日期:
D7:Prevent Recurrence预防重复发生
对策实施的第一批将在外箱右上角“★”标示,以示新对策实施后的产品。
品质异常处理报告书8D

7.推广至类似产品(同类产品、同类过程)
负责人
完成日期
主管
知会单位
□业务 □品管□制造□研发□模具□生管
结案确认
完成日期
状态
标准化
1.更改作业标准
是□/否□
文件编号/版本
负责人
更新日期
2.更改检验标准
是□/否□
文件编号/版本
负责人
更新日期
3.更改控制计划
是□/否□
文件编号/版本
负责人
更新日期
4.更改FMEA
是□/否□
文件编号/版本
负责人
更新日期
5.其它相关文件
是□/否□
文件编号/版本
负责人
更新日期
6.培训
负责人
XXXXX有限公司
品质异常处理报告书8D
抱怨客户
抱 怨 者
职务
抱怨时间
品名规格
订单数量
交货日期
处理期限
抱怨性质
□重大投诉□一般投诉
发生地点
登 陆 人
抱怨项目
□1.品质缺陷 □2.数量不符 □3.规格不符 □ 4.包装不良 □5.搬运损坏 □6.其它
抱怨内容
发生了什么问题(技术语言)
如何(第一次、重发)
为何产生抱怨(客户抱怨内容)
不合格数量(不良率)?
立即对策(现品调查)
a.围堵对策(客户端取回不良、隔离、全检、返工)
b.对可能受影响库存件的评审结论及挑拣情况
地点
挑拣数量
不合格数量
挑拣品序列号/批号范围
处理结果
客户库存(包括途中)
公司内库存
供应商零件库存
c.合格品出货日期
出货数量
最新8D报告全解读
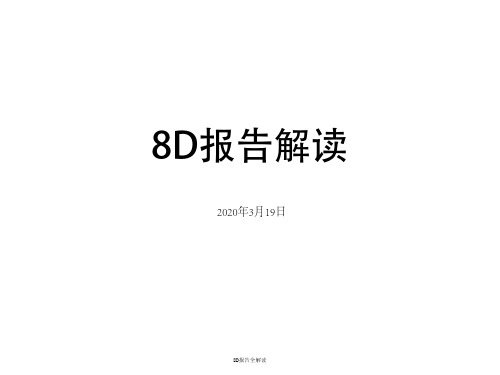
2020年3月19日
8D报告全解读
目录
一.什么是8D 二.为什么要推行8D 三.8D解读 四.8D改善案例 五.结束语
8D报告全解读
一.什么是8D
8D 的原名叫做8 Disciplines,又称团队导 向问题解决方法。是由福特公司始创,全球化品 质管制及改善的特殊必备方法,之后已成为 QS9000/ ISO TS16949、福特公司的特殊要求。凡 是做福特的零件,必需采用 8D 作为品质改善的 工具,目前有些企业并非福特的供应商或汽车业 的合作伙伴,也很喜欢用这个方便而有效的方法 解决品质问题,成为一个固定而有共识的标准化 问题解决步骤。
8D报告全解读
一.什么是8D
此方法以团队运作导 向以事实为基础,避 免个人主见之介入, 使问题之解决能更具 条理。
面对问题应群策群力, 互相帮助、相互提拔、 如此才能彻底解决问题。
4
8D报告全解读
二. 为什么要推行8D
8D报告全解读
三. 8D解读
1. 8D步骤概述 2. 每个步骤的解读
8D报告全解读
c Breakdown c Service c
c
Supply disruption
c
Other ……
项目范围注意事项;
起初8D是用来解决客诉的质量问题的,经过不断的完善和推广以后已
经应用于各种问题的解决。比如: 安全:产品有安全隐患、工厂内存在安全隐患…… 故障:设备故障、工艺过程失效……
以制造为中心, 其它部门都是 服务部门。
