材料成形工艺学上课后习题
材料成型技术习题库+答案

材料成型技术习题库+答案一、单选题(共37题,每题1分,共37分)1.手工电弧焊焊接薄板时,为防止烧穿常采用的工艺措施之一是A、氩气保护B、CO2保护C、直流正接D、直流反接正确答案:D2.炒菜用的铸铁锅适合用下列哪种成形方法___A、锻造B、挤压铸造C、冲压D、砂型铸造正确答案:B3.零件工作时的正应力方向与纤维方向应该A、垂直B、无关C、平行D、相交正确答案:C4.下列焊接方法中,只适于立焊的是A、手弧焊B、埋弧自动焊C、电渣焊D、CO2保护焊正确答案:D5.表现为铸件的外形尺寸减小的是A、液态收缩B、固态收缩C、凝固收缩D、合并收缩正确答案:B6.锻造时当金属的加热温度过高,内部晶粒急剧长大,使塑性降低的现象称为A、硬化B、过烧C、过热D、熔化正确答案:C7.生产中为提高合金的流动性,常采用的方法是A、降低出铁温度B、延长浇注时间C、提高浇注温度D、加大出气口正确答案:C8.预锻模膛与终锻模膛相比,它的A、应有冲孔连皮B、圆角应大些,斜度应小些C、带有飞边槽D、圆角和斜度应大些正确答案:D9.合金化学成份对流动性的影响主要取决于A、过热温度B、凝固点C、熔点D、结晶温度区间正确答案:D10.以下冲压工序中,属于冲裁工序的是A、冲挤B、弯曲C、拉深D、落料正确答案:D11.焊接低碳钢或普低钢时,选用电焊条的基本原则是A、等强度原则B、经济性原则C、可焊性原则D、施工性原则正确答案:A12.自由锻件坯料质量的计算公式是A、G坯料=G锻件+G飞边B、G坯料=G锻件+C烧损C、G坯料=G锻件+G飞边+C烧损D、G坯料=G锻件+G烧损+G料头正确答案:D13.锻造前坯样加热的目的是A、提高塑性,降低韧性B、提高强度,降低韧性C、提高塑性,提高变形抗力D、提高塑性,增加韧性正确答案:D14.下列零件不属于轴类零件的是___A、垫圈B、螺栓C、拔叉D、丝杠正确答案:A15.生产火车车轮、重型水压机横梁等重型机械最适合的材料是A、铸钢B、铸铁C、铸造黄铜D、铸造合金正确答案:A16.生产较大的套筒、管类铸件,常用的铸造方法是A、挤压铸造B、压力铸造C、熔模铸造D、离心铸造正确答案:D17.具有较好的脱氧、除硫、去氢和去磷作用以及机械性能较高的焊条是A、不锈钢焊条B、结构钢焊条C、酸性焊条D、碱性焊条正确答案:D18.可锻铸铁的制取方法是,先浇注成A、球墨组织B、灰口组织C、麻口组织D、白口组织正确答案:D19.齿轮毛坯锻造前,应先对棒料进行A、拔长B、打磨C、镦粗D、滚挤正确答案:C20.不属于埋弧自动焊的特点是A、节省材料B、焊接质量好C、生产率高D、适应性广正确答案:D21.焊接热影响区中,对焊接接头性能不利的区域是A、部分相变区B、正火区C、熔合区D、焊缝金属正确答案:C22.铸件的缩孔常出现在铸件的A、厚部B、底部C、芯部D、最后凝固部位正确答案:D23.钢的杂质元素中哪一种会增加其冷脆性____A、TiB、NiC、SD、P正确答案:D24.下列哪一项不是热裂纹的特征A、形状曲折B、尺寸较短C、缝隙较宽D、金属光泽正确答案:D25.影响焊接热影响区大小的主要因素是A、焊接方法B、焊接规范C、接头形式D、焊缝尺寸正确答案:B26.下列制品中最适宜于铸造的是A、铁锅B、哑铃C、钢精锅D、子弹壳正确答案:B27.氩弧焊特别适于焊接容易氧化的金属和合金,是因为A、氩气是惰性气体B、氩弧温度高C、氩弧热量集中D、氩气容易取得正确答案:A28.航空发动机机箱的成形方法可以是___A、铝合金铸造B、圆钢锻造C、板料冲压D、球墨铸铁铸造正确答案:A29.为简化锻件形状而增加的那部分金属称为A、余量B、坯料C、敷料D、余块正确答案:C30.闪光对焊属于哪种焊接类别A、激光焊B、熔焊C、钎焊D、压焊正确答案:D31.铸件最小壁厚要受到限制,主要是由于薄壁件中金属流动性低,容易产生A、缩孔和缩松B、应力和变形C、冷隔和浇不足D、开裂正确答案:C32.铸件壁越厚,其强度越低,主要是由于A、冷隔严重B、碳含量态低C、易浇不足D、晶粒粗大正确答案:D33.下列合金线收缩率最大的A、铸造黄铜B、铸钢C、铸铁D、铸铝正确答案:A34.手弧焊时,操作最方便,焊缝质量最易保证,生产率又高的焊缝空间位置是A、立焊B、仰焊C、平焊D、横焊正确答案:C35.对于由几个零件组合成的复杂部件,可以一次铸出的铸造方法是A、熔模铸造B、挤压铸造C、压力铸造D、离心铸造正确答案:A36.普通车床床身浇注时,导轨面应该A、朝右侧B、朝下C、朝左侧D、朝上正确答案:B37.下列属于变形工序的是A、修整B、拉深C、落料D、冲裁正确答案:B二、判断题(共63题,每题1分,共63分)1.冲压件成形后一般不再进行机械加工才即可作为零件使用。
材料成形工艺基础华中科技大学第四版课后习题答案

材料成形工艺基础华中科技大学第四版课后习题答案1. 金属材料的机械性能通常用哪几个指标衡量?答:强度、塑性、硬度、冲击韧性、疲劳极限等。
2. 何谓同素异晶转变,纯铁不同温度下的晶格变化如何?答:同素异晶转变:金属在固态下,随温度的改变由一种晶格转变为另一种晶格的现象称为同素异晶转变。
纯铁在1538。
C结晶为σ-Fe ,体心立方结构;温度降到1394。
C时,σ-Fe转变为γ-Fe,面心立方结构;降到912。
C时,γ-Fe转变为α-Fe,为体心立方结构3. 从状态图看含碳0.4%、0.9%的碳钢在室温下由哪些组织构成?答:0.4%由铁素体(F)+珠光体(P)0.9%由二次渗碳体(Fe3CⅡ)+珠光体(P)4. 淬火的目的是什么?答:淬火的主要目的是使奥氏体化后的工年获得尽量多的马氏体(或下贝氏体组织),然后配以不同的温度回火获得各种需要的性能。
例如:提高钢件的机械性能,诸如硬度、耐磨性、弹性极限、疲劳强度等,改善某些特殊钢的物理或者化学性能,如增强磁钢的铁磁性,提高不锈钢的耐蚀性等。
5.某弹簧由优质碳素钢制造,应选用什么牌号的钢?应选用怎样的热处理工艺?答:含碳量在0.6%-0.9%之间,65、70、85、65Mn.65Mn淬火+中温回火6.从下列钢号中,估计出其主要元素大致含量20 45 T10 16Mn 40Cr答:0.2%C 、0.45%C、1.0%C,Mn≤0.4%,Si≤0.35、0.16%C,Mn1.2%-1.6% 、0.4%C,0.8-1.1%Cr7.简述铸造成型的实质及优缺点。
答:铸造成型的实质是:利用金属的流动性,逐步冷却凝固成型的工艺过程。
优点:1.工艺灵活生大,2.成本较低,3.可以铸出外形复杂的毛坯缺点:1.组织性能差,2机械性能较低,3.难以精确控制,铸件质量不够稳定4.劳动条件太差,劳动强度太大。
8.合金流动性取决于哪些因素?合金流动性不好对铸件品质有何影响?答:合金流动性取决于 1.合金的化学成分 2.浇注温度 3.浇注压力 4.铸型的导热能力5.铸型的阻力合金流动性不好:产生浇不到、冷隔等缺陷,也是引起铸件气孔、夹渣和缩孔缺陷的间接原因。
材料成形原理课后习题解答

材料成型原理第一章(第二章的内容)第一部分:液态金属凝固学1.1 答:(1)纯金属的液态结构是由原子集团、游离原子、空穴或裂纹组成。
原子集团的空穴或裂纹内分布着排列无规则的游离的原子,这样的结构处于瞬息万变的状态,液体内部存在着能量起伏。
(2)实际的液态合金是由各种成分的原子集团、游离原子、空穴、裂纹、杂质气泡组成的鱼目混珠的“混浊”液体,也就是说,实际的液态合金除了存在能量起伏外,还存在结构起伏。
1.2答:液态金属的表面张力是界面张力的一个特例。
表面张力对应于液-气的交界面,而界面张力对应于固-液、液-气、固-固、固-气、液-液、气-气的交界面。
表面张力σ和界面张力ρ的关系如(1)ρ=2σ/r,因表面张力而长生的曲面为球面时,r为球面的半径;(2)ρ=σ(1/r1+1/r2),式中r1、r2分别为曲面的曲率半径。
附加压力是因为液面弯曲后由表面张力引起的。
1.3答:液态金属的流动性和冲型能力都是影响成形产品质量的因素;不同点:流动性是确定条件下的冲型能力,它是液态金属本身的流动能力,由液态合金的成分、温度、杂质含量决定,与外界因素无关。
而冲型能力首先取决于流动性,同时又与铸件结构、浇注条件及铸型等条件有关。
提高液态金属的冲型能力的措施:(1)金属性质方面:①改善合金成分;②结晶潜热L要大;③比热、密度、导热系大;④粘度、表面张力大。
(2)铸型性质方面:①蓄热系数大;②适当提高铸型温度;③提高透气性。
(3)浇注条件方面:①提高浇注温度;②提高浇注压力。
(4)铸件结构方面:①在保证质量的前提下尽可能减小铸件厚度;②降低结构复杂程度。
