焦炉烟道废气脱硫脱硝除尘及余热回收一体化技术
(详细方案)焦炉烟道气余热利用脱硫脱硝一体化技术方案-1
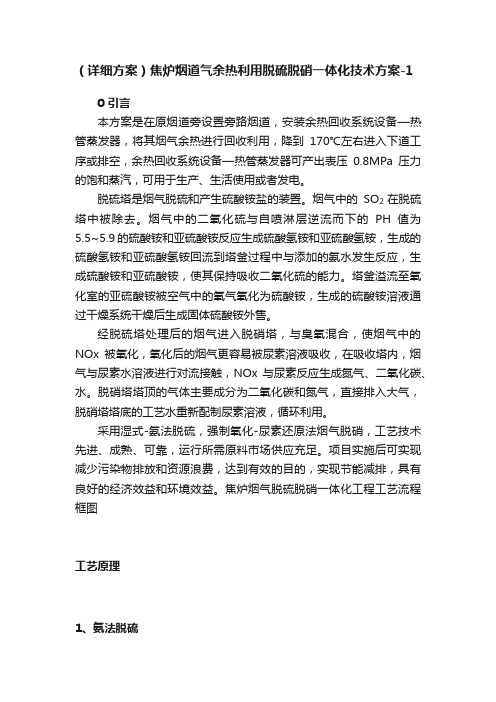
(详细方案)焦炉烟道气余热利用脱硫脱硝一体化技术方案-10 引言本方案是在原烟道旁设置旁路烟道,安装余热回收系统设备—热管蒸发器,将其烟气余热进行回收利用,降到170℃左右进入下道工序或排空,余热回收系统设备—热管蒸发器可产出表压0.8MPa压力的饱和蒸汽,可用于生产、生活使用或者发电。
脱硫塔是烟气脱硫和产生硫酸铵盐的装置。
烟气中的SO2在脱硫塔中被除去。
烟气中的二氧化硫与自喷淋层逆流而下的PH值为5.5~5.9的硫酸铵和亚硫酸铵反应生成硫酸氢铵和亚硫酸氢铵,生成的硫酸氢铵和亚硫酸氢铵回流到塔釜过程中与添加的氨水发生反应,生成硫酸铵和亚硫酸铵,使其保持吸收二氧化硫的能力。
塔釜溢流至氧化室的亚硫酸铵被空气中的氧气氧化为硫酸铵,生成的硫酸铵溶液通过干燥系统干燥后生成固体硫酸铵外售。
经脱硫塔处理后的烟气进入脱硝塔,与臭氧混合,使烟气中的NOx被氧化,氧化后的烟气更容易被尿素溶液吸收,在吸收塔内,烟气与尿素水溶液进行对流接触,NOx 与尿素反应生成氮气、二氧化碳、水。
脱硝塔塔顶的气体主要成分为二氧化碳和氮气,直接排入大气,脱硝塔塔底的工艺水重新配制尿素溶液,循环利用。
采用湿式-氨法脱硫,强制氧化-尿素还原法烟气脱硝,工艺技术先进、成熟、可靠,运行所需原料市场供应充足。
项目实施后可实现减少污染物排放和资源浪费,达到有效的目的,实现节能减排,具有良好的经济效益和环境效益。
焦炉烟气脱硫脱硝一体化工程工艺流程框图工艺原理1、氨法脱硫氨法脱硫是利用二氧化硫[SO2]与氨[NH3]在常温下反应,生成亚硫酸铵[(NH4)2SO3],然后氧化生成硫酸铵[(NH4)2SO4]的原理,对烟气中的二氧化硫进行治理。
该法不仅避免了双碱法、石灰石-石膏法等工艺会产生大量石膏[CaSO4]混合物无法处理的弊端,还有另一个优点就是脱硫效率随着烟气含硫量增加而增加,对二氧化硫[SO2]含量大于1000mg/Nm3的烟气,其脱硫效率可达到98%以上。
焦化厂烟气脱硝脱硫一体化解决方案1

110万吨/年焦炉烟气脱硝脱硫一体化技术方案110万吨/年焦炉烟道气与脱硝脱硫一体化设计方案廊坊市晋盛节能技术服务有限公司目录1. 项目概述 (2)1.1. 项目概况 (2)2. 设计依据 (2)2.1. 设计原则 (2)2.2. 设计标准 (3)2.3. 设计原始参数 (3)2.3.1 烟气参数 (3)2.3.2 气候条件 (4)2.4. 设计要求 (4)2.5. 工程范围 (4)3. 烟气脱硫脱硝一体化工艺 (5)3.1. 总工艺流程 (5)3.2. 脱硝工艺 (5)3.3. 脱硫工艺 (7)4. 烟气脱硫脱硝一体化技术说明 (8)4.1. 脱硝技术 (8)4.1.1脱硝系统的构成 (8)4.1.2脱硝系统主要设备 (9)4.2. 脱硫技术 (11)4.2.1脱硫工艺描述 (11)4.2.2脱硫主要设备 (11)5. 经济及环境效益分析 (13)5.1脱硫脱硝环境效益及节约费用 (13)5.2脱硫脱硝运行费用 (13)5.3脱硫脱硝投资费用 (14)5.4设备清单 (13)1.项目概述1.1.项目概况焦化厂是专门从事冶金焦炭生产及冶炼焦化产品、加工、回收的专业工厂。
焦、NOx及烟尘炉烟囱排放的大气污染物为焦炉煤气燃烧后产生的废气,主要有SO2等,污染物呈有组织高架点源连续性排放,是污染最为严重的行业之一。
2012年6月,环境保护部及国家质量监督检验检疫局联合发布了《炼焦化学工业污染物排放标准》,明确规定了焦化工业的大气污染物排放标准。
廊坊市晋盛节能技术服务有限公司一体化烟气治理技术,就是将烟气烟气除尘技术,烟气脱硫、脱硝技术捆绑在一起,形成一套集成创新的装置,这套装置既能除尘、脱硫、脱硝,从而达到烟气资源化利用的目的。
从此改变烟气治理只有投入,没有产出的困境。
2.设计依据2.1.设计原则2.1.1脱硫脱硝➢对尾气同时进行脱硝及脱硫治理。
➢采用高效、先进、运行稳定、管理方便的治理工艺及技术,保证废气的达标排放;➢烟气净化治理不影响焦化厂生产工艺的正常运行。
焦炉烟气脱硫脱硝+余热回收技术探讨与实践
