数控机床系统设计(1)
数控机床控制系统设计

数控机床控制系统设计数控机床控制系统是现代机械加工中的重要设备,不仅减轻了人工操作的负担,还能够实现高效精确加工。
本文将从数控机床控制系统的设计原理、控制器的分类以及系统设计中需要考虑的因素等各方面进行详细阐述。
一、数控机床控制系统设计原理数控机床是一种以计算机控制的工具设备。
数控机床的工作原理是通过加工程序与自动化机床相连接,由计算机系统对机床运动进行控制。
数控机床的加工程序是一种由G代码和M 代码组成的程序,G代码主要用于控制机床的直线运动和圆弧运动、刀具半径、零点位置等,M代码则是用于控制机床的主轴转速、冷却液开关等控制信号。
基本上数控机床可以实现加工各种形状的物件,而且加工精度高,生产效率高。
二、控制器的分类数控机床控制器根据其构成和结构可以大致分为以下几个类型:1、点位控制器(P控制器):点位控制器可以控制每一个轴单独移动到预定的位置后,马上停止这一轴的运动,使其它轴继续运动。
2、直线插补控制器(L控制器):直线插补控制器是比点位控制器更为先进的控制器,它不仅在每个轴位置上进行控制,还可以控制各轴在不同的位置上同时启动或同时停止。
3、圆弧插补控制器(C控制器):圆弧插补控制器是对圆弧运动进行控制的控制器。
它可以自动地计算和控制机床在坐标平面或变位平面上的转折点、曲线半径以及运动方向等,圆心和半径的计算完全由控制器来完成。
4、模态控制器(M控制器):模态控制器是负责管理机床程序重复执行的控制器。
它只需输入一次程序,就可以重复地使用该程序。
换言之,它可以使用多个程序段,从而实现切换各种不同加工方式,同时还可以根据不同的工件要求随时更改程序的具体内容。
三、系统设计中需要考虑的因素在设计数控机床控制系统时,需要考虑如下因素:1、系统稳定性:稳定性是数控机床控制系统设计的重要指标,必须保证系统在加工过程中不会出现任何一个运动轴的失控。
系统设计时需要合理选用现代控制技术,同时要对硬件和软件进行完整测试,保证系统的稳定性。
基于PLC的数控机床控制系统设计
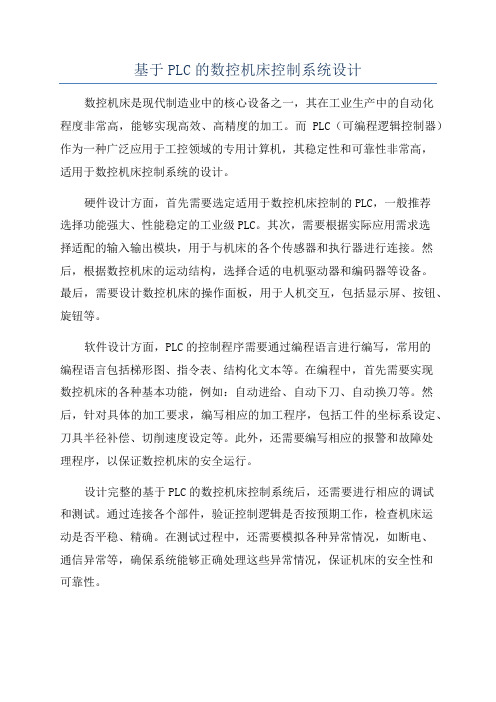
基于PLC的数控机床控制系统设计数控机床是现代制造业中的核心设备之一,其在工业生产中的自动化程度非常高,能够实现高效、高精度的加工。
而PLC(可编程逻辑控制器)作为一种广泛应用于工控领域的专用计算机,其稳定性和可靠性非常高,适用于数控机床控制系统的设计。
硬件设计方面,首先需要选定适用于数控机床控制的PLC,一般推荐选择功能强大、性能稳定的工业级PLC。
其次,需要根据实际应用需求选择适配的输入输出模块,用于与机床的各个传感器和执行器进行连接。
然后,根据数控机床的运动结构,选择合适的电机驱动器和编码器等设备。
最后,需要设计数控机床的操作面板,用于人机交互,包括显示屏、按钮、旋钮等。
软件设计方面,PLC的控制程序需要通过编程语言进行编写,常用的编程语言包括梯形图、指令表、结构化文本等。
在编程中,首先需要实现数控机床的各种基本功能,例如:自动进给、自动下刀、自动换刀等。
然后,针对具体的加工要求,编写相应的加工程序,包括工件的坐标系设定、刀具半径补偿、切削速度设定等。
此外,还需要编写相应的报警和故障处理程序,以保证数控机床的安全运行。
设计完整的基于PLC的数控机床控制系统后,还需要进行相应的调试和测试。
通过连接各个部件,验证控制逻辑是否按预期工作,检查机床运动是否平稳、精确。
在测试过程中,还需要模拟各种异常情况,如断电、通信异常等,确保系统能够正确处理这些异常情况,保证机床的安全性和可靠性。
