药品生产风险评估
药品生产企业风险评估指南

药品生产企业风险评估指南
1概述
(1)适用人群:该评估指南可供安全监管/行业主管部门安全监管专职人员,安全责任主体单位(企业的安全监管等岗位的人员),以及安全管理系统的研发人员参考使用。
(2)编制思路:本指南在进行药品生产企业风险识别中,从生产设备及产品本身、生产过程和管理因素三个方面进行评价。
着重考虑原材料自身因素及生产过程所涉及的可能风险。
通过分析影响药品生产企业安全的各个影响因素,设置各项总分数,在表格中对各项不同内容进行打分。
(3)评分规则:本指南评估采用100分制,根据打分结果按照风险从高到低依次分为红色(85分以上)、橙色(75至85分以下)、黄色(55至75分以下)、蓝色(55分及以下)四个等级。
(4)引用文件(凡未注日期的引用文件,其最新版本适用于本文件):
《关于进一步加强药品生产工作的通知》(粤食药监安〔2011〕9号)
《危险化学品生产储存企业安全风险评估诊断分级指南(试行)》(应急〔2018〕19号)
《危险化学品重大危险源辨识》(GB18218-2018)
《食品药品监管总局关于印发药品生产现场检查风险评定指导原则的通知》(食药监药化监〔2014〕53号)
《中华人民共和国特种设备安全法》(中华人民共和国主席令第四号)
《广东省应急管理厅关于安全风险分级管控办法(试行)》(粤应急规〔2019〕1号)
2评价指标
风险主要指标以及权重见下表:
表药品生产企业风险评价指标及评分标准。
药品生产风险管理:评估与控制方法

药品生产风险管理:评估与控制方法在药品生产过程中,风险管理是至关重要的环节。
良好的风险管理可以确保药品的质量、安全性和合规性,同时也有助于降低生产过程中的各种风险。
本文将介绍药品生产中常见的风险,以及评估和控制这些风险的方法。
药品生产中的常见风险在药品生产过程中,存在着多种风险,包括但不限于以下几个方面:1.原材料风险:药品生产的原材料质量直接影响着最终产品的质量,原材料可能存在纯度不足、受到污染等问题,导致最终产品不符合要求。
2.工艺风险:生产工艺不当可能导致产品性能不稳定、产量低、污染严重等问题,从而影响产品质量。
3.设备风险:药品生产中使用的设备可能存在运行不稳定、材料老化等问题,这些问题可能导致产品质量波动,甚至严重事故发生。
4.人为失误风险:人为操作不当、员工培训不足等因素可能导致生产事故发生,严重影响生产安全和产品质量。
5.合规性风险:药品生产必须符合各种法规和标准,一旦不符合合规要求,可能导致产品召回、追溯等问题,对企业造成巨大影响。
评估药品生产风险的方法评估药品生产风险是为了全面了解潜在的风险因素,从而有针对性地制定风险管理措施。
以下是评估药品生产风险的方法:1.风险识别:通过对药品生产过程及相关环节的分析,识别潜在的风险因素,包括原材料、工艺、设备、人为因素等。
2.风险分析:对已识别的风险进行深入分析,确定各种风险可能对生产过程和产品质量造成的具体影响。
3.风险评估:评估每种风险的发生可能性和影响程度,为后续的优先级制定提供依据。
4.风险优先级制定:根据风险评估结果,确定各种风险的优先级,以便有序地制定相应的风险管理措施。
控制药品生产风险的方法控制药品生产风险是为了降低风险发生的可能性和影响程度,保障产品质量和生产安全。
以下是控制药品生产风险的方法:1.制定风险控制计划:根据风险评估结果,制定风险控制计划,明确各项风险管理措施的实施时间、责任人等。
2.设备维护:定期对生产设备进行维护和检查,确保设备运行稳定、安全。
药品生产过程中的质量风险评估与控制效果评估

药品生产过程中的质量风险评估与控制效果评估药品的生产过程中,质量风险评估和控制效果评估是非常重要的环节。
通过对药品生产过程进行评估,可以有效降低质量风险,并确保生产出符合质量标准的药品。
本文将介绍药品生产过程中的质量风险评估与控制效果评估的方法和重要性。
一、质量风险评估质量风险评估是指对药品生产过程中可能存在的质量风险进行全面评估和分析。
其目的是确定可能出现的风险,并采取相应的控制措施以降低风险发生的概率。
质量风险评估可以从以下几个方面进行:1. 原材料风险评估:对原材料进行检查和评估,确保其符合质量要求,同时评估原材料可能带来的潜在风险。
2. 制造工艺风险评估:评估制造工艺的合理性和风险性,包括工艺步骤、操作规范、设备设施等方面,以确定潜在的风险并采取相应的控制措施。
3. 环境条件风险评估:评估生产环境的清洁度、温湿度控制等条件,确保符合药品生产的标准,并降低环境条件对药品质量的不利影响。
4. 检测方法风险评估:评估药品的检测方法的准确性和可靠性,确保检测结果的准确性,并防止检测方法可能带来的误判。
二、控制效果评估控制效果评估是指对已经采取的控制措施的有效性进行评估和验证。
通过控制效果评估,可以判断已采取的措施是否有效,并进一步完善和改进控制策略。
控制效果评估可以从以下几个方面入手:1. 检测方法验证:对已采取的检测方法进行验证,确保其准确性和可靠性。
验证结果应与已知标准进行对比,以判断检测方法的有效性。
2. 生产过程监控:对生产过程中关键环节进行监控,确保操作规范的执行和质量控制的有效性。
如对温度、湿度、压力等参数进行实时监测,并对异常情况进行及时处理。
3. 质量管理体系审核:对质量管理体系进行定期的内部审核和外部审核,评估质量管理体系的有效性,并及时发现和纠正存在的问题。
三、质量风险评估与控制效果评估的重要性质量风险评估和控制效果评估对药品生产过程的质量管理和控制具有重要意义。
其重要性主要表现在以下几个方面:1. 提高生产效率:通过准确评估质量风险和控制效果,可以合理安排生产中的各个环节,避免不必要的质量问题和生产延误,从而提高生产效率。
药品生产过程中的质量风险评估与控制

药品生产过程中的质量风险评估与控制药品作为保障人民健康的重要物品,其质量问题直接关系到患者的生命安全和康复效果。
