聚氨酯配方系列—回弹性高的聚氨酯泡沫参考配方
聚氨酯配方系列—回弹性高的聚氨酯泡沫参考配方

聚氨酯制品参考配方系列—回弹性高的聚氨酯泡沫配方有制备高回弹泡沫时,有机多异异氰酯、高分子量多元醇、催化剂、发泡剂、泡沫稳定剂等原料中,可加入高分子量四官能度聚醚多元醇,制得的泡沫回弹性高。
工艺参数液温℃----------------------------------------25硫化温度,℃----------------------------------70硫化时间,分----------------------------------5模具温度,℃----------------------------------55—60℃多元醇多元醇A-1:聚氧化乙烯氧化丙烯甘油醚多元醇,羟值31,末端环氧乙烷付加量为16%。
多元醇A-2:聚氧化乙烯氧化丙烯甘油醚多元醇,羟值28,末端环氧乙烷付加量为16%。
多元醇A-3:聚氧化乙烯氧化丙烯甘油醚多元醇,羟值24,末端环氧乙烷付加量为14%。
多元醇B-1:季戊四醇为起始剂,先加入环氧丙烷,再加入环氧乙烷,聚合反应后制得聚醚多元醇,羟值35,末端环氧乙烷付加量为10%。
多元醇B-2:季戊四醇为起始剂,先加入环氧丙烷,再加入环氧乙烷,聚合反应后制得聚醚多元醇,羟值32,末端环氧乙烷付加量为12%。
多元醇B-3:季戊四醇为起始剂,先加入环氧丙烷,再加入环氧乙烷,聚合反应后制得聚醚多元醇,羟值28,末端环氧乙烷付加量为10%。
多元醇C-1:甘油和环氧丙烷、环氧乙烷(末端付加量14%)所得的羟值33的聚醚多元醇100份,与丙烯腈25份,在130℃,1份偶氮二异丁腈作起始剂,制得羟值27的多元醇。
多元醇C-2:多元醇A-2-100份和丙烯腈27份,苯乙烯15份,0.2份二(4特丁环己基)过氧化二羧酸酯作起始剂,在120℃反应制得羟值20的多元醇。
多元醇C-3:多元醇B-2-100份和丙烯腈27份、苯乙烯15份,在120℃反应制得羟值22的多元醇。
配方原料------------------------------------------重量份数多元醇A-1------------------------------30多元醇A-2--------------------------------------30多元醇A-3-----------------------------------------------30多元醇B-1------------------------------30多元醇B-2--------------------------------------30多元醇B-3-----------------------------------------------30多元醇C-1------------------------------40------40-------40三乙醇胺--------------------------------4-------4--------4水--------------------------------------3.0-----3.0------3.0DABCO-33LV-----------------------------0.4-----0.4------0.4Polycat41------------------------------0.1-----0.1------0.1硅油5309-------------------------------0.3-----0.3------0.3硅油SRX-274C---------------------------0.4-----0.4------0.4TDI80/29和聚MDI混合物-----------------46.2----45.9-----45.5 (重量比为8/2)异氰酸酯指数----------------------------105-----105------105性能整体密度,kg/m-³-------------------------48.8----48.7-----49.0 芯密度,-kg/m-³--------------------------42.8----42.7-----42.9 拉伸强度,kg/cm²-------------------------1.33----1.39-----1.41 伸长率,%--------------------------------90------96-------110 撕裂强度,kg/cm--------------------------0.62----0.63-----0.64 25%ILD(4英寸),kg/314cm²----------------22.2----21.2-----17.0 压缩永久变形,%--------------------------3.2-----3.2-------3.8 湿热变定,%------------------------------12.0----12.8------13.3 回弹率,%--------------------------------75------76--------75以上内容仅供参考,来源/华南聚氨酯原料商城。
聚氨酯软泡配方

聚氨酯软泡的配方因所需硬度、密度和弹性等特性而异,以下提供了三种不同配方的聚氨酯软泡:
1、密度为8kg/立方米的软泡配方:
聚醚:100份
水:7份
硅油:2.8份
辛酸亚锡:0.7份
胺催化剂:0.17份
二氯甲烷:30份
TDI指数:117(即79.7+8.7=76.61.17=89.6)
2、密度为12kg/立方米的软泡配方:
聚醚:100份
水:6份
硅油:1.5份
辛酸亚锡:0.3份
胺催化剂:0.14份
二氯甲烷:15份
TDI指数:120
3、密度为16kg/立方米的软泡配方:
聚醚:100份
水:4.9份
硅油(l-580):1.3份
辛酸亚锡:0.3份
a33催化剂:0.12份
二氯甲烷:9.3份
填料:8份
TDI指数:62
这些配方仅供参考,实际生产中可能因材料品牌、环境温度和湿度等因素有所调整。
建议在专业人士指导下进行操作。
一种高回弹聚氨酯软泡配方

一种高回弹聚氨酯软泡配方以下是一种高回弹聚氨酯软泡配方:材料:1.聚氨酯预聚体(TDI、MDI等)-60%2. 聚醚多元醇(Polyol)- 40 %3.化学发泡剂-1-2%4.催化剂-0.1-0.5%5.稳定剂-0.5-1%步骤:1. 准备聚醚多元醇(Polyol):-将适量的聚醚多元醇加入聚氨酯发泡机的反应器中。
-调整反应器的温度至适宜的反应温度(通常在30-60摄氏度之间)。
-添加适量的稳定剂,并搅拌混合均匀。
2.准备聚氨酯预聚体:-将适量的聚氨酯预聚体(TDI、MDI等)加入聚醚多元醇中。
