丁基橡胶氮气氛围下的最大热分解温度
不同补强剂增强HNBR复合材料的结构和性能

王小萍等.不同补强剂增强m喝R复合材料的结构和性能
圈1不同补强剂增强HNBR硫化胶的TEM图
2.3lDmR复合材料TGA分析
图2和表2是不同补强剂增强的Ⅷ临R硫化胶在氮气和空气氛围下的TGA图及其数据。
常规填料炭黑,白炭黑增强m旧R硫化胶在氮气和空气氛围中的起始分解温度和最大分解温度都得到较大幅度提高,白炭黑比炭黑补强的硫化胶在两种气体氛围中的最大分解温度均高6℃左右,这说明白碳黑耐热性能优于炭黑。
有机蒙脱土增强m临R硫化胶与空白样相比,在氮气和空气氛围中的起始分解温度都明显要低,而最大分解温度分别提高了14。
C和160C,与白炭黑补强m临R硫化胶的最大分解温度接近。
而且,与同样分量没有改性的蒙脱土相比,在氮气氛围和空气氛围下最大分解温度也分别提高了20C和190C。
zDMA补强HNBR硫化胶在氮气和空气中的最大分解温度比空白样明显提高,而在空气氛围中的起始分解温度均低于空白样,这是因为不饱和羧酸盐在高温空气氛围中不稳定,容易分解。
从上面的TGA数据与表2中m婚R硫化胶热空气老化性能对照发现,不同补强剂增强m临R硫化胶的热空气老化性能和热稳定性不一致。
我们认为这是由于常规填料,蒙脱土和不饱和羧酸盐三种不同补强剂增强}玎NBR硫化胶的热分解机理不一样导致的,这一点作者将在另外一篇论文中进一步阐述[131。
这也说明TGA不能完全准确表征不同分解机理的聚合物材料的热稳定性和老化性能。
蓬
盖
墨
Temperature/。
C
图2不同补强剂增强HNBR硫化胶在氮气(10。
c,min)和空气(20。
c,mjn)的TG图・。
常用橡胶的品种及使用温度
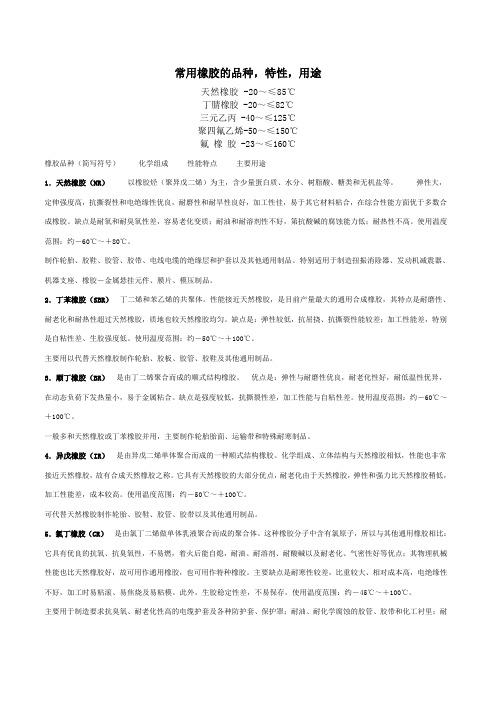
常用橡胶的品种,特性,用途天然橡胶 -20~≤85℃丁腈橡胶 -20~≤82℃三元乙丙 -40~≤125℃聚四氟乙烯-50~≤150℃氟橡胶 -23~≤160℃橡胶品种(简写符号)化学组成性能特点主要用途1.天然橡胶(NR)以橡胶烃(聚异戊二烯)为主,含少量蛋白质、水分、树脂酸、糖类和无机盐等。
弹性大,定伸强度高,抗撕裂性和电绝缘性优良,耐磨性和耐旱性良好,加工性佳,易于其它材料粘合,在综合性能方面优于多数合成橡胶。
缺点是耐氧和耐臭氧性差,容易老化变质;耐油和耐溶剂性不好,第抗酸碱的腐蚀能力低;耐热性不高。
使用温度范围:约-60℃~+80℃。
制作轮胎、胶鞋、胶管、胶带、电线电缆的绝缘层和护套以及其他通用制品。
特别适用于制造扭振消除器、发动机减震器、机器支座、橡胶-金属悬挂元件、膜片、模压制品。
2.丁苯橡胶(SBR)丁二烯和苯乙烯的共聚体。
性能接近天然橡胶,是目前产量最大的通用合成橡胶,其特点是耐磨性、耐老化和耐热性超过天然橡胶,质地也较天然橡胶均匀。
缺点是:弹性较低,抗屈挠、抗撕裂性能较差;加工性能差,特别是自粘性差、生胶强度低。
使用温度范围:约-50℃~+100℃。
主要用以代替天然橡胶制作轮胎、胶板、胶管、胶鞋及其他通用制品。
3.顺丁橡胶(BR)是由丁二烯聚合而成的顺式结构橡胶。
优点是:弹性与耐磨性优良,耐老化性好,耐低温性优异,在动态负荷下发热量小,易于金属粘合。
缺点是强度较低,抗撕裂性差,加工性能与自粘性差。
使用温度范围:约-60℃~+100℃。
一般多和天然橡胶或丁苯橡胶并用,主要制作轮胎胎面、运输带和特殊耐寒制品。
4.异戊橡胶(IR)是由异戊二烯单体聚合而成的一种顺式结构橡胶。
化学组成、立体结构与天然橡胶相似,性能也非常接近天然橡胶,故有合成天然橡胶之称。
它具有天然橡胶的大部分优点,耐老化由于天然橡胶,弹性和强力比天然橡胶稍低,加工性能差,成本较高。
使用温度范围:约-50℃~+100℃。
丁腈橡胶/氯化丁基橡胶共混物的性能研究

团一C 使 得丁腈 橡 胶 具有 优 异 的耐 油 性 能 , N, 适 于 用作 耐油 橡 胶 制 品 。但一C 空 间位 阻 大 , N 使
丁腈橡 胶玻 璃化温 度较高 , 低温性 能较 差 ; 且分 而
XK一1O型双辊 开 炼机 : 京橡 塑 机 械厂 产 6 南
子 链 中有 不 饱 和 双 键 , 耐 高 温 性 能 也 较 差 。 其 ] 氯化 丁基 橡胶 ( I 是 丁基 橡 胶 的 氯化 产 物 , CI R) 具
本 文通 过 C I IR共混改性 NB 提高 NB 的 R, R
耐 热和低 温性能 , 在耐油性 变化 较小 时 , 到高低 得 温性 能较好 的耐 油 NB R制 品L ] 3 。 “
器仪 表 厂 产 品 ; yi7 P r e型动 态 力学 分 析 仪 : 国 s 美
P r i E me 公 司 产 品 。 ekn l r 14 试 样 制 备 .
