钣金冲裁毛刺标准及检验方法
钣金件加工检验通用标准
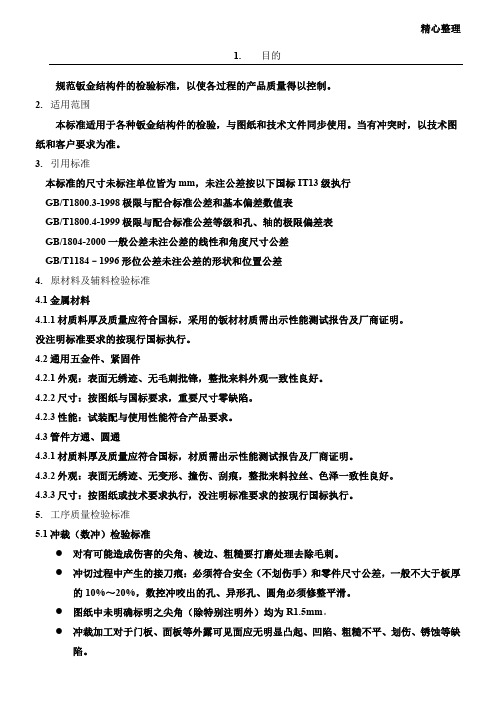
精心整理1.目的规范钣金结构件的检验标准,以使各过程的产品质量得以控制。
2.适用范围本标准适用于各种钣金结构件的检验,与图纸和技术文件同步使用。
当有冲突时,以技术图纸和客户要求为准。
3.引用标准本标准的尺寸未标注单位皆为mm,未注公差按以下国标IT13级执行4.4.14.1.14.24.2.14.2.24.2.34.34.3.14.3.24.3.35.工序质量检验标准5.1冲裁(数冲)检验标准●对有可能造成伤害的尖角、棱边、粗糙要打磨处理去除毛刺。
●冲切过程中产生的接刀痕:必须符合安全(不划伤手)和零件尺寸公差,一般不大于板厚的10%~20%,数控冲咬出的孔、异形孔、圆角必须修整平滑。
●图纸中未明确标明之尖角(除特别注明外)均为R1.5mm。
●冲裁加工对于门板、面板等外露可见面应无明显凸起、凹陷、粗糙不平、划伤、锈蚀等缺陷。
●毛刺:冲裁后毛刺高L≤5%t(t为板厚)。
●划伤、刀痕:以用手触摸不刮手为合格,应≤0.1mm。
●冲裁尺寸符合技术图纸要求,平面度公差要求见表一。
附表一、平面度公差要求5.25.2.1。
5.2.25.2.35.35.3.1【附表三:尺寸公差要求】5.3.2压铆件压铆螺母(柱)、压铆螺钉、涨铆螺母(柱)、拉铆螺母等,压上零部件后,螺纹不得变形(螺母或螺钉能自由进出,顺畅无卡滞现象),压铆件应与板面相平,不允许凸起或凹进(手感触摸应平滑),压铆件与板面垂直,压铆后压铆区无变形、猪嘴现象,拉包的高度、壁厚应均匀一致,顶部不应有毛刺。
5.3.3焊接焊缝应牢固、均匀,不得有虚焊、裂纹、未焊透、焊穿、豁口、咬边等缺陷。
焊缝长度、高度不均不允许超过长度、高度要求的10%。
8~12mm,两焊点之间的距离150±15mm,焊点位置要对称,上50mm65.45.4.15.4.25.4.3A5.4.4R≤2,5.55.5.1打磨后工件表面平面度要求为≤0.3mm/m,用手摸感觉有轻微内陷状,但不能过深,其凹坑深度不得大于0.20mm,不允许有比工件表面高的凸点,用手摸无触手感觉。
钣金检验标准
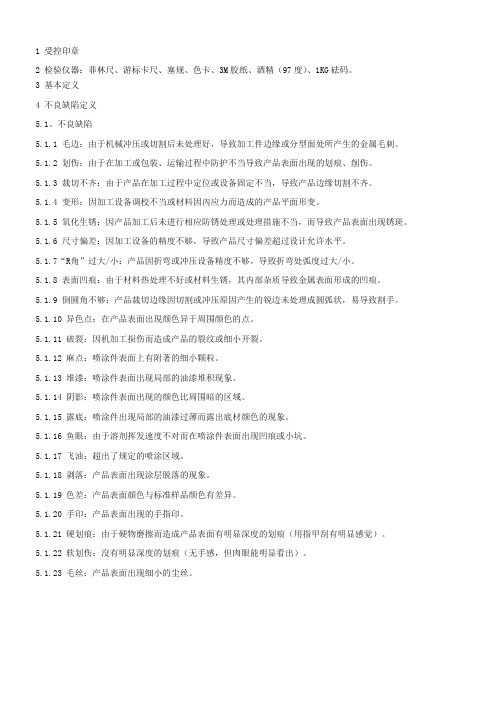
1 受控印章2 检验仪器:菲林尺、游标卡尺、塞规、色卡、3M胶纸、酒精(97度)、1KG砝码。
3 基本定义4 不良缺陷定义5.1、不良缺陷5.1.1 毛边:由于机械冲压或切割后未处理好,导致加工件边缘或分型面处所产生的金属毛刺。
5.1.2 划伤:由于在加工或包装、运输过程中防护不当导致产品表面出现的划痕、削伤。
5.1.3 裁切不齐:由于产品在加工过程中定位或设备固定不当,导致产品边缘切割不齐。
5.1.4 变形:因加工设备调校不当或材料因內应力而造成的产品平面形变。
5.1.5 氧化生锈:因产品加工后未进行相应防锈处理或处理措施不当,而导致产品表面出现锈斑。
5.1.6 尺寸偏差:因加工设备的精度不够,导致产品尺寸偏差超过设计允许水平。
5.1.7“R角”过大/小:产品因折弯或冲压设备精度不够,导致折弯处弧度过大/小。
5.1.8 表面凹痕:由于材料热处理不好或材料生锈,其内部杂质导致金属表面形成的凹痕。
5.1.9 倒圆角不够:产品裁切边缘因切割或冲压原因产生的锐边未处理成圆弧状,易导致割手。
5.1.10 异色点:在产品表面出現颜色异于周围颜色的点。
5.1.11 破裂:因机加工损伤而造成产品的裂纹或细小开裂。
5.1.12 麻点:喷涂件表面上有附著的细小颗粒。
5.1.13 堆漆:喷涂件表面出现局部的油漆堆积现象。
5.1.14 阴影:喷涂件表面出现的颜色比周围暗的区域。
5.1.15 露底:喷涂件出现局部的油漆过薄而露出底材颜色的现象。
5.1.16 鱼眼:由于溶剂挥发速度不对而在喷涂件表面出现凹痕或小坑。
5.1.17 飞油:超出了规定的喷涂区域。
5.1.18 剥落:产品表面出现涂层脱落的现象。
5.1.19 色差:产品表面顏色与标准样品颜色有差异。
5.1.20 手印:产品表面出现的手指印。
5.1.21 硬划痕:由于硬物磨擦而造成产品表面有明显深度的划痕(用指甲刮有明显感觉)。
5.1.22 软划伤:沒有明显深度的划痕(无手感,但肉眼能明显看出)。
钣金加工质量检验标准
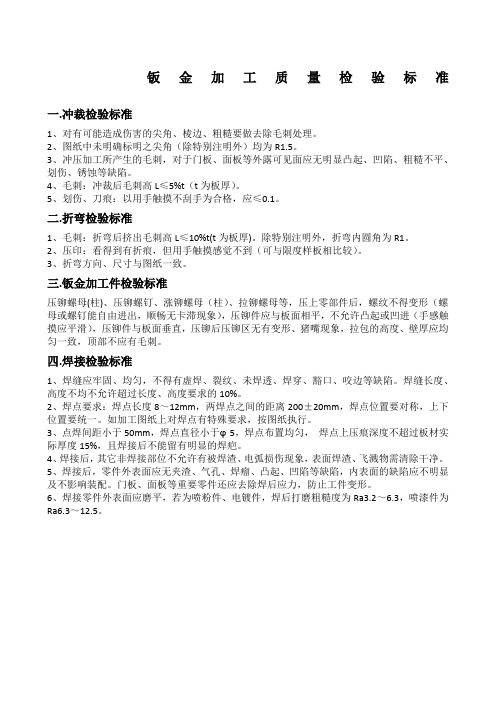
钣金加工质量检验标准一.冲裁检验标准1、对有可能造成伤害的尖角、棱边、粗糙要做去除毛刺处理。
2、图纸中未明确标明之尖角(除特别注明外)均为R1.5。
3、冲压加工所产生的毛刺,对于门板、面板等外露可见面应无明显凸起、凹陷、粗糙不平、划伤、锈蚀等缺陷。
4、毛刺:冲裁后毛刺高L≤5%t(t为板厚)。
5、划伤、刀痕:以用手触摸不刮手为合格,应≤0.1。
二.折弯检验标准1、毛刺:折弯后挤出毛刺高L≤10%t(t为板厚)。
除特别注明外,折弯内圆角为R1。