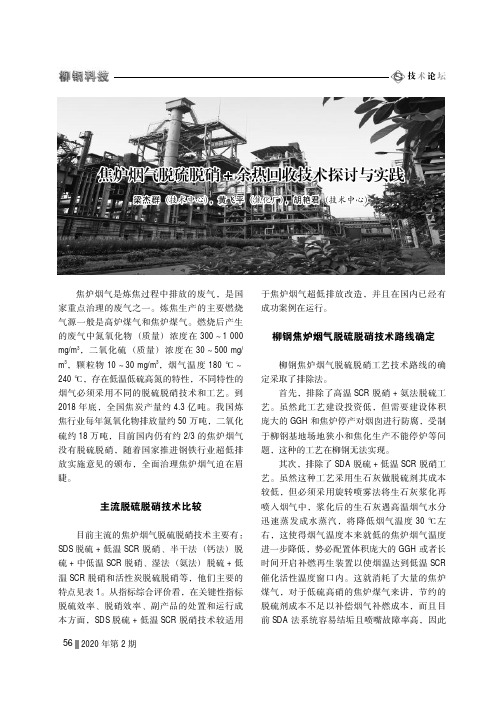
2020年第2期焦炉烟气是炼焦过程中排放的废气,是国家重点治理的废气之一。
炼焦生产的主要燃烧气源一般是高炉煤气和焦炉煤气。
燃烧后产生的废气中氮氧化物(质量)浓度在300~1000mg/m 3,二氧化硫(质量)浓度在30~500mg/m 3,颗粒物10~30mg/m 3,烟气温度180℃~240℃,存在低温低硫高氮的特性,不同特性的烟气必须采用不同的脱硫脱硝技术和工艺。
到2018年底,全国焦炭产量约4.3亿吨。
我国炼焦行业每年氮氧化物排放量约50万吨,二氧化硫约18万吨,目前国内仍有约2/3的焦炉烟气没有脱硫脱硝,随着国家推进钢铁行业超低排放实施意见的颁布,全面治理焦炉烟气迫在眉睫。
主流脱硫脱硝技术比较目前主流的焦炉烟气脱硫脱硝技术主要有:SDS 脱硫+低温SCR 脱硝、半干法(钙法)脱硫+中低温SCR 脱硝、湿法(氨法)脱硫+低温SCR 脱硝和活性炭脱硫脱硝等,他们主要的特点见表1。
从指标综合评价看,在关键性指标脱硫效率、脱硝效率、副产品的处置和运行成本方面,SDS 脱硫+低温SCR 脱硝技术较适用于焦炉烟气超低排放改造,并且在国内已经有成功案例在运行。
柳钢焦炉烟气脱硫脱硝技术路线确定柳钢焦炉烟气脱硫脱硝工艺技术路线的确定采取了排除法。
首先,排除了高温SCR 脱硝+氨法脱硫工艺。
虽然此工艺建设投资低,但需要建设体积庞大的GGH 和焦炉停产对烟囱进行防腐,受制于柳钢基地场地狭小和焦化生产不能停炉等问题,这种的工艺在柳钢无法实现。
其次,排除了SDA 脱硫+低温SCR 脱硝工艺。
虽然这种工艺采用生石灰做脱硫剂其成本较低,但必须采用旋转喷雾法将生石灰浆化再喷入烟气中,浆化后的生石灰遇高温烟气水分迅速蒸发成水蒸汽,将降低烟气温度30℃左右,这使得烟气温度本来就低的焦炉烟气温度进一步降低,势必配置体积庞大的GGH 或者长时间开启补燃再生装置以使烟温达到低温SCR 催化活性温度窗口内。
这就消耗了大量的焦炉煤气,对于低硫高硝的焦炉煤气来讲,节约的脱硫剂成本不足以补偿烟气补燃成本,而且目前SDA 法系统容易结垢且喷嘴故障率高,因此焦炉烟气脱硫脱硝余热回收技术探讨与实践梁杰群(技术中心),黄飞平(焦化厂),胡艳君(技术中心)技术论坛562020年第2期SDA 脱硫+低温SCR 脱硝工艺也被排除。
焦炉烟道气脱硫脱硝及余热回收利用一体化技术
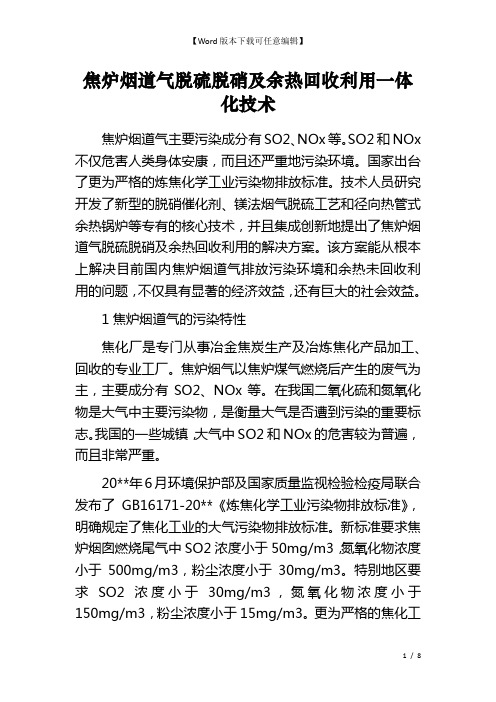
焦炉烟道气脱硫脱硝及余热回收利用一体化技术焦炉烟道气主要污染成分有SO2、NOx等。
SO2和NOx 不仅危害人类身体安康,而且还严重地污染环境。
国家出台了更为严格的炼焦化学工业污染物排放标准。
技术人员研究开发了新型的脱硝催化剂、镁法烟气脱硫工艺和径向热管式余热锅炉等专有的核心技术,并且集成创新地提出了焦炉烟道气脱硫脱硝及余热回收利用的解决方案。
该方案能从根本上解决目前国内焦炉烟道气排放污染环境和余热未回收利用的问题,不仅具有显著的经济效益,还有巨大的社会效益。
1焦炉烟道气的污染特性焦化厂是专门从事冶金焦炭生产及冶炼焦化产品加工、回收的专业工厂。
焦炉烟气以焦炉煤气燃烧后产生的废气为主,主要成分有SO2、NOx等。
在我国二氧化硫和氮氧化物是大气中主要污染物,是衡量大气是否遭到污染的重要标志。
我国的一些城镇,大气中SO2和NOx的危害较为普遍,而且非常严重。
20**年6月环境保护部及国家质量监视检验检疫局联合发布了GB16171-20**《炼焦化学工业污染物排放标准》,明确规定了焦化工业的大气污染物排放标准。
新标准要求焦炉烟囱燃烧尾气中SO2浓度小于50mg/m3,氮氧化物浓度小于500mg/m3,粉尘浓度小于30mg/m3。
特别地区要求SO2浓度小于30mg/m3,氮氧化物浓度小于150mg/m3,粉尘浓度小于15mg/m3。
更为严格的焦化工业大气污染物排放标准和日益紧张的能源供应,急需技术更为先进、经济、合理的焦炉烟气处理方法。
中钢集团***热能研究院公司联合中科院技术人员集成低温SCR烟气脱硝技术、镁法烟气脱硫工艺和径向热管式余热锅炉等专有的核心技术,提出了焦炉烟道气脱硫、脱硝及余热回收利用的综合解决方案。
