品质改善活动的改善案例ppt课件
合集下载
品质改善专案完美版PPT

4、设 计对 灌注 口的 保护 装置。 订 立长 期灭 蚊的 方案程 序 。
包 装 厂
包 装 厂 品 检 部 XM/包 装 厂
专案具体的目标及成效
专案具体的目标:
• 杂质事故发生率为“3瓶/一百万瓶”(3瓶/5000T) (此处指小包装油中含有较明显的杂质,即引起
消费者反感/不满的异物) • 小包装油内有蚊子或其它飞虫的事故发生率为0
蚊子
环境
1
0.11
合计
972
100
备注
表二数据说明:1)70%的杂质来源于物料或设备产生, 小黑点多为焊 点、锈点,还有一部分较难发现的小黑点可能来自瓶子本身。2)明显来 自物料 的杂质占了29%,这类杂质有三种:A、透明胶丝:一般残留 瓶口的丝状披锋;B、白胶丝:套瓶口时刮伤白色手挽所致或密封盖里 面残留的锋边。C、胶冰颗粒:附在瓶子里面,直径较大,约0.5至3MM 3)由环境因素引起的杂质比例虽然不到1%,但属严重质量问题,有头发、
蚊子、蚂蚁。
此专案成立背景(续二)
出现较严重的有关产品质量方面的投诉
市场上曾经发现我司极少量的小包装 产品中含有苍蝇、蚊虫等昆虫及头发、纸 屑等杂质;
小包装产品杂质来源分析
编编号 杂质来源
改善方案
负责部门
1 空瓶(空罐)中 1. 含有的杂质来源 2.
3.
加大对空瓶进货检验的抽样量,从 0.1%提高到 0.2%
分之三,相差千倍。 D线由于较多PVC材料胶樽,而PVC由于带静电而吸引较多杂质
于胶樽之内,导致杂质出现机率较多
此专案成立背景(续一)
二、杂质来源分析表(表二)
杂质名称 来 源 数量(支) 百分比%
小黑点 设备或物料 681
包 装 厂
包 装 厂 品 检 部 XM/包 装 厂
专案具体的目标及成效
专案具体的目标:
• 杂质事故发生率为“3瓶/一百万瓶”(3瓶/5000T) (此处指小包装油中含有较明显的杂质,即引起
消费者反感/不满的异物) • 小包装油内有蚊子或其它飞虫的事故发生率为0
蚊子
环境
1
0.11
合计
972
100
备注
表二数据说明:1)70%的杂质来源于物料或设备产生, 小黑点多为焊 点、锈点,还有一部分较难发现的小黑点可能来自瓶子本身。2)明显来 自物料 的杂质占了29%,这类杂质有三种:A、透明胶丝:一般残留 瓶口的丝状披锋;B、白胶丝:套瓶口时刮伤白色手挽所致或密封盖里 面残留的锋边。C、胶冰颗粒:附在瓶子里面,直径较大,约0.5至3MM 3)由环境因素引起的杂质比例虽然不到1%,但属严重质量问题,有头发、
蚊子、蚂蚁。
此专案成立背景(续二)
出现较严重的有关产品质量方面的投诉
市场上曾经发现我司极少量的小包装 产品中含有苍蝇、蚊虫等昆虫及头发、纸 屑等杂质;
小包装产品杂质来源分析
编编号 杂质来源
改善方案
负责部门
1 空瓶(空罐)中 1. 含有的杂质来源 2.
3.
加大对空瓶进货检验的抽样量,从 0.1%提高到 0.2%
分之三,相差千倍。 D线由于较多PVC材料胶樽,而PVC由于带静电而吸引较多杂质
于胶樽之内,导致杂质出现机率较多
此专案成立背景(续一)
二、杂质来源分析表(表二)
杂质名称 来 源 数量(支) 百分比%
小黑点 设备或物料 681
《品质改善计划案》PPT课件培训资料
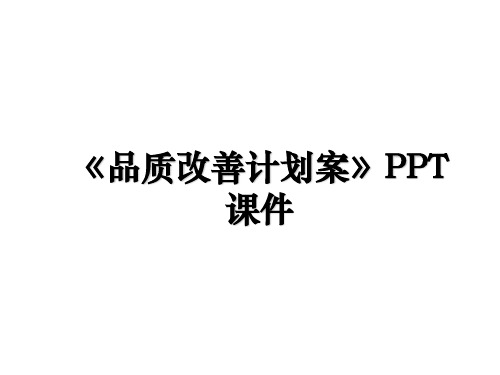
21
Байду номын сангаас
管理者及领导人的工作
1.制定流程及方法。(ex.作业指导书) 2.已决定的事情,要执行并指导作业员按要求作
业。 3.做过的事情应做好记录归档(ex.确认明细表) 4.跟进。
①定期确认是否有严格按照指示做事 ②一旦发现问题(或不良)、应马上调查原因 。
☆品质是要靠全体人员努力!☆
结束
实施项目
项目
来料品质 制造品质(工程 品质) 出货品质 完善「方案」
内容
实况调査~对策 实况调査~对策
资料etc
检查标准 作业指导书
实况调査~对策
是否有做到“正确=不流出 不良品”的方案?