1.4 解:浇注模型如下:则产生机械粘砂的临界压力ρ=2σ/r显然 r =21×0.1cm =0.05cm 则 ρ=410*5.05.1*2-=6000Pa 不产生机械粘砂所允许的压头为H =ρ/(ρ液*g )=10*75006000=0.08m 1.5 解: 由Stokes 公式 上浮速度 92(2v )12r r r -= r 为球形杂质半径,γ1为液态金属重度,γ2为杂质重度,η为液态金属粘度γ1=g*ρ液=10*7500=75000γ2=g 2*ρMnO =10*5400=54000所以上浮速度 v =0049.0*95400075000(*10*1.0*223)-)(-=9.5mm/s 3.1解:(1)对于立方形晶核 △G 方=-a 3△Gv+6a 2σ①令d △G 方/da =0 即 -3a 2△Gv+12a σ=0,则临界晶核尺寸a *=4σ/△Gv ,得σ=4*a △Gv ,代入① △G 方*=-a *3△Gv +6 a *24*a △Gv =21 a *2△Gv 均质形核时a *和△G 方*关系式为:△G 方*=21 a *3△Gv (2)对于球形晶核△G 球*=-34πr *3△Gv+4πr *2σ 临界晶核半径r *=2σ/△Gv ,则△G 球*=32πr *3△Gv 所以△G 球*/△G 方*=32πr *3△Gv/(21 a *3△Gv) 将r*=2σ/△Gv ,a *=4σ/△Gv 代入上式,得△G 球*/△G 方*=π/6<1,即△G 球*<△G 方*所以球形晶核较立方形晶核更易形成材料成型原理第 3 页 共 16 页3-7解: r 均*=(2σLC /L)*(Tm/△T)=319*6.618702731453*10*25.2*25)+(-cm =8.59*10-9m △G 均*=316πσLC 3*Tm/(L 2*△T 2) =316π*262345319*)10*6.61870(2731453*10*10*25.2()+()-=6.95*10-17J3.2答: 从理论上来说,如果界面与金属液是润湿得,则这样的界面就可以成为异质形核的基底,否则就不行。
材料成型基础课后习题答案
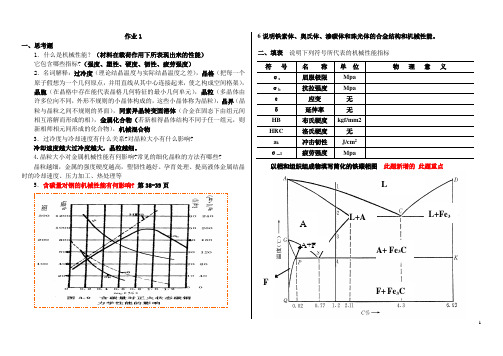
作业1一、思考题1.什么是机械性能?(材料在载荷作用下所表现出来的性能)它包含哪些指标?(强度、塑性、硬度、韧性、疲劳强度)2.名词解释:过冷度(理论结晶温度与实际结晶温度之差),晶格(把每一个原子假想为一个几何原点,并用直线从其中心连接起来,使之构成空间格架),晶胞(在晶格中存在能代表晶格几何特征的最小几何单元),晶粒(多晶体由许多位向不同,外形不规则的小晶体构成的,这些小晶体称为晶粒),晶界(晶粒与晶粒之间不规则的界面),同素异晶转变固溶体(合金在固态下由组元间相互溶解而形成的相),金属化合物(若新相得晶体结构不同于任一组元,则新相师相元间形成的化合物),机械混合物3.过冷度与冷却速度有什么关系?对晶粒大小有什么影响?冷却速度越大过冷度越大,晶粒越细。
4.晶粒大小对金属机械性能有何影响?常见的细化晶粒的方法有哪些?晶粒越细,金属的强度硬度越高,塑韧性越好。
孕育处理、提高液体金属结晶时的冷却速度、压力加工、热处理等5.含碳量对钢的机械性能有何影响?第38-39页6说明铁素体、奥氏体、渗碳体和珠光体的合金结构和机械性能。
二、填表说明下列符号所代表的机械性能指标符号名称单位物理意义σs屈服极限Mpaσb抗拉强度Mpaε应变无δ延伸率无HB 布氏硬度kgf/mm2HRC 洛氏硬度无a k冲击韧性J/cm2σ—1疲劳强度Mpa以相和组织组成物填写简化的铁碳相图此题新增的此题重点LL+A L+Fe3 AA+FFA+ Fe3CF+Fe3C图1--1 简化的铁碳合金状态图三、填空1.碳溶解在体心立方的α-Fe中形成的固溶体称铁素体,其符号为 F ,晶格类型是体心立方晶格,性能特点是强度低,塑性好。
2.碳溶解在面心立方的γ-Fe中形成的固溶体称奥氏体,其符号为 A ,晶格类型是面心立方晶格,性能特点是强度低,塑性好。
3.渗碳体是铁与碳的金属化合物,含碳量为 6.69 %,性能特点是硬度很高,脆性很差。
4.ECF称共晶转变线,所发生的反应称共晶反应,其反应式是得到的组织为L(4.3% 1148℃)=A(2.11%)+Fe3C。
材料成型技术基础第2版课后习题答案

第一章金属液态成形1.①液态合金的充型能力是指熔融合金充满型腔,获得轮廓清晰、形状完整的优质铸件的能力。
②流动性好,熔融合金充填铸型的能力强,易于获得尺寸准确、外形完整的铸件。
流动性不好,则充型能力差,铸件容易产生冷隔、气孔等缺陷。
③成分不同的合金具有不同的结晶特性,共晶成分合金的流动性最好,纯金属次之,最后是固溶体合金。
④相比于铸钢,铸铁更接近更接近共晶成分,结晶温度区间较小,因而流动性较好。
2.浇铸温度过高会使合金的收缩量增加,吸气增多,氧化严重,反而是铸件容易产生缩孔、缩松、粘砂、夹杂等缺陷。
3.缩孔和缩松的存在会减小铸件的有效承载面积,并会引起应力集中,导致铸件的力学性能下降。
缩孔大而集中,更容易被发现,可以通过一定的工艺将其移出铸件体外,缩松小而分散,在铸件中或多或少都存在着,对于一般铸件来说,往往不把它作为一种缺陷来看,只有要求铸件的气密性高的时候才会防止。
4 液态合金充满型腔后,在冷却凝固过程中,若液态收缩和凝固收缩缩减的体积得不到补足,便会在铸件的最后凝固部位形成一些空洞,大而集中的空洞成为缩孔,小而分散的空洞称为缩松。
浇不足是沙型没有全部充满。
冷隔是铸造后的工件稍受一定力后就出现裂纹或断裂,在断口出现氧化夹杂物,或者没有融合到一起。
出气口目的是在浇铸的过程中使型腔内的气体排出,防止铸件产生气孔,也便于观察浇铸情况。
而冒口是为避免铸件出现缺陷而附加在铸件上方或侧面的补充部分。
逐层凝固过程中其断面上固相和液相由一条界线清楚地分开。
定向凝固中熔融合金沿着与热流相反的方向按照要求的结晶取向进行凝固。
5.定向凝固原则是在铸件可能出现缩孔的厚大部位安放冒口,并同时采用其他工艺措施,使铸件上远离冒口的部位到冒口之间建立一个逐渐递增的温度梯度,从而实现由远离冒口的部位像冒口方向顺序地凝固。
铸件相邻各部位或铸件各处凝固开始及结束的时间相同或相近,甚至是同时完成凝固过程,无先后的差异及明显的方向性,称作同时凝固。
工程材料与技术成型基础课后习题答案

工程材料与技术成型基础课后习题答案第一章1-1由拉伸实验可以得出哪些力学性能指标?在工程上这些指标是如何定义的? 答:强度和韧性.强度(σb)材料抵抗塑性变形和断裂的能力称为强度。
塑性(δ)材料在外力作用下产生永久变形而不被破坏的能力.强度指标里主要测的是:弹性极限,屈服点,抗拉强度等.塑性指标里主要测的是:伸长率,断面收缩率.1-21-3锉刀:HRC 黄铜轴套:HB 供应状态的各种非合金钢钢材:HB 硬质合金刀片:HRA,HV 耐磨工件的表面硬化层:HV调质态的机床主轴:HRC 铸铁机床床身:HB 铝合金半成品:HB1-4公式HRC=10HBS,90HRB=210HBS,HV=HBS800HV>45HRC>240HBS>90HRB1-7材料在加工制造中表现出的性能,显示了加工制造的难易程度。
包括铸造性,锻造性,切削加工性,热处理性。
第二章2-2 答:因为γ-Fe为面心立方晶格,一个晶胞含4个原子,致密度为0.74。
γ-Fe冷却到912°C 后转变为α-Fe后,变成体心立方晶格,一个晶胞含2个原子,致密度为0.68,尽管γ-Fe 的晶格常数大于α-Fe的晶格常数,但多的体积部分抵不上因原子排列不同γ-Fe变成α-Fe 体积增大的部分,故γ-Fe冷却到912℃后转变为α-Fe时体积反而增大。
2-3.答:(1)过冷度理论结晶温度与实际结晶温度只差。
(2)冷速越快则过冷度越大,同理,冷速越小则过冷度越小(3)过冷度越大则晶粒越小,同理,过冷度越小则晶粒越大。
过冷度增大,结晶驱动力越大,形核率和长大速度都大,但过冷度过大,对晶粒细化不利,结晶发生困难。
2-4:答:(1)在一般情况下,晶粒越小,其强度塑性韧性也越高。
(2)因为晶粒越小则晶界形成就越多,产生晶体缺陷,在晶界处晶格处于畸变状态,故晶界能量高因此晶粒的大小对金属的力学性能有影响。
(3)在凝固阶段晶粒细化的途径有下列三种:①提高结晶时的冷却速度增加过冷度②进行变质处理处理:在液态金属浇筑前人工后加入少量的变质剂,从而形成大量非自发结晶核心而得到细晶粒组织。
工程材料及成型工艺基础习题及答案

〔2〕影响液态合金充型能力的因素有合金的流动性、浇注条件、铸型充填条件。
〔1〕合金在铸造生产条件下,获得优质铸件的难易程度。 〔2〕流动性和收缩。合金的流动性越好、收缩越小,铸造性能越好。
2.什么是合金的铸造性能?衡量合金铸造性能的主要指标是什么 ?其是如何影响的?
