推移图和对策表
整理好的排列图因果图对策表
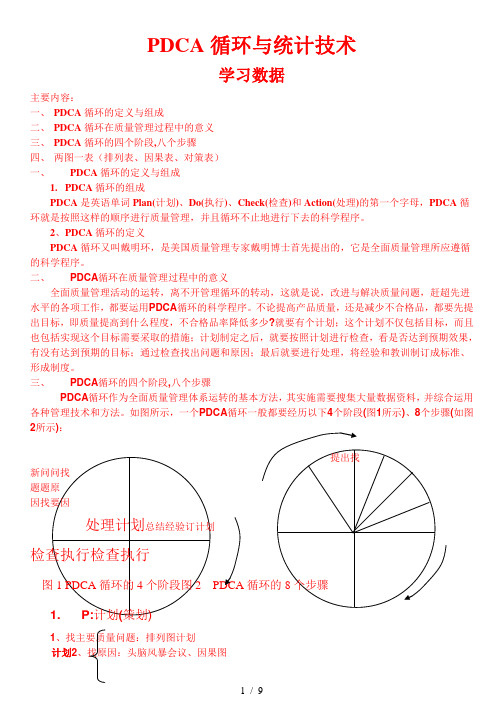
PDCA循环与统计技术学习数据主要内容:一、PDCA循环的定义与组成二、PDCA循环在质量管理过程中的意义三、PDCA循环的四个阶段,八个步骤四、两图一表(排列表、因果表、对策表)一、PDCA循环的定义与组成1.PDCA循环的组成PDCA是英语单词Plan(计划)、Do(执行)、Check(检查)和Action(处理)的第一个字母,PDCA循环就是按照这样的顺序进行质量管理,并且循环不止地进行下去的科学程序。
2、PDCA循环的定义PDCA循环又叫戴明环,是美国质量管理专家戴明博士首先提出的,它是全面质量管理所应遵循的科学程序。
二、PDCA循环在质量管理过程中的意义全面质量管理活动的运转,离不开管理循环的转动,这就是说,改进与解决质量问题,赶超先进水平的各项工作,都要运用PDCA循环的科学程序。
不论提高产品质量,还是减少不合格品,都要先提出目标,即质量提高到什么程度,不合格品率降低多少?就要有个计划;这个计划不仅包括目标,而且也包括实现这个目标需要采取的措施;计划制定之后,就要按照计划进行检查,看是否达到预期效果,有没有达到预期的目标;通过检查找出问题和原因;最后就要进行处理,将经验和教训制订成标准、形成制度。
三、PDCA循环的四个阶段,八个步骤PDCA循环作为全面质量管理体系运转的基本方法,其实施需要搜集大量数据资料,并综合运用各种管理技术和方法。
如图所示,一个PDCA循环一般都要经历以下4个阶段(图1所示)、8个步骤(如图2所示):1、找主要质量问题:排列图计划计划2、找原因:头脑风暴会议、因果图3、找要因:排列图、计分法、验证4、制定对策(计划)措施:对策表2. D:执行(实施)执行5、实施对策措施3、C:执行(检查)执行6、检查实施效果:排列图、因果图4、A:处理(总结)7、标准化处理处理8、遗留问题转下一循环四、两图一表1、排列图•定义:又叫帕累托图,它将质量改进项目最重要到最次要进行排列而采用的一种简单的图示技术。
QC七大手法及其他常用图表介绍

出口星状轮 导入异常
停机电眼感应
停方式机不佳电眼感 电眼应无法方侦测式不佳
夹瓶器夹夹头材瓶器夹头材
质选用不当 质选用不当
夹瓶器夹头软防
蚀性不佳
定位方式无 标准
星状轮定位 位置不佳
制瓶班不良 品流入
瓶子成型 不良
管制 不当
固定力不足
未锁紧
设计不良
护栏固定夹 松脱
星状轮卡死 无运转
设计不佳
黄油嘴位置 不当
步骤三:决定中小要因。
制造
人员 金额
生产条件不好
没有生产 计划配合
订单掌握不 正确
利润低
为 何
没有式样
没有交货意识 运输成本高
延
单方面决定
迟
库存安全 量低
方法不明确 交货期短
没有交货 计划
交 货
存放位置
不足
数量少
物品
交货
步骤四:决定影响问题点的主要原因。
制造
人员 金额
为
生产条件不 好
没有生 产计划
脑力激荡法原则
(一)严禁批评他人构想和意见 (二)意见越多越好 (三)欢迎自由奔放的构想 (四)顺着他人的创意或意见发
展自己的创意(搭便车)
为 什 么 延 迟 交 货
步骤一:决定问题的质量特性。
环 境 作业方法 材 料
特 性
机械
作业人员
步骤二:决定大要因。
环 境 作业方法 材 料