检查标准
作业指导书 确认
担当
期限
「方案」的推行、 按照“方案”实施。确认其 确认明细表
持续
结果并反馈。
建立管理体制
管理层教育-4
*从玉置K报告书看、品质改善的关键 (付1/6报告书) ①作业遗漏属频繁发生现象 ②集中确认体制一事(作业员与其他检查员一起检查。) ③作业员不能活用作业指导书。无法读懂作业指导书的内容
/也无法理解其内容。因此,现状是需有生产线的管理人 员进行指导下才能生产。
①一定要使用确认明细表 ②一定要建立按照作业指导书作业的体制 ③一定要实施不良对策~再发防止对策
19
案例方法-1
*事先收集情报 ①正确编制作业指导书。⇒前提条件 ⇒作业指导书的确认由客户方事先完成实施。 ②未严格按照作业指导书正确作业。⇒問題点 ③检查工位发现工程不良时,只是返回重做。⇒无再发防止对策。
“应该要做的事情未完成”是个最大的問題点!作业员的问题,或管理者、领导的 问题!
20
案例方法-2
Байду номын сангаас
管理者及领导人的工作
1.制定流程及方法。(ex.作业指导书) 2.已决定的事情,要执行并指导作业员按要求作
业。 3.做过的事情应做好记录归档(ex.确认明细表) 4.跟进。
①定期确认是否有严格按照指示做事 ②一旦发现问题(或不良)、应马上调查原因 。
☆品质是要靠全体人员努力!☆
结束
实施项目
项目
来料品质 制造品质(工程 品质) 出货品质 完善「方案」
内容
实况调査~对策 实况调査~对策
资料etc
检查标准 作业指导书
实况调査~对策
是否有做到“正确=不流出 不良品”的方案?
检查标准
作业指导书 确认
担当
期限
「方案」的推行、 按照“方案”实施。确认其 确认明细表
持续
结果并反馈。
建立管理体制
管理层教育-4
*从玉置K报告书看、品质改善的关键 (付1/6报告书) ①作业遗漏属频繁发生现象 ②集中确认体制一事(作业员与其他检查员一起检查。) ③作业员不能活用作业指导书。无法读懂作业指导书的内容
/也无法理解其内容。因此,现状是需有生产线的管理人 员进行指导下才能生产。
①一定要使用确认明细表 ②一定要建立按照作业指导书作业的体制 ③一定要实施不良对策~再发防止对策
19
案例方法-1
*事先收集情报 ①正确编制作业指导书。⇒前提条件 ⇒作业指导书的确认由客户方事先完成实施。 ②未严格按照作业指导书正确作业。⇒問題点 ③检查工位发现工程不良时,只是返回重做。⇒无再发防止对策。
“应该要做的事情未完成”是个最大的問題点!作业员的问题,或管理者、领导的 问题!
20
案例方法-2
品质改善及计划PPT课件
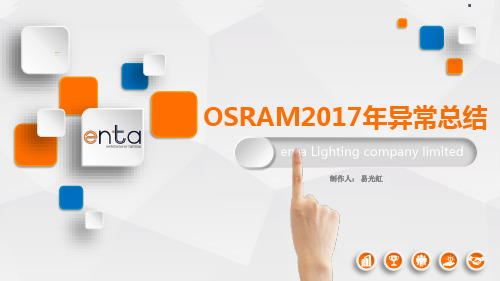
检验数量 合格数 不良率 灯珠偏位 IC偏位 ICL连锡 其他
479699 6607 1.377% 0.259% 0.553% 0.322% 0.243%
SMT炉后不良统计
0.243% 0.259%
0.322%
0.553%
灯珠偏位 IC偏位 ICL连锡 其他
检验数量
2017年成品不良数据统计(主要不良统计)
经理:1 人
文员/文控 1 人
检验组:组长/副主管 1 人
三楼 QC:6 人
三楼 IPQC: 1人
6 楼 QC: 9人
6楼 FQC:2 人
6楼 IPQC:2 人
SQE 1 人 IQC 组长 1 人 IQC:2 人
QE 2 人
6楼 QA:3 人
实验室技术员 1人
品质工作计划
序 任务名称 号
1
品质流程改善
不合格数 不良率 灯不亮
不良分类
丝印不良 脏污
焊盘偏位 其他
479699
8946 1.87% 0.768% 0.378% 0.250%
成品检验不良分类
0.019% 0.45%
0.45% 0.019%
0.250%
0.768%
0.378%
灯不亮 丝印不良 脏污 焊盘偏位 其他
SMT不良改善——灯珠不亮
二、改善对策 1.来料过程: ①由SQE重新制定检验标准“针对性VIP客户专项检验标准,检验报表修改”,避免作业人员操作时按照其内容执行无遗漏操作或检验不彻底登现象。——已完成 (FPC、标签) ②SQE对与IQC平时作业方式进行监督、稽核确认作业方式是否合理,按照规定执行,品质经理每天不定时进行现场稽核 ③对于来料检验样品进行整理,归类,建立电子档案,便于查找 ④供应商对此异常进行流程改善——
479699 6607 1.377% 0.259% 0.553% 0.322% 0.243%
SMT炉后不良统计
0.243% 0.259%
0.322%
0.553%
灯珠偏位 IC偏位 ICL连锡 其他
检验数量
2017年成品不良数据统计(主要不良统计)
经理:1 人