图2-3 铸铁顶盖的两种设计方案
8.分析图2-4所示零件分型方案的优缺点,并选择其中与零件生产类型相适应的分型方案。
大批量生产
单件生产
1
2
方案1
方案1
方案2
方案2
图(b)方案1:优点是起模高度小,砂箱高度减小;缺点是分开模造型对合箱精度要求较高,不易保证整个螺纹内孔外表的质量,且需要砂芯. 方案2:优点是整体模造型,铸件的尺寸精度易于保证;铸件螺纹内孔外表质量均匀;可以直接铸出铸件的内腔,省去了型芯。缺点是下砂箱高度大,起模高度较大. 单件生产时,应选择方案2。
图2-1 铸造应力框铸件
5. 灰口铸铁的组织和性能决定于什么因素?为什么在灰口铸铁中,碳硅含量越高,则其强度越低?
1〕灰口铸铁的组织和性能决定于化学成分和冷却速度。
2〕因为碳、硅含量越高,铸铁中的石墨片就越粗大,石墨数量也越多,对基体的破坏就越严重。同时基体中铁素体的量增加,珠光体的量减少。所以铸铁的强度越低。
金属材料成形根底作业〔2〕
4.铸件在凝固过程中所造成的体积缩减如得不到液态金属的补充,将产生缩孔或缩松。凝固温度范围窄的合金,倾向于“逐层凝固〞,因此易产生缩孔;而凝固温度范围宽的合金,倾向于“糊状凝固〞,因此易产生缩松。 5.准确地估计铸件上缩孔可能产生的位置是合理安排冒口和冷铁的主要依据。生产中确定缩孔位置的常用方法有画等温线法、内切圆法和计算机模拟凝固法等。 6.顺序凝固原则主要适用于 逐层凝固的合金,其目的是消除缩孔;同时凝固原则主要适用于 糊状凝固的合金,其目的是减小应力。
(完整版)高分子材料成型加工课后习题答案

1、什么是“非分散混合”,什么是“分散混合”,两者各主要通过何种物料运动和混合操作来实现?答:①非分散混合在混合中仅增加离子在混合物中空间分布均匀性而不减小粒子初始尺寸的过程称为非分散混合或简单混合。
这种混合的运动基本形式是通过对流来实现的,可以通过包括塞形流动和不需要物料连续变形的简单体积排列和置换来达到。
②分散混合是指在混合过程中发生粒子尺寸减小到极限值,同时增加相界面和提高混合物组分均匀性的混合过程。
分散混合主要是靠剪切应力和拉伸应力作用实现的。
分散混合的目的是把少数组分的固体颗粒和液相滴分散开来,成为最终粒子或允许的更小颗粒或滴,并均匀地分散到多组分中,这就涉及少组分在变形粘性流体中的破裂为题,这是靠强迫混合物通过窄间隙而形成的高剪切区来完成的。
2、在热固性塑料模压成型中,提高压力应相应地降低还是升高模压压力才对模压成型工艺有利?为什么?答:在一定温度范围内,模温升高,物料流动性提高,模压压力可降低,但模温提高也会使塑料的交联反应速率加速,从而导致熔融物料的粘度迅速增高,反而需要更高的模压压力。
3、热固性塑料模压成型中物料的预热温度对模压压力有何影响?为什么?答:对塑料进行预热可以提高流动性,降低模压压力,但如果预热温度过高或预热时间过长会使塑料在预热过程中有部分固化,会抵消预热增大流动性效果,模压是需更高的压力来保证物料充满型腔。
1、什么是聚合物的结晶取向?它们有何不同?研究结晶和取向对高分子材料加工有何实际影响?答:结晶是聚合物分子在三维空间呈周期性重复排列的过程,而取向是取向单元在外力作用下择优排列的过程,取向单元可以是:基团、链段、分子链、晶粒、晶片或变形的球晶等。
结晶是材料自身的性质,只发生在分子、原子、离子这些基础的单元上,取向的产生是外力作用的结果,取向单元也更多样。
结晶可以影响材料的拉伸强度、弹性模量、冲击强度、耐热性、耐候性、吸水性、透明性、透气性、成型收缩性等物性。
取向后的聚合物,在取向方向和垂直于取向方向上性能差异特别显著。
材料成型基本原理习题答案答案
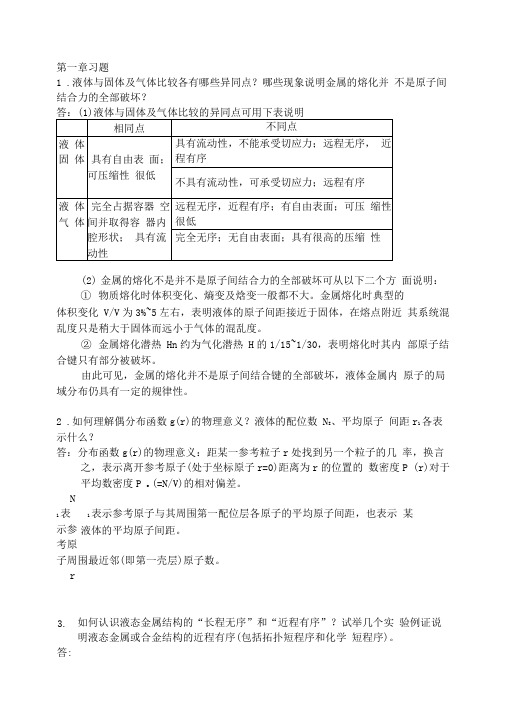
第一章习题1 .液体与固体及气体比较各有哪些异同点?哪些现象说明金属的熔化并 不是原子间结合力的全部破坏?答:(1)液体与固体及气体比较的异同点可用下表说明(2) 金属的熔化不是并不是原子间结合力的全部破坏可从以下二个方 面说明: ① 物质熔化时体积变化、熵变及焓变一般都不大。
金属熔化时典型的体积变化 V/V 为3%~5左右,表明液体的原子间距接近于固体,在熔点附近 其系统混乱度只是稍大于固体而远小于气体的混乱度。
② 金属熔化潜热 Hn 约为气化潜热 H 的1/15~1/30,表明熔化时其内 部原子结合键只有部分被破坏。
由此可见,金属的熔化并不是原子间结合键的全部破坏,液体金属内 原子的局域分布仍具有一定的规律性。
2 .如何理解偶分布函数g(r)的物理意义?液体的配位数 N I 、平均原子 间距r 1各表示什么?答:分布函数g(r)的物理意义:距某一参考粒子r 处找到另一个粒子的几 率,换言之,表示离开参考原子(处于坐标原子r=0)距离为r 的位置的 数密度P (r)对于平均数密度P o (=N/V)的相对偏差。
N1表示参考原子周围最近邻(即第一壳层)原子数。
r如何认识液态金属结构的“长程无序”和“近程有序”?试举几个实 验例证说明液态金属或合金结构的近程有序(包括拓扑短程序和化学 短程序)。
1表示参考原子与其周围第一配位层各原子的平均原子间距,也表示 某液体的平均原子间距。
3. 答:(1 )长程无序是指液体的原子分布相对于周期有序的晶态固体是不规则的,液体结构宏观上不具备平移、对称性。
近程有序是指相对于完全无序的气体,液体中存在着许多不停“游荡” 着的局域有序的原子集团(2)说明液态金属或合金结构的近程有序的实验例证① 偶分布函数的特征对于气体,由于其粒子(分子或原子)的统计分布的均匀性,其偶分布函数 g(r) 在任何位置均相等,呈一条直线 g(r)=1 。
晶态固体因原子以特定方式周期排列,其 g(r) 以相应的规律呈分立的若干尖锐峰。
材料成型工艺基础习题答案剖析

材料成型工艺基础(第三版)部分课后习题答案第一章⑵.合金流动性决定于那些因素?合金流动性不好对铸件品质有何影响?答:①合金的流动性是指合金本身在液态下的流动能力。
决定于合金的化学成分、结晶特性、粘度、凝固温度范围、浇注温度、浇注压力、金属型导热能力。
②合金流动性不好铸件易产生浇不到、冷隔等缺陷,也是引起铸件气孔、夹渣、缩孔缺陷的间接原因。
⑷.何谓合金的收缩?影响合金收缩的因素有哪些?答:①合金在浇注、凝固直至冷却至室温的过程中体积和尺寸缩减的现象,称为收缩。
②影响合金收缩的因素:化学成分、浇注温度、铸件结构和铸型条件。
⑹.何谓同时凝固原则和定向凝固原则?试对下图所示铸件设计浇注系统和冒口及冷铁,使其实现定向凝固。
答:①同时凝固原则:将内浇道开在薄壁处,在远离浇道的厚壁处出放置冷铁,薄壁处因被高温金属液加热而凝固缓慢,厚壁出则因被冷铁激冷而凝固加快,从而达到同时凝固。
