制药行业配料称重系统方案
配料称重自动控制系统怎么调

配料称重自动控制系统怎么调1. 简介配料称重自动控制系统是一种通过电子秤和控制器实现对配料称重的自动化控制系统。
它可以广泛应用于食品、化工、医药等行业,提高生产效率和产品质量。
在使用配料称重自动控制系统之前,需要对系统进行调试和调整,以确保系统能够正常工作并提供准确的称重结果。
本文将介绍如何对配料称重自动控制系统进行调整。
2. 系统调整前的准备工作在进行系统调整之前,需要进行以下准备工作:•确保所有设备和传感器的连接正确并稳定,包括电子秤和控制器之间的连接。
•检查系统的电源供应是否正常,确保电源电压和频率符合要求。
•确保控制器的参数已经正确设置,包括称重范围、精度要求等。
3. 系统调整步骤步骤一:调整零点和秤量补偿1.连接电子秤和控制器,并打开系统电源。
2.设置称重范围,确保称重范围适合当前的称重任务。
3.将电子秤置为空载状态,即没有物料放置在上面。
4.进入控制器的零点和秤量补偿调整模式。
5.按照控制器的操作指南,根据实际情况进行调整。
6.调整零点时,确保电子秤显示为零。
7.调整秤量补偿时,将已知质量的物料放置在电子秤上,并确保电子秤的显示与实际质量相符。
步骤二:校准称重精度1.取一定数量的已知质量物料,如标准砝码。
2.将已知质量物料放置在电子秤上,并记录下称重结果。
3.比较电子秤的称重结果与已知质量物料的真实质量,计算出误差。
4.根据误差结果,进入控制器的校准模式,根据实际情况进行调整。
5.调整校准参数时,根据误差结果逐步调整,直到达到所要求的精度。
步骤三:调整称重速度1.根据生产工艺要求,确认所需的称重速度。
2.进入控制器的速度调整模式。
3.根据实际情况调整控制器的参数,包括传输速度和称重响应速度。
4.通过实际测试和调整,确保控制器能够在要求的时间范围内完成称重任务。
步骤四:系统稳定性测试1.将一定数量的实际物料进行称重测试。
2.运行测试过程中,观察系统的稳定性和准确性。
3.根据实际情况,进行必要的调整和优化。
配料称重自动控制系统怎样操作

配料称重自动控制系统操作指南1. 系统概述配料称重自动控制系统是一种用于自动化控制配料称重的设备,主要应用于生产线上的配料工序。
该系统能够精确称量不同重量的配料,提高生产效率和质量控制,并减少人力成本和配料误差。
2. 系统组成配料称重自动控制系统由以下几个主要组成部分构成:2.1 称重传感器称重传感器是系统中起主要作用的部分。
它通过测量物料重量并输出电信号来实现准确的配料称重。
在安装和使用称重传感器时,需要遵循以下步骤:•确保称重传感器固定在平稳、牢固的支撑结构上,以避免重量分布不均导致测量错误。
•检查传感器的电源连接和信号连接是否正常,确保传感器能够正常工作。
•对于不同类型的传感器,需要按照相应的规范进行校准和调试,以确保称重准确度。
2.2 控制器控制器是系统的核心部分,用于接收传感器的信号并进行相应的控制操作。
控制器通常由一个微处理器和一些逻辑电路组成。
在操作控制器时,需要按照以下步骤进行操作:•打开控制器电源,确保电源供应正常。
•连接称重传感器和控制器,确保信号传输无误。
•设置控制器的工作参数,如配料重量范围、传感器灵敏度等。
•按下启动按钮,控制器将开始接收传感器信号并进行相应的控制操作。
2.3 操作界面操作界面是用户与系统进行交互的通道,通常由触摸屏或键盘等设备组成。
在操作界面上,用户可以进行以下操作:•输入配料的目标重量,控制器将根据用户的输入进行相应的控制操作。
•监控系统的工作状态,包括当前称重重量、运行时间等。
•进行系统的设置和参数调整,如称重单位、显示方式等。
3. 操作步骤下面是配料称重自动控制系统的一般操作步骤:3.1 系统启动•打开控制器电源,并确保称重传感器和操作界面正常连接。
•检查控制器和传感器的工作状态,确保系统准备就绪。
•启动系统,进入操作界面。
3.2 配料准备•根据生产需要,准备需要配料的容器和物料。
•将容器放置在配料区域,确保容器固定不动。
•打开配料区域的门,准备进行配料操作。
梅特勒-托利多称重方案

梅特勒-托利多制药行业称重技术方案梅特勒-托利多(常州)称重设备系统有限公司2009 V2.0目录1.客户需求分析 (3)2.衡器通用知识介绍 (4)3.制药行业解决方案介绍 (10)4.公司简介 (12)21. 客户需求分析客户已经详细列举秤的准确度、最小读数、量程以及材质,但是还有一些非常关键的参数没有提供,例如称量器的最小称量值,也就是客户将在所选称量器上称重的最小值,称量的允许误差要求也没有提及(如百分之几的误差要求,1%,0.5%,还是0.1%?),还有称量器的重复性、安全过载等指标,这些都是影响称量器准确度和使用寿命的重要因素。