2、压印:看得到有折痕,但用手触摸感觉不到(可与限度样板相比较)。
3、折弯方向、尺寸与图纸一致。
三.钣金加工件检验标准压铆螺母(柱)、压铆螺钉、涨铆螺母(柱)、拉铆螺母等,压上零部件后,螺纹不得变形(螺母或螺钉能自由进出,顺畅无卡滞现象),压铆件应与板面相平,不允许凸起或凹进(手感触摸应平滑),压铆件与板面垂直,压铆后压铆区无有变形、猪嘴现象,拉包的高度、壁厚应均匀一致,顶部不应有毛刺。
四.焊接检验标准1、焊缝应牢固、均匀,不得有虚焊、裂纹、未焊透、焊穿、豁口、咬边等缺陷。
焊缝长度、高度不均不允许超过长度、高度要求的10%。
2、焊点要求:焊点长度8~12mm,两焊点之间的距离200±20mm,焊点位置要对称,上下位置要统一。
如加工图纸上对焊点有特殊要求,按图纸执行。
3、点焊间距小于50mm,焊点直径小于φ5,焊点布置均匀,焊点上压痕深度不超过板材实际厚度15%,且焊接后不能留有明显的焊疤。
4、焊接后,其它非焊接部位不允许有被焊渣、电弧损伤现象,表面焊渣、飞溅物需清除干净。
5、焊接后,零件外表面应无夹渣、气孔、焊瘤、凸起、凹陷等缺陷,内表面的缺陷应不明显及不影响装配。
门板、面板等重要零件还应去除焊后应力,防止工件变形。
6、焊接零件外表面应磨平,若为喷粉件、电镀件,焊后打磨粗糙度为Ra3.2~6.3,喷漆件为Ra6.3~12.5。
钣金件加工检验通用标准
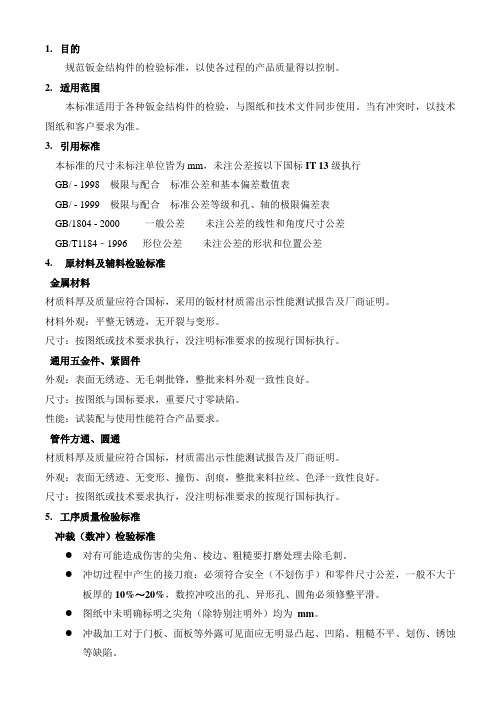
1.目的规范钣金结构件的检验标准,以使各过程的产品质量得以控制。
2.适用范围本标准适用于各种钣金结构件的检验,与图纸和技术文件同步使用。
当有冲突时,以技术图纸和客户要求为准。
3.引用标准本标准的尺寸未标注单位皆为mm,未注公差按以下国标IT 13级执行GB/ - 1998 极限与配合标准公差和基本偏差数值表GB/ - 1999 极限与配合标准公差等级和孔、轴的极限偏差表GB/1804 - 2000 一般公差未注公差的线性和角度尺寸公差GB/T1184–1996 形位公差未注公差的形状和位置公差4.原材料及辅料检验标准金属材料材质料厚及质量应符合国标,采用的钣材材质需出示性能测试报告及厂商证明。
材料外观:平整无锈迹,无开裂与变形。
尺寸:按图纸或技术要求执行,没注明标准要求的按现行国标执行。
通用五金件、紧固件外观:表面无绣迹、无毛刺批锋,整批来料外观一致性良好。
尺寸:按图纸与国标要求,重要尺寸零缺陷。
性能:试装配与使用性能符合产品要求。
管件方通、圆通材质料厚及质量应符合国标,材质需出示性能测试报告及厂商证明。
外观:表面无绣迹、无变形、撞伤、刮痕,整批来料拉丝、色泽一致性良好。
尺寸:按图纸或技术要求执行,没注明标准要求的按现行国标执行。
5.工序质量检验标准冲裁(数冲)检验标准●对有可能造成伤害的尖角、棱边、粗糙要打磨处理去除毛刺。
●冲切过程中产生的接刀痕:必须符合安全(不划伤手)和零件尺寸公差,一般不大于板厚的10%~20%,数控冲咬出的孔、异形孔、圆角必须修整平滑。
●图纸中未明确标明之尖角(除特别注明外)均为mm。
●冲裁加工对于门板、面板等外露可见面应无明显凸起、凹陷、粗糙不平、划伤、锈蚀等缺陷。
●毛刺:冲裁后毛刺高L ≤5% t(t为板厚)。
●划伤、刀痕:以用手触摸不刮手为合格,应≤mm。
●冲裁尺寸符合技术图纸要求,平面度公差要求见表一。
附表一、平面度公差要求5.2折弯检验标准毛刺:折弯后挤出毛刺高L≤10% t (t为板厚)。
钣金冲压件毛刺高度标准及检验方法
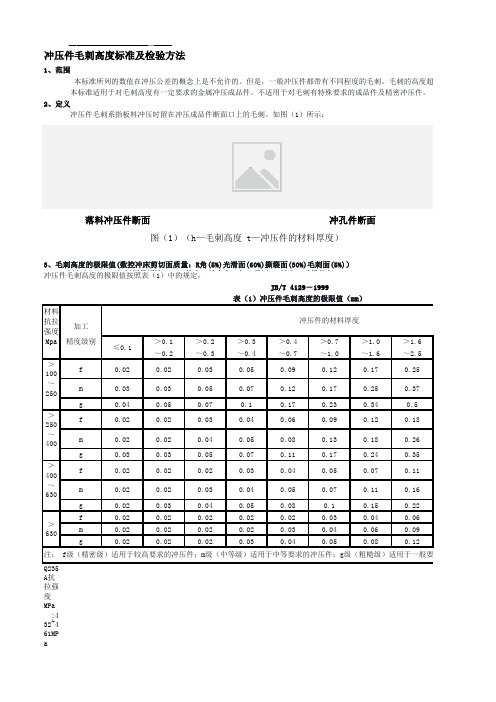
材料抗拉强度加工Mpa 精度级别>0.1>0.2>0.3>0.4>0.7>1.0>1.6~0.2~0.3~0.4~0.7~1.0~1.6~2.5>100f 0.020.020.030.050.090.120.170.25~250m 0.030.030.050.070.120.170.250.37g 0.040.050.070.10.170.230.340.5>250f 0.020.020.030.040.060.090.120.18~400m 0.020.020.040.050.080.130.180.26g 0.030.030.050.070.110.170.240.35>400f 0.020.020.020.030.040.050.070.11~630m 0.020.020.030.040.050.070.110.16g0.020.030.040.050.080.10.150.22f 0.020.020.020.020.020.030.040.06m 0.020.020.020.020.030.040.060.09g0.020.020.020.030.040.050.080.12Q235A抗拉强度MPa :432~461MP a本标准适用于对毛刺高度有一定要求的金属冲压成品件。
不适用于对毛刺有特殊要求的成品件及精密冲压件。
