我国烟气脱硫技术现状综述
我国火电厂烟气脱硫工艺现状及发展综述

我国火电厂烟气脱硫工艺现状及发展综述随着人们环保意识的提高以及国家相关政策的推出,整治大气污染势在必行,尤其是近几年来雾霾天气的频发,对人们的生活造成了严重的影响,空气治理成为现下社会关注的热点。
其中,火电厂烟气排放是形成大气污染的罪魁祸首之一,并且相关数据显示由火电厂排放的含硫烟气占总排量的,为此研究和探讨火电厂烟气脱硫工艺技术具有十分重要的意义。
本文简要分析火电厂脱硫工艺的发展过程,探讨现阶段火电厂烟气脱硫工艺应用情况以及应用存在的问题,分析选择脱硫工艺的原则和方法,以此作为科学、合理选择脱硫工艺的依据。
标签:火电厂;烟气脱硫;发展状况二氧化硫的排放是对环境造成污染以及加重酸雨状况的重要原因,其中酸雨对大自然有着严重的危害,可以导致森林退化,腐蚀建筑物等,严重威胁着人们的生存环境,而且威胁着人们身体健康。
在排放二氧化硫的罪魁祸首中,火电厂担负着较大的责任,在用电量需求不断增加的情况下,只能加强对火电厂烟气脱硫工艺的研究,选择合理、科学的脱硫方法实施火电厂烟气脱硫,以经济性和实用性作为相应的选择原则,逐渐提高脱硫工艺的质量和效率,在确保火电厂供电量的基础上优化火电厂烟气脱硫工艺,降低火电厂含硫烟气的排放量。
1 我国火电厂烟气脱硫工艺发展现状1.1 现阶段普遍应用的烟气脱硫方法现阶段,我国火电厂普遍应用四种烟气脱硫方法,其一是喷雾干燥法,这种烟气脱硫方法早在90世纪就已经基本成熟,并迅速普及应用在电力工艺方面,其中国内相关企业和部门进行了喷雾干燥法的实验和改进,有着较为成熟的实验数据。
其二是石灰石-石膏湿法,这种方法是四种烟气脱硫技术中最成熟的一种方法,实施过程中耗费的成本较低,而且烟气脱硫效率和质量都较好,可以达到国家相关规定和标准,并且使用的材料在使用之后还可以进行废料回收,十分环保,因此有着最广泛的应用范围。
其三是循环流化床法,这种方法耗费的水量较少,在排放过程中不需要使用防腐的煙囱,排放的烟气具有较高的温度,而且操作过程中副产物比较容易处理。
烟气脱硫脱硝技术的现状及发展分析
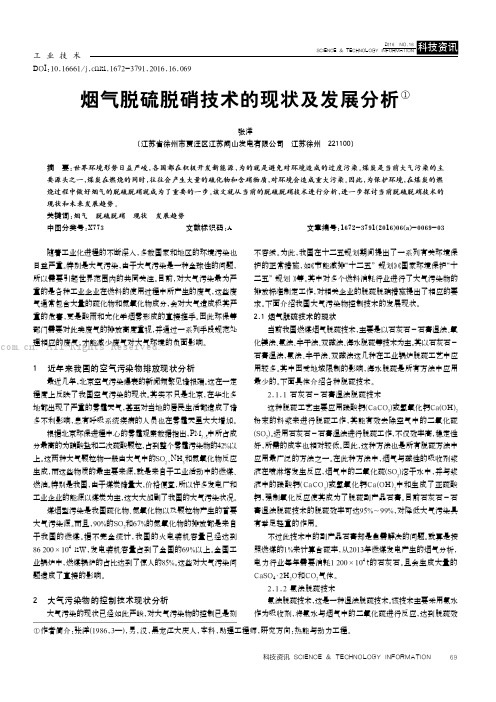
科技资讯2016 NO.16SCIENCE & TECHNOLOGY INFORMATION工 业 技 术随着工业化进程的不断深入,多数国家和地区的环境污染也日益严重。
特别是大气污染,由于大气污染是一种全球性的问题,所以需要引起世界范围内的共同关注。
目前,对大气污染最为严重的是各种工业企业在燃料的使用过程中所产生的废气,这些废气通常包含大量的硫化物和氮氧化物成分,会对大气造成极其严重的危害,更是酸雨和光化学烟雾形成的直接推手。
因此环保等部门需要对此类废气的排放高度重视,并通过一系列手段规范处理相应的废气,才能减少废气对大气环境的负面影响。
1 近年来我国的空气污染物排放现状分析最近几年,北京空气污染爆表的新闻频繁见诸报端。
这在一定程度上反映了我国空气污染的现状。
其实不只是北京,在华北多地都出现了严重的雾霾天气,甚至对当地的居民生活都造成了诸多不利影响,患有呼吸系统疾病的人员也在雾霾天里大大增加。
根据北京环保进程中心的雾霾观察数据指出,PM 2.5中所占成分最高的为硝酸盐和二次硫酸颗粒,占到整个雾霾污染物的42%以上。
这两种大气颗粒物一般由大气中的SO 2、NH 3和氮氧化物反应生成,而这些物质的最主要来源,就是来自于工业活动中的燃煤、燃油。
特别是我国,由于煤炭储量大,价格便宜,所以许多发电厂和工业企业的能源以煤炭为主,这大大加剧了我国的大气污染状况。
煤烟型污染是我国硫化物、氮氧化物以及颗粒物产生的首要大气污染源。
而且,90%的SO 2和67%的氮氧化物的排放都是来自于我国的燃煤。
据不完全统计,我国的火电装机容量已经达到86200×104 kW,发电装机容量占到了全国的69%以上。
全国工业锅炉中,燃煤锅炉的占比达到了惊人的85%。
这些对大气污染问题造成了直接的影响。
2 大气污染物的控制技术现状分析大气污染的现状已经如此严峻,对大气污染物的控制已是刻不容缓。
为此,我国在十二五规划期间提出了一系列有关环境保护的正常措施,如《节能减排“十二五” 规划》《国家环境保护“十二五” 规划 》等。
烟气脱硫技术现状及展
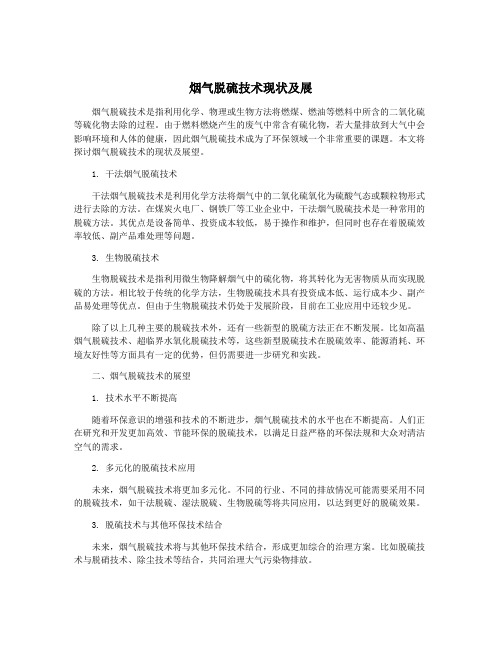
烟气脱硫技术现状及展烟气脱硫技术是指利用化学、物理或生物方法将燃煤、燃油等燃料中所含的二氧化硫等硫化物去除的过程。
由于燃料燃烧产生的废气中常含有硫化物,若大量排放到大气中会影响环境和人体的健康,因此烟气脱硫技术成为了环保领域一个非常重要的课题。
本文将探讨烟气脱硫技术的现状及展望。
1. 干法烟气脱硫技术干法烟气脱硫技术是利用化学方法将烟气中的二氧化硫氧化为硫酸气态或颗粒物形式进行去除的方法。
在煤炭火电厂、钢铁厂等工业企业中,干法烟气脱硫技术是一种常用的脱硫方法。
其优点是设备简单、投资成本较低,易于操作和维护,但同时也存在着脱硫效率较低、副产品难处理等问题。
3. 生物脱硫技术生物脱硫技术是指利用微生物降解烟气中的硫化物,将其转化为无害物质从而实现脱硫的方法。
相比较于传统的化学方法,生物脱硫技术具有投资成本低、运行成本少、副产品易处理等优点。
但由于生物脱硫技术仍处于发展阶段,目前在工业应用中还较少见。
除了以上几种主要的脱硫技术外,还有一些新型的脱硫方法正在不断发展。
比如高温烟气脱硫技术、超临界水氧化脱硫技术等,这些新型脱硫技术在脱硫效率、能源消耗、环境友好性等方面具有一定的优势,但仍需要进一步研究和实践。
二、烟气脱硫技术的展望1. 技术水平不断提高随着环保意识的增强和技术的不断进步,烟气脱硫技术的水平也在不断提高。
人们正在研究和开发更加高效、节能环保的脱硫技术,以满足日益严格的环保法规和大众对清洁空气的需求。
2. 多元化的脱硫技术应用未来,烟气脱硫技术将更加多元化。
不同的行业、不同的排放情况可能需要采用不同的脱硫技术,如干法脱硫、湿法脱硫、生物脱硫等将共同应用,以达到更好的脱硫效果。
3. 脱硫技术与其他环保技术结合未来,烟气脱硫技术将与其他环保技术结合,形成更加综合的治理方案。
比如脱硫技术与脱硝技术、除尘技术等结合,共同治理大气污染物排放。
随着科技的进步,新技术在烟气脱硫领域的应用也将成为未来的发展方向。