而且客户没有提及设备需要符合GMP的要求,由于梅特勒-托利多对制药工艺的不同环节给提供不同的解决方案,以帮助客户降低投资成本、提高生产效率,所以此方案将会分为如下几个内容:z衡器通用知识的介绍z制药行业解决方案介绍z方案介绍在方案的最后,附有梅特勒-托利多根据客户要求生成的GWP(Good Weighing Practice)的报告,客户可以根据报告进行电子秤的选择、称量风险的评估以及测试用砝码的选择。
2. 衡器通用知识介绍执行标准:OIML R76 国际计量组织电子衡器检定规程建议JJG555-1996 非自动衡器通用检定规程JJG539-1997 数字指示秤检定规程JJF1059 测量不确定度的评定和表示2.1. 称重原理介绍现今使用比较广泛的两种称重方式为:电阻应变计原理和电磁力补偿原理,其中普通精度秤和中精度秤都是采用电阻应变计原理的传感器,高精度秤和天平大多是采用电磁力补偿原理的传感器。
电阻应变计原理(模拟式):通过在弹性体上贴电阻应变计,当秤体受到外力作用时,弹性体发生形变,根据惠斯通桥原理,应变计输出信号给仪表处理。
随着外力的增加,弹性体的形变越大,测量误差也会随之增加。
所以不适合大皮重小称量的应用。
而且每次加载的相同外力情况下,输出的信号会发生变化,导致重复性、线性、角差等较差。
动态配料称重控制系统的设计和实现

动态配料称重控制系统的设计和实现一、引言(约200字)二、动态配料称重控制系统的设计(约400字)1.系统需求分析在设计动态配料称重控制系统之前,首先需要对系统的需求进行详细分析。
根据生产线的要求,确定所需物料种类和配比比例。
同时,考虑到生产线的工作速度,要求系统能够实现快速、准确地完成物料的配料。
2.系统架构设计根据需求分析结果,设计动态配料称重控制系统的架构。
该系统主要分为两个部分:硬件系统和软件系统。
硬件系统主要包括传感器、称重仪表和控制器,用于实现对物料的称重;软件系统则负责实时监控和控制称重过程。
3.硬件设计根据系统架构设计,进行硬件系统的设计。
选择合适的传感器和称重仪表,并进行连接和布置。
同时,需要设计一个稳定、可靠的控制电路,确保称重过程的准确性和稳定性。
4.软件设计软件系统主要包括数据采集和处理模块、控制模块和界面模块。
数据采集和处理模块用于实时获得称重数据,并进行数据处理,比如滤波、去噪等。
控制模块负责根据配料要求控制传感器和称重仪表的工作,并实时调整相关参数。
界面模块则提供一个可视化的界面,方便用户进行操作和监控。
三、动态配料称重控制系统的实现(约400字)1.硬件实现根据硬件设计完成硬件系统的连接和调试工作。
确保传感器和称重仪表能够正常工作,并能够稳定地获得称重数据。
同时,对控制电路进行测试和优化,确保称重过程的准确性和稳定性。
2.软件实现根据软件设计完成软件系统的开发和调试。
保证数据采集和处理模块能够准确获取和处理称重数据,同时实现实时的数据显示和监控。
控制模块能够根据配料要求控制传感器和称重仪表的工作,实现准确的配比。
界面模块提供一个直观、友好的界面,方便用户进行操作和监控。
3.系统测试和优化完成系统的开发和调试后,对整个系统进行测试和优化。
通过与实际生产情况的比对,检查系统的准确性和稳定性,并根据测试结果进行优化。
确保系统在生产线上能够稳定、可靠地工作。
四、总结(约200字)本文对动态配料称重控制系统的设计和实现进行了详细的介绍。
配料称重自动控制系统流程
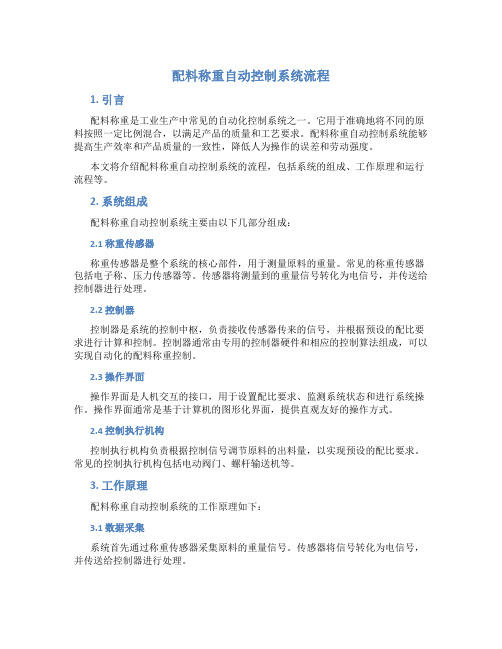
配料称重自动控制系统流程1. 引言配料称重是工业生产中常见的自动化控制系统之一。
它用于准确地将不同的原料按照一定比例混合,以满足产品的质量和工艺要求。
配料称重自动控制系统能够提高生产效率和产品质量的一致性,降低人为操作的误差和劳动强度。
本文将介绍配料称重自动控制系统的流程,包括系统的组成、工作原理和运行流程等。
2. 系统组成配料称重自动控制系统主要由以下几部分组成:2.1 称重传感器称重传感器是整个系统的核心部件,用于测量原料的重量。
常见的称重传感器包括电子称、压力传感器等。
传感器将测量到的重量信号转化为电信号,并传送给控制器进行处理。