药品生产过程中的质量风险评估与控制是确保药品质量的重要环节。
本文将从质量风险评估工具、质量风险控制措施两个方面进行论述。
1. 质量风险评估工具质量风险评估是指对药品生产过程中可能出现的质量问题进行系统分析和评价的过程。
以下是几种常用的质量风险评估工具。
1.1 故障模式与影响分析(FMEA)故障模式与影响分析(FMEA)是一种常用的质量风险评估工具。
它通过识别可能出现的故障模式,评估故障对药品质量的影响程度,并提出相应的预防措施和改进建议。
例如,在药品生产过程中可能出现原材料污染的故障模式,可以通过加强原材料检验和采购渠道管理等措施进行预防和控制。
1.2 事件树分析事件树分析是一种用于分析事故发生的概率和可能结果的方法。
在药品生产过程中,可能存在的事件包括生产设备故障、操作失误等。
通过事件树分析,可以评估这些事件发生的概率以及它们对药品质量可能造成的影响。
评估结果可以帮助制定相应的预防和应急措施,减少质量风险的发生。
1.3 流程故障模式与影响分析(PFMEA)流程故障模式与影响分析(PFMEA)是FMEA在生产过程中的一种应用。
它通过对药品生产流程中的每个环节进行分析,发现可能出现的故障模式和其对药品质量的影响。
比如,在药品灌装环节可能存在灌装量偏大或偏小的故障模式,可以通过加强操作培训和设备校准等措施进行预防和控制。
2. 质量风险控制措施质量风险控制是指通过采取相应的措施,降低或消除质量风险的过程。
以下是几种常用的质量风险控制措施。
2.1 严格遵守GMP要求GMP(Good Manufacturing Practice)是药品生产过程中的质量管理规范。
通过遵守GMP要求,能够规范药品生产过程,减少质量风险的发生。
例如,实施清洁消毒制度、设立检验报告文件等都是履行GMP 要求的措施,可以有效降低药品污染和交叉污染的风险。
药品风险评估指导原则

药品风险评估指导原则
1. 评估范围,药品风险评估应该覆盖药品的研发、生产、质量
控制、临床试验、上市后监测等全过程,全面考虑药品可能存在的
各种风险。
2. 风险识别,对药品可能存在的各种风险进行全面识别和分类,包括药理毒理风险、药物相互作用风险、药物不良反应风险、生产
质量控制风险等。
3. 风险评估,对已识别的风险进行定量或定性评估,评估风险
的可能性和严重程度,以确定风险的优先级和紧急程度。
4. 风险控制,针对评估出的各种风险,制定相应的控制措施,
包括在药品研发过程中加强药理毒理实验、临床试验设计合理性、
加强质量管理等方面的控制措施。
5. 风险沟通,对评估出的风险及其控制措施进行及时、准确的
沟通,包括向监管机构、医疗机构、患者和公众等各方进行风险沟通,提高对药品风险的认识和理解。
6. 风险监测,建立健全的药品风险监测体系,及时监测药品使用过程中出现的新风险和不良反应,以便及时调整和改进风险控制措施。
总的来说,药品风险评估指导原则强调全面、系统地对药品可能存在的各种风险进行评估和管理,以保障药品的安全有效使用,保护患者和公众的健康。
同时,也需要在不同阶段和环节中加强风险沟通和监测,不断改进和完善风险评估和管理体系。
药品生产过程中的质量风险评估与控制

药品生产过程中的质量风险评估与控制在药品生产过程中,质量风险评估与控制是至关重要的环节。
通过对质量风险的评估,药品生产企业可以识别潜在的风险源,并制定相应的控制措施,以确保生产出的药品符合质量标准,保障患者的用药安全。
本文将从质量风险评估的概念、评估方法和控制策略等方面展开探讨。
一、质量风险评估的概念质量风险评估是指在药品生产过程中,通过科学系统的方法识别、分析和评估可能对药品质量产生不利影响的因素。
它不仅包括生产环节中可能存在的风险,还涵盖了药品原材料的供应风险、药品贮存和运输过程中的风险等。
通过对这些潜在风险进行评估,可以有针对性地采取控制措施,降低质量风险的发生概率。
二、质量风险评估的方法1. 隐患分析法隐患分析法是一种常用的质量风险评估方法,它通过对生产过程中可能存在的隐患进行归纳、分析和评估,确定潜在的质量风险。
该方法主要包括以下步骤:(1)明确评估目标:确定质量风险评估的目标范围和重点,明确需要评估的流程或环节。
(2)收集数据:收集与评估目标相关的数据,包括相关文件、记录、采购来源等。
(3)隐患识别:分析收集到的数据,识别可能存在的潜在隐患。
(4)隐患评估:对识别出的隐患进行定性和定量评估,确定其对药品质量的风险程度。
(5)控制措施:制定相应的控制措施,降低或消除质量风险。
(6)风险再评估:在实施控制措施后,对质量风险进行再评估,评估措施的有效性。
2. 专家讨论法专家讨论法是一种集体智慧的评估方法,通过邀请相关领域的专家进行讨论和意见交流,共同评估质量风险。
该方法主要包括以下步骤:(1)确定讨论目标:明确评估的目标和范围,制定明确的讨论议题。
(2)邀请专家:邀请相关领域的专家参与讨论,确保参与者具备相关的专业知识和经验。
(3)讨论过程:组织专家进行讨论,充分发表各自观点,并形成共识。
(4)评估结果:根据专家的意见和共识,对质量风险进行评估,并制定相应的控制措施。
(5)风险再评估:在实施控制措施后,对质量风险进行再评估,评估措施的有效性。
药品生产安全风险评估

药品生产安全风险评估
药品生产安全风险评估是指对药品生产过程中可能存在的各种安全风险进行评估和分析,以确定风险的严重程度,并采取相应的控制措施来降低风险发生的可能性和影响。
药品生产过程中可能存在的安全风险包括但不限于以下几个方面:
1. 原料和辅料的安全性风险:原料和辅料的质量不合格、含有有害物质或微生物污染等情况可能存在安全风险,可能导致药品的质量问题和不良反应。
2. 生产工艺和设备的安全风险:生产工艺和设备存在不合理、不稳定或不安全的设计,可能导致生产过程中的事故和事故风险,例如爆炸、火灾等。