5W2H
WHO
谁
WHAT 什么
WHEN 何时
WHERE 何地
WHY
为什么
HOW
怎么样
8D报告

8D报告上一篇/ 下一篇2007-07-12 17:29:11 / 个人分类:品质规范查看( 120 ) / 评论( 2 ) / 评分( 6 / 0 )1.目的:1.1回复8D之制作与文件管制作业规范。
2.范围:2.1处理客户抱怨都可利用8D之制作方式,回复客户。
2.2当客户规定有解决问题的格式时,按规定的格式回复客户。
3.定义:3.1 8D:8 Disciplines,八项项目,为回复抱怨的一般格式。
4.作业流程图:如下图所示客户结案客户抱怨客户抱怨处理回复8D8D归档5.内容说明:5.1 8D格式制作说明:8D格式设计有八个部分,以下针对每个部分进行说明。
5.1.1问题解决团队Team Approach成立问题解决团队,解决该问题。
其成员为来自与该问题有相关之领域或问题之发生单位的专家或业务执行单位。
并由经理级以上之人员担任Chair。
5.1.1.1选择并记录内部/外部成员;l 选择小组的指导者(可以帮助小组移走障碍的管理成员);l 选择小组长(直接指挥并对小组负责的成员);5.1.2问题描述Problem Description。
问题描述:问题描述需基于客户所开的客诉加以分析,将问题发生的时间、发生问题的内容如失效模式为何?影响的广度与浓度为何?受影响的料号、批号为何?发生客户是谁?缺点率等相关问题陈述的内容加以说明,明确说明真正的问题。
l 使用顾客理解的术语;l 描述引起问题的状态变化;l 用量化的术语来表示状态。
5.1.3分析与发现Analysis & Finding。
分析与发现:分析相关的异常信息,确认缺点或问题的形成过程,进行问题的澄清与验证。
确认问题所影响的制程范围,如回溯问题批号之生产记录,关于参数数据如管制图有无异常,检验资料有无异常。
l 描述为什么变化会发生,或识别系统中允许问题存在并不能发现的“漏洞”;l 根本原因分类,如:---材料,机器,方法,人员,维护,环境。
8D-纠正预防措施报告-课件
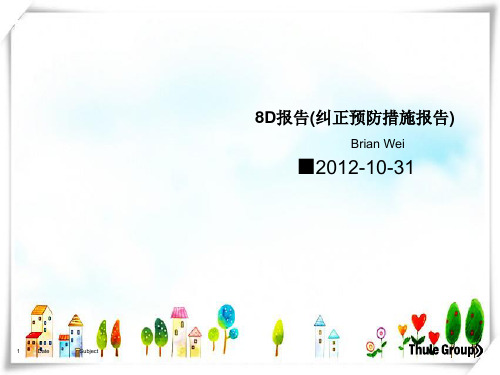
20
Date
Subject
D4 – 根本原因的确定
潜在原因
可能原因
根本原因
就问题的描述和收集到的资料进行比较分析,分
析有何差异和改变,识别可能的原因,测验每一个 原因,以找出最可能的原因,予以证实 (发生vs 流 出)。 (通过团队智慧发掘根本原因)
21
Date
Subject
方法、度量
环境
材料
人员
➢ 纠正措施是针对消除问题原因的改进行动 ➢ 纠正措施可以针对下列情况:
● 客户抱怨 ● 内部不符合项 ● 供应商问题 ● 审核发现的问题 ● 未达标的产品和工艺指标等 ●……
9
Date
Subject
防错法
Poka Yoke 防错法
➢Poka Yoke 来源于日本, 意思是 “防错法”,(防呆) ➢真正的纠正措施应有防错的效果, 无论在工艺或设计方
17
Date
Subject
判断: 问题描述好不好?