橡胶 制 品 。
关键 词 :丁 腈橡 胶 ; 化 丁基 橡 胶 ; 混 物 ; 能 氯 共 性
中 图分 类 号 : 3 . ; Q 3 . TQ 3 3 7 T 3 3 6
文献 标 识 码 : A
文 章 编 号 : 0 5 3 7 ( 0 8 O — O 8O 1 O — l 4 2 O ) 6 0 2 一3
品 ; 脂 酸 : 津 市 苏 应 化 学 试 剂 厂 产 品 ; 老 剂 硬 天 防
胶 料各项 物理 性 能 均按 相 应 国家标 准 测 定 ;
D MA 曲线 在 动 态力 学 分 析 仪 上进 行 测 试 , 样 试
长 5 0 mm, 1 , 2mm , 度 范 围 一 5 ~ 宽 Omm 厚 温 0
丁 腈 橡 胶 ( R) 子 结 构 中 具 有 极 性 基 NB 分
【5A版】耐热橡胶介绍
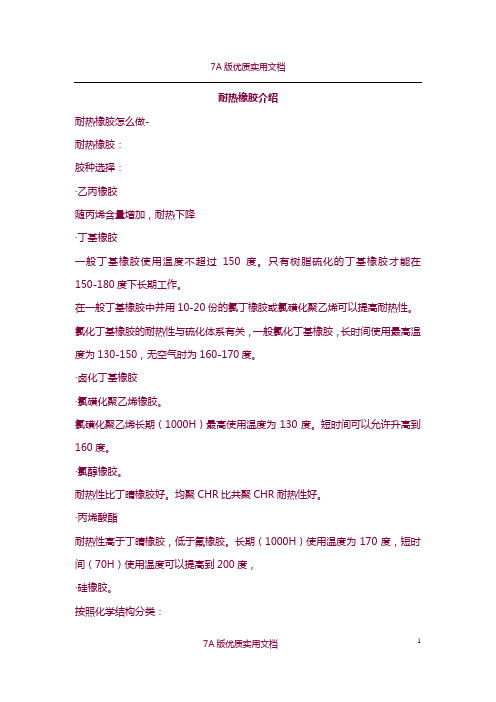
耐热橡胶介绍耐热橡胶怎么做-耐热橡胶:胶种选择:·乙丙橡胶随丙烯含量增加,耐热下降·丁基橡胶一般丁基橡胶使用温度不超过150度。
只有树脂硫化的丁基橡胶才能在150-180度下长期工作。
在一般丁基橡胶中并用10-20份的氯丁橡胶或氯磺化聚乙烯可以提高耐热性。
氯化丁基橡胶的耐热性与硫化体系有关,一般氯化丁基橡胶,长时间使用最高温度为130-150,无空气时为160-170度。
·卤化丁基橡胶·氯磺化聚乙烯橡胶。
氯磺化聚乙烯长期(1000H)最高使用温度为130度。
短时间可以允许升高到160度。
·氯醇橡胶。
耐热性比丁晴橡胶好。
均聚CHR比共聚CHR耐热性好。
·丙烯酸酯耐热性高于丁晴橡胶,低于氟橡胶。
长期(1000H)使用温度为170度,短时间(70H)使用温度可以提高到200度,·硅橡胶。
按照化学结构分类:1.二甲基硅橡胶(MQ)2.甲基乙烯基硅橡胶(MVQ)3.甲基苯基硅橡胶(MPQ)4.甲基苯基乙烯基硅橡胶(MPVQ)5.亚苯基硅橡胶6.亚苯醚基硅橡胶7.氟硅橡胶8.晴硅橡胶9.硼硅橡胶==》耐热性最好。
可以在400度下长期工作,在420-480度下可以连续工作几个小时。
硅橡胶是所有橡胶中耐热等级最高的一种橡胶。
但不耐湿热老化。
-50到+100度:无限期长/120度:10-20年/150度:5-10年/205度:2-5年/260度:3个月-2年/315度:7天-2个月/370度:6H-7天/420度:10分钟-2H。
·氟橡胶。
按照化学组成分类如下:·含氟烯氢氟橡胶类:1.偏氟乙烯与三氟氯乙烯共聚物.国外品牌KEL-F。
国产品牌FPM2301/23022.偏氟乙烯与六氟丙烯共聚物。
国外品牌:VITONA;国产品牌:FPM2601/2602;3.偏氟乙烯,四氟乙烯,与六氟丙烯三元共聚物。
国外品牌:VITONB;国产品牌:FPM2464.四氟乙烯与丙烯共聚物。
丁基橡胶使用温度范围

丁基橡胶使用温度范围
摘要:
1.丁基橡胶的概述
2.丁基橡胶的使用温度范围
3.影响丁基橡胶使用温度范围的因素
4.丁基橡胶在不同温度下的性能表现
5.结论
正文:
1.丁基橡胶的概述
丁基橡胶,又称丁基合成橡胶,是一种合成橡胶材料。
它以丁二烯为基本原料,通过聚合反应制成。
丁基橡胶具有优良的耐热性、耐老化性、耐化学腐蚀性以及电绝缘性,因此在各个领域有着广泛的应用。
2.丁基橡胶的使用温度范围
丁基橡胶的使用温度范围一般在-50℃至100℃之间。
在这个温度范围内,丁基橡胶可以保持良好的弹性、耐磨性和耐化学品性能。
3.影响丁基橡胶使用温度范围的因素
丁基橡胶的使用温度范围受到以下几个因素的影响:
(1)分子结构:不同的分子结构会导致丁基橡胶的性能差异,从而影响其使用温度范围。
(2)硫化体系:硫化体系是影响丁基橡胶性能的关键因素。
不同的硫化体系会对丁基橡胶的耐热性、耐寒性产生不同的影响。
(3)填充材料:丁基橡胶中添加的填充材料,如碳黑、硅烷等,也会影响其使用温度范围。
4.丁基橡胶在不同温度下的性能表现
(1)低温性能:在-50℃以下的低温环境中,丁基橡胶的弹性会降低,硬度会增加,但仍能保持较好的抗拉强度和耐磨性。
(2)高温性能:在100℃以上的高温环境中,丁基橡胶的弹性会变好,但耐热性会有所降低,容易出现软化、流淌现象。
5.结论
综上所述,丁基橡胶在使用过程中,其温度范围主要受分子结构、硫化体系和填充材料等因素影响。
在不同的温度环境下,丁基橡胶的性能表现也有所差异。
橡胶热分解温度

橡胶热分解温度