总之,基于PLC的数控机床控制系统设计需要考虑到硬件和软件两个方面,确保系统功能完善、稳定可靠。
通过合理的硬件设计和编写高效的控制程序,可以实现数控机床的自动化加工,提高生产效率和产品质量。
数控车床控制系统的设计样本

CK6163数控车床控制系统设计1.本课题项目背景及研究意义金融危机爆发以来, 国际机床市场不断下滑, 国内经济型数控机床市场也受到了相称大影响, 产销量大幅下降。
虽然数据显示上半年已经止住下滑趋势, 略微回升, 但研究应对方略仍旧是当务之急。
经济型数控机床是国内数控机床行业发展起步产品, 发展时间比较长, 生产公司对此类机床技术掌握状况和生产能力也都比较成熟。
正由于如此, 加之其在国内拥有大量市场空间, 金融危机爆发之前产量较大。
但从去年金融危机后来总体状况来看, 国内经济型数控机床生产公司生产能力明显过剩。
近来中华人民共和国机床工具工业协会调研成果中得到公司生产状况显示, 重要生产经济型数控机床公司受到冲击比较大, 特别是某些产品档次比较低、产量比较大公司受到冲击更大, 甚至浮现某些公司限产现象。
导致这种状况浮现重要因素还是由于市场需求在减少, 加上经济型数控机床生产能力比较强, 生产公司比较多, 竞争比较激烈,同步经济型车床、钻床和铣床出口量下降比较严重, 某些产品出口转内销, 进一步加剧了国内市场竞争。
而对于产品档次比较高公司来说, 受到冲击就不是很明显, 特别是高精尖高档机床仍旧是供不应求。
数控机床代表着机械制造业当代科学技术发展方向和水平。
当前, 国内数控机床发展不但从技术水平上已研制出五坐标数控铣床加工中心, CNC系统和自动编程系统等。
同步, 也拥有了一定数量数控机床开发、生产、使用以及拥有量等都与世界上先进国家有较大差距。
要达到世界先进水平, 迅速发展国内数控机床行业势在必行。
经济型数控机床设计必然性: 数控机床能较好地解决形状复杂、精密、小批多变零件加工问题。
可以稳定加工质量和提高生产率, 也具备适应性强、较高加工精度。
但是应用数控机床还受到其他条件限制。
价格昂贵, 一次性投资巨大, 对于中小公司心有余而力局限性。
当前各公司均有大量通用机床, 完全用数控机床代替主线不也许, 并且代替下来机床闲置起来, 又会导致挥霍。
数控车床进给系统设计

数控车床进给系统设计一、进给系统的结构设计1.可靠性高:进给系统的关键零部件应采用优质的材料和加工工艺,以保证系统的稳定性和长寿命。
2.刚性好:进给系统的结构应具备足够的刚度,以保证在高速切削和大负载的工况下,机床能够保持稳定运行。
3.灵活性强:设计时应考虑到不同工件的加工要求,进给系统应能够快速调整和变换,以满足不同工件的加工需求。
二、进给系统的控制方法设计1.PTP控制方式:即点对点控制方式,根据工件形状和切削要求设计程序,实现工件形状的控制和切削路径的规划。
2.直线插补控制方式:通过数学模型进行直线切削路径的插补计算,实现工件形状的控制和切削路径的规划。
3.圆弧插补控制方式:通过数学模型进行圆弧切削路径的插补计算,实现工件形状的控制和切削路径的规划。
三、进给系统的传动方式设计传统数控车床进给系统的传动方式有液压传动和蜗杆传动两种,在设计进给系统时需要选择合适的传动方式,以满足不同加工工况的需求。
1.液压传动:液压传动以其可适应性强、能源利用率高等优点,在高负载和高速切削的工况下表现出较好的性能。
2.蜗杆传动:蜗杆传动以其结构简单、体积小、传动精度高等优点,在精密加工和高速加工的场合得到广泛应用。
四、进给系统的反馈装置设计进给系统的反馈装置是保证机床加工精度的重要组成部分,主要分为位置反馈和力反馈两种。