D2 – 问题描述
➢ 美国客户投诉车顶篮U形螺栓包装时出现错放
不好 – 1.信息不足 (产品编号, 日期, 不良率…) 2.问题描述中带有明显的导向性推断
➢ Thule 瑞典客户于2012/3/21反馈订单123456,
841000产品存在标贴漏贴现象, 抽样24箱发现5箱 该不良
8D的八个步骤:
➢ D1: 建立团队 ➢ D2: 定义问题 ➢ D3: 围堵措施 ➢ D4: 根本原因 ➢ D5: 制定纠正措施 ➢ D6: 实施和验证纠正措施 ➢ D7: 预防再发生/分享经验 ➢ D8: 祝贺奖励
14
Date
Subje强调小组的协同性。小组合在一起后,其 作用和智慧会超过个人单独作用的总和。
客户抱怨不良分析8D报告

Problem Analysis Problem Analysis (Logic to conclude the root cause) 问题分析问题分析 1月25日,XXX 从客户端取回高温与高温高湿测试NG2pcs 样品,我们对其进行如下分析:1. 对其2片产品进行外观检查,确认无不良。
2. 对其2片产品进行功能测试,发现一片产品功能OK,一片产品功能NG. (1)1片OK 品测试数据图形(测试数据)(2)1片功能NG 品测试数据图形线性端点阻抗序号 线性X 线性Y 端点阻抗X 端点阻抗Y 标准≤1.5 ≤1.5100-1000 100-10001#0.731.09403244线性端点阻抗序号 线性X 线性Y 端点阻抗X 端点阻抗Y 标准≤1.5 ≤1.5100-1000 100-10002#9.021.344162513. 对制程工艺进行异常排查确认,发现此产品在做样品贴合工站,人员作业手法的不当及贴合用滚轮清洁不干净综上所述,我们分析认为造成客户端样品试验不良原因如下:1. 产品在玻璃与菲林人工贴合过程中,人员作业手法不2. 此处膜受损折伤造成此片产品不良,产品在做可靠性试验时异常现象加重导由上层菲林ITO 层受损造成此片产品功能NG.5D) Permanent Corrective Actions.5D) Permanent Corrective Actions.长期对策长期对策长期对策 directed to eliminate the root cause into an actions taken into a provisionally manner.提出长期有效的对策Action *Action *对策对策对策 1.厂内培训及加强宣导人员作业手法,产品贴合后产线需进行外观自检。
巡检时重点检查贴合站产品贴合后外观,且PQC 对现场人员作业手法重点稽核。
使用前需检查确认是否干净。
8D报告、供应商预防纠正措施行动表

Responsible:
分析原因责任人
Name of individual responsible for root cause analysis
完成日期
Completion Date:
根本原因分析完成时间The completion date of root cause analysis
纠正措施
证明通过改善可以防止类似问题的发生或将此改善行动拓展于类似的过程以防止再发或标准化于我们现行的过程,(如:控制计划,形成文件,设备、夹具改造等)Use this section to provide improvement evidence to prevent complaints recurrence; or transform preventive actions into process or standardize our current process to avoid recurrence. (Control plans, documents, equipment/jig updates, etc.)
责任人
Responsible:
制定应急措施的责任人
Name of individual responsible for establishing emergency action
完成日期
Completion Date:
应急措施的完成时间
The completion date of containment actions