2.2 控制器控制器是系统的控制中枢,负责接收传感器传来的信号,并根据预设的配比要求进行计算和控制。
控制器通常由专用的控制器硬件和相应的控制算法组成,可以实现自动化的配料称重控制。
2.3 操作界面操作界面是人机交互的接口,用于设置配比要求、监测系统状态和进行系统操作。
操作界面通常是基于计算机的图形化界面,提供直观友好的操作方式。
2.4 控制执行机构控制执行机构负责根据控制信号调节原料的出料量,以实现预设的配比要求。
常见的控制执行机构包括电动阀门、螺杆输送机等。
3. 工作原理配料称重自动控制系统的工作原理如下:3.1 数据采集系统首先通过称重传感器采集原料的重量信号。
传感器将信号转化为电信号,并传送给控制器进行处理。
3.2 配比计算控制器根据预设的配比要求,对不同原料的重量信号进行计算和比较。
根据计算结果,控制器生成相应的控制信号。
3.3 控制执行控制信号被传送到控制执行机构,控制执行机构根据信号的大小调节原料的出料量。
控制执行机构可以调节电动阀门的开关状态或螺杆输送机的转速等。
3.4 过程监控与反馈在控制执行的过程中,系统会不断地采集和监测原料的重量变化。
控制器通过与预设的控制策略进行比较和分析,判断系统的工作状态是否正常。
如果系统发生异常,控制器会及时发出报警信号,提醒操作员进行处理。
配料秤技术方案
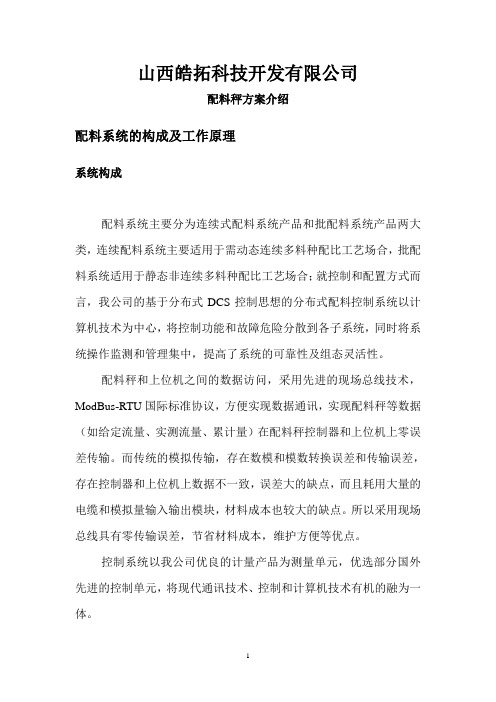
山西皓拓科技开发有限公司配料秤方案介绍配料系统的构成及工作原理系统构成配料系统主要分为连续式配料系统产品和批配料系统产品两大类,连续配料系统主要适用于需动态连续多料种配比工艺场合,批配料系统适用于静态非连续多料种配比工艺场合;就控制和配置方式而言,我公司的基于分布式DCS控制思想的分布式配料控制系统以计算机技术为中心,将控制功能和故障危险分散到各子系统,同时将系统操作监测和管理集中,提高了系统的可靠性及组态灵活性。
配料秤和上位机之间的数据访问,采用先进的现场总线技术,ModBus-RTU国际标准协议,方便实现数据通讯,实现配料秤等数据(如给定流量、实测流量、累计量)在配料秤控制器和上位机上零误差传输。
而传统的模拟传输,存在数模和模数转换误差和传输误差,存在控制器和上位机上数据不一致,误差大的缺点,而且耗用大量的电缆和模拟量输入输出模块,材料成本也较大的缺点。
所以采用现场总线具有零传输误差,节省材料成本,维护方便等优点。
控制系统以我公司优良的计量产品为测量单元,优选部分国外先进的控制单元,将现代通讯技术、控制和计算机技术有机的融为一体。
配料系统主要由上位计算机系统和现场闭环控制系统组成。
现场闭环控制系统主要由若干个由计量给料机、数字调节器、控制器及执行器等组成的典型的单回路控制系统组成,若干个单回路控制系统之间以标准信号联系并和上位机系统以数据通讯方式有机结合,构成分布式控制系统。
本系统构成部分主要有:皮带机、称重传力机构、测速传感器、LC200称重显示控制器、工业控制计算机等构成。
根据生产工艺要求,操作人员可通过工业计算机将各配料皮带机的给定流量通过RS485通迅总线传至配料秤的称重控制仪表上,仪表通过配料皮带秤的计量得到瞬时流量,根据实测流量与给定流量进行PID 运算,将控制输出量通过4~20mA电流送至变频器,由变频器控制配料皮带机电机转速,从而调节配料皮带机的瞬时流量,以达到自动配料的目的。
制药厂配料控制系统

制药厂配料控制系统RAY-FAR在多年的工业自动化实践经验的基础上,结合最新的国内国际案例,开发生产这套高精度制药厂配料控制系统(配比混合控制系统)。
各种不同型号的称重配料控制系统在多个工业行业的的大小工厂现场正在成功稳定运行。
例如:陶瓷配料控制系统、玻璃配料控制系统、化工配料系统、食品添加配料系统、粮食称重控制、配煤控制系统、烧结料配料控制、冶金保护材料配料配比控制、混泥土搅拌控制、制药厂配料控制等。
若配料的原料是液体、胶体,或是固体、液体、胶体的混合控制系统,也请参考:液体混合配料控制系统。
制药厂配料控制系统主机采用工业PC机作为上位机(工业计算机,与普通计算机完全兼容,更为适应工业恶劣环境)+ PLC+ 称重模块(或称重信号采样板)+荷重传感器+称重执行机构。
可含计量控制主机(上位机)、称重软件(计量软件/控制软件)、pl c称重控制仪表、称重传感器、称量仓(也称作斗式秤、仓式秤,方式可以是增量秤和减量秤);执行机构-一般为绞刀、皮带、电振机、可控阀门等,并且大多数情况下用变频器控制。