文员/文控 1 人
检验组:组长/副主管 1 人
三楼 QC:6 人
三楼 IPQC: 1人
6 楼 QC: 9人
6楼 FQC:2 人
6楼 IPQC:2 人
SQE 1 人 IQC 组长 1 人 IQC:2 人
QE 2 人
6楼 QA:3 人
实验室技术员 1人
品质工作计划
序 任务名称 号
1
品质流程改善
不合格数 不良率 灯不亮
不良分类
丝印不良 脏污
焊盘偏位 其他
479699
8946 1.87% 0.768% 0.378% 0.250%
成品检验不良分类
0.019% 0.45%
0.45% 0.019%
0.250%
0.768%
0.378%
灯不亮 丝印不良 脏污 焊盘偏位 其他
SMT不良改善——灯珠不亮
二、改善对策 1.来料过程: ①由SQE重新制定检验标准“针对性VIP客户专项检验标准,检验报表修改”,避免作业人员操作时按照其内容执行无遗漏操作或检验不彻底登现象。——已完成 (FPC、标签) ②SQE对与IQC平时作业方式进行监督、稽核确认作业方式是否合理,按照规定执行,品质经理每天不定时进行现场稽核 ③对于来料检验样品进行整理,归类,建立电子档案,便于查找 ④供应商对此异常进行流程改善——
品质提升改善方案(ppt共20张)

品质提升改善方案(PPT20页)
品质提升改善方案(PPT20页)
长期计划
制程
来料
工程
品质
检查 体制
提升 体制
品质提升改善方案(PPT20页)
品质提升改善方案(PPT20页)
实施细则(1)
来料品质--进料接收标准,供方审核
一、供应商现场检讨分析 二、来料不良追踪/回复/改善效果确认 三、供应商定期辅导培训 四、供应商现场审核 五、供应商品质异常处罚 六、供应商份额调配 页)
改善方针
三
不接受不良品
不
不制造不良品
原
则
不传递不良品
制定严禁不良品流入下一工序的管理方案,并持续不断地 构建一个完善的管理体系。
品质提升改善方案(PPT20页)
品质提升改善方案(PPT20页)
改善团队
姓名
XX XX XX XX XX XX XX XX XX XX XX XX XX
品质体系提升
质量体系--全员参与,提高品质意识
一、工作流程化 二、作业标准化 三、文件规范化 四、人员信息化 五、质量精细化
品质提升改善方案(PPT20页)
供应商管理
来料品质--进料接收标准,供方审核
一、完善进料品质检查记录,确保源数据的 真实性、可靠性及可追溯性,对异常频发的 供应商进行辅导,推动供应商进行内部改善。 二、年内对供应商进行审核评分,对供应商 的经营状况、财务状况、生产能力、设备状 况及质量管理体系等方面进行摸查,对未能 达到我司要求的供应商进行淘汰更换。
品质提升改善方案(PPT20页)
品质提升改善方案(PPT20页)
实施细则(5)
提升体制--全员参与,提高品质意识
一、建立品质考核制度,提升操作人员 的责任感。
品质提升改善方案(PPT20页)
长期计划
制程
来料
工程
品质
检查 体制
提升 体制
品质提升改善方案(PPT20页)
品质提升改善方案(PPT20页)
实施细则(1)
来料品质--进料接收标准,供方审核
一、供应商现场检讨分析 二、来料不良追踪/回复/改善效果确认 三、供应商定期辅导培训 四、供应商现场审核 五、供应商品质异常处罚 六、供应商份额调配 页)
改善方针
三
不接受不良品
不
不制造不良品
原
则
不传递不良品
制定严禁不良品流入下一工序的管理方案,并持续不断地 构建一个完善的管理体系。
品质提升改善方案(PPT20页)
品质提升改善方案(PPT20页)
改善团队
姓名
XX XX XX XX XX XX XX XX XX XX XX XX XX
品质体系提升
质量体系--全员参与,提高品质意识
一、工作流程化 二、作业标准化 三、文件规范化 四、人员信息化 五、质量精细化
品质提升改善方案(PPT20页)
供应商管理
来料品质--进料接收标准,供方审核
一、完善进料品质检查记录,确保源数据的 真实性、可靠性及可追溯性,对异常频发的 供应商进行辅导,推动供应商进行内部改善。 二、年内对供应商进行审核评分,对供应商 的经营状况、财务状况、生产能力、设备状 况及质量管理体系等方面进行摸查,对未能 达到我司要求的供应商进行淘汰更换。
品质提升改善方案(PPT20页)
品质提升改善方案(PPT20页)
实施细则(5)
提升体制--全员参与,提高品质意识
一、建立品质考核制度,提升操作人员 的责任感。
品质改善计划PPT课件
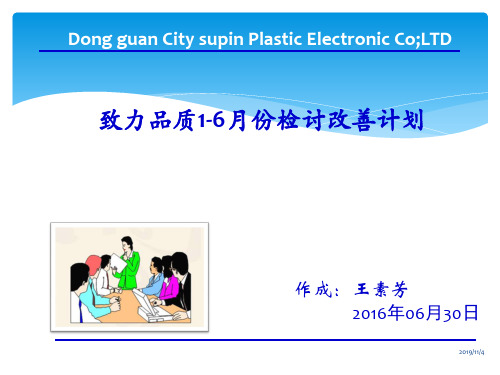
功能不良 累计不良率
尺寸不良