特 性
机 械 作业人员
决定大要因
用四M一E来分类。 Man(作业人员)、Machine(机器)、 Material(材料)、Method(作业方式)等 四类,在再加上Environment(环境)。
学习计划推移图

学习计划推移图
第一阶段:明确目标
时间:1周
目标:明确学习目标和计划
计划:在本周内,仔细思考并明确学习目标,并根据目标制定学习计划。
第二阶段:查缺补漏
时间:2周
目标:对已学知识进行系统梳理,查缺补漏。
计划:在接下来的两周内,对已经学习过的知识进行复习巩固,查缺补漏,建立扎实的基础。
第三阶段:系统学习
时间:8周
目标:系统学习相关知识,建立完整的知识体系
计划:在接下来的两个月内,系统学习相关知识,建立完整的知识体系,包括理论学习、实践应用、案例分析等方面。
第四阶段:综合实践
时间:4周
目标:在实际项目中将所学知识进行应用和实践
计划:在接下来的一个月内,积极参与实际项目,将所学知识进行应用和实践,做到学以致用。
第五阶段:巩固提高
时间:4周
目标:对已学知识进行巩固提高,深化理解。
计划:在接下来的一个月内,对已学知识进行深化理解和提高,不断巩固学习成果,做到知识牢固、理解透彻。
第六阶段:评估总结
时间:1周
目标:全面评估学习成果,进行总结
计划:在最后一个周内,对整个学习过程进行评估和总结,总结经验,总结收获,为下一步学习做好准备。
总结:
以上就是我的学习计划推进图,通过明确目标、查缺补漏、系统学习、综合实践、巩固提高和评估总结,我相信我一定能够取得学习的优异成绩。
在学习的道路上,我们要一步一个脚印,踏实稳健,才能走得更远。
希望我的学习计划能够对大家有所启发,也希望大家一起努力,共同进步。
层别法图表

11 16 12 12 12 14 13 13 11 9 123 0.29
总运转时间 3502 5115 4852 4606 4820 3374 5065 5119 2955 2844 42252 ——
故障率(%) 0.31 0.31 0.25 0.26 0.25 0.41 0.26 0.25 0.37 0.32 0.29 ——
具体明确因素。
5
第五页,课件共有35页
(三)实地演练
《降低TBA/9 300A线充填机环式压缩机压力异常故障率》
——台湾杨梅总厂 智力圈
改善前数据收集:
日期:5/2~5/13
项目
日期
热交换器堵塞
收集人:黄沐祥
单位:包
5/2 5/3 5/4 5/5 5/6 5/9 5/10 5/11 5/12 5/13 合计 故障率
层别法图表
1
第一页,课件共有35页
▪ 查检表的定义
查检表的分类
为何要用查检表
实际演练
2
第二页,课件共有35页
(一)查检表的定义
系统地收集资料和累积资料,确认事实并
对资料进行粗略的整理和简单分析的统计图表。
3
第三页,课件共有35页
(二)查检表的分类
·记录用(改善用)查检表:
查
把数据分类成数个项目,以符号、数字记录作为分
先作层别才有意义,才能做进一步的解析
18
,才能取得更多的情报。
16
(2)层别法无固定之图形,必须与其他
14
QC手法作应用,如特性要因图、柏拉图、 12
10
直方图、散布图、管制图等,方能发挥
8
效用。
6
4
2
0
护理护理质量数据处理工具10种K

分类