制药厂配料控制系统中原料配料自动控制自动称重方式,从生产全过程来看,是动态自动称重方式,但计量的瞬间是静态计量,保证了计量控制的精度。
制药厂配料控制系统上位机的软件在Windows操作系统下由本自行公司开发,量身度造的软件控制效率将更高,编程软件也可采用组态软件。
制药厂配料控制系统功能和特点:l 适用于286、386到Pentium Ⅲ、P4甚至是以后的任何PC-Base的工控机或商业计算机、手提电脑;l 上位机+ PLC的结构提高了系统的可靠性。
上位机除了下达初始工艺参数和控制指令外,不参与PLC的实时控制过程,即使上位机处于脱机状态,PLC也能顺利地完成当前的生产任务;l 高级语言与汇编混合编程,既保证了系统的可靠性,又便于软件升级;l 中文(简体或繁体)或英文(按要求)友好人机界面,操作非常简便,仅需1个小时即可学会操作;l 动态的工艺流程显示画面,操作人员可通过彩色显示器直观地监视整个配料控制过程,包括料仓输送设备的工作状态、秤量数据、混合机和各种工艺闸阀门的工作状态等;l 参数修改、功能设置更加灵活,系统智能化程度高;l 产量数据可存入硬盘;l 留有连网端口;l 系统可实时检测监测、显示、存储、打印各瞬时信号、变量、参数等;l 具有零点/皮重快速去除功能;l 可设系统防误操作等功能;l 具有自诊断功能;l 计量控制精度0.2%(视现场的情况而定)。
称重自动配料系统规划方案

称重自动配料系统规划方案随着科学技术的不断发展以及工业制造业的大力发展,无论是在生产、加工或是销售等方面,都对于装配线、生产线以及配料系统提出了更高的要求。
针对传统人工配料方式,由于其低效、易出错、不稳定性等问题,逐渐被人们所淘汰。
为了更好地适应市场的需求以及提高自身竞争力,我们计划开发一款称重自动配料系统。
本文将从计划、需求、功能模块和系统架构等方面进行详细讲述。
1. 计划为了更好地实施称重自动配料系统,并使其能够顺利地运营,我们将会遵循以下计划:1.1 确定团队成员及各自职责。
团队成员包括负责人、设计师、系统工程师、软件工程师、测试工程师、运维工程师等。
1.2 制定时间表,明确开发周期以及各个阶段时间节点。
1.3 确立开发预算,包括硬件、软件成本以及劳动力成本等。
1.4 确定开发环境及所需设备。
2. 需求2.1 硬件需求对于硬件方面,称重自动配料系统需要使用称重传感器、PLC、伺服电机、气动执行器等设备,同时还需要配备计算机控制系统。
2.2 软件需求系统需要使用的软件包括系统控制软件、数据库软件、人机交互软件等。
2.3 功能需求系统需要实现以下功能:2.3.1 自动化调配原材料,实现配方自动配比、称重。
2.3.2 可以进行在线监测,保证生产质量。
2.3.3 可以实现数据共享并提供分析,可以实现数据历史查询并输出报表。
3. 功能模块为了实现上述需求,系统需要包含以下功能模块:3.1 数据采集模块:该模块用于采集机器传感器的称重数据,同时也可以实现其他数据的采集。
3.2 数据处理模块:该模块用于处理采集到的数据,保证数据质量及准确性,支持数据分析等功能。
3.3 控制逻辑模块:该模块用于控制系统与用户之间的交互,通过人机交互界面实现用户对系统的控制与辅助。
3.4 数据存储模块:该模块用于存储系统采集到的数据,并按照时间顺序存储。
4. 系统架构4.1 硬件架构硬件架构主要由计算机、PLC、称重传感器、气动执行器、伺服电机等设备组成,计算机作为控制系统的核心控制装置,通过PLC来与气动执行器、伺服电机进行通信;称重传感器则是系统中不可或缺的重要部件。
药厂称量间的设计、布局和操作

药厂称量间的设计、布局和操作称量间是来自仓库的物料进入处理区的切入点和过渡点。
谨慎的设计、布局和操作是必不可少的。
每一个药品生产厂都有一个特定的区域,在那里原材料被称重并转移到干净的容器中。
这个区域有不同的名称,包括配料间、称量间、中心称量室、药剂室、药房、配药室、分装间。
不管它叫什么,它的设计是必不可少的。
本文概述了这些领域的设计、布局和操作的一些最佳做法。
任何医药称量间的设计都应该遵循下面三个基本原则:◆ 物料和人员的单向流动;◆ 区分危险和非危险物料;◆ 储存和生产物品以及空间的分离。
在过去,为了方便,称量间一般都位于物料储存的仓库附近。
现在,称量间被认为是来自仓库的物料进入处理区的切入点和过渡点。
因此,具体标准将决定最佳位置。
典型的称量间由三部分组成:原材料暂存区,称量室和制品区。
称量间的设计取决于生产区域中正在进行的工艺过程。