-继续搅拌混合,确保预聚体和多元醇均匀混合。
3.添加化学发泡剂:-将适量的化学发泡剂加入反应器中,并搅拌均匀。
-发泡剂将在反应过程中释放出气体,形成泡沫结构。
4.添加催化剂:-将适量的催化剂加入反应器中。
-催化剂可以加速聚合反应,促进泡沫形成。
-搅拌反应器,确保催化剂均匀分布。
5.反应和固化:-将反应器封闭,并控制温度和压力,以促进聚合反应和固化。
-反应时间根据材料的特性和要求,通常为数分钟到数小时。
-一般会使用压力来控制密度和回弹性,通常在0.1-1兆帕(MPa)之间。
6.制备和整形:-将固化的聚氨酯软泡从反应器中取出,并切割成所需的形状和尺寸。
-装配和安装所需的材料,如家具、汽车座椅等。
注意事项:-在操作过程中,必须注意个人防护措施,如佩戴手套和防护眼镜。
-根据实际需要和要求,可以根据上述配方进行适当调整。
这种高回弹聚氨酯软泡配方可用于各种应用,如座椅、垫子、枕头等。
配方的具体比例和材料类型可能会根据应用的要求而有所不同。
因此,在实际生产中,需要根据具体需求进行配方的调整和优化。
高回弹模塑发泡配方
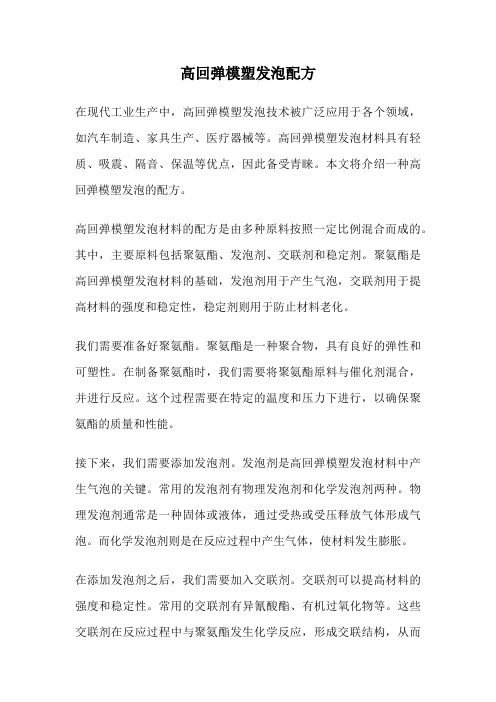
高回弹模塑发泡配方在现代工业生产中,高回弹模塑发泡技术被广泛应用于各个领域,如汽车制造、家具生产、医疗器械等。
高回弹模塑发泡材料具有轻质、吸震、隔音、保温等优点,因此备受青睐。
本文将介绍一种高回弹模塑发泡的配方。
高回弹模塑发泡材料的配方是由多种原料按照一定比例混合而成的。
其中,主要原料包括聚氨酯、发泡剂、交联剂和稳定剂。
聚氨酯是高回弹模塑发泡材料的基础,发泡剂用于产生气泡,交联剂用于提高材料的强度和稳定性,稳定剂则用于防止材料老化。
我们需要准备好聚氨酯。
聚氨酯是一种聚合物,具有良好的弹性和可塑性。
在制备聚氨酯时,我们需要将聚氨酯原料与催化剂混合,并进行反应。
这个过程需要在特定的温度和压力下进行,以确保聚氨酯的质量和性能。
接下来,我们需要添加发泡剂。
发泡剂是高回弹模塑发泡材料中产生气泡的关键。
常用的发泡剂有物理发泡剂和化学发泡剂两种。
物理发泡剂通常是一种固体或液体,通过受热或受压释放气体形成气泡。
而化学发泡剂则是在反应过程中产生气体,使材料发生膨胀。
在添加发泡剂之后,我们需要加入交联剂。
交联剂可以提高材料的强度和稳定性。
常用的交联剂有异氰酸酯、有机过氧化物等。
这些交联剂在反应过程中与聚氨酯发生化学反应,形成交联结构,从而提高材料的力学性能。
我们需要加入稳定剂。
稳定剂可以防止材料老化和分解。
常用的稳定剂有抗氧化剂、紫外线吸收剂等。
这些稳定剂可以与聚氨酯形成化学键,阻止氧气和紫外线对材料的损害。
通过以上的配方,我们可以得到高回弹模塑发泡材料。
这种材料具有良好的回弹性和强度,可以广泛应用于各个领域。
总结起来,高回弹模塑发泡配方主要包括聚氨酯、发泡剂、交联剂和稳定剂。
这些原料经过一系列的反应和混合,最终形成高回弹模塑发泡材料。
这种材料具有轻质、吸震、隔音、保温等优点,被广泛应用于工业生产中。
随着技术的不断发展,高回弹模塑发泡材料的配方也在不断优化,以满足不同领域的需求。
聚氨酯制品参考配方系列—冷固化高回弹聚氨酯泡沫
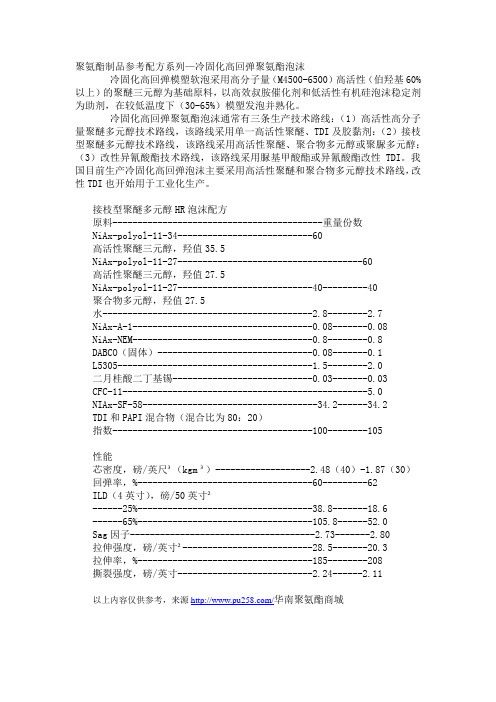
聚氨酯制品参考配方系列—冷固化高回弹聚氨酯泡沫冷固化高回弹模塑软泡采用高分子量(M4500-6500)高活性(伯羟基60%以上)的聚醚三元醇为基础原料,以高效叔胺催化剂和低活性有机硅泡沫稳定剂为助剂,在较低温度下(30-65%)模塑发泡并熟化。
冷固化高回弹聚氨酯泡沫通常有三条生产技术路线:(1)高活性高分子量聚醚多元醇技术路线,该路线采用单一高活性聚醚、TDI及胶黏剂:(2)接枝型聚醚多元醇技术路线,该路线采用高活性聚醚、聚合物多元醇或聚脲多元醇:(3)改性异氰酸酯技术路线,该路线采用脲基甲酸酯或异氰酸酯改性TDI。
我国目前生产冷固化高回弹泡沫主要采用高活性聚醚和聚合物多元醇技术路线,改性TDI也开始用于工业化生产。
接枝型聚醚多元醇HR泡沫配方原料------------------------------------------重量份数NiAx-polyol-11-34---------------------------60高活性聚醚三元醇,羟值35.5NiAx-polyol-11-27-------------------------------------60高活性聚醚三元醇,羟值27.5NiAx-polyol-11-27---------------------------40---------40聚合物多元醇,羟值27.5水------------------------------------------2.8--------2.7NiAx-A-1------------------------------------0.08-------0.08NiAx-NEM------------------------------------0.8--------0.8DABCO(固体)-------------------------------0.08-------0.1L5305---------------------------------------1.5--------2.0二月桂酸二丁基锡----------------------------0.03-------0.03CFC-11-------------------------------------------------5.0NIAx-SF-58-----------------------------------34.2------34.2TDI和PAPI混合物(混合比为80:20)指数----------------------------------------100--------105性能芯密度,磅/英尺³(kgm-³)-------------------2.48(40)-1.87(30)回弹率,%-----------------------------------60---------62ILD(4英寸),磅/50英寸²------25%-----------------------------------38.8-------18.6------65%-----------------------------------105.8------52.0Sag因子-------------------------------------2.73-------2.80拉伸强度,磅/英寸²--------------------------28.5-------20.3拉伸率,%-----------------------------------185--------208撕裂强度,磅/英寸---------------------------2.24------2.11以上内容仅供参考,来源/华南聚氨酯商城。