中央集中型:把要分析的问题放在图的中央位置,把同“问题 ”发生关系的因素逐层排列在其周围。
单侧汇集型:把要分析的问题放在右侧或左侧,与其发生关
联的因素从由向左或从左向右逐层排列。
定义
◆ 为解决某一个问题所收集的数据、材料,往往是综合
性的。这些数据、材料可按其来源、特征、属性等标识 分作两个以上的组,这样一个组称作“层”。 •1、定义:按照一定的标志,把搜 •索到的大量有关某一特定主题的统 •计数据加以归类、整理和汇总的一 •种方法。
目录
头脑风暴 亲和图 查检表 排列图 分层法 因果图 树图 关联图 散布图 流程图 对策表 柱状图 推移图 控制图 雷达图
目录
头脑风暴 亲和图 查检表 排列图 分层法 因果图 树图 关联图 散布图 流程图 对策表 柱状图 推移图 控制图 雷达图
定义
•
树图又叫系统图,树图是表示某个质量问题与其组成
要素之间的关系,从而明确问题的重点,寻求达到目的
所应采取的最适当的手段和措施的一种树枝状图。
目录
头脑风暴 亲和图 查检表 排列图 分层法 因果图 树图 关联图 散布图 流程图 对策表 柱状图 推移图 控制图 雷达图
作用
• 1、方针目标实施项目的开展
• 2、在新产品开发中进行质量设计展开 • 3、为确保质量保证活动而进行的保证质量要素(事项)的展开 • 4、对为解决企业内质量、成本、产量等问题所采取的措施加以展开 • 5、工序分析中对质量特性进行主导因素的展开 • 6、对各部门职责、权限展开,用于机构调整时职能分配 • 7、用于多层次因果关系的分析,以弥补因果图的不足
EHS工作蓝图及推移表专业版参考模板范本

EHS
单次 单次 单次
体系文件编制(程序文件)
变更管理程序 用工管理程序
EHS 单次 EHS 单次
施工管理控制程序
EHS 单次
职业健康监护管理程序
EHS 单次
体系
工作安全许可管理程序
EHS
建设项目EHS三同时管理程 序废水、废气、噪音管制程序
EHS EHS
废弃物管理控制程序
EHS
《应急准备和响应管理程序 》
安全生产事故预警管理制度 EHS
重点危险区域及盲区安全管 理制度
EHS
体系文件编制(作业指导书) 美工刀安全管理规定
EHS
易燃易爆化学品安全操作指 导书
EHS
电气安全管理规定
EHS
义务消防队管理指规定
EHS
安全警示标志管理制度
EHS
安全生产费用提取和使用管 理办法
EHS
班组岗位达标管理办法
EHS
领导现场带班制度
EHS
单次 单次 单次
EHS培训教育管理程序 《信息交流和协商管理程 序.》 文件、资料控制程序
EHS 单次 EHS 单次 EHS 单次
化学品管理程序
EHS 单次
厂内外机动车辆管理程序
EHS 单次
个人防护用品管理程序
EHS 单次
设施设备EHS管理程序
EHS
特种设备与特种作业人员管 理程序
EHS
用电控制管理程序
750MW产能扩建项目节能评估报告
工厂排污许可证
现有项目和扩建项目的排污指标申报
危险废弃物合同签订
危险废弃物
危险废弃物合规处理 危废仓库建设
厂内的危废收集、转移、暂
存管理
QC七大手法及其他常用图表介绍

无运转
设计不佳
黄油嘴位置 不当
未落实保养
培林无润滑
其他
启动夹瓶
护栏未 调定位
出星状轮 空瓶歪斜
卡瓶处理后 容易跳脱
障 率 高
何谓原因、要因与真因?