2一体化解决技术针对客户的要求和焦炉现有煤气处理工序,中钢热能研究人员研究开发并且集成了焦炉烟道气脱硫脱硝及余热回收利用的一体化技术。
2.1方案描述焦炉烟气处理流程(如图1所示):焦炉→焦炉烟道气→脱硝反应器→热管式烟气换热器→增压风机→脱硫塔→塔顶烟囱排放。
焦炉烟气脱硫脱硝余热回收一体化研究应用
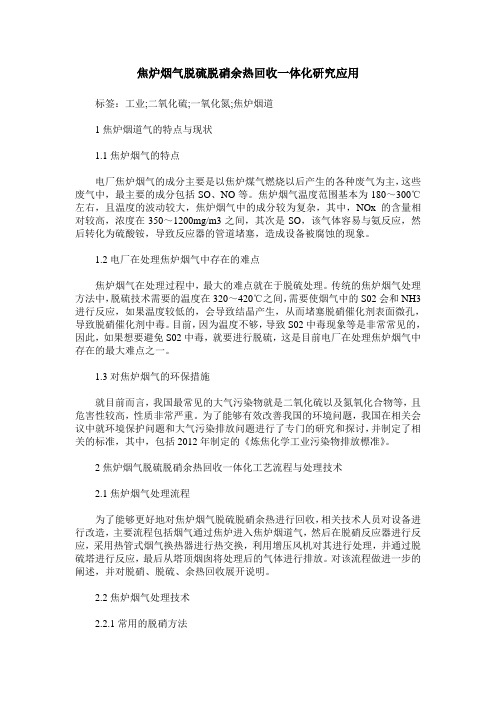
焦炉烟气脱硫脱硝余热回收一体化研究应用标签:工业;二氧化硫;一氧化氮;焦炉烟道1焦炉烟道气的特点与现状1.1焦炉烟气的特点电厂焦炉烟气的成分主要是以焦炉煤气燃烧以后产生的各种废气为主,这些废气中,最主要的成分包括SO、NO等。
焦炉烟气温度范围基本为180~300℃左右,且温度的波动较大,焦炉烟气中的成分较为复杂,其中,NOx的含量相对较高,浓度在350~1200mg/m3之间,其次是SO,该气体容易与氨反应,然后转化为硫酸铵,导致反应器的管道堵塞,造成设备被腐蚀的现象。
1.2电厂在处理焦炉烟气中存在的难点焦炉烟气在处理过程中,最大的难点就在于脱硫处理。
传统的焦炉烟气处理方法中,脱硫技术需要的温度在320~420℃之间,需要使烟气中的S02会和NH3进行反应,如果温度较低的,会导致结晶产生,从而堵塞脱硝催化剂表面微孔,导致脱硝催化剂中毒。
目前,因为温度不够,导致S02中毒现象等是非常常见的,因此,如果想要避免S02中毒,就要进行脱硫,这是目前电厂在处理焦炉烟气中存在的最大难点之一。
1.3对焦炉烟气的环保措施就目前而言,我国最常见的大气污染物就是二氧化硫以及氮氧化合物等,且危害性较高,性质非常严重。
为了能够有效改善我国的环境问题,我国在相关会议中就环境保护问题和大气污染排放问题进行了专门的研究和探讨,并制定了相关的标准,其中,包括2012年制定的《炼焦化学工业污染物排放標准》。
2焦炉烟气脱硫脱硝余热回收一体化工艺流程与处理技术2.1焦炉烟气处理流程为了能够更好地对焦炉烟气脱硫脱硝余热进行回收,相关技术人员对设备进行改造,主要流程包括烟气通过焦炉进入焦炉烟道气,然后在脱硝反应器进行反应,采用热管式烟气换热器进行热交换,利用增压风机对其进行处理,并通过脱硫塔进行反应,最后从塔顶烟囱将处理后的气体进行排放。
对该流程做进一步的阐述,并对脱硝、脱硫、余热回收展开说明。
2.2焦炉烟气处理技术2.2.1常用的脱硝方法就目前而言,采用脱硝反应器进行脱硝是目前常用的脱硝方法,在处理硝酸过程中,主要采用的方法有非催化还原法、氧化吸收法、催化还原法等。
焦化厂烟气脱硫脱硝及余热利用工艺
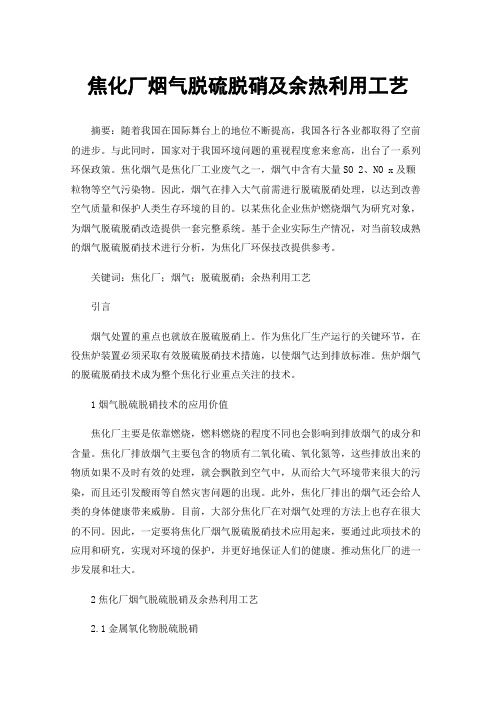
焦化厂烟气脱硫脱硝及余热利用工艺摘要:随着我国在国际舞台上的地位不断提高,我国各行各业都取得了空前的进步。
与此同时,国家对于我国环境问题的重视程度愈来愈高,出台了一系列环保政策。
焦化烟气是焦化厂工业废气之一,烟气中含有大量SO 2、NO x及颗粒物等空气污染物。
因此,烟气在排入大气前需进行脱硫脱硝处理,以达到改善空气质量和保护人类生存环境的目的。
以某焦化企业焦炉燃烧烟气为研究对象,为烟气脱硫脱硝改造提供一套完整系统。
基于企业实际生产情况,对当前较成熟的烟气脱硫脱硝技术进行分析,为焦化厂环保技改提供参考。
关键词:焦化厂;烟气;脱硫脱硝;余热利用工艺引言烟气处置的重点也就放在脱硫脱硝上。
作为焦化厂生产运行的关键环节,在役焦炉装置必须采取有效脱硫脱硝技术措施,以使烟气达到排放标准。
焦炉烟气的脱硫脱硝技术成为整个焦化行业重点关注的技术。
1烟气脱硫脱硝技术的应用价值焦化厂主要是依靠燃烧,燃料燃烧的程度不同也会影响到排放烟气的成分和含量。
焦化厂排放烟气主要包含的物质有二氧化硫、氧化氮等,这些排放出来的物质如果不及时有效的处理,就会飘散到空气中,从而给大气环境带来很大的污染,而且还引发酸雨等自然灾害问题的出现。
此外,焦化厂排出的烟气还会给人类的身体健康带来威胁。
目前,大部分焦化厂在对烟气处理的方法上也存在很大的不同。
因此,一定要将焦化厂烟气脱硫脱硝技术应用起来,要通过此项技术的应用和研究,实现对环境的保护,并更好地保证人们的健康。
推动焦化厂的进一步发展和壮大。
2焦化厂烟气脱硫脱硝及余热利用工艺2.1金属氧化物脱硫脱硝可以理解为利用载体上的金属氧化物与二氧化硫和氧气完成反应,以此生成硫酸盐,该反应生成物能够作为催化剂,达到脱硫脱硝的目的。