一种高回弹聚氨酯软泡配方

一种高回弹聚氨酯软泡配方以下是一种高回弹聚氨酯软泡配方,详情如下:原材料:1.聚醚多元醇:用作聚氨酯软泡的主要基材,可选择聚醚氧化物或聚醚醇。
2.异氰酸酯(TDI或MDI):用作活性聚氨酯预聚体的异氰酸酯。
3.含水聚醇:用于瞬间产生二氧化碳和硬化反应,形成气泡并使软泡膨胀。
4.填充材料:可选择轻质粉末如滑石粉、珍珠岩粉末等,用于改善软泡的物理性能。
5.催化剂:用于加速聚氨酯硬化反应的发生。
6.稳定剂:用于防止氧化和增强软泡的耐久性。
7.发泡剂:用于产生气泡和软泡的膨胀。
配方如下:1.主聚醚多元醇:根据需要选择合适的主聚醚多元醇,并根据软泡的硬度要求确定用量。
一般来说,主聚醚多元醇的含量在整个配方中约为20-40%。
2.异氰酸酯(TDI或MDI):根据需要选择合适的异氰酸酯,并根据软泡的硬度要求确定用量。
异氰酸酯的含量在整个配方中约为20-40%。
3.含水聚醇:根据需要选择合适的含水聚醇,并根据软泡的回弹性要求确定用量。
含水聚醇的含量在整个配方中约为10-20%。
4.填充材料:根据需要选择合适的填充材料,并根据软泡的物理性能要求确定用量。
填充材料的含量在整个配方中约为10-20%。
5.催化剂:根据软泡的硬化速度要求选择合适的催化剂,并根据软泡的物理性能要求确定用量。
催化剂的含量在整个配方中约为0.5-2%。
6.稳定剂:根据软泡的耐久性要求选择合适的稳定剂,并根据软泡的物理性能要求确定用量。
稳定剂的含量在整个配方中约为0.1-0.5%。
7.发泡剂:根据软泡的膨胀要求选择合适的发泡剂,并根据软泡的物理性能要求确定用量。
发泡剂的含量在整个配方中约为1-5%。
以上配方根据软泡的硬度、回弹性、物理性能和耐久性要求而定,可以根据实际情况进行适当调整。
使用时,请遵循相关安全操作规程,确保自身安全及产品质量。
聚氨酯泡沫塑料的配方设计
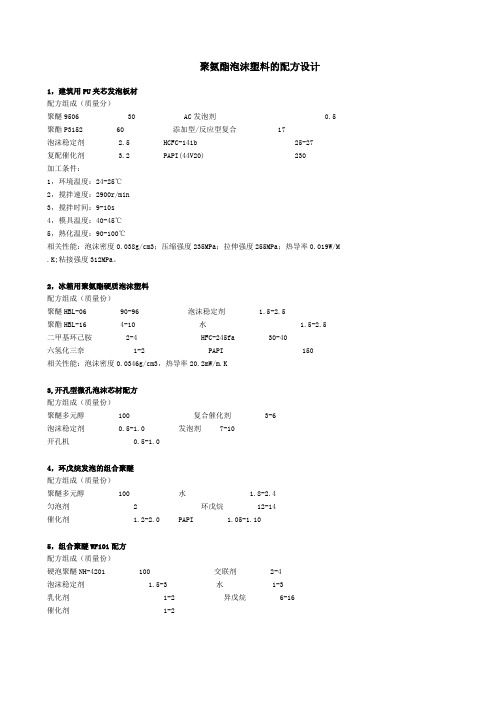
聚氨酯泡沫塑料的配方设计1,建筑用PU夹芯发泡板材配方组成(质量分)聚醚9506 30 AC发泡剂 0.5 聚酯P3152 60 添加型/反应型复合 17泡沫稳定剂 2.5 HCFC-141b 25-27复配催化剂 3.2 PAPI(44V20) 230加工条件:1,环境温度:24-25℃2,搅拌速度:2900r/min3,搅拌时间:9-10s4,模具温度:40-45℃5,熟化温度:90-100℃相关性能:泡沫密度0.038g/cm3;压缩强度235MPa;拉伸强度255MPa;热导率0.019W/M .K;粘接强度312MPa。
2,冰箱用聚氨酯硬质泡沫塑料配方组成(质量份)聚醚HBL-06 90-96 泡沫稳定剂 1.5-2.5聚酯HBL-16 4-10 水 1.5-2.5二甲基环己胺 2-4 HFC-245fa 30-40六氢化三奈 1-2 PAPI 150相关性能:泡沫密度0.0346g/cm3,热导率20.2mW/m.K3,开孔型微孔泡沫芯材配方配方组成(质量份)聚醚多元醇 100 复合催化剂 3-6泡沫稳定剂 0.5-1.0 发泡剂 7-10开孔机 0.5-1.04,环戊烷发泡的组合聚醚配方组成(质量份)聚醚多元醇 100 水 1.8-2.4匀泡剂 2 环戊烷 12-14催化剂 1.2-2.0 PAPI 1.05-1.105,组合聚醚WF101配方配方组成(质量份)硬泡聚醚NH-4201 100 交联剂 2-4泡沫稳定剂 1.5-3 水 1-3乳化剂 1-2 异戊烷 6-16催化剂 1-26,复合面料泡沫垫配方组成(质量份)聚醚三元醇(MN=6000) 100 有机硅表面活性剂 0.5山梨醇聚醚多元醇 1 水 3.2胺催化剂NIAX-1 0.18 MDI 52胺催化剂NIAX-4 0.45 异氰酸酯 1007,软质PU泡沫塑料配方组成(质量份)1# 2# 3# 4# 5# 6#聚醚多元醇 100 100 100 100 100 100异氰酸酯 37.5 51.1 51.1 53.5 51.1 64.6水 2.7 4.0 4.0 4.2 4.0 5.0F11硅油表面活性剂 0.8 0.9 0.9 1.1 1.1 1.3胺催化剂 0.1 0.12 0.1 0.12 0.15 0.15锡催化剂 0.2 0.24 0.24 0.21 0.25 0.25相对密度 0.034 0.028 0.026 0.024 0.020 0.020拉伸强度 0.11 0.10 0.10 0.09 0.08 0.05伸长率 130 120 140 145 160 75压缩变形 3.5 5.0 5.5 4.8 6.9 5.88,聚醚型块状PU软质泡沫塑料配方组成(质量份)聚醚三元醇 100 泡沫稳定剂 0.1TDI80/20 45-47 水 3-4有机锡 0.3-0.5 F-11 0-15叔胺 0.2-0.3相关性能:相对密度0.02-0.025;拉伸强度0.09-0.1MPa;撕裂强度0.3-0.4KN/m;伸长率200%-500%;50$%压缩强度0.006MPa;落球回弹率35-40%9,PU硬质泡沫塑料(配方组成)质量份喷涂配方浇注配方喷涂配方浇注配方2型阻燃醚 100 100 F11 80 -403聚醚70 18 TCEP(发泡剂) 80 6泡沫稳剂 5 5 水-6有机锡0.8 0.1 PAPI 290 1 97三乙烯二胺/乙二醇 8 --10,聚氨酯泡沫塑料配方组成(质量份)聚醚100;硅油1-4; PAPI 140-180;三乙醇胺0.7-1.5;蒸馏水0.4-1.5。
一种高回弹聚氨酯软泡配方

一种高回弹聚氨酯软泡配方
当今市场上有许多种聚氨酯软泡配方,形式各异,从低伸长到高回弹,从廉价到昂贵,广泛应用于家具、软包、鞋垫、乘坐装置、汽车座椅垫、各种体育设施上。
本文中,我们
将介绍一种高回弹聚氨酯软泡配方。
在制作高回弹聚氨酯软泡配方时,首先要确定所需要用的原料和比例,搭配起来主要
有固体聚氨酯、增塑剂、催化剂等原料,比例为20%固体聚氨酯、4%催化剂、76%增塑剂。
然后我们需要准备一个搅拌机,将上述原料放入搅拌机中混合攪拌,调节搅拌机的搅
拌速度,使混合物完全搅拌均匀,达到最好的配制状态,在搅拌过程中可以添加各种聚氨
酯凝胶,来加强硬度以及促进泡沫的发泡效果。
接着,准备一个压延机,将面粉轻轻地撒在压延机上,配制好的混合物放入压延机中,将两者结合压延,使其表面光滑,增加贴合面粉效果,也可以进行材料修边。
最后,准备木丸子和滚压机,将面粉修边后放入木丸子中,用滚压机将其压型,彻底
滚压,使其表面均一细腻,可以让聚氨酯软泡更加抗压性更强,回弹更好,由此我们就可
以制作出一款高回弹的聚氨酯软泡了!