橡胶的热分解温度与橡胶的具体类型、结构和添加剂等因素有关,通常天然橡胶(NR)和其他合成橡胶如丁苯橡胶(SBR)、丁腈橡胶(NBR)、氯丁橡胶(CR)等在不同的温度下开始发生热分解。
一般来说:
- 天然橡胶的初始分解温度大约在200至300摄氏度之间,随着温度升高,其分解过程加速。
- 合成橡胶的热稳定性有所不同,例如,某些类型的合成橡胶由于分子结构不同,可能具有更高的分解温度,但通常也在200至450摄氏度范围内。
请注意,实际应用中,橡胶制品在接近其分解温度时性能会显著下降,因此,在设计橡胶产品时需充分考虑其工作环境温度,并选择适合的橡胶材料以确保长期稳定性和安全性。
此外,添加抗氧化剂和其他助剂可以提高橡胶材料的耐热性。
丁基橡胶配合和应用手册

Exxon™丁基橡胶配合和应用手册目录前言 (4)丁基橡胶的开发 (4)丁基橡胶聚合的化学机理 (4)丁基橡胶的生产 (6)丁基橡胶的化学特性 (9)丁基橡胶的化学特性 (9)丁基橡胶聚合物的分子结构 (10)Exxon™ 丁基橡胶牌号 (11)丁基橡胶的一般特性 (11)不饱和度对丁基橡胶耐热性的影响 (13)不饱和度对丁基橡胶硫化特性的影响 (13)分子量对丁基橡胶聚合物应力应变特性的影响 (14)丁基橡胶的硫化 (16)硫磺硫化 (16)秋兰姆促进的硫化 (18)酚醛树脂硫化 (21)醌硫化体系 (25)丁基橡胶混料 (26)丁基橡胶:聚合物的共混 (26)丁基橡胶:与炭黑共混 (30)丁基橡胶:与矿物填料共混 (32)丁基橡胶:增塑剂的影响 (35)丁基橡胶:加工助剂的影响 (38)优化丁基橡胶配合物的关键特性 (39)丁基橡胶:渗透性 (39)丁基橡胶:耐热性 (40)丁基橡胶:动态阻尼性能 (41)丁基橡胶配合物的加工工艺 (43)丁基橡胶:混炼 (44)丁基橡胶:挤出 (46)丁基橡胶:压延 (47)丁基橡胶的应用 (49)丁基橡胶:内胎 (49)丁基橡胶:球胆和硫化胶囊 (51)总结 (55)参考资料 (61)摘要得益于低渗透性,丁基橡胶和其它异丁烯聚合物得到了广泛使用。
异丁烯聚合物具有高度饱和的主链。
对于交联的异丁烯聚合物,是把少量异戊二烯通过共聚加成到饱和主链上。
异丁烯聚合物是通过阳离子反应聚合,使用布朗斯特德酸作为引发剂,使用路易斯酸作为共引发剂,例如水和氯化铝。
聚异丁烯的玻璃化温度 (Tg) 约为 -60°C,在无应变条件下是无定型的。
聚合物表现出了较宽的阻尼峰和低高弹模量。
这些聚合物具有优异的低气体渗透性,广泛用做轮胎中的气密层。
通过与炭黑或其它填料共混可以实现最优的物理特性。
可以通过各种机理将化合物交联成为硫化弹性体。
硫磺用于提供多硫交联,而树脂和氧化锌硫化体系将提供碳-碳交联。
橡胶的分类及介绍分解
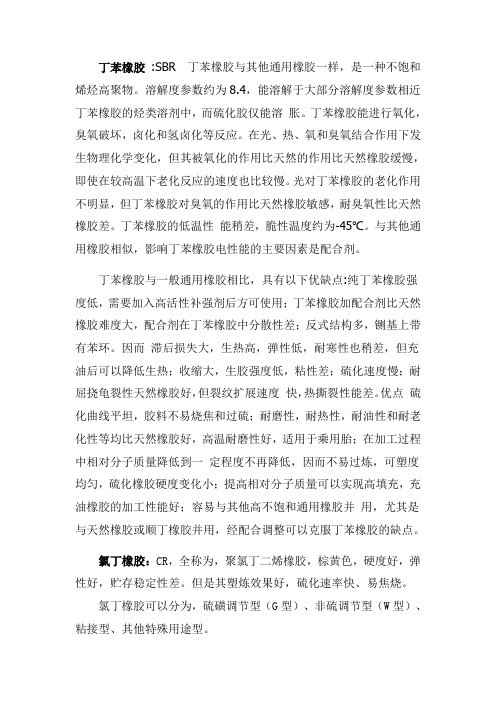
氯丁橡胶的混炼生热较大,所以辊温以50℃为宜。补强剂只能少量逐次加,软化剂可和软质填充剂同时加入。密炼机混炼时间一般在5~15分钟之间。为了使分散良好,混炼时间需要稍长一点。在密炼机上炼胶时,为了防止产生炭黑凝胶或焦烧,应尽量采用低温混炼。但是如果使用陶土,碳酸钙及其他无机填充剂时,由于其含水分较多,致使分散不良,如果将胶料温度提高到100℃左右进行混炼,借以减少水分,则分散良好。
丁苯橡胶:SBR丁苯橡胶与其他通用橡胶一样,是一种不饱和烯烃高聚物。溶解度参数约为8.4,能溶解于大部分溶解度参数相近丁苯橡胶的烃类溶剂中,而硫化胶仅能溶胀。丁苯橡胶能进行氧化,臭氧破坏,卤化和氢卤化等反应。在光、热、氧和臭氧结合作用下发生物理化学变化,但其被氧化的作用比天然的作用比天然橡胶缓慢,即使在较高温下老化反应的速度也比较慢。光对丁苯橡胶的老化作用不明显,但丁苯橡胶对臭氧的作用比天然橡胶敏感,耐臭氧性比天然橡胶差。丁苯橡胶的低温性能稍差,脆性温度约为-45℃。与其他通用橡胶相似,影响丁苯橡胶电性能的主要因素是配合剂。
丁苯橡胶与一般通用橡胶相比,具有以下优缺点:纯丁苯橡胶强度低,需要加入高活性补强剂后方可使用;丁苯橡胶加配合剂比天然橡胶难度大,配合剂在丁苯橡胶中分散性差;反式结构多,铡基上带有苯环。因而滞后损失大,生热高,弹性低,耐寒性也稍差,但充油后可以降低生热;收缩大,生胶强度低,粘性差;硫化速度慢;耐屈挠龟裂性天然橡胶好,但裂纹扩展速度快,热撕裂性能差。优点硫化曲线平坦,胶料不易烧焦和过硫;耐磨性,耐热性,耐油性和耐老化性等均比天然橡胶好,高温耐磨性好,适用于乘用胎;在加工过程中相对分子质量降低到一定程度不再降低,因而不易过炼,可塑度均匀,硫化橡胶硬度变化小;提高相对分子质量可以实现高填充,充油橡胶的加工性能好;容易与其他高不饱和通用橡胶并用,尤其是与天然橡胶或顺丁橡胶并用,经配合调整可以克服丁苯橡胶的缺点。