提供相关的证据显示问题已得到改善,如:图片、文件、数据等(14天内完成)
Provide relevant evidences to prove the problem has been improved, e.g. pictures, documents, data, etc.(completed within 14 days)
客诉8D报告格式

客诉8D报告格式客户抱怨改善⾏动报告9⽉9⽇客户SQE 反馈联创10086型号扬声器,有⾳沙现象9⽉10⽇收到客户退回的10011扬声器⾳沙不良6pcs制成:王⼤⼤2. 团队成员:组长:王⼩⼆(责任主管)成员:王⼤⼤(品质专员)/张三(技术⼯程师)/李四(技术⼯程师)/王五(⽣产主管)3. 原因分析:a )不良品确认… ....... .......... ...................... ......... . ........ . ....... . . ......1.9⽉10⽇收到客退⾳沙不良 6pcs ,观察外观⽆不良,如下图:2. ⽤⾳频扫描发⽣器把电压调⾄规格书要求 2.56V ,频率200-2KHZ ,⽤声腔对客退不良进⾏⾳质确认,确认⾳质⾳沙异常,如下图:3. 再将客诉不良品进⾏ BK 曲线测试,测试结果符合曲线要求,如下图:b )原因分析1. 技术员对客退不良品进⾏ X-ray 扫描分析,确认⽆不良,如下图:2. 研发⼯程师对客退进⾏拆解分析,拆去上壳,确认壳内外未不良,如下图:3. 技术员对单体拆解,稀释前盖胶,取下前盖 --〉观察膜⽚及边缘胶--〉稀释边缘胶--〉观察⾳圈及磁路, 如下图:3.1在拆解过程中,每步拆解都对部件进⾏仔细观察,确认⽆不良再进⾏下⼀步动作,技术员打开膜⽚时,发现⾳圈内侧有异物(⽤放⼤镜观测看出⾳圈内侧有异物),如图:⼩结:因⾳圈内有异物,导致⾳沙不良3.2流出原因①对产线进⾏排查发现,6S 良好②对⼈员确认,⼈员⾛动频繁,排查发现16条线其中2位套⾳圈⼈员2套膜⽚⼈员未佩带⼿指套未配戴⼿指套作业,如图:③对⼯装进⾏排查,现场⼯装都⼲净整洁,清洗记录亦⽆异常④查询OQC 检验记录,OQC ⼰录未记录检验的产品唯⼀编码,不能确认是否检验过⑤确认产线听⾳作业模式,2h 更换⼀次听⾳作业⼈员,排除疲劳作业,查看当天听⾳⼈员安排状况:有安排新⼈进⾏听⾳作业=====〉怀疑为新⼈不熟悉听⾳导致漏检⼩结:线上作业⼈员不按规范作业,⼈员⾛动频繁,导致异物落在⾳圈内,导致⾳沙,听⾳新⼈上线,导致⼚内漏检分析⼈:李四/张三4. 短期对策:对库存内该新⼈上线期间的产品进⾏下线听⾳作业,⾛返⼯流程5. 长期对策:客户名称不良数量风险批量编制1.问题描述:TCL 王⼤⼤审核产品型号投诉⽇期回复⽇期 2016-9-9 2016-9-10 张三/李四/王五精品⽂档交流。
8D报告格式

DISCIPLINE 4:Define and Verify Root Cause (定义及验证根本原因)
担当者(Executed by):执行日期(Effective Date):
DISCIPLINE 5:Permanent Corrective Action (纠正措施)
作成
(Maker)
DISCIPLINE 8:Closure结案
Judgement: (判定)
□Accept
(接受)
□Reject
(退回)
Person incharge(责任人)
Checked
(审核)
Approved
(核准)
Conclusion:(结案描述)
Actual close date:(实际结案日)
Attached documents(附檔):□Yes□No
表单编号:XXX-XX-001版本:A/0
DISCIPLINE 7:Recurrence Prevention & Standardization (预防再发及标准化)
是否修改相關文件□Yes□QC工程图□SOP□承认书□其它
□No
担当者(Executed by):执行日期(Effective Date):
核准(Approved)
审核
(Check)
8 Discipline Report
客户名称Hale Waihona Puke Customer):交货数
(P/O ntity):
编号
Report No.
