金属断裂机理完整版
金属材料的疲劳断裂机理解析

金属材料的疲劳断裂机理解析疲劳断裂是一种金属材料在受到反复加载后,由于应力集中作用而在载荷作用下出现的断裂现象。
在工程应用中,经常会受到相反方向的交替载荷的作用,这样会引起疲劳断裂问题。
因此,了解金属材料的疲劳断裂机理对于确保工程结构的安全可靠性至关重要。
疲劳断裂机理的研究历史可以追溯到20世纪初期,最初是在航空领域进行的。
人们开始注意到,航空器上的零件由于反复加载而发生疲劳断裂,如轴、桁架、螺栓等零部件。
在研究中,人们发现疲劳断裂与材料中的微观缺陷有关。
这些缺陷可以是材料内的夹杂、异相、孔洞、裂纹等,也可以是表面上的裂纹、腐蚀痕迹等。
对于金属材料疲劳断裂机理的研究,人们通常采用线应力范围S-N曲线进行实验研究。
这种曲线是将载荷幅值S和疲劳寿命N 以双对数坐标轴上绘制,研究者根据实验结果绘制不同应力幅值下的S-N曲线。
在这种曲线上可以找到最小疲劳强度极限,也就是金属可以承受多少次疲劳循环,最终导致疲劳断裂。
线应力范围S-N曲线的研究是设计金属零部件的必要环节之一,只有在了解材料特性中的疲劳强度极限和影响因素之后,才能够准确地进行零部件的设计。
在实际的工程应用中,疲劳断裂机理是多种多样的。
因此,根据组织结构不同,疲劳断裂机理也有所不同。
下面我们对金属材料的疲劳断裂机理进行详细分析:1. 基体内夹杂贡献金属材料中的夹杂是人工制备和自然形成的,包括铁锈、铝夹杂、夹杂物等。
这些夹杂在载荷作用下可以引起应力集中作用,从而在周围材料中形成一个高应力集中区域。
当这个区域受到一定数量的冲击时,就会导致夹杂物内部的微裂纹增长。
这些微裂纹随着载荷的增加而逐渐扩展,最终导致疲劳断裂。
2. 不均匀形变贡献金属材料在受到载荷作用时,所受到的变形十分不均匀。
在材料中,往往存在一些应力集中区域,这些区域所受到的变形也会比周围的区域更大。
这种不均匀形变会导致表面裂纹、夹杂物等缺陷的内部发生更多的塑性变形,因此这些缺陷的情况也会随着时间的推移变得更加严重。
金属断裂机理(完整版)
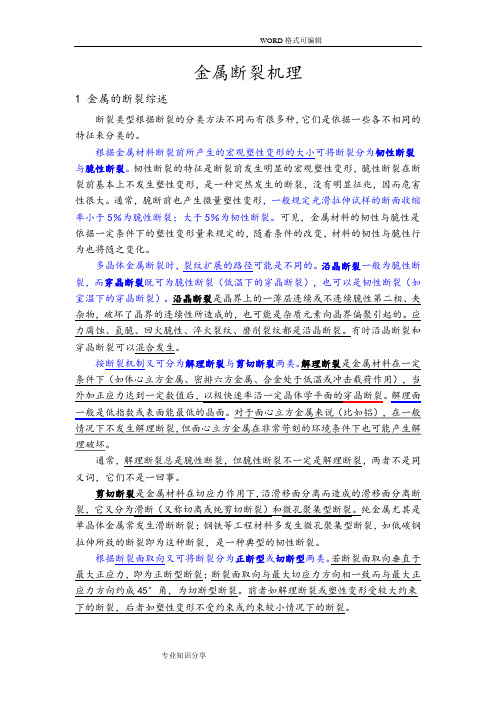
金属断裂机理1 金属的断裂综述断裂类型根据断裂的分类方法不同而有很多种,它们是依据一些各不相同的特征来分类的。
根据金属材料断裂前所产生的宏观塑性变形的大小可将断裂分为韧性断裂与脆性断裂。
韧性断裂的特征是断裂前发生明显的宏观塑性变形,脆性断裂在断裂前基本上不发生塑性变形,是一种突然发生的断裂,没有明显征兆,因而危害性很大。
通常,脆断前也产生微量塑性变形,一般规定光滑拉伸试样的断面收缩率小于5%为脆性断裂;大于5%为韧性断裂。
可见,金属材料的韧性与脆性是依据一定条件下的塑性变形量来规定的,随着条件的改变,材料的韧性与脆性行为也将随之变化。
多晶体金属断裂时,裂纹扩展的路径可能是不同的。
沿晶断裂一般为脆性断裂,而穿晶断裂既可为脆性断裂(低温下的穿晶断裂),也可以是韧性断裂(如室温下的穿晶断裂)。
沿晶断裂是晶界上的一薄层连续或不连续脆性第二相、夹杂物,破坏了晶界的连续性所造成的,也可能是杂质元素向晶界偏聚引起的。
应力腐蚀、氢脆、回火脆性、淬火裂纹、磨削裂纹都是沿晶断裂。
有时沿晶断裂和穿晶断裂可以混合发生。
按断裂机制又可分为解理断裂与剪切断裂两类。
解理断裂是金属材料在一定条件下(如体心立方金属、密排六方金属、合金处于低温或冲击载荷作用),当外加正应力达到一定数值后,以极快速率沿一定晶体学平面的穿晶断裂。
解理面一般是低指数或表面能最低的晶面。
对于面心立方金属来说(比如铝),在一般情况下不发生解理断裂,但面心立方金属在非常苛刻的环境条件下也可能产生解理破坏。
通常,解理断裂总是脆性断裂,但脆性断裂不一定是解理断裂,两者不是同义词,它们不是一回事。
剪切断裂是金属材料在切应力作用下,沿滑移面分离而造成的滑移面分离断裂,它又分为滑断(又称切离或纯剪切断裂)和微孔聚集型断裂。
纯金属尤其是单晶体金属常发生滑断断裂;钢铁等工程材料多发生微孔聚集型断裂,如低碳钢拉伸所致的断裂即为这种断裂,是一种典型的韧性断裂。
根据断裂面取向又可将断裂分为正断型或切断型两类。
第一章 材料在静载下的力学行为3(4.1金属的断裂)
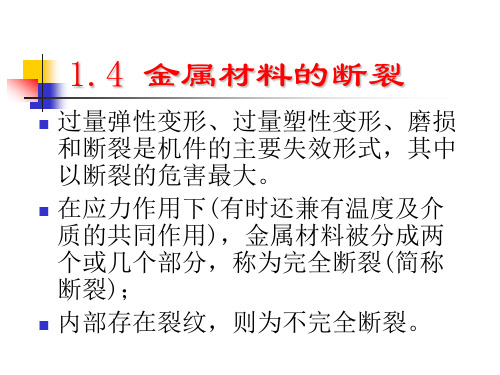
沿晶断裂的断口形貌呈冰糖状,有时也称“萘状断 口”,上左图为18CrNiWA钢的冰糖状断口。 如晶粒很细小,则肉眼无法辨认出冰糖状形貌,此 时断口一般呈晶粒状,颜色较纤维状断口明亮,但 比纯脆性断口要灰暗些。 穿晶断裂和沿晶断裂有时可以混合发生。
剪切断裂与解理断裂
(1)剪切断裂是金属材料在切应力作用下沿滑 移面分离而造成的滑移面分离断裂,其中又 分滑断(纯剪切断裂)和微孔聚集型断裂。
(2)解理断裂
解理断裂是金属材料在一定条件下(如低温),当外 加正应力达到一定数值后,以极快速率沿一定晶体 学平面产生的穿晶断裂,因与大理石断裂类似,故 称此种晶体学平面为解理面。 一般在体心立方、密排六方金属中发生,而面心立 方金属只在特殊情况下才发生。 解理面一般是低指数晶面或裸露后表面能最低的晶 面。 解理断裂总是脆性断裂,但有时在解理断裂前也显 示一定的塑性变形,所以解理断裂与脆性断裂不是 同义词,解理断裂指断裂机理而言,脆性断裂则指 断裂的宏观性态。