同时,金属硫酸盐还能和甲烷进行还原反应,以此生成金属硫化物,该物质的作用在于能够在烟气中进一步氧化生成金属氧化物,可以用于二次脱硫脱硝。
该工艺中对氧化铜同时脱硫脱硝工艺的研究相对深入,将三氧化二铝作为载体,能够保证90%以上的二氧化硫脱除率以及80%左右的氮氧化物脱除率。
焦化厂烟气脱硫脱硝及余热利用工艺
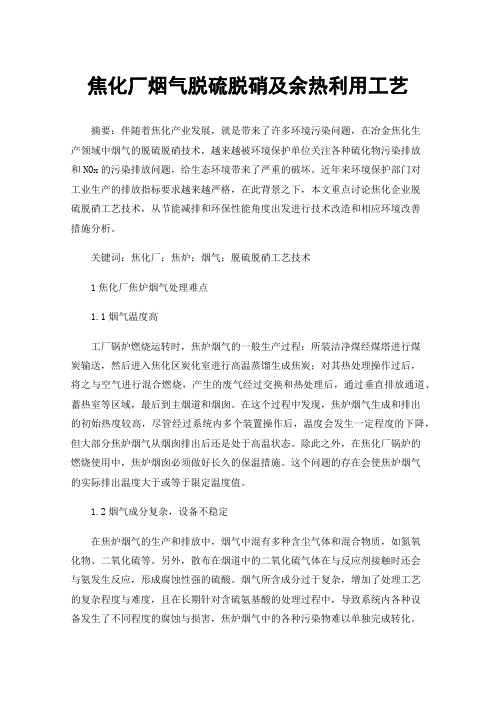
焦化厂烟气脱硫脱硝及余热利用工艺摘要:伴随着焦化产业发展,就是带来了许多环境污染问题,在冶金焦化生产领域中烟气的脱硫脱硝技术,越来越被环境保护单位关注各种硫化物污染排放和NOx的污染排放问题,给生态环境带来了严重的破坏。
近年来环境保护部门对工业生产的排放指标要求越来越严格,在此背景之下,本文重点讨论焦化企业脱硫脱硝工艺技术,从节能减排和环保性能角度出发进行技术改造和相应环境改善措施分析。
关键词:焦化厂;焦炉;烟气;脱硫脱硝工艺技术1焦化厂焦炉烟气处理难点1.1烟气温度高工厂锅炉燃烧运转时,焦炉烟气的一般生产过程:所装洁净煤经煤塔进行煤炭输送,然后进入焦化区炭化室进行高温蒸馏生成焦炭;对其热处理操作过后,将之与空气进行混合燃烧,产生的废气经过交换和热处理后,通过垂直排放通道、蓄热室等区域,最后到主烟道和烟囱。
在这个过程中发现,焦炉烟气生成和排出的初始热度较高,尽管经过系统内多个装置操作后,温度会发生一定程度的下降,但大部分焦炉烟气从烟囱排出后还是处于高温状态。
除此之外,在焦化厂锅炉的燃烧使用中,焦炉烟囱必须做好长久的保温措施。
这个问题的存在会使焦炉烟气的实际排出温度大于或等于限定温度值。
1.2烟气成分复杂,设备不稳定在焦炉烟气的生产和排放中,烟气中混有多种含尘气体和混合物质,如氮氧化物、二氧化硫等。
另外,散布在烟道中的二氧化硫气体在与反应剂接触时还会与氨发生反应,形成腐蚀性强的硫酸。
烟气所含成分过于复杂,增加了处理工艺的复杂程度与难度,且在长期针对含硫氨基酸的处理过程中,导致系统内各种设备发生了不同程度的腐蚀与损害,焦炉烟气中的各种污染物难以单独完成转化。
2焦化厂主要焦炉烟气脱硫技术2.1干法脱硫技术干法脱硫工艺技术原理:碳酸钙固体在高温下喷入炉中进行锻造和燃烧,反应生成氧化钙,后与焦炉烟气中的二氧化硫发生化学反应转化为硫酸钙。
或根据焦化厂的具体情况,通过活性炭吸附或电子束辐照的方式,将烟气中的二氧化硫转化成硫酸或硫酸铵,该工艺也称为干法脱硫技术。
焦炉烟气脱硫脱硝余热回收技术改造
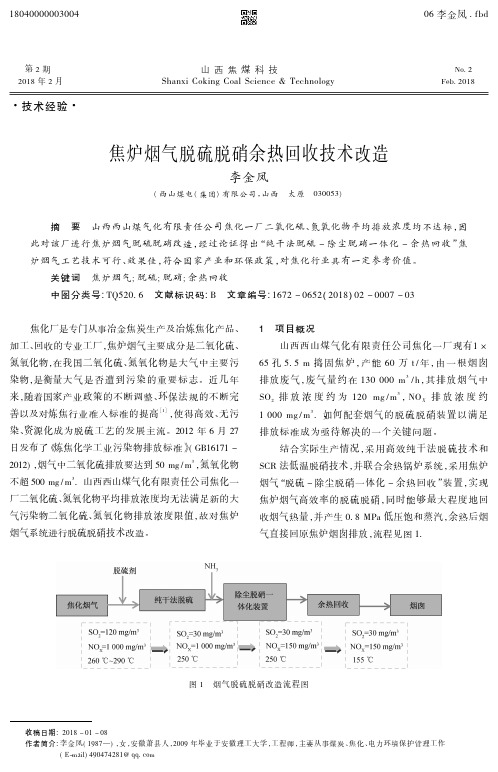
06 李金凤 . fbd
第2期 2018 年 2 月
·技术经验·
山西焦煤科技 Shanxi Coking Coal Science & Technology
No. 2 Feb. 2018
焦炉烟气脱硫脱硝余热回收技术改造
李金凤
( 西山煤电( 集团) 有限公司,山西 太原 030053)
Hale Waihona Puke 图 1 烟气脱硫脱硝改造流程图
收稿日期: 2018 - 01 - 08 作者简介: 李金凤( 1987—) ,女,安徽萧县人,2009 年毕业于安徽理工大学,工程师,主要从事煤炭、焦化、电力环境保护管理工作
( E-mail) 490474281@ qq. com
18040000003004
06 李金凤 . fbd
SO2 + 1 /2O2 + 2NaHCO3 → Na2 SO4 + H2 O + 2CO2 SO2 + 2NaHCO3 →Na2 SO3 + H2 O + 2CO2
脱 硫 后 烟 气 在 上 升 过 程 中 ,未 反 应 完 的 碳 酸 氢 钠 干 粉 及 颗 粒 物 一 部 分 随 烟 气 被 带 出 吸 收 塔 ,一 部 分 因 自重重新回流到循环流化床内。
结合实际生产情况,采用高效纯干 法 脱 硫技术 和 SCR 法低温脱硝技术,并联合余热锅炉系统,采用焦炉 烟气“脱硫 - 除尘脱硝一体化 - 余热回收”装置,实现 焦炉烟气高效率的脱硫脱硝,同时能够最 大程 度 地 回 收烟气热量,并产生 0. 8 MPa 低压饱和蒸汽,余热后烟 气直接回原焦炉烟囱排放,流程见图 1.