高饱和丁腈橡胶介绍

高饱和丁腈橡胶—HNBR(一)氢化丁腈橡胶(HNBR)也叫做高饱和丁腈橡胶与传统的丁腈橡胶(NBR)相比,其分子结构中含有少量或不含碳碳双键(C=C),它不仅具有NBR的耐油、耐磨、耐低温等性能,而且还具有更优异的耐热氧老化、耐臭氧、耐化学介质、良好的动态性能等,是目前最具发展潜力的橡胶品种之一,在许多方面已取代了氟橡胶等其它特种橡胶,已广泛地应用于汽车、油田等工业领域。
尤其是汽车用传动带,已占其用量的50%以上。
一、氢化丁腈橡胶(Hydrogenated nitrile rubber)氢化丁腈橡胶因烃链上的不饱和双键被氢化还原成饱和键,故也称高饱和丁腈橡胶,代号HNBR或HSN。
二、历史HNBR最早由德国Bayer公司于1984年小批量生产,商品名为Therban;日本Zeon公司也在同年建厂生产,商品名为Zetpol;随后加拿大的Polysar公司亦于1988年投产,商品名为Tornac(被Bayer兼并,已无此牌号);我国兰化公司于1999年开发成功,牌号:LH-9901、LH9902。
目前,世界HNBR总生产能力约7 500t/a,其中日本占五成、欧洲占三成、北美占二成。
在欧洲其消耗量55%为传动带、密封件20%、胶管11%、电缆5%、其它9%[1]。
三、制造方法:氢化丁腈橡胶制法有三:即乳液加氢化、丙烯腈-乙烯共聚法和丁腈橡胶乳液加氢法三种。
前两法尚在试验阶段,后一种制法已实现工业化。
丁腈橡胶乳液加氢法就是将制成的丁腈橡胶溶解,然后进行催化加氢而制得。
目前多致力于乳液催化加氢技术。
四、品种牌号国外生产氢化丁腈橡胶的厂家有日本瑞翁公司,德国Bayer公司和加拿大Polysar公司三家。
瑞翁公司牌号Zetpol HSN后缀以四位数字,前两位数字表示丙烯腈含量,10和20分别表示高和中高丙烯腈含;后两位数字表示碘值或不饱和度,10或20分别表示饱和度为95%和90%,数字后的字母L表示门尼粘度值低。
热失重法快速评估交联聚乙烯材料热老化寿命的可靠性研究

2021 年 6 月
电线电缆
No.3 2021
Wire & Cable
Jun.,2021
热失重法快速评估交联聚乙烯材料
热老化寿命的可靠性研究
胡诚成,倪 勇
( 上海电缆研究所有限公司 特种电缆技术国家重点实验室,上海 200093)
摘要:采用热失重技术研究交联聚乙烯( XLPE) 材料在氮气与空气两种氛围下的热降解过程,分别参照 JB / T
及依据。
从而影响电线电缆的运行可靠性及使用寿命。 根据
1 试验部分
老化原因,电缆绝缘老化分为机械老化、化学老化、
电老化和热老化 [2⁃4] 。 电线电缆失效主要是由热老
化直接或间接引起的,在综合考虑热老化评估的可
行性及热环境的普遍适用性后,对电线电缆的寿命
评估首选热老化寿命评估
[2]
。
收稿日期:2020⁃05⁃06
1544—2015、ASTM E1641⁃07—2012 和 ASTM E1877⁃00—2015 标准并结合常规老化法及阿伦尼乌斯经验公
式,以 5%失重为 XLPE 使用寿命失效终点,分别用恒温法和升温法评估了空气氛围下的热老化寿命,并建立
了两种方法下的热老化寿命方程 lnt = 14 970 / T- 23 8 与 lgt f = 6 581 6 / T f - 10 574,最后综合实际运行寿命、
Abstract: Thermogravimetry is used to study the thermal degradation process of cross⁃linking polyethylene material
under two atmospheres of nitrogen and air, referring to JB / T 1544—2015, ASTM E1641⁃07—2012, and ASTM
丁基再生胶热失重报告
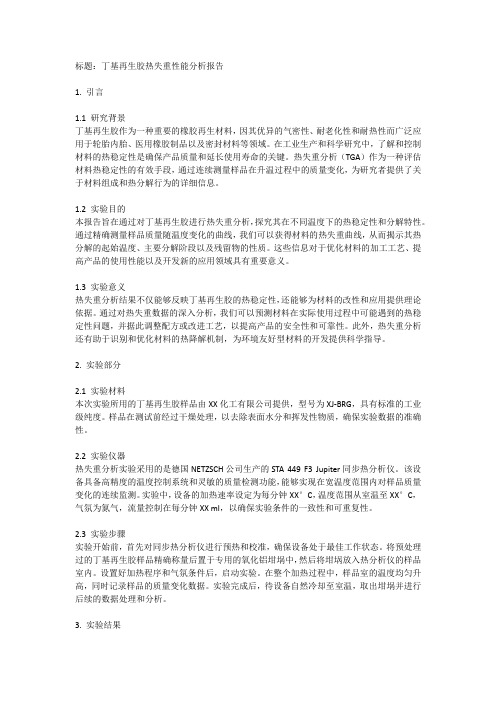
标题:丁基再生胶热失重性能分析报告1. 引言1.1 研究背景丁基再生胶作为一种重要的橡胶再生材料,因其优异的气密性、耐老化性和耐热性而广泛应用于轮胎内胎、医用橡胶制品以及密封材料等领域。
在工业生产和科学研究中,了解和控制材料的热稳定性是确保产品质量和延长使用寿命的关键。