料号
(Part No):
不良数
(DefectiveQuantity):
8D报告格式说明
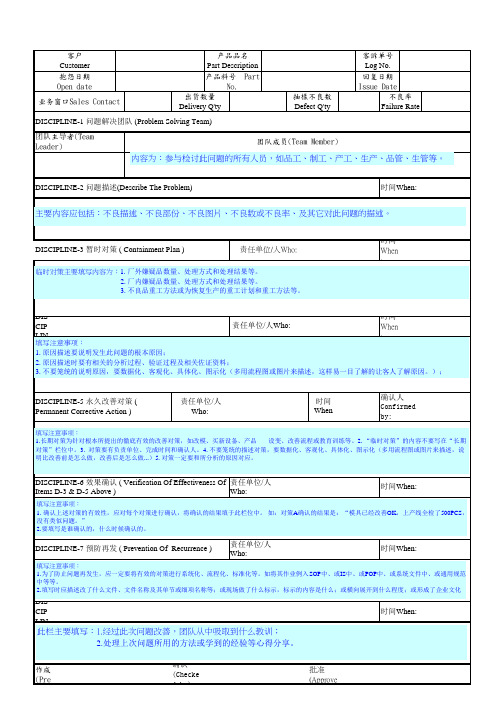
表ห้องสมุดไป่ตู้编号:QR-Q-066
版本:A0
DISCIPLINE-4 根本原因分析 ( Describe The Root Cause )
责任单位/人Who:
时间When:
填写注意事项: 1. 原因描述要说明发生此问题的根本原因; 2. 原因描述时要有相关的分析过程、验证过程及相关佐证资料; 3. 不要笼统的说明原因,要数据化、客观化、具体化、图示化(多用流程图或图片来描述,这样易一目了解的让客人了解原因。);
主要内容应包括:不良描述、不良部份、不良图片、不良数或不良率、及其它对此问题的描述。
DISCIPLINE-3 暂时对策 ( Containment Plan )
责任单位/人Who:
时间When:
临时对策主要填写内容为:1. 厂外嫌疑品数量、处理方式和处理结果等。 2. 厂内嫌疑品数量、处理方式和处理结果等。 3. 不良品重工方法或为恢复生产的重工计划和重工方法等。
DISCIPLINE-6 效果确认 ( Verification Of Effectiveness Of 责任单位/人 Items D-3 & D-5 Above ) Who:
时间When:
填写注意事项: 1. 确认上述对策的有效性,应对每个对策进行确认,将确认的结果填于此栏位中。 如:对策A确认的结果是:“模具已经改善OK,上产线全检了500PCS, 没有类似问题。” 2.要填写是谁确认的,什么时候确认的。
DISCIPLINE-1 问题解决团队 (Problem Solving Team) 团队主导者(Team Leader) 团队成员(Team Member)
内容为:参与检讨此问题的所有人员,如品工、制工、产工、生产、品管、生管等。
8D问题解决报告

D
5
真正原因分析Root Cause:(从以下5个方面进行分析)
何时When
①人Man:
②机器Machine
③材料Material
④方法Method
⑤环境/系统Environment/System
D
6
改善对策Corrective Action:
□质量审核QualityAudit
□其他Etc.
Ratio(%)
比例
Issued By:
发出人
P
L
A
N
项目Section
计划Schedule
W( )
W( )
W( )
W( )
W( )
W( )
W( )
D1
问题解决团队组成Composition of Team
D2
问题描述ProblemDescription
1
问题解决团队组成Composition of Team:
①负责人Chair Person:
②责任小组成员Responsible Team Member:
③行动小组成员Action Team Member:
④支持小组成员Support Team Member:
D
2
问题描述ProblemDescription:
项目Section
备注Remarks
问题点Problem
不良确认Status Check
D
3
分析与发现Analysis & Finding:
流程/库存
Process/ Stock:
批号
Lotcode:
电容PS异常客户抱怨处理8D报告表 模版
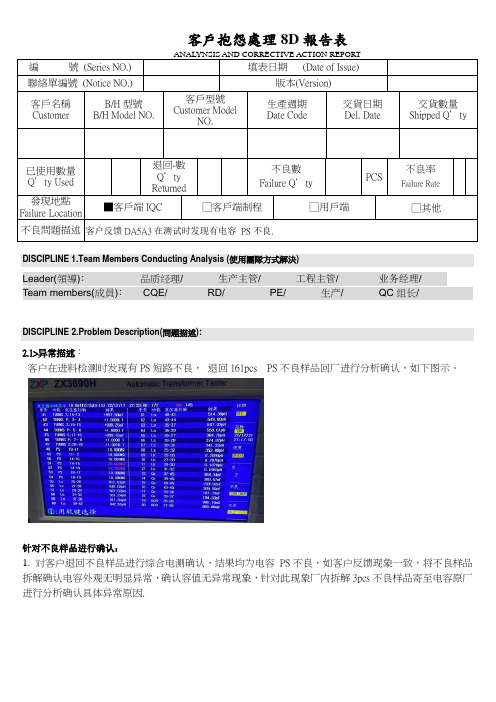
客戶抱怨處理8D報告表DISCIPLINE 1.Team Members Conducting Analysis (使用團隊方式解決)Leader(領導)﹕品质经理/ 生产主管/ 工程主管/ 业务经理/Team members(成員)﹕CQE/ RD/ PE/ 生产/ QC组长/DISCIPLINE 2.Problem Description(問題描述):2.1>异常描述:客户在进料检测时发现有PS短路不良,退回161pcs PS不良样品回厂进行分析确认,如下图示。