制造业务包括:活性药物成分(API)、固体剂型(SDF)、液体、软膏和乳膏(LOC)、无菌注射剂(SI)和生物制品(细胞培养和发酵)。
原材料发放原材料发放区和制品区应该是直接与称量间相邻,从而减少对于过渡空间的要求。
当称重完成后,容器内可能仍然有从客户端收到的物料残留。
大宗的物料会被返回到仓库,但少量,特别是那些将很快再次使用的材料,可以存储在托盘上或搁置在原材料分发区。
许多成分需要特殊的储存条件,如温度和湿度控制。
如果该材料要在这个地方储存任意时间,应采取适当措施。
大宗配料对于活性药物成分、固体制剂和软膏和乳膏来说,量大的物料可以称到容量达2000公升大小的中型散装容器(IBC)。
例如片剂和胶囊等固体制剂,辅料通常在原材料中所占的比例最大。
这些惰性成分,如玉米淀粉和乳糖,可以作为片剂和胶囊剂中的填充剂,用于片剂的成型和胶囊的填充。
在这些房间的称量设备通常是最小尺寸为48×48英寸嵌入式地秤或在支架或起重机后安装电池。
在这两种情况下,粉末应通过重力或真空转移。
称重配料控制系统方案
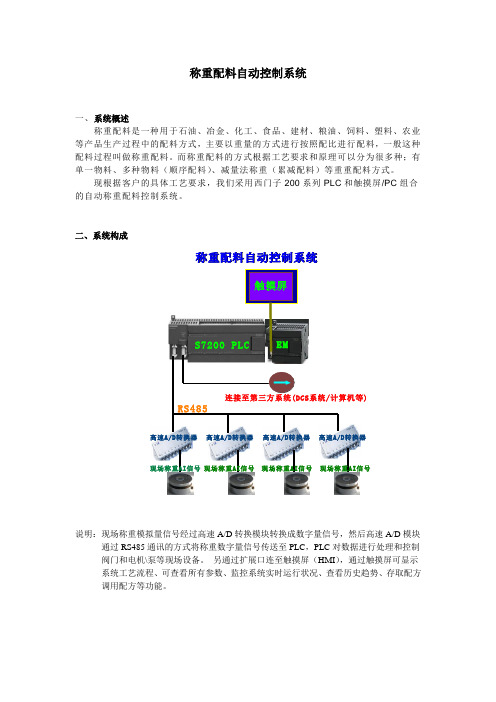
称重配料自动控制系统一、系统概述称重配料是一种用于石油、冶金、化工、食品、建材、粮油、饲料、塑料、农业等产品生产过程中的配料方式,主要以重量的方式进行按照配比进行配料,一般这种配料过程叫做称重配料。
而称重配料的方式根据工艺要求和原理可以分为很多种;有单一物料、多种物料(顺序配料)、减量法称重(累减配料)等重重配料方式。
现根据客户的具体工艺要求,我们采用西门子200系列PLC和触摸屏/PC组合的自动称重配料控制系统。
二、系统构成EMS7200 PLC连接至第三方系统(DCSRS485高速A/D转换器高速A/D转换器高速A/D转换器高速A/D转换器现场称重AI信号现场称重AI信号现场称重AI信号现场称重AI信号说明:现场称重模拟量信号经过高速A/D转换模块转换成数字量信号,然后高速A/D模块通过RS485通讯的方式将称重数字量信号传送至PLC,PLC对数据进行处理和控制阀门和电机\泵等现场设备。
另通过扩展口连至触摸屏(HMI),通过触摸屏可显示系统工艺流程、可查看所有参数、监控系统实时运行状况、查看历史趋势、存取配方调用配方等功能。
三、系统功能1、操控功能操控功能可以选择系统操作模式(装卸联动、定量装料、定量卸料、手动操作、配方存取、配方选择等)。
2、监控功能监控功能能够实时反应系统运行状态的指示(正在装料、正在卸料、装料停止、卸料停止、配料完成、延时卸料等);设备状态的指示(欠载、超载、动态不稳定、通讯故障、设备启动故障等);系统数据的实时监控(所有重量参数、配方参数、运行状态、内部参数、现场设备运行状态等)。
3、现场和远程校准功能可通过现场触摸屏对系统进行校准,也可以通过连接至第三方系统或则计算机可以对系统校准操作。
工艺流程配方管理参数设置历史趋势报警管理用户登录用户注销模式选择称校准画面称校准画面空称标定毛重:砝码重xxxx.xKg加载标定确定当前是空称?确定取消毛重xxxx.xKg 毛重xxxx.xKg 按 确定 则标零按 取消 则返回确定称已加载xxxxKg 确定取消毛重xxxx.xKg按 确定 则标定按 取消 则返回4、联锁功能(根据工艺要求现场设备的联锁动作和保护)。
制药包装中称重和配发系统优化方案二
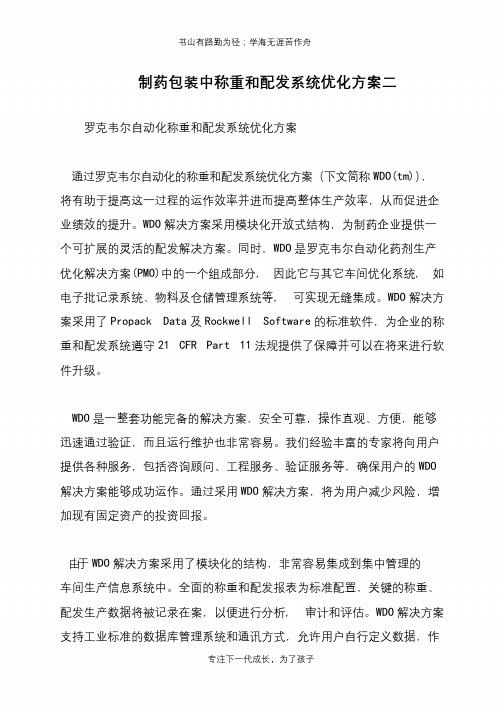
制药包装中称重和配发系统优化方案二罗克韦尔自动化称重和配发系统优化方案通过罗克韦尔自动化的称重和配发系统优化方案(下文简称WDO(tm)),将有助于提高这一过程的运作效率并进而提高整体生产效率,从而促进企业绩效的提升。
WDO解决方案采用模块化开放式结构,为制药企业提供一个可扩展的灵活的配发解决方案。
同时,WDO是罗克韦尔自动化药剂生产优化解决方案(PMO)中的一个组成部分, 因此它与其它车间优化系统, 如电子批记录系统、物料及仓储管理系统等, 可实现无缝集成。
WDO解决方案采用了Propack Data及Rockwell Software的标准软件,为企业的称重和配发系统遵守21 CFR Part 11法规提供了保障并可以在将来进行软件升级。
WDO是一整套功能完备的解决方案,安全可靠,操作直观、方便,能够迅速通过验证,而且运行维护也非常容易。
我们经验丰富的专家将向用户提供各种服务,包括咨询顾问、工程服务、验证服务等,确保用户的WDO 解决方案能够成功运作。