②定向凝固原则:在铸件可能出现缩孔的厚大部位安放冒口,使铸件远离冒口的部位最先凝固,靠近冒口的部位后凝固,冒口本身最后凝固。
第二章⑴ .试从石墨的存在和影响分析灰铸铁的力学性能和其他性能特征。
答:石墨在灰铸铁中以片状形式存在,易引起应力集中。
石墨数量越多,形态愈粗大、分布愈不均匀,对金属基体的割裂就愈严重。
灰铸铁的抗拉强度低、塑性差,但有良好的吸震性、减摩性和低的缺口敏感性,且易于铸造和切削加工。
石墨化不充分易产生白口,铸铁硬、脆,难以切削加工;石墨化过分,则形成粗大的石墨,铸铁的力学性能降低。
⑵.影响铸铁中石墨化过程的主要因素是什么?相同化学成分的铸铁件的力学性能是否相同?答:①主要因素:化学成分和冷却速度。
②铸铁件的化学成分相同时铸铁的壁厚不同,其组织和性能也不同。
在厚壁处冷却速度较慢,铸件易获得铁素体基体和粗大的石墨片,力学性能较差;而在薄壁处,冷却速度较快,铸件易获得硬而脆的白口组织或麻口组织。
⑸.什么是孕育铸铁?它与普通灰铸铁有何区别?如何获得孕育铸铁?答:①经孕育处理后的灰铸铁称为孕育铸铁。
工程材料及成型技术习题及答案讲解学习
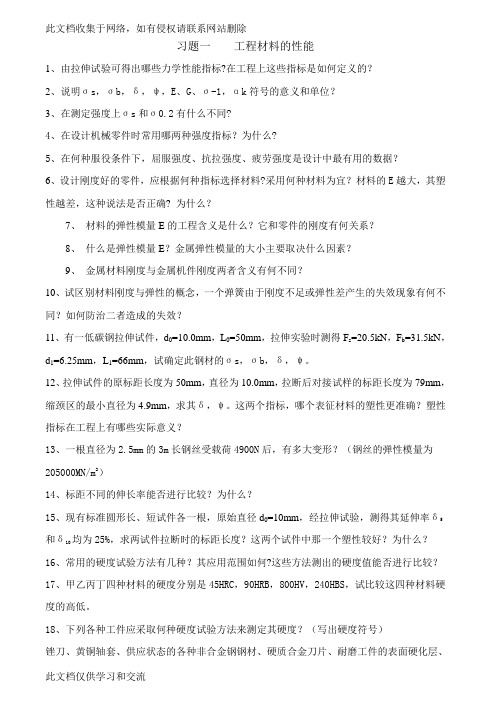
习题一工程材料的性能1、由拉伸试验可得出哪些力学性能指标?在工程上这些指标是如何定义的?2、说明σs,σb,δ,ψ,E、G、σ-1,αk符号的意义和单位?3、在测定强度上σs和σ0.2有什么不同?4、在设计机械零件时常用哪两种强度指标?为什么?5、在何种服役条件下,屈服强度、抗拉强度、疲劳强度是设计中最有用的数据?6、设计刚度好的零件,应根据何种指标选择材料?采用何种材料为宜?材料的E越大,其塑性越差,这种说法是否正确? 为什么?7、材料的弹性模量E的工程含义是什么?它和零件的刚度有何关系?8、什么是弹性模量E?金属弹性模量的大小主要取决什么因素?9、金属材料刚度与金属机件刚度两者含义有何不同?10、试区别材料刚度与弹性的概念,一个弹簧由于刚度不足或弹性差产生的失效现象有何不同?如何防治二者造成的失效?11、有一低碳钢拉伸试件,d0=10.0mm,L0=50mm,拉伸实验时测得F s=20.5kN,F b=31.5kN,d1=6.25mm,L1=66mm,试确定此钢材的σs,σb,δ,ψ。
12、拉伸试件的原标距长度为50mm,直径为10.0mm,拉断后对接试样的标距长度为79mm,缩颈区的最小直径为4.9mm,求其δ,ψ。
这两个指标,哪个表征材料的塑性更准确?塑性指标在工程上有哪些实际意义?13、一根直径为2.5mm的3m长钢丝受载荷4900N后,有多大变形?(钢丝的弹性模量为205000MN/m2)14、标距不同的伸长率能否进行比较?为什么?15、现有标准圆形长、短试件各一根,原始直径d0=10mm,经拉伸试验,测得其延伸率δ5和δ10均为25%,求两试件拉断时的标距长度?这两个试件中那一个塑性较好?为什么?16、常用的硬度试验方法有几种?其应用范围如何?这些方法测出的硬度值能否进行比较?17、甲乙丙丁四种材料的硬度分别是45HRC,90HRB,800HV,240HBS,试比较这四种材料硬度的高低。
合工大版材料成型原理课后习题参考答案(重要习题加整理)

第二章 凝固温度场P498. 对于低碳钢薄板,采用钨极氩弧焊较容易实现单面焊双面成形(背面均匀焊透)。
采用同样焊接规范去焊同样厚度的不锈钢板或铝板会出现什么后果?为什么?解:采用同样焊接规范去焊同样厚度的不锈钢板可能会出现烧穿,这是因为不锈钢材料的导热性能比低碳钢差,电弧热无法及时散开的缘故;相反,采用同样焊接规范去焊同样厚度的铝板可能会出现焊不透,这是因为铝材的导热能力优于低碳钢的缘故。
9. 对于板状对接单面焊焊缝,当焊接规范一定时,经常在起弧部位附近存在一定长度的未焊透,分析其产生原因并提出相应工艺解决方案。
解:(1)产生原因:在焊接起始端,准稳态的温度场尚未形成,周围焊件的温度较低,电弧热不足以将焊件熔透,因此会出现一定长度的未焊透。
(2)解决办法:焊接起始段时焊接速度慢一些,对焊件进行充分预热,或焊接电流加大一些,待焊件熔透后再恢复到正常焊接规范。
生产中还常在焊件起始端固定一个引弧板,在引弧板上引燃电弧并进行过渡段焊接,之后再转移到焊件上正常焊接。
第四章 单相及多相合金的结晶 P909.何为成分过冷判据?成分过冷的大小受哪些因素的影响? 答: “成分过冷”判据为:R G L <NLD RLL L e K K D C m δ-+-0011当“液相只有有限扩散”时,δN =∞,0C C L =,代入上式后得R G L<000)1(K K D C m L L -( 其中: G L — 液相中温度梯度 R — 晶体生长速度 m L — 液相线斜率 C 0 — 原始成分浓度 D L — 液相中溶质扩散系数 K 0 — 平衡分配系数K )成分过冷的大小主要受下列因素的影响:1)液相中温度梯度G L , G L 越小,越有利于成分过冷 2)晶体生长速度R , R 越大,越有利于成分过冷 3)液相线斜率m L ,m L 越大,越有利于成分过冷 4)原始成分浓度C 0, C 0越高,越有利于成分过冷 5)液相中溶质扩散系数D L, D L 越底,越有利于成分过冷6)平衡分配系数K 0 ,K 0<1时,K 0 越 小,越有利于成分过冷;K 0>1时,K 0越大,越有利于成分过冷。
高分子材料成型加工唐颂超第三版课后习题答案仅供参考学习资料
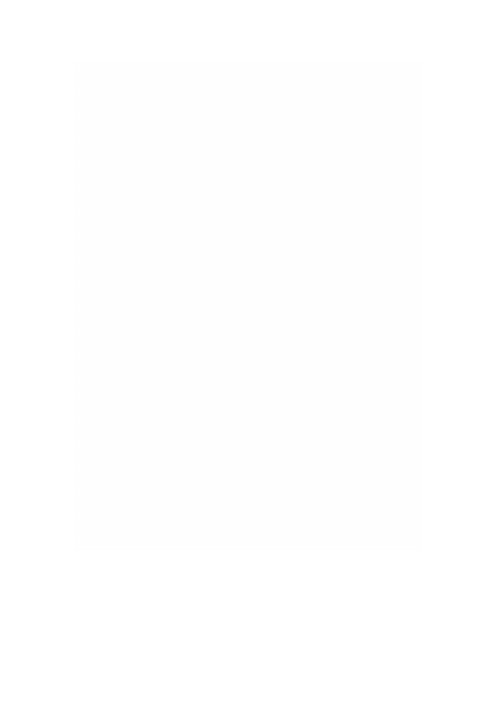
精品文档 -10课后习题答案(仅供参考)高分子材料成型加工Chapter2 Chapter2高分子材料学3 2、分别区分“通用塑料”和“工程塑料”1.、“热塑性塑料”和“热固性塑料”,并请各举例。
、、PVC价廉的塑料。
通用塑料有PE、PP答:通用塑料:一般指产量大、用途广、成型性好、PS 等刚性好、100℃,50MPa冲击强度大于6kJ/m2 ,长期耐热温度超过工程塑料是指拉伸强度大于、PET耐腐蚀等可代替金属用作结构件的塑料。
工程塑料有PA、蠕变小、自润滑、电绝缘、等。
PBT、POM热塑性塑料:加热时变软以至流动,冷却变硬。
这种过程是可逆的、可以反复进行。
如聚乙聚苯醚好和氯化聚醚等都是热塑性塑料。
聚苯乙烯、聚甲醛、聚砜、烯、聚丙烯、聚氯乙烯、产生化学反应一交链固化而变加热到一定温度,热固性塑料:第一次加热时可以软化流动,硬,这种变化是不可逆的。
此后,再次加热时,已不能再变软流动了。
正是借助这种特性进进而固化成为确定形状和尺利用第一次加热时的塑化流动在压力下充满型腔,行成型加工,寸的制品。