我国火电厂烟气脱硫现状及展望

三、未来烟气脱硫技术的研究方 向和应用前景
1、加强技术创新和研究开发
针对当前烟气脱硫技术存在的问题和不足,未来需要加强技术创新和研究开 发。一方面,研发新型高效的烟气脱硫技术,提高脱硫效率和净化程度;另一方 面,加强设备研发和工艺优化,提高设备的可靠性和使用寿命,降低运行成本。
2、多种脱硫技术联合应用
单一的烟气脱硫技术往往存在一定的局限性,难以满足不同火电厂的需求。 因此,未来可以探讨多种脱硫技术的联合应用,以达到更好的脱硫效果。例如, 可以将石灰石-石膏法与其它烟气脱硫技术相结合,充分发挥各自优势,提高整 体脱硫效果。
3、智能化和自动化控制
随着科技的不断进步,智能化和自动化控制技术在火电厂烟气脱硫中将会得 到更加广泛的应用。通过引入智能传感器、数据分析和优化算法等手段,实现对 烟气脱硫过程的实时监控和自动调节,提高脱硫效率和稳定性,降低人工干预成 本。
参考内容
关键词:火电厂,烟气脱硫,现 状,发展,火电厂烟气脱硫工艺成为了环保领域的 重要研究方向。我国作为世界上最大的能源消费国,火电厂数量众多,烟气脱硫 工艺的发展对我国环保事业和能源结构的优化具有重要意义。本次演示将概述我 国火电厂烟气脱硫工艺的现状,探讨其未来发展方向,以期为相关领域的研究和 实践提供参考。
4、绿色发展理念
未来烟气脱硫技术的发展需要更加注重绿色发展理念。在设备选材、工艺设 计、运行管理等方面要尽可能减少对环境的影响,努力实现零排放、低能耗、高 效率的绿色脱硫。同时,要注重开展副产物资源化利用研究,提高资源利用率, 实现循环经济。
结论
我国火电厂烟气脱硫在取得一定成绩的也面临着诸多问题和挑战。未来,需 要加强技术创新和研究开发,推动多种脱硫技术联合应用,实现智能化和自动化 控制,并秉承绿色发展理念,以推动我国火电厂烟气脱硫事业取得更加显著的成 果。
烟气脱硫技术的现状分析与应用

烟气脱硫技术的现状分析与应用近年来,环境保护成为社会关注的焦点,大气污染是其中一个重要问题。
烟气中的二氧化硫是大气污染的主要来源之一,因此研究烟气脱硫技术成为当前环保领域研究的热点之一。
本文将从现状分析与应用两个方面探讨烟气脱硫技术的相关发展。
烟气脱硫技术的现状分析目前,烟气脱硫技术主要包括干法脱硫和湿法脱硫两种常用方法。
干法脱硫主要通过烟气与固态吸收剂接触,使二氧化硫与吸收剂反应生成硫化物,以达到脱硫效果。
常用的干法脱硫方法有活性碳吸附法、氧化剂吸附法和物理吸附法等。
然而,干法脱硫方法存在着吸附剂消耗快、脱硫效率低、操作复杂等不足之处。
湿法脱硫是目前应用较为广泛的烟气脱硫方法,主要通过将烟气与石灰乳或氨水等吸收剂进行接触,使二氧化硫与吸收剂反应生成硫酸盐或硫代硫酸盐的水溶液,达到脱硫效果。
常见的湿法脱硫方法有石灰石石膏法、石灰乳法和氨法等。
目前,石灰乳法广泛应用于燃煤电厂等大型工业设备中,该方法具有脱硫效率高、操作简单、适应性广等优点。
然而,湿法脱硫方法也存在一些问题。
首先,石灰乳法需大量消耗石灰石,造成资源浪费;其次,湿法脱硫方法产生大量废水,对环境造成二次污染;此外,湿法脱硫设备庞大,投资高,造成了一定的经济负担。
烟气脱硫技术的应用现状烟气脱硫技术在电力、冶金、化工和环保等领域得到广泛应用。
在电力行业,燃煤发电是主要的电力供应方式,但也是大气污染的重要来源之一。
因此,对烟气进行脱硫处理对于减少二氧化硫排放至关重要。
目前,国内外的燃煤发电厂广泛采用湿法脱硫技术。
在冶金行业,冶炼过程中产生的废气中含有大量的二氧化硫。
采用烟气脱硫技术可以有效降低废气中的二氧化硫含量,减少对环境的污染。
在化工行业,如化肥、石油化工等领域,二氧化硫是常见的废气排放物,采用烟气脱硫技术可以减少对大气的污染。
在环保行业,烟气脱硫技术也有广泛的应用。
比如,工业废气处理、污水处理等领域,烟气脱硫技术可有效减少排放的二氧化硫浓度。
烟气脱硫技术现状及展
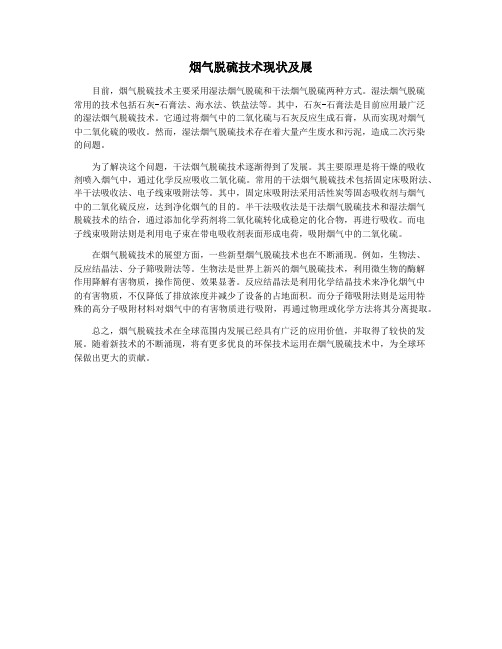
烟气脱硫技术现状及展目前,烟气脱硫技术主要采用湿法烟气脱硫和干法烟气脱硫两种方式。
湿法烟气脱硫常用的技术包括石灰-石膏法、海水法、铁盐法等。
其中,石灰-石膏法是目前应用最广泛的湿法烟气脱硫技术。
它通过将烟气中的二氧化硫与石灰反应生成石膏,从而实现对烟气中二氧化硫的吸收。
然而,湿法烟气脱硫技术存在着大量产生废水和污泥,造成二次污染的问题。
为了解决这个问题,干法烟气脱硫技术逐渐得到了发展。
其主要原理是将干燥的吸收剂喷入烟气中,通过化学反应吸收二氧化硫。
常用的干法烟气脱硫技术包括固定床吸附法、半干法吸收法、电子线束吸附法等。
其中,固定床吸附法采用活性炭等固态吸收剂与烟气中的二氧化硫反应,达到净化烟气的目的。
半干法吸收法是干法烟气脱硫技术和湿法烟气脱硫技术的结合,通过添加化学药剂将二氧化硫转化成稳定的化合物,再进行吸收。
而电子线束吸附法则是利用电子束在带电吸收剂表面形成电荷,吸附烟气中的二氧化硫。
在烟气脱硫技术的展望方面,一些新型烟气脱硫技术也在不断涌现。
例如,生物法、反应结晶法、分子筛吸附法等。
生物法是世界上新兴的烟气脱硫技术,利用微生物的酶解作用降解有害物质,操作简便、效果显著。
反应结晶法是利用化学结晶技术来净化烟气中的有害物质,不仅降低了排放浓度并减少了设备的占地面积。
而分子筛吸附法则是运用特殊的高分子吸附材料对烟气中的有害物质进行吸附,再通过物理或化学方法将其分离提取。
总之,烟气脱硫技术在全球范围内发展已经具有广泛的应用价值,并取得了较快的发展。
随着新技术的不断涌现,将有更多优良的环保技术运用在烟气脱硫技术中,为全球环保做出更大的贡献。
烟气脱硫技术现状及存在的主要问题
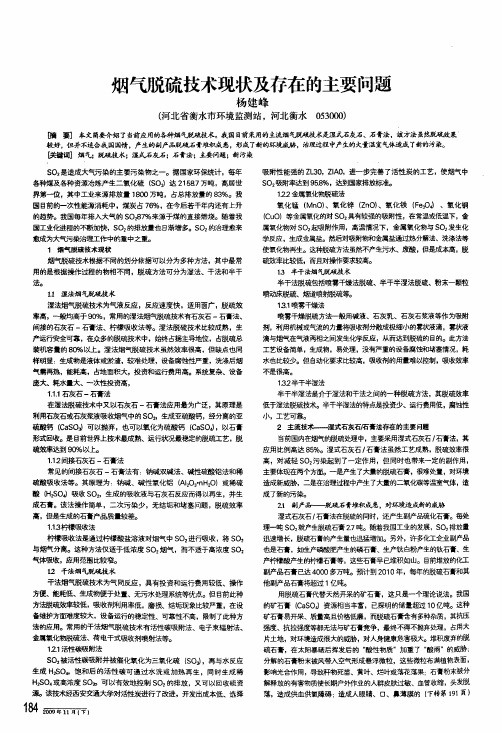
烟气脱硫技术现状及存在的主要问题杨建峰(河北省衡水市环境监测站,河北衡水053000)脯要】本文简要介绍了当前应用的各种烟气脱磁教术。
我国目前采用的主流烟气脱硫技术是湿式石灰石、石膏法。
该方法虽然脱硫效果较好,但并不适合我国国情,产生的副产品腻磁石膏堆积成患,形成了新的环境成|办,治理过程中产生的大量温室气体造成了新的污染。
瞎j键词】烟气;脱硫槛术;湿式石友石;石膏法;主要问题;新污染S O:是造成大气污染的主要污染物之一。