热失重分析(TGA)作为一种评估材料热稳定性的有效手段,通过连续测量样品在升温过程中的质量变化,为研究者提供了关于材料组成和热分解行为的详细信息。
1.2 实验目的本报告旨在通过对丁基再生胶进行热失重分析,探究其在不同温度下的热稳定性和分解特性。
通过精确测量样品质量随温度变化的曲线,我们可以获得材料的热失重曲线,从而揭示其热分解的起始温度、主要分解阶段以及残留物的性质。
这些信息对于优化材料的加工工艺、提高产品的使用性能以及开发新的应用领域具有重要意义。
1.3 实验意义热失重分析结果不仅能够反映丁基再生胶的热稳定性,还能够为材料的改性和应用提供理论依据。
通过对热失重数据的深入分析,我们可以预测材料在实际使用过程中可能遇到的热稳定性问题,并据此调整配方或改进工艺,以提高产品的安全性和可靠性。
此外,热失重分析还有助于识别和优化材料的热降解机制,为环境友好型材料的开发提供科学指导。
2. 实验部分2.1 实验材料本次实验所用的丁基再生胶样品由XX化工有限公司提供,型号为XJ-BRG,具有标准的工业级纯度。
样品在测试前经过干燥处理,以去除表面水分和挥发性物质,确保实验数据的准确性。
2.2 实验仪器热失重分析实验采用的是德国NETZSCH公司生产的STA 449 F3 Jupiter同步热分析仪。
该设备具备高精度的温度控制系统和灵敏的质量检测功能,能够实现在宽温度范围内对样品质量变化的连续监测。
实验中,设备的加热速率设定为每分钟XX°C,温度范围从室温至XX°C,气氛为氮气,流量控制在每分钟XX ml,以确保实验条件的一致性和可重复性。
甲基乙烯基硅橡胶_丁基橡胶硫化性能和耐热性能研究
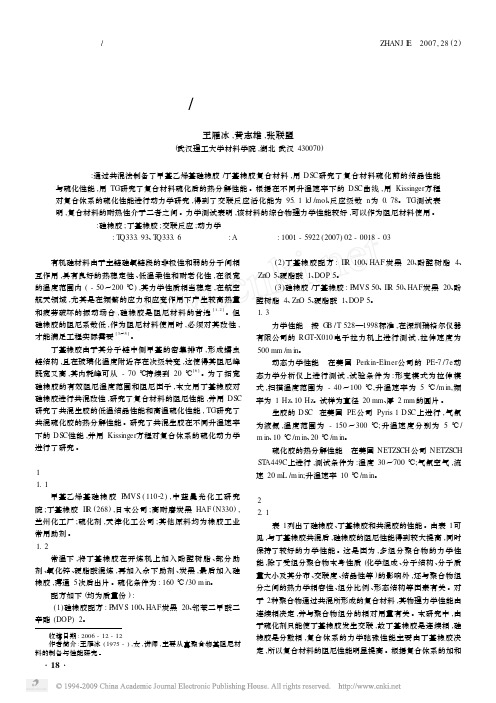
F ig. 1 D SC d ia g ram fo r IIR a nd DMVS / IIR 图 1 IIR 与 PMVS / IIR 的 D SC 图
如表观活化能和反应级数等 ,对了解交联反应具有重要作用 。 表 2列出了不同升温速率下 PMVS/ IIR 的起始硫化温度 、峰 值温度 、结束温度等硫化参数 。
远大于 2TP时 ,则 2TP可忽略 ,式 (3)变为
dln (β) d ( 1 / TP )
=
-
(ΔEa ) nR
(4)
lnβ与 1 / TP呈线性关系 。以 lnβ对 1 / TP作图可得一直
线 ,由该直线的斜率可求得交联反应级数 n。
图 4为 lnβ对 1 / TP曲线 ,由斜率得反应级数 n = 0. 74。
线可根据此式求出活化能 Ea。图 3 为 ln (β/ TP2 )对 1 / TP 作 图所得的曲线 ,从斜率可求得交联活化能 ΔEa = 95. 1 kJ /mol。
反应级数 n可由 Grane方程求得 [8 ] :
dln (β) d ( 1 / TP )
=
-
(ΔEa nR
+ 2TP )
(3)
其中 n为反应级数 ,其他参数意义同式 ( 2 ) 。当 ΔE / nR
F ig. 4 C u rve o f In β - 1 / Tp 图 4 lnβ- 1 / TP 图
2. 3 热分解性能 图 5、图 6为 IIR、PMVS、共混胶硫化后的 TG和 DTG图 。
表 3是从 2图中得出的热分解数据 。
Ta b. 3 The rm o lys is tem p e ra tu re fo r IIR a nd PMVS / IIR 表 3 IIR、PMVS 以及 PMVS / IIR 的热分解温度
橡胶制品硫化的三大参数:时间、温度、压力
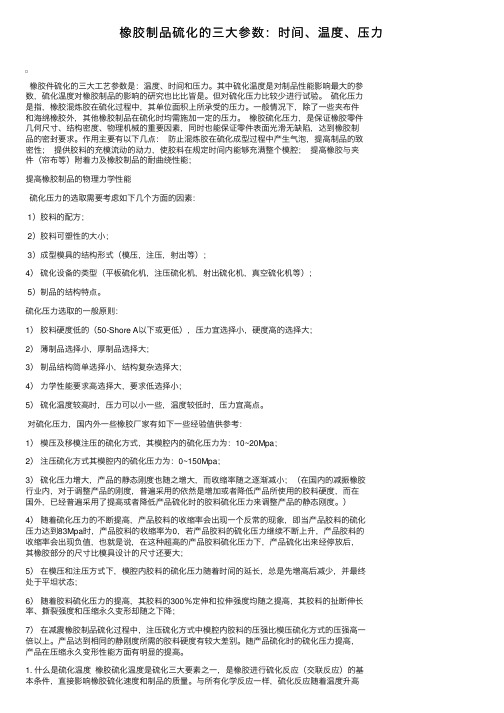
橡胶制品硫化的三⼤参数:时间、温度、压⼒橡胶件硫化的三⼤⼯艺参数是:温度、时间和压⼒。
其中硫化温度是对制品性能影响最⼤的参数,硫化温度对橡胶制品的影响的研究也⽐⽐皆是。
但对硫化压⼒⽐较少进⾏试验。
硫化压⼒是指,橡胶混炼胶在硫化过程中,其单位⾯积上所承受的压⼒。
⼀般情况下,除了⼀些夹布件和海绵橡胶外,其他橡胶制品在硫化时均需施加⼀定的压⼒。
橡胶硫化压⼒,是保证橡胶零件⼏何尺⼨、结构密度、物理机械的重要因素,同时也能保证零件表⾯光滑⽆缺陷,达到橡胶制品的密封要求。
作⽤主要有以下⼏点:防⽌混炼胶在硫化成型过程中产⽣⽓泡,提⾼制品的致密性;提供胶料的充模流动的动⼒,使胶料在规定时间内能够充满整个模腔;提⾼橡胶与夹件(帘布等)附着⼒及橡胶制品的耐曲绕性能;提⾼橡胶制品的物理⼒学性能硫化压⼒的选取需要考虑如下⼏个⽅⾯的因素:1)胶料的配⽅;2)胶料可塑性的⼤⼩;3)成型模具的结构形式(模压,注压,射出等);4)硫化设备的类型(平板硫化机,注压硫化机,射出硫化机,真空硫化机等);5)制品的结构特点。