120.00% 100.00% 80.00% 60.00% 40.00% 20.00% 0.00%
前三大不良 外观不良 作業不良 功能不良
原因分析
改善对策
责任人
1.员工对品质意识不强,没有做好自检 好。 2.品管没有严格依样品检查,工作疏忽 导致不良品流出 3.黑色产品表面发亮,因调机不合理, 温度未控制好导致
06mms155pc202371a0spnr支架16000043抽檢48pcs發現變形及熱溶銅柱包膠2pcsg330pe601732a0spnr面板29900156抽檢32pcs發現碰傷3pcs飛油2pcss155pj200821aspnr992015抽檢40pcs發現水口位毛邊6pcss155pc202331a0spnr支架2840s155pl201271a0spnr導光柱1200003437抽檢32pcs發現來料乳白色1pcs導燈發黃10pcss555rj200881a0spnr4400063抽檢32pcs發現缺料2pcss155pj200812a0spnr抽檢12pcs發現表面印力痕明顯10s155pl201271a0spnr導光柱390000333抽檢12pcs發現來料燈發黃4pcs11s155pb201301a0spnr5640125抽檢32pcs發現來料側面削傷4pcss555pj200871a0spnr4320313抽檢32pcs發現殘膠絲10pcs13s555pa200811a0spnr面板1790094抽檢32pcs發現表面料花2pcs水口未削平1pcs14g330pb602541a0spnr15000229抽檢48pcs發現卡鉤變形11pcs15s458pj200711a0spnr86801抽檢20pcs發現卡鉤變形2pcs16s155pl201271a0spnr90000125抽檢32pcs發現燈頭毛邊4pcss458pc2019912001a0spnr前后架36000125抽檢32pcs發現前后架混料4pcs18s555pa200811a0spnr面板6750125抽檢32pcs發現刮傷2pcs飛油2pcs19g330pb602541aspnr14200145抽檢48pcs發現卡鉤斷1pcs變形6pcs20s555pa200811a0spnr160019抽檢32pcs發現發白5pcs水口削傷1pcs21s458pe202873b0spnr67302抽檢10pcs發現拉高2pcs22s458pe202873b0spnr抽檢32pcs發現拉高及雜質dongguancitysupinplastielectronicco
《品质的改善与提升》PPT课件

1
2
3
4
5
6
7
8
9
10
11
12
客诉总数
21
10
10
客诉总数
25
20
15
客诉总数 10
5
0
1
2
3
4
5
6
7
8
9
10
11
12
存在关键问题: 虽然连续3个月虽客诉数量在下降,但是仍无影灯电器部件问题及液压床漏油、不动作等问题在连续发生:1、品质保
证的预警机制不强,预防为主机制执行较差;2、相关检验测试人员的专业性与过程控制能力不强。
1、产品实现全过程的品控保证体系还需 强化执行力与持续改进与完善; 2、供应链的质量保证能力要求与管理提 升势在必行;
内部 因素
公司的生产规模与产值急剧 扩大,产品种类较多,质量 管理工作难度增加;
公司领导战略决策,公司产 品向高端进军规划
1、建立系统化的质量成本管理与价值创 新工程管理是关键; 2、流程与制度标准化、组织职能全面强 化,质量管理工作要求更趋于精细化与专 业化;要求组织团队的快速反应能力与效 率的持续提升; 3、真正具有核心竞争力的供应链建设;
h
8
二、内外部环境因素变化对未来公司质量管理的要求
h
9
环境变化实事描述
对质量管理的要求
外部 因素
行业产品之间的竞争更趋白 热化“产品品质与服务品质 整合“更为突出
医疗器械产品法规、认证要 求不断升级与处罚加严将成 为必然的趋势与强制性要求 执行,企业的风险加剧!
1、持续稳定与提升产品品质为核心任务 2、建立完善服务品质保证机制与持续改 进;
5、实行工序能力“CPK”定标管制控制与改进,给员
《品质改善计划案》课件

根据实际数据和指标 ,制定针对性门间的沟通与协作,共同推进品质改善工作。
定期召开跨部门会议,分享经验,解决问题,提高工作效率。
品质改善的策略
策略三:员工培训与激励 对员工进行品质意识培训,提高其对品质的认识和重视程度。
设立品质奖励机制,激励员工积极参与品质改善工作。
01
02
03
预期效果二:提升产品 竞争力
提高产品合格率和减少 不良率,降低生产成本
。
增强产品在市场上的竞 争力,提高市场份额。
品质改善的预期效果和目标