据国家环保统计,每年各种煤及各种资源冶炼产生二氧化硫(S02)达2158.7万吨,高居世界第—位,其中工业来源排放量1800万吨,占总排放量的83%。
我国目前的一次性能源消耗中,煤炭占76%,在今后若干年内还有上升的趋势。
我国每年排入大气的S0287%来源于煤的直接燃烧。
随着我国工业化进程的不断加快,SO:的排放量也日浙增多。
S02的治理愈来愈成为大气污染治理工作中的重中之重。
1烟气脱硫技术现状烟气脱硫技术根据不同的划分依据可以分为多种方法,其中最常用的是根据操作过程的物相不同,脱硫方法可分为湿法、干法和半干法。
1.1湿法烟气脱硫技术湿法烟气脱硫技术为气液反应,反应速度快,适用面广,脱硫效率高,—般均高于90%,常用的湿法烟气脱硫技术有石灰石一石膏法、间接的石灰石一石膏法、柠檬吸收法等。
湿法脱硫技术比较成熟,生产运行安全可靠,在众多的脱硫技术中,始终占据主导地位,占脱硫总装机容量的80%以上。
湿法烟气脱硫技术虽然效率很高,但缺点也同样明显:生成物是液体或淤渣,较难处理,设备腐蚀性严重,洗涤后烟气需再热,能耗高,占地面积大,投资和运行费用高。
系统复杂、设备庞大、耗水量大、一次性投资高,1.1.1石灰石一石膏法在湿法脱硫技术中又以石灰石一石膏法应用最为广泛,其原理是利用石灰石或石灰浆液吸收烟气中的S02,生成亚硫酸钙,经分离的亚硫酸钙(C aS03)可以抛弃,也可以氧化为硫酸钙(C aS04),以石膏形式回收。
我国燃煤烟气脱硫技术应用现状综述

Summar ize Presen t S itua tion on Applica tion of O ur Coun try Burn s Coa l Haze D esulphur iza tion Technology
WAN G X iaoΟfei, L IU Lun, RUAN YanΟjun, ZHAN G GuoΟqi
随着人类社会的不断进步与发展和人们环保意 识的增强 ,专家认为消减 SO2 排放总量是今后中国 环保工作的重点 ,烟气脱硫是目前控制二氧化硫污 染最有效和最主要的技术手段 。烟气脱硫 ( Flue Gas Desulfurization) ,即煤燃烧后脱硫 。烟气脱硫技术 [ 1 ] 主要利用各种碱性的吸收剂或吸附剂捕集烟气中的 二氧化硫将之转化为较为稳定且易机械分离的硫化 合物或单质硫 ,从而达到脱硫的目的 。根据脱硫过 程是否有 水 参 与 及 脱 硫 产 物 的 干 湿 状 态 可 分 为 湿 法 、半干法和干法烟气脱硫 [ 2 ] 。
氧化镁法烟气脱硫的基本原理是用 MgO 浆液 吸收烟气中的 SO2 , 生成含水亚硫酸镁和硫酸镁 。 该法技术成熟 、运行可靠 ,脱硫效率高 ,副产品 (如硫 酸镁 、亚硫酸镁 /硫酸镁等 )在工业生产中具有较高 的商业利用价值 ,在日本 、台湾 、东南亚得到了广泛 应用 [ 8 ] 。我国氧化镁资源丰富 ,该工艺适合我国国 情 ,具有广阔的应用前景 。尤其在中小型热电行业 是比较经济实用的一种脱硫方式 ,但要求必须对烟 气进行预先的除尘和除氯 ,而且该过程中会有少部 分 M gO 流失 ,造成二次污染 。
目前对该法的研究报道较多 ,例如 ,蒋思国 [ 4 ]以 江油脱硫工程为例 ,较详细的介绍了该脱硫方法的 特点 、原理 、工艺流程及其实际应用 ,对于引进型烟 气脱硫技术的消化吸收与在实际工程中合理应用的 结合有着借鉴和参考的意义 。禾志强等 [ 5 ]通过分析
烟气脱硫技术现状及展

烟气脱硫技术现状及展烟气脱硫技术是指通过一系列工艺措施将燃煤、燃油、焚烧垃圾等工业产品所产生的烟尘中的二氧化硫(SO2)等硫化物去除,以达到净化大气、保护环境的目的。
烟气脱硫技术的研究与发展,一直是环保领域的热点和重点。
本文将从烟气脱硫技术的现状和发展展望两方面进行探讨。
一、烟气脱硫技术现状目前,国内烟气脱硫技术已经取得了一系列成果,多种成熟的烟气脱硫装备和工艺被广泛应用于电力、钢铁、化工、建材等行业。
主要的烟气脱硫技术包括石灰石烟气脱硫技术、石膏法烟气脱硫技术和氨法烟气脱硫技术。
这些技术各有特点,适用于不同的工业界别和污染状况。
1. 石灰石烟气脱硫技术石灰石烟气脱硫技术是利用石灰石制备的吸收剂,通过干法或湿法进行烟气脱硫,形成硫酸钙或硫酸镁等产物,实现二氧化硫的去除。
这种技术工艺简单,成本较低,但存在着对设备耐腐蚀性和处理后废渣处理的问题。
石膏法烟气脱硫技术是在石灰石脱硫的基础上,再将形成的硫酸钙与二氧化硫混合反应生成石膏并进行分离回收利用。
这种技术能够减少废渣量,但同样需要对废渣进行处理,且对循环泵、过滤机等设备要求严格。
氨法烟气脱硫技术利用氨水或氨气与二氧化硫进行反应生成硫化氢,再与空气或氧气氧化生成硫酸,从而实现二氧化硫的脱除。
这种技术能够实现高效脱硫,但需要关注氨气外泄和废水处理等环保问题。
以上三种主要的烟气脱硫技术在中国都有着广泛的应用,而且在技术革新、设备更新等方面也有了长足的进步。
还有部分新兴的脱硫技术,比如活性炭脱硫技术、氧化钙法等,也在逐步发展和应用之中。
尽管当前烟气脱硫技术已经取得了许多成果,但在环保要求日益严格的情况下,还存在一些问题和挑战,比如节能减排、废渣处理和资源综合利用等方面的技术难题。
未来烟气脱硫技术将主要集中在以下几个方面的发展:1. 高效节能技术目前烟气脱硫过程中能耗较高,需要大量的吸收剂和能源。
未来需要优化脱硫工艺,减少吸收剂消耗和能源消耗,实现绿色低碳的脱硫过程。
我国烟气脱硫工艺技术发展现状和趋势
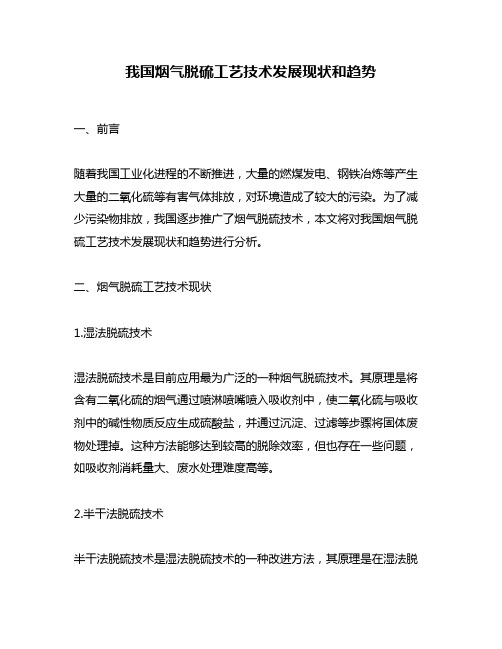
我国烟气脱硫工艺技术发展现状和趋势一、前言随着我国工业化进程的不断推进,大量的燃煤发电、钢铁冶炼等产生大量的二氧化硫等有害气体排放,对环境造成了较大的污染。
为了减少污染物排放,我国逐步推广了烟气脱硫技术,本文将对我国烟气脱硫工艺技术发展现状和趋势进行分析。
二、烟气脱硫工艺技术现状1.湿法脱硫技术湿法脱硫技术是目前应用最为广泛的一种烟气脱硫技术。
其原理是将含有二氧化硫的烟气通过喷淋喷嘴喷入吸收剂中,使二氧化硫与吸收剂中的碱性物质反应生成硫酸盐,并通过沉淀、过滤等步骤将固体废物处理掉。
这种方法能够达到较高的脱除效率,但也存在一些问题,如吸收剂消耗量大、废水处理难度高等。