1.原因:所有可能造成问题的因素都称为原因。
2.要因:根据经验或投票所圈选出来的原因(并 没有实际到现场收集数据来验证)
3.真因:至现场对现物收集数据后,所验证出来 的真正原因,也就是用数据圈选出来的 原因。
合计
月日 月日
查检表之注意事项
1.收集与查检力求简单,容易执行。 2.决定查检表格式要考虑查检频率及查检项目。 3.查检表之纵横坐标须考虑合计字段或平均字段。 4.与其他手法合并使用效果更好。 5.查检基准需一致。 6.查检项目宜完整,并增列空白字段(最好不用其
他项代替)
管制图
检验的质量管理
第一次世界大战期间,工厂组织更复杂,单靠领班已 无法管理工人,只有委派受过特别训练的检验人员负 责检验制品质量,使生产工作与检验工作分开。
检查用查检表
线别:
○○股份有限公司
自动焊锡炉日保养记录表(T-5-5-3-QW0905-05) 年 月
日期 项目
1
2
3
4
5
6
7
8
9
1 0
1 1
1 2
1 3
1 4
1 5
1 6
1 7
1 8
1 9
2 0
2 1
2 2
2 3
2 4
2 5
2 6
2 7
2 8
2 9
3 0
3 1
机身内外擦拭清 洁
预热器的玻离挡 板清洁
品管手法之推移图
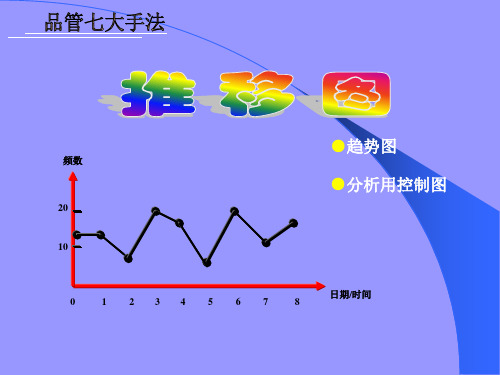
3-1 改善后数据的收集与描点 3-2 改善后数据的平均数线
改善前
结论:在改善的过程中, 结论:在改善的过程中,控制平均水 平逐渐得到改善。 平逐渐得到改善。
改善中 改善后
10 11 12 13 14 15 16 17 18 19 20 21
采购部门 交货递延率 曲线图 曲线图 柱状图
品质部门
不良率 工程改善 客户抱怨
物料部门 存货周转率 曲线图 呆滞品金额 曲线图
改善过程中的推移图案例
1-1 改善前数据的收集与描点 1-2 改善前数据的平均数线 2-1 改善中数据的收集与描点 2-2 改善中数据的平均数线
18 16 14 12 10 8 6 4 2 0
●趋势图 趋势图
频数
●分析用控制图 分析用控制图
20
10
0
1
2
3
4
5
6
பைடு நூலகம்
7
8
日期/时间 日期 时间
定义:一种随着时间的移动,将设定工作推动的项目, 一种随着时间的移动,将设定工作推动的项目,
结合设定的指标而将实绩在成果绘制在图上, 结合设定的指标而将实绩在成果绘制在图上,以 观察实际的成果与设定指标的差距, 观察实际的成果与设定指标的差距,以便采取调 整措施的一种图表; 整措施的一种图表 目的:改变了一般报表在文字上的体现, 目的:改变了一般报表在文字上的体现,并且也弥补 了一般报表不容易查觉到随时间的变动所呈现 结果的变化起伏状况; 结果的变化起伏状况 适应范围: 适应范围: 日常管理工作; 日常管理工作; 研究质量数据可控制幅度。 研究质量数据可控制幅度。
图 示 柱状图 曲线图 曲线图 柱状图 曲线图 柱状图 曲线图 曲线图 曲线图 柱状图 曲线图 曲线图 曲线图
对策表

❖ 对策表是PDCA循环第一阶段及P(策划)阶 段找问题、查原因、分主次和订措施等步骤 中第四个步骤的产物。也是P阶段找问题、 查原因、分主次三个步骤应用因果图、排列 图分析方法之后“两图一表”联用的必然结 果。
二、对策表的设计
❖ 对策表一般采用表格的形式,对策表的表头 栏目应依次排出,5W1H的问题。即What(原 因),Why (目标),How (措施),Who (执行 者),Where (执行地点),When (完成时间)等。