3. 工人操作的安全风险:工人在生产过程中的操作不规范、缺乏培训和安全意识等问题可能导致事故和职业伤害的发生。
4. 管理和监督控制的安全风险:药品生产中缺乏有效的管理制度和监督控制措施,可能导致生产环境不合格、质量问题被忽视等情况发生。
为了对上述安全风险进行评估,可以采取以下步骤:
1. 风险识别和分类:对药品生产过程中可能存在的各类风险进行识别和分类,包括原料和辅料安全、生产工艺和设备安全、工人操作安全和管理控制安全等。
2. 风险评估和分析:对已识别的风险进行评估和分析,包括确定风险的严重程度、可能性和影响等因素,以便确定重点关注的风险。
3. 风险控制措施的制定:根据风险评估的结果,制定相应的风险控制措施,包括采取技术措施、管理措施和培训措施等,以降低风险发生的可能性和影响。
4. 风险监控和评估:实施控制措施后,需要对风险的监控和评估,以确定是否有效控制了风险,并及时对措施进行调整和改进。
最后,药品生产安全风险评估需要遵守相关的法律法规和标准,确保评估的准确性和可靠性,并及时报告和处理评估结果中发现的问题和风险。
药品生产企业的质量风险评估
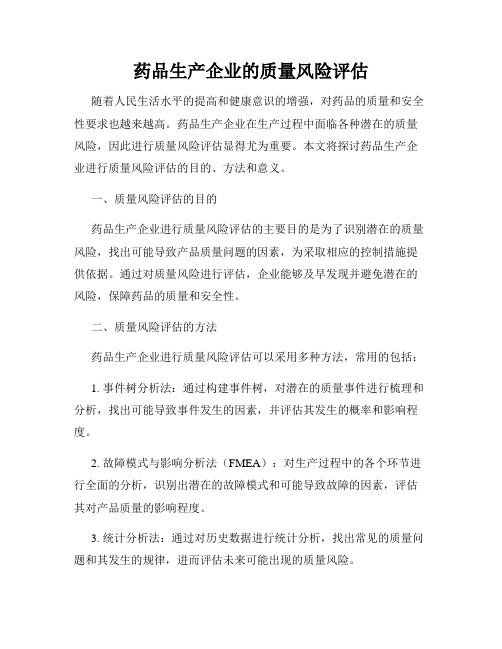
药品生产企业的质量风险评估随着人民生活水平的提高和健康意识的增强,对药品的质量和安全性要求也越来越高。
药品生产企业在生产过程中面临各种潜在的质量风险,因此进行质量风险评估显得尤为重要。
本文将探讨药品生产企业进行质量风险评估的目的、方法和意义。
一、质量风险评估的目的药品生产企业进行质量风险评估的主要目的是为了识别潜在的质量风险,找出可能导致产品质量问题的因素,为采取相应的控制措施提供依据。
通过对质量风险进行评估,企业能够及早发现并避免潜在的风险,保障药品的质量和安全性。
二、质量风险评估的方法药品生产企业进行质量风险评估可以采用多种方法,常用的包括:1. 事件树分析法:通过构建事件树,对潜在的质量事件进行梳理和分析,找出可能导致事件发生的因素,并评估其发生的概率和影响程度。
2. 故障模式与影响分析法(FMEA):对生产过程中的各个环节进行全面的分析,识别出潜在的故障模式和可能导致故障的因素,评估其对产品质量的影响程度。
3. 统计分析法:通过对历史数据进行统计分析,找出常见的质量问题和其发生的规律,进而评估未来可能出现的质量风险。
4. 专家评估法:邀请相关领域的专家进行评估,利用其经验和知识来识别潜在的质量风险,并评估其发生的可能性和影响程度。
三、质量风险评估的意义1. 风险预警:通过质量风险评估,企业能够及早识别潜在的风险,及时采取相应的预防措施,避免质量问题的发生,降低风险损失。
2. 资源优化:企业在质量控制和风险管理方面可以根据评估结果合理配置资源,优化生产过程,提高生产效率和质量水平。
3. 提升市场竞争力:药品市场竞争激烈,优质的产品更容易获得市场认可和消费者的信赖。
通过质量风险评估,企业能够提高产品的质量水平,增强市场竞争力。
4. 合规管理:随着监管政策的不断加强,企业需要确保自身的质量管理符合法规要求。
质量风险评估能够帮助企业发现潜在的合规风险,并采取相应的控制措施,确保生产过程的合规性。
药品生产过程质量风险评估报告模板
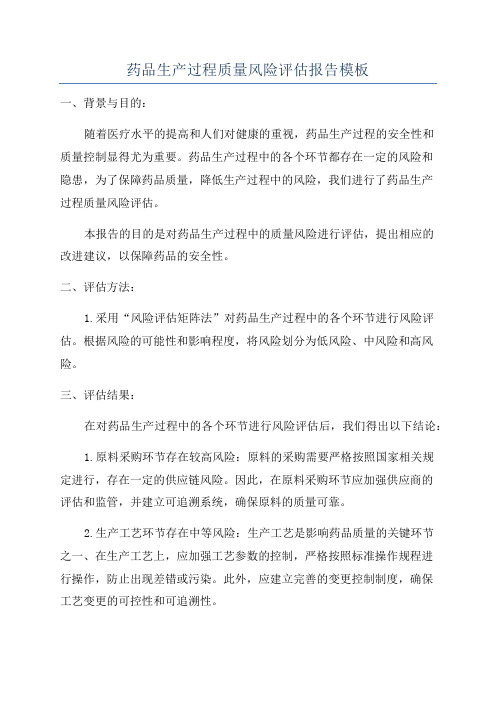
药品生产过程质量风险评估报告模板一、背景与目的:随着医疗水平的提高和人们对健康的重视,药品生产过程的安全性和质量控制显得尤为重要。
药品生产过程中的各个环节都存在一定的风险和隐患,为了保障药品质量,降低生产过程中的风险,我们进行了药品生产过程质量风险评估。
本报告的目的是对药品生产过程中的质量风险进行评估,提出相应的改进建议,以保障药品的安全性。
二、评估方法:1.采用“风险评估矩阵法”对药品生产过程中的各个环节进行风险评估。
根据风险的可能性和影响程度,将风险划分为低风险、中风险和高风险。
三、评估结果:在对药品生产过程中的各个环节进行风险评估后,我们得出以下结论:1.原料采购环节存在较高风险:原料的采购需要严格按照国家相关规定进行,存在一定的供应链风险。
因此,在原料采购环节应加强供应商的评估和监管,并建立可追溯系统,确保原料的质量可靠。
2.生产工艺环节存在中等风险:生产工艺是影响药品质量的关键环节之一、在生产工艺上,应加强工艺参数的控制,严格按照标准操作规程进行操作,防止出现差错或污染。
此外,应建立完善的变更控制制度,确保工艺变更的可控性和可追溯性。
3.检验检测环节存在较低风险:检验检测环节是保障药品质量的最后一道防线。
在检验检测环节,应加强仪器设备的维护和校准,确保结果的准确性。
此外,应制定完善的检验检测标准和方法,以确保检验结果的可靠性。
四、改进建议:基于对药品生产过程质量风险的评估结果,我们提出以下改进建议:1.建立健全原料采购管理制度,加强供应商的评估和监管。
2.加强生产工艺的控制,严格按照标准操作规程进行操作。
3.建立完善的变更控制制度,确保工艺变更的可控性和可追溯性。
4.加强仪器设备的维护和校准,制定完善的检验检测标准和方法。
5.定期进行内部审计和风险评估,及时发现和解决潜在的质量风险。
六、结论:通过对药品生产过程质量风险的评估,我们找出了存在的问题和风险,并提出了相应的改进建议。
只有加强对药品生产过程质量的管理和监控,才能降低质量风险,确保药品的安全性。
药品质量风险的评估报告
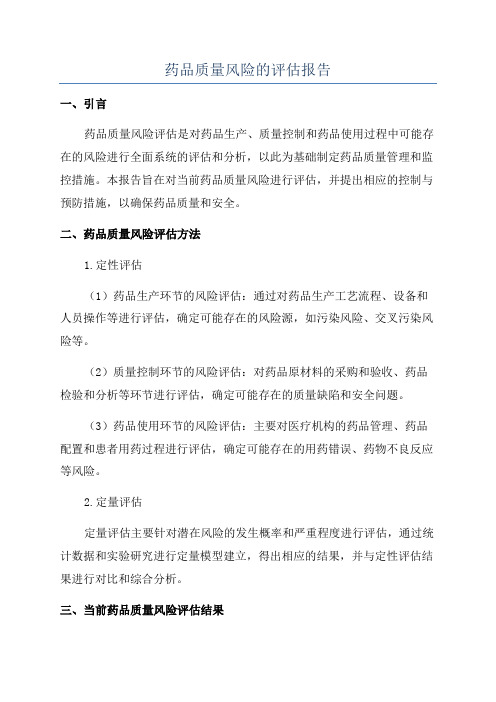
药品质量风险的评估报告一、引言药品质量风险评估是对药品生产、质量控制和药品使用过程中可能存在的风险进行全面系统的评估和分析,以此为基础制定药品质量管理和监控措施。
本报告旨在对当前药品质量风险进行评估,并提出相应的控制与预防措施,以确保药品质量和安全。
二、药品质量风险评估方法1.定性评估(1)药品生产环节的风险评估:通过对药品生产工艺流程、设备和人员操作等进行评估,确定可能存在的风险源,如污染风险、交叉污染风险等。