2.半干法脱硫技术半干法脱硫技术是湿法脱硫技术的一种改进方法,其原理是在湿法脱硫的基础上加入干燥剂,将烟气中的水分减少,从而减少废水产生量。
这种方法对吸收剂的消耗量也有所降低。
3.干法脱硫技术干法脱硫技术是将含有二氧化硫的烟气通过干式吸附剂进行处理,其原理是利用吸附剂对二氧化硫进行吸附,再通过振动、筛分等步骤将固体废物处理掉。
这种方法能够达到较高的脱除效率,并且不产生废水,但吸附剂消耗量大、能耗高等问题也需要解决。
三、烟气脱硫工艺技术发展趋势1.多元化发展目前我国烟气脱硫工艺技术主要以湿法为主,但随着环保要求的提高和新型材料、新型设备等技术的不断发展,未来烟气脱硫工艺技术将会逐步多元化发展,包括湿法、半干法、干法等多种形式。
2.低成本高效率目前烟气脱硫工艺技术中存在吸收剂消耗大、能耗高等问题,未来的发展趋势将会是低成本高效率的方向。
例如,采用新型吸收剂、新型设备等技术可以有效降低成本和能耗。
3.智能化发展未来烟气脱硫工艺技术还将会向智能化方向发展。
通过引入先进的控制系统和自动化设备,实现对整个脱硫过程的智能监测和控制,提高生产效率和产品质量。
四、结论总体来看,我国烟气脱硫工艺技术已经取得了较大的进展,在未来的发展中将会逐步多元化、低成本高效率、智能化发展。
烟气脱硫脱硝技术现状及分析

65一、烟气脱硫脱销技术应用现状1.活性焦一体化脱硫脱硝技术这种技术在使用的时候,需要设置两级塔结构,一、二两级分别为脱硫和脱硝塔,前者主要是利用活性焦较高的比表面积和其内部的丰富的空隙结构,在有效吸附SO 2的同时,将绝大部分的颗粒物进行去除,这些经过脱硫塔处理的烟气便可进入到脱硝塔中,并在活性焦的催化作用下,使用NH 3将NOx还原成无害的氮气。
该项技术在实际的使用环节中,可以将烟气的流动方向作为基础划分为错流和逆流两种形式。
前者则是烟气在水平进入到一级塔之后,通过横穿移动的活性焦床层完成烟气的脱硫除尘操作,随后这些气体在二级塔的入口和稀释的氨气混合之后,进入到二级塔内进行催化还原脱硝处理,活性焦在吸附SO 2气体达到饱和状态的时候则需要通过加热解析,用于回收浓度较高的SO 2气体制备硫酸。
后者则是在烟气进入到模块移动床吸附塔内之后,位于其内的活性焦依赖重力从脱硝塔顶端降到脱硫塔的底端,烟气以一种自下而上的状态先通过脱硫塔,同样实现脱硫除尘处理,此后进入到脱硝塔内的处理与前者完全一致。
这一技术的实际脱硫和脱硝效率可以分别达到98%和85%。
这种技术虽然实现了副产物的大幅度回收利用目标,并且也做到了同时处理其他污染物,但是成本投入较为巨大,并且能耗较高也很容易带来自燃问题,其制酸废水的处理也是一个巨大痛点。
2.半干法脱硫和中低温SCR脱硝技术组合选择性的催化还原脱硝技术,是指在催化剂的作用下,还原剂可以在280~400℃的范围内,有选择性的将NO、NO 2还原成N 2、H 2O,这一技术简称就是SCR。
而作为SCR技术核心的催化剂,则成为了烟气脱硝技术中的关键。
一般情况下,使用的催化剂体系是钒钛基催化剂,其活性温度的窗口相对较高,使其在脱硝技术中得到了较为广泛的应用,并取得了十分良好的效果。
这种烟气脱硫脱硝处理工艺主要是使用半干法脱硫和中温SCR的组合,半干法脱硫和湿法脱硫相比,温度下降方面相对较小,但是需要在脱硝塔之前,设置相应的烟气换热装置和燃用高炉煤气的烟气升温装置,从而保障烟气的温度,可以达到中温催化剂的活性窗口阈值,除此之外,还需要将烟气的回转气使换热器添加在SCR的反应器之后,从而确保脱硝后的烟气余热可以进一步用于脱硝前的烧结烟气的加热,做到有效的回收和利用烟气余热。
烟气脱硫技术现状及展

烟气脱硫技术现状及展烟气脱硫技术是指利用化学方法或物理方法去除燃烧过程中产生的二氧化硫等有害气体的技术。
随着环保意识的提高和政府对环境保护的重视,烟气脱硫技术的研究和应用得到了广泛的关注。
本文将对烟气脱硫技术的现状进行分析,并展望其未来发展。
烟气脱硫技术的现状主要可以从技术原理、应用领域和发展趋势三个方面进行分析。
技术原理方面,烟气脱硫技术主要包括干法脱硫和湿法脱硫两种方法。
干法脱硫是指将固体吸收剂喷入烟气中,通过干法吸收硫化物,再进行后续处理得到硫酸盐。
湿法脱硫是指将含有碱性溶液的吸收剂喷洒在烟气中,通过化学反应将二氧化硫转化为硫酸盐。
这两种方法各有优劣,干法脱硫适用于高温大气流量条件下,对吸收剂的选择要求高;湿法脱硫适用于低温小气流量条件下,处理效果稳定。
在应用领域方面,烟气脱硫技术主要应用于燃煤电厂、钢铁厂、石化厂等工业领域。
燃煤电厂是二氧化硫的主要排放源,因此烟气脱硫技术在燃煤电厂中得到了广泛的应用。
钢铁厂和石化厂等工业领域也是二氧化硫排放的重要来源,因此烟气脱硫技术在这些领域也有较大的市场需求。
在发展趋势方面,随着环保法规的日益严格和能源结构的调整,烟气脱硫技术将迎来更多的机遇和挑战。
一方面,政府对环境保护的政策支持将推动烟气脱硫技术的进一步应用。
随着新能源的发展和清洁能源的使用,燃煤电厂的数量和排放量将逐渐减少,这将对烟气脱硫技术的市场需求产生一定影响。
从以上分析可以看出,烟气脱硫技术的现状呈现出技术不断进步、应用领域逐渐扩大、发展趋势向着清洁化和高效化方向发展的特点。
在未来的发展中,烟气脱硫技术将面临以下几个方面的挑战和机遇:随着国家环保法规的不断完善和严格执行,对排放标准的要求将越来越高,这将需要烟气脱硫技术不断创新和提升,以满足市场需求。
随着环保意识的提高和清洁能源的推广,燃煤电厂等传统能源行业的发展将面临转型和调整,这将带动烟气脱硫技术在清洁能源行业中的应用。
随着科技的进步和经济的发展,烟气脱硫技术的成本将逐渐降低,这将增加其在中小型企业和新兴产业中的应用。
我国燃煤电厂烟气脱硫技术现状及发展趋势
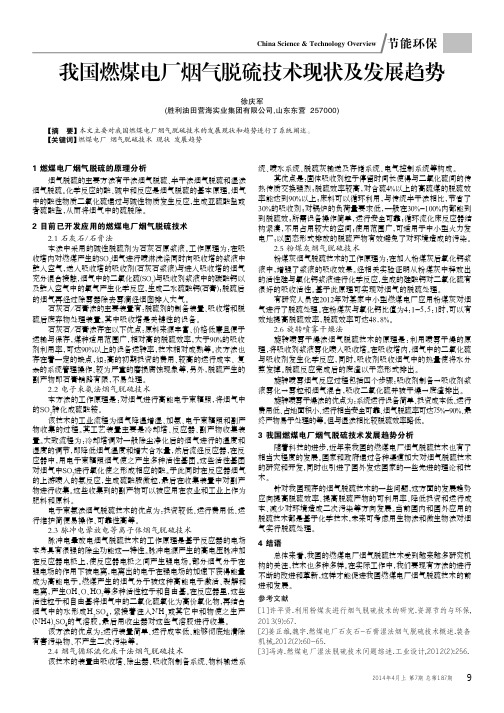
92014年4月上 第7期 总第187期1 燃煤电厂烟气脱硫的原理分析烟气脱硫的主要方法有干法烟气脱硫、半干法烟气脱硫和湿法烟气脱硫。
化学反应的酸、碱中和反应是烟气脱硫的基本原理。
烟气中的酸性物质二氧化硫通过与碱性物质发生反应,生成亚硫酸盐或者硫酸盐,从而将烟气中的硫脱除。
2 目前已开发应用的燃煤电厂烟气脱硫技术2.1 石灰石/石膏法本法中采用的碱性脱硫剂为石灰石原浆液。