1 项目概况 山西西山煤气化有限责任公司焦化一厂现有1 ×
焦化行业烟气脱硝--余热回收--脱硫工艺方案
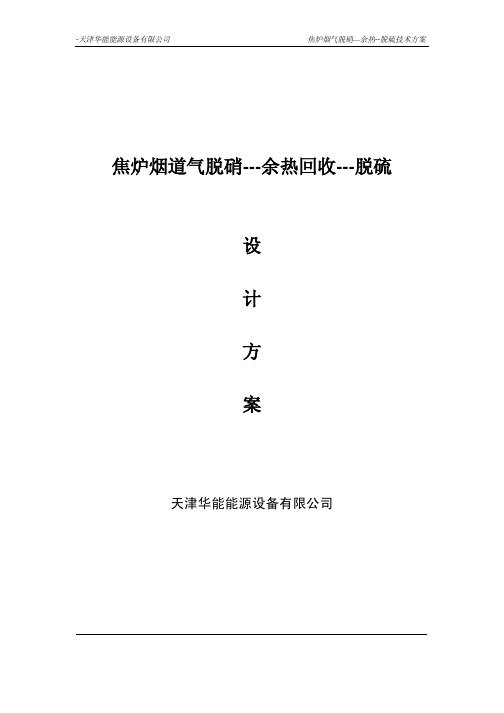
mg/ Nm3
5
入口 SO2 浓度
mg/ Nm3
280-290 20
1800 450
2.3.2 气候条件
2.4. 设计要求
脱硫脱硝工程技术性能指标
序号 2 3
名称 NOx SO2
初始浓度(mg/Nm³) 1800 450
排放浓度(mg/Nm³) ≤500 ≤50
4
氨逃逸
脱除率(%) ≥72.2 ≥77.78 ≤5ppm
因,致使焦炉 250—320℃高温烟气直接排放,浪费了大量的废热能源。 近年来,国内已有部分大型焦化厂开始注重焦炉烟气余热利用,如太钢,采用了煤调
湿装置,利用焦炉烟道部分废气,在流化床设备内将原料煤按要求进行粒度分级,同时利 用焦炉烟道气热量脱出煤中部分水分,从而达到优化炼焦煤粒度、调整水分及预热的目的。
但该项目一是投资费用较大,而且设备占地面大,二是只能利用部分废气的热量,还有较 大的废气未被利用。
2009 年 4 月,天津华能能源设备有限公司开发的国内首套烟道气热管余热锅炉系统, 在唐山达丰焦化有限公司成功运行,生产低压饱和蒸汽或过热蒸汽,生产蒸汽 100Kg/吨焦,
用于焦化生产,大大降低了生产成本。随后旭阳焦化集团、金牛天铁焦化公司、唐山九江 钢铁、山西美锦能源、山东傅山焦化等 40 多家企业进行了改造,为几十家企业,带来了客
产尾气中的SO2, 生产亚硫铵和硫铵。
第一步, SO2和NH3的反应为基础的吸收过程:
SO2+H2O+xNH3 = (NH4) xH2-XSO3 因此,采用氨法脱硫首先得到亚硫酸铵中间产品。
(1)
第二步,采用空气对亚硫铵直接强制氧化:
(NH4)XH2-XSO3+1/2O2 +(2-x)NH3=(NH4)2SO4
国内焦化企业烟气脱硫脱硝技术
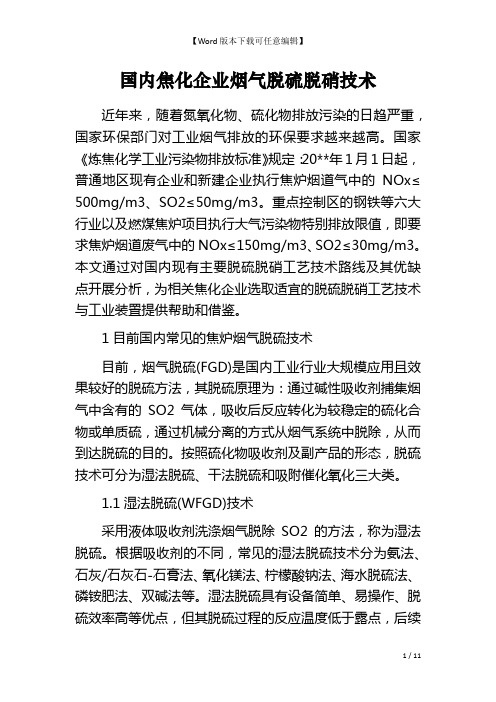
国内焦化企业烟气脱硫脱硝技术近年来,随着氮氧化物、硫化物排放污染的日趋严重,国家环保部门对工业烟气排放的环保要求越来越高。
国家《炼焦化学工业污染物排放标准》规定:20**年1月1日起,普通地区现有企业和新建企业执行焦炉烟道气中的NOx≤500mg/m3、SO2≤50mg/m3。
重点控制区的钢铁等六大行业以及燃煤焦炉项目执行大气污染物特别排放限值,即要求焦炉烟道废气中的NOx≤150mg/m3、SO2≤30mg/m3。
本文通过对国内现有主要脱硫脱硝工艺技术路线及其优缺点开展分析,为相关焦化企业选取适宜的脱硫脱硝工艺技术与工业装置提供帮助和借鉴。
1目前国内常见的焦炉烟气脱硫技术目前,烟气脱硫(FGD)是国内工业行业大规模应用且效果较好的脱硫方法,其脱硫原理为:通过碱性吸收剂捕集烟气中含有的SO2气体,吸收后反应转化为较稳定的硫化合物或单质硫,通过机械分离的方式从烟气系统中脱除,从而到达脱硫的目的。
按照硫化物吸收剂及副产品的形态,脱硫技术可分为湿法脱硫、干法脱硫和吸附催化氧化三大类。
1.1湿法脱硫(WFGD)技术采用液体吸收剂洗涤烟气脱除SO2的方法,称为湿法脱硫。
根据吸收剂的不同,常见的湿法脱硫技术分为氨法、石灰/石灰石-石膏法、氧化镁法、柠檬酸钠法、海水脱硫法、磷铵肥法、双碱法等。
湿法脱硫具有设备简单、易操作、脱硫效率高等优点,但其脱硫过程的反应温度低于露点,后续管道和设备腐蚀问题严重。
1.1.1湿式氨法脱硫技术该技术是利用二氧化硫SO2与氨NH3在常温下反应,生成亚硫酸铵(NH4)2SO3,然后氧化生成硫酸铵(NH4)2SO4的原理,对烟气中的二氧化硫开展治理。
湿式氨法脱硫技术反应原理为:(a)吸收反应过程:吸收反应过程中,产生的酸式盐(NH4)HSO3对二氧化硫SO2不具备吸收能力,反应(3)为湿式氨法脱硫反应过程中真正的吸收反应过程。
(1)反应发生通入氨量较少的情况下;(2)反应发生在通入氨量较多的情况下。
焦炉烟气脱硫脱硝余热回收一体化研究应用
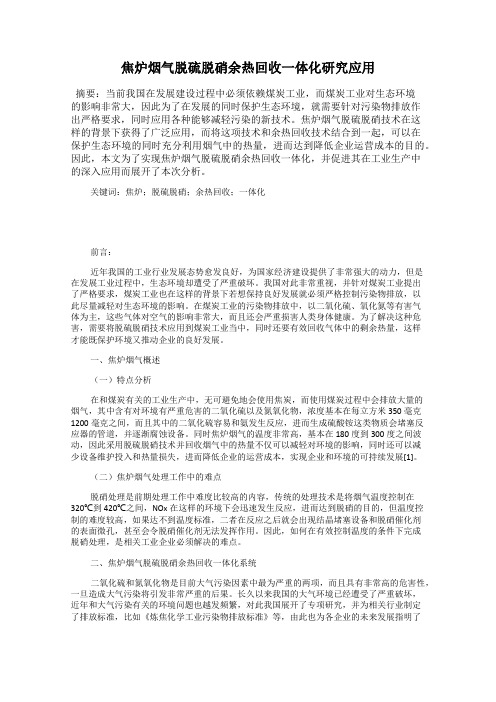
焦炉烟气脱硫脱硝余热回收一体化研究应用摘要:当前我国在发展建设过程中必须依赖煤炭工业,而煤炭工业对生态环境的影响非常大,因此为了在发展的同时保护生态环境,就需要针对污染物排放作出严格要求,同时应用各种能够减轻污染的新技术。
焦炉烟气脱硫脱硝技术在这样的背景下获得了广泛应用,而将这项技术和余热回收技术结合到一起,可以在保护生态环境的同时充分利用烟气中的热量,进而达到降低企业运营成本的目的。
因此,本文为了实现焦炉烟气脱硫脱硝余热回收一体化,并促进其在工业生产中的深入应用而展开了本次分析。
关键词:焦炉;脱硫脱硝;余热回收;一体化前言:近年我国的工业行业发展态势愈发良好,为国家经济建设提供了非常强大的动力,但是在发展工业过程中,生态环境却遭受了严重破坏。
我国对此非常重视,并针对煤炭工业提出了严格要求,煤炭工业也在这样的背景下若想保持良好发展就必须严格控制污染物排放,以此尽量减轻对生态环境的影响。
在煤炭工业的污染物排放中,以二氧化硫、氧化氮等有害气体为主,这些气体对空气的影响非常大,而且还会严重损害人类身体健康。
为了解决这种危害,需要将脱硫脱硝技术应用到煤炭工业当中,同时还要有效回收气体中的剩余热量,这样才能既保护环境又推动企业的良好发展。