通过以上步骤,我们就可以制作出一种高回弹聚氨酯软泡配方,该产品具有舒适性好、可快速回弹、防滑防滚性能良好等优点,广泛应用于家具、软包、鞋垫、乘坐装置、汽车
座椅垫、各种体育设施上。
另外,它还可以在应用过程中,提供出软质的触感、高耐压度
和回弹力,可以缓和人体的负荷,使您享受更舒适的座椅体验。
聚氨酯实用配方(详细含硅油小料配比)

聚氨酯硬泡配方计算方法(实用)一:硬泡组合料里最需要计算的东西是黑白料比例(重量比)是不是合理,另一个正规的说法好像叫“异氰酸指数”是否合理,翻译成土话就是“按重量比例混合的白料和黑料要完全反应完”。
因此,白料里所有参和跟-NCO反应的东西都应该考虑在内。
理论各组分消耗的-NCO摩尔量计算如下㈠主料:聚醚、聚酯、硅油(普通硬泡硅油都有羟值,因为加了二甘醇之类的稀释,部分泡沫稳定剂型硅油还含有氨基)配方数乘以各自的羟值,然后相加得数Q,S1 = Q÷56100㈡水:水的配方量W S2 = W÷9㈢参和消耗-NCO的小分子物:配方量为K,其分子量为M,官能度为N S3 =K× N/M(用了两种以上小分子的需要各自计算再相加) S = S1+S2+S3 基础配方所需粗MDI份量[(S×42)÷0.30 ] ×1.05 (所谓异氰酸指数1.05)其实以上计算只是一个最基本的消耗量,由于黑白料反应过程复杂,实际-NCO消耗量肯定不止这个数,比如有三聚催化剂的情况,到底额外消耗了多少-NCO,这个没人说得清楚。
另外,聚醚里有水分,偏高0.1%就很严重;聚醚羟值也是看人家宣传单的,我见过有聚醚羟值范围跨度90mgKOH/g,那个计算数出来后只能参考,不能认真![试验设计]之“冰箱、冷柜”类本组合料体系重要要求及说明1、流动性要好,密度分布“尽量”均匀。
首先要考虑粘度,只有体系粘度小了,初期流动性才会好(主份平均粘度6000mPa.S以下,组合料350mPa.S以下),其次体系中的钾、钠杂离子要控制在一个低限(20ppm以内),从而可控制避免三聚反应提前,即:体系粘度过早变大。
如果流动性欠佳,发泡料行进至注料口远端就会出现拉丝痕致使泡孔结构橄榄球化,这个位置一定抗不住低温收缩。
2、泡孔细密,导热系数要低。
不难理解泡孔细密是导热系数低的第一前提,此时首先考虑加有403或某些芳香胺醚进入体系(它们所起的作用是首先和-NCO反应,其生成物和其它组份互溶、乳化稳定性提升,并保证发泡体系初期成核稳定,也就是避免迸泡,从而使泡孔细密)其次聚醚本身单独发泡其泡孔结构要好(例如以山梨醇为起始的635SA比蔗糖为起始的1050泡孔要细密均匀得多,还有含有甘油为起始剂的835比1050细密,即便是所谓的4110牌号的聚醚,含丙二醇起始的比二甘醇的好。
聚氨酯发泡胶生产配方
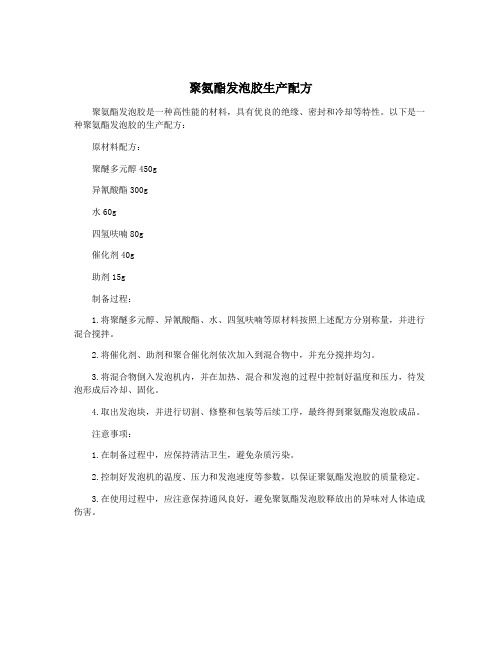
聚氨酯发泡胶生产配方
聚氨酯发泡胶是一种高性能的材料,具有优良的绝缘、密封和冷却等特性。
以下是一种聚氨酯发泡胶的生产配方:
原材料配方:
聚醚多元醇450g
异氰酸酯300g
水60g
四氢呋喃80g
催化剂40g
助剂15g
制备过程:
1.将聚醚多元醇、异氰酸酯、水、四氢呋喃等原材料按照上述配方分别称量,并进行混合搅拌。
2.将催化剂、助剂和聚合催化剂依次加入到混合物中,并充分搅拌均匀。
3.将混合物倒入发泡机内,并在加热、混合和发泡的过程中控制好温度和压力,待发泡形成后冷却、固化。
4.取出发泡块,并进行切割、修整和包装等后续工序,最终得到聚氨酯发泡胶成品。
注意事项:
1.在制备过程中,应保持清洁卫生,避免杂质污染。
2.控制好发泡机的温度、压力和发泡速度等参数,以保证聚氨酯发泡胶的质量稳定。
3.在使用过程中,应注意保持通风良好,避免聚氨酯发泡胶释放出的异味对人体造成伤害。
聚氨酯配方

聚氨酯床垫配方及性能①为非芳香族的胺类催化剂。
②为改性的甲苯二异氰酸酯。
③60%的MDI与40% 的TDI (65/35)的混合物。
半硬泡自结皮PU泡沫配方配方组成(质量份)1# 2# 3# 4#聚醚多元醇100 100 100 100乙二醇7 -- 7 --1,4丁二醇-- 8 -- 8三亚乙基二胺 1.5 1.5 1.5 1.5F11 17 17 17 17液化MDI(1040指数)30-40(105) 30-40(105)液化MDI(1050指数)30-40(105) 30-40(105) 低密度低硬度高回弹PU泡沫塑料配方组成(质量份)1# 2# 聚醚100 100 水 2.4 2.4 二乙醇胺 1 2二(2-二甲胺基乙基)醚0.06 0.06 硅泡沫稳定剂0.06 0.06 T9 0.10 0.15 F11 5 5 TDI8020 30-50(103) 30-50(103)高回弹海绵配方供参考高活性聚醚多元醇....................100份TDl........................................43.4份DEOA....................................1.5份水.........................................3.5份L5333...................................1.0份A230.....................................0.23份D22.......................................0.04份慢回弹枕头配方1030=40330=503628=10水=3A33=0.8DMEA=0.52乙=1.5A1=0.153002=0.8141B=25TDI/MDI=2:1聚氨酯高回弹MDI组合料配方A33--0.3DMEA--0.62乙--0.53乙--0.3141B--1.5H20--0.155596-5005=3比1中硬度高回弹PU配方配方组成(质量份)1# 