2、定义冲压件毛刺高度标准及检验方法1、范围本标准所列的数值在冲压公差的概念上是不允许的。
但是,一般冲压件都带有不同程度的毛刺。
毛刺的高度超过用性能。
冲压件毛刺系指板料冲压时留在冲压成品件断面口上的毛刺。
如图(1)所示:落料冲压件断面冲孔件断面图(1)(h—毛刺高度 t—冲压件的材料厚度)3、毛刺高度的极限值(数控冲床剪切面质量:R角(5%)光滑面(60%)撕裂面(30%)毛刺面(5%))(30%)毛刺面(5%),可切板厚最厚达4MM.。
特点:精度高,加工灵活.。
缺点:受模具限冲压件毛刺高度的极限值按照表(1)中的规定。
钣金件加工检验通用标准
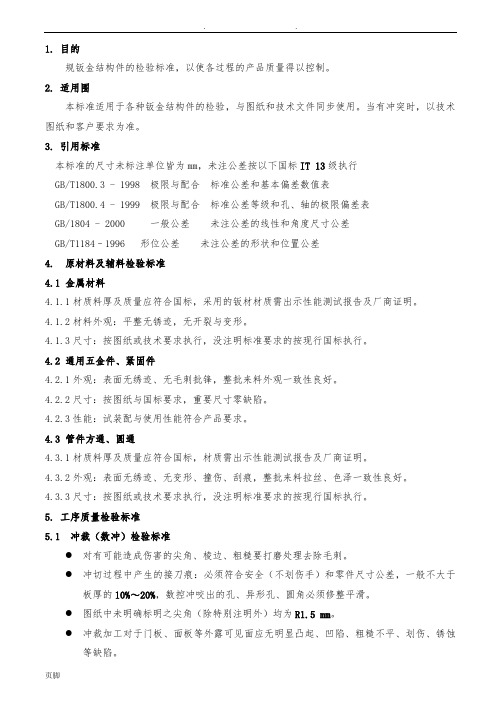
1.目的规钣金结构件的检验标准,以使各过程的产品质量得以控制。
2.适用围本标准适用于各种钣金结构件的检验,与图纸和技术文件同步使用。
当有冲突时,以技术图纸和客户要求为准。
3.引用标准本标准的尺寸未标注单位皆为mm,未注公差按以下国标IT 13级执行GB/T1800.3 - 1998 极限与配合标准公差和基本偏差数值表GB/T1800.4 - 1999 极限与配合标准公差等级和孔、轴的极限偏差表GB/1804 - 2000 一般公差未注公差的线性和角度尺寸公差GB/T1184–1996 形位公差未注公差的形状和位置公差4.原材料及辅料检验标准4.1 金属材料4.1.1材质料厚及质量应符合国标,采用的钣材材质需出示性能测试报告及厂商证明。
4.1.2材料外观:平整无锈迹,无开裂与变形。
4.1.3尺寸:按图纸或技术要求执行,没注明标准要求的按现行国标执行。
4.2 通用五金件、紧固件4.2.1外观:表面无绣迹、无毛刺批锋,整批来料外观一致性良好。
4.2.2尺寸:按图纸与国标要求,重要尺寸零缺陷。
4.2.3性能:试装配与使用性能符合产品要求。
4.3 管件方通、圆通4.3.1材质料厚及质量应符合国标,材质需出示性能测试报告及厂商证明。
4.3.2外观:表面无绣迹、无变形、撞伤、刮痕,整批来料拉丝、色泽一致性良好。
4.3.3尺寸:按图纸或技术要求执行,没注明标准要求的按现行国标执行。
5.工序质量检验标准5.1 冲裁(数冲)检验标准●对有可能造成伤害的尖角、棱边、粗糙要打磨处理去除毛刺。
●冲切过程中产生的接刀痕:必须符合安全(不划伤手)和零件尺寸公差,一般不大于板厚的10%~20%,数控冲咬出的孔、异形孔、圆角必须修整平滑。
●图纸中未明确标明之尖角(除特别注明外)均为R1.5 mm。
●冲裁加工对于门板、面板等外露可见面应无明显凸起、凹陷、粗糙不平、划伤、锈蚀等缺陷。
●毛刺:冲裁后毛刺高L ≤ 5% t(t为板厚)。
钣金件加工检验通用标准
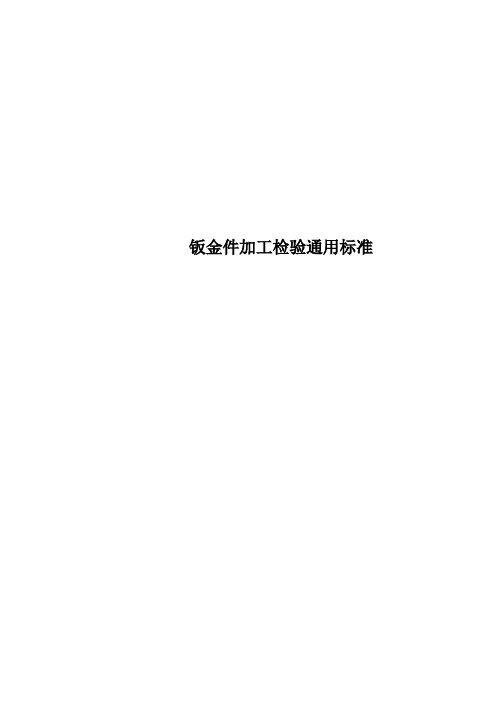
钣金件加工检验通用标准1.目的规范钣金结构件的检验标准,以使各过程的产品质量得以控制。
2.适用范围本标准适用于各种钣金结构件的检验,与图纸和技术文件同步使用。
当有冲突时,以技术图纸和客户要求为准。
3.引用标准本标准的尺寸未标注单位皆为mm,未注公差按以下国标IT 13级执行GB/T1800.3 - 1998 极限与配合标准公差和基本偏差数值表GB/T1800.4 - 1999 极限与配合标准公差等级和孔、轴的极限偏差表GB/1804 - 2000 一般公差未注公差的线性和角度尺寸公差GB/T1184–1996 形位公差未注公差的形状和位置公差4.原材料及辅料检验标准4.1 金属材料4.2 通用五金件、紧固件4.3 管件方通、圆通5.工序质量检验标准5.1 冲裁(数冲)检验标准●对有可能造成伤害的尖角、棱边、粗糙要打磨处理去除毛刺。
●冲切过程中产生的接刀痕:必须符合安全(不划伤手)和零件尺寸公差,一般不大于板厚的10%~20%,数控冲咬出的孔、异形孔、圆角必须修整平滑。
●图纸中未明确标明之尖角(除特别注明外)均为R1.5 mm。
●冲裁加工对于门板、面板等外露可见面应无明显凸起、凹陷、粗糙不平、划伤、锈蚀等缺陷。
●毛刺:冲裁后毛刺高L ≤5% t(t为板厚)。
●划伤、刀痕:以用手触摸不刮手为合格,应≤0.1 mm。
●冲裁尺寸符合技术图纸要求,平面度公差要求见表一。
附表一、平面度公差要求5.2折弯检验标准毛刺:折弯后挤出毛刺高L≤10% t (t为板厚)。
除特别注明外,折弯内圆角为R1.0 mm 。
接刀痕深度控制在0.30 mm 以内。
【附表二:对角线公差要求】5.3 钣金加工件检验标准尺寸按图纸要求检验,尺寸公差见表三。
【附表三:尺寸公差要求】压铆螺母(柱)、压铆螺钉、涨铆螺母(柱)、拉铆螺母等,压上零部件后,螺纹不得变形(螺母或螺钉能自由进出,顺畅无卡滞现象),压铆件应与板面相平,不允许凸起或凹进(手感触摸应平滑),压铆件与板面垂直,压铆后压铆区无变形、猪嘴现象,拉包的高度、壁厚应均匀一致,顶部不应有毛刺。
钣金件加工检验通用标准