预期效果三:建立品质文化
提高员工对品质的认识和重视程度,形成全员 参与的品质文化。
培养一支具有高度责任感和工作热情的员工队 伍。
04
品质改善的实施与监控
通过实施品质改善计划,产品质量得到了显著提 升,客户满意度提高。
生产效率提高
通过优化生产流程和减少浪费,生产效率得到了 显著提高,降低了生产成本。
员工参与度增强
品质改善计划的实施过程中,员工的参与度和归 属感得到了增强,提高了工作积极性。
品质改善的效益分析
经济效益
品质改善计划实施后,企业经济效益得到了显著提升,销售额和 利润增长。
对品质改善计划的实施效果进行 总结,分析成功经验和存在的问 题,为后续的品质改善提供借鉴
和参考。
优化与改进
根据总结和反馈的结果,对品质 改善计划进行优化和改进,以提
高实施效果。
推广与应用
将成功的品质改善经验在组织内 进行推广和应用,以提高整体品
质水平。
05
品质改善的成果与展望
品质改善的成果展示
产品质量提升
品质改善的步骤和时间安排
步骤一:问题识别 收集和分析客户反馈,识别产品或服务中存在的问题。
品质提升计划改善报告ppt
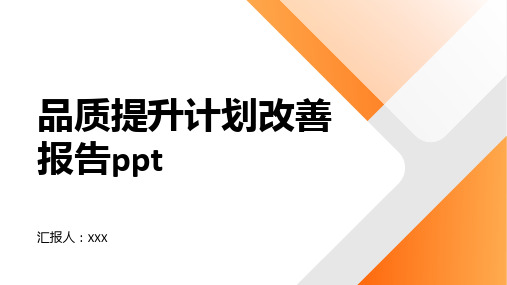
品质提升计划改善后的效果预测
效率提高
预计工作流程优化后,生产效率和整
体产出将得到大幅提升。 01
客户满意度增加
预计客户对于改进后的产品和服务的
满意度将得到显著提升。
03
减少次品率
预测经过改善,产品的次品率将大幅
下降,从而提高整体产品质量。 02
04
品质提升计划改善后的 效果评估
品质提升计划改善后的效果对比
生产效率提升 01
改善后,生产效率提高了20%,产品制造周期缩短。
质量合格率提高 02
经过改善,产品质量合格率由原先的85%提高到了95% 以上。
客户投诉率降低 03
品质提升计划改善后,客户投诉率降低了30%,客户满 意度得到显著提高。
品质提升计划改善后的经验总结
优化生产流程
简化流程、提高效率和产品质 量
04 加强品质监控
加强品质监控和检测,及时发现和解决品质问 题,确保产品品质稳定提升。
05
品质提升计划未来展望
品质提升计划未来的发展方向与目标
持续改进
我们将持续优化品质管理体系, 通过技术创新和流程优化提升 产品品质。
客户满意度提升
我们将深入了解客户需求,加 强与客户沟通,不断提升客户 满意度。
品质提升效果
通过品质提升计划,产 品合格率提高了20%, 客户满意度也相应提升。
成本节约
品质提升计划实施后, 减少了因退货和重新生 产导致的成本浪费,为 公司节约了大量资金。
员工参与度
品质提升计划的实施, 提高了员工的参与度和 责任感,形成了全员关 注品质的良好氛围。
02
品质提升计划实施过程
品质提升计划的实施步骤
3
《品质改善报告》课件
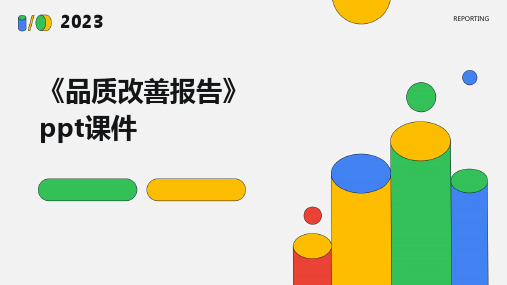
REPORTING
总结
品质改善的背景
介绍当前品质问题的严重性, 以及品质改善的必要性和紧迫
性。
品质改善的历程
概述品质改善的整个过程,包 括问题识别、原因分析、解决 方案制定和实施等。
品质改善的成果
详细介绍品质改善所取得的成 果,包括产品合格率提升、客 户满意度提高、成本降低等。
品质改善的经验教训
总结在品质改善过程中所遇到 的问题和困难,以及应对策略
03
02
详细描述
04
引入先进的生产技术和方法,优化工艺流 程。
制定详细实施计划,确保工艺改进顺利进 行。
05
06
持续监测改进效果,进行必要的调整和优 化。
方案二:设备升级
总结词:通过升级生产设 备,提高产品质量、生产
效率和降低成本。
对现有设备进行全面评估 ,确定需要升级的设备和
部位。
制定设备安装和调试计划 ,确保设备正常运行。
对培训效果进行评估和反 馈,持续改进培训计划。
2023
PART 04
品质改善实施计划
REPORTING
实施步骤一:方案准备
目标设定
明确品质改善的目标,包括提高 产品合格率、降低不良品率等。
现状分析
对当前品质状况进行深入分析, 找出问题所在,为后续方案制定
提供依据。
方案制定
根据现状分析结果,制定相应的 品质改善方案,包括改进工艺、
随着市场竞争的日益激烈,提高产品 品质成为企业赢得市场的关键。
企业生产过程中存在一些品质问题, 如不良品率较高、产品性能不稳定等 ,需要解决。
客户对品质要求提高
客户需求日益多样化,对产品品质的 要求也越来越高,促使企业不断改进 品质。
质量改善案例模板.ppt

生产科/ 技术品 管科
程兴/何 永华
2011.1.16
Y
追求技术创新,铸造完美品质
质量问题 ,我去解决
请领导批评指正!