(2)质量控制环节的风险评估:对药品原材料的采购和验收、药品检验和分析等环节进行评估,确定可能存在的质量缺陷和安全问题。
(3)药品使用环节的风险评估:主要对医疗机构的药品管理、药品配置和患者用药过程进行评估,确定可能存在的用药错误、药物不良反应等风险。
2.定量评估定量评估主要针对潜在风险的发生概率和严重程度进行评估,通过统计数据和实验研究进行定量模型建立,得出相应的结果,并与定性评估结果进行对比和综合分析。
三、当前药品质量风险评估结果根据定性和定量评估的结果,得出以下结论:1.药品生产环节的风险:存在一定程度的污染风险和交叉污染风险,主要由于工艺流程不规范、设备维护不良、人员操作不规范等原因引起。
3.药品使用环节的风险:医疗机构药品管理和患者用药过程中存在用药错误和药物不良反应的风险,主要是由于医疗机构的管理制度不健全、患者用药不规范等原因引起。
四、控制与预防措施基于以上评估结果,提出以下控制与预防措施:1.药品生产环节的控制与预防措施:加强工艺流程规范化与标准化管理,保证设备的正常运行和维护,加强人员培训与管理,确保操作规范和安全。
2.质量控制环节的控制与预防措施:建立更加严格的原材料采购和验收标准,加强对供应商的监管和审核,确保原材料的质量安全。
3.药品使用环节的控制与预防措施:完善医疗机构的药品管理制度,加强患者用药指导与监护,减少用药错误和药物不良反应的发生。
五、结论药品质量风险评估是有效控制和预防药品质量问题的重要手段,通过定性和定量相结合的方法,能够全面分析和评估药品生产、质量控制和药品使用过程中可能存在的风险。
药品共线生产风险评估报告
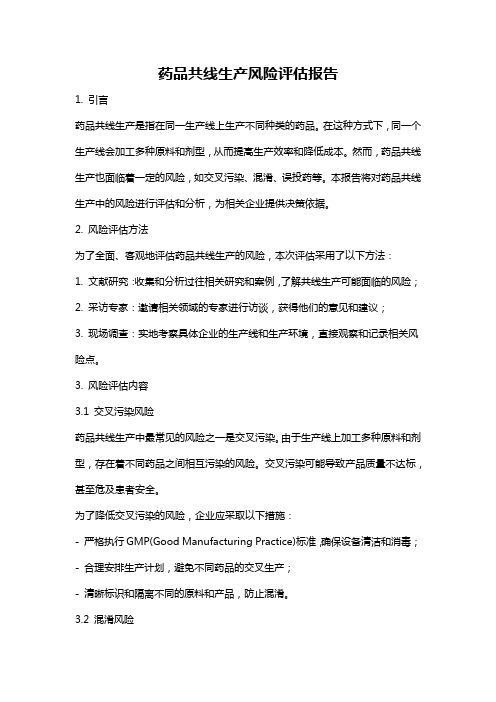
药品共线生产风险评估报告1. 引言药品共线生产是指在同一生产线上生产不同种类的药品。
在这种方式下,同一个生产线会加工多种原料和剂型,从而提高生产效率和降低成本。
然而,药品共线生产也面临着一定的风险,如交叉污染、混淆、误投药等。
本报告将对药品共线生产中的风险进行评估和分析,为相关企业提供决策依据。
2. 风险评估方法为了全面、客观地评估药品共线生产的风险,本次评估采用了以下方法:1. 文献研究:收集和分析过往相关研究和案例,了解共线生产可能面临的风险;2. 采访专家:邀请相关领域的专家进行访谈,获得他们的意见和建议;3. 现场调查:实地考察具体企业的生产线和生产环境,直接观察和记录相关风险点。
3. 风险评估内容3.1 交叉污染风险药品共线生产中最常见的风险之一是交叉污染。
由于生产线上加工多种原料和剂型,存在着不同药品之间相互污染的风险。
交叉污染可能导致产品质量不达标,甚至危及患者安全。
为了降低交叉污染的风险,企业应采取以下措施:- 严格执行GMP(Good Manufacturing Practice)标准,确保设备清洁和消毒;- 合理安排生产计划,避免不同药品的交叉生产;- 清晰标识和隔离不同的原料和产品,防止混淆。
3.2 混淆风险除了交叉污染,药品共线生产还存在混淆的风险。
由于生产线上可能同时存在多种不同的原料和产品,操作人员易混淆不同种类的药品,导致加工错误。
为了降低混淆的风险,企业应采取以下措施:- 严格执行SOP(Standard Operating Procedure),确保操作人员清楚和准确理解操作流程;- 提供明确的标识和包装,减少混淆可能性;- 进行员工培训,加强操作人员的技能和责任意识。
3.3 误投药风险在药品共线生产中,误投药也是一个较为严重的风险。
误投药指的是将某种药品错误地添加到另一种药品中,从而导致错误的成品。
为了降低误投药的风险,企业应采取以下措施:- 设立严格的质量控制体系,对原料、半成品和成品进行严格检验和验证;- 对每个工序进行仔细核对和确认;- 加强员工培训,提高员工的注意力和细致度。
药品生产企业风险评估报告
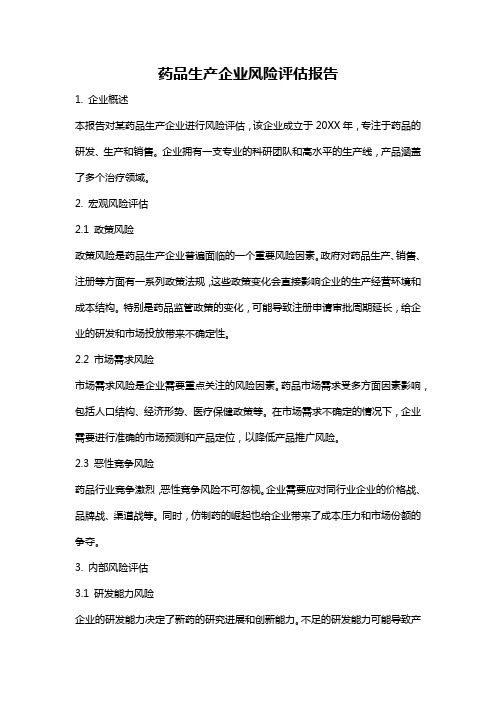
药品生产企业风险评估报告1. 企业概述本报告对某药品生产企业进行风险评估,该企业成立于20XX年,专注于药品的研发、生产和销售。
企业拥有一支专业的科研团队和高水平的生产线,产品涵盖了多个治疗领域。
2. 宏观风险评估2.1 政策风险政策风险是药品生产企业普遍面临的一个重要风险因素。
政府对药品生产、销售、注册等方面有一系列政策法规,这些政策变化会直接影响企业的生产经营环境和成本结构。
特别是药品监管政策的变化,可能导致注册申请审批周期延长,给企业的研发和市场投放带来不确定性。
2.2 市场需求风险市场需求风险是企业需要重点关注的风险因素。
药品市场需求受多方面因素影响,包括人口结构、经济形势、医疗保健政策等。
在市场需求不确定的情况下,企业需要进行准确的市场预测和产品定位,以降低产品推广风险。
2.3 恶性竞争风险药品行业竞争激烈,恶性竞争风险不可忽视。
企业需要应对同行业企业的价格战、品牌战、渠道战等。
同时,仿制药的崛起也给企业带来了成本压力和市场份额的争夺。
3. 内部风险评估3.1 研发能力风险企业的研发能力决定了新药的研究进展和创新能力。
不足的研发能力可能导致产品种类单一、创新不足。
企业应加强科研团队建设,提高研发能力,降低技术风险。
3.2 生产质量风险药品生产质量是企业的生命线,存在质量风险将直接损害企业的声誉和市场地位。
企业应严格遵守生产管理规范,提高产品质量,减少质量事故的可能性。
3.3 营销渠道风险企业的销售渠道和市场拓展能力对药品销售起着至关重要的作用。
如果渠道布局不合理或者销售能力不足,将导致销售额下滑和市场份额的损失。
企业应建立稳定的销售渠道和网络,提高市场份额。
4. 风险应对策略4.1 多样化研发产品企业应加大研发投入,拓宽产品线,不依赖单一产品,降低市场需求风险和恶性竞争风险。
同时,加强与科研机构的合作,提高创新能力。