❖ 为防止不合格的再发生,需要针对查找出的 主要问题的主要原因,制定切实可行的纠正 措施计划。
❖ 对策表实质上就是表格化的纠正措施计划。 ❖ 对策表具有简明清晰的特点,一目了然。 ❖ 有助于纠正措施计划地制订、评价、实施和
检查。
四、应用实例
下表是某厂为了解决“降低离心风机 的振动”这一质量问题经因果图分析后制 定的对策表。
序号 1 2 3 4
要因
现状
对策
目标
措施
对工作人 员进行轴 承端盖装 配技术的 培训不够
轴承端盖 轴向尺寸
过大
叶轮端面 变形
工作人员 XXX等人未 经过培训, 对轴承装配 能力仅达
50%
1)对XXX等人 进行轴承端盖 装配的培训; 2)送部分人 到专业学校学
习取经
端盖与轴承 外转有0.6
㎜紧力
1)在端盖与 轴承座接触面 处加0.85 ㎜青 壳纸片;2) 将端盖与轴使 用。如前所述,排列图是用以查找出存在的 问题,因果图用以查找出产生质量问题的原 因。常将以上三种工具称为“两图一表”。
一、对策表的概念
❖ 所谓“对策”是针对问题、原因而言的。 要排除产生问题的原因,寻求有效的质量 改进途径需要有相应的对策、措施。
推移图分析
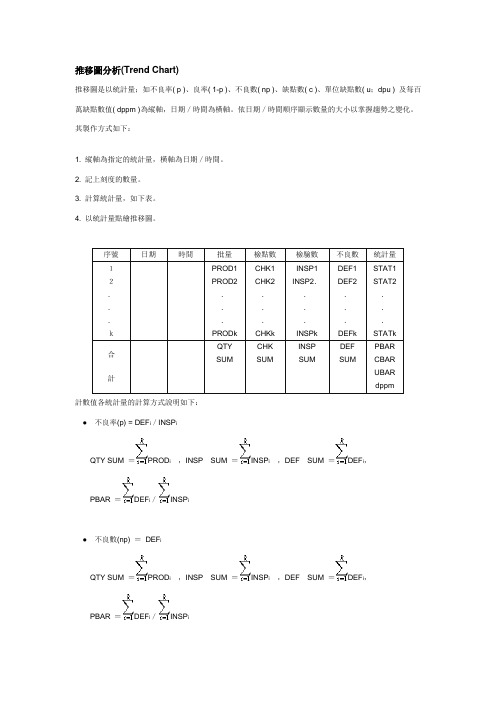
推移圖分析(Trend Chart)推移圖是以統計量;如不良率( p )、良率( 1-p )、不良數( np )、缺點數( c )、單位缺點數( u ;dpu ) 及每百萬缺點數值( dppm )為縱軸,日期/時間為橫軸。
依日期/時間順序顯示數量的大小以掌握趨勢之變化。
其製作方式如下:1. 縱軸為指定的統計量,橫軸為日期/時間。
2. 記上刻度的數量。
3. 計算統計量,如下表。
4. 以統計量點繪推移圖。
計數值各統計量的計算方式說明如下: ● 不良率(p) = DEF i /INSP iQTY SUM =PROD i ,INSP SUM =INSP i ,DEF SUM =DEF i ,PBAR =DEF i /INSP i● 不良數(np) = DEF iQTY SUM =PROD i ,INSP SUM =INSP i ,DEF SUM =DEF i ,PBAR =DEF i /INSP i●良數(1-p) =1-DEF i/INSP iQTY SUM =PROD i,INSP SUM =INSP i,DEF SUM =DEF i,PBAR =DEF i/INSP i●缺點數(c) =DEF iQTY SUM =PROD i,INSP SUM =INSP i,DEF SUM =DEF i,CBAR =DEF i/INSP i●單位缺點數(u;dpu) =DEF i/INSP iQTY SUM =PROD i,INSP SUM =INSP i,DEF SUM =DEF i,UBAR =DEF i/INSP i●每百萬缺點數(dppm) =(DEF i/(CHK i x INSP i)) x 106QTY SUM =PROD i,CHK SUM =CHK i x INSP i,DEF SUM =DEF i ,dppm =(DEF i/CHK i INSP i x 106。
Q7手法之推移图
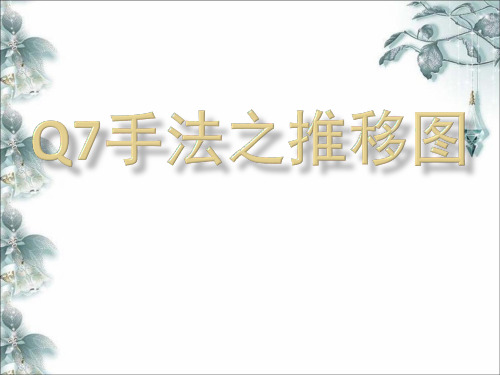
注意事项: 1、下一次上课前交作业,交到应小倩处。 2、培训成绩按时公布在食堂公告栏。
题目: 1、手绘完成一份任意一个型号的滑块厚度数据的 直方图,要有数据与过程。
学以致用!