追求技术创新,铸造完美品质
Hale Waihona Puke 5改善后此产品胶口位置已改动, 产品质量问题稳定
对比
追求技术创新,铸造完美品质
品质改善专项工作汇报
质量问题 ,我去解决
3、下周改善工作计划:
问题描述 原因分析
改善对策
责任部 门
责任人
计划完成 实际完 状 态 时间 成时间 G/Y/R
备注
J48副仪表 板本体调 试时报废 过多
机床、工艺不 稳定
召集汽车件车间相 关技术人员共同讨 论各工序的控制。
品质改善专项工作汇报
质量问题 ,我去解决
2、改善工作成果展示:
改善1: 改善前:客户多次投诉产品胶口处未修平,导致主机厂焊接有缝隙。 改善后:根据客户样件要求,工程科对模具进行改进,现客户已认可,产品质量处
于稳定状态。 见下图:
改善前
工程科见产品封样件的要 求整改
此位置有5个胶口需要对其胶口改位置
目录
质量问题 ,我去解决
一、品质改善专项工作汇报
1、上周改善专项工作内容 2、改善工作成果展示(最好以数据说话) 3、下周改善工作计划
追求技术创新,铸造完美品质
品质改善专项工作汇报
1、上周改善专项工作内容:
质量问题 ,我去解决
客户多次投诉产品胶口处维修平,导致主 机厂焊接有缝隙
追求技术创新,铸造完美品质
产品品质改善报告模版 ppt课件
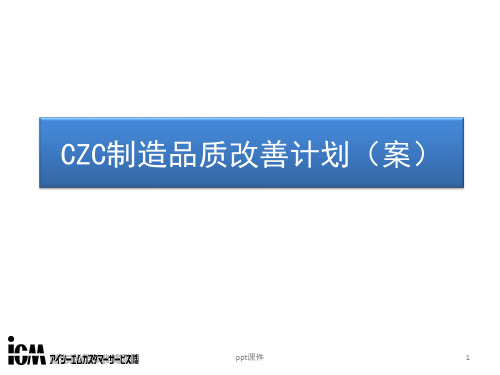
ppt课件
16
• 针对品质改善的管理
(生产线上管理者及领导者的任务)
ppt课件
17
不良对策3原则 1.不接收不良品 2.不生产不良品 3.不流出不良品
基本方针
→来料品质 →(制造)工程品质 →出货品质
制定严禁不良品流到下一工程的“方案”、并持续不断地构建一个完善的管 理体制。
ppt课件
18
重点措施
CZC制造品质改善计划(案)
ppt课件
1
不良对策3原则 1.不接收不良品 2.不生产不良品 3.不流出不良品
基本方针
→来料品质 →(制造)工程品质 →出货品质
制定严禁不良品流到下一工程的“方案”、并持续不断地构 建一个完善的管理体制。
ppt课件
2
重点措施
采用ISO的手法 1.构建“正确”的方案
⇒“正确”的方案要标准化。 2.全员理解该“方案”。 3.实施该“方案”,并要让其延续。 4.保留实施“方案”的记录。 5.结果跟进。
ppt课件
15
管理层教育-4
*从玉置K报告书看、品质改善的关键 (付1/6报告书) ①作业遗漏属频繁发生现象 ②集中确认体制一事(作业员与其他检查员一起检查。) ③作业员不能活用作业指导书。无法读懂作业指导书的内容
/也无法理解其内容。因此,现状是需有生产线的管理人 员进行指导下才能生产。
①一定要使用确认明细表 ②一定要建立按照作业指导书作业的体制 ③一定要实施不良对策~再发防止对策
☆ 管理者、领导层 包括作業员需有全员共识 :「严禁不良品流出」
ppt课件
6
实施项目
项目
来料品质 制造品质(工程 品质) 出货品质 完善「方案」
内容
- 1、下载文档前请自行甄别文档内容的完整性,平台不提供额外的编辑、内容补充、找答案等附加服务。
- 2、"仅部分预览"的文档,不可在线预览部分如存在完整性等问题,可反馈申请退款(可完整预览的文档不适用该条件!)。
- 3、如文档侵犯您的权益,请联系客服反馈,我们会尽快为您处理(人工客服工作时间:9:00-18:30)。
QCC改善活动资料
1
选定主题—选择
异常原因分析和对策中必备项:
1.生产不良 制造原因只有在产品生产时发生及对策
2.流出不良 流出原因在制造过程和检查过程都会 产生。并如在出货检查时防止异常流出, 可达成客户要求的标签与实物不符不良 不良件数“0”目标
2
选定主题—定案
减少客户投诉中多数量不良,达成客户 PPM目标。 理由是: *客户每年都有相关联络,要求各供应商 减少标签与实物不符的异常。 *品管检查作业方法中可以对应。
件
10月份纳入不良个数明细
不良数 不良比率
500
112233445050505050500000000000
56.1% 386 43.3%
2 0.2%
1 0.1%
1 0.1%
60.0% 50.0% 40.0% 30.0% 20.0% 1 10.0% 0.1% 0.0%
标签与实物不符 外观不良 露底不良 寸法不良 组装不良 性能不良
作业台
人
培训不足 标准不了解
未按照作业标 准实施
线上配料异常
料
工作时间太 长,疲惫
人员工作时精 神不集中
个人原因
流
出
不
良
原
因
分
析
来料错误
来料错误时,受入检查 和工程中的生产前确认 可发现,需提前预防。
8
喔哦~
原因分析—分析结论说明
NO
不良项目
原因
对策
人
1.培训后向受训人确认培
为 因
训内容是否理解;
6
设定目标
来来来,一 起来改善!
出货检查流程及方法: 1.制造完成品检查
(全数检查)
☆本次对应改善的工程 为出货检查区域,检 查人员的警惕性提升, 标签与实物不符为0
挑中你 了~~
2.品管出货检查 (初期流动品和海外向的全 检,
其他的抽检)
3.制造出库后入生管仓库 (入库品不可再开箱和换标签)
4.按照日期出货
4
分析图中异常项目说明
不良项目依次为:
GA-1标签错误,GA-2产品混装, GC-1异品组装,GC-3组装位异常, GC-6连接不良, GC-8组装部位欠品, GD-1外观破损, GD-2外观变形, GD-3有瑕疵打痕, GD-4打磨或颜色不良,GD-5表面处理不良, GD-8外观缩水, GD-9其他外观异常, GE-1操作不良, GE-2性能不良, GE-4异音不良, GE-7回转不良, GF-1未加工, GF-2尺寸不良, GF-4形状异常, GF-9加工时其他不良, GZ-9其他不良项
3
分析现状—异常分析图
09年度纳入不良明细
不良个数 不良件数
1200
9
1000
10448
不良发生时个数较多
8
7
800
不
良
599
个 600
4
4
数
5 4
6 不
5
5良
4件 数
400 3
3
3
3
245 2
22 2 2
22 2
2
22
200
2 7 13 2 25 6 18
1 1 4 1 11 5 29 35 11 2
7
原因分析—鱼骨图分析 怎么办 呢?