通过采用WDO解决方案,将为用户减少风险,增加现有固定资产的投资回报。
由于WDO解决方案采用了模块化的结构,非常容易集成到集中管理的车间生产信息系统中。
全面的称重和配发报表为标准配置,关键的称重、配发生产数据将被记录在案,以便进行分析, 审计和评估。
WDO解决方案支持工业标准的数据库管理系统和通讯方式,允许用户自行定义数据,作为批记录的一部分,生成各种报表。
通过简便的信息集成,增强了车间的透明度,更加方便企业的其它部门了解该车间的生产状况。
WDO解决方案为车间现场操作和控制系统与企业资源规划系统(ERP)之间的有效集成提供了基础。
罗克韦尔自动化将配发操作与ERP系统集成在一起,同时它们又是一个开放的系统,并提供丰富的标准接口供更广泛的商务系统与之进行集成。
这将确保用户的ERP 系统能够安全、准确、稳定地与其它系统协同运作,如生产计划系统和原辅料消耗报表系统等。
制药包装中称重和配发系统优化方案三
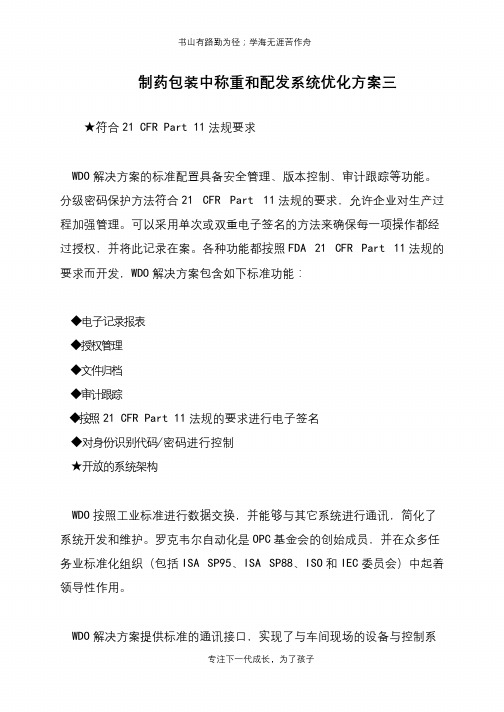
制药包装中称重和配发系统优化方案三★符合21 CFR Part 11法规要求WDO解决方案的标准配置具备安全管理、版本控制、审计跟踪等功能。
分级密码保护方法符合21 CFR Part 11法规的要求,允许企业对生产过程加强管理。
可以采用单次或双重电子签名的方法来确保每一项操作都经过授权,并将此记录在案。
各种功能都按照FDA 21 CFR Part 11法规的要求而开发,WDO解决方案包含如下标准功能:◆电子记录报表◆授权管理◆文件归档◆审计跟踪◆按照21 CFR Part 11法规的要求进行电子签名◆对身份识别代码/密码进行控制★开放的系统架构WDO按照工业标准进行数据交换,并能够与其它系统进行通讯,简化了系统开发和维护。
罗克韦尔自动化是OPC基金会的创始成员,并在众多任务业标准化组织(包括ISA SP95、ISA SP88、ISO和IEC委员会)中起着领导性作用。
WDO解决方案提供标准的通讯接口,实现了与车间现场的设备与控制系统、企业制造执行系统和商务系统之间的通讯。
罗克韦尔自动化的WDO能轻易地与如下系统集成:◆称重设备◆条码标签打印机及扫描器◆企业资源规划系统(ERP)◆物料及仓储管理系统◆电子批记录系统◆产品规格及配方管理系统◆过程控制系统与车间控制系统间的双向联系使得操作员能够通过单一的用户界面执行多种配发任务。
在标准化、开放式系统架构的帮助下,使得用户能够对所有的自动化和控制系统进行监管,从而在使用现有设备的情况下,提高生产能力。
通过将先进的称重技术与丰富的制药业称重及配发应用项目经验结合在一起,使得WDO解决方案能够减轻用户的维护和验证费用。
通过WDO解决方案稳定、安全的模块,以及基于互联网(Web)的系统架构,减轻了系统的复杂程度,为系统提供了更大的灵活性。
通过这一方法,使得整个车间的操作尽在掌握之中,并能够进步一提高操作效率。
★全面实施电子化批记录通过开放的关联型数据库,可以方便地对批记录和批次追溯跟踪信息进行归档和分析。
制药行业配料称重系统方案
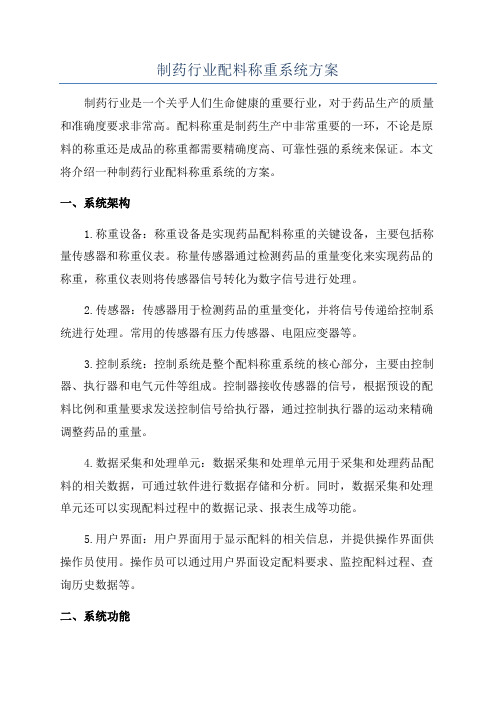
制药行业配料称重系统方案制药行业是一个关乎人们生命健康的重要行业,对于药品生产的质量和准确度要求非常高。
配料称重是制药生产中非常重要的一环,不论是原料的称重还是成品的称重都需要精确度高、可靠性强的系统来保证。
本文将介绍一种制药行业配料称重系统的方案。
一、系统架构1.称重设备:称重设备是实现药品配料称重的关键设备,主要包括称量传感器和称重仪表。
称量传感器通过检测药品的重量变化来实现药品的称重,称重仪表则将传感器信号转化为数字信号进行处理。
2.传感器:传感器用于检测药品的重量变化,并将信号传递给控制系统进行处理。
常用的传感器有压力传感器、电阻应变器等。
3.控制系统:控制系统是整个配料称重系统的核心部分,主要由控制器、执行器和电气元件等组成。
控制器接收传感器的信号,根据预设的配料比例和重量要求发送控制信号给执行器,通过控制执行器的运动来精确调整药品的重量。
4.数据采集和处理单元:数据采集和处理单元用于采集和处理药品配料的相关数据,可通过软件进行数据存储和分析。
同时,数据采集和处理单元还可以实现配料过程中的数据记录、报表生成等功能。
5.用户界面:用户界面用于显示配料的相关信息,并提供操作界面供操作员使用。
操作员可以通过用户界面设定配料要求、监控配料过程、查询历史数据等。