这种材料称为热固性塑料。
酚醛、脲醛、三聚氰胺甲醛、不饱和聚酯、有机硅等塑料都是热固性塑料。
什么是聚合物的结晶和取向?它们有何不同?研究结晶和取向对高分子材料加工有何实2.际意义?聚合物的结晶:高聚物发生的分子链在三维空间形成局部区域的、高度有序的排列的过程。
链段聚合物的取向:高聚物的分子链沿某特定方向作优势的平行排列的过程。
包括分子链、和结晶高聚物的晶片、晶带沿特定方向择优排列。
高分子的结晶属于高分子的一个物理特性,不是所有的高聚物都会结晶,而1)(不同之处:结晶是某些局部区域内分子链在三维空2)所有的高聚物都可以在合适的条件下发生取向。
(是在外力作用下整个分子链间的规整排列,而取向一般是在一定程度上的一维或二维有序,结晶是在分子链内部和分子链之间的相互作用下发生的,3)沿特定方向发生较为规整排列。
(没有外力取向一般是在外力作用和环境中发生的,外部作用也可以对结晶产生一定的影响;范围内,而取向可以发生在Tg~Tm的作用,取向一般不会内部产生。
材料成型与工艺课后答案 1-3,1-4
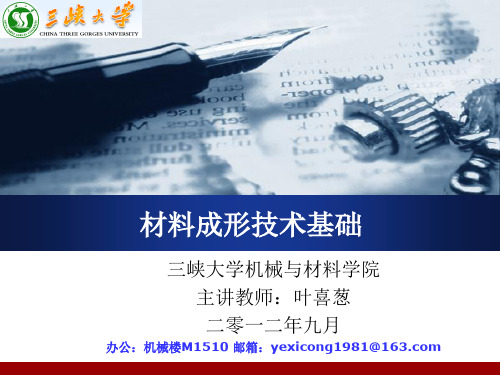
(4)阶梯式浇注系统 是具有多层内浇道。 优点:兼有底注式和顶 注式的优点,又克服了 两者的缺点,即浇注平 稳,减少了飞溅,又有 利于补缩。 缺点:浇注系统结构复 杂,加大了造型和铸件 清理工作量。 多用于高度较高、型腔 较复杂、收缩率较大或 品质要求较高的铸件。
3. 内浇道与铸件型腔连接位置的选择原则
2)铸件的大平面应朝下,减少辐射,防开裂夹渣。
3)面积较大的薄壁部分应置于铸型下部或垂直、 倾斜位置。防止产生浇不足、冷隔。
4)易形成缩孔的铸件,较厚部分置于上部或 侧面。考虑安放冒口利于补缩。
5) 应尽量减少型芯的数量。
6)要便于安放型芯、固定和排气。
Back to page-4
浇注位置
内浇道的位置、数目应服从所选定的凝固顺序和补缩方法。
内浇道在铸件上开设位置的选择可遵循如下原则:
1.为使铸件实现同时凝固,对壁厚均匀的铸件,可选用多个内
浇道分散引入金属液。对壁厚不太均匀的铸件,内浇道应开设 在薄壁处。
2.为使铸件实现顺序凝固,内浇道应设在有冒口的厚壁处,
从厚壁处引入金属液,形成铸件从薄壁至厚壁,最后到冒口的 凝固顺序。
分型面
浇注位置和分型面选择总原则: 优先保证铸件质量为主
操作便捷为辅:造型、起模、下芯、合箱
不可牺牲铸件质量来满足操作便利
四、铸造工艺参数的确定
铸造工艺参数包括收缩余量、加工余量、起模斜度、 铸造圆角、型芯和芯头等。 1)收缩余量 模样比铸件图纸尺寸增大的数值称收缩余量。 在制作模样和芯盒时,模样和芯盒的制造尺寸应比铸件 放大一个该合金的线收缩率。这个线收缩率称为铸造收缩 率: ∑=(L模-L铸件)/ L模*100% 通常,灰铸铁的铸造收缩率为0.7%~1.0%,铸造碳钢的 铸造收缩率为1.3%~2.0%,铝硅合金的铸造收缩率为0.8 %~1.2%,锡青铜的铸造收缩率为1.2%~1.4%。
材料成型加工与工艺学-习题解答(1,2)汇总
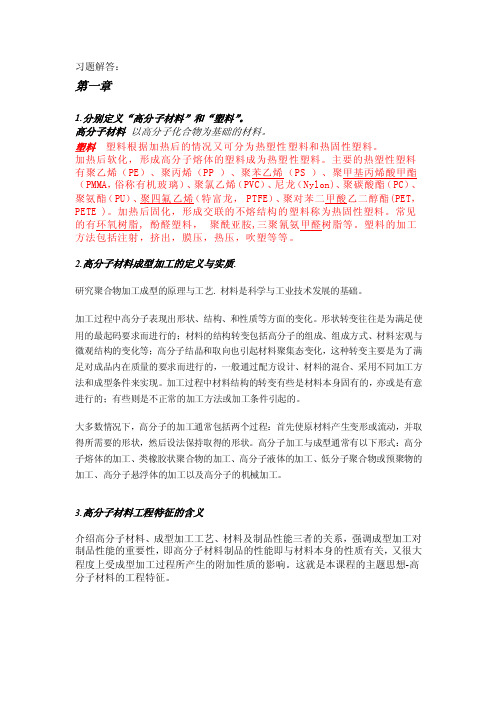
习题解答:第一章1.分别定义“高分子材料”和“塑料”。
高分子材料以高分子化合物为基础的材料。
塑料塑料根据加热后的情况又可分为热塑性塑料和热固性塑料。
加热后软化,形成高分子熔体的塑料成为热塑性塑料。
主要的热塑性塑料有聚乙烯(PE)、聚丙烯(PP )、聚苯乙烯(PS )、聚甲基丙烯酸甲酯(PMMA,俗称有机玻璃)、聚氯乙烯(PVC)、尼龙(Nylon)、聚碳酸酯(PC)、聚氨酯(PU)、聚四氟乙烯(特富龙, PTFE)、聚对苯二甲酸乙二醇酯(PET,PETE )。
加热后固化,形成交联的不熔结构的塑料称为热固性塑料。
常见的有环氧树脂, 酚醛塑料,聚酰亚胺,三聚氰氨甲醛树脂等。
塑料的加工方法包括注射,挤出,膜压,热压,吹塑等等。
2.高分子材料成型加工的定义与实质.研究聚合物加工成型的原理与工艺. 材料是科学与工业技术发展的基础。
加工过程中高分子表现出形状、结构、和性质等方面的变化。
形状转变往往是为满足使用的最起码要求而进行的;材料的结构转变包括高分子的组成、组成方式、材料宏观与微观结构的变化等;高分子结晶和取向也引起材料聚集态变化,这种转变主要是为了满足对成品内在质量的要求而进行的,一般通过配方设计、材料的混合、采用不同加工方法和成型条件来实现。
加工过程中材料结构的转变有些是材料本身固有的,亦或是有意进行的;有些则是不正常的加工方法或加工条件引起的。
大多数情况下,高分子的加工通常包括两个过程:首先使原材料产生变形或流动,并取得所需要的形状,然后设法保持取得的形状。
高分子加工与成型通常有以下形式:高分子熔体的加工、类橡胶状聚合物的加工、高分子液体的加工、低分子聚合物或预聚物的加工、高分子悬浮体的加工以及高分子的机械加工。
3.高分子材料工程特征的含义介绍高分子材料、成型加工工艺、材料及制品性能三者的关系,强调成型加工对制品性能的重要性,即高分子材料制品的性能即与材料本身的性质有关,又很大程度上受成型加工过程所产生的附加性质的影响。
高分子材料成型工艺学_常州大学中国大学mooc课后章节答案期末考试题库2023年
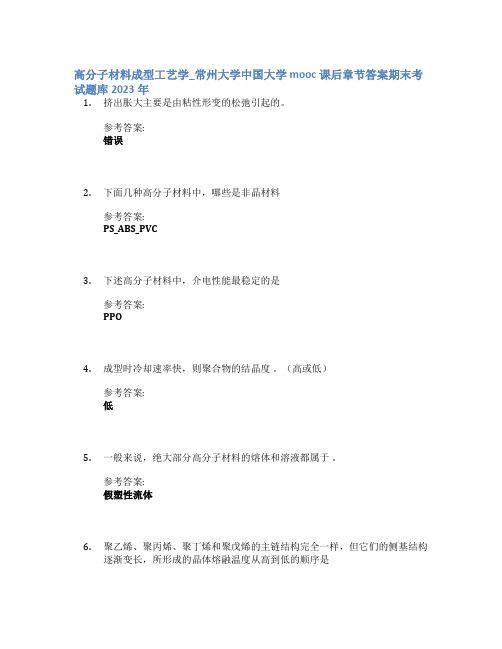
高分子材料成型工艺学_常州大学中国大学mooc课后章节答案期末考试题库2023年1.挤出胀大主要是由粘性形变的松弛引起的。
参考答案:错误2.下面几种高分子材料中,哪些是非晶材料参考答案:PS_ABS_PVC3.下述高分子材料中,介电性能最稳定的是参考答案:PPO4.成型时冷却速率快,则聚合物的结晶度。
(高或低)参考答案:低5.一般来说,绝大部分高分子材料的熔体和溶液都属于。
参考答案:假塑性流体6.聚乙烯、聚丙烯、聚丁烯和聚戊烯的主链结构完全一样,但它们的侧基结构逐渐变长,所形成的晶体熔融温度从高到低的顺序是参考答案:聚丙烯>聚乙烯>聚丁烯>聚戊烯7.聚乙烯、聚丙烯、聚苯乙烯的主链结构完全一样,但它们的侧基位阻逐渐变大,它们的玻璃化转变温度从低到高的顺序是参考答案:聚乙烯8.影响聚合物熔体流动行为的因素是。
参考答案:熔体温度_分子链的特性_剪切速率9.表征高聚物熔体流动性的基本参数有两个,分别是。
参考答案:表观粘度_熔体流动速率10.聚合物结晶的必要条件是参考答案:结构规整性_分子链规整性11.分子链的刚性越强,则材料的耐热性能越。
(差或好)参考答案:好12.硬质PVC和软质PVC的重要区别是基体树脂PVC的分子量和增塑剂含量的不同,一般硬质PVC制品选用分子量大的基体树脂,软质PVC则选用分子量小的基体树脂。