设计反馈装置时需要考虑以下几个因素:1.精度要求:根据机床加工的精度要求选择合适的反馈装置,以保证加工精度的稳定性。
2.反馈方式:根据加工工况选择合适的反馈方式,如光电编码器、脉冲等。
3.反馈信号的处理:对反馈信号进行合理的滤波和放大处理,以保证控制系统的稳定性和精度。
总之,数控车床进给系统的设计直接影响机床的加工精度和工作效率。
在设计进给系统时应考虑到结构、控制方法、传动方式和反馈装置等方面的因素,以满足不同加工要求。
同时,还需要对系统进行可靠性和稳定性分析,以确保数控车床的长期稳定运行。
简易数控铣床的系统设计
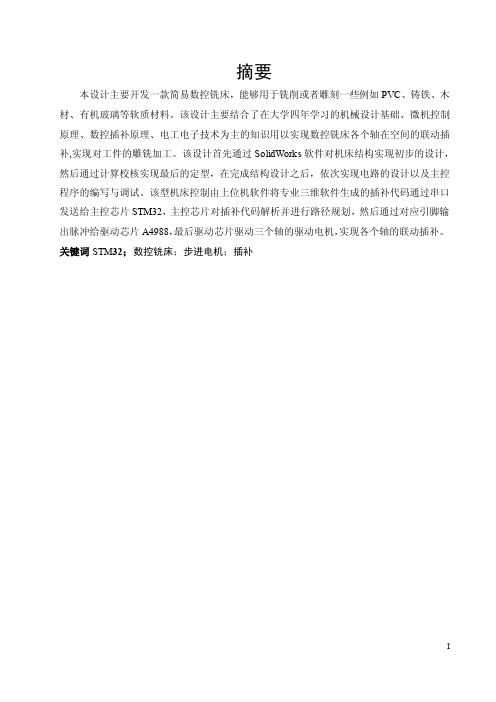
摘要本设计主要开发一款简易数控铣床,能够用于铣削或者雕刻一些例如PVC、铸铁、木材、有机玻璃等软质材料。
该设计主要结合了在大学四年学习的机械设计基础、微机控制原理、数控插补原理、电工电子技术为主的知识用以实现数控铣床各个轴在空间的联动插补,实现对工件的雕铣加工。
该设计首先通过SolidWorks软件对机床结构实现初步的设计,然后通过计算校核实现最后的定型,在完成结构设计之后,依次实现电路的设计以及主控程序的编写与调试。
该型机床控制由上位机软件将专业三维软件生成的插补代码通过串口发送给主控芯片STM32,主控芯片对插补代码解析并进行路径规划,然后通过对应引脚输出脉冲给驱动芯片A4988,最后驱动芯片驱动三个轴的驱动电机,实现各个轴的联动插补。
关键词STM32;数控铣床;步进电机;插补AbstractThis design mainly developed a simple CNC milling machine, can be used for milling or sculpture such as PVC, soft material such as cast iron, wood, organic glass.This design is mainly combined the study in the university four years of mechanical design basis, principle of microcomputer control, numerical control interpolation principle, electrical and electronic technology as the main knowledge to achieve the linkage of the CNC milling machine each axis in space interpolation, realize the artifact carved milling processing.This design first by SolidWorks software structure to realize the preliminary design of nc machine tools, and then by calculating and checking the final shape, after complete the structural design, the realization of circuit design as well as the master control program written in turn and debugging.The type of machine tool control by the PC software to professional 3d interpolation