2#聚醚100 100水 2.4 2.8二乙醇胺 1.2 1二(2-二甲胺基乙基)醚0.08 0.08硅泡沫稳定剂0.4 0.4T9 0.15 0.15TDI8020 30-40(110)30-40(110)密度为8kg/m3 的软泡配方配方原料重量份数聚醚三元醇,羟值56 100水 6.6三乙烯二胺(33 %溶液) 0.18TEGOSTAB B8110硅油 3.8(非水介性的聚硅烷一聚氧烷共聚物高活性泡沫稳定剂,高施米特公司产品)幸酸亚锡0.4二氯甲烷34TDI 80/20 103密度,kg/m3 8低密度自结皮配方(座椅用)330N:55POP:45EG: 6A33:0.3DMEA: 0.45TEOA: 0.85A-1: 0.2B8681:0.5H20: 0.3141B: 12NE-113:48~50聚氨酯床垫的配方聚氨酯床垫配方及性能生产方式聚醚型“冷熟化”模塑软泡聚醚型“冷熟化”模塑软泡用途作各种坐垫作全泡沫家具配方/份聚醚(分子量为3000)100 聚醚(分子量为4800) 100 水3 水2.5三亚乙基二胺0.3 稳定剂1三乙胺0.4 三乙醉胺1交联剂①0.6 三乙胺0.4稳定剂1 三亚乙基二胺0.2异氰酸酯②46.4 异氰酸酯③39性能密度/(kg/cm3) 43 密度/(kg/cm3) 40拉伸强度/MPa 0.06 拉伸强度/MPa 0.06伸长率/% 135 伸长率/% 90压缩负荷(40%)/Pa 2352 压缩负荷(40%)/Pa 2156压缩变形(90%)/% 4.1 压缩变形(90%)/% 3回弹率/% 62 回弹率/% 70①为非芳香族的胺类催化剂。
一种耐高温高回弹聚氨酯泡沫组合物及其制备方法与流程
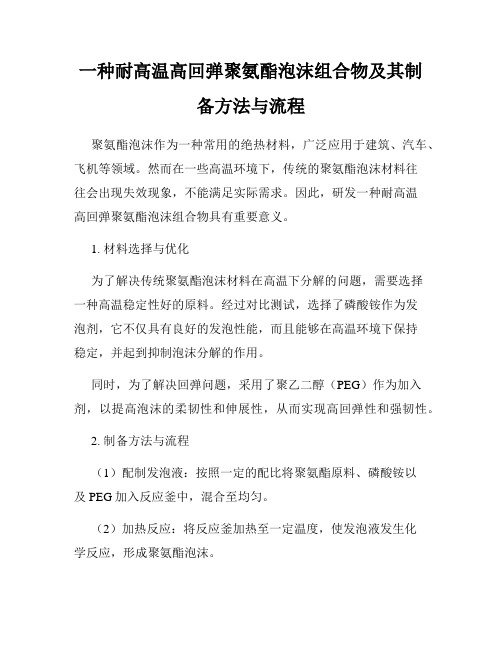
一种耐高温高回弹聚氨酯泡沫组合物及其制
备方法与流程
聚氨酯泡沫作为一种常用的绝热材料,广泛应用于建筑、汽车、飞机等领域。
然而在一些高温环境下,传统的聚氨酯泡沫材料往
往会出现失效现象,不能满足实际需求。
因此,研发一种耐高温
高回弹聚氨酯泡沫组合物具有重要意义。
1. 材料选择与优化
为了解决传统聚氨酯泡沫材料在高温下分解的问题,需要选择
一种高温稳定性好的原料。
经过对比测试,选择了磷酸铵作为发
泡剂,它不仅具有良好的发泡性能,而且能够在高温环境下保持
稳定,并起到抑制泡沫分解的作用。
同时,为了解决回弹问题,采用了聚乙二醇(PEG)作为加入剂,以提高泡沫的柔韧性和伸展性,从而实现高回弹性和强韧性。
2. 制备方法与流程
(1)配制发泡液:按照一定的配比将聚氨酯原料、磷酸铵以
及PEG加入反应釜中,混合至均匀。
(2)加热反应:将反应釜加热至一定温度,使发泡液发生化
学反应,形成聚氨酯泡沫。
(3)冷却固化:将发泡后的聚氨酯泡沫通过机械方式切割成所需尺寸,然后在室温下进行冷却固化处理。
3. 性能测试与实际应用
将研制得到的聚氨酯泡沫组合物进行性能测试,结果显示其耐高温性良好,可以在500℃下保持结构稳定,且具有高回弹性和较强的强度。
实际应用中,该组合物可以用于航空航天、高速列车等领域,能够有效提高设备的绝热性能和使用寿命。
总之,研制一种耐高温高回弹聚氨酯泡沫组合物不仅解决了传统泡沫材料易出现失效现象的问题,同时也拓展了其在高温环境下的应用范围,具有重要的应用前景和经济效益。
聚氨酯实用配方(详细含硅油小料配比)

聚氨酯实用配方(详细含硅油小料配比)聚氨酯硬泡配方计算方法(实用)一:硬泡组合料里最需要计算的东西是黑白料比例(重量比)是不是合理,另一个正规的说法好像叫“异氰酸指数”是否合理,翻译成土话就是“按重量比例混合的白料和黑料要完全反应完”。
因此,白料里所有参与跟-NCO反应的东西都应该考虑在内。
理论各组分消耗的-NCO摩尔量计算如下㈠主料:聚醚、聚酯、硅油(普通硬泡硅油都有羟值,因为加了二甘醇之类的稀释,部分泡沫稳定剂型硅油还含有氨基)配方数乘以各自的羟值,然后相加得数Q,S1 = Q÷56100㈡水:水的配方量W S2 = W÷9㈢参与消耗-NCO的小分子物:配方量为K,其分子量为M,官能度为N S3 =K× N/M(用了两种以上小分子的需要各自计算再相加) S = S1+S2+S3 基础配方所需粗MDI份量[(S×42)÷0.30 ] ×1.05 (所谓异氰酸指数1.05)其实以上计算只是一个最基本的消耗量,由于黑白料反应过程复杂,实际-NCO消耗量肯定不止这个数,比如有三聚催化剂的情况,到底额外消耗了多少-NCO,这个没人说得清楚。
另外,聚醚里有水分,偏高0.1%就很严重;聚醚羟值也是看人家宣传单的,我见过有聚醚羟值范围跨度90mgKOH/g,那个计算数出来后只能参考,不能认真![试验设计]之“冰箱、冷柜”类本组合料体系重要要求及说明1、流动性要好,密度分布“尽量”均匀。
首先要考虑粘度,只有4、相溶性。
指“聚醚、聚酯/硅油/水/催化剂/物理发泡剂”所组成的体系要互溶性好,均相稳定-----至少存放一段时间不能分层。