1.甄纳-斯特罗位错塞积理论
在滑移面上的切应力作用下, 刃型位错在晶界前受阻并互 相靠近形成位错塞积,如果 塞积头处的应力集中不能为 塑性变形所松弛,当切应力 达到某一临界值时,塞积头 处的最大拉应力能够等于材 料理论断裂强度而形成高nb、 长为r的楔形裂纹。
解理裂纹的形成,并不意味着裂纹将迅速扩 展而导致金属材料完全断裂。 柯垂耳用能量分析法推导出解理裂纹扩展的 临界条件为
放射区的形成过程
纤维区中裂纹扩展是很慢的,当其达到临界尺寸后 就快速扩展而形成放射区。 放射区有放射线花样特征。放射线平行于裂纹扩展 方向而垂直于裂纹前端(每一瞬间)的轮廓线,并逆 指向裂纹源。 撕裂时塑性变形量越大,则放射线越粗。对于几乎 不产生塑性变形的极脆材料,放射线消失。 温度降低或材料强度增加,由于塑性降低,放射线 由粗变细乃至消失。
金属材料的断裂力学分析
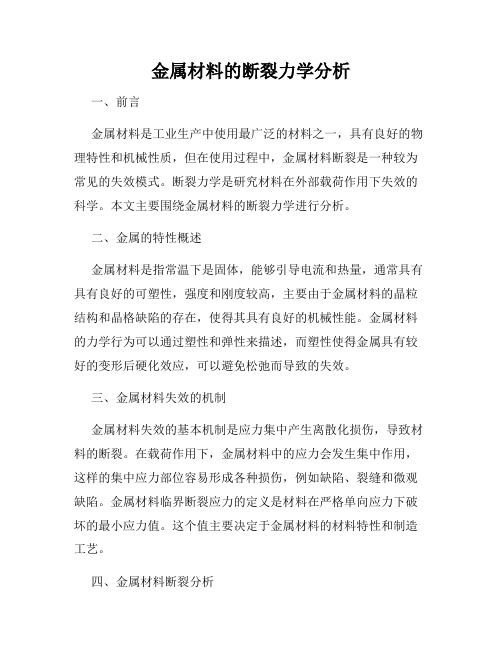
金属材料的断裂力学分析一、前言金属材料是工业生产中使用最广泛的材料之一,具有良好的物理特性和机械性质,但在使用过程中,金属材料断裂是一种较为常见的失效模式。
断裂力学是研究材料在外部载荷作用下失效的科学。
本文主要围绕金属材料的断裂力学进行分析。
二、金属的特性概述金属材料是指常温下是固体,能够引导电流和热量,通常具有具有良好的可塑性,强度和刚度较高,主要由于金属材料的晶粒结构和晶格缺陷的存在,使得其具有良好的机械性能。
金属材料的力学行为可以通过塑性和弹性来描述,而塑性使得金属具有较好的变形后硬化效应,可以避免松弛而导致的失效。
三、金属材料失效的机制金属材料失效的基本机制是应力集中产生离散化损伤,导致材料的断裂。
在载荷作用下,金属材料中的应力会发生集中作用,这样的集中应力部位容易形成各种损伤,例如缺陷、裂缝和微观缺陷。
金属材料临界断裂应力的定义是材料在严格单向应力下破坏的最小应力值。
这个值主要决定于金属材料的材料特性和制造工艺。
四、金属材料断裂分析金属材料的断裂分析主要涵盖了材料损伤形成、损伤扩展和破坏机理分析等。
微观结构、应力、损伤、断裂等因素都可以影响材料的断裂力学行为。
因此,断裂力学的分析需要结合多个方面的知识与技术来展开。
常用的断裂力学分析方法主要包括有限元分析、断裂力学模型和试验分析等。
有限元分析是利用计算机程序把真实的结构抽象化成有限的元素,利用这些元素之间的相对位置关系和应力、位移等变量来求解物体的力学行为。
通过有限元分析可以评估金属材料中存在的缺陷和微观结构对其力学性能的影响。
断裂力学常用的模型包括破裂、塑性和弹塑性模型、裂缝力学模型和疲劳模型等。
这些模型可以用于描述材料的基本性质,例如断裂韧性、脆性和持久性等参数。
试验分析是将不同载荷下的材料样品进行试验,以获取其断裂行为。
这些试验包括金属的拉伸试验、压缩试验、扭转试验等,可用于获得属于材料的力学行为数据。
五、结论本文通过对金属材料的特性、失效机制和断裂分析等方面的阐述,介绍了金属材料的断裂力学分析。
金属断裂机理
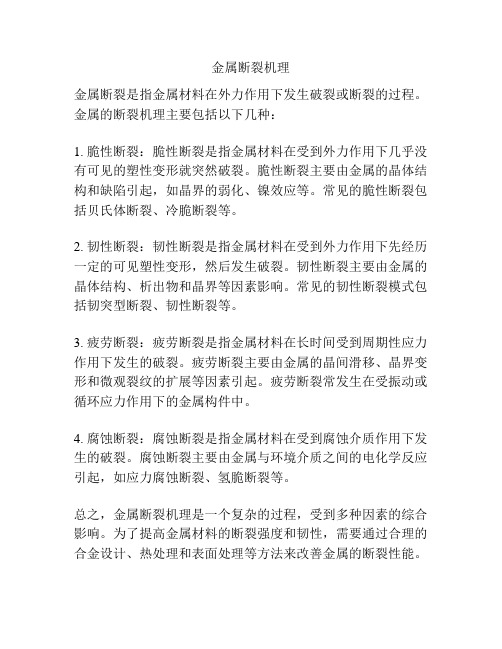
金属断裂机理
金属断裂是指金属材料在外力作用下发生破裂或断裂的过程。
金属的断裂机理主要包括以下几种:
1. 脆性断裂:脆性断裂是指金属材料在受到外力作用下几乎没有可见的塑性变形就突然破裂。
脆性断裂主要由金属的晶体结构和缺陷引起,如晶界的弱化、镍效应等。
常见的脆性断裂包括贝氏体断裂、冷脆断裂等。
2. 韧性断裂:韧性断裂是指金属材料在受到外力作用下先经历一定的可见塑性变形,然后发生破裂。
韧性断裂主要由金属的晶体结构、析出物和晶界等因素影响。
常见的韧性断裂模式包括韧突型断裂、韧性断裂等。
3. 疲劳断裂:疲劳断裂是指金属材料在长时间受到周期性应力作用下发生的破裂。
疲劳断裂主要由金属的晶间滑移、晶界变形和微观裂纹的扩展等因素引起。
疲劳断裂常发生在受振动或循环应力作用下的金属构件中。
4. 腐蚀断裂:腐蚀断裂是指金属材料在受到腐蚀介质作用下发生的破裂。
腐蚀断裂主要由金属与环境介质之间的电化学反应引起,如应力腐蚀断裂、氢脆断裂等。
总之,金属断裂机理是一个复杂的过程,受到多种因素的综合影响。
为了提高金属材料的断裂强度和韧性,需要通过合理的合金设计、热处理和表面处理等方法来改善金属的断裂性能。
金属断裂机理完整版
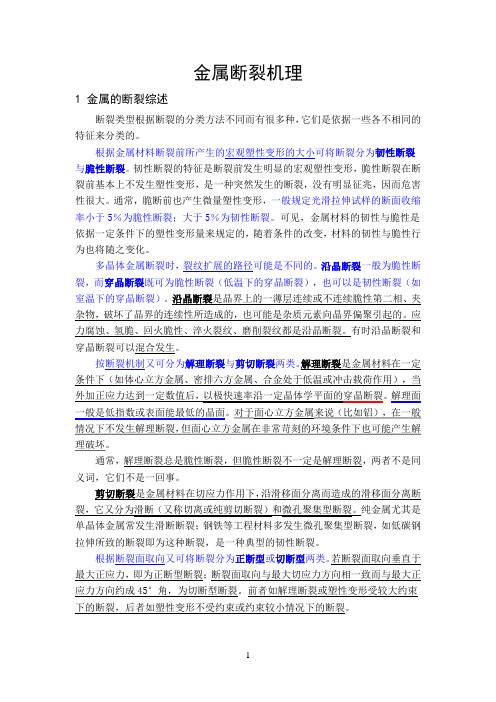
金属断裂机理1 金属的断裂综述断裂类型根据断裂的分类方法不同而有很多种,它们是依据一些各不相同的特征来分类的。
根据金属材料断裂前所产生的宏观塑性变形的大小可将断裂分为韧性断裂与脆性断裂。
韧性断裂的特征是断裂前发生明显的宏观塑性变形,脆性断裂在断裂前基本上不发生塑性变形,是一种突然发生的断裂,没有明显征兆,因而危害性很大。
通常,脆断前也产生微量塑性变形,一般规定光滑拉伸试样的断面收缩率小于5%为脆性断裂;大于5%为韧性断裂。