针对不良样品进行确认:1. 对客户退回不良样品进行综合电测确认,结果均为电容PS不良,如客户反馈现象一致,将不良样品拆解确认电容外观无明显异常,确认容值无异常现象,针对此现象厂内拆解3pcs不良样品寄至电容原厂进行分析确认具体异常原因.不良现象与客户端一致,PS不良拆解不良样品,确认电容未明显外观异常. 将不良样品寄至电容原厂进一步解析.DISCIPLINE 3.Containment & Short Term Corrective Actions (短暫且立即遏止問題之對策):廠內在製品﹕厂内在制品为0廠內庫存品﹕厂内在库品为0客端庫存品﹕客户端库存品1pcs退我司返工处理,DISCIPLINE 4.Define & Verify Root Cause (詳細說明與驗證根本原因):4.1 针对电容PS异常原因,电容原厂分析详见附档分析报告:总论:从以上原厂分析结果可以确认电容DF/IR异常主要为内部高压测试击穿所致:1、电容是被高电压电流击穿。
2. 确认客户端有通过高压2250 DC 1S 1MA进行测试.DISCIPLINE 5. Implement Permanent Corrective Action(實施執行改善對策)5.1、根据12月3号与厂内RD/生产工程、至客户端现埸同步了解确认情况,客户端测试标准与厂内有不同平情况,针对此点我司RD对测试规范重新优化与客户端对齐,如附件生产测试规范.5.2、主要针对电容PS产生原因:降低L-G耐压规格,从2250降低到1500VDC5.3、流出原因:取消CP绝缘电阻,增加CP容值测试責任人 : 執行日期:DISCIPLINE6 : Verify Permanent Corrective Action (驗證對策之有效性)依优化后生产规范进行测试生产.DISCIPLINE 7 : Prevent Recurrence (預防再發生)水平展开同系列产品DISCIPLINE 8 : Closure (結案)客戶端確認﹕电性测试规格书--改后.xlsx。
- 1、下载文档前请自行甄别文档内容的完整性,平台不提供额外的编辑、内容补充、找答案等附加服务。
- 2、"仅部分预览"的文档,不可在线预览部分如存在完整性等问题,可反馈申请退款(可完整预览的文档不适用该条件!)。
- 3、如文档侵犯您的权益,请联系客服反馈,我们会尽快为您处理(人工客服工作时间:9:00-18:30)。
編號(Series NO.)
填表日期(Date of Issue)
聯絡單編號(Notice NO.)
版本(Version)
客戶名稱
Customer
B/H型號
B/H Model NO.
客戶型號
Customer Model NO.
生產週期
Date Code
交貨日期Del. Date
DISCIPLINE 8﹐Closure (結案)
客端品保結案注記:
核准
(Approved By)
審核
(Checked By)ቤተ መጻሕፍቲ ባይዱ
填寫人
(Prepared By)
交貨數量
Shipped Q’ty
已使用數量
Q’ty Used
PCS
不良數
Failure Q’ty
PCS
退回數
Q’ty Returned
PCS
不良率
Failure Rate
發現地點
Failure Location
客戶抱怨內容
DISCIPLINE 1
Leader(領導)﹕
Team members(成員)﹕
DISCIPLINE 2﹐Problem Description.(問題描述):
DISCIPLINE 3﹐Containment & Short Term Corrective Actions (短暫且立即遏止問題之對策)
DISCIPLINE 4﹐Define & Verify Root Cause (詳細說明與驗證根本原因)
DISCIPLINE 5﹐Implement Permanent Corrective Action.(實施執行改善對策)
DISCIPLINE 6﹐Verify Permanent Corrective Action.(驗證對策之有效性)
DISCIPLINE 7﹐Prevent Recurrence.(預防再發生)