1)官能度构成及骨架类型。
原则上说官能度越高,所发泡体的物理性能数值(尺寸稳定、抗压强度等)就越“理想”,但往往官能度高的聚醚粘度偏大(多挂PO也能降低粘度,价格又下不来),所以,平均一下,4个官能度马马虎虎可以对付了;另外,如果聚醚体系中有芳香结构(苯环)引入,无疑也会提升泡体的物理性能。
聚氨酯弹性体参考配方

聚氨酯弹性体参考配方配方如下:1.聚酯多元醇:60-70份2.异佛尔酮二异氰酸酯(TDI):30-40份3.链延长剂:2-3份4.稳定剂:0.2-0.5份5.催化剂:0.5-1份6.塑料化剂:根据需要添加聚酯多元醇是聚氨酯制备的主要原料,可以选择聚酯多元醇根据需要的性能来确定。
常用的聚酯多元醇有聚酯多元醇A、聚酯多元醇B等。
聚酯多元醇具有良好的柔软性、耐磨性和低温性能。
异佛尔酮二异氰酸酯(TDI)是聚氨酯制备的硬段原料,可以通过调整其用量来控制聚氨酯材料的硬度和弹性。
在配方中,可以根据需要将TDI分为两个部分添加,一部分作为预聚体与聚酯多元醇反应,另一部分作为链延长剂与预聚体反应,从而得到所需的硬度和弹性。
链延长剂用于调节聚氨酯材料的分子量和柔软性,一般选择具有双官能团的分子作为链延长剂。
常用的链延长剂有乙二醇、丁二醇等。
稳定剂用于提高聚氨酯材料的稳定性,防止氧化和黄变等现象的发生。
可以选择有机锡化合物等作为稳定剂。
催化剂用于促进聚氨酯材料的硬化反应,常用的催化剂有二甲苯胺(DMA)、四乙基二氮唑(DABCO)等。
塑料化剂可以根据需要添加,用于调节聚氨酯材料的流动性和柔软性。
常用的塑化剂有聚醚、聚乙烯醇等。
配方制备过程如下:1.将聚酯多元醇、TDI和链延长剂按照配方比例混合搅拌,使其均匀混合。
2.添加稳定剂和催化剂,继续搅拌混合。
3.如有需要,可以添加塑化剂进行调节,继续搅拌混合。
4.将混合物倒入模具中,进行加热硬化过程,通常需要在150-200°C下进行。
5.根据需要,可以通过改变硬化温度和时间来调节聚氨酯弹性体的硬度和弹性。
以上是一种聚氨酯弹性体的参考配方和制备过程,需要根据具体需求进行调整。
在实际制备过程中,还需要进行反应的控制和工艺的优化,以获得所需的产品性能。
中硬度高回弹PU泡沫塑料
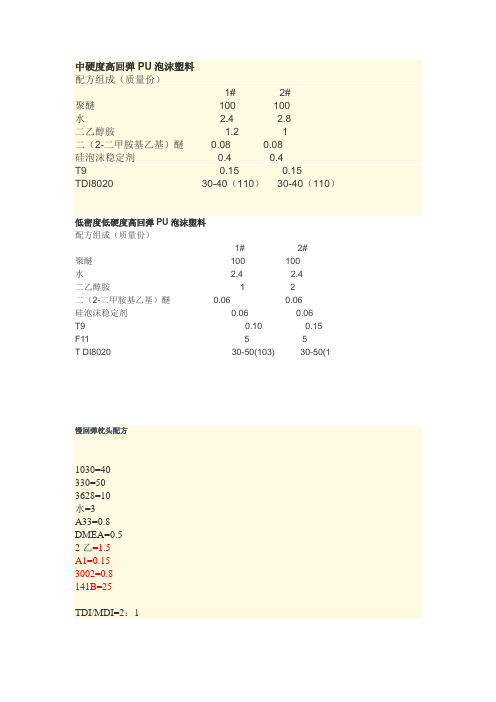
中硬度高回弹PU泡沫塑料配方组成(质量份)1# 2#聚醚100 100水 2.4 2.8二乙醇胺 1.2 1二(2-二甲胺基乙基)醚0.08 0.08硅泡沫稳定剂0.4 0.4T9 0.15 0.15TDI8020 30-40(110) 30-40(110)低密度低硬度高回弹PU泡沫塑料配方组成(质量份)1# 2#聚醚 100 100水 2.4 2.4二乙醇胺 1 2二(2-二甲胺基乙基)醚0.06 0.06硅泡沫稳定剂 0.06 0.06T9 0.10 0.15F11 5 5T DI8020 30-50(103) 30-50(1慢回弹枕头配方1030=40330=503628=10水=3A33=0.8DMEA=0.52乙=1.5A1=0.153002=0.8141B=25TDI/MDI=2:1低密度、全MDI环保型车用座垫5 采用纯MDI的同系物:M50——即4,4’MDI 50%2,4’MDI 50%的产品,可以室温发泡,提高流动性,降低制品密度,减轻车辆重量,是很具发展前景的产品:本部分设定了隐藏,您已回复过了,以下是隐藏的内容配方:高活性聚醚多元醇(OH:28mgKOH/g) 95pbw310助剂* 5pbwDabco 33LV 0.3pbwDabco 8154 0.7pbw硅表面活性剂B4113 0.6pbwA-1 0.1pbw水 3.5pbwM50 50pbw异氰酸酯指数 88物性:拉丝时间(s) 62上升时间(s) 98自由泡密度,kg/m332.7压缩载荷挠曲,kpa:40% 1.5伸长率,% 180撕裂强度,N/m 220聚氨酯轮胎配方聚醚DEP-330N 80聚醚POP3628 20BG 11EG 6DEG 4SI 0.1有机锡 0.1A33 0.5F141B 8B组分找NCO在19%的鞋底B料就可以了A:B=100:100这是我用的经验公式,请大家多指教,以期共同进步;D=100/水-3 若搭配辅助发泡剂,可将其折算成相当于水的用量,跟水的量加在一起。
聚氨酯发泡配方

聚氨酯发泡配方1. 聚醚多元醇这可是聚氨酯发泡配方里很重要的一部分呢。
聚醚多元醇就像是一个基础的搭建者,它能提供羟基,和异氰酸酯反应,让发泡体有个基本的框架结构。
它的种类有很多,不同种类的聚醚多元醇会影响发泡体的柔软度、硬度还有弹性等性能。
比如说,有的聚醚多元醇做出来的发泡体就很柔软,适合做沙发坐垫之类的东西。
2. 异氰酸酯异氰酸酯这个成分很有趣。
它就像一个活跃的小能手,特别容易和聚醚多元醇里的羟基发生反应。
而且这个反应速度还挺关键的,如果太快了,可能发泡过程就不好控制,要是太慢呢,又会影响生产效率。
它的用量也得拿捏好,多了少了都会让发泡体的性能出问题,像强度、密度这些都会受影响。
3. 发泡剂发泡剂那可就是让聚氨酯发泡的关键啦。
它在反应过程中会产生气体,就像给发泡体注入了小泡泡一样。
常见的发泡剂有物理发泡剂和化学发泡剂。
物理发泡剂像是二氧化碳、氟利昂(不过因为环保问题现在用得少了),它们是靠自身的挥发或者膨胀来产生气泡的。