可见,金属材料的韧性与脆性是依据一定条件下的塑性变形量来规定的,随着条件的改变,材料的韧性与脆性行为也将随之变化。
多晶体金属断裂时,裂纹扩展的路径可能是不同的。
沿晶断裂一般为脆性断裂,而穿晶断裂既可为脆性断裂(低温下的穿晶断裂),也可以是韧性断裂(如室温下的穿晶断裂)。
沿晶断裂是晶界上的一薄层连续或不连续脆性第二相、夹杂物,破坏了晶界的连续性所造成的,也可能是杂质元素向晶界偏聚引起的。
应力腐蚀、氢脆、回火脆性、淬火裂纹、磨削裂纹都是沿晶断裂。
有时沿晶断裂和穿晶断裂可以混合发生。
按断裂机制又可分为解理断裂与剪切断裂两类。
解理断裂是金属材料在一定条件下(如体心立方金属、密排六方金属、合金处于低温或冲击载荷作用),当外加正应力达到一定数值后,以极快速率沿一定晶体学平面的穿晶断裂。
解理面一般是低指数或表面能最低的晶面。
对于面心立方金属来说(比如铝),在一般情况下不发生解理断裂,但面心立方金属在非常苛刻的环境条件下也可能产生解理破坏。
通常,解理断裂总是脆性断裂,但脆性断裂不一定是解理断裂,两者不是同义词,它们不是一回事。
剪切断裂是金属材料在切应力作用下,沿滑移面分离而造成的滑移面分离断裂,它又分为滑断(又称切离或纯剪切断裂)和微孔聚集型断裂。
纯金属尤其是单晶体金属常发生滑断断裂;钢铁等工程材料多发生微孔聚集型断裂,如低碳钢拉伸所致的断裂即为这种断裂,是一种典型的韧性断裂。
根据断裂面取向又可将断裂分为正断型或切断型两类。
金属材料疲劳断裂机理分析
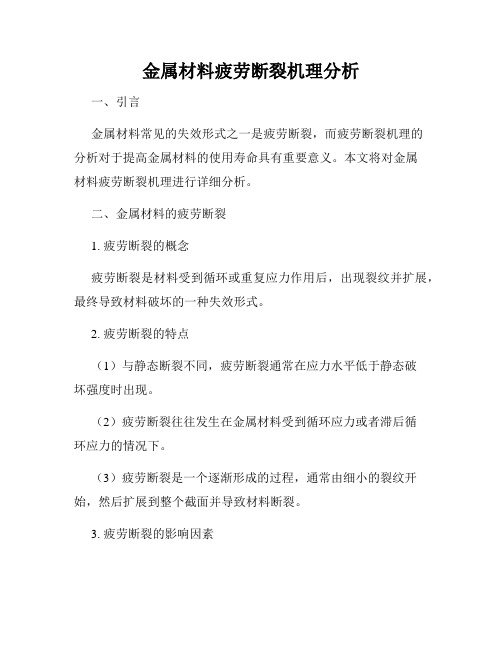
金属材料疲劳断裂机理分析一、引言金属材料常见的失效形式之一是疲劳断裂,而疲劳断裂机理的分析对于提高金属材料的使用寿命具有重要意义。
本文将对金属材料疲劳断裂机理进行详细分析。
二、金属材料的疲劳断裂1. 疲劳断裂的概念疲劳断裂是材料受到循环或重复应力作用后,出现裂纹并扩展,最终导致材料破坏的一种失效形式。
2. 疲劳断裂的特点(1)与静态断裂不同,疲劳断裂通常在应力水平低于静态破坏强度时出现。
(2)疲劳断裂往往发生在金属材料受到循环应力或者滞后循环应力的情况下。
(3)疲劳断裂是一个逐渐形成的过程,通常由细小的裂纹开始,然后扩展到整个截面并导致材料断裂。
3. 疲劳断裂的影响因素(1)应力幅值对于金属材料疲劳断裂的影响很大。
一般来说,应力幅值越大,疲劳断裂的损伤就越严重。
(2)材料的力学性质对于疲劳断裂也有很大的影响。
通常来说,强度越高的材料越难发生疲劳断裂,但是当强度相同时,材料的硬度越高,就越容易疲劳断裂。
(3)疲劳断裂还受到持续时间、温度、材料的化学成分和缺陷的影响。
4. 疲劳断裂的分类根据裂纹的扩展速率和应力比,疲劳断裂可以分为以下几类:(1)低周疲劳断裂:在循环应力下,材料的裂纹扩展速率很慢,往往需要上百万以上次循环才会导致疲劳断裂。
(2)中周疲劳断裂:循环应力下材料的裂纹扩展速率较快,在千-十万次循环后就能导致疲劳断裂。
(3)高周疲劳断裂:循环应力下材料的裂纹扩展速率极快,在数十万-数百万次循环内就会导致疲劳断裂。
5. 疲劳断裂的机理(1)金属材料的疲劳断裂过程一般分为始裂阶段和稳定扩展阶段。
(2)始裂阶段:在材料表面出现较小的裂纹,形成的原因是在应力作用下,材料中的微小缺陷和夹杂物开始聚集和扩散。
(3)稳定扩展阶段:当裂纹扩展到一定长度时,会出现塑性形变,当扩展到一定程度时,材料就会出现断裂。
(4)材料疲劳断裂机理可以采用形变、断裂学和金相学等多方面知识进行解释。
三、疲劳断裂机理分析1. 循环应力下的金属变形材料在循环应力下,会出现塑性变形和弹性变形两种不同的变形形式。
金属材料的力学行为与断裂机理
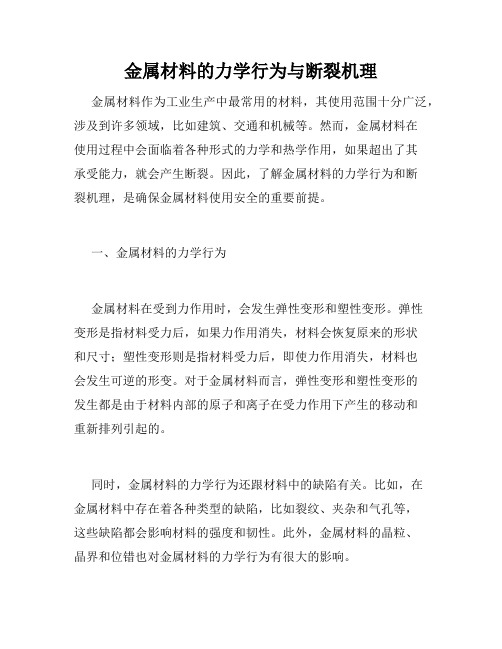
金属材料的力学行为与断裂机理金属材料作为工业生产中最常用的材料,其使用范围十分广泛,涉及到许多领域,比如建筑、交通和机械等。
然而,金属材料在使用过程中会面临着各种形式的力学和热学作用,如果超出了其承受能力,就会产生断裂。
因此,了解金属材料的力学行为和断裂机理,是确保金属材料使用安全的重要前提。
一、金属材料的力学行为金属材料在受到力作用时,会发生弹性变形和塑性变形。
弹性变形是指材料受力后,如果力作用消失,材料会恢复原来的形状和尺寸;塑性变形则是指材料受力后,即使力作用消失,材料也会发生可逆的形变。
对于金属材料而言,弹性变形和塑性变形的发生都是由于材料内部的原子和离子在受力作用下产生的移动和重新排列引起的。
同时,金属材料的力学行为还跟材料中的缺陷有关。
比如,在金属材料中存在着各种类型的缺陷,比如裂纹、夹杂和气孔等,这些缺陷都会影响材料的强度和韧性。
此外,金属材料的晶粒、晶界和位错也对金属材料的力学行为有很大的影响。
二、金属材料的断裂机理金属材料的断裂机理十分复杂,具体的机理取决于材料的类型、应力状态和温度等因素。
一般来说,金属材料的断裂可以分为两种类型:韧性断裂和脆性断裂。
韧性断裂是金属材料在受到一定的力作用后发生的变形和形变之后,最终断裂。
这种类型的断裂是由于材料在受力过程中,几乎所有的原子和离子都参与了变形,使得材料的内部形成了许多弥散的、大小不等的微小裂纹。