一、焦炉烟气概述(一)特点分析在和煤炭有关的工业生产中,无可避免地会使用焦炭,而使用煤炭过程中会排放大量的烟气,其中含有对环境有严重危害的二氧化硫以及氮氧化物,浓度基本在每立方米350毫克1200毫克之间,而且其中的二氧化硫容易和氨发生反应,进而生成硫酸铵这类物质会堵塞反应器的管道,并逐渐腐蚀设备。
同时焦炉烟气的温度非常高,基本在180度到300度之间波动,因此采用脱硫脱硝技术并回收烟气中的热量不仅可以减轻对环境的影响,同时还可以减少设备维护投入和热量损失,进而降低企业的运营成本,实现企业和环境的可持续发展[1]。
(二)焦炉烟气处理工作中的难点脱硝处理是前期处理工作中难度比较高的内容,传统的处理技术是将烟气温度控制在320℃到420℃之间,NOx在这样的环境下会迅速发生反应,进而达到脱硝的目的,但温度控制的难度较高,如果达不到温度标准,二者在反应之后就会出现结晶堵塞设备和脱硝催化剂的表面微孔,甚至会令脱硝催化剂无法发挥作用。
焦炉烟气脱硫脱硝除尘一体化技术
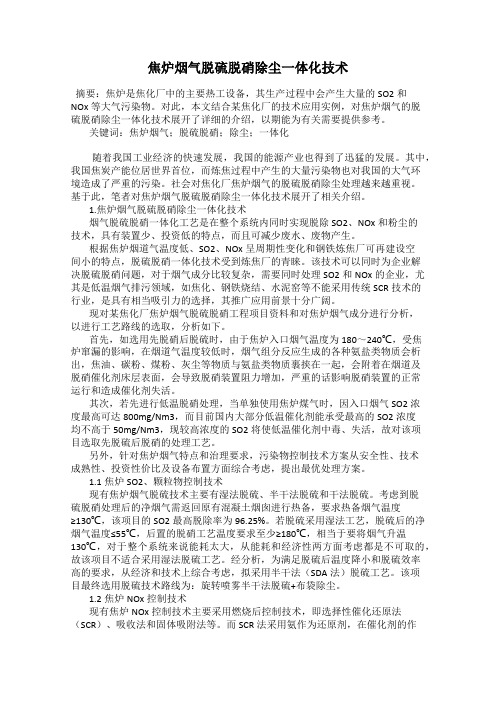
焦炉烟气脱硫脱硝除尘一体化技术摘要:焦炉是焦化厂中的主要热工设备,其生产过程中会产生大量的SO2和NOx等大气污染物。
对此,本文结合某焦化厂的技术应用实例,对焦炉烟气的脱硫脱硝除尘一体化技术展开了详细的介绍,以期能为有关需要提供参考。
关键词:焦炉烟气;脱硫脱硝;除尘;一体化随着我国工业经济的快速发展,我国的能源产业也得到了迅猛的发展。
其中,我国焦炭产能位居世界首位,而炼焦过程中产生的大量污染物也对我国的大气环境造成了严重的污染。
社会对焦化厂焦炉烟气的脱硫脱硝除尘处理越来越重视。
基于此,笔者对焦炉烟气脱硫脱硝除尘一体化技术展开了相关介绍。
1.焦炉烟气脱硫脱硝除尘一体化技术烟气脱硫脱硝一体化工艺是在整个系统内同时实现脱除SO2、NOx和粉尘的技术,具有装置少、投资低的特点,而且可减少废水、废物产生。
根据焦炉烟道气温度低、SO2、NOx呈周期性变化和钢铁炼焦厂可再建设空间小的特点,脱硫脱硝一体化技术受到炼焦厂的青睐。
该技术可以同时为企业解决脱硫脱硝问题,对于烟气成分比较复杂,需要同时处理SO2和NOx的企业,尤其是低温烟气排污领域,如焦化、钢铁烧结、水泥窑等不能采用传统SCR技术的行业,是具有相当吸引力的选择,其推广应用前景十分广阔。
现对某焦化厂焦炉烟气脱硫脱硝工程项目资料和对焦炉烟气成分进行分析,以进行工艺路线的选取,分析如下。
首先,如选用先脱硝后脱硫时,由于焦炉入口烟气温度为180~240℃,受焦炉窜漏的影响,在烟道气温度较低时,烟气组分反应生成的各种氨盐类物质会析出,焦油、碳粉、煤粉、灰尘等物质与氨盐类物质裹挟在一起,会附着在烟道及脱硝催化剂床层表面,会导致脱硝装置阻力增加,严重的话影响脱硝装置的正常运行和造成催化剂失活。
其次,若先进行低温脱硝处理,当单独使用焦炉煤气时,因入口烟气SO2浓度最高可达800mg/Nm3,而目前国内大部分低温催化剂能承受最高的SO2浓度均不高于50mg/Nm3,现较高浓度的SO2将使低温催化剂中毒、失活,故对该项目选取先脱硫后脱硝的处理工艺。
焦炉烟气脱硫脱硝及余热回收一体化新技术的工业应用 任翼泽

焦炉烟气脱硫脱硝及余热回收一体化新技术的工业应用任翼泽发表时间:2019-05-24T11:06:03.390Z 来源:《电力设备》2018年第34期作者:任翼泽[导读] 摘要:当前我国已经成为了世界第一焦炭生产大国和消耗大国以及出口大国。
(身份证号码:14048119781022xxxx)摘要:当前我国已经成为了世界第一焦炭生产大国和消耗大国以及出口大国。
其产生的焦炉烟气不仅严重危害人们的身体健康,还对环境生态造成了极大的污染,因此焦炉烟气的脱硫脱硝技术开始被重视和应用,在我国国内的部分大型焦化厂和钢铁厂已经开始注重焦炉烟气的余热利用,并开发了新型的脱硝催化剂、镁法烟气脱硫工艺和径向的热管式余热锅炉等专有的技术核心,并且创新的提出了焦炉烟气脱硫、脱硝以及余热回收一体化利用的解决方案。
因此本文针对焦炉烟气脱硫脱硝以及余热回收一体化新技术在工业的应用展开研究和分析,通过对该技术的发展现状和本人的实际工作经验对其进行探讨,以期焦炉烟气脱硫脱硝和余热回收一体化新技术能够更好的发展和应用。
关键词:焦炉烟气;脱硫脱硝;余热回收一体化;工业应用引言目前我国的SO2和NOx的排放量已经排在世界各国的前列,其这两种化学成分也是形成酸雨的主要物质之一,对大气环境和酸雨问题都有极大的影响,使之日益严重,对人类的身体健康和生态系统都有巨大的危害,已经成为了制约我国社会经济可持续发展的一个重要因素。
而焦炉烟气排放的污染物主要为硫和硝的化学混合物以及颗粒,其排放量受到多种因素的影响,其中就包括加热煤气的净化程度、加热火道的湿度、加热煤气的燃烧条件、焦炉加热系统的密封性等等。
在我国的工业生产中,已经有部分企业开始重视这一问题,并开始注重焦炉烟气的余热利用,采用了煤调湿装置,利用焦炉烟气在流化床设备内将原料煤按照相关的要求进行粒度分级,同时利用焦炉烟气热量脱出的煤中部分水分,从而在一定程度上达到优化炼焦煤粒度和调整水分以及预热的目的。
焦化厂烟气脱硝脱硫一体化解决方案

序号
名称
烟气参数
备注
单位
数据
1
烟气流量
Nm3/h
300000
2
烟气温度
℃
280-290
3
入口粉尘浓度
mg/ Nm3
20
4
入口NOx浓度
mg/ Nm3
1800
5
入口SO2浓度
mg/ Nm3
450
2.3.2
2.4.