化学发泡剂呢,是通过化学反应产生气体,像水就可以当化学发泡剂,和异氰酸酯反应产生二氧化碳气体来发泡。
4. 催化剂催化剂就像一个小助手,能加快聚醚多元醇和异氰酸酯的反应速度。
如果没有催化剂,这个反应可能会很慢很慢,就没法高效地生产聚氨酯发泡产品了。
常见的催化剂有叔胺类催化剂和有机金属催化剂。
叔胺类催化剂能让反应比较均匀地进行,有机金属催化剂有时候能让反应更有针对性,比如让发泡的某个阶段反应得更快或者更慢。
5. 表面活性剂表面活性剂就像是一个调节大师。
它能降低液体的表面张力,让发泡过程中气泡分布得更均匀。
这样做出来的发泡体,内部结构就会很规整,不会出现有的地方气泡大,有的地方气泡小的情况。
而且它还能让气泡稳定,不会轻易破裂,对发泡体的质量提升很有帮助。
二、不同用途下聚氨酯发泡配方的调整1. 用于建筑保温如果是做建筑保温用的聚氨酯发泡,那对密度和保温性能要求就比较高。
一般会增加聚醚多元醇的比例,让发泡体的结构更紧密,这样保温效果会更好。
聚氨酯弹性体参考配方(一)
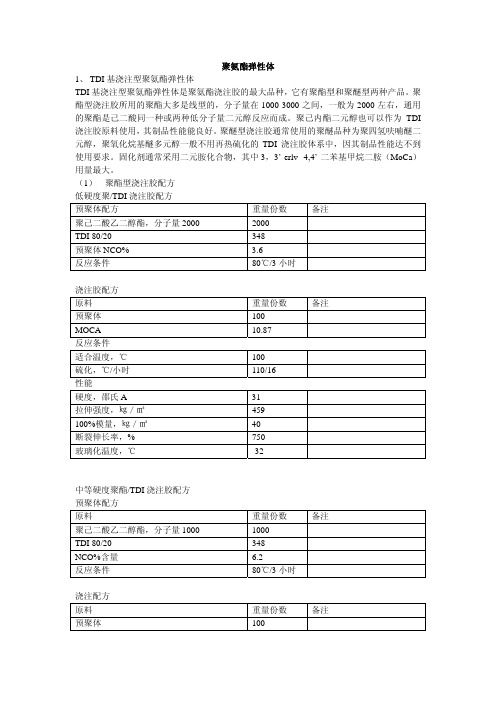
硫化条件 混合温度,℃ 硫化,℃/小时
性能 硬度,邵氏 A 拉伸强度,㎏/㎝² 100%模量,㎏/㎝² 回弹率,% 压缩变定,% 70℃×22 小时
2,4TDI 为基的聚氨酯浇注胶配方 预聚体配方 原料 聚四氢呋喃醚二元醇(分子量 1000) 2,4TDI 反应温度,℃ 反应时间,小时
高硬度聚己内酯/TDI 浇注胶配方 预聚体配方 原料 聚己内酯二元醇,分子量 840 TDI 80/20 预聚体 NCO 含量%
浇注配方 原料 预聚体 MOCA 物性 硬度,邵氏 A 100%模量,公斤/厘米² 300%模量,公斤/厘米² 拉伸强度,公斤/厘米² 伸长率,% 撕裂强度,公斤/厘米 压缩永久变形,% 回弹率
标题:
聚氨酯弹性体
主题:
作者: 关键词: 备注:
微软用户
创建日期:
2012-12-10 16:00:00
修订号: 上次保存日期: 上次保存者:
2 2012-12-10 16:02:00 微软用户
编辑时间总计: 上次打印时间: 打印最终结果
1 分钟 2012-12-10 16:02:00
页数:
4
字数: 字符数:
备注
中等硬度聚酯/TDI 浇注胶配方 预聚体配方 原料 聚己二酸乙二醇酯,分子量 1000 TDI 80/20 NCO%含量 反应条件
浇注配方 原料 预聚体
重量份数 1000 348 6.2 80℃/3 小时
备注
重量份数 100
备注
MOCA 反应条件 适合温度,℃ 硫化,℃/小时 物性 硬度,邵氏 A 拉伸强度,㎏/㎡ 100%模量,㎏/㎡ 断裂伸长率,% 玻璃化温度,℃
847 (约) 1,119 (约)
聚氨酯实用配方(详细含硅油小料配比)
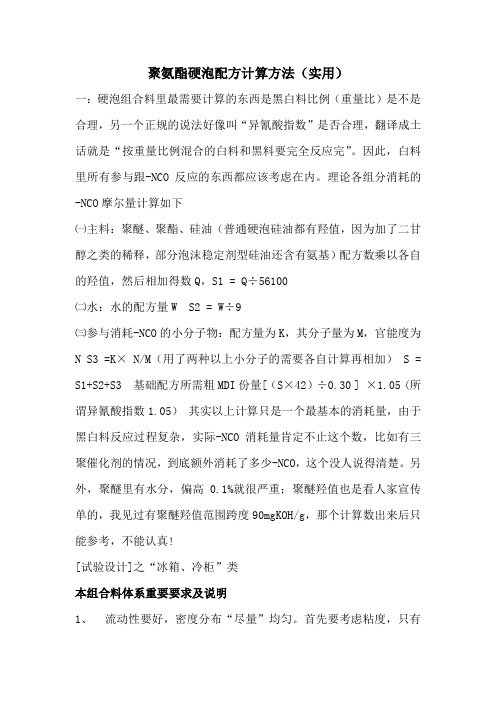
聚氨酯硬泡配方计算方法(实用)一:硬泡组合料里最需要计算的东西是黑白料比例(重量比)是不是合理,另一个正规的说法好像叫“异氰酸指数”是否合理,翻译成土话就是“按重量比例混合的白料和黑料要完全反应完”。
因此,白料里所有参与跟-NCO反应的东西都应该考虑在内。
理论各组分消耗的-NCO摩尔量计算如下㈠主料:聚醚、聚酯、硅油(普通硬泡硅油都有羟值,因为加了二甘醇之类的稀释,部分泡沫稳定剂型硅油还含有氨基)配方数乘以各自的羟值,然后相加得数Q,S1 = Q÷56100㈡水:水的配方量W S2 = W÷9㈢参与消耗-NCO的小分子物:配方量为K,其分子量为M,官能度为N S3 =K× N/M(用了两种以上小分子的需要各自计算再相加) S = S1+S2+S3 基础配方所需粗MDI份量[(S×42)÷0.30 ] ×1.05 (所谓异氰酸指数1.05)其实以上计算只是一个最基本的消耗量,由于黑白料反应过程复杂,实际-NCO消耗量肯定不止这个数,比如有三聚催化剂的情况,到底额外消耗了多少-NCO,这个没人说得清楚。
另外,聚醚里有水分,偏高0.1%就很严重;聚醚羟值也是看人家宣传单的,我见过有聚醚羟值范围跨度90mgKOH/g,那个计算数出来后只能参考,不能认真![试验设计]之“冰箱、冷柜”类本组合料体系重要要求及说明1、流动性要好,密度分布“尽量”均匀。
首先要考虑粘度,只有体系粘度小了,初期流动性才会好(主份平均粘度6000mPa.S以下,组合料350mPa.S以下),其次体系中的钾、钠杂离子要控制在一个低限(20ppm以内),从而可控制避免三聚反应提前,即:体系粘度过早变大。
如果流动性欠佳,发泡料行进至注料口远端就会出现拉丝痕致使泡孔结构橄榄球化,这个位置一定抗不住低温收缩。
2、泡孔细密,导热系数要低。
不难理解泡孔细密是导热系数低的第一前提,此时首先考虑加有403或某些芳香胺醚进入体系(它们所起的作用是首先与-NCO反应,其生成物与其它组份互溶、乳化稳定性提升,并保证发泡体系初期成核稳定,也就是避免迸泡,从而使泡孔细密)其次聚醚本身单独发泡其泡孔结构要好(例如以山梨醇为起始的635SA比蔗糖为起始的1050泡孔要细密均匀得多,还有含有甘油为起始剂的835比1050细密,即便是所谓的4110牌号的聚醚,含丙二醇起始的比二甘醇的好。
- 1、下载文档前请自行甄别文档内容的完整性,平台不提供额外的编辑、内容补充、找答案等附加服务。
- 2、"仅部分预览"的文档,不可在线预览部分如存在完整性等问题,可反馈申请退款(可完整预览的文档不适用该条件!)。