工作原理为:在吸收塔内对燃煤产生的SO 2烟气进行喷淋洗涤同时向吸收塔的浆液中鼓入空气,送入吸收塔的吸收剂(石灰石浆液)与进入吸收塔的烟气充分混合接触,烟气中的二氧化硫(SO 2)与吸收剂浆液中的碳酸钙以及鼓入空气中的氧气产生化学反应,生成二水硫酸钙(石膏);脱硫后的烟气再经过除雾器除去雾滴经烟囱排入大气。
石灰石/石膏法的主要装置有:脱硫剂的制备装置、吸收塔和脱硫后废弃物处理装置。
其中吸收塔是关键性的设备。
石灰石/石膏法存在以下优点:原料来源丰富、价格低廉且便于运输与保存,煤种适用范围广,相对高的脱硫效率,大于90%的吸收剂利用率,可达90%以上的设备运转率,技术相对成熟等。
次方法也存在着一定的缺点,如:高的初期投资的费用、较高的运行成本、 复杂的系统管理操作、较为严重的磨损腐蚀现象等,另外,脱硫产生的副产物即石膏销路有限,不易处理。
2.2 电子束氨法烟气脱硫技术本方法的工作原理是:对烟气进行高能电子束辐照,将烟气中的SO 2转化成硫酸铵。
该技术的工业流程为烟气降温增湿、加氨、电子束辐照和副产物收集的过程。
其工艺装置主要是冷却塔、反应器、副产物收集装置。
大致流程为:冷却塔调对一般除尘净化后的烟气进行的温度和湿度的调节,即降低烟气温度和增大含水量,然后流经反应器,在反应器中,用电子束辐照烟气使之产生多种活性基团。
这些活性基团对烟气中SO 2进行氧化使之形成相应的酸。
于此同时在反应器烟气的上游喷入的氨反应,生成硫酸胺微粒,最后在收集装置中对副产物进行收集。
中国脱硫技术的现状与对策
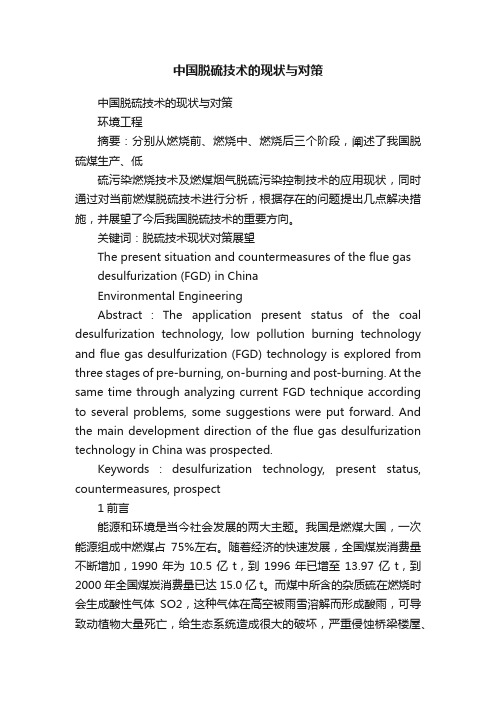
中国脱硫技术的现状与对策中国脱硫技术的现状与对策环境工程摘要:分别从燃烧前、燃烧中、燃烧后三个阶段,阐述了我国脱硫煤生产、低硫污染燃烧技术及燃煤烟气脱硫污染控制技术的应用现状,同时通过对当前燃煤脱硫技术进行分析,根据存在的问题提出几点解决措施,并展望了今后我国脱硫技术的重要方向。
关键词:脱硫技术现状对策展望The present situation and countermeasures of the flue gasdesulfurization (FGD) in ChinaEnvironmental EngineeringAbstract:The application present status of the coal desulfurization technology, low pollution burning technology and flue gas desulfurization (FGD) technology is explored from three stages of pre-burning, on-burning and post-burning. At the same time through analyzing current FGD technique according to several problems, some suggestions were put forward. And the main development direction of the flue gas desulfurization technology in China was prospected.Keywords:desulfurization technology, present status, countermeasures, prospect1前言能源和环境是当今社会发展的两大主题。
烟气脱硫技术的现状分析与应用

烟气脱硫技术的现状分析与应用烟气脱硫技术的现状分析与应用烟气脱硫技术是一种处理工业烟气中二氧化硫污染物的方法,广泛应用于燃煤发电、钢铁冶炼、化工和石油炼制等行业。
随着环境保护意识的提高和政府对大气污染防治的重视,烟气脱硫技术的研究和应用越来越受到关注。
本文将对烟气脱硫技术的现状进行分析,并探讨其在工业生产中的应用情况。
一、烟气脱硫技术的现状分析1.常见的烟气脱硫技术目前常见的烟气脱硫技术主要包括湿法烟气脱硫和干法烟气脱硫两大类。
湿法烟气脱硫技术是指将脱硫剂溶解在水中,通过喷洒或浸泡等方式将湿润的脱硫剂与烟气进行接触反应,以达到脱硫的目的。
浆式脱硫和石灰石熄焦水脱硫是湿法烟气脱硫技术的代表。
干法烟气脱硫技术则是指将脱硫剂直接喷洒在烟气中,使其与烟气中的污染物进行接触反应,并达到脱硫的效果。
干法电除尘除湿工艺和反应器内喷射层状脱硫技术是干法烟气脱硫技术的主要代表。
2.烟气脱硫技术的优缺点湿法烟气脱硫技术具有脱硫效率高、适用范围广的优点。
它能够同时去除烟气中的二氧化硫和氮氧化物等多种污染物,并且对烟气中的微尘也有较好的去除效果。
湿法烟气脱硫技术的脱硫效率可以达到90%以上,且对烟气中的颗粒物也有较好的去除效果。
但是,湿法烟气脱硫技术存在着酸性废水的产生、设备占地面积大、设备运行成本高等缺点。
干法烟气脱硫技术具有设备结构简单、设备占地面积小、设备运行成本低的优点。
干法烟气脱硫技术的脱硫效率可以达到80%以上,且对烟气中的微尘有较好的去除效果。
但是,干法烟气脱硫技术对烟气中的水分和温度要求较高,且不能同时去除烟气中的氮氧化物和颗粒物。
二、烟气脱硫技术的应用状况1.燃煤发电行业燃煤发电是重要的能源供应方式之一,但同时也是重要的大气污染源。
据统计,我国的燃煤发电行业占全国工业二氧化硫排放总量的50%以上。
为了减少燃煤发电对大气环境的污染,大规模应用烟气脱硫技术势在必行。
目前,我国在燃煤发电行业普遍采用湿法烟气脱硫技术。
我国火电厂烟气脱硫工艺现状及发展综述

我国火电厂烟气脱硫工艺现状及发展综述摘要:我国的电力企业一直以来都是以火电为主,电气企业所产生的污染物是空气中的硫化物质的污染的主要来源,随着我国的经济发展以及对电量的需求的不断增加,我国的空气质量面对着很大的挑战。
本文将针对现在我国的火电厂烟气脱硫工艺的现状,对于现在我国的火电厂的烟气脱硫工艺进行一定的分析和比较,从而对我国的火电厂的脱硫工艺的现状及其发展做出一定的分析。
关键词:烟气脱硫火电厂现状及发展1、火电厂烟气脱硫技术发展的必要性1.1 我国火电厂排放so2对环境造成了严重的危害众所周知,二氧化硫是我国大气环境污染的一个重要的原因,其最突出的表现就是引起了我国的酸雨的危害。