脱硫脱硝工程技术性能指标
序号
名称
初始浓度(mg/Nm³)
排放浓度(mg/Nm³)
脱除率(%)
备注
2
NOx
1800
≤500
≥72.2
3
SO2
450ቤተ መጻሕፍቲ ባይዱ
≤50
≥77.78
4
氨逃逸
≤5ppm
2.5.
1、项目容
(1)烟气SCR脱硝系统、脱硫系统的详细工程设计和施工。
(2)成套设备和材料供货。
(3)技术服务。
二、施工界线及相关条件
(1)烟气进出口管道及阀门
(2)给水管道进口至蒸汽管道出口,以平台框架为界
2012年6月,环境保护部及国家质量监督检验检疫局联合发布了《炼焦化学工业污染物排放标准》,明确规定了焦化工业的大气污染物排放标准。
市晋盛节能技术服务一体化烟气治理技术,就是将烟气烟气除尘技术,烟气脱硫、脱硝技术捆绑在一起,形成一套集成创新的装置,这套装置既能除尘、脱硫、脱硝,从而达到烟气资源化利用的目的。从此改变烟气治理只有投入,没有产出的困境。
2.
2.1.
2.1.1脱硫脱硝
对尾气同时进行脱硝及脱硫治理。
采用高效、先进、运行稳定、管理方便的治理工艺及技术,保证废气的达标排放;
- 1、下载文档前请自行甄别文档内容的完整性,平台不提供额外的编辑、内容补充、找答案等附加服务。
- 2、"仅部分预览"的文档,不可在线预览部分如存在完整性等问题,可反馈申请退款(可完整预览的文档不适用该条件!)。
- 3、如文档侵犯您的权益,请联系客服反馈,我们会尽快为您处理(人工客服工作时间:9:00-18:30)。
1 引言
我国的SO:和NOx排放量高居世界各国前列, SO:、NOx是形成酸雨的主要物质之一,造成大气污 染和酸雨问题日益严重.对人类健康和生态系统等 危害严重,已经成为制约我国经济社会可持续发展 的因素。
焦炉烟囱排放污染物,主要为SO:、NOx及颗粒 物,排放量取决于多种因素,其中最具有代表性的 因素有:加热煤气的净化程度;加热火道的温度;加 热煤气的燃烧条件;焦炉加热系统的密封性等。
燃气在焦炉立火道燃烧时,会产生氮氧化物 (NOx),氮氧化物通常多指NO和NO:的混合物,大 气中的氮氧化物破坏臭氧层,造成酸雨,污染环境。 研究表明,在燃烧生成的NOx中,NO占95%,NO: 为5%左右,在大气中NO缓慢转化为NO:。焦炉烟 囱废气排放的NOx浓度一般在800~1200mg/m3。
焦炉烟道废气通过热回收温度降低到~160℃. 喷入超细的NaHC03粉末,NaHC03粉末在焦炉烟道 废气中发生分解,吸附焦炉烟道废气中的SO:,最后通 过袋式过滤器除去焦炉烟道废气的颗粒物.烟气中
SO:达到<50/30 m咖3,烟气通过烟囱排人到大气。 4工艺原理和工艺流程
4.1 低温SCR脱硝工艺原理 在SCR反应器内氨与焦炉烟道废气中的NOx
5)NH,逃逸率的控制是个难点。如果采用电厂 常用的NH,一SCR法对焦炉烟道气进行脱硝.由于 低温脱硝效率较低,所以经过脱硝后的NH,逃逸量 很难满足国家排放标准要求。
6)独立焦化厂采用焦炉煤气加热焦炉烟道废 气含水约为20%。采用常规湿法脱硫工艺产生大量 废水形成二次污染,采用常规石灰干法脱硫.在110 ℃以上不能满足脱硫要求;采用半干法,导致烟气温 度下降40~60℃,不能进行热回收。
混合气体进入位于烟道内的氨注入格栅,在注 入格栅前设有调节和流量指示,在系统投运后根据 烟道进出口检测NOx浓度来调节氨的分配量。
混合气体进入烟道通过氨/烟道废气混合器再 与烟道废气充分混合,然后进入SCR反应器,SCR 反应器操作温度可在220~290℃,SCR反应器的位 置位于焦炉烟囱附近区域。温度测量点位于SCR反 应器前的进El烟道上,出现160 oC以下温度情况时. 温度信号将自动连锁关闭氨进入氨/空气混合器的 快速切断阀。
反应生成氮气和水,反应方程式如下: 4N0+4NH3+02_+6H20“N2
NO+N02+2NH3—÷3H20+2N2
反应生成水和氮气残留在焦炉烟道废气中。 4.2干法脱硫工艺原理
焦炉烟道废气脱硫工艺以碳酸氢钠(NaHCO,) 作为吸收剂,过量的碳酸氢钠粉在高温烟气中受热 分解生成碳酸钠,碳酸钠吸收焦炉烟道废气中的
焦炉煤气中的碳颗粒物在加热时形成碳黑。焦 炉煤气中的烃类热裂解也形成碳黑.焦炉炭化室逸 出的粗煤气(粗煤气中含焦油和细分散煤尘)进入 到燃烧室。形成的废气中的碳颗粒浓度可达到100
mg/m3以上。 自2015年1月1日1起,现有企业执行《炼焦
化学工业污染物排放标准}GBl6171-2012“表5”规 定大气污染物排放限值:在国土开发密度较高、环 境承载能力开始减弱.或大气环境容量较小、生态 环境脆弱.容易发生严重大气污染环境问题而需要 采取特别保护措施的地区,执行GBl6171—2012“表 6”规定大气污染物特别排放限值。,具体规定见下 表1。
焦炉烟气脱硫脱硝,具体方案为: 焦炉烟道废气温度一般在220~290 oC之间.采 用低温选择性催化还原反应(SCR)技术,满足焦炉烟 道废气中NOx排放要求,即NO。排放浓度<500/150 ms/Nm3以下。SCR催化剂采用成都华西化工研究所 股份有限公司与合作单位开发的蜂窝式催化剂.主 要活性成分为TiO:和V20,,少量的W03、Re等稀土
2015焦化行业节能减排及干熄焦技术交流会
焦炉烟道废气脱硫脱硝除尘及余热回收—体化技术
任毅
(成都华西化工研究所股份有限公司)
[摘要]针对炼焦烟道废气的特点及脱硫脱硝技术发展现状,成都华西化工研究所股份有限公 司成功开发了一种焦炉烟道废气脱硫、脱硝、除尘及余热回收一体化技术。本文介绍了工艺流程, 并就工艺特点、脱硫、脱硝、除尘机理等方面做了简单阐述,并与其他工艺进行了对比,提出了合理 的工艺路线。