1.目的标准钣金结构件的检验标准,以使各过程的产品质量得以控制。
2.适用范围本标准适用于各种钣金结构件的检验,与图纸和技术文件同步使用。
当有冲突时,以技术图纸和客户要求为准。
3.引用标准本标准的尺寸未标注单位皆为mm,未注公差按以下国标IT 13级执行- 1998 极限与配合标准公差和基本偏差数值表GB/T1800.4 - 1999 极限与配合标准公差等级和孔、轴的极限偏差表GB/1804 - 2000 一般公差未注公差的线性和角度尺寸公差GB/T1184–1996 形位公差未注公差的形状和位置公差4.原材料及辅料检验标准金属材料材质料厚及质量应符合国标,采用的钣材材质需出示性能测试报告及厂商证明。
4.1.2材料外观:平整无锈迹,无开裂与变形。
4.1.3尺寸:按图纸或技术要求执行,没注明标准要求的按现行国标执行。
4.2 通用五金件、紧固件4.2.1外观:外表无绣迹、无毛刺批锋,整批来料外观一致性良好。
4.2.2尺寸:按图纸与国标要求,重要尺寸零缺陷。
4.2.3性能:试装配与使用性能符合产品要求。
4.3 管件方通、圆通4.3.1材质料厚及质量应符合国标,材质需出示性能测试报告及厂商证明。
4.3.2外观:外表无绣迹、无变形、撞伤、刮痕,整批来料拉丝、色泽一致性良好。
4.3.3尺寸:按图纸或技术要求执行,没注明标准要求的按现行国标执行。
5.工序质量检验标准冲裁〔数冲〕检验标准●对有可能造成伤害的尖角、棱边、粗糙要打磨处理去除毛刺。
●冲切过程中产生的接刀痕:必须符合安全〔不划伤手〕和零件尺寸公差,一般不大于板厚的10%~20%,数控冲咬出的孔、异形孔、圆角必须修整平滑。
●图纸中未明确标明之尖角〔除特别注明外〕均为mm。
●冲裁加工对于门板、面板等外露可见面应无明显凸起、凹陷、粗糙不平、划伤、锈蚀等缺陷。
●毛刺:冲裁后毛刺高L ≤5% t〔t为板厚〕。
●划伤、刀痕:以用手触摸不刮手为合格,应≤mm。
●冲裁尺寸符合技术图纸要求,平面度公差要求见表一。
钣金件加工检验通用标准
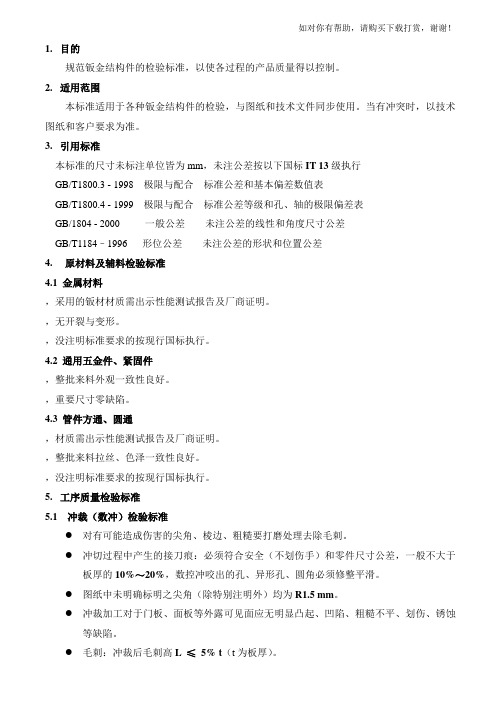
1.目的规范钣金结构件的检验标准,以使各过程的产品质量得以控制。
2.适用范围本标准适用于各种钣金结构件的检验,与图纸和技术文件同步使用。
当有冲突时,以技术图纸和客户要求为准。
3.引用标准本标准的尺寸未标注单位皆为mm,未注公差按以下国标IT 13级执行GB/T1800.3 - 1998 极限与配合标准公差和基本偏差数值表GB/T1800.4 - 1999 极限与配合标准公差等级和孔、轴的极限偏差表GB/1804 - 2000 一般公差未注公差的线性和角度尺寸公差GB/T1184–1996 形位公差未注公差的形状和位置公差4.原材料及辅料检验标准4.1 金属材料,采用的钣材材质需出示性能测试报告及厂商证明。
,无开裂与变形。
,没注明标准要求的按现行国标执行。
4.2 通用五金件、紧固件,整批来料外观一致性良好。
,重要尺寸零缺陷。
4.3 管件方通、圆通,材质需出示性能测试报告及厂商证明。
,整批来料拉丝、色泽一致性良好。
,没注明标准要求的按现行国标执行。
5.工序质量检验标准5.1 冲裁(数冲)检验标准●对有可能造成伤害的尖角、棱边、粗糙要打磨处理去除毛刺。
●冲切过程中产生的接刀痕:必须符合安全(不划伤手)和零件尺寸公差,一般不大于板厚的10%~20%,数控冲咬出的孔、异形孔、圆角必须修整平滑。
●图纸中未明确标明之尖角(除特别注明外)均为R1.5 mm。
●冲裁加工对于门板、面板等外露可见面应无明显凸起、凹陷、粗糙不平、划伤、锈蚀等缺陷。
●毛刺:冲裁后毛刺高L ≤5% t(t为板厚)。
●划伤、刀痕:以用手触摸不刮手为合格,应≤0.1 mm。
●冲裁尺寸符合技术图纸要求,平面度公差要求见表一。
附表一、平面度公差要求5.2折弯检验标准5.2.1 毛刺:折弯后挤出毛刺高L≤10% t (t为板厚)。
除特别注明外,折弯内圆角为R1.0 mm。
5.2.2 压印:看得到有折痕,但用手触摸感觉不到(可与限度样板相比较),折弯过程产生产的接刀痕深度控制在0.30 mm以内。
钣金表面处理通用检验标准

检验标准名称:表面处理通用检验标准图号:. 003拟制:***审核:***标准化:***IQC会签:***批准:***目次表面处理通用检验标准○、总则零部件表面处理前应去除毛刺、飞边、划痕、氧化层等缺陷,锐边棱角倒钝。
表面应作相应的除油、除锈、磷化、烘干等处理。
喷漆件全部做底漆(防锈漆)。
涂覆层正面(指机柜、机箱、前门板等正面)在运转装配过程原则上不允许有损伤。
其它部位在运转装配过程中引起的损伤,允许补漆。
外观缺陷允许的具体程度参照产品表面外观缺陷的限定标准()执行。
来料检验的抽样方法和程序按IQC部门的相关规范执行。
一、电镀镍检验标准试样要求挂镀工艺材料:20 冷轧钢尺寸:80×125×1 ~4 (mm)表面粗糙度:Ra ≤1 ?m表面处理:镀铜+光亮镍。