4.2 建立质量管理体系企业应建立完善的生产质量管理体系,严格按照药品生产质量管理规范要求进行生产,确保产品质量,减少质量风险和企业声誉损失。
GMP-风险评估

GMP-风险评估一、引言随着制药行业的发展,药品生产质量管理规范(GMP)已经成为确保药品质量和安全的重要手段。
风险评估作为GMP的重要组成部分,旨在识别、评估和管理药品生产过程中的各种风险,从而提高药品的安全性和有效性。
本文将详细介绍GMP-风险评估的相关内容,包括风险评估流程、方法、人员培训与资质以及实施建议等方面。
二、风险评估流程风险识别:识别药品生产过程中可能出现的风险因素,如设备故障、原材料质量不稳定等。
风险评估:对识别出的风险因素进行定性和定量评估,确定其可能对药品质量和安全产生的影响。
风险控制:根据风险评估结果,制定相应的控制措施,降低或消除风险。
风险监控:对控制措施的实施情况进行监控,确保其有效性和持续性。
风险回顾:定期对风险评估结果进行回顾,更新风险数据库,提高风险评估的准确性和有效性。
三、风险评估方法故障模式与影响分析(FMEA):通过分析潜在的故障模式及其对系统的影响,确定优先控制的风险因素。
风险矩阵:将风险因素按照发生的可能性和后果严重程度进行分类,确定相应的控制措施。
风险指数:通过综合考虑风险因素的发生概率、后果严重程度和可控制性等因素,计算出风险指数,从而确定相应的控制措施。
事件树分析:通过对事件发展过程的模拟和分析,确定可能导致事故发生的各阶段和因素,制定相应的预防措施。
故障树分析:通过分析系统故障的逻辑关系,找出导致故障的原因和因素,制定相应的预防措施。
四、人员培训与资质培训内容:培训员工GMP-风险评估的相关知识和技能,包括但不限于风险评估流程、方法以及相关的管理工具和软件等。
培训形式:采用线上和线下相结合的方式进行培训,包括理论授课、案例分析、实践操作等形式。
资质要求:参与GMP-风险评估的人员应具备相应的专业知识和经验,具备相应的资质证书或经过专业培训。
培训考核:对参与培训的人员进行考核,确保其掌握相关的知识和技能,符合要求的人员可参与GMP-风险评估工作。
药品生产企业的质量风险评估与防控
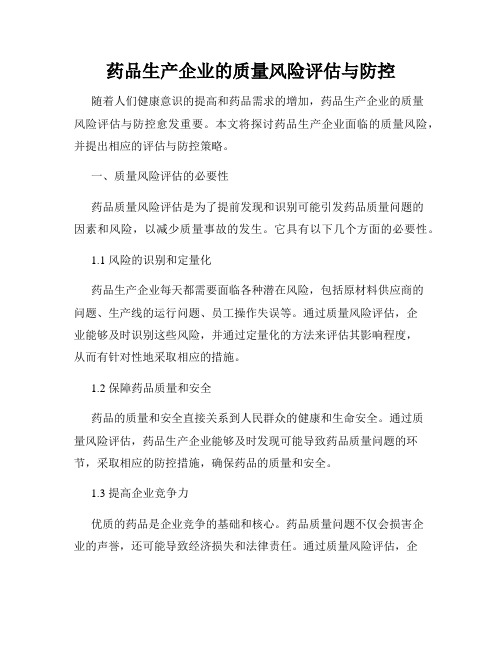
药品生产企业的质量风险评估与防控随着人们健康意识的提高和药品需求的增加,药品生产企业的质量风险评估与防控愈发重要。
本文将探讨药品生产企业面临的质量风险,并提出相应的评估与防控策略。
一、质量风险评估的必要性药品质量风险评估是为了提前发现和识别可能引发药品质量问题的因素和风险,以减少质量事故的发生。
它具有以下几个方面的必要性。
1.1 风险的识别和定量化药品生产企业每天都需要面临各种潜在风险,包括原材料供应商的问题、生产线的运行问题、员工操作失误等。
通过质量风险评估,企业能够及时识别这些风险,并通过定量化的方法来评估其影响程度,从而有针对性地采取相应的措施。
1.2 保障药品质量和安全药品的质量和安全直接关系到人民群众的健康和生命安全。
通过质量风险评估,药品生产企业能够及时发现可能导致药品质量问题的环节,采取相应的防控措施,确保药品的质量和安全。
1.3 提高企业竞争力优质的药品是企业竞争的基础和核心。
药品质量问题不仅会损害企业的声誉,还可能导致经济损失和法律责任。
通过质量风险评估,企业能够及时发现和解决潜在的质量问题,提高产品质量和合规性,提升企业的竞争力。
二、质量风险评估与防控的方法2.1 引入风险管理体系药品生产企业应引入风险管理体系,建立科学的质量管理体系并与其错综复杂的业务流程相结合。
通过风险管理体系,企业能够全面了解各个环节的风险,采取相应的管理和防控措施。
2.2 采用风险评估工具药品生产企业可以使用各种风险评估工具,如故障模式与影响分析(FMEA)、故障树分析(FTA)等,对各种潜在的质量风险进行评估和分析。
评估工具的选择应根据具体情况和需求进行,并与企业的风险管理体系相衔接。
2.3 培养高素质员工员工是企业质量管理的重要一环,应通过培训和考核等方式提高员工的素质和技能。
同时,企业应建立激励机制,激励员工积极参与质量风险的评估与防控工作。
2.4 建立完善的供应商管理体系药品生产企业需要与优质的供应商建立长期稳定的合作关系,并建立供应商质量管理体系。
药品安全质量风险评估

药品安全质量风险评估
药品安全质量风险评估是指对药品生产、贮存、运输、销售和使用过程中可能存在的安全质量风险进行全面评估和分析的过程。
其目的是为了发现潜在的风险因素,预防和控制药品质量安全问题的发生,保障患者用药的安全性和有效性。
药品安全质量风险评估主要包括以下几个方面:
1. 原料药的质量风险评估:对原料药的来源、质量指标、生产工艺和质量管理进行评估,确定可能存在的质量风险因素。
2. 制剂工艺的质量风险评估:对制剂工艺的设计和操作流程进行评估,确定可能存在的质量风险,如工艺控制不合理、生产环境不洁净等。
3. 药品稳定性的质量风险评估:对药品的稳定性进行评估,确定药品在贮存和使用过程中可能遇到的质量问题。
4. 药品包装和标签的质量风险评估:对药品包装和标签的合规性和可靠性进行评估,确定可能存在的安全质量问题。
5. 药品配送和销售的质量风险评估:对药品配送、销售和使用环节进行评估,确定可能存在的质量风险,如温度控制不当、药品交叉污染等。
通过对药品安全质量风险的评估,可以有效地识别和分析潜在
的风险因素,采取相应的预防和控制措施,确保药品质量的安全性和有效性,最终提高患者用药的安全水平。
药品生产过程中的质量风险评估与控制效果评估

药品生产过程中的质量风险评估与控制效果评估药品的质量是保障患者用药安全和有效的重要因素之一。
因此,在药品生产过程中进行质量风险评估和控制效果评估显得尤为重要。
本文将介绍药品生产过程中的质量风险评估和控制效果评估的相关内容。