硫化压⼒选取的⼀般原则:1)胶料硬度低的(50-Shore A以下或更低),压⼒宜选择⼩,硬度⾼的选择⼤;2)薄制品选择⼩,厚制品选择⼤;3)制品结构简单选择⼩,结构复杂选择⼤;4)⼒学性能要求⾼选择⼤,要求低选择⼩;5)硫化温度较⾼时,压⼒可以⼩⼀些,温度较低时,压⼒宜⾼点。
对硫化压⼒,国内外⼀些橡胶⼚家有如下⼀些经验值供参考:1)模压及移模注压的硫化⽅式,其模腔内的硫化压⼒为:10~20Mpa;2)注压硫化⽅式其模腔内的硫化压⼒为:0~150Mpa;3)硫化压⼒增⼤,产品的静态刚度也随之增⼤,⽽收缩率随之逐渐减⼩;(在国内的减振橡胶⾏业内,对于调整产品的刚度,普遍采⽤的依然是增加或者降低产品所使⽤的胶料硬度,⽽在国外,已经普遍采⽤了提⾼或者降低产品硫化时的胶料硫化压⼒来调整产品的静态刚度。
)4)随着硫化压⼒的不断提⾼,产品胶料的收缩率会出现⼀个反常的现象,即当产品胶料的硫化压⼒达到83Mpa时,产品胶料的收缩率为0,若产品胶料的硫化压⼒继续不断上升,产品胶料的收缩率会出现负值,也就是说,在这种超⾼的产品胶料硫化压⼒下,产品硫化出来经停放后,其橡胶部分的尺⼨⽐模具设计的尺⼨还要⼤;5)在模压和注压⽅式下,模腔内胶料的硫化压⼒随着时间的延长,总是先增⾼后减少,并最终处于平坦状态;6)随着胶料硫化压⼒的提⾼,其胶料的300%定伸和拉伸强度均随之提⾼,其胶料的扯断伸长率、撕裂强度和压缩永久变形却随之下降;7)在减震橡胶制品硫化过程中,注压硫化⽅式中模腔内胶料的压强⽐模压硫化⽅式的压强⾼⼀倍以上。
丁基橡胶氮气氛围下的最大热分解温度

在化学领域中,丁基橡胶是一种常见的合成橡胶,通常用于制作轮胎,密封件,管道等产品。
在这些应用中,丁基橡胶需要具有较高的耐热性能,以确保产品在高温环境下不发生失效。
了解丁基橡胶在氮气氛围下的最大热分解温度对于产品设计和安全性评估具有重要意义。
1. 知识背景在讨论丁基橡胶在氮气氛围下的最大热分解温度之前,首先需要了解几个基本概念。
丁基橡胶是一种弹性良好的合成橡胶,通常具有良好的耐热性能。
然而,在空气中长时间高温下,丁基橡胶仍然可能发生热分解,从而影响产品的使用寿命和安全性能。
为了进一步提高丁基橡胶的耐热性能,研究人员通常会考虑在氮气氛围下进行实验,因为氮气氛围可以减少氧气对材料的影响,从而更准确地评估材料的热稳定性。
2. 实验方法为了确定丁基橡胶在氮气氛围下的最大热分解温度,实验研究通常会采用热重分析法(TGA)进行测试。
热重分析法是一种常用的分析技术,用于研究材料在控制温度条件下的质量变化情况。
在实验中,样品通常会置于热重天平中,随着温度的升高,观察样品的质量随温度变化的情况,从而确定材料的热分解温度。
3. 结果分析通过对丁基橡胶在氮气氛围下的热重分析实验,研究人员可以得到丁基橡胶的热分解曲线,并据此确定最大热分解温度。
根据过往的研究成果,丁基橡胶在氮气氛围下的最大热分解温度通常在XXX°C左右。
这一结果意味着在氮气氛围下,丁基橡胶具有较高的热稳定性,可以在较高温度下长时间使用而不发生失效。
4. 个人观点从我个人的观点来看,丁基橡胶在氮气氛围下的热分解温度对于其在高温环境下的应用具有重要意义。
通过详细研究材料的热稳定性,可以为产品设计和材料选型提供重要参考,从而确保产品在实际使用中能够安全可靠地工作。
对于其他类似的合成材料,也可以借鉴类似的研究方法,以期提高材料的热稳定性,推动材料科学的发展。
总结回顾丁基橡胶在氮气氛围下的最大热分解温度是一个重要的研究课题。
通过实验方法和结果分析,我们可以得出丁基橡胶在氮气氛围下的最大热分解温度通常在XXX°C左右的结论。
常识
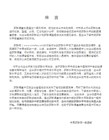
泄漏处理:迅速撤离泄漏污染区人员至上风处,并隔离直至气体散尽,切断火源,建议应急处理人员戴自给式呼吸器,穿一般消防服,切断气源,喷雾状水稀释溶解,通风对流,稀释扩散,如有可能,将漏出气用排风机送至空旷地方或装设适当喷头烧掉。漏气容器不能再用,且要经过技术处理以清除可能剩下的气体。
3.燃烧(分解)产物:一氧化碳,二氧化碳
4.稳定性:稳定 聚合危害:能发生 禁忌物:强氧化剂,强酸。
灭火方法:切断火源,若不能立即切断气源,则不允许熄灭正在燃烧的气体,喷水冷却容器,可能的话将容器从火场移至空旷处。雾状水,泡沫,二氧化碳。