当材料受到足够大的拉伸应力时,这些微小裂纹就会逐渐扩展,直到穿过整个材料,导致材料的断裂。
脆性断裂则是指金属材料在受到一定力作用后,很快就会发生断裂,而在断裂前无明显的塑性变形。
脆性断裂通常发生在低温和高应力的条件下,这是由于在这种条件下,材料内部的微观结构受到应力作用后无法形成有效的位错滑移,因此引发的应力集中会直接导致断裂。
三、金属材料的力学行为和断裂机理的影响因素金属材料的力学行为和断裂机理受到许多因素的影响,这些因素包括:温度、应力状态、速率、材料缺陷和晶格结构等。
金属断口机理及分析

名词解释延性断裂:金属材料在过载负荷的作用下,局部发生明显的宏观塑性变形后断裂。
蠕变:金属长时间在恒应力,恒温作用下,慢慢产生塑性变形的现象。
准解理断裂:断口形态与解理断口相似,但具有较大塑性变形〔变形量大于解理断裂、小于延性断裂〕是一种脆性穿晶断口沿晶断裂:裂纹沿着晶界扩展的方式发生的断裂。
解理断裂:在正应力作用下沿解理面发生的穿晶脆断。
应力腐蚀断裂:拉应力和腐蚀介质联合作用的低应力脆断疲劳辉纹:显微观察疲劳断口时,断口上细小的,相互平行的具有规则间距的,与裂纹扩展方向垂直的显微条纹。
正断:断面取向与最大正应力相垂直〔解理断裂、平面应变条件下的断裂〕韧性:材料从变形到断裂过程中吸收能量的大小,是材料强度和塑性的综合反映。
冲击韧性:冲击过程中材料吸收的功除以断的面积。
位向腐蚀坑技术:利用材料腐蚀后的几何形状与晶面指数之间的关系研究晶体取向,分析断裂机理或断裂过程。
河流把戏:解理台阶及局部塑性变形形成的撕裂脊线所组成的条纹。
其形状类似地图上的河流。
断口萃取复型:利用AC纸将断口上夹杂物或第二相质点萃取下来做电子衍射分析确定这些质点的晶体构造。
氢脆:金属材料由于受到含氢气氛的作用而引起的低应力脆断。
卵形韧窝:大韧窝在长大过程中与小韧窝交截产生的。
等轴韧窝:拉伸正应力作用下形成的圆形微坑。
均匀分布于断口外表,显微洞孔沿空间三维方向均匀长大。
第一章断裂的分类及特点1.根据宏观现象分:脆性断裂和延伸断裂。
脆性断裂裂纹源:材料外表、内部的缺陷、微裂纹;断口:平齐、与正应力相垂直,人字纹或放射花纹。
延性断裂裂纹源:孔穴的形成和合并;断口:三区,无光泽的纤维状,剪切面断裂、与拉伸轴线成45º .2.根据断裂扩展途分:穿晶断裂与沿晶断裂。
穿晶断裂:裂纹穿过晶粒内部、可能为脆性断裂也可能是延性断裂;沿晶断裂:裂纹沿着晶界扩展,多属脆断。
应力腐蚀断口,氢脆断口。
3根据微观断裂的机制上分:韧窝、解理〔及准解理〕、沿晶和疲劳断裂4根据断面的宏观取向与最大正应力的交角分:正断、切断正断:断面取向与最大正应力相垂直〔解理断裂、平面应变条件下的断裂〕切断:断面取向与最大切应力相一致,与最大应力成45º交角〔平面应力条件下的撕裂〕根据裂纹尖端应力分布的不同,主要可分为三类裂纹变形:裂纹张开型、边缘滑开型〔正向滑开型〕、侧向滑开型〔撒开型〕裂纹尺寸与断裂强度的关系Kic:材料的断裂韧性,反映材料抗脆性断裂的物理常量〔不同于应力强度因子,与K准则相似〕:断裂应力〔剩余强度〕 a :裂纹深度〔长度〕Y:形状系数〔与试样几何形状、载荷条件、裂纹位置有关〕脆性材料K准则:KI是由载荷及裂纹体的形状和尺寸决定的量,是表征裂纹尖端应力场强度的计算量;KIC是材料固有的机械性能参量,是表示材料抵抗脆断能力的试验量第二章裂纹源位置的判别方法:T型法〔脆断判别主裂纹〕,分差法〔脆断判别主裂纹〕,变形法〔韧断判别主裂纹〕,氧化法〔环境断裂判别主裂纹〕,贝纹线法〔适用于疲劳断裂判别主裂纹〕。
经典金属疲劳裂纹扩展至断裂机理讲解(专业级)
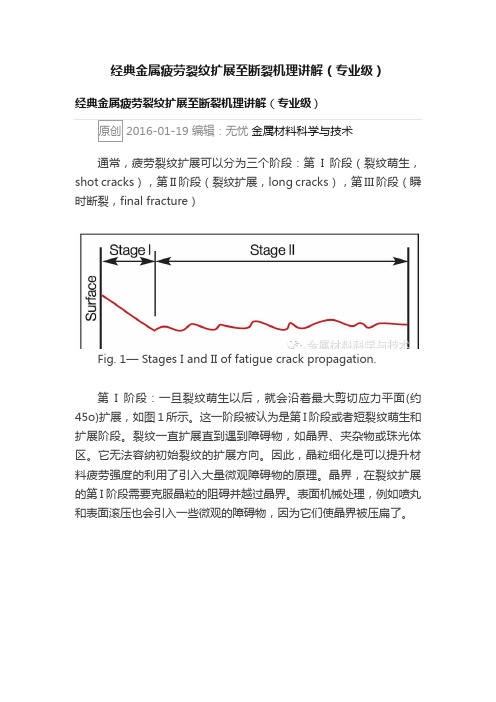
经典金属疲劳裂纹扩展至断裂机理讲解(专业级)经典金属疲劳裂纹扩展至断裂机理讲解(专业级)通常,疲劳裂纹扩展可以分为三个阶段:第I阶段(裂纹萌生,shot cracks),第II阶段(裂纹扩展,long cracks),第III阶段(瞬时断裂,final fracture)Fig. 1— Stages I and II of fatigue crack propagation.第I阶段:一旦裂纹萌生以后,就会沿着最大剪切应力平面(约45o)扩展,如图1所示。
这一阶段被认为是第I阶段或者短裂纹萌生和扩展阶段。
裂纹一直扩展直到遇到障碍物,如晶界、夹杂物或珠光体区。
它无法容纳初始裂纹的扩展方向。
因此,晶粒细化是可以提升材料疲劳强度的利用了引入大量微观障碍物的原理。
晶界,在裂纹扩展的第I阶段需要克服晶粒的阻碍并越过晶界。
表面机械处理,例如喷丸和表面滚压也会引入一些微观的障碍物,因为它们使晶界被压扁了。