手动计算可以加深理解!
ห้องสมุดไป่ตู้
(1)推移图就是数据的变动,以点与折线连接起 来的图。 (2)功能: 1.推移图作为视查数据时间变化的一种好方法。 2.影响数据要因如能区分记入,就可以了解其影 响度
(1)决定期间收集数据。 (2)计算不良率或每单位缺点数。 (3)方格纸上划上纵轴与横轴,纵轴记入分度(特 性),横轴记入时间。 (4)依数据打点,点与点之间折线连接。 (5)计算各期间之总平均值。 总不良动 总不良率 P = ---------------- ≠ -----------------总检查数 总天数 (6)记人数据之期间及记录表目的。
(1)总推移图:表示各要因总和之影响情形。
(2)层别推移图:表示各要因别之影响情形。
层别法就是为要区别各种不同原因,对结果之影 响,而以各别原因为主体,分别作统计分析的方 法。
(1)异常值必需记录发生之现象,原因并加以说 明,于计算中除去异常值。 (2)以数字表示真正效果,必须将改善前所收集 之数据全部列出。 (3)改善中对策需分段实施,推移图记入对策编 号,有异常点亦必须划在方格子中间,以确认各 对策之效果。 (4)效果有副作用时,必须两者同时比较利弊得 失。
(5)对策实施中要注意效果,有严重不良发生时 ,应立即停止对策实施。 (6)确认效果之尺寸需前后一致,特性要相同。 (7)数据要不断的收集,未完成之对策继续实施 ,再确认效果。 (8)效果确认之时间 1.改善前----对策开始实施以前。 2.改善中----改善对策实施至对策标准化以前。 3.改善后----有效对策实施标准化以后。
QC旧七大手法基础知识及图表制作

通常为1
★直方图的功用:
•评估和检查工序能力; •指出采取措施的必要; •检查执行纠正措施是否有效; •比较设备、物料、人员及供应商;
QC 七手法
★直方图实例练习
1.某罐头厂生产罐头,罐头容量305 310 309 312 313 311 304 309 317 306 310 316 312 315 307 308 311 312 306 302 309 307 307 305 317 310 309 316 314 311 305 303 305 316 315 311 309 312 308 307 304 318 317 309 320 314 310 318
QC 七手法
泉州科力感应洁具有限公司 QC旧七大手法基础知识及 常用图表制作
品保科:尚玉兵2012/02/17
QC 七手法
起源
新旧七种工具都是由日本人总结出来的。日 本人在提出旧七种工具推行并获得成功之后, 1979年又提出新七种工具。之所以称之为 “七种工具”,是因为日本古代武士在出阵 作战时,经常携带有七种武器,所谓七种工 具就是沿用了七种武器。有用的质量统计管 理工具当然不止七种。除了新旧七种工具以 外,常用的工具还有甘特图、饼图、推移图 等。
•确定基本内容:N=50 •组数:K=7(参考经验数值) •最大值L=320 最小值S=302 全距R=320-302=18 •计算组距H H=R/K 18÷7=2.5 取H为3(为测定值最小单位的整数倍)
QC 七手法
•第一组下限值=S-测定值最小位数/2=302-0.5=301.5 第一组上限值=第一组下限值+组距 •计算各组中心值=(上组界+下组界)/2 •作次数分配表
~50 50~100 100~250
QC七大手法管制图推移图ppt课件

0.12
0.1
0.15 0.12
UCL=0.05
0
1 2 3 4 5 6 7 8 9 10 11 12 13 14 15 16 17 18 19 20 21 22 23 24 25 26 27 28 29 30
樣本號數
8
UMC
品保部
一. 針對管制圖進行分析
由管制圖中我們可以發現來自樣本12及25的兩點 超出管制上限,故制程是在非管制狀態,必須進一步探 討是否有異常原因.分析樣本12得知,在這半小時里,有 一批新進的包裝袋被使用,所以這異常的現象是由于新 原料加入引起.而在樣本25那半小時,有一個沒有經驗 的員工在操作此機器,而使樣本25有這麼高的不良率.