code generated by the software via a serial port sent to the main control chip STM32, master control chip for interpolation code parsing and path planning, and then through the output pulse of the corresponding pin to drive chip A4988, finally the drive motor driver chip driver three axis, realize the interaction of each axis interpolation.Keywords STM32; CNC milling machine; stepper motor ; interpolation辽宁工程技术大学毕业设计(论文)引言近些年,随着互联网的发展,以美国为代表的发达国家的“再工业化”概念,以及以中国为首的新兴国家的崛起使得以德国为首的制造业强国的工业产品销售受到不同程度的影响。
数控机床进给系统设计
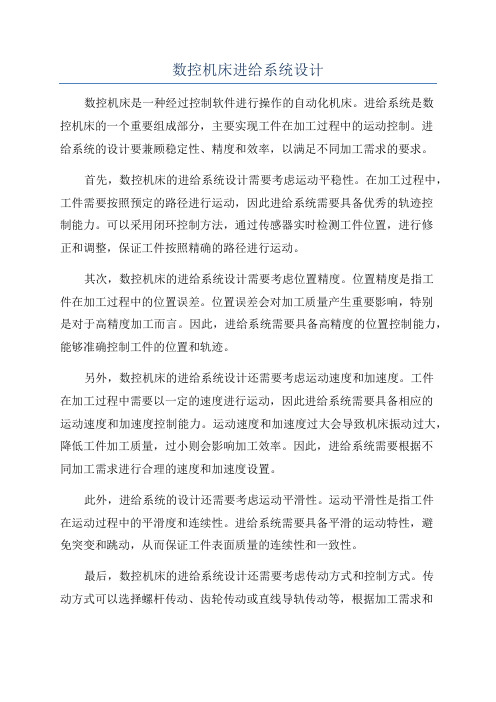
数控机床进给系统设计数控机床是一种经过控制软件进行操作的自动化机床。
进给系统是数控机床的一个重要组成部分,主要实现工件在加工过程中的运动控制。
进给系统的设计要兼顾稳定性、精度和效率,以满足不同加工需求的要求。
首先,数控机床的进给系统设计需要考虑运动平稳性。
在加工过程中,工件需要按照预定的路径进行运动,因此进给系统需要具备优秀的轨迹控制能力。
可以采用闭环控制方法,通过传感器实时检测工件位置,进行修正和调整,保证工件按照精确的路径进行运动。
其次,数控机床的进给系统设计需要考虑位置精度。
位置精度是指工件在加工过程中的位置误差。
位置误差会对加工质量产生重要影响,特别是对于高精度加工而言。
因此,进给系统需要具备高精度的位置控制能力,能够准确控制工件的位置和轨迹。
另外,数控机床的进给系统设计还需要考虑运动速度和加速度。
工件在加工过程中需要以一定的速度进行运动,因此进给系统需要具备相应的运动速度和加速度控制能力。
运动速度和加速度过大会导致机床振动过大,降低工件加工质量,过小则会影响加工效率。
因此,进给系统需要根据不同加工需求进行合理的速度和加速度设置。
此外,进给系统的设计还需要考虑运动平滑性。
运动平滑性是指工件在运动过程中的平滑度和连续性。
进给系统需要具备平滑的运动特性,避免突变和跳动,从而保证工件表面质量的连续性和一致性。
最后,数控机床的进给系统设计还需要考虑传动方式和控制方式。
传动方式可以选择螺杆传动、齿轮传动或直线导轨传动等,根据加工需求和机床类型进行选择。
控制方式可以选择基于位置、速度或力控制等,根据具体应用进行选择。
综上所述,数控机床的进给系统设计需要兼顾运动平稳性、位置精度、运动速度和加速度、运动平滑性、传动方式和控制方式等因素。
通过合理的设计和调试,可以提高数控机床的加工质量和效率,满足不同加工需求的要求。
数控机床进给系统设计
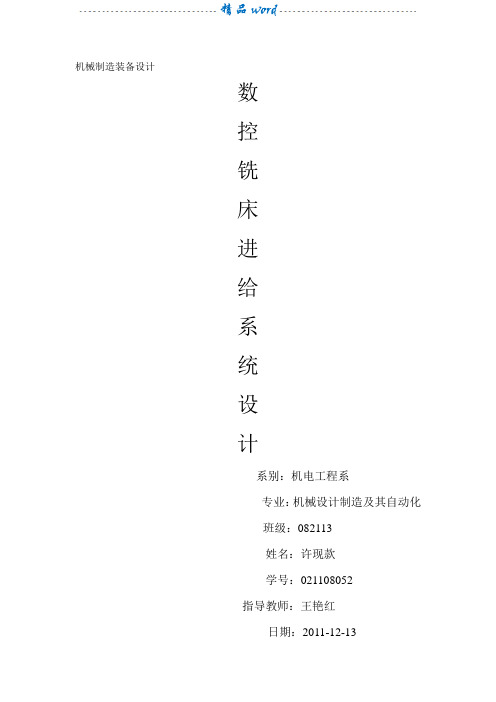
机械制造装备设计数控铣床进给系统设计系别:机电工程系专业:机械设计制造及其自动化班级:082113姓名:许现款学号:021108052指导教师:王艳红日期:2011-12-13数控机床进给系统设计1总体方案设计1.1对进给伺服系统的基本要求带有数字调节的进给驱动系统都属于伺服系统,进给伺服系统不仅是数控机床的一个重要组成部分,也是数控机床区别于一般机床的一个特殊部分。