一、质量风险评估质量风险评估是指通过对药品生产过程中可能存在的质量问题进行全面分析和评估,确定风险的程度和影响因素,并制定相应的控制策略。
质量风险评估包括以下几个方面:1.风险辨识:识别药品生产过程中可能引发质量问题的因素和环节,比如原材料的质量、工艺参数的控制、操作人员的技术水平等。
2.风险分析:对辨识出的风险因素进行量化分析,确定其可能引发的质量问题的概率和严重程度。
3.风险评估:综合考虑风险的概率和严重程度,对各个风险因素进行评估,并确定优先处理的风险。
4.风险控制策略:制定针对不同风险的控制措施,包括质量控制标准的制定、工艺参数的优化、操作规范的制定等。
通过质量风险评估,药品生产企业可以全面了解生产过程中可能存在的质量问题,并采取相应的措施进行控制,提高产品质量和安全性。
二、控制效果评估控制效果评估是指对质量风险控制措施的实施效果进行评估,判断是否达到预期的质量控制目标。
控制效果评估包括以下几个方面:1.质量指标评估:通过对药品质量指标进行监测和分析,判断是否符合质量控制目标。
2.过程监控:对生产过程进行实时监测和记录,及时发现异常情况并采取相应的纠正措施。
3.质量控制标准评估:评估质量控制标准的合理性和有效性,是否能够真正起到控制质量的作用。
4.风险回顾:定期对质量风险评估结果进行回顾,评估质量控制措施的长期效果,并进行必要的调整和优化。
通过控制效果评估,药品生产企业可以及时了解质量控制措施的实施效果,并根据评估结果进行持续改进,确保产品质量的稳定性和可靠性。
结论药品生产过程中的质量风险评估和控制效果评估对于保障药品质量和患者用药安全具有重要意义。
通过科学的质量风险评估,可以识别和评估可能存在的质量风险,并制定相应的控制策略。
2024年度药品质量风险评估方案

一、背景介绍药品质量是关系到人民群众生命健康的重要问题,为了保障药品质量,社会各界对药品质量风险进行评估具有重要意义。
本文将就2024年度药品质量风险评估方案进行详细阐述。
二、评估目标本次评估的目标是全面了解2024年度国内药品市场的质量状况,发现潜在的风险,并提出改进建议,以提高药品质量和保障人民群众的用药安全。
三、评估内容1.收集数据:收集2024年度国内药品市场的质量数据,包括药品生产企业的注册情况、药品审批情况、药品抽检情况等。
2.数据分析:对收集到的数据进行统计和分析,包括药品质量合格率、不合格药品的种类和原因、不合格药品在市场上的流通情况等。
3.风险评估:综合考虑不同因素,评估药品质量风险,确定风险大小和影响范围,并分析风险的原因和潜在危害。
4.改进建议:针对评估结果,提出改进药品质量的具体措施和建议,包括加强药品生产监管、提高药品质量检验能力、完善药品质量监管体系等。
四、评估方法本次评估将采用定性和定量相结合的方法进行,主要包括以下几个方面:1.数据收集方法:通过收集药品相关数据、抽检报告、企业注册情况等,获取全面的评估数据。
2.数据分析方法:采用统计学和质量控制方法对数据进行分析,包括计算药品质量合格率、统计不合格药品的种类和原因等。
3.风险评估方法:通过对数据分析结果的综合考虑,结合相关法规标准进行风险评估。
4.改进建议方法:通过对评估结果的分析和讨论,提出具体的改进措施和建议,并进行可行性分析。
五、评估时间安排本次评估的时间安排如下:1.数据收集:2024年4月至2024年1月,持续9个月。
2.数据分析:2024年2月至4月,持续3个月。
3.风险评估:2024年5月至7月,持续3个月。
4.改进建议:2024年8月至10月,持续3个月。
六、评估成果与推广1.评估报告:根据评估结果撰写评估报告,进行内部审定后公布。
2.政策推广:将评估结果和改进建议向相关政府部门和药品生产企业进行推广,促进药品质量的提高和保障人民群众的用药安全。
药品监管中的药品生产质量风险评估案例分析方法探究与应用实例

药品监管中的药品生产质量风险评估案例分析方法探究与应用实例药品的生产质量一直是药品监管中一个重要的关注点,对于药品生产企业和监管机构来说,评估药品生产质量风险是确保药品质量安全的一项重要措施。
本文将探究和应用一种药品生产质量风险评估的案例分析方法,并提供实际应用实例。
一、药品生产质量风险评估方法药品生产质量风险评估方法有多种,其中一种常用的方法是风险矩阵分析法。
该方法通过对药品生产过程中各个环节的风险进行评估,将风险按照可能性和严重性进行分类,并根据分类结果进行相应的控制措施。
在进行风险评估时,需要考虑的因素包括药品生产的环境条件、生产设备的可靠性、操作人员的培训水平、药品配方和生产工艺的合理性等。
通过对这些因素进行评估,可以确定出可能存在的风险点,并制定相应的风险控制措施。
二、药品生产质量风险评估应用实例以某药品生产企业为例,该企业生产的一种药品被发现有一定的质量问题,需要对生产质量进行评估,并提出相应的风险控制措施。
1. 环境条件评估首先,对该企业的生产车间环境进行评估。
通过实地考察和数据收集,发现车间的温湿度控制不稳定,容易影响药品生产的质量。
因此,可以将这一环节的风险等级确定为中等。
2. 生产设备评估其次,评估生产设备的可靠性。
该企业的部分生产设备存在故障率较高的情况,可能对药品生产的质量造成一定影响。
因此,将生产设备的风险等级评定为较高。
3. 操作人员评估进一步,对操作人员的培训水平进行评估。
通过与操作人员的交流和培训记录的查阅,发现一些操作人员的培训水平不够,可能会存在操作不规范的情况。
因此,将操作人员的风险等级评定为中等。
4. 药品配方和生产工艺评估最后,对药品配方和生产工艺进行评估。
通过对配方和工艺文件的审查,发现部分车间的配方和工艺存在不合理之处,可能对药品的质量稳定性造成影响。
因此,将药品配方和生产工艺的风险等级评定为高。
根据以上的风险评估结果,该企业可以制定相应的风险控制措施,如优化生产环境控制手段、加强生产设备维护和检修、提高操作人员的培训水平、优化药品配方和生产工艺等。