滚镀工艺材料:20 冷轧钢尺寸:依工艺设备特点选择适当形状和大小的试样,要求其至少有一平面面积大于30 ×30 (mm)表面粗糙度:Ra ≤1 ?m表面处理:镀铜+光亮镍。
外观所有零件都应按GB 5926-86 进行外观检查。
镍镀层应是光亮或带有柔和浅黄色的银白色。
镀层结晶应均匀、细致、光滑、连续。
在零件的非主视表面,允许有以下缺陷:1)小而少的夹具印(夹具印小于1×1 mm2);2)镀层局部呈雾状(雾状面积小于10×10 mm2)。
不允许:1)镀层有斑点、黑点、烧焦、粗糙、针孔、麻点、分层、起泡、起皮、脱落:2)树枝状、海绵状和条纹状镀层;3)局部无镀层(盲孔内、以及深度大于直径的孔内部分除外);4)以及节中未包含的其它缺陷。
镀层厚度按GB 5930-86 进行检测。
厚度检查在零件上进行;每批零件供应方都需检测。
对钢铁零件表面:凡能被直径为20 mm的球接触到的区域,其局部总厚度必须达到30 μm 以上,其中铜镀层为20-25μm,镍镀层为10-15μm ;盲孔内、以及深度大于直径或开口宽度的部分不规定厚度。
冲压件毛刺高度标准及检验方法

1、范围本标准所列的数值在冲压公差的概念上是不允许的。
但是,一般冲压件都带有不同程度的毛刺。
毛刺的高度超过一定限度,将影响产品的质量和使用性能。
本标准适用于对毛刺高度有一定要求的金属冲压成品件。
不适用于对毛刺有特殊要求的成品件及精密冲压件。
2、定义冲压件毛刺系指板料冲压时留在冲压成品件断面口上的毛刺。
如图(1)所示:落料冲压件断面冲孔件断面图(1)(h—毛刺高度 t—冲压件的材料厚度)3、毛刺高度的极限值冲压件毛刺高度的极限值按照表(1)中的规定。
JB/T 4129-1999表(1)冲压件毛刺高度的极限值(mm)材料抗拉强度MPa 加工精度级别冲压件的材料厚度≤0.1>0.1~0.2>0.2~0.3>0.3~0.4>0.4~0.7>0.7~1.0>1.0~1.6>1.6~2.5>2.5~4.0>4.0~6.5>6.5~10.0>100 ~250 f 0.02 0.02 0.03 0.05 0.09 0.12 0.17 0.25 0.36 0.60 0.95 m 0.03 0.03 0.05 0.07 0.12 0.17 0.25 0.37 0.54 0.90 1.42 g 0.04 0.05 0.07 0.10 0.17 0.23 0.34 0.50 0.72 1.20 1.90>250 ~400 f 0.02 0.02 0.03 0.04 0.06 0.09 0.12 0.18 0.25 0.36 0.50 m 0.02 0.02 0.04 0.05 0.08 0.13 0.18 0.26 0.37 0.54 0.75 g 0.03 0.03 0.05 0.07 0.11 0.17 0.24 0.35 0.50 0.73 1.00>400 ~630 f 0.02 0.02 0.02 0.03 0.04 0.05 0.07 0.11 0.20 0.22 0.32 m 0.02 0.02 0.03 0.04 0.05 0.07 0.11 0.16 0.30 0.33 0.48 g 0.02 0.03 0.04 0.05 0.08 0.10 0.15 0.22 0.40 0.45 0.65>630 f 0.02 0.02 0.02 0.02 0.02 0.03 0.04 0.06 0.09 0.13 0.17 m 0.02 0.02 0.02 0.02 0.03 0.04 0.06 0.09 0.13 0.19 0.26 g 0.02 0.02 0.02 0.03 0.04 0.05 0.08 0.12 0.18 0.26 0.354、检测检测环境:常温常压。
钣金检验规程
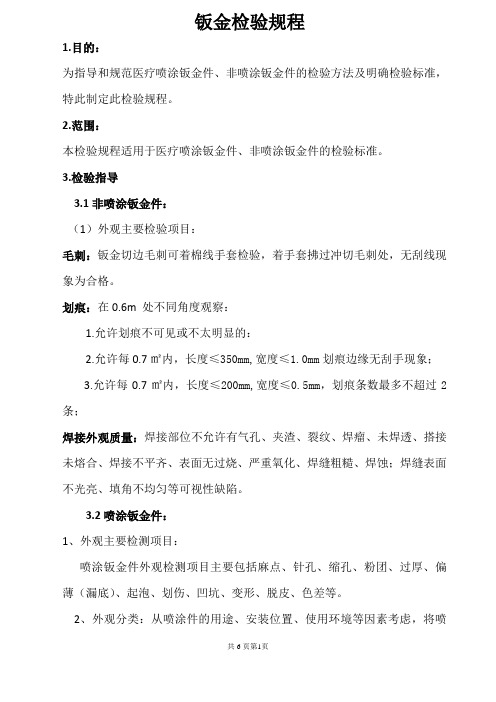
钣金检验规程1.目的:为指导和规范医疗喷涂钣金件、非喷涂钣金件的检验方法及明确检验标准,特此制定此检验规程。
2.范围:本检验规程适用于医疗喷涂钣金件、非喷涂钣金件的检验标准。
3.检验指导3.1非喷涂钣金件:(1)外观主要检验项目:毛刺:钣金切边毛刺可着棉线手套检验,着手套拂过冲切毛刺处,无刮线现象为合格。
划痕:在0.6m 处不同角度观察:1.允许划痕不可见或不太明显的:2.允许每0.7㎡内,长度≤350mm,宽度≤1.0mm划痕边缘无刮手现象;3.允许每0.7㎡内,长度≤200mm,宽度≤0.5mm,划痕条数最多不超过2条;焊接外观质量:焊接部位不允许有气孔、夹渣、裂纹、焊瘤、未焊透、搭接未熔合、焊接不平齐、表面无过烧、严重氧化、焊缝粗糙、焊蚀;焊缝表面不光亮、填角不均匀等可视性缺陷。
3.2喷涂钣金件:1、外观主要检测项目:喷涂钣金件外观检测项目主要包括麻点、针孔、缩孔、粉团、过厚、偏薄(漏底)、起泡、划伤、凹坑、变形、脱皮、色差等。
2、外观分类:从喷涂件的用途、安装位置、使用环境等因素考虑,将喷涂件的外观面按其对产品外观的影响程度及重要性,依次分为A类外观面、B类外观面、C类外观面、D类外观面。