酸雨对环境的危害主要表现在酸雨可以引起森林的退化以及湖泊的酸化,早成湖泊中的鱼类死亡,其中的水生生物的生物种类减少,对农业来讲可以造成农田的酸化,从而使得农田的产量减少,土地变得贫瘠,并且还会加重农田中的有毒重金属的污染的危害,粮食和蔬菜等等的农作物在这样的环境下会大量的减产,并且还会造成农作物的产品中含有大量的重金属等等的成分,使得产品本身带有一定的毒性。
对于建筑来讲,酸雨可以腐蚀建筑物和桥梁等等,很多的建筑物在酸雨过后变得面目全非。
酸雨还可以引起人们的疾病,人类在直接接触到了酸雨之后会患上很多种疾病,比如说对酸物质比较敏感的眼睛还有呼吸系统等等的疾病。
酸雨或者是酸雾对这些系统都有很强的腐蚀作用。
所以酸雨对人们的生产和生活都有很大的影响。
在我国,酸雨的腐蚀性主要的有瘾就是燃烧煤炭产生的各种硫化物质的排放,在我国的各个省市自治区中,不同的地域之间可以互相引起酸雨的危害,并且直接危害到人民的生产安全。
在我国的国土面积中,有一半左右的土地受到了酸雨的危害,在我国的很多的城市中也面临着酸雨的危害,很多的城市在经受了酸雨过后,很多的建筑物还有公共服务设施遭到了破坏,直接影响到了人们的正常生活。
在我国,酸雨的主要分布区为长江以南的我国的大部分的南方地区,主要的省市为我国的广东省、福建省、浙江省、江苏省还有四川省、湖北省以及安徽上海等等地方。
烟气脱硫技术现状及展
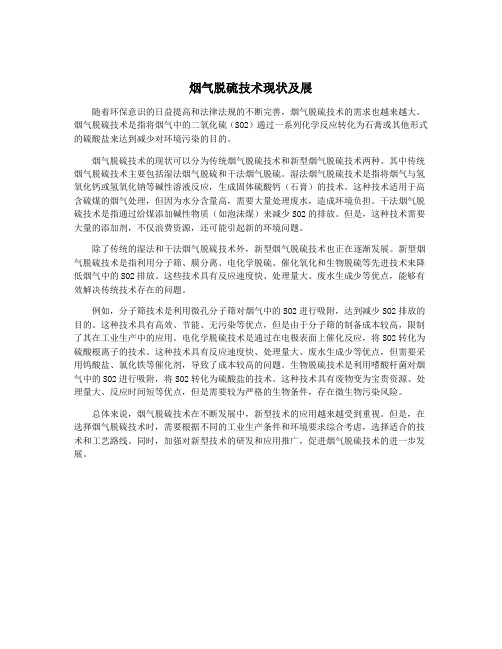
烟气脱硫技术现状及展随着环保意识的日益提高和法律法规的不断完善,烟气脱硫技术的需求也越来越大。
烟气脱硫技术是指将烟气中的二氧化硫(SO2)通过一系列化学反应转化为石膏或其他形式的硫酸盐来达到减少对环境污染的目的。
烟气脱硫技术的现状可以分为传统烟气脱硫技术和新型烟气脱硫技术两种。
其中传统烟气脱硫技术主要包括湿法烟气脱硫和干法烟气脱硫。
湿法烟气脱硫技术是指将烟气与氢氧化钙或氢氧化钠等碱性溶液反应,生成固体硫酸钙(石膏)的技术。
这种技术适用于高含硫煤的烟气处理,但因为水分含量高,需要大量处理废水,造成环境负担。
干法烟气脱硫技术是指通过给煤添加碱性物质(如泡沫煤)来减少SO2的排放。
但是,这种技术需要大量的添加剂,不仅浪费资源,还可能引起新的环境问题。
除了传统的湿法和干法烟气脱硫技术外,新型烟气脱硫技术也正在逐渐发展。
新型烟气脱硫技术是指利用分子筛、膜分离、电化学脱硫、催化氧化和生物脱硫等先进技术来降低烟气中的SO2排放。
这些技术具有反应速度快、处理量大、废水生成少等优点,能够有效解决传统技术存在的问题。
例如,分子筛技术是利用微孔分子筛对烟气中的SO2进行吸附,达到减少SO2排放的目的。
这种技术具有高效、节能、无污染等优点,但是由于分子筛的制备成本较高,限制了其在工业生产中的应用。
电化学脱硫技术是通过在电极表面上催化反应,将SO2转化为硫酸根离子的技术。
这种技术具有反应速度快、处理量大、废水生成少等优点,但需要采用钨酸盐、氯化铁等催化剂,导致了成本较高的问题。
生物脱硫技术是利用嗜酸杆菌对烟气中的SO2进行吸附,将SO2转化为硫酸盐的技术。
这种技术具有废物变为宝贵资源、处理量大、反应时间短等优点,但是需要较为严格的生物条件,存在微生物污染风险。
总体来说,烟气脱硫技术在不断发展中,新型技术的应用越来越受到重视。
但是,在选择烟气脱硫技术时,需要根据不同的工业生产条件和环境要求综合考虑,选择适合的技术和工艺路线。
烟气脱硫技术的发展现状与趋势
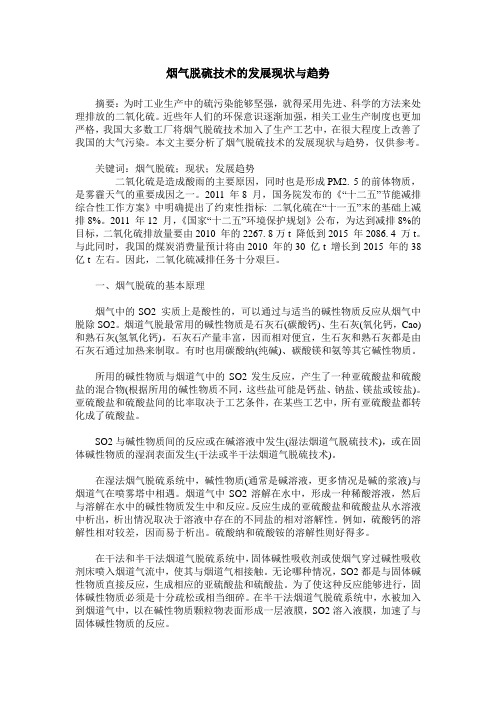
烟气脱硫技术的发展现状与趋势摘要:为时工业生产中的硫污染能够坚强,就得采用先进、科学的方法来处理排放的二氧化硫。
近些年人们的环保意识逐渐加强,相关工业生产制度也更加严格,我国大多数工厂将烟气脱硫技术加入了生产工艺中,在很大程度上改善了我国的大气污染。
本文主要分析了烟气脱硫技术的发展现状与趋势,仅供参考。
关键词:烟气脱硫;现状;发展趋势二氧化硫是造成酸雨的主要原因,同时也是形成PM2. 5的前体物质,是雾霾天气的重要成因之一。
2011 年8 月,国务院发布的《“十二五”节能减排综合性工作方案》中明确提出了约束性指标: 二氧化硫在“十一五”末的基础上减排8%。
2011 年12 月,《国家“十二五”环境保护规划》公布,为达到减排8%的目标,二氧化硫排放量要由2010 年的2267. 8万t 降低到2015 年2086. 4 万t。
与此同时,我国的煤炭消费量预计将由2010 年的30 亿t 增长到2015 年的38 亿t 左右。
因此,二氧化硫减排任务十分艰巨。
一、烟气脱硫的基本原理烟气中的SO2 实质上是酸性的,可以通过与适当的碱性物质反应从烟气中脱除SO2。
烟道气脱最常用的碱性物质是石灰石(碳酸钙)、生石灰(氧化钙,Cao)和熟石灰(氢氧化钙)。
石灰石产量丰富,因而相对便宜,生石灰和熟石灰都是由石灰石通过加热来制取。
有时也用碳酸纳(纯碱)、碳酸镁和氨等其它碱性物质。
所用的碱性物质与烟道气中的SO2发生反应,产生了一种亚硫酸盐和硫酸盐的混合物(根据所用的碱性物质不同,这些盐可能是钙盐、钠盐、镁盐或铵盐)。
亚硫酸盐和硫酸盐间的比率取决于工艺条件,在某些工艺中,所有亚硫酸盐都转化成了硫酸盐。
SO2与碱性物质间的反应或在碱溶液中发生(湿法烟道气脱硫技术),或在固体碱性物质的湿润表面发生(干法或半干法烟道气脱硫技术)。
在湿法烟气脱硫系统中,碱性物质(通常是碱溶液,更多情况是碱的浆液)与烟道气在喷雾塔中相遇。
烟道气中SO2溶解在水中,形成一种稀酸溶液,然后与溶解在水中的碱性物质发生中和反应。
烟气脱硫技术的发展现状与趋势
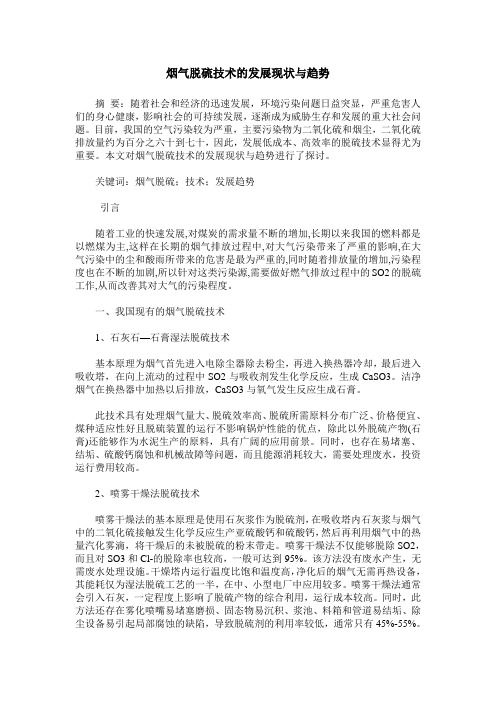
烟气脱硫技术的发展现状与趋势摘要:随着社会和经济的迅速发展,环境污染问题日益突显,严重危害人们的身心健康,影响社会的可持续发展,逐渐成为威胁生存和发展的重大社会问题。
目前,我国的空气污染较为严重,主要污染物为二氧化硫和烟尘,二氧化硫排放量约为百分之六十到七十,因此,发展低成本、高效率的脱硫技术显得尤为重要。
本文对烟气脱硫技术的发展现状与趋势进行了探讨。