Fig. 2 — Fatigue striations in (a) interstitial free steel and (b)aluminum alloy AA2024-T42. Figure (c) shows the fatigue fracture surface of a cast aluminum alloy, where a fatigue crack was nucleated from a casting defect, presenting solidification dendrites on the surface; fatigue striations are indicated by the arrow, on the top right side.第II阶段:由于裂纹扩展,实际载荷的上升,应力强度因子K不断增加,在裂纹尖端附近的不同平面上开始发生滑移,于是就进入了第II阶段。
金属疲劳断裂的微观机理分析

金属疲劳断裂的微观机理分析一、金属疲劳断裂的基本概念金属疲劳断裂是指金属材料在受到重复或循环加载作用下,经过一定周期后发生的断裂现象。
这种现象在工程结构中极为常见,对材料的可靠性和安全性构成了严重威胁。
金属疲劳断裂是一个复杂的物理过程,涉及到材料的微观结构、应力状态、加载条件等多种因素。
1.1 金属疲劳断裂的定义与分类金属疲劳断裂通常可以分为低周疲劳和高周疲劳两种类型。
低周疲劳是指在较少的循环次数下,材料因塑性变形累积而发生断裂;而高周疲劳则是在大量的循环加载下,材料在没有明显塑性变形的情况下发生断裂。
此外,根据断裂的微观机制,金属疲劳断裂还可以进一步细分为穿晶断裂和沿晶断裂。
1.2 金属疲劳断裂的影响因素金属疲劳断裂的影响因素众多,包括但不限于材料的化学成分、微观组织、晶粒大小、应力集中、加载频率、环境条件等。
这些因素通过不同的机制影响材料的疲劳寿命和断裂行为。
1.3 金属疲劳断裂的研究意义深入研究金属疲劳断裂的微观机理,对于提高工程结构的可靠性、预测和防止疲劳失效具有重要的理论和实际意义。
通过优化材料设计、改进加工工艺、采用合理的加载方式等措施,可以有效延长材料的疲劳寿命,减少因疲劳断裂导致的损失。
二、金属疲劳断裂的微观机理金属疲劳断裂的微观机理是材料科学领域的研究热点之一。
通过对金属疲劳断裂过程中微观结构变化的观察和分析,可以揭示疲劳裂纹的萌生、扩展和最终断裂的内在机制。
2.1 疲劳裂纹的萌生机理疲劳裂纹通常在材料表面或内部的应力集中区域萌生。
在循环加载作用下,材料表面或内部的微观缺陷(如夹杂、孔洞、晶界等)会逐渐发展成为微裂纹。
微裂纹的形成和发展与材料的微观结构、应力状态和加载条件密切相关。
2.2 疲劳裂纹的扩展机理当微裂纹形成后,会在循环应力的作用下逐渐扩展。
疲劳裂纹的扩展过程可以分为三个阶段:裂纹的微观扩展、宏观扩展和快速断裂。
在微观扩展阶段,裂纹主要沿着晶粒内部扩展,受到晶粒取向、位错运动等因素的影响。
金属脆断裂的三个阶段
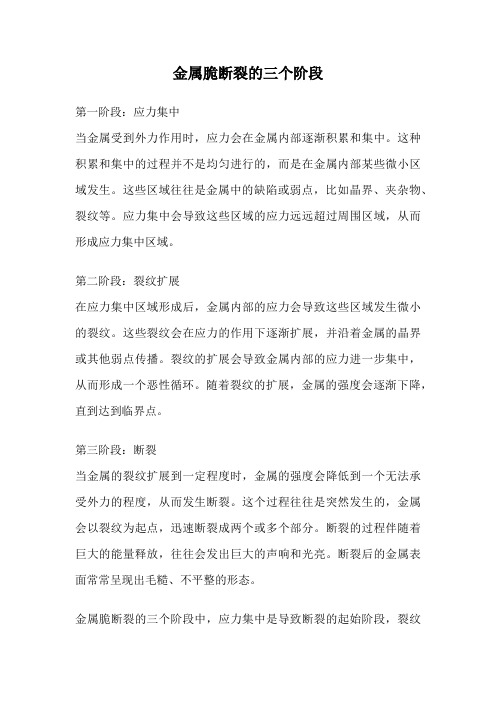
金属脆断裂的三个阶段
第一阶段:应力集中
当金属受到外力作用时,应力会在金属内部逐渐积累和集中。
这种积累和集中的过程并不是均匀进行的,而是在金属内部某些微小区域发生。
这些区域往往是金属中的缺陷或弱点,比如晶界、夹杂物、裂纹等。
应力集中会导致这些区域的应力远远超过周围区域,从而形成应力集中区域。
第二阶段:裂纹扩展
在应力集中区域形成后,金属内部的应力会导致这些区域发生微小的裂纹。
这些裂纹会在应力的作用下逐渐扩展,并沿着金属的晶界或其他弱点传播。
裂纹的扩展会导致金属内部的应力进一步集中,从而形成一个恶性循环。
随着裂纹的扩展,金属的强度会逐渐下降,直到达到临界点。
第三阶段:断裂
当金属的裂纹扩展到一定程度时,金属的强度会降低到一个无法承受外力的程度,从而发生断裂。
这个过程往往是突然发生的,金属会以裂纹为起点,迅速断裂成两个或多个部分。
断裂的过程伴随着巨大的能量释放,往往会发出巨大的声响和光亮。
断裂后的金属表面常常呈现出毛糙、不平整的形态。
金属脆断裂的三个阶段中,应力集中是导致断裂的起始阶段,裂纹
扩展是导致断裂的主要过程,而断裂则是结果。
了解金属脆断裂的三个阶段对于工程和材料科学领域的研究和应用具有重要意义。
只有深入了解金属脆断裂的机理和特点,才能更好地设计和制造出更安全可靠的金属材料。
金属材料的断裂和断裂韧性课件PPT
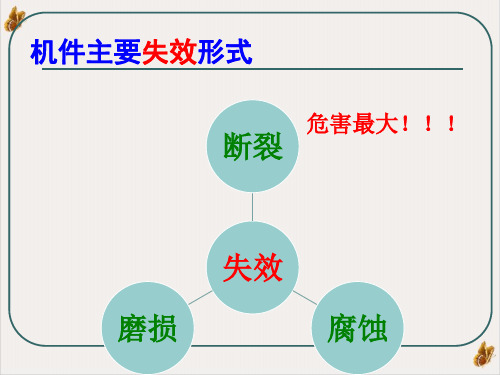
撕裂棱的形成过程示意图
19
准解理断裂和解理断裂的异同
同:穿晶断裂,脆性断裂,有小解理刻面、台阶。
①断裂起源:准解理源于晶粒内部的空洞、夹杂物、第二相粒子 ,而 解理则自晶界/相界一侧向另一侧延伸; ② 裂纹传播途径:准解理向四周放射状不连续扩展,与晶粒位向无关, 与细小第二相有关,解理是由晶界向晶内扩展,形成河流花样; ③ 解理位向:准解理小平面的位向与基体解理面之间无确定的对应关 系,源头不清。
微观:大量韧窝,内含夹杂物或第二相,微孔萌生处。
无明显塑性变形,沿解理面分离,穿晶断裂
在晶内微孔聚合,穿晶断裂
应力强度因子KI和断裂韧性KIc
ห้องสมุดไป่ตู้
低于许用应力,构件突然断裂 金属:裂纹尖端塑性区尺寸远小于裂纹长度。
微孔聚集断裂机理:形核—长大—聚合
三种基本断裂类型的实例
宏观解理断口:较为平坦、发亮的结晶状断面。
前推进直至断裂。
27
微孔聚合的三种形式 剪切裂纹一般沿滑移线发生.