数控机床对进给伺服系统的性能指标可归纳为:定位精度要高;跟踪指令信号响应要快;系统的稳定性要好。
1.2进给伺服系统的设计要求机床的位置调节对进给伺服系统提出了很高的要求,其中在静态设计方面:(1)能够克服摩擦力和负载,当加工中最大切削力为20000N——30000N时,电机轴上的转矩需要10N.m——40N.m;;(2)很小的进给移动量。
目前最小分辨率为0.1m(3)高的静态扭转刚度;(4)足够的调速范围;(5)进给速度均匀,在速度很低是无爬行现象。
在动态设计方面有:(1)具有足够的加速和制动装矩,以便快速的完成启动和制动;(2)具有良好的动态传递性能,以保证在加工中获得高的轨迹精度和满意的表面质量;(3)负载引起的轨迹误差尽可能小。
对数控机床机械传动部件则有以下要求:(1)被加速的运动部件具有较高的惯量;(2)高的刚度和良好的阻尼;(3)传动部件在拉压刚度、扭转刚度、摩擦阻尼特性和间隙等方面具有尽可能小的非线性。
1.3总体方案进给伺服系统总体方框图如下图3.1所示。
2进给伺服系统机械部分设计进给伺服系统机械部分的计算与选型内容包括:确定脉冲当量,计算切削力,滚珠丝杆螺母副的设计、计算与选型,齿轮传动计算,步进电机的计算和选型等。
微机光电隔离光电隔离光电隔离功率放大功率放大功率放大步进电机步进电机步进电机向向向图3.1进给伺服系统总体方框图2.1确定脉冲当量,计算切削力1确定系统的脉冲当量脉冲当量是指一个进给脉冲使机床执行部件产生的进给量,它是衡量数控机床加工精度的一个重要参数,因此。
数控机床液压系统设计

数控机床液压系统设计数控机床的液压系统是其重要组成部分,主要用于机床各种运动的驱动和定位。
合理的液压系统设计可以提高机床的工作效率和加工质量。
以下是一份1200字以上的数控机床液压系统设计。
液压系统设计首先要确定机床的工作要求,包括工作压力、流量、稳定性等方面的要求,然后根据这些要求选择合适的液压元件和系统参数。
在液压系统的设计中,首先需要确定所需的液压泵的类型和工作参数。
常用的液压泵有齿轮泵、齿轮泵和柱塞泵等。
选取液压泵时需要考虑机床的工作压力和流量要求以及液压泵的工作效率。
根据机床的实际情况和工作要求,选择合适的液压泵。
其次,需要选择合适的液压马达,用于驱动机床的各种运动部件。
液压马达的选择要考虑机床的负载要求和流量需求。
合适的液压马达可以确保机床具有稳定的运动性能和高的工作效率。
液压系统中还需要选择合适的液压阀。
液压阀的选择要根据机床的控制要求和系统的流量需求。
常用的液压阀有方向控制阀、比例控制阀和流量控制阀等。
合理的液压阀选择可以确保机床具有准确的控制和稳定的运动。
此外,液压系统中还需要设计合适的油箱、油管和附件等。
油箱要具有足够的容积和散热面积,以确保液压系统的稳定工作。
油管要选择合适的直径和材料,以确保液体的流通畅通。
附件的选择要根据机床的实际需要,如压力表、油温计和滤油器等。
液压系统设计中还需要充分考虑系统的安全性和可靠性。
例如,可以在系统中设置安全阀和溢流阀等保护装置,以防止系统超载和泄漏。
同时,还可以设计系统的自动监测和报警装置,及时发现并解决系统故障。
总之,液压系统设计是数控机床设计中重要的一部分。
合理的液压系统设计可以提高机床的工作效率和加工质量,同时确保机床的安全性和可靠性。
在液压系统设计中,需根据机床的工作要求选择合适的液压元件和系统参数,并充分考虑系统的安全性和可靠性。
这样才能设计出满足机床工作需求的液压系统。
- 1、下载文档前请自行甄别文档内容的完整性,平台不提供额外的编辑、内容补充、找答案等附加服务。