改善前
结论:在改善的过程中,控制平均水 平逐渐得到改善。
10
改善中
8 改善后
6
4
2
0
1 2 3 4 5 6 7 8 9 10 11 12 13 14 15 16 17 18 19 20 21
6
UMC
品保部
例: 寶光廠生產的MOUSE用的包裝袋,檢驗其底部是否有破損即 包裝為不良品,取30個樣本,每個樣本數為50個,這些樣本是 在機器每天三班制的連續工作每半小時取一次而得.
1
0.12
6 08/06 1051
2
0.19
检查数
1400
不良数
1200
不良率% 1000
800
600
400
200
8月4日
8月5日
0 8月6日
4
UMC
品保部
日常管理推移图资料
部门 人事部门 营业部门 采购部门 物料部门
项目 公司总人数 缺勤率 流动率 营业额 交货递延率 退货率 采购金额 交货递延率 退货率 存货数量 存货周转率 呆滞品金额
来料超额运费推移图

2500
2000
来料超额运费推移图 (目标值<1000元)
1月
2月
3月
4月
5月
6月
7月
8月
9月 10月 11月 12月
合计
0
1000 1000 1000 1000 1000 1000 1000 1000 1000 1000 1000 1000
超额运 费
1500
1000
500
0 1月 2月 3月 4月 5月 6月 7月 8月 9月 10月 11月 12月
备注
超额运费=当月实际发生的额外运输费用 超额运费统计来源:1、因异常导致重新送货所发生的运输费用;
2、因供应商自已原因导致分批交付,所发生的运输费用; 3、为满足交期,变更运输方式,如海运变空运,空运与海运的差异运输费用; 4、其它方式或原因导致的来料额外运输费用。 5、原则上来料超额运费均是由供应商承担,除非是亚达责任导致的由亚达承担!
批准:
审核:
制表:Leabharlann
护理质量与管理工具

用途
1、确定影响质量的 主要因素。按重要 顺序显示出每个质 量改进项目对整个 质量问题的影响。
✓寻找主要问题 ✓识别质量改进机会 ✓检查改进效果
目录
头脑风暴 亲和图 查检表 排列图 分层法 因果图
树图 关联图 散布图
流程图 对策表 柱状图 推移图 控制图 雷达图
服错药 打错针 烫伤 断针 注射化脓 褥疮 其他
用途
2、确定采取措施的顺序
3、动态排列图可评价采取措施的效果。在实 施改进措施后,用排列图进行前后对比,以此 来说明改进措施的有效性。
目录
头脑风暴 亲和图 查检表 排列图 分层法 因果图
树图 关联图 散布图
流程图 对策表 柱状图 推移图 控制图 雷达图
排列图做图步骤演示
某医院某年护理差错原因
原因 (1)
目录
头脑风暴 亲和图 查检表 排列图 分层法 因果图
树图 关联图 散布图
流程图 对策表 柱状图 推移图 控制图 雷达图
优点
• 1、尽可能地发挥小组的创造力
先由一个人发言,提出一个建议,抛砖引玉,启发大家的灵 感,产生连锁反应效果。
• 2、提高创造力
通过全员参与思考、产生智慧火花,树立“只要做就能成”的 自信心。
目录
头脑风暴 亲和图 查检表 排列图 分层法 因果图
树图 关联图 散布图
流程图 对策表 柱状图 推移图 控制图 雷达图
图例
A
A1
合并A2
A1-1
同类项A2-1
A1-2
A2-2
A1-3
A3
B
B1 B2 B3
目录
头脑风暴 亲和图 查检表 排列图 分层法 因果图
- 1、下载文档前请自行甄别文档内容的完整性,平台不提供额外的编辑、内容补充、找答案等附加服务。
- 2、"仅部分预览"的文档,不可在线预览部分如存在完整性等问题,可反馈申请退款(可完整预览的文档不适用该条件!)。
- 3、如文档侵犯您的权益,请联系客服反馈,我们会尽快为您处理(人工客服工作时间:9:00-18:30)。
示例
品管圈课题对策实施表
序号 要因 项目现状 目标 对策措施 负责人 完成期限
谢 谢!