高强材度料钢内常部发本生身这存种在模着式大的片微的孔夹聚杂合,,微 微孔成核源:第二相粒子其。韧孔性通较过“脆正弱常的的夹”杂微连孔成聚裂合纹模。式要 在应力作用下,基体和第差二。相这粒是子不的合界格面材脱料开出,现的一种缺陷 或第二相粒子本身开裂,于是出现微孔。
的流向与裂纹扩展方向一致 。
➢ 原因一:通过扭曲晶界或大角度晶界,相邻晶粒内解理面位向差很
大,裂纹在晶界受阻,裂纹尖端高应变激发晶界另一侧面裂纹成核。
➢ 原因二:裂纹不沿单一晶面发生,在跨越若干个相互平行的位于不
同高度上的解理面处发生,在交界处形成台阶。
➢ 解理断裂的另一个微观特征:舌状花样,它是解理裂纹沿孪晶界扩
金属的应力腐蚀和氢脆断裂(最全版)PTT文档

3、显微组织对耐磨性的影响 4、服役工况的影响
三、提高材料耐磨性的措施
1、工况分析 2、选材及其强化处理
Hale Waihona Puke 感谢观看金属的应力腐蚀和氢脆断裂
二、应力腐蚀
1、机理 滑移——溶解理论(钝化膜破坏 理论) a)应力作用下,滑移台阶露头 且钝化膜破裂(在表面或裂纹 面); b)电化学腐蚀(有钝化膜的金 属为阴极,新鲜金属为阳极); c)应力集中,使阳极电极电位 降低,加大腐蚀; d)若应力集中始终存在,则微 电池反应不断进行,钝化膜不能 恢复。则裂纹逐步向纵深扩展。 (该理论只能很好地解释沿晶断 裂的应力腐蚀)
间隙原子状 固溶在金属中;
将不发生应力腐蚀断裂的最大应力场强度因子,称为应力腐蚀临界应力场强度因子。
1、是材料的物性与服役工况的综合表现。 b)电化学腐蚀(有钝化膜的金属为阴极,新鲜金属为阳极); 化学物(氢化物)。
二、氢脆类型及其特征
1、氢蚀(或称气蚀) 高压气泡(H2,CH4) 宏观断口:呈氧化色,颗粒状(沿晶); 微观断口:晶界明显加宽,沿晶断裂。
三、钢的氢致延滞断裂机理
三个阶段:孕育,亚稳扩展,失稳扩展。 1)孕育期 氢原子数量↑;扩散,偏聚。 氢固溶,在位错线周围偏聚,形成气团;位错运动受 阻,产生应力集中,萌生裂纹。 2)温度的影响 tt3<>)ttHH应氢氢力扩气状散团况率扩很散漫,,无不氢形脆成。氢脆;t=tH 最敏感; 应变速率高,不会出现氢脆。拉应力促进H溶解。
高强钢的氢致延滞裂还具有可逆性。[循环软化]
四、氢致延滞断裂与应力腐蚀的关系。 “相互促进” 阳极溶解、金属开裂 阴极吸氢,延滞断裂。
五、防止氢脆的措施 1)材料 降低含氢量,细化组织 2)环境 减少吸氢的可能性 3)力学因素 减小残余应力
材料力学 论金属的断裂
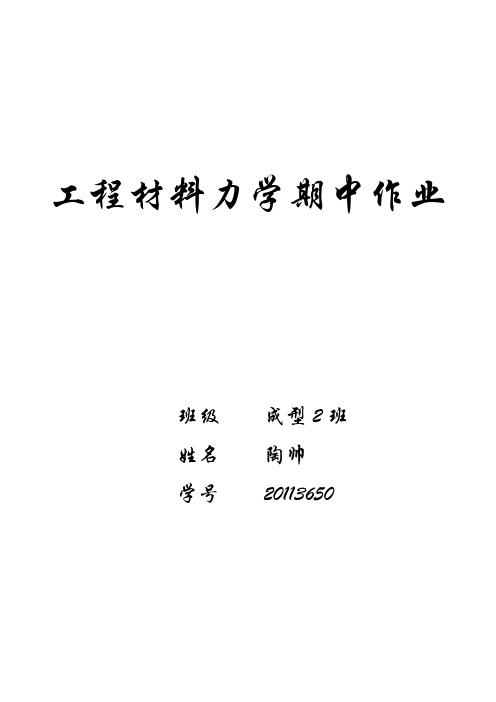
工程材料力学期中作业班级成型2班姓名陶帅学号20113650论述金属的断裂一、基本介绍概念:金属材料在外力作用下断裂成两部分的现象。
磨损、腐蚀和断裂是机件的三种主要失效形式,其中以断裂的危害最大。
在应力作用下(有时还兼有热及介的共同作用),金属材料被分成两个或几个部分,称为完全断裂;内部存在裂纹,则为不完全断裂。
实践证明,大多数金属材料的断裂过程都包括裂纹形成与扩展两个阶段。
对于不同的断裂类型,这两个阶段的机理与特征并不相同。
二、断裂的基本类型弹性变形→塑性变形→断裂1,根据材料断裂前产生的宏观塑性变形量的大小来确定断裂类型,可分为韧性断裂和脆性断裂。
2,多晶体金属断裂时,按裂纹扩展路径可以分为穿晶断裂和沿晶断裂。
3,根据应力类型可分为纯剪切断裂和微孔聚集型断裂、解理断裂。
三、具体分析1,韧性断裂韧性断裂是金属材料断裂前产生明显宏观塑性变形的断裂,这种断裂有一个缓慢的撕裂过程,在裂纹扩展过程中不断地消耗能量。
韧性断裂的断裂面一般平行于最大切应力并与主应力成45º角。
用肉眼或放大镜观察时,端口呈纤维状,灰暗色。
纤维状是苏醒变形过程中微裂纹不断扩展和相连造成的,灰暗色则是纤维断口表面对光反射能力很弱所致。
中、低强度钢的光滑圆柱试样在室温下的静拉伸断裂是典型的韧性断裂,其宏观断口呈杯锥形,由纤维区、放射区和剪切唇三个区域组成,即所谓的断口特征三要素。
当光滑圆柱拉伸试样受拉伸力作用,在试验力达到拉伸力-伸长曲线最高点时,便在试样局部区域产生缩颈,同时试样的应力状态也由单向变为三向,且中心轴向应力最大。
在中心三向拉应力作用下,塑性变形难于进行,致使试样中心部分的夹杂物或第二相质点本身碎裂,或使夹杂物质点与基体界面脱离而形成微孔。
微孔不断长大和聚合就形成显微裂纹。
早期形成的显微裂纹,其端部产生较大塑性变形,且集中于极窄的高变形带内。
这些剪切变形带从宏观上看大致与径向呈50º~60º角。
金属材料的塑性变形与断裂机理
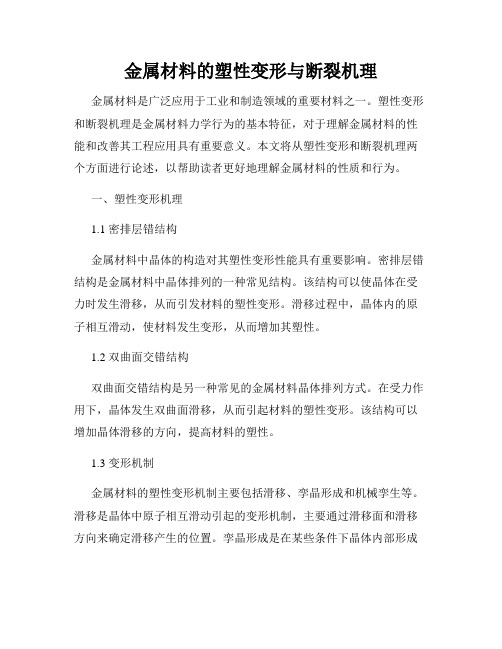
金属材料的塑性变形与断裂机理金属材料是广泛应用于工业和制造领域的重要材料之一。
塑性变形和断裂机理是金属材料力学行为的基本特征,对于理解金属材料的性能和改善其工程应用具有重要意义。
本文将从塑性变形和断裂机理两个方面进行论述,以帮助读者更好地理解金属材料的性质和行为。
一、塑性变形机理1.1 密排层错结构金属材料中晶体的构造对其塑性变形性能具有重要影响。
密排层错结构是金属材料中晶体排列的一种常见结构。
该结构可以使晶体在受力时发生滑移,从而引发材料的塑性变形。
滑移过程中,晶体内的原子相互滑动,使材料发生变形,从而增加其塑性。
1.2 双曲面交错结构双曲面交错结构是另一种常见的金属材料晶体排列方式。
在受力作用下,晶体发生双曲面滑移,从而引起材料的塑性变形。
该结构可以增加晶体滑移的方向,提高材料的塑性。
1.3 变形机制金属材料的塑性变形机制主要包括滑移、孪晶形成和机械孪生等。
滑移是晶体中原子相互滑动引起的变形机制,主要通过滑移面和滑移方向来确定滑移产生的位置。
孪晶形成是在某些条件下晶体内部形成镜像结构,从而产生变形。
机械孪生是晶体中发生变形所产生的一种特殊形态。
二、断裂机理2.1 断裂类型金属材料的断裂类型包括韧性断裂、脆性断裂和疲劳断裂。
韧性断裂是材料发生延性断裂,即在承受一定载荷后,材料仍能继续变形;脆性断裂是材料在承受载荷后突然断裂,变形能力较差;疲劳断裂是材料在长时间重复加载的作用下产生的断裂现象。
2.2 断裂因素金属材料的断裂受到多种因素的影响,主要包括应力、环境和缺陷等。
应力是导致材料发生断裂的最主要因素,当应力超过材料的承受能力时,断裂就会发生。
环境因素如温度、湿度等也会对金属材料的断裂行为产生影响。
此外,材料内部的缺陷如裂纹、夹杂等也会加速材料的断裂。
2.3 断裂表征方法断裂行为的表征对于评估材料的性能具有重要意义。