关键词:烟气脱硫;技术;发展趋势引言随着工业的快速发展,对煤炭的需求量不断的增加,长期以来我国的燃料都是以燃煤为主,这样在长期的烟气排放过程中,对大气污染带来了严重的影响,在大气污染中的尘和酸雨所带来的危害是最为严重的,同时随着排放量的增加,污染程度也在不断的加剧,所以针对这类污染源,需要做好燃气排放过程中的SO2的脱硫工作,从而改善其对大气的污染程度。
一、我国现有的烟气脱硫技术1、石灰石—石膏湿法脱硫技术基本原理为烟气首先进入电除尘器除去粉尘,再进入换热器冷却,最后进入吸收塔,在向上流动的过程中SO2与吸收剂发生化学反应,生成CaSO3。
洁净烟气在换热器中加热以后排放,CaSO3与氧气发生反应生成石膏。
此技术具有处理烟气量大、脱硫效率高、脱硫所需原料分布广泛、价格便宜、煤种适应性好且脱硫装置的运行不影响锅炉性能的优点,除此以外脱硫产物(石膏)还能够作为水泥生产的原料,具有广阔的应用前景。
同时,也存在易堵塞、结垢、硫酸钙腐蚀和机械故障等问题,而且能源消耗较大,需要处理废水,投资运行费用较高。
2、喷雾干燥法脱硫技术喷雾干燥法的基本原理是使用石灰浆作为脱硫剂,在吸收塔内石灰浆与烟气中的二氧化硫接触发生化学反应生产亚硫酸钙和硫酸钙,然后再利用烟气中的热量汽化雾滴,将干燥后的未被脱硫的粉末带走。
喷雾干燥法不仅能够脱除SO2,而且对SO3和Cl-的脱除率也较高,一般可达到95%。
该方法没有废水产生,无需废水处理设施。
干燥塔内运行温度比饱和温度高,净化后的烟气无需再热设备,其能耗仅为湿法脱硫工艺的一半,在中、小型电厂中应用较多。
- 1、下载文档前请自行甄别文档内容的完整性,平台不提供额外的编辑、内容补充、找答案等附加服务。
- 2、"仅部分预览"的文档,不可在线预览部分如存在完整性等问题,可反馈申请退款(可完整预览的文档不适用该条件!)。
- 3、如文档侵犯您的权益,请联系客服反馈,我们会尽快为您处理(人工客服工作时间:9:00-18:30)。
我国烟气脱硫技术现状综述我国烟气脱硫技术现状综述——工业脱硫技术姓名:李凯雷学号: 20081400班级:2008027我国烟气脱硫技术现状综述高浓度SO2烟气脱硫技术大规模工业化应用,SO2含量高于3%的烟气,通常称为高浓度二氧化硫烟气。
它可采用钒催化剂接触催化制硫酸等方法脱硫回收利用硫资源。
目前,我国基本上都已采用催化转化脱硫制酸,不仅有效地控制了二氧化硫污染,而且使冶炼烟气二氧化硫成为重要的硫资源,补充了我国缺乏的硫资源。
低浓度SO2烟气脱硫技术的工业化应用处于起步阶段,SO2含量低于3%的烟气,通常称为低浓度二氧化硫烟气。
我国2亿kW机组火电厂锅炉烟气及钢铁、有色、建材等部门50万台工业锅炉、18万台工业窑炉排放的主要是这类烟气。
由于烟气中的二氧化硫浓度低(一般仅为0.1%~0.5%),采用传统的接触法脱硫制酸等方法,技术经济上难度大。
目前我国这类烟气的脱硫技术工业化应用程度还很低,已应用的主要是引进的国外烟气脱硫装置和中小锅炉简易除尘脱硫装置。
从20世纪70年代后期,我国先后从国外引进烟气脱硫装置,包括“氨-硫铵法”烟气脱硫装置、“碱式硫酸铝法”烟气脱硫装置、“湿式石灰石-石膏法”烟气脱硫装置、“旋转喷雾干燥法”脱硫装置和“电子束辐照法”装置。
这些烟气脱硫装置的引进为我国烟气脱硫吸收国外先进成熟的技术奠定了基础。
我国中小锅炉占全国燃煤锅炉的70%,为此我国探索中小型燃煤锅炉二氧化硫污染控制多种途径,如低硫燃料、型煤固硫等技术的同时,针对中小锅炉特点,开发了一批简易烟气脱硫技术。
目前这类技术申请的专利已达几十种,应用数百套。
简易烟气脱硫除尘技术一般是在各类除尘设备的基础上,采用石灰、冲渣水等碱性浆液为固硫剂,应用水膜除尘、文丘里除尘、旋风除尘的机理和旋流塔、筛板塔、鼓泡塔、喷雾塔吸收等机理相结合同时除尘脱硫。
已形成冲激旋风除尘脱硫技术、湿式旋风除尘脱硫技术、麻石水膜除尘脱硫技术、脉冲供电除尘脱硫技术、多管喷雾除尘脱硫技术、喷射鼓泡除尘脱硫技术等在同一设备内进行除尘脱硫的烟气脱硫技术,其共同特点是设备少、流程短、操作简便,一般除尘效率70%~90%,脱硫效率30%~80%。
我国从70年代开始引进国外烟气脱硫成套装置,但到目前为止,却仅有不到1%装机容量的火力电厂和少数中小型锅炉实施烟气脱硫。
主要有脱硫成本问题、产物出路问题以及引进技术国产化的问题。
由国外引进的烟气脱硫装置,设备投资和运行费用高,如我国重庆珞璜电厂引进的“石灰石-石膏法”烟气脱硫装置,投资约4000万美元,每年还需运行费4000万元人民币,脱硫运行成本为每吨SO21100元,设备建设费用占到了电厂投资的16%。
另一方面,国内外目前应用的主要烟气脱硫技术,无论是国外引进的“石灰石-石膏法”、“旋转喷雾干燥法”,还是国内的简易脱硫除尘一体化技术,都存在因产物无出路,不得不作为固体废弃物抛弃的问题。
如重庆珞璜电厂一期工程,每年就有25万t固体物排放。
近年来,我国在发展烟气脱硫技术方面有了较快进展。
提倡以“湿式石灰石-石膏法”为主引进国外烟气脱硫技术并通过国产化制造烟气脱硫装置,降低烟气脱硫装置建设投资、减小脱硫成本的呼声甚高。
通过国外先进烟气脱硫技术的国产化来加速我国烟气脱硫。
(1)虽然水泥的堆积密度随其堆积紧密程度变化而变化,不是很稳定,但是在一定的操作制度下进行试验所得的结果还是可以接受的, 从自然的松散堆积状态逐渐敲击容器底部,在没有外界干扰的情况下,水泥堆积密度在敲击次数为500次(这一数据与锤子和容器的匹配有关)时是比较稳定的了。
(2)试验所测得的普通砂的表观密度与传统排水法测得的结果很接近,二者平均值相差不到0.01g/cm3。
对普通砂和陶砂的表观密度测试结果中,两次测试结果相差均没有超过0.02g/cm3,可以满足集料测试中规定的两次测试结果不得大于0.02g/cm3或平均值2%的要求。
从表4的结果看,用参考文献[2]规程中的方法三次试验结果中,最大值和最小值相差0.062g/cm3,就不能满足要求了,笔者认为这是陶砂表面面干状态很难受人为控制所造成的。
(3)从本方法测试吸水率的过程看出,本操作方法是非常客观,且易行的。
本方法测试吸水率的方法所测得的结果离散性比较小,说明试验操作受人为影响小,因此用本方法测试吸水率能较好的满足要求。
相对来说,用参考文献[2]规程中的测陶粒吸水率的方法测试的结果离散性就大多了,从表4的结果来看,同样的试样1h 吸水率最大值和最小值相差达 1.24%,而且其试验操作也很困难硫的进程是必要的,但不是唯一选择。