二、系统功能1.称重准确:系统需要具备高精度的称重功能,能够精确地称量出预设比例的药品,保证药品的配料准确性。
2.可靠稳定:系统需要具备良好的稳定性和可靠性,能够在长时间运行的情况下保持高精度的称重性能,减小出错和漏称的可能性。
3.自动化控制:系统需要具备自动化控制功能,能够根据预设的配料要求自动调整各种药品的用量和重量,实现智能化的配料操作。
4.数据记录和分析:系统需要能够记录和存储配料过程中的相关数据,并提供数据分析功能,帮助制药企业分析和改进配料过程,提高生产效率和质量。
5.远程监控:系统需要支持远程监控功能,使制药企业的管理人员能够通过互联网远程监控和管理配料过程,及时了解生产情况。
配料称重自动控制系统PLC程序

配料称重自动控制系统PLC程序一、概述配料称重是制造业中一个重要的环节,在标准化生产中,确保原料的准确配比是非常关键的。
传统的手动称重工作效率低下且容易出错,而采用自动控制系统PLC(Programmable Logic Controller)可以提高效率且减少错误。
本文将详细介绍配料称重自动控制系统的PLC程序设计。
二、PLC程序设计流程1. 系统需求分析在进行PLC程序设计之前,首先需要进行系统需求分析。
这包括确定所需的传感器、执行器、控制器等硬件设备,并明确功能要求和工作流程。
2. 硬件配置根据系统需求分析的结果,确定所需的硬件设备。
这包括称重传感器、输送带、电磁阀等。
确保硬件设备的性能和功能能够满足系统要求。
3. PLC程序设计PLC程序将配料称重系统的工作流程编码为一系列的指令,用于控制硬件设备的运行。
以下是PLC程序设计的主要步骤:3.1 输入输出定义根据系统需求和硬件配置,定义输入和输出。
输入通常包括传感器的信号,如称重传感器的信号和输送带的状态。
输出通常包括执行器的信号,如电磁阀的控制信号。
3.2 程序逻辑设计根据需求和工作流程,设计程序的逻辑。
这通常包括使用逻辑门和定时器等功能块来控制输入和输出的逻辑关系。
例如,在配料称重系统中,需要按照一定的顺序控制输送带的运行和称重传感器的采样。
3.3 编写程序根据逻辑设计,编写PLC程序。
PLC程序一般采用类似于 ladder diagram 的语言编写,使用一系列的逻辑块和指令。
编写程序时,需注意程序的可读性和维护性。
3.4 调试和测试在编写完程序后,进行调试和测试。
通过连接硬件设备,检查程序的正确性和性能。
4. 配料称重自动控制系统的PLC程序本节将介绍具体的配料称重自动控制系统的PLC程序。
该系统的工作流程如下:1.检测传感器状态,如输送带是否为空、原料桶的状态等。
2.如果输送带为空,则启动输送带。
3.在原料桶中放入所需的原料,并关闭原料桶。
- 1、下载文档前请自行甄别文档内容的完整性,平台不提供额外的编辑、内容补充、找答案等附加服务。
- 2、"仅部分预览"的文档,不可在线预览部分如存在完整性等问题,可反馈申请退款(可完整预览的文档不适用该条件!)。
- 3、如文档侵犯您的权益,请联系客服反馈,我们会尽快为您处理(人工客服工作时间:9:00-18:30)。
制药行业配料称重系统方案
——智能制造/营销部
海得控制可以为客户提供制药工艺各个工序的配料称重解决方案,包括:配料、配液、物料管理、物料分装,成品检重等环节。
构建高安全、质量和生产效率的制药行业解决方案。
一、配料系统介绍
原辅料配料系统
根据制药生产工艺规程,将原辅料按一定比例混合在一起;是针对一种或者多种物料按预先设定好的值和误差进行加料和放料的过程。
配料工艺要求无粉尘,可复核可追溯,并最大限度地降低粉体物料转运过程中污染、交叉污染以及混淆、差错等风险。
1、配料工艺路径:
2、配料称重系统:
3、自动配料称重系统
1)按制药生产配方自动进行配料
2)全过程密闭执行
3)电子记录配料过程数据
4)自动生成配料报告,实现物料正反向追踪
4、手动配料称重系统
1)称重及配料程序按照GMP要求进行
2)条码标签扫描防止用错材料
3)生成符合要求的称重报告
二、系统结构与信息流程
1、制药称重自动化系统
海得e-Control PLC控制器通过串口总线协议与电子称重仪器、条码扫描仪、变频器等设备连接,PLC出厂预设程序或netSCADA组态软件自带的电子秤驱动包括:
1)Mettler SICS(梅特勒);Mettler Toledo(梅特勒托利多) Terminals ID1,ID2,
ID3, ID5, ID7, GD12 using the MMR protocol;