参考答案:错误13.下面几种材料中最容易进行电镀或喷漆的是参考答案:PC14.PET、PC和PPO都是常用的工程塑料,它们的热变形温度由高到低的顺序是参考答案:PPO>PC>PET15.一般来说,高分子材料熔体的表观粘度越大,则熔体流动速率越大。
参考答案:错误16.高分子熔体的粘度随着温度的升高而。
(增加或是降低)参考答案:降低17.假塑性流体的典型特征是粘度随着剪切速率的增加而。
(增加或是降低)参考答案:降低18.晶态聚合物分子链的取向结构没有非晶态聚合物的聚向结构稳定。
材料成型工艺基础习题解答

第一章金属材料与热处理1、常用的力学性能有哪些?各性能的常用指标是什么?答:刚度:弹性模量E强度:屈服强度和抗拉强度塑性:断后伸长率和断面收缩率硬度:冲击韧性:疲劳强度:2、4、金属结晶过程中采用哪些措施可以使其晶粒细化?为什么?答:过冷细化:采用提高金属的冷却速度,增大过冷度细化晶粒。
变质处理:在生产中有意向液态金属中加入多种难溶质点(变质剂),促使其非自发形核,以提高形核率,抑制晶核长大速度,从而细化晶粒。
7、9、什么是热处理?钢热处理的目的是什么?答:热处理:将金属材料或合金在固态范围内采用适当的方法进行加热、保温和冷却,以改变其组织,从而获得所需要性能的一种工艺。
热处理的目的:强化金属材料,充分发挥钢材的潜力,提高或改善工件的使用性能和加工工艺性,并且可以提高加工质量、延长工件和刀具使用寿命,节约材料,降低成本。
第二章铸造成型技术2、合金的铸造性能是指哪些性能,铸造性能不良,可能会引起哪些铸造缺陷?答:合金的铸造性能指:合金的充型能力、合金的收缩、合金的吸气性;充型能力差的合金产生浇不到、冷隔、形状不完整等缺陷,使力学性能降低,甚至报废。
合金的收缩合金的吸气性是合金在熔炼和浇注时吸入气体的能力,气体在冷凝的过程中不能逸出,冷凝则在铸件内形成气孔缺陷,气孔的存在破坏了金属的连续性,减少了承载的有效面积,并在气孔附近引起应力集中,降低了铸件的力学性能。
6、什么是铸件的冷裂纹和热裂纹?防止裂纹的主要措施有哪些?答:热裂是在凝固末期,金属处于固相线附近的高温下形成的。
在金属凝固末期,固体的骨架已经形成,但树枝状晶体间仍残留少量液体,如果金属此时收缩,就可能将液膜拉裂,形成裂纹。
冷裂是在较低温度下形成的,此时金属处于弹性状态,当铸造应力超过合金的强度极限时产生冷裂纹。
防止措施:热裂——合理调整合金成分,合理设计铸件结构,采用同时凝固原则并改善型砂的退让性。
冷裂——对钢材材料合理控制含磷量,并在浇注后不要过早落砂。
《高分子材料成型加工》课后习题参考答案
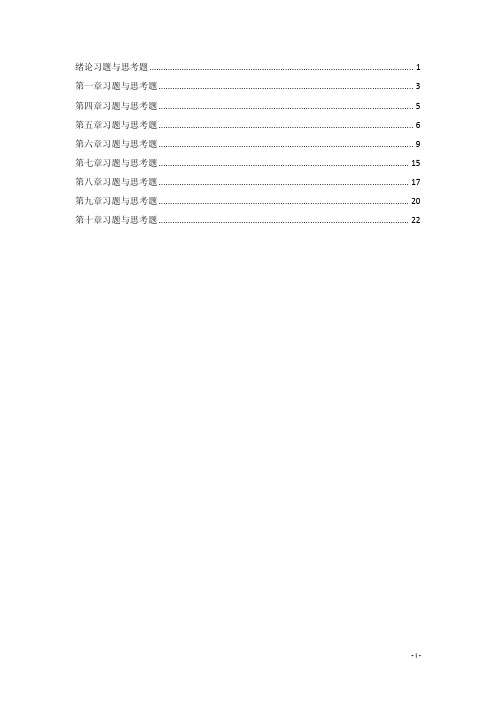
绪论习题与思考题 (1)第一章习题与思考题 (3)第四章习题与思考题 (5)第五章习题与思考题 (6)第六章习题与思考题 (9)第七章习题与思考题 (15)第八章习题与思考题 (17)第九章习题与思考题 (20)第十章习题与思考题 (22)绪论习题与思考题2.分别区分“通用塑料”和“工程塑料”,“热塑性塑料”和“热固性塑料”,“简单组分高分子材料”和“复杂组分高分子材料”,并请各举2~3例。
答:通用塑料:一般指产量大、用途广、成型性好、价廉的塑料。
通用塑料有:PE,PP,PVC,PS等;工程塑料:是指拉伸强度大于50MPa,冲击强度大于6kJ/m2 ,长期耐热温度超过100℃的,刚性好、蠕变小、自润滑、电绝缘、耐腐蚀等,可代替金属用作结构件的塑料。
工程塑料有:PA,PET,PBT,POM等;工程塑料是指被用做工业零件或外壳材料的工业用塑料,是强度、耐冲击性、耐热性、硬度及抗老化性均优的塑料。
日本业界将它定义为“可以做为构造用及机械零件用的高性能塑料,耐热性在100℃以上,主要运用在工业上”。
热塑性塑料:加热时变软以至流动,冷却变硬,这种过程是可逆的,可以反复进行。
聚乙烯、聚丙烯、聚氯乙烯、聚苯乙烯、聚甲醛、聚砜、聚苯醚,氯化聚醚等都是热塑性塑料。
(热塑性塑料中树脂分子链都是线型或带支链的结构,分子链之间无化学键产生,加热时软化流动、冷却变硬的过程是物理变化;)热固性塑料:第一次加热时可以软化流动,加热到一定温度,产生化学反应一交链固化而变硬,这种变化是不可逆的,此后,再次加热时,已不能再变软流动了。
正是借助这种特性进行成型加工,利用第一次加热时的塑化流动,在压力下充满型腔,进而固化成为确定形状和尺寸的制品。
这种材料称为热固性塑料。
(热固性塑料的树脂固化前是线型或带支链的,固化后分子链之间形成化学键,成为三维的网状结构,不仅不能再熔触,在溶剂中也不能溶解。
)酚醛、脲醛、三聚氰胺甲醛、不饱和聚酯、有机硅等塑料,都是热固性塑料。
材料成型与工艺课后答案 1-3,1-4
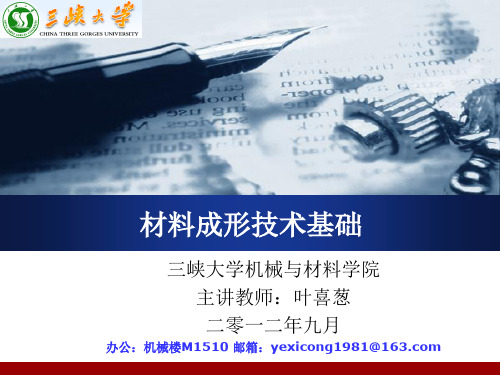
铸造工艺图:铸造工艺图是利用各种工 艺符号,把制造模样和铸型所需的资料, 直接绘在零件图上的图样。
它是制造模样和铸型,进行生产准备和铸件检验的依 据——基本工艺文件 收缩余量
工 浇注位置 艺 方 分型面的选择 案
工 加工余量 艺 参 起模斜度 数 铸造圆角 型芯及芯头
浇 组成及作用 注 常见类型 系 统 冒口
2)铸件的大平面应朝下,减少辐射,防开裂夹渣。
3)面积较大的薄壁部分应置于铸型下部或垂直、 倾斜位置。防止产生浇不足、冷隔。
4)易形成缩孔的铸件,较厚部分置于上部或 侧面。考虑安放冒口利于补缩。
5) 应尽量减少型芯的数量。
6)要便于安放型芯、固定和排气。
Back to page-4
浇注位置
较大的铸件,宜将内浇道
从铸件薄壁处引入,以利 铸件同时凝固,减少铸件 的内应力、变形,防止裂 纹产生。
二、浇注位置的选择-六点注意
浇注位置:浇注时铸件在铸型中所处的空间位置;浇 注位置对铸件质量及铸造工艺都有很大影响。选择时应考 虑如下原则:
选择原则:
1)铸件的重要加工面和受力面应朝下或位于侧面, 避免砂眼气孔和夹渣。
1)冒口就近设在铸件热节的上方或侧旁; 2) 冒口尽量设在铸件最高、最厚的部位,对低处的热节增设补 贴或使用冷铁。 3)冒口不应设在铸件重要的、受力大的部位,以防晶粒粗大降 低力学性能。 4)冒口位置不要选在铸造应力集中处,应注意减轻对铸件的收 缩阻碍,以免引起裂纹。 5)尽量用一个冒口同时补缩几个热节或铸件 6)冒口布置在加工面上,可借加工精整铸件表面,零件外观质 量好。 7)对不同高度上的多个冒口,应用冷铁使各个冒口的补缩范围 相隔开