- 2、"仅部分预览"的文档,不可在线预览部分如存在完整性等问题,可反馈申请退款(可完整预览的文档不适用该条件!)。
- 3、如文档侵犯您的权益,请联系客服反馈,我们会尽快为您处理(人工客服工作时间:9:00-18:30)。
红字的意思是没找到答案,蓝字的意思是不确定;有错别字不负责啊。
学渣整理,此资料仅供参考╮(╯▽╰)╭一⒈数控机床通常由哪几部分组成?各部分的作用和特点是什么? 控制介质 作用:在数控机床加工时,携带和传输所需的各种控制信息。
特点:是存储数控加工所要的全部动作和刀具相对于工件位置信息的媒介物,它记载着零件的加工程序。
数控装置 作用:是数控机床的核心,它根据输入的程序和数据,经过数控装置的系统软件或逻辑电路进行编译、 运算和逻辑处理后,输出各种信号和指令,控制机床的各个部分,进行规定的、有序的动作。
特点:可分为普通数控系统NC和计算机数控系统CNC两类。
伺服机构 作用:根据数控装置发来的速度和位移指令控制执行部件的进给速度、方向和位移。
特点:由伺服驱动电路和伺服驱动装置组成,与机床上的执行部件和机械部件组成数控机床的进给系统。
机械部件 作用:包含有主运动部件、进给运动执行部件、拖板和传动部件等。
特点:传动结构要求更为简单,精度、刚度、抗震性等方面要求更高,且其传动和变速系统要便于实现 自动化控制。
⒉简述数控机床的分类 按运动方式分 点位控制系统:需要从一点准确的移动到另一点,移动过程不需要切削; 点位直线控制系统:需要从一点准确的移动到另一点,且运动轨迹为直线,移动部件在移动过程中 进行切削; 轮廓控制系统:需要从一点准确的移动到另一点,并能控制将零件加工成一定的轮廓形状。
按控制方式分 开环控制系统:不具有反馈装置,系统精度较低; 半闭环控制系统:具有角位移检测装置,定位精度较高,调试方便,稳定性好; 闭环控制系统:具有直线位置检测装置,具有检测、比较和反馈装置,定位精度高,但结构复杂。
按数控系统的功能水平分:低、中、高档次⒊什么是开环、半闭环和闭环控制系统?其特点是什么?适用于什么场合? ①开环控制系统是指不带反馈装置的控制系统;特点是不能进行误差校正,因此系统精度较低;适用于低精度要求 的数控机床。
②半闭环控制系统是在开环控制系统的伺服机构中装有角位移检测装置的控制系统;特点是调试方便,稳定性好精 度较高;目前应用较为广泛。
③闭环控制系统是在机床移动部件位置上直接装有直线位置检测装置的控制系统;特点是定位精度高,调试维修较 为困难;适用于精度要求高的数控机床。
⒋脉冲当量、定位精度和重复定位精度的含义是什么? 脉冲当量:数控装置每发出一个脉冲信号,反映到机床位移部件上的移动量。
定位精度:数控机床工作台等移动部件在确定的终点所到达的实际位置的精度。
重复定位精度:在同一台数控机床上,应用相同程序、相同代码加工一批零件,所得到的连续结果的一致程度。
⒌数控轴数与联动轴数的区别。
控制轴即机床数控装置能够控制轴的数目,而联动轴即同时控制多个轴的运动。
数控轴数越多,功能就越强,机床 的复杂程度和技术含量也越高;联动轴数越多,机床控制和编程难度越大。
⒎数控车床床身和导轨有几种布局形式?每种布局形式的特点是什么? 有四种布局形式 ①平床身:工艺性好,便于导轨面的加工; ②斜床身:排屑方便,便于安装自动排屑器,操作方便,易于实现单机自动化和封闭式防护; ③平床身斜滑板:工艺性好,排屑方便; ④立床身:排屑最为方便。
二⒈数控机床设计方案的特点是什么? 设计手段计算机化;设计方法综合化;设计对象系统化;设计问题模型化;设计过程程式化与并行化。