•其他事物发展或解决的趋势
推移图 应用推移图的要点
要有目标线,如果没有,不能有效地引起大家的注意 当发现超出目标线时,要分析原因,找出改进的机会 一般以每周、每月或每年为单位制作推移图,也可以
以每天为单位做推移图 推移图要适当保存,以便前后推移图进行对比层别
推移图 推移图制作步骤
确定主题
2月份某专业厂制程抽检不良率推移图
不良率(%)
4 3.5 3 2.5 2 1.5 1 0.5 0 1 2 3 4 5 6 7 8 9 10 11 12 13 14 15 16 17 18 19 20 21 22 23 24 25 26 27 28
对策表
对策表既是实施的计划,又是检查的依 据,是PDCA循环中P(计划)阶段制定 对策这一步骤的产物
2018/9/5
推移图和对策表
主讲:
时间:
推移图
推移图是指管理研究事项随时间而变化的
图形。由于推移图有目标线,因此它是一个 有效地控制工具,当推移点超出目标线时, 能有效地引起管或不 合格品数) 的趋势
在工厂, 推移图一 般应用于 以下方面
每天生产完 成产量的趋 势
设计推移图的表格
收集数据
依据数据画出推移图
判定
示例:某专业厂2月份制程抽检不良率推移图
2月份制程抽检不良效率统计表
日期 脏污 重量不符 瓶变形 脱墨 毛刺 当日不良数 当日抽检数 当日不良率(%)
1 2 3 4 5 6 7 8 9 10 11 12 13 14 15 16 17 18 19 20 21 22 23 24 25 26 27 28
1 0 0 1 2 0 0 1 0 1 2 1 2 0 1 0 0 1 2 3 1 2 0 1 3 1 2 5
5 6 7 8 1 1 2 1 0 3 2 3 0 2 1 3 2 3 4 5 1 1 6 3 1 1 2 3
10 11 11 17 10 2 5 5 5 6 7 6 6 5 6 8 6 8 11 10 9 6 12 9 6 12 6 12
对策表制定时的注意事项:
对策表的表头项目应回答SW1H的问题 在制定各项目标时应尽量用定量化的数
据,不应采取模糊的抽象化的语言作为目标 目标对策的实施应全体成员参与
对策表的作用
对策表可用于针对不合格原因,防止不合格
的再发生而采取纠正措施的计划制订 对措施计划的评价并有效贯彻实施 检查和评价所采取措施的结果及其有效性
500 500 500 500 500 500 500 500 500 500 500 500 500 500 500 500 500 500 500 500 500 500 500 500 500 500 500 500
2 2.2 2.2 3.4 2 0.4 1 1 1 1.2 1.4 1.2 1.2 1 1.2 1.6 1.2 1.6 2.2 2 1.8 1.2 2.4 1.8 1.2 2.4 1.2 2.4
1 2 1 2 3 0 1 2 3 1 1 1 1 0 0 2 1 0 2 0 5 1 2 3 1 2 0 3
1 1 1 1 0 0 0 0 0 0 0 0 2 1 1 1 2 1 1 2 1 0 2 2 1 3 0 0
2 2 2 5 4 1 2 1 2 1 2 1 1 2 3 2 1 3 2 0 1 2 2 0 0 5 2 1