A类:指成套钣金件的外表面、装配在整机上之后从产品外观角度可直接观察到的表面;如前、后门板、两侧门板等可视外观面。
B类:指成套钣金件、内部钣金件装配后的可视表面;C类:指成套钣金件、内部钣金件装配后的不可视表面;D类:指所有钣金件的外表面,如底支撑、顶支撑等。
3、各类外观缺陷的定义和特征:麻点:涂膜表面产品凸起,呈颗粒状(或近似圆形)分布在整个或局部表面上,缺陷最大尺寸在1.0mm以上称为“疙瘩”;缺陷最大尺寸不大与1.0mm 的称为“痱子”。
“疙瘩”与“痱子”统称“麻点”。
针孔:涂膜表面产生凹陷,呈圆形(或近似圆形)分布在整个或局部表面上,缺陷最大尺寸在1.0mm以上称为“凹洼”,缺陷最大尺寸不大于1.0mm的称为“缩孔”。
钣金验收标准

钣金验收标准1、目的金属冷加工件检查项目及为检验员提供检验规则和检验方法。
2、应用范围2 1适用于数控机床(NCT)下料、折弯、钳加工、冲压成型、及切削加工工件的检验。
2.2有特别要求的部件以该部件之检查指示书或客户标准为依据检查。
3、定义3.1毛刺:金属冲压时由于模具异常在断裂面留下的非正常毛边,或钳加工中在孔或螺纹孔反边留下的毛边及激光切割反面的毛边。
3.2披锋:金属冲压时,在沿断裂面边缘形成的凸起状尖角:3.3接点:零件同一边线在数控机床冲裁过程中因刀具在不同时段冲裁而留下的接刀痕迹;3.4连料点:在机床冲裁过程中防止冲压零件与板材脱离,在板材与零件或零件与零件的适当位置留下的连接点。
3.5划伤:用小指肚接触有凹入感觉并挂指甲,镀锌板目视有划破镀锌层的缺陷:3.6划花:用小指肚接触无感觉,且不挂指甲,但目视有痕迹;3.7擦伤:目视有痕迹,但不露基层,称为擦伤:3.8压印:产品表面受外力影响形成的凹坑,称为压痕(模印折弯痕除外); 3.9折弯痕:金属表面在折弯过程中因与折弯下模V槽边缘接触挤压留下的痕迹:3.10 A级面:客户(最终使用该整机产品的客户)能直接正视的外部表面和组装品开启后,能直接正视的内表面以及全部丝印面;3.11 B级面:非重要的外部表面或内部结构件(散件交货)的产品表面: 3.12 C级面:不易察看的内部表面和无外观要求的散件表面;4、检验项目及验收标准4.1尺寸规格:符合图纸要求。
4.1.1切削加、钳加工工件未注公差按;备注:1、折弯如未指明尺寸或尾部无法控制时,则只测量产品根部尺寸,尾部按角度控制尺寸公差;2、倒角按孔公差:3、工艺孔或工艺槽不做检查要求:4.2平面度:图样无明确要求的按产品平面最长尺寸的2/1000计算检查。
4.3成形角度:图样无明确要求的按士1°控制检查。
4.4压铆件质量控制标准4.4.1尾部高度:图样无明确要求的可凹入0.1mm或突出0.05mm以下;4.4.2垂直度:對于螺柱和銷釘類五金件必須保証其垂直度在士O.5度之内;4.4.3扭力:(铆接孔直径x2.5)kgf4.4.4压力:2.5kgf以上;4 .4.5铆接后本体和铆钉都不准有裂纹。
钣金质量检验标准

钣金质量检验标准
1、主视面:板面平整、过渡圆滑、接缝严密,无裂纹、飞边、毛刺、锈蚀、错位、变形、锤痕、磕碰、划伤、凸凹不平及非工艺性孔洞等缺陷。
如有轻微外观缺陷需打磨平整并作抛光处理。
非主视面:板面较平整、过渡较圆滑,无严重磕碰划伤,允许有轻微凸凹不平及错位,不允许有裂纹及非工艺性孔洞等缺陷。
2、顶盖、立柱、前后风挡、下围等关键部位搭接处必须采用满焊,要求焊接牢固、焊缝平直,无虚焊、漏焊、焊瘤、夹渣、飞溅、烧穿等缺陷,焊后打磨平整并作抛光处理;车身地板、前围、后围、侧围及顶盖等部位连接处采用断续焊,焊缝长度15-20mm,焊缝分布均匀,间距60-80mm,搭接周圈要求切实,搭接处间隙≤2mm;加强梁及加固板等重要位置采用断续焊,焊缝长度20-30mm,焊缝分布均匀,间距30-40mm 焊接螺母:焊接牢固可靠,焊后攻丝处理。
2
3、车门:铰链安装牢固、转动灵活,车门启闭可靠,无干涉、卡滞及异响现象,车门闭合后周边间隙均匀,车门密封间隙15±2mm。
4、前风窗:弧度与封样玻璃吻合良好,周边间隙均匀一致(5~6mm),风窗对角线偏差≤3mm。
5、轮罩:以轮轴中心线为基准,前后偏差不超过5mm,上下偏差不超过5mm,内外偏差不超过5mm。
6、灯框、门框、门洞周圈、前围周圈等能够影响外观质量的部位要打磨圆滑,不能影响刮腻子及后道工序的施工。
其他:风道宽度误差≤5mm,车身左右偏移≤7mm,左右高度偏差≤7mm。
7、车身无漏焊、漏件,材料厚度及其他装配尺寸严格按图纸要求执行
2。
钣金表面处理通用检验标准

钣金表面处理通用检验标准Company Document number:WTUT-WT88Y-W8BBGB-BWYTT-19998检验标准名称:表面处理通用检验标准图号:. 003拟制:***审核:***标准化:***IQC会签:***批准:***目次表面处理通用检验标准○、总则零部件表面处理前应去除毛刺、飞边、划痕、氧化层等缺陷,锐边棱角倒钝。