⒉数控机床设计的主要内容和步骤是什么? 主要技术指标设计:用途、生产率、性能指标、主要参数、驱动方式; 总体方案设计:运动功能设计、基本参数设计、传动系统设计、总体结构布局设计、控制系统设计; 总体方案综合评价与选择; 总体方案的设计修改(优化); 详细设计(技术设计、施工设计); 机床整机综合评价。
⒊数控机床设计应满足哪些基本要求? 精度:几何精度、运动精度、传动精度、定位精度、工作精度、精度保持性; 刚度:机床系统抵抗变形的能力; 抗振性:机床在交变载荷作用系抵抗变形的能力,它包括抵抗受迫振动的能力和抵抗自激振动的能力; 热变形:机床在工作时受到内部热源和外部热源的影响,使机床各部分温度发生变化; 噪声:机床工作时各种不同振动频率和不同振幅而产生的无规律的声音; 低速运动平稳性:当运动部件低速运行时,主动件匀速运动,被动件会出现爬行现象。
⒌工件表面发生线的形成方法是什么? 轨迹法(描述法):由点切削刃做直线运动轨迹形成的; 成形法(仿形法):刀具是线切削刃,它的形成不需要刀具与工件的相对运动; 相切法(旋切法):圆母线是面切削刃运动轨迹的包络线,为形成圆母线,刀具和工件之间需要刀具的旋转运动、刀 具回转中心与与工件之间按回转轨迹进行相对运动; 展成法(滚切法):由线切削刃在刀具与工件作占城运动时所形成的一系列轨迹线的包络线。
⒍机床的主参数及尺寸参数根据什么确定? 主参数根据加工零件或被加工面的尺寸参数来确定;尺寸参数根据与被加工零件有关的尺寸和标准化工具或夹具的 安装面尺寸来确定。
三⒈数控机床对主传动系统有哪些要求? 运动要求:具有一定转速和足够的转速范围、转速级数,能够实现运动的开停、变速、换向和制动; 动力要求:具有祖东的功率,全部机构和元件具有足够的强度和刚度; 工作性能要求:具有足够高的精度、抗振性,热变形和噪声小,传动效率高; 使用要求:操作灵活可靠,调整维修方便,润滑密封良好; 经济性要求:结构简单紧凑,工艺性好,成本低。
⒉数控机床主传动系统有哪几种配置方式?各有何特点? 有四种配置方式 ①带有变速齿轮的主传动:能满足主轴低速时对输出转矩特性的要求,能使交流或直流电动机成为分段无级变速, 实现滑动齿轮的位移; ②通过带传动的主传动:能避免齿轮传动引起的振动与噪声; ③用两个电动机分别驱动:克服了低速时转矩不够且电动机功率不能充分利用的缺陷; ④内装电动机主轴传动结构:提高主轴部件的刚度,单电机发热对主轴影响较大。
⒊某机床主轴转速为等比数列,其公比ψ=1.58,主轴最高转速n max=4000r/min,主轴转速级数Z=10,电动机转速 为1440r/min,试拟定合理的转速图,确定齿轮齿数,画出主传动系统图。
⒏变速箱齿轮布置时如何缩短轴向尺寸和径向尺寸? 缩短轴向尺寸的方法:①把三联齿轮一分为二,②把两个传动组统一安排; 缩短径向尺寸的方法:①缩短轴间距离,②采用轴线相互重合方式,③相邻各轴在横剖面图上布置成三角形,④在 一个传动组内取最大传动比等于最小传动比的倒数。
四⒈主轴组件应满足哪些基本要求? 旋转精度:在无载荷、低转速的条件下,主轴的轴向和径向跳动; 刚度:指在外加载荷的作用下抵抗变形的能力; 抗振性:抵抗受迫振动和自激振动; 温升和热变形:对温升有一定限制,以保证热变形的范围; 精度保持性:指长期保持其原始制造精度的能力。
⒉简述主轴常用滚动轴承的类型及其特点。
①圆锥孔双列圆柱滚子轴承:线接触,滚子数多,承载能力较大; ②滚子轴承:滚子是中空的,润滑油可从中流过,冷却滚子,减小温升,并由一定减振效果; ③双向推力角接触球轴承:接触角大,钢球直径较小而数量较多,轴承承载能力和精度较高,极限转速较高,温升 低,运转平稳和工作可靠; ④角接触球轴承:极限转速较高; ⑤陶瓷滚动轴承:压力和滑动摩擦小,滚动体胀系数小,温升较低,弹性模量大,轴承的刚度大; ⑥磁浮轴承:无机械磨损,理论上无速度限制,无噪声,温升小,能耗低,环保,适用于多种环境。