常见的断裂表征方法包括断口形貌观察、断口分析和断裂韧性测试等。
通过观察断口形貌可以了解材料的断裂模式,进一步深入分析可以推测断裂的原因。
金属断裂的微观机理与典型形貌

金属断裂的微观机理与典型形貌金属断裂是指金属材料在受到外力作用下发生破裂的现象。
金属断裂具有微观机理与典型形貌,这些机理与形貌的研究对于金属材料的设计和应用具有重要意义。
金属材料的断裂主要有两种机制:韧性断裂和脆性断裂。
韧性断裂是金属材料在外力作用下发生塑性变形后断裂,具有较大的断口伸长率和断口收缩面积。
脆性断裂则是金属材料在外力作用下发生无明显塑性变形而迅速断裂,具有较小的断口伸长率和断口收缩面积。
金属材料的断裂机理与其晶体结构和微观缺陷密切相关。
金属材料的晶体结构是由原子通过原子键结合而成的,其中包含晶粒、晶界和位错。
当金属材料受到外力作用时,原子之间的键会受到拉伸、剪切等力的作用,从而导致晶界滑移、位错运动等塑性变形。
当外力继续增大时,晶界和位错可能无法继续运动,从而导致金属材料的断裂。
金属材料的断裂形貌可以通过金属断口的观察来研究。
金属断口通常包括拉伸断口、韧窝和脆窝等不同形貌。
拉伸断口是金属在拉伸过程中发生断裂后的断口形貌,通常呈现出光洁的平面面貌。
韧窝是金属在韧性断裂过程中形成的圆形凹陷,它是由于金属在拉伸过程中发生局部塑性变形而形成的。
脆窝则是金属在脆性断裂过程中形成的不规则凹陷,它是由于金属在受到外力作用下迅速断裂而形成的。
金属断裂的微观机理与典型形貌对于金属材料的设计和应用具有重要意义。
通过研究金属断裂机理,可以了解金属材料在外力作用下的变形和破裂行为,从而指导金属材料的合理设计和使用。
同时,通过观察金属断口的形貌,可以评估金属材料的断裂韧性和脆性,为金属材料的选择和应用提供依据。
金属断裂具有微观机理与典型形貌。
金属材料的断裂机理与其晶体结构和微观缺陷密切相关,包括晶粒、晶界和位错等。
金属材料的断裂形貌可以通过金属断口的观察来研究,包括拉伸断口、韧窝和脆窝等不同形貌。
金属断裂的微观机理与典型形貌对于金属材料的设计和应用具有重要意义,可以指导金属材料的合理设计和使用。
通过研究金属断裂机理和观察金属断口的形貌,可以评估金属材料的断裂韧性和脆性,为金属材料的选择和应用提供依据。
- 1、下载文档前请自行甄别文档内容的完整性,平台不提供额外的编辑、内容补充、找答案等附加服务。
- 2、"仅部分预览"的文档,不可在线预览部分如存在完整性等问题,可反馈申请退款(可完整预览的文档不适用该条件!)。
- 3、如文档侵犯您的权益,请联系客服反馈,我们会尽快为您处理(人工客服工作时间:9:00-18:30)。
金属断裂机理完整版Newly compiled on November 23, 2020金属断裂机理1 金属的断裂综述断裂类型根据断裂的分类方法不同而有很多种,它们是依据一些各不相同的特征来分类的。
根据金属材料断裂前所产生的宏观塑性变形的大小可将断裂分为韧性断裂与脆性断裂。
韧性断裂的特征是断裂前发生明显的宏观塑性变形,脆性断裂在断裂前基本上不发生塑性变形,是一种突然发生的断裂,没有明显征兆,因而危害性很大。
通常,脆断前也产生微量塑性变形,一般规定光滑拉伸试样的断面收缩率小于5%为脆性断裂;大于5%为韧性断裂。
可见,金属材料的韧性与脆性是依据一定条件下的塑性变形量来规定的,随着条件的改变,材料的韧性与脆性行为也将随之变化。
多晶体金属断裂时,裂纹扩展的路径可能是不同的。
沿晶断裂一般为脆性断裂,而穿晶断裂既可为脆性断裂(低温下的穿晶断裂),也可以是韧性断裂(如室温下的穿晶断裂)。
沿晶断裂是晶界上的一薄层连续或不连续脆性第二相、夹杂物,破坏了晶界的连续性所造成的,也可能是杂质元素向晶界偏聚引起的。
应力腐蚀、氢脆、回火脆性、淬火裂纹、磨削裂纹都是沿晶断裂。
有时沿晶断裂和穿晶断裂可以混合发生。
按断裂机制又可分为解理断裂与剪切断裂两类。
解理断裂是金属材料在一定条件下(如体心立方金属、密排六方金属、合金处于低温或冲击载荷作用),当外加正应力达到一定数值后,以极快速率沿一定晶体学平面的穿晶断裂。
解理面一般是低指数或表面能最低的晶面。
对于面心立方金属来说(比如铝),在一般情况下不发生解理断裂,但面心立方金属在非常苛刻的环境条件下也可能产生解理破坏。
通常,解理断裂总是脆性断裂,但脆性断裂不一定是解理断裂,两者不是同义词,它们不是一回事。
剪切断裂是金属材料在切应力作用下,沿滑移面分离而造成的滑移面分离断裂,它又分为滑断(又称切离或纯剪切断裂)和微孔聚集型断裂。
纯金属尤其是单晶体金属常发生滑断断裂;钢铁等工程材料多发生微孔聚集型断裂,如低碳钢拉伸所致的断裂即为这种断裂,是一种典型的韧性断裂。
根据断裂面取向又可将断裂分为正断型或切断型两类。
若断裂面取向垂直于最大正应力,即为正断型断裂;断裂面取向与最大切应力方向相一致而与最大正应力方向约成45°角,为切断型断裂。
前者如解理断裂或塑性变形受较大约束下的断裂,后者如塑性变形不受约束或约束较小情况下的断裂。
按受力状态、环境介质不同,又可将断裂分为静载断裂(如拉伸断裂、扭转断裂、剪切断裂等)、冲击断裂、疲劳断裂;根据环境不同又分为低温冷脆断裂、高温蠕变断裂、应力腐蚀和氢脆断裂;而磨损和接触疲劳则为一种不完全断裂。
常用的断裂分类方法及其特征见下表:2 微孔聚合断裂机制相关概念定义:微孔聚合型断裂过程是在外力作用下,在夹杂物、第二相粒子与基体的界面处,或在晶界、孪晶带、相界、大量位错塞积处形成微裂纹,因相邻微裂纹的聚合产生可见微孔洞,以后孔洞长大、增殖,最后连接形成断裂。
微孔萌生的时间:若材料中第二相与基体结合强度低,在颈缩之前;反之,在颈缩之后。
微孔萌生成为控制马氏体时效钢断裂过程的主要环节。
微孔聚合型断裂形成的韧窝有三种:1)拉伸型等轴状韧窝;2)剪切型伸长韧窝;3)拉伸撕裂型伸长韧窝。
韧窝的大小和深浅取决于第二相的数量、分布以及基体的塑性变形能力,如第二相较少、分布均匀且基体塑性变形能力又强,那么韧窝大而深;若基体的加工硬化能力很强,韧窝大而浅。
断口形貌特征A种(15 mA cm2)变体钢断裂面的形貌---兼有微孔聚合断裂和解理断裂B (30 mA cm2)种变体钢断裂面形貌---兼有韧窝和二次裂纹以上图片是对“800 C–Mn–Si超强度钢(TRIP 800 steels)”的A、B两种变体钢试样进行拉伸试验的断口形貌,括号中标注的是实验具体使用的电流密度值。
本实验研究氢含量对TRIP 800 steels性质和断口形貌的影响,上面图2-1说明氢含量高使得断口表现出了较多较浅的韧窝,韧窝浅因为氢脆效应降低了材料的塑性变形能力。