药品生产企业的质量风险评估
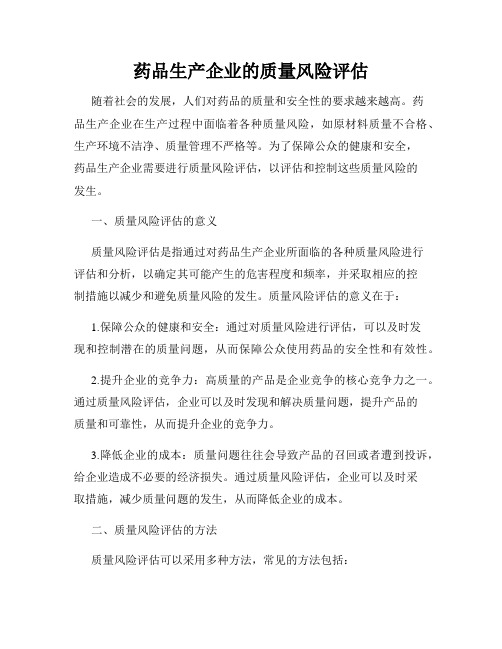
药品生产企业的质量风险评估随着社会的发展,人们对药品的质量和安全性的要求越来越高。
药品生产企业在生产过程中面临着各种质量风险,如原材料质量不合格、生产环境不洁净、质量管理不严格等。
为了保障公众的健康和安全,药品生产企业需要进行质量风险评估,以评估和控制这些质量风险的发生。
一、质量风险评估的意义质量风险评估是指通过对药品生产企业所面临的各种质量风险进行评估和分析,以确定其可能产生的危害程度和频率,并采取相应的控制措施以减少和避免质量风险的发生。
质量风险评估的意义在于:1.保障公众的健康和安全:通过对质量风险进行评估,可以及时发现和控制潜在的质量问题,从而保障公众使用药品的安全性和有效性。
2.提升企业的竞争力:高质量的产品是企业竞争的核心竞争力之一。
通过质量风险评估,企业可以及时发现和解决质量问题,提升产品的质量和可靠性,从而提升企业的竞争力。
3.降低企业的成本:质量问题往往会导致产品的召回或者遭到投诉,给企业造成不必要的经济损失。
通过质量风险评估,企业可以及时采取措施,减少质量问题的发生,从而降低企业的成本。
二、质量风险评估的方法质量风险评估可以采用多种方法,常见的方法包括:1.风险识别:通过对药品生产企业生产过程中可能存在的质量风险进行识别和分析,明确风险的来源和可能导致的后果。
2.风险评估:对已识别的质量风险进行评估,确定其可能发生的概率和可能产生的危害程度。
评估的方法可以采用定性评估和定量评估相结合的方式,综合考虑风险的大小。
3.风险控制:对评估得出的高风险质量问题,制定相应的控制措施,以减少和避免质量风险的产生。
控制措施可以包括改进生产工艺、提升原材料检验标准、完善质量管理体系等。
三、质量风险评估的挑战进行质量风险评估时,药品生产企业可能面临以下挑战:1.数据不足:质量风险评估需要大量的数据支持,包括生产过程数据、原材料质量数据等。
但是有些数据可能难以获取,或者企业内部对数据的管理不规范,导致评估的结果不准确。
药品生产质量管理中的质量风险评估方法研究
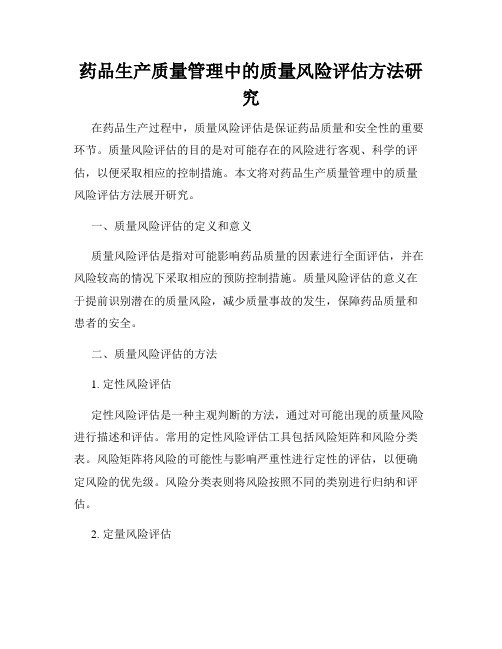
药品生产质量管理中的质量风险评估方法研究在药品生产过程中,质量风险评估是保证药品质量和安全性的重要环节。
质量风险评估的目的是对可能存在的风险进行客观、科学的评估,以便采取相应的控制措施。
本文将对药品生产质量管理中的质量风险评估方法展开研究。
一、质量风险评估的定义和意义质量风险评估是指对可能影响药品质量的因素进行全面评估,并在风险较高的情况下采取相应的预防控制措施。
质量风险评估的意义在于提前识别潜在的质量风险,减少质量事故的发生,保障药品质量和患者的安全。
二、质量风险评估的方法1. 定性风险评估定性风险评估是一种主观判断的方法,通过对可能出现的质量风险进行描述和评估。
常用的定性风险评估工具包括风险矩阵和风险分类表。
风险矩阵将风险的可能性与影响严重性进行定性的评估,以便确定风险的优先级。
风险分类表则将风险按照不同的类别进行归纳和评估。
2. 定量风险评估定量风险评估是一种基于数据和统计方法进行的风险评估方法。
通过收集和分析大量的数据,计算出风险事件发生的概率、影响程度和相关的损失,以便确定风险的大小和优先级。
常用的定量风险评估方法包括事件树分析、故障模式和影响分析、贝叶斯网络分析等。
3. 隐患排查方法隐患排查是通过对生产环节存在的隐患进行全面排查和评估,以便减少事故发生的可能性。
常用的隐患排查方法包括层次分析法、事故现场模拟和模型检测等。
三、质量风险评估的关键要素1. 风险识别风险识别是质量风险评估的第一步,需要通过对生产过程、设备和人员等进行全面的调查和观察,识别出可能存在的风险点。
2. 风险评估风险评估是根据识别出的风险点,对其可能性、影响程度和相关损失进行评估,以便确定风险的优先级和采取相应的控制措施。
3. 风险控制风险控制是在风险评估的基础上,采取相应的控制措施或制定相应的标准和规范,以减少风险发生的可能性和影响程度。
四、质量风险评估的应用案例以某药品生产企业为例,通过对其生产环节进行质量风险评估,发现若干存在的问题和风险。
- 1、下载文档前请自行甄别文档内容的完整性,平台不提供额外的编辑、内容补充、找答案等附加服务。
- 2、"仅部分预览"的文档,不可在线预览部分如存在完整性等问题,可反馈申请退款(可完整预览的文档不适用该条件!)。
- 3、如文档侵犯您的权益,请联系客服反馈,我们会尽快为您处理(人工客服工作时间:9:00-18:30)。
附件4:风险评估报告格式
×××市(州)药品生产企业××××年度风险评估报告
一、药品生产企业概况
药品生产企业数量(生产、停产);批准文号数量、常年生产的品种数量,本年度上报注册申请(含补充申请)数量,新取得批准文号数量以及分布、注册分类情况;许可证换发、变更情况;监督备案情况;委(受)托生产和检验情况;药品质量安全情况(产品偏差及处理,产品回收、退货及处理,以及质量投诉及不良反应监测情况);经济发展指标数据(生产产值、销售收入、利税、增长率统计汇总数据,销售上千万元和上亿元的单个品种情况)
二、生产企业监管情况
1、安全监管信息(GMP认证、跟踪检查、飞行检查、专项检查、日常监督检查、驻厂监督检查等情况,发现的缺陷项目情况,信用等级初评情况,开展培训情况,药品稽查情况);
2、药品质量信息(评价性抽检、监督抽验情况);
三、风险分析评估及结论(药品生产企业存在主要问题、成因分析以及采取的措施,下一步监管工作建议)。
×××市州食品药品监督管理局(公章)
××××年××月××日
风险评估过程注意事项
在风险评估过程中,有几个关键的问题需要考虑。
首先,要确定保护的对象(或者资产)是什么?它的直接和间接价值如何?