另附资料说明
法
检查指示书在正式 使用前会做检查前 培训,如有疑问或 后续有疑问时也可 资料难懂 提出,视情况可追 加项目。
作业指示书说 明不足
作业区域无法调 整,到再增产或 有必要时,开两 班检查
作业区域小,人 员作业位置小
作业环境不够 亮,无法检出
每月进行灯管 确认,750露 克斯以上,可 对应
多,导致生产延迟,出货时
协助对应;
间不更改,紧急对应品增多 3 . 做不定期的不良测试
及
日常生活中都有心情 唯有提高检查员的警惕
对 策
3
个人原因,精 烦闷之时,所以无法 神不集中 避免会有开小差的事
性,并了解产品的重要性 后,认真对待检查品
*做不定期的不良测试,
情
提升检查员的警惕性
9
原因分析– 补充
9
102
1 12
1
0
0
GA-1标G签A-错2产误G品C-混1G异装C-品3组组装装G位CG-异C6-连常8组接装不部良G位D-欠1外品G观D-破2G外损DG-观D3-有变4打瑕形磨疵G或打D-颜痕5表色面不处良G理DG-不D8-外良9其观他缩外水G观E-异1操常G作E-不2性良G能E-不4异良G音E-不7回良转G不F-良1G未F-加2尺工GG寸FF--不94加形良工状时异G其常Z-他9其不他良不良项
5
现状分析—年度数据
不良个数最高为:
1.颜色异常1044个(多工序检查,品管抽检,无法全数管控) 2.标签错误599个(多工序检查,品管可管控) 3.产品混装245个(多工序检查,品管抽检,无法全数管控)
不良件数最高为:
1.颜色不良5件(多工序检查,品管抽检,无法全数管控) 2.寸法不良5件(成形组立工程检查,品管无法管控) 3.产品混装4件(多工序检查,品管抽检,无法全数管控) 4.连接不良4件(多工序检查,品管抽检,无法管控) 5.操作不良4件(多工序检查,品管抽检,无法管控)
1
培训不足
培训后不理解
2.正式作业前对受训人做 作业观察,并确认其检查
素
后的产品(班组长); 3.做不定期的不良测试
原
1.随着客户增产的趋势,生 1.控制加班时间,每天加
因 分 析
产线也随着产量提升,检查 班不超过3小时,每周有一
2
工作时间长,
量也增加;
天休息;
易疲劳
2.因前生产线中少部品项 2.需要前工序等相关部门
12
结果分析—不良说明 郁闷
期间:10月~
PD
44..实实施施结结果 果
A C 3.确认 测试结果:HANDLE有24人,
10月份标 签与实物 不良再发1
件
不合格有2人
KEY-SET有5人,
未达成
不合格为0
2010年HDL能力调查总结.xls
2010年受入检查与KEY-SET出货检查能力
11
对策实施—图表
郁闷 ing
10月份标 签与实物 不良再发1
10
对策实施
哇唔..改善 ,改善…
对应点:减少多个数不良流出
11..作作成成计计划划
措施:做不定期不良测试,提
2.实施2.实施 项目:1.标签与实物不符,
高检查员的警惕性,以防流出不良。
2.左右混入,3.少数
作成:HANDLE 李治平/ KEY-SET 谢江
4.异品混入
对象人员:所有出货检查员
10月份开始
检查方法说明:
1.待检区推部品,同时需要确认整车产品品番、纳期一致 2.推到检查区后确认检查用的资料与待检品,须一致 3.检查时按照《检查作业手顺书》检查,盖章(异常时联络班组长确认处理) 4.检查完成后再次确认整车产品品番、纳期一致 5.确认完成后推到检查完成品放置区
*检查方法没有问题,如按照检查基准实施可防止异常流出
1
选定主题—选择
异常原因分析和对策中必备项:
1.生产不良 制造原因只有在产品生产时发生及对策
2.流出不良 流出原因在制造过程和检查过程都会 产生。并如在出货检查时防止异常流出, 可达成客户要求的标签与实物不符不良 不良件数“0”目标
2
选定主题—定案
减少客户投诉中多数量不良,达成客户 PPM目标。 理由是: *客户每年都有相关联络,要求各供应商 减少标签与实物不符的异常。 *品管检查作业方法中可以对应。
件
10月份纳入不良个数明细
不良数 不良比率
500
112233445050505050500000000000
56.1% 386 43.3%
2 0.2%
1 0.1%
1 0.1%
60.0% 50.0% 40.0% 30.0% 20.0% 1 10.0% 0.1% 0.0%
标签与实物不符 外观不良 露底不良 寸法不良 组装不良 性能不良
作业台
人
培训不足 标准不了解
未按照作业标 准实施
线上配料异常
料
工作时间太 长,疲惫
人员工作时精 神不集中
个人原因
流
出
不
良
原
因
分
析
来料错误
来料错误时,受入检查 和工程中的生产前确认 可发现,需提前预防。
8
喔哦~
原因分析—分析结论说明
NO
不良项目
原因
对策
人
1.培训后向受训人确认培
为 因
训内容是否理解;
6
设定目标
来来来,一 起来改善!