- 3、如文档侵犯您的权益,请联系客服反馈,我们会尽快为您处理(人工客服工作时间:9:00-18:30)。
聚氨酯制品参考配方系列—回弹性高的聚氨酯泡沫配方
有制备高回弹泡沫时,有机多异异氰酯、高分子量多元醇、催化剂、发泡剂、泡沫稳定剂等原料中,可加入高分子量四官能度聚醚多元醇,制得的泡沫回弹性高。
工艺参数
液温℃----------------------------------------25
硫化温度,℃----------------------------------70
硫化时间,分----------------------------------5
模具温度,℃----------------------------------55—60℃
多元醇
多元醇A-1:聚氧化乙烯氧化丙烯甘油醚多元醇,羟值31,末端环氧乙烷付加量为16%。
多元醇A-2:聚氧化乙烯氧化丙烯甘油醚多元醇,羟值28,末端环氧乙烷付加量为16%。
多元醇A-3:聚氧化乙烯氧化丙烯甘油醚多元醇,羟值24,末端环氧乙烷付加量为14%。
多元醇B-1:季戊四醇为起始剂,先加入环氧丙烷,再加入环氧乙烷,聚合反应后制得聚醚多元醇,羟值35,末端环氧乙烷付加量为10%。
多元醇B-2:季戊四醇为起始剂,先加入环氧丙烷,再加入环氧乙烷,聚合反应后制得聚醚多元醇,羟值32,末端环氧乙烷付加量为12%。
多元醇B-3:季戊四醇为起始剂,先加入环氧丙烷,再加入环氧乙烷,聚合反应后制得聚醚多元醇,羟值28,末端环氧乙烷付加量为10%。
多元醇C-1:甘油和环氧丙烷、环氧乙烷(末端付加量14%)所得的羟值33的聚醚多元醇100份,与丙烯腈25份,在130℃,1份偶氮二异丁腈作起始剂,制得羟值27的多元醇。
多元醇C-2:多元醇A-2-100份和丙烯腈27份,苯乙烯15份,0.2份二(4特丁环己基)过氧化二羧酸酯作起始剂,在120℃反应制得羟值20的多元醇。
多元醇C-3:多元醇B-2-100份和丙烯腈27份、苯乙烯15份,在120℃反应制得羟值22的多元醇。
配方
原料------------------------------------------重量份数
多元醇A-1------------------------------30
多元醇A-2--------------------------------------30
多元醇A-3-----------------------------------------------30
多元醇B-1------------------------------30
多元醇B-2--------------------------------------30
多元醇B-3-----------------------------------------------30
多元醇C-1------------------------------40------40-------40
三乙醇胺--------------------------------4-------4--------4
水--------------------------------------3.0-----3.0------3.0
DABCO-33LV-----------------------------0.4-----0.4------0.4
Polycat41------------------------------0.1-----0.1------0.1
硅油5309-------------------------------0.3-----0.3------0.3
硅油SRX-274C---------------------------0.4-----0.4------0.4
TDI80/29和聚MDI混合物-----------------46.2----45.9-----45.5 (重量比为8/2)
异氰酸酯指数----------------------------105-----105------105
性能
整体密度,kg/m-³-------------------------48.8----48.7-----49.0 芯密度,-kg/m-³--------------------------42.8----42.7-----42.9 拉伸强度,kg/cm²-------------------------1.33----1.39-----1.41 伸长率,%--------------------------------90------96-------110 撕裂强度,kg/cm--------------------------0.62----0.63-----0.64 25%ILD(4英寸),kg/314cm²----------------22.2----21.2-----17.0 压缩永久变形,%--------------------------3.2-----3.2-------3.8 湿热变定,%------------------------------12.0----12.8------13.3 回弹率,%--------------------------------75------76--------75
以上内容仅供参考,来源/华南聚氨酯原料商城。