其次,资产面临哪些潜在威胁?导致威胁的问题所在?威胁发生的可能性有多大?
第三,资产中存在哪里弱点可能会被威胁所利用?利用的容易程度又如何?
第四,一旦威胁事件发生,组织会遭受怎样的损失或者面临怎样的负面影响?
最后,组织应该采取怎样的安全措施才能将风险带来的损失降低到最低程度?
解决以上问题的过程,就是风险评估的过程。
进行风险评估时,有几个对应关系必须考虑:
每项资产可能面临多种威胁
威胁源(威胁代理)可能不止一个
每种威胁可能利用一个或多个弱点
风险评估的三种可行途径
在风险管理的前期准备阶段,组织已经根据安全目标确定了自己的安全战略,其中就包括对风险评估战略的考虑。
所谓风险评估战略,其实就是进行风险评估的途径,也就是规定风险评估应该延续的操作过程和方式。
风险评估的操作范围可以是整个组织,也可以是组织中的某一部门,或者独立的信息系统、特定系统组件和服务。
影响风险评估进展的某些因素,包括评估时间、力度、展开幅度和深度,都应与组织的环境和安全要求相符合。
组织应该针对不同的情况来选择恰当的风险评估途径。
目前,实际工作中经常使用的风险评估途径包括基线评估、详细评估和组合评估三种。
基线评估
如果组织的商业运作不是很复杂,并且组织对信息处理和网络的依赖程度不是很高,或者组织信息系统多采用普遍且标准化的模式,基线风险评估(Baseline Risk Assessment)就可以直接而简单地实现基本的安全水平,并且满足组织及其商业环境的所有要求。
采用基线风险评估,组织根据自己的实际情况(所在行业、业务环境与性质等),对信息系统进行安全基线检查(拿现有的安全措施与安全基线规定的措施进行比较,找出其中的差距),得出基本的安全需求,通过选择并实施标准的安全措施来消减和控制风险。
所谓的安全基线,是在诸多标准规范中规定的一组安全控制措施或者惯例,这些措施和惯例适用于特定环境下的所有系统,可以满足基本的安全需求,能使系统达到一定的安全防护水平。
组织可以根据以下资源来选择安全基线:
国际标准和国家标准,例如BS 7799-1、ISO 13335-4;
行业标准或推荐,例如德国联邦安全局IT 基线保护手册;
来自其他有类似商务目标和规模的组织的惯例。
当然,如果环境和商务目标较为典型,组织也可以自行建立基线。
基线评估的优点是需要的资源少,周期短,操作简单,对于环境相似且安全需求相当的诸多组织,基线评估显然是最经济有效的风险评估途径。
当然,基线评估也有其难以避免的缺点,比如基线水平的高低难以设定,如果过高,可能导致资源浪费和限制过度,如果过低,可能难以达到充分的安全,此外,在管理安全相关的变化方面,基线评估比较困难。
基线评估的目标是建立一套满足信息安全基本目标的最小的对策集合,它可以在全组织范围内实行,如果有特殊需要,应该在此基础上,对特定系统进行更详细的评估。
详细评估
详细风险评估要求对资产进行详细识别和评价,对可能引起风险的威胁和弱点水平进行评估,根据风险评估的结果来识别和选择安全措施。
这种评估途径集中体现了风险管理的思想,即识别资产的风险并将风险降低到可接受的水平,以此证明管理者所采用的安全控制措施是恰当的。
详细评估的优点在于:
1、组织可以通过详细的风险评估而对信息安全风险有一个精确的认识,并且准确定义出组织目前的安全水平和安全需求;
2、详细评估的结果可用来管理安全变化。
当然,详细的风险评估可能是非常耗费资源的过程,包括时间、精力和技术,因此,组织应该仔细设定待评估的信息系统范围,明确商务环境、操作和信息资产的边界。
组合评估
基线风险评估耗费资源少、周期短、操作简单,但不够准确,适合一般环境的评估;详细风险评估准确而细致,但耗费资源较多,适合严格限定边界的较小范围内的评估。
基于次实践当中,组织多是采用二者结合的组合评估方式。
为了决定选择哪种风险评估途径,组织首先对所有的系统进行一次初步的高级风险评估,着眼于信息系统的商务价值和可能面临的风险,识别出组织内具有高风险的或者对其商务运作极为关键的信息资产(或系统),这些资产或系统应该划入详细风险评估的范围,而其他系统则可以通过基线风险评估直接选择安全措施。
这种评估途径将基线和详细风险评估的优势结合起来,既节省了评估所耗费的资源,又能确保获得一个全面系统的评估结果,而且,组织的资源和资金能够应用到最能发挥作用的地方,具有高风险的信息系统能够被预先关注。
当然,组合评估也有缺点:如果初步的高级风险评估不够准确,某些本来需要详细评估的系统也许会被忽略,最终导致结果失准。
编辑本段风险评估的常用方法
在风险评估过程中,可以采用多种操作方法,包括基于知识(Knowledge-based)的分析方法、基于模型(Model-based)的分析方法、定性(Qualitative)分析和定量(Quantitative)分析,无论何种方法,共同的目标都是找出组织信息资产面临的风险及其影响,以及目前安全水平与组织安全需求之间的差距。
基于知识的分析方法
在基线风险评估时,组织可以采用基于知识的分析方法来找出目前的安全状况和基线安全标准之间的差距。
基于知识的分析方法又称作经验方法,它牵涉到对来自类似组织(包括规模、商务目标和市场等)的“最佳惯例”的重用,适合一般性的信息安全社团。
采用基于知识的分析方法,组织不需要付出很多精力、时间和资源,只要通过多种途径采集相关信息,识别组织的风险所在和当前的安全措施,与特定的标准或最佳惯例进行比较,从中找出不符合的地方,并按照标准或最佳惯例的推荐选择安全措施,最终达到消减和控制风险的目的。