防护措施与急救:
1.工程控制:生产过程密闭,全面通风; 2.呼吸系统保护:高浓度环境中佩戴供气或呼吸器; 3.眼睛保护:一般不需要特殊保护,高浓度接触可戴化学安全防护眼镜。 4.保护服:穿工作服; 5.受保护:一般不需要特殊保护,高浓度接触可戴防护手套。 6.其他:现场严禁吸烟,避免长期反复接触,进入罐或其他高浓度区作业需有人监护。
丙烯
1.燃烧性:易爆 建规火线分级:甲 闪点:-108度 自然温度:455度 爆炸下限:1.0 爆炸上线:15.0
2.危险特性:与空气混合能到形成爆炸性混合物,遇明火高热能引起燃烧爆炸。其蒸汽比空气重。能在较低处扩散到相当远的地方。遇火源引着回燃。若遇高热,容器内压增大,有开裂和爆炸的危险。
急救:迅速脱离现场至空气新鲜处,注意保暖,保持呼吸通畅,呼吸困难时给输氧,呼吸停止时立即进行人工呼吸,就医。
泄漏处理:迅速撤离泄漏污染区人员至上风处,并隔离直至气体散尽,切断火源,建议应急处理人员戴自给式呼吸器,穿一般消防服,切断气源,喷雾状水稀释溶解,通风对流,稀释扩散,如有可能,将漏出气用排风机送至空旷地方或装设适当喷头烧掉。漏气容器不能再用,且要经过技术处理以清除可能剩下的气体。
丁基橡胶氮气氛围下的最大热分解温度
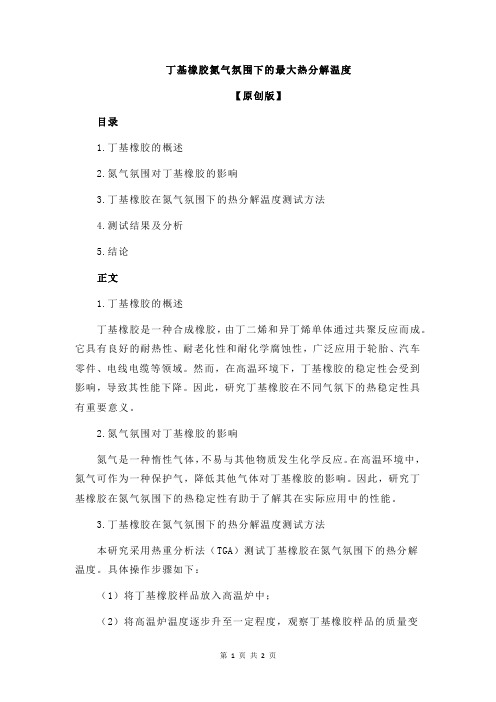
丁基橡胶氮气氛围下的最大热分解温度
【原创版】
目录
1.丁基橡胶的概述
2.氮气氛围对丁基橡胶的影响
3.丁基橡胶在氮气氛围下的热分解温度测试方法
4.测试结果及分析
5.结论
正文
1.丁基橡胶的概述
丁基橡胶是一种合成橡胶,由丁二烯和异丁烯单体通过共聚反应而成。
它具有良好的耐热性、耐老化性和耐化学腐蚀性,广泛应用于轮胎、汽车零件、电线电缆等领域。
然而,在高温环境下,丁基橡胶的稳定性会受到影响,导致其性能下降。
因此,研究丁基橡胶在不同气氛下的热稳定性具有重要意义。
2.氮气氛围对丁基橡胶的影响
氮气是一种惰性气体,不易与其他物质发生化学反应。
在高温环境中,氮气可作为一种保护气,降低其他气体对丁基橡胶的影响。
因此,研究丁基橡胶在氮气氛围下的热稳定性有助于了解其在实际应用中的性能。
3.丁基橡胶在氮气氛围下的热分解温度测试方法
本研究采用热重分析法(TGA)测试丁基橡胶在氮气氛围下的热分解
温度。
具体操作步骤如下:
(1)将丁基橡胶样品放入高温炉中;
(2)将高温炉温度逐步升至一定程度,观察丁基橡胶样品的质量变
化;
(3)绘制温度 - 质量曲线,确定丁基橡胶在氮气氛围下的最大热分解温度。
4.测试结果及分析
经过多次实验,得到丁基橡胶在氮气氛围下的最大热分解温度为270℃。
这说明在氮气氛围下,丁基橡胶具有较好的热稳定性,可在高温环境中保持其性能。
5.结论
本研究表明,在氮气氛围下,丁基橡胶具有较高的热稳定性,其最大热分解温度为 270℃。
丁基橡胶氮气氛围下的最大热分解温度

丁基橡胶氮气氛围下的最大热分解温度丁基橡胶是一种常见的合成橡胶,具有优良的物理性能和化学稳定性,被广泛应用于汽车轮胎、工业密封件等领域。
而丁基橡胶在实际应用中,常常需要在高温环境下工作,因此其热分解温度也成为一个重要的研究课题。
在氮气氛围下的最大热分解温度更是对其热稳定性的重要指标,本文将对此进行深入探讨。
一、丁基橡胶的热分解特性在热分解过程中,丁基橡胶分子链中的碳-碳键和碳-氢键将被断裂,导致橡胶材料失去弹性和机械性能。
热分解温度是衡量丁基橡胶热稳定性的关键指标,而氮气氛围下的最大热分解温度则能够更准确地反映其在实际工作环境中的热稳定性。
二、影响丁基橡胶热分解温度的因素1. 分子结构:丁基橡胶的分子结构中存在不饱和双键,这些双键在高温下容易发生热分解反应,因而影响了最大热分解温度的值。
2. 添加剂:在实际应用中,常常向丁基橡胶中添加各种防老剂和增塑剂,这些添加剂的种类和含量也会对其热分解温度产生一定影响。
3. 加工工艺:丁基橡胶制品在加工过程中,如硫化和挤压成型等,也会对其热分解温度造成影响。
三、氮气氛围下的最大热分解温度的意义在实际工作环境中,丁基橡胶制品通常会暴露在各种气氛环境下,其中氮气氛围被广泛应用于防止氧化和热解等过程,因此在氮气氛围下的最大热分解温度对于预测丁基橡胶在实际工作条件下的稳定性具有重要意义。
通过对氮气氛围下的最大热分解温度的研究,可以促进丁基橡胶材料在高温环境下的应用,提高其使用寿命和安全性。