表面应作相应的除油、除锈、磷化、烘干等处理。
喷漆件全部做底漆(防锈漆)。
涂覆层正面(指机柜、机箱、前门板等正面)在运转装配过程原则上不允许有损伤。
其它部位在运转装配过程中引起的损伤,允许补漆。
外观缺陷允许的具体程度参照执行。
来料检验的抽样方法和程序按IQC部门的相关规范执行。
一、电镀镍检验标准试样要求挂镀工艺材料: 20 冷轧钢尺寸: 80×125×1 ~ 4 (mm)表面粗糙度: Ra ≤ 1 m表面处理:镀铜+光亮镍。
滚镀工艺材料: 20 冷轧钢尺寸:依工艺设备特点选择适当形状和大小的试样,要求其至少有一平面面积大于 30 ×30 (mm)表面粗糙度: Ra ≤ 1 m表面处理:镀铜+光亮镍。
外观所有零件都应按 GB 5926-86 进行外观检查。
镍镀层应是光亮或带有柔和浅黄色的银白色。
镀层结晶应均匀、细致、光滑、连续。
在零件的非主视表面,允许有以下缺陷:1)小而少的夹具印(夹具印小于 1×1 mm2);2)镀层局部呈雾状(雾状面积小于10×10 mm2)。
不允许:1)镀层有斑点、黑点、烧焦、粗糙、针孔、麻点、分层、起泡、起皮、脱落:2)树枝状、海绵状和条纹状镀层;3)局部无镀层(盲孔内、以及深度大于直径的孔内部分除外);4)以及节中未包含的其它缺陷。
镀层厚度按 GB 5930-86 进行检测。
厚度检查在零件上进行;每批零件供应方都需检测。
对钢铁零件表面:凡能被直径为 20 mm的球接触到的区域,其局部总厚度必须达到 30 μm 以上,其中铜镀层为 20-25μm,镍镀层为 10-15μm ;盲孔内、以及深度大于直径或开口宽度的部分不规定厚度。
钣金冲裁毛刺标准及检验方法

材料抗拉强度加工Mpa 精度级别>0.1>0.2>0.3>0.4>0.7>1.0>1.6~0.2~0.3~0.4~0.7~1.0~1.6~2.5>100f 0.020.020.030.050.090.120.170.25~250m 0.030.030.050.070.120.170.250.37g 0.040.050.070.10.170.230.340.5>250f 0.020.020.030.040.060.090.120.18~400m 0.020.020.040.050.080.130.180.26g 0.030.030.050.070.110.170.240.35>400f 0.020.020.020.030.040.050.070.11~630m 0.020.020.030.040.050.070.110.16g0.020.030.040.050.080.10.150.22f 0.020.020.020.020.020.030.040.06m 0.020.020.020.020.030.040.060.09g0.020.020.020.030.040.050.080.12Q235A抗拉强度MPa :432~461MPa检测环常温常压。
检测方行轮廓投影测量。
如果精度要求不是很高,可以用千分尺、高度尺等机械长度测量工具进行测量。
本标准适用于对毛刺高度有一定要求的金属冲压成品件。
不适用于对毛刺有特殊要求的成品件及精密冲压件。
2、定义冲压件毛刺高度标准及检验方法1、范围本标准所列的数值在冲压公差的概念上是不允许的。
但是,一般冲压件都带有不同程度的毛刺。
毛刺的高度超过一定性能。
冲压件毛刺系指板料冲压时留在冲压成品件断面口上的毛刺。
如图(1)所示:落料冲压件断面 冲孔件断面图(1)(h—毛刺高度 t—冲压件的材料厚度)3、毛刺高度的极限值(数控冲床剪切面质量:R角(5%)光滑面(60%)撕裂面(30%)毛刺面(5%))(30%)毛刺面(5%),可切板厚最厚达4MM.。
冲压件毛刺高度标准及检验方法

冲压件毛刺高度标准及检验方法仪器培训中心: 时间:2009-5-21 10:35:00 浏览:2237 次【评论】【报错】1、范围本标准所列的数值在冲压公差的概念上是不允许的。
但是,一般冲压件都带有不同程度的毛刺。
毛刺的高度超过一定限度,将影响产品的质量和使用性能。
本标准适用于对毛刺高度有一定要求的金属冲压成品件。
不适用于对毛刺有特殊要求的成品件及精密冲压件。
2、定义冲压件毛刺系指板料冲压时留在冲压成品件断面口上的毛刺。
如图(1)所示:落料冲压件断面冲孔件断面图(1)(h—毛刺高度 t—冲压件的材料厚度)3、毛刺高度的极限值冲压件毛刺高度的极限值按照表(1)中的规定。