在烟气脱硫的发展道路上有两个误区。
“引进、引进、再引进”的误区国内外技术发展的经验告诉我们,发展中国家由于技术落后于发达国家,往往采取“从国外发达国家购买产品,从国外购买引进生产设备,将引进生产设备进行国产化”的道路。
但这种一度被认为是提高发展中国家技术水平正确的道路,有一显著的负效应,就是它导致发展中国家的技术陷入“引进、引进、再引进”的困境,技术水平永远落后于发达国家。
“盲目照搬”的误区国外发达国家成功应用烟气脱硫技术解决了二氧化硫污染问题。
但他们实行的是高投入、高消耗解决二氧化硫污染的模式,烟气脱硫装置投资达150~280美元/kW,脱硫成本为每tSO2350~600美元。
我国的经济状况决定了我国不能照搬国外发达国家高投入、高消耗的烟气脱硫模式。
而我国人均土地资源有限,又是一个硫磺等资源缺乏,但天然石膏资源丰富的国家,因而美、日、德等发达国家脱硫副产物出路的解决方式难以在我国应用。
湿法脱硫工艺是目前世界上应用最多、最为成熟的技术,固硫剂价廉易得,副产物便于利用,煤种适应范围宽,并有较大幅度降低工程造价的可能性。
目前单机容量在20万kW以上的火电机组容量占火电总装机容量的55%,高参数、大容量火电机组是当前和今后相当长时间内火电发展的方向。
因此,大机组脱硫是火电厂脱硫的工作重点,是控制火电厂SO2的关键,而湿法脱硫工艺是当前国际上通行的大机组火电厂烟气脱硫的基本工艺,所以,我国应重点发展湿法脱硫技术。
烟气循环流化床脱硫工艺脱硫效率高,建设投资较省,占地面积较少,在能满足高品位石灰供应和妥善处理脱硫灰的条件下,具有较好的发展前景,尤其适用于中小机组和老机组的脱硫改造。
喷雾干燥法脱硫、炉内喷钙尾部增湿活化脱硫、海水脱硫、电子束脱硫等脱硫工艺在国内已有示范项目,要认真总结示范项目的经验,结合当地实际情况充分论证,进行合理消化利用。
炉内喷钙和复合固硫剂结合起来,向炉内直接喷入效果较好的复合固硫剂,即复合固硫剂炉内喷射脱硫工艺,可比LIFAC工艺省去活化塔的巨大投资,在大大降低了成本的情况下,稍微降低了脱硫率,这样既可以把资金应用到多台机组的技术改造当中去,又可以满足环保的要求。
2我国烟气脱硫技术现状我国的烟气脱硫技术研究开发工作始于上世纪60年代,当时主要是围绕有色冶金废气和硫酸尾气的净化和硫酸回收利用项目进行的,从二氧化硫浓度高于0.5%烟气回收硫,供氮肥厂生产硫酸胺,既可减少S认对大气的污染,又可以回收我国资源不丰富的硫,项目比较成功,并已建成了一批工业化规模装置投人运行。
与此同时也有一些科研院所和高等院校进行了电厂脱硫技术的探索,主要进行了干法、湿法和半干法等烟气脱硫技术研究,并先后在上海杨浦电厂、上海闸北电厂、四川白马电厂、豆坝电厂、湖南三厂及松木坪电厂,进行了示范项目建设。
上世纪80年代开始,国家有关部门有计划有选择地引进了一些烟气脱硫技术,建成一批工业脱硫装置和大型工业示范性工程,如重庆路磺电厂石灰石一石膏烟气脱硫、太原第一热电厂简易湿式石灰石一石膏烟气脱硫、山东黄岛电厂旋转喷雾干燥脱硫、深圳西部电厂海水烟气脱硫、南京下关电厂炉内喷钙尾部增湿活化脱硫、成都热电厂电子束脱等,我国的电厂烟气脱硫才开始走上了发展轨道。
另一方面,为了鼓励开发适合国情的脱硫技术,国家科技部一直安排脱硫专项经费支持科研院所和高校进行脱硫技术开发,一些机构也先后开发出了一些具有自主知识产权的烟气脱硫技术,当然这些技术因各种原因还尚未得到广泛应用,但有很好的应用前景。
不过尽管我国的脱硫技术研发很早,但由于种种原因发展很慢,完全跟不上国外先进国家的步伐,目前的脱硫技术总体上很落后。
我国投运、在建和已经签订合同的引进烟气脱硫技术中,石灰石一石膏湿法烟气脱硫技术约占90%以上,这些脱硫项目均是依靠国内的一些专业脱硫公司来实施。
据统计,我国拥有10万kw及以上机组烟气脱硫工程总承包业绩的公司超过了50家,合同容量超过1000万kw装机的公司也有10家,我国的烟气脱硫产业已初步具备了年承担近亿kw装机脱硫工程设计、设备制造及总承包能力。
另一方面,我国的一些大型专业脱硫公司通过技术引进、消化、吸收和再创新,已开发出了一些具有自主知识产权的湿法脱硫技术。
如中电投远达环保工程有限公司、苏源环保工程股份有限公司、北京国电龙源环保工程有限公司分别开发了YDesBSP、01及龙源湿法烟气脱硫技术,并已成功应用于南阳电厂2义300MW烟气脱硫工程、太仓港环保发电有限公司二期2只300MW烟气脱硫工程、江阴苏龙发电有限公司三期2x330MW烟气脱硫工程。
这些采用国产脱硫技术的项目造价低,目前在200一30。
元/kW左右,而且这些项目根据我国燃煤含硫量高、石灰石品质差等特点进行设计,整体效果也比较好。
近年来我国的脱硫工作取得了很大成绩,脱硫设备的制造已走向产业化,设备的国产化率已达90肠以上,引进的石灰石一石膏湿法烟气脱硫工艺中,浆液循环泵、真空皮带脱水机、增压风机、气气换热器和烟气挡板等关键设备,均已具备了批量生产加工能力。
近十几年来,我国政府有关部门多次组织了中小型燃煤工业锅炉烟气脱硫技术的攻关研究,先后开发出了一批具有自主知识产权的脱硫技术,包括喷射石灰/石灰石、氨法、铁法、循环法及炭法等40余种新的脱硫技术,其中一些技术运行较为稳定,脱硫效率也能达到国家标准,见表1。
根据我国的国情及脱硫产业现状,这些技术应该得到鼓励和推广。
(1)国内脱硫企业自主创新能力不足。
我国目前在建和运行的脱硫装置,所采用的技术与设备绝大多数是从国外引进的,国内脱硫公司的消化吸收和再创新能力还比较弱,一些脱硫公司宣称拥有了自主知识产权技术,实质上还是在模仿国外技术,缺少本质上的创新。
(2)已建脱硫装置运行不足。
目前我国已建成投产的烟气脱硫设施实际投运率不足60%,其原因除了经济上不合理和环保执法不严外,还因为部分脱硫公司对国外技术和设备依赖度较高,而且没有完全掌握工艺技术或者系统设计先天不足,设备运行不稳定,效果不理想,个别设备出现故障后难以及时修复。
(3)石灰石一石膏湿法脱硫技术的自身缺陷。
采用石灰石一石膏湿法工艺,脱硫副产物的硫石膏产量巨大,这些硫石膏虽然也可以作为建筑材料进行综合利用,但是质量上还存在许多问题,目前大部分脱硫石膏只能堆放储存,造成环境的二次污染,同时采用这种工艺还会增加二氧化碳的排放。