个人观点和理解:经过对丁基橡胶氮气氛围下的最大热分解温度的深入研究,我认为在实际工程应用中,不仅需要关注其热分解温度,还需考虑到制品在特定环境下的稳定性和安全性。
有必要继续开展更多针对氮气氛围下的最大热分解温度的研究,以提高丁基橡胶的热稳定性,满足不同领域对其高温环境下性能的需求。
总结与回顾:通过对丁基橡胶氮气氛围下的最大热分解温度进行分析和讨论,我们可以清晰地了解到这一指标对于材料的热稳定性的重要性。
常用橡胶的品种及使用温度

常用橡胶的品种,特性,用途天然橡胶 -20~≤85℃丁腈橡胶 -20~≤82℃三元乙丙 -40~≤125℃聚四氟乙烯-50~≤150℃氟橡胶 -23~≤160℃橡胶品种(简写符号)化学组成性能特点主要用途1.天然橡胶(NR)以橡胶烃(聚异戊二烯)为主,含少量蛋白质、水分、树脂酸、糖类和无机盐等。
弹性大,定伸强度高,抗撕裂性和电绝缘性优良,耐磨性和耐旱性良好,加工性佳,易于其它材料粘合,在综合性能方面优于多数合成橡胶。
缺点是耐氧和耐臭氧性差,容易老化变质;耐油和耐溶剂性不好,第抗酸碱的腐蚀能力低;耐热性不高。
使用温度范围:约-60℃~+80℃。
制作轮胎、胶鞋、胶管、胶带、电线电缆的绝缘层和护套以及其他通用制品。
特别适用于制造扭振消除器、发动机减震器、机器支座、橡胶-金属悬挂元件、膜片、模压制品。
2.丁苯橡胶(SBR)丁二烯和苯乙烯的共聚体。
性能接近天然橡胶,是目前产量最大的通用合成橡胶,其特点是耐磨性、耐老化和耐热性超过天然橡胶,质地也较天然橡胶均匀。
缺点是:弹性较低,抗屈挠、抗撕裂性能较差;加工性能差,特别是自粘性差、生胶强度低。
使用温度范围:约-50℃~+100℃。
主要用以代替天然橡胶制作轮胎、胶板、胶管、胶鞋及其他通用制品。
3.顺丁橡胶(BR)是由丁二烯聚合而成的顺式结构橡胶。
优点是:弹性与耐磨性优良,耐老化性好,耐低温性优异,在动态负荷下发热量小,易于金属粘合。
缺点是强度较低,抗撕裂性差,加工性能与自粘性差。
使用温度范围:约-60℃~+100℃。
一般多和天然橡胶或丁苯橡胶并用,主要制作轮胎胎面、运输带和特殊耐寒制品。
4.异戊橡胶(IR)是由异戊二烯单体聚合而成的一种顺式结构橡胶。
化学组成、立体结构与天然橡胶相似,性能也非常接近天然橡胶,故有合成天然橡胶之称。
它具有天然橡胶的大部分优点,耐老化由于天然橡胶,弹性和强力比天然橡胶稍低,加工性能差,成本较高。
使用温度范围:约-50℃~+100℃。
- 1、下载文档前请自行甄别文档内容的完整性,平台不提供额外的编辑、内容补充、找答案等附加服务。
- 2、"仅部分预览"的文档,不可在线预览部分如存在完整性等问题,可反馈申请退款(可完整预览的文档不适用该条件!)。
- 3、如文档侵犯您的权益,请联系客服反馈,我们会尽快为您处理(人工客服工作时间:9:00-18:30)。
丁基橡胶氮气氛围下的最大热分解温度
摘要:
一、引言
二、丁基橡胶简介
1.丁基橡胶的性质
2.丁基橡胶的应用领域
三、氮气氛围下的丁基橡胶热分解
1.丁基橡胶在氮气氛围下的变化
2.最大热分解温度的测定方法
四、影响丁基橡胶最大热分解温度的因素
五、结论
正文:
一、引言
丁基橡胶作为一类重要的合成橡胶,被广泛应用于轮胎、密封件等众多领域。
为了进一步挖掘丁基橡胶的性能潜力,研究人员对丁基橡胶在氮气氛围下的热分解温度进行了深入研究。
本文将围绕这一主题,对相关研究成果进行梳理和总结。
二、丁基橡胶简介
1.丁基橡胶的性质
丁基橡胶是一种具有良好气密性、耐热性和耐化学腐蚀性的合成橡胶。
其分子结构中,由于含有大量的碳-碳双键,使其具有较高的可塑性和可硫化性。
2.丁基橡胶的应用领域
丁基橡胶广泛应用于轮胎、密封件、电线电缆、涂料等领域,其中,轮胎制造是丁基橡胶的最大消费市场。
三、氮气氛围下的丁基橡胶热分解
1.丁基橡胶在氮气氛围下的变化
在氮气氛围下,丁基橡胶的分子结构受到热分解作用,发生一系列化学反应,导致其物理性质和化学性质发生变化。
2.最大热分解温度的测定方法
最大热分解温度的测定通常采用差热分析法(DTA)和热重分析法(TGA)进行。
通过这两种方法,可以得到丁基橡胶在不同气氛下的热分解曲线,从而确定其在氮气氛围下的最大热分解温度。
四、影响丁基橡胶最大热分解温度的因素
丁基橡胶的最大热分解温度受多种因素影响,如分子结构、硫化程度、填充材料等。
在实际应用中,需要根据具体需求对丁基橡胶进行合理的配方设计,以满足不同场景下的性能要求。
五、结论
氮气氛围下的丁基橡胶最大热分解温度是一个重要的性能参数,对丁基橡胶的加工和使用具有重要指导意义。