2)Sartorius (赛多利斯)XBPI and MP8 using the xBPI protocol。
2、举例:中药称重系统电子记录
当配料通过条形码识别器被添加进去时,中药称重系统会自动查找产品资源和可用原材料之间的关系。
它也会为每一个批处理过程产生唯一的识别数量,并投放相应数量的带条形码的配料。
当配料添加进来时,它们会被通过条形码扫描器扫描和确认。
中药称重系统采用电子记录的最大优点就是它不允许无序操作,减少了人为错误发生的机率。
三、netSCADA 配料称重系统主要功能
1、统计与质量控制
提供配置灵活的统计报表功能,包括基本报表和MES报名,采用独特的技术方案有效的解决了复杂的SQL查询,多维数据建模等问题。
提供偏差分类与预定义,偏差处理流程预先定义,偏差报告自动产生。
2、支持配方系统
配方个数不受限制,数据类型灵活,支持对每个配方加密保护,配方表格控件提供了灵活的配置方式。
3、全程可追溯性
无论是手动、半自动或自动配方和配料系统,都有相应的软件以便于提供全过程可追溯性和集中的配方管理。
4、数据通信功能
通过工厂网络将称重数据集成到更高级别的应用,如MES和ERP,接口开放可定制,将准确的称重数据可靠地连接至您的网络, 灵活的系统集成解决方案。
四、自动化设备选型
1、PLC部分选型(e-Control 系列PLC)
CPU模块 EH10-CPU-001 配置4个或者8个IO插槽的背板,自带电源模块
IO模块:EH10-RS-001 :4 x RS232/RS485通信模块
IO模块:EH10-AI-C01 2点16Bit模拟量输入,4通道DI模块,4通道DO模块
2、工业平板 12.1寸或15寸;带指纹识别或人脸识别等访问验证功能。
3、netSCADA组态软件:(单机版或网络版均可)500点IO配置。
五、称重防错配料系统(MES软件部分)介绍
其中netSCADA MES 物料称重管理模块包括如下功能模块:
物料入库;物料领用;液体计量;物料称重;中间体管理;物料平衡;物料追溯;车间成品出/入库;容器管理;
依据原料批号、原辅料批号、设备号、中间体标志、成品批号等实现正反向追踪;防差错、防交叉污染。
1、称重防错配料系统
面向车间的物料管理和称量管理,应用条码、称量设备集成,实现车间物料精细化、透明化管理。
防差错,减少由于物料差错产生的成本。
通过准确的车间物料消耗与库存记录,减少车间物料积压,提高周转率。
取消库存手工帐,避免重复劳动。
netSCADA MES支持制药生产中存在下面两种称量方式:
✧自动称重配料
✧手工称重配料
1)自动称重配料
MES系统指导自动称配系统按照配方要求称重配料;在生产开始前MES系统下发生产工
单到配料系统,操作员在配料系统选择工单进行投料操作,配料系统根据配方验证MES产
生的条码,确认投入物料的正确性;配料完成后,生成标签、写入RFID,并回传每个料仓
的配料信息到MES。
2)手工称重配料
MES系统对手工称量配料进行管理。
在称量间设置操作客户端,连接扫描枪、电子秤、条
码打印机。
称量指令通过电子SOP指导操作员按照配方要求进行称量。
称量后的结果系
统从电子秤中自动读取并打印条码,称量过程和结果在称量间界面上显示,并与生产任务
进行核对,核对不符时产生报警信息。
同时系统应当对称量衡器的校验、标定进行统一管
理和提示。
2、物料平衡功能
记录各个工序(房间)物料消耗数量、废品数量、退库数量、取样数量,计算收率和物料平衡,综合理论用量,计算物料平衡率,果超出允差范围,给予异常报警。
提供报表方式查询功能。
3、
六、案例例举
1、锦州万德药业,药包称重分拣系统
2、辽宁中成药业,子弹头称重分拣系统
3、OEM客户,粉末包装称重分拣和药片检测系统
……
>>>>>>>>>>>>>>>>>>>>>>>>>>>>>>>>>>>>>>>>>>>>>>>>>>>>>>>>>>>>>>>>
海得控制:提供智能工厂信息化整体解决方案
制药行业客户智能工厂信息化包括数据采集与集中监控系统(SCADA)、制造执行系统(MES)、实验室信息管理系统(LIMS)、仓库管理系统(WMS)、自动配料称重系统等。
海得控制可提供符合GMP、FDA、EMA等规范的智能工厂信息化系统,其中包括:
——数据采集与监视控制系统(netSCADA)
——制造执行系统(netSCADA-MES)
——自动配料称重系统等(netSCADA )
——制药工厂(企业级)私有云平台系统(indusCloud)。