另外,图2-2是在加入了氢吸收促进剂之后的断裂形貌,除了有韧窝出现,还有了二次断裂,并且产生于夹杂物(即氢吸收促进剂)旁边。
微孔聚合断裂机制微孔聚集断裂为剪切断裂的一种形式,微孔聚集断裂是材料韧性断裂的普遍形式,其断口在宏观上常呈现暗灰色、纤维状,微断口特征花样则是端口上分布大量“韧窝”,微孔聚集断裂过程包括微孔形核、长大、聚合直至断裂。
微孔聚合断裂过程由于应力状态或加载方式的不同,微孔聚合型断裂所形成的韧窝有三种类型:(1)拉伸型的等轴状韧窝。
裂纹扩展方向垂直于最大主应力σmax,σmax是均匀分布于断裂平面上,拉伸时呈颈缩的试样中心部分就显示这种韧窝状。
(2)剪切型的伸长韧窝。
在拉伸试样的边缘,两侧均由剪应力切断,显示这种韧窝形状,韧窝很大如卵形,其上下断面所显示的韧窝,其方向是相反的。
(3)拉伸撕裂的伸长韧窝。
产生这种韧窝的加载方式有些和等轴状韧窝类似,但是等轴状韧窝可以认为是在试样中心加拉伸载荷的,而拉伸型韧窝是在试样边缘加载的,因而不是沿截面均匀分布的,在边缘部分应力很大,裂纹是由表面逐渐向内部延伸的,σmax好像我们把粘着的两张纸,从一端把它们逐渐撕开一样故称拉伸撕裂型。
表面有缺口的试样或者裂纹试样,其断口常显示这种类型。
这种类型的韧窝,韧窝小而浅,裂纹扩展快,故在宏观上常为脆断,所以不要把微孔聚合型的微观机制都归之为韧断,这也是宏观和微观不能完全统一之处。
SPA-H集装箱板断口形貌700×上图为拉伸断口形貌,断裂全部为韧性断裂,断口呈韧窝状,夹杂物少。
断口形貌分析图4与图5分别给出了复合材料室温和高温拉伸后试样的断口形貌。
可以看出,室温条件下,TMC1 为韧性断裂,其断口有许多较浅的韧窝,而TMC2 为典型脆性断裂,其断口存在河流花样以及脆性解离面。
与等轴组织较浅的韧窝相比,TMC1 的层片状组织的增强体附件韧窝相对较深且较细小,这主要是因为层片组织对源自增强体断裂的裂纹具有很好的阻碍作用。
同样,从断口来看,层片组织的TMC2 较等轴组织的延性要略好,这些结果与力学性能是一致的。
高温条件下,两种热处理下的TMCs 都表现出明显的延性断裂特征,并且温度越高韧窝越深。
而由于层片组织不利于协调变形,因而塑性韧窝不易聚集长大,故表现出的相对细小的韧窝。
不同组织的复合材料室温拉伸的扫描电镜断口形貌不同组织的复合材料高温拉伸的扫描电镜断口形貌3 解理断裂形貌特征解理断裂的端口形貌是河流状花样。
解理台阶、河流花样以及舌状花样都是解理断裂的基本微观特征。
形成原理解理断裂是在正应力作用产生的一种穿晶断裂,断裂面沿一定的晶面发生的,这个平面叫做解理面。
解理台阶是沿两个高度不同的平行解理面上扩展的解理裂纹相交时形成的。
形成过程有两种方式:通过解理裂纹与螺型位错相交形成;通过二次解理或撕裂形成。
第一种,当解理裂纹与螺型位错相遇时,便形成一个台阶,裂纹继续向前扩展,与许多螺型位错相交便形成众多台阶,他们沿裂纹前端滑动而相互交汇,同号台阶相互汇合长大,异号台阶相互抵消,当汇合台阶足够大的时候便在电镜下观察为河流状花样。
第二种,二次解理是指在解理裂纹扩展的两个互相平行解理面间距较小时产生的,但若解理裂纹的上下两个面间距远大于一个原子间距时,两解理裂纹之间的金属会产生较大的塑性变形,结果由于塑性撕裂而形成台阶,称为撕裂棱晶界。
舌状花样是由于解理裂纹沿孪晶界扩散留下的舌头状凹坑或凸台,故在匹配断口上“舌头”为黑白对应的。
42CrMo钢的冲击试样断口的解理断口微观形貌解理断口形貌特征河流花样(riverpattern)解理断口电子图像的主要特征是“河流花样”,河流花样中的每条支流都对应着一个不同高度的相互平行的解理面之间的台阶。
解理裂纹扩展过程中,众多的台阶相互汇合,便形成了河流花样。
在河流的“上游”,许多较小的台阶汇合成较大的台阶,到“下游”,较大的台阶又汇合成更大的台阶。
河流的流向恰好与裂纹扩展方向一致。
所以人们可以根据河流花样的流向,判断解理裂纹在微观区域内的扩展方向。
舌状裂面解理裂纹与孪晶(见孪生)相遇时可沿孪晶面形成局部裂纹,它发展到一定程度后与解理面上的裂纹相连通,形成像躺在解理面上的舌状裂面。
这种裂面在低温高速加载的条件下最易发生。
解理扇台阶状解理裂纹不能直接通过晶界扩展到相邻晶粒中去,只能在晶界附近相邻晶粒内某些区域形成一些新裂缝,它们在传播过程中汇集成河流状花样并形成扇面形向四周扩展。
“河流”上游即解理扇,扇柄处是裂纹源,扇面下游即裂纹扩展方向。
准解理准解理断裂介于解理断裂和韧窝断裂之间,它是两种机制的混合。
准解理与解理的共同点:都是穿晶断裂;有小解理面;有台阶或撕裂棱及河流状花样。
不同点:准解理小刻面不是晶体学解理面;真正解理裂纹常源于晶界,而准解理裂纹则常源于晶内硬质点,形成从晶内某点发源的放射状河流花样。
它是另一种型式的准解理断裂,其断裂面上显现有较大的塑性变形,特征是断口上存在由于几个地方的小裂纹分别扩展相遇发生塑性撕裂而形成的撕裂岭。
准解理断裂面不是一个严格准确的解理面,有人认为准解理断裂是解理和微孔聚合的混合机制,它常见于淬火回火钢中。
4 沿晶断裂概念沿晶断裂是指裂纹在晶界上形成并沿晶界扩展的断裂形式。
金属材料中的裂纹沿晶界扩展而产生断裂。
当沿晶断裂断口形貌呈粒状时又称晶间颗粒断裂。
多数情况下沿晶断裂属于脆性断裂,但也可能出现韧性断裂,如高温蠕变断裂。
在多晶体变形中,晶界起协调相邻晶粒变形的作用。
但当晶界受到损伤,其变形能力被削弱,不足以协调相邻晶粒的变形时,便形成晶界开裂。
裂纹扩展总是沿阻力最小的路径发展,遂表现为沿晶断裂。
钼的沿晶断裂形成原因产生沿晶断裂一般有如下原因:(1)晶界上存在有脆性沉淀相;(2)杂质和合金元素在晶界偏析,致使晶界弱化;(3)热应力作用;(4)环境引起的沿晶腐蚀;(5)晶界有弥散相析出。
晶界上有脆性沉淀相如果脆性相在晶界面上覆盖得不连续,例如AIN粒子在钢的晶界面上的分布,将产生微孔聚合型沿晶断裂;如果晶界上的脆性沉淀相是连续分布的,例如奥氏体Ni—Cr钢中形成的连续碳化物网状,则将产生脆性薄层分裂型断裂。
晶界有使其弱化的夹杂物如钢中晶界上存在P、S、As、Sb、Sn等元素。
有害元素沿晶界富集,降低了晶界处表面能,使脆性转变温度向高温推移,明显提高了材料对温度和加载速率的敏感性,在低温或动载条件下发生沿晶脆断。
Ni原本是穿晶断裂,加入S元素后就变为沿晶断裂热应力作用材料在热加工过程中,因加热温度过高,造成晶界熔化,严重减弱了晶界结合力和晶界处的强度,在受载时,产生早期的低应力沿晶断裂。
由于淬火工艺不当,产生淬火裂纹,使弹簧在使用时发生断裂。