出货检查流程及方法: 1.制造完成品检查
(全数检查)
☆本次对应改善的工程 为出货检查区域,检 查人员的警惕性提升, 标签与实物不符为0
挑中你 了~~
2.品管出货检查 (初期流动品和海外向的全 检,
其他的抽检)
3.制造出库后入生管仓库 (入库品不可再开箱和换标签)
4.按照日期出货
4
分析图中异常项目说明
不良项目依次为:
GA-1标签错误,GA-2产品混装, GC-1异品组装,GC-3组装位异常, GC-6连接不良, GC-8组装部位欠品, GD-1外观破损, GD-2外观变形, GD-3有瑕疵打痕, GD-4打磨或颜色不良,GD-5表面处理不良, GD-8外观缩水, GD-9其他外观异常, GE-1操作不良, GE-2性能不良, GE-4异音不良, GE-7回转不良, GF-1未加工, GF-2尺寸不良, GF-4形状异常, GF-9加工时其他不良, GZ-9其他不良项
3
分析现状—异常分析图
09年度纳入不良明细
不良个数 不良件数
1200
9
1000
10448
不良发生时个数较多
8
7
800
不
良
599
个 600
4
4
数
5 4
6 不
5
5良
4件 数
400 3
3
3
3
245 2
22 2 2
22 2
2
22
200
2 7 13 2 25 6 18
1 1 4 1 11 5 29 35 11 2
7
原因分析—鱼骨图分析 怎么办 呢?
另附资料说明
法
检查指示书在正式 使用前会做检查前 培训,如有疑问或 后续有疑问时也可 资料难懂 提出,视情况可追 加项目。
作业指示书说 明不足
作业区域无法调 整,到再增产或 有必要时,开两 班检查
作业区域小,人 员作业位置小
作业环境不够 亮,无法检出
每月进行灯管 确认,750露 克斯以上,可 对应
多,导致生产延迟,出货时
协助对应;
间不更改,紧急对应品增多 3 . 做不定期的不良测试
及
日常生活中都有心情 唯有提高检查员的警惕
对 策
3
个人原因,精 烦闷之时,所以无法 神不集中 避免会有开小差的事
性,并了解产品的重要性 后,认真对待检查品
*做不定期的不良测试,
情
提升检查员的警惕性
9
原因分析– 补充
9
102
1 12
1
0
0
GA-1标G签A-错2产误G品C-混1G异装C-品3组组装装G位CG-异C6-连常8组接装不部良G位D-欠1外品G观D-破2G外损DG-观D3-有变4打瑕形磨疵G或打D-颜痕5表色面不处良G理DG-不D8-外良9其观他缩外水G观E-异1操常G作E-不2性良G能E-不4异良G音E-不7回良转G不F-良1G未F-加2尺工GG寸FF--不94加形良工状时异G其常Z-他9其不他良不良项
5
现状分析—年度数据
不良个数最高为:
1.颜色异常1044个(多工序检查,品管抽检,无法全数管控) 2.标签错误599个(多工序检查,品管可管控) 3.产品混装245个(多工序检查,品管抽检,无法全数管控)
不良件数最高为:
1.颜色不良5件(多工序检查,品管抽检,无法全数管控) 2.寸法不良5件(成形组立工程检查,品管无法管控) 3.产品混装4件(多工序检查,品管抽检,无法全数管控) 4.连接不良4件(多工序检查,品管抽检,无法管控) 5.操作不良4件(多工序检查,品管抽检,无法管控)
1
培训不足
培训后不理解
2.正式作业前对受训人做 作业观察,并确认其检查
素
后的产品(班组长); 3.做不定期的不良测试
原
1.随着客户增产的趋势,生 1.控制加班时间,每天加
因 分 析
产线也随着产量提升,检查 班不超过3小时,每周有一
2
工作时间长,
量也增加;
天休息;
易疲劳
2.因前生产线中少部品项 2.需要前工序等相关部门
12
结果分析—不良说明 郁闷
期间:10月~
PD
44..实实施施结结果 果
A C 3.确认 测试结果:HANDLE有24人,
10月份标 签与实物 不良再发1
件
不合格有2人
KEY-SET有5人,
未达成
不合格为0
2010年HDL能力调查总结.xls
2010年受入检查与KEY-SET出货检查能力
11
对策实施—图表
郁闷 ing
10月份标 签与实物 不良再发1
10
对策实施
哇唔..改善 ,改善…
对应点:减少多个数不良流出
11..作作成成计计划划
措施:做不定期不良测试,提
2.实施2.实施 项目:1.标签与实物不符,
高检查员的警惕性,以防流出不良。
2.左右混入,3.少数
作成:HANDLE 李治平/ KEY-SET 谢江
4.异品混入
对象人员:所有出货检查员
10月份开始
检查方法说明:
1.待检区推部品,同时需要确认整车产品品番、纳期一致 2.推到检查区后确认检查用的资料与待检品,须一致 3.检查时按照《检查作业手顺书》检查,盖章(异常时联络班组长确认处理) 4.检查完成后再次确认整车产品品番、纳期一致 5.确认完成后推到检查完成品放置区
*检查方法没有问题,如按照检查基准实施可防止异常流出