组分,该催化剂活性温度范围宽,在160~400 oC范 围都具有很好的催化活性。
脱硝采用16~26%的氨水作为还原剂。为炼焦 自产的焦化浓氨水并通过精制达到脱硝的要求。
脱硝后的焦炉烟道废气通过热管余热锅炉回 收焦炉烟道废气中热量生产蒸汽,蒸汽回收量可以 达到~100 ks/t焦炭(蒸汽发生量与人13焦炉烟道废 气密切相关)。
表2相关参数
蒸发段
烟道废气进口温度
290℃
℃
省煤段
烟道废气入口温度
195℃
烟道废气出口温度
160℃
工质入口温度
20℃
工质出口温度
154℃
采用热管余热锅炉。该结构最大优点是在设备 出现问题时,不影响炼焦生产的正常运行,对于炼 焦系统而言.安全性高。
热管是一根管子,里面存有工质(水),当烟道 废气加热热管时,水即蒸发并向上流动,与热管上 部的冷水接触,热管传热给冷水。热管中蒸汽凝结 并依靠重力流到热段。这个过程就形成了烟道废气 给冷水的热量传递。热管换热器热段与冷段用隔板 隔开。当烟道废气侧热管破裂时.水不能跑到烟道 废气侧,所以不影响炼焦烟道废气系统。只能引起 热管失效,即影响排烟温度。
表1 GBl6171-2012焦炉烟囱大气污染物排放 标准浓度限值
大气污染物排放限值 颗粒物
“表5”规定
30
“表6”规定
15
S02 mg,m3 50
30
NOx mg/m3
500 150
2焦炉烟道废气脱硝特点
1)焦炉烟道气温度较低。受焦炉炉型、燃料类 型、操作制度、现场管理水平等因素的影响,不同焦 化厂焦炉烟道气温度差别很大,一般在220~290 oC 之间,而电厂烟道废气温度为300。400 oC的,焦炉 烟道气温度相对较低,如果直接采用电厂烟道废气 脱硝所用的催化剂进行脱硝,脱硝效率低,很难满 足国家排放标准要求。
2015焦化行业节能减排及干熄焦技术交流会
67
5.3干法脱硫 焦炉烟道废气干法脱硫工艺以碳酸氢钠
(NaHCO,)作为吸收剂,碳酸氢钠经过粉碎机粉碎, 粉碎后过量的碳酸氢钠粉在高温烟气中受热分解 生成碳酸钠,碳酸钠吸收焦炉烟道废气中的S02和 SO,,表面反应生成Na2S04和Na 2。SO,,烟气携带未反 应的碳酸钠和反应生成的硫酸钠通过袋式除尘器 送到烟囱。
在SCR反应器内氨与氧化氮反应生成氮气和 水.反应方程式如下:
4NO+4NH3+02_÷6H20+4N2
NO+N02+2NH3-斗3H20+2N2
反应生成水和氮气随烟道废气进人热管余热 锅炉。
在SCR进口设置NOx,02、温度监视分析仪,在 SCR出口设置NOx,02、NH3监视分析仪。
注人格栅前分布管上设有厂用压缩空气管道, 当注人格栅喷头发生堵塞时进行吹扫。在氨气进装 置分管阀后设有氮气预留阀及接口。在停工检修时 用于吹扫管内氨气。 5.2焦炉烟道废气热量回收
焦炉烟囱排放的SO:是焦炉加热煤气中所含硫 化物燃烧产生的。主要包含焦炉加热用焦炉煤气中 H2s燃烧所生成的SO:;焦炉加热用焦炉煤气中有机 硫燃烧所生成的SO:;因焦炉炉体窜漏导致荒煤气 进入燃烧系统,其中所含的硫化物燃烧所生成的 SO:。焦炉烟道废气中排放的SO:根据各厂煤气净化 的程度和焦炉的管理水平,一般在100—600 mg/m3。
2)焦炉烟囱必须始终处于热备状态。焦炉烟道 气经过脱硫脱硝以后必须回到焦炉烟囱排放至大 气,使焦炉烟囱始终处于热备状态,一旦脱硫脱硝 装置故障停产,烟道废气能够通过原烟囱排放到大 气,不影响焦炉正常生产。因此经过脱硫脱硝后的
2015焦化行业节能减排及干熄焦技术交流会
烟道气温度必须高于烟道废气露点温度。且不得低 于130℃,不能直接采用电厂常用的湿法脱硫技术 进行烟道气脱硫。
3)NOx含量较高。目前运行的焦化厂焦炉烟道 气中NOx含量为800—1200 mg/Nm3。
4)SO:含量对低温脱硝的影响。独立焦化厂焦 炉烟道气中S02含量为50—600 mg/m3;采用SCR脱 硝在V20,催化剂的作用下,有一部分SO:被选择性 地转化为S03。在180℃至230℃温度区间内,NH, 与S03反应极易生成N14lI-ISO。。NI-LIHSO。极易潮解, 其熔点温度为147 oC,沸点为350℃。该物质非常粘 稠且难以清除,粘附在催化剂表面,会严重影响催 化剂使用效率。
SO:和S03,表面反应生成Na=,SO。和N硝O,,烟气携
带未反应的碳酸钠和反应生成的硫酸钠通过袋式 除尘器送到烟囱。
脱硫化学反应过程为:
2NaHC03—}Na2C03+C02+H20 Na2C03+S02-+Na2s03+2C02 2NaEC03+S02+02_+Na§04+C02 通过设置袋式除尘器分离脱硫后烟气中的反 应产物,控制滤袋的阻力损失.在滤袋表面形成一 定厚度的过滤层,在过滤层中Na2CO,继续与烟气中 酸性气态污染物发生反应,将焦炉烟道废气中SO:
降低到小于50/30 ms/Nm3。脱硫反应产物中还有部 分未反应的Na:CO,,通过循环再次喷人焦炉烟道废 气中,提高Na:CO,的利用效率。
5 焦炉烟道废气脱硫脱硝余热回收 工艺流程及工艺特点
工艺主要分为四个部分:焦炉烟道废气低温 SCR脱硝、热量回收、干法脱硫、浓氨水精制。
2015焦化行业节能减排及干熄焦技术交流会
从焦炉烟道废气脱硝装置来的烟道废气先经
过热管换热器换热,烟道废气温度降至195 oC.然后 进入省煤器预热锅炉给水,烟道废气温度进一步降 低至160 oC,送到干法脱硫装置。
来自界外的软水(20℃)进入除氧器,经热力除 氧后经锅炉给水泵升压进入省煤器预热至159 oC后 进入汽包。