JB/T 4129-1999表(1)冲压件毛刺高度的极限值(mm)材料抗拉强度MPa 加工精度级别冲压件的材料厚度≤0.1>0.1~0.2>0.2~0.3>0.3~0.4>0.4~0.7>0.7~1.0>1.0~1.6>1.6~2.5>2.5~4.0>4.0~6.5>6.5~10.>100~250f0.020.020.030.050.090.120.170.250.360.600.95 m0.030.030.050.070.120.170.250.370.540.90 1.42 g0.040.050.070.100.170.230.340.500.72 1.20 1.90>250~400f0.020.020.030.040.060.090.120.180.250.360.50 m0.020.020.040.050.080.130.180.260.370.540.75 g0.030.030.050.070.110.170.240.350.500.73 1.00>400~630f0.020.020.020.030.040.050.070.110.200.220.32 m0.020.020.030.040.050.070.110.160.300.330.48 g0.020.030.040.050.080.100.150.220.400.450.65>630f0.020.020.020.020.020.030.040.060.090.130.17 m0.020.020.020.020.030.040.060.090.130.190.264、检测检测环境:常温常压。
- 1、下载文档前请自行甄别文档内容的完整性,平台不提供额外的编辑、内容补充、找答案等附加服务。
- 2、"仅部分预览"的文档,不可在线预览部分如存在完整性等问题,可反馈申请退款(可完整预览的文档不适用该条件!)。
- 3、如文档侵犯您的权益,请联系客服反馈,我们会尽快为您处理(人工客服工作时间:9:00-18:30)。
0.3
0.33
0.4 0.09 0.13 0.18
0.45 0.13 0.19 0.26
适用于一般要求的冲压件。
>6.5 ~10.0
0.95
1.42 1.9 0.5
0.75 1
0.32
0.48 0.65 0.17 0.26 0.35
应检测毛刺的最高峰值。如果精度要求高,可以使
>0.1 ~0.2 0.02
0.03 0.05 0.02
0.02 0.03 0.02
0.02 0.03 0.02 0.02 0.02
>0.2 ~0.3 0.03
0.05 0.07 0.03
0.04 0.05 0.3 ~0.4 0.05
0.07 0.1 0.04
0.07 0.1 0.03 0.04 0.05
>1.0 ~1.6 0.17
0.25 0.34 0.12
0.18 0.24 0.07
0.11 0.15 0.04 0.06 0.08
>1.6 ~2.5 0.25
0.37 0.5 0.18
0.26 0.35 0.11
0.16 0.22 0.06 0.09 0.12
测量。如果 精度要求不 是很高,可 以用千分尺 、高度尺等 机械长度测 量工具进行 测量。
毛刺的高度超过一定限度,将影响产品的质量和使 精密冲压件。
>2.5 ~4.0
0.36
>4.0 ~6.5
0.6
0.54 0.72 0.25
0.9 1.2 0.36
0.37 0.5 0.2
0.54 0.73 0.22
JB/T 4129-1999 表(1)冲压件毛刺高度的极限值(mm)
材料 抗拉 强度 Mpa
加工 精度级别
> 100
f
~ 250
m
g
> 250
f
~ 400
m
g
> 400
f
~ 630
m
g
f
> 630
m
g
≤0.1
0.02
0.03 0.04 0.02
0.02 0.03 0.02
0.02 0.02 0.02 0.02 0.02
落料冲压件断面
冲孔件断面
图(1)(h—毛刺高度 t—冲压件的材料厚度)
3、毛刺高度的极限值(数控冲床剪切面质量:R角(5%)光滑面(60%)撕裂面(30%)毛刺面(5%)) (冲3压0%件)毛毛刺刺面高(度5%的),极可限切值板按厚照最表厚(达1)4M中M.的。规特定点。:精度高,加工灵活.。缺点:受模具限
冲压件毛刺高度标准及检验方法
1、范围 本标准所列的数值在冲压公差的概念上是不允许的。但是,一般冲压件都带有不同程度的毛刺。毛刺的高度超过一定限度,将影响
用性能。本标准适用于对毛刺高度有一定要求的金属冲压成品件。不适用于对毛刺有特殊要求的成品件及精密冲压件。 2、定义
冲压件毛刺系指板料冲压时留在冲压成品件断面口上的毛刺。如图(1)所示:
0.05 0.07 0.03
0.04 0.05 0.02 0.02 0.03
冲压件的材料厚度
>0.4 ~0.7 0.09
0.12 0.17 0.06
0.08 0.11 0.04
0.05 0.08 0.02 0.03 0.04
>0.7 ~1.0 0.12
0.17 0.23 0.09
0.13 0.17 0.05
注: f级(精密级)适用于较高要求的冲压件;m级(中等级)适用于中等要求的冲压件;g级(粗糙级)适用于一般要求的冲压件。
Q235 A抗 拉强 度 MPa
:4 32~4 61MP a
4、检测
检测 常温常压。 环检测 根据产品的精度要求和材质,使用光学投影仪、工具显微镜、千分尺或其它等效方法检测。检测时应检测毛刺的最高峰值。如果精度 方 行用轮光廓学投投影影仪进