起模斜度的大小根据立壁的高度、造型方法和模样材料来 确定:立壁愈高,斜度愈小;外壁斜度比内壁小;机器造型 的一般比手工造型的小;金属模斜度比木模小。具体数据可 查有关手册。一般外壁为3º ~ 15°,内壁为3°~10°。
材料成型加工与工艺学-习题解答(7-8)

第六章压制成型2. 简述热固性塑料模压成型的工艺步骤。
将热固性模塑料在以加热到指定温度的模具中加压,使物料熔融流动并均匀地充满模腔,在加热和加压的条件下经过一定的时间,使其发生化学反应而变成具有三维体形结构的热固性塑料制品。
(1)计量(2)预压(3)预热(4)嵌件安放(5)加料(6)闭模(7)排气(8)保压固化(9)脱模冷却(10)制品后处理4. 在热固性塑料模压成型中,提高模温应相应地降低还是提高模压压力才对模压成型工艺有利?为什么?在一理论的操作温度下,模温提高时,物料的黏度下降、流动性增加,可以相对应的降低模压;但假设继续升高模温会使塑料交联反应速度增快、固化速率升高此时便需要提高模压。
一般而言提高温度应提高模压压力。
8. 试述天然橡胶硫化后的物理性能的变化,并解释之。
橡胶在硫化的过程中,交联密度发生了显着的变化。
随着交联密度的增加,橡胶的密度增加,气体、液体等小分子就难以在橡胶内运动,宏观表现为透气性、透水性减少,而且交联后的相对分子质量增大,溶剂分子难以在橡胶分子之间存在,宏观表现为能使生胶溶解的溶剂只能使硫化胶溶胀,而且交联度越大,溶胀越少。
硫化也提高了橡胶的热稳定性和使用温度范围。
天然橡胶在硫化过程中,随着线型大分子逐渐变为网状结构,可塑性减小,拉伸强度、定伸强度、硬度、弹性增加,而伸长率、永久变形、疲劳生热等相应减小,但假设硫化时间再延长,则出现拉伸强度、弹性逐渐下降,伸长率、永久变形反而会上升的现象。
10. 橡胶的硫化历程分为几个阶段?各阶段的实质和意义是什么?(1) 焦烧阶段又称硫化诱导期,是指橡胶开始前的延迟作用时间,在此阶段胶料尚未开始交联,胶料在模型内有良好的流动性。
对于模型硫化制品,胶料的流动、充模必须在此阶段完成,否则就会发生焦烧,出现制品花纹不清、缺胶等缺陷。
焦烧阶段的长短决定了胶料的焦烧性能和操作安全性。
(2) 预硫化阶段焦烧期以后橡胶开始交联的阶段。
在此阶段,随着交联反应得进行,橡胶的交联程度逐渐增加,并形成网状结构,橡胶的物理机械性能逐渐上升,但尚未到达预期的水平,但有些性能如撕裂性能、耐磨性能等却优于正硫化阶段时的胶料。
- 1、下载文档前请自行甄别文档内容的完整性,平台不提供额外的编辑、内容补充、找答案等附加服务。
- 2、"仅部分预览"的文档,不可在线预览部分如存在完整性等问题,可反馈申请退款(可完整预览的文档不适用该条件!)。
- 3、如文档侵犯您的权益,请联系客服反馈,我们会尽快为您处理(人工客服工作时间:9:00-18:30)。
1.金属液态成型工艺特点:1适应性强。
铸造方法不受零件大小、形状和结构复杂程度的限制,又可铸造各种合金2尺寸精度高。
节约金属材料和机械加工工时3成本低。
4废旧金属可以再生利用。
5存在结构缺陷。
铸件一般组织疏松,晶粒粗大,铸件内部有时会出现缩孔、缩松、裂纹和偏析等缺陷,导致力学性能降低6废品率高。
工序多,每道工序难以精确控制7对周围环境污染严重,生产环境差,劳动环境差、强度高2.液态金属充型过程有哪些水力学特点?1多相黏性流动。
钢水中含有夹杂物和气体2不稳定流动。
充型过程中物理场(温度、断面积、流速)在不断变化3紊流流动。
Re>>Re临,流路方向变化,紊流流动4在“多孔管”中流动。
浇注系统和铸型的型腔有透气性,像“多孔管”,液体在“多孔管”中流动5.奥赞公式的意义和成立条件是浇注系统水力学计算的基本公式,为合理设计浇注系统提供了依据成立条件:1浇注系统内充满流动2浇口杯液面保持不变3透气性好,4需满足伯努利(能量)方程6.液态金属充型能力,它与液态金属流动性有什么区别和联系?充型能力:液态金属充满型腔,获得完整形状、轮廓清晰的铸件的能力流动性:即合金金属的流动能力,是决定液态金属充型能力的内因,起主导作用,即流动性是充型能力的量度。
而充型能力还受外界条件的影响,铸型性质、浇注条件、铸型(件)结构也可以影响金属液的充型能力7.液态金属充型过程停止流动机理是?1对纯金属、共晶合金、窄结晶间隔的合金,靠近管壁的液态金属首先凝固,一般以柱状晶组织向管壁内推进,而中心的过热金属可以继续向前流动,而且可以全部或部分熔化正在生长的柱状晶,当液态金属的过热度散尽,柱状晶生长到中心,中间卡死,液态金属停止流动2对于有一定结晶温度范围的合金,他们在一定的范围内结晶,不断接触管壁的液态金属前端首先到达凝固温度,并有部分枝晶析出。
随着枝晶的增多,流动的阻力越来越大,流速越来越慢,到某一程度后,前端阻塞,液态金属停止流动。
影响因素:合金本身性能,铸型条件,浇铸工艺8.金属凝固动态曲线的意义是什么?把不同时间,不同位置到达同一温度点连接起来,就得到凝固动态曲线凝固动态曲线可以明确凝固区间,确定凝固过程中典型温度点(液固相温度)可以知道在某一时间某个断面所处的凝固状态(L、SL、S),从而合理制定铸造工艺。
逐层凝固:流动性好,易于获得健全的凝固体。
液体补缩性好,凝固的的组织致密,形成集中缩孔的倾向大,热裂倾向小,气孔倾向小,应力大,宏观偏析严重体积凝固:中间凝固:三砂两孔缺陷的特点,形成机理,影响因素,防止措施:夹砂结疤、鼠尾:鼠尾:型壁表面呈带状翘起,翘起砂层未破裂;沟槽:型壁表面呈带状凸起,凸起砂层未破裂;夹砂:型壁表面呈带状凸起后砂层破裂,但未折断;结疤:型壁表面呈带状凸起破裂后折断。
形成机理:浇筑过程中,砂型表面被金属液烘烤使砂型里外层产生温度差,产生水分迁移现象,形成了干砂区和高湿度低强度的水分饱和凝聚区,由于砂型里外层温度不同而使砂型各层的膨胀量不同,当表面烘干层膨胀受助时就会形成较大的热压应力。
当干砂区的热压应力大于水分饱和凝聚区的剪切应力时,干砂区边缘翘起而形成鼠尾缺陷;当水分饱和凝聚区热湿拉强度较低时,干砂区就会凸起导致分层,严重时砂层破裂金属液进入层间孔隙而形成夹砂缺陷,如果金属液将凸起的砂层冲断,在砂层折断部位就形成结疤缺陷,漂走的砂块还可能形成砂眼和表面砂孔缺陷等。
影响因素:干砂区的热应力越小,水分饱和凝聚区的抗拉强度越大,越容易产生防止措施:造型材料方面:1使用粒度分散的原砂2使用Na/Ca基膨润土做粘结剂可以提高热湿拉强度3使用能提高砂型热湿拉强度,降低表面烘干层热压应力的附加物,如煤粉,渣油4控制型砂含水量,降低含泥量.工艺方面:1缩短浇注时间,使金属液尽快充满型腔2合理设计浇注系统和浇注位置,避免局部型壁烘烤时间过长和过热3排气通畅4紧实度均匀,不宜过大粘砂:(机械/化学粘砂)特点:砂粒或含砂物质粘附在铸件表面难以清除形成机理:机械粘砂:根据毛细理论,将型砂表面砂粒间的微孔看成是直径细小的毛细管,金属液渗入微孔中便形成机械粘砂。