⒊主轴轴承的配置形式主要有哪几种?各适用于什么场合? ①速度型:主轴前后轴承都采用角接触球轴承,适用于高速轻载或精密机床; ②刚度型:前支承采用双列短圆柱滚子轴承和60°角接触双列向心推力球轴承,后支承采用双列短圆柱滚子轴承, 适用于中等转速和切削负载较大、要求刚度高的机床; ③刚度速度型:前轴承采用三联角接触球轴承,后支承采用双列短圆柱滚子轴承,适用于径向刚度好、有较高转速 的机床。
⒋简述双列短圆柱滚子轴承的间隙调整方法。
(通过螺母经中间隔套,轴向移动内圈来实现。
——老师说的) 采用轴承内圈膨胀径向预紧方式。
①从左面压内圈,结构简单,控制调整量难,预紧过大时松卸不方便; ②用右边螺母控制调整量,调整方便,但主轴前端需要有螺纹才能实现,工艺性差; ③用螺钉代替控制螺母,主轴前端需要螺孔,工艺性好,但当力不一致时,影响旋转精度; ④将右边隔套制成两半,可取下来修磨其宽度,以便控制其调整量。
⒌主轴滚动轴承必须预紧的原因是什么?常用的预紧方式有哪些? 原因:使轴承滚道预先承受一定的载荷,消除间隙,并使得滚动体与滚道之间发生一定的变形,增大接触面积,轴 承受力时变形减小,抵抗变形的能力增大,提高轴的回转精度和抗振性。
方式:①径向预紧方式,②轴向预紧方式。
⒎采用什么方法可以使用较低精度等级的滚动轴承装配出较高旋转精度的机床主轴组件?⒐主轴为何需要“准停”?如何实现“准停”? “准停”便于机械手对刀具的装夹,提高定位精度;电磁吸附可实现“准停”。
五⒈数控机床对进给伺服系统的要求是什么? 精度要求:必须保证机床的定位精度和加工精度; 响应速度:要求跟踪指令信号的响应要快; 调速范围:指生产机械要求电动机能提供的最高转速和最低转速之比; 低速、大转矩:在低速下进给驱动系统必须有大的转矩输出。
[⒉试说明开环伺服进给系统与闭环伺服进给系统的区别,各有什么优点? 开环伺服进给系统:由步进电动机及其驱动线路等组成,系统中没有位置检测器和反馈路线,精度较差; 优点是结构简单、易于调整,精度要求不太高; 闭环伺服进给系统:由伺服电动机、检测装置、比较电路、伺服放大系统等部分组成,精度较高; 优点是能实现精度高的反馈控制。
⒊数控机床为什么要采用滚珠丝杠螺母副作为传动元件?它有什么特点? 因为它的存在使丝杠与螺母之间是滚动摩擦,仅在滚珠之间存在滑动摩擦; 特点是:①摩擦损失小、传动效率高,②运动平稳、摩擦力小、灵敏度高、低速时无爬行,③轴向刚度高、反向定 位精度高,④磨损小、寿命长、维护简单,⑤传动具有可逆性、不能自锁,⑥同步性好,⑦有专业厂生产, 选用配套方便。
⒋滚珠丝杠螺母副的滚珠循环方式可分为哪两类?结构有何区别?各应用于哪些场合? 分为内循环和外循环;内循环结构为单圈循环,外循环结构为多圈循环;⒌滚珠丝杠螺母副为什么要预紧?具体有哪几种调整间隙的预紧方法? 为了消除间隙、提高传动刚度; 调整间隙的预紧方法:①垫片调隙式,②螺纹调隙式,③齿差调隙式。
⒍滚珠丝杠螺母副为什么要预拉伸?试说明预拉伸的具体操作方法。
为了消除内应力;⒎数控机床消除齿侧间隙的方法有哪些?各用在什么场合? ①偏心轴套调整法:用于电动机与丝杠之间的齿轮传动; ②变齿厚圆柱齿轮调整法: ③斜齿轮轴向垫片调整法:用于承载力低的场合; ④双片直齿轮错齿调整法: ⑤轴向弹簧调整法: ⑥锥齿轮双齿错齿调整法:用于轻载齿轮; ⑦双齿轮弹簧预紧调整法:用于工作行程较大的大型数控机床。