形成条件:P金〉P临=P气-P腔-P毛(2ocosO/r)影响因素:机械粘砂:1金属液凝固时间2砂型特点,孔尺寸大,激冷能力越弱,蓄热量越小,发气量越小,越容易产生机械粘砂3界面特性,控制界面气氛可以改变金属液对砂型的润湿性4金属液静压力:砂型某部位的金属液静压力与铸件高度和浇注位置有关,金属液静压力大的部位容易产生粘砂防止措施:1缩小砂型孔隙:使用细沙或刷涂料,提高紧实度 2缩短金属液对砂型的热作用时间:适当降低浇注温度,使用激冷材料3加附加物改善界面润湿条件型砂中加入受热时可生成不被金属液润湿的材料,可产生还原性气氛的附加物。
4调整液态金属的静压力化学粘砂:概念:金属氧化物渗入砂型微孔中并与砂粒起反应砂层结构:粘砂层=金属氧化层+烧结层(低熔点化合物)影响因素:氧化气氛和热作用防止措施:1控制氧化层,加入附加物产生还原性气氛,降低浇注温度,加入氧化铁粉等氧化剂2控制烧结层,加入附加物不被润湿,使用非石英砂非石英质涂料气孔特点:浇注时产生的大量气体未来得及排出侵入性气孔特点:1 数量少,体积大 2 孔壁光滑,表面氧化 3 梨形、椭圆形形成机理:在铸件/砂型界面处,P气>P静+P阻+P腔时,气体就会侵入到金属液中形成气泡,随着金属液的凝固,来不及上浮的气泡就形成气孔影响因素:1砂型的发气性、透气性 2 液态金属的性质:表面张力,润湿性等 3 浇注条件防止措施:1 控制砂型的发气性,减少造型材料中的发气物质,使用发气速度慢,发气温度高的造型材料。
2 增加砂型的透气性,扎气眼,设置排气道等,使用透气性好的背砂3 降低浇注温度胀砂:特点:砂型膨胀导致铸件尺寸变大形成机理:砂型受热膨胀,在金属液浇注凝固后,铸件依照胀的箱凝固,造成铸件尺寸变大,严重时铸件报废防止措施:1选用热膨胀系数小的镁砂或锆砂2增加砂型的排气能力3适当降低砂型的含水量4紧实均匀,紧实度不宜过大沙孔特点:在铸件表面或内部充塞着型砂形成机理:1 散落砂,未清理干净或合箱搬运中出现掉砂 2 冲砂金属液的冲击或者冲刷使砂型脱落,这些砂块在金属液凝固前未浮到冒口或积砂孔内,就会产生砂眼影响因素:落砂、冲砂防止措施:1 提高型砂的表面强度刷涂料,改进型砂配方 2 合理设置浇注系统和冒口,采用缓流,底注式浇注系统,设置排渣冒口 3严格执行操作规程,清理落砂11.砂型铸造时铸件铸型界面存在的作用?1热作用--传热,传质。
在金属和砂型之间有热交换,水分迁移,气体迁移和元素扩散。
热作用使砂型膨胀,容易使铸件产生夹砂结疤缺陷2机械作用--冲击,冲刷,静压力。
如果砂型表层强度不够,金属液将冲坏型壁,使铸件产生砂眼等表面缺陷。
如果砂型整体强度不够,型壁在金属液静压力下发生移动,使铸件产生尺寸误差(胀箱,肥大)3化学和物理化学作用--造型材料自身的分解和化学反应,可以改变界面气氛和压力,引起铸件气孔缺陷。
金属液和造型材料起化学和物理化学反应,可引起铸件粘砂,表面成分改变,气孔等缺陷。
18.湿型砂的型砂要求具备哪些工艺性能,这些性能对铸件质量有什么影响?4个基本性能:湿态强度,透气性,流动性,可塑性韧性;1个综合性能:干湿程度2个扩充性能:抗夹砂结疤能力,抗粘砂能力湿态强度:湿态强度、干态强度、高温强度、残余强度过低时,在造型、下芯、合箱、搬运中可造成砂型破损,在浇注时砂型表面易被金属液冲坏、型壁移动,使铸件产生砂眼,胀箱和跑火缺陷;过高时,砂型的退让性差,铸件易产生裂纹,落砂不易,影响铸件表面质量。
检测方法:(试样)万能强度试验机湿态强度(砂型)型砂表面强度计测表面强度。
透气性:差时,排气不利,铸件产生气孔、浇不足缺陷,严重时出现呛火;太好时,型砂微孔尺寸大,易产生粘砂和表面粗糙检测方法:透气性测定仪流动性:好时,可形成紧实度均匀、轮廓清晰、表面光洁的型腔,造型效率高检测方法:阶梯硬度法,侧孔质量法,环形空腔法和试样质量法可塑性和韧性:好时,型砂起模性好,砂型不易损坏,型腔轮廓清晰,造型效率高检测方法:破碎指数抗粘砂能力:发气量小时粘砂,发气量大时,气孔,冷隔,浇不足干湿程度:太湿时,易夹砂结疤,气孔,浇不足,胀砂;太干时,易冲砂,砂眼,所以砂型要有适宜的干湿度,才能减少缺陷。
20. 原砂有哪些性能?对型砂性能有哪些影响?原砂性能包括含泥量、颗粒组成、颗粒形貌、矿物组成和化学成分、pH值和需酸值影响:1含泥量 1原砂中泥分增多,则型砂的孔隙直径减小,透气性下降 2其他条件相同时,含泥量增加,型砂的湿态抗压强度提高,达到最适宜干湿程度的型砂含水量也提高 3若泥分中不含粘土矿物,则含泥量增加会使型砂变脆,起模性差2颗粒组成:包括粒度和粒度分布,颗粒组成会影响型砂的孔隙率和微孔尺寸,孔隙率越大,透气性越好。
3颗粒形貌:包括砂粒的形状和砂粒的表面状况1砂粒形状:对湿型砂而言,通常选用圆形砂,有利于粘结剂更有规则和均匀的分布,使砂粒间能形成较好的粘结膜,另一方面,圆形砂流动性好,易紧实,可得到较高的湿态强度和适宜的透气性4矿物组成和化学成分:石英砂的矿物成分主要是石英砂, SiO2含量越高,型砂的耐火度越高5需酸值:需酸值是原砂中含有的与酸反应的物质的表征,需酸值高,会影响树脂砂的硬化性能和终强度22.粘土的矿物成分,粘土的矿物晶体结构的基本结构单位,膨润土的结构特点和性能粘土的矿物成分是含水的硅酸盐,用化学式表示为mAl2O3·nSiO2·xH2O 基本结构单位是硅氧四面体和铝氧八面体膨润土的性能:颗粒尺寸较细,吸水膨胀性大,加热体积变化大,粘结性好,型砂流动性,韧性好,钠基膨润土热湿拉强度高25.连铸机的主要形式:垂直立弯形直弧形全弧形椭圆形水平式26.连铸机生产铸坯的断面有哪几种,铸坯断面形式是有什么决定的?方坯连铸机板坯连铸机圆坯连铸机矩形坯连铸机异形坯连铸机断面形式由结晶器决定28. 影响连铸坯表面质量的因素?结晶器的传热性,结晶器的振动,保护渣的性能,结晶器的倒锥度30.连铸坯的凝固过程有何特点?钢液表面有保护渣,主要通过结晶器散热结晶器上部有渣膜(润滑)保护,不和钢液直接接触,结晶器下部已经凝固成壳,中间有气隙钢坯内部有很深的液心铸坯断面多为向心的柱状晶24. 酸催化树脂自硬砂有何特点?使用何种树脂和催化剂?如何控制自硬砂的硬化速度和硬化强度?酸催化树脂自硬砂是指原砂(或再生砂)以呋喃树脂或热固性酚醛树脂为黏结剂,在相应的酸性催化剂作用下,在室温下自行硬化成形的一类型(芯)砂,其基本特点为:1型(芯)砂的硬化过程无需加热,同时可采用木质或塑料芯盒和模板2与黏土砂和水玻璃砂相比,铸件的